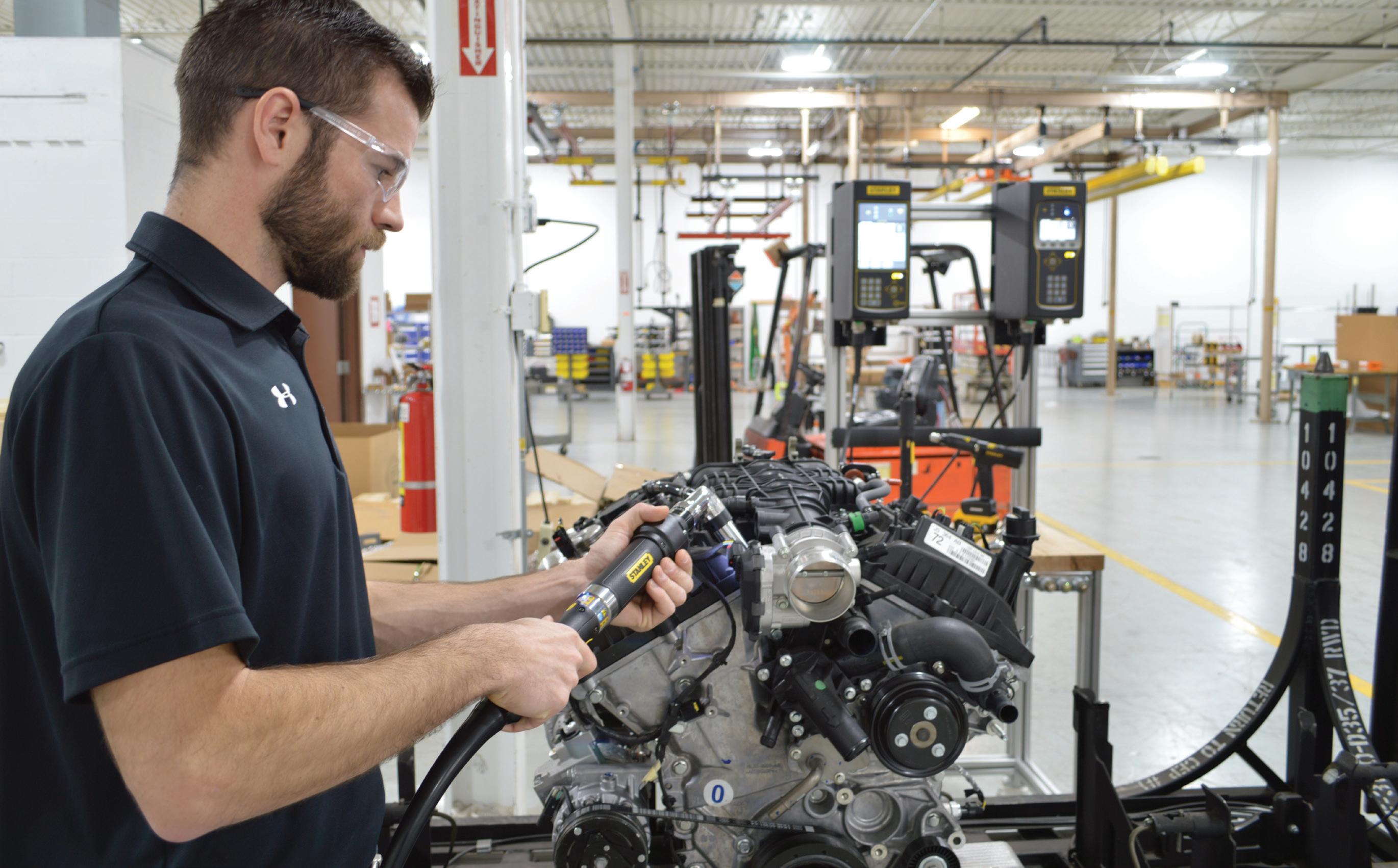
6 minute read
TOOLS
Director Program Management STANLEY Industrial
Reducing downtime is one key to a successful preventive maintenance program for tool and equipment use. Ensure the correct tools are in place, plan ahead for replacement parts, and always ensure workers are properly trained.
What are the best practices for tool and equipment preventive maintenance?
Reducing or eliminating the risk of unplanned downtime, manufacturing interruptions, and missing repair stock is an issue every manufacturer addresses at some point. One effective way to achieve best practices is to work on implementing a service preventive maintenance (PM) program to maximize manufacturing time and extend product quality and machine life.
Gaining a commitment within one’s organization to set up a regular PM program is the first step but implementing preventive maintenance in a way that’s flexible and manageable is critical to ensure that downtime and interruption risks are avoided. It’s not just saying it, it’s doing it.
What are the key drivers for success? A manufacturer can begin the PM journey by defining what they want to achieve, such as: • Extended tool and equipment lifecycles by eliminating breakdowns or failures • Increased tool and equipment product quality • Decreased high-dollar expediting fees and spare-part costs by planning out PM schedules • Decreased cost of additional workforce required to run or verify backup processes
To create a comprehensive plan:
Gather tool and equipment manufacturer (OEM) information on the tools and equipment Evaluate, with the OEM, the usage and PM guidelines from the factory — based on your application usage, create a baseline plan for preventive maintenance and repair Plan a PM program (some areas of the plant may be different based on applications and use of the tools and equipment) Ensure the proper supplies and spare parts are on hand and a re-order plan is in place once the parts are consumed to ensure the necessary inventory is always on hand Establish checklists for each area Audit the plan and implement changes based on successes or failures
Who drives success? The ideal leader for any given PM program is the maintenance team. Along with possessing the correct skills, they’re experienced practitioners of the product workflow and are responsible for the high-quality output.
In addition:
• Engage the service and repair teams (internal and/or external) in the planning and ask for feedback • Involve the quality team to implement the process as part of the standard operating procedure • Lean on OEMs and/or your distribution partners who can provide sales and servicing support • Manufacturing and operations teams must buy-in and commit to the plan to rotate tools and equipment for preventive maintenance to ensure a quality PM program
The lack of expertise and acceptance from the team is the primary reason PM programs may fail.
Accessing the proper assistance, support, and knowledge can help develop the correct processes and habits from the start to support the team — and to keep the program active.
Once the assessment of and planning for the program are complete, the PM implementation team will depend on the size and complexity of the facility. Typically, this team is relatively small.
The focus should be on the rollout, acceptance, and results of the program with the extended teams.
How can success be measured? When the program is implemented, success can be measured and celebrated with the team involved after any ongoing challenges or problems are resolved.
Depending on the tools, equipment, and the type of application, some of the performance indicators to measure success are:
THE IDEAL LEADER
FOR ANY GIVEN PM PROGRAM IS THE MAINTENANCE TEAM.
A successful maintenance program means decreasing the likelihood of tool or equipment breakdowns and failures. Invest in quality products and follow the manufacturer’s guidelines for use and care.
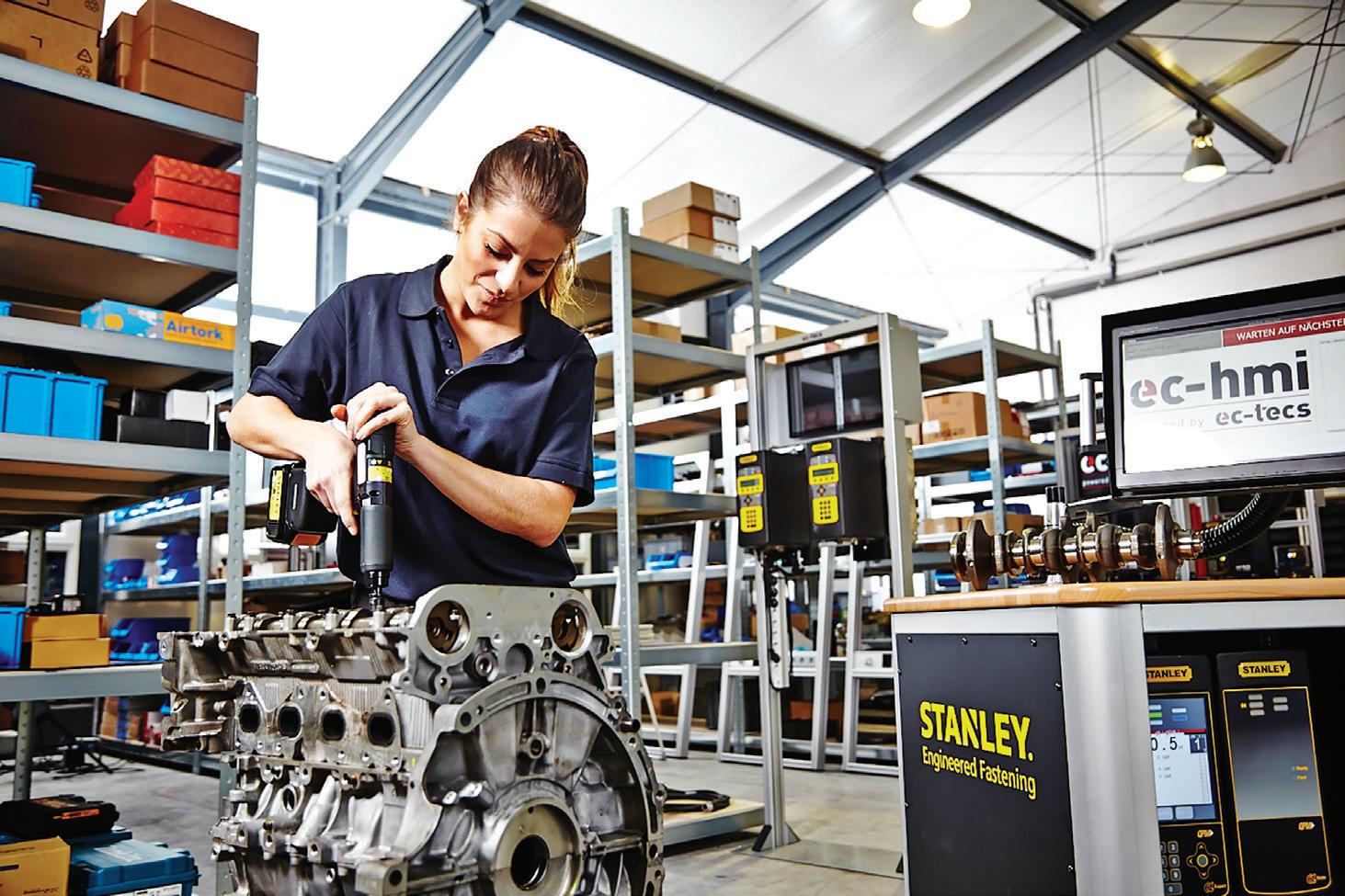
TOOLS
• Improved system uptime • Reduced system lifecycle costs • Planned maintenance percentage – the time spent on planned versus unplanned maintenance • Preventive maintenance compliance rate – how many scheduled PM work orders are completed within a set amount of time • Critical scheduled maintenance percentage – the impact of late planned maintenance work • Downtime analysis for root cause and resolution timing – downtime resolution and timing
With any program, there are opportunities to enhance and supplement the program with digital tools to assist in collecting data, tracking maintenance and repairs, and supporting the team with the necessary information to excel. The team can and should identify this when the goals of the program are created and evaluated.
Summary There are several reasons why it’s important to implement a preventive maintenance program and, over time, the program will pay for itself.
Avoid waiting for the high cost of downtime and failure, or losing on investments, before implementing such a strategy.
Implementing a PM program will:
• Ensure continued uptime, while reducing downtime • Reduce the chances of complete breakdowns • Recognize the problems earlier through a preventive maintenance plan • Reduce the chance of emergency repair calls and overtime to resolve issues • Reduce downtime for bringing in and expediting spare parts • Reduce the potential of unnecessary repairs
Structural Adhesives to Replace Traditional Fasteners
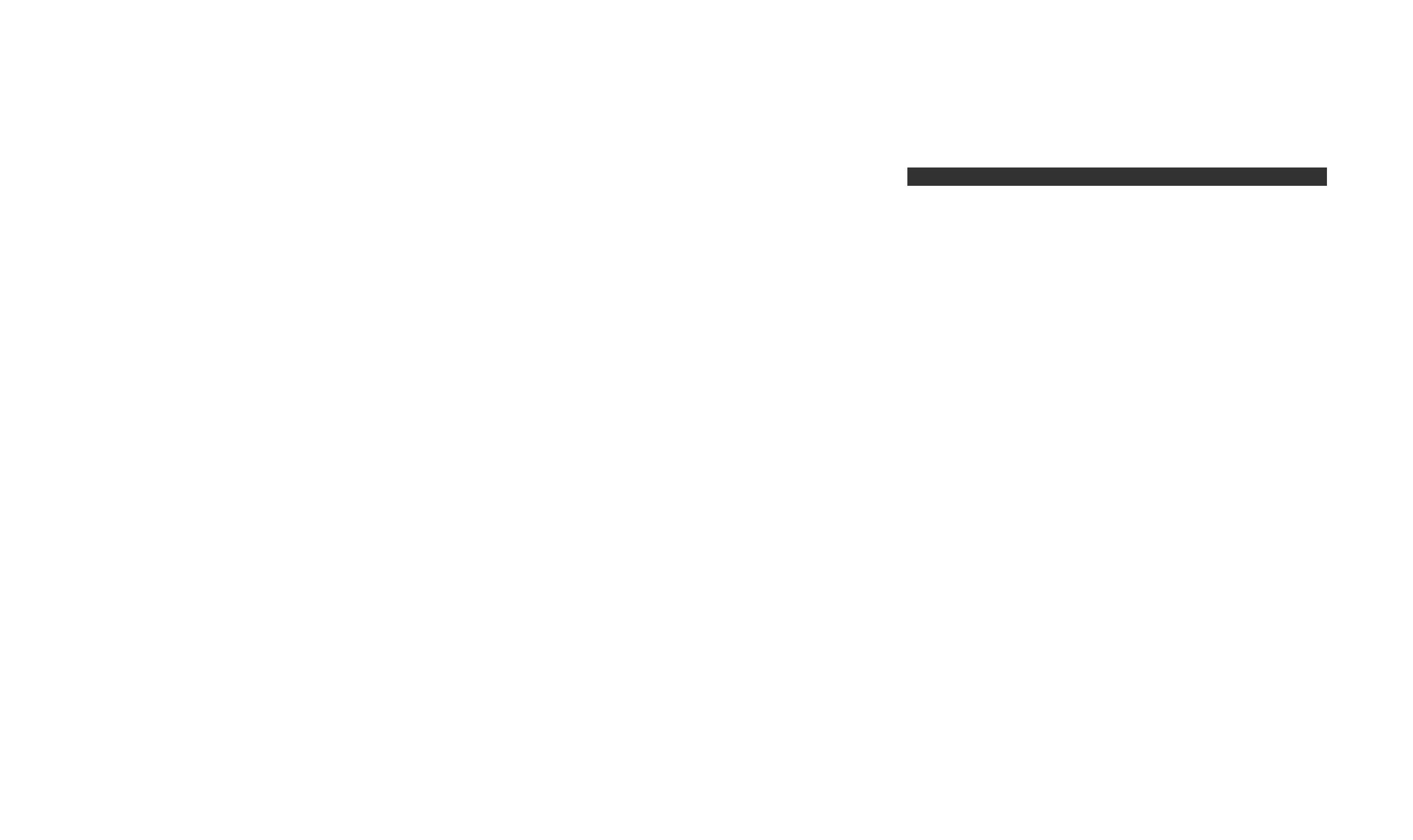
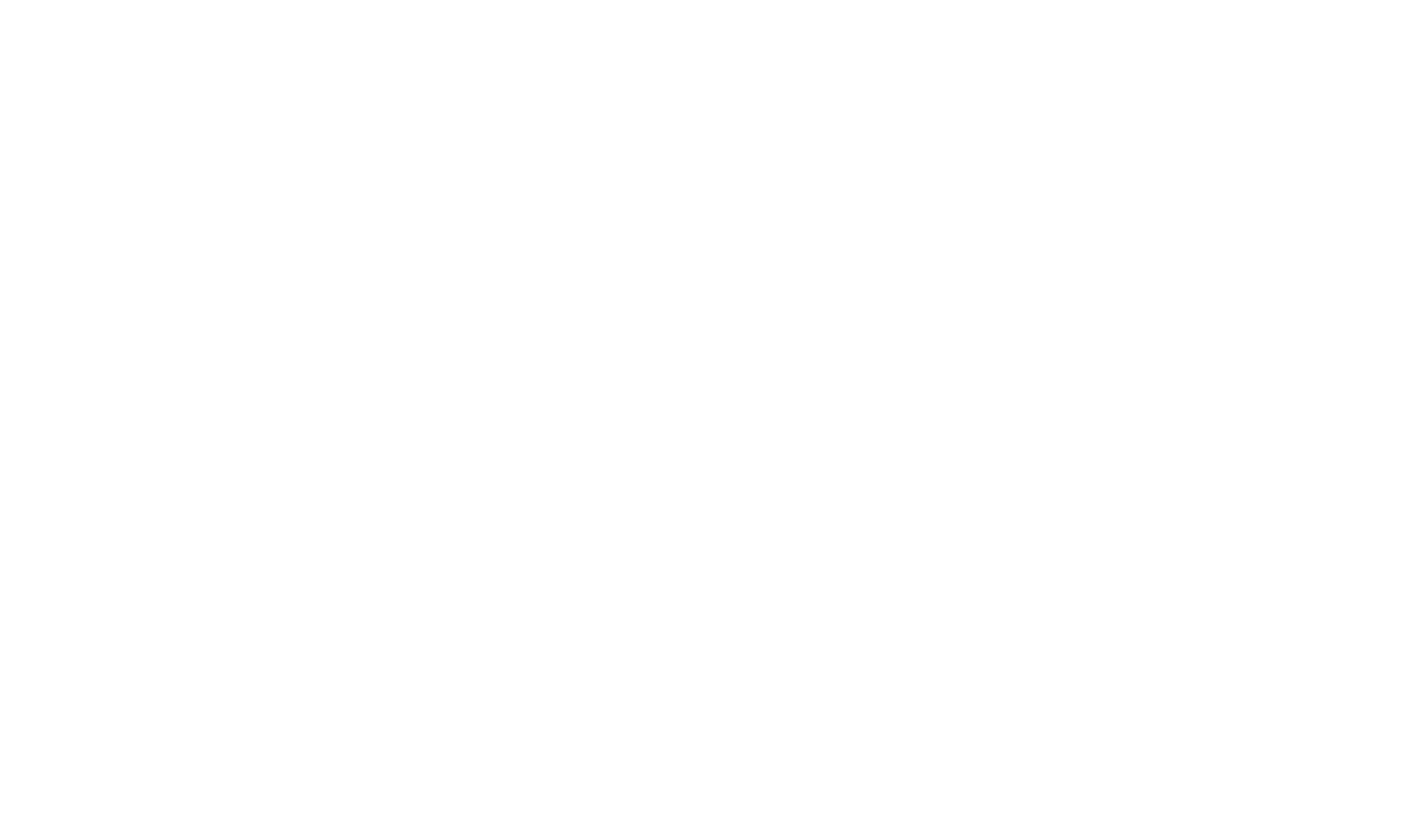
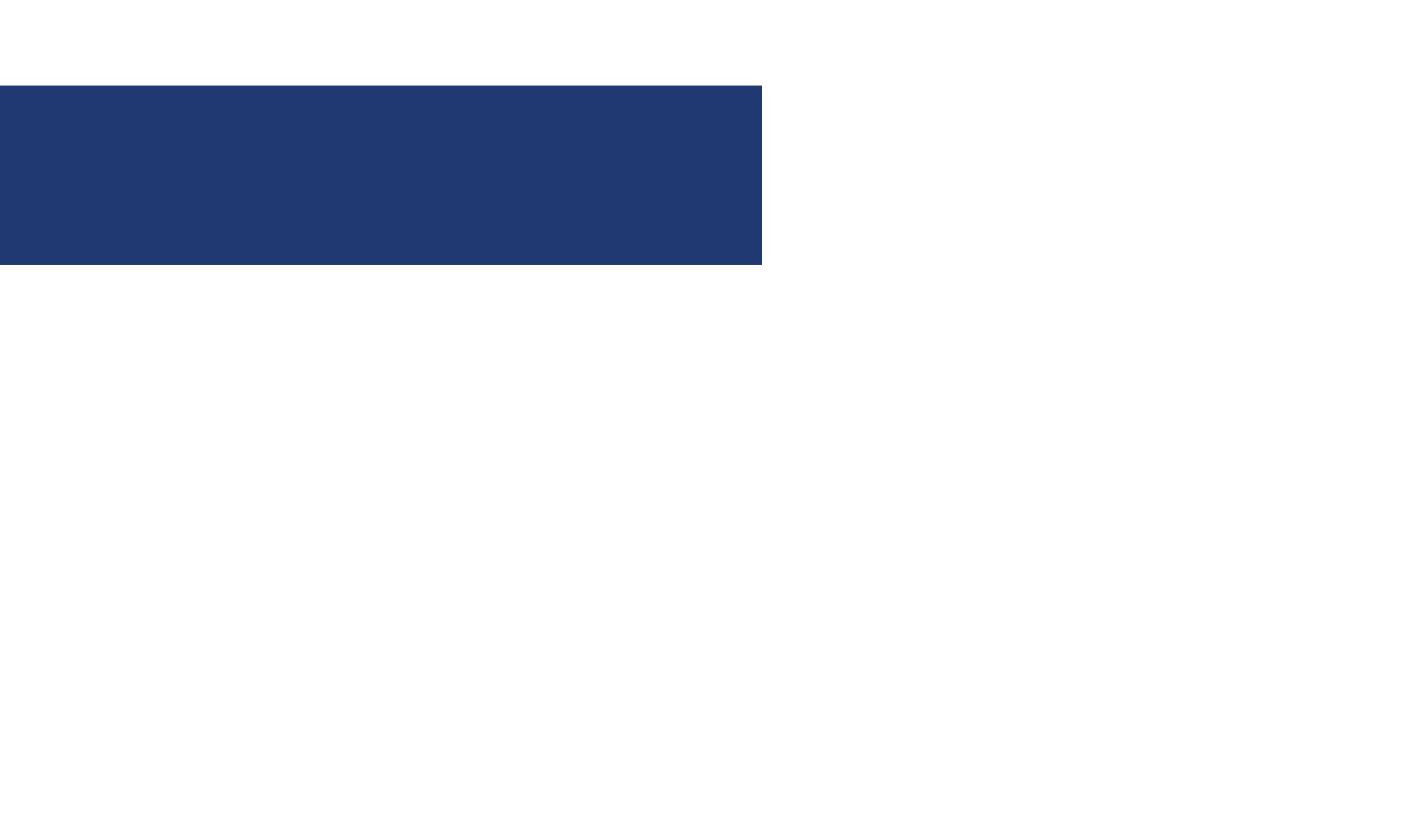
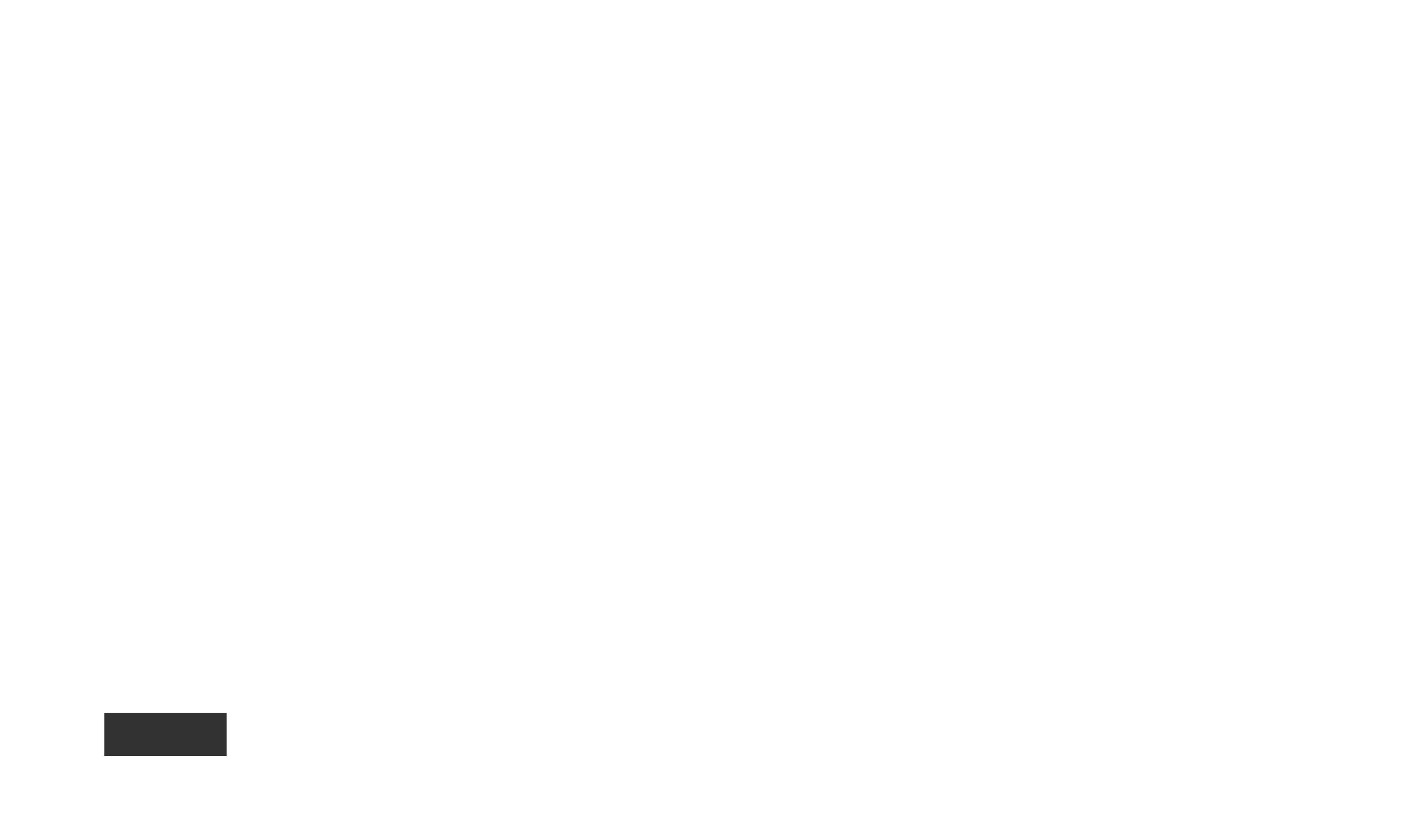
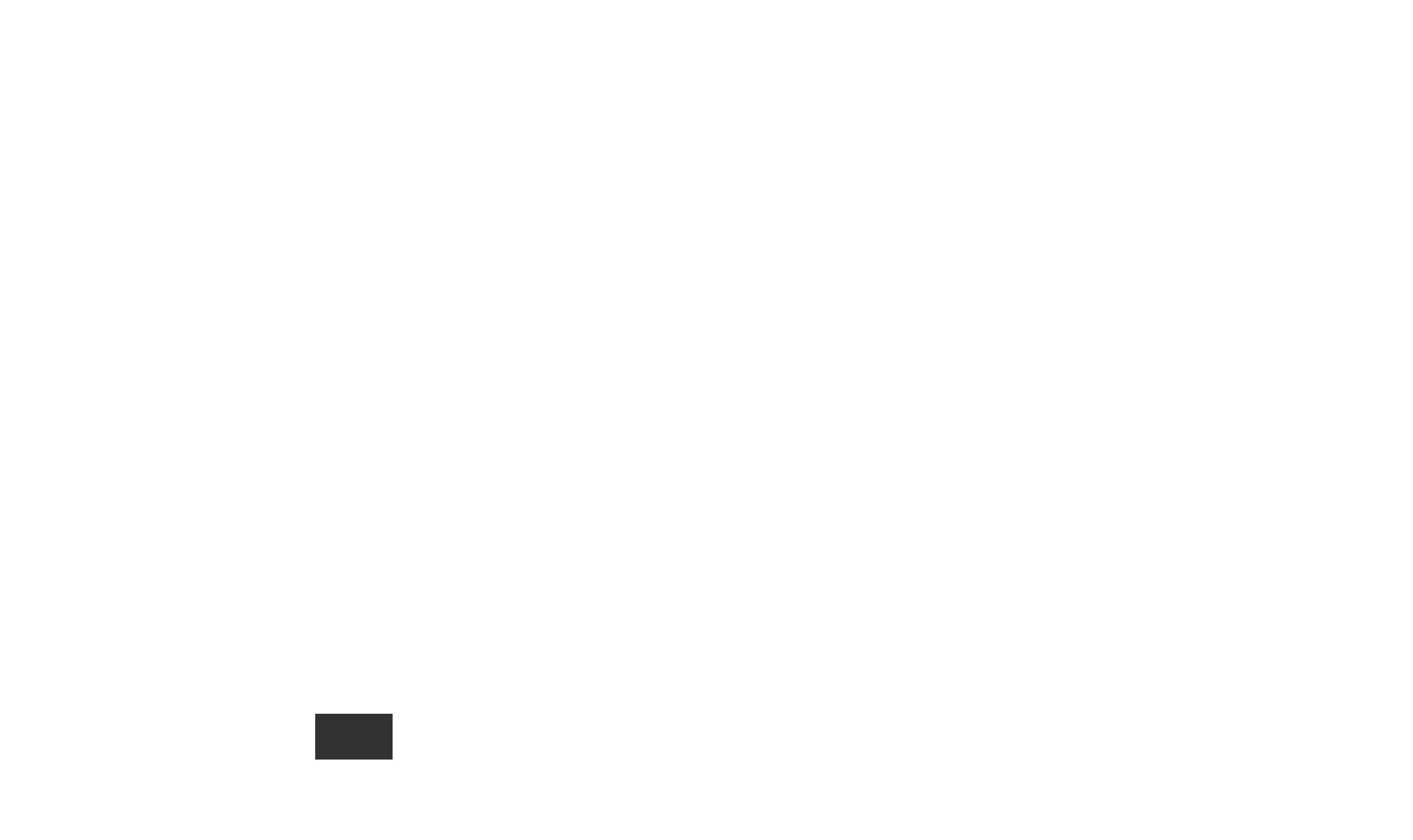
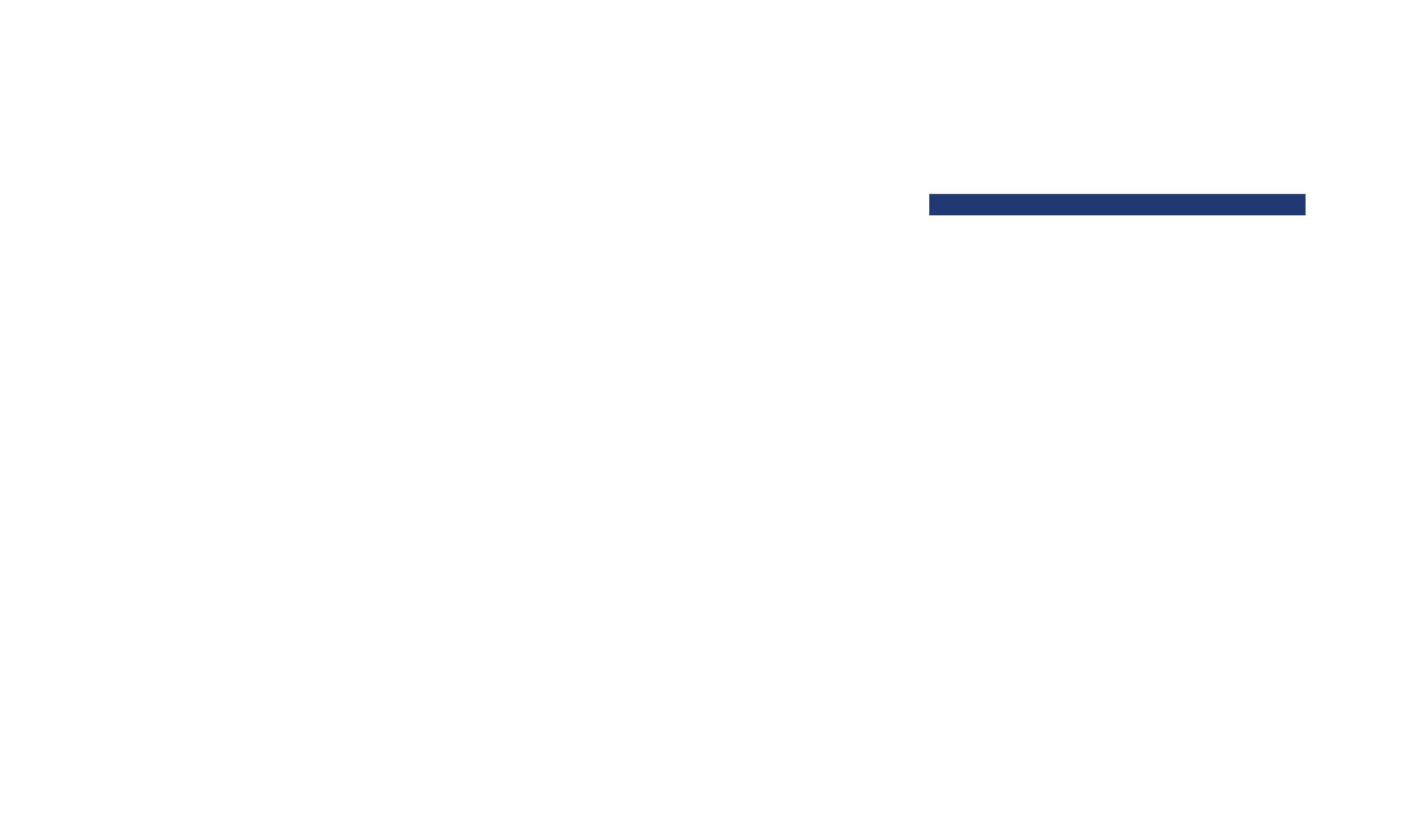
Let our team of experts help you make the switch to adhesives.
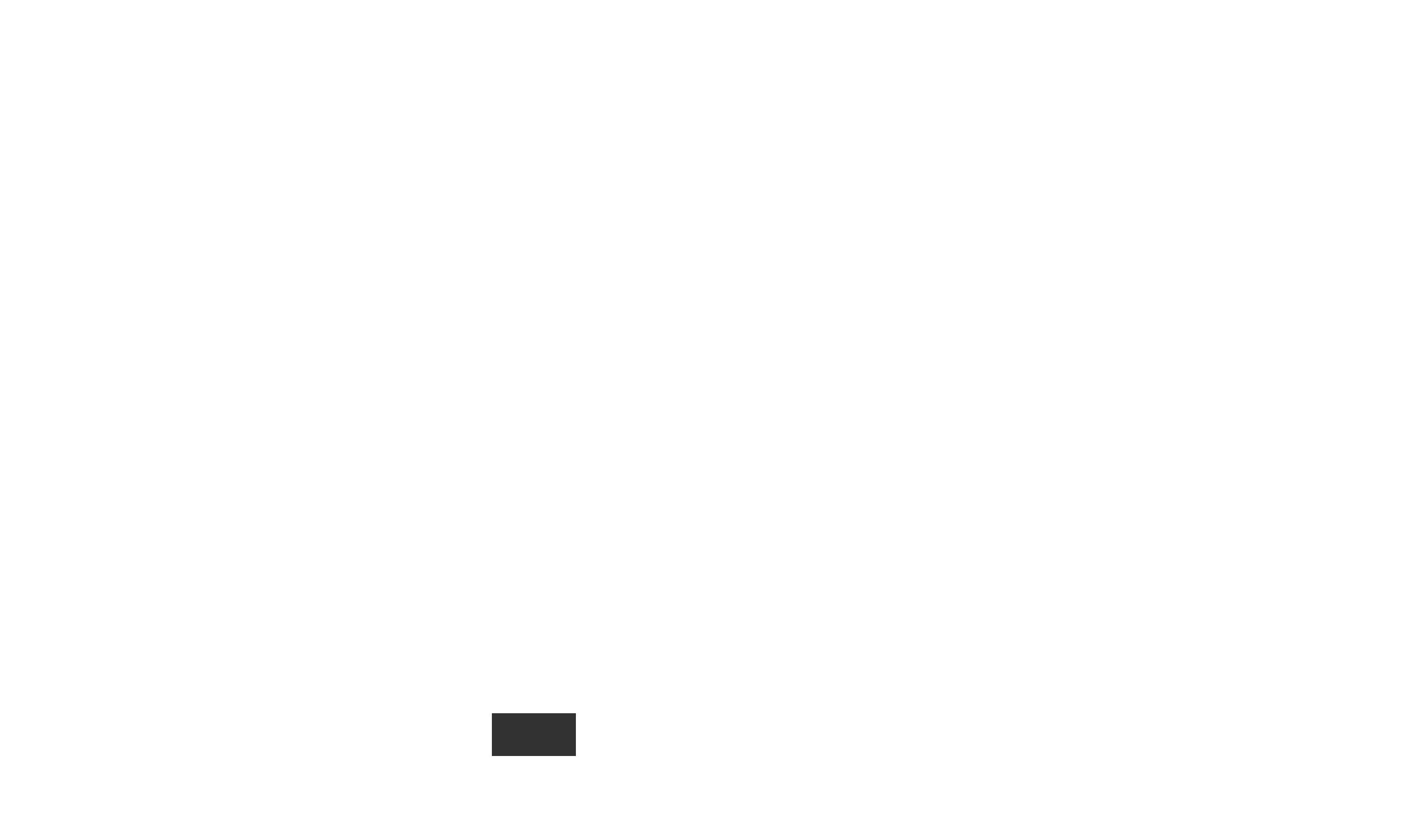
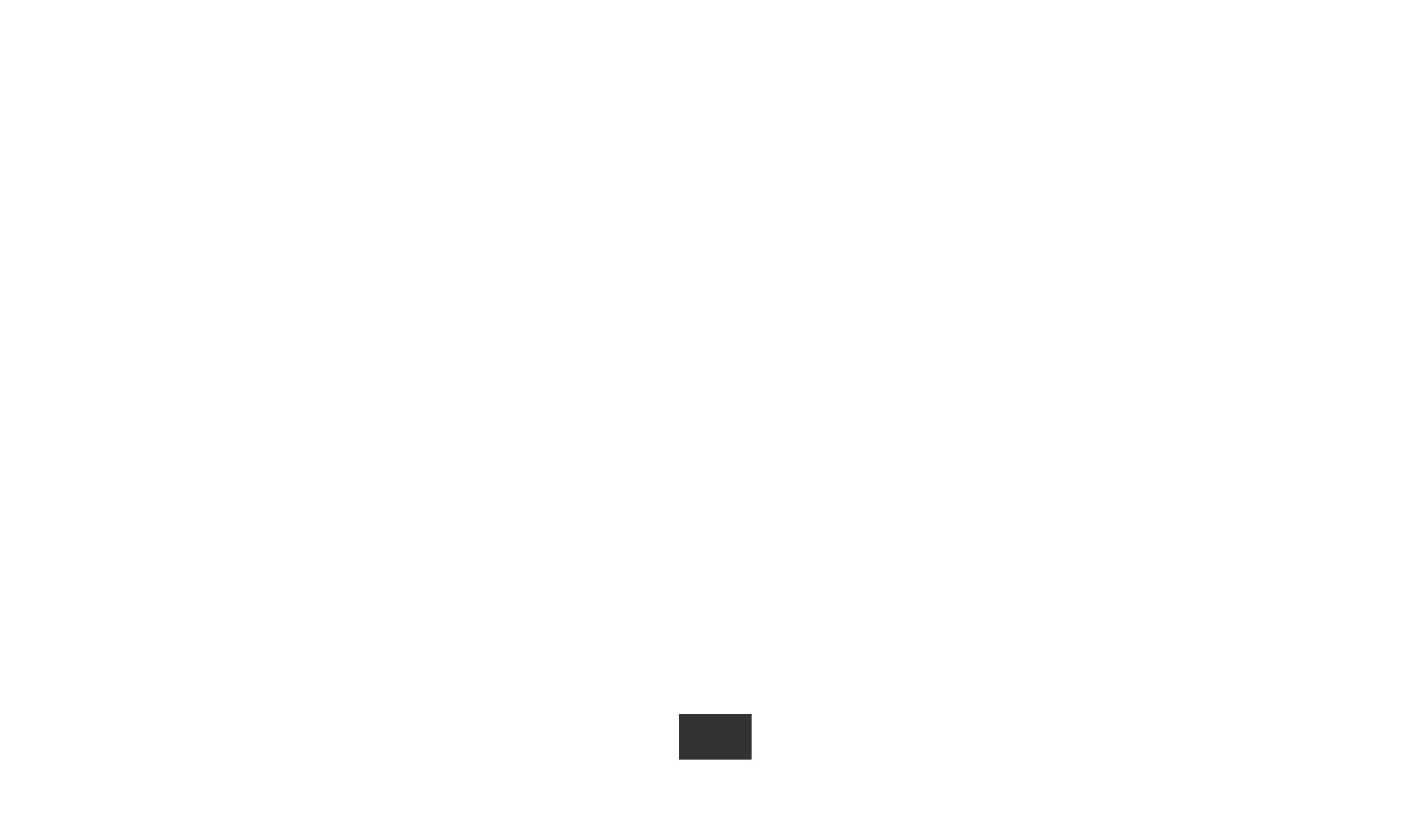
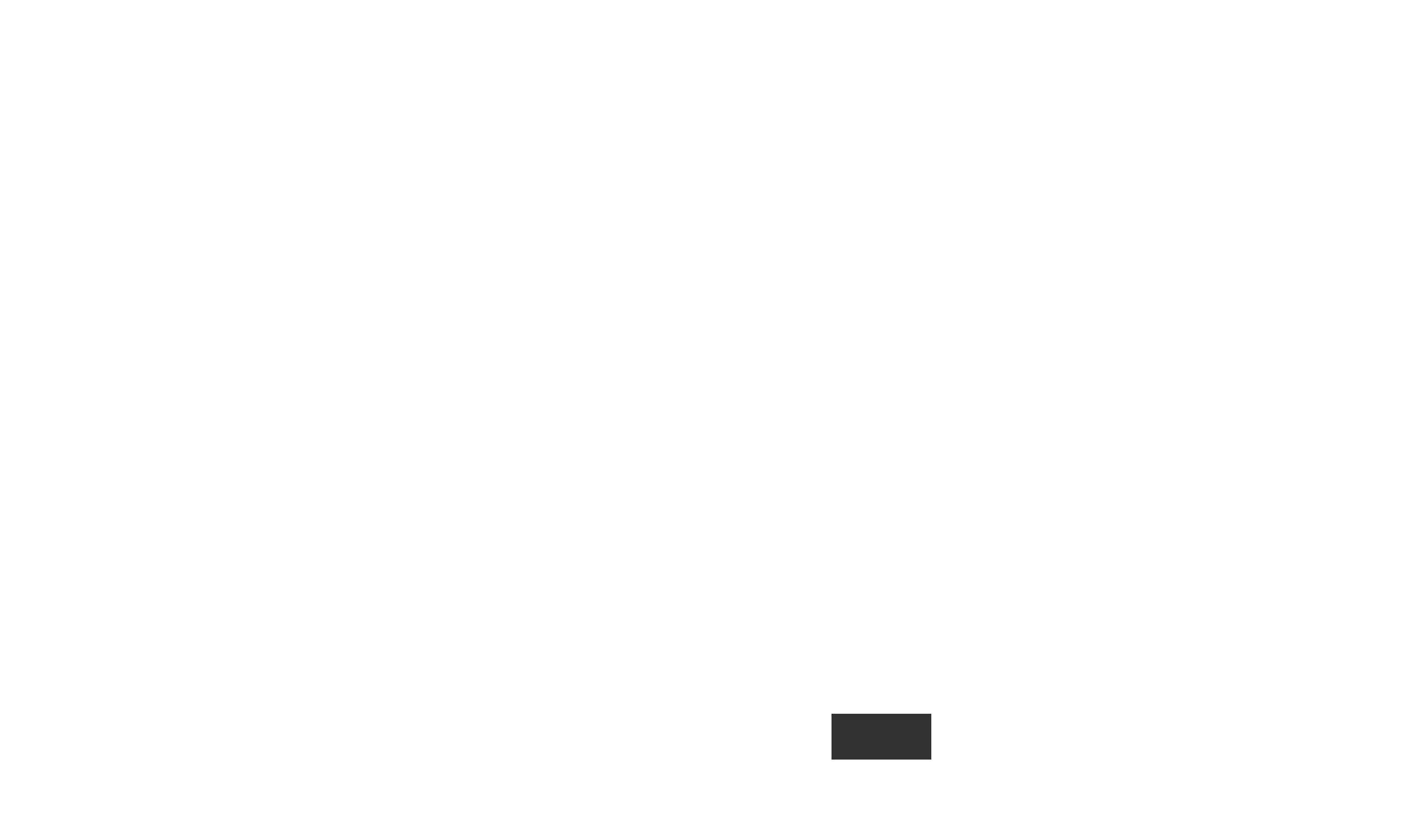
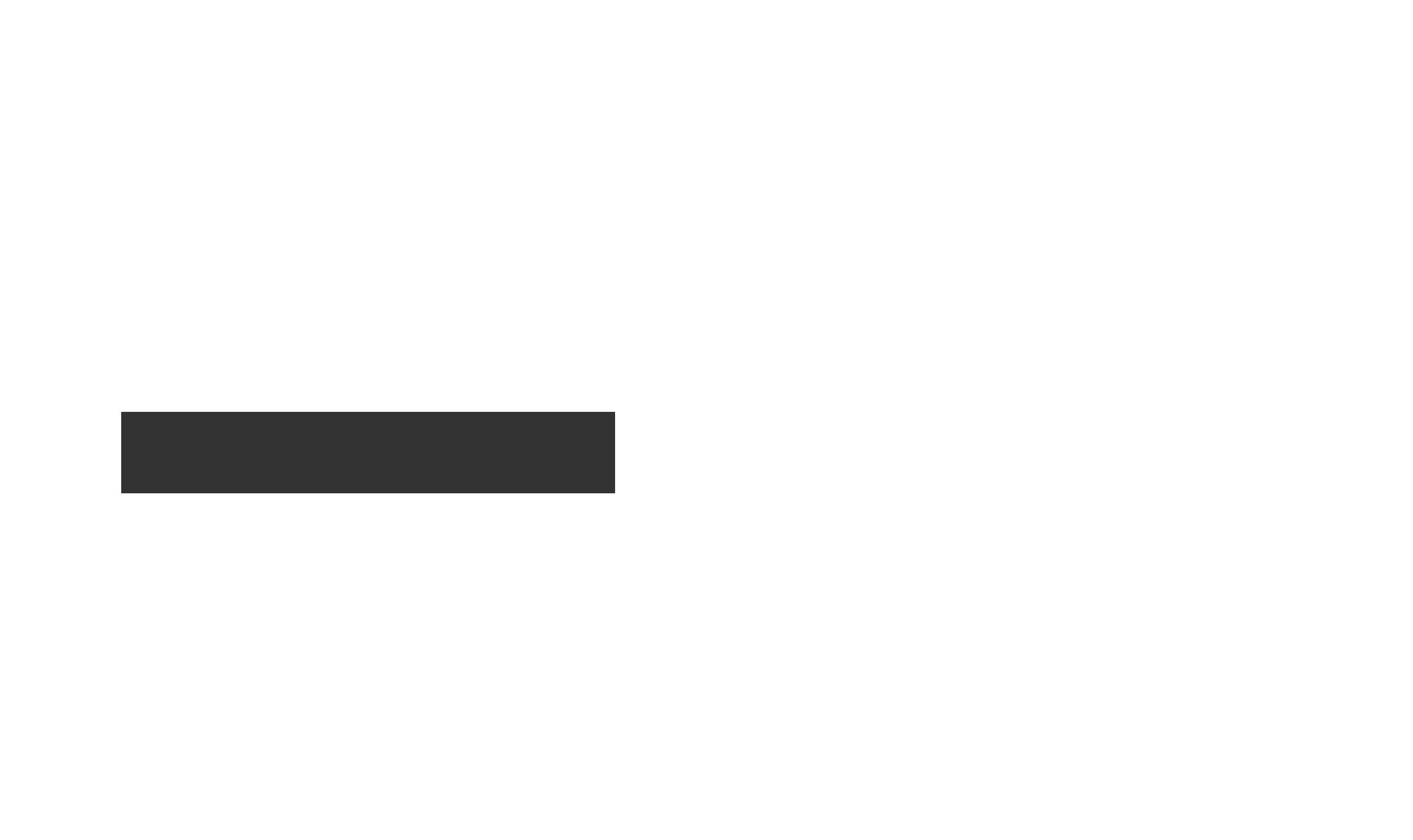

Your total solutions provider in specialty chemicals & application equipment.
800.888.0698 | ellsworth.com | info@ellsworth.com
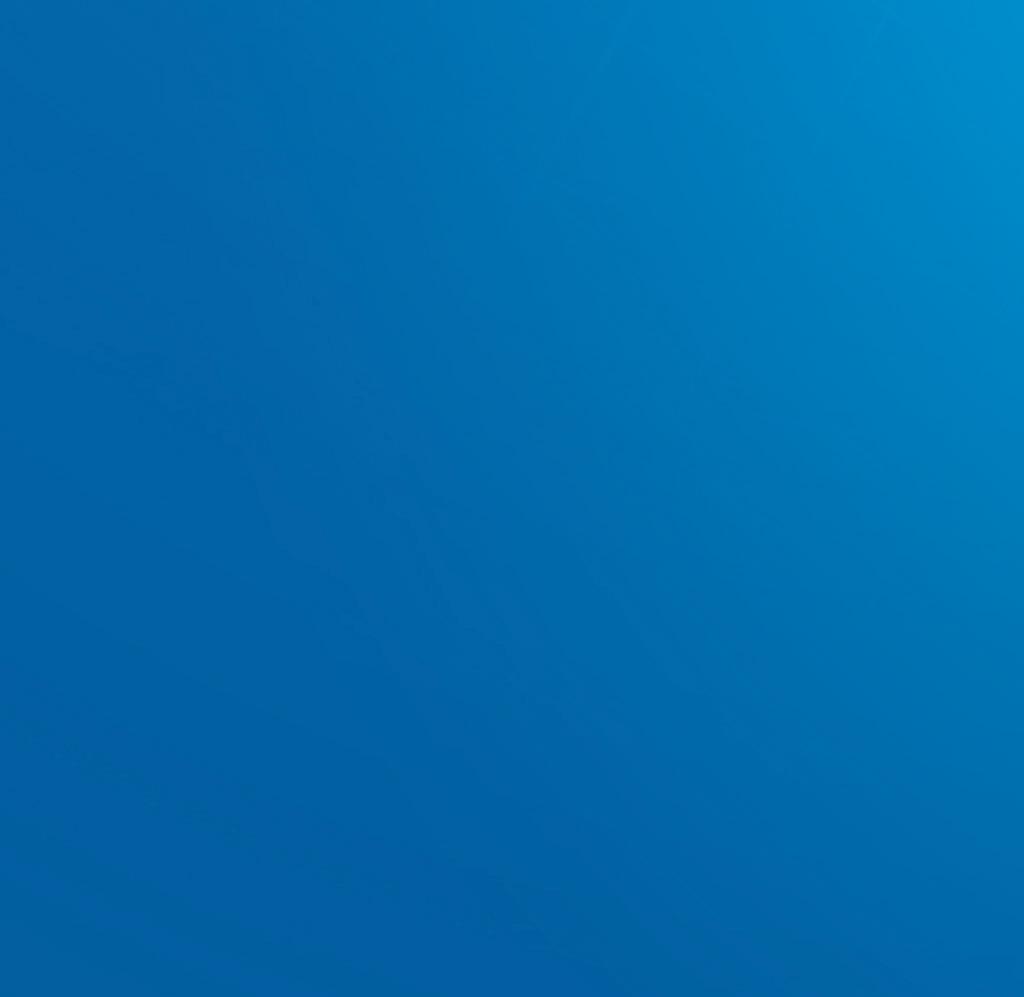
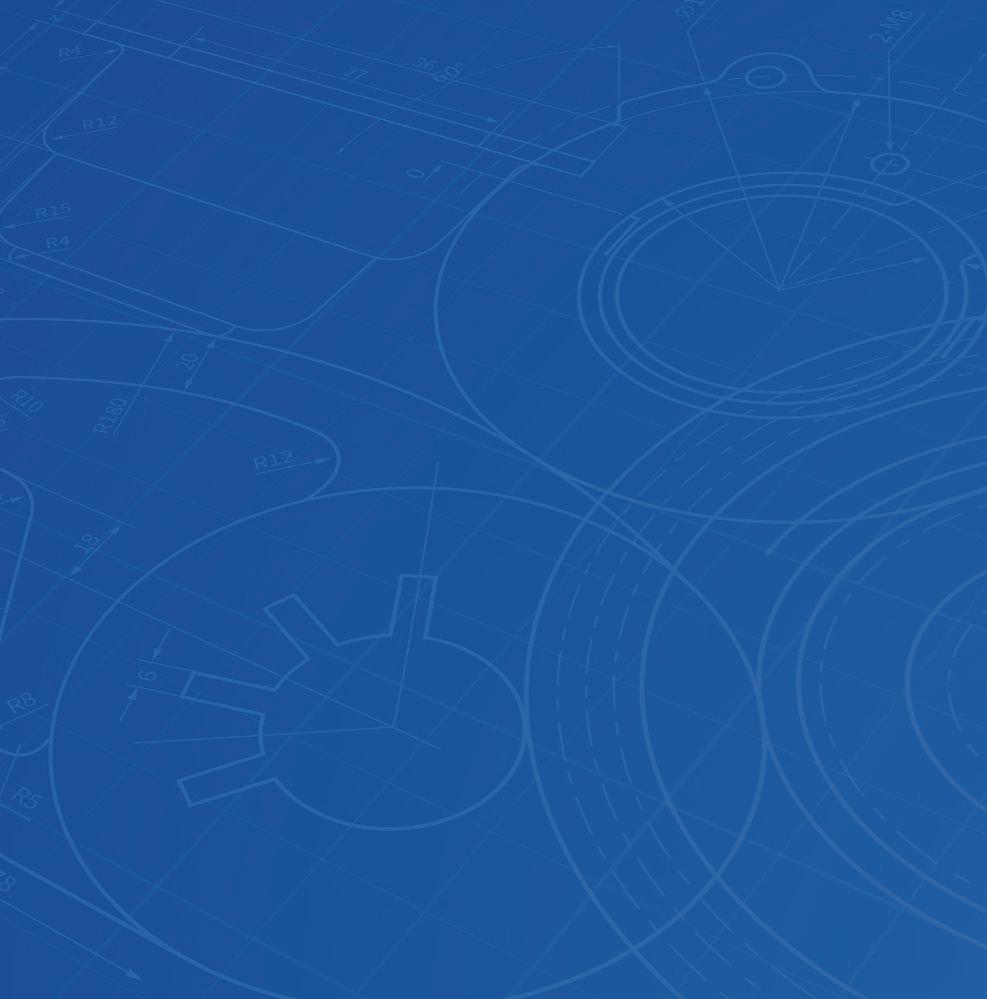
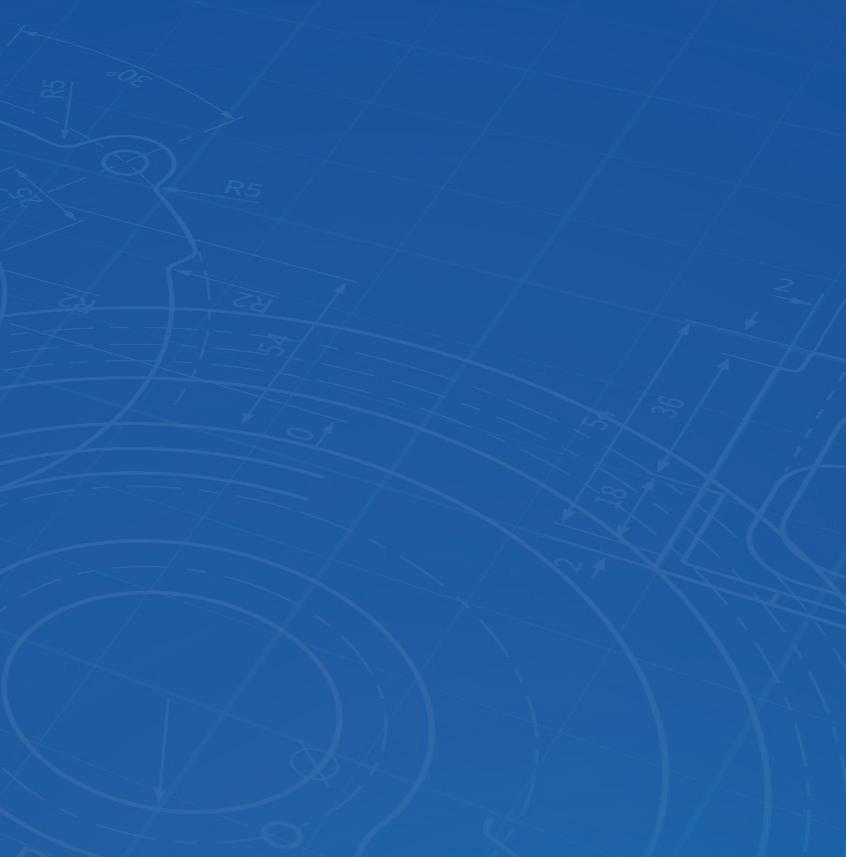
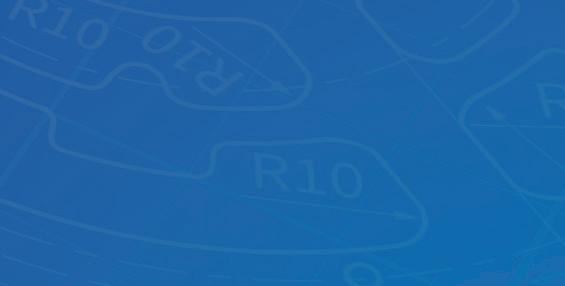
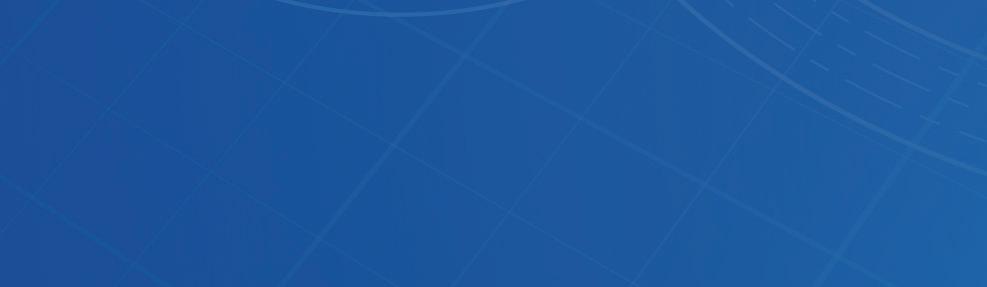
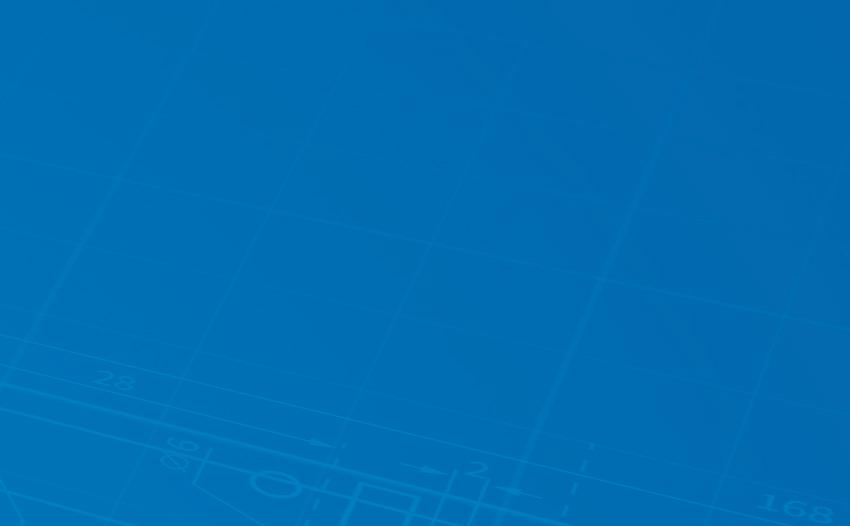
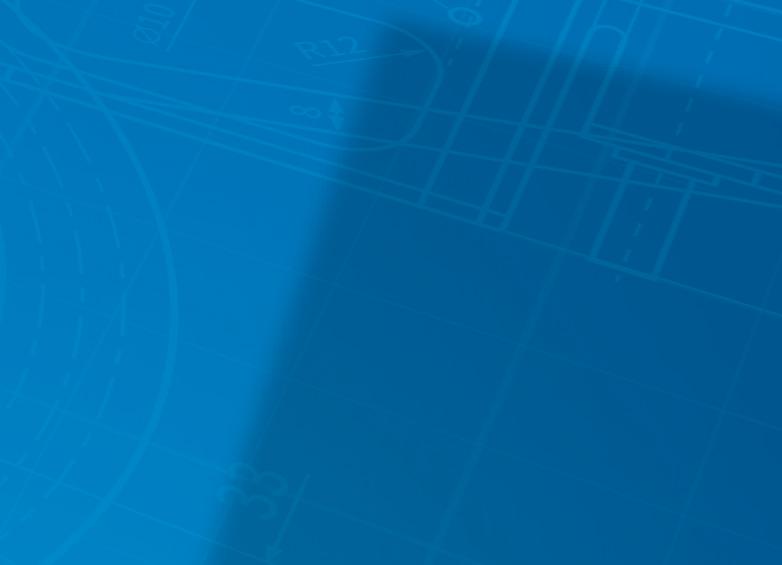
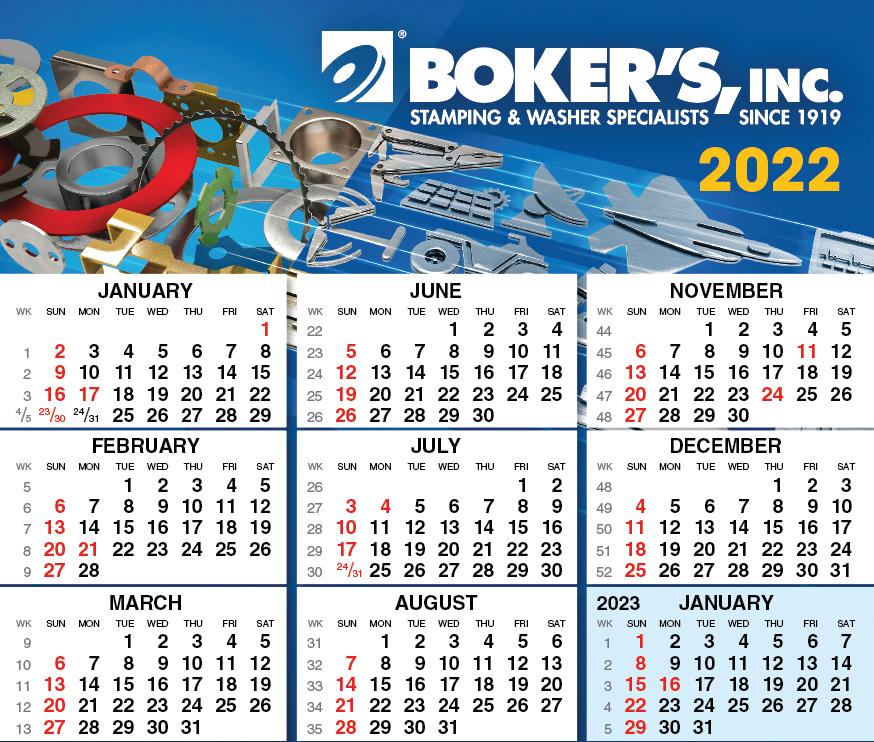
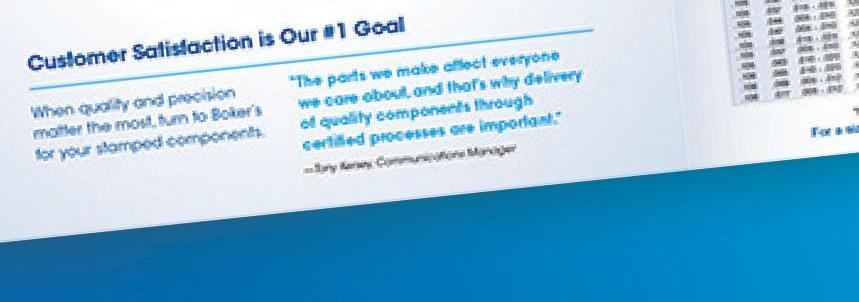
800-WASHERS
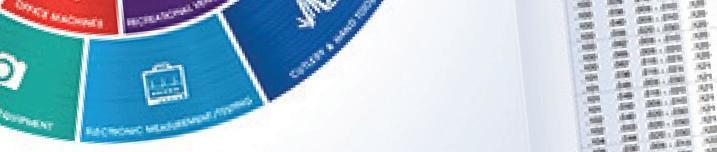
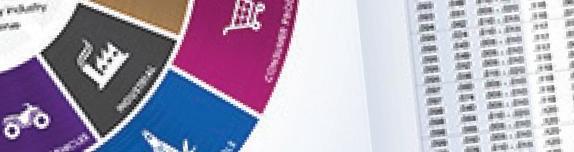


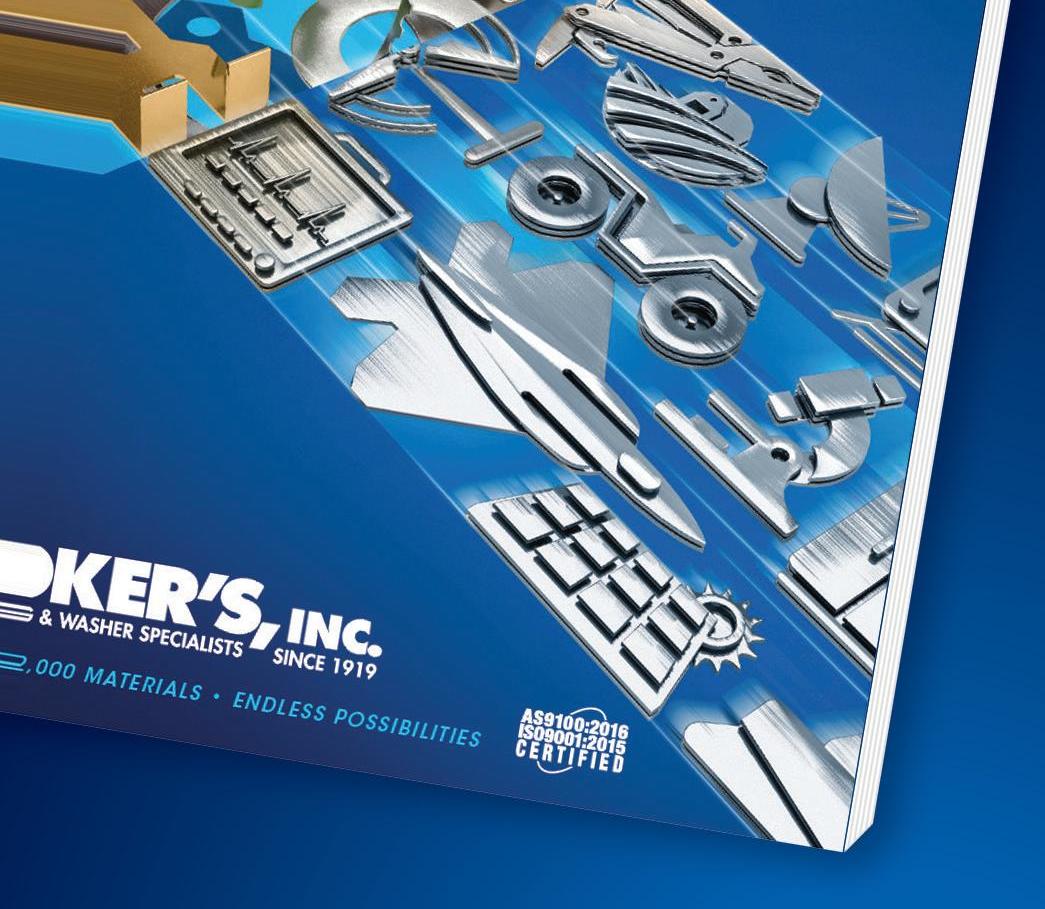
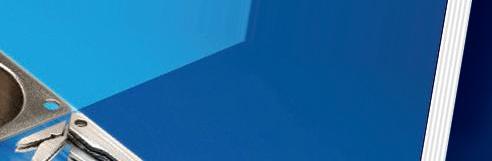

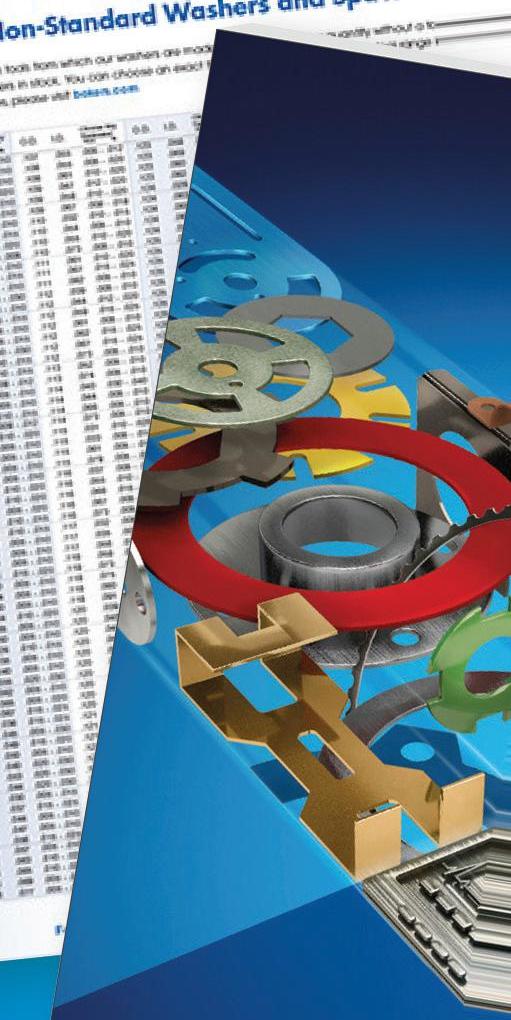