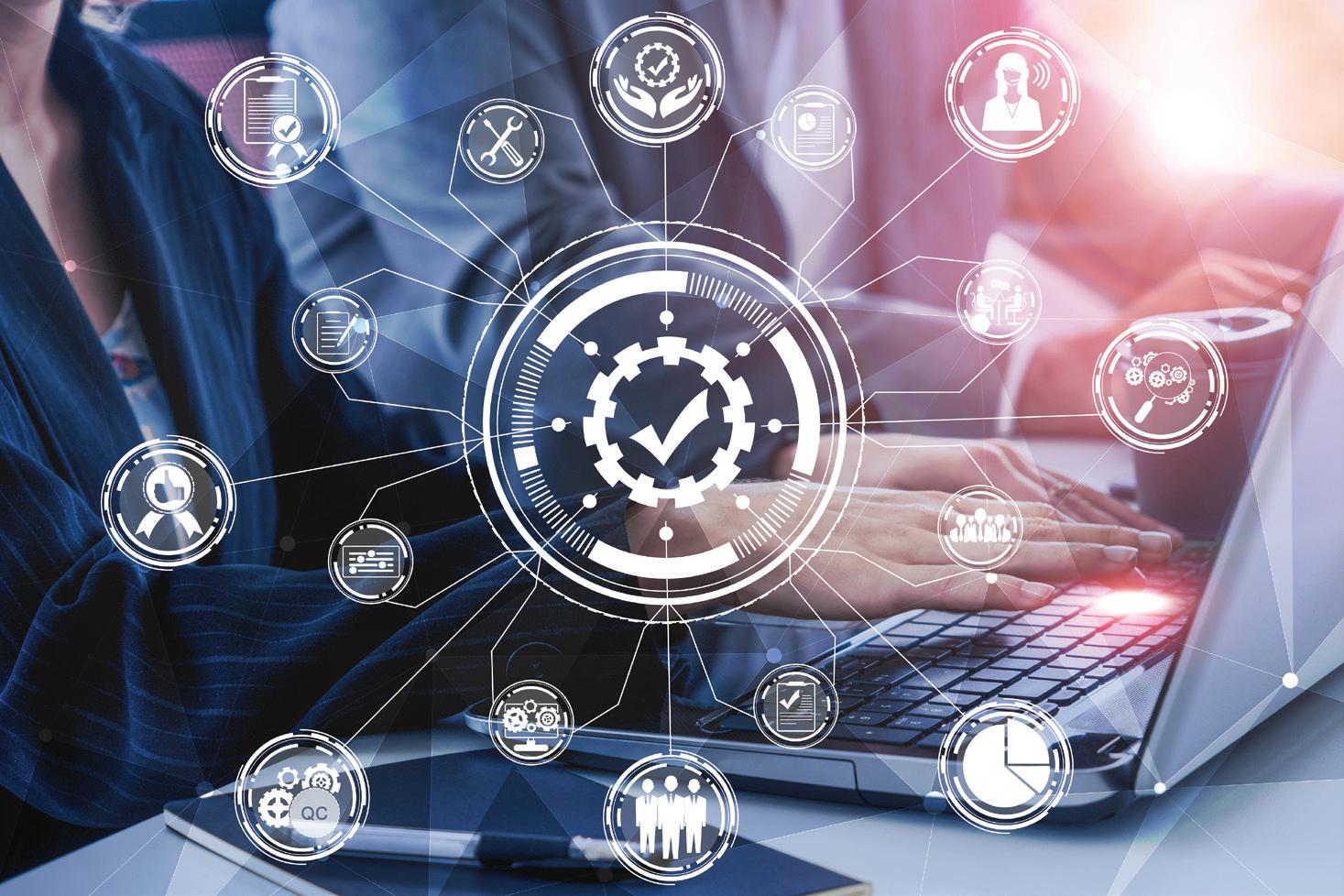
19 minute read
WELDING: Materials
Global Product Manager Ultrasonics, Branson Welding and Assembly at Emerson
What advances in welding address material variations?
Conventional ultrasonic welding technology, using single-parameter weld modes, has enabled electronics manufacturers to achieve high levels of assembly quality and reliability. This is particularly true for products built from rigid, molded plastic components.
Ultrasonic welding creates a highfrequency, heat-generating motion between the components to be bonded. It’s been used to join thermoplastics for more than 70 years and has frequently been chosen when parts were too complex or costly to be molded in one piece. Instead, they were molded in multiple parts, which allowed for more efficient and cost-effective welding.
This type of welding uses single, weld-parameter modes such as downforce, distance/collapse, depth, time, or energy to manage weld consistency and high repeatability.
However, controlling weld quality with single-parameter modes becomes more challenging when assembling plastic parts that are:
• Compressible or contain compressible elements • Inserted into substrates that vary in hardness • Installed over or contain sensitive metal or electronic components
To assemble hard-to-handle or variable parts, manufacturers have typically had to add an external measuring device to the welder, which allows for the adaptation of a critical weld parameter. This practice adds time, complexity, and cost to the process.
Manufacturers facing nextgeneration product assembly challenges — from miniaturization to increased electronic contents — require a new range of assembly innovations.
Fortunately, advanced technology is offering just that and eliminating the need for external measuring devices. This new, “dynamic mode” for ultrasonic welding
can automatically adjust to respond to part-to-part variabilities and unique materials while avoiding the need to add external measurement or sensing devices.
This technique can safely weld small, thin, or complex plastic parts onto plastic structures directly atop sensors or delicate electronics without damage. It can also weld parts atop plastic assemblies containing compressible internal elements, such as elastomeric seals or cores.
Working in dynamic mode The dynamic welding mode can monitor,
As next-generation electronic devices become smaller and lighter, ultrasonic techniques are evolving to create repeatable welds atop delicate components.
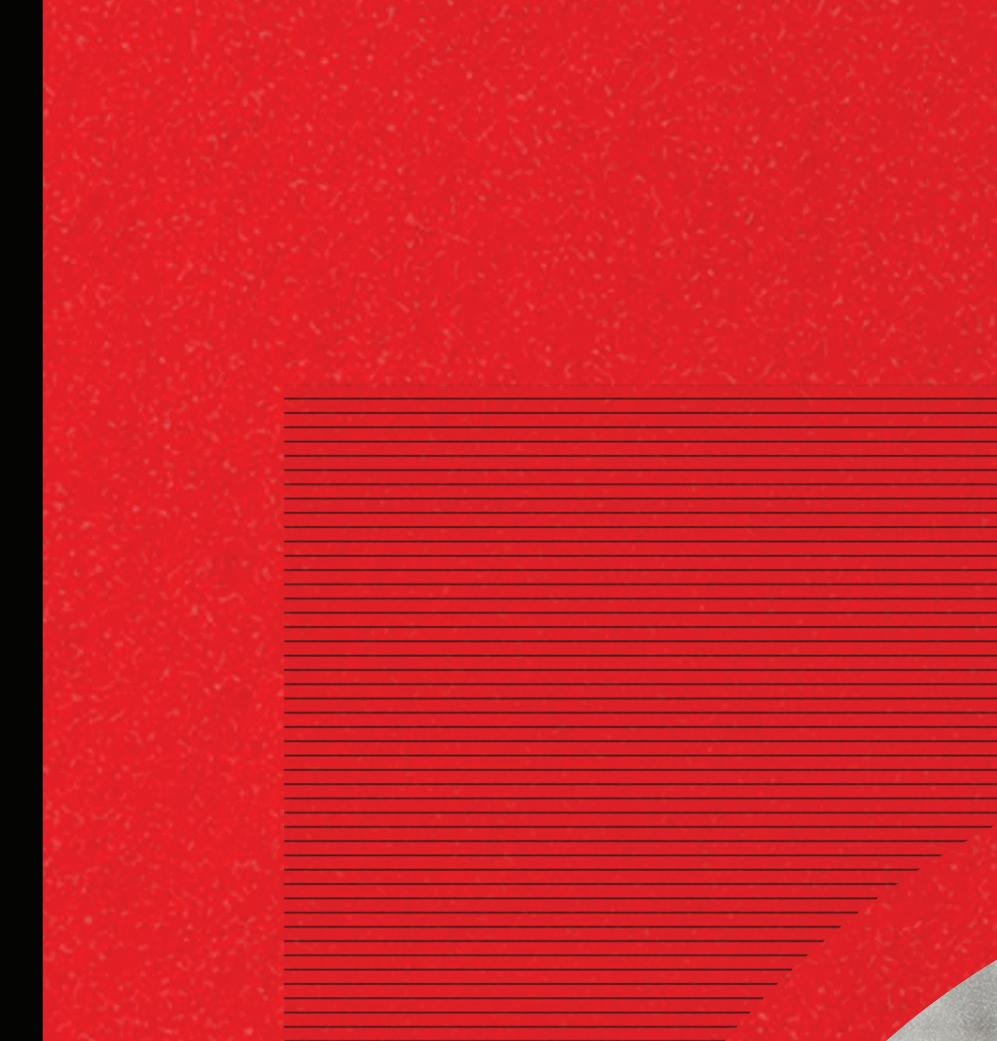
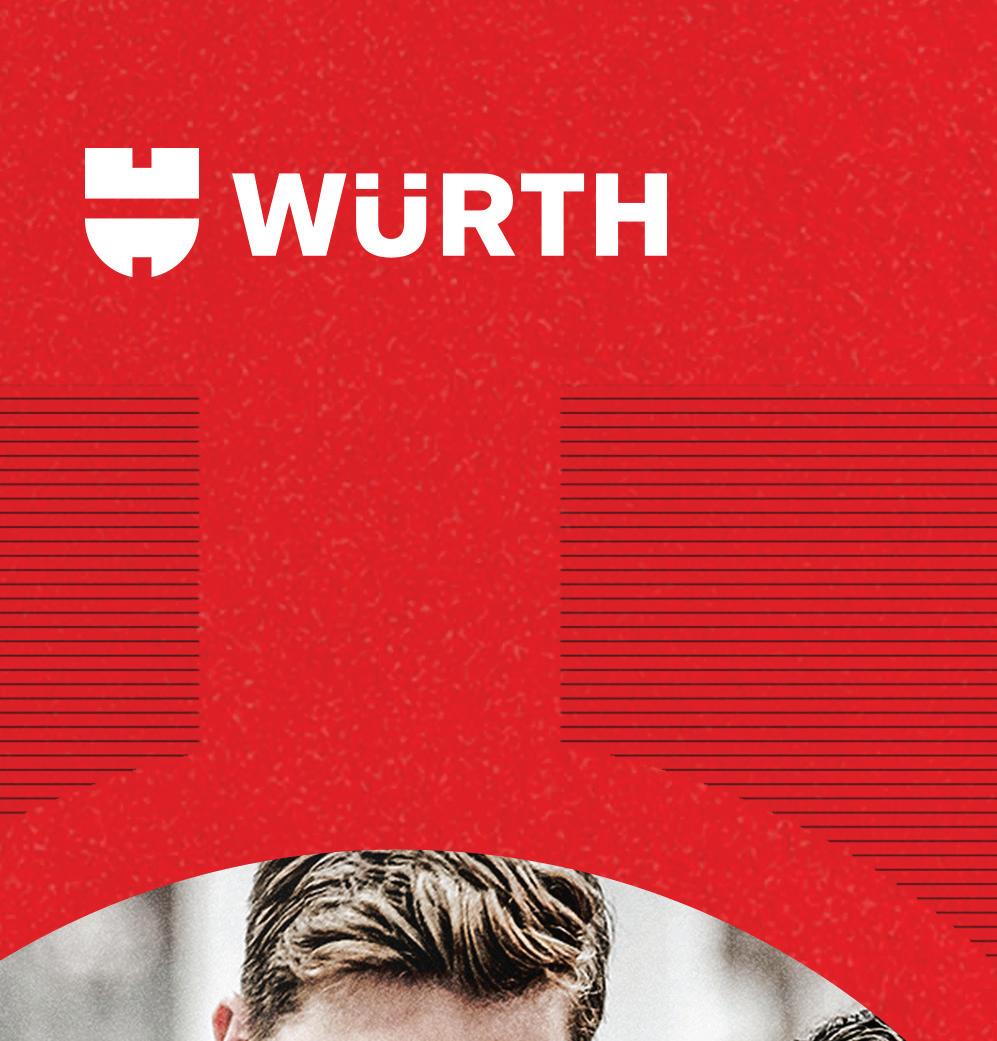
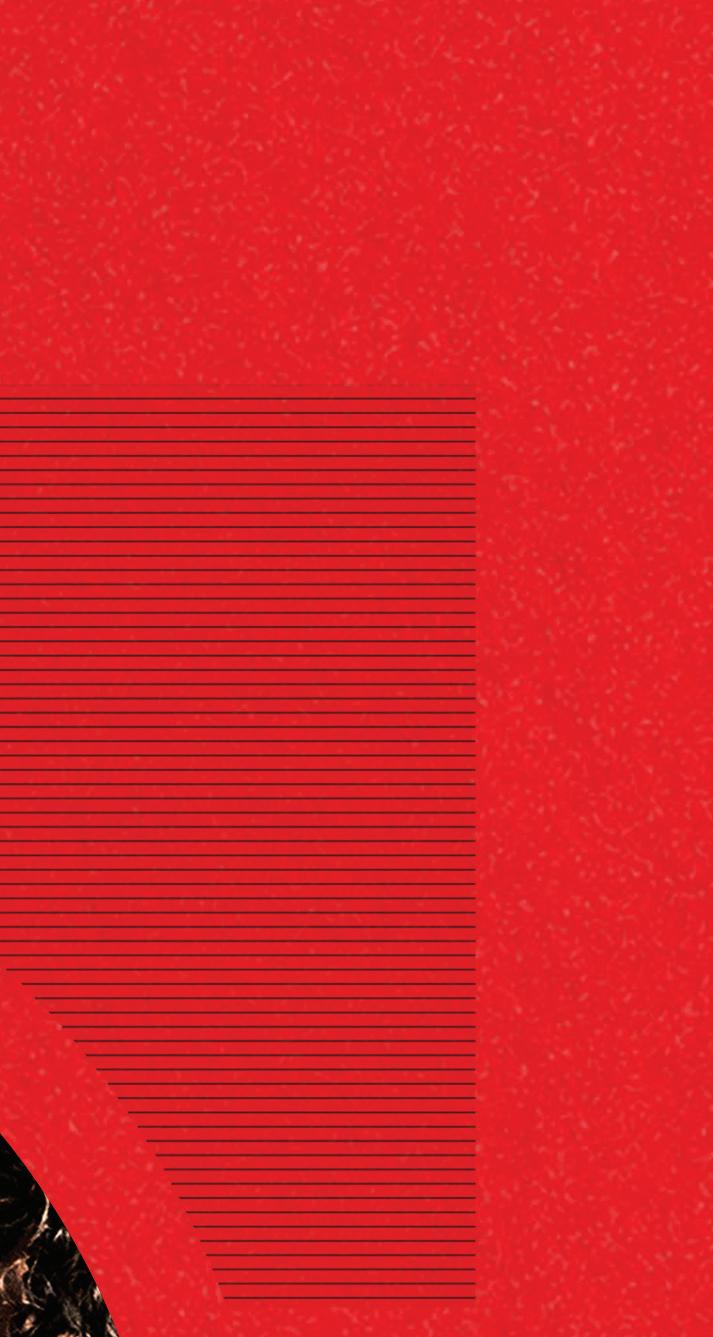
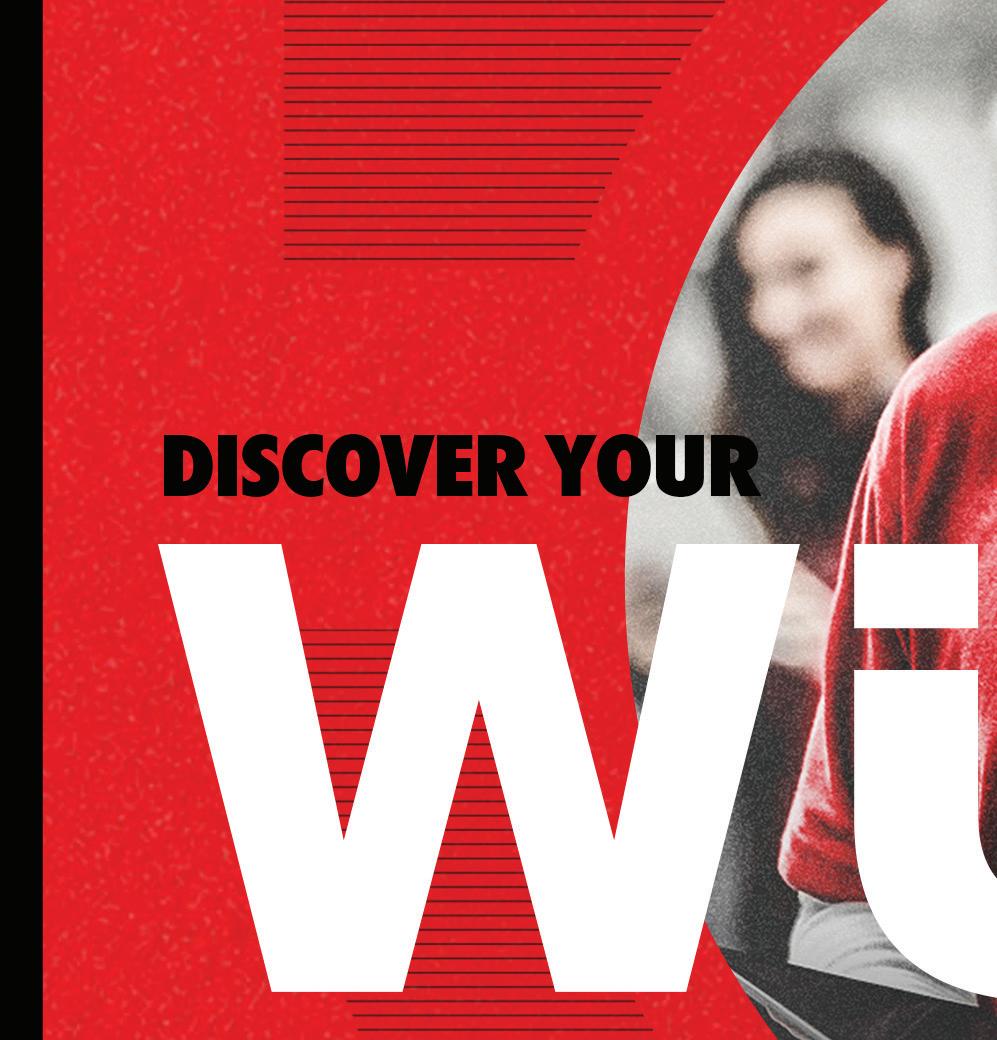

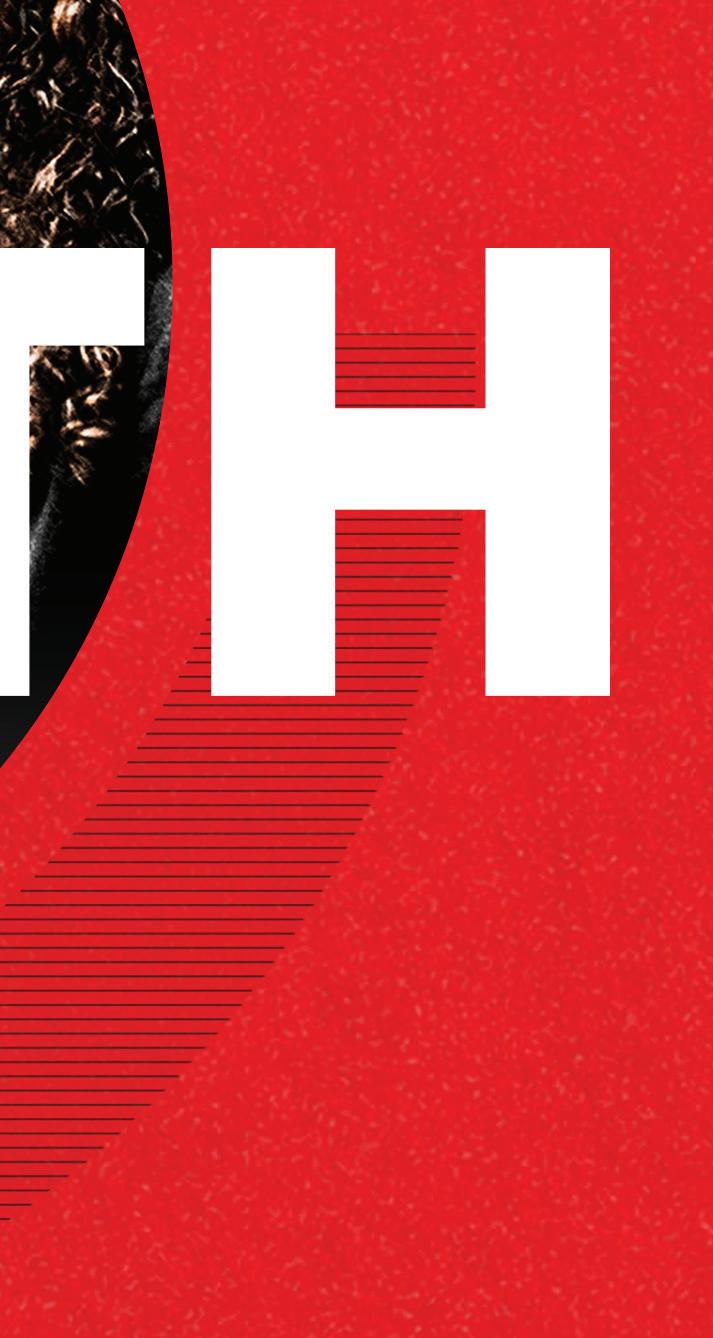
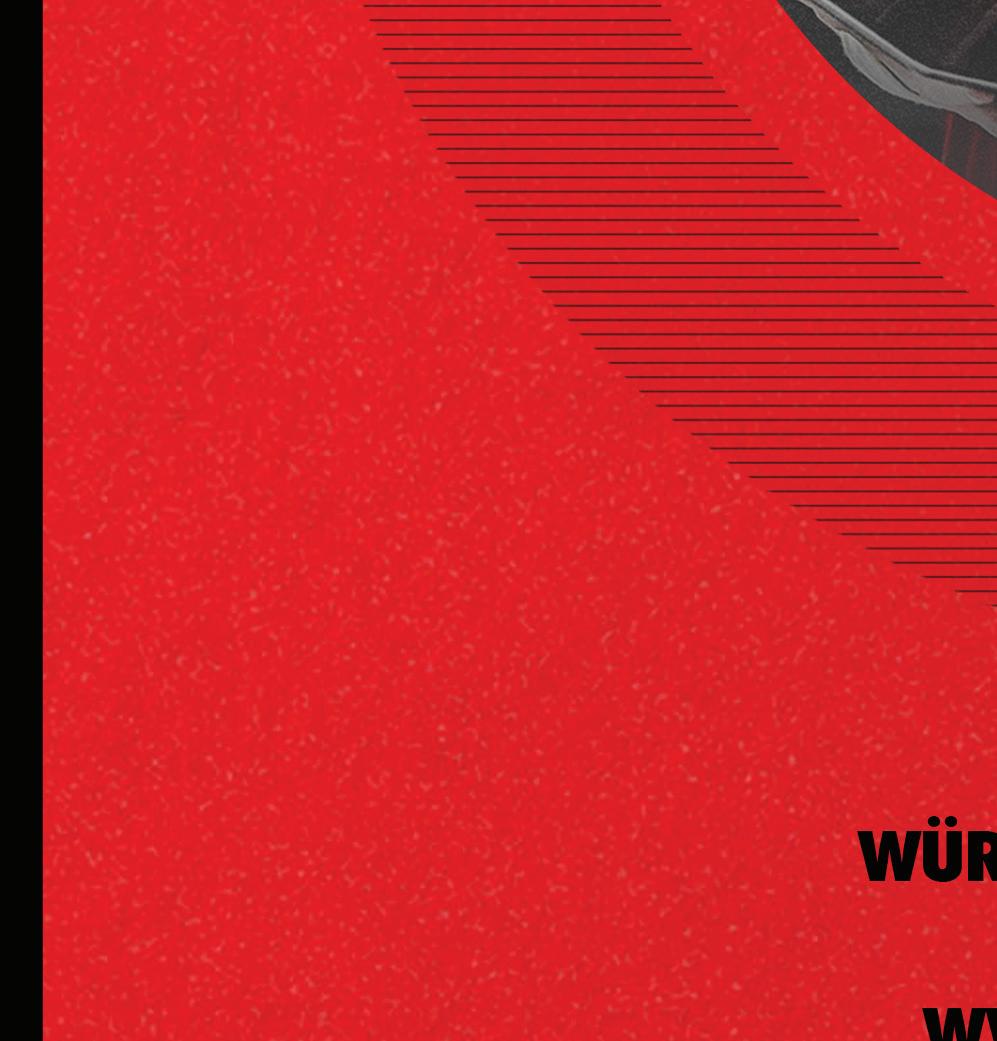
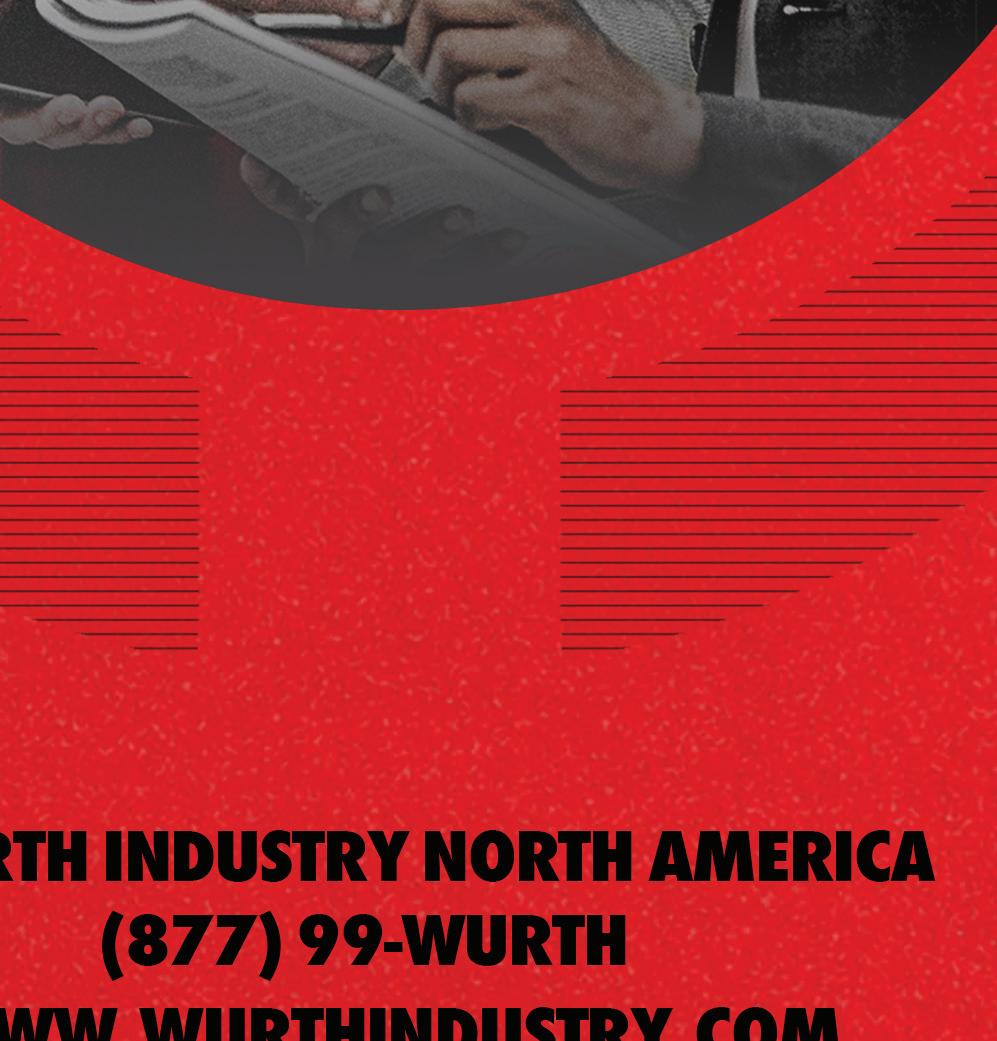
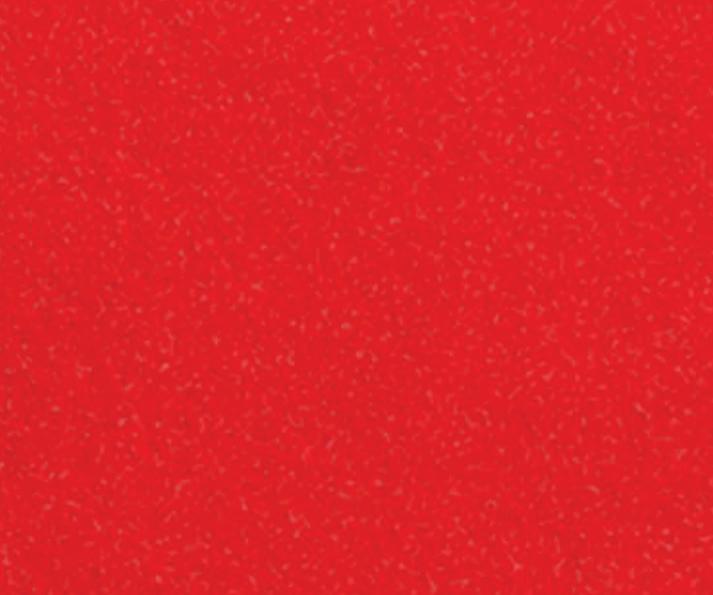
welding: materials
recalculate, and adjust multiple weld parameters in real-time to optimize weld performance within a user-specifi ed target result. This provides users greater versatility and more consistent results by welding in accordance with a design profi le instead of a single parameter.
To do so, users must fi rst select the single-parameter weld mode that o ers the ideal application results, and then enter two application-specifi c scores. These act as limits for the dynamic mode activity.
The fi rst score is a material density score that characterizes the hardness or resistance of the material that’s to receive the welded, staked, or inserted part. The second is a weld reactivity score, which impacts the reaction time to achieve the desired density setting. The dynamic mode then monitors each weld cycle and optimizes it in response to specifi c, part-to-part variabilities throughout the production run.
Here are two examples of how the dynamic mode weld cycle can overcome the limitations of single-parameter weldmode controls.

1. Sealing a watertight cover over electronics. In this example, a plastic cover must bond gap-free, watertight, and without the cover structure contacting or compressing the sensitive electronics inside the lower component. A single-parameter weld mode (the weld distance or collapse depth) could exert too much pressure on the cover and damage internal device electronics.
By using a dynamic welding mode instead, a manufacturer can optimize the distance/collapse depth mode in each cycle and enable the weld actuator to produce enough collapse depth for a watertight seal. At the same time, this mode detects and avoids a higher resistance that could compress the cover and damage the electronics below the welded cover.
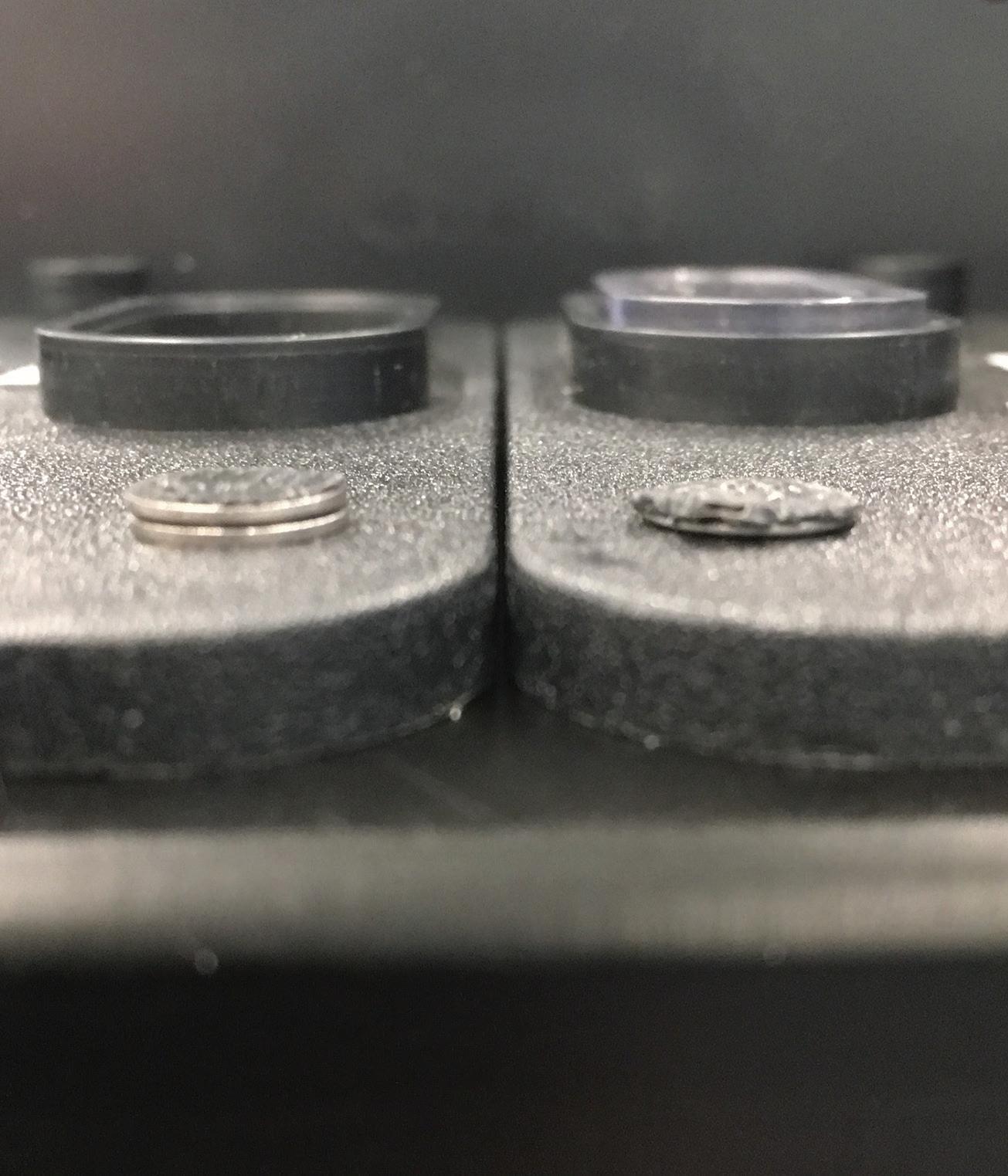
2. Welding a sealed, elastomer-core pin connector. The challenge is to assemble an elastomer-fi lled, two-way pin connector so that the connecting pins

Before view: Staking application with di erent number of metal washers (single and double). After view: Single recipe setting in dynamic mode used to weld both single and double washer staking applications.
are embedded in a compressible core of elastomeric plastic. The fi nished plugs must be air and watertight, so the weldedon lid compresses the elastomer around the inserted pins. A fl at fi t is essential for the lid, but the height of the plug’s elastomeric core may vary by up to 10%.
The use of a single-parameter weld mode (downforce, distance/collapse depth) risks producing unacceptable variances in the lid height, which would expose the length of connecting pins and could compromise the watertight sealing capability.
In the dynamic mode, however, the materials density score allows for a weld-by-weld adjustment, which compensates for the varied consistency and height of the plug’s elastomer core. This mode requires that the actuator “sense” or “feel” for the specifi ed amount of resistance (so, the contact with the harder material on the plug’s rim) before beginning the lid weld.
As advances in electronics develop, so do the assembly technologies that ensure a strong and reliable bond. Fortunately, plastic welding now o ers more than one way to meet new demands.
These before-and-after views show the fl exibility of dynamic mode in staking a pair of metal washers onto posts. By using the Branson GSX-E1, Elite Precision+’s “dynamic mode,” a consistent weld result was obtained (see image on the right), and even though the application set-up was di erent and based on the number of metal washers being staked. This is not possible using an alternative weld mode. The dynamic mode stored the material density and reactivity information, enabling it to detect the completion of the stake and dynamically shut the weld down early.
2021 A D V E R T I S E M E N T
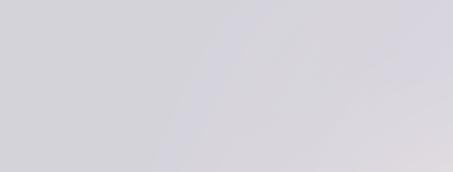
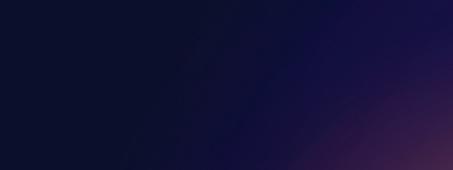

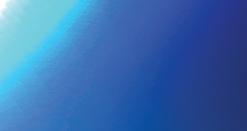
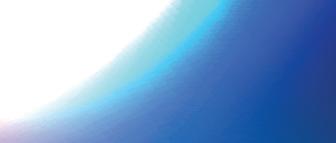
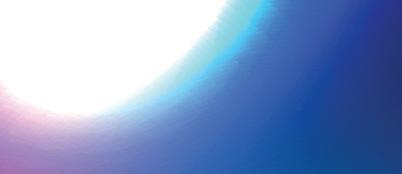
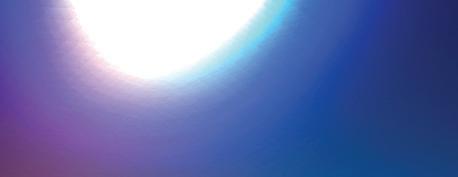

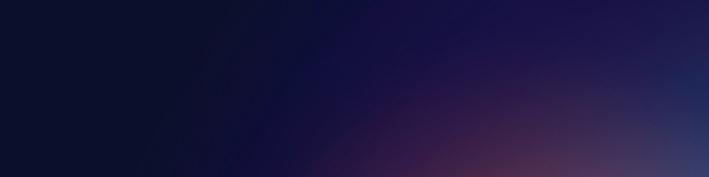
Vendors in the fastener industry
NBK America

NBK’s historic past since 1560 has
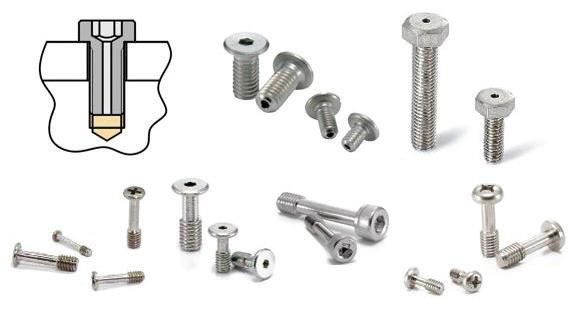
allowed it to provide new value to customers by constantly renewing itself. The NBK brand stands for strong design, precise manufacturing and sales of products based upon the needs of its customers. NBK provides high-precision, high-performance specialty screws and machinery components such as the following: Low Profile, Small Head, Vacuum Ventilation, Seizing / Galling Resistant, Specialty Metal (Inconel, Hastelloy, etc.), Miniature, Captive, Clamping, Tamper Resistant, Plastic, Loosening Resistant, Ball Roller (Transfer), Roller Chain Bolts, Spring Plungers, Knobs, and more. Furthermore, NBK has Flexible Shaft Couplings, Wireless Positioning Units, Clampers, and additional products. We can customize these products flexibly should the need arise. NBK products are used in advanced industries, such as manufacturing equipment for automation, robotics, semiconductors, and medical devices.
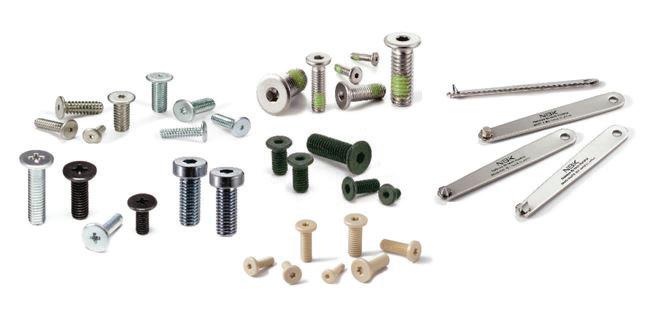
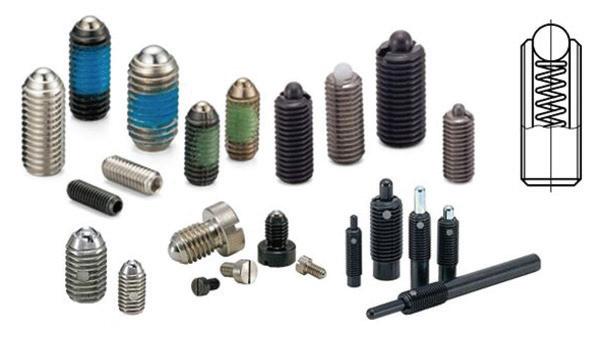
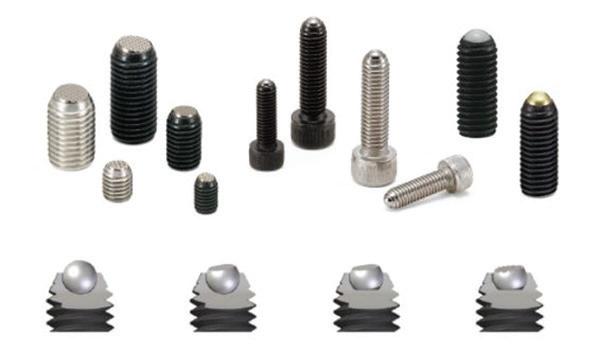

NBK America LLC
307 East Church Road, Suite 7 King of Prussia, PA 19406 Web: www.nbk1560.com Phone: 484-685-7500 Fax: 484-685-7600 Email: info.us@nbk1560.com
2021 A D V E R T I S E M E N T
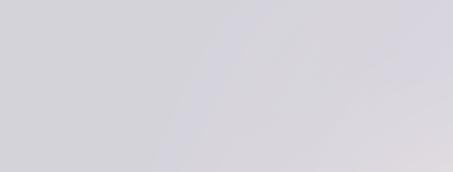
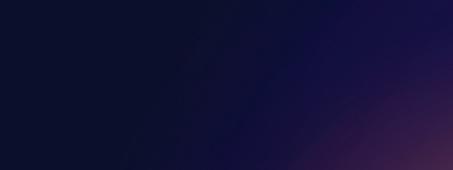

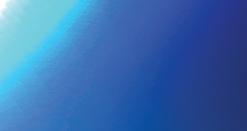
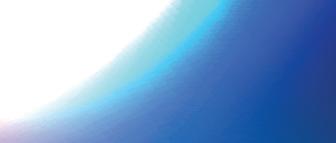
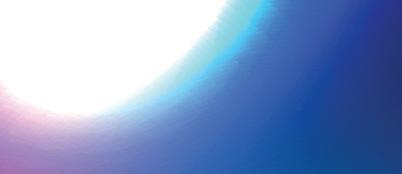
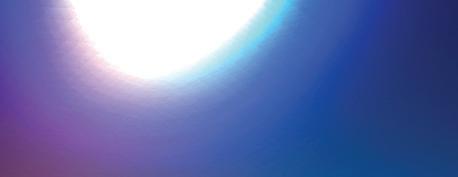

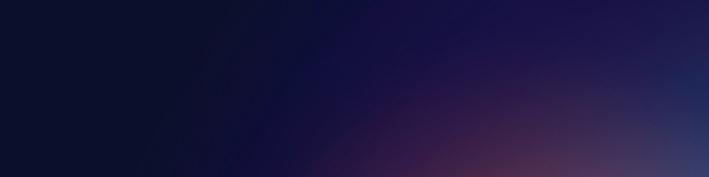
Pivot Point
Vendors in the fastener industry

Pivot Point is a designer and manufacturer of Non-Threaded Fasteners - i.e. clevis pins, cotter pins, quick-release pins/devices, wire rope cable assemblies, and more. A family-owned company, the Leitzke family’s manufacturing heritage dates back to the 1920’s, and continues today in Pivot Point’s line of classic, and unique, fastening solutions. Wide stock selection and endless customization options allow us to solve application challenges on tight timelines, fixed budgets, and with creative solutions. Pivot Point is known for our inventive, original, fastening solutions like our SLIC Pin™ (a quick-locking pin featuring a selfcontained cotter), Bow-Tie Locking Cotter, Rue Ring Locking Cotter, U-Lock Nylon Tether and others. Our state-of-the-art Wisconsin manufacturing facility features in-house pin design as well as automation capabilities, making Pivot Point a powerhouse in fastening solutions – at prices that can compete with imports. Pivot Point is proud to offer digital, and in-person, product training sessions. These are live, interactive sessions that cover “NonThreaded Fastener Basics.” The training is tailored to industries, teams and individuals, and schedules. Full of application examples, product comparisons, and best practices, the 1 hour (or less) session is intended to round out the knowledge of any design professional. Reach out today and let us know how we can help!
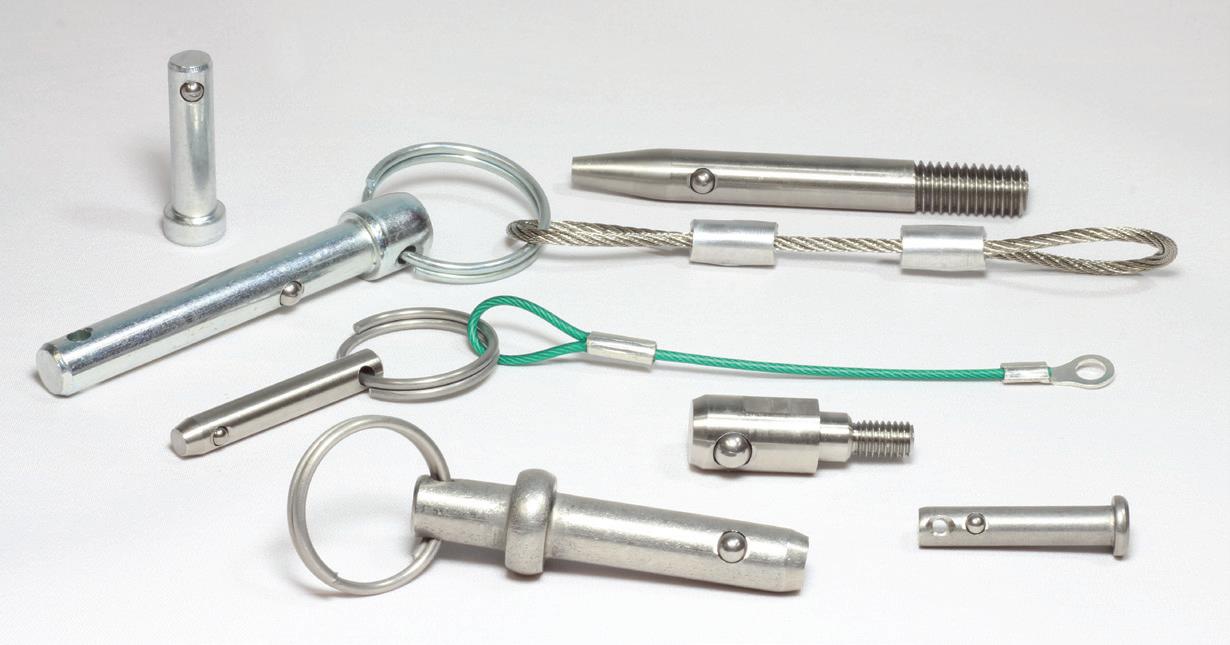
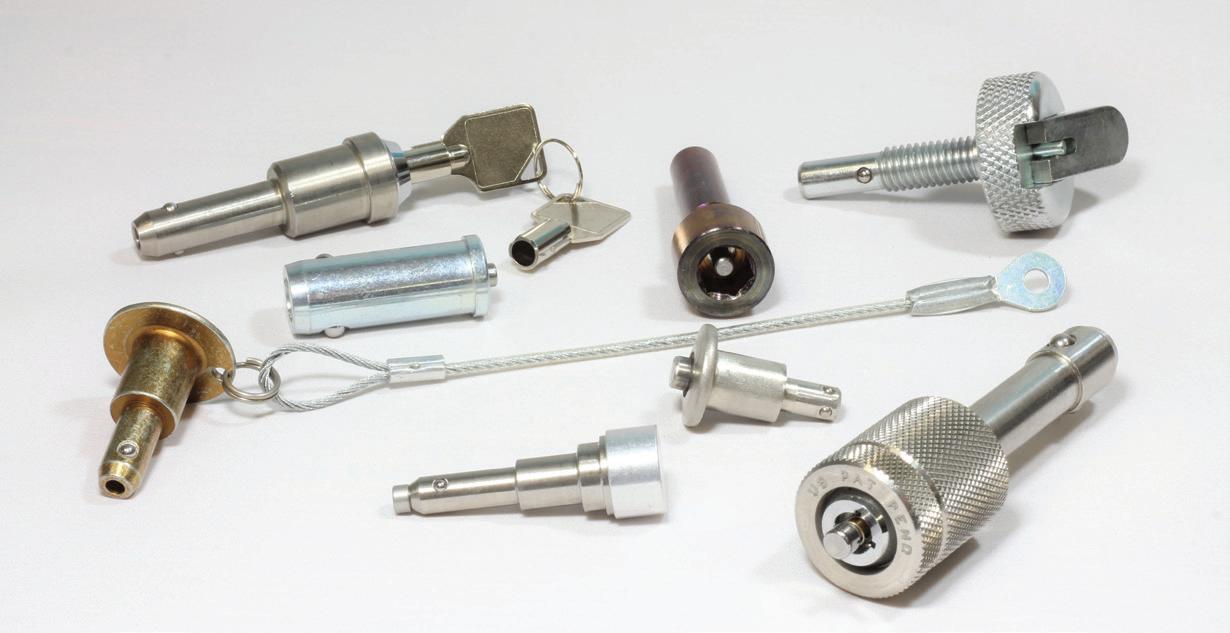

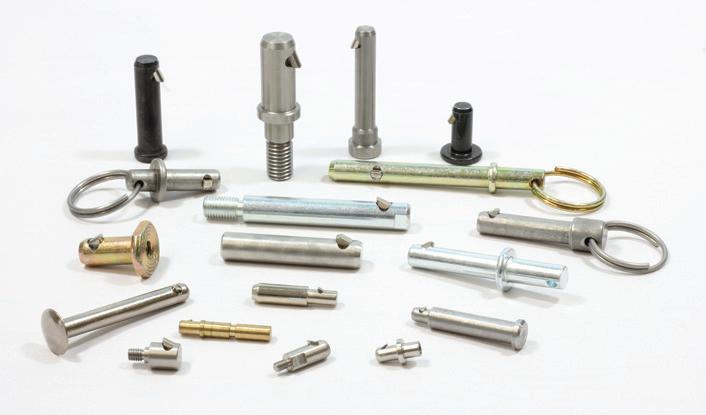
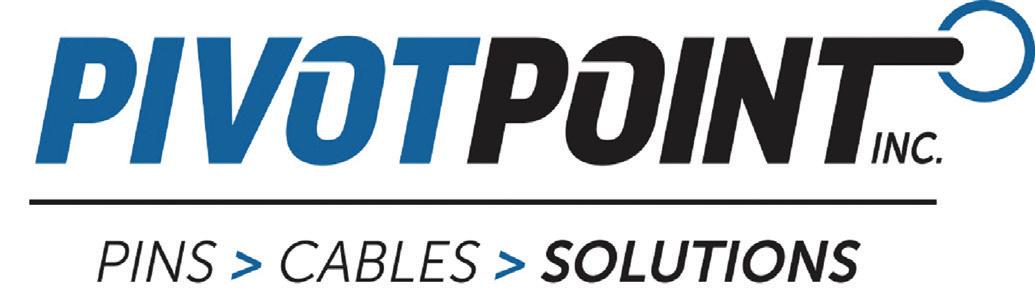
Pivot Point, Inc.
PO Box 488 761 Industrial Lane Hustisford, WI 53034 Phone: (800) 222-2231 Fax: (920) 349-3253 Email: mail@pivotpins.com
2021 A D V E R T I S E M E N T
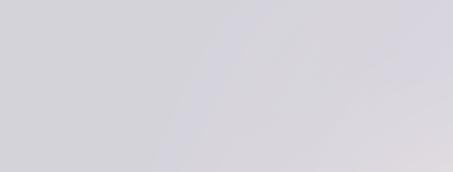
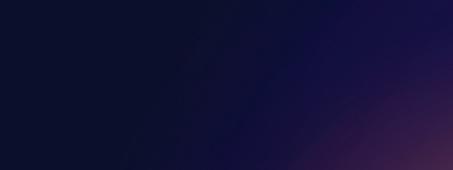

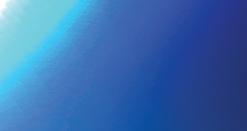
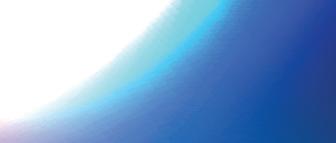
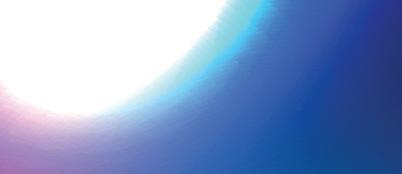
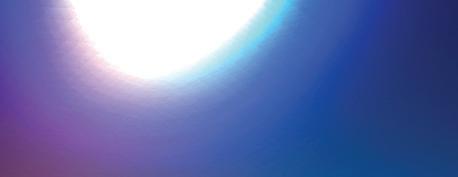

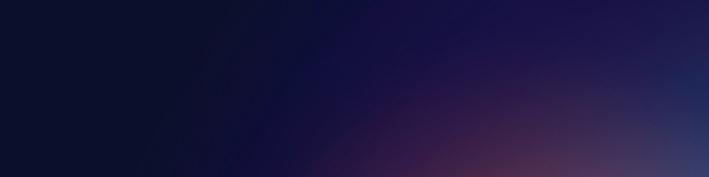
Smalley
Vendors in the fastener industry

Founded over 100 years ago, Smalley has evolved to become the world leader in the manufacturing and development of Retaining Rings, Spirolox® Retaining Rings, Constant Section Rings, and Wave Springs. Smalley has led the way in introducing state-of-theart products and continues to lead the way in innovations for the future.
Smalley stocks over 10,000 standard parts across 30 configurations and 400 sizes. If a standard part doesn’t meet your requirements, you’ll work with our team of over 30 industry-specialized engineers to quickly create an economical custom part in the material of your choice, all without new tooling. Prototype or production volume, our No-Tooling-Charges™ manufacturing process meets the design flexibility your application, budget, and timeline requires.
While all of our manufacturing is made in our U.S.-based 300,000 ft2 facility, our global network of offices, engineers, and distribution partners allows you to receive parts and support from anywhere in the world quickly. Smalley’s dedication to quality and manufacturing excellence has earned us multiple service and quality awards and the trust of OEMs worldwide.
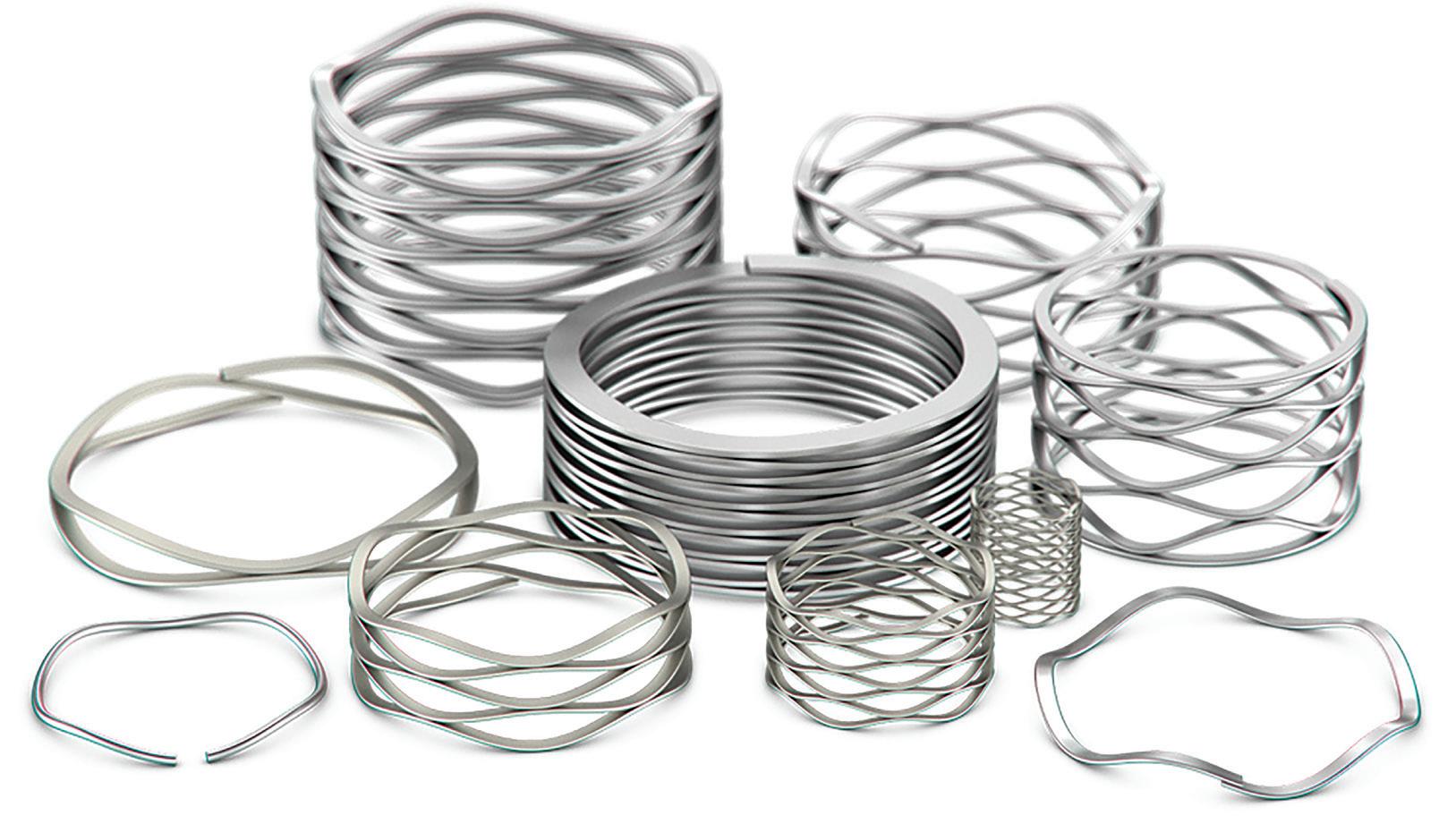

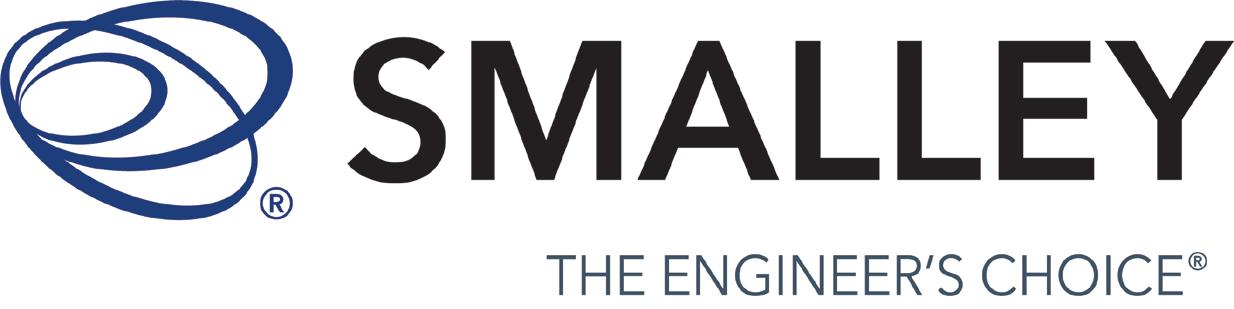
Smalley
555 Oakwood Road Lake Zurich, IL 60047
Phone: +1 847 719 5900 Email: info@smalley.com smalley.com
Selecting the Optimal Washer
Flat: Generally used for load disbursement
Tab/Lock: Designed to effectively lock an assembly into place
Finishing: Often found on consumer products
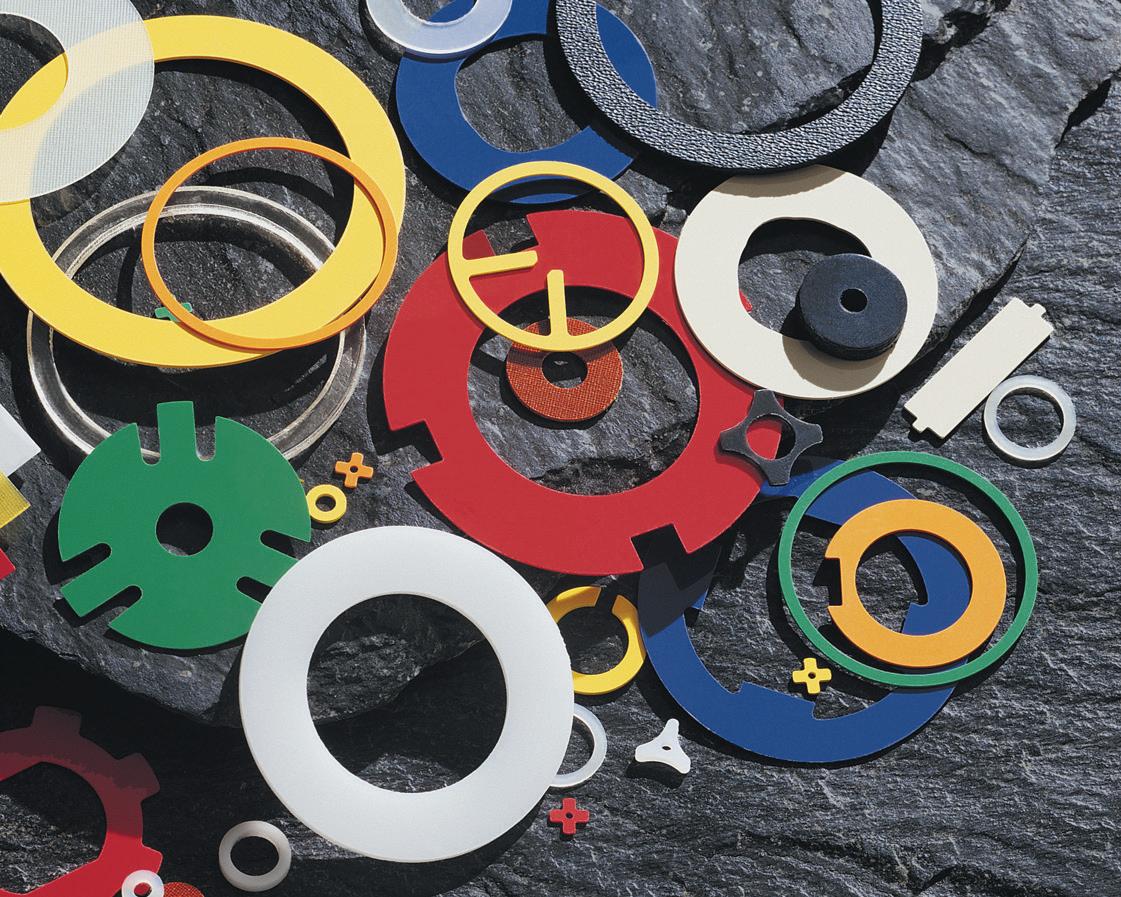
Wave: For obtaining loads when the load is static or the working range is small
Belleville: Delivers the highest load capacity of all the spring washers
Fender: Distributes a load evenly across a large surface area
Shim Stacks: Ideal for simple AND complex applications Boker’s Inc. 3104 Snelling Avenue Minneapolis, MN 55406-1937 Phone: 612-729-9365 TOLL-FREE: 800-927-4377
(in the US & Canada)
bokers.com
Structural Adhesives For Specialty Trucks and Trailers

Many truck and trailer manufacturers are making the switch to adhesives instead of traditional welding and fastening. Lowering fuel cost, wind drag, and weight has become an important component in manufacturing specialty vehicles. Several trial applications have been performed, and results have shown that the bonds of structural adhesives are stronger and more reliable. Ellsworth Adhesives offers a variety of acrylic, epoxy, and urethane structural adhesives.
Structural adhesives can be used to configure work truck equipment, trailer assembly, and aftermarket upfitting. Applications can range from panel bonding for trailers, installation of toolboxes in construction trucks, shelf hanging for delivery vehicles, plumbing equipment for firetrucks, to electrical components in utility vehicles. Ellsworth Adhesives (877) 454-9224
Ellsworth.com
J.W. Winco, Inc.
Spring Loaded Devices from JW Winco
When you need to align, hold, or latch di erent parts of equipment together, you need a spring loaded device.These locking systems are designed to facilitate repetitive positioning operations on machines and equipment or parts undergoing machining. Spring loaded devices create a secure connection with limited play. JW Winco has many di erent versions and types for your application requirement.
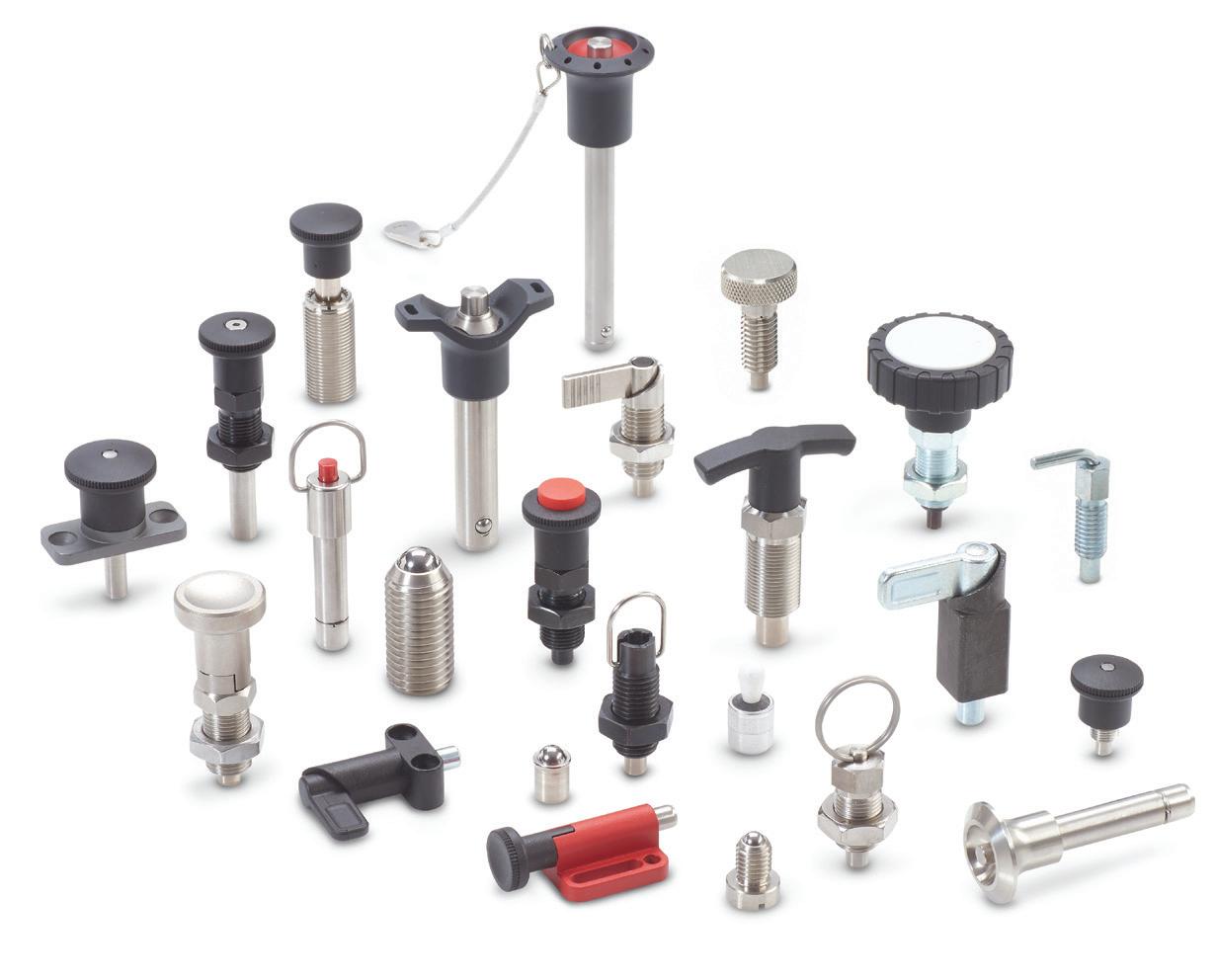
Check out www.jwwinco.com to fi nd out more!
Keystone Electronics Corp.
A World Class Manufacturer of precision electronic components & hardware for over 70 years. Keystone’s design and engineering experts are fully integrated with their inhouse precision tool & die division supported by advanced manufacturing systems to produce close tolerance Stamping, Machining, Assembly, CNC and Injection Molded parts. Keystone utilizes state-of-the-art software to support the thousands of standard products found in their Product Design Guide M70 and Keystone’s Dynamic Catalog on-line.
Product Overview: Battery Clips, Contacts & Holders; Fuse Clips & Holders; Terminals & Test Points; Spacers & Stando s; Panel Hardware; Pins, Plugs, Jacks & Sockets; Multi-Purpose Hardware. As an ISO9001:2015 certifi ed manufacturer, Keystone’s quality control system, responsive customer service and custom manufacturing division can meet your challenges with a standard or custom design solution.
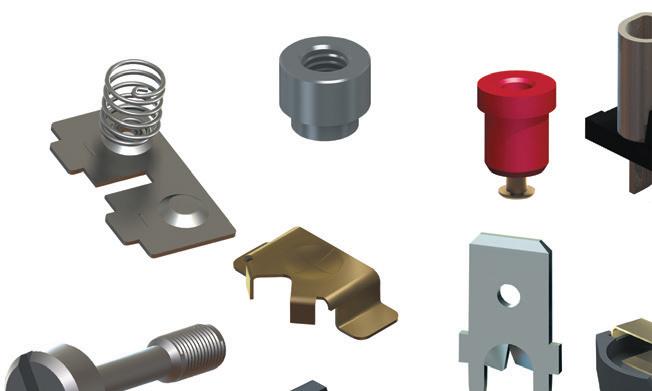
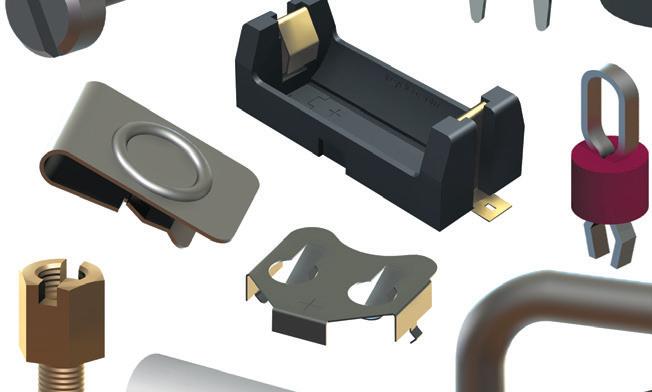

DESIGNERS & MANUFACTURERS Keystone Electronics 55 S. Denton Ave. New Hyde Park, NY 11040
www.keyelco.com
Tel: 1.800.221.5510 www.keyelco.com
Custom Plastic Machined & Molded Fastener Components
ADAPTERS • BACKUP WASHERS • BOLTS •
COUPLINGS • CONNECTORS • HEX BOLTS •
INSULATORS • NUTS • SEALS • SET SCREWS •
SHOULDER BUSHINGS • PAN HEAD SCREWS •
PINS • SLEEVES • SLOTTED SET SCREWS •
SPACERS • WASHERS

Materials Utilized: ABS, Acetal, Acrylic, Delrin®, HDPE, KEL-F, Phenolics (G10, G11, XXX, CE, LE), PEEK, PTFE, Polycarbonate, Polypropylene, PVC, PVDF, Torlon®, UHMW and Ultem®
Please visit us at www.nextlevelmanufacturing.com
Manufacturing Solutions Since 2001
Next Level Manufacturing 401 E. Edgewater Street Portage, WI 53901
sales@nextlevelmanufacturing.com (608) 975-7424
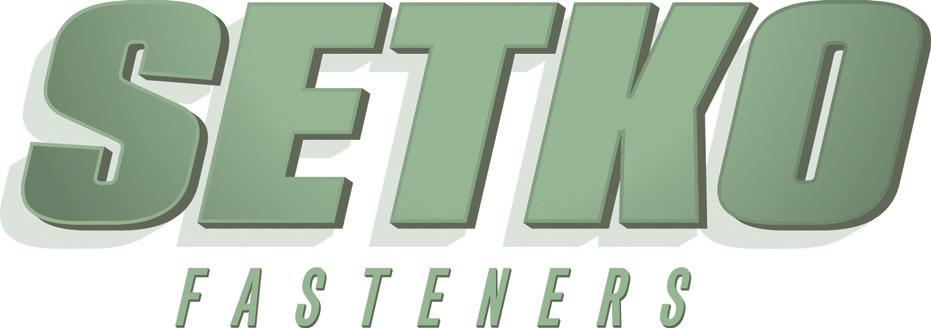
SET SCREWS • HEX KEYS • SHOULDER BOLTS • NYLON TIP
• SOCKET CAP SCREWS • STAINLESS • METRIC / INCH •
ZINC PLATED SOCKETS • SHORT ARM HEX KEYS • 6-LOBE
SOCKETS • BUTTON HEAD CAP SCREW • DOWEL PINS •
IMPORT / USA • BRASS TIP • STANDARDS / SEMI-STANDARDS
• SQUARE HEAD SET SCREWS • HEX JAM SCREWS • LONG ARM HEX KEYS • NYLON PATCH • LOW HEADS 6-LOBE
(TORX) KEYS • BUTTON FLANGE CAP SCREWS
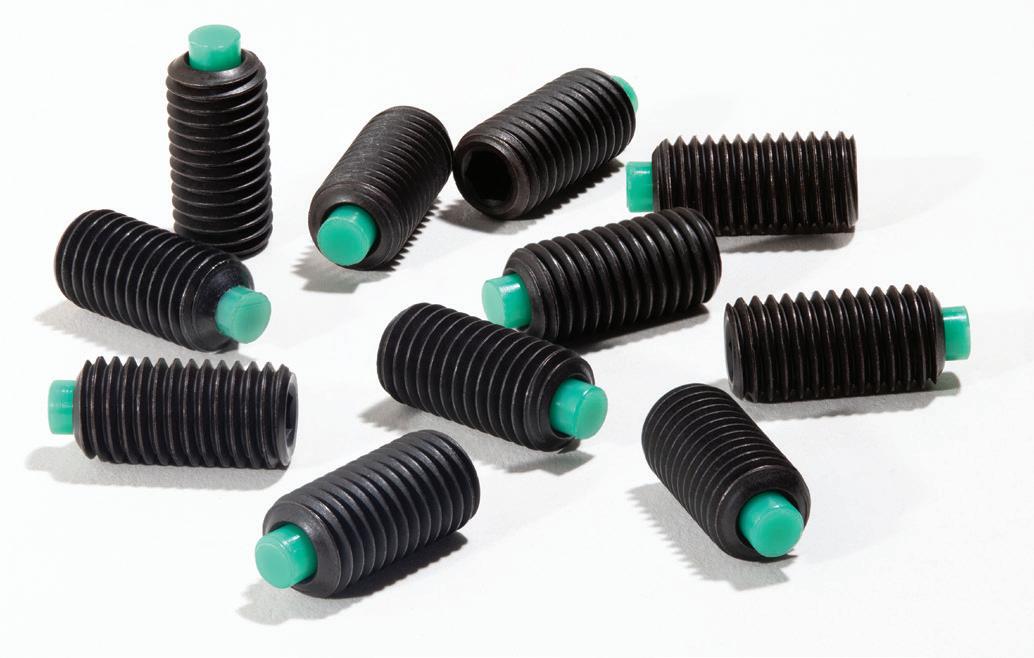
Please visit us at www.SetkoFasteners.com Setko Fasteners & Distribution 300 N. Klick St. Unit A • Hampshire, IL 60140
AD INDEX
Able Electropolishing .......................... IBC Boker’s Inc. ................................................49 Ellsworth Adhesives ..............................48 J.W. Winco, Inc. ......................................... 17 Keystone Electronics Corp ....................7 NBK America LLC ...................................IFC Next Level Manufacturing ...................34 Pivot Point Inc..........................................35 Setko Fasteners ...................................... 31 Smalley Steel Ring ................................ BC Würth Industry North America ..........55
NBK America LLC ...................................58 Pivot Point Inc. .......................................59 Smalley Steel Ring .................................60
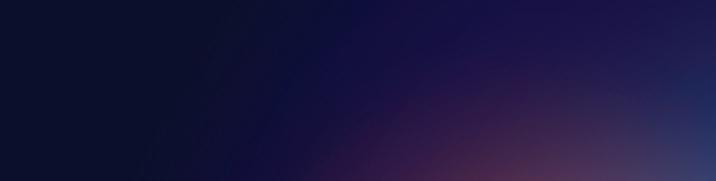
SALES LEADERSHIP TEAM
Ryan Ashdown rashdown@wtwhmedia.com 216.316.6691
Jami Brownlee jbrownlee@wtwhmedia.com 224.760.1055
Mary Ann Cooke mcooke@wtwhmedia.com 781.710.4659
Jim Dempsey jdempsey@wtwhmedia.com 216.387.1916
Mike Francesconi mfrancesconi@wtwhmedia.com 630.488.9029
Jim Powers jpowers@wtwhmedia.com 312.925.7793 @jpowers_media
Courtney Nagle cseel@wtwhmedia.com 440.523.1685 @wtwh_CSeel Publisher Mike Emich memich@wtwhmedia.com 508.446.1823 @wtwh_memich
Managing Director Scott McCafferty smccafferty@wtwhmedia.com 310.279.3844 @SMMcCafferty
EVP Marshall Matheson mmatheson@wtwhmedia.com 805.895.3609 @mmatheson
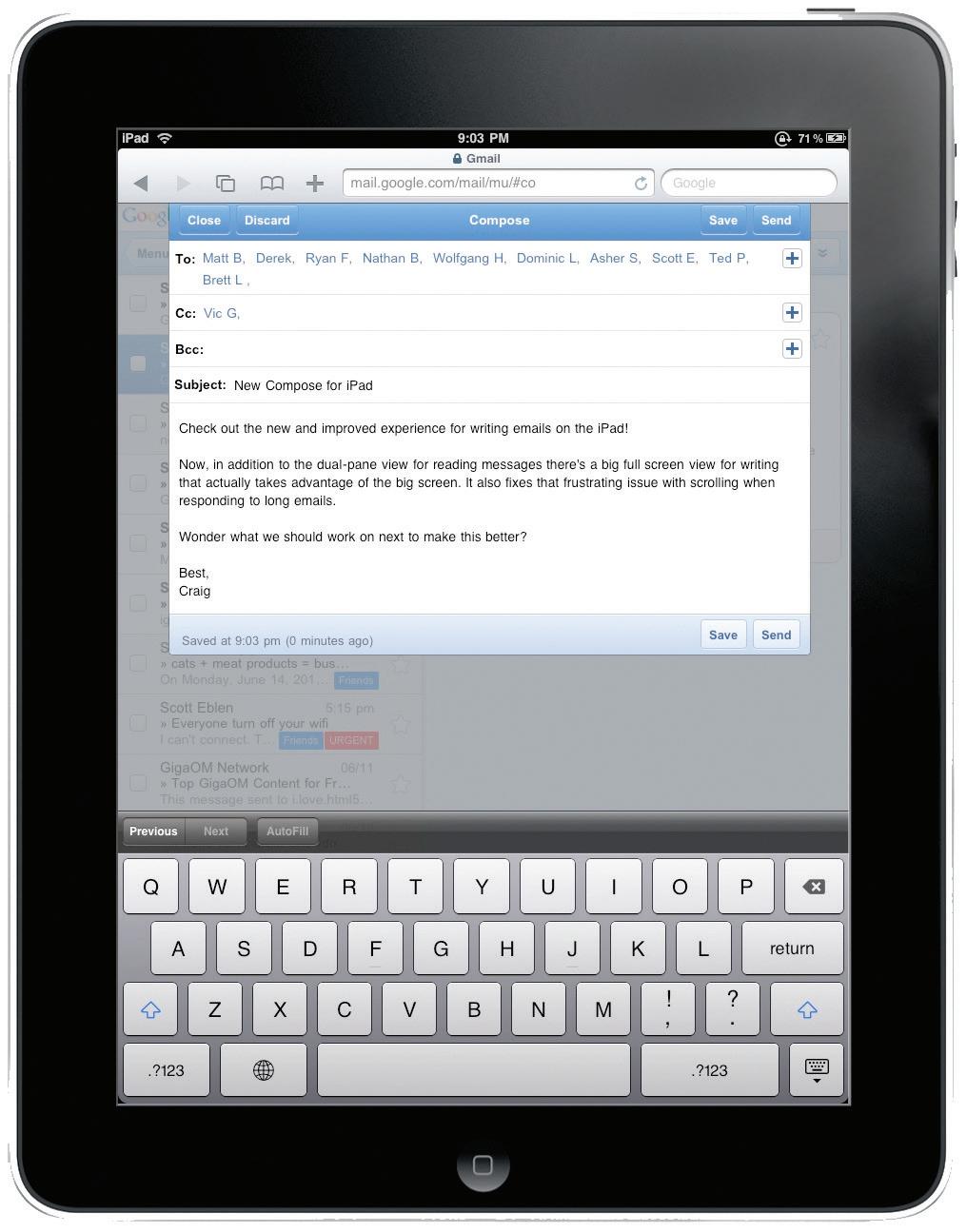
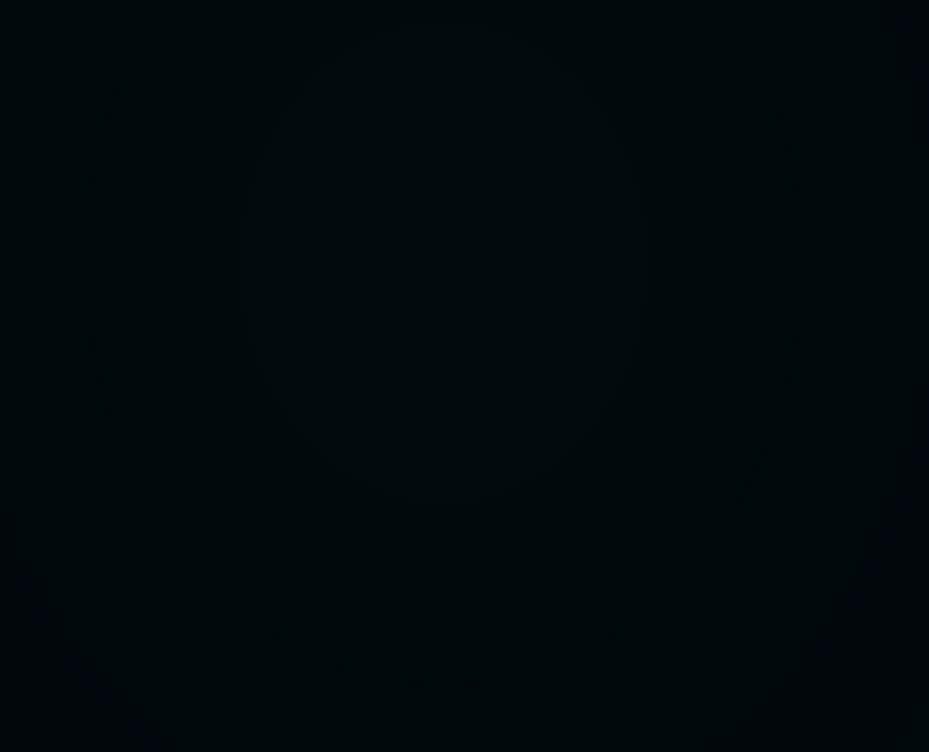
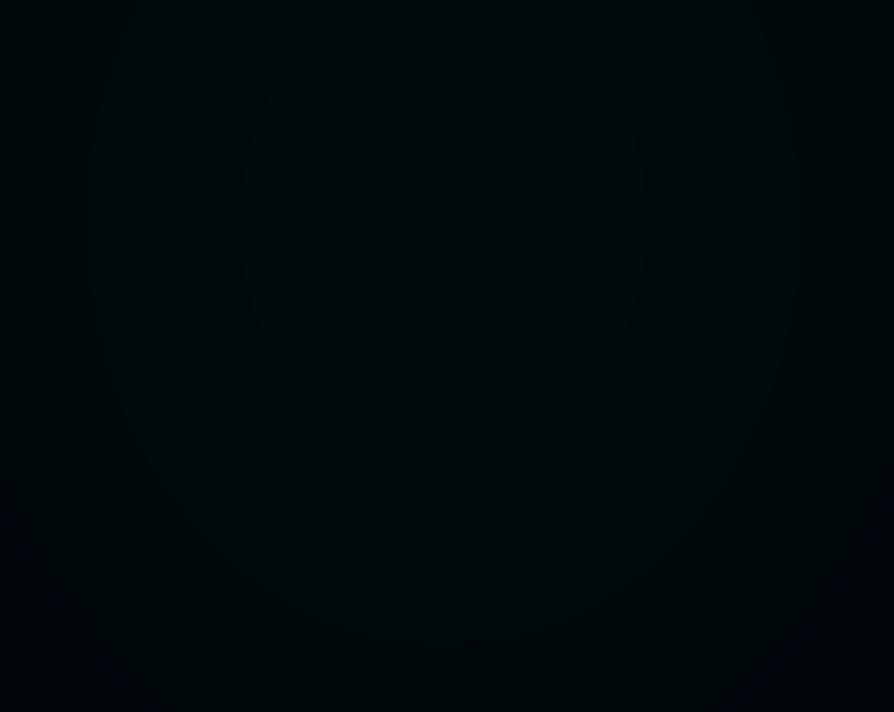
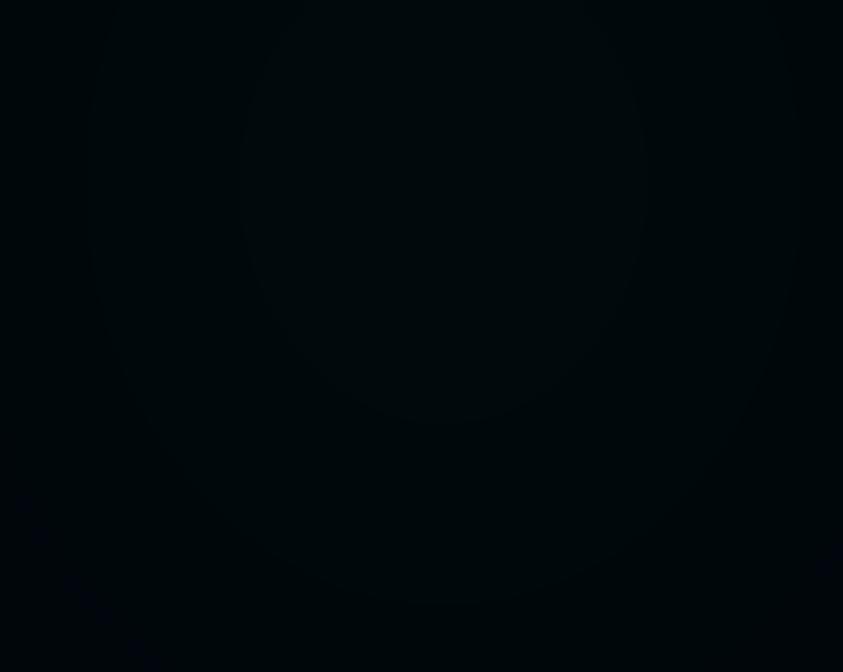
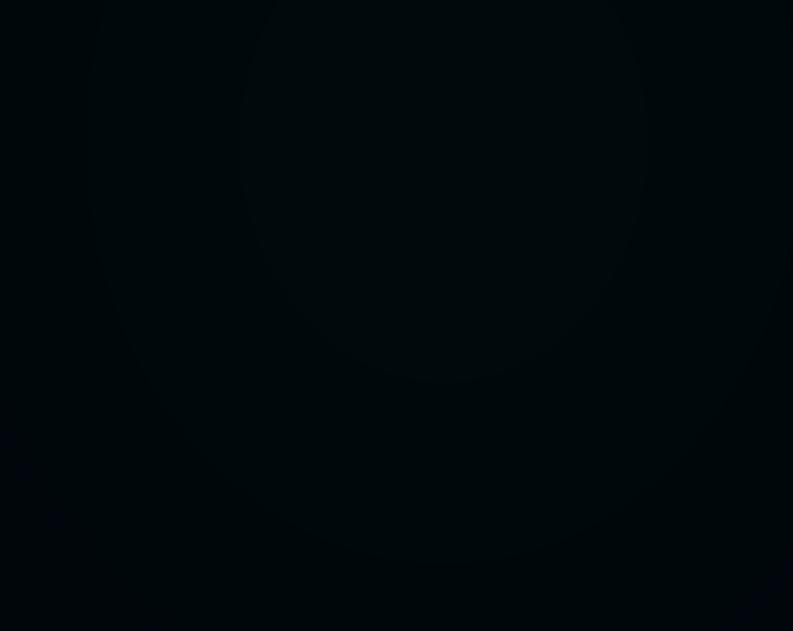
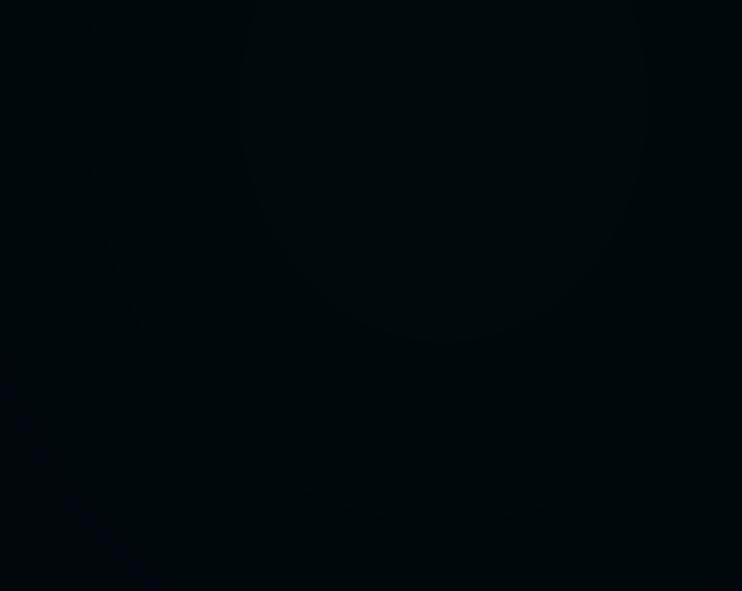

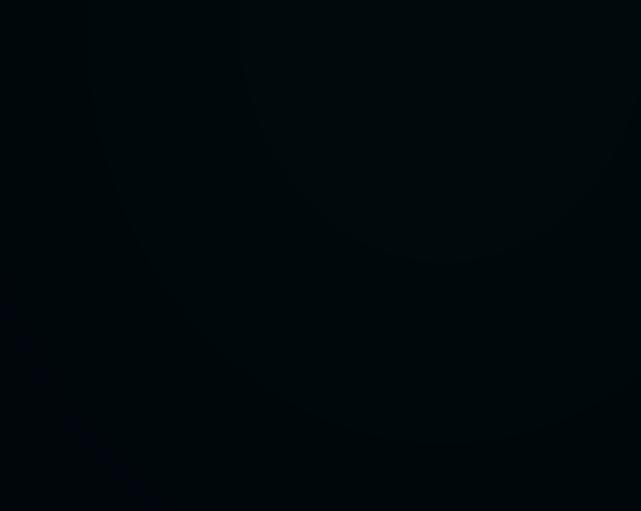
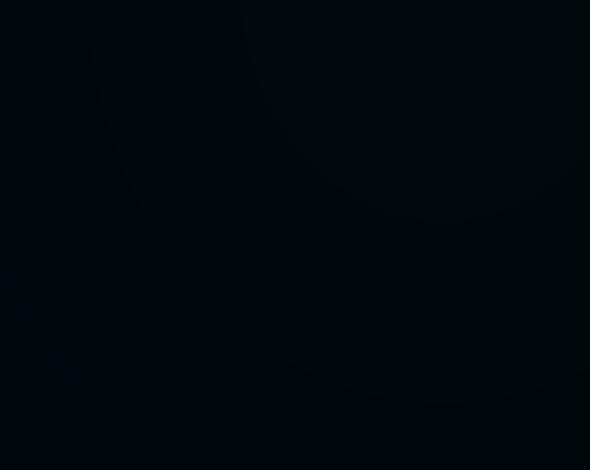
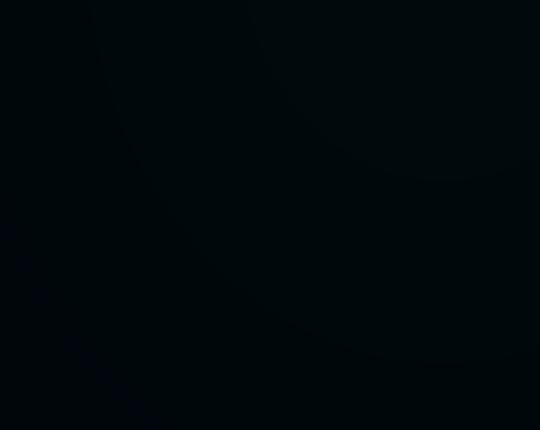
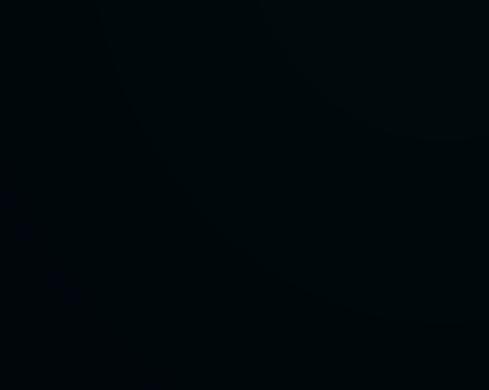

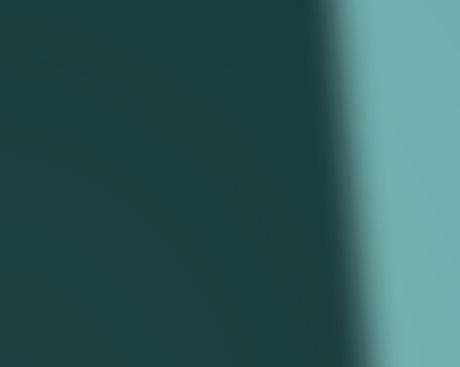

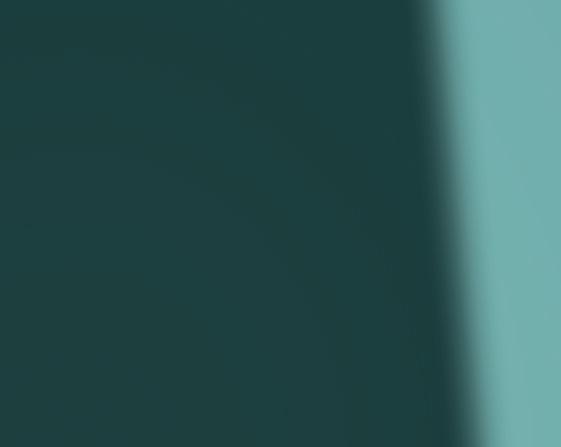
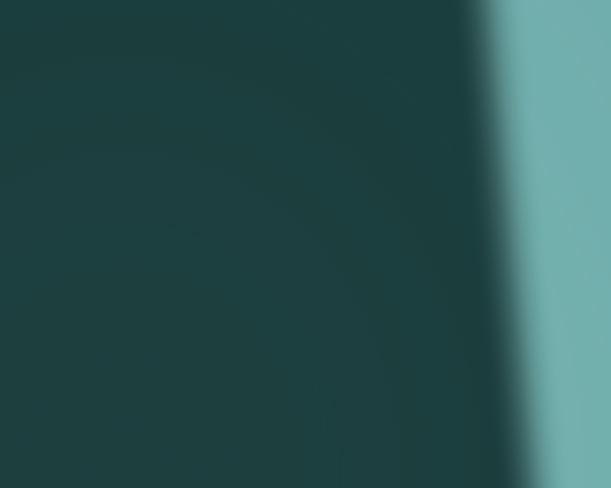
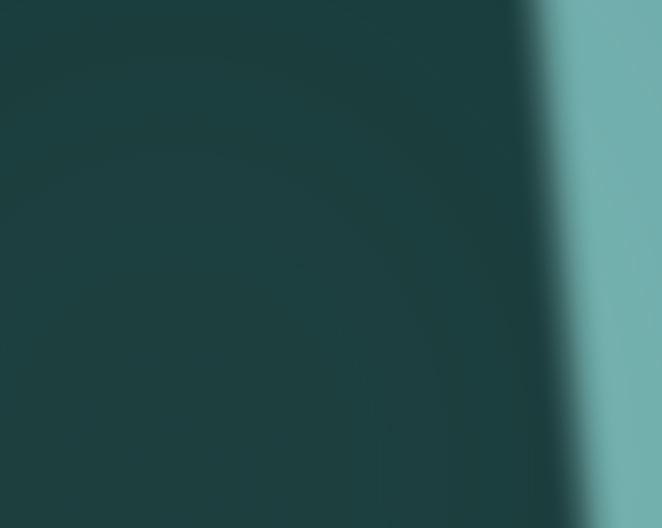
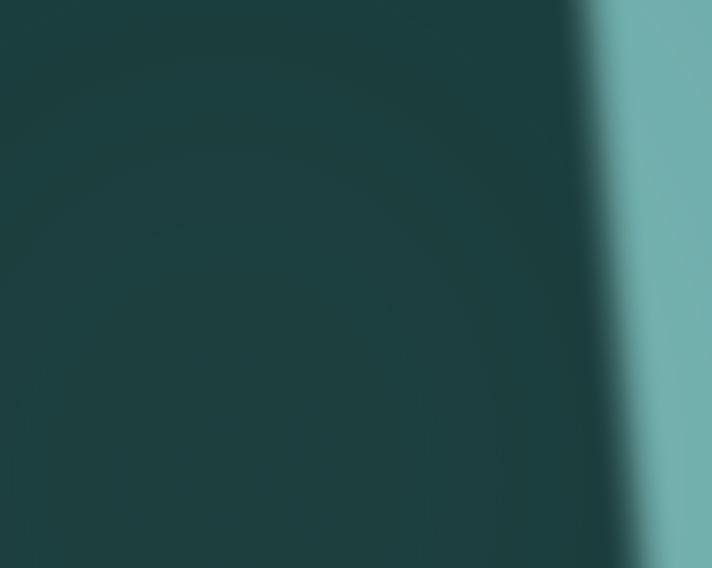
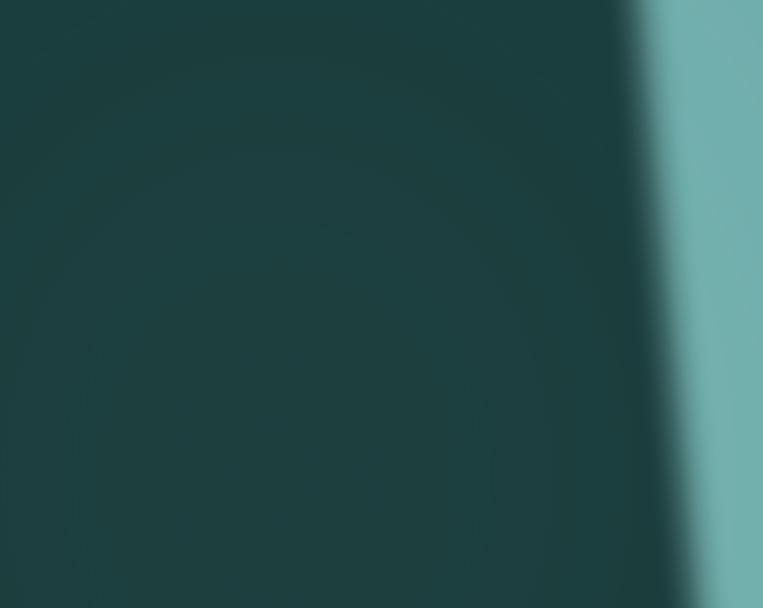
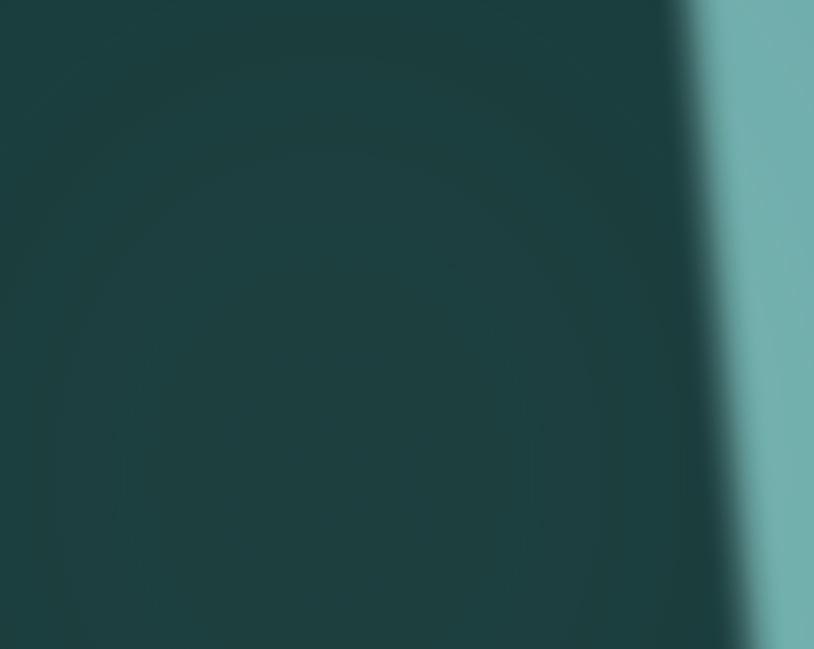
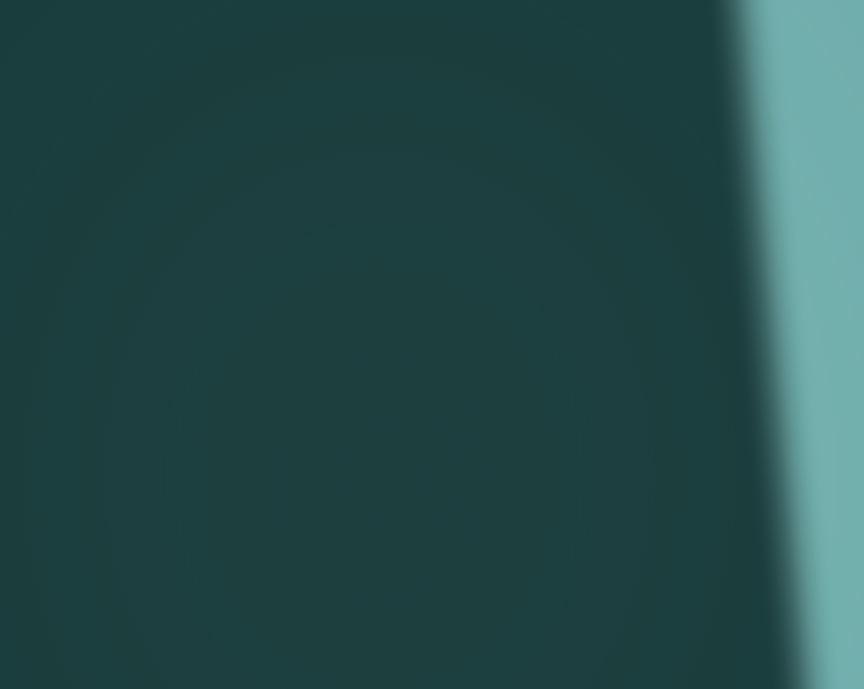
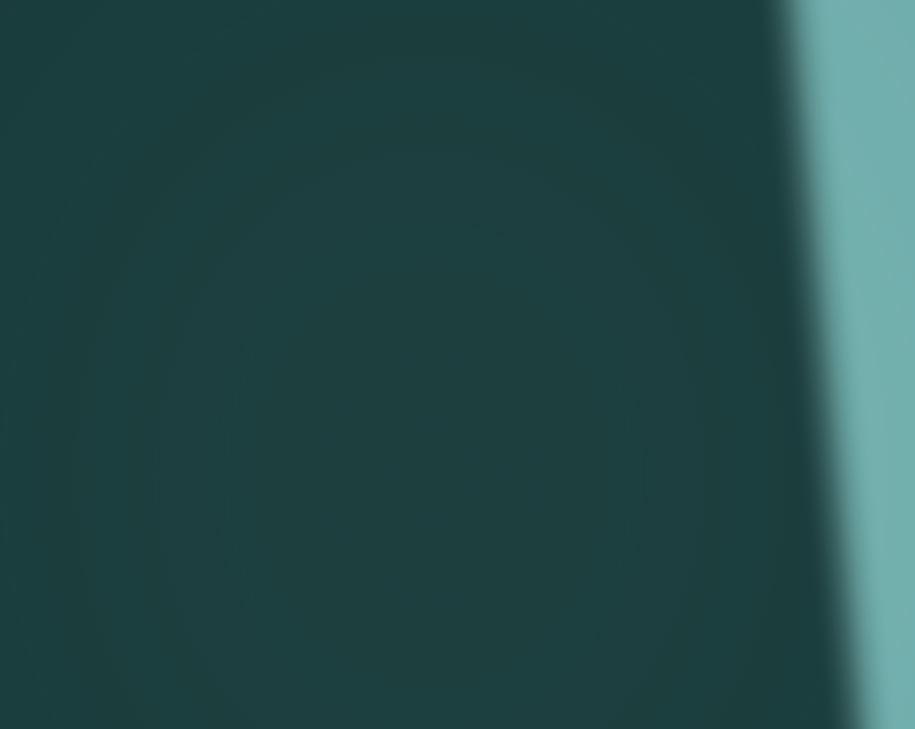
December 2021 www.fastenerengineering.com
2021 Handbook Fastener
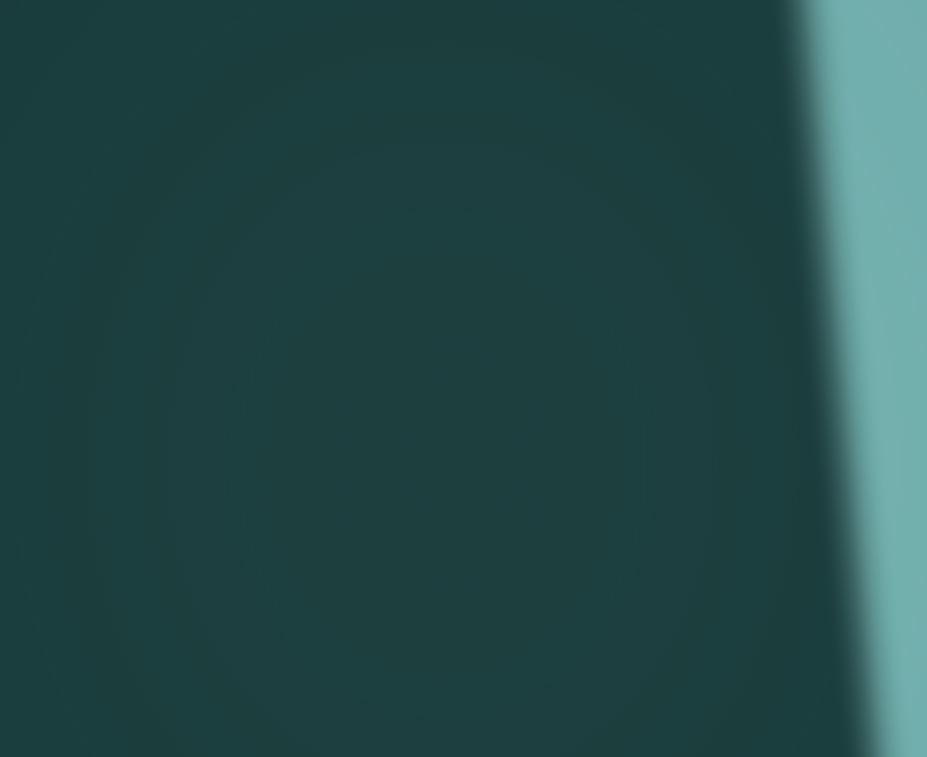
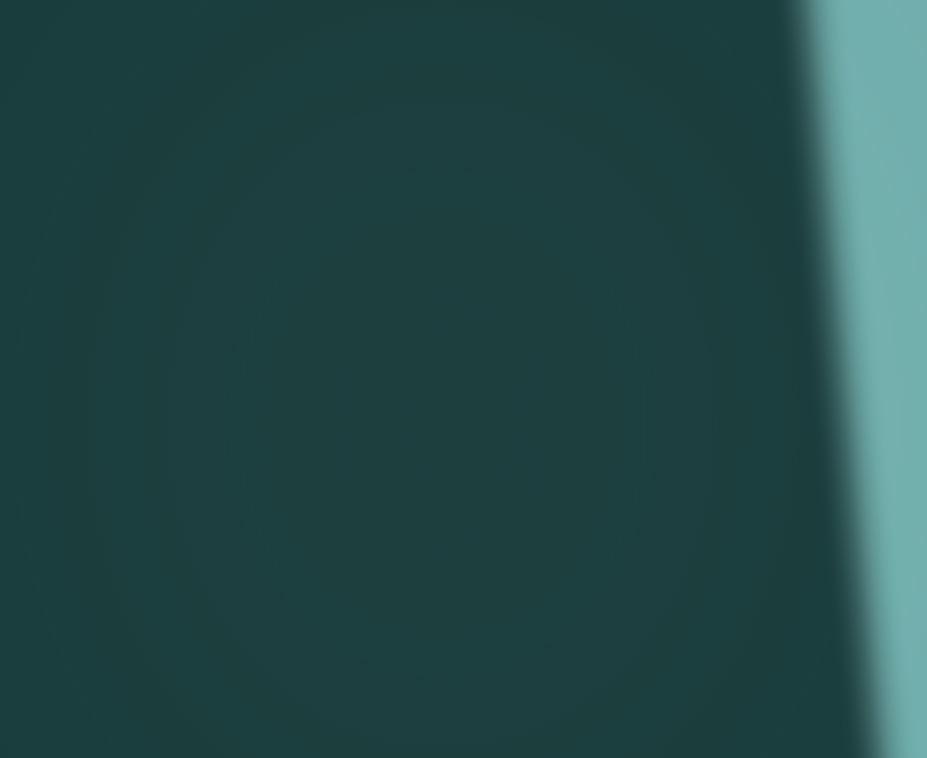
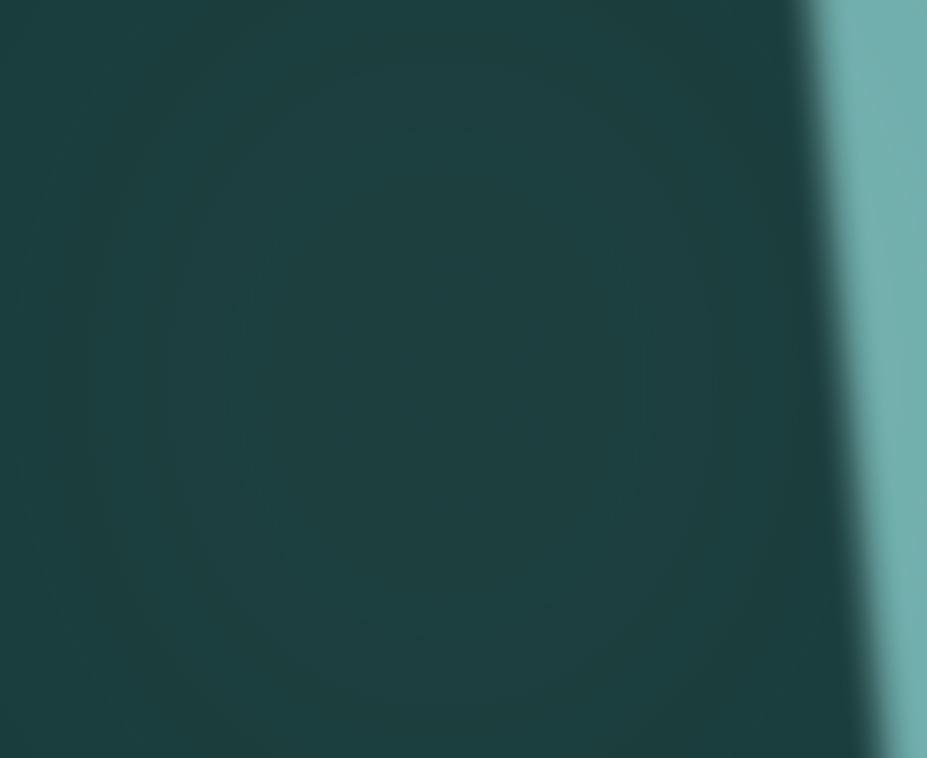
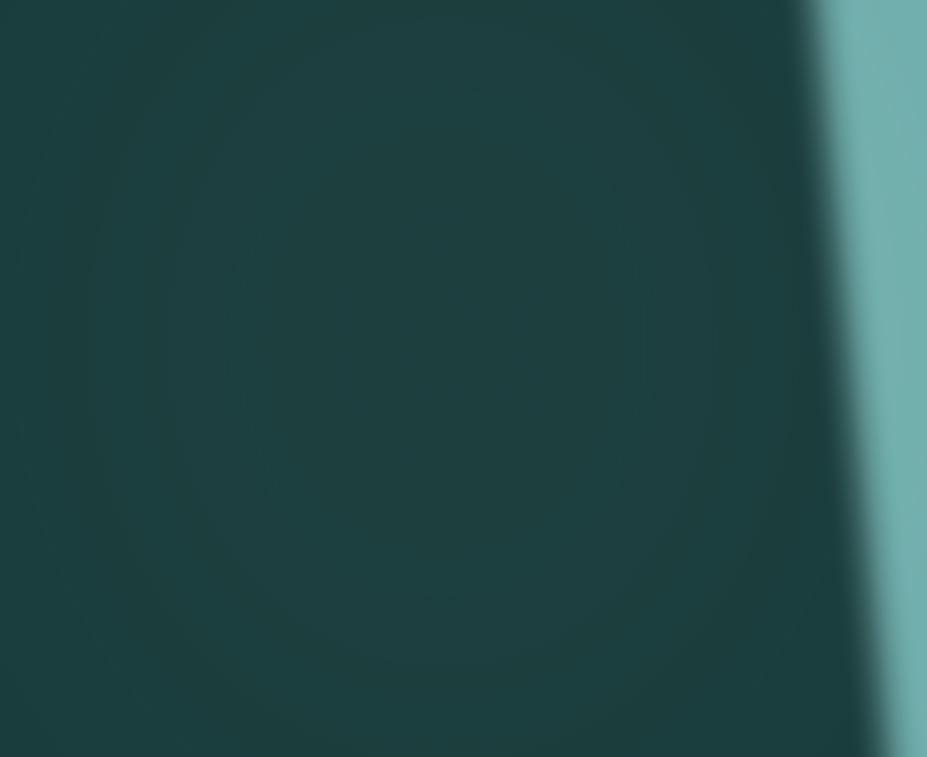

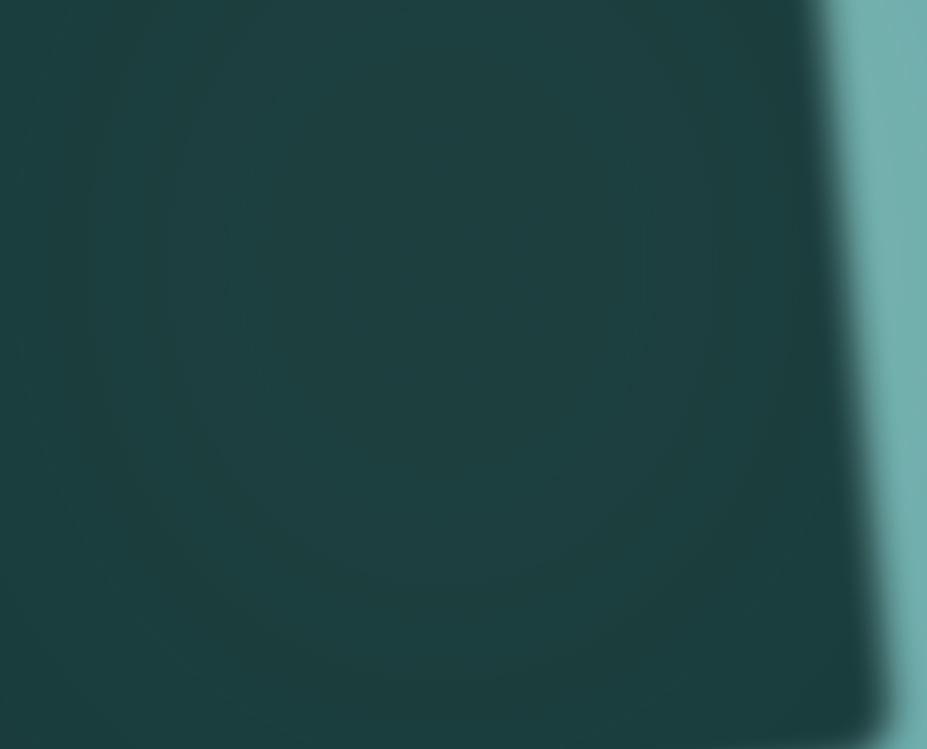
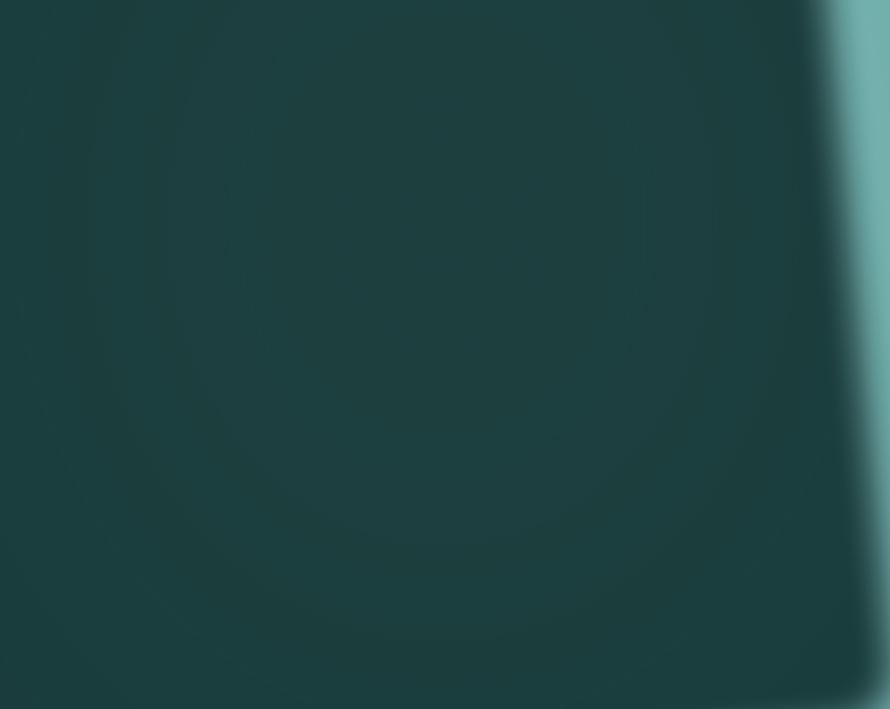
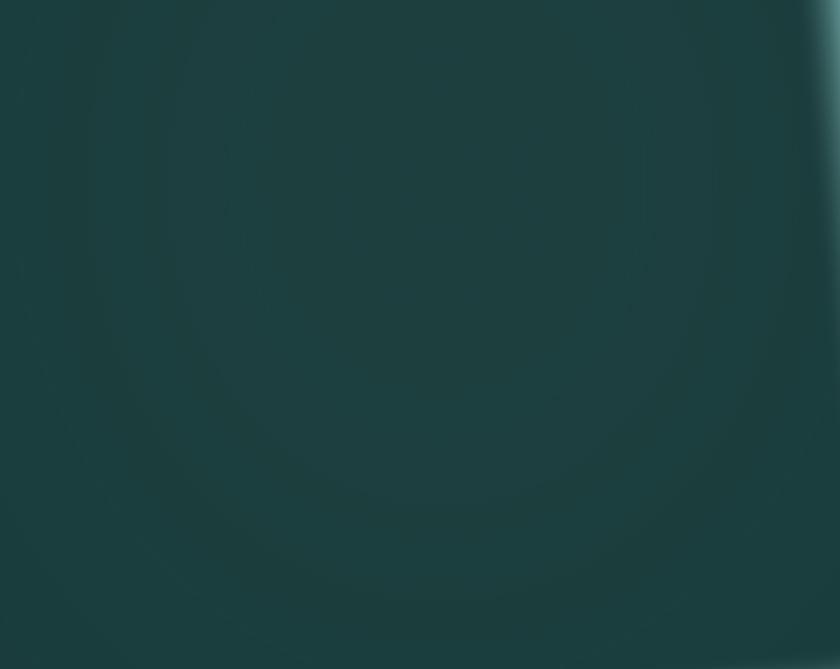
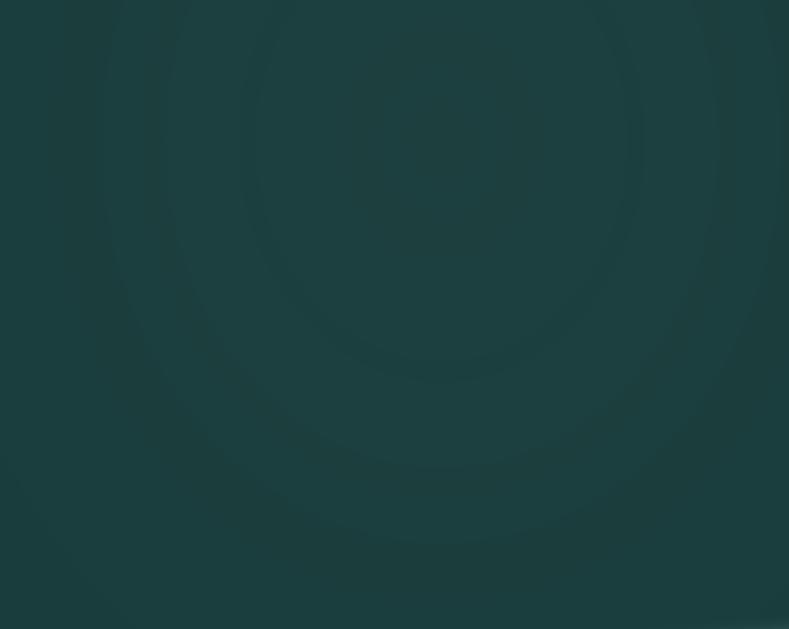

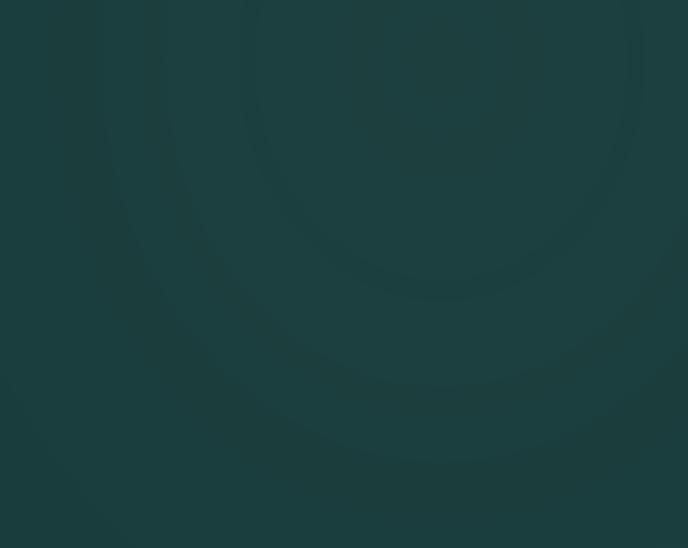
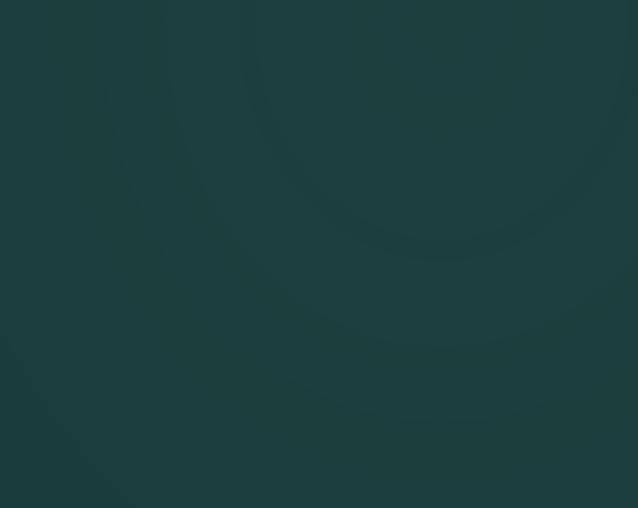
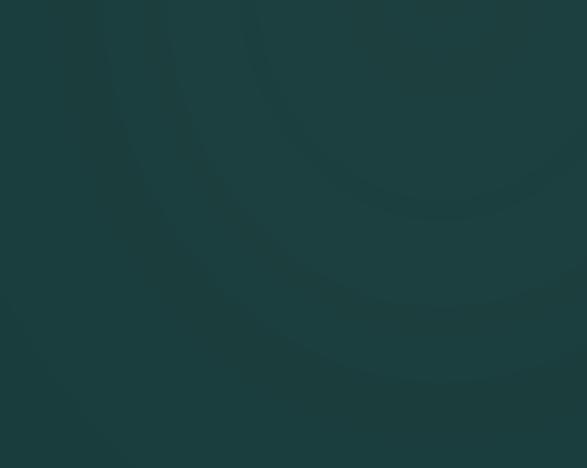
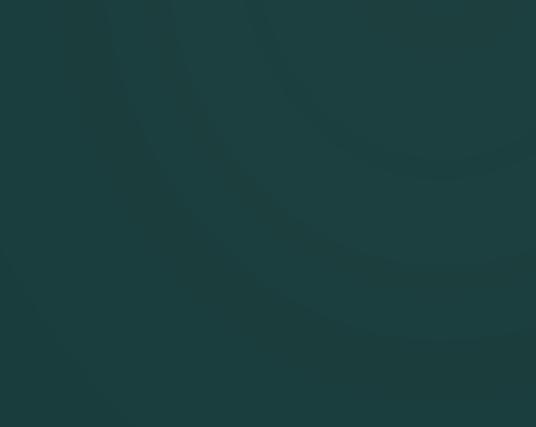
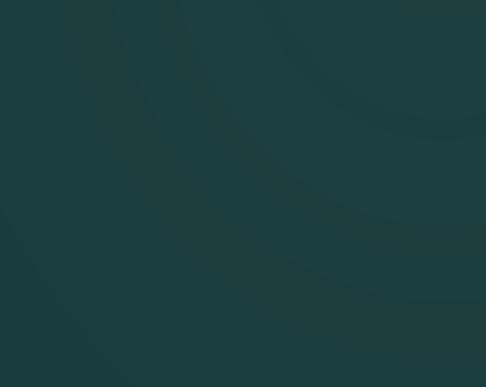

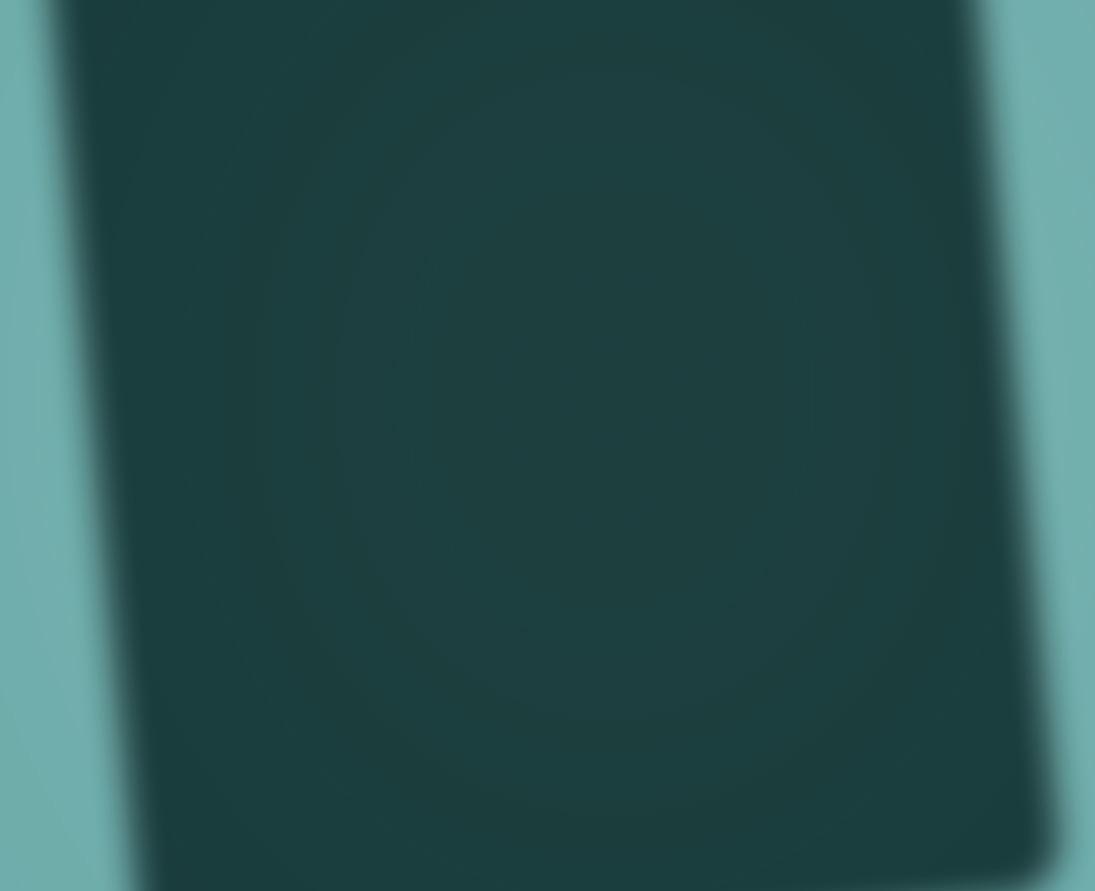
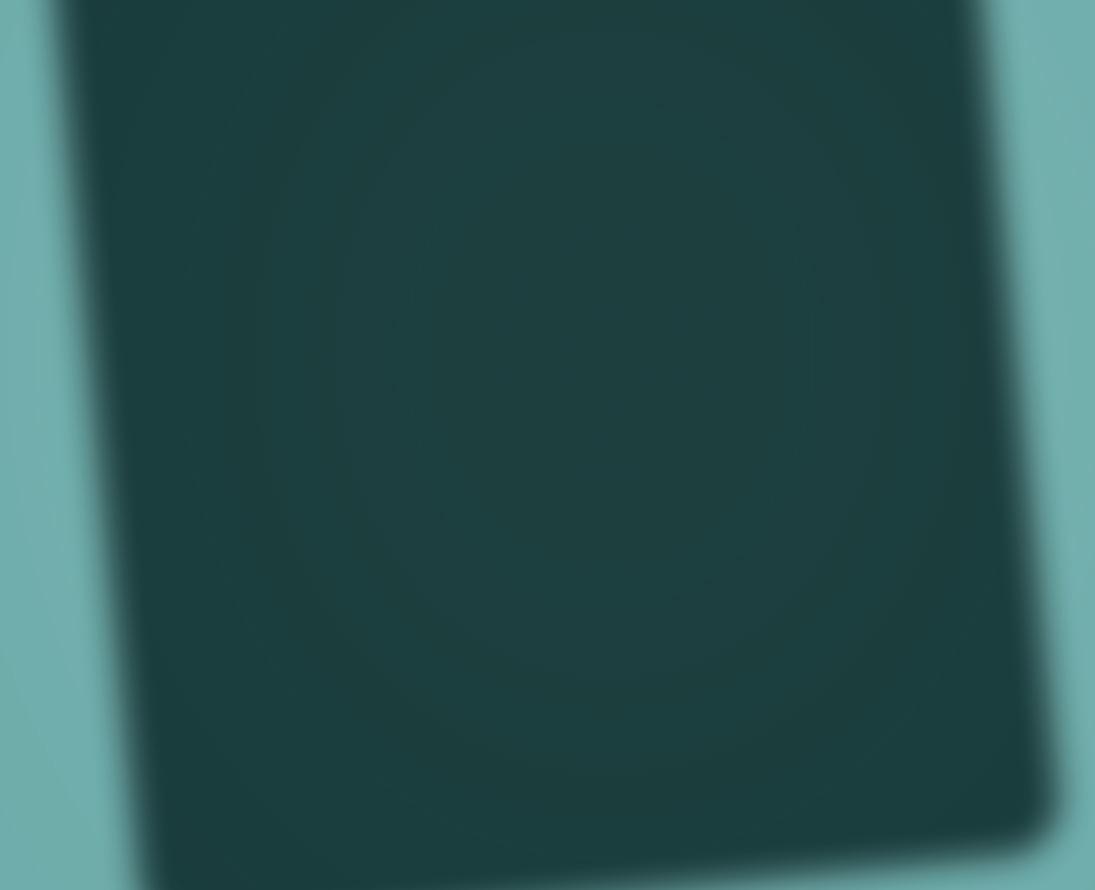
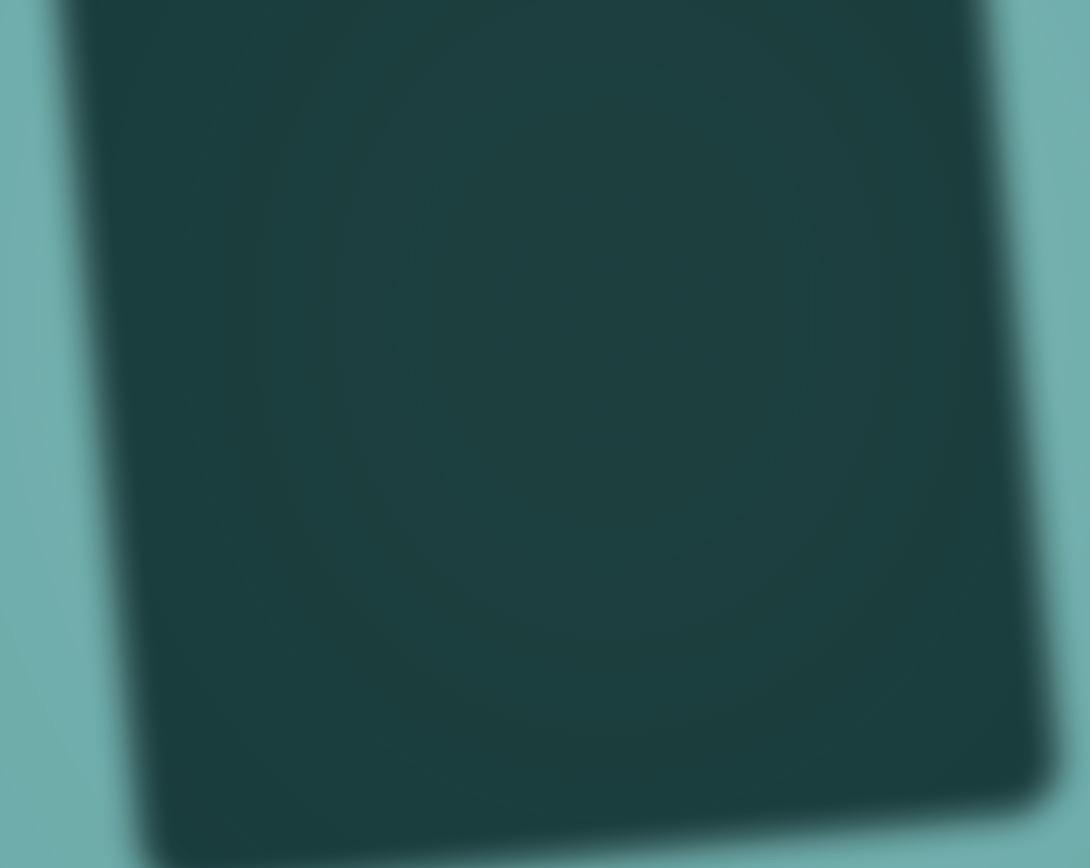
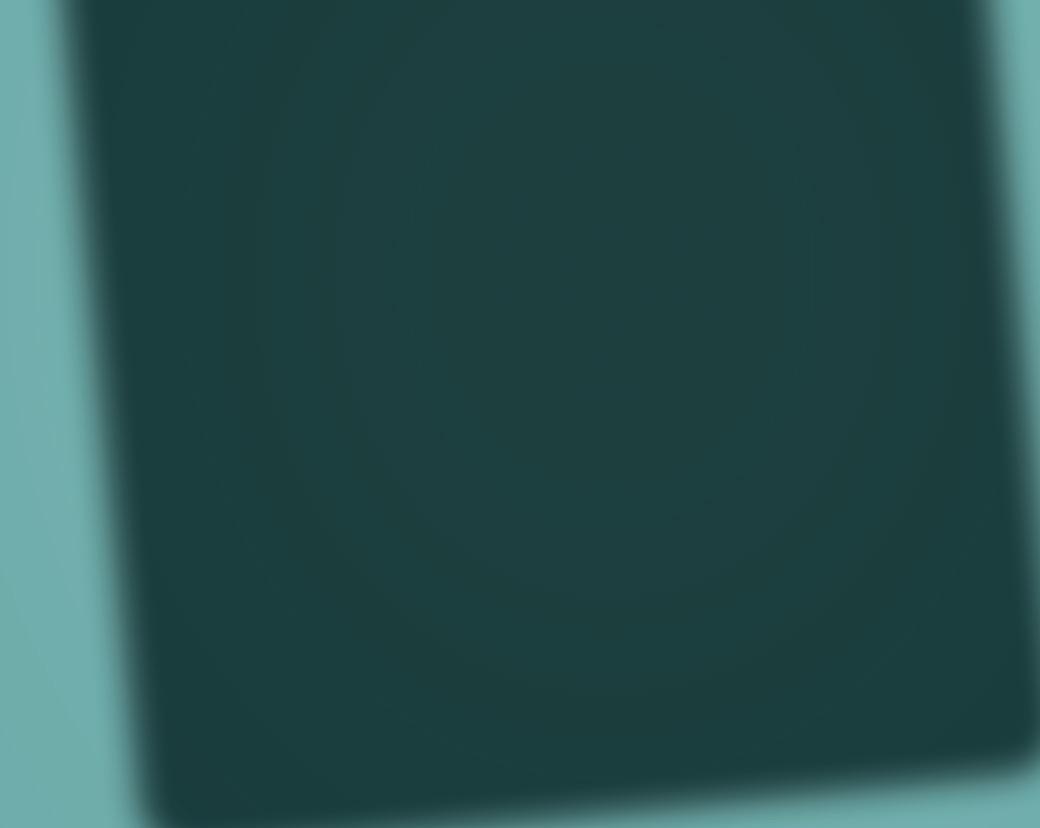
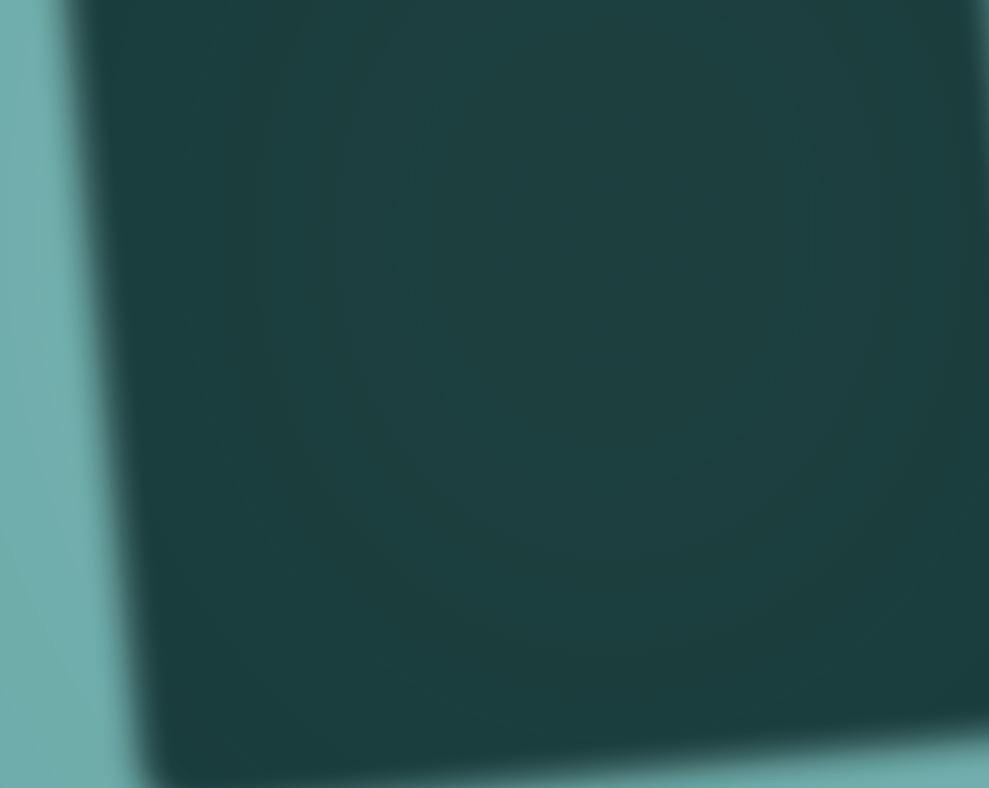
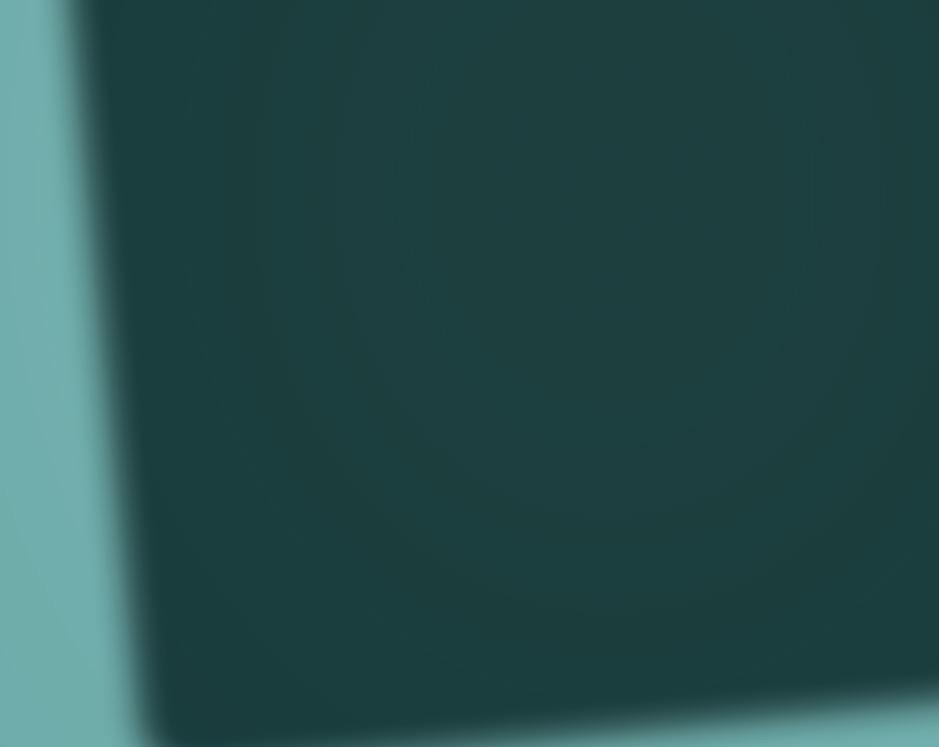
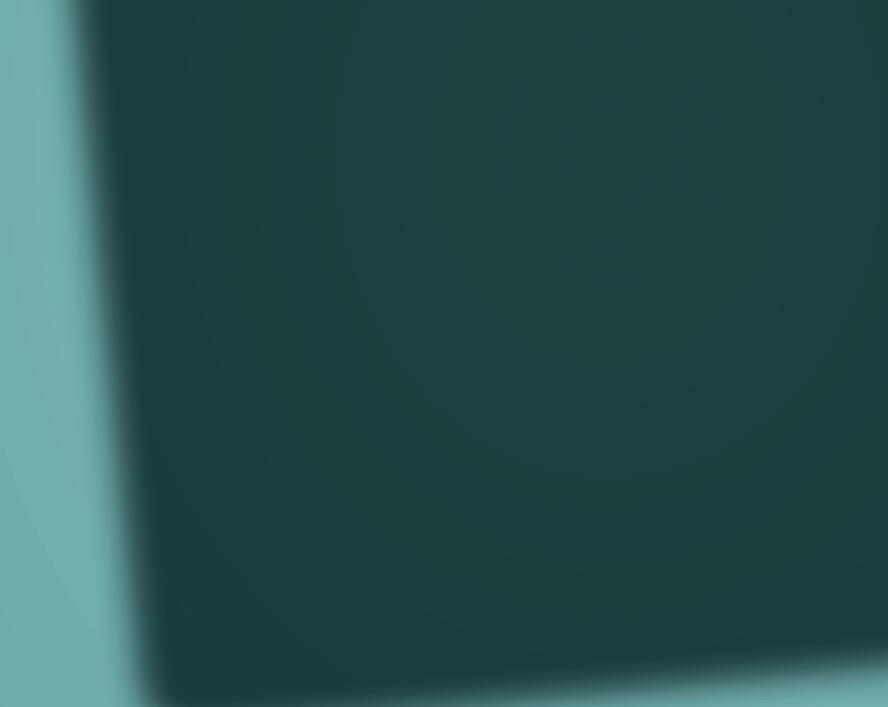
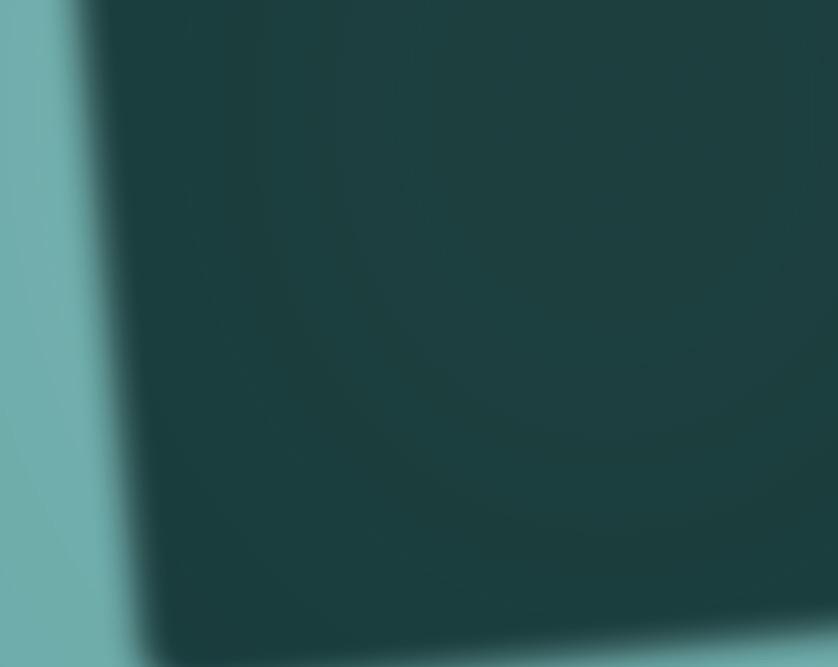

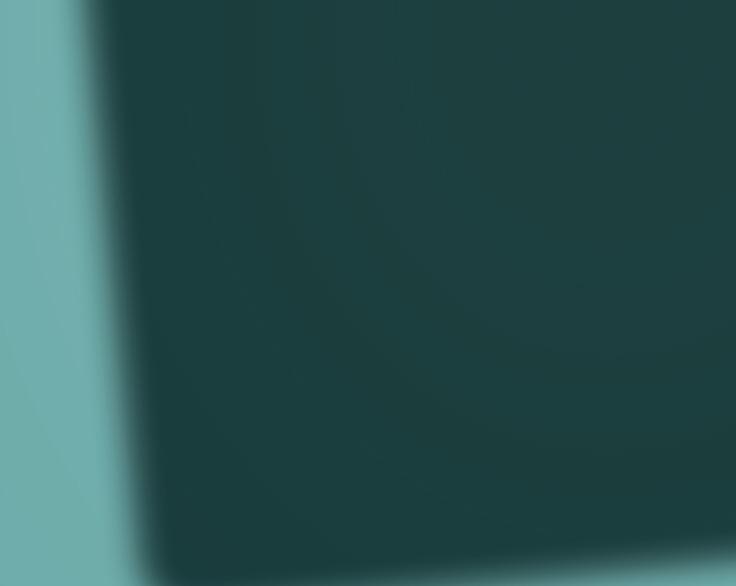

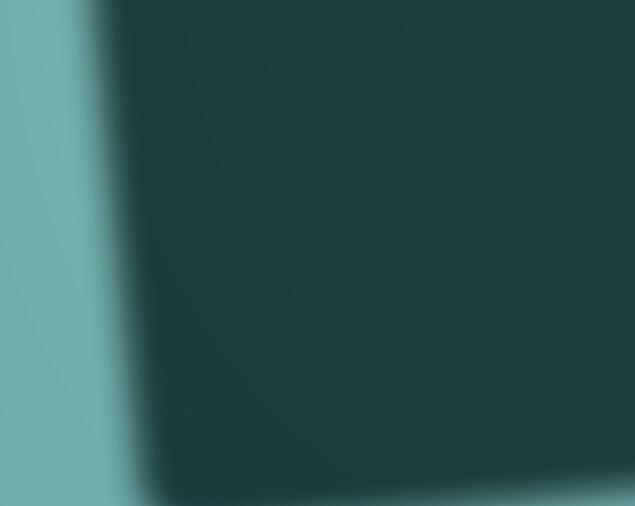
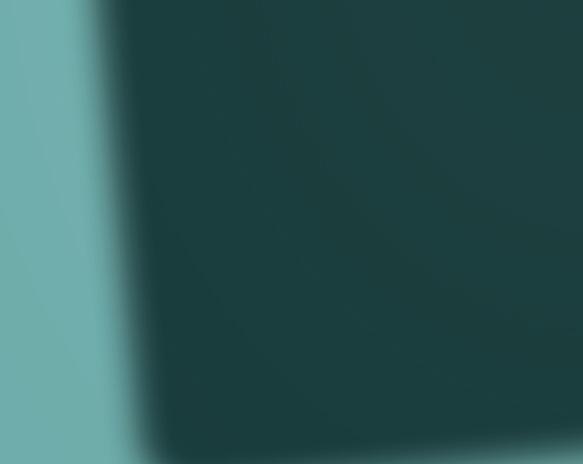

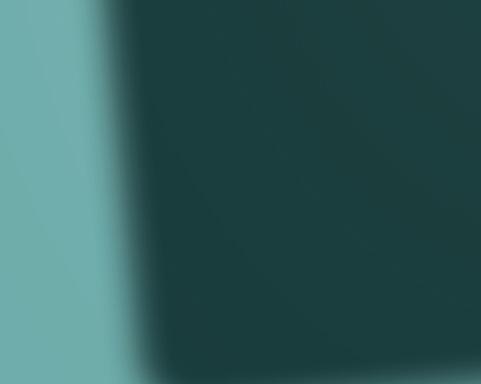




Check out the digital edition!
So much happens between issues that even another issue would not be enough to keep up. That’s why it makes sense to visit fastenerengineering.com and stay on Twitter, Facebook and Linkedin. It’s updated regularly with relevant technical information and other signifi cant news for the design engineering community.
fastenerengineering.com
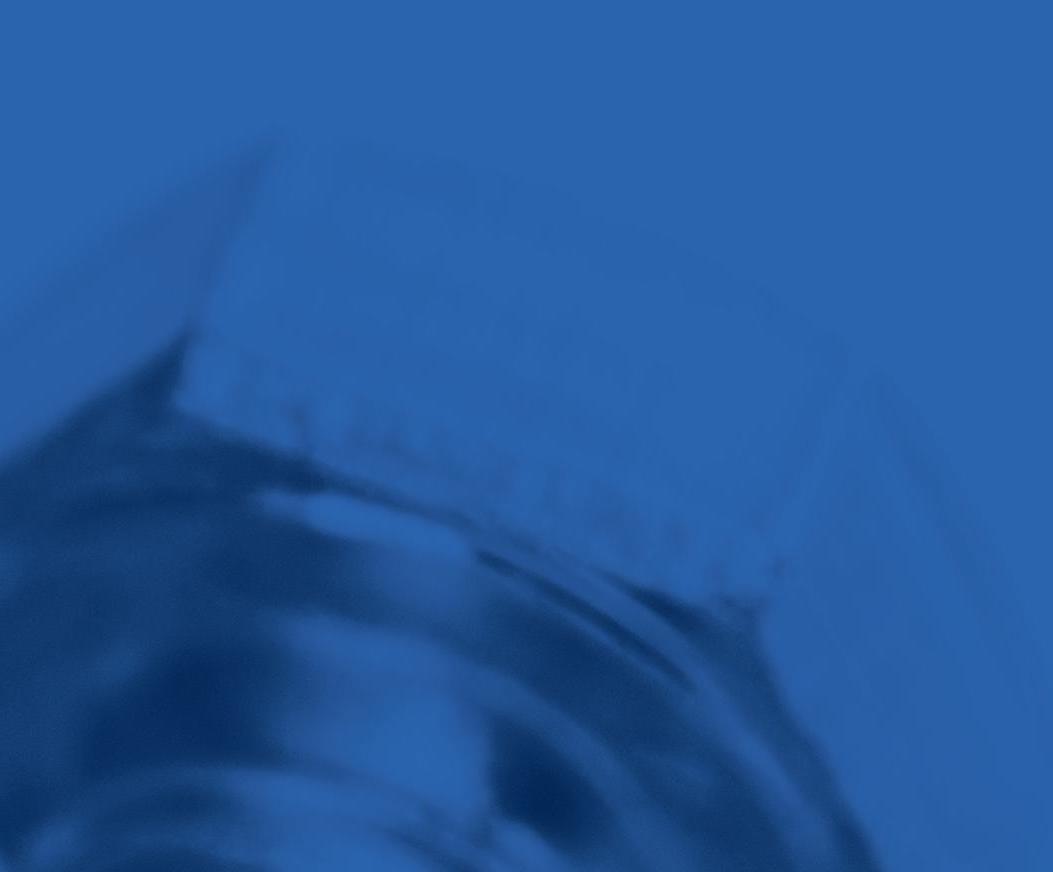
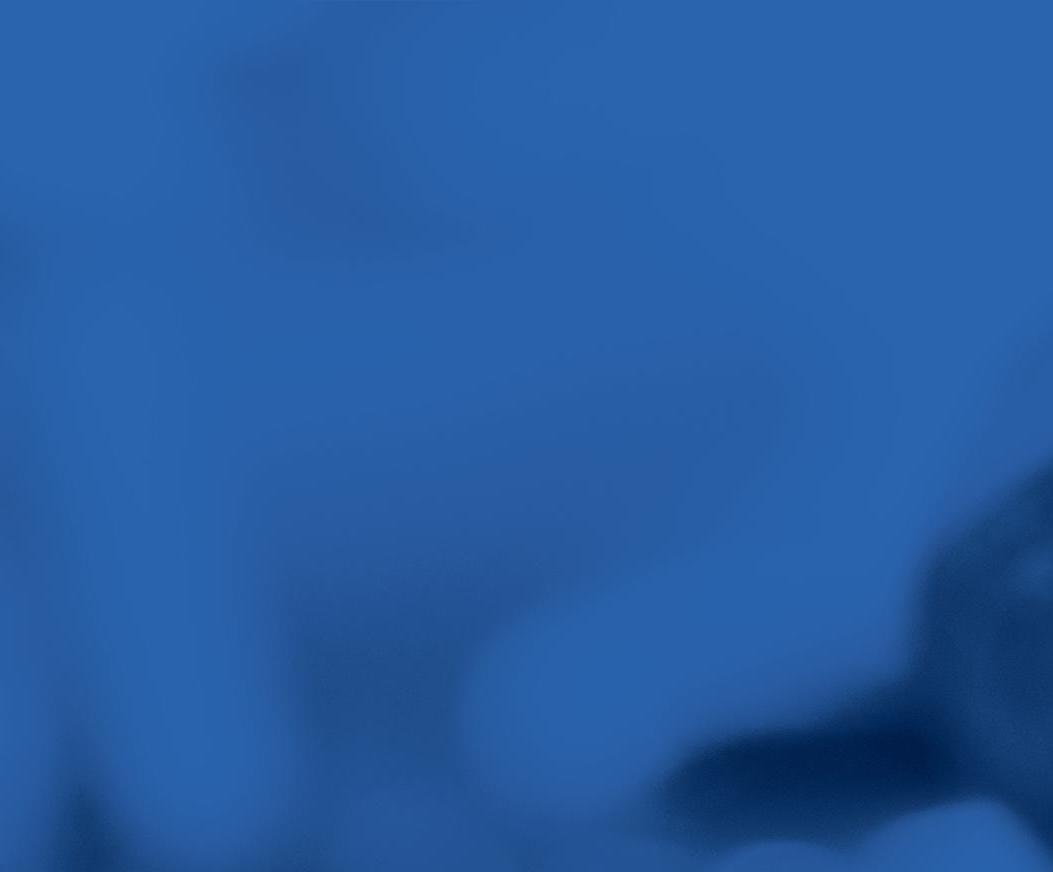
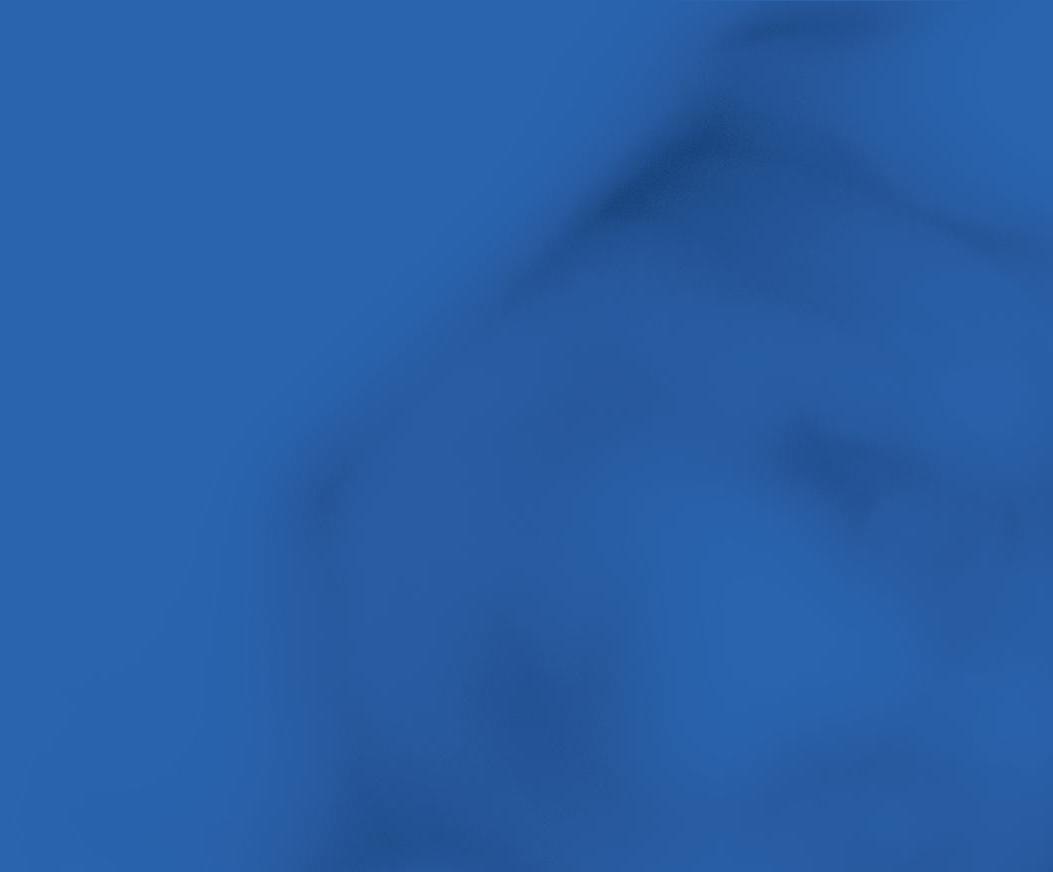
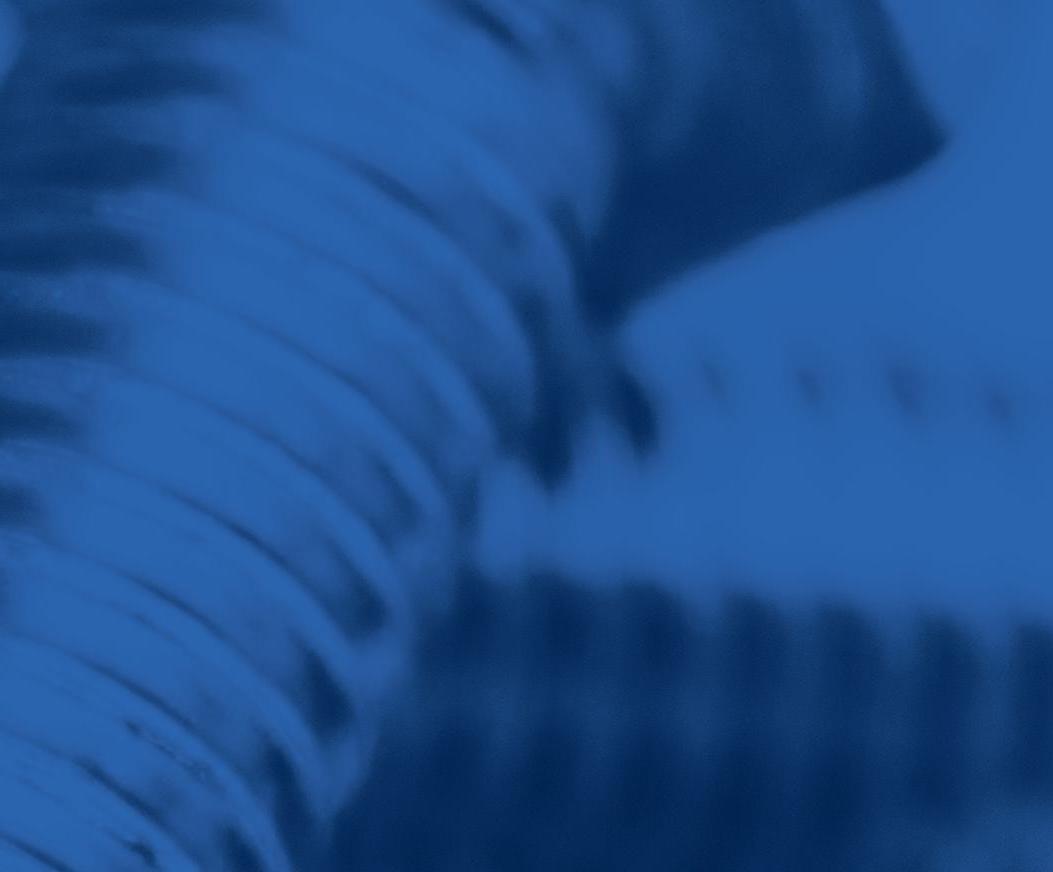

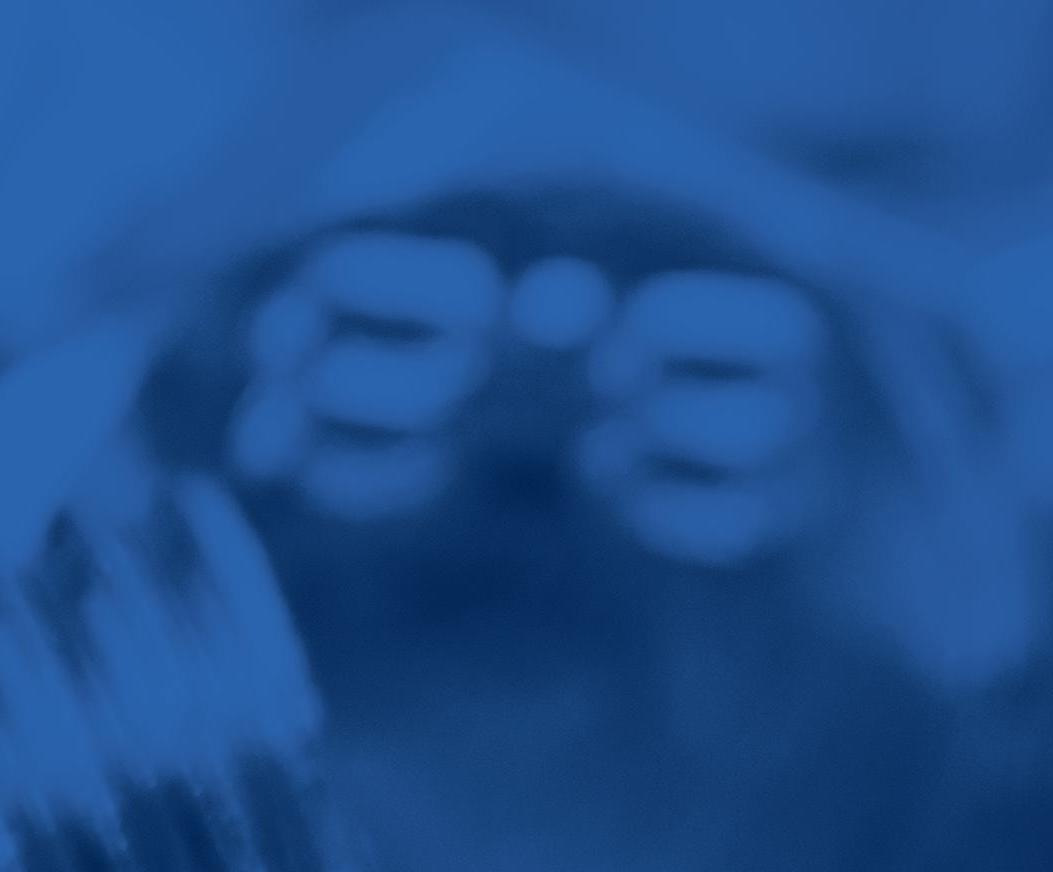
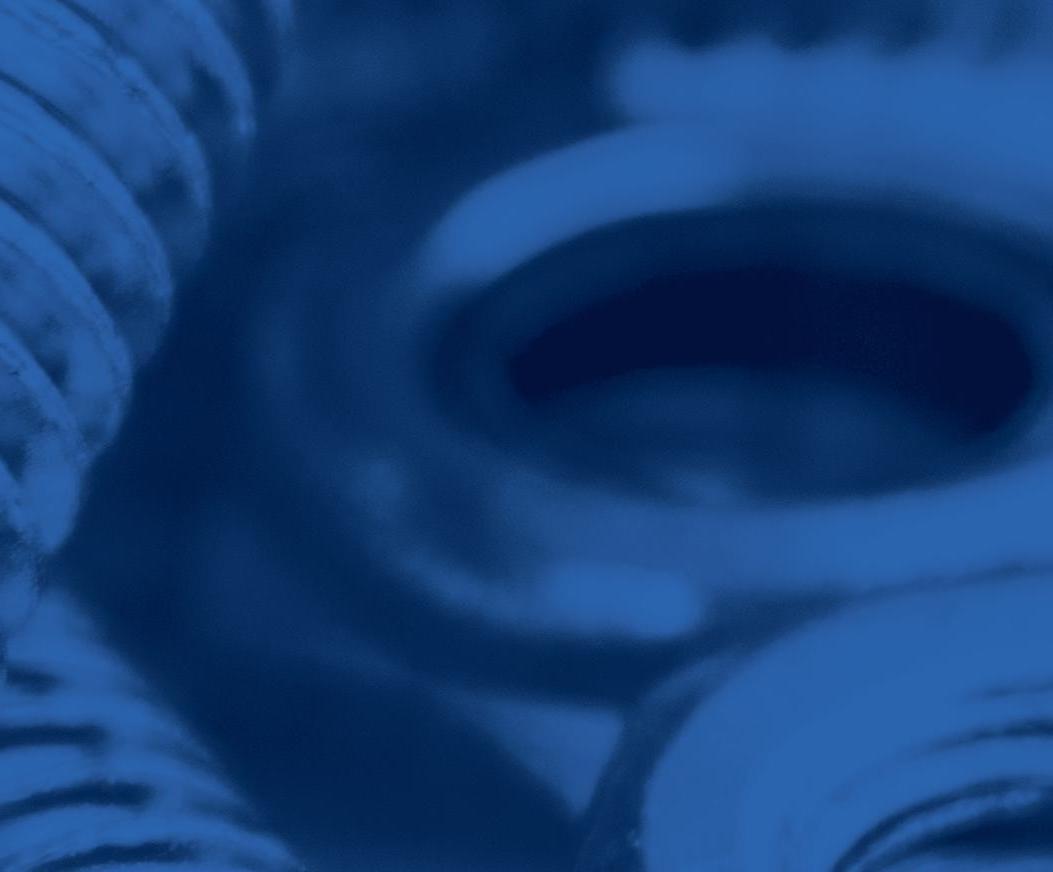

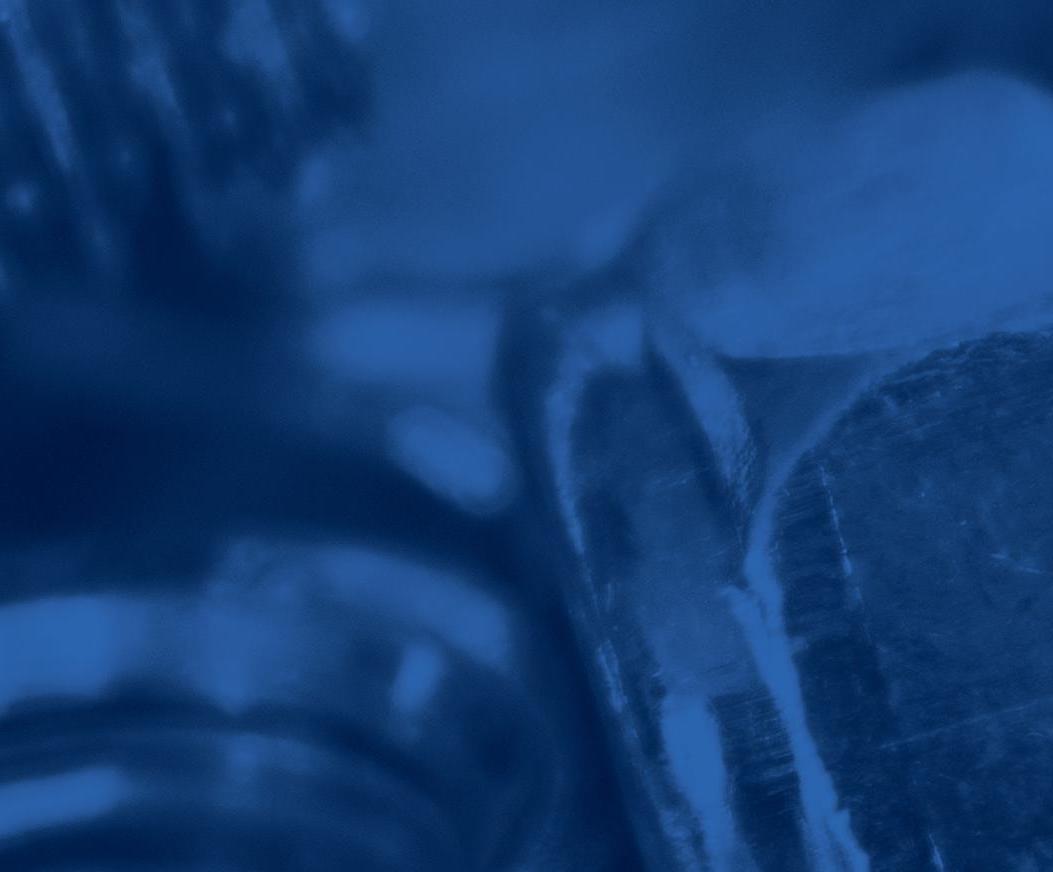
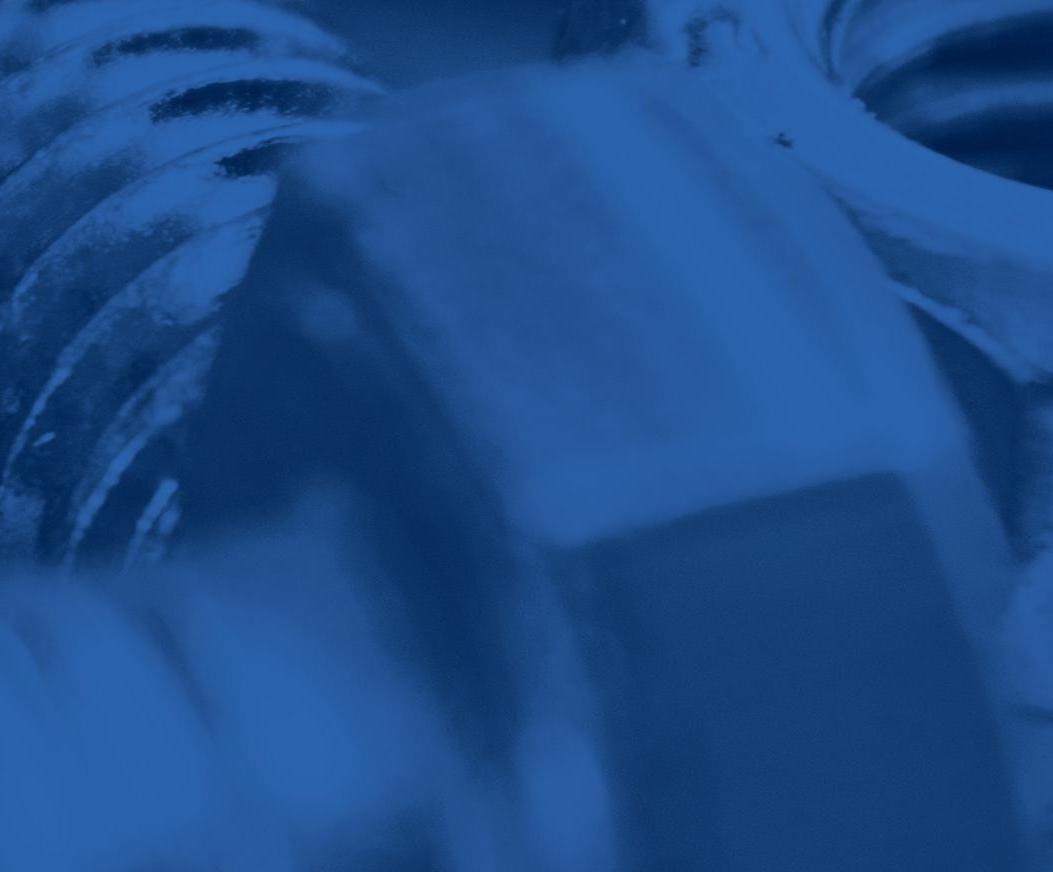
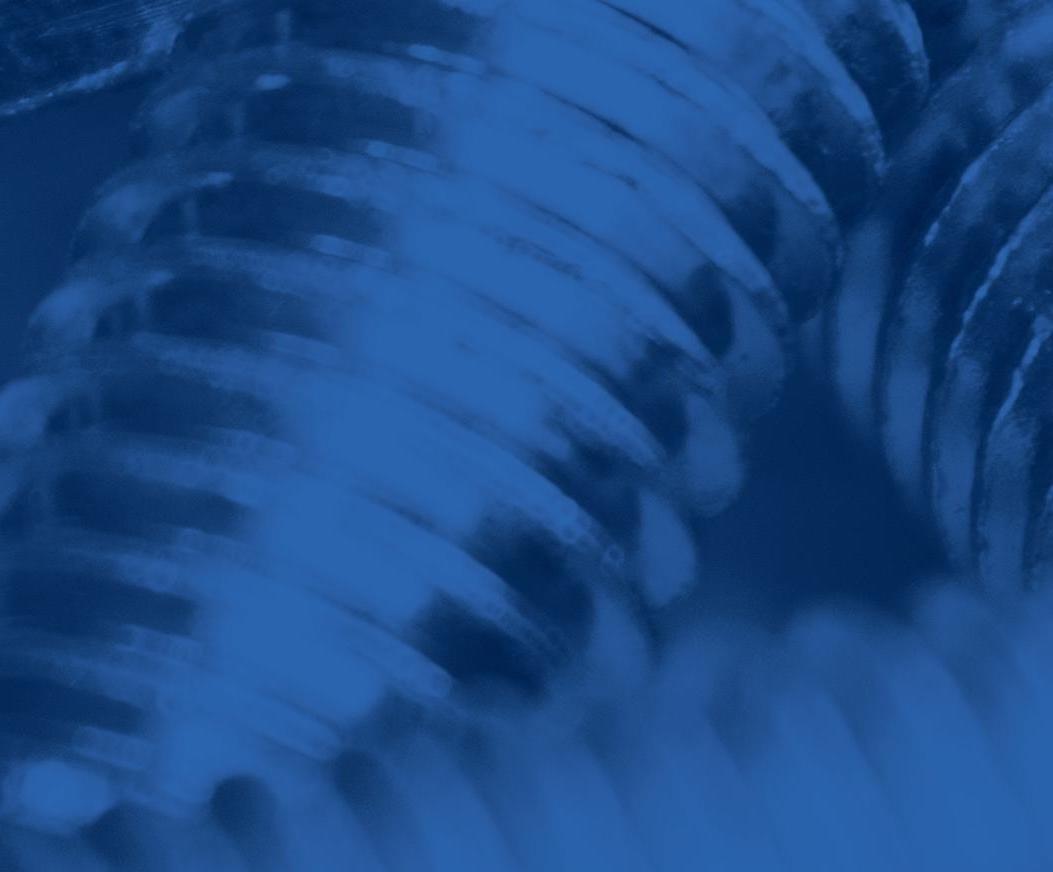
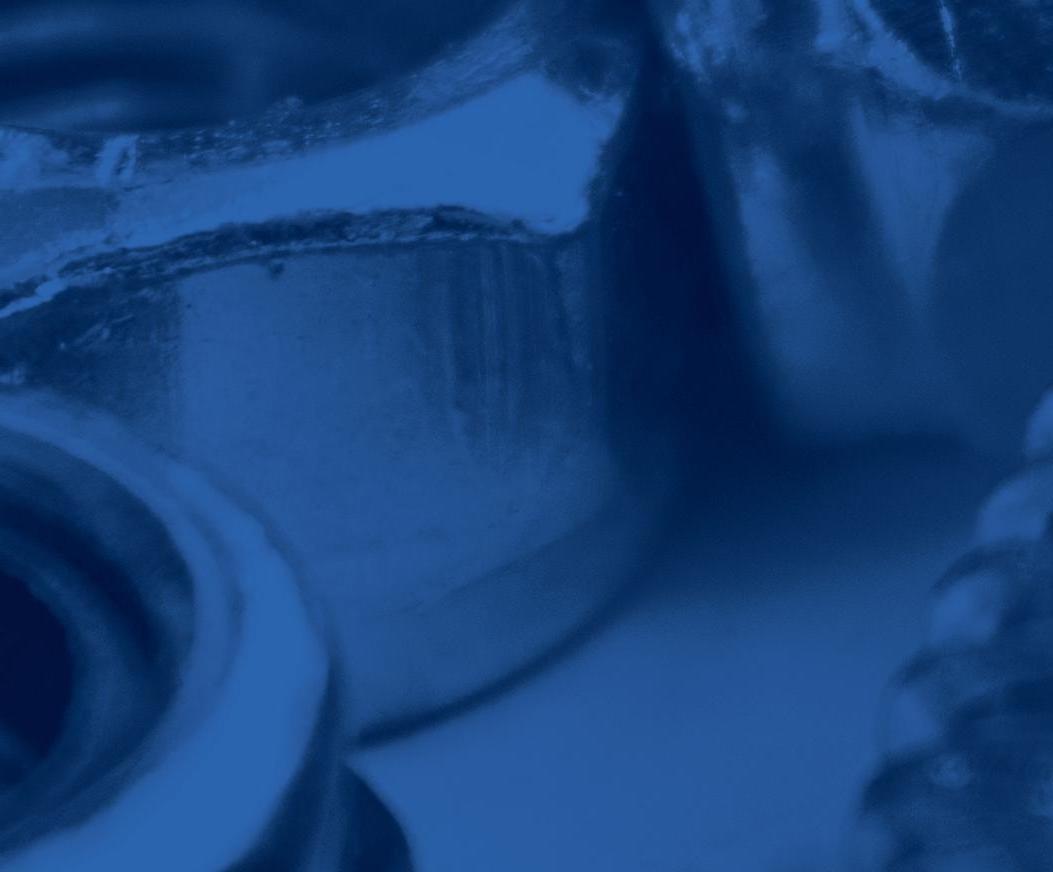
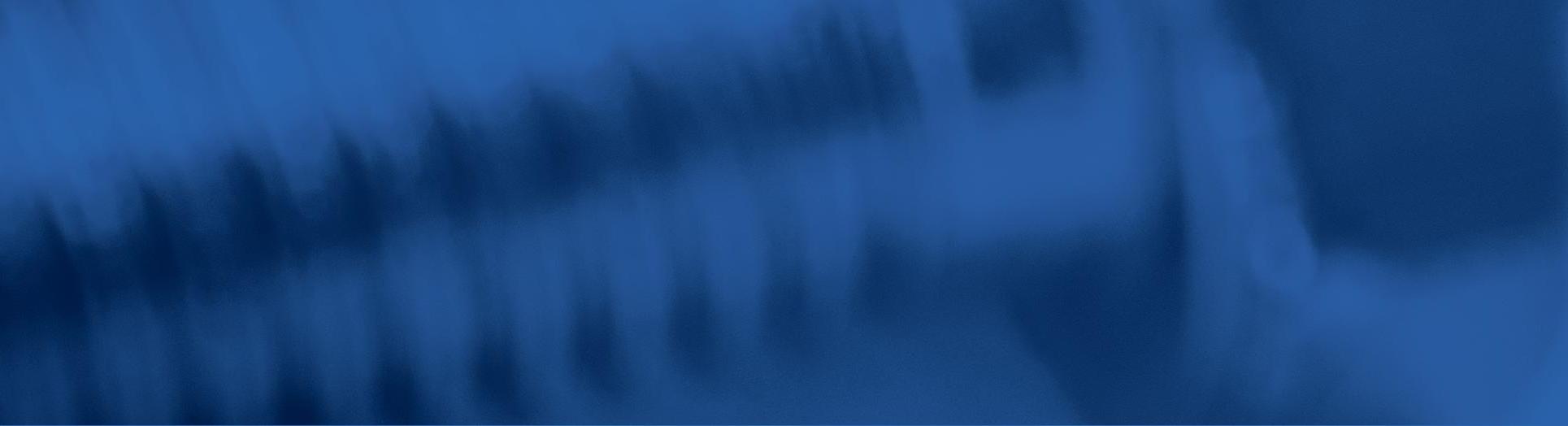
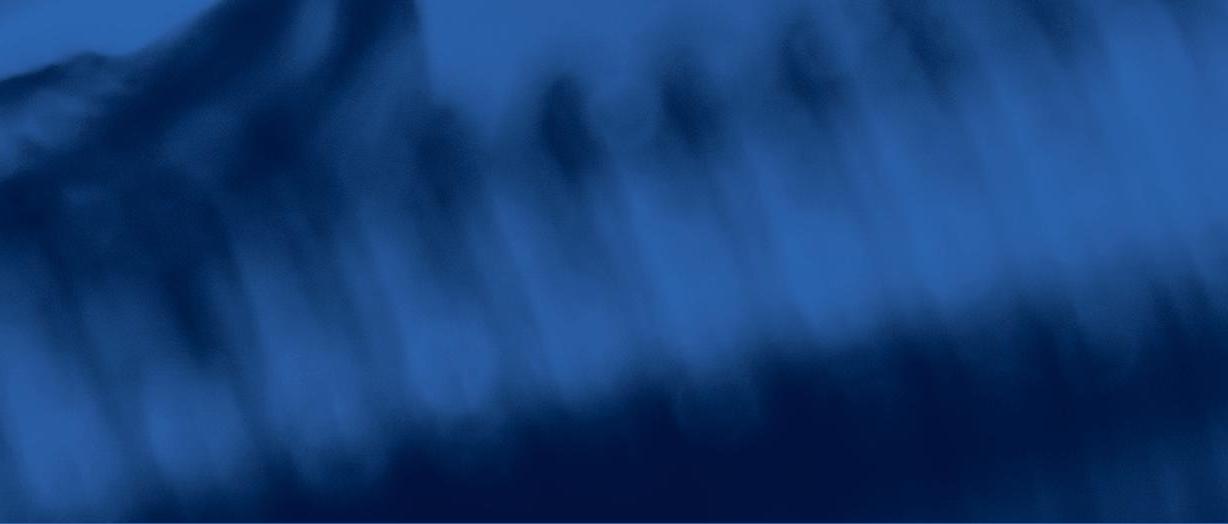