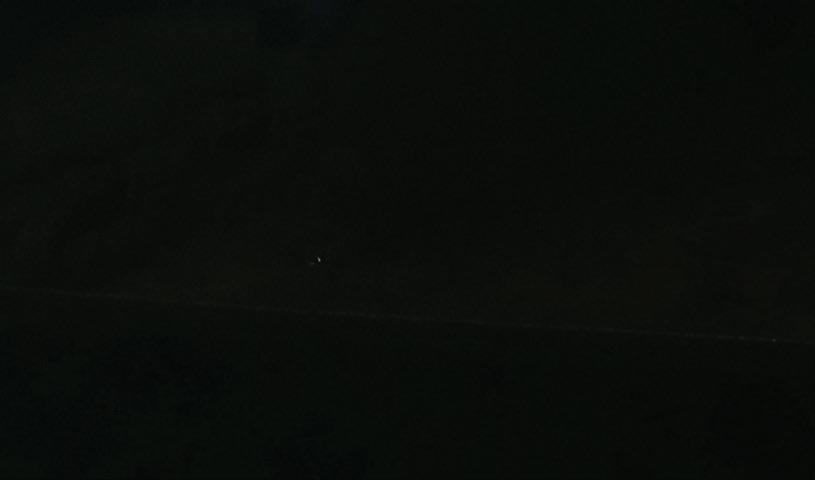
4 minute read
WELDING: Joints
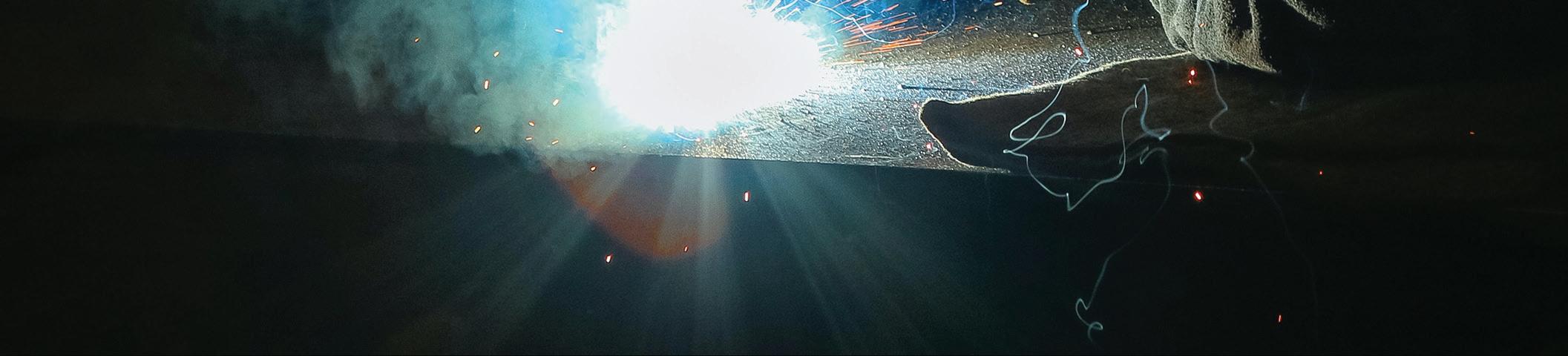
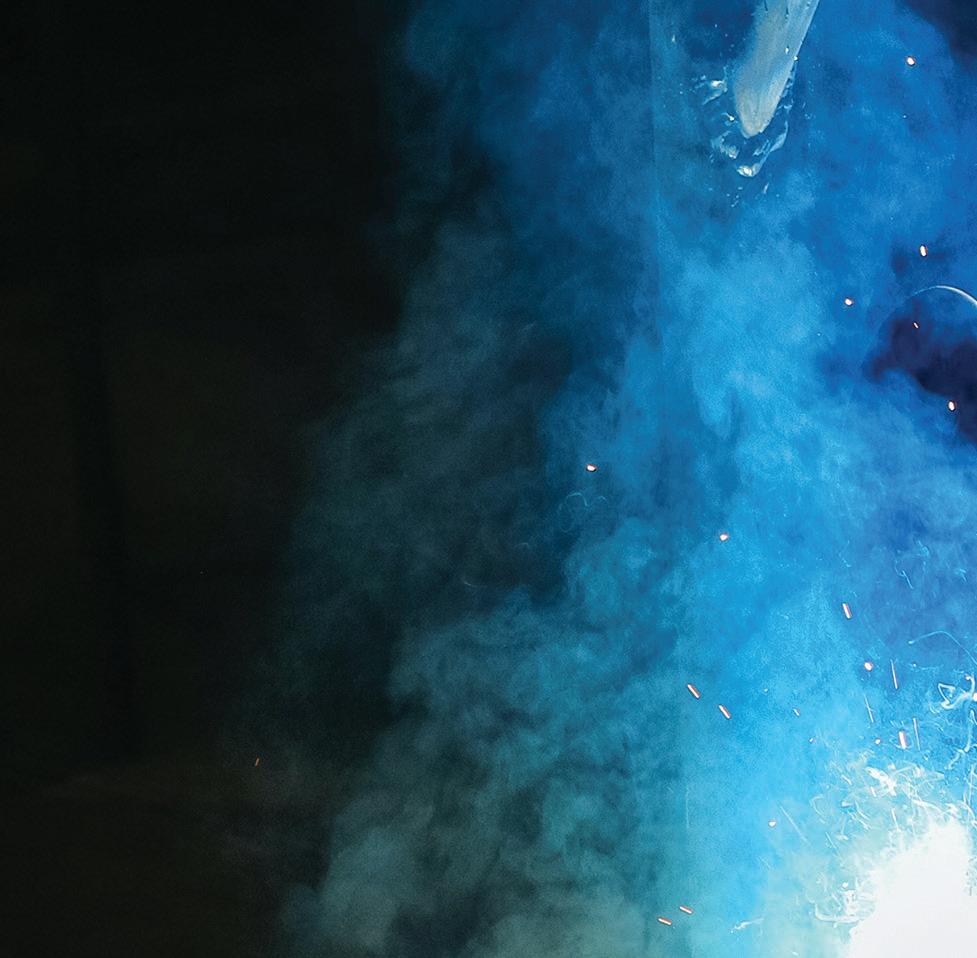
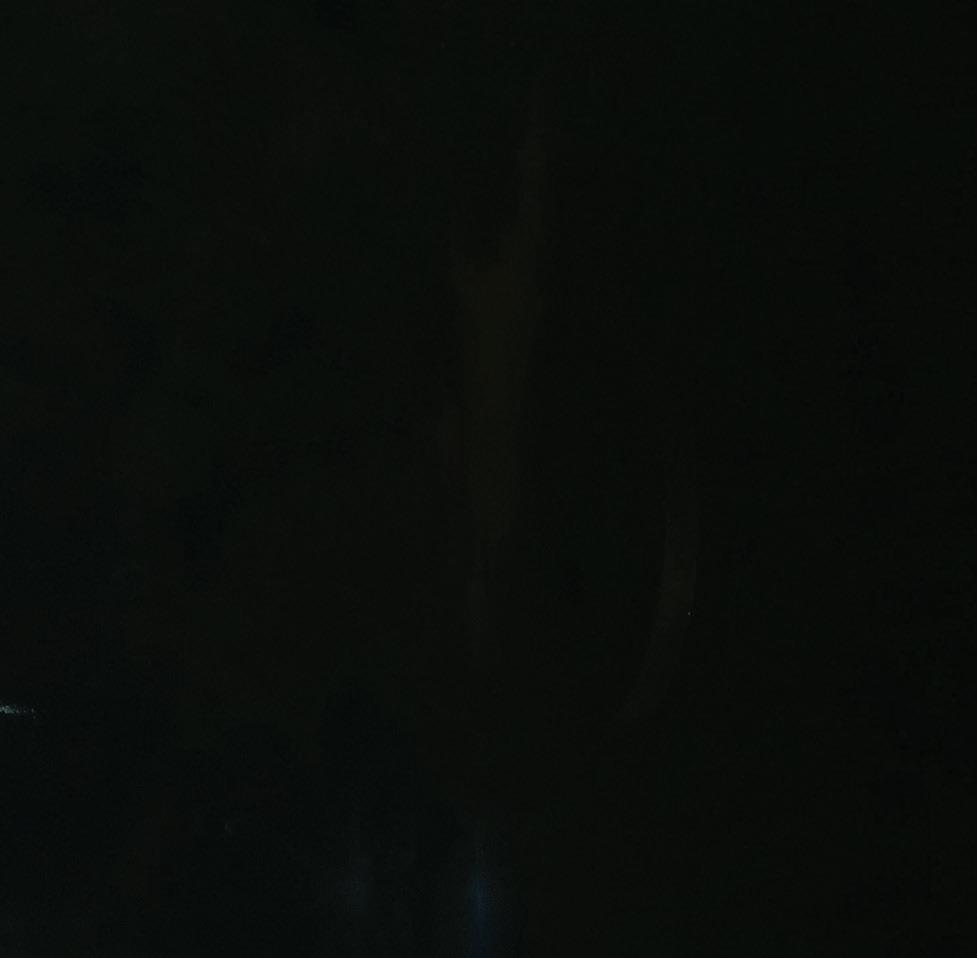
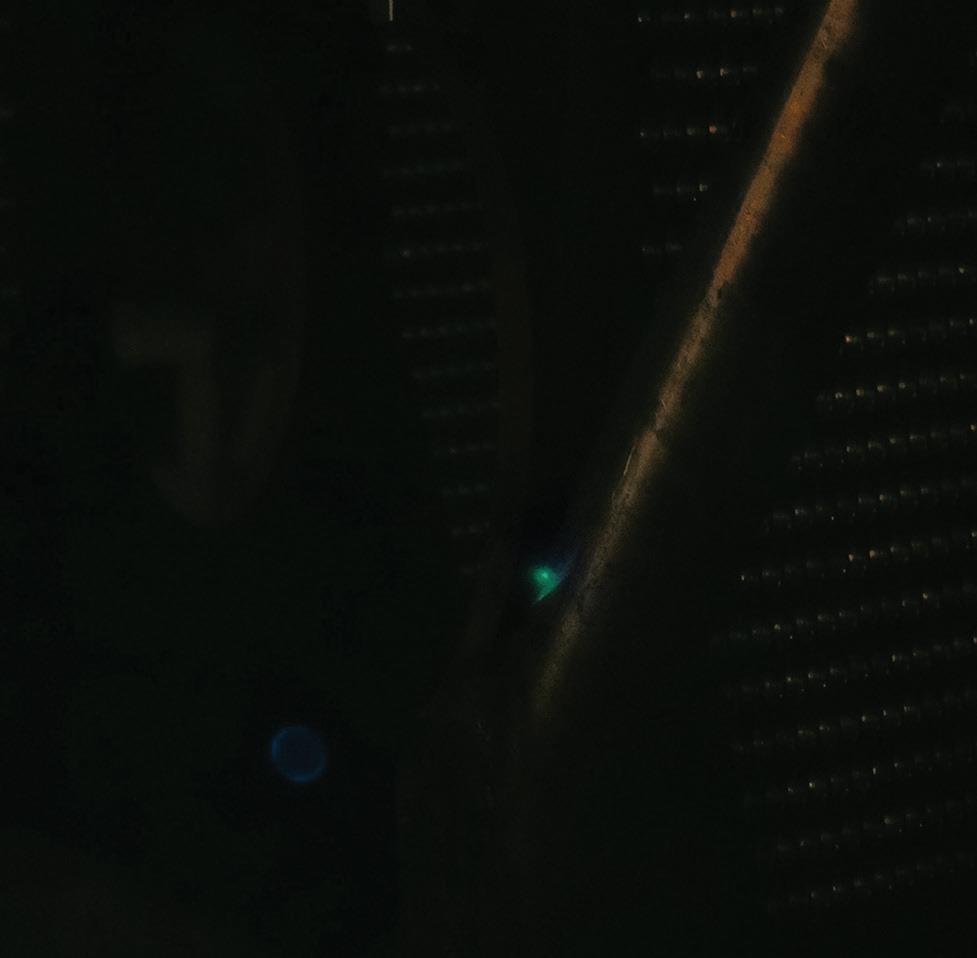
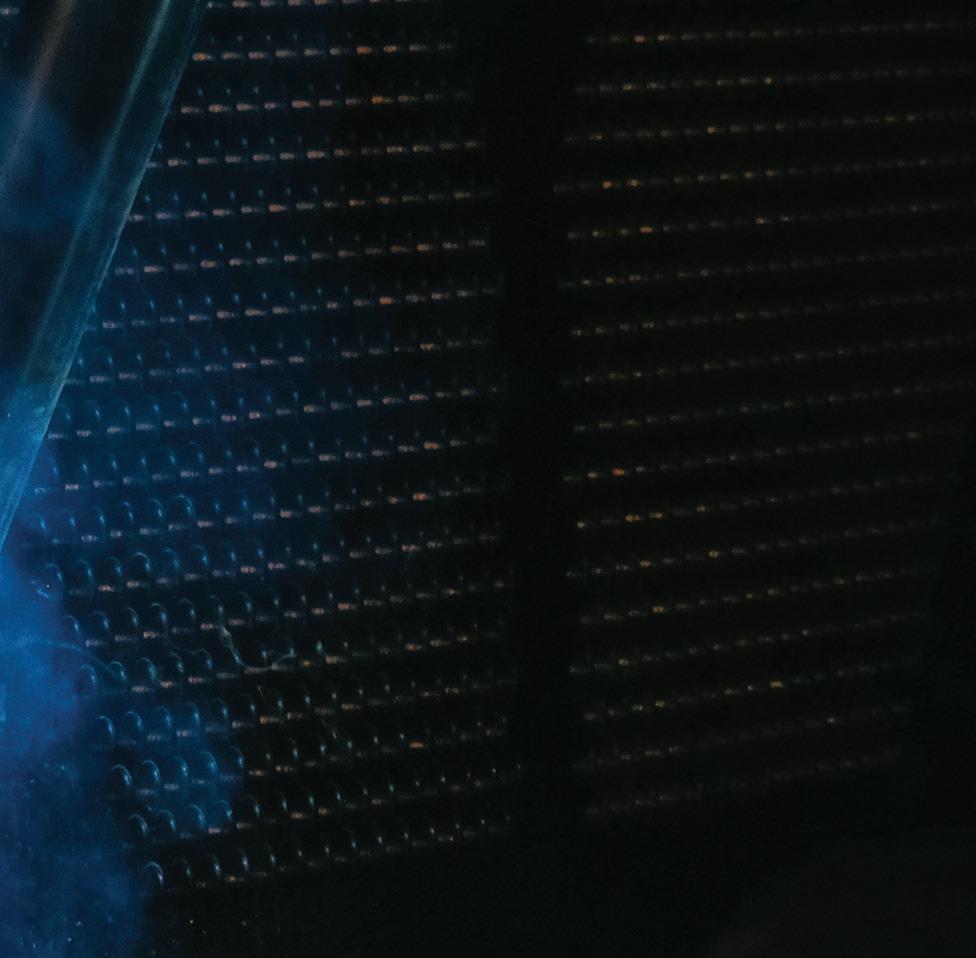

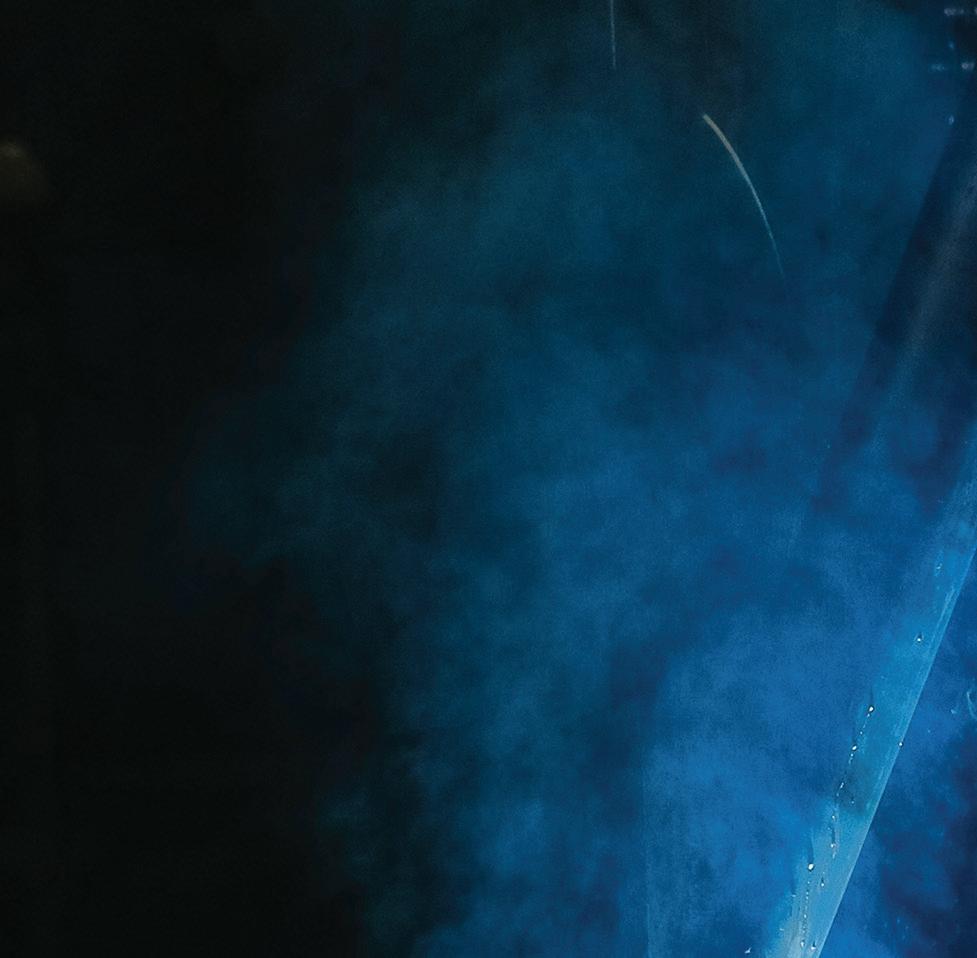
Welding pre-heat is commonly used before welding steel or steel alloy materials that are one-inch thick or more. Typically, thicker components require pre-heat, but it depends on the materials and assembly goals.
When do joints need to be pre-heated before welding?
Welding is a fabrication process that joins materials — typically metals or thermoplastics — by using high heat to melt the parts together and then allowing them to cool to cause fusion. Welding is distinct from lowertemperature, metal-joining techniques such as brazing and soldering, which do not melt the base metal.
Pre-heating components before welding can reduce the rate of cooling and result in stronger and more reliable welds. The process can involve heating the area around the weld joint or the entire part to a specifi ed temperature before welding.
When thicker components are preheated, it’s typically possible to achieve an ideal bond with less heat during the welding process. Thicker material means that more of it, including the surrounding material, will act as a heat sink when welded. This leads the weld to cool more rapidly after the energy source is removed.
Although thicker components (usually one inch or thicker) are more likely to require or benefi t from preheating, there are several criteria to consider beforehand.
To accurately assess if a welding assembly requires pre-heat fi rst consider the type and thickness of the base material. Although it’s di cult to provide simple rules for the material thickness at which pre-heating is ideal, there are rules-of-thumb and di erent

considerations for di erent materials.
For example, with alloys, the tensile and yield strength are signifi cant considerations. Tensile strength refers to the breaking point of an alloy and yield strength is the point at which stress or pressure causes an alloy to deform.
Typically, pre-heating is based on the welding code that’s used for the project. Welding codes are developed and available from several organizations and set the requirements for approved materials, design specifi cations, testing, inspection, as well as the welding itself.
The most commonly used codes are from the American Society of Mechanical Engineers (ASME | Section IX) and the American Welding Society (AWS | D1.1). The advantages The rapid heating and cooling of the base metal during routine welding can put heavy stresses into the parts, creating hard structures that are susceptible to hydrogen embrittlement.
Hydrogen embrittlement is a permanent loss of ductility in a metal or alloy caused by hydrogen in combination with stress. Pre-heating reduces the cooling rate of the weld and drives out moisture. A slower cooling process provides more time for hydrogen to defuse from the weld-a ected zone, which reduces the risk of cracking.
Additionally, slower cooling produces microstructures in the weld metal and the heat-a ected zone, which are more ductile and provide a greater resistance to cracking. Shrinkage stresses are also less likely to occur.
Residual hydrogen can become trapped at different sites within the metal, so the technique and weld temperature are important considerations that might require adjusting. Depending on the metals, welding with a longer contact-tip-towork distance can remove hydrogen from the weld area. A longer electrical tip can create greater preheating of the wire, burning off more hydrogen before the parts weld.
However, it’s critical to follow the recommended ranges for the material to be bonded. Careful monitoring of the base metal’s temperature between weld passes is important to ensure the material remains within the required range, regardless of the technique used.
Joint preparation is also critical because dirt, rust, debris, coatings, or oils can introduce hydrogen into the weld. Ensure the joint is clean and completely dry before welding.
Welding with restraint can generate additional residual stresses in the weld, which may cause cracking. With each assembly, be mindful of how the parts for joining are positioned and how the material reacts to welding.
When an ideal option, pre-heating can be achieved using di erent heat sources. For smaller components, a furnace or oven can be used, and this may provide the best process control.
For larger components, options include:
• Arrays of torches • Electrical resistance heaters • Induction heaters • Radiation heaters
Process control is extremely important when pre-heating, to ensure the material is heated to the correct temperature and that it remains within the required temperature tolerance throughout the welding process.
This involves three key process parameters:
1. Pre-heat temperature: the temperature of the surfaces to be joined before welding begins 2. Maximum interpass temperature: the maximum temperature at which subsequent weld runs are deposited, a ecting the microstructural development 3. Minimum interpass temperature: the minimum temperature at which subsequent weld runs are deposited, a ecting hydrogen cracking — typically, this is similar to the pre-heat temperature
The minimum interpass temperature might need to be maintained for a specifi ed period of time after the weld is deposited to ensure su cient hydrogen di usion. The temperatures can be monitored using temperature-indicating crayons, thermocouples, or contact thermometers.
Several welding pre-heating methods are available, so it’s important to understand the di erences and pros and cons of each in relation to your project. The aim should be to choose a method that optimizes e ciency and costs while producing high-quality welds in your application.