
PAGE 18
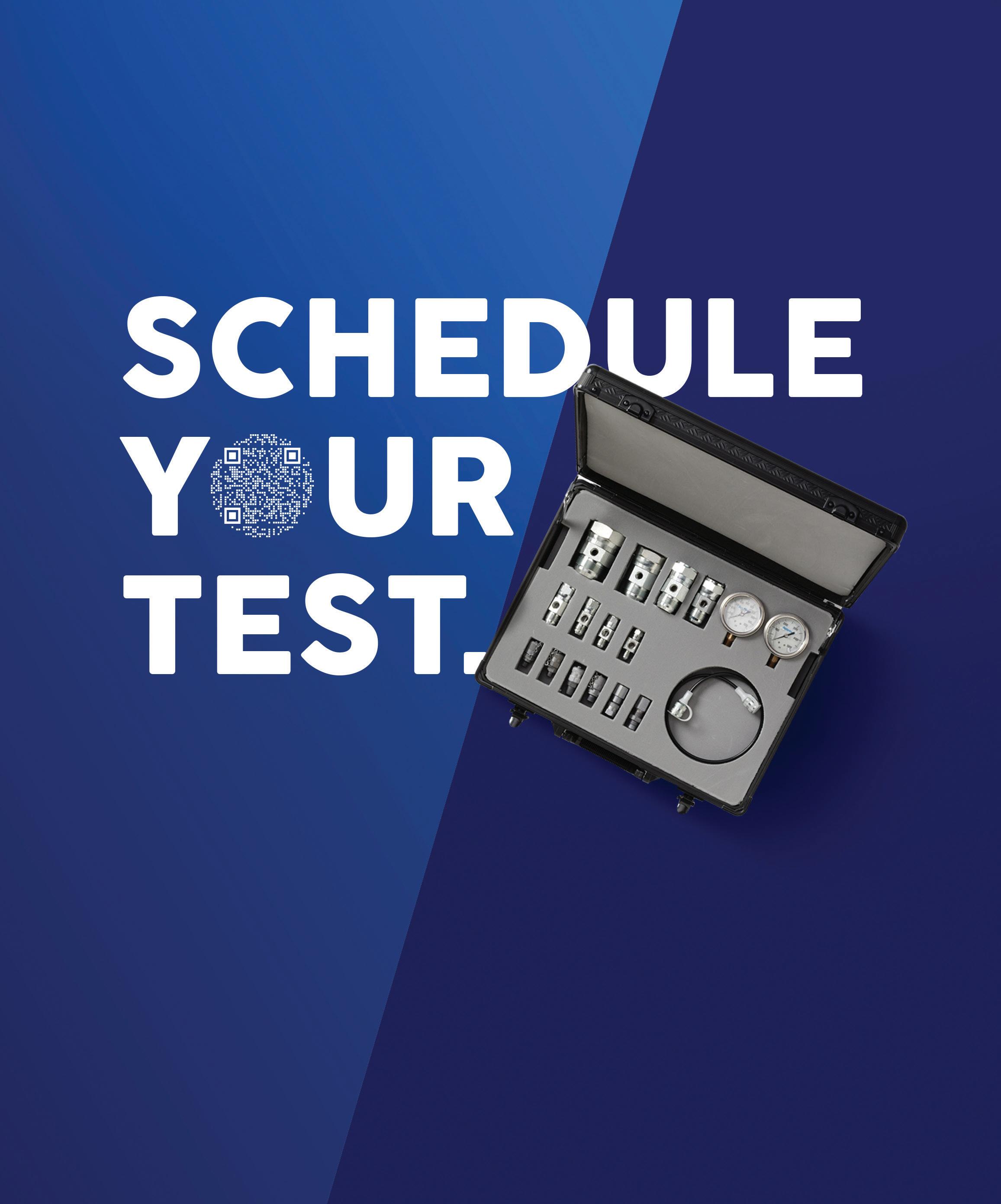
Mary C. Gannon • Editor-in-Chief
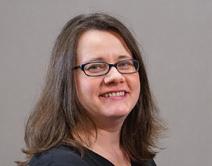
PAGE 18
Mary C. Gannon • Editor-in-Chief
from your Fluid Power World team! We are excited to launch these brand-new, digital-only magazine issues which will come to your inbox on the last Wednesday in March, May, July, September, and November.
We plan to grow these additions over the coming months, but know that you will see some new types of content and regular departments each issue. Our Design Notes section, penned by Rachael Pasini, will continue to be at the front of the magazine. Turn to page 6 to learn about a robotic jellyfish from Cornell featuring hydraulic fluid as well as a look at Teledyne FLIR’s hydraulic fault detection systems.
You will also see a slightly different layout than our traditional print magazine.
For example, we bring back our Association Watch department, and it moves to the back of the book. Please turn to page 24 to learn about the many technical opportunities supported by our industry associations. Get details about NFPA technical conference programming at three upcoming trade shows; about the Bath/ASME symposium on fluid power and motion control that is slated for August of this year in Anaheim, California; and learn how to nominate your favorite fluid power professional to the Fluid Power Hall of Fame, sponsored by the International Fluid Power Society.
This issue also features some regular departments like our Energy Efficiency department, page 8, where Ron Marshall continues to tackle compressed air concerns, as well as our Maintenance column, page 10, where Joe Jelinek of MCE Automation offers insight on critical spare management in the oil and gas industries.
Kicking off our features is our newest series, Profiles in Fluid Power, on page 12, with a look at an amazing woman of fluid power, Chauntelle Baughman of OneHydraulics. We also feature a deeper dive into automotive manufacturing on page 18, where Josh Cosford discusses the power and precision of cylinders used in these applications. You may notice a theme in that much of the content matches similar topics from our February and upcoming April issues as we continue to cover major industry events and markets regularly throughout Fluid Power World. For example, Josh’s article on automotive manufacturing is the second article covering this industry, as we had an excellent piece from Bosch Rexroth on hydraulic cushioning in automotive stamping presses in February. Additionally, our market focus on the oil and gas industry continues in our April edition, where we highlight several hydraulic manufacturers exhibiting at the Offshore Technology Conference show in Houston in May, as well as a look at
how Delta Motion controllers were used in unique cold press machines for marine vessel fittings.
Finally, I’m excited to announce that Josh Cosford will be penning the Perspectives column in these digital editions. As a reader favorite, Josh educates us on so much fluid power technology with his own unique and clever writing style. Check out his first column on page 4 where he asked the question — what if efficiency really didn’t matter anymore?
Thank you as always for subscribing and reading. Please do reach out to let us know how we’re doing and what additional content you’d like to see coming your way throughout the rest of this year. FPW
Mary C. Gannon • Editor-in-Chief mgannon@wtwhmedia.com linkedin.com/in/marygannonramsak
Chauntelle Baughman steers
OneHydraulics to success
Learn how Chauntelle Baughman has created one of Texas' fastest-growing distributors. 18
The power behind automotive manufacturing
Hydraulic — and even pneumatic — cylinders are used massively throughout auto manufacturing, providing the power, precision and
EDITORIAL
VP, Editorial Director
Paul J. Heney pheney@wtwhmedia.com @wtwh_paulheney
Editor-in-Chief Mary Gannon mgannon@wtwhmedia.com @dw_marygannon
Technology Editor Ken Korane kkorane@wtwhmedia.com @fpw_kenkorane
Senior Editor Rachael Pasini rpasini@wtwhmedia.com
Associate Editor Heather Hall hhall@wtwhmedia.com @wtwh_heathhall
Contributing Editor Josh Cosford @FluidPowerTips
Contributing Editor Carl Dyke @carlindustry
Contributing Writer Robert Sheaf rjsheaf@cfc-solar.com
www.nfpa.com
PRODUCTION
VP, Creative Services Matthew Claney mclaney@wtwhmedia.com @wtwh_designer
Art Director, FPW Erica Naftolowitz enaftolowitz@wtwhmedia.com
Art Director, FPW Digital Eric Summers esummers@wtwhmedia.com
Director, Audience Growth Rick Ellis rellis@wtwhmedia.com
Audience Growth Manager Angela Tanner atanner@wtwhmedia.com
Customer Service Manager Stephanie Hulett shulett@wtwhmedia.com
Customer Service Representative Tracy Powers tpowers@wtwhmedia.com
Customer Service Representative JoAnn Martin jmartin@wtwhmedia.com
Customer Service Representative Renee Massey-Linston renee@wtwhmedia.com
Customer Service Representative Trinidy Longgood tlonggood@wtwhmedia.com
WTWH
FLUID POWER WORLD does not pass judgment on subjects of controversy nor enter into dispute with or between any individuals or organizations. FLUID POWER WORLD is also an independent forum for the expression of opinions relevant to industry issues. Letters to the editor and by-lined articles express the views of the author and not necessarily of the publisher or the publication. Every effort is made to provide accurate information; however, publisher assumes no responsibility for accuracy of submitted advertising and editorial information. Non-commissioned articles and news releases cannot be acknowledged. Unsolicited materials cannot be returned nor will this organization assume responsibility for their care.
FLUID POWER WORLD does not endorse any products, programs or services of advertisers or editorial contributors. Copyright© 2025 by WTWH Media, LLC. No part of this publication may be reproduced in any form or by any means, electronic or mechanical, or by recording, or by any information storage or retrieval system, without written permission from the publisher.
VP, Operations Virginia Goulding vgoulding@wtwhmedia.com @wtwh_virginia
Digital Marketing Manager Taylor Meade tmeade@wtwhmedia.com @wtwh_taylor
SALES
Ryan Ashdown 216-316-6691 rashdown@wtwhmedia.com
Jami Brownlee 224.760.1055 jbrownlee@wtwhmedia.com
Mary Ann Cooke
781.710.4659 mcooke@wtwhmedia.com
Jim Powers 312.925.7793 jpowers@wtwhmedia.com @jpowers_media
Courtney Nagle 440.523.1685 cseel@wtwhmedia.com @wtwh_CSeel
CEO Matt Logan mlogan@wtwhmedia.com
Co-Founders Scott McCafferty Mike Emich
SUBSCRIPTION RATES: Free and controlled circulation to qualified subscribers. Nonqualified persons may subscribe at the following rates: U.S. and possessions: 1 year: $125; 2 years: $200; 3 years: $275; Canadian and foreign, 1 year: $195; only US funds are accepted. Single copies $15 each. Subscriptions are prepaid, and check or money orders only.
SUBSCRIBER SERVICES: To order a subscription please visit our web site at www.fluidpowerworld.com
FLUID POWER WORLD (ISSN 2375-3641) is published six times a year: in February, April, June, August, October, and December by WTWH Media, LLC; 1111 Superior Ave., Suite 2600, Cleveland, Ohio 44114. Periodicals postage paid at Cleveland, OH & additional mailing offices.
POSTMASTER: Send address changes to: Fluid Power World, 1111 Superior Ave., Suite 2600, Cleveland, OH 44114
Josh Cosford • Contributing Editor
I JUST ROLLED OVER 50 YEARS on the speedometer of life this week, and without a doubt, this exact time in history is the craziest I’ve been a part of, and I even include the pandemic. At least during the initial stages of lockdowns and nose swabs, the world was united against a singular foe. But the recent tidal forces are swapping between spring and neap on a level not seen since this Canadian has been walking this green Earth. I mention my nationality to declare I have no skin in the American political game, except perhaps some potential tariffs on the goods my company manufactures.
Blue or red, elephants or donkeys, your alignment matters little for the next few years because we still have to carry on and Git-RDone. With the policy changes diverting the focus from green energy, the situation has me wondering what a fluid power world would look like where efficiency no longer mattered. I don’t necessarily mean throwing away piston pumps entirely, but that could happen as well. I’m thinking, what if an abundance of energy were combined with apathy towards climate change … what would our industry look like?
First of all, you can forget about emissions controls on internal combustion-motivated machinery, both on-highway and off. We would ditch some or all of the Tier 4 Final equipment, such as sophisticated electronics and Selective Catalytic Reduction, which add cost and complexity. I don’t think we’d want to go back to machinery spewing smoke like diesel drag strip trucks, but the industry would focus on profits
In many cases, a piston pump might still provide the best option, especially in applications where total machine redesign is not possible, such as a 6,000 psi dozer.
and productivity. Manufacturers had to spend so much time splitting hairs over efficiency and weight to downside power units, so I’d expect machines to once again grow in size.
For that matter, if a technology doesn’t improve performance or reduce machine cost, it’s going to be swapped out for something simpler and cheaper. If a piston pump costing twenty large can be swapped for something that costs only a few Benjamin Franklins, then what’s the harm in making it a hair larger in displacement to accommodate for the reduced efficiency?
In many cases, a piston pump might still provide the best option, especially in applications where total machine redesign is not possible, such as a 6,000 psi dozer. Such a case would require so many changes to beef up the machine to handle actuators twice the size, but machines (mobile or otherwise) running advanced technology like asynchronous motordriven pumps with servo-controlled pressure
IF EFFICIENCY NO LONGER MATTERED, THERE STILL WOULD BE NO POINT IN GOING BACK TO PRE-TIER 4 MACHINES, AS THE TIME AND INVESTMENT TO GET US HERE TODAY WAS TOO VAST TO WRITE OFF AS A
and displacement control would go down like sophisticated dinosaurs.
In many ways, industrial hydraulics have been more sophisticated than the bulk of mobile machines, so I wouldn’t expect 500ton injection molding machines to ditch their servovalves. However, you bet that me, you and all the injection molding machine manufacturers are collectively irate over the exponentially increasing price of electric motors. It’s like 2010 came in like, “Oh sure, you can have this 89% efficient motor over here for $199, but that 91% efficient motor is on sale for $FirstBorn, so don’t sleep on it.”
The reality is that we won’t be taking many big steps back over the next four years since the time and investment to get us here today was too vast to write off as a sunk cost. If anything, we’re just moonwalking backwards but in the same direction. So regardless of unknowns as we move towards 2030, always remember that sneakers of progress keep moonwalking. FPW
Darrell Taylor • Director of Global Acoustics Business Development, Teledyne FLIR
WE LIVE IN A SOCIETY that wants things quicker, builds bigger, and travels faster. The machines that put this world together work longer and harder than ever. At the core of these machines, one type of power transfer is commonplace — namely, hydraulic systems, with pumps serving as the heart. Although they vary in type and size, hydraulic pumps are vital components, moving fluid around the system and enabling rams to move within the cylinders.
The most common units used in industrial applications are piston pumps or vane pumps. Both types are very susceptible to debris and impurities. In the case of a piston pump, a small hole allows lubrication of the piston shoe as it rotates around the swash plate. If the hole gets blocked, the shoes quickly wear, and a tell-tale sign is the heat generation as friction increases. Vane pumps are equally susceptible to deposits as the individual vanes fail to move freely within the barrel, increasing friction and associated heat. Pump failure can result relatively quickly when oil starvation occurs, causing the whole system to fail. For this reason, changes in pump temperature must be taken seriously
and acted upon as soon as they are identified.
Most maintenance engineers struggle to detect when a pump is running abnormally hot. Many hydraulic pumps are in difficult-to-access areas and are, therefore, not regularly checked. In most pump failures, problems manifest only when the whole system goes down, bringing production to a standstill until a replacement pump is identified and fitted.
This is where thermal imaging becomes useful. FLIR is a global company that researches and produces thermal imaging cameras. Its latest Exx-Series cameras can detect heat abnormalities in components, such as hydraulic pumps, from several meters away (or tens of meters away with the right lens). Those hardto-reach areas can be analyzed, allowing remedial action to be taken, thus avoiding costly pump failure and the associated production downtime.
Whether it’s hydraulic pumps, industrial gearboxes, compressors, turbines, or other units that can emit heat during abnormalities, thermal imaging cameras can be invaluable analytical tools. Through regular analysis,
a temperature profile is obtained such that any temperature rise indicates wear problems and maintenance needs. Some cameras in the ExxSeries allow for interchangeable lenses, bringing into focus those more distant components.
The instruments are supported by FLIR-patented MSX (Multi-Spectral Dynamic Imaging) enhancement. The cameras provide the ability to organize images and add detailed notes directly from the large touchscreen incorporated into the camera. Images can then be directly uploaded to the FLIR Ignite cloud storage space, providing easy access from any device.
Less experienced operators can make the most of the thermal imaging cameras by following a prescribed inspection route preloaded into the camera’s onboard software, FLIR Inspection Route. This allows engineers with less experience to conduct a large survey in a logical sequence, providing management with a detailed report of the manufacturing process. FPW
Teledyne FLIR flir.com
Rachael
Pasini • Senior Editor
ROB SHEPHERD , professor of mechanical engineering at Cornell University, wants to make agile robots that can operate untethered for longer — and he’s using hydraulic fluid to do it.
“Hydraulic fluids are a great way to get high power output from robots, but people prefer to use batteries powering dc motors,” he said. “I started making the hydraulic fluid also a battery. That led us to making a fish that swims underwater hydraulically, where you hydraulically actuate a soft member, which bends, and then that hydraulic fluid powers the pump that’s causing the hydraulic fluid to move. We called it robot blood.”
If you’ve ever seen the first Alien movie where the traitor android named Ash gets decapitated and a milky-white liquid pours out of its body, then you know the inspiration behind Shepherd’s robot blood.
“But this fish we made, it wasn’t designed well. It weighed a lot and didn’t have that much hydraulic fluid,” he said. “What I like to talk about is the system’s energy density — how much energy per gram is in the robot — and I want to get up to 90% of the weight of the robot as energy storage. That brings us to the jellyfish because the jellyfish is mostly water, so we could make the weight of the robot be mostly battery and hydraulic fluid.”
Batteries are heavy. Therefore, designing multi-purpose components can make solutions more lightweight.
“It can change some people’s perspective on when a hydraulically actuated machine is a better choice because now the weight is also providing the electrical power to the system,” said Shepherd.
Hydraulic fluid actuates the jellyfish like a balloon that inflates and changes shape, and a gear pump and motor pull a wire that moves the fluid.
His team also made a worm with five segments or pods, each actuated by a motor and a tendon. The motor and tendon compress the pod, and an incompressible fluid, acting as a hydrostatic skeleton, provides stiffness to the pod proportional to the compression. This motion creates an undulating effect and, along with Shepherd’s battery system, allows the worm to travel untethered longer than many other worm-like crawlers. This is useful for pipe inspection applications with complex networks.
As for the jellyfish, the design is a stepping stone along the pathway toward building something bigger. The current design can hold four liters of hydraulic fluid. The more hydraulic fluid that’s used, the more energy it transmits. So, the bigger the team designs the jellyfish, the more sense it makes.
“That jellyfish is what’s called a Lagrangian drifter, and it has basically the same density as the ocean. So when there’s a current, it can follow that current and monitor the health of the ocean, and then it can choose to come up out of the current, transmit its data, and then go back down into the current,” said Shepherd.
SHEPHERD’S JELLYFISH ROBOT USES A LIQUID ELECTROLYTE FROM A REDOX FLOW BATTERY AS BOTH A HYDRAULIC FLUID AND ELECTRICAL ENERGY STORAGE.
His team is also designing a larger fish, approximately three meters long with 30 liters of hydraulic fluid. This design has an efficient swimming motion that should be able to swim for weeks at a time, where the ocean recharges the battery.
“We’re going to orient it vertically, and then have the waves pump the liquid through a turbine inside of it and recharge the battery. That is going to take weeks to recharge, but what’s it doing anyway? May as well sit there and recharge,” he said.
For now, this jellyfish robot’s primary purpose and application is carbon dioxide (CO2) sequestration and monitoring in the ocean.
“There's a huge effort to sequester CO2 at the bottom of the ocean, but it’s kind of catastrophic if you put it all down into one place and then it all comes out at once,” said Shepherd. “So, being able to persistently monitor all those CO2 sinks is what we’re trying to build it for. It can patrol the different areas in perpetuity and make sure there's no CO2 leakage.” FPW
Cornell Engineering engineering.cornell.edu
Ron Marshall • Contributing Editor
DURING A WALK-THROUGH AUDIT, a compressed air auditor noticed a pail collecting lubricant from a filter drain. The pail was almost completely full, causing the auditor some concern. He knew that this was a sign of several possible problems.
High oil or lubricant accumulation downstream of a lubricated screw compressor is often caused by issues with the oil separator, operating conditions, or maintenance practices. One of the most common reasons is a failed or saturated oil separator element, which allows excess oil to pass through instead of being properly removed. Using an incorrect or poorquality separator can also reduce efficiency, leading to higher oil carryover. Additionally, high air velocity caused by running the compressor above its rated capacity can overwhelm the separator, allowing more lubricant to escape into the system.
Maintaining the correct oil level in the compressor is crucial, as overfilling the reservoir forces excess oil into the air stream. A faulty or improperly set minimum pressure valve can also contribute by failing to maintain proper separator tank pressure. Another factor is oil degradation (or the use of incorrect lubricants), which can cause foaming and reduced separation efficiency, increasing oil carryover.
“Maintaining the correct oil level in the compressor is crucial, as overfilling the reservoir forces excess oil into the air stream. A faulty or improperly set minimum pressure valve can also contribute by failing to maintain proper separator tank pressure.”
Worn seals, gaskets, or internal baffles in the separator tank may also allow oil to bypass the separator. If coalescing filters are clogged or faulty, they may fail to capture oil mist, allowing accumulation in downstream components. Frequent start-stop operation disrupts stable separation conditions, leading to slugging and higher oil contamination.
Regular inspections, oil changes, and proper maintenance of the compressor, separators, and filters are essential to minimizing oil accumulation and ensuring clean, efficient compressed air delivery.
Investigation of this customer revealed that the lubricant was coming from a lightly loaded variable speed drive compressor running below minimum speed, a point at which the internal separator is less efficient at removing oil. Adjustment of the operating parameters in this multi-compressor system allowed this compressor to turn off when not required, reducing the lubricant carryover problem. FPW
OIL RIGS AND FRACKING OPERATIONS FACE EXTREME AND UNFORGIVING CONDITIONS, INCLUDING EXTREME RAIN, SNOW, AND TEMPERATURE SWINGS. TO AVOID COSTLY EQUIPMENT FAILURES, ENSURE YOU HAVE CRITICAL SPARES ON HAND.
PREMATURE FAILURE of your equipment’s hydraulic system poses significant risks to the oil and gas industry — including unplanned downtime, costly repairs, environmental hazards, and compromised worker safety. Avoid costly downtime with prevention tips and guidance on managing critical spares.
Oil rigs and fracking operations face extreme and unforgiving conditions, including extreme rain, snow, and temperature swings. These harsh environments often lead to equipment failures — an unwelcome and costly consequence of prolonged exposure to corrosive elements. Additional challenges commonly encountered in fracking and wellhead operations include:
• Saltwater
• Sand
• Wind
• Hazardous gases
• Toxic chemicals
• Changing geological formations
• High-pressure environments deep underground
In some regions, temperature fluctuations from –50° to 100°F further exacerbate stress on equipment. These conditions not only increase the likelihood of emergency repairs but also complicate maintenance by requiring hard-tofind replacement parts, escalating costs and downtime events.
To combat these challenges, timely replacement of critical fluid power components — such as hoses, fittings, and filtration systems — is essential.
Effective asset management isn’t just an operational necessity; it’s a cornerstone of maintaining efficiency and reducing long-term costs.
The total annual direct cost of corrosion in the U.S. oil and gas production industry is estimated at $1.4 billion. 1
One common reason for equipment breakdown is corrosion. The process starts when reactive elements come into contact with the
internal parts of the hydraulic hose or the metal components. Signs of early corrosion include:
• Rust
• Leaks
• Dullness
• Scaling
• Pitting in material
• Reduced performance
• Damage to inner structure or outer surface coating
When oil and gas operations are interrupted due to equipment failure from corrosion or wear and tear, any delays in sourcing spare parts needed for proper repair can have severe financial impacts. Financial impacts such as these compound over time, with no relief in sight.
For perspective, the hourly cost of unplanned downtime in the oil and gas sector rose by 50% in 2021 compared to 2019. Reasons for the increase included inflation, rising cost of manufactured and processed goods, higher sales prices, increased demand for business digitization, and Industry 4.0 strategies.2
The cost of unplanned downtime impacts direct costs (loss of production and revenue) but also reflects the following indirect costs:
• Compromised project timelines and penalties
• Cost of wages and paying employees who can’t work
• Cost of wages for those repairing equipment
• Cost of emergency repairs
• Potential legal fees
You can prevent unplanned downtime from asset corrosion and wear and tear by adopting a monitoring program that evaluates equipment conditions and implements maintenance practices. Follow these three tips to prevent wear:
1. Select quality products made from appropriate materials and coatings. Choosing quality hydraulic hose components from the
INSPECTING CRITICAL COMPONENTS REGULARLY, SUCH AS HOSE FOR WEAR AND ABRASION AND KEY COMPONENTS LIKE VALVES FOR RUST, REDUCES THE RISK OF DAMAGE, DOWNTIME AND COSTLY REPAIRS.
same product line and manufacturer ensures each component works seamlessly. Mixing and matching assembly components from different lines compromises the reliability at each connection point. These components should be designed with the proper materials and coatings to handle high pressures, extreme temperatures, and abrasive environments common in oil and gas. They should also follow Mine Safety and Health (MSHA) guidelines for maximum safety and reliability.
2. Implement a regular visual inspection program of hydraulic components. Regular inspection of your hydraulic systems is key to avoiding unexpected failure. By implementing a visual inspection program, you can spot early signs of wear, rust, or contamination that may cause corrosion. Look for other signs of component failure due to factors such as hose abrasion (exposed wire reinforcement that can lead to corrosion and failure), kinked hoses or tubes, punctured hoses with pinhole leaks, or leaking fittings due to over-tightening or damaged O-rings. In addition to examining components for wear, check hydraulic fluids for signs of degradation. Don’t forget to inspect filtration systems. Failure to do so can shorten equipment life, increase downtime events, and add to the cost of repairs.
3. Have critical spares and inventory on hand for rapid repair. Having equipment offline is costly. Access to frequently used or essential components allows for quick repairs, minimizes downtime, prevents production disruptions, and reduces costs associated with emergency purchase orders. When managing critical spares, it’s essential to have data on what components are most likely to fail and require backup stock. Consider lead times and procurement costs when developing an inventory management plan on these items.
Partnering with a hydraulic assembly expert streamlines your purchasing activity, provides in-depth knowledge of your industry needs, and ensures your hydraulic system operates at peak capacity and reliability. By embracing effective inventory management techniques, you can experience:
Simplified purchasing with effective supply chain management (min/max, replenishment triggers, reporting).
Cost savings through product consolidation, labor mitigation, reduced carrying costs, and fewer purchase orders.
Reduced stockouts and overages with easy-to-use dashboards and adequate product storage.
Better data visibility on product usage, business metrics, reviews, and diagnostics. Look for inventory management options that will benefit your operation, such as:
• Vendor-managed inventory An effective asset management plan means you always have the critical spares and inventory needed for rapid repair. When you enroll in a vendor-managed inventory (VMI) program with a trusted supplier, they’ll help you set dynamic inventory levels, replenishment triggers, and reporting mechanisms to identify trends in usage.
• Customer-managed inventory — If a business prefers to manage inventory internally, some suppliers offer customer-managed inventory (CMI) programs. CMI allows you to direct product replenishment as you see fit and shifts the responsibility of tracking inventory levels, placing orders, and managing supplier relationships to the company. This inventory model is ideal for customers requiring specific product configurations, high customization levels, or those needing inventory management solutions for remote or restricted locations.
• Proactive stocking agreements — In addition to offering VMI or CMI, some suppliers can assist oil and gas companies with proactive stocking agreements. A proactive stocking agreement is a contract between a company and its supplier. Based on usage trends, the supplier agrees to house mission-critical inventory in their warehouse to eliminate the risk of stockouts. This option can allow for prompt procurement while alleviating any space constraints for housing missioncritical inventory.
Partnering with a supplier that knows your industry and collaborates with your organization to ensure critical spares are always on hand is the best way to better critical spares management and reduced downtime. FPW
CHAUNTELLE BAUGHMAN IS THE FACE OF ONEHYDRAULICS, PROMOTING HER WOMANOWNED BUSINESS REGULARLY.
By: Mary C. Gannon, Editor-in-Chief
Learn how Chauntelle Baughman has created one of Texas' fastest-growing distributors.
If you work within the fluid power industry, chances are, you know Chauntelle Baughman, CFPHS, or have at least seen some of her popular social media posts. Baughman is the president, CEO and cofounder of OneHydraulics, a woman-owned distributor and integrator serving the greater Houston area.
She stepped into fluid power right out of college, having graduated from Texas A&M in 2006 with a degree in Industrial Distribution.
“In my Senior year at Texas A&M University, I found myself at a crossroads, with job offers spanning several diverse industries. Unsure of my career path, I turned to my dad for advice. He suggested I embrace the challenge, reassuring me I could always switch gears if I needed to. Intrigued by the unknown, I ventured into fluid power engineering — a realm completely new to me,” Baughman said. “Despite my initial uncertainty, I quickly became enamored with the field’s dynamism, where every day presents a new challenge, and my career was always far from boring. The industry has stuck with me ever since.”
Her employer placed a high value on IFPS certifications, which she still carries with her to this day. Being a CFPHS was a requirement for sales there, so she attained her certification within a few months of that first job, which launched her career into fluid power sales. Baughman truly believes in the value and importance of the IFPS and its certification program. So much so that she became heavily involved in the organization.
“Being a young female in a predominantly male industry could be intimidating. However, the esteemed reputation of the IFPS within the fluid power community provided me with a tangible credential and a testament to my capabilities, boosting my confidence and gaining the respect from my peers in the fluid power industry as technically competent and capable,” she said. “Motivated by the desire to contribute a unique perspective as a young female professional in fluid power, I became active with the IFPS. Serving as a member of the IFPS Board of Directors and most recently as the VP Marketing Chair, I have had the opportunity to actively shape the direction of the organization and help steer us into a very exciting future. IFPS plays a pivotal role in shaping the workforce of tomorrow through education and certification, and I’m so excited and grateful to be a part of creating that.”
Baughman is probably one of the most prominent woman-owned fluid power businesses out there. She is known for her unique social media posts, particularly on LinkedIn, where she is featured in every post — highlighting the work her team does in providing quality fluid power sales, service and design.
Because OneHydraulics is still a small and new company, she carries a diverse array of responsibilities. “As a relatively young and agile company, I have the privilege of assuming many roles, spanning from human resources to quality management, from marketing to finance,” she said. “Since our establishment in 2016, our journey has been marked by remarkable growth, albeit accompanied by significant
challenges inherent to scaling operations.
“The most exhilarating facet of my position lies in confronting these challenges head-on, devising innovating solutions, and fostering an environment where my team feels empowered to overcome obstacles and exceed customer expectations,” Baughman continued. “I derive immense satisfaction from the creative process involved in problem-solving and from recognizing and nurturing the talents of my incredibly gifted and hardworking team. Managing a team of such talented and intelligent individuals adds an extra dimension to my role. Their collective dedication and constant willingness to question the status quo are pivotal in driving our company’s success.
“While aspects of my job like financial management, human resources, and quality control may not always evoke the same level of excitement, I recognize their indispensable role in laying the foundation for our future and sustaining the steady
growth trajectory that has characterized our journey thus far,” she concluded.
She co-founded the company in 2016 with Brett Holmes, VP of sales and cofounder, who she had worked with at HydraQuip. Baughman attributes her husband, Mark, who is VP of Finance for OneHydraulics, with giving her the nudge to embark on business ownership.
“He has always believed in me, sometimes more than I believed in myself. I had spent 10 years working in fluid power sales, and during that time, I had the privilege of working alongside some incredibly talented people and gaining invaluable industry experience. When I made the decision to move on, I saw it as an opportunity to build something new — something that reflected the kind of company I wanted to be a part of.
“The transition from sales to ownership was both exhilarating and terrifying,” Baughman said. “I left a stable job and stepped into the unknown, but I was
"Our leadership sets the tone by fostering an environment where everyone feels valued and respected, and everyone has an opportunity to be heard."
driven by a clear vision: to create a business focused on technical expertise, exceptional customer service, and a strong company culture. Looking back, it was one of the most challenging but rewarding decisions I’ve ever made.”
Baughman attributes her success to her unique, quirky, customer-centric viewpoint. “Just because fluid power is technical, I don’t believe it has to be boring! I envisioned creating a brand and workplace that aligned with my values and aspi-
rations, a place where I would genuinely enjoy working,” she said.
“What truly drives me is the ability to enact positive change and shape the future of fluid power. Having the autonomy to implement my vision and build something that resonates with my ideals is incredibly fulfilling. Running OneHydraulics allows me to channel my passion for innovation and customer delight into tangible outcomes, creating the kind of fluid power future I envision for our industry.”
Although there are challenges to working in the fluid power industry, Baughman said that one of the most fulfilling aspects of working in the industry is its sense of community — it’s like a big family, she noted.
“I love that I can go to a trade show or an industry meeting and see so many familiar faces from various points in my career and pick up right where our friendships left off. Despite how large the industry really is,
there really is a sense of interconnectedness where people can easily build relationships that last a lifetime,” she said.
She did note that with this closeness comes a challenge: the impending retirement of many seasoned experts. “These individuals hold a wealth of knowledge, gained through years of experience. As they prepare to step back, there’s a pressing need to ensure their wisdom isn’t lost. Finding and nurturing the next generation of talent is key to overcoming this great challenge and keeping the industry thriving,” Baughman added.
To combat this, she agrees that increasing the participation of women and younger individuals in the fluid power industry is crucial, but hinges on proactive outreach and engagement efforts across the industry. “Fluid power is a hidden gem – everyone who touches it, considers it as the focus of their career. I have personally taken up mentoring to shine a light on our industry, and I love connecting with univer-
sity professors to show students the exciting opportunities in fluid power,” she said. “I’m a huge supporter of STEM education, and I love to see events like the NFPA’s Fluid Power Action Challenge. It’s all about spreading the word and showing people how cool our industry is! Through our efforts together, we can ensure a vibrant and diverse talent pipeline for the future.”
“Looking ahead, I see even greater opportunities for major innovation in the near future. AI will play a pivotal role in optimizing system efficiencies and enabling predictive maintenance, allowing us to anticipate and prevent failures before they occur."
Baughman takes these programs to heart and is active in supporting future fluid power professionals through OneHydraulics and industry involvement.
“At our company, inclusivity and support are ingrained in our culture. We prioritize equal opportunities, ensuring fair treatment and advancement prospects for all employees regardless of gender, ethnicity, or background. Our leadership sets the tone by fostering an environment where everyone feels valued and respected, and everyone has an opportunity to be heard,” she said. “We actively promote professional development and mentorship opportunities, as well as host regular trainings with our seasoned industry veterans to foster talent and help people grow in their careers. We really do believe that the more you know, the more you grow.”
Baughman recently began mentoring students from the engineering school through her involvement with the Soci-
ety of Women in Industrial Distribution at Texas A&M University. She said that as an alumna, stepping into the role of mentor was initially a bit surreal, but immensely rewarding. “I vividly recall the uncertainty and excitement of navigating the professional world, and it’s fulfilling to share my experiences and insights with those just beginning their careers,” she said. “In my mentoring sessions, I focus on practical guidance such as resume tips, interview preparation, and insights as to what employers value in their employees. These conversations center around empowering mentees to present themselves confidently and make a positive impression in interviews. By sharing my own journey and lessons learned, I hope to support and inspire the next generation of engineers as they embark on their career paths.”
Every career has challenges, and Baughman noted that her biggest was clearly in starting her own business from scratch.
“Beginning at a kitchen table with literally a blank sheet of paper and a dream was a formidable task. Every aspect of the business, from vendor partnerships to customer relationships, had to be crafted and built from the ground up,” she said. “Despite possessing a strong technical background in fluid power sales, I realized quickly that success would hinge on a lot more than just technical expertise.
“To overcome this challenge, I immersed myself in learning. I’ve always been a bit of a bookworm, so I began to voraciously read every business book I could get my hands on — management, quality, human resources, accounting, web design, entrepreneurship, marketing, even biographies of company founders I admire,” she said.
“This commitment to continuous learning enabled me to expand my skill set and knowledge base, equipping me with the tools and insights I’d need to navigate the complexities of business ownership.”
Baughman said that one of the most valuable lessons from engineering she learned as a student is the skill of independent problem solving. Engineers learn
to navigate unfamiliar territory by drawing upon fundamental principles and applying creating thinking to find solutions. “This ability proved crucial when we started OneHydraulics, as I ventured into new disciplines such as human resources and accounting,” she said. “Despite lacking prior experience, I was able to approach these concepts with confidence, leveraging my engineering mindset to learn quickly and adapt to the demands of running a quickly growing business.”
As Baughman edges up on a decade of business ownership, she recognized that the fluid power industry is changing. “We’re truly in the midst of a transformative era, where technology is revolutionizing fluid power systems, and we’re only just scratching the surface of its potential,” she said. “The increased utilization of sensors, advanced materials, and simulation and modeling software has led to remarkable improvements in system efficiency and reliability.
“Looking ahead, I see even greater opportunities for major innovation in the near future. AI will play a pivotal role in optimizing system efficiencies and enabling predictive maintenance, allowing us to anticipate and prevent failures before they occur. Additive manufacturing (3D printing) will revolutionize the production of fluid power components, enabling manufacturers to develop lighter, more efficient designs with enhanced performance characteristics,” she concluded. “Overall, I envision a future where fluid power systems are not only more efficient and reliable, but also more intelligent and adaptable. It’s a future that I really can’t wait to see.”
Connect with Chauntelle Baughman on LinkedIn and visit onehydraulics.com for more information. FPW
Hydraulic — and even pneumatic — cylinders are used massively throughout auto manufacturing, providing the power, precision and durability needed.
By Josh Cosford, Contributing Editor
If you’re (un)lucky enough to sell and service hydraulics in the automotive manufacturing industry, you understand life in the belly of the beast. The automotive manufacturing industry is not for the faint of heart. Over 3% of North American GDP is related to vehicle production, which equates to nearly a trillion dollars of production.
However, with so much money on the line, the auto manufacturing industry is wildly competitive, unforgiving, and highly demanding at every stage of the process. Manufacturers obsess over the smallest margin improvements, which stem from continuous improvement, tight bookkeeping and operational efficiency. As well, the numerous suppliers they count on to supply parts such as drivetrain, interior components, and electronics are expected to help manufacturers remain profitable and competitive.
FIGURE 1. HYDRAULIC PRESSES ARE USED PREDOMINANTLY IN AUTO MANUFACTURING, RELYING ON THE POWER AND STRENGTH OF HYDRAULICS FOR CHASSIS MANUFACTURING.
You might be surprised to know that auto manufacturers make very little of what they sell and, by and large, are engineering, marketing and assembly outfits. There are generally three tiers to the automotive supply chain. Tier 1 suppliers sell their components directly to the manufacturer, such as Bosch, Linamar and ZF, to name a few. Tier 2 suppliers will manufacture sub-components to the Tier 1 suppliers, such as a gear for a transmission or frame rail for a seat. Finally, Tier 3 suppliers will provide raw materials ranging from billets of metal to plastic pellets to all levels of the pyramid.
Regardless of who makes what, fluid power plays a major role in the manufacture of passenger vehicles, especially so with cylinders. Nearly every type of material and machine is used at one stage or another of the vehicle manufacturing process. It might help to discuss a few vehi-
cle components and the types of applications and cylinders used to make each part. Although there are 30,000 individual parts of a car, let’s look at a few major families to cover the majority of applications: steel chassis components, plastic panels and drivetrain parts.
What first comes to mind when you think about what constitutes a car is that good old steel likely takes the top spot. Steel and iron make up 65% of a car’s mass, and its strength and shape are what keep you safe in an unfortunate accident. Manufacturing chassis components as large as frames, subframes and cross members require equally large machinery.
Using thousands of tons of force, the hydraulic press, Figure 1, is a mainstay in chassis component manufacturing. Using large dies installed on the bed (lower portion) and slide (upper portion), sheet metal is placed into the press before the massive cylinders extend to push the dies together, forming the metal as easily as Play-Doh.
Even high-strength steel is no match for the compressive strength of these presses, which are so large that they may stand a few stories tall.
Depending on the size and strength of the press, it will typically have two or four cylinders. These cylinders will have large bores, but strokes may vary widely. You will rarely see any standard, such as NFPA, used as the primary press cylinders in these applications. Almost entirely custom and with bores up to 20 in. in diameter or larger, these cylinders usually have rods sized to match their overall strength. With so much force potential, you will often find ram cylinders used on hydraulic presses, as well.
A ram is simply a rod that acts as the piston as well, often requiring no seals while it floats within the cylinder bore. It is sealed and supported by the massive bearing or gland at the head side of the cylinder. It matters not the lack of sealing at the “piston” side of the ram since all
Regardless of who makes what, fluid power plays a major role in the manufacture of passenger vehicles, especially so with cylinders. Nearly every type of material and machine is used at one stage or another of the vehicle manufacturing process.
pressure surrounding the rod is equal and opposite in every direction but the piston area. Pressure on one side of the rod is cancelled by the opposite end, so the only direction for force to work is downward. Typically, these presses will have separate cylinders to lift and lower the slide and only employ the press cylinders to bear the brunt of the heavy lifting.
Critical to press applications (and any automotive application) is the requirement for ease of repair. The effort and time to remove and repair a hydraulic cylinder topping a ton is extensive, so designs to speed up the repair work are mandatory. A bearing and seal package installed on the rod side performs best when it can be removed and serviced while the body of the cylinder remains installed on the machine. A repair that takes only a couple of hours ensures that critical production machinery uptime is prioritized.
Because stamped steel panels rarely achieve their final appearance in a single action, they move through a series of machines and dies to achieve their shape. Using tandem presses for large panels or transfer presses for smaller panels, manufacturers pass the material through a series of dies with progressively finished shapes. A tandem setup uses multiple, large presses where the material is moved to each machine with robots, conveyors
or both. Meanwhile, a transfer press uses a series of stations inside a single press to achieve similar results on smaller parts.
Plastic panels range from those used on interior surfaces, such as doors, pillars and kick panels and a surprising number of exterior panels may also be plastic, such as bumper covers and side view mirror housings. Injection molding is, by and large, the most popular method for creating plastic parts. Injection molding machines clamp a set of dies shaped like the auto part and then through either thermoplastic (think plastic pellets) or thermoset injection molding (think chemical reactions).
The injection molding machine, Figure 2, comes in a vast range of sizes, depending on the size of the part being made, obviously. Two opposing molds are supported by tie bars and the moving mold attached to the clamping unit employs four hydraulic cylinders to ensure the
mold remains closed during the highpressure injection of plastic. The force required to clamp is a combination of the projected area and the injection pressure, but for parts such as dashboards and bumper covers, you can expect well over a thousand tons.
provide excellent column strength to prevent buckling, and because the retraction force is low, the annular piston area can remain small.
In addition to the clamping cylinders, part ejection cylinders are placed throughout the mold to pop the completed plastic
The hydraulic chuck for a through-bore lathe is a unique beast in the fluid power world, as it uses an annular piston to allow long material to reside within the chuck to prevent excessive overhang.
Again, cylinders this large are often custom to the application, especially because of the nature in which the cylinders are integrated into the machine. For smaller machines, NFPA cylinders might be suitable for the clamping function, but it’s more likely that custom cylinders with large rods are used. Large rods provide a strong extend proposition because they
piece(s) out of the mold. These cylinders may be NFPA or custom but are always small enough to be buried within the confines of the mold. The injection unit may also use a single, large-bore hydraulic cylinder. Plastic pellets are heated and fed into the barrel, which prepares the shot for injection. The injection cylinder is often precisely controlled through proportional
or servovalves to offer accurate and quick injection of plastic to prevent waste and non-conforming parts.
By far, the most numerous pieces of a vehicle, excluding fasteners, are the machined bits that make up the drivetrain. Gears, bearings, shafts, cams and pumps constitute hundreds of individual pieces that power and drive your internal combustion vehicle. Mostly from metal, each piece is forged, cast or made from billet, but almost always finish machined to the precise and accurate final component.
It’s hard to think of a more reliable and over-engineered man-made item than vehicle drivetrains. Consider that some manufacturers will offer a warranty spanning a decade, and to offer that confidence, parts must be so finely machined as to be nearly bulletproof. Machine tools are any piece of equipment designed to remove
material to create a finished workpiece, such as lathes, mills and grinders, to name a few.
Although, admittedly, CNC machines offer a modest hydraulic accoutrement compared to presses and injection molding machines, they provide the power and speed to improve the workflow of every manufacturer providing drivetrain parts. A hydraulic chuck, Figure 3, on a lathe beats using a keyed chuck to clamp work material any day of the week, and a hydraulic clamp beats out manual vices within a vertical milling center.
The hydraulic chuck for a through-bore lathe is a unique beast in the fluid power world, as it uses an annular piston to allow long material to reside within the chuck to prevent excessive overhang. The piston pushes on the wedge plunger (or may be the plunger itself), which opens the chuck slightly to allow removal and reinstallation of the workpiece. A rotary joint passes hydraulic fluid from the valve and into the rotating chuck, which is a requirement for such an application. Although it doesn’t provide infinite range throughout and across the distance the jaws move, it provides a fast and powerful method to hold tubes, bars or rods.
Cylinders are pivotal to the operation, performance and reliability of machinery used in automobile manufacturing.
Similar to the hydraulic chuck is the hydraulic clamp used in vertical milling centers or other machines with fixed work pieces. It is much faster and more powerful than manually operated clamps, and foot pedal operation provides operators with free hands to remove and replace the piece or to adjust it for a second operation. The clamp might use a tiny hydraulic cylinder to squeeze a clamp together, or it may use one or more swing clamps to hold material fast.
A swing clamp is a small cylinder that rotates partially to lift up and out of the way to place or remove material. When activated, it swings back down and clamps the workpiece with a clamping arm, keeping it fixed in place
while the high-powered tooling sheds chips from the material while it works toward its final shape. They often use a ball detent mechanism that requires the ball on the body to follow the helical groove in the rod, providing partial rotation.
Pneumatic cylinders, Figure 4, are also used throughout automotive manufacturing for their consistent and efficient movements. They offer precise control for items like gripping, welding and assembling of components. They are often used in robotics cells as well as assembly lines to position and handle parts.
Cylinders are pivotal to the operation, performance and reliability of machinery used in automobile manufacturing. From standard to custom designs, machine designs prioritize productivity and uptime to keep the automotive realm lean and profitable. FPW
4. PNEUMATIC CYLINDERS DON’T GET THE SPOTLIGHT, BUT THEY DO THE HEAVY LIFTING — LITERALLY. WITH STEEL BODIES AND AIR-POWERED EFFICIENCY, THEY KEEP AUTOMOTIVE AUTOMATION FAST, CLEAN, AND COST-EFFECTIVE. HERE, NC9 AIR CYLINDERS FROM PENINSULAR CYLINDER CO. ARE BUILT TO A FORD STANDARD (STEEL AIR CYLINDERS).
Mary C. Gannon • Editor-in-Chief
AS IT CONTINUES TO EXPAND fluid power’s presence throughout multiple industries, the National Fluid Power Association is putting together technical conferences at three upcoming trade shows and conferences over the next year.
First up will be Automate 2025, slated for May 12-15 in Detroit. Recent advances in the digitalization of fluid power have increased its capabilities and provided for deeper hybridization and integration with electrical and other systems on industrial machines, said NFPA President/CEO Eric Lanke. Speakers will showcase the application of these new technologies in the in-plant environment.
The sessions on May 14 include:
1:30-2:15 PM — Emerging Technologies and Architectures of Automated Systems with Integrated Functional Safety, presented by Linda Caron, Global Product Sales Manager, Factory Automation & Machinery Safety, Parker Hannifin. Emerging technologies have added a degree of sophistication to the plant floor. Collective wiring has migrated to networked communication. Different topologies can be used to connect devices such as IO-Link. The integration of safety circuits both hardwired and over network bring about new challenges. The session will explore the integration of emerging technology and the expansion of functional safety to fluid power components.
2:30-3:15 PM — Pneumatic Operational Improvement via Digitalization, presented by Frank Latino, Product Manager, Festo. Leveraging digital technologies such as digital communications, machine learning, artificial intelligence, Internet of Things, and Edge Computing can improve the operation of pneumatic systems. Specifically, the maintenance process, energy consumption, and machine safety. Machines must be digitally connected to access data from smart devices to achieve this. The basis will be on Ethernet and IO-Link. He will touch on perfor-
mance characteristics such as speed, capacity, and security and will then look at use cases that will provide benefits to machine builders, including networked safety, sustainability, and predictive analysis.
3:30-4:15 PM — The Electrification of Industrial Hydraulics – A Glimpse into the Future (Now), presented by Christopher Parisse, Senior Controls Product Engineer, Bosch Rexroth. When you think about traditional hydraulic systems, the first thing that may come to mind is a loud energy hogging oily solution. These types of machines are a thing of the past thanks to the harmony of electrification with hydraulic systems. This transition is driven by advancements in hydraulic motion control, variable speed drives and clever system design, enabling the replacement of conventional hydraulic components with electro-hydraulic alternatives. Electrified hydraulic systems offer benefits such as improved energy efficiency, reduced emissions, lower maintenance requirements, and enhanced system controllability. He will discuss the integration of VFDs and servo drives in hydraulic applications, a different concept of a hydraulic power unit, and the benefits of power density with hydraulics.
Get more information and register at automateshow.com/conference
Next, in addition to encouraging companies to exhibit, NFPA will once again present a Hydraulics Technology Conference at iVT Expo USA 2025, to be held August 20-21
in Chicago. iVT EXPO is focused on all types of industrial and off-highway vehicles, with exhibits that are highly focused on key technologies, including new powertrains, electric and hybrid systems, control systems, sensors, and autonomous technologies. With hydraulics serving as a key enabling technology for these vehicles and many of these systems, iVT EXPO is a platform for growth and expansion of hydraulics.
NFPA is planning a two-day conference. Proposals have been submitted and are under review. Topics could include any of the following:
• Hydraulic system designs, architectures, and products optimized for performance on off-highway vehicles with electrified powertrains
• Thermal management strategies for hydraulically-actuated, electrified off-highway vehicles
• Improvements in hydraulic system efficiency, especially those that help to increase battery life on electrified offhighway vehicles
• Strategies for reducing the volume and harshness of hydraulic noise on electrified off-highway vehicles
• Hydraulic data collection and utilization strategies that provide system or machinelevel performance improvements
• Hydraulic systems that operate in partial or fully autonomous modes
• Cutting-edge research innovations that may change the use or application of fluid power technologies
And last, but not least, The NFPA will co-locate an advanced hydraulics conference for off-highway vehicle and other fluid power engineers at CONEXPO-CON/AGG 2026, March 3-7, 2026, in Las Vegas. A call for papers will be issued later this year and will include topics similar to those suggested for iVT Expo.
Visit NFPA.com for more details. FPW
SIX YEARS AGO, the International Fluid Power Society relaunched the industry's Fluid Power Hall of Fame, having its first class in 2019 after several decades. The Hall of Fame was established to acknowledge those individuals who have dedicated their careers and have made significant contributions to fluid power technology. Over the past six years, 32 individuals have been inducted into the Hall of Fame including several who were nominated posthumously.
IFPS notes in its call for nominations that the success of the fluid power industry is not in its hardware, pumps, valves, cylinders, and hoses — but rather the success is through the efforts of the dedicated individuals — innovators, researchers, application engineers, educators, as well as sales and service personnel. These people are the reason that our industry continues to thrive.
Nominations are accepted until April 15 each year.
Any person can nominate an individual, living or deceased, who demonstrated excellence within their 25+ year fluid power career; however, an individual is only allowed to nominate for 1) living and 1) posthumous.
To be eligible for the award nominees must have had verifiable 25+ cumulative years in the fluid power industry. Those nominated are asked to complete a 15-question application.
A panel of judges reviews the applications and selects the Class of Inductees. The Hall of Fame Inductees will be announced on June 19 — Fluid Power Professionals' Day.
Visit fluidpowerhalloffame.org to learn more and to submit nominations. FPW
THE FLUID POWER SYSTEMS & Technology Division (FPST) of the American Society of Mechanical Engineers (ASME) and The University of Bath Centre for Power Transmission and Motion Control (PTMC) will once again host the 2025 International Symposium on Fluid Power and Motion Control (FPMC). This year’s event will be held in Anaheim, California, August 17-20.
The 38th symposium covers current and future trends in fluid power and motion control for academia and industry. It will be held as part of the IDETC-CIE conference, featuring technical presentations, social events, and a keynote speech given by the 2025 recipient of the prestigious Robert E. Koski Medal, who will be announced later this year.
Conference topics and themes will be announced in a couple months, but presentations could include the following:
• Fluid power system design
• Fluid power system control
• Fluid power component design
• Environmentally friendly materials for fluid power components
• Fluid power in renewable energy applications
• Zero carbon fluid power technologies
• AI in fluid power (machine learning, neural networks)
Visit www.bath.ac.uk/campaigns/fpmcbath-asme-symposium-on-fluid-power-andmotion-control to learn more. FPW