Hydraulics powers machine tools p. 28 A new romance: mobile hydraulics and electrics p. 32 Pneumatics for food & beverage packaging p. 36 www.fluidpowerworld.com hydraulicsHomerun PAGE 16 August 2022
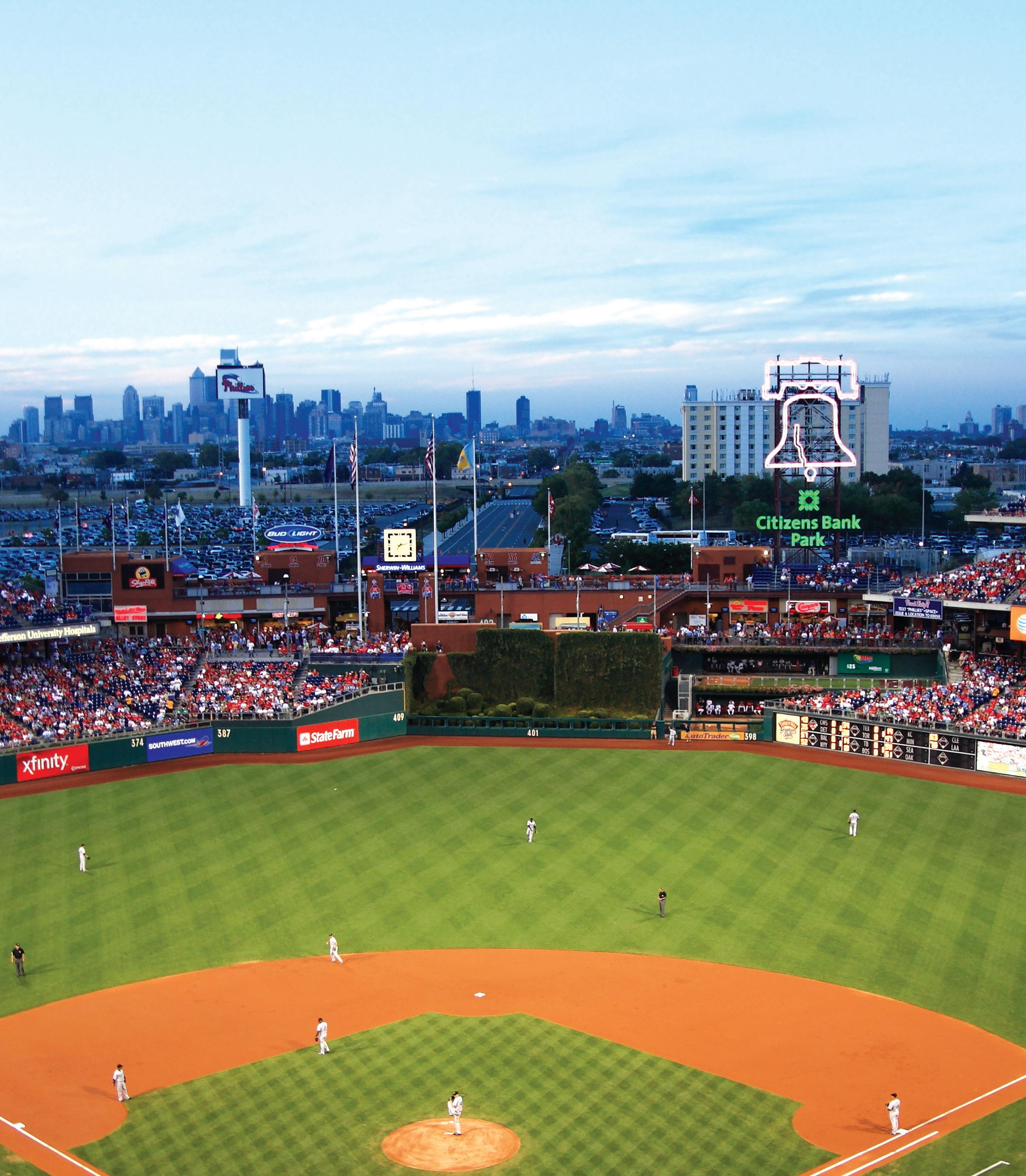
tompkinsind.com800-255-1008ALWAYS ADAPTING. TOUGHER WITH EVERY TEST.
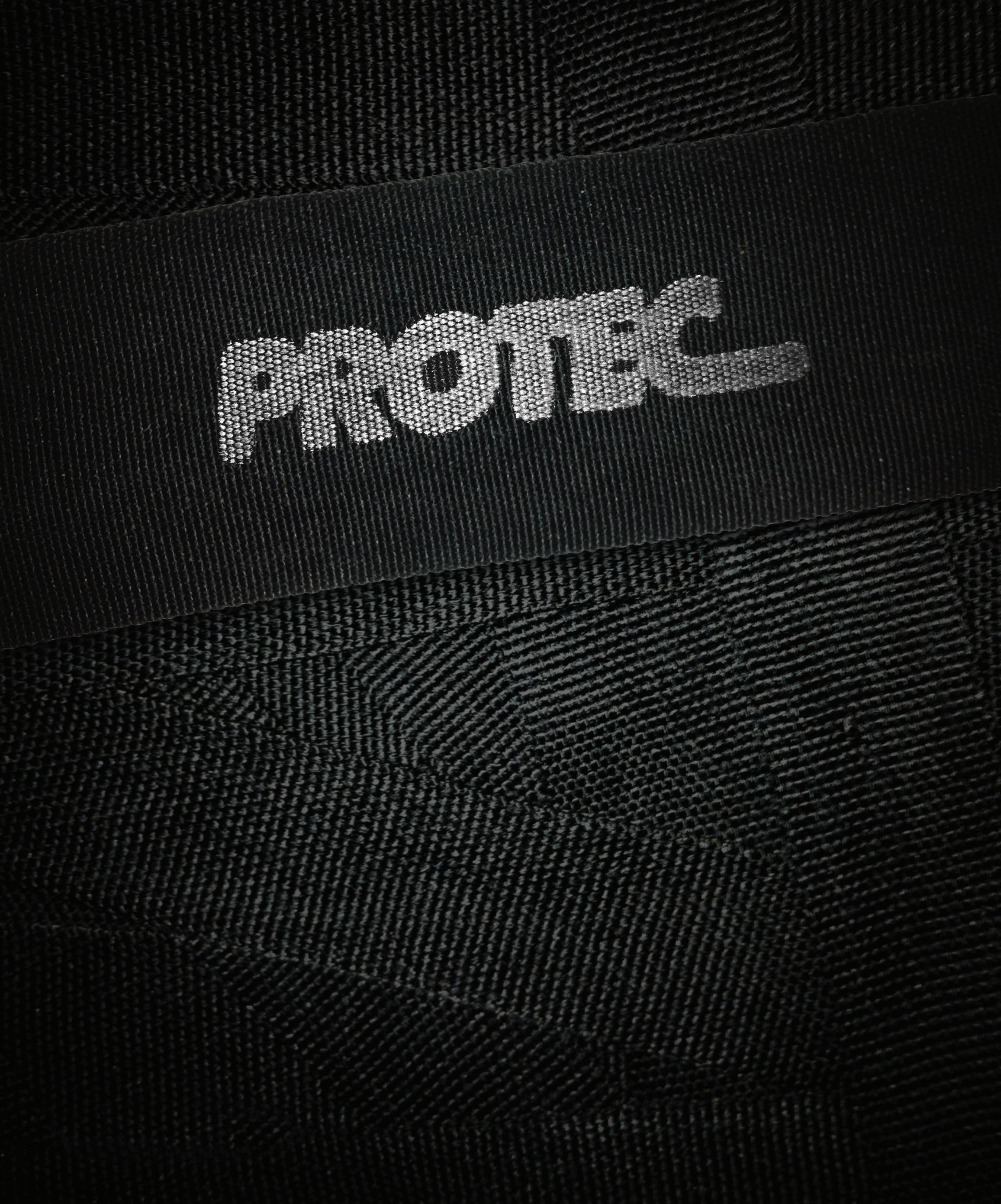
the #1 value in automation Order Today, Ships Fast! * See our Web site for details and restrictions. © Copyright 2022 AutomationDirect, Cumming, GA USA. All rights reserved. 1-800-633-0405 Research, price, buy www.automationdirect.com/enclosuresat: NEW! Fandis Filter Fans... Fandis Virdis series lter fans provide a low-cost thermal management solution in applications where the surrounding air temperature is low enough to be used to cool the inside of an enclosure. Over 7,100 top brand enclosures starting at only $6.25 • Wall-mount • Junction boxes • Pushbutton • Floor-mount • Freestanding • Modular • Disconnect • Internal disconnectsmount • Consoles consoletsand • Wire troughs • workstationsDesktop • Various types of metallic constructionsnon-metallicand • And much more... • Cover slides open for easy filter change without tools • No-screw installation • Low noise • 120 VAC, 230 VAC, and 24 VDC models • Permanent Polyurethane sealing gasket • G3 (coarse) and G4 (coarse) replacement filter mats • NEMA 3R or 12 models • Roof mount units can be used when side mounting is not available We o er a full line of quality enclosures from the best manufacturers in the world Plus over 5,800 low-cost accessories and wiring solutions for those all-important nishing touches!Also Available CommunicationDataRacksandcomponents


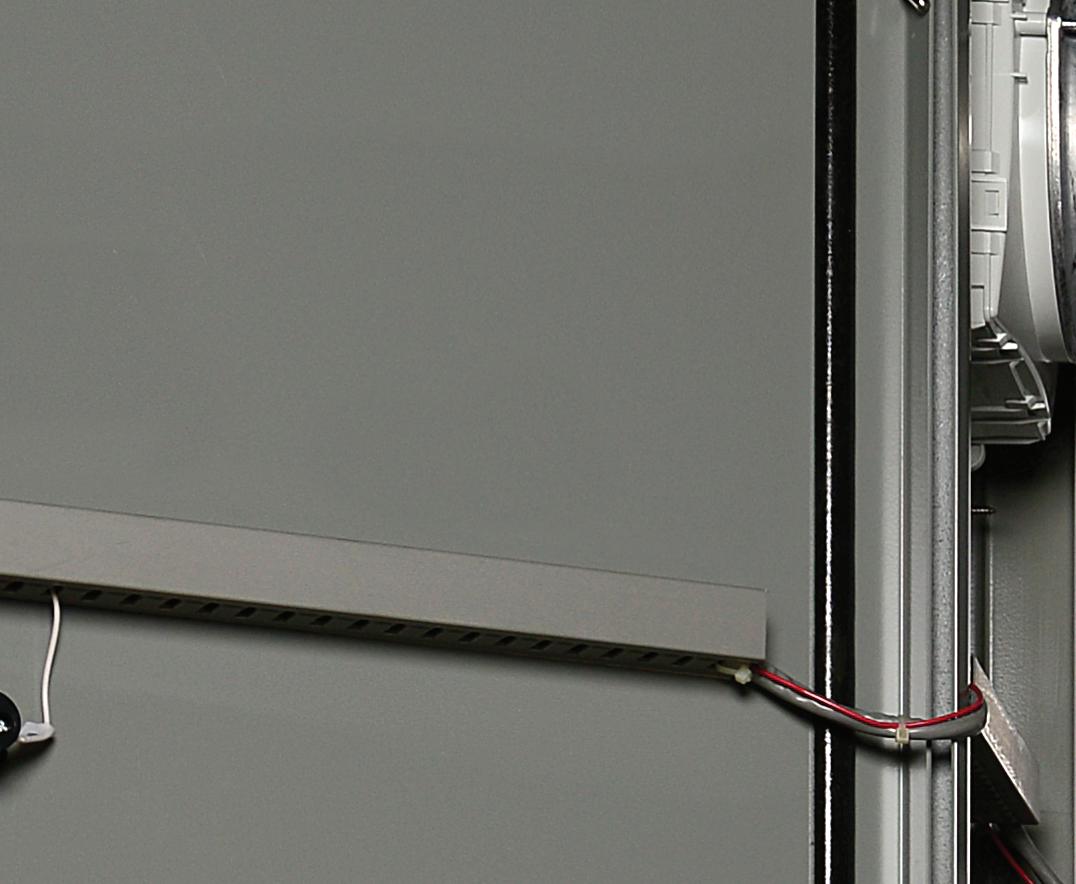
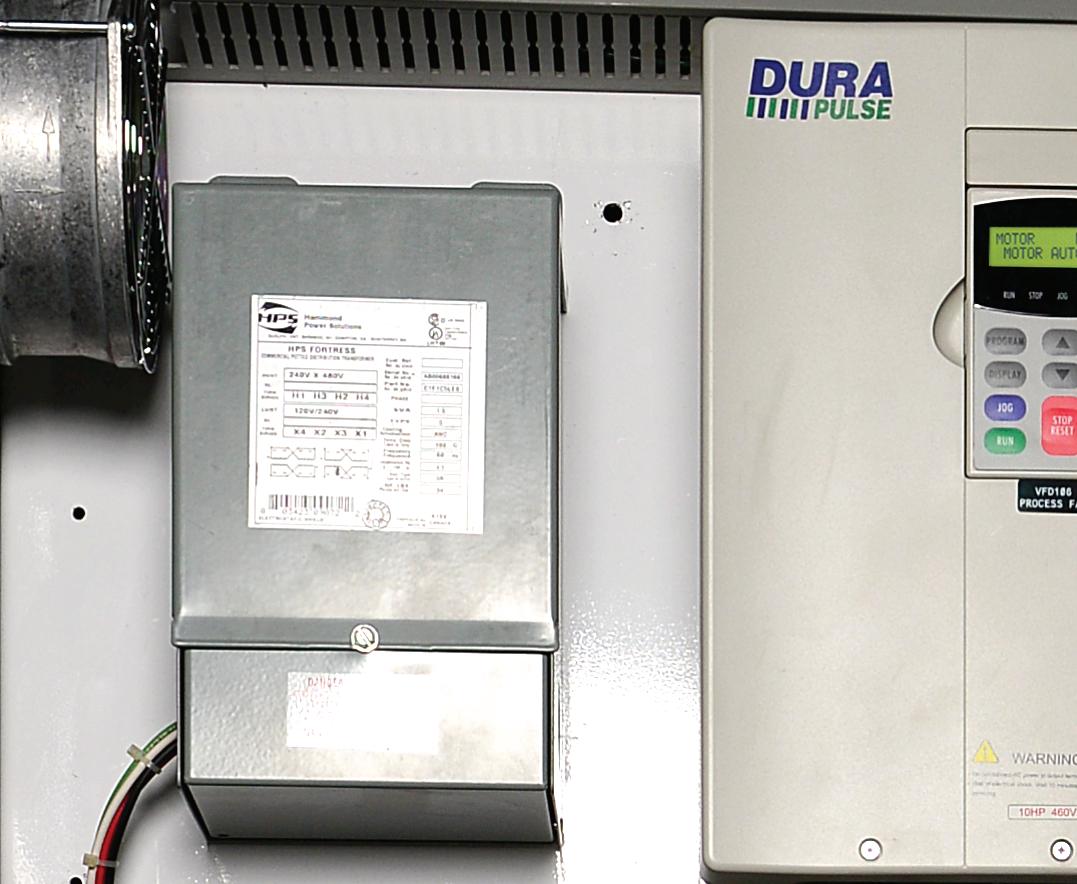
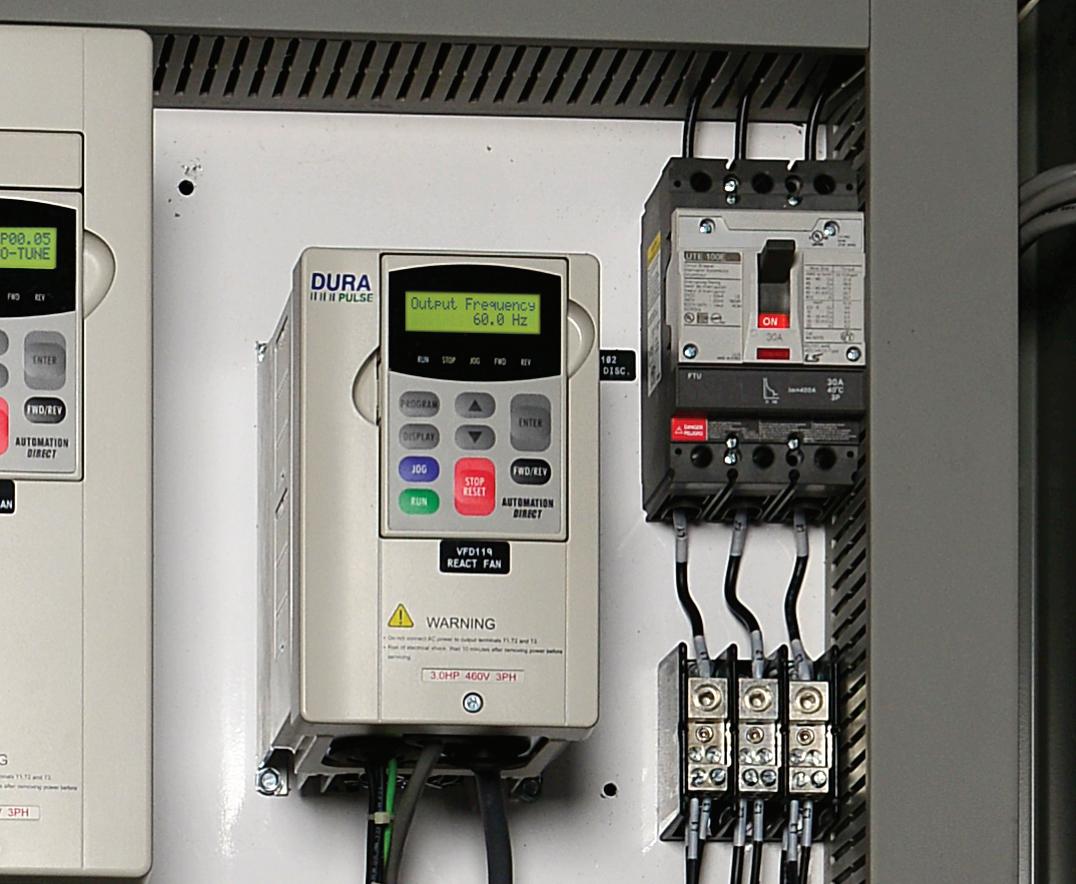

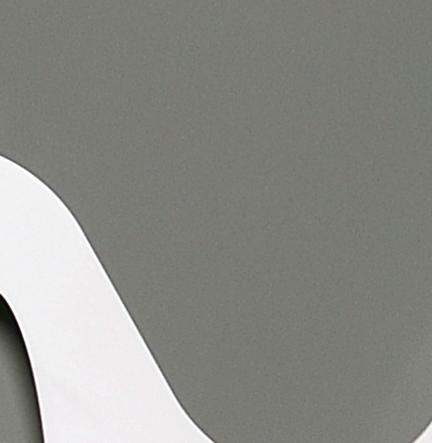

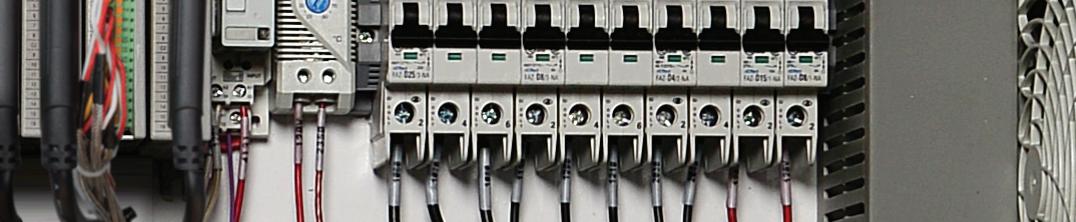
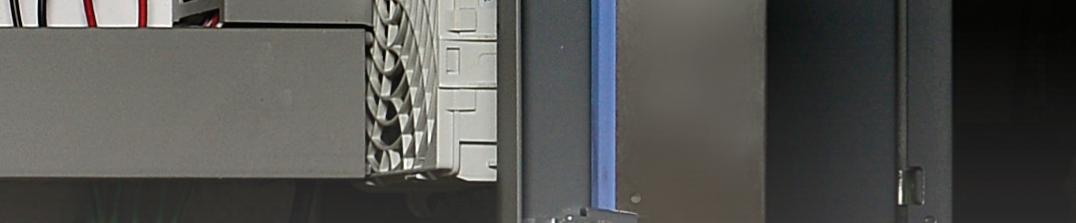
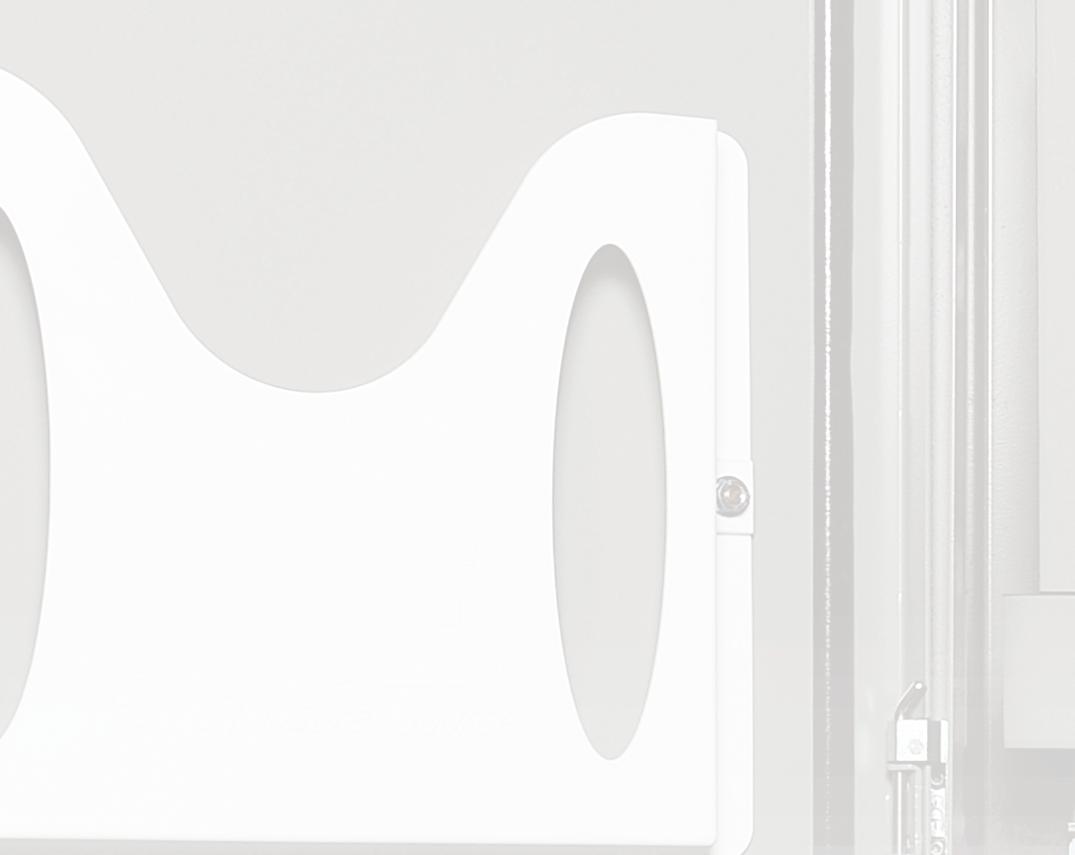
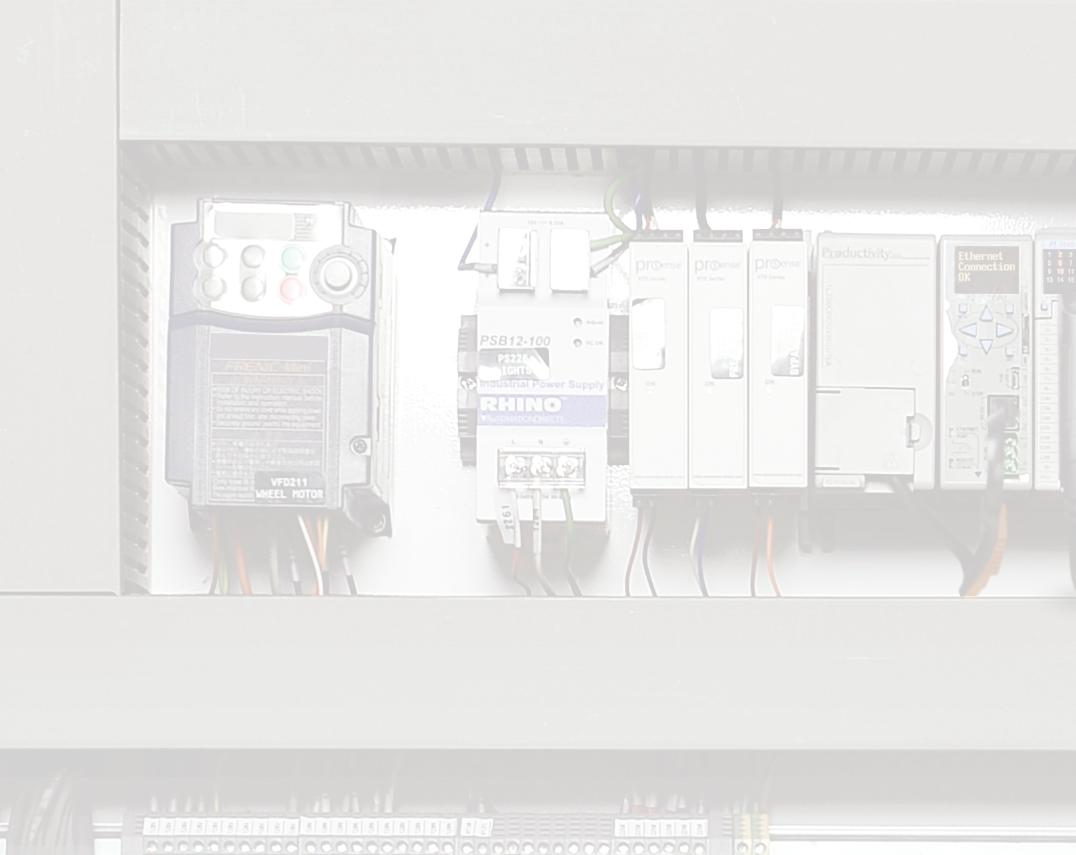

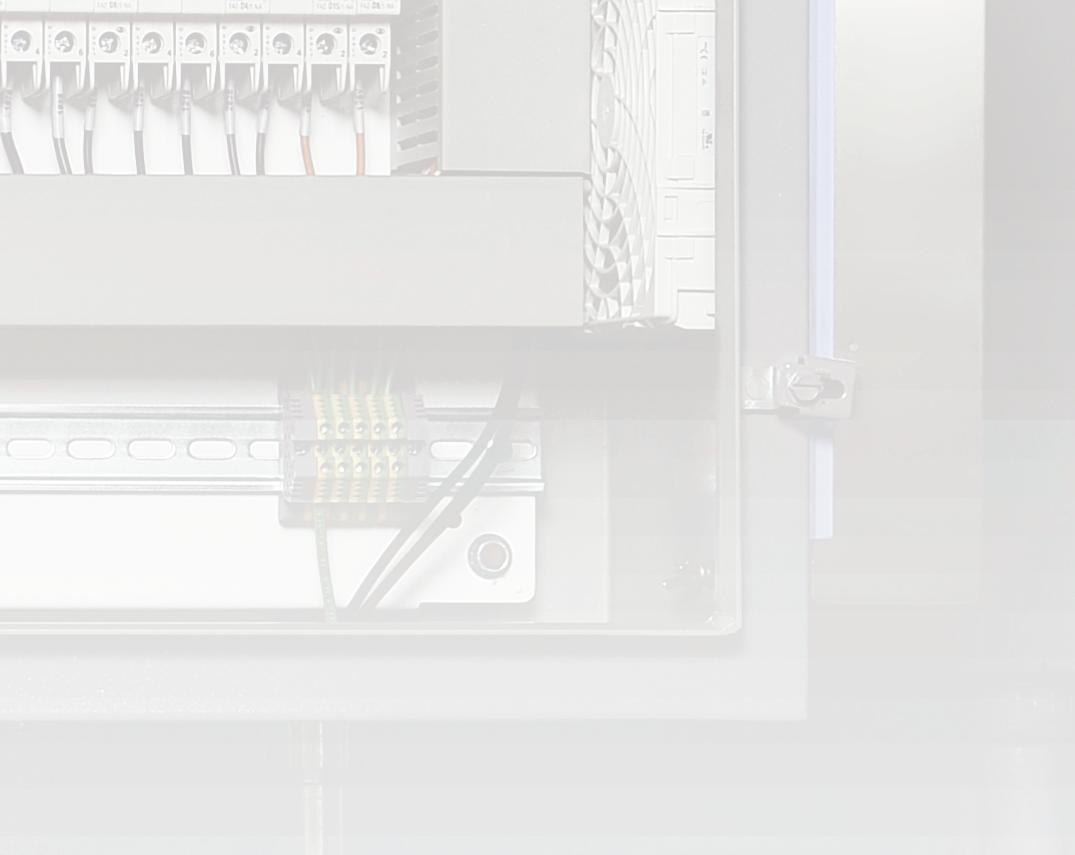
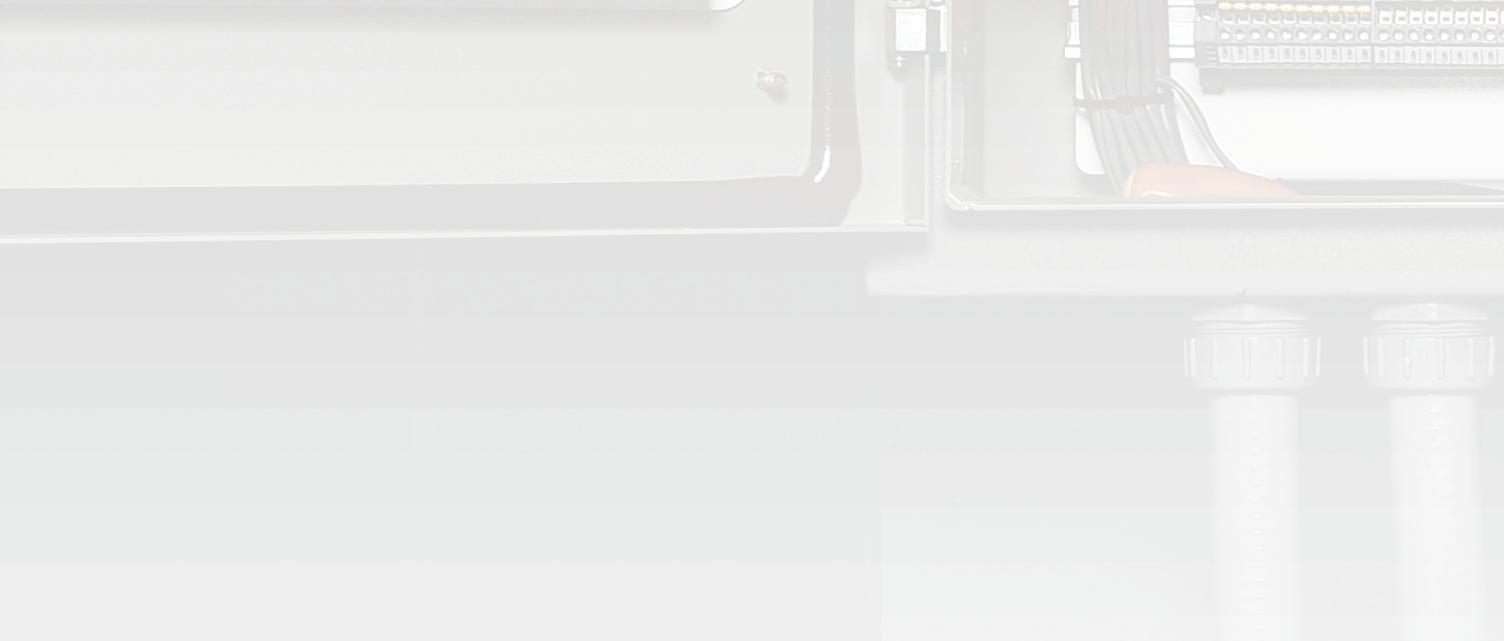
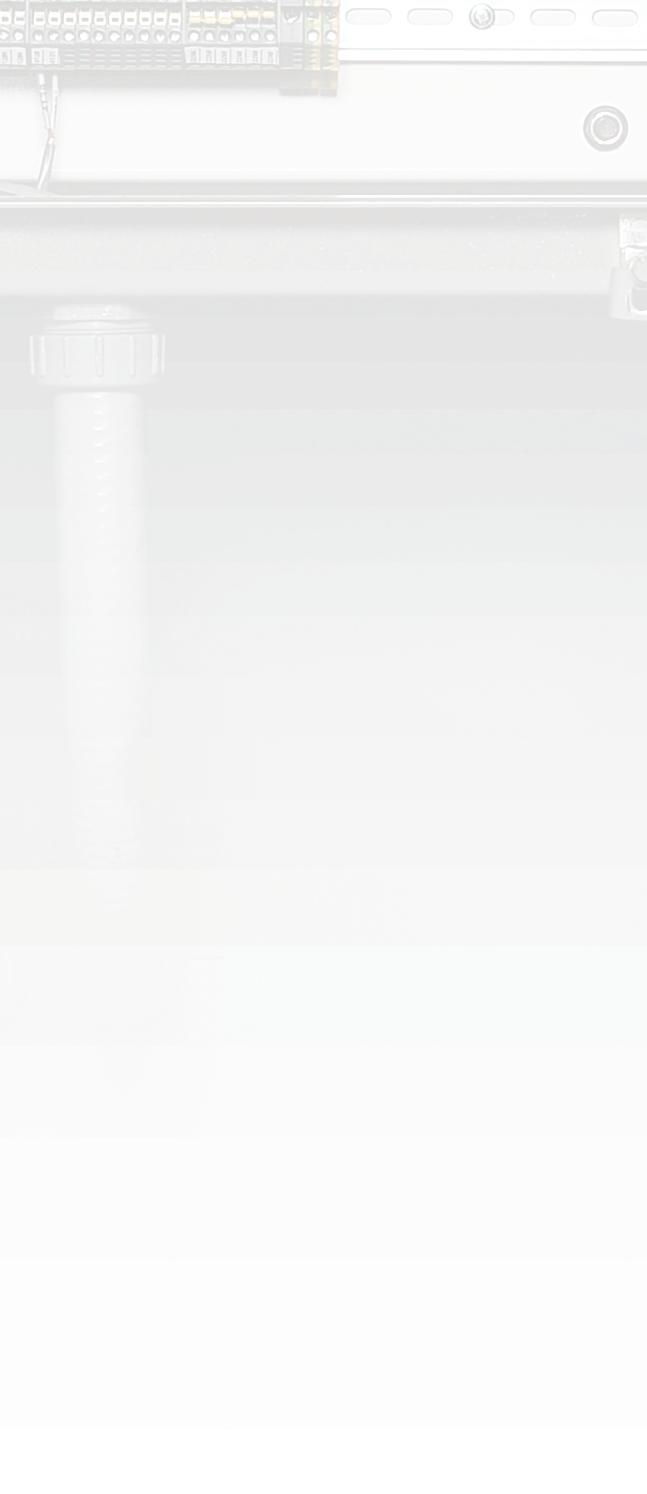

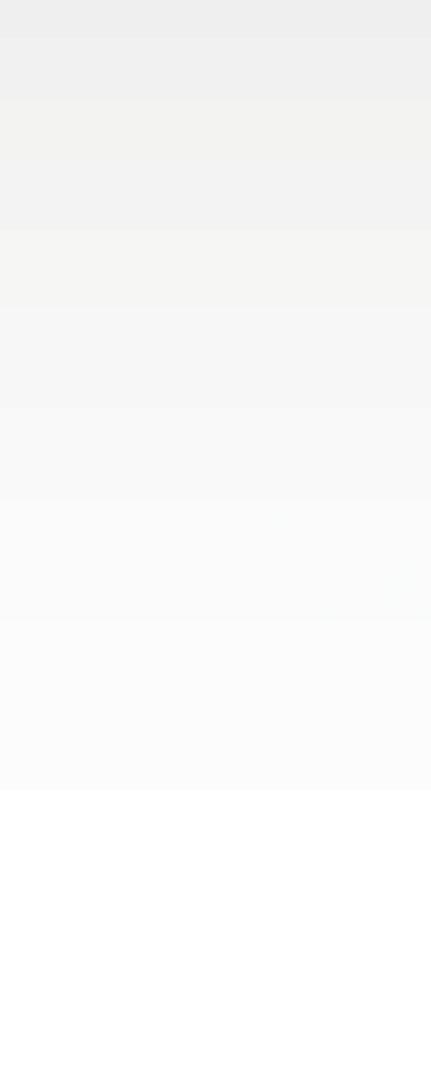
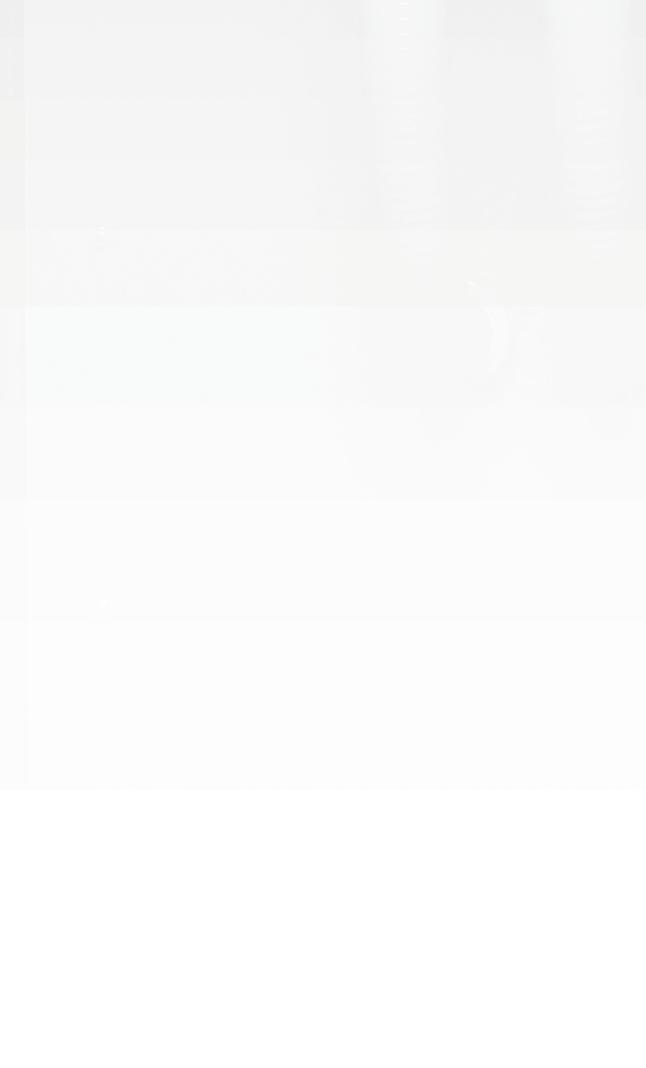
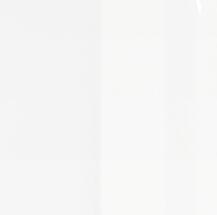
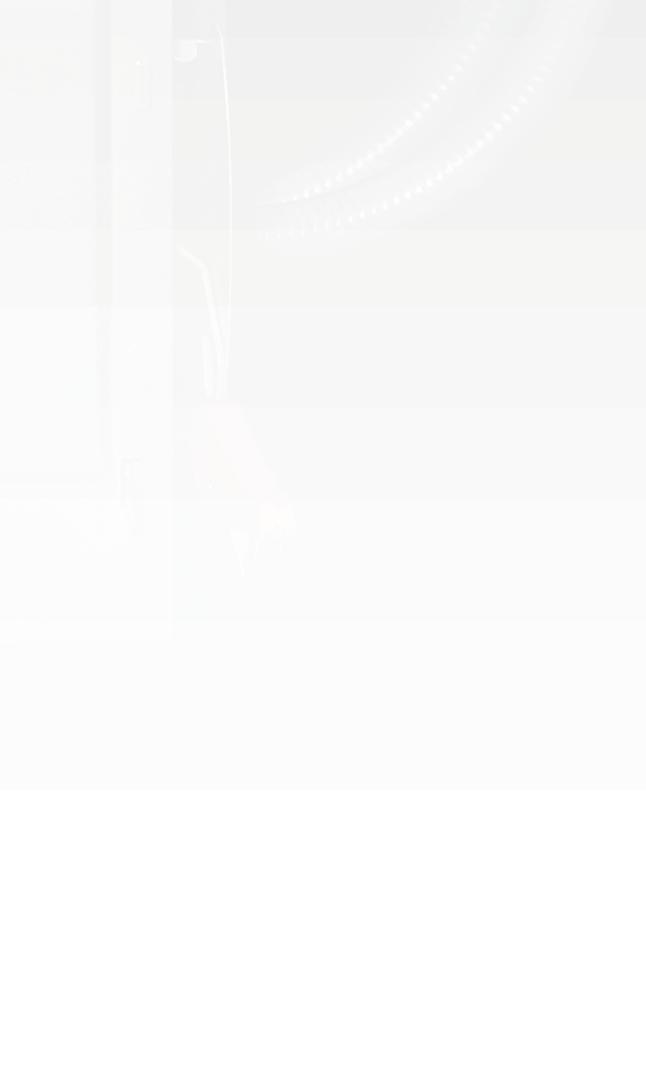
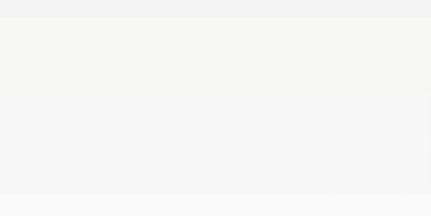
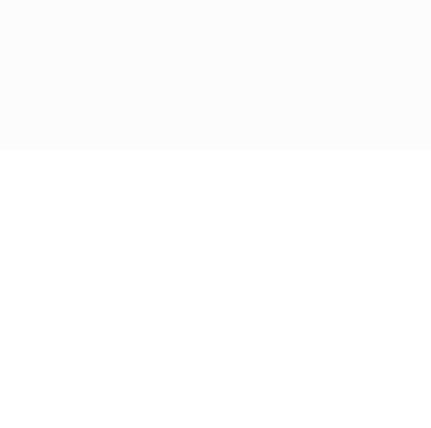

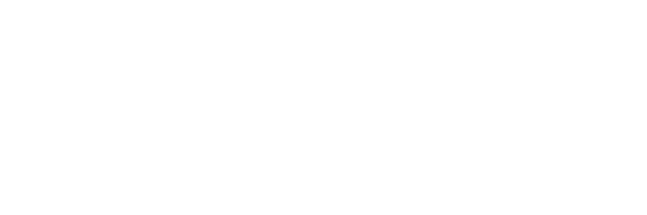



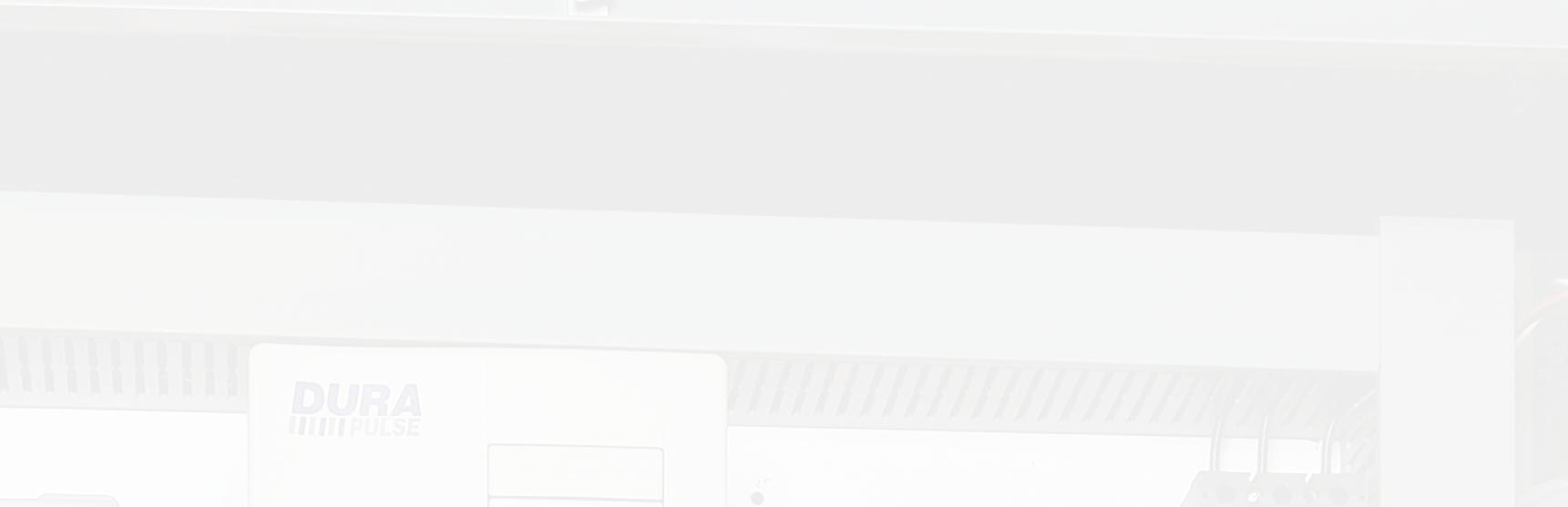
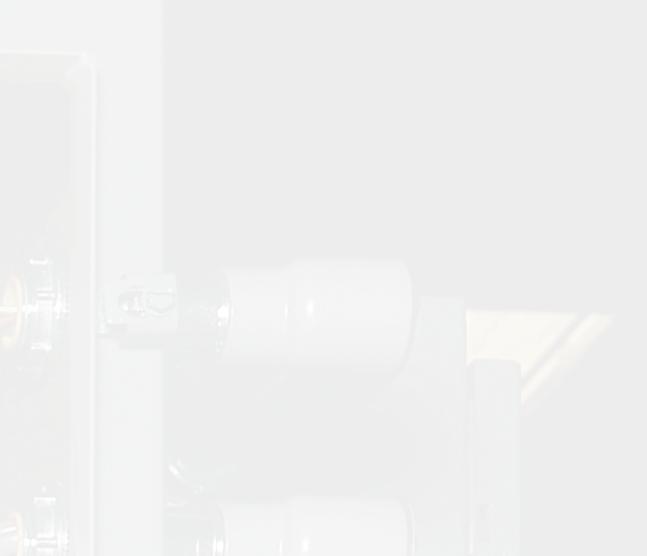
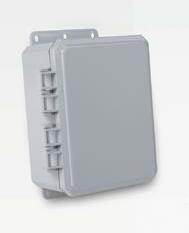

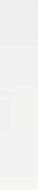

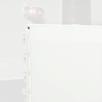
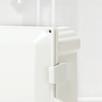
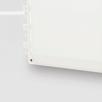
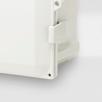


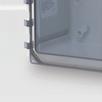
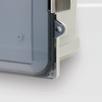


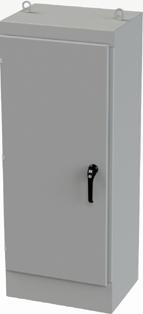
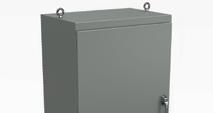
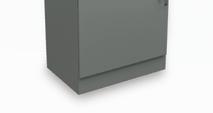
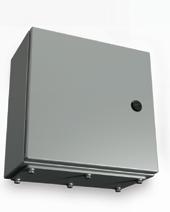

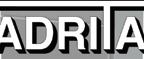
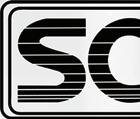

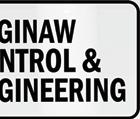
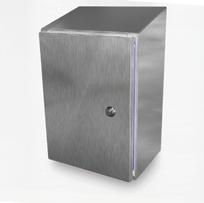
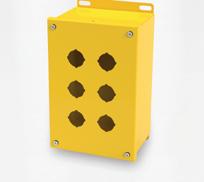
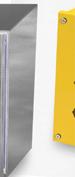
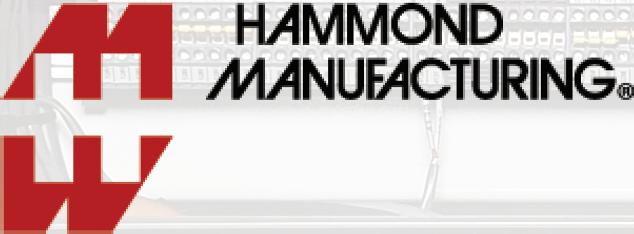


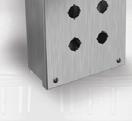

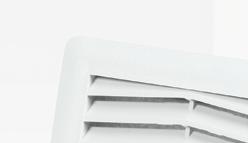

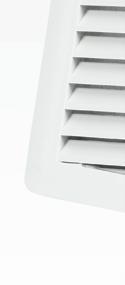
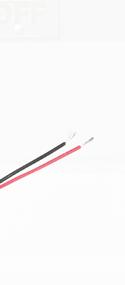
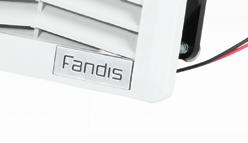
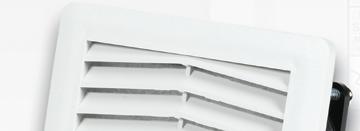

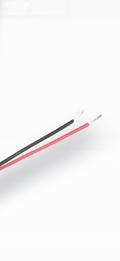
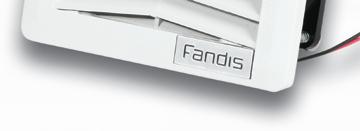
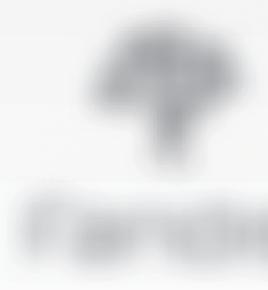
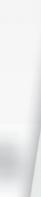


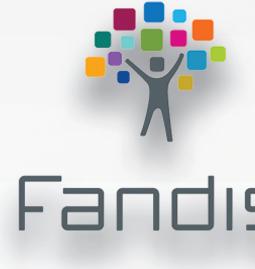

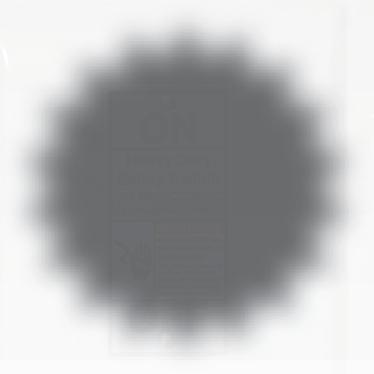
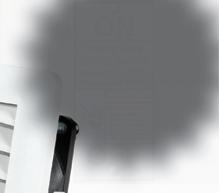
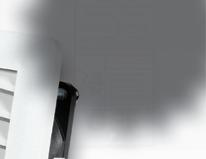
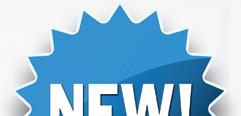
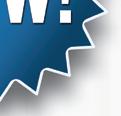
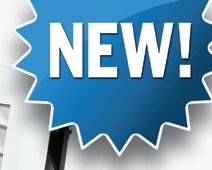
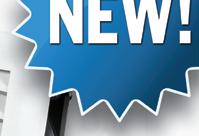
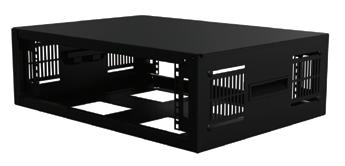
a friend and legend POSITION SENSORS FOR HYDRAULIC CYLINDERS Absolute detection of the cylinder stroke No piston drilling necessary Can also be used in telescopic cylinders High shock and vibration resistance, IP69K SIKO Products Inc., www.siko-global.com
Tom was an expert in hydraulic component and system design reviews, development, and evaluation; field troubleshooting and failure analysis; and fluids, filtration, and contamination control in hydraulic systems. The number of awards and recognitions he received over the years are too many to list, but suffice to say, they were all well-deserved. His knowledge and passion for the industry will likely not be surpassed in my lifetime. So we bid farewell to one of our industry stalwarts. Thank you, Tom, for your friendship and generosity over the years in teaching so many of us the ins and outs of this technology and more importantly, why we love this industry — people such as yourself make it great.
• Editor-in-Chief FLUIDLINES Bidding a sad
On Twitter @FPW_marygannon Mary
FPW Mary C. Gannon • Editor-in mgannon@wtwhmedia.com-Chief C. Gannon farewell to
It was a sad day on June 22, when word came from the Milwaukee School of Engineering that Tom Wanke, CFPE, director of the Fluid Power Industrial Consortium and Industry Relations, had passed away unexpectedly the day before. As a young editor at the beginning of my career, I was glad to count Tom Wanke as a mentor who helped teach me about fluid power. And as my career continued over the years, I was blessed to work directly with him on many occasions through our events and editorial coverage. Tom was probably one of the most passionate teachers of fluid power systems I’ve ever met and he became a great friend to me over the years. I will truly miss his friendship. I first met him when I attended a week-long basic hydraulics course at MSOE, where he made a cameo in the classroom. But more importantly, I had the pleasure of working with him many times over the years in conjunction with our Fluid Power Technology Conference in particular, as he helped us coordinate several of these events. He also served as a favorite presenter throughout the years. This partnership meant frequent phone calls, meetings, and occasional dinners and drinks at industry events. I was delighted to finally meet his wife Ann in February at the NFPA Annual Meeting. Because if there was one thing Tom loved more than fluid power, it was his family. I don’t think I’ve met another person as passionate about this industry as Tom; he was integral in shaping many young engineering minds throughout his 50-year career at MSOE, beginning as a technician in the university’s Fluid Power Institute through to his final days as the director of the FPIC, which he helped to establish in 2016.
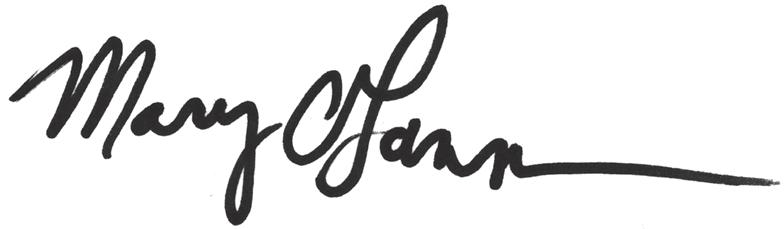
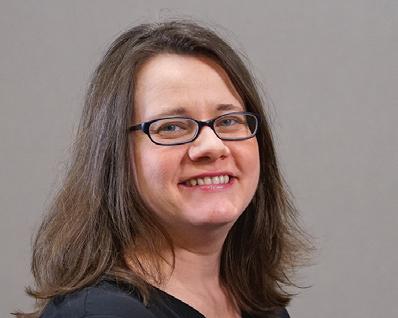
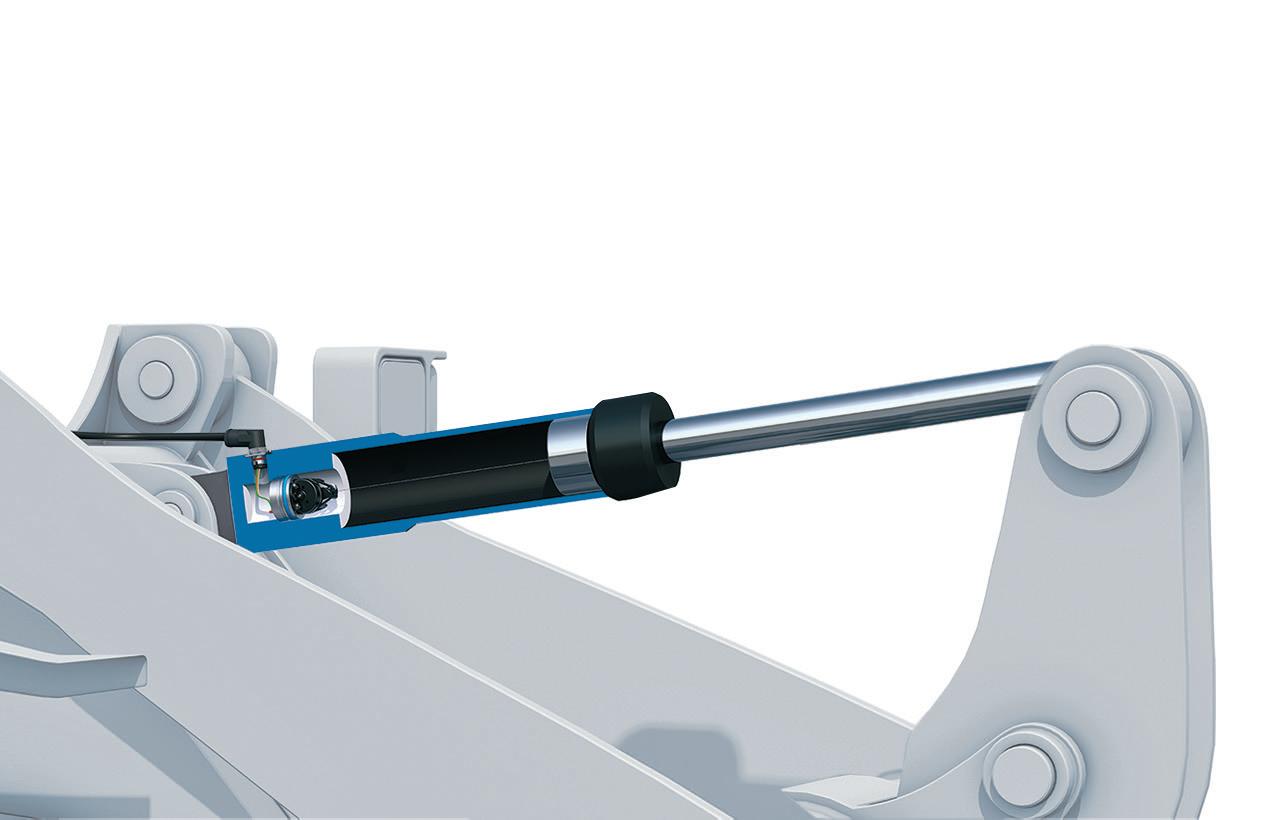
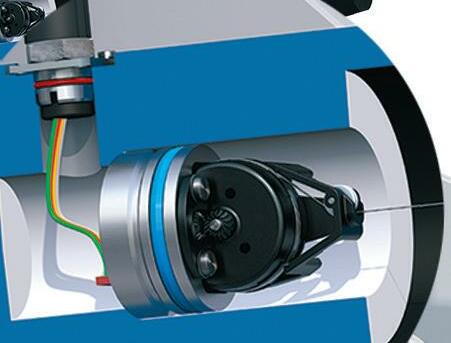

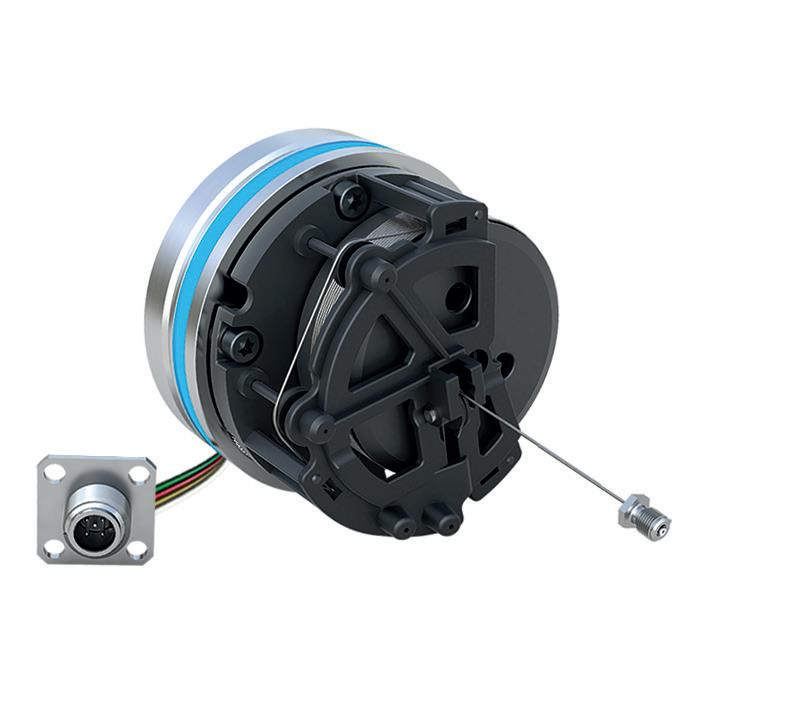
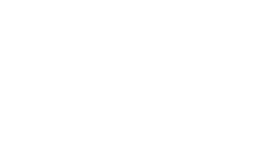
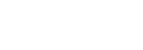
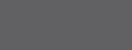
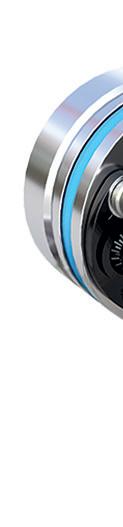
engineered by Terzo’s Hydrapulse ® Technology offers OEMs and engineers incredible flexibility, efficiency, and performance in a compact and powerful package. Complete electro-hydraulic system with built-in intelligence for industrial, mobile, machine tool and trucking markets Three standard frame sizes (the F1, F2 and F3) All new F3 designed specifically for large commercial trucking, mining and off-highway electrification applications Electrify any fluid power system including steering, coolant pumps, air compressors, hydraulic power units and auxiliary systems Explore electrifying your application today by visiting our website A NEW BENCHMARK FOR ELECTRO-HYDRAULICS Next Gen Technology Today
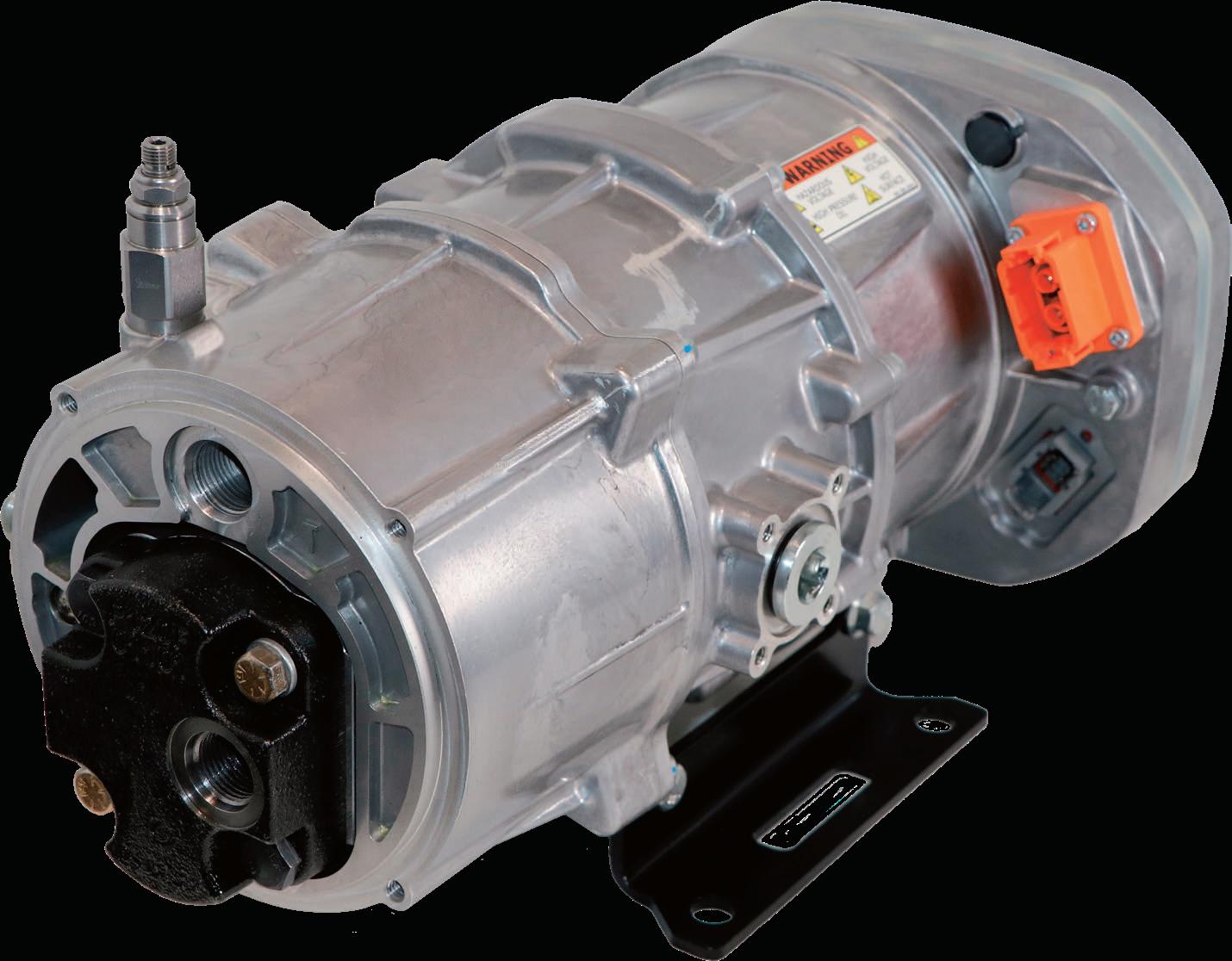
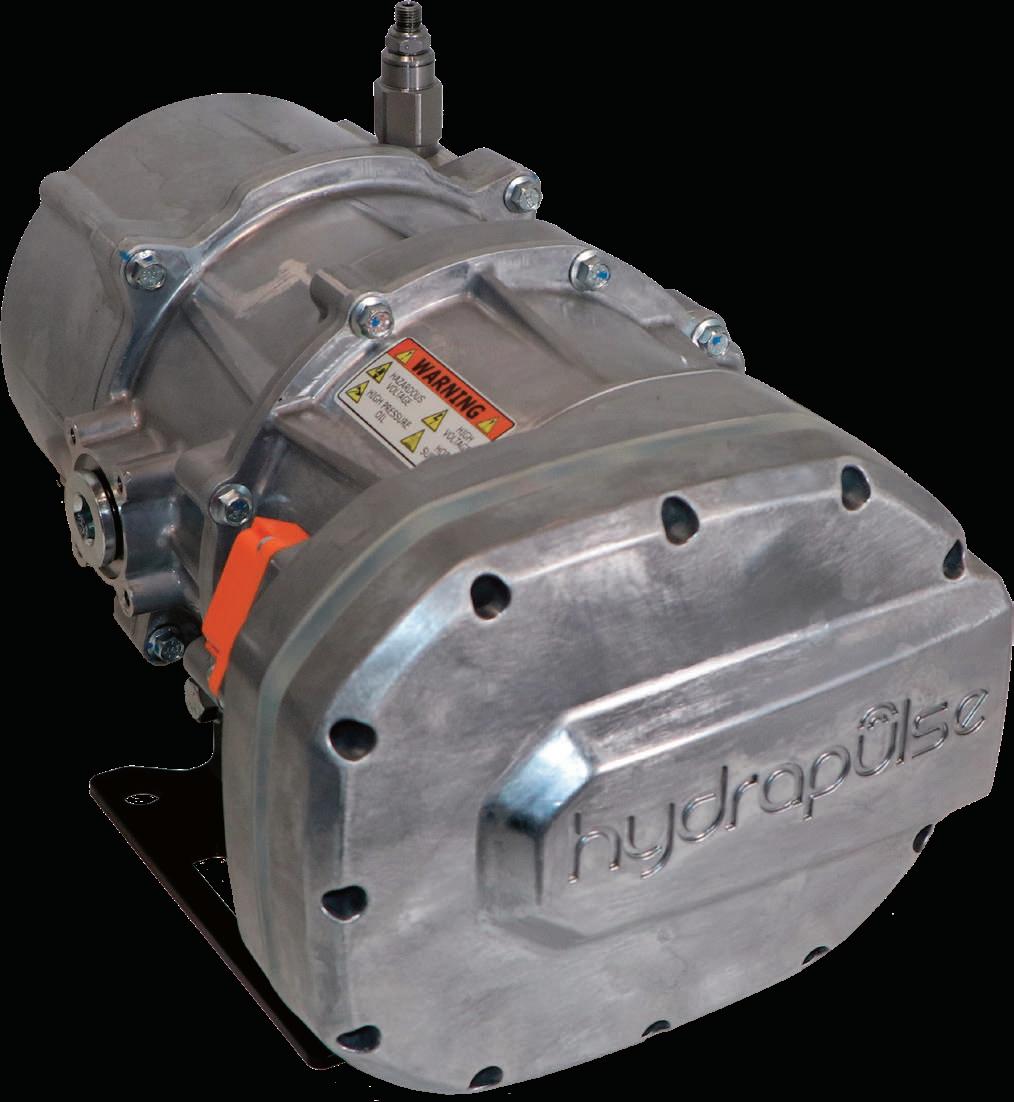
Paul J. Heney • VP, Editorial Director manufacturer consolidation?
FPW
Specifically, we learned about products that, more than ever, incorporate hydraulics with electronics and software. This will lead to easier user experiences, additional flexibility in the equipment’s operation, and more efficient machines.
So, what does this mean for fluid power? Are we entering into a new age of consolidation in this industry? What will happen to smaller manufacturers who can’t keep up with the rapid advances in component technology? Some may simply not make it. Others may find niche innovations that make them attractive targets to today’s “big three” of Bosch Rexroth, Parker Hannifin, and Danfoss. Could some even find themselves becoming essentially suppliers to one of the big three?
These new, more sophisticated electrified components are going to be difficult to compete with for smaller manufacturers. A company like Bosch Rexroth has deep pockets and the ability to do extensive R&D — not to mention plan for a decade or more ahead. Many smaller companies don’t have that luxury and must keep a wary eye on the economy’s trajectory over the coming months or year.
FROM THE FIELD 4 FLUID POWER WORLD 8 • 2022 www.fluidpowerworld.com
CFCINDUSTRIALTRAINING.com 7042 Fairfield Business Drive Fairfield, Ohio 45014 +1 info@cfcindustrialtraining.com513.874.3225 UPSKILL ONSITEWORKFORCE!YOUR AND CERTIFICATION FOR: TRAINING CFC provides direct, Industry and/or Machine specific training to companies the world over. Electrical Techs & Engineers Hydraulic Techs & Engineers Pneumatic Techs & Engineers Our Hands-On Training Equipment is mobilized directly to your facility with Certified Instructors traveling on-site. This turnkey approach includes all books, materials, equipment, and travel arrangements. We have the capability to upskill your entire workforce NOW! Multicraft Techs & Engineers
And don’t discount the idea that certain manufacturers could be purchased for their manufacturing capabilities — or even their engineering staffs. Given the talent crunch we’re seeing in fluid power and many other engineering specialties, that idea may not be so far-fetched in the near future. Regardless, what develops in the coming years will certainly be interesting to watch.
Will technology lead to a new age of
This is all wonderful news for OEM design engineers, for customers that will be using the equipment, and for the environment. But it also got me thinking about what this trend means for the fluid power industry itself. Let’s first take a step back in time.
At a recent user conference put on by Bosch Rexroth in suburban Chicago, the company presented specifics on some of its latest components designed for use on mobile machinery.
Paul J. Heney VP, Editorial pheney@wtwhmedia.comDirector On Twitter @wtwh_paulheney
Earlier in my career of covering fluid power, we experienced a period where the big three manufacturers at the time — Parker Hannifin, Eaton Corp., and Bosch Rexroth — were quite active in buying smaller companies. There were so many fluid power manufacturers that were created when soldiers came back from World War II and had, say, the idea for a hydraulic valve, and started a company. Certain ones grew larger than others, but as some of the companies reached a big enough size or came up with specific innovations, they were gobbled up by the larger players. As such, our industry saw a significant consolidation in the 1990s and 2000s. This consolidation surely slowed in the last decade, but how long will that slowdown last?
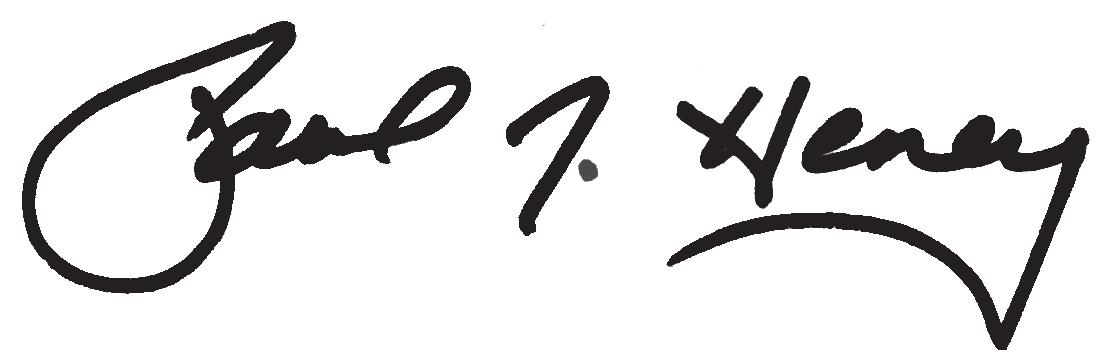
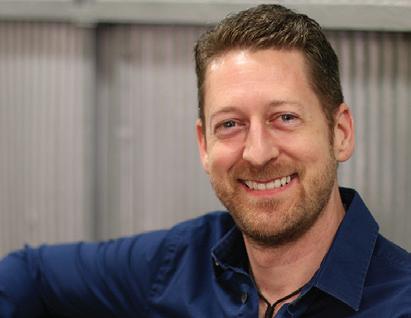

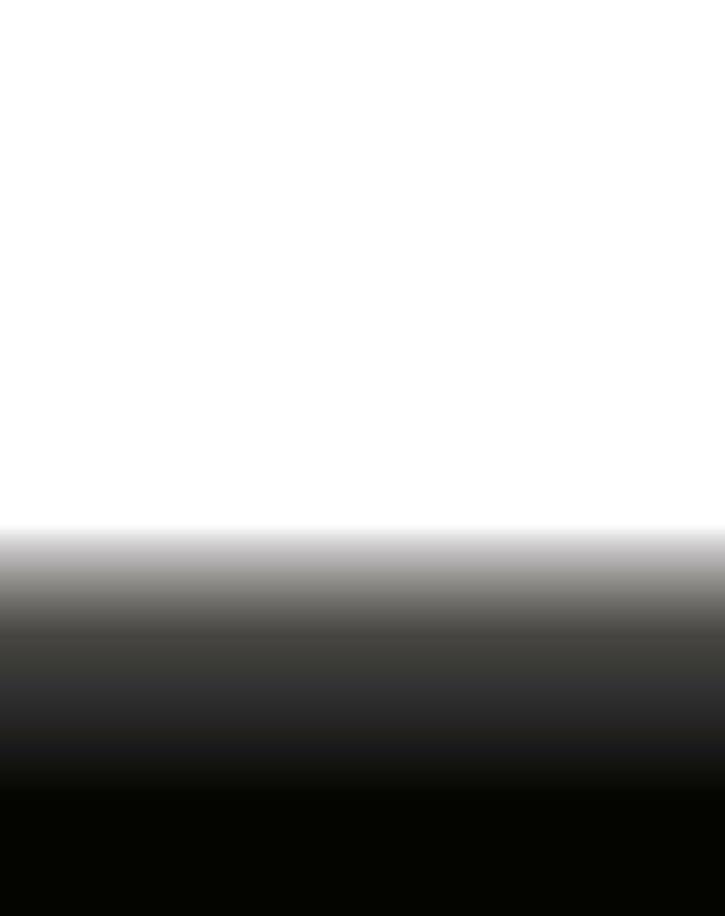
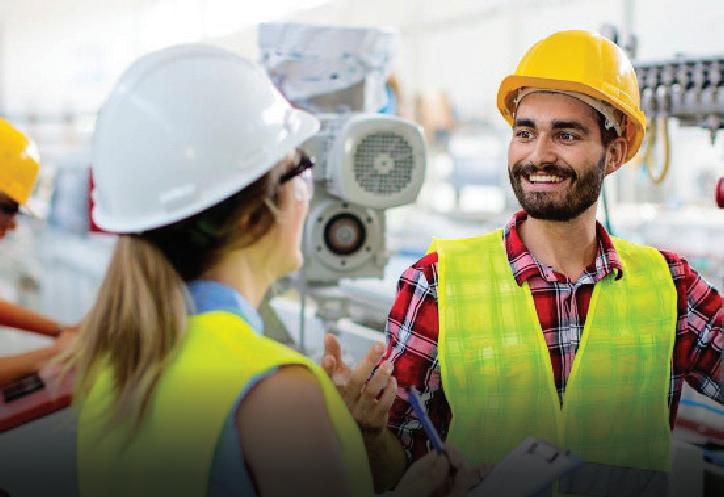
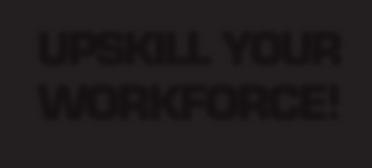
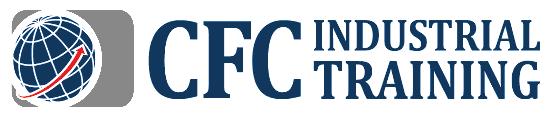
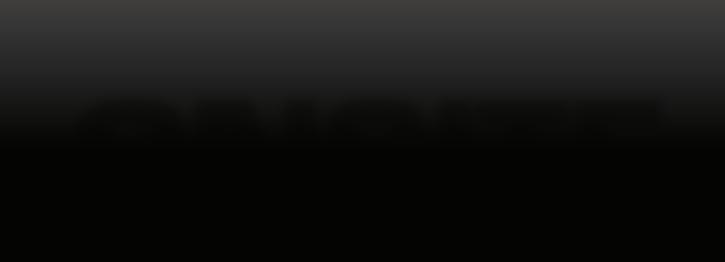
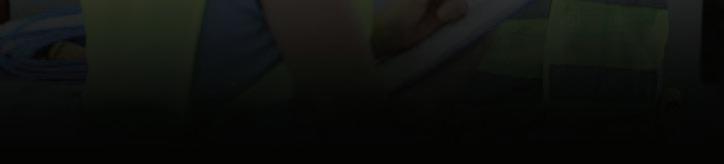




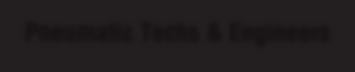
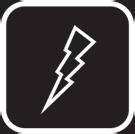
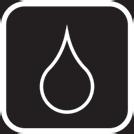


Solutions for E-Vehicles Move from manual to electrical control with minimal design changes and maximum return! ELECTRIFICATION & HYDRAULICS HYD2207-2349www.HYDAC-NA.com | www.HYDAC.com • Our “In pin” angle sensor stays safe and sound on your machine - it’s designed to be integrated inside a hollow pin assembly in the joint of the machine, not externally. • Keeping track of it all, our controllers are available in a wide variety of I/O options for differing levels of complexity. • HYDAC TTControl Displays are characterized by low reflectivity and high color saturations for optimal readability in a variety of conditions.•The HYDAC FLKS-SC series has been specially developed for cooling in mobile applications for electrical drives, inverters, chargers and batteries. In proven design, it is routinely used as a semi-closed cooling circuit in vehicle construction. • The HYDAC HLT 1300 detects linear position and measures pressure and temperature in a single device.

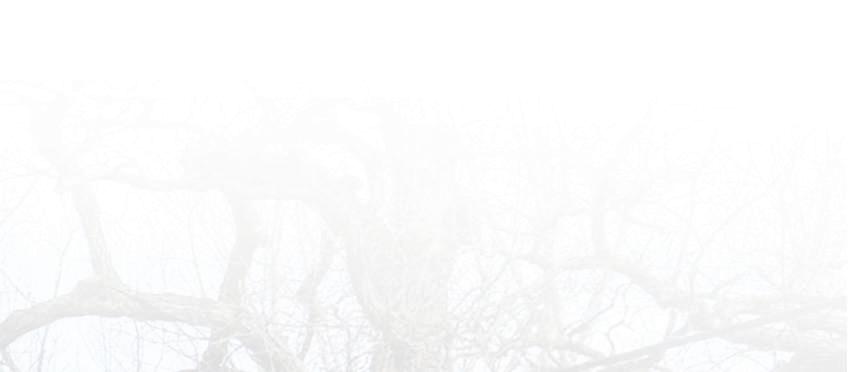
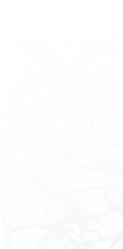
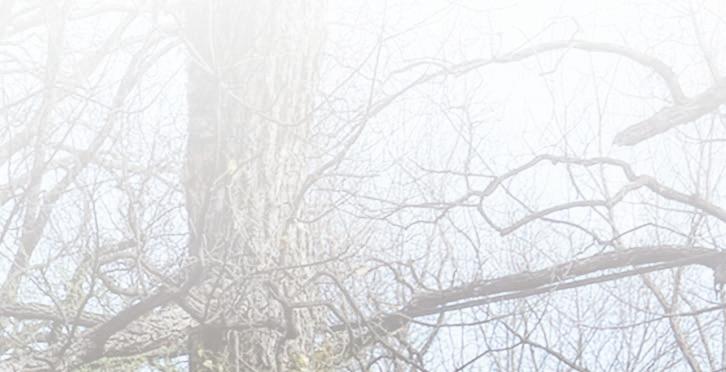

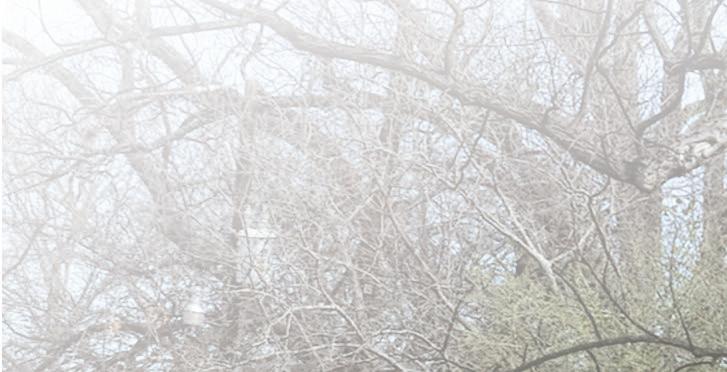
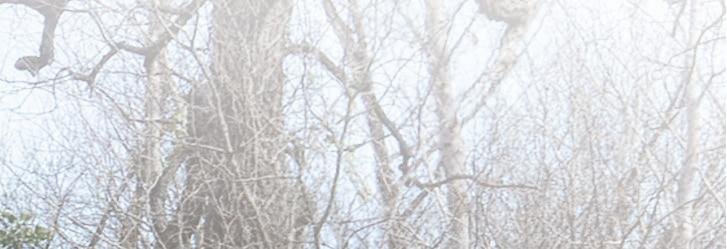
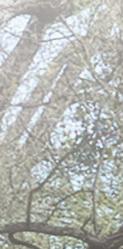

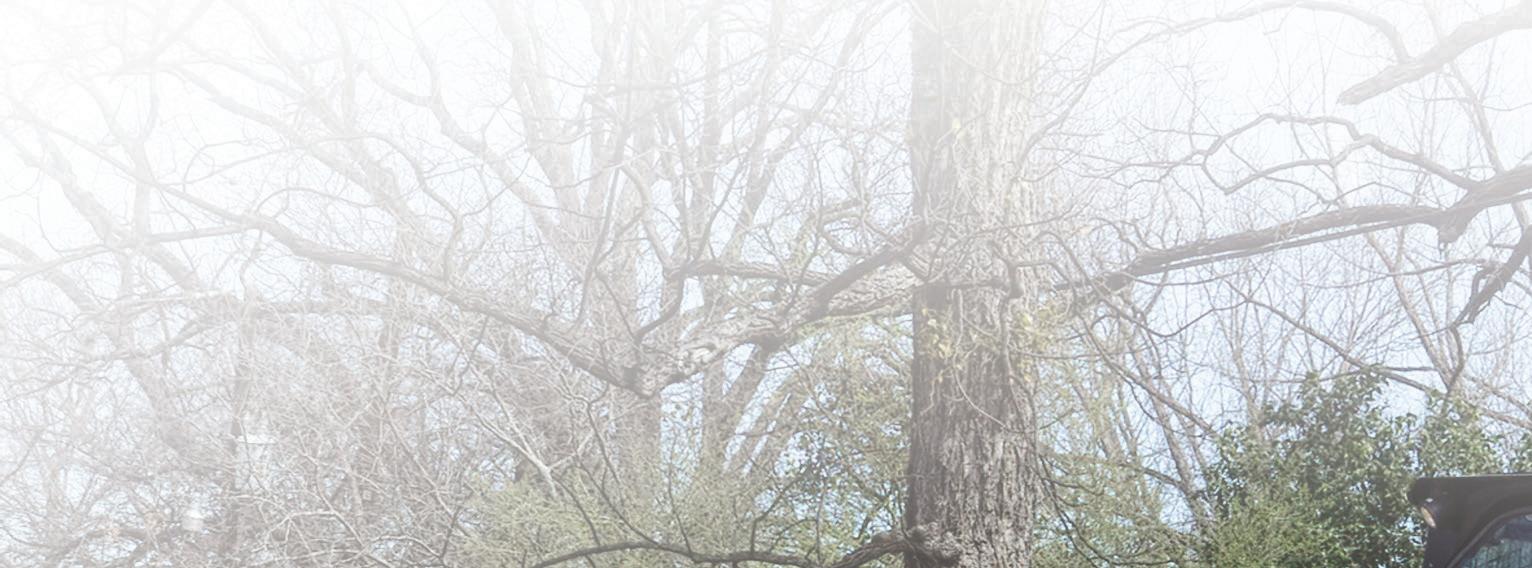

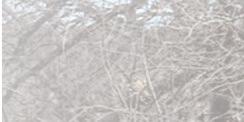

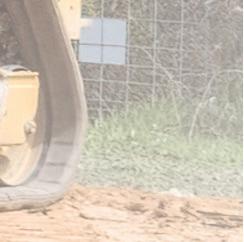

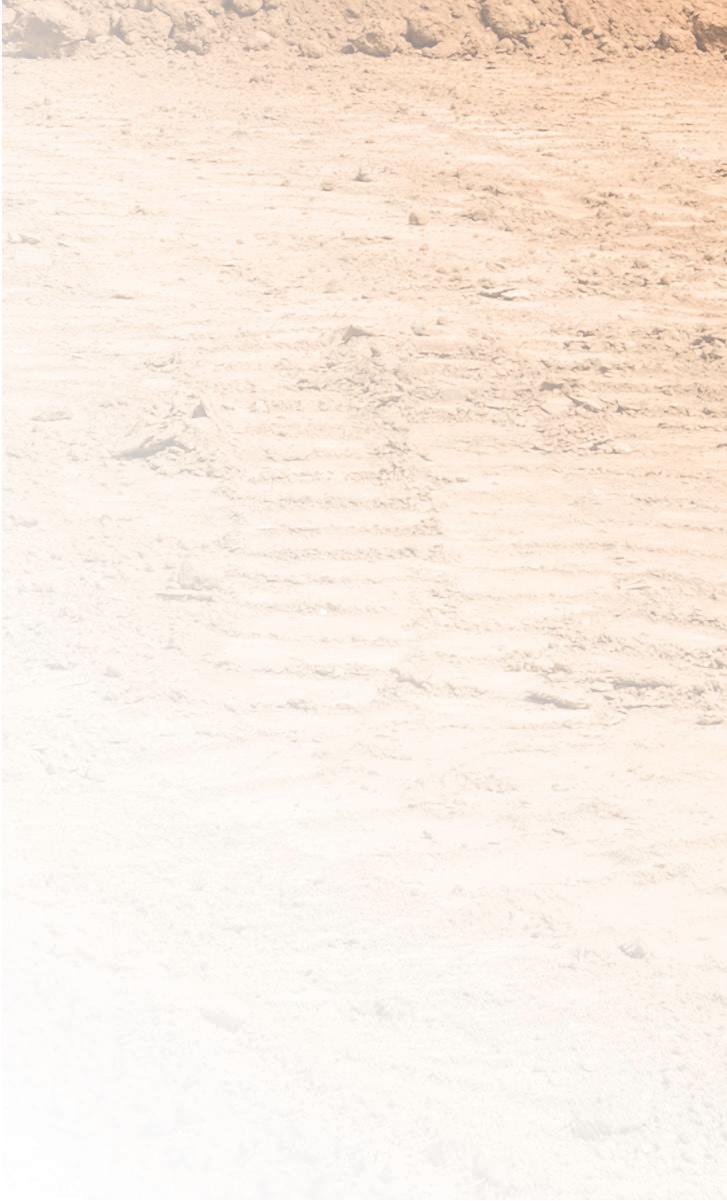
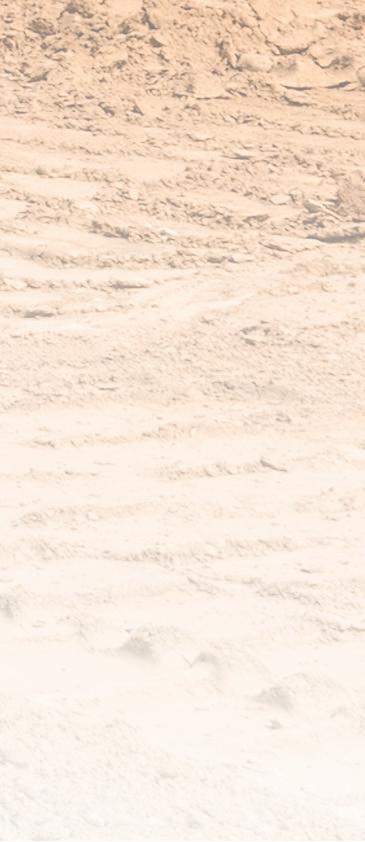

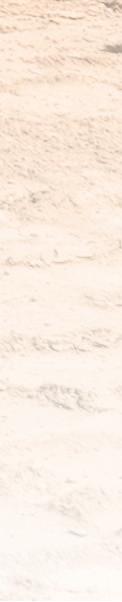
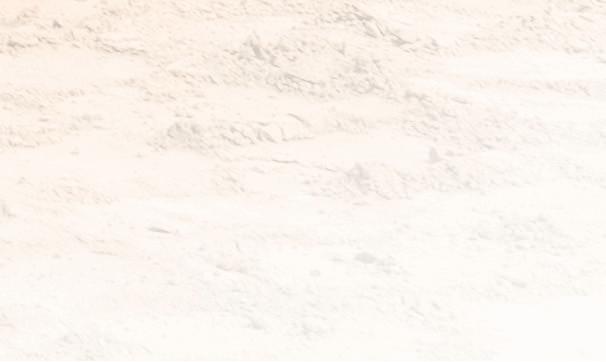
































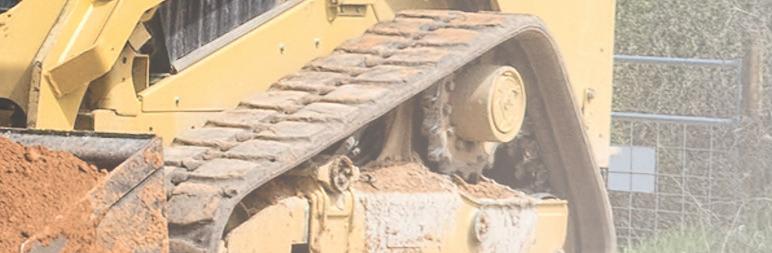




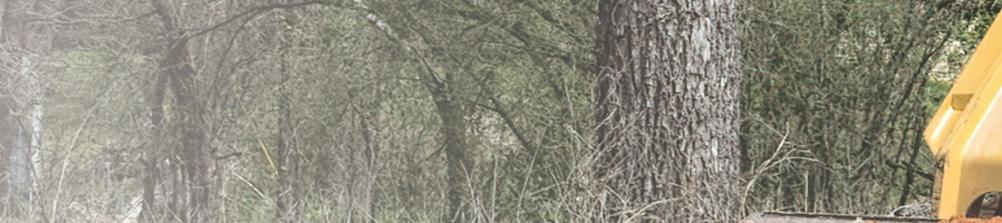







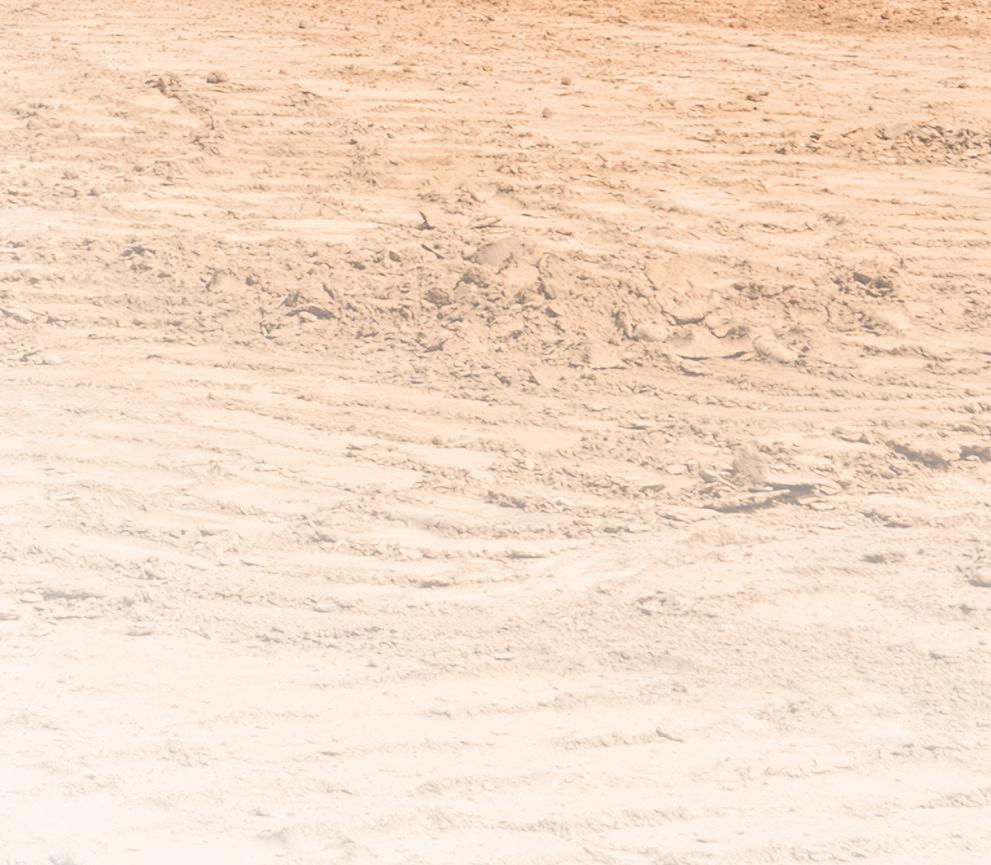

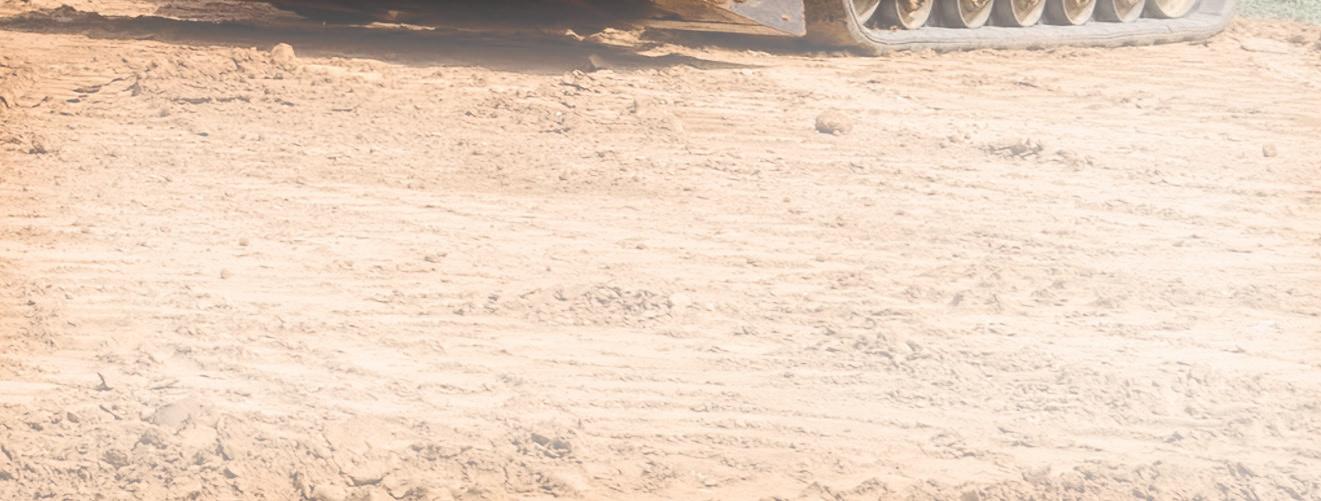



























































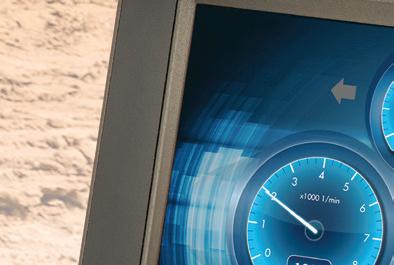

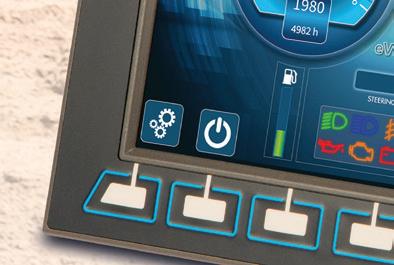



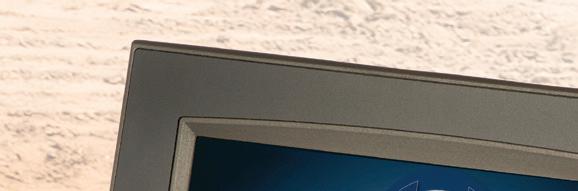
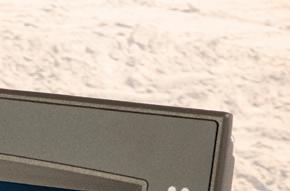
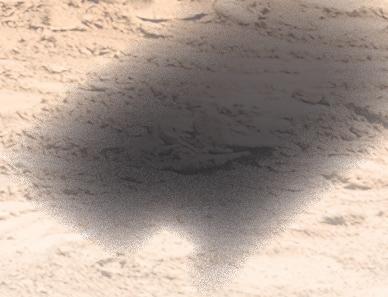
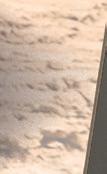
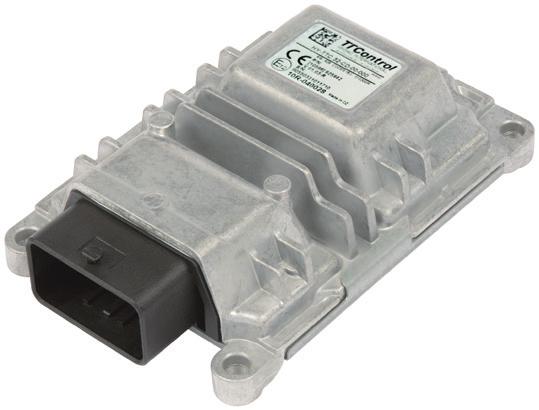
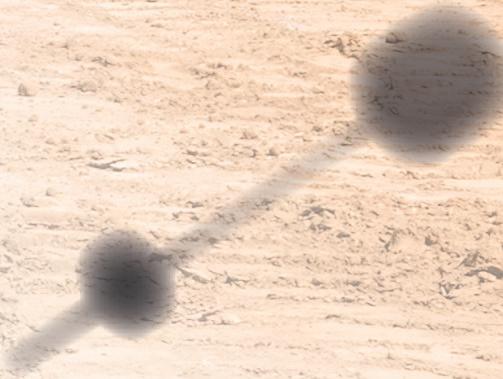
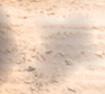
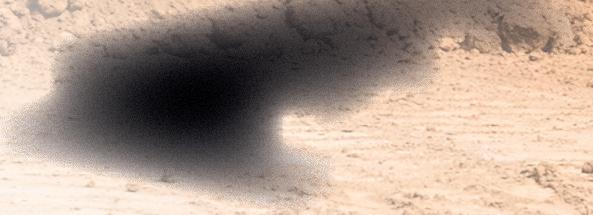
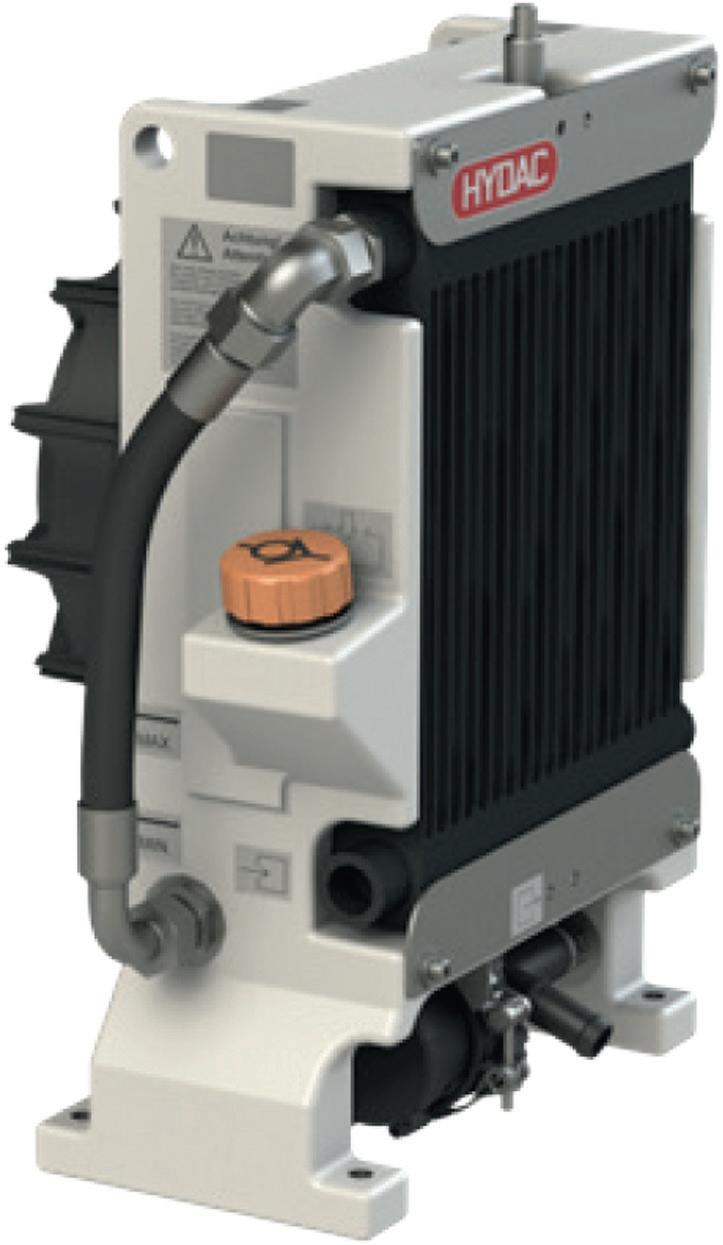

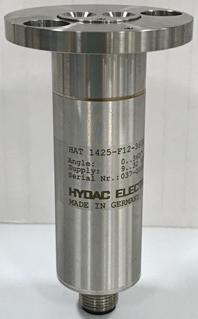
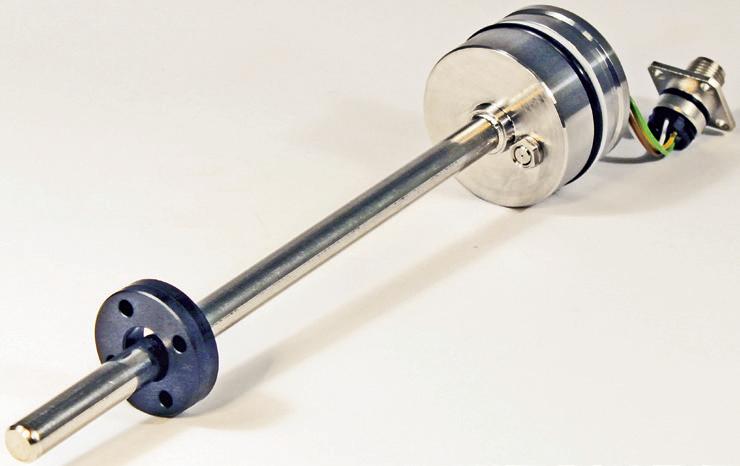
6 FLUID POWER WORLD 8 • 2022 2836404446322022AUGUSTHydraulicsINDUSTRIALFEATURESHYDRAULICSputsthepowerinmachinetools Many unique hydraulic applications offer the power and reliability needed by CNC machines. MOBILE HYDRAULICS A new romance for mobile hydraulics Far from being the threat it once seemed, is a coupling of electronics with hydraulics turning out to be destiny? PNEUMATICS Pneumatics in food packaging These tips not only adhere to food safety guidelines, but also serve to improve machine utilization and performance. SHOW PREVIEWS Pack Expo heads back to the Midwest Pack Expo is scheduled to run from October 23-26 at McCormick Place Convention Center. IMTS is ready for its Chicago comeback IMTS, or the International Manufacturing Technology Show, returns to Chicago September 12-17. Mobile machinery makers head to Munich Construction and mining machinery industry prepared for bauma 2022, set for October 24-30. Contents | vol 9 no 5 | fluidpowerworld.com • 8 • 2022 ON THE COVER Modernized hydraulics, sensing technologies and controls helped the Philadelphia Phillies’ Liberty Bell ring again. | Courtesy of The Phillies/Miles Kennedy asbpe.org NASILVERTIONALAWARD asbpe.org REGIONALSILVERAWARD DEPARTMENTS 02 FluidLines 04 From The Field 10 Korane’s Outlook 12 TroubleshootingChallenge 14 Association Watch 16 Design Notes 24 Fundamentals 26 Energy Efficiency 51 Products 55 Component Focus 56 Ad Index
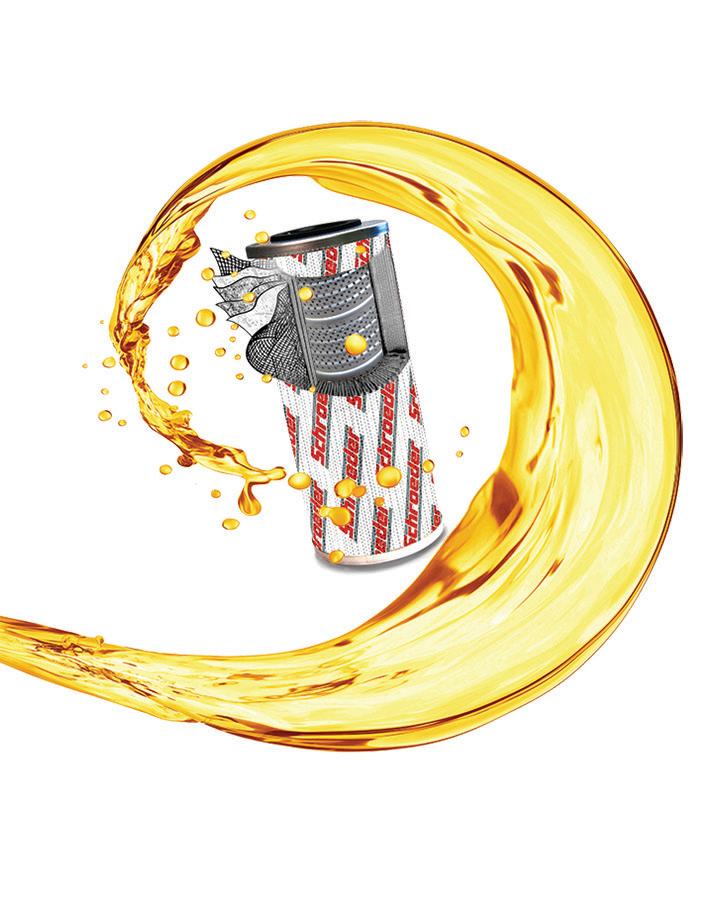
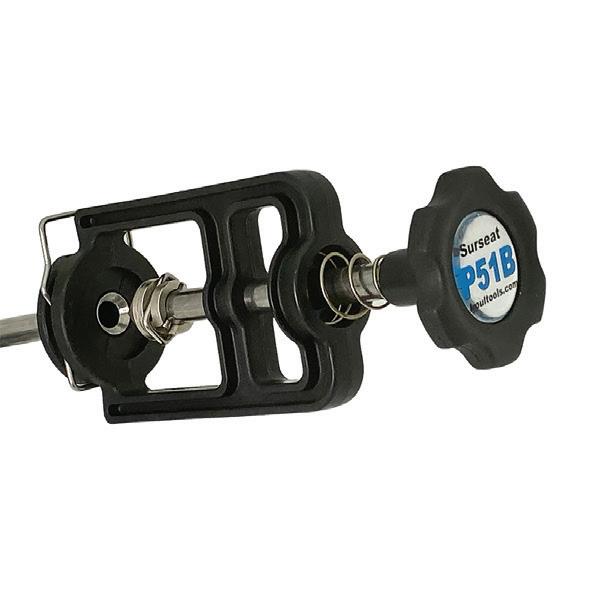


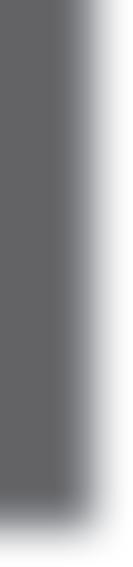

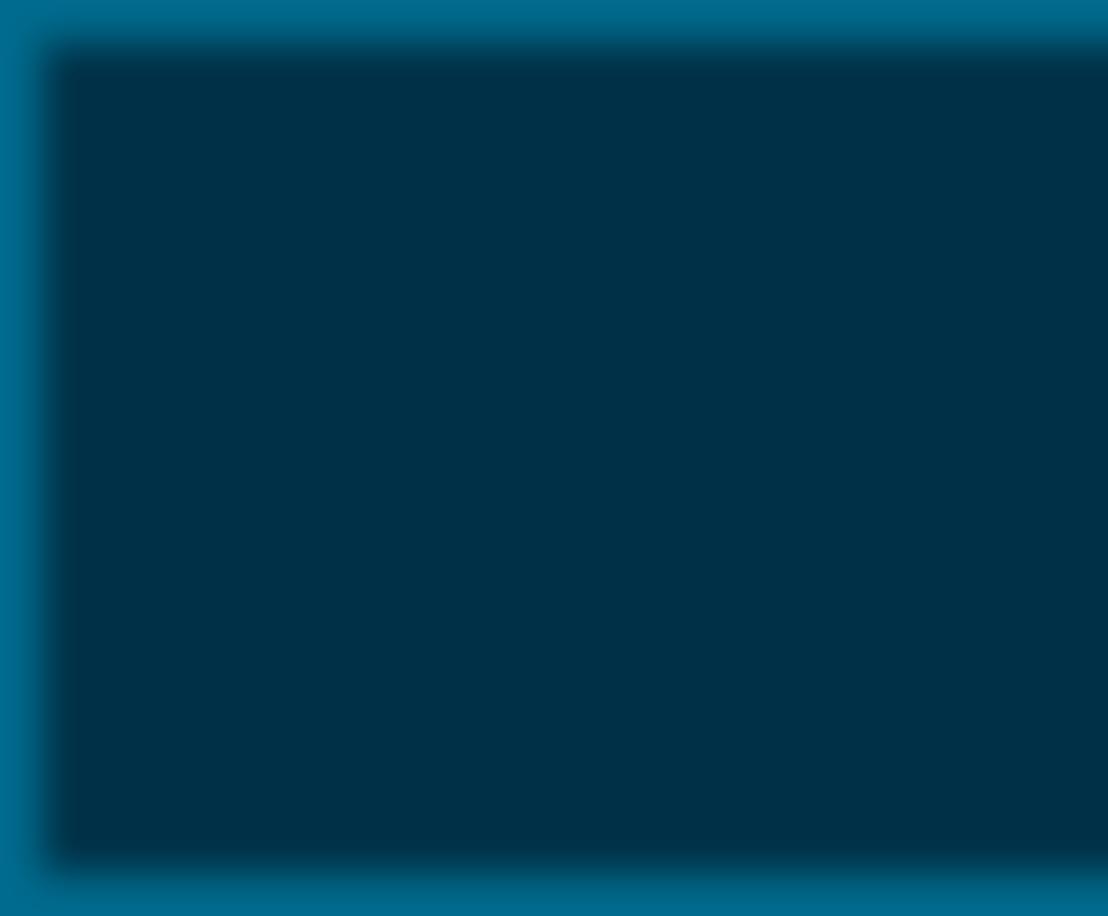
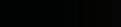


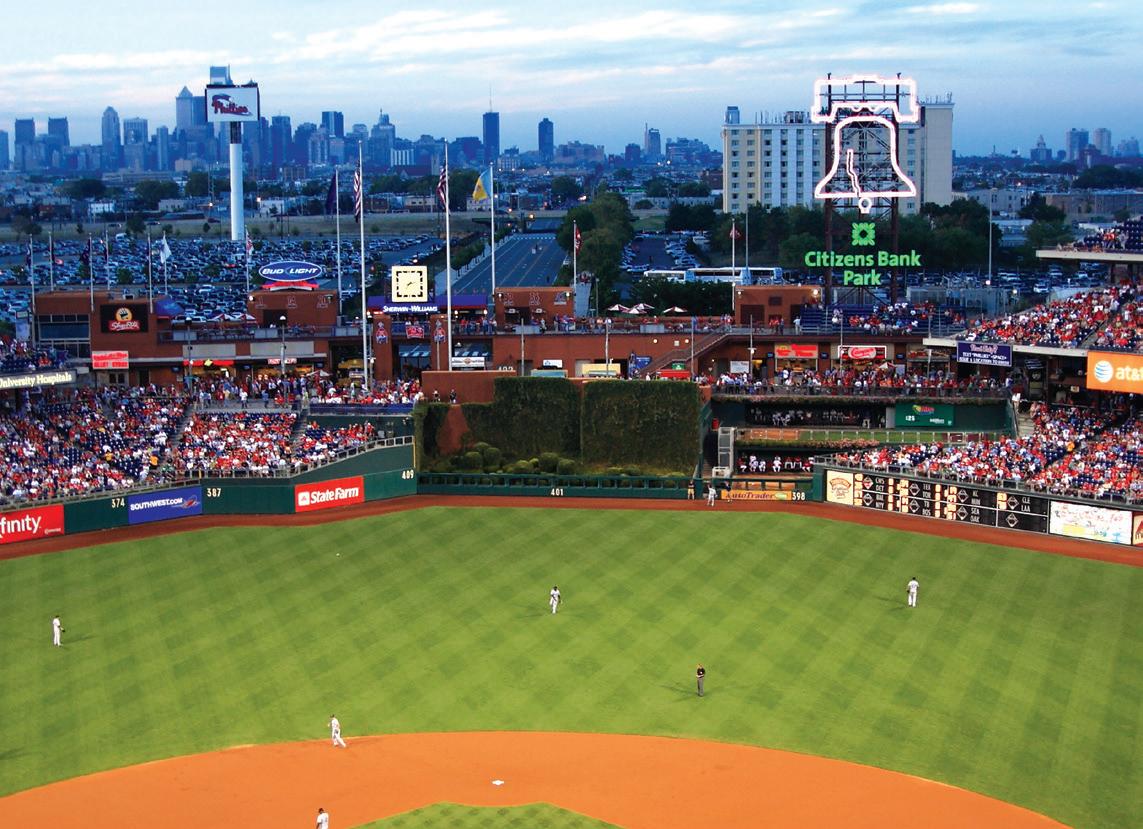
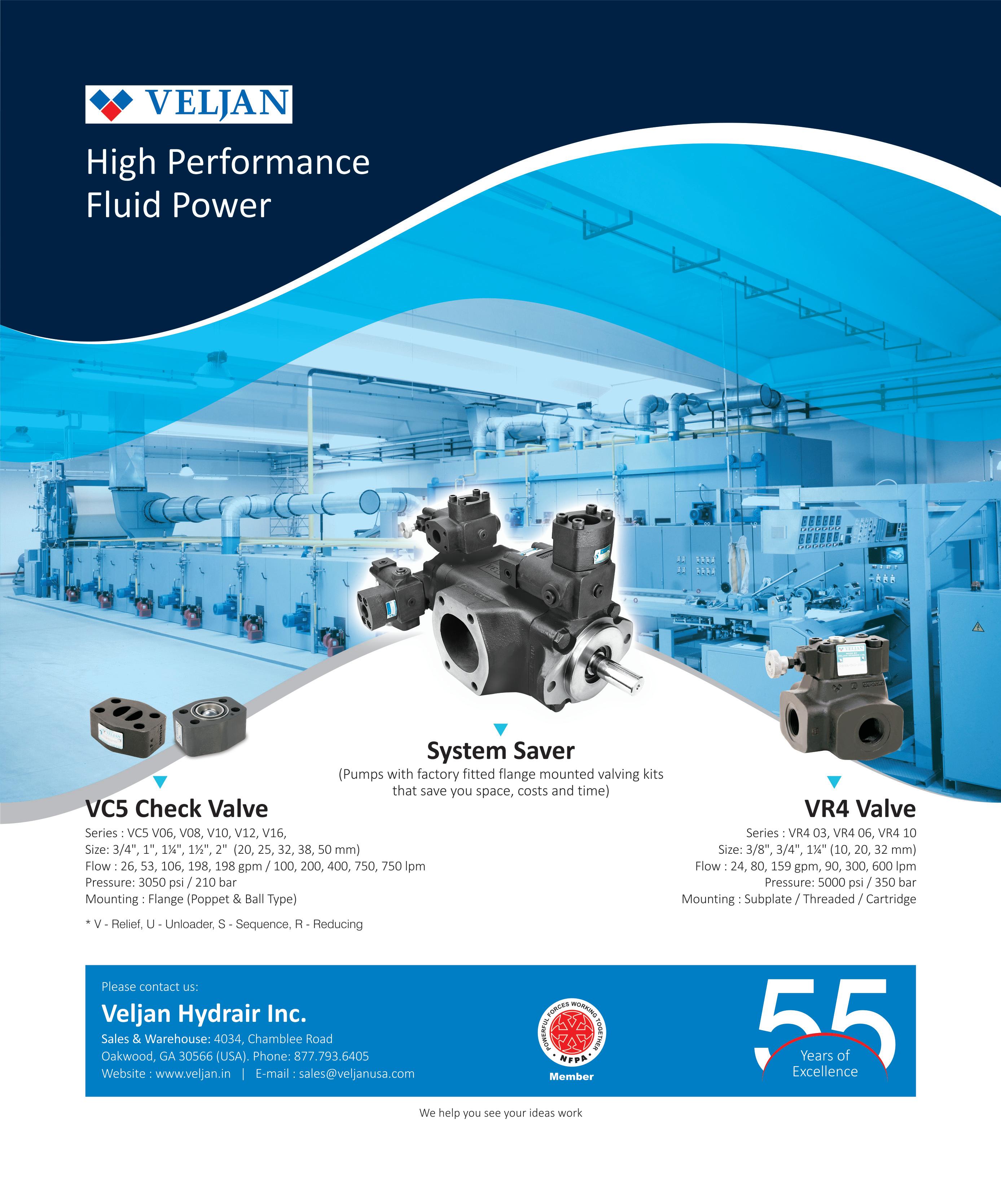
WTWH Media, LLC 1111 Superior Ave., Suite 2600, Cleveland, OH 44114 Ph: 888.543.2447 • Fax: 888.543.2447
FLUID POWER WORLD does not endorse any products, programs or services of advertisers or editorial contributors. Copyright© 2022 by WTWH Media, LLC. No part of this publication may be reproduced in any form or by any means, electronic or mechanical, or by recording, or by any information storage or retrieval system, without written permission from the publisher.
SUBSCRIPTION RATES: Free and controlled circulation to qualified subscribers. Non-qualified persons may subscribe at the following rates: U.S. and possessions: 1 year: $125; 2 years: $200; 3 years: $275; Canadian and foreign, 1 year: $195; only US funds are accepted. Single copies $15 each. Subscriptions are prepaid, and check or money orders only.
VP,EDITORIALEditorial Director Paul J. Heney @wtwh_paulheneypheney@wtwhmedia.com MaryEditor-in-ChiefGannon @dw_marygannonmgannon@wtwhmedia.com Technology Editor Ken Korane @fpw_kenkoranekkorane@wtwhmedia.com Associate Editor Heather Hall @wtwh_heathhallhhall@wtwhmedia.com Associate Editor Mike Santora @dw_mikesantoramsantora@wtwhmedia.com Contributing Editor Josh Cosford @FluidPowerTips Contributing Editor Carl Dyke @carlindustry Contributing Writer Robert Sheaf rjsheaf@cfc-solar.com VirginiaVP,MARKETINGDigitalMarketingGoulding @wtwh_virginiavgoulding@wtwhmedia.com Digital Marketing Manager Taylor Meade @wtwh_taylortmeade@wtwhmedia.com Digital SamanthaMarketingProduction/DesignerKing sking@wtwhmedia.com Marketing Graphic Designer Hannah Bragg hbragg@wtwhmedia.com Webinar Manager Matt Boblett mboblett@wtwhmedia.com Webinar Coordinator Halle Kirsh hkirsh@wtwhmedia.com Webinar Coordinator Kim Dorsey kdorsey@wtwhmedia.com www.nfpa.com AUGUST 2022 • vol 9 no 5 • www.fluidpowerworld.com VIDEO SERVICES Video BradleyManagerVoyten @bv10wtwhbvoyten@wtwhmedia.com GarrettVideographerMcCa erty gmccafferty@wtwhmedia.com KaraVideographerSingleton ksingleton@wtwhmedia.com SALESRyanAshdown rashdown@wtwhmedia.com216-316-6691 Jami Brownlee jbrownlee@wtwhmedia.com224.760.1055 Mary Ann Cooke mcooke@wtwhmedia.com781.710.4659 Jim Powers @jpowers_mediajpowers@wtwhmedia.com312.925.7793 Courtney Nagle @wtwh_CSeelcseel@wtwhmedia.com440.523.1685 ONLINE DEVELOPMENT & WebPRODUCTIONDevelopment Manager B. David Miyares @wtwh_webdavedmiyares@wtwhmedia.com Senior Digital Media Manager Patrick Curran @wtwhseopatrickpcurran@wtwhmedia.com Front End Developer Melissa Annand mannand@wtwhmedia.com Software Engineer David Bozentka dbozentka@wtwhmedia.com Digital Production Manager Reggie Hall rhall@wtwhmedia.com Digital Production Specialist Nicole Lender nlender@wtwhmedia.com Digital Production Specialist Elise Ondak eondak@wtwhmedia.com Digital Production Specialist Nicole Johnson njohnson@wtwhmedia.com VP, Strategic Initiatives Jay Hopper jhopper@wtwhmedia.com FINANCEControllerBrianKorsberg bkorsberg@wtwhmedia.com Accounts JamilaSpecialistReceivableMilton jmilton@wtwhmedia.com IN-PERSON EVENTS Events Manager Jen Osborne @wtwh_jenjkolasky@wtwhmedia.com Event Marketing Specialist Olivia Zemanek ozemanek@wtwhmedia.com Event Marketing Coordinator Alexis Ferenczy aferenczy@wtwhmedia.com PRODUCTION SERVICES Customer Service Manager Stephanie Hulett shulett@wtwhmedia.com Customer TracyRepresentativeServicePowers tpowers@wtwhmedia.com Customer JoAnnRepresentativeServiceMartin jmartin@wtwhmedia.com Customer ReneeRepresentativeServiceMassey-Linston renee@wtwhmedia.com PRINT PRODUCTION VP, Creative Services Mark Rook @wtwh_graphicsmrook@wtwhmedia.com Senior Art Director Matthew Claney @wtwh_designermclaney@wtwhmedia.com Senior Graphic Designer Allison Washko @wtwh_allisonawashko@wtwhmedia.com Graphic Designer Mariel Evans @wtwh_marielmevans@wtwhmedia.com Director, Audience Development Bruce Sprague bsprague@wtwhmedia.com Don’t compromise! Use MAIN Manufacturing Products, Inc. as your source for hydraulic flanges Dependable - 60 yrs service Informed - members of SAE & NFPA tech committees Quick - Thousands in stock specials can be 3-4 days MAINInfo@MainMfg.comGrandProducts,ManufacturingInc.Blanc,MIUSA800.521.7918MAINMfg.com SAE 4-bolt, JIS, DIN, ISO standard & special adapters Socket and Butt weld, NPTF BSPT, ORB, BSPP, 6149, etc. Materials: Carbon, 304L, 316L, duplex, Cu-NI, ductile, alum. etc. In-line, el, tee, F, blind, cross, reducing, flange heads Made in USA tompkinsind.com800-255-1008ALWAYS ADAPTING. TOUGHER WITH EVERY TEST. 8 FLUID POWER WORLD 8 • 2022 2011- 2020 FLUID POWER WORLD does not pass judgment on subjects of controversy nor enter into dispute with or between any individuals or organizations. FLUID POWER WORLD is also an independent forum for the expression of opinions relevant to industry issues. Letters to the editor and by-lined articles express the views of the author and not necessarily of the publisher or the publication. Every effort is made to provide accurate information; however, publisher assumes no responsibility for accuracy of submitted advertising and editorial information. Noncommissioned articles and news releases cannot be acknowledged. Unsolicited materials cannot be returned nor will this organization assume responsibility for their care.
2013- 20172014- 2016 2014 Winner
SUBSCRIBER SERVICES: To order a subscription please visit our web site at www.fluidpowerworld.com
POSTMASTER: Send address changes to: Fluid Power World, 1111 Superior Ave., Suite 2600, Cleveland, OH 44114
FLUID POWER WORLD (ISSN 2375-3641) is published seven times a year: in February, April, June, July, August, October, and December by WTWH Media, LLC; 1111 Superior Ave., Suite 2600, Cleveland, Ohio 44114. Periodicals postage paid at Cleveland, OH & additional mailing offices.



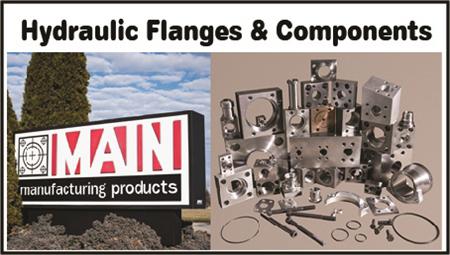
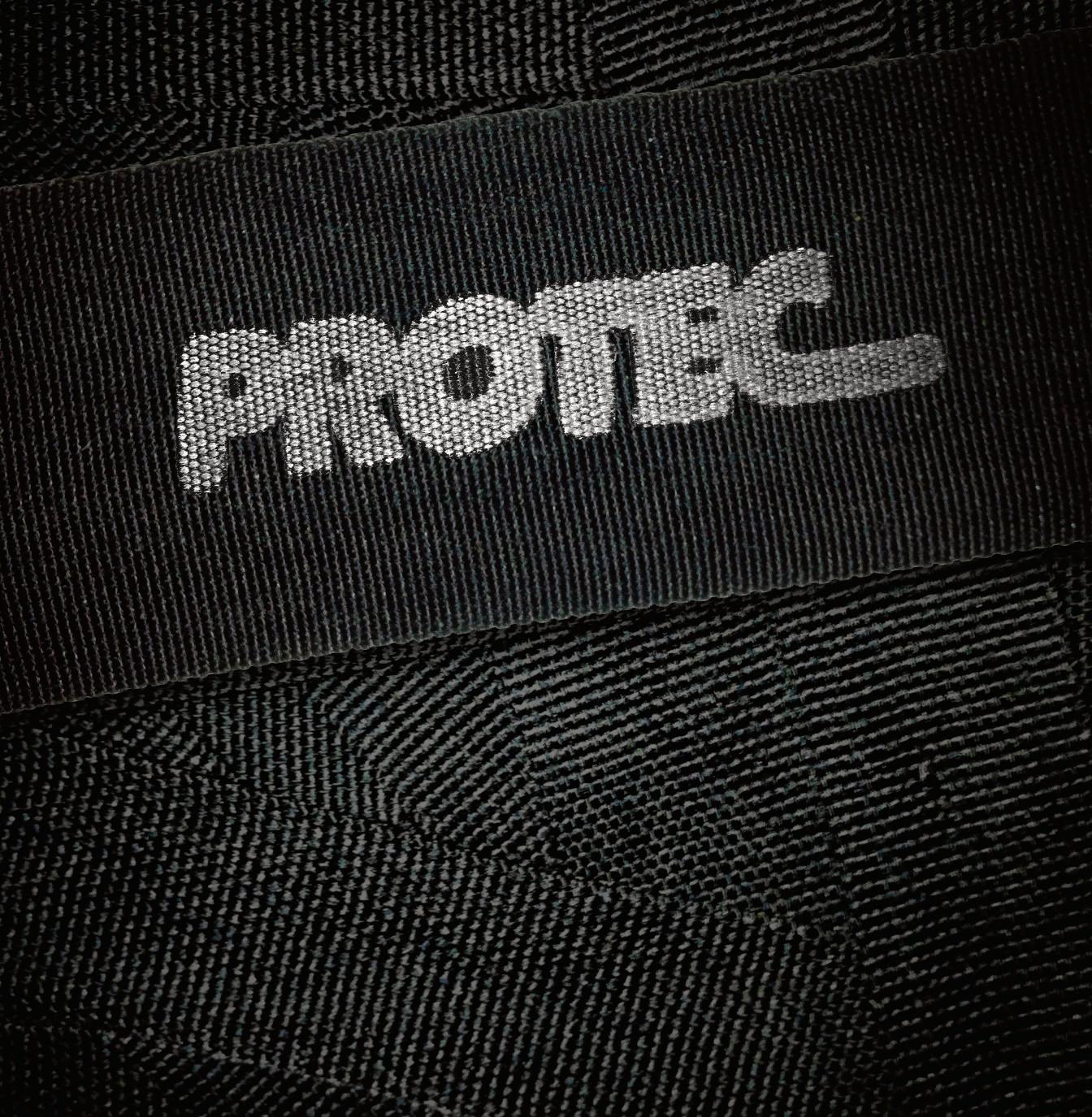


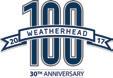





Industries Served: • Oil & Gas • Industrial Hydraulics • Mining • Forestry • Chemical & General Processing Plants • Medical • Aerospace • Factories • Mobile Equipment • Defense • Machine Tool • Testing Equipment • Ocean Depth Technology • Automotive • Food Processing • Agriculture • Industrial • Aviation • Petrochemical • Marine • Subsea DELAWARE MANUFACTURING INDUSTRIES CORPORATION Solutions Under Pressure ISO 9001 Certified Check Valves Bar & ManifoldsCustomMedium-HighPressureValvesLow SuctionPressureValves Flow NeedleControlValves SAE Port Flanges Subsea & Gas Valves Specialty Valves SSW Power Unit System 800.248.DMIC(3642) • WWW.DMIC.COM • SALES@DMIC.COM Made In America Tank Accessories Ball TransferSSWPressureBarFlangesNeedleFlowCheckValvesValvesControlValvesValves&Adapters&CustomManifoldsGauges&SnubbersPowerUnitSystemsPumps
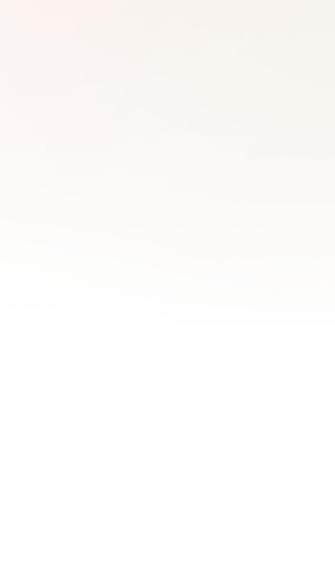
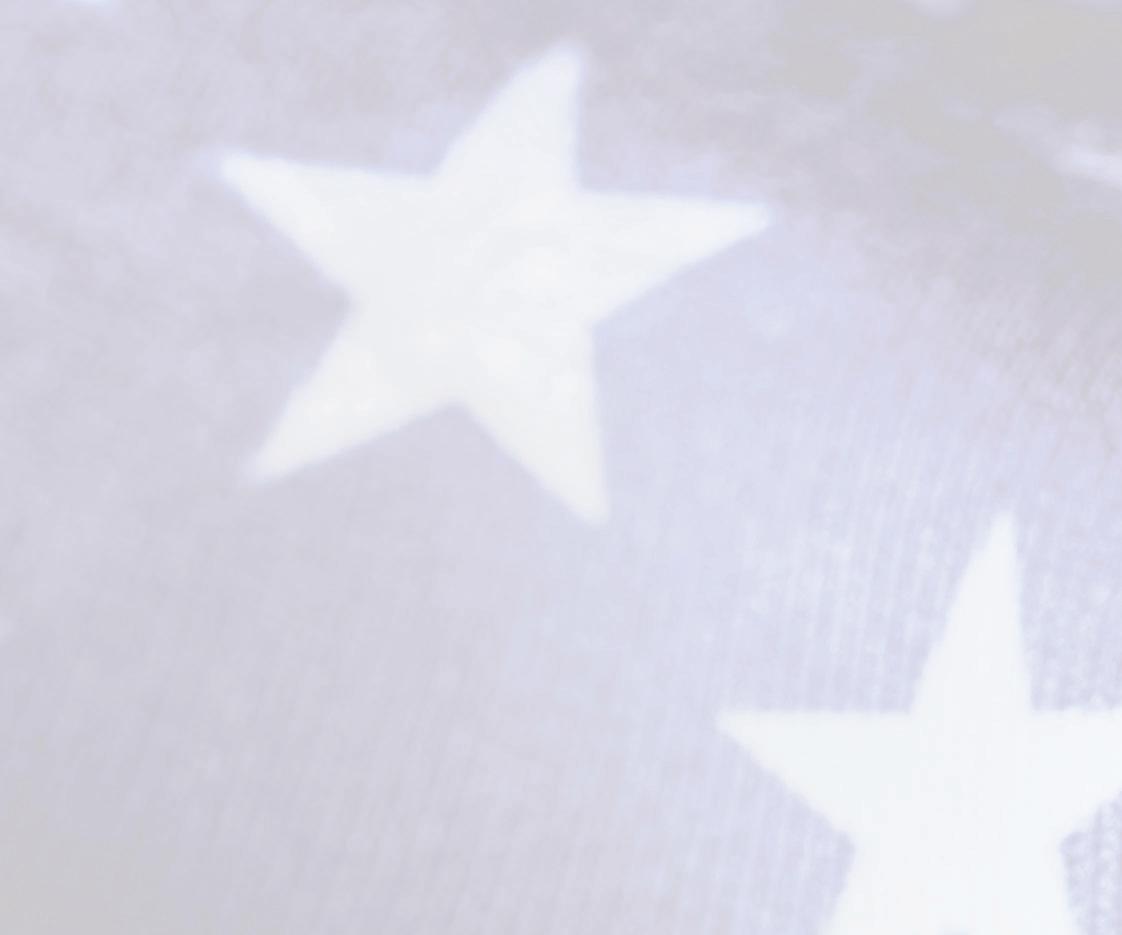
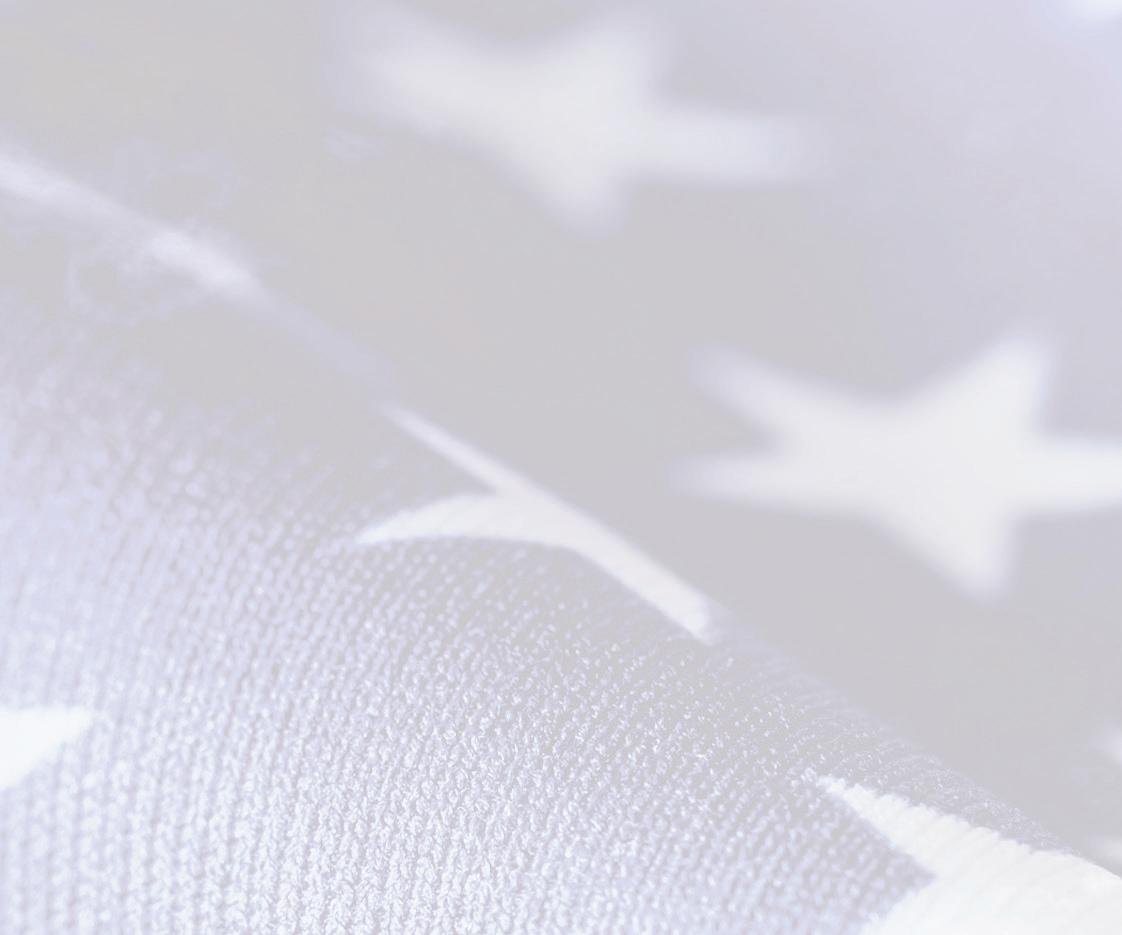


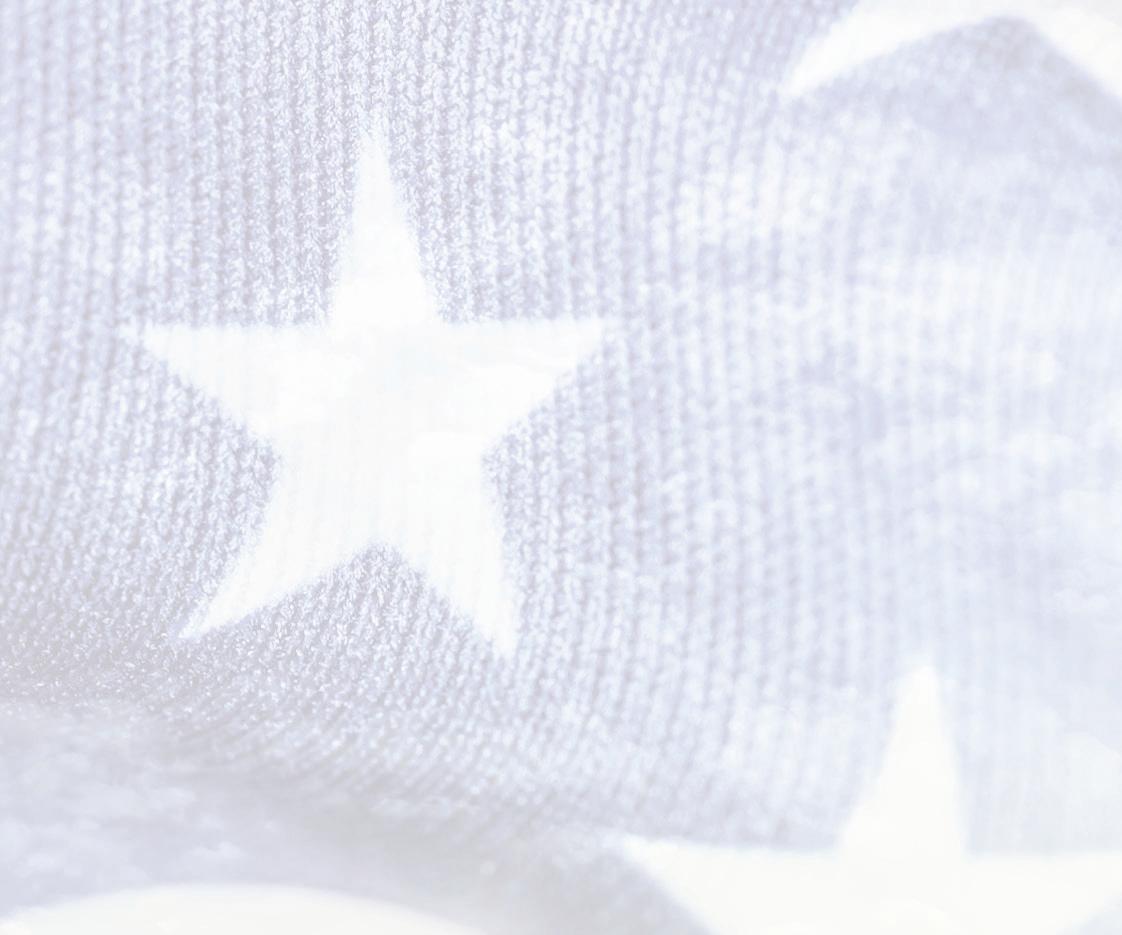
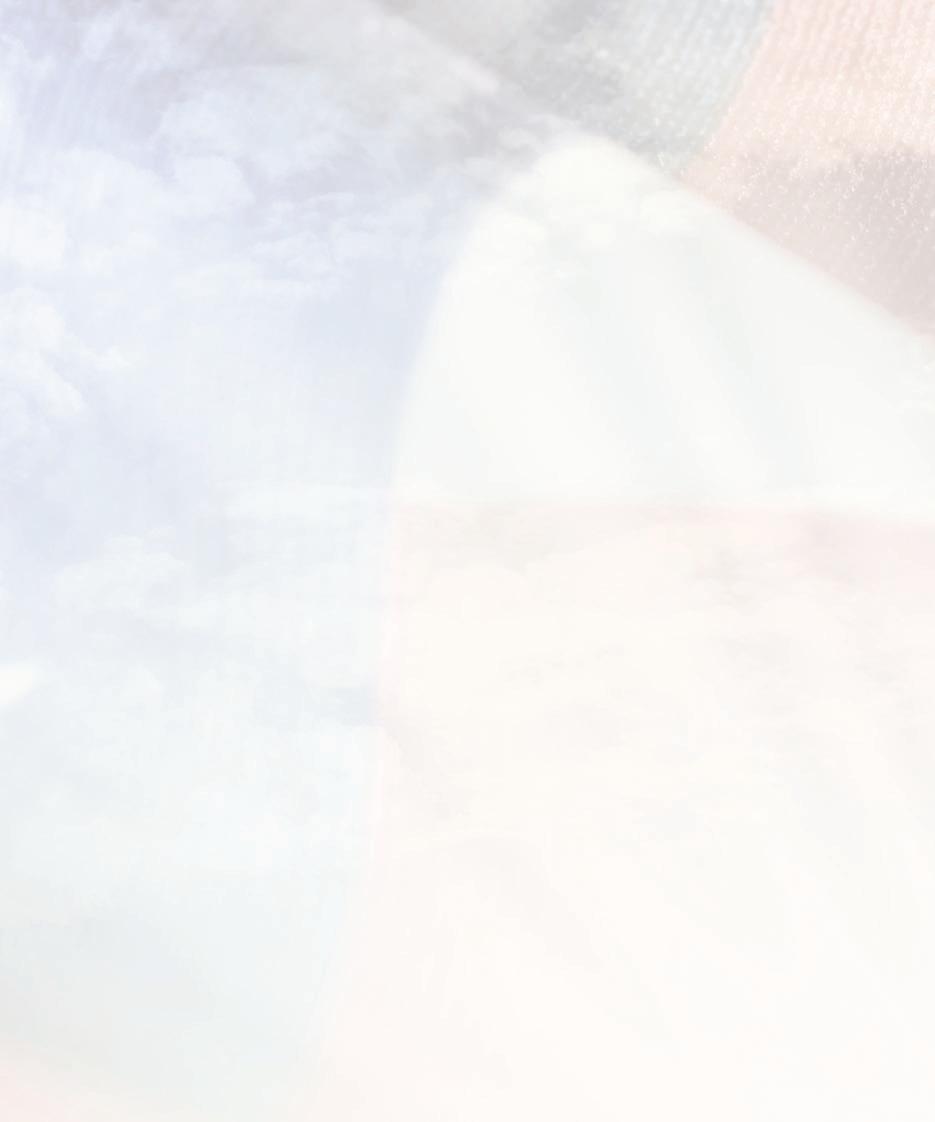
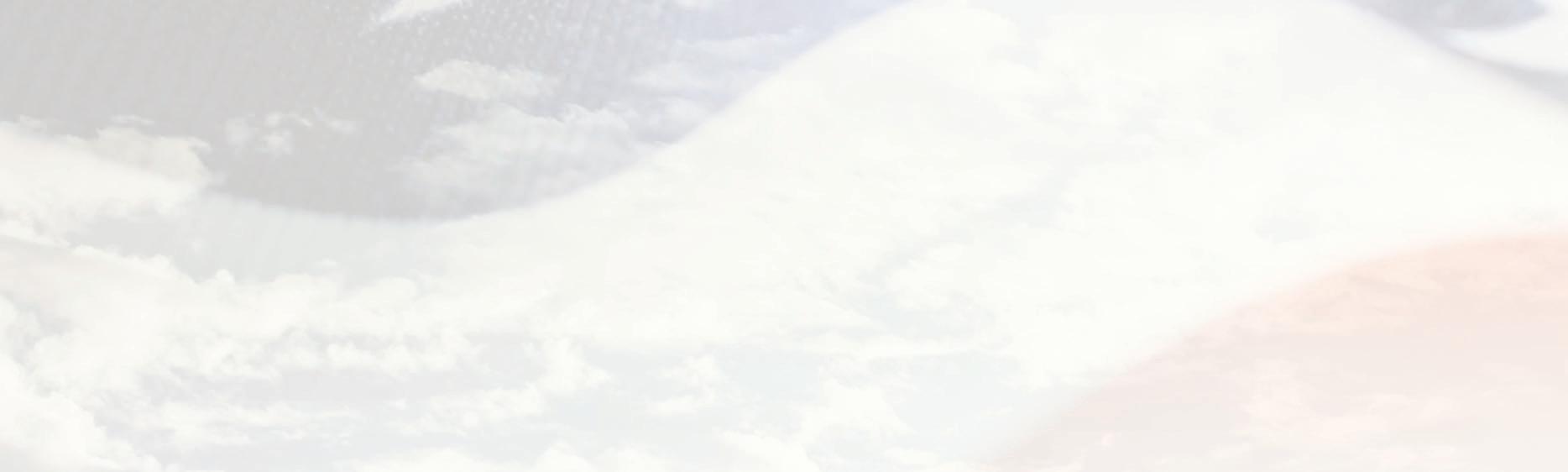
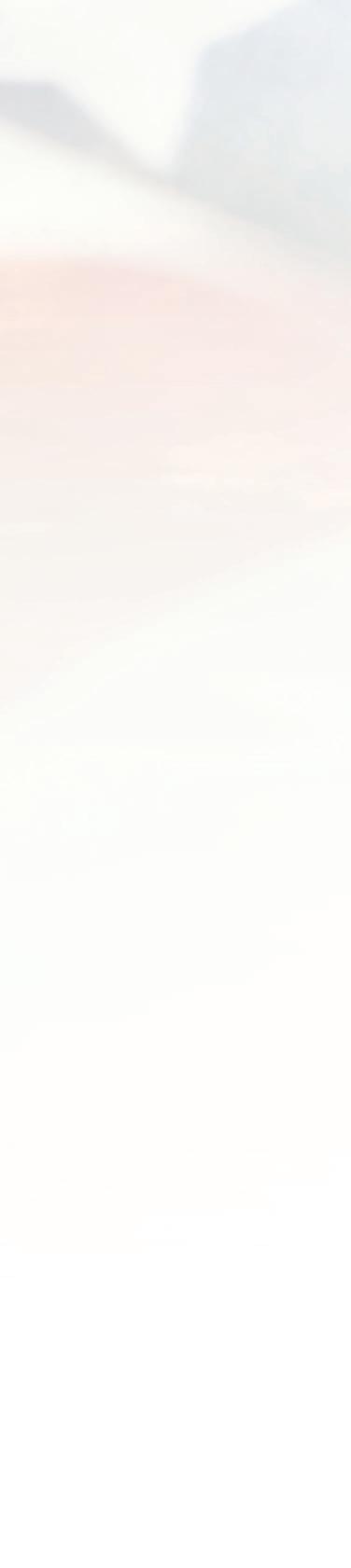

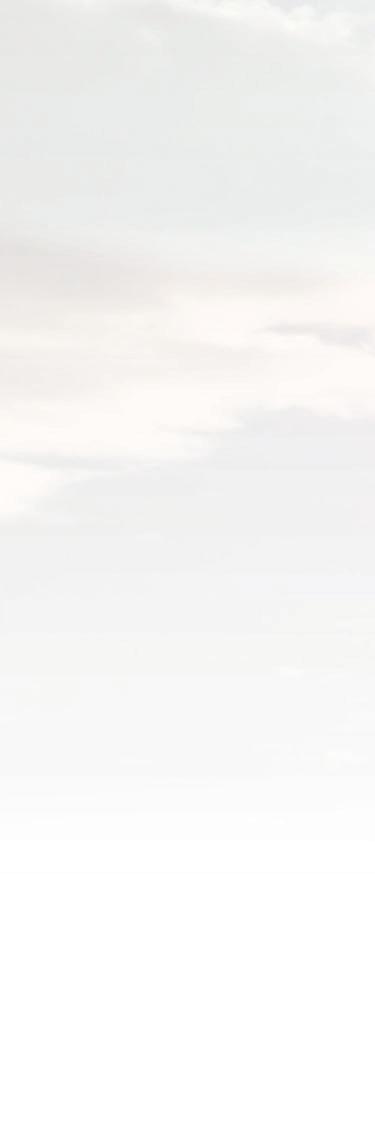
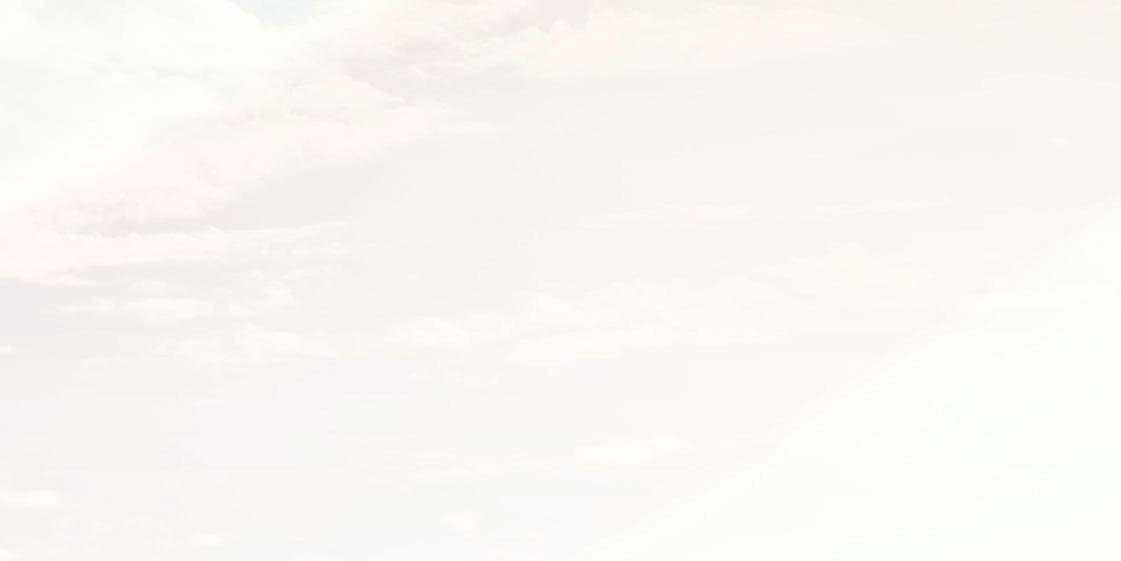
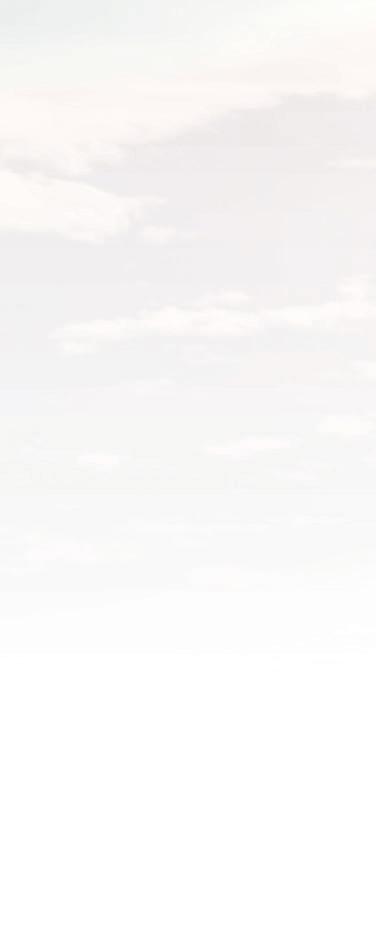

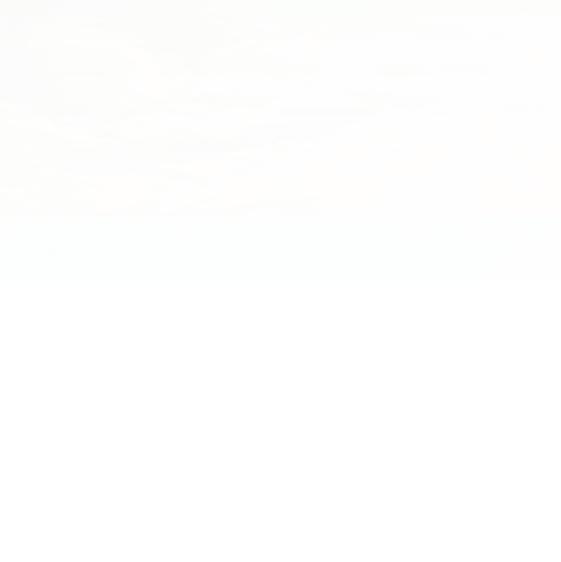
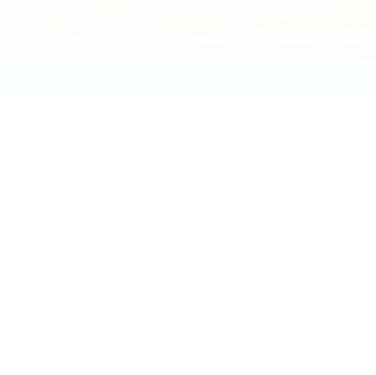
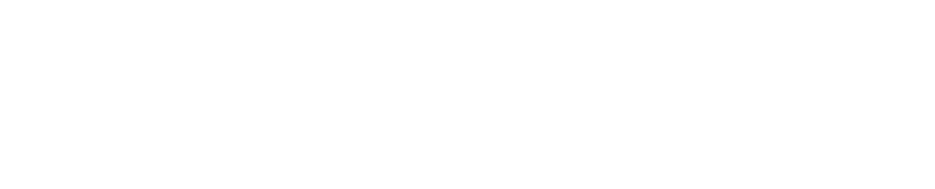

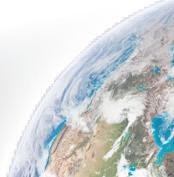
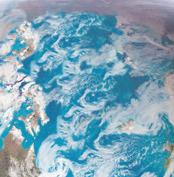
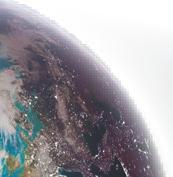
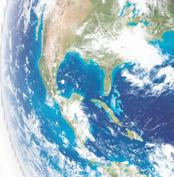

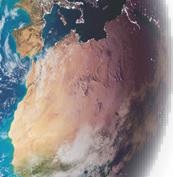
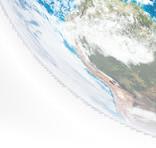

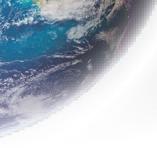
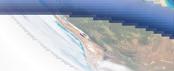
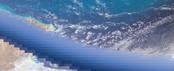
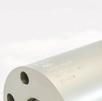
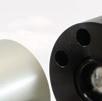
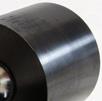
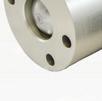
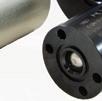




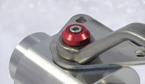

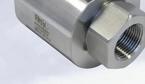

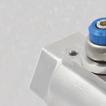
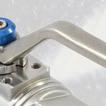

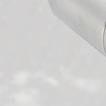
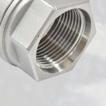
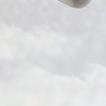
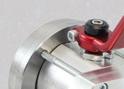

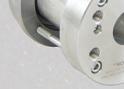

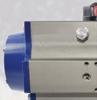
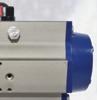
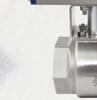
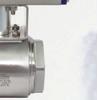

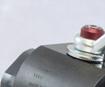
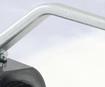
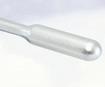
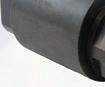
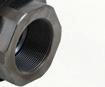
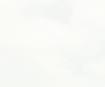
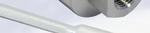
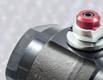
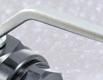
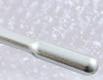

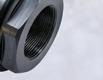
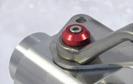
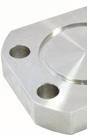
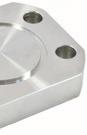

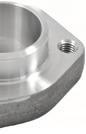
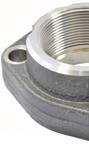

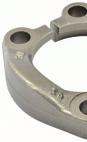
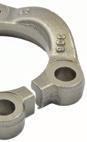
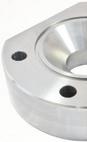
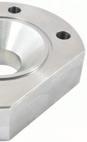
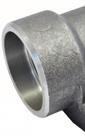

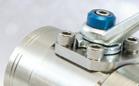
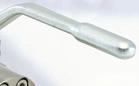
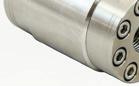
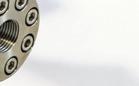
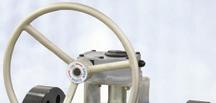
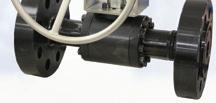
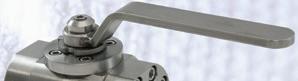
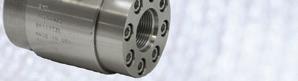



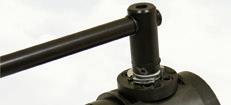
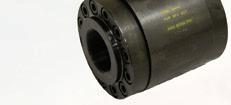
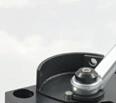
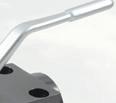
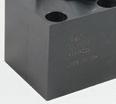
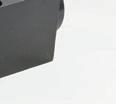
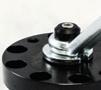
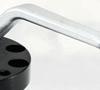
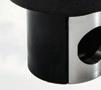
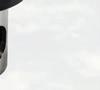
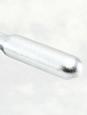

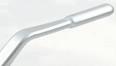

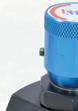
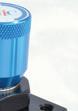
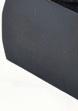
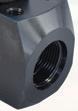
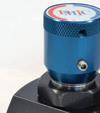


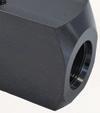
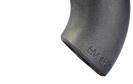
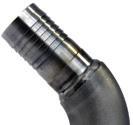

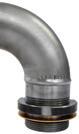
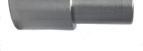
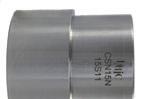
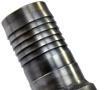


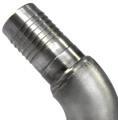
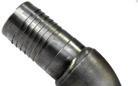
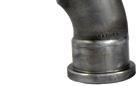
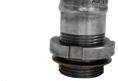
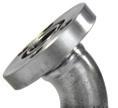
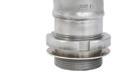
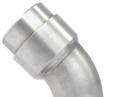




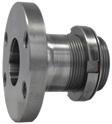


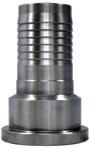
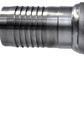
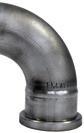











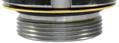
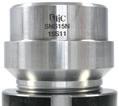
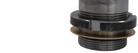
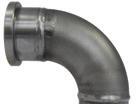
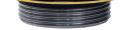
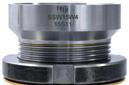
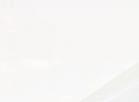
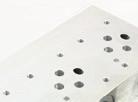
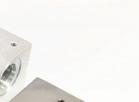
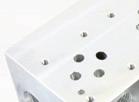
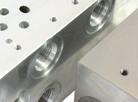

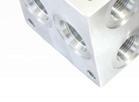
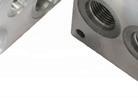
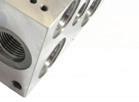
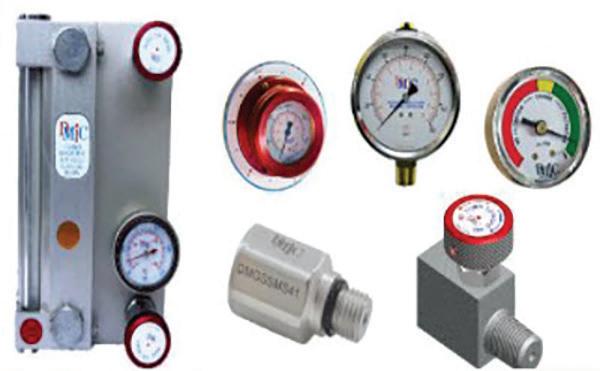

10 FLUID POWER WORLD 8 • 2022 www.fluidpowerworld.com
FPW
Thanks to financial and technical support from Parker Hannifin, Vacca’s team spent countless hours to develop a next-generation trainer that overcomes many of these limitations. The Purdue hydraulic trainer includes a touchscreen display, numerous position, pressure, flow and speed sensors, and electronically control valves, along with a pressure- or flow-controlled supply. With it, users can explore wide-ranging control options like velocity, force, torque and position control; resistive and overrunning loads; and set-ups with single or multiple actuators. The result is more than 50 lab experiences covering basic to advanced mobile and industrial hydraulic concepts — everything from load-sensing systems and proportional hydraulics to troubleshooting for aeration or cavitation. The design proved to be a success with students. Nonetheless, the trainers are available to relatively few users, and cost and space are still issues. And it doesn’t meet today’s expectation that students should be able to learn on a computer. If we don’t accept that, we won’t get the new generation to be passionate about fluid power technology, said Vacca. There are several E-learning software packages on the market that attempt to simulate systems, but they don’t offer a hands-on experience. Thanks to extensive development and programming work, Vacca’s team has created the Maha virtual hydraulic trainer to bridge that gap. The sophisticated virtual reality tool exactly replicates the physical Purdue hydraulic trainer — even to the point of generating sound effects based on noise recorded under actual operating conditions. It uses object-oriented programming and a graphical user interface that lets students follow schematics, connect components, decide on measurement points and sensor placement, and so on. And then run simulations and generate technical reports. How well does it work? Since 2020, over 90% of undergraduate and graduate students gave it positive reviews. The virtual trainer requires much less space, is economical, safe, and available to many more users. Plus it’s pandemic proof. Modern hydraulic trainers help fulfill the goal of attracting engineering students to the fluid power discipline, said Vacca. The Purdue hydraulic trainer is available to universities, thanks to Parker Hannifin; and a version of the virtual trainer is ready for distribution.
Nearly 30 years ago, the late Bob Koski of Sun Hydraulics made a provocative presentation titled “Fluid Power Education – What went wrong?” He noted that every mechanical and electric engineer learns about electrical power actuation and motion control, but only about 5% of mechanical engineering graduates learn about fluid power actuation and control.
Overcoming the roadblocks to fluid power education
The technological vacuum that resulted, he said, makes it difficult to convince potential users of the advantages that fluid power offers over alternative means of mechanical power transmission. That pretty much still holds true today. Prof. Andrea Vacca, Maha Fluid Power Faculty Chair at Purdue Univ., is trying to overcome such hurdles with innovative ways to teach fluid power to the new generation of engineers. One fundamental problem is a lack of up-todate fluid power textbooks, as most are at least a decade old. Vacca and Dr. Germano Franzoni recently authored “Hydraulic Fluid Power” to fill that void. The content not only focuses on basic principles, components, and the design of complete hydraulic circuits, it also delves into practical concepts for controlling state-of-the-art systems. Print and E-book versions are available at www.wiley.com and Amazon. Another challenge is that many universities shy away from fluid power because teaching it requires large and expensive labs. In addition, fluid power can be seen as a design discipline and unfortunately, design classes have been eliminated from the curriculum of many schools or relegated to electives and special or senior-level projects. Yet academic and industry leaders agree we need flexibility and hands-on experience to teach fluid power. So one bottleneck lies in the design and cost of modular fluid power training platforms, or simply trainers. “The problems with current trainers are that they take up a lot of space, they’re expensive, safety can be an issue, and the experience for students in many of them is not that great,” said Vacca. Most don’t give the perception of the latest technology, and they’re not versatile enough to encompass a wide range of experiences. Commercial trainers tend to be professionally built and are good for simple circuits and troubleshooting. But they offer limited flexibility and aren’t particularly user-friendly.
KORANE’S OUTLOOK Ken Korane • Technology Editor
Hydraulic Fluid Power offers a contemporary look at how to design and operate the latest cost-effective and highly efficient systems.
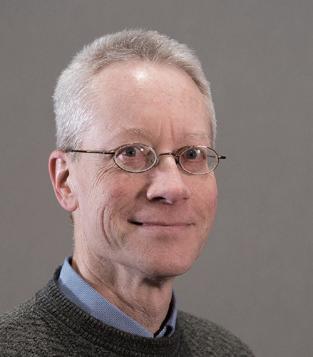
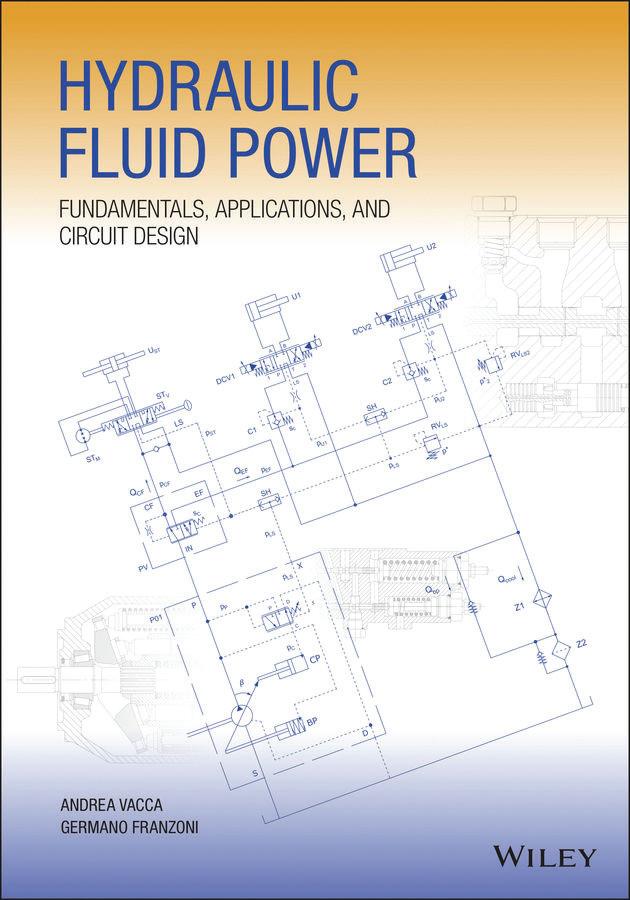
WE’RE GIVING MOREYOUKamanFluidPower’sParkerStores are now Mi Fluid Power Solutions. MORE CHOICES. MORE INVENTORY. MORE EXPERTISE.
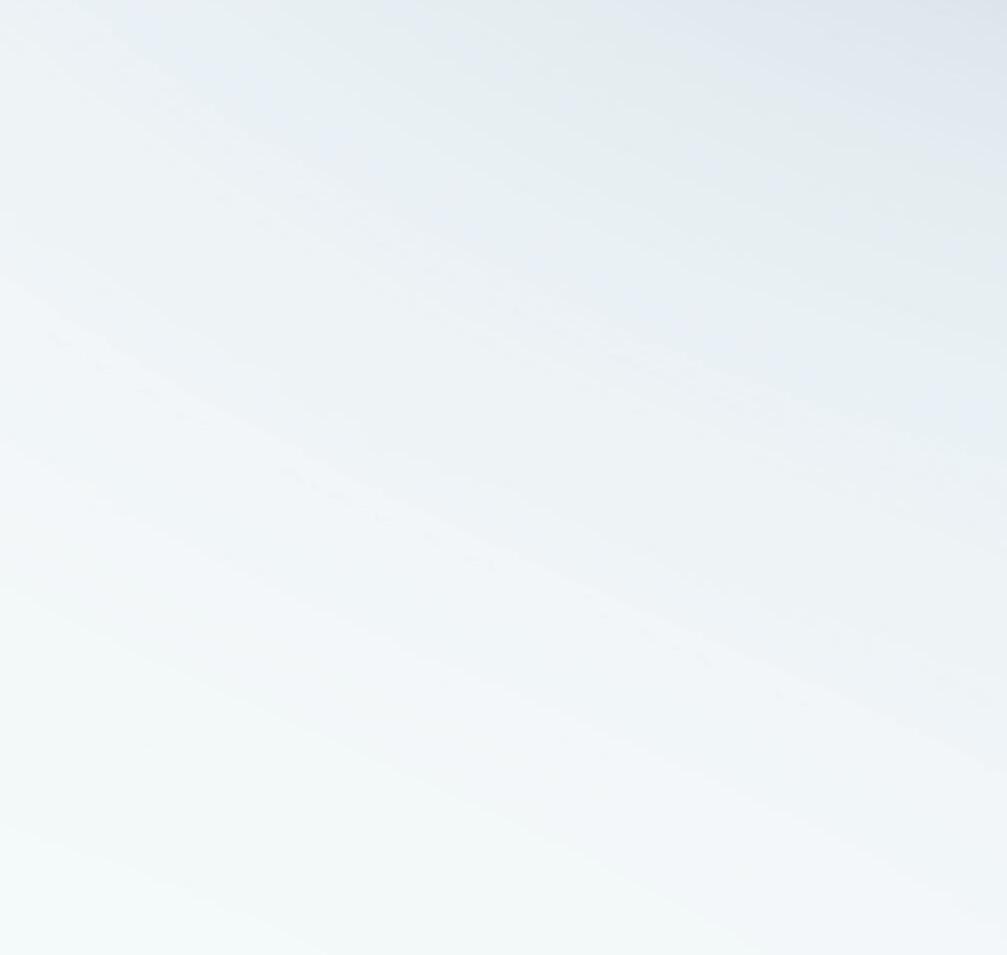
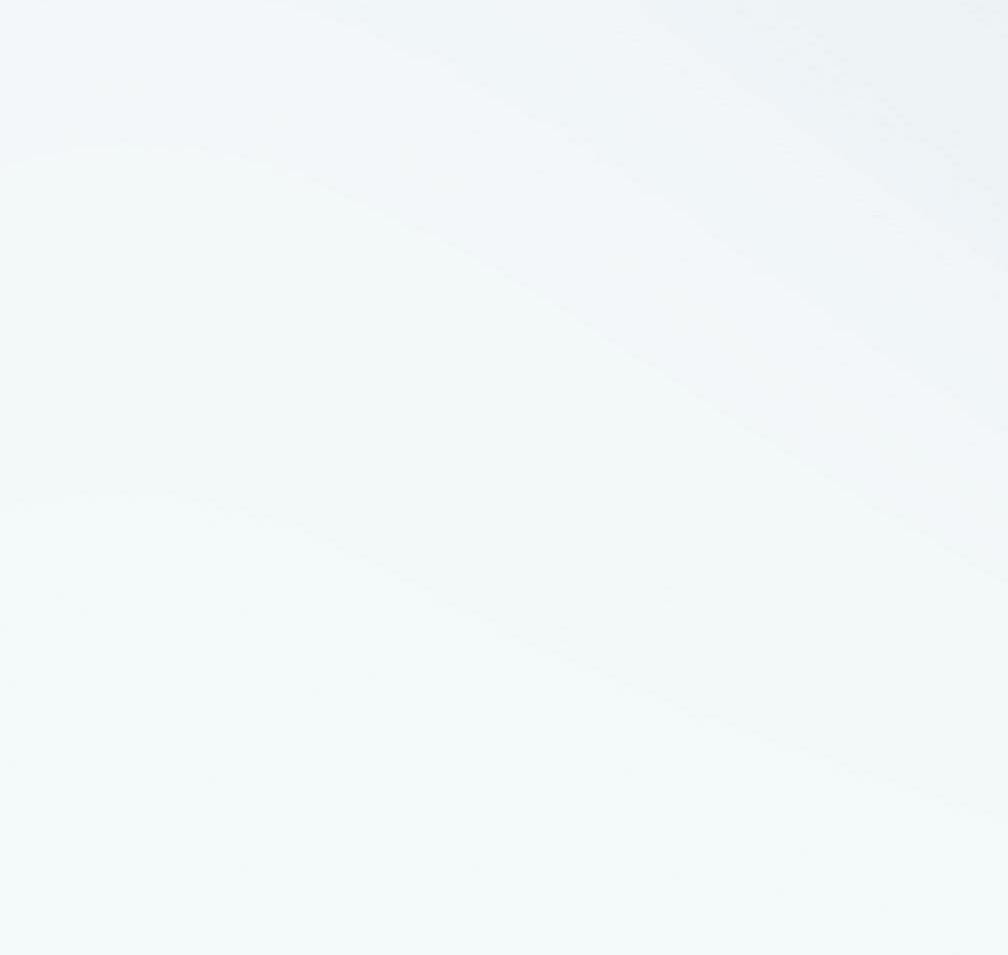


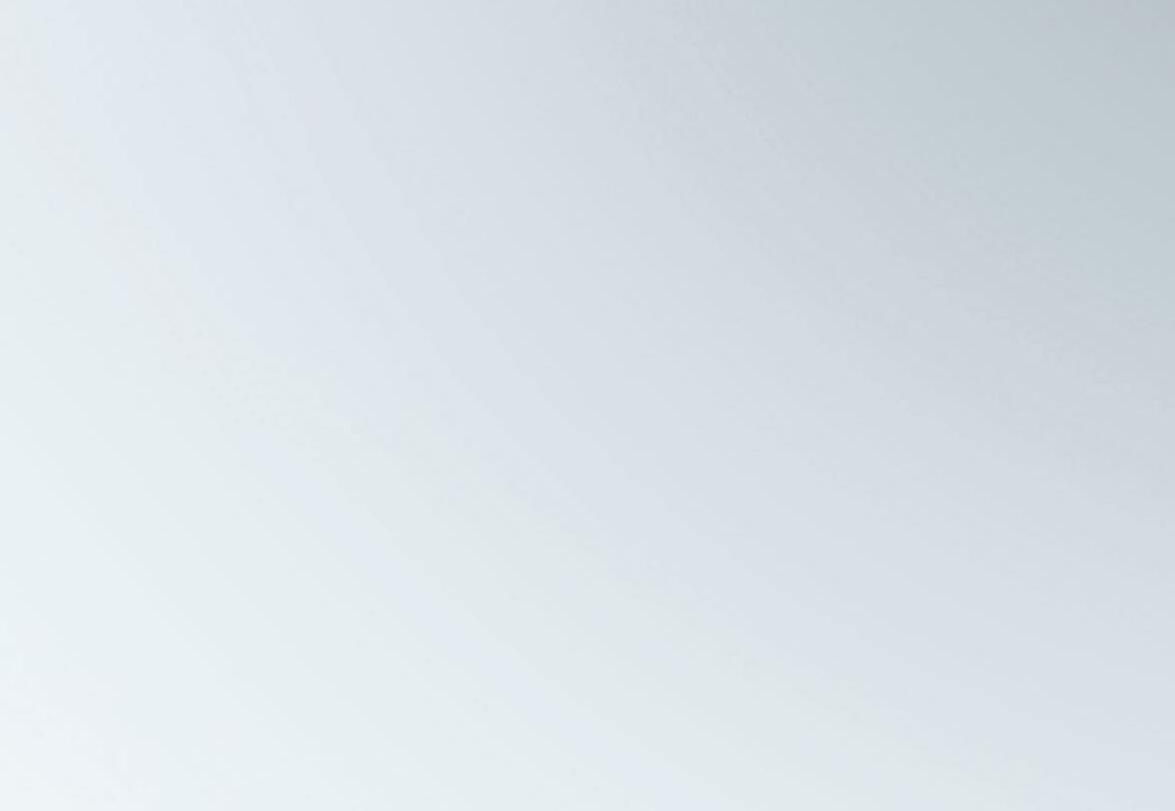
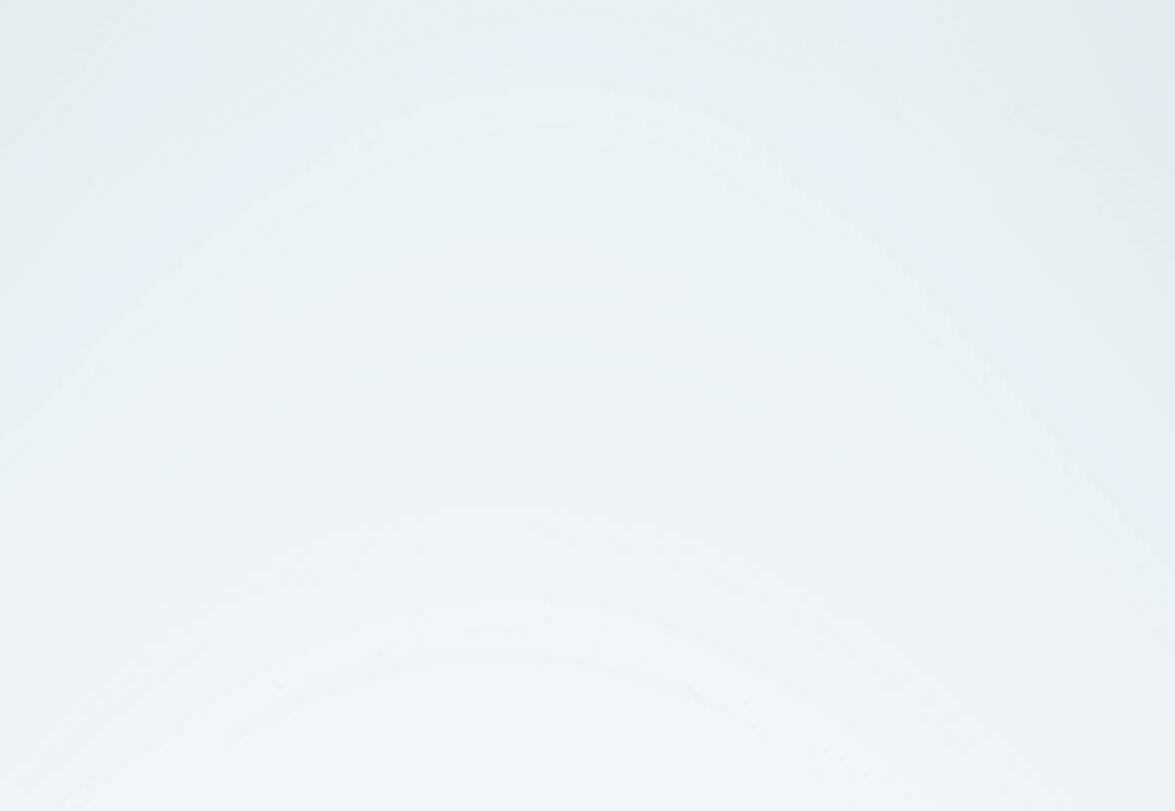
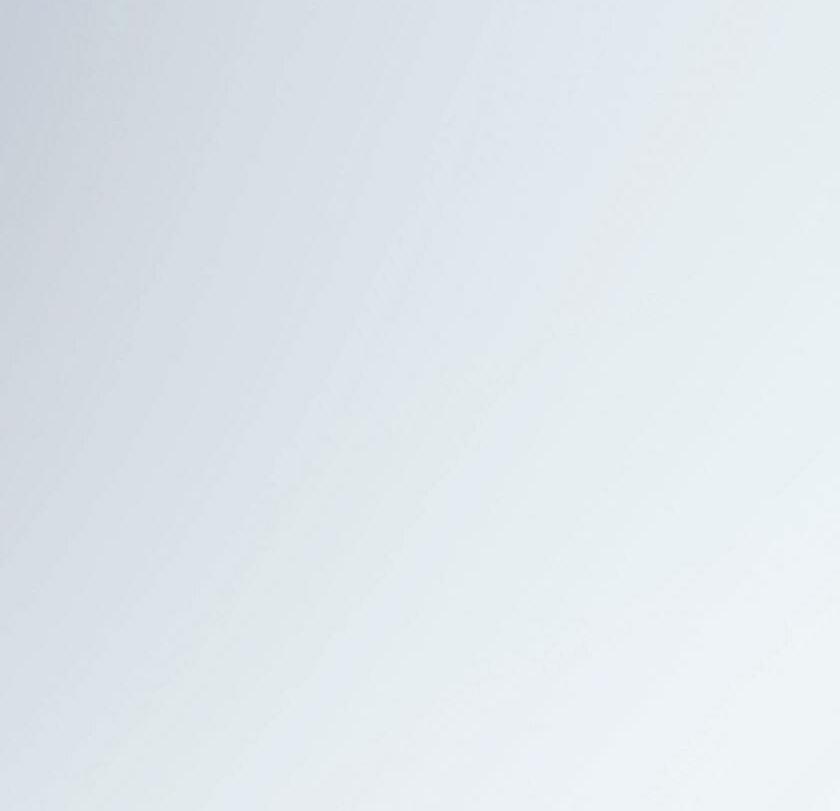
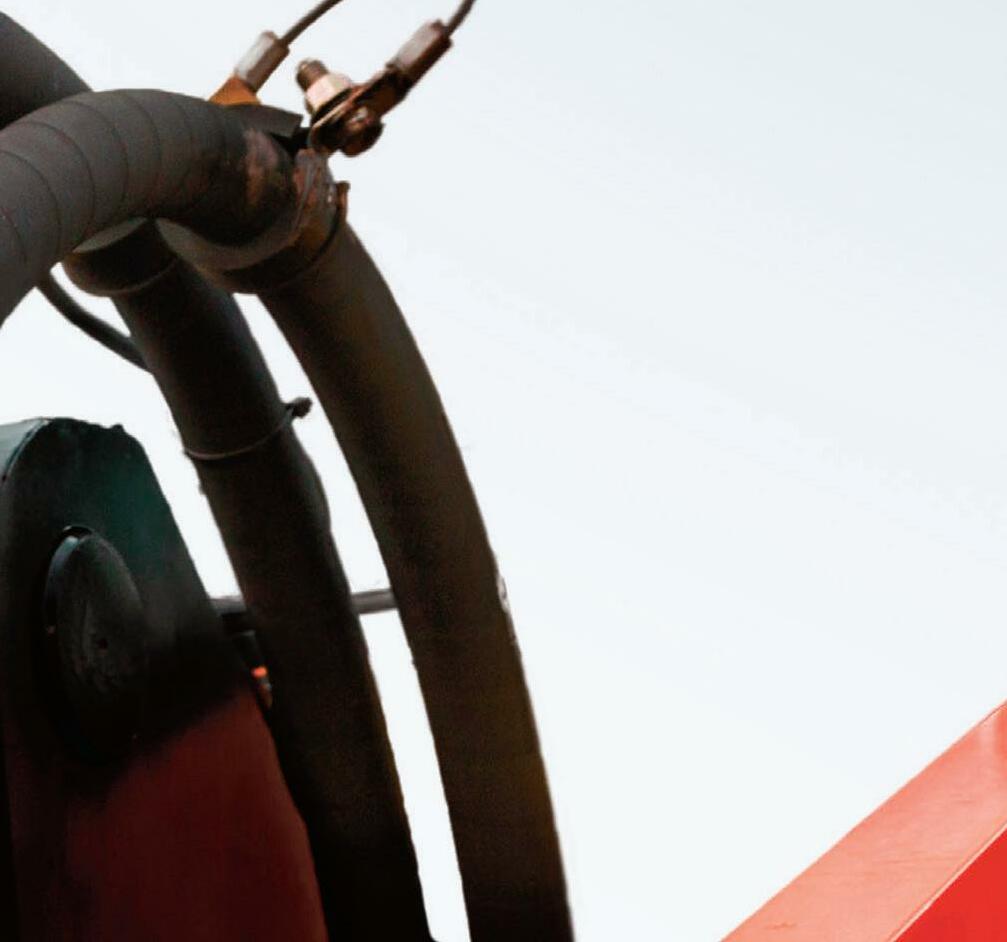




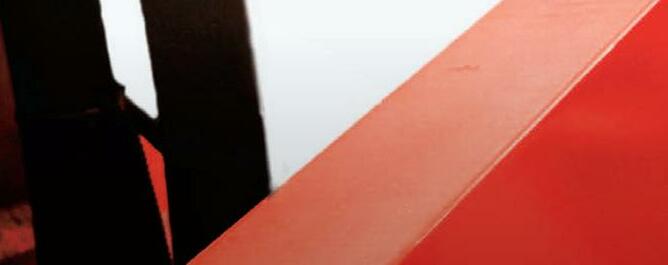
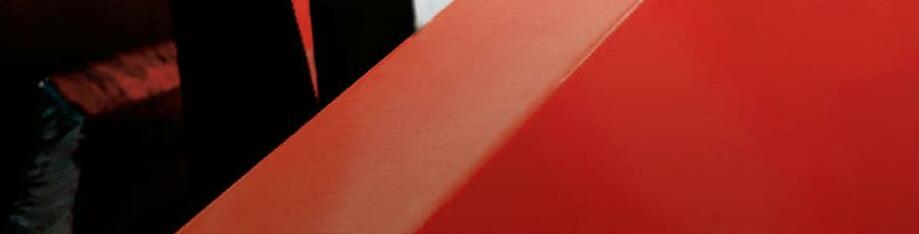


Gage
12 FLUID POWER WORLD 8 • 2022 www.fluidpowerworld.com Solutions to troubleshooting
Set at
The advantage of using load-sense pumps is that they greatly reduce the pressure drop across flow control devices resulting in less heat buildup. The attached circuit is a good example of a simple cylinder circuit that incorporates a load-sense pump with a proportional valve. The cylinder would push and pull fixtures in and out of a machine each cycle. Some fixtures required higher pressures to overcome breakaway friction. The hydraulics functioned well for months and then would only build pressure on the extend function but then only build 300 psi on the retract function. They switched the “A” and “B” connections at the valve but experienced the same low pressure on the retract function. Can you identify the problem? We welcome responses of all kinds directly to Robert Sheaf at rjsheaf@cfc-solar.com or to mgannon@wtwhmedia.com. The solution will be provided in our October 2022 issue. FPW
System could only build pressure
CheckPSI
CFC Industrial Training TROUBLESHOOTING CHALLENGE
NV 1
Robert Sheaf • Founder/CEO of
PO check 8:1 ratio x y FC 1 ½ PSI 5 PSI
The second question was: What would gauge “E” pressure read if the ram were held retracted with solenoids 1B and 2B energized and pump pressure output is 2,500 psi?
Gage
The first question was: What approximate pressure would gauge “A” read if only the electric motor was running, and all three solenoids were de-energized? If solenoid 1B is not energized, the relief would unload at whatever the bias spring pressure rating is, mostly in the 25 to 35 psi range. So, it would theoretically read “25 to 35” psi plus any pressure drop caused by the plumbing size and full pump flow.
Gage
E.M.
All pressure control spring chambers are sensitive to any hydraulic pressure in the chamber. Most are drained to tank. This would be the case when the system is in the neutral and extend function. However, any pressure in the retracted mode is additive to the pressure-reducing valve spring setting allowing full pump pressure to retract the cylinder, thus gauge “E” would read 2,500 psi. FPW
LOADRodsq.in.50sq.in.Piston
on one end of cylinder hydraulic circuit used for training
Circuit 7 EM Gage A Sol. 1A Sol. 1B 3000 PSI Set Max Compensator to 2700 PSI Set Load Sense to 300 PSI CB Circuit 4 Set 3000atPSI Gage D Gage B C Gage E Gage A Sol. 2BSol. 2A Sol. 1B 5 CheckPSI #1 65 #2 1500SetPSIat 2500 PSI40 40
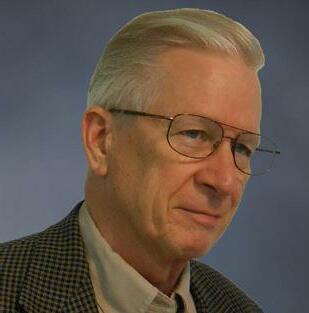
LEAD TIMES OF HOURS INSTEAD OF DAYS OR WEEKS. With today’s logistics challenges and stretched lead times, we’re here for you with our Hydraulex Reman™ line. Remanufactured pumps, motors and valves engineered to deliver OEM level performance and that carry an industry-best 24-month warranty. With our unmatched on-the-shelf inventory of units and parts, and our ability to convert or build units in hours instead of days or weeks, we’re sure to have the unit or part you need right now. Speed and availability redefined. Put a Hydraulex Reman™ unit to work for 1-800-422-4279you. www.hydraulex.comsales@hydraulex.com COME SEE US AT BOOTH: A3.207
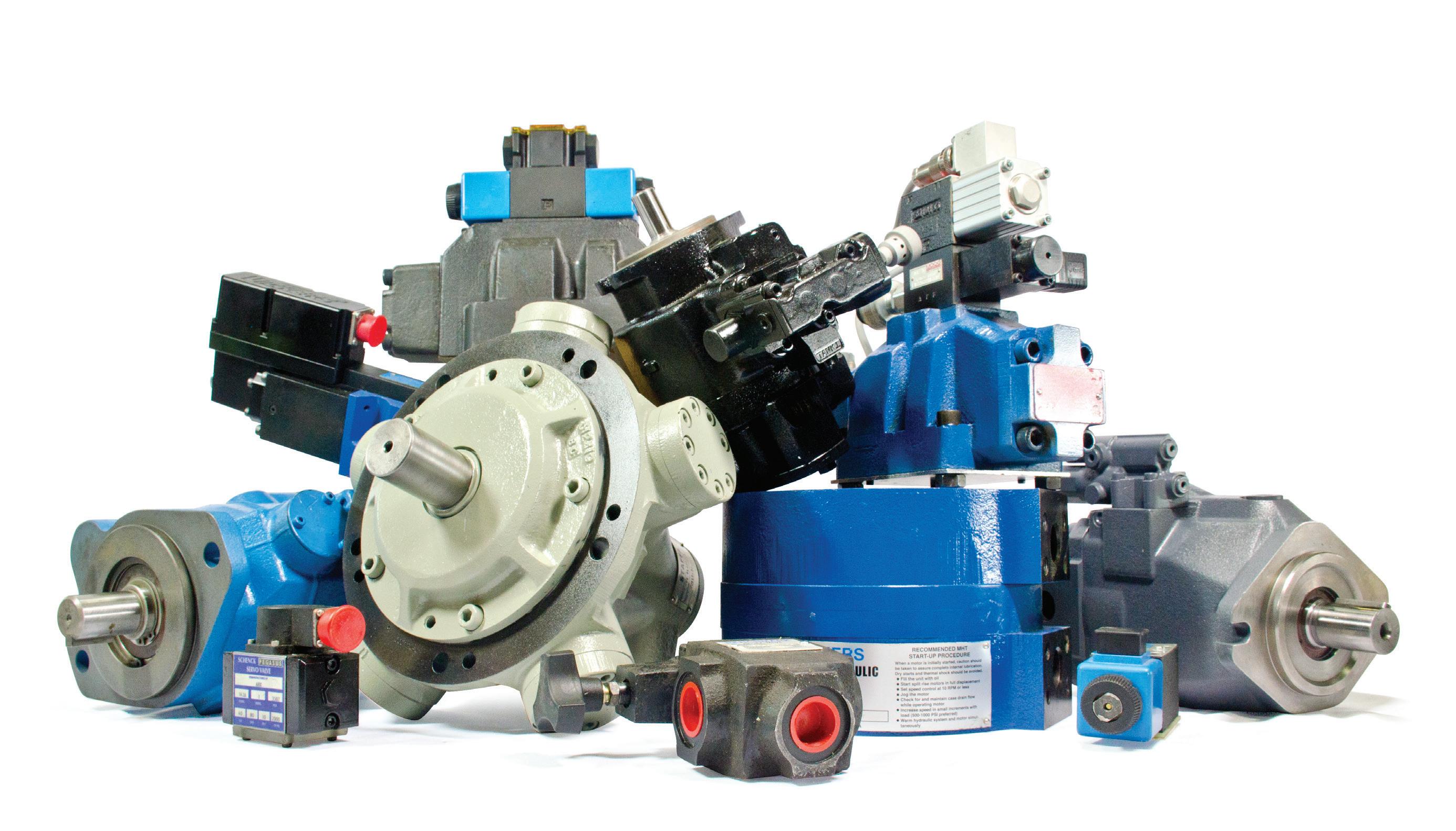
Fluid Power Hall of Fame adds two new inductees for 2022
14 FLUID POWER WORLD 8 • 2022 www.fluidpowerworld.com
• Editor-in-Chief ASSOCIATION WATCH
As early as 1957, Flick saw one of his inventions go into space: six tiny nuts were used to seal the highly corrosive fuel, helping to thrust a 4 1/2-pound Vanguard satellite while 300 miles up. Implementing his fervor for education, he trained hundreds of his employees. He became known for his successful and effective employment policies and was known to have “trained the industry.”
The International Fluid Power Society announced its Fluid Power Hall of Fame Class of 2022. The Hall of Fame recognizes those individuals innovators, researchers, application engineers, educators, as well as sales and service personnel — who have dedicated their careers, and have made significant contributions to fluid power technology.
Visit fluidpowerhalloffame.org/2022inductees for more information. FPW
This year’s class includes two inductees. Robert (Bob) E. Kraft and his wife Marie, founded Kraft Fluid Systems (KFS), in 1972. The now 100% employeeowned company addresses the growing need for integrated mobile hydraulic and electronic control systems. KFS serves 11 Midwestern and Mid-Atlantic States. Setting the standard for employee education, training, and experience, KFS is an industry leader, and requires IFPS Certification for all technical employee-owners. CFPE certifications early in his member of IFPS and served on the Board of Directors from 2003 through 2008, leading as President of the IFPS Board in 2007. Before his retirement, he was committed to the Fluid Power Distributors Association (FPDA), and the Strongsville Chamber of Commerce. In 1961, he earned a BSME from Ohio University and then served 3 ½ years in the U.S. Navy. During his naval service, he was awarded a patent for the Inductive Kick Suppression Solenoid. While employed at Paul Munroe Hydraulics, Kraft was a principal contributor to the first edition of the Lightning Reference Handbook, which became the fluid power industry’s standard reference book. Quoting Kraft, “Throughout my career, I believed education, training, and experience lead to learning and competency.” More than 20 years ago, he and Marie established the Kraft Family Associate Professorship Awards. These professorships have provided monetary and professional support for the junior faculty in the Department of Engineering Technology and Management at his Alma Mater, Ohio University. Frank S. Flick (1906 –1986), was inducted posthumously. Flick graduated from Loyola Academy and in 1927 earned a Bachelor of Science in Mechanical Engineering from the University of Illinois. Flick is credited with 56 patents, of which 42 were for improvements and innovations for both pneumatic and hydraulic cylinders. About 460 of his original cylinder dimensions are now incorporated into the industry wide NFPA cylinder standards. Along with his partner, William J. Reedy, Flick purchased the Miller Motor Company in 1942 and the descendant of that company has been known by both Flick Reedy Company and Miller Fluid Power Company. Miller is now a division of Parker Hannifin Corporation. Flick received numerous awards, including three National Industrial Recreation Association Helms Awards for excellence in employee relations. He was awarded Citizen of the Year and an Americanism Award from the VFW, the First Partnership Award of the Labor-Management Association, Senior Citizen of the Year Award from the Chicago Park District, and the Pro Ecclesia et Pontific designation from Pope Paul VI.
Edited by Mary Gannon


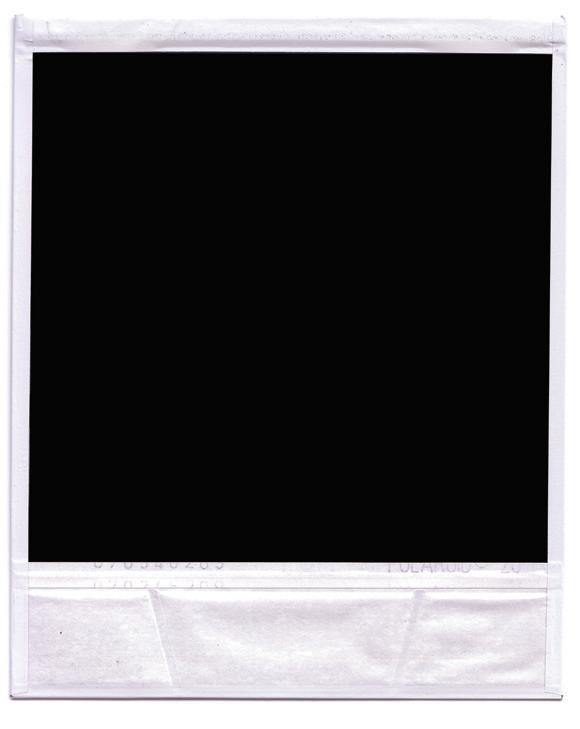
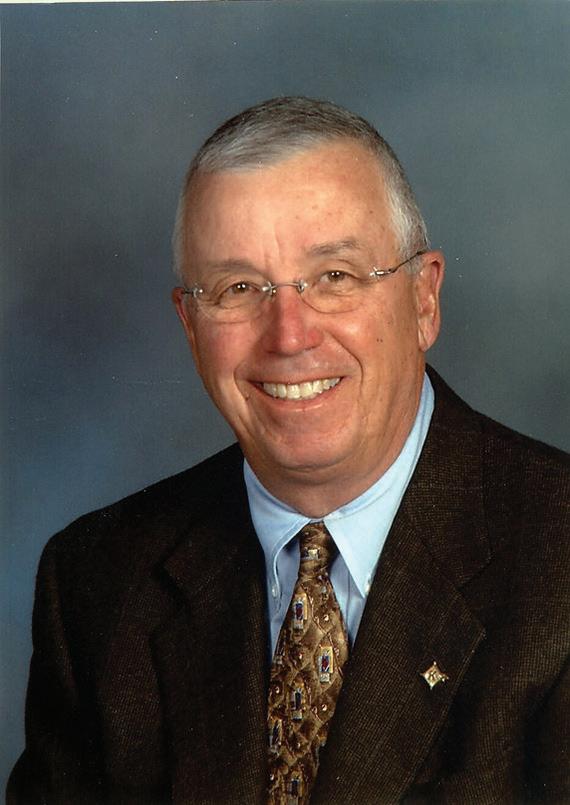
This fall will mark 14 years of The National Fluid Power Association hosting the Fluid Power Action Challenge and eight years of NFPA offering schools/ organization grants. NFPA would like to thank the hundreds of individuals in NFPA member companies and education partner institutions who have been involved in mentorship, classroom activities, and events related to the Fluid Power Action Challenge, which has engaged more than 26,000 students through classroom activities and events to date.
NFPA supports elementary education through Fluid Power Action Challenge grants
www.fluidpowerworld.com 8 • 2022 FLUID POWER WORLD 15
The NFPA Fluid Power Action Challenge Grant application period is open for 2022-23 to schools/organizations interested in receiving funding for fluid power programs and events for the 2022-23 academic year. NFPA encourages schools/organizations to apply as soon as possible. A pipeline into fluid power continues to be created through NFPA’s Fluid Power Action Challenge grants and other workforce programs. It is NFPA’s pleasure to congratulate all the schools and organizations that received grants for the academic year 2021-22. Programs like the Fluid Power Action Challenge grant are made partly by the generous support of industry volunteers and NFPA Education and Technology Foundation, and Pascal Society donors. Support these efforts by making a donation.
FPW
This past academic year, the National Fluid Power Foundation issued 64 Fluid Power Action Challenge grants totaling more than $30,000 to 54 schools/organizations across the country. These funds support schools and organizations that would otherwise not be able to participate in fluid power programming in the classroom or at events across the US. The grants were used to purchase classroom mechanical devices and help cover Fluid Power Action Challenges expenses, such as registration and transportation.
If you are interested in the NFPA Fluid Power Action Challenge and NFPA Fluid Power Action Challenge grants, contact NFPA Workforce Program Manager Eric Pannell at epannell@nfpa.com or 414-778-3364.
PERFORMANCEWHENMATTERS tust ACE Controls with your motion & controlvibrationneeds www.acecontrols.comTools productsStandard available Buy ResourcesOnline ▪ ACE CAD database ▪ ACETips video tutorials ▪ Technical blog & case studies ▪ Online calculations & selectionproduct ▪ Chat function for applicationassistance Sizing & specification Online & downloadable Visit us at booth #10401 IndustrialIndustrialabsorbersshockgasspringsVibrationisolation
“The Fluid Power Action Challenge is one of our flagship outreach and education programs that introduces young students to fluid power technology and careers,” said Eric Lanke – NFPA President/CEO. Through our grant program, thousands of middle and high school students learn about and have fun with fluid power.”
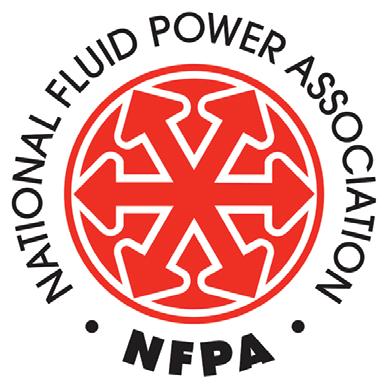
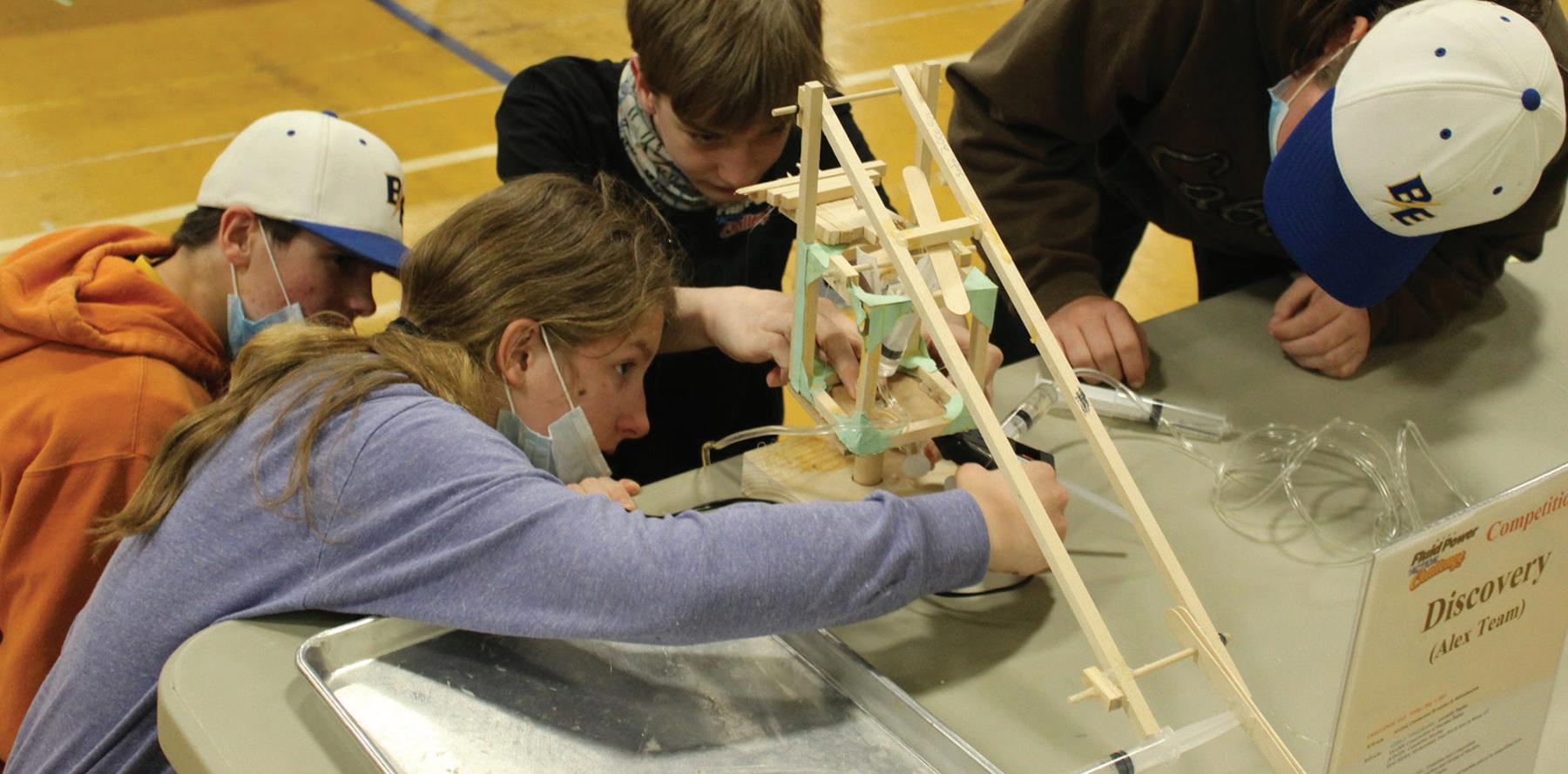
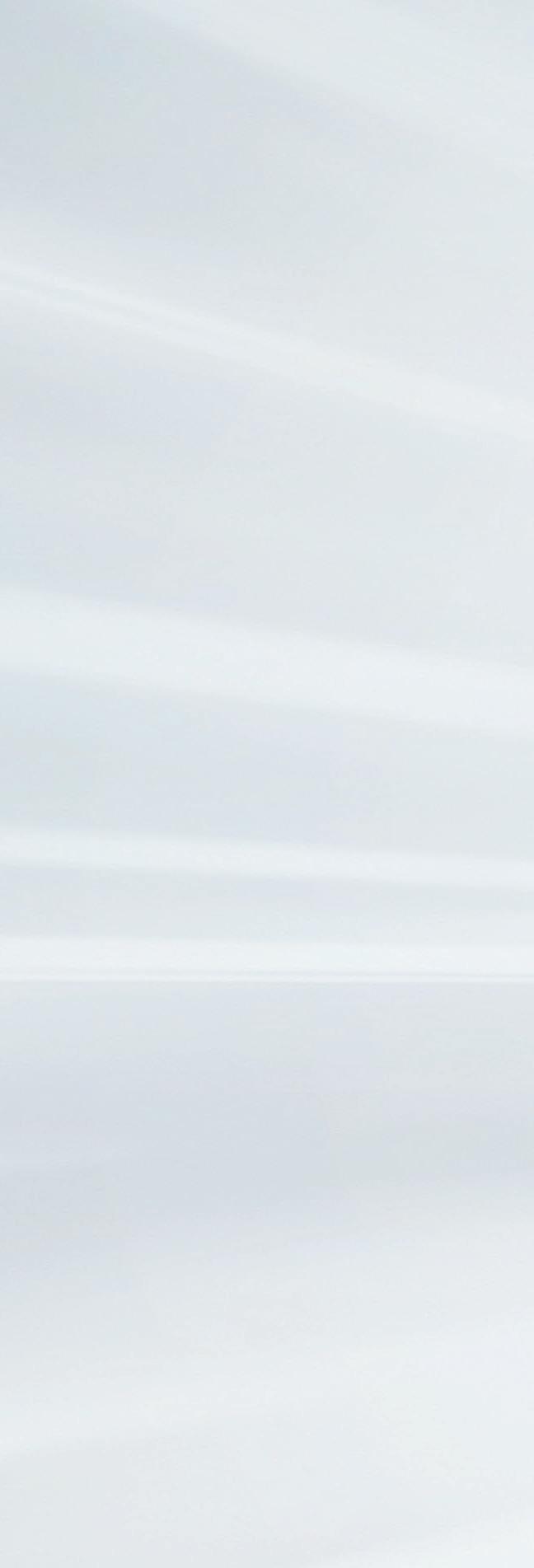


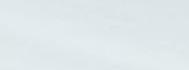



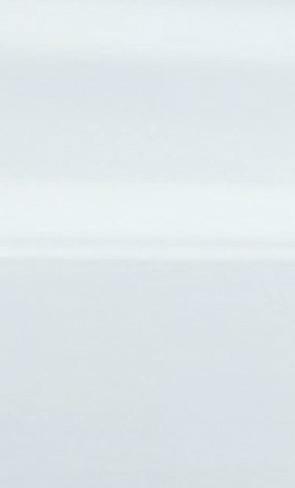
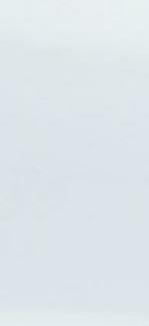
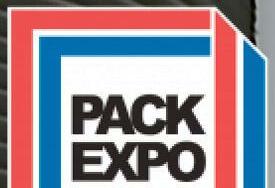
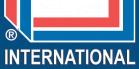

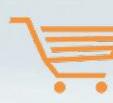
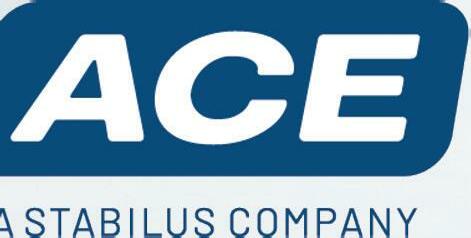

A group of about a dozen limit switches were designed to know the position of the bell, so that when it was turned on, a limit switch would know to stop and go back and swing backwards, said Andrew Roach, Project Manager for Ballpark Renovations. “Birds would sit on the limit switches, believe it or not. And, then, they would get knocked out of whack and then the bell really didn’t know where its current position was,” Roach said. “Then, it would think it was at the end, so it wouldn’t move, or it would be stopped in the middle and then it wouldn’t move when we would hit the button.”
It was soon realized that the current company that was charged with maintaining the hydraulics system would not be able
“We didn’t deviate too far from the original. In my mind I wanted to figure out how we could build in some additional range of motion in terms of speed and functionality. The main method of how the Liberty Bell moves is through hydraulics,” Kicera said. “Looking at that system, it had been upgraded and different pieces and parts added onto over the years. It was sort of cobbled together. And, obviously, from my time in the entertainment industry, I knew what was possible from that perspective and how to clean it up and make it more efficient and sort of just bring it up to the current technology.
Ringing in a home run with simplified and modernized hydraulics
“So that was ultimately the driving force — to restore the speed and range of motion, as well as just making it something that was bulletproof and was going to work when they hit the Go button.”
So, as the season wrapped up in 2021, Roach’s team reached out to Tyler Kicera, of köllab group, who is an expert in designing kinetic motion systems for entertainment purposes, to assess the situation and determine what steps should be taken to revamp the bell’s control system.
16 FLUID POWER WORLD 8 • 2022 www.fluidpowerworld.com
History and baseball are intertwined at Citizens Bank Park in Philadelphia. Whenever a Phillies’ player hits a home run or the game is won, the iconic Liberty Bell swings and chimes. But getting fans excited with this experience was a bit of a struggle in recent years, as the bell’s hydraulic control system was older and outdated and not running as it should. There was often a question of whether the bell would swing and chime as expected when it was set in operation.
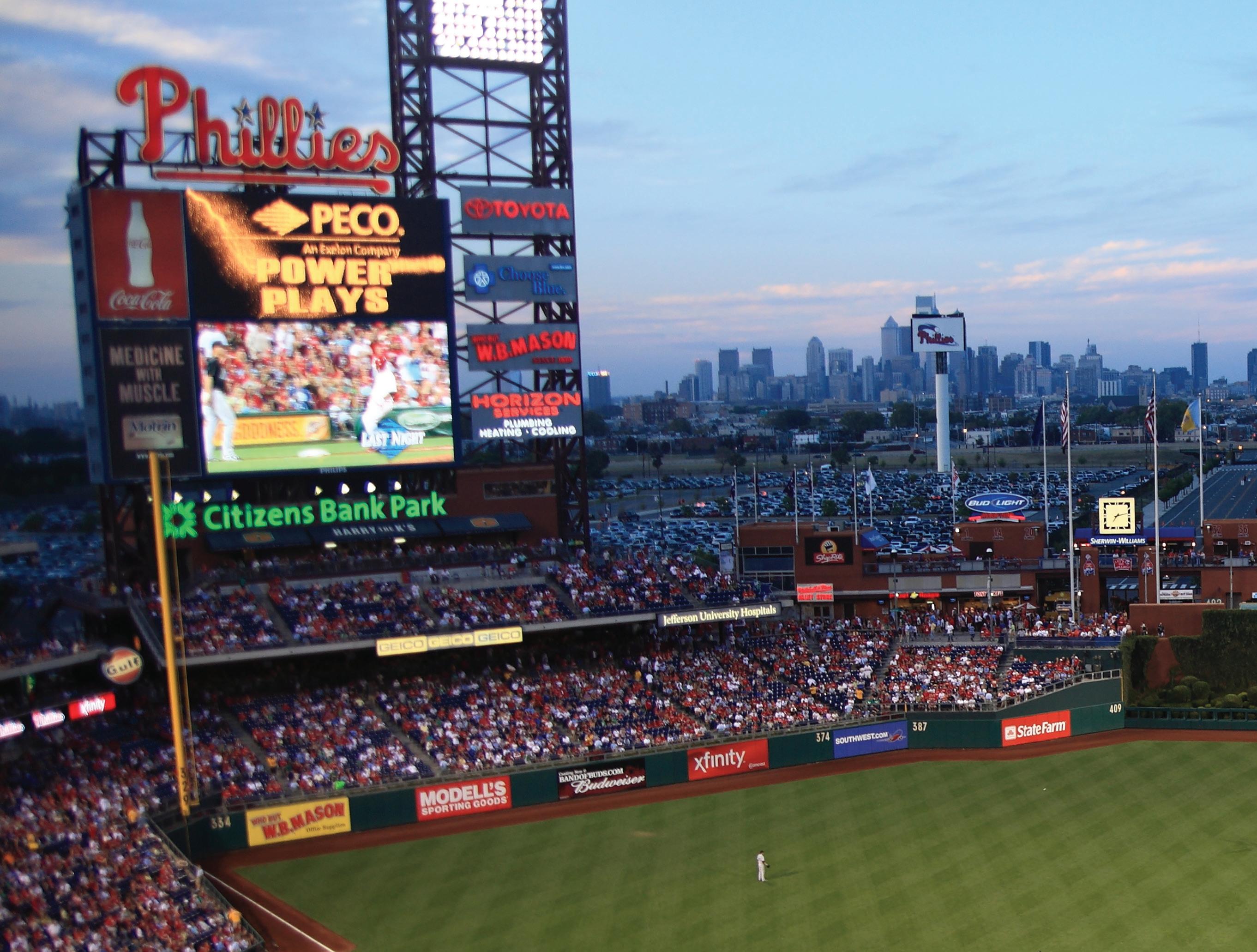
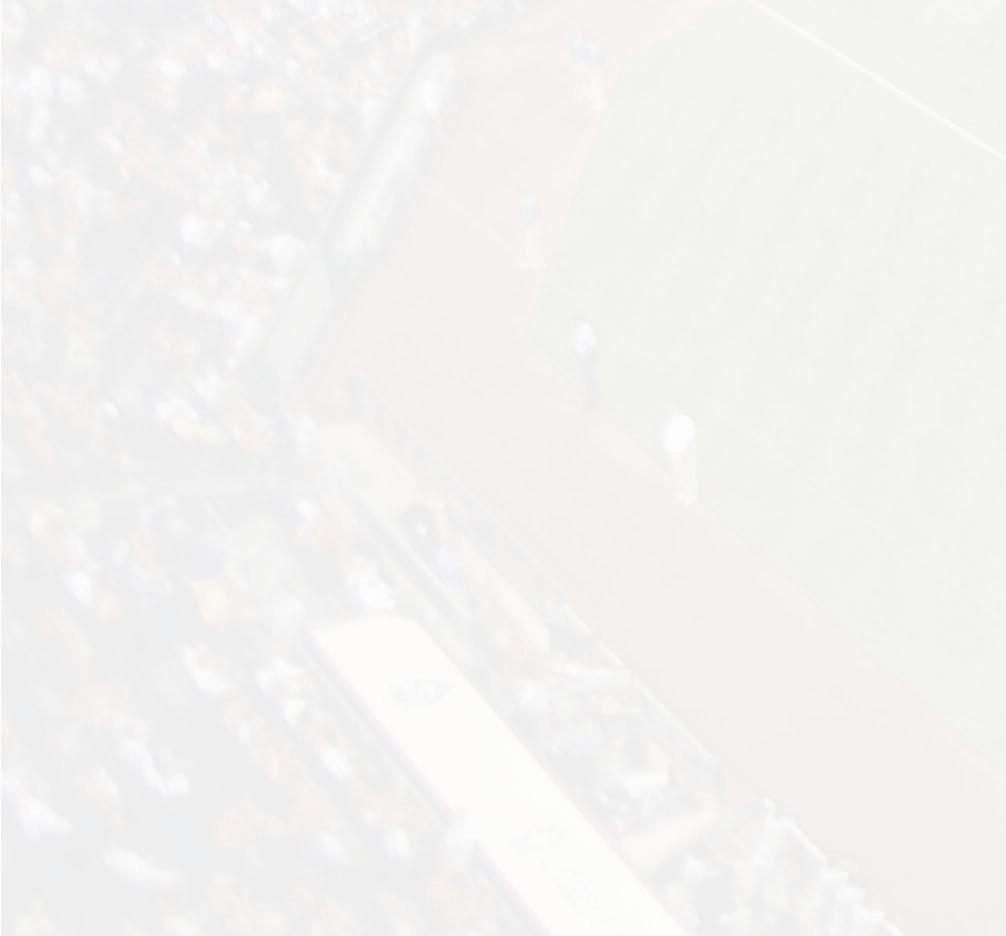
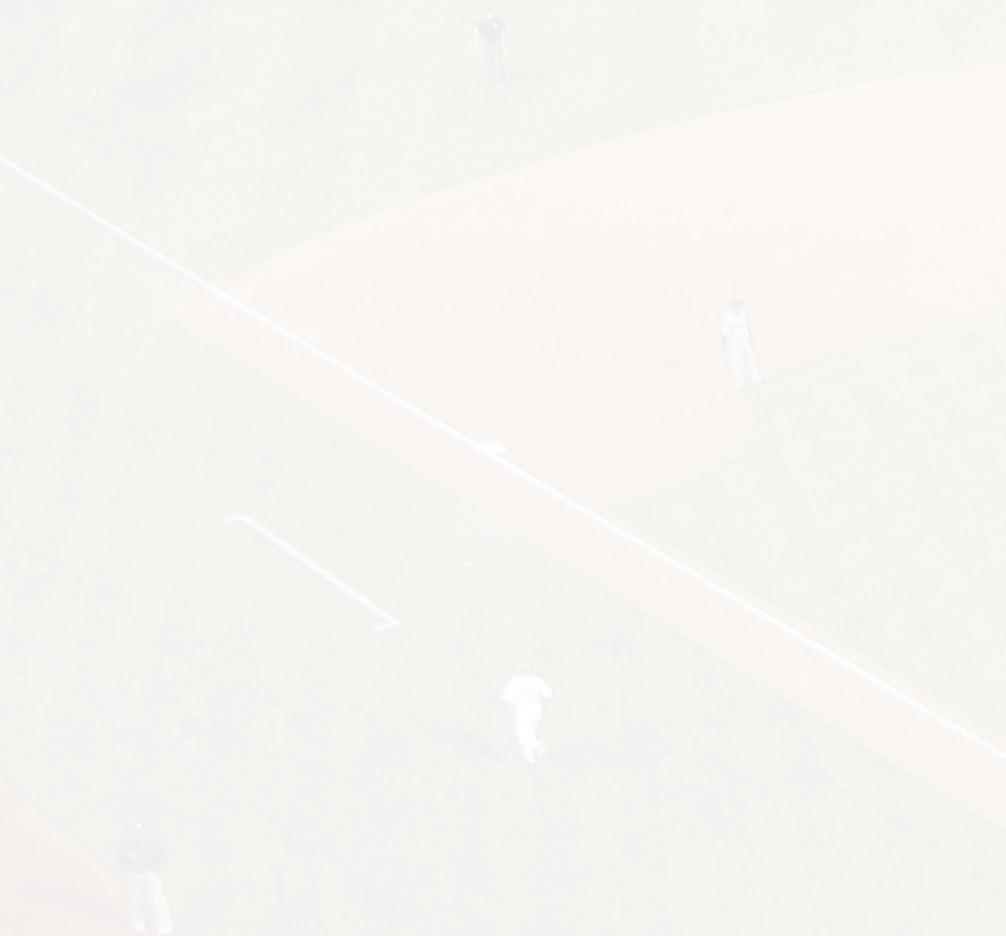


“So, what we found was a very inefficient hydraulic system, and it probably got that way over the many years of using outdated components. Admittedly, being 85 feet in the air is not conducive or the most convenient for doing the hydraulic maintenance,” Turner added. After watching countless hours of videos of the bell in operation over the years as well as just bells in general, the team had a very tight window to turn around the project. Turner’s team removed the old unit and brought it to the shop to reconstruct the enclosure and system.
“The issue with the old bell was that there DESIGN NOTES By Mary C. Gannon • Editor-in-Chief
Whenever a Philadelphia Phillies’ player hits a home run or the game is won, the iconic Liberty Bell swings and chimes. But last season, it was determined the hydraulics and controls for the Bell needed an overhaul.
|
Courtesy of The Phillies/Miles Kennedy to update the system as Kicera envisioned. So, he reached out to Turner Hydraulics because he had worked extensively with them in the past. “Hydraulics in general, can be very agricultural and that’s not what we needed here. We needed something that was more intelligent and had a higher level of functionality. And, that was something I knew from working with Turner in the entertainment industry, that they knew how to approach those types of problems.”
Dan Turner, owner and President of Turner Hydraulics/TASCorp., of Carlisle, Pa., was excited by the challenge. Between both companies of Turner Hydraulics and TASCorp. as well as his inhouse fabrication shop, they were able to limit the number of people involved to streamline design and build. The HPU enclosure required additional fabrication and Turner was able to work directly with the crane company to coordinate lifting the unit up the nearly 90-ft tall bell tower. “With the original hydraulics, I was a little surprised that it almost appeared to be products that were installed right at the end of their current lifespan, if that makes sense. I think these products probably went into an obsolete mode within just a few years of being installed, which makes it difficult. So, we knew that we wanted to pick items that were going to be common items around for a long time,” Turner said. Turner said the proportional valves were about 20 years old and outdated, so the team went up and did a diagnosis of the system. They studied flow rate and pressures required to move the bell and the bell clapper. “We were able to determine that the pressure and flow rates were at a level that allowed us to reduce from a 30-hp electric motor down to a 20-hp electric motor. And the valves were selected based on the flow rates for the motion that was being requested,” Turner said. “From the way the bell was working the last couple of years, it’s now operating about twice as fast as it had been, even with the lower horsepower.
www.fluidpowerworld.com 8 • 2022 FLUID POWER WORLD 17
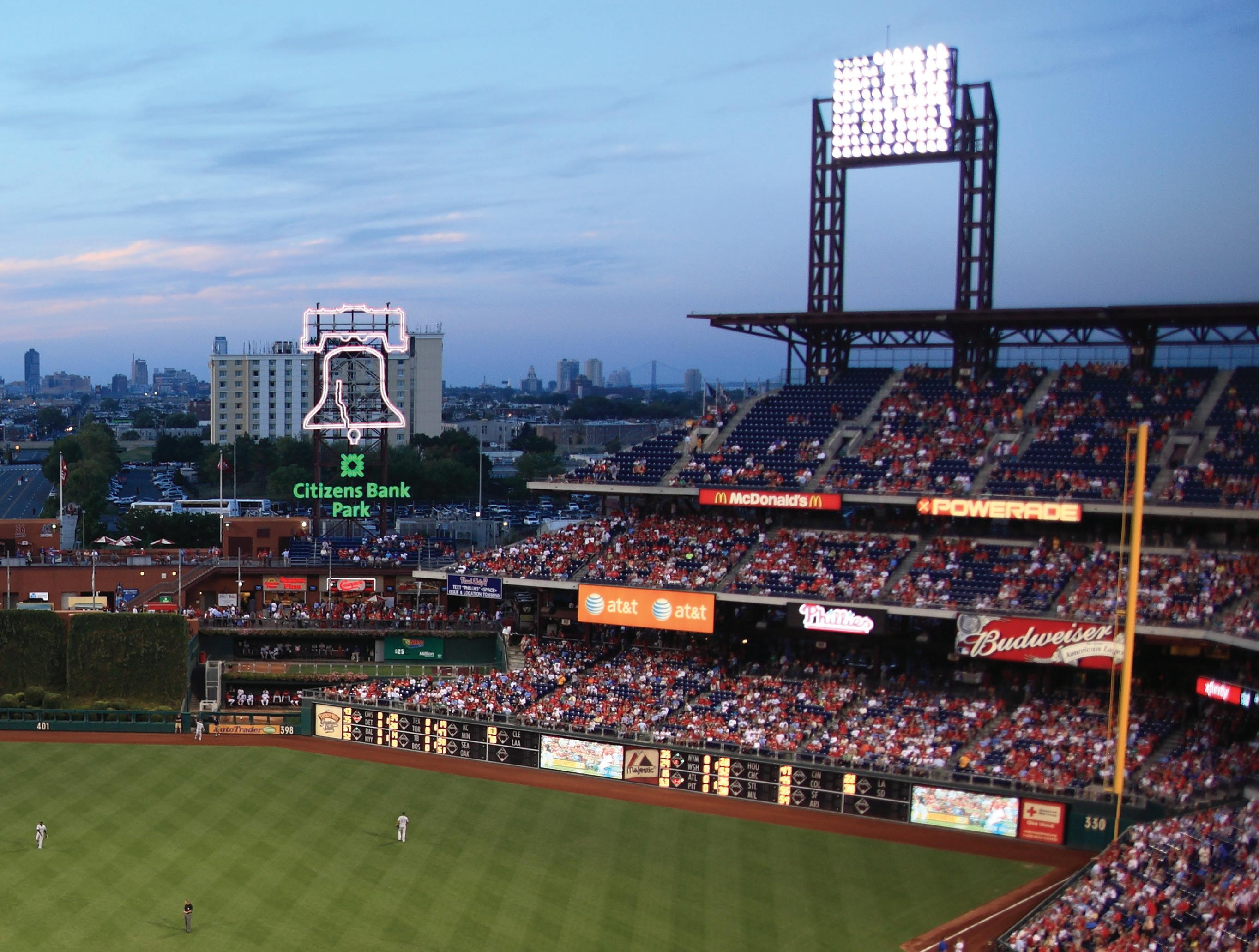
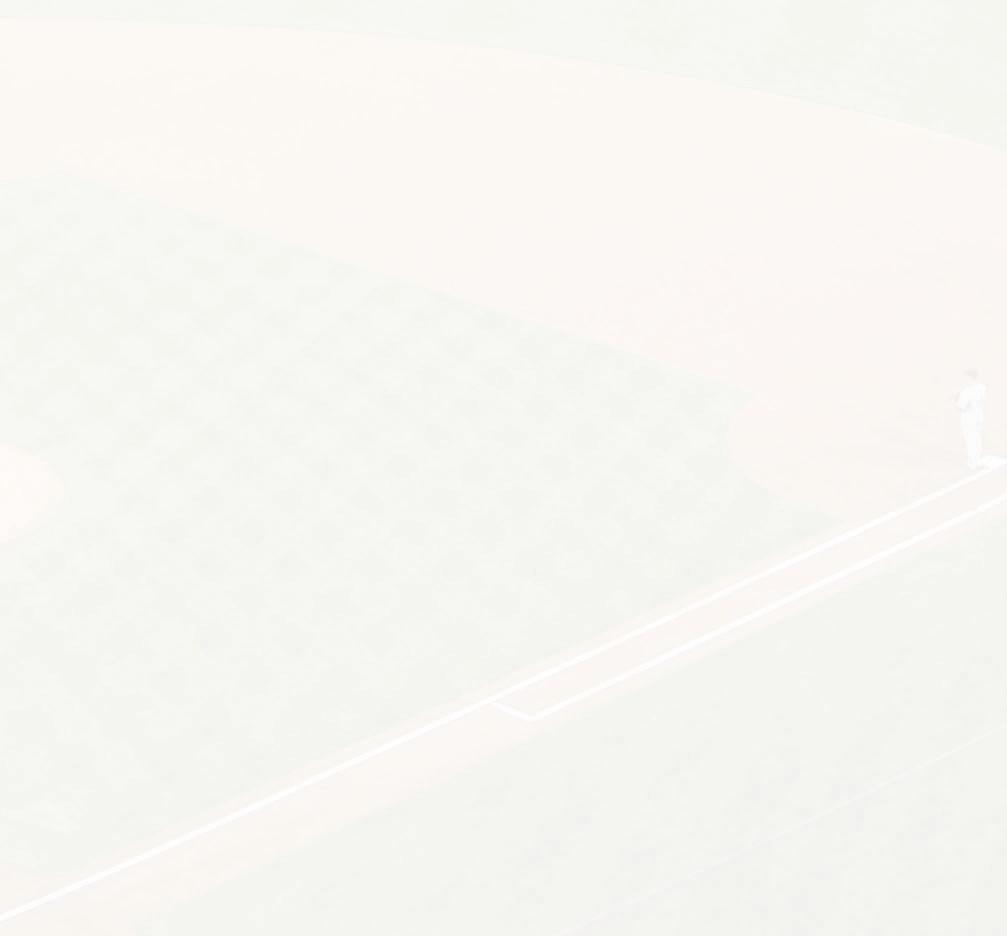

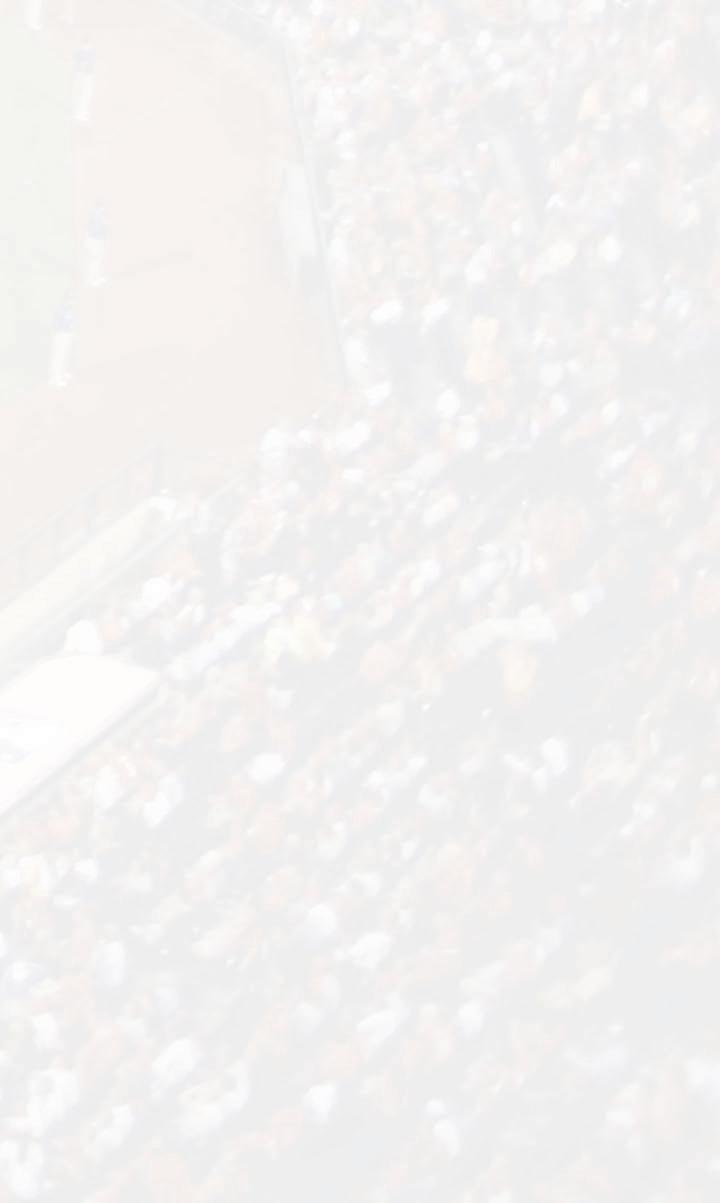

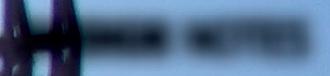

18 FLUID POWER WORLD 8 • 2022 www.fluidpowerworld.com DESIGN NOTES
“And the clapper had very much the same system of limit switches. So, on the tower, there were probably 10 different limits switches which we removed, and then we put on just two of the LVDTs, one for the bell and one for the clapper.”
“So, what we did is we built the electrical panel right there on the HPU that’s sitting up in the enclosure on the platform and we put local control on there. So, just by pushing buttons, we can operate the bell so we can be self-sufficient for any troubleshooting and tuning that we want to do,” Turner said. “And so, what we’ve done for them is when they push the button, they get feedback as to what is happening. “The motor is starting up. The valve is in this position. And if there is no motion, they get told why, and when there is motion, they get told, or the availability is there for them to know basically everything about what the HPU is doing. It gives them faster accessibility to see if they have any problems, which, hopefully, they haven’t yet so far since it’s still mid-season. After removing and refreshing the cylinders, the goal was to be able to automate the ringing of the bell, said Kicera. “Before, in the control room they had to watch when the clapper met the bell and then someone pushed a dong
The HPU itself was also redesigned to be more compact and lightweight. By reducing the size of the motor and eliminating a heat exchanger, they eliminated extra points of failure, Turner said. The pump was changed from a vane pump to a HPVR pressure-compensated piston pump from Continental. And finally, the Turner/TASCorp. team remanufactured the enclosure and worked to install it 85 ft up in the air on a
The hydraulic power unit from the Bell’s control tower, before being rebuilt by Tuner Hydraulics.
was no feedback. So you would hit, ‘Start moving.’ And the bell wouldn’t move and you would just be like, ‘Did it not get the signal? Did it get the signal and just decide not to move for some reason?’ So there was no two-way communication,” Roach said. “Now up in the control room on the wall, we have a screen that shows the current status of the bell. If we restart the HPU and reboot the computer, that shows that there’s communication back and forth between the two systems; between our touch screen on the wall, and the bell itself, and the hydraulics. So it just gives us a lot more info on what’s going on up there,” Roach concluded. The Turner team got to work fast, focusing first on the position sensing of the system. Limit switches were able to tell when the bell was to the left and when it was to the right. They also had a slow down left, slow down right, and a center position limit switch. “The limit switches seemed to be as much a problem as anything on the system and made it difficult to troubleshoot and get their finger on what was happening at which point,” Turner said. “And so, what we did, we took off the limit switches. We put on a linear encoder, like an LVDT. And, therefore, we were able to tell the bell’s position no matter where it was at. With the limit switches, you didn’t know where the bell was until it tripped one of the limit switches.
| Courtesy of Turner Hydraulics/TASCorp.
Courtesy of The Phillies/Miles Kennedy
After working with Turner Hydraulics/ TASCorp. and the köllab group, the Phillies’ Liberty Bell swings and chimes better than it has ever done, with modernized lighting and controls.
|
windy and chilly, early spring day, as the bell needed to function on opening day. One of the things that the Phillies didn’t have previously was local control. So, if you wanted to see the bell operate, you had to be on the phone for troubleshooting and you had to call to somebody who was at the main control panel of the ballpark, and they would then push the button and the bell would move.
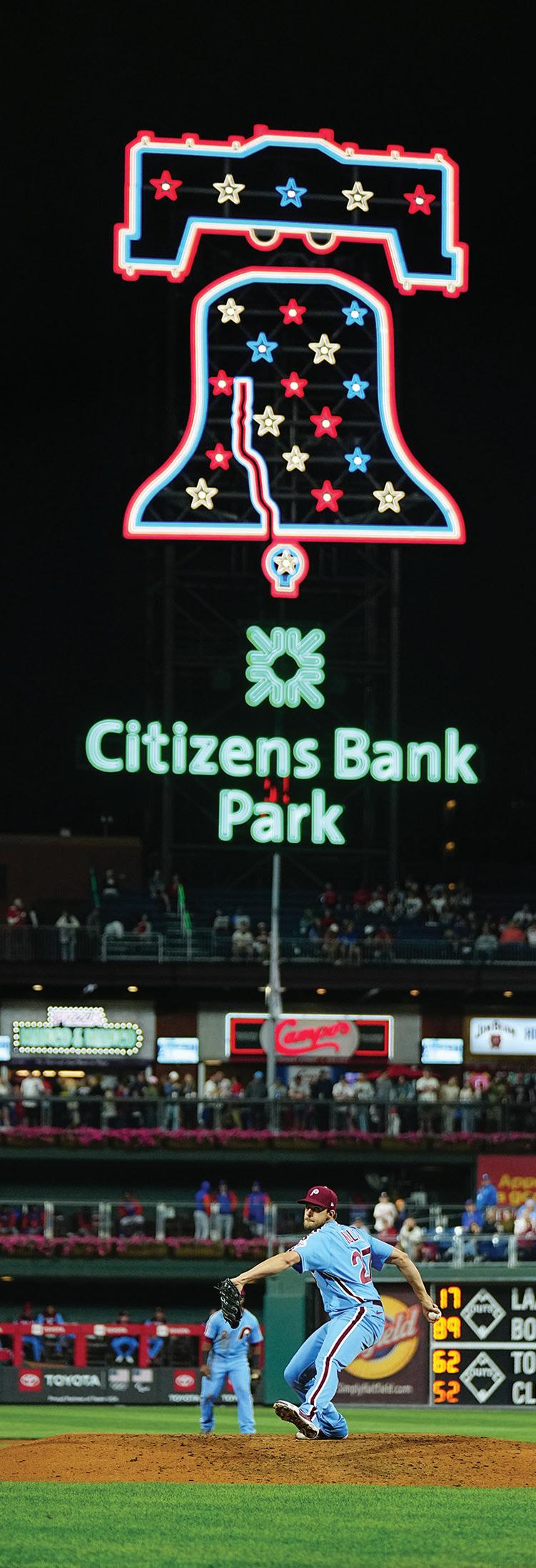
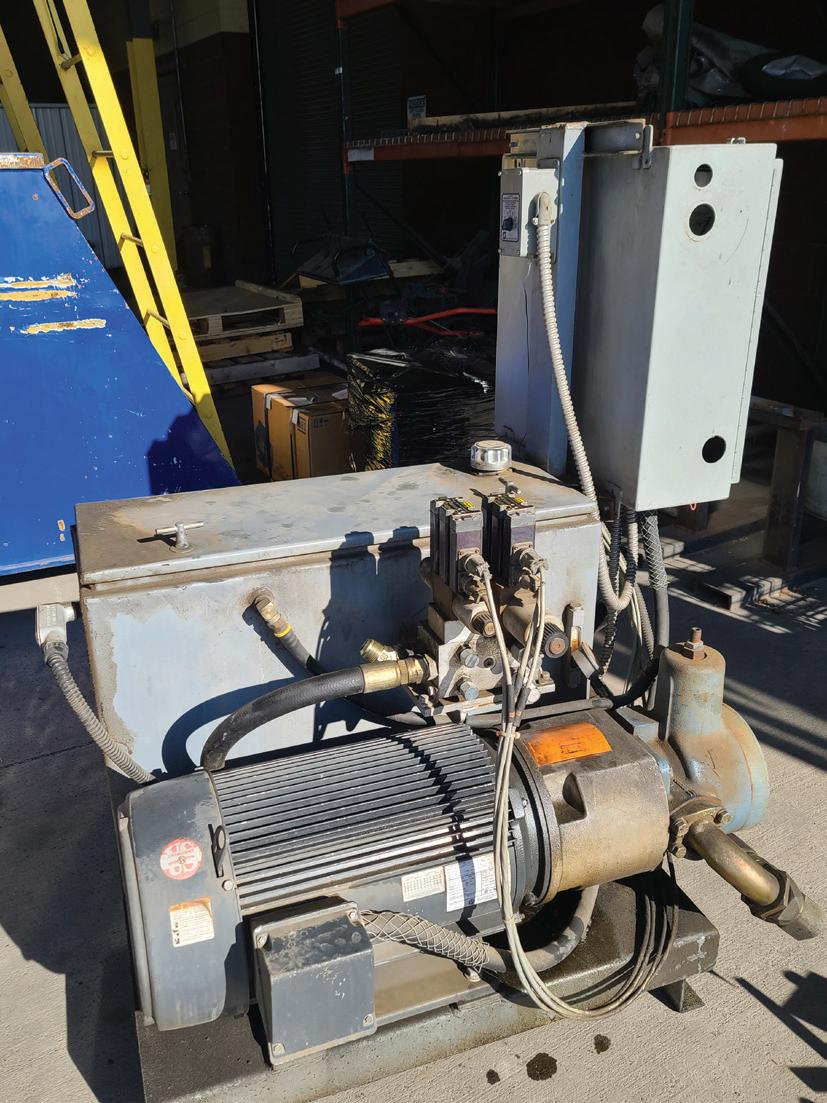
Turner
FPW Kawasaki Precision Machinery (U.S.A.) Inc. • Grand Rapids, MI • www.kpm-usa.com • 616.975.3100 Kawasaki is a world-leader in motor efficiency and performance. Inside our range of products you’ll find some of the most efficient axial piston motors available on the market today. Our engineers understand our customers’ needs, each motor has been designed to deliver high performance across a diverse range of applications. Axial Piston Motor • 85, 112, and 160cc displacements • 420 bar pressurecontinuousrating • Electric, hydraulic, two-position displacement and pressure related displacement controls • 85 & 112cc fixed displacement versions available • Optional Speed Sensor / X ReliabilityPerformancePrecisionQuality 8 • 2022 FLUID POWER WORLD 19 The old power unit being removed from the nearly 90-ft tall tower. | Courtesy of Turner Hydraulics/TASCorp.
button to make the sound. And obviously that tied into their entertainment control system that they’re using to basically listen for cues,” he said. “There was a number of different profiles that were programmed. The backend control system that they’re using now can speak to the hydraulic power unit’s control and could all be kind of synchronized real time. “In general, it’s much more robust. The goal obviously was to enhance the reliability so that when they hit go or that cue got triggered it actually was going to work. We have a system that’s considerably more flexible in not only the ability to ramp up and down speed but go to different points within the travel. We’re not limited to the end of travel limits. And just control-wise, the feedback loop gives the folks who are operating the bell and all the various other systems that go along with it good visibility into to what’s happening.” “It’s one of those things where the bell needs to work. The first at bat was a home run for the Phillies,” Turner concluded. “At the end of the game, they showed the bell swinging and dinging, and the announcer actually said, ‘What a day for the Phillies. And look, the bell, it’s working. “I think, because of my passion for hydraulics, that kind of a statement really gets me. Because, hydraulics should work. And, when I see a system that is expected to work and doesn’t because somebody didn’t use the right vendor or it’s not been maintained properly, then, hydraulics gets a bad rap. And it’s not the hydraulics. It’s, generally, somewhere along the line that the best decision for the hydraulic design team was not made.” tascorp.usturnerhydraulics.comHydraulics/TASCorp.
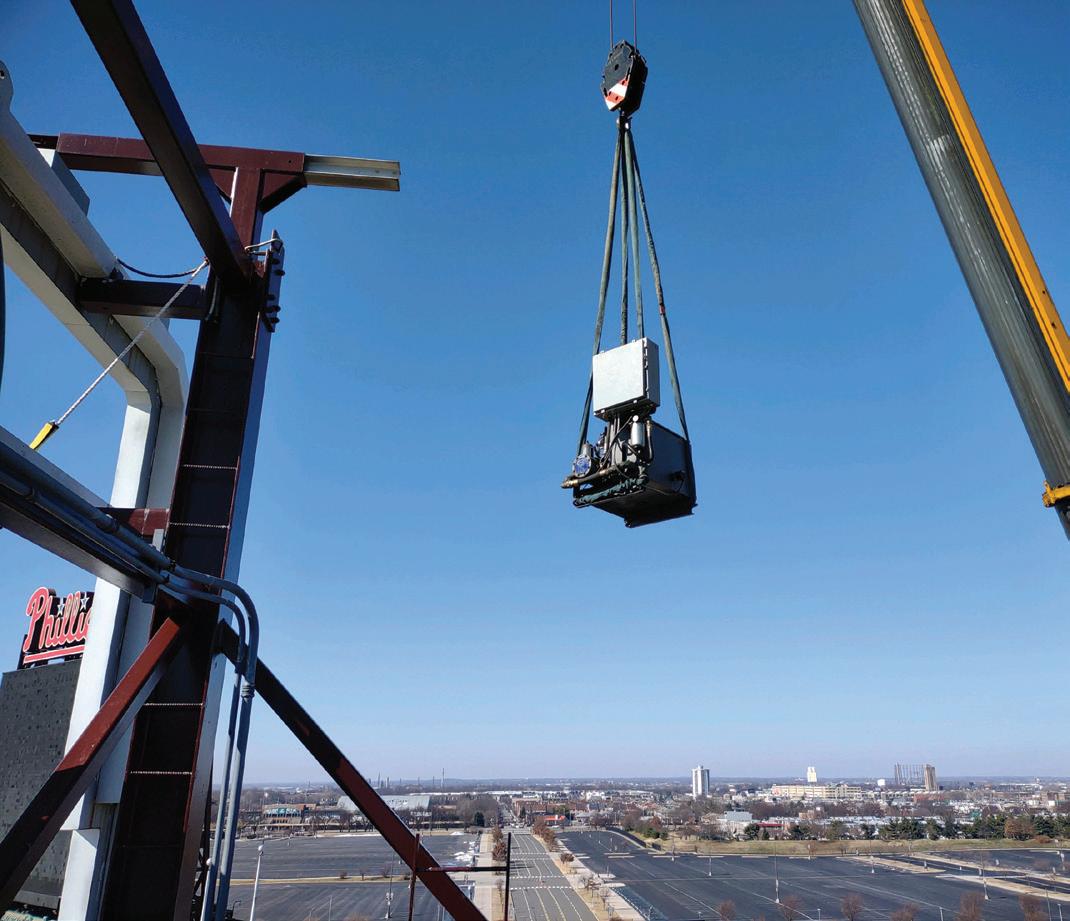
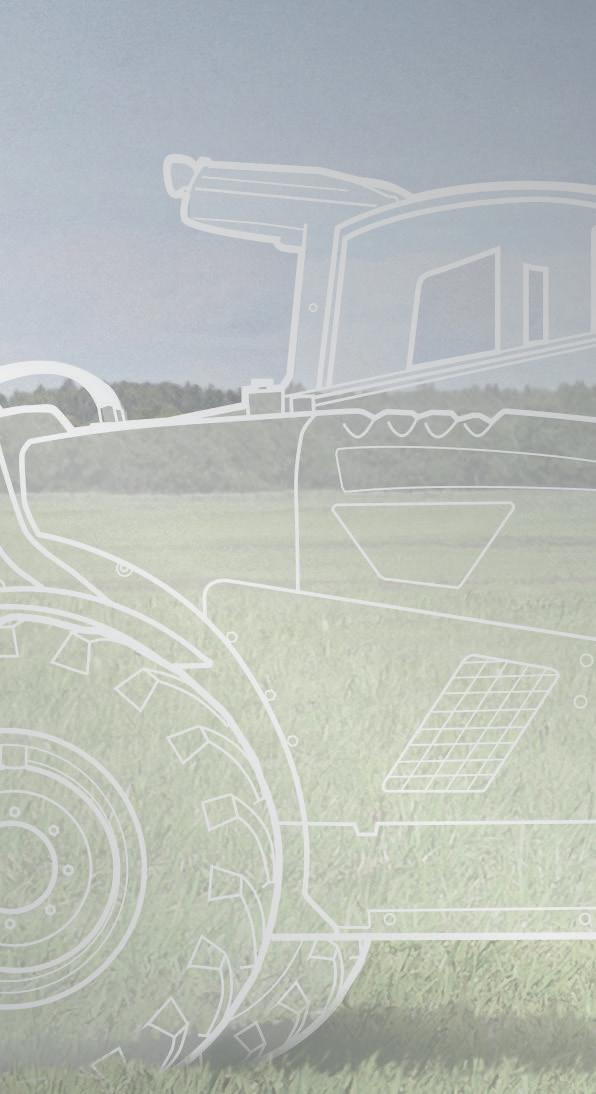
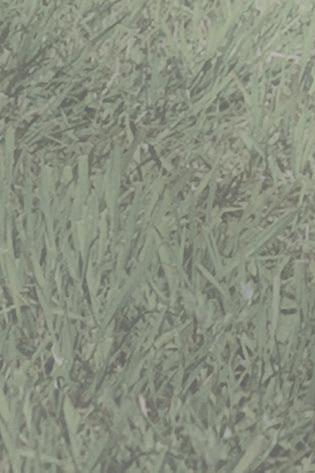

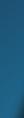


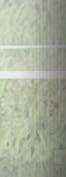
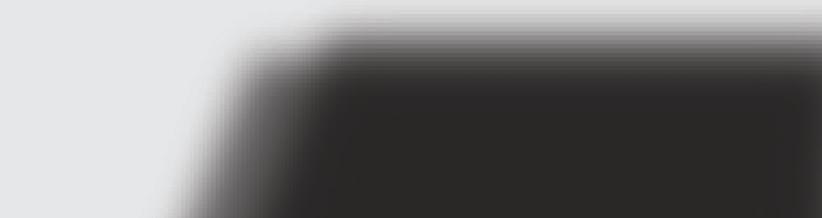

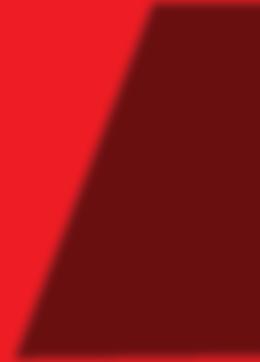

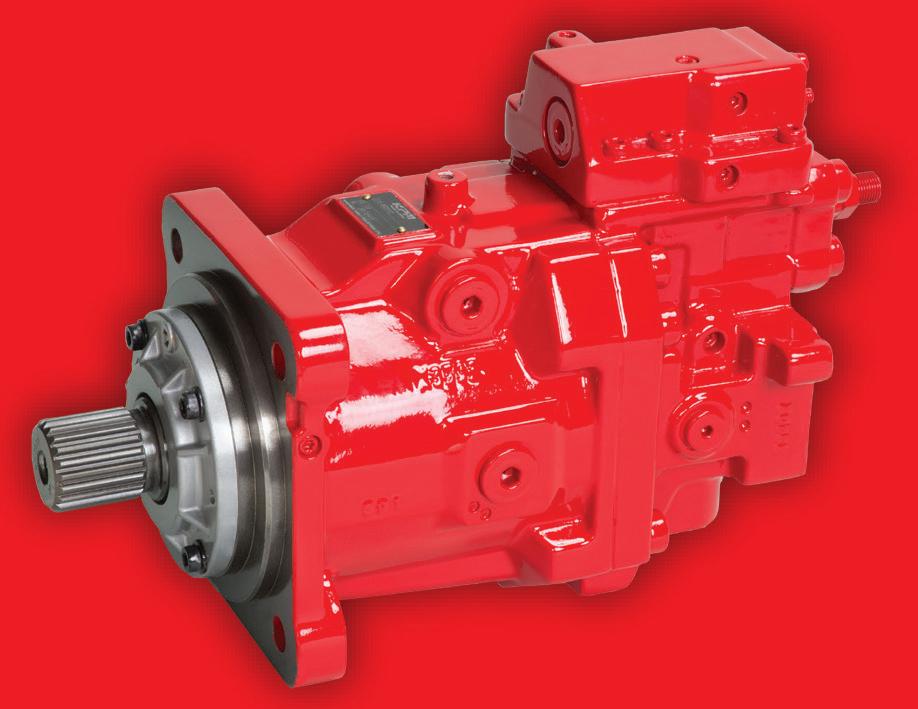

MM basics Metamorphic manufacturing (MM) combines the incremental thermo-mechanical deformation techniques of a metalsmith with the precision of computer controlled robotic systems. It’s often referred to as robotic blacksmithing. In essence, MM is well-controlled open-die forging where machine accuracy and repeatability replace a worker’s limited precision. It relies on closed-loop, digitally controlled, incremental forming to fashion intricate parts with specific engineering properties and locally defined microstructures. Proponents envision it as a new, powerful, agile way to make components that attempts to optimize shape and properties using well-understood metal-processing methods. Glenn Daehn, professor of materials science and engineering at The Ohio State University, sees it as a key part of a broader concept called hybrid autonomous manufacturing. “There are really only six fundamental things that you do in manufacturing: remove, deposit, deform, transform, position and inspect. When you’re doing the deformation, metallurgists know very well how to use thermomechanical processing to change material properties. That’s the big idea behind trying to make hybrid autonomous systems, to put the skills of an artisan into reproducible digital systems,” he said.
Parts are shaped by repeatedly and incrementally forming a piece of metal which is precisely positioned into a press. By automating the process of shaping a part, but using the basic approach of a blacksmith, a machine can treat larger parts and be more efficient and reproducible than a human ever could, said Daehn.
By
Though still in the development stage, digitally controlled robots equipped with powerful hydraulic actuators could form the basis of a new incremental forming technique. of AdobeStock Ken Korane
• Technology Editor DESIGN NOTES 20 FLUID POWER WORLD 8 • 2022 www.fluidpowerworld.com
Tech building blocks
The five basic elements needed for MM, to certain degrees, already exist: sensors, thermal control, actuators and forming tools, robotic manipulation systems and computational power. Fully developing MM requires a synthesis of these underlying
A new way to craft complex parts
O shore supply chain snarls, national-security concerns and the pandemic have all heightened the focus on domestic manufacturing capabilities. A new concept that is currently under development — metamorphic manufacturing — may usher in the capacity for local, flexible production that is especially suited for rapid and economical fabrication of small batch, complex, customized parts with tailored material properties.
| Courtesy
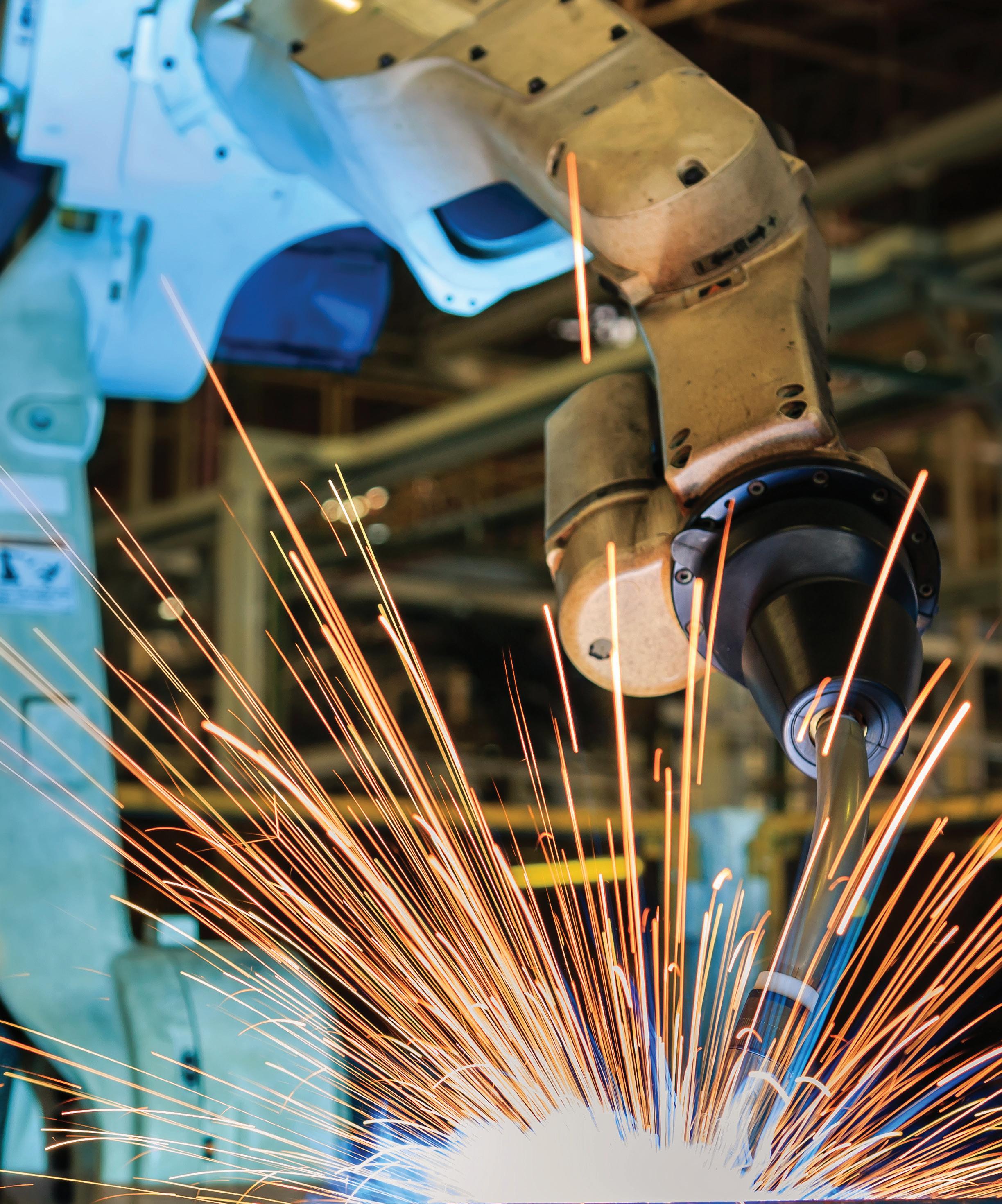
The actuators and associated tools are essential because they provide the plastic deformation needed to move from raw material to final product. High-speed mechanical peening hammers or rollers are possibilities, but hydraulic actuators are ideally suited for the task. They’re generally proven, off-the-shelf components that stand up to the rigors of industrial environments.
Numerous advantages Some experts consider MM the third wave of digital manufacturing, following CNC machining and additive manufacturing. And ongoing advances in software and manufacturing technologies associated with CNC and 3D printing will help spur development of MM. This will bring numerous advantages. CNC machining and additive manufacturing typically don’t produce parts with the highest levels of strength or toughness, and they lack the ability to tailor material properties, as in thermomechanical deformation. A part might need corrosion resistance in one area and high toughness in another. MM can do that by both modifying the chemistry through locally-controlled deposition in additive manufacturing and then deforming the material into the best possible structure, said Daehn. Because small deformation bites are taken, the component can be much larger than the press and MM can be used to fabricate parts of any size, including very large structural components for aircraft, ships, submarines and locomotives. Or the concept could be scaled down to make small individualized medical implants. “We can imagine this being used in operating rooms, where you could deform a nominal mandibular plate to fit a patient’s specific anatomy and do that very quickly, much more quickly than you could with additive manufacturing and, importantly, with better properties,” he Automationsaid.can make these processes more agile and more productive. We can generally turn out parts much faster versus 3D printing or CNC machining, he said. Because it is a shaping technology, there is little material loss, which drastically reduces the amount of waste material compared to CNC machining. And MM uses a lot less energy than does additive manufacturing. “Deformation is inherently a very green process,” said Daehn. In addition, MM can minimize or eliminate the need for component-specific manufacturing dies which often have long lead times and are expensive to machine and store. This dieless manufacturing technique is ideal for rapid prototyping and small batch production. The ability to make components on demand is often essential, such as to replace a forged aircraft landing gear that is decades old and is no longer in production. And the technology might lower the economic barriers many small- and medium-sized manufacturers face and help expand domestic production capacity. Challenges ahead MM could offer manufacturers a better, faster, more costeffective way to make complex, 3D components. Much work is still needed to make it a reality, including integrating
technologies, said Daehn. The system must be able to sense and understand the shape, temperature and condition of the material at each location of the part being formed.
The suite of sensors might range from vision systems for geometric measurements to thermal cameras, hardness testers and ultrasonic devices to measure internal stresses.
Simultaneously it must control the temperature to produce the right structure and properties. The actuator must contact the component where needed with robotic control, deforming the part bit by bit. And a computer must make decisions on how to move and strike the part in order to optimize shape and properties, often learning from how previous parts were made.
Local thermal control could be via induction, plasma or flame heat treating, as well as gas or liquid cooling sprays. Advanced robots driven by CAD/CAM software would precisely manipulate tools and actuators and could run non-stop.
Advanced computers, software and AI capabilities lie at the heart of successful MM integration. They would handle tasks like specifying tool paths and sequencing operations, but would also collect and process sensor data and adapt operations in response to changing component shape or properties. The system might also tap into the latest materials engineering software models to better control properties and microstructures, and even encompass predictiveIncorporatingsimulations.allof these elements into a seamless work cell is no simple task. But the idea of integrating robots and tools with sensors and software, the essence of IoT, is increasingly being embraced across the manufacturing landscape. All of the base technologies needed for MM are progressing rapidly, and there is no reason they cannot be quickly melded together as a useful and practical manufacturing technology, said Daehn.
www.fluidpowerworld.com 8 • 2022 FLUID POWER WORLD 21
“Closed-loop, servohydraulic actuators would be the gold standard, where you could run in displacement control,” said Daehn. “At forming temperatures, most materials have a flow strength of around 50,000 psi, so relatively small tooling sets can take bites of about one square inch at a time.” But engineers can readily tailor pressure levels and actuator size to generate the requisite forces to suit the task at hand.
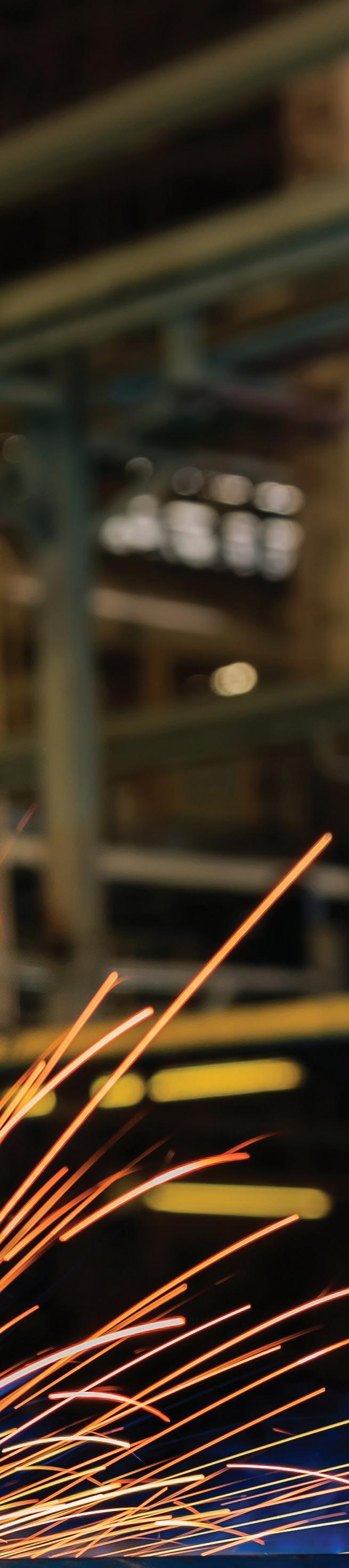
Metamorphic manufacturing work cells would include a network of sensors, thermal controls, hydraulic actuators, forming tools, robotic manipulation systems and substantial computational power.
DESIGN NOTES 22 FLUID POWER WORLD 8 • 2022
|
The Ohio State University, Dept. of Materials Science and mse.osu.eduEngineering
|
FPW
Courtesy of The Ohio State University
Ohio State students used conventional machine tools and plastic materials to test out hybrid autonomous manufacturing concepts.
The trials were part of the LIFT (Lightweight Innovations for Tomorrow) competition sponsored by the American Lightweight Materials Manufacturing Innovation Institute.
Courtesy of The Ohio State University hardware and software into an actual, autonomous production cell. The same holds for research into areas like computational materials-engineering models that accurately predict material behavior throughout the various stages of the MM process. A major roadblock is funding. Several affiliated universities around the country are beginning to consider hybrid autonomous manufacturing, but significant government support is only starting to catch up to the concepts. Federal agencies annually provide significant grants to advance science and engineering, but they haven’t been particularly kind to new process developments that focus on problem solving via integration versus new fundamental ideas, said Daehn. European and Asian funding models have a more favorable view of manufacturing R&D because it ultimately benefits their economies, he said. “We are getting a lot of good traction from the defense world,” he continued. This February, the DoD issued a report, “Securing Defense-Critical Supply Chains,” that detailed forgings and castings as one of the four most critical vulnerabilities to national security, the others being hypersonics, energy storage and batteries, and microelectronics.Forgedandcast components are essential in everything from ships and subs to aircraft, combat vehicles and weapons systems. But due to offshoring and industry consolidation there are relatively few domestic suppliers of many mission-critical components. For instance, China produces four times the tonnage of castings as does the U.S. “DoD counts on foreign countries, including China, for very large cast and forged products used in the production of some defense systems and many machine tools and manufacturing systems in which the DoD is reliant,” said the report. “The other thing we don’t recognize enough is these are key processes in making the machines that make the machines. If you’re going to build a big press, you need big forgings and big castings. Our capacity to make those kinds of machines has diminished,” added Daehn. DoD’s action plan for castings and forgings involves devising a strategy to increase the industry base, expand partnerships and develop domestic production capability. Current plans call for publication of a roadmap no later than the end of the second quarter of FY 2023. “The center of gravity in metal forming is absolutely outside the U.S.,” said Daehn. “There are a handful of professors here in the United States that do metal forming, a very small handful. And we have a hard time fighting for funds. Whereas the Chinese metal-forming society is very robust. Germany likewise has a very robust metal-forming culture, a number of professors and chairs, and a strong tradition. “I think we have a fairly unique approach, trying to bring together the machines, the controls, and really putting the material science kind of front and center to it. But there are labs in Germany that are better equipped and staffed than we are. The same holds for China and, to a certain extent, Japan. In many ways the United States did a lot of the great, early machine tool work, but the center of gravity has been absolutely moving away from us,” he said. We’ve talked to people across the aerospace industry, as well as forgings suppliers, Air Force research labs, logistics experts and equipment makers, said Daehn. “We have a consensus that, yes, this is a good idea. We’ve made a lot of converts and I haven’t had anybody who has maintained skepticism. “If we are going to reverse this trend, the workforce is also crucial. We need to start getting students involved and encourage a lot more people to be in manufacturing,” he said. To achieve widespread MM adoption, the next-generation will need a broad understanding of materials science and engineering, manufacturing processes and robotics, and software engineering.
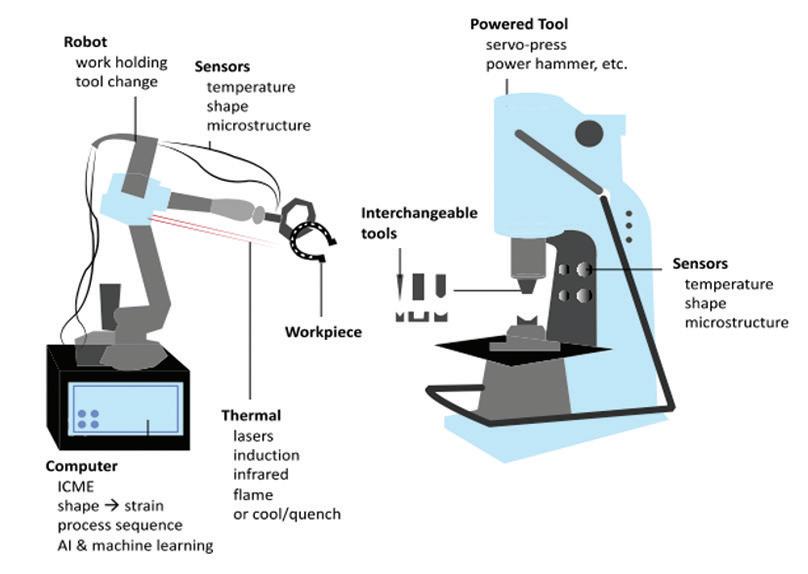
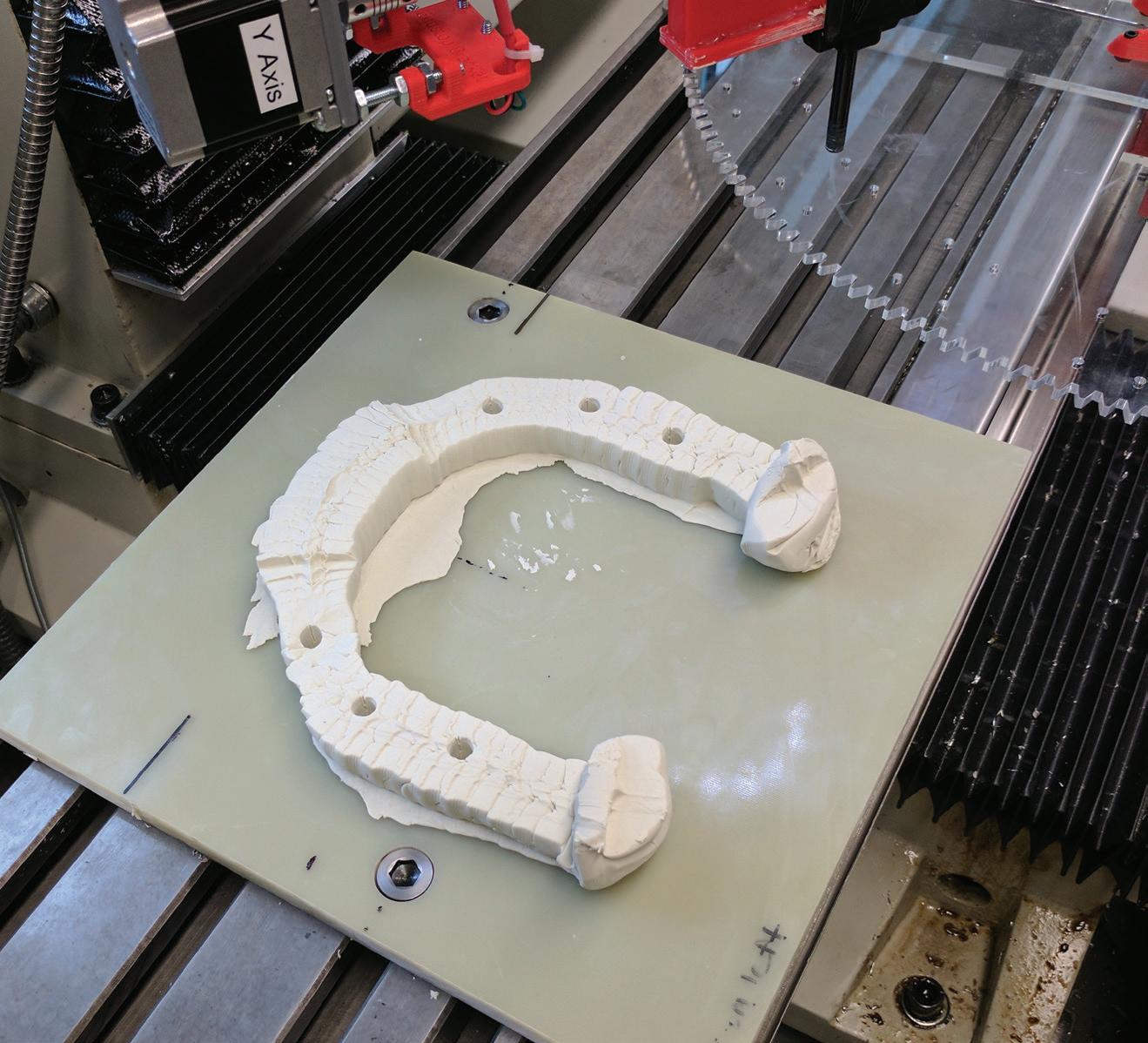
www.hawe.com • 1.704.509.1599 Twenty-five years ago, North America was introduced to HAWE Hydraulik through its American subsidiary, HAWE Hydraulik. Today, many of America’s most rugged industries rely on 70 plus years of HAWE’s dependable German engineering and experience to help them build equipment with extremely robust hydraulic systems. Congratulates CELEBRATING 25 YEARS IN NORTH1997AMERICA-2022 2
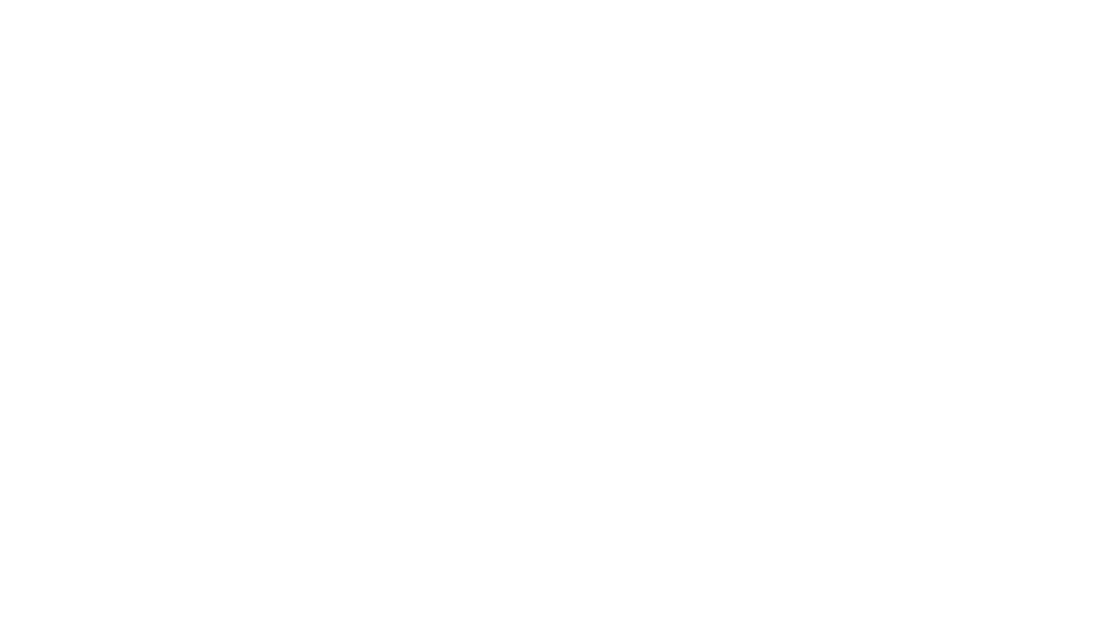
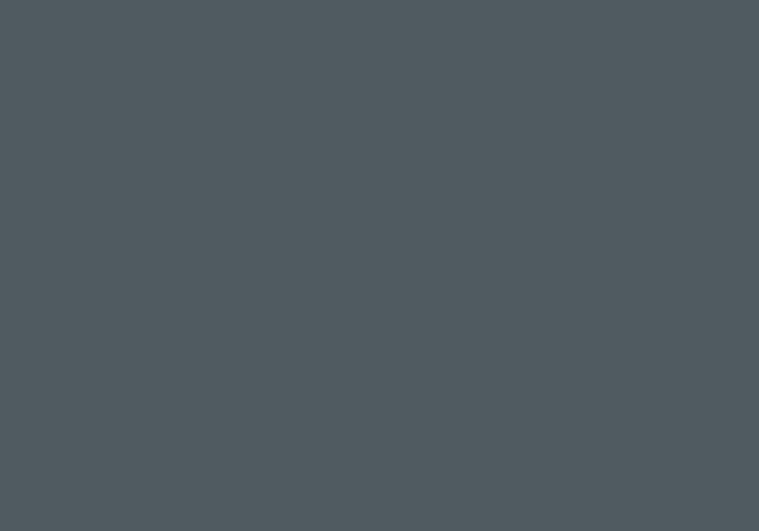
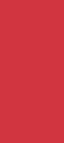
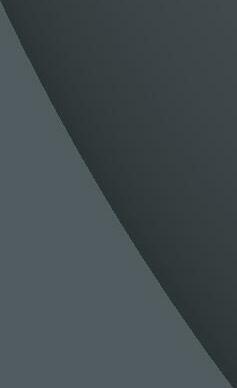
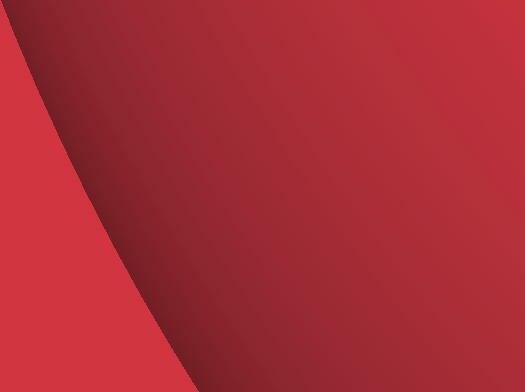
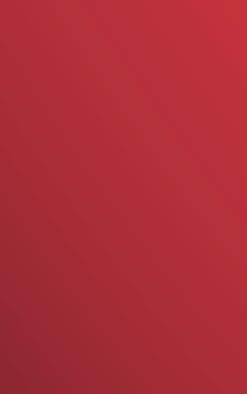
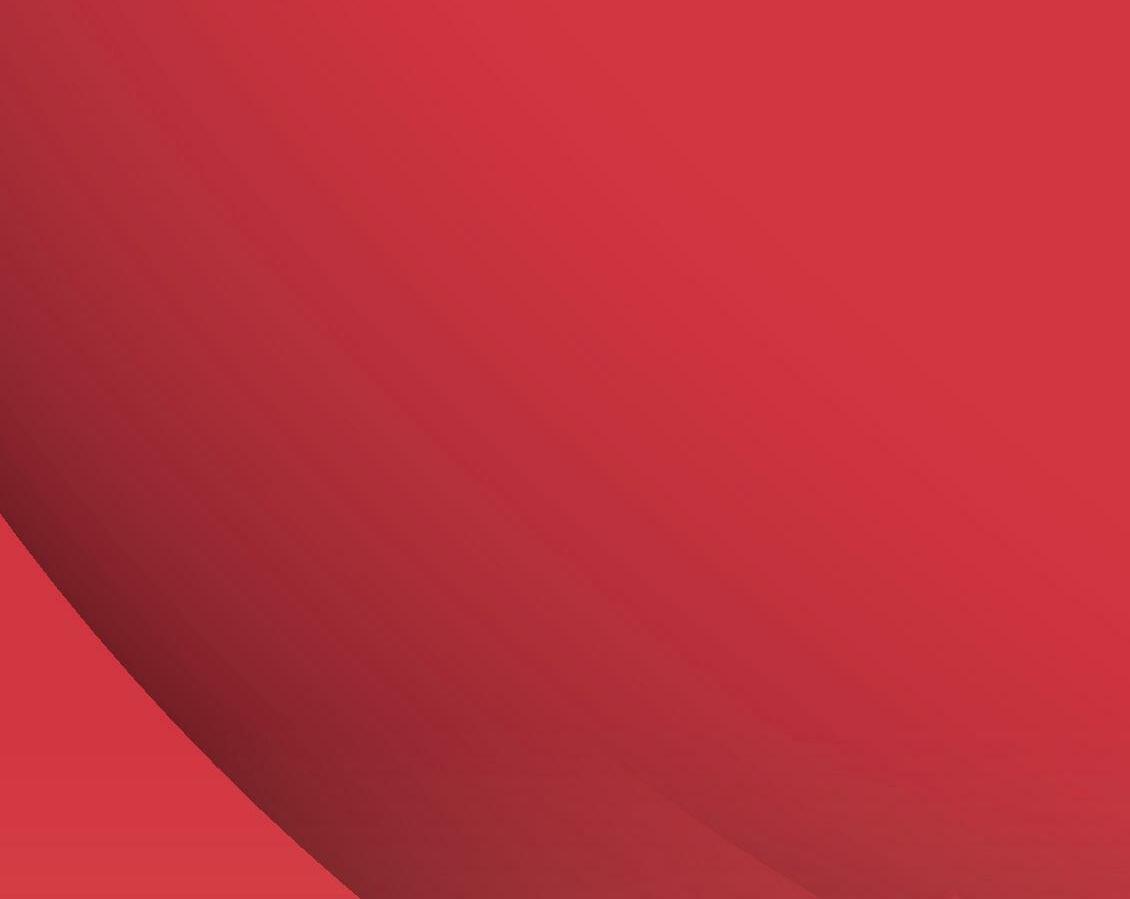
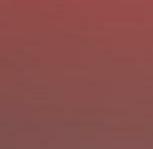
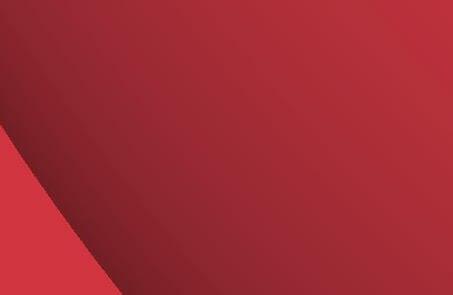
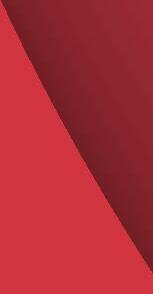
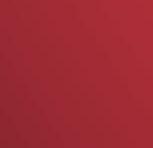



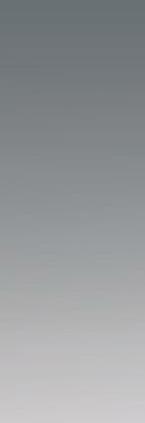
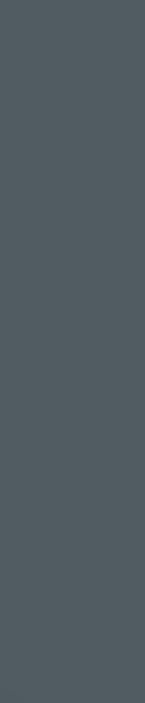
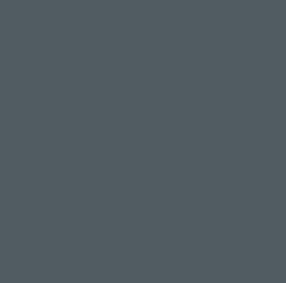
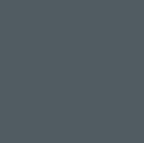

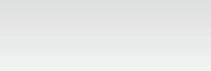
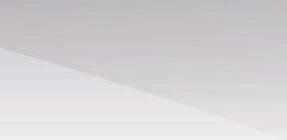


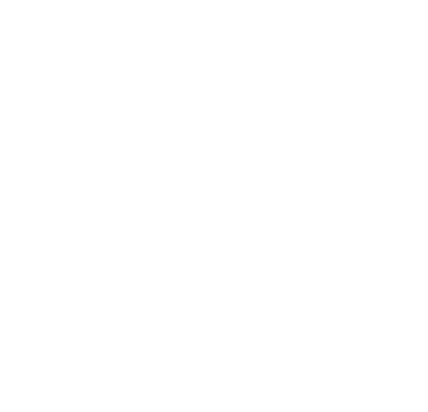
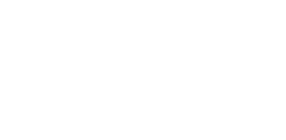
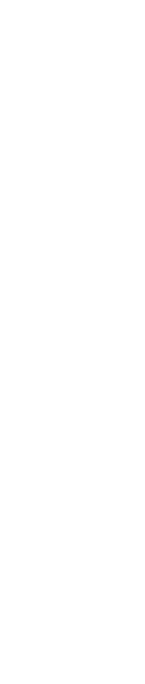
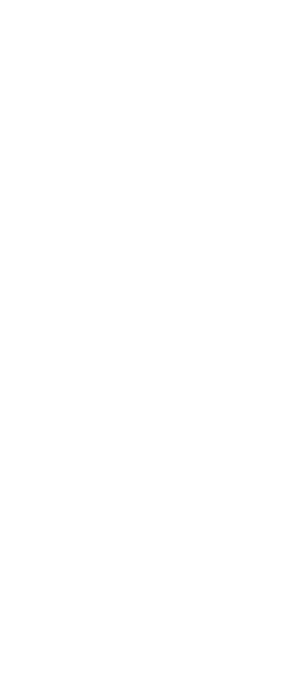
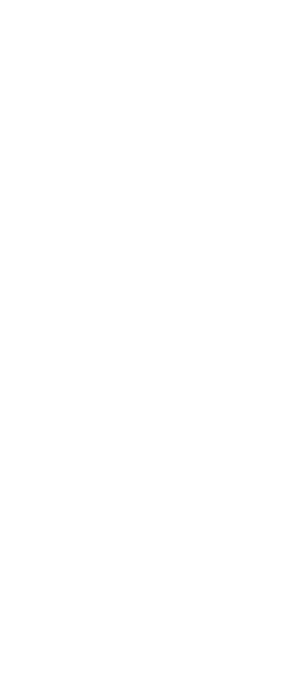

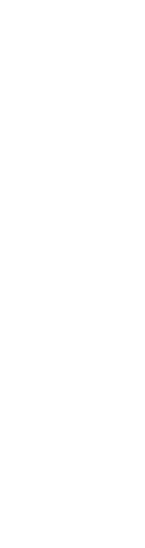
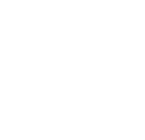
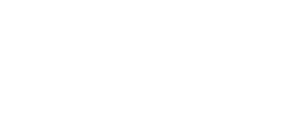
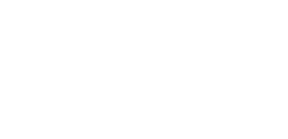
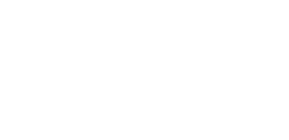
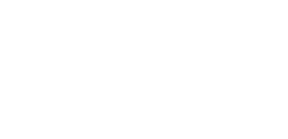
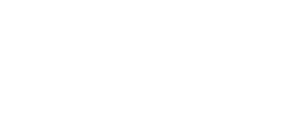
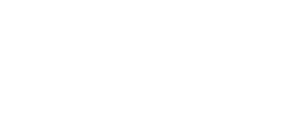
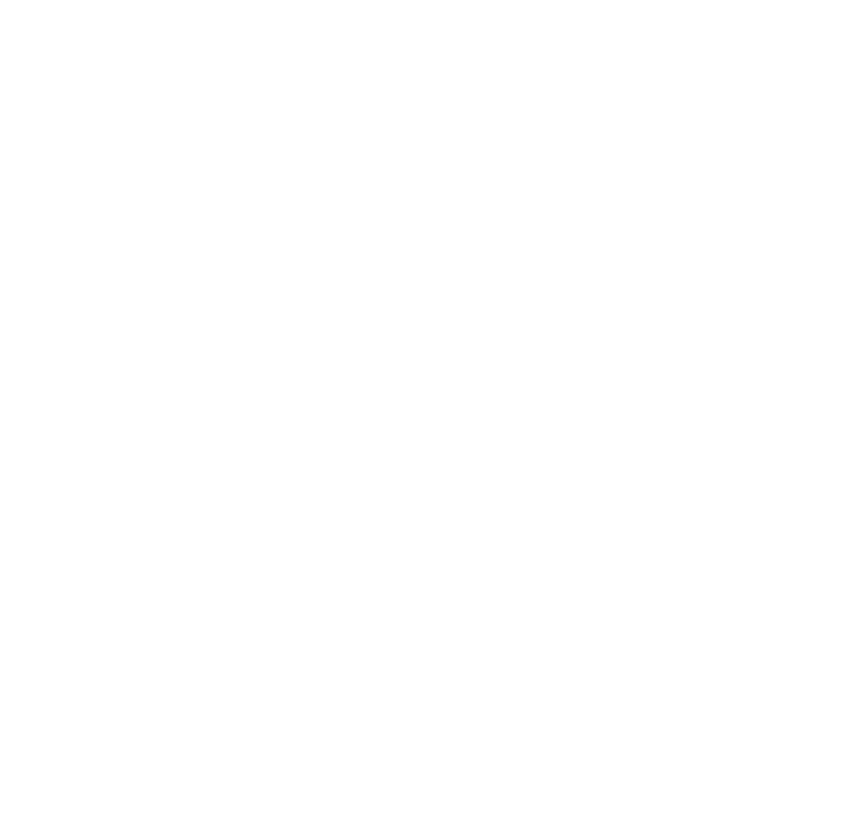
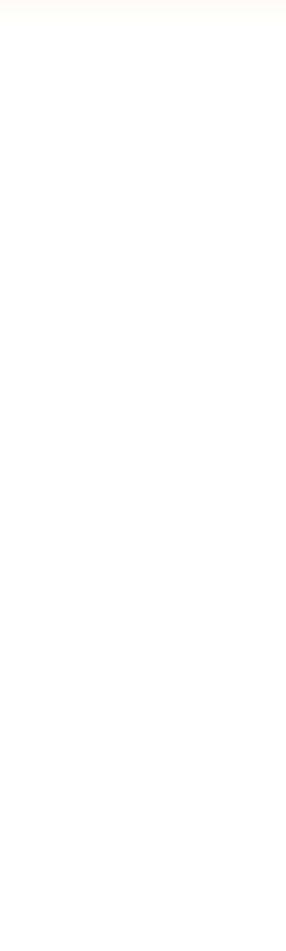

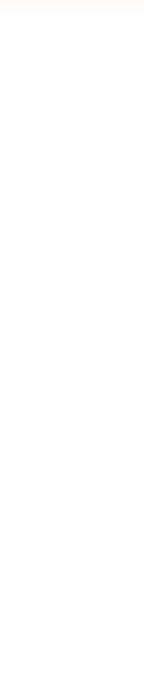

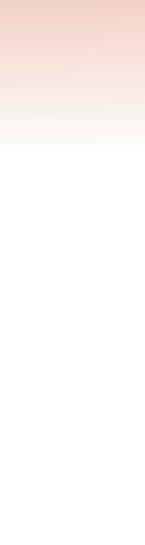

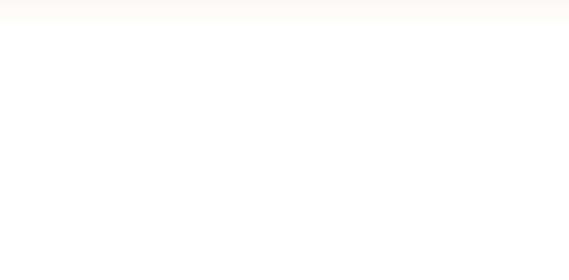
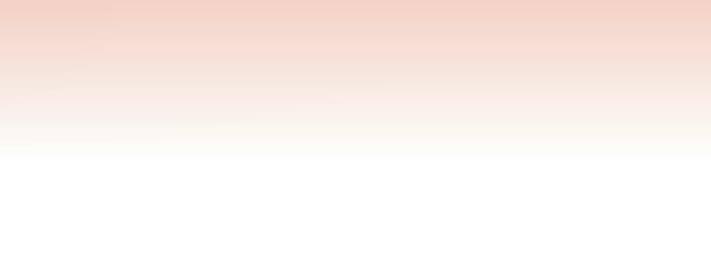

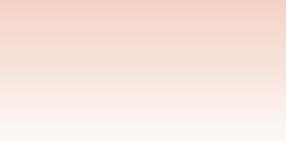
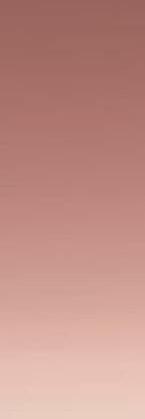
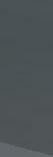
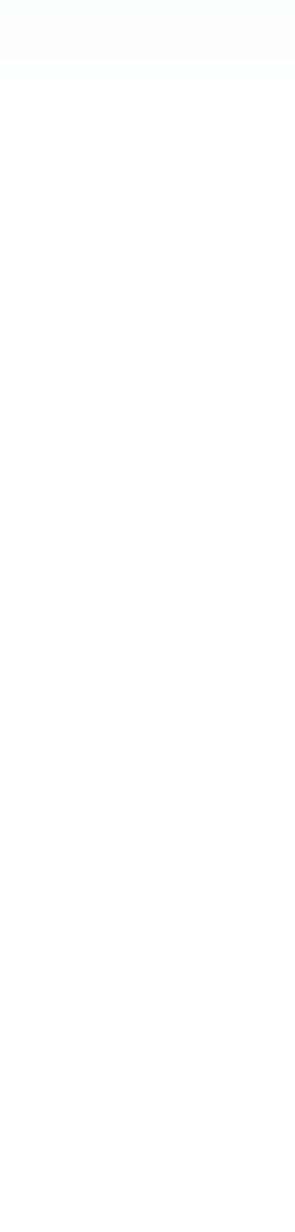
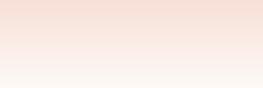
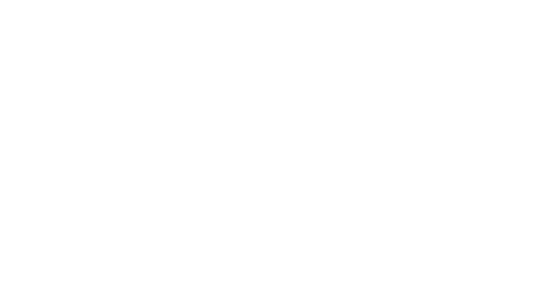
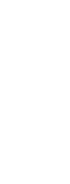

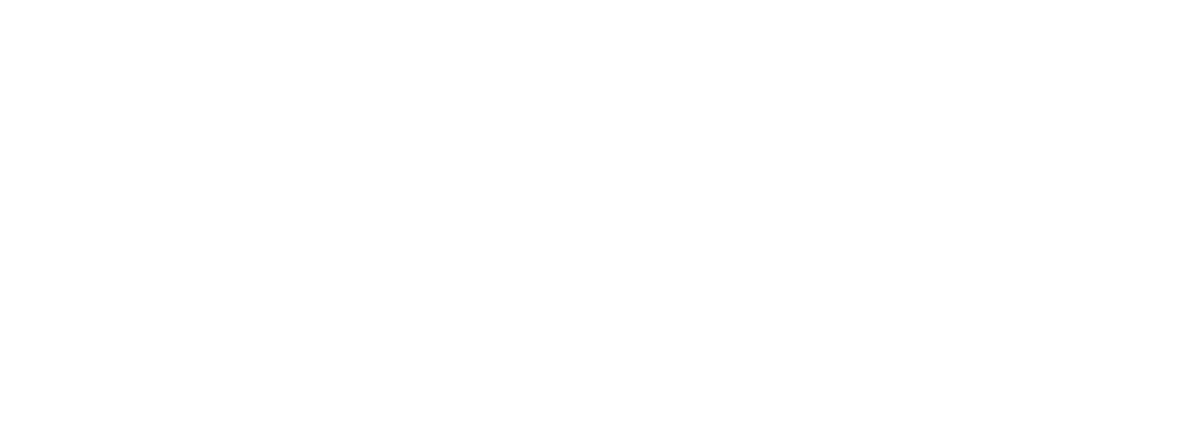
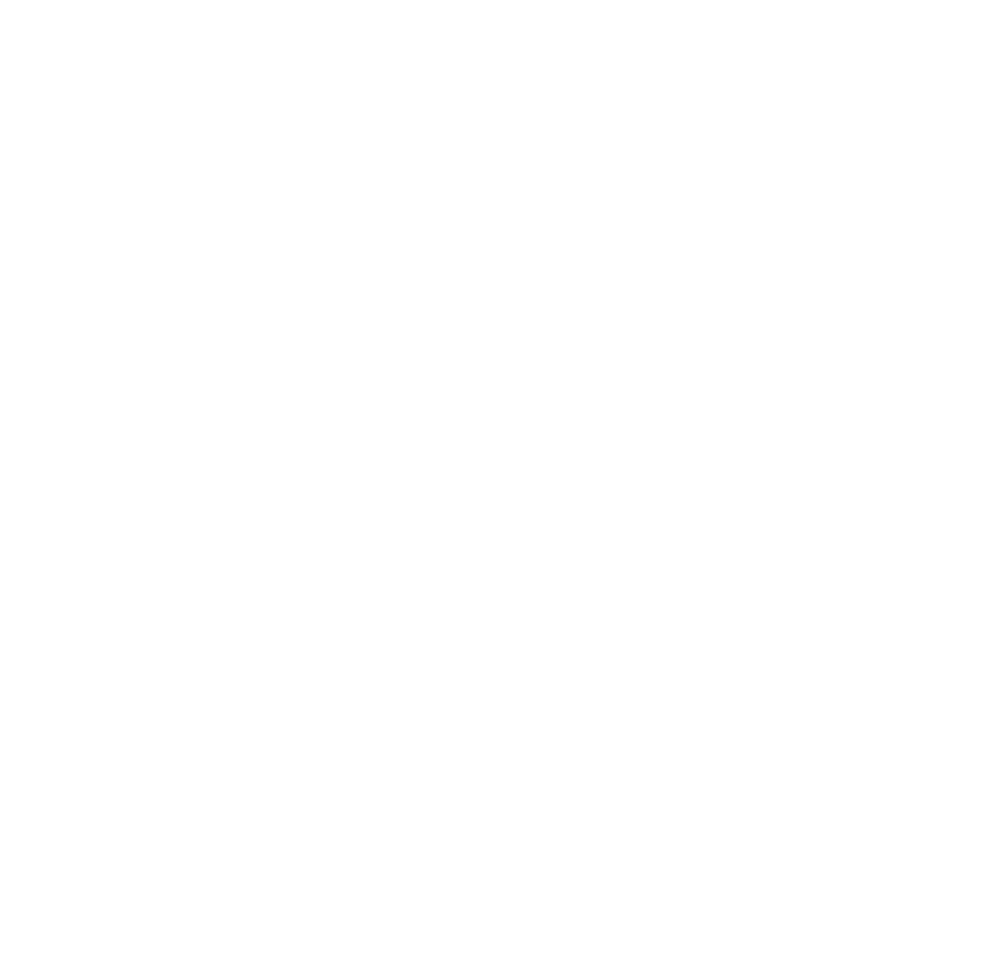
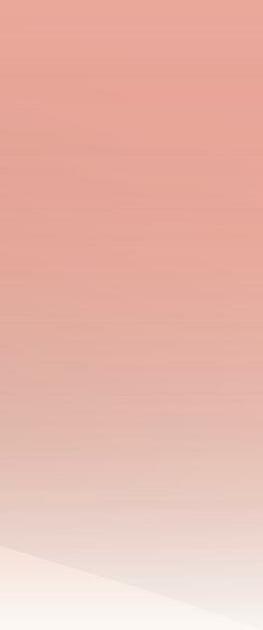

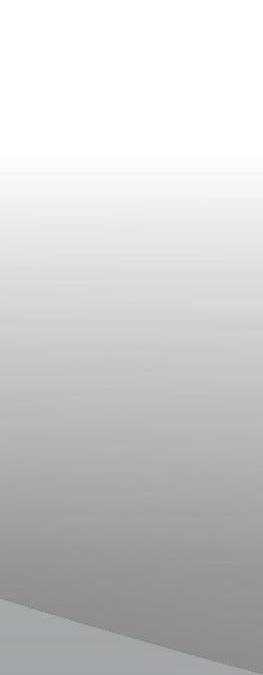

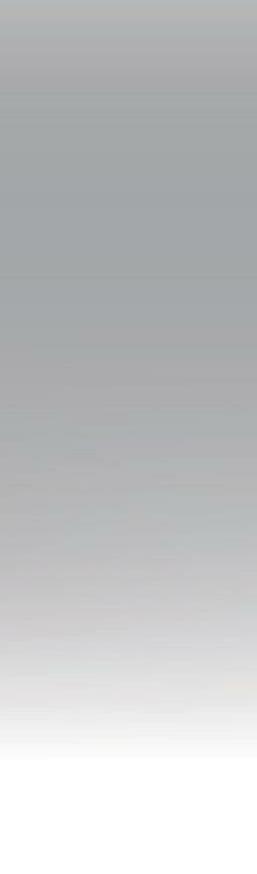
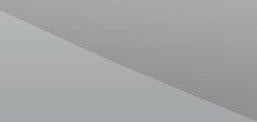
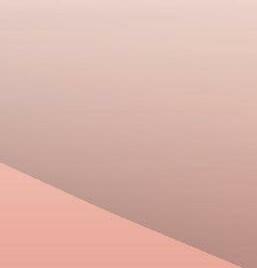
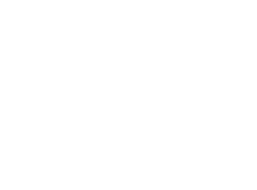


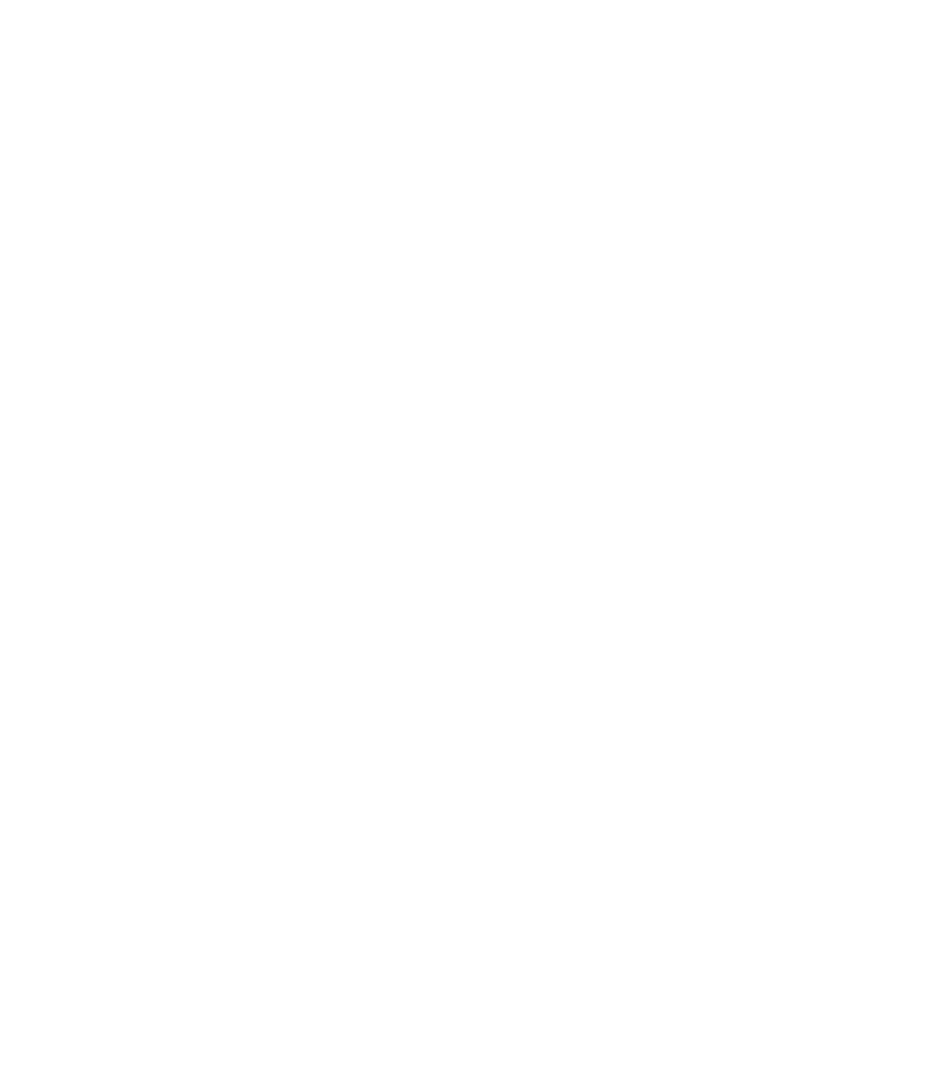
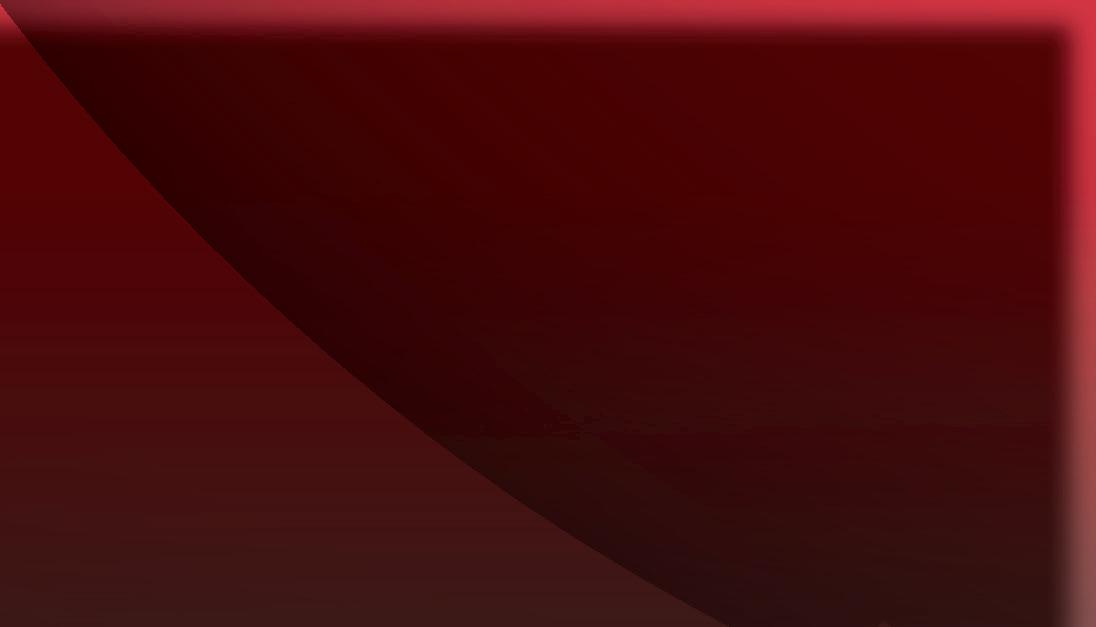
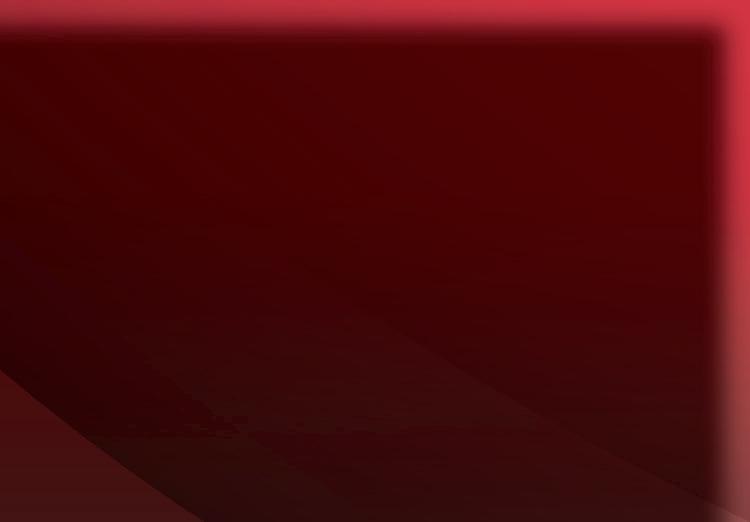
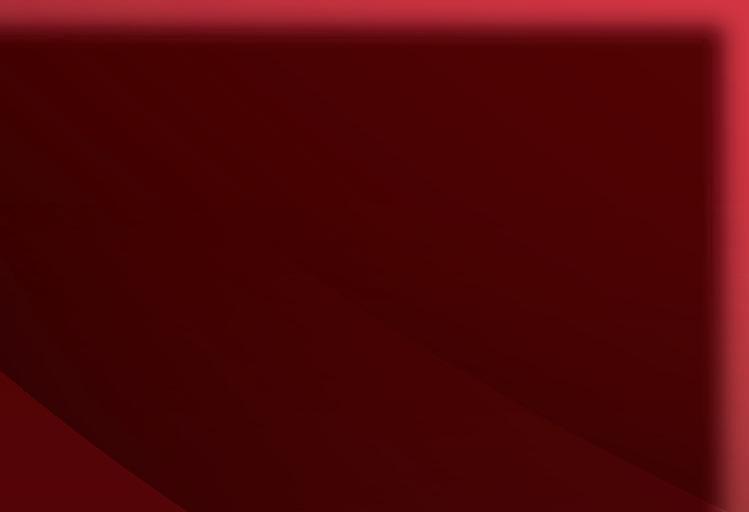
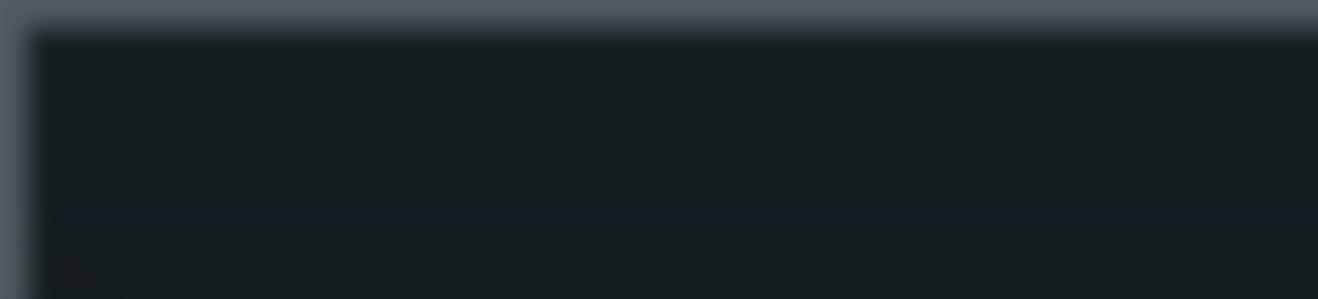
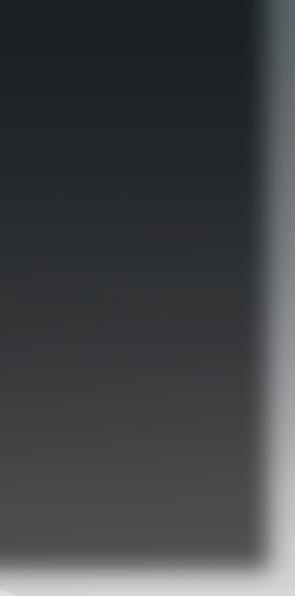
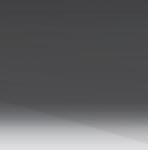
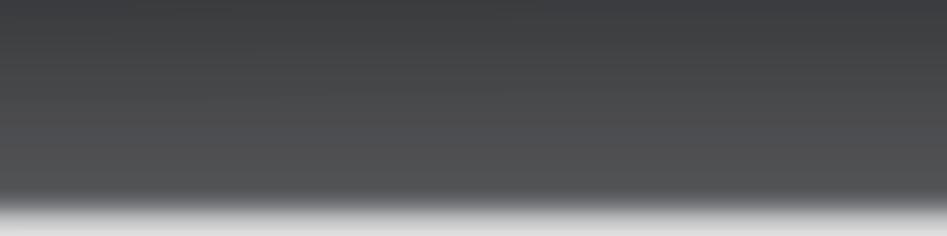

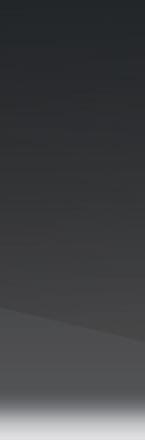
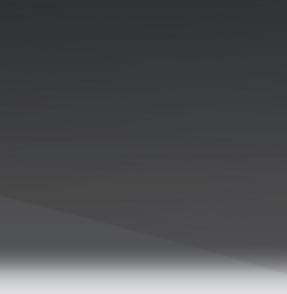
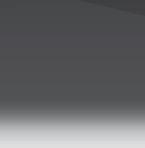
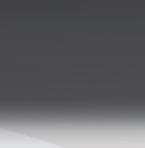
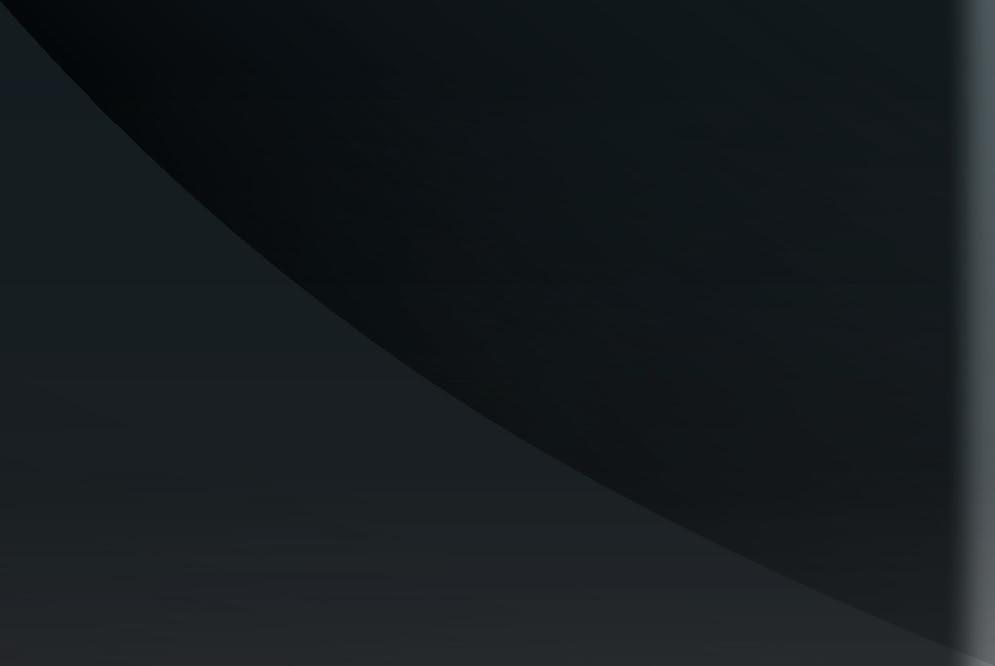
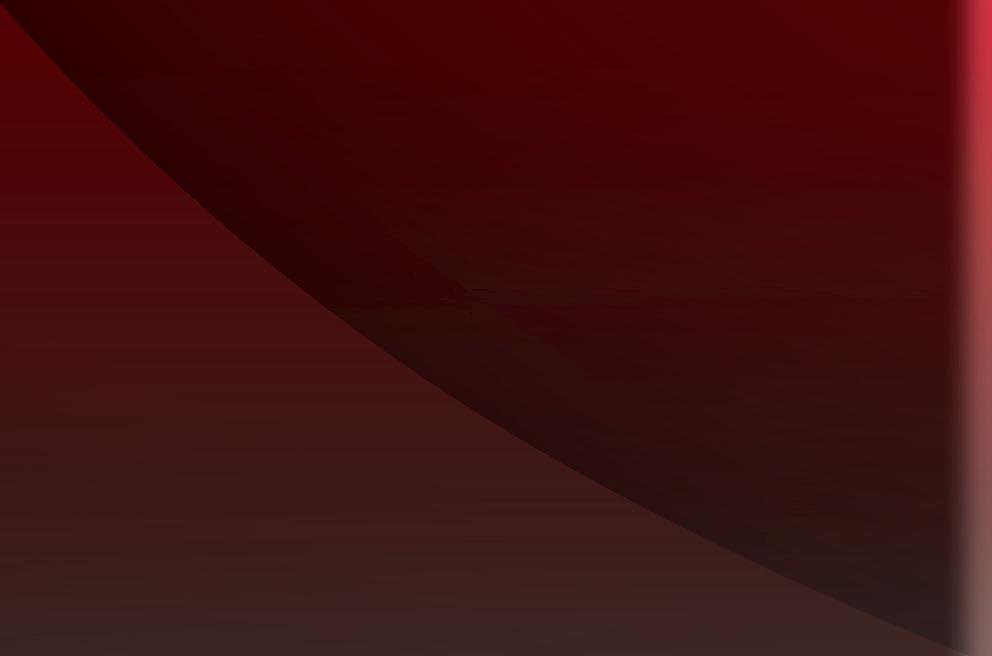
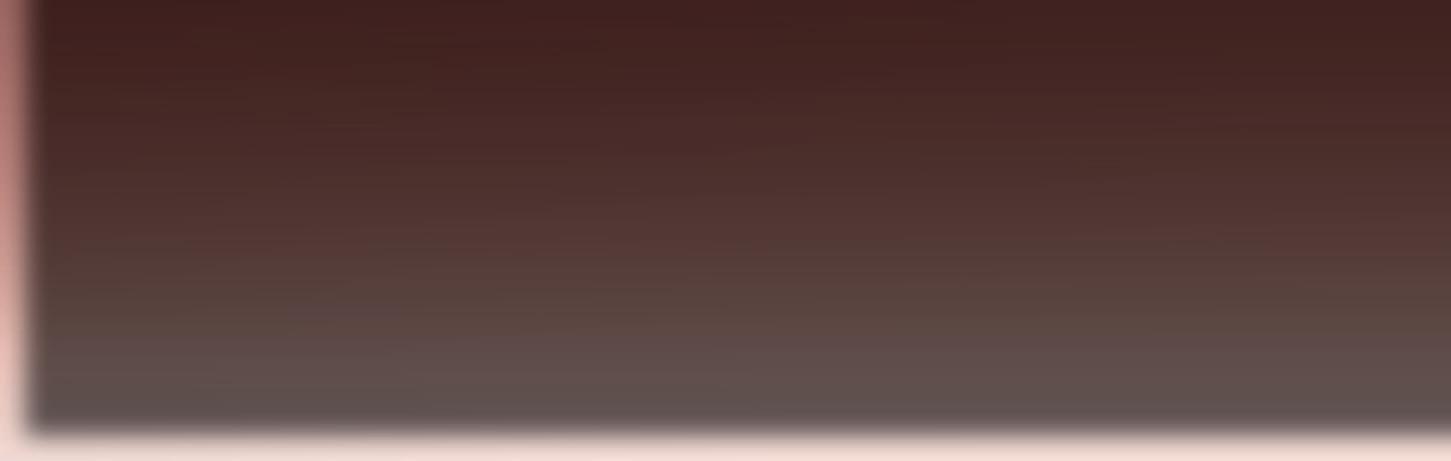
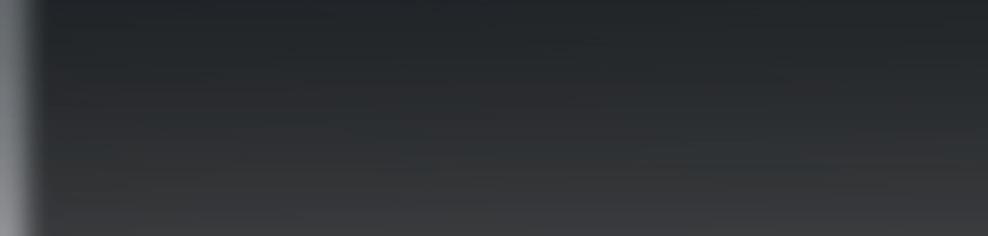
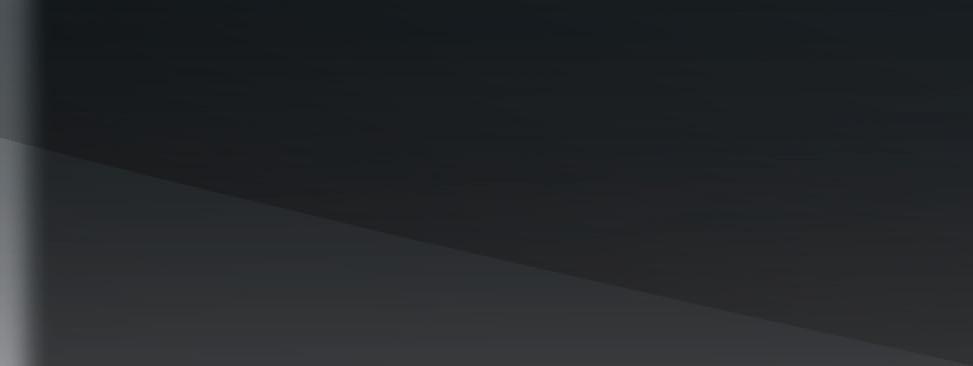
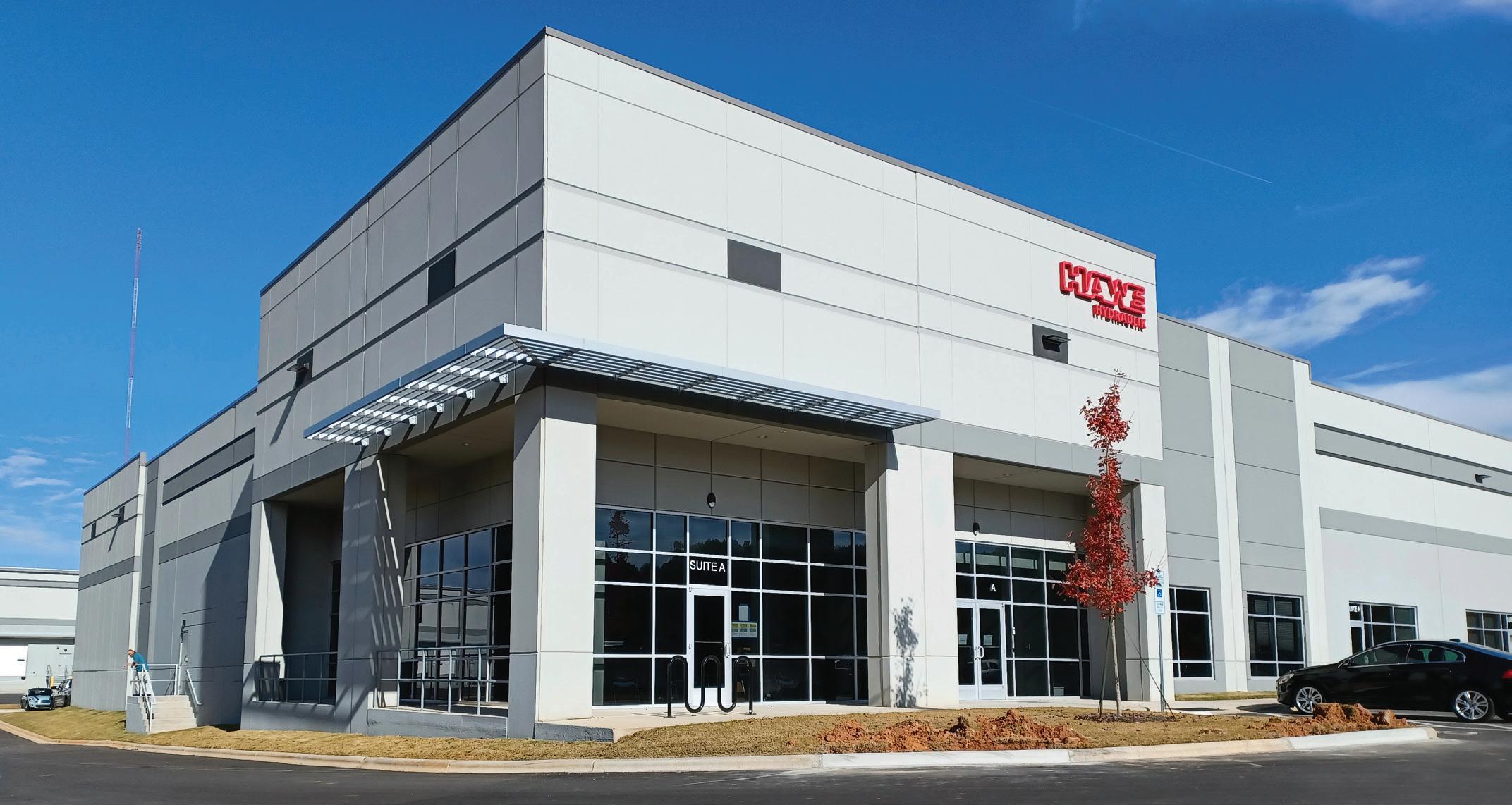
Although spring motion is periodic, meaning it will continue to oscillate until prevented from doing so, you can view this motion as linear. Linear motion such as the forward travel of a vehicle will continue until acted upon by an outside force, assuming we ignore friction. For example, a vehicle uses brakes to convert its inertia into heat, slowing the vehicle to a stop. The same effect must be applied to a spring — its inertia must be converted to heat to slow the oscillation.Mostintuitively know that shock absorbers slow the spring’s oscillation (and therefore the vehicle’s bouncing) but are unaware they do so by converting that motion into heat. As a fluid power professional, you probably know better than most how fluid dynamics govern the behavior of shock absorbers and that friction from pads on steel is not the only way to convert motion into Restrictiheat.ngfluid motion under pressure offers a convenient and controllable energy conversion method. The kinetic energy comes from the imparted inertia created when a vehicle dives, pitches, rolls or hits a bump or hole. The pressure created inside the shock absorber must go somewhere, or the entire unit would just blow apart. Orifices inside the piston of monotube “shocks” restrict flow and convert the hydraulic energy into heat as the fluid passes under pressure.
The diff erence between automotive
FUNDAMENTALS 24 FLUID POWER WORLD 8 • 2022 www.fluidpowerworld.com
Miniature shock absorbers | Courtesy of Ace Controls and industrial shock absorbers
A look at design Shock absorbers are essentially small-bore hydraulic cylinders equipped (or drilled) with orifices in the piston. Those orifices’ combined crosssectional area dictates the piston’s flow rate potential. The “compound orifice” of the drillings equates to an overall orifice size that adheres to any chart displaying pressure versus flow curves. The smaller the orifice size, the less flow across the shock absorber piston and the higher spring braking effect. Larger orifices result in a more relaxed damping effect on the spring oscillation, while smaller orifices reign tighter control over the suspension movement. In real-world terms, you’d correctly expect a luxury vehicle to take advantage of the relaxed damping of larger orifice sizes. At the same time, sports cars wish their suspension movement highly damped to more quickly subdue the movement of their stiffer springs. High-performance shock absorbers use much more sophisticated technology than the simple example described above, ignoring modern examples such as magnetorheological dampers. A primary high-performance shock absorber uses a monotube design alongside nitrogen charging, making it a sophisticated hydraulic component. Imagine placing a second floating piston in the space between the primary piston and the cap and then nitrogen charging the volume between the cap and floating piston, much like a piston Your first thought upon hearing the term shock absorber leads your mind to the cylindrical tubes mounted to the four corners of your vehicle’s suspension system. Other than the misnomer (“shocks”), your correct thinking applies to the term. Even the term “shock absorber” is a bit misleading, and industry professionals may prefer you to call them dampers. But just as another vehicle suspension component — the anti-roll bar – is sullied with “roll bar,” we’ve learned to live with such colloquial terms. Vehicle shock absorbers don’t even absorb shock the way you assume. A vehicle with only four coil springs will absorb the impacts of bumps just fine — only once the spring compresses to absorb that bump, the energy stored in that compression releases to expand the spring past its previous resting point. If you’ve experienced a ride in a vehicle with “blown shocks” or driven in any American-made sedan from the 1980s, you’ll remember the wallowing that occurred after a large bump. The vehicle would continue to oscillate until the chassis settled down once again. Springing into action Springs naturally oscillate when attached to a mass spurred into motion. The oscillation rate depends on the weight of the mass and the spring’s constant or spring rate. The spring rate defines the compressibility of the spring, usually described in pounds per inch. For example, if 200 lb were loaded onto a spring, causing it to compress 2 in., the spring rate is 100 lb/ in. A loaded spring will oscillate indefinitely in a vacuum with no friction, but on a vehicle, friction eventually tames the spring until it once again achieves balance.
By Josh Cosford • Contributing Editor
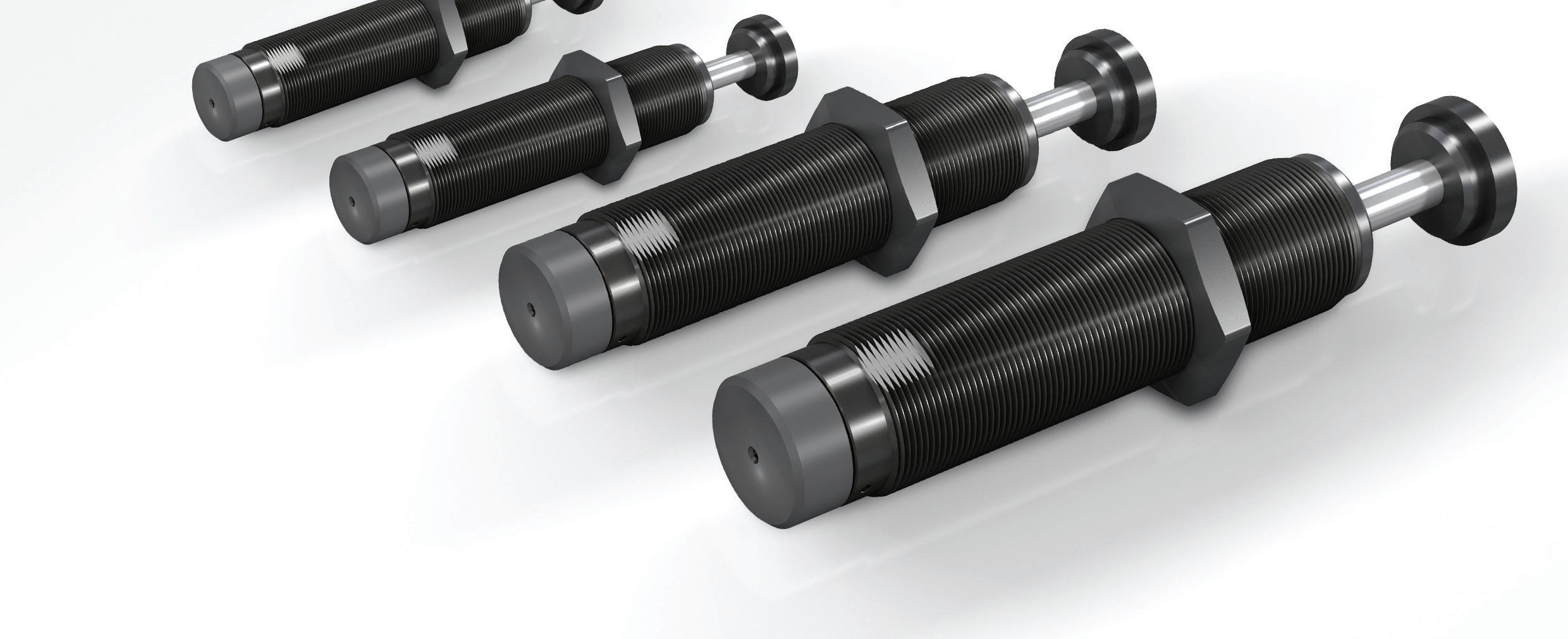
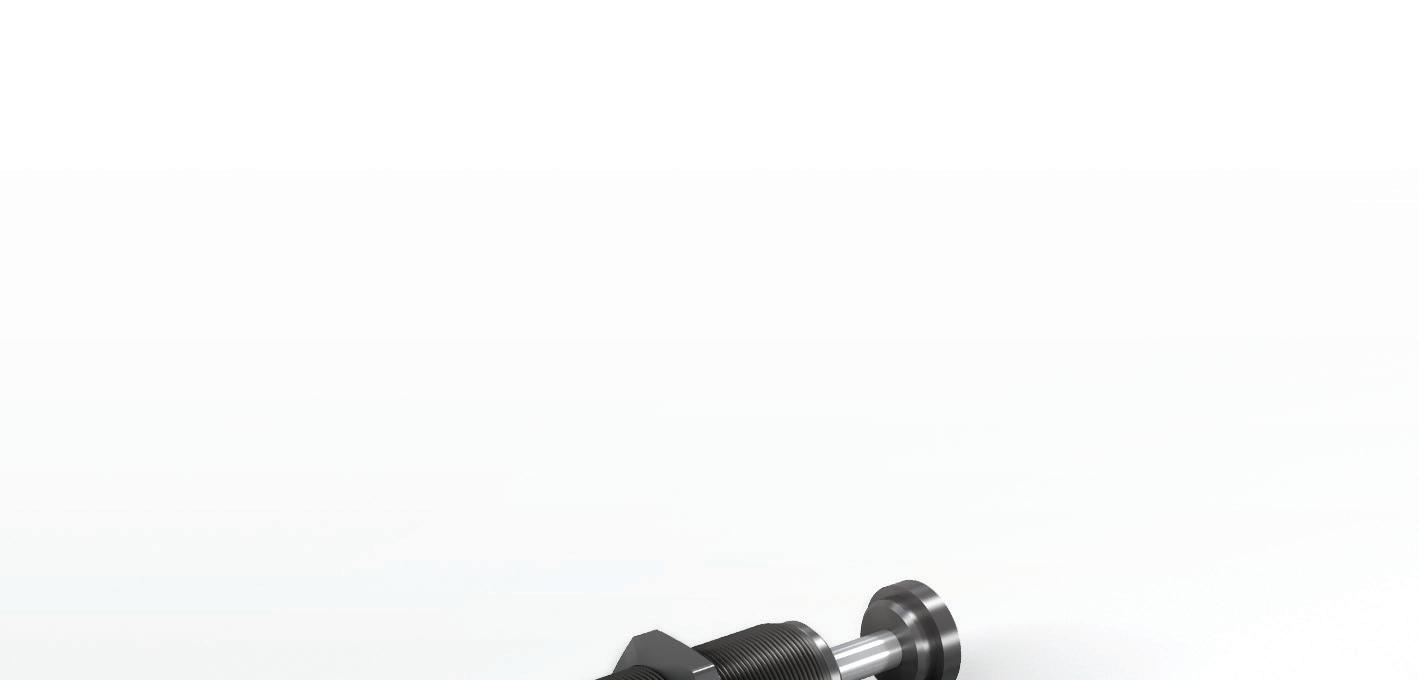
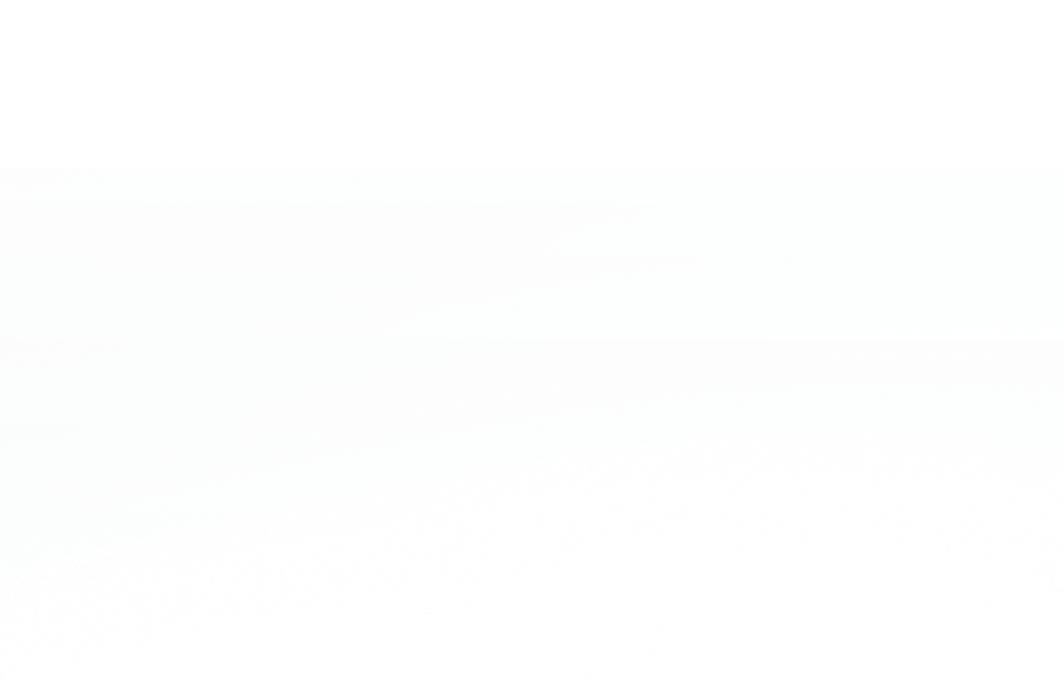
absorber assembly and the piston travels down the length of the shock tube, fluid exits all four orifices under pressure, where a relatively light damping action takes place.
The piston covers the hole and continues past the first orifice, reducing the flow potential across the combined orifices. As a result, the shock absorber slows further with only three holes to pass pressurized fluid. The same effect occurs as the piston covers the second orifice, leaving only two left to evacuate fluid, once again reducing the velocity of the piston.
Courtesy of Enidine
The construction of industrial shock absorbers differs slightly from those used in automobiles. Both designs use orifices to meter the flow of oil, although where the oil is metered varies by design. The more popular multiple-orifice shock absorber uses an ingenious yet simple method to increase the damping response sequentially as the device nears its bottom position. The shock tube equivalent to the pressure tube used in automotive looks similar until you discover the orifice drillings in the shock tube itself. Rather than equip disc valves and axially aligned drillings, the industrial shock absorber uses orifices along the tube length to increase damping force inversely proportional to the stroke length. For example, assume the tube has four drillings along its length, evenly spaced between the piston’s retracted position and the cap. Then, as the load compresses the shock
Because a shock absorber is a differential cylinder, you fluid power professionals are intuitively wondering where the cap side fluid has gone since you know its larger volume cannot fill the less volume taking up space around the rod. As fluid exits the shock tube, it flows into a cavity between the tube and the primary cylinder. A hole in the shock tube ports to the rod’s area, so fluid entering there helps prevent cavitation. The rest is absorbed by a foam accumulator and stored until the piston retracts, drawing the fluid out and back into the shock tube. Industrial shock absorbers come in downright tiny versions with perhaps less than 10-mm bore shock tubes, growing across various sizes and configurations up to 8 in. bore or larger. The smallest examples may absorb loads of 250 lb at a velocity of 50 in./sec or faster (although not simultaneously). Larger bore shock absorbers damp the movement of even the most enormous loads, quickly tackling 200,000 lb of force. Remember that the spring installed with the shock does the heavy lifting to handle a high load, and the shock absorber itself simply damps the motion of the spring.
|
Finally, when only the last orifice remains open, the load should have slowed proportionately relative to stroke length, and combined with the increased spring force, the load will stop.
Industrial shock absorber construction
www.fluidpowerworld.com 8 • 2022 FLUID POWER WORLD 25
I should mention that shock absorbers cannot simultaneously handle their maximum shock force rating with their maximum acceptable velocity. If you’re unsure, discuss your requirements with your shock absorber manufacturer of choice. Ultimately, automotive and industrial shock absorbers are dynamic orifices designed to transform kinetic energy into heat. That damping may be against an oscillating load or simply one piston compression stroke. Either example offers a peek into yet another fluid dynamic principle that fascinates our industry. FPW accumulator. Add fixed flow control valves to each side of the piston, and you have a highperformance shock absorber. The pistons are more complex than the machined round slug used in hydraulic cylinders, using multiple layers, plates and disc valves. Their combination allows different damping rates for compression and rebound while also allowing multi-stage damping. A low-speed orifice allows easy fluid flow for shallow dips or bumps, providing a gentle ride. When a harsh impact results in rapid movement, the disc valves close to direct fluid through the more-restrictive orifices, attenuating suspension movement more rapidly. Twin-tube shock absorbers previously dominated the market, most notably because they became popular more quickly. Early suspension damping technology used two leather-covered sleeves mounted one inside the other, and clamping devices allowed mechanics to increase the friction as the assembly wore. Not a sophisticated component, modifications to its design led to the twin-tube shock absorber, where a valve assembly was added to the piston and the cap of the primary tube. Twin-tube shocks were also popular because of their inexpensive cost to manufacture. Their barrel requires no precision machining, such as on the monotube design. Without a precision-machined tube, the floating piston designed to separate the nitrogen from the oil would have no chance of sealing. The twin tube design was also more prone to aeration as the nitrogen gas could quickly enter the primary tube, although some modern designs now employ a bladder. Shock absorber applications aren’t limited to automotive applications, of course. Industrial shock absorbers find themselves on material handling applications, trollies, conveyor systems and even amusement rides — machines and applications where a moving object must slow quickly and safely without slamming or bouncing. An ideal shock absorption damping rate is linear and should neither bounce off the rod end nor slam down against the shock absorbers bump stop. The deceleration rate should appear on a graph as a 45° downward slope with the initial velocity at the top and dead stop at the bottom. Without using the shock’s full stroke, you’re damping too quickly or not quickly enough. The shock absorber should come to a rest near (but not at) the bottom of the stroke.
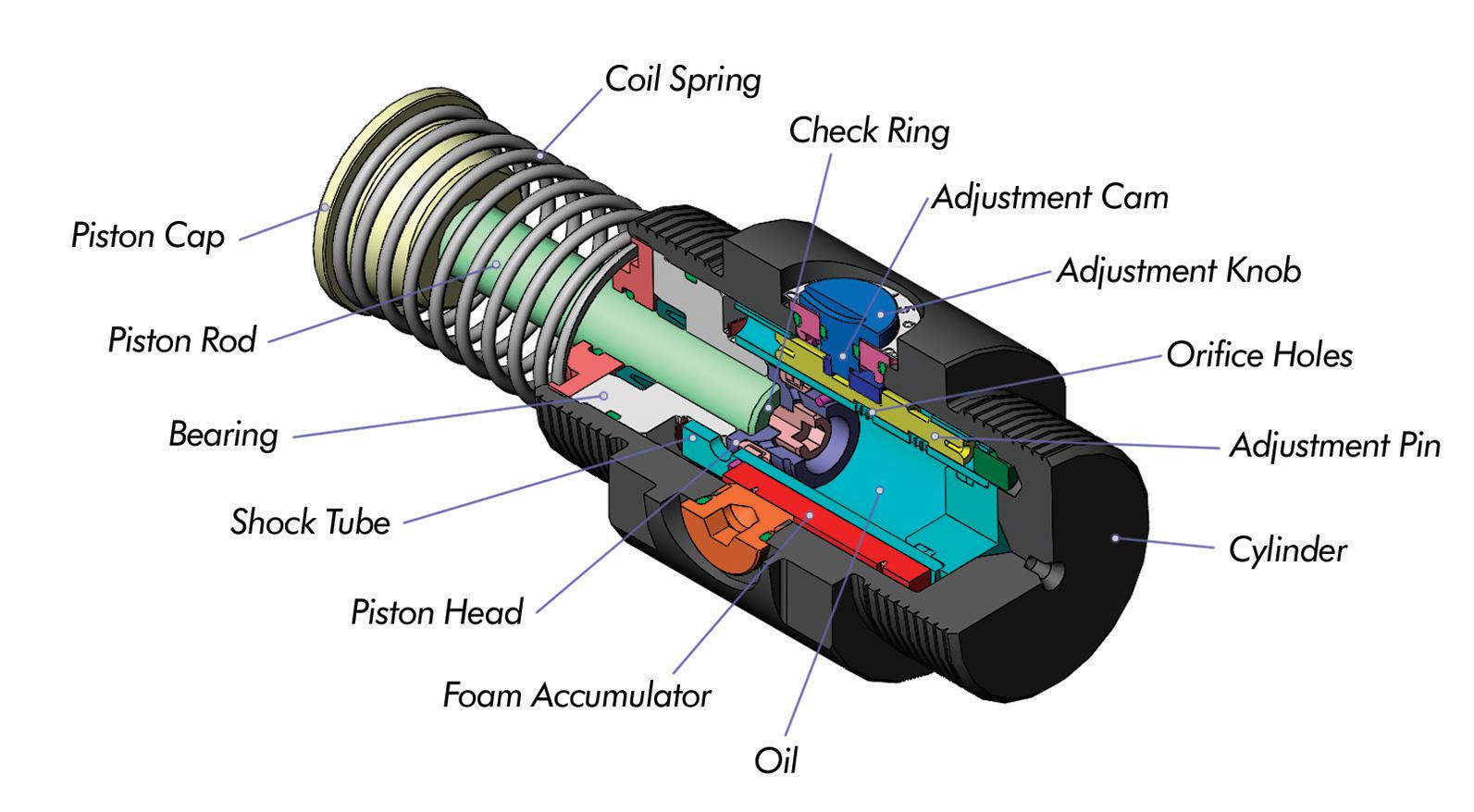
A wood products manufacturer decided to save money by hiring a small service company to maintain its compressors. The company had minimal experience in repairing compressors, but agreed to do the job. The company didn’t have parts available to replace the faulty controls on the two screw compressors — so they did the best with what they had, even when the parts didn’t fit. Never a good start to a story!
26 FLUID POWER WORLD 8 • 2022 www.fluidpowerworld.com
Compressed air fail: Frankenstein controls
Fig. 2. Poor modulating control caused huge fluctuations in pressure and inefficiency.
Figure 1. A non-standard part did not fit on this air compressor, so it was left to rest on the floor.
Figure 1 shows the subtractive pilot valve for the compressor inlet valve control resting on the floor rather than being mounted on the side of the compressor. This probably would have been okay, had the repair worked. However, the style of valves was all wrong for the compressors, leaving them to regulate the pressure very poorly. The system pressure varied from a high of 120 psi at light load to a low of 85 psi at higher loads. This caused problems with the compressors, as they were only rated at 100 psi. The modulating control caused the system specific power to peak as high as 100 kW per 100 cfm — much higher than the typical 22 kW/ 100 cfm of a normal system, making the system extremely inefficient. The poor pressure during peak flows left the plant wanting more. In fact, there was a critical machine at the end of the line that was malfunctioning and slowing down the plant production. A compressed air system auditor assessed the system and found that the compressors could be running in a more efficient load/ unload mode, and all the proper controls existed for this to happen. The system storage capacity totals about 3,000 gallons, which would allow very good compressor control if set up properly. The pressure problem turned out to be undersized piping in the compressor room and dirty filters, a somewhat easy fix. A remote storage tank with a check valve was installed at the critical machine to help stabilize the pressure. The plant is purchasing a variable speed drive compressor, which will be even more efficient than the load/unload operation. Because the system was running so poorly, the simple installation of a properly sized VSD compressor will save about 50% in power costs, worth roughly $70,000 per year. That’s monster savings!
FPW
Ron Marshall • Contributing Editor ENERGY EFFICIENCY
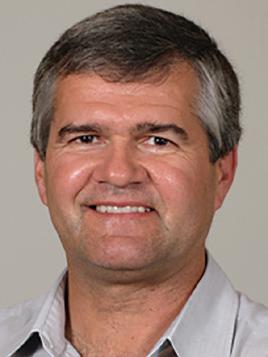
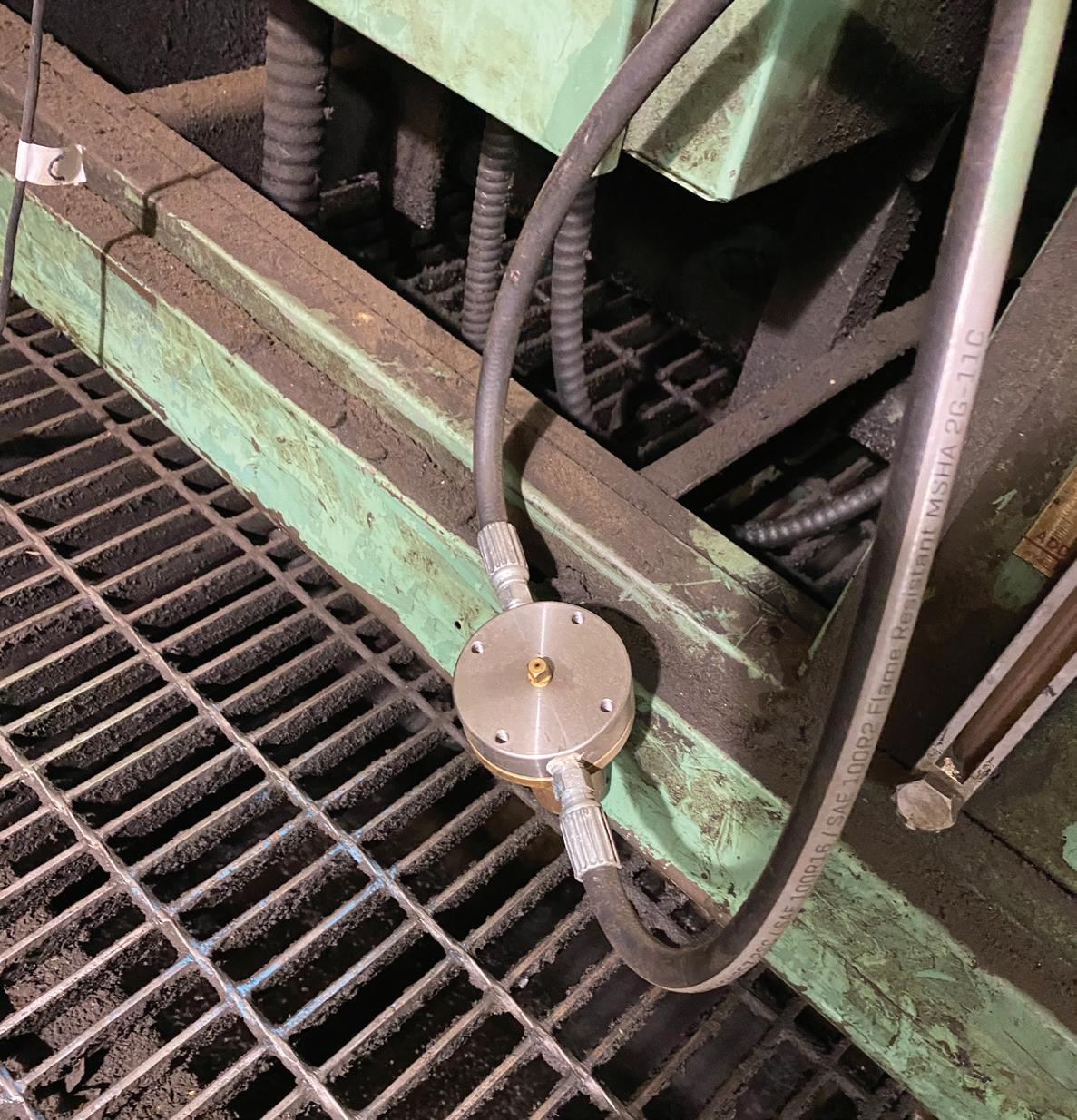
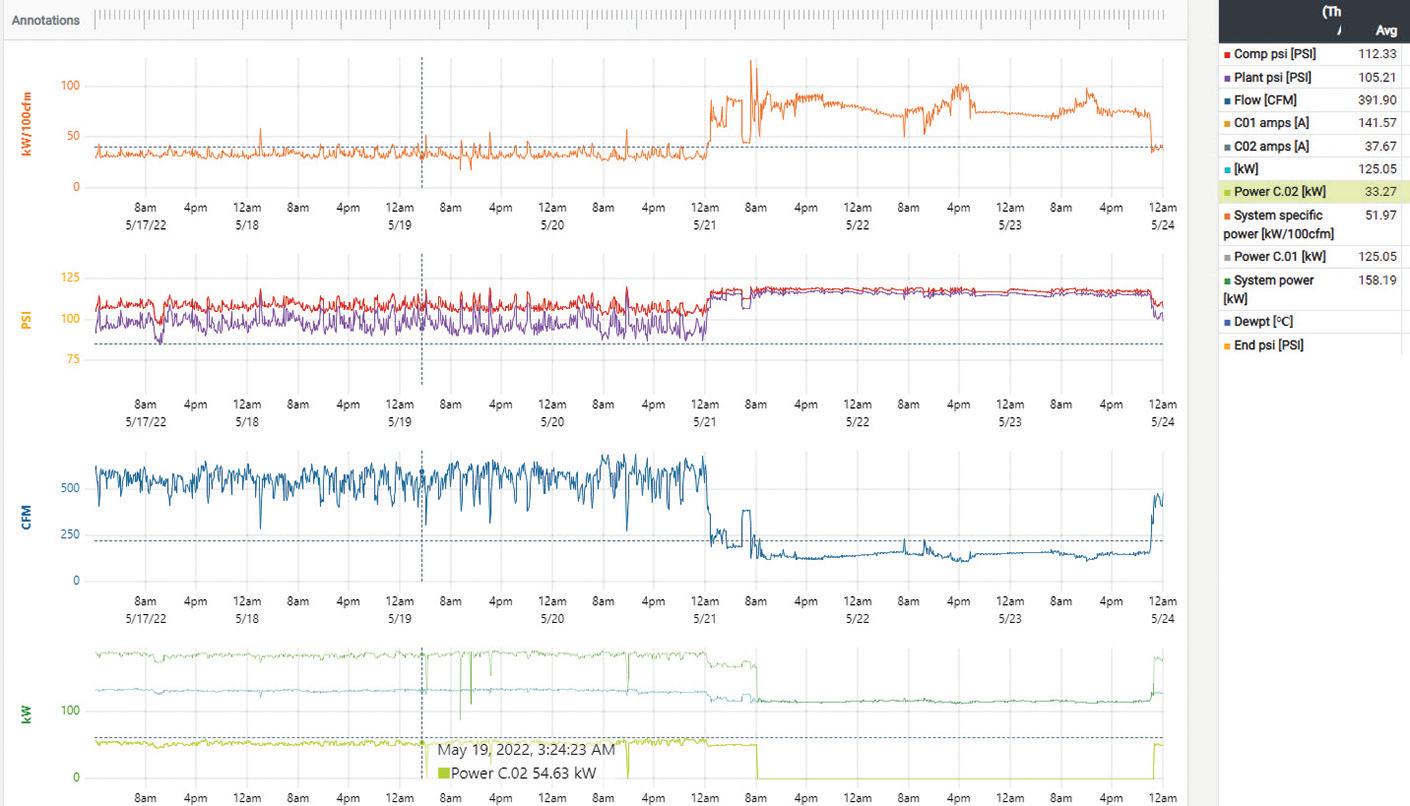

ALA Industries Limited 3410 Delta Dr • Portage, IN 46368 Tel: 877-419-8536 Fax: 219-762-2066 Web: www.alaindustrieslimited.com Since 1986, GRH mono-blocks.valves,sectionalpowermotors,pumps,suchcomponentshydraulicmanufacturedhasasgearorbitalpacks,and

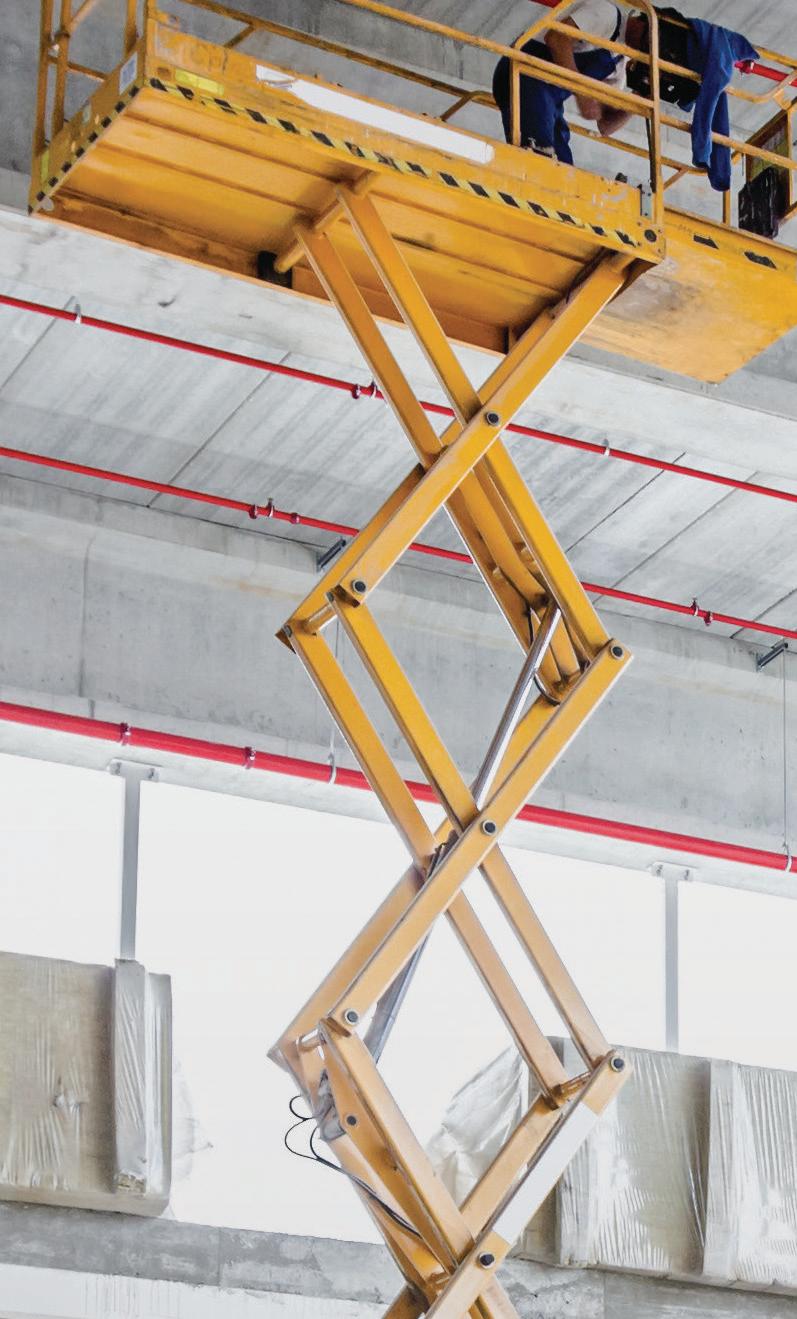

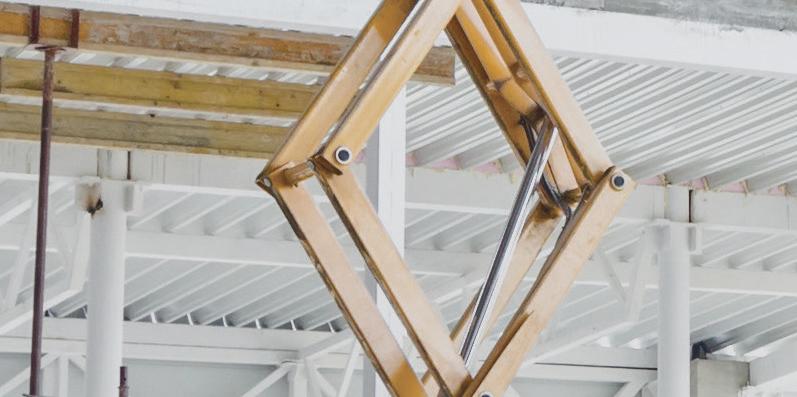
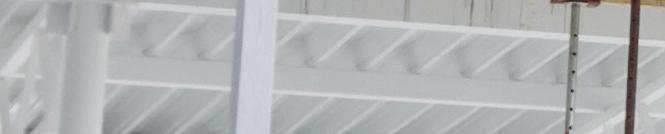
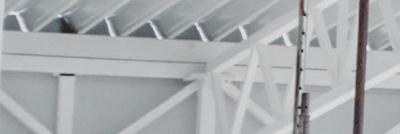



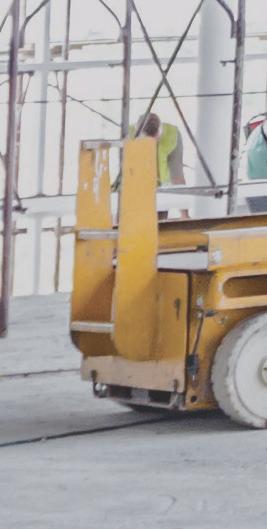

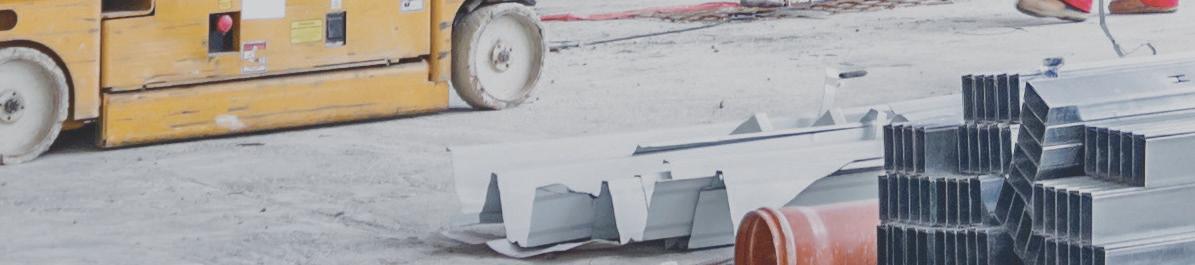


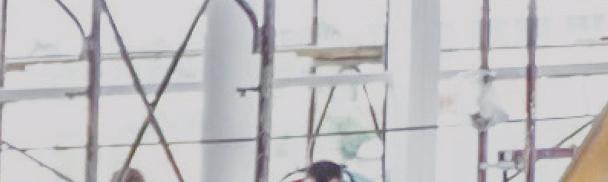

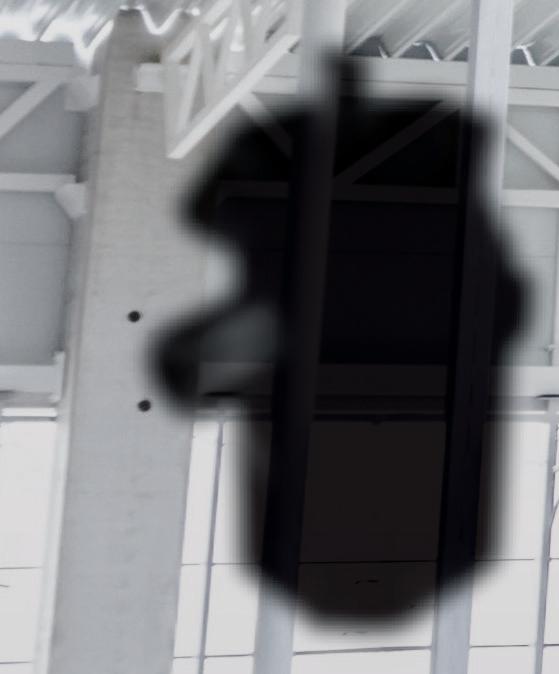



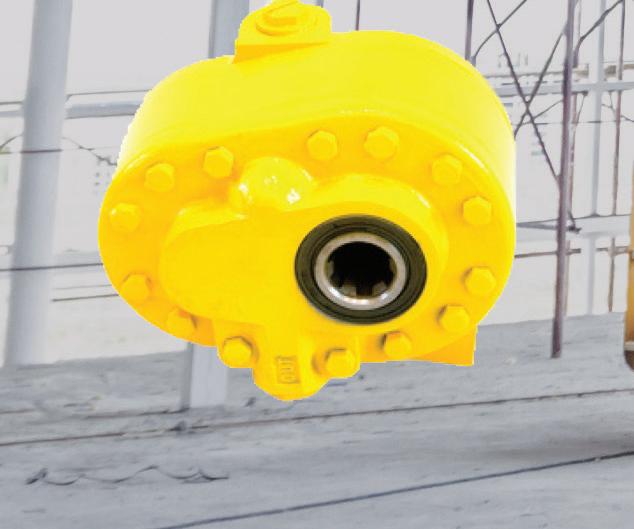


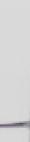

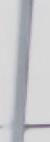
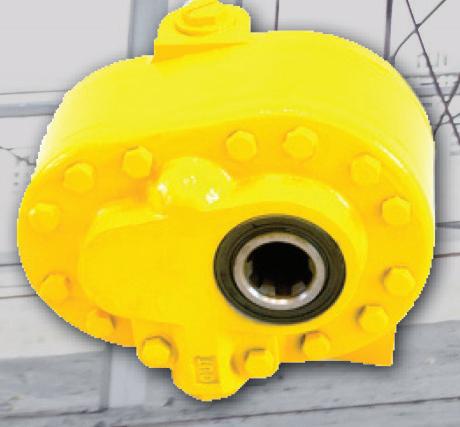
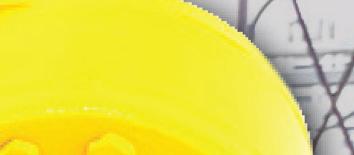
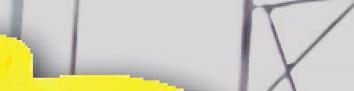


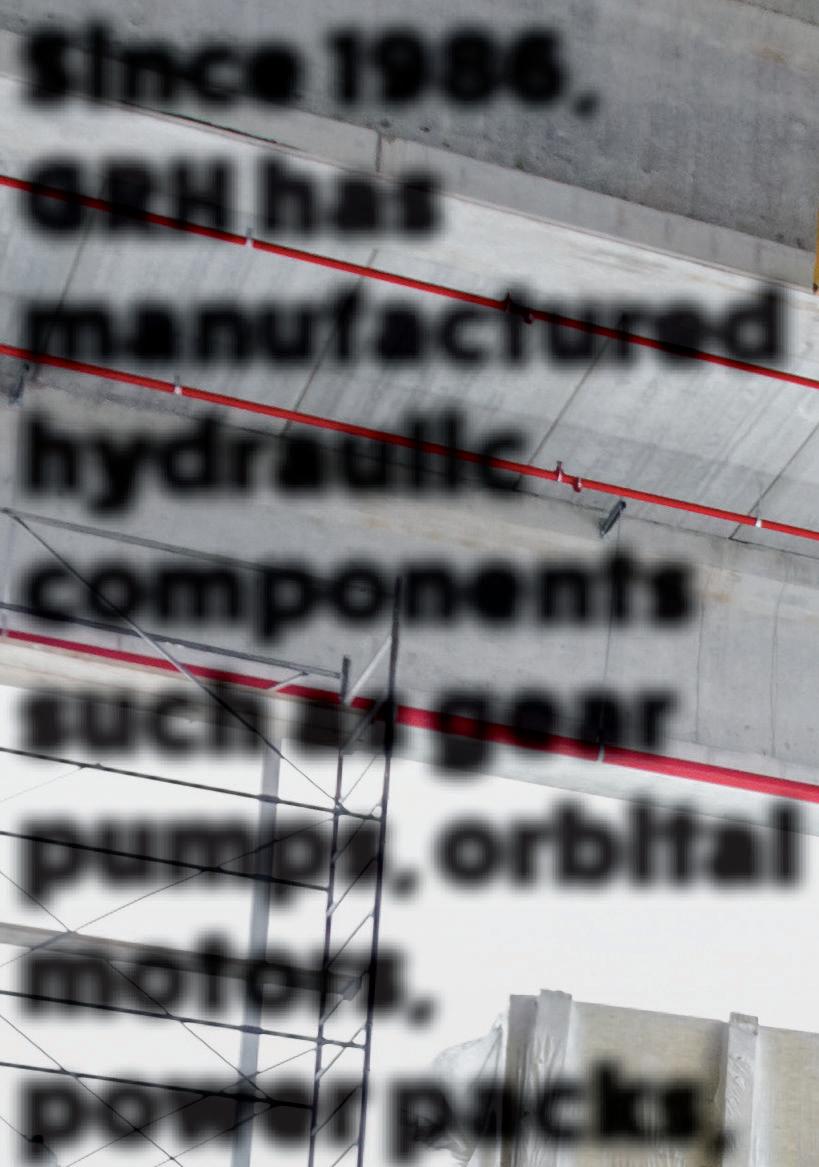
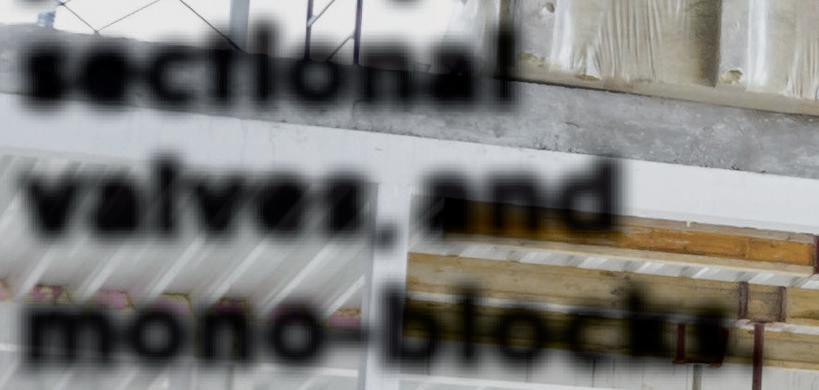
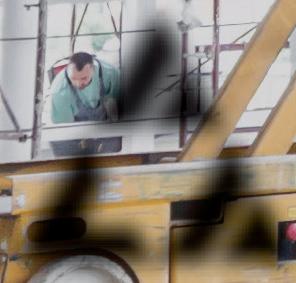

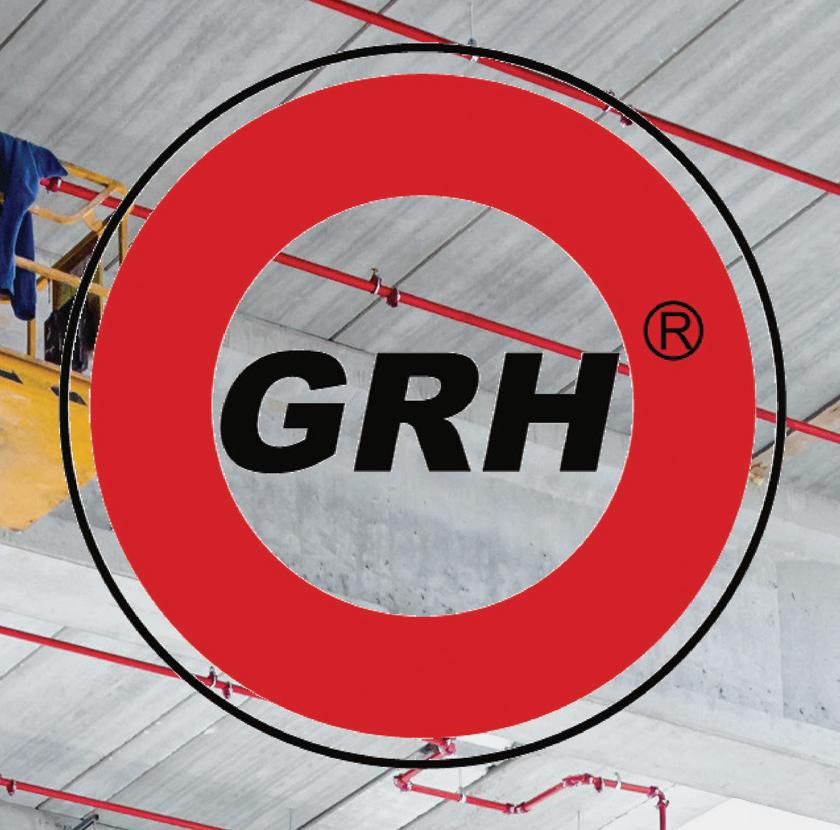

applicationshydraulicuniqueofferthepowerandreliabilityneededbycncmachines.
INDUSTRIAL HYDRAULICS
28 FLUID POWER WORLD 8 • 2022 www.fluidpowerworld.com
tools
hydraulics provides an invaluable tool for machine tool designers to perform powerful and practical functions to improve the performance and reliability of their CNC lathes, mills and other machines. A machine tool is a machine that cuts, grinds, shapes or mills material to create finished components for literally every other industry.
If you're a fluid power professional, you probably think you've seen every hydraulic application.
Disc valve motors, charge pumps, slip-in cartridge valves and hydraulic joysticks don't find themselves on every machine. Still, they're familiar enough that most have heard of them. However, unless you're intimately familiar with machine tool technology, plenty of unique hydraulic applications are used in and around CNC machines you likely have never seen. Although nearly all CNC machines run primarily from an electric motor, such as with vertical and horizontal machining centers, most auxiliary functions operate from fluid power. The power of hydraulic chucks A CNC lathe clamps and then rotates a workpiece while cutting tools dig away to create a cylindrical profile to match the pre-programmed shape. A workpiece must remain firmly fixed to prevent wobbling or loosening, which may damage the workpiece, tooling or machine itself. The clamp used to hold the workpiece in the lathe is called a chuck and was previously a manually operated devise, requiring a special key.
josh contributingcosford,editor
hydraulicsputsthepowerinmachine
The key rotates gears internal to the chuck, which collapse onto the cylindrical workpiece to prevent it from spinning inside the chuck or moving axially. T-handle keys work best because of the torque required to firmly clamp the workpiece using this old method. In fact, some machinists would use hammers against the key to more firmly lock the workpiece in place, but over time that hydraulic swing clamp. | courtesy of clamptek many



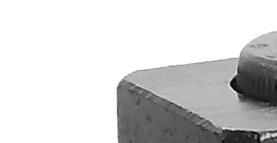

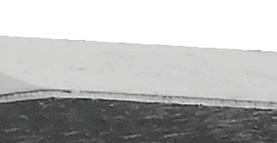
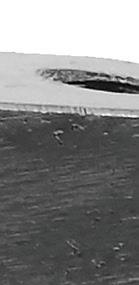

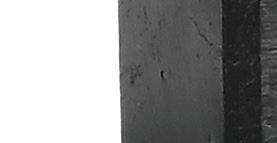

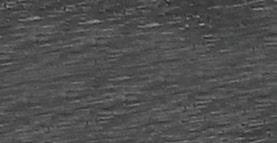

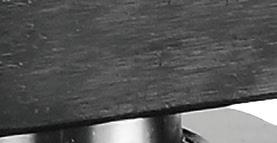
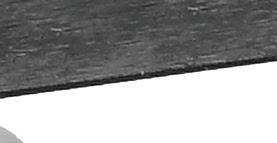
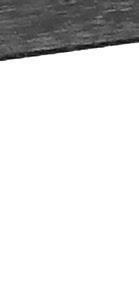

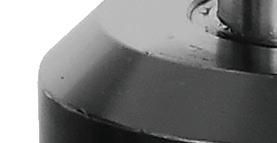
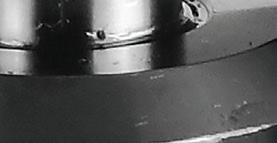


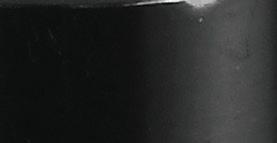
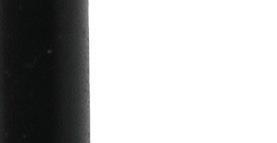
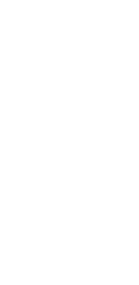

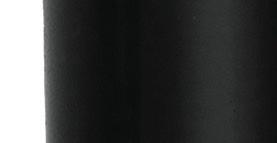
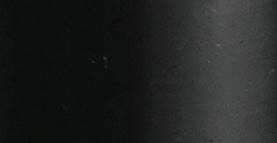
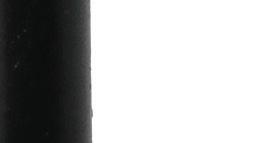
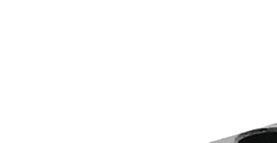
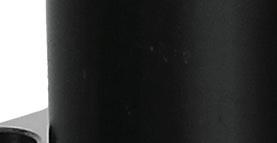
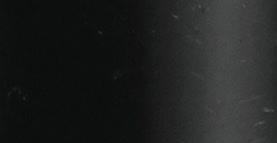

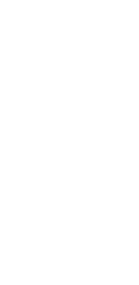

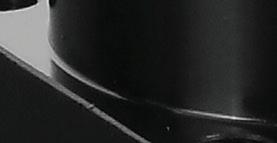

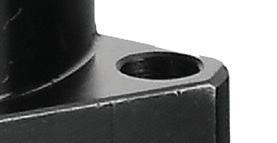
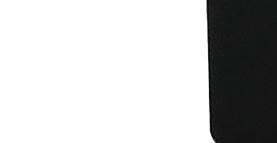
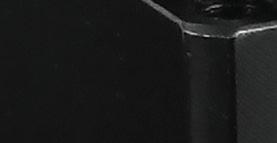
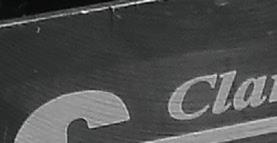
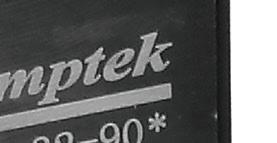
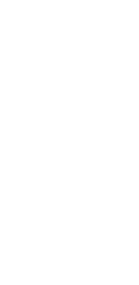
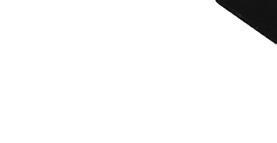

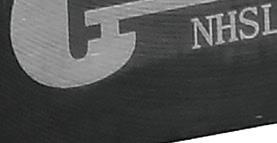


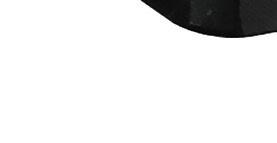
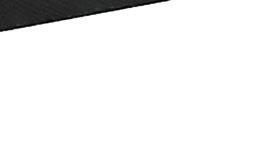

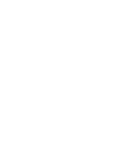

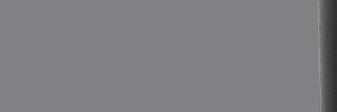



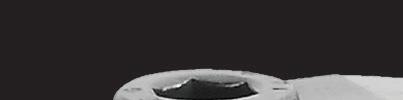
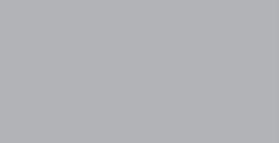

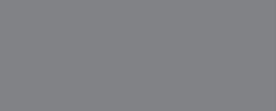
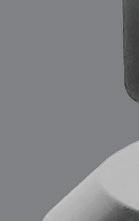
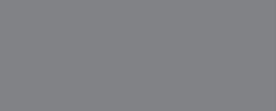
Hydraulic vises for secure clamping You’ll see a pattern with machine tool hydraulic actuators — they’re used primarily for quick and powerful workholding applications. The rotating chucks and cylinders for CNC lathes are rather complicated, but CNC vertical mills employ more straightforward solutions to clamp and hold Nomaterial.shopis complete without a bench vise, and vises are integral to the operation of a mill. Many lower-cost mills use simple vises for manual operation, either through a built-in handle or a square socket with an air ratchet to decrease cycle times.
www.fluidpowerworld.com 8 • 2022 FLUID POWER WORLD 29 method damages the key and chuck itself. A hydraulic chuck, as seen in the exploded view from Kitagawa, takes all the work out of clamping material, providing a fast, secure method superior to keyed chucks. Hydraulic fluid from a small hydraulic power unit pressurizes a draw nut, pushing it against a wedge assembly. The angles of the wedge assembly attach to the jaws. Depending on the direction the draw nut is actuated; it will clamp or unclamp the material when the directional valve is operated.
Although milling operations tend to take longer than lathe operations, every minute saved in a lean manufacturing plant provides product to the end customer more quickly and for less cost. The hydraulic vise, much like the hydraulic chuck, allows the operator to clamp and unclamp work material using either buttons on the HMI or via a footswitch. The primary advantage of hydraulic clamping may be speed, but clamping strength ensures the workpiece remains in place for accurate and safe machining. Should the workpiece
Just as with chucks, the ultimate in work holding uses hydraulic power to quickly and firmly clamp any square material for machining. Auxiliary hydraulic valves operate as part of the G-code programmed cycle inputted manually or through CAM software.
Most hydraulic chucks operate under pressure in both directions of jaw travel. The CNC machine clamps material from the outside diameter for material such as cylinder piston rods but can also clamp from the inside diameter, such as with cylinder barrels. Although most CNC lathe operators will manually clamp and unclamp using a foot pedal, the operation is programmable for "lights out" machining using robots. Either manually operated or electroproportional control, pressure-reducing valves allow the programmer to change the clamping force. Different materials may require higher or lower clamping force, so this option prevents the chuck from damaging thinner material. When the CNC lathe machines many of the same components from a single bar, a method to feed the bar speeds up production to avoid the operator manually pushing material into the machine and then touching off the workpiece to reset the zero position. Touching off is the process of moving the chuck using a manual override of the tool position while the chuck is stationary to touch the tool against the workpiece, thereby telling the machine where to start making chips. Sophistication and precision of drawbar cylinders The drawbar cylinder is another unique hydraulic actuator seen nearly exclusively in the machine tool industry. Essentially an annular cylinder, the drawbar cylinder exploded view of a hydraulic chuck. | courtesy of kitagawa will clamp the workpiece between cycles and move it forward into the machine. To continue using hydraulic cylinder examples, imagine a round bar of bronze to manufacture rod bushings for air or hydraulic cylinders. As the machine cuts the bearing details and nears completion, a part-off tool cuts the bushing off the bar entirely to leave the blank end of the bar in the chuck. The drawbar cylinder clamps and then precisely extends the bar forward into the machine to reset the bronze for the following work cycle. Drawbar cylinders are actually quite sophisticated. Their construction requires that they spin at the same high speed as the chuck, which allows the machine to feed material forward while still spinning the chuck. In addition, these units contained precise sensors to position the material accurately along the X-axis to prepare the material for the next operation.
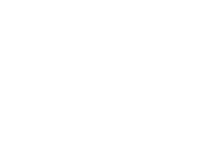

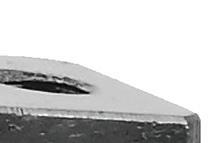


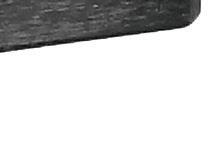
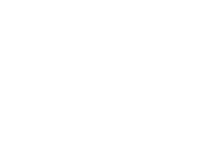

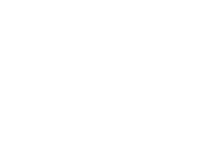
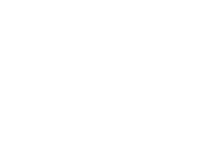

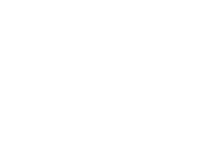
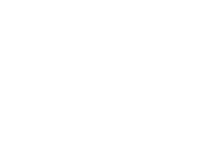

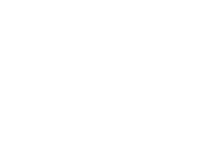
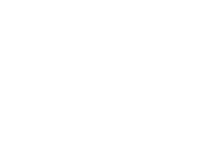

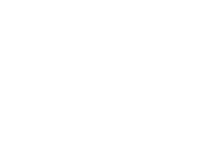
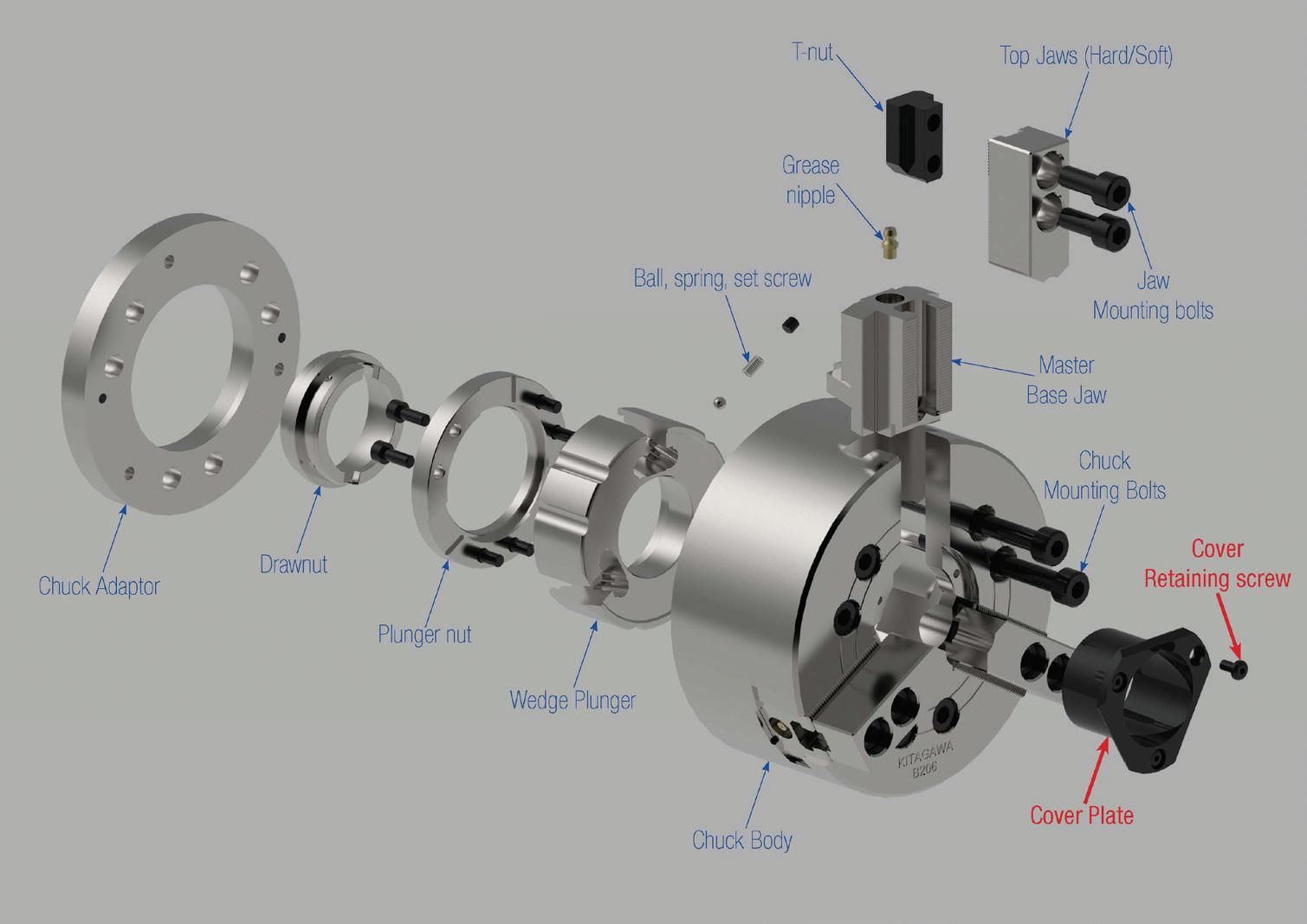
specifications.additionof they do work but require high effort from the operator and may be time-consuming as well. Rotating hydraulic swing clamp The hydraulic swing clamp is yet another unique machine tool application. These clamps simultaneously rotate and clamp to firmly hold the material against the bed, whether one or a dozen are required. These swing clamps attach to the bed at their cap end, while the rods extend upwards with the clamp threaded directly to the rod end. The clamps swing to allow easy removal of the workpiece, regardless of size. Even large material may be lowered onto the bed using a gantry crane while the clamps are safely swung outside the path of the material being lowered. The clamps are often modular in design, meaning the clamp attachment can be swapped out for different designs or moved around the bed as needed to suit differently shaped or sizedAsmaterials.withother auxiliary hydraulic components, these swing clamps require hydraulic pressure. While many clamps could join the task of work holding, most or all clamps may join together in a parallel circuit operated by a single hydraulic valve. With parallel hydraulic circuits, no guarantee can be offered that the clamps will actuate simultaneously, but in this case, it matters little. So long as all clamps are holding firm before the machining cycle begins, the "path of least resistance" sequence will not affect performance. Even if other industries use hydraulics in unique ways, few other machines offer many applications exclusively and specifically. These examples show you what is possible with a different approach to design and implementation. They show us we need not remain in the same traditional cylinder and motor execution to actuator design. FPW draw bar cylinder. | courtesy of kitagawa hydraulic vise. | courtesy of roemheld
30 FLUID POWER WORLD 8 • 2022 www.fluidpowerworld.com
INDUSTRIAL HYDRAULICS move inside the vise, the material will be scrapped at best. But with high-powered machining capable of rapid travel speed, a workpiece may even fly out of the vise entirely, acting much like a projectile with the potential to damage the machine or harm the operator. The hydraulic vise tends to be an option on CNC mills, and because a PLC very much runs the machine, you may add accessory functions quite easily. However, more often than not, CNC machines come with only the bare essentials. The industry is highly competitive, so offering the lowest sticker price possible often makes or breaks the sale. Rarely will you find a CNC machine with redundant valves from the factory. In fact, I’ve known customers who omit the hydraulic power unit altogether so they can have one created locally to their exact specifications.Nevertheless, even machines with tiny factory power units are easily upgraded to include additional hydraulic valves or, in some cases, diverter valves added to the existing circuit. The 6-way, 2-position diverter valve allows a single upstream directional valve to control two different actuators. The caveat, of course, is that only one actuator may operate at a time. A third option is the addition of an entirely new, multistation manifold. Such a manifold allows the addition of many more valves, should they be required, with the understanding that pump flow may not operate many valves simultaneously. Sometimes the size and shape of the workpiece require unique fixturing options unsuitable for a simple vise, which limits clamping to the horizontal plane on two surfaces only. Large, oddly-shaped material must be fixed to the mill bed with specialized clamps. Hand-actuated toggle clamps
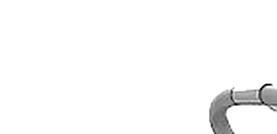
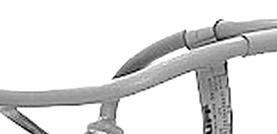

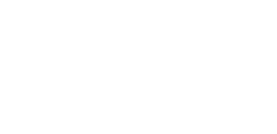

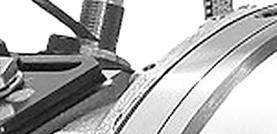
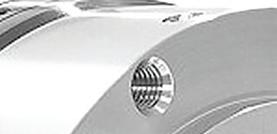
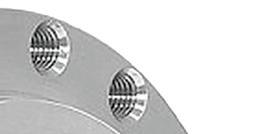
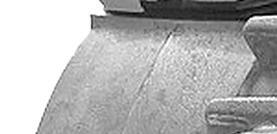
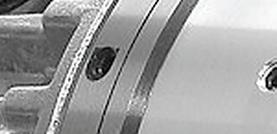

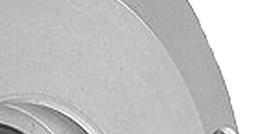
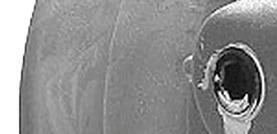
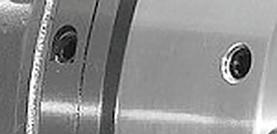
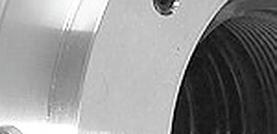
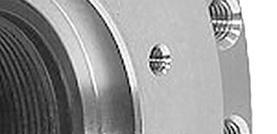
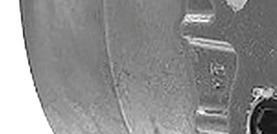

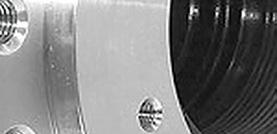
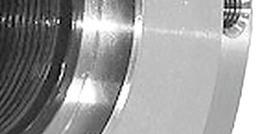
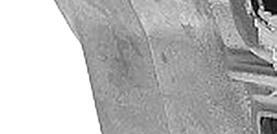
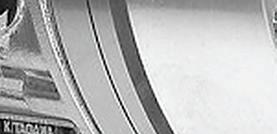

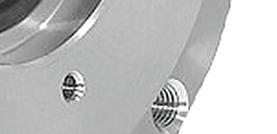
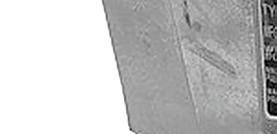
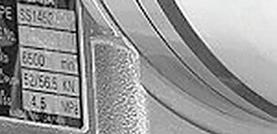
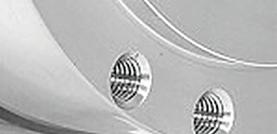

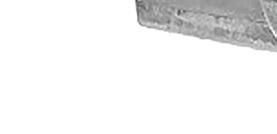
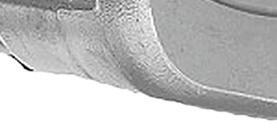
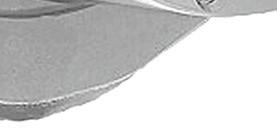
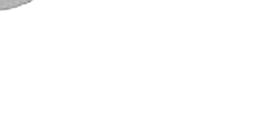
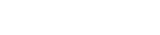
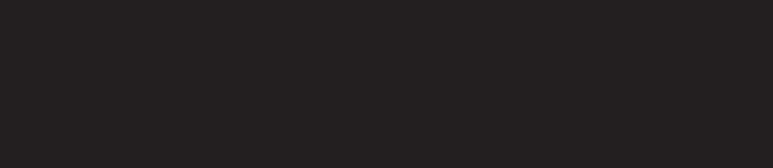


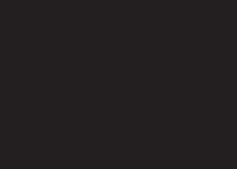
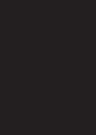

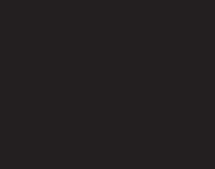
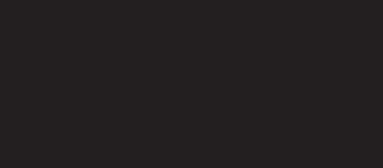
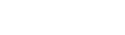
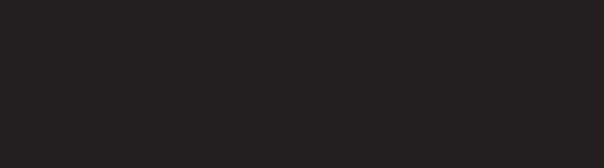
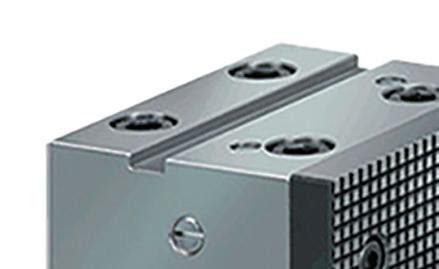
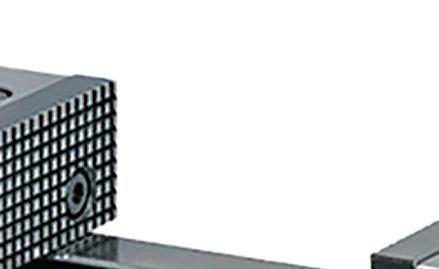
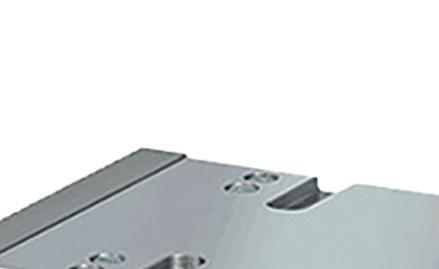
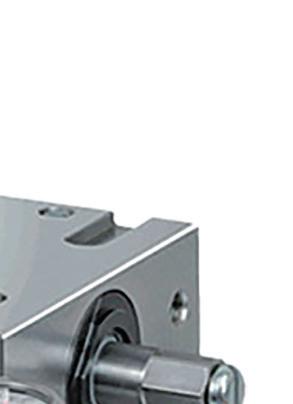
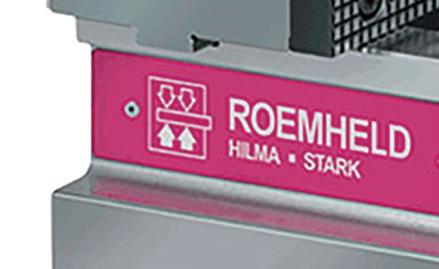

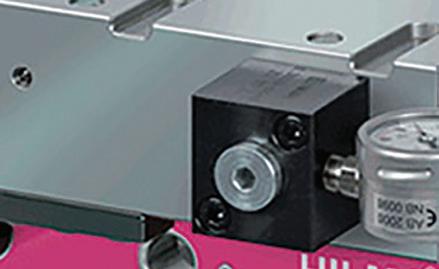
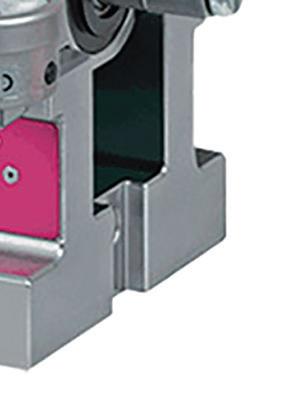
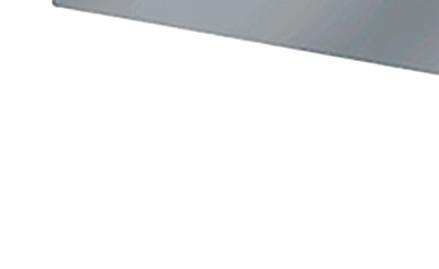
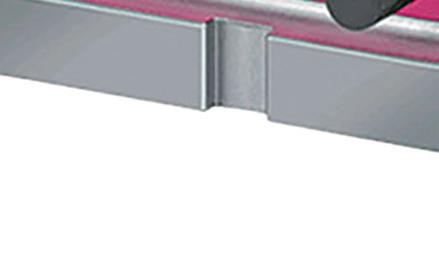
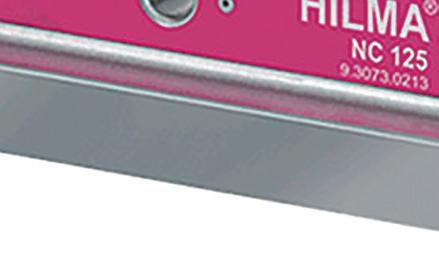


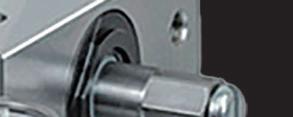




A NEWFORROMANCEMOBILE 32 FLUID POWER WORLD 8 • 2022 HYDRAULICS?BYPAULJ.HENEY | All component photos courtesy of Bosch Rexroth FAR FROM BEING THE THREAT IT ONCE SEEMED, IS A COUPLING OF ELECTRONICS WITH HYDRAULICS TURNING OUT TO BE DESTINY? MOBILE HYDRAULICS

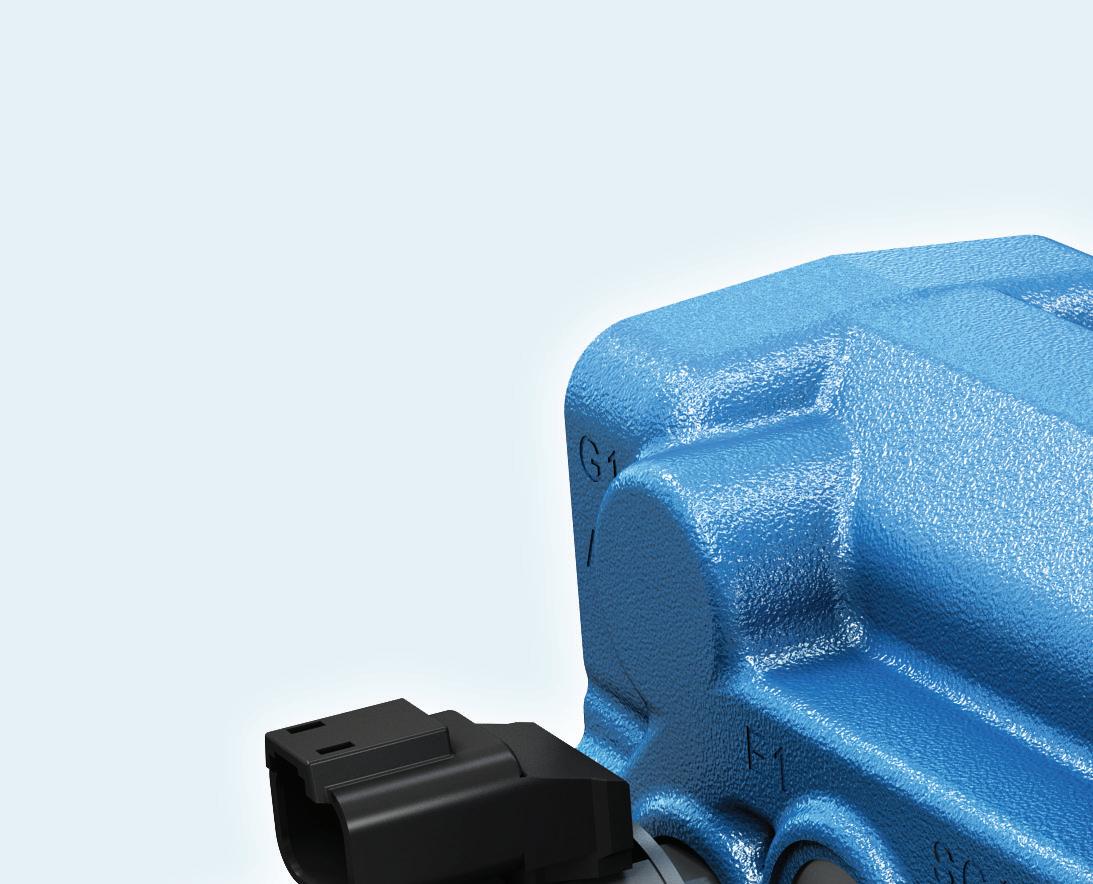

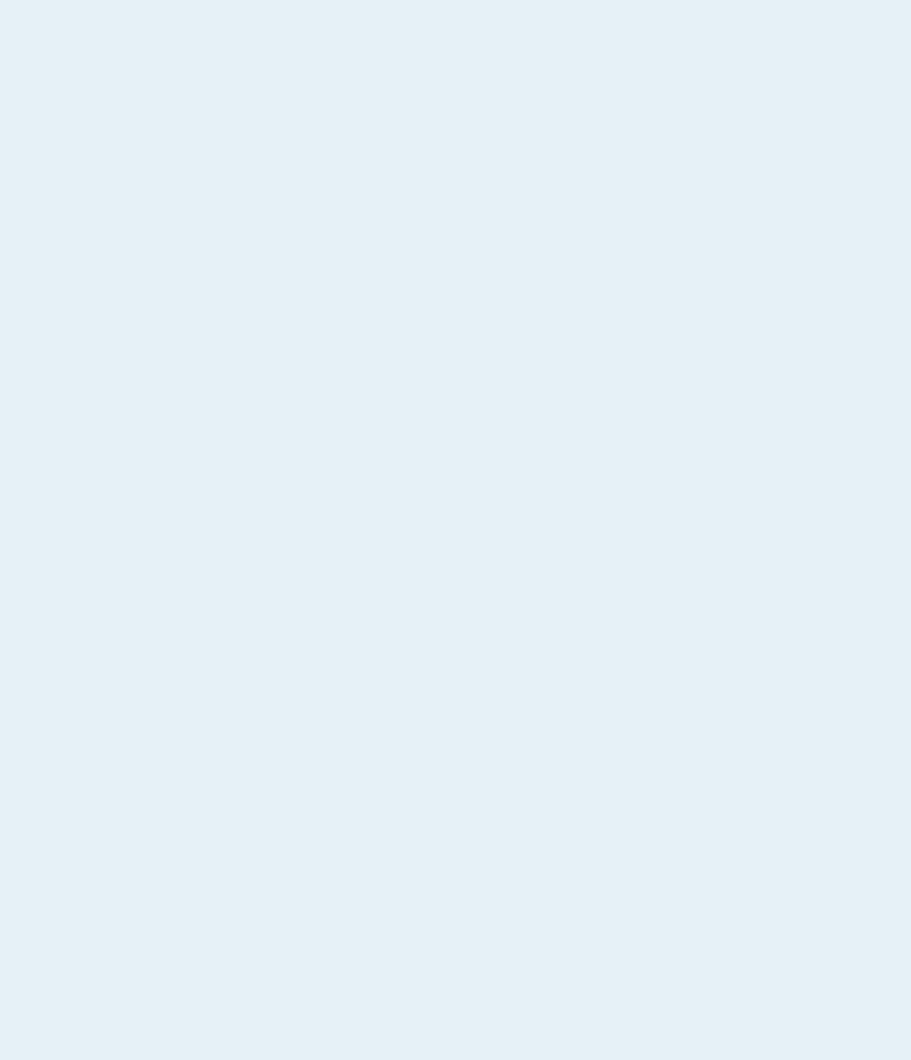
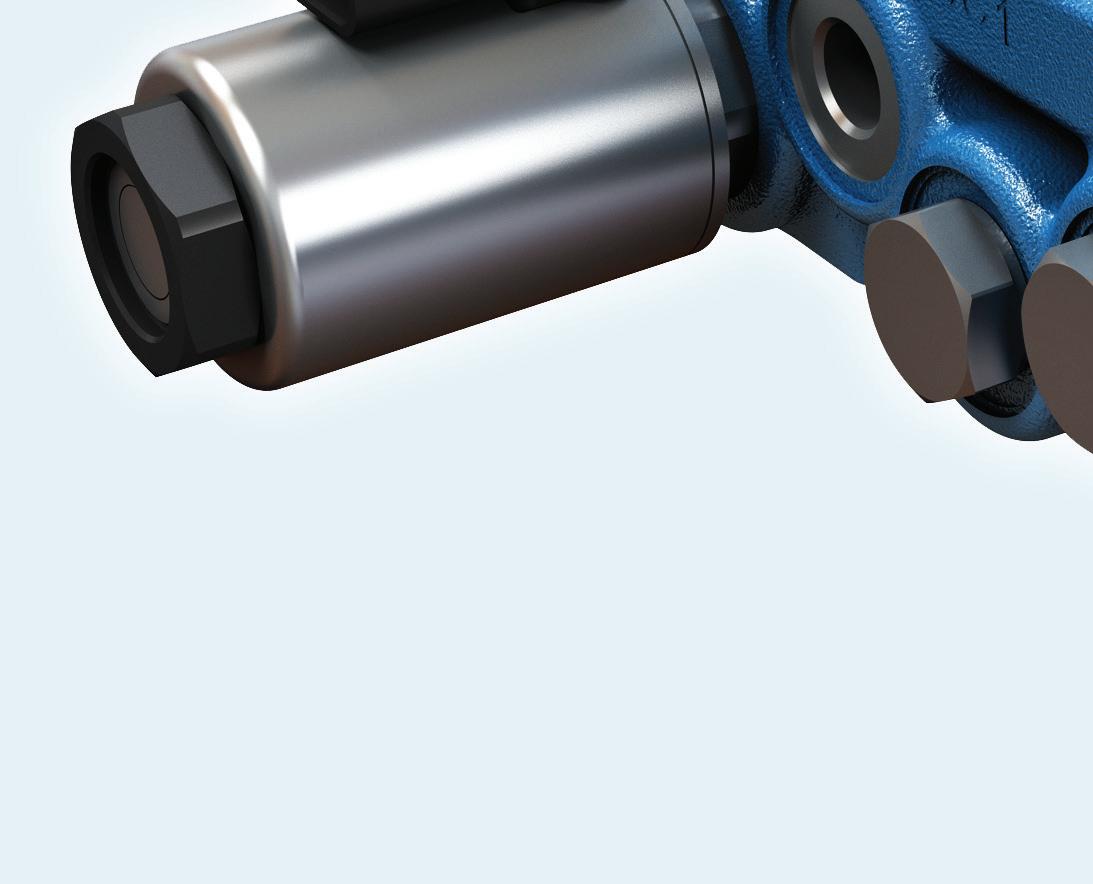
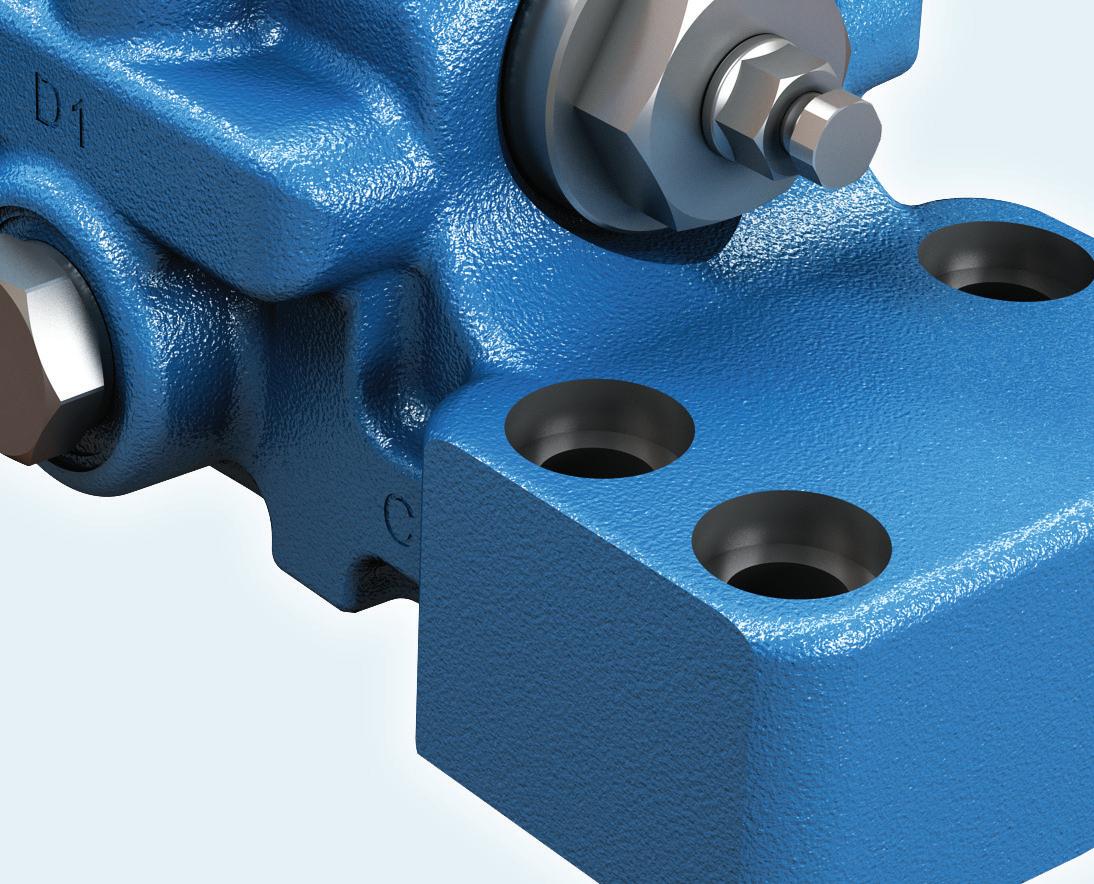
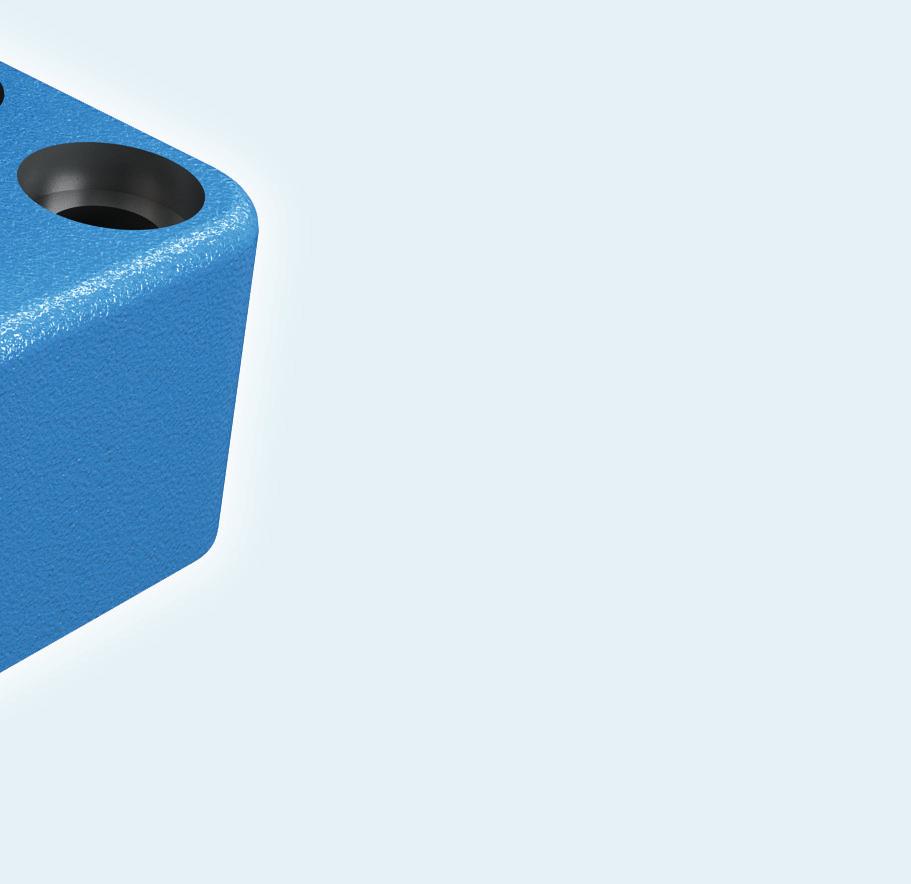

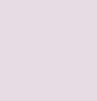
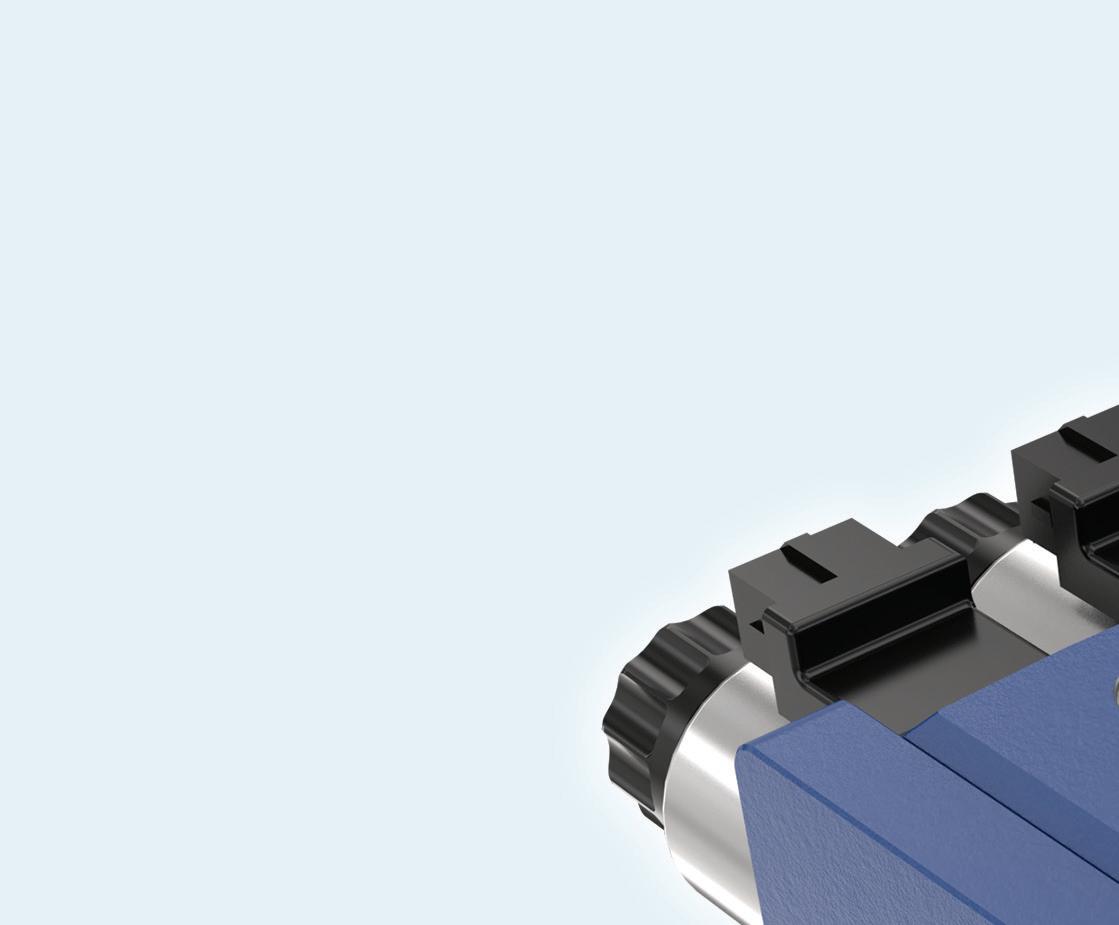
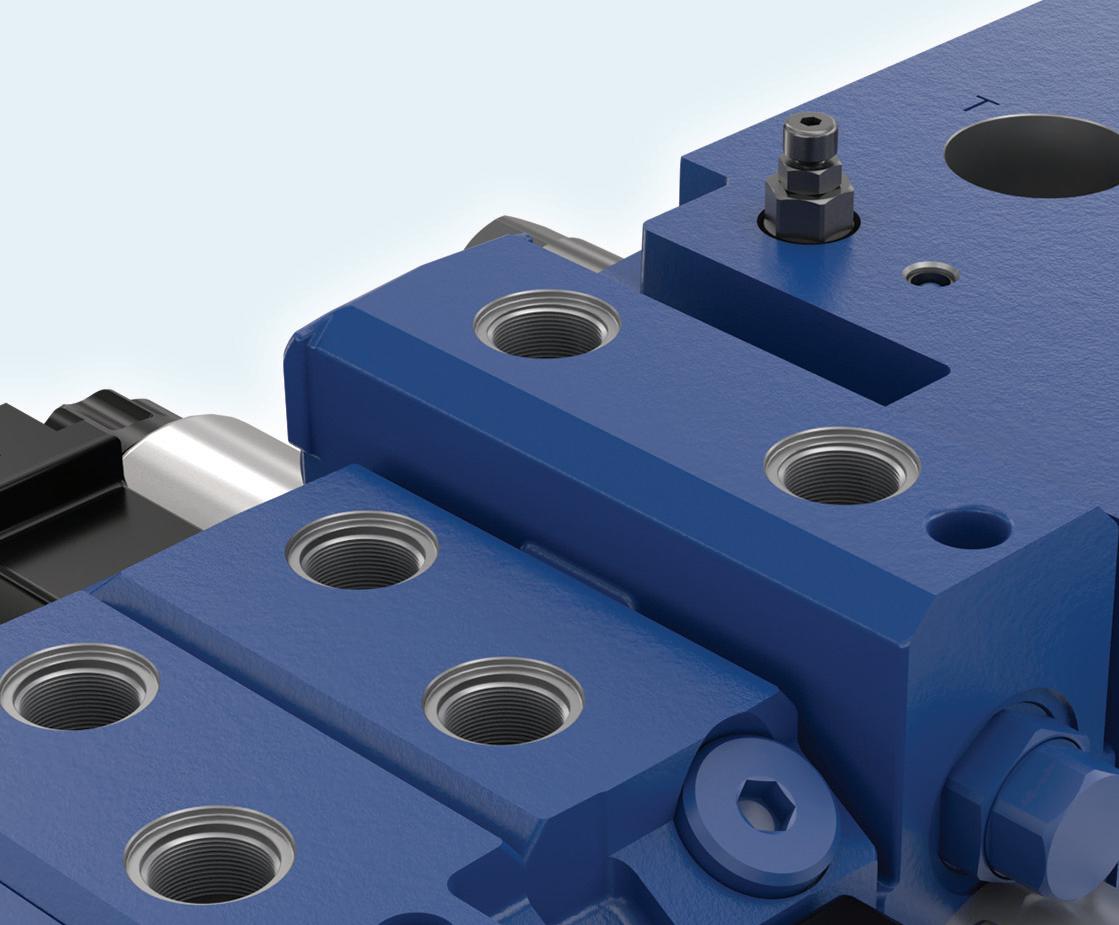

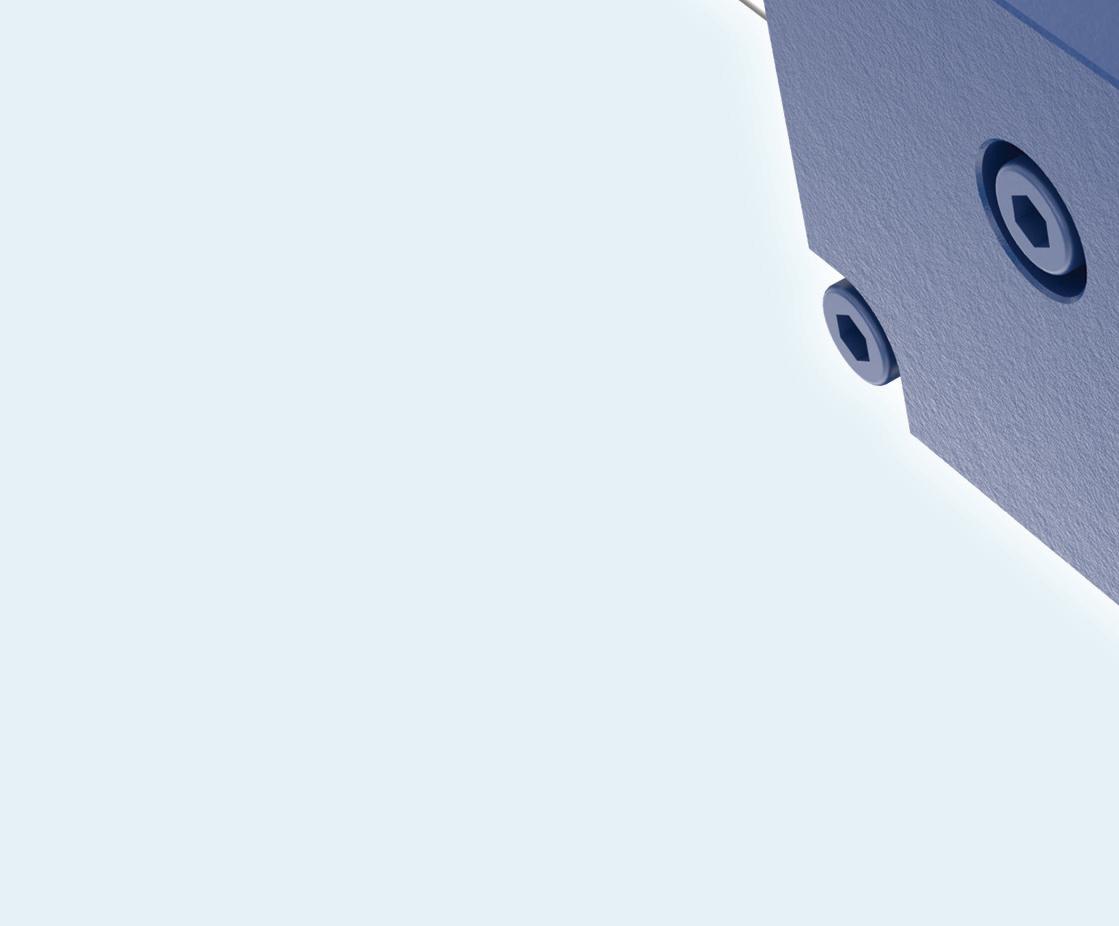
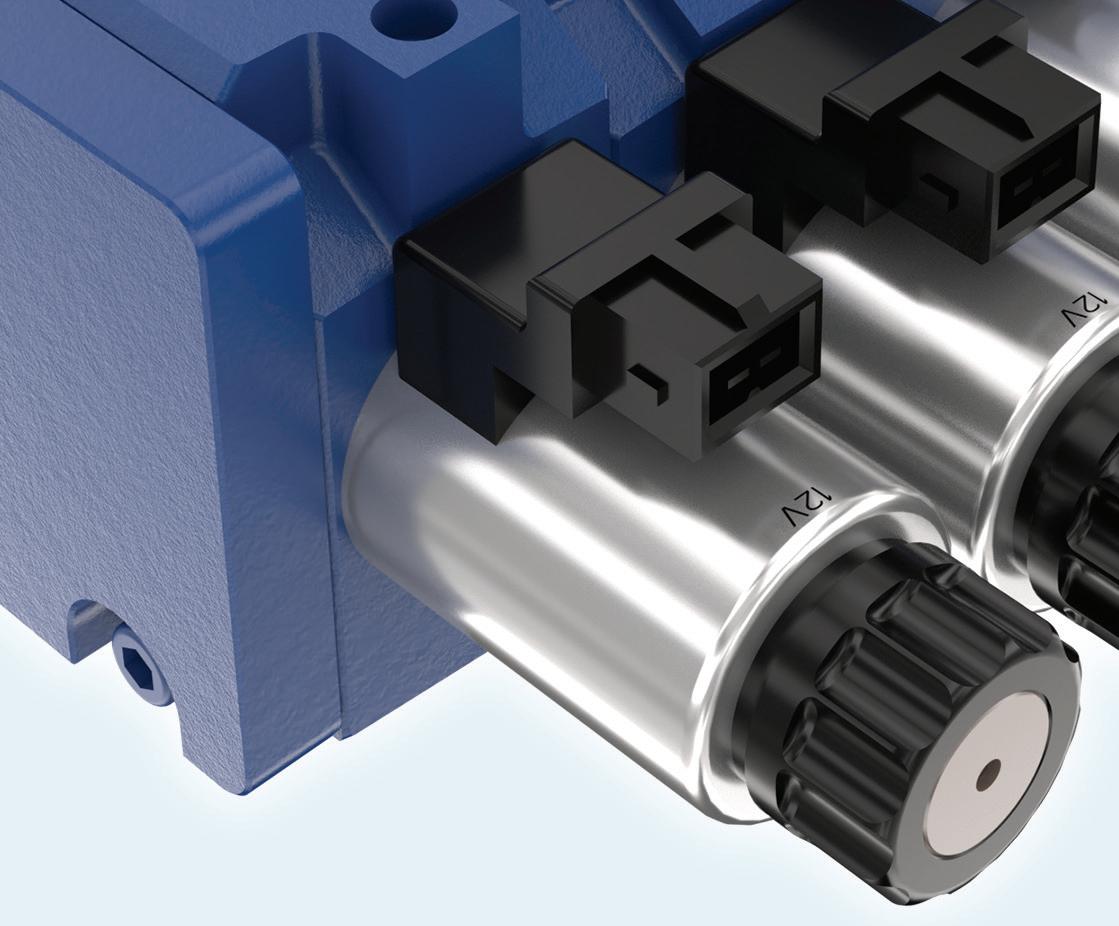


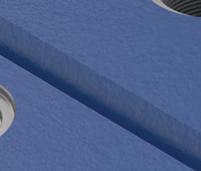
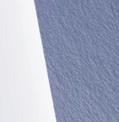
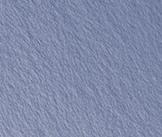

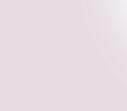
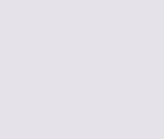
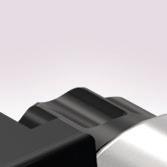

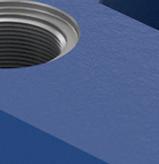
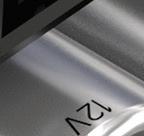
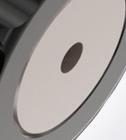
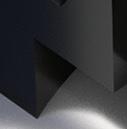
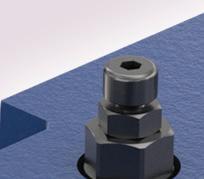
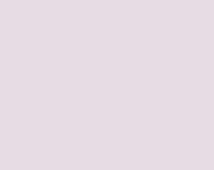
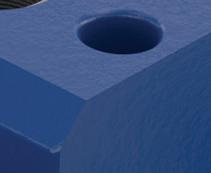

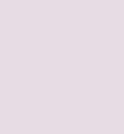
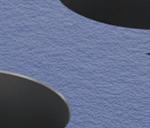


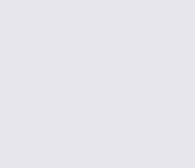
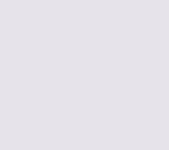
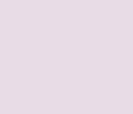
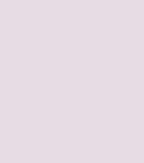
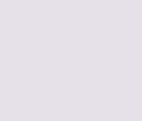
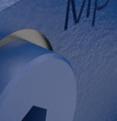
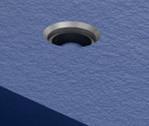

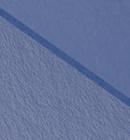
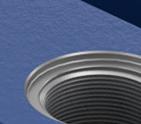
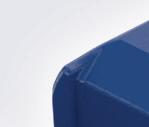



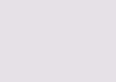

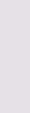

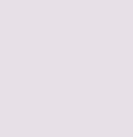
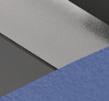
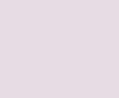
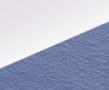
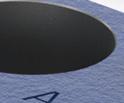

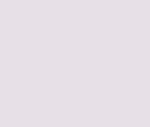


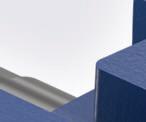
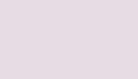
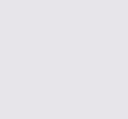
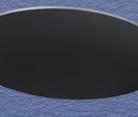
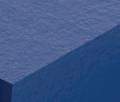

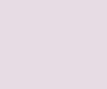



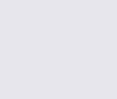
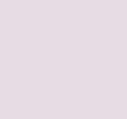
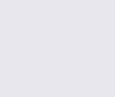
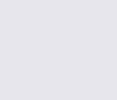






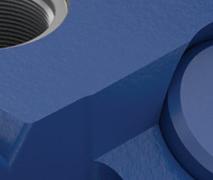
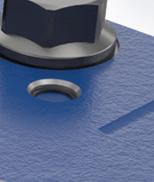
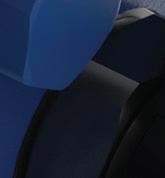

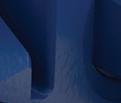
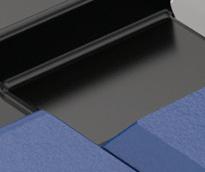

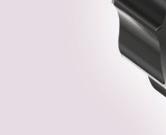

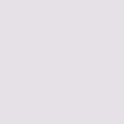
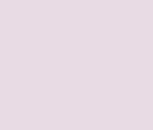
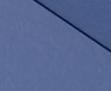

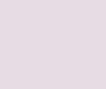



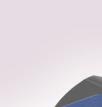
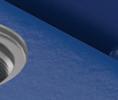
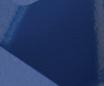











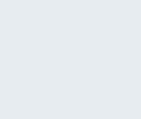
any word like “electric” as a bit of a bugaboo.
Following are some things to watch for in tomorrow’s electrified mobile hydraulics.
www.fluidpowerworld.com 8 • 2022 FLUID POWER WORLD 33
But who would have thought that the future might turn out to be a different one — one where hydraulics and electronics would get together in sort of an unexpected romance? And a wonderful romance at that, where each is greater than the sum of their parts, ushering in a promising new day for mobile hydraulics.
A recent users conference in suburban Chicago, put on by component manufacturer Bosch Rexroth, provided some interesting glimpses into this promising new union.
Dr. Jonathan Meyer, Control Systems Engineer, explained that many companies are focusing on the challenges that we have today with the workforce. There are fewer workers, many of them are not experienced, and they are very used to technology, having grown up with mobile phones. How can we make mobile equipment something that’s intuitive to use? What’s more, there are different markets worldwide and different users may expect the machine to operate in different manners. Maybe one user wants a more aggressive handling technique, while another user wants the equipment to function in a more relaxed and precise manner. This is all compounded with inflation and cost pressures, as well as a desire for efficiency.
“Let’s look at a standard hydro mechanical machine that we have today,” said Meyer. “We have the hydro mechanical control pump, we have pilot-operated joysticks. We have hydromechanical valves. We have hydraulic hoses — and all of this requires installation effort, as well as hardware. ‘Set it and forget it’ could be the tagline for hydraulics. But does it have to really be that way? Or can we get more flexibility in the system?” Meyer said that electrohydraulic solutions will provide more functionality and efficiency and remove barriers — all from moving things Soon after I began to cover fluid power back in the mid 1990s, I heard the drumbeat from many worried hydraulic component manufacturers — the electrics are coming to get us. There was a lot of fear (as well as a lot of doubt in some corners) that someday, electric actuators would replace hydraulic cylinders. When that day would arrive, if ever, was a great topic to get engineers talking over drinks after a long day at a trade show. One side would point to the fact that physics is physics, and hydraulics’ incredible power density would never be replaced, especially on mobile machinery. The other side would grumble nervously about all the strides electric actuators had made over the years, not to mention advances in batteries, and even point out individual applications, such as a particular airplane, where electrics were gaining traction. Because of that, I suppose, hydraulics people of a certain age tend to think of
It’s all about the software





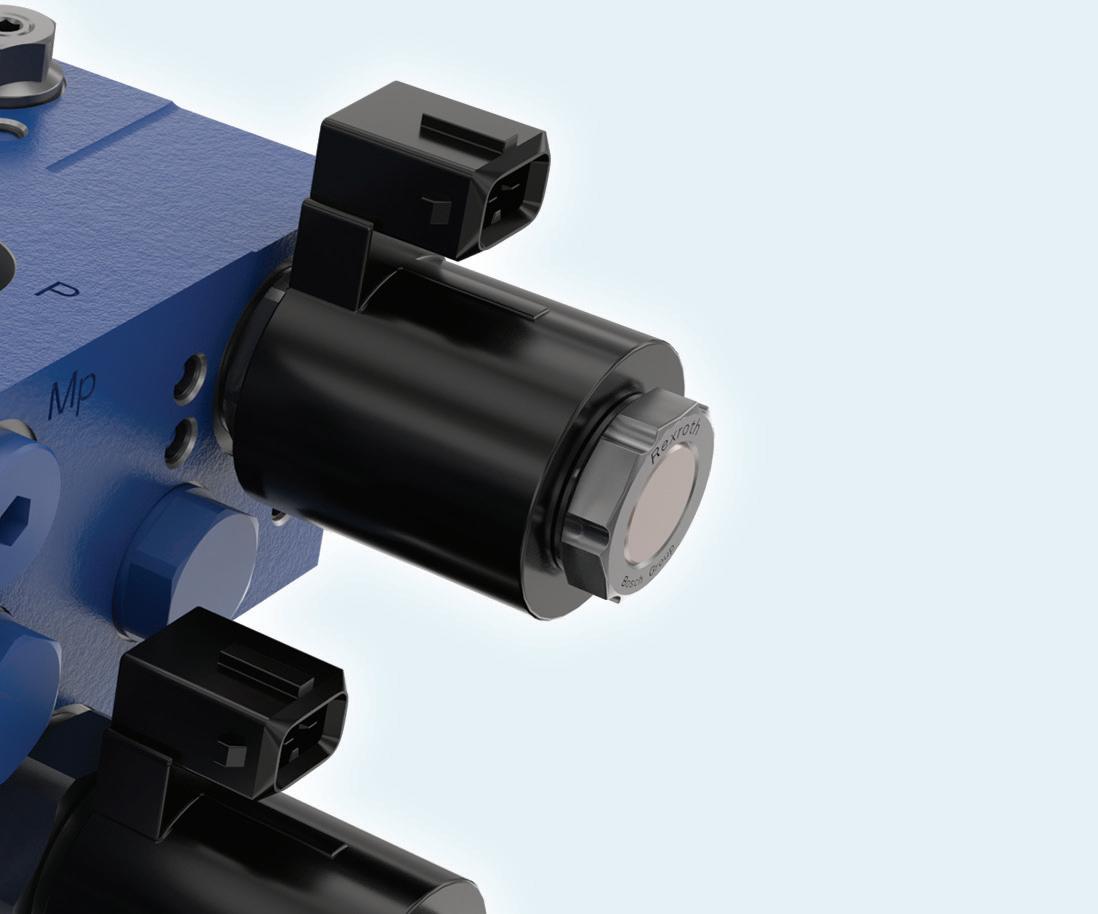

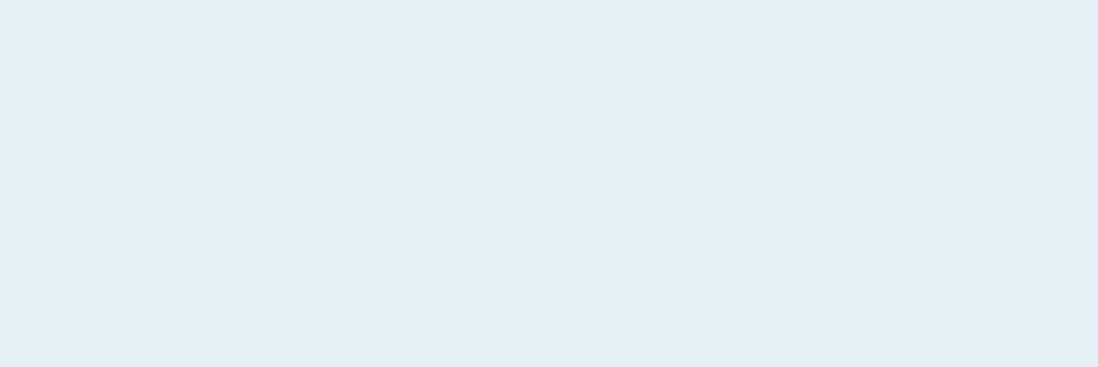
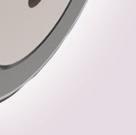

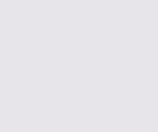
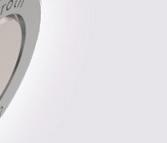
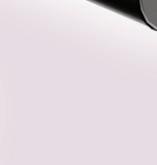

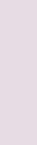
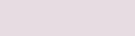

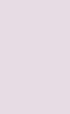

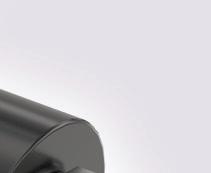
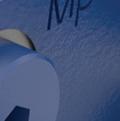
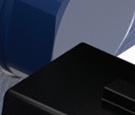

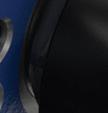

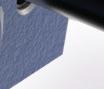

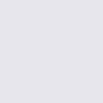
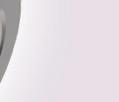


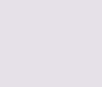
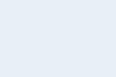
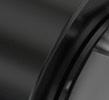
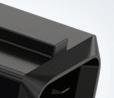
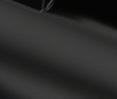
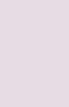


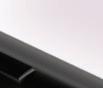








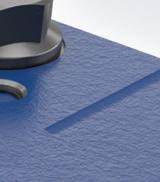
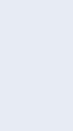

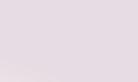

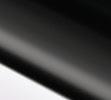


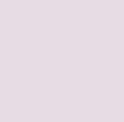



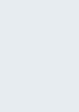
Safety is key “There’s that old saying that once you fall in love with hydraulics and get some oil in your blood, that’s it — you’re in it for life, and I think I’m going to be a lifer,” said Jean Pierre Zola, Business Unit Leader – Compact Hydraulics North America, Bosch Rexroth. “Now, machines are growing more and more sophisticated. Our customers’ expectations are higher, and there’s more focus on efficiency, and more focus on safety, too — because the number of skilled operators is very low here in the United States.”
Oftentimes, automation means less human interaction, such as what’s seen in autonomous vehicles — be they automobiles, huge mining trucks, or agricultural equipment. But when these vehicles are being used in somewhat close proximity to workers, defining a zone of safety is paramount. Meyer noted that if you look at the amount of coding effort that’s spent per feature, Rexroth saw this growth going up exponentially. From 2010 to 2016, that factor went up by almost a factor of three. “We had to put in three times the amount of effort in each one of those features that we had in 2010. And they weren’t just functional features. They were also the non-functional, the safety, the testability, the scalability features,” he said.
MOBILE HYDRAULICS an electronic flushing valve, and we’re able to reduce the standby flow. Plus, it is nothing that is fixed to a specific user or to a specific machine.”
New components are coming According to Peter Braun, Sales Director, having a bigger engine in mobile machinery is not necessarily helpful anymore, and smaller engines of course result in less available power. Trends are being driven by material regulations or the Stage V emission standards in Europe — there, manufacturers are seeing a continued trend of downsizing of the diesel engine and the downsizing of the available engine power. That all means new components are needed, and electrification is the wave of the future. One example of the new generation of components is the Rexroth’s eLION range of electric motor-generators, inverters, and
more into software as opposed to on the hardware side. The first step is the pump. They have created electronic open circuit (or EOC) pump control. This is not just software, Meyer said, but a combination of hardware and software.“Wehave developed pumps specifically for this application, where we can integrate the control of the pump with the software and sensors on the machine to give us more performance than we have today with less complexity,” he said. With hydromechanical controls, Meyer said that currently, we must mechanically adjust the settings — such as different pressure control options. By going to more of an electronic control architecture, that’s taking all those hardware variants and moving them into software, gaining flexibility.
34 FLUID POWER WORLD 8 • 2022 www.fluidpowerworld.com
Now, you can have one pump for all of your machines and you’re able to set those settings however you want — specific to that machine, specific for the region that you’re sending it to, and specific to how the user wants it to Anotheroperate.example he gave is in valves. Now, machine operators can take off the hydromechanical valves and replace them with an electrohydraulic valve. Then the software is what controls the entire system, “For example, standby flow management — currently that’s set by a mechanical setting you have to change on the flushing valve. We can replace that with
Meyer explained that legislative requirements, functional safety requirements, noise requirements, and emission requirements all come into play here. But as safety standards change across time or location, it’s not in any customer’s best interest to have to start from scratch. With the new control software available, customers are able to set the dynamics, set different drive modes, set different HMIs — all within the parametrization. The software meets functional safety standards. That means zero costs — they don’t have to have software engineers who are developing over and over.
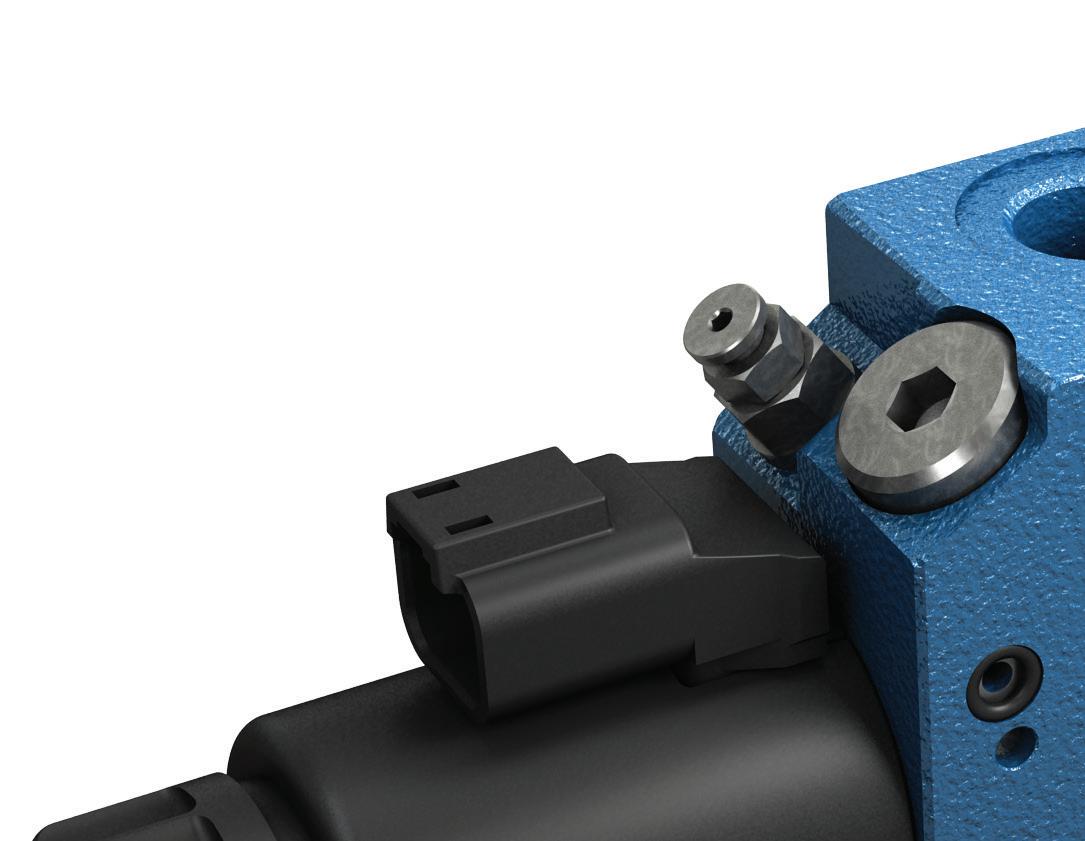



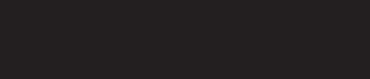
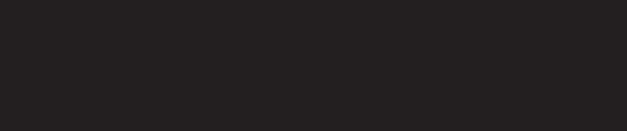
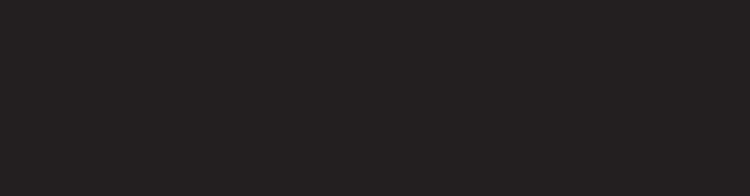

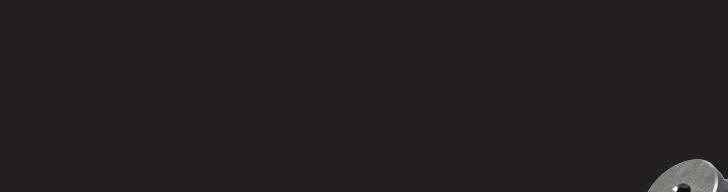
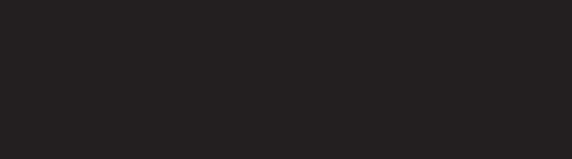
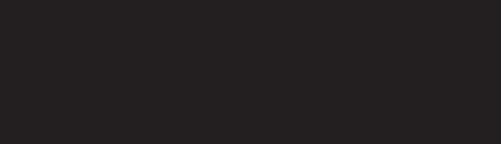

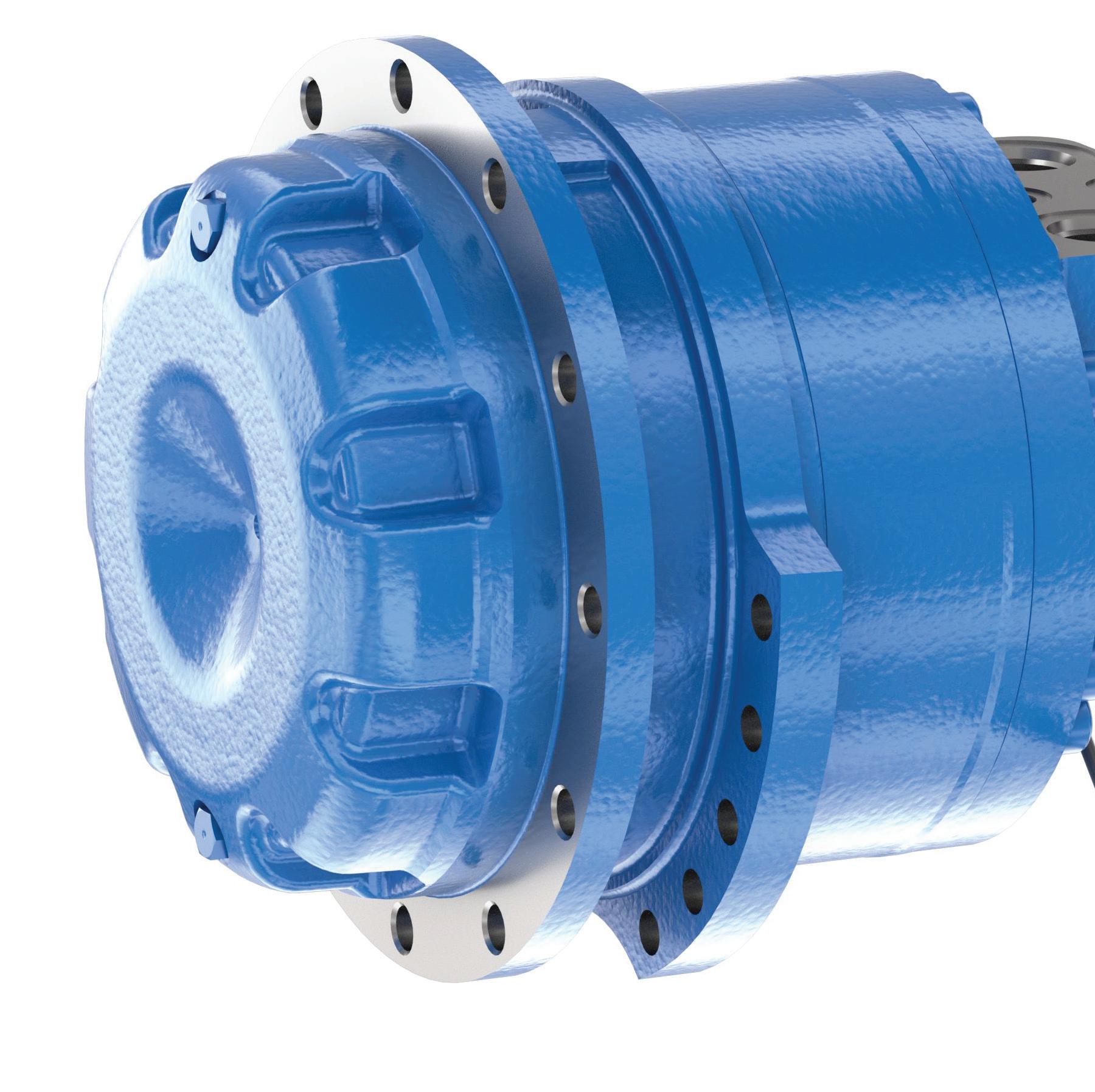
WE TAKE THE PUSH OUT OF PUSH-LOK accessories. The line also contains tailored gearboxes, hydraulics, and software. These components, specifically designed for the challenging environmental conditions of off-highway applications, are scalable, with a nominal power range from 20 to 200 kW for driving and work functions. The eLION range was introduced last September in Germany, and the company said production on the components is starting in 2022. Pilot projects have already been conducted with OEMs that include Kalmar and Sennebogen. Matthias Kielbassa, VP Electrification, emphasized the three most important properties of the new product platform are scalability, robustness, and functional safety. The product family’s electric 700 V eLION motor-generators deliver nominal torques of up to 1050 Nm and maximum torque to 2400 Nm. They are available in four sizes with different lengths and winding configurations. Depending on the design, they are available in a fast or standardspeed version. The company said that more than 80 configurations are possible, for maximum design freedom for manufacturers when electrifying existing and new vehicle architectures. To accompany the range of motors, eLION also includes inverters in various power classes with up to 300 A continuous current and high overload capacity. The inverters support DC bus voltages from 400 to 850GearboxesV. with high power density for hub and central drive configurations (eGFT and eGFZ) are also part of the eLION portfolio and allow compact drive units for a wide range of applications. BODAS software modules are available for the entire eLION platform, along with matching hydraulic components such as axial piston pumps. And other electrical components such as DC/ DC converters, power distribution units, on-board chargers and highvoltage cables round off the range. Manufacturers can rely on these integrated solutions regardless of the energy source (such as hybrid or battery). Possibilities across segments “Once you have electronified your machine, there are basically endless possibilities — you can incorporate our virtual measurement unit with our kinematic resistance software, and we’re able to perform, for example, easy grade functions on machines,” said Meyer. “We’re able to create virtual walls, joystick steering … and this is scalable in everything. You can choose to electrify just the pump or you can electrify the whole system. You can add advanced assistance functionalities at any time, and you can use this with any end-engine technology. And we can use this in any compact segment there is today.”
WORKS WITH A VARIETY OF FITTINGS using easy to change Click-On mandrel system. Mandrel design services are available for your specific application.
FPW Bosch Rexroth | boschrexroth.com
SAVES TIME, install fittings correctly the first time with an easy to load hose grip and up to 300 psi of fitting insertion force.
PORTABLE, take it to where the hose repair is, no additional tools needed, a convenient carrying case with extra storage is included.
BARB-TECH III IS NOW AVAILABLE, a second tool with increased capacity has been added to our product line to handle up to 1” hose and fittings.
REDUCES INJURIES by reducing required hand forces to a 1/3 of the typical fitting installation process of gripping the hose by hand.
HOW ARE YOU ASSEMBLING PUSH-LOK HOSE AND FITTINGS?
BARBTECHTOOLS.COM | 541-204-1899
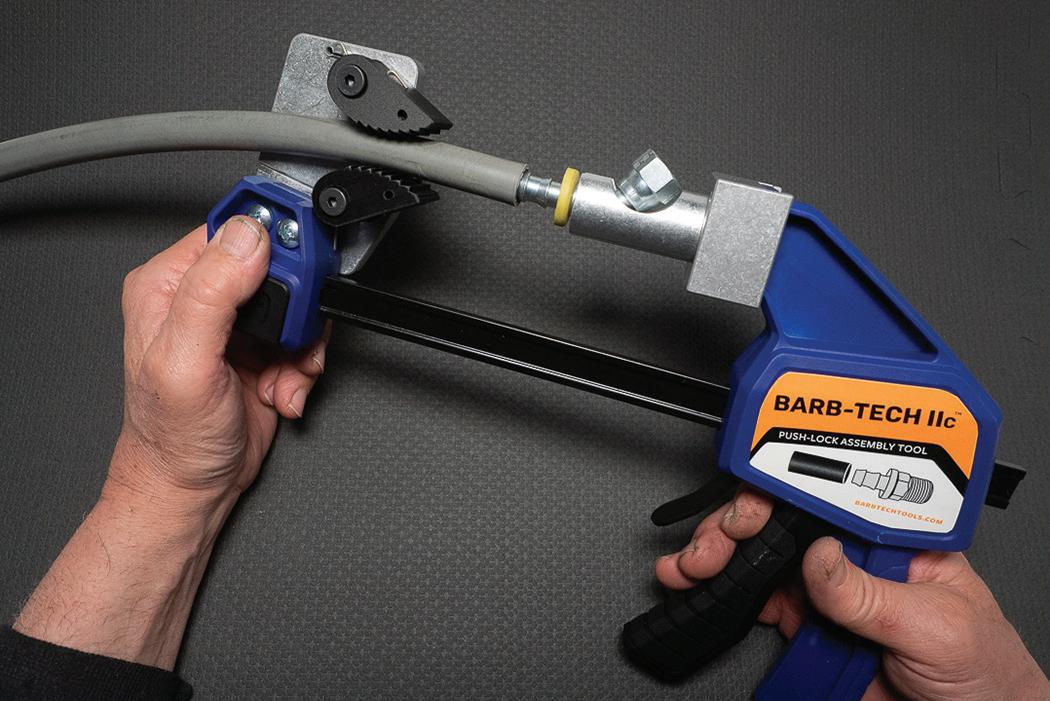
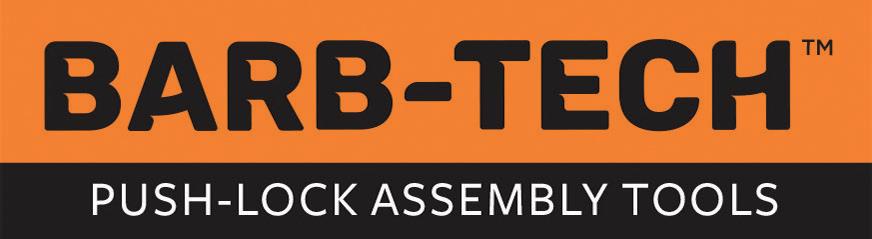
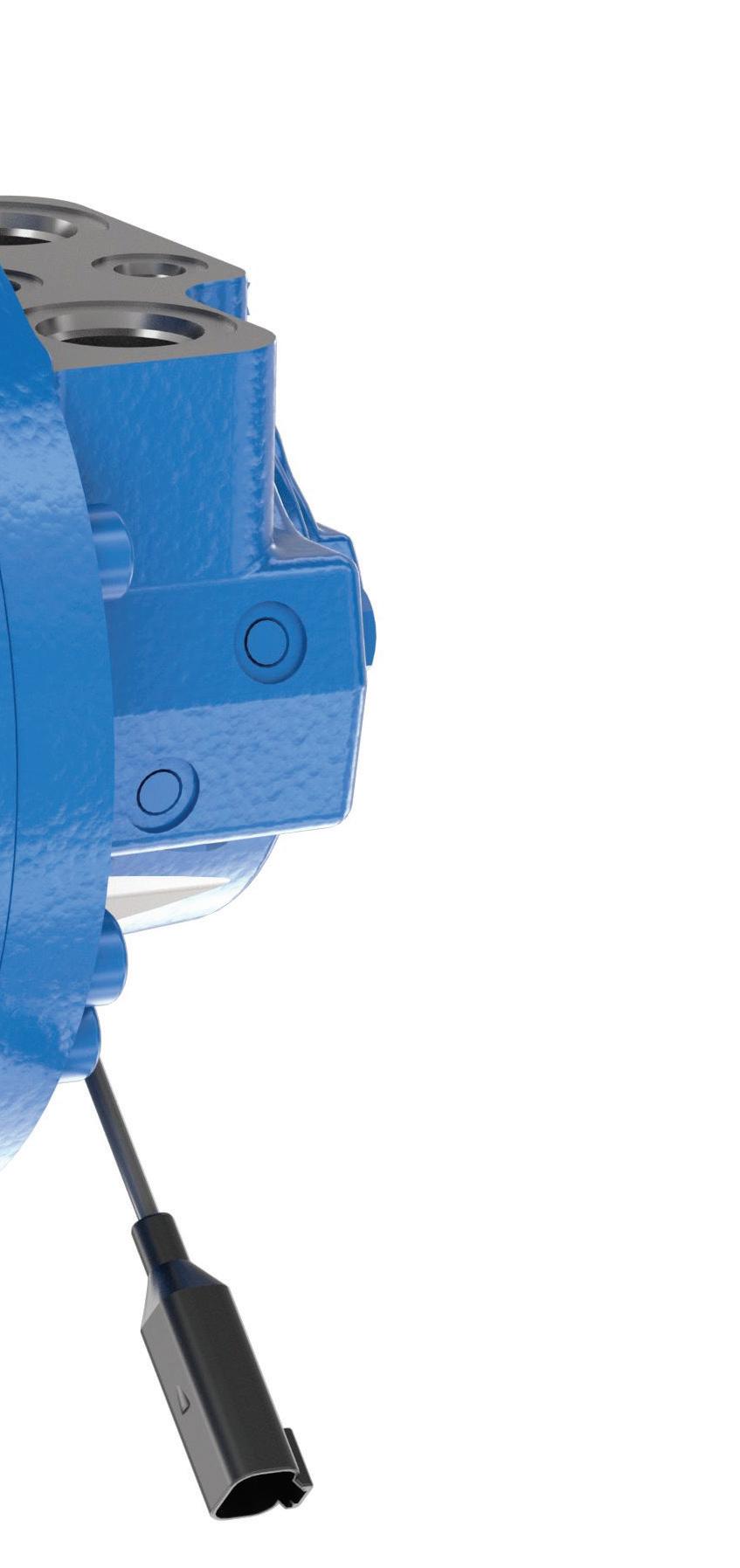
PNEUMATICS
THESE TIPS NOT ONLY ADHERE TO FOOD SAFETY GUIDELINES, BUT ALSO SERVE TO IMPROVE MACHINE UTILIZATION AND PERFORMANCE. BY STEVE BAIN, FOOD AND BEVERAGE INDUSTRY SEGMENT
FOUR pneumatic automation design tips for food and beverage packaging applications, it is a good idea to answer a fundamental question: Why apply pneumatic automation in the food zone instead of electric Pneumatiautomation?cautomation remains a key solution because of its lower relative cost compared to electric automation in food and beverage applications. In the food and splash zones, components must withstand harsh cleaning processes; even in dry cleaning applications, they still need to be cleanable. Moisture, chemicals, and electronics do not mix well. While electric automation can and does exist in food and beverage packaging automation, the cost of protecting the electronics and motor drives up the price. When electrics are applied, they therefore tend to be used selectively. applicaticomponentsFurthermore,inmanyfoodonshave MANAGER, FESTO
TOASEALINGGASKETANDELIMINATEEXPOSEDTHREADS.
PARALLELG-THREADSONTHESEFITTINGS,FRONTANDREAR,SECURETOASEALINGGASKETANDELIMINATEEXPOSEDTHREADS.|COURTESYOFFESTO remains a key
36 FLUID POWER WORLD 8 • 2022 www.fluidpowerworld.com
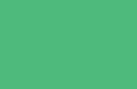













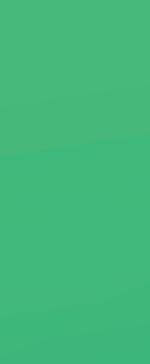

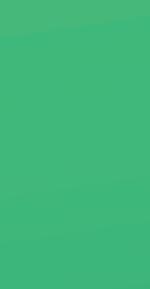
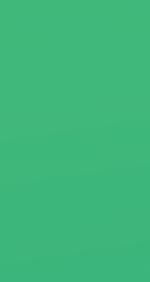
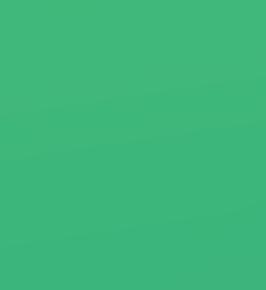
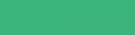
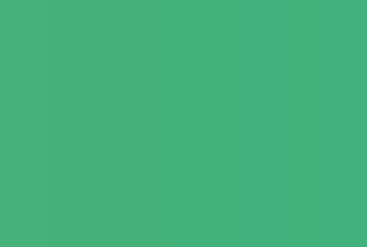



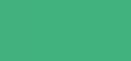


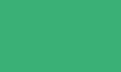

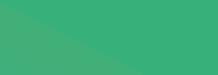
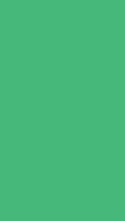
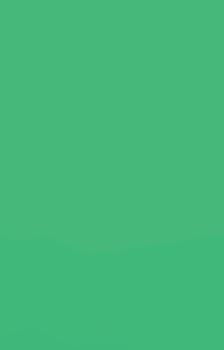
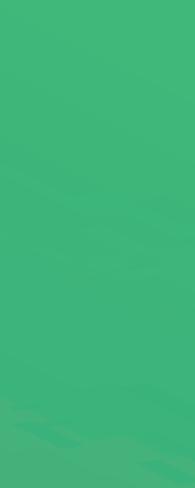
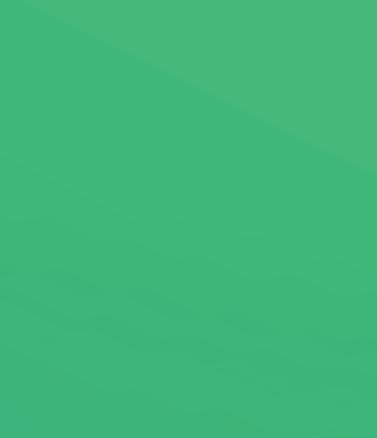
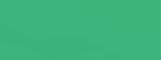



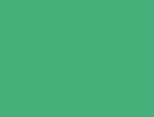
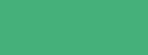
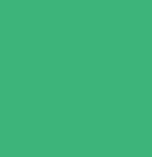
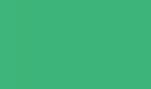


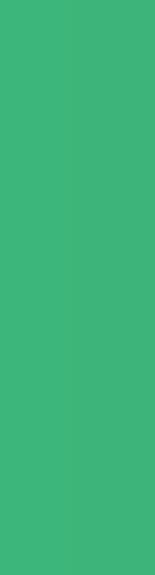


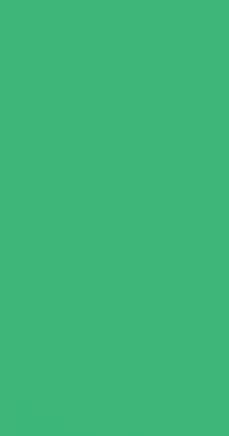
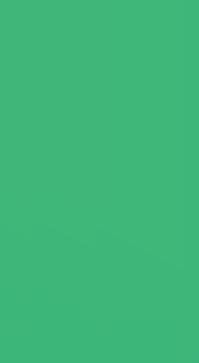
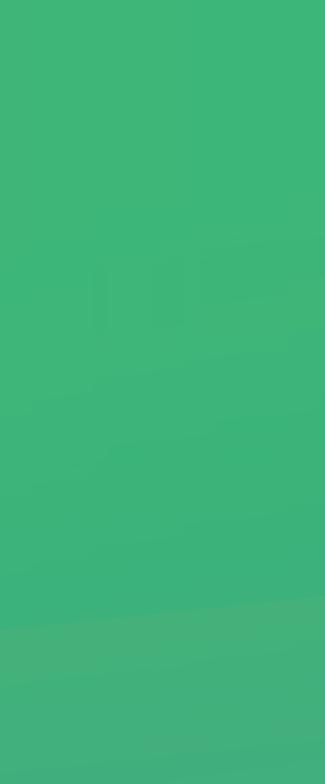

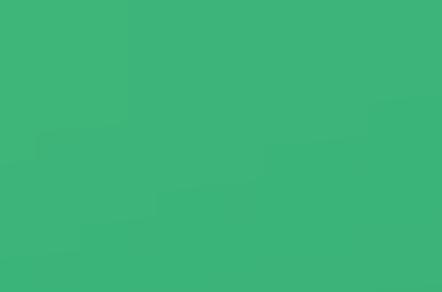
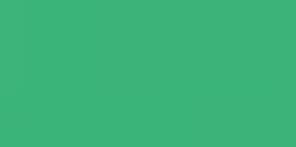
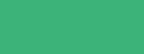

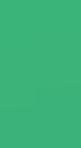
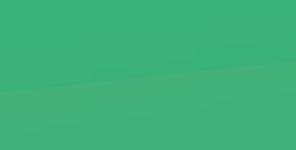
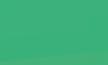
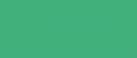


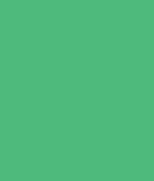
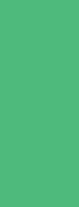
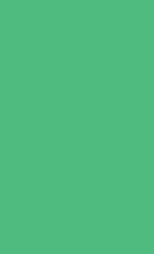
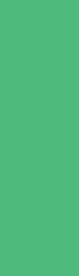
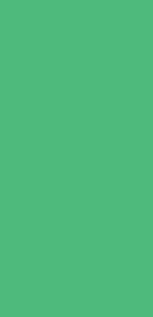
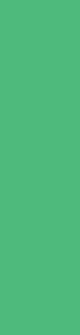

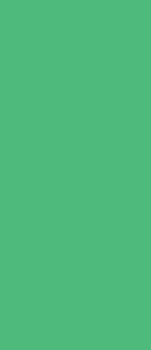
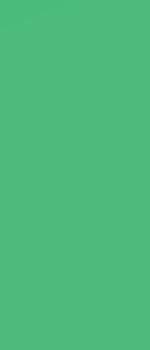

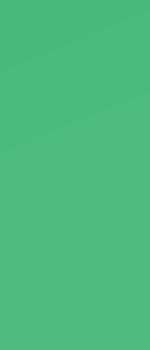
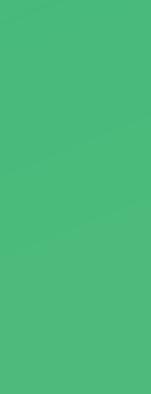

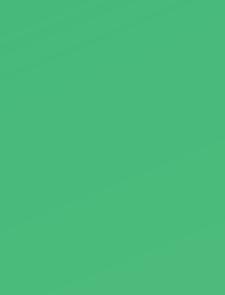

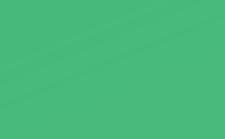
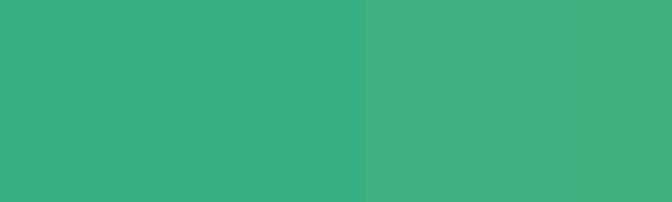



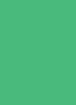

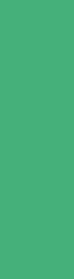

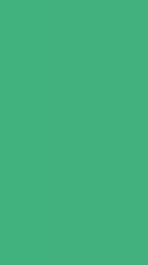
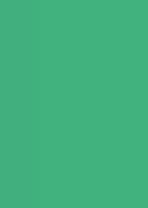


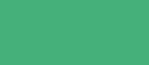
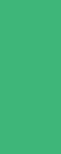
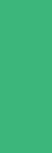


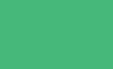


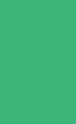
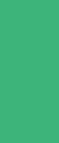
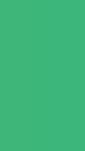

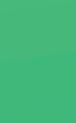




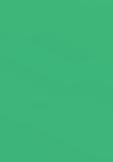

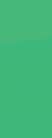
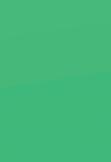






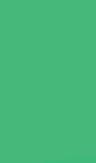




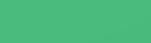


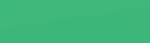




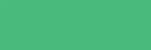
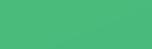
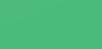

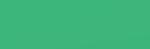



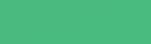

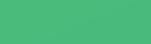
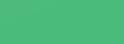





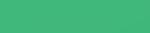

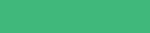
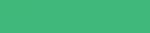

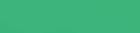
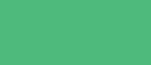
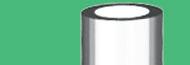
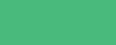

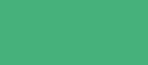
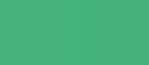

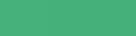









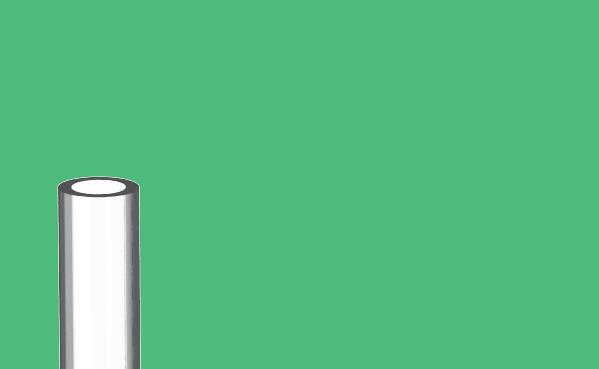
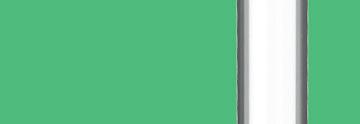

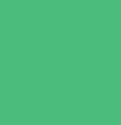
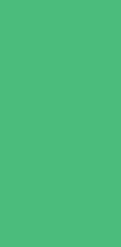

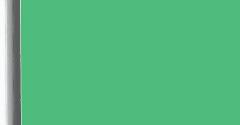




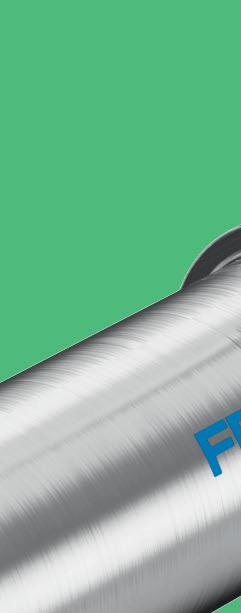

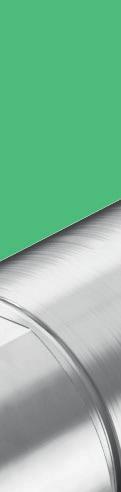

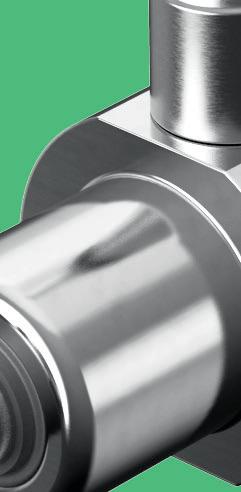
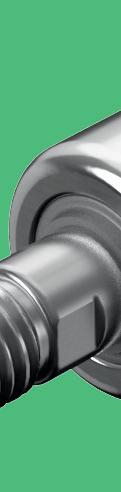
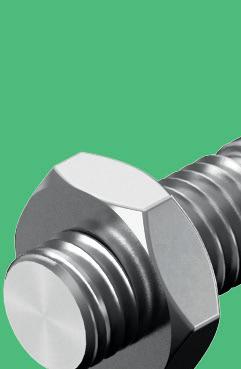







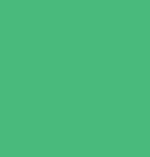
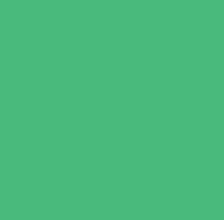


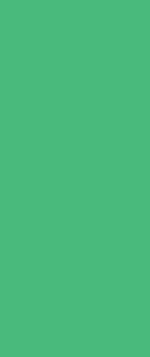

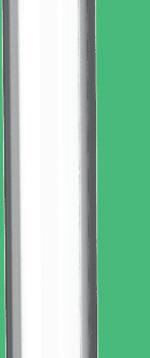
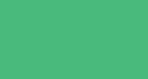
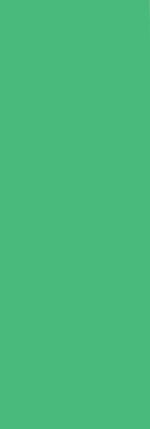

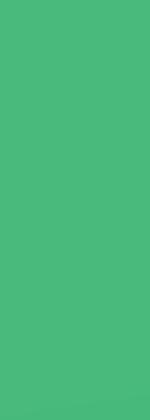






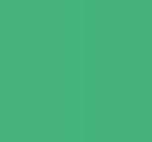
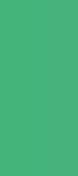
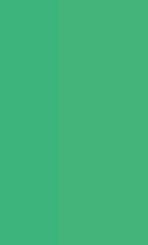
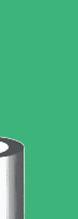

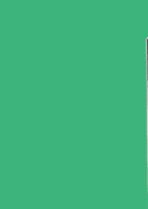
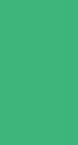



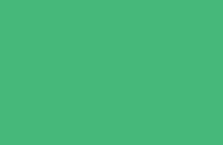


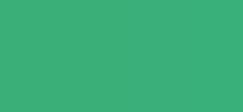

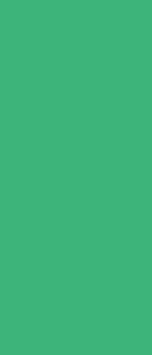



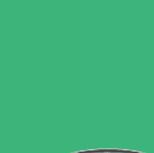





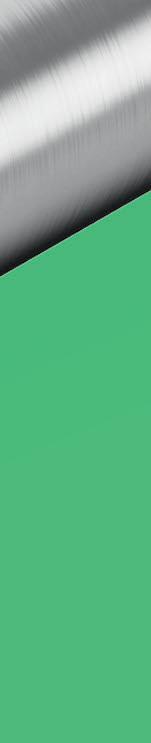
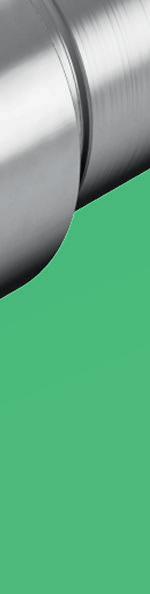

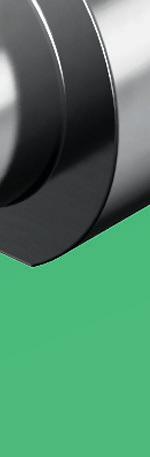
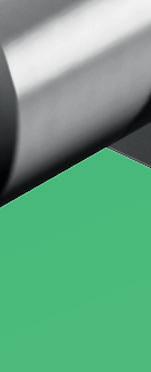
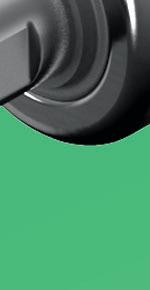
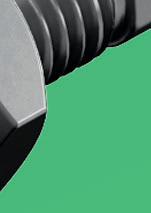



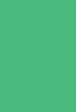






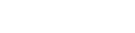
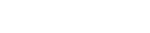







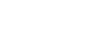




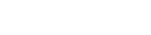








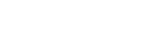





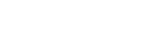













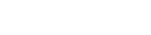










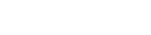





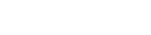








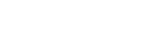




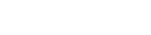







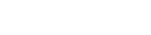








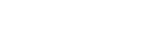



















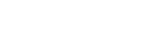




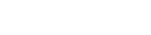




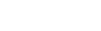
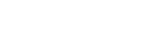




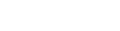





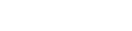


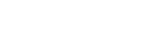








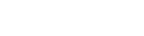











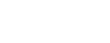

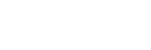







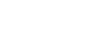



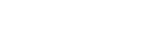


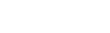





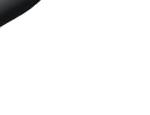




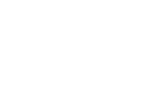

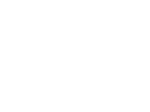




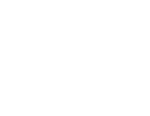




THIS CRDSNU STAINLESS-STEEL CLEANDESIGN PNEUMATIC ACTUATOR TICKS ALL THE BOXES – LARGE RADII, NONCORROSIVE, HIGH GLOSS, AND READY FOR G-THREAD FITTINGS. | COURTESY OF FESTO
Tip 2: Select a clean-design cylinder family Instead of designing with generic cylinders, begin by identifying a metric cylinder family that was created for washdown and cleanability in food and beverage applications. Then design the pneumatic automation system around that family. Food and beverage cylinders are intended to be easy and fast to clean. They have large radii that do not pose a hygiene risk because they promote high flow velocities of the cleaning agents and disinfectants. There are no tight spaces where required cleaning cannot be achieved. These cylinders feature high-gloss surface finishes, which are essential for components in the food zone. High gloss reduces microbial contamination. FDAapproved seals and NSF-H1 grease protect against unintentional adulteration of the food product. Be sure the cylinders have dry run seals for long service life. Other key qualities for these cylinders include machine parts that resist corrosion, are mechanically and chemically stable, and rigorously designed to conform to cGMP criteria. A cylinder’s self-adjusting end position cushioning system should be constructed without contaminantsusceptible adjusting screws.
www.fluidpowerworld.com 8 • 2022 FLUID POWER WORLD 37 shorter operational lives due to the harsh environment, which means parts need replacing sooner. Replacing a less expensive pneumatic actuator keeps operational costs lower. Taken as a whole, pneumatic automation is the predominant solution for its lowest total lifecycle cost due to the harsh environments.
• Increased machine performance
The following advice taken together achieves three important design objectives: Conformance to food safety and sanitary design guidelines Improved machine utilization
Tip 1: Standardize on metric pneumatic systems for food and beverage packaging applications The reason for standardizing on metric pneumatic systems is that tubing and fittings for metric cylinders use G-thread fittings that have parallel threads. Parallel threads seal flush to a gasket and eliminate exposed crevices. Utilizing G-threads with metric tubing is optimum for Food Safety Modernization Act (FSMA) compliance. On the other hand, imperial NPT fittings pose a contamination risk. The imperial fittings seal by wedging threads together. They require sealing tape. These tapered threads risk contamination, not only with exposed threads, but also through metal fragments or flaking tape. Utilizing G-threads lowers the risk of contamination and cleans faster, which equals greater machine utilization.
Tip 3: Do not exhaust valves over the food zone Exhausting a valve over the food zone is similar to holding a blow gun and blasting unfiltered air directly into the food or packaging. The only difference is that rather than the air coming directly from the compressor, air exhausted from the valve has also passed through the valves, into and out the cylinder, and back through the valve, picking up contaminants along the way. Either mount the valves below the food/packaging zone or mount them above and duct the exhaust below the food zone. Check valves are often overlooked in the food zone. While check valves can help improve machine cycle time because the air does not exhaust back to the valve, this means the air is exhausting over the food zone. If a check valve must be used, the exhaust should be ducted below the food zone.
•
•

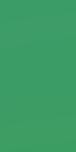
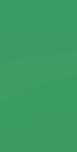
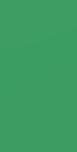
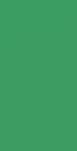
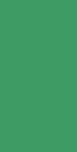
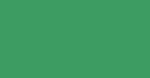
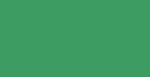
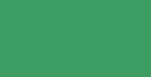
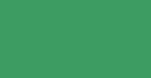
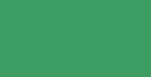
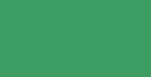
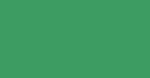

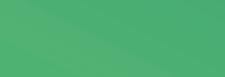
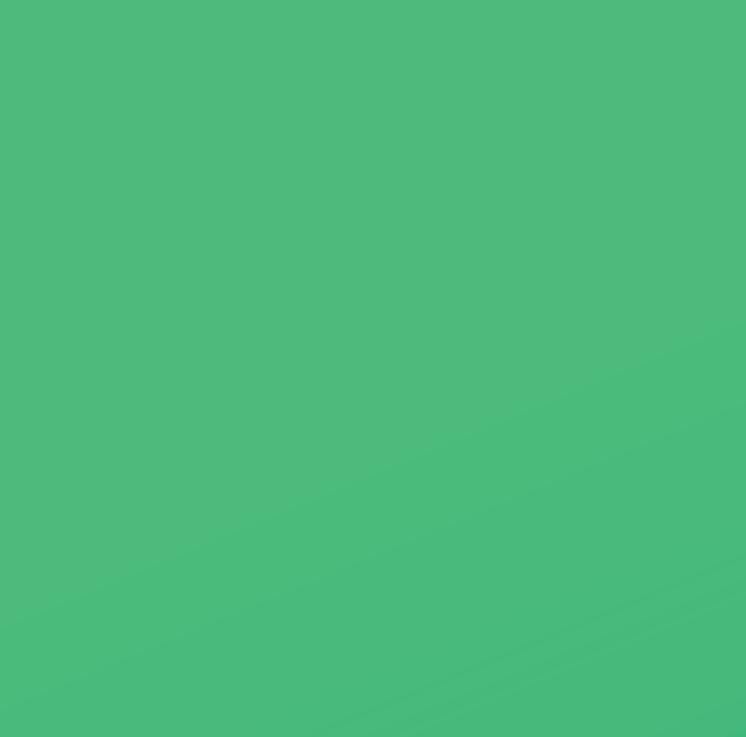
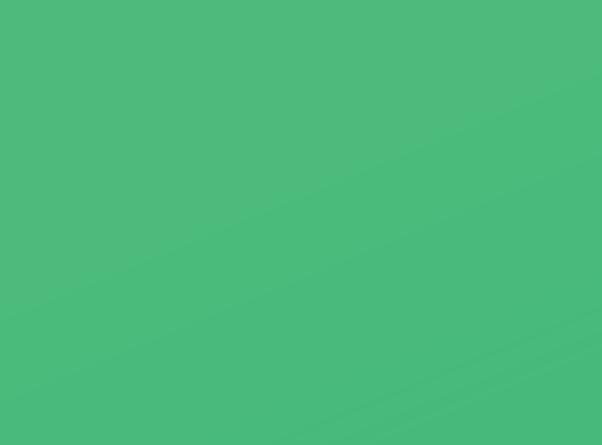
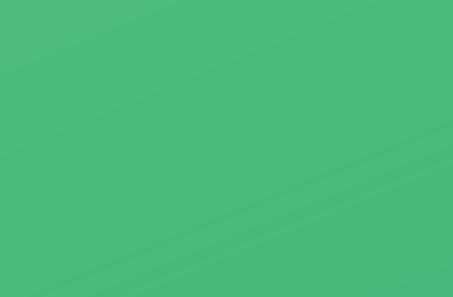

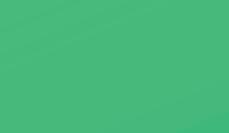
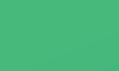


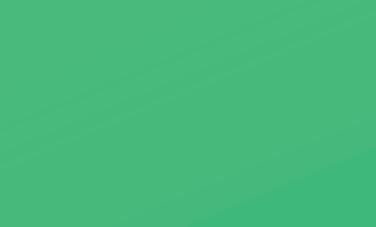
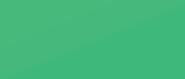


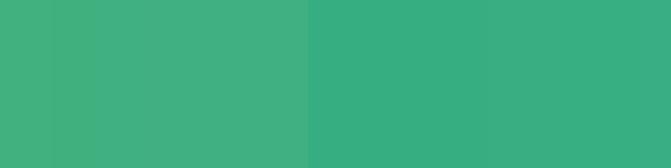
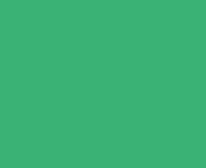
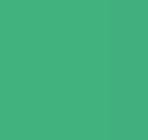


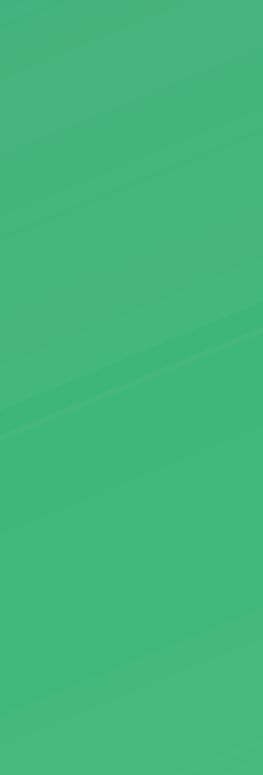
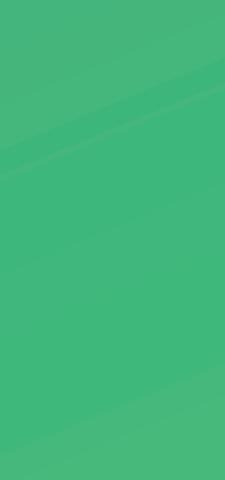


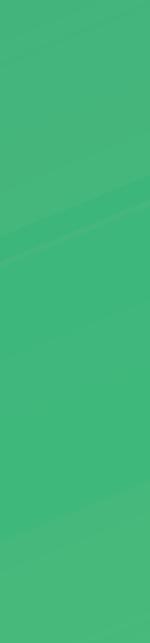
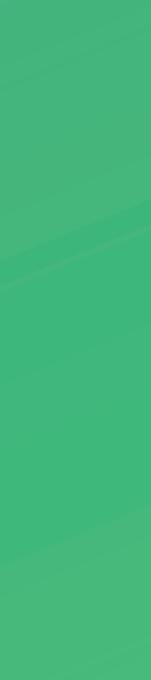







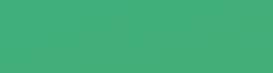
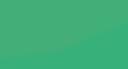
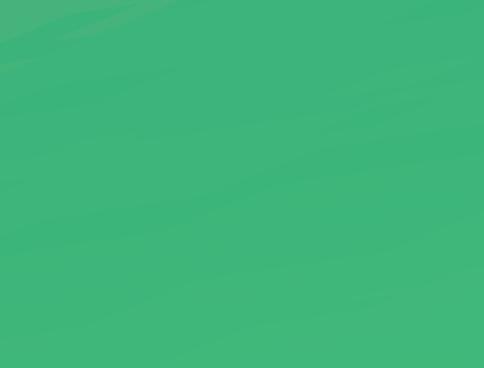
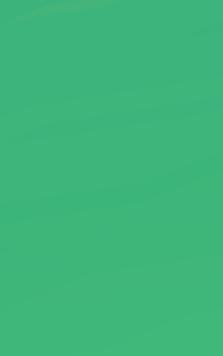
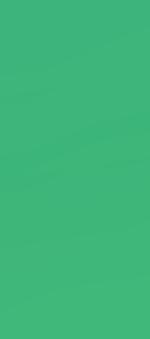
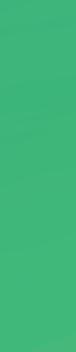















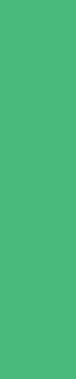
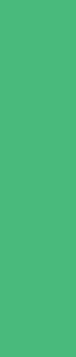
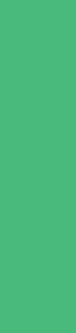
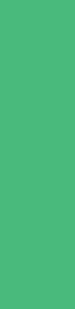


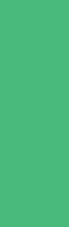

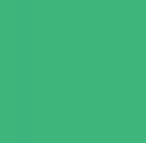
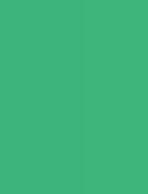
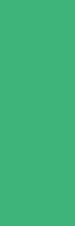


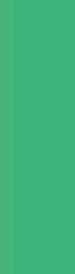


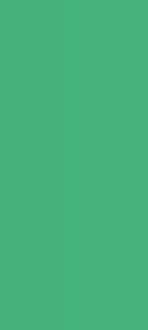
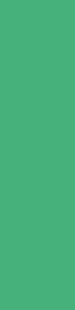
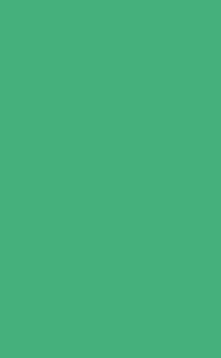


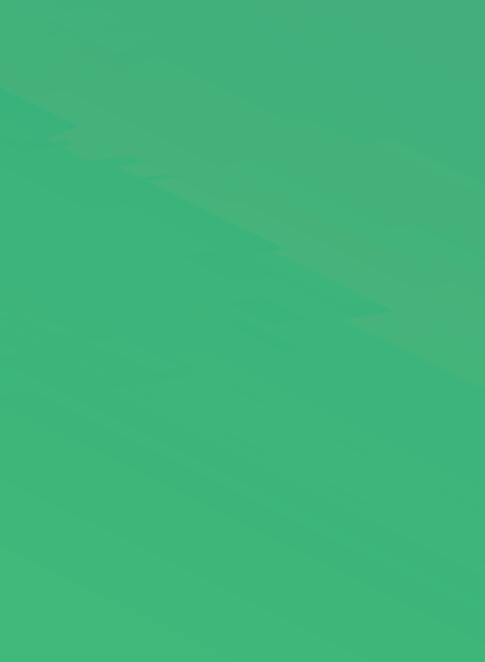
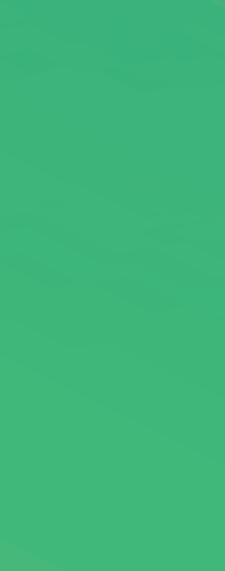


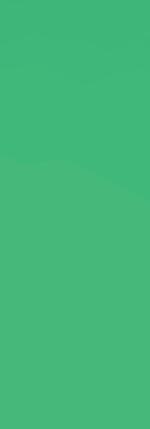
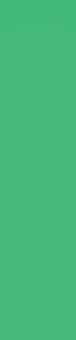
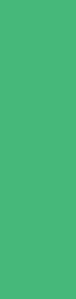
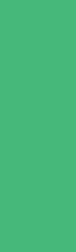

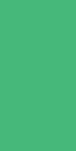
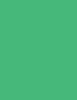
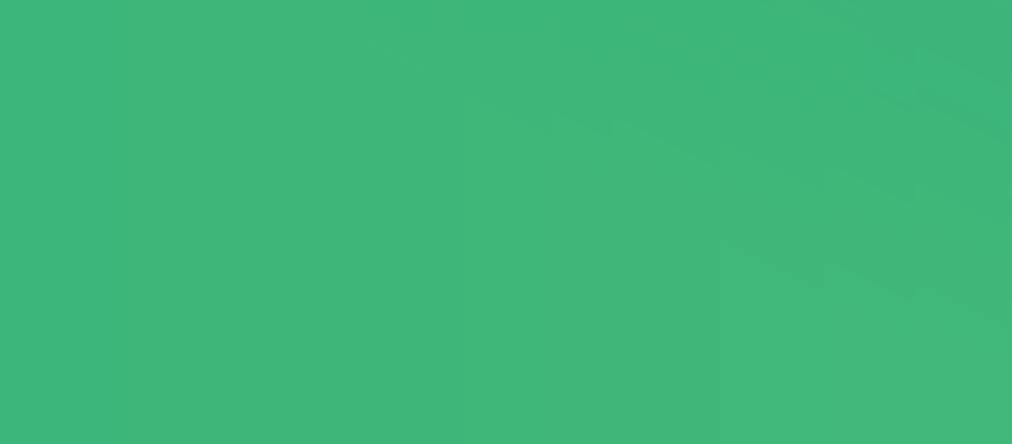



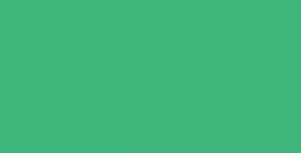




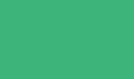

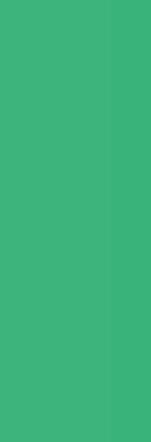
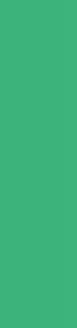
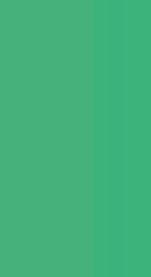

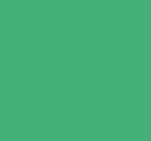

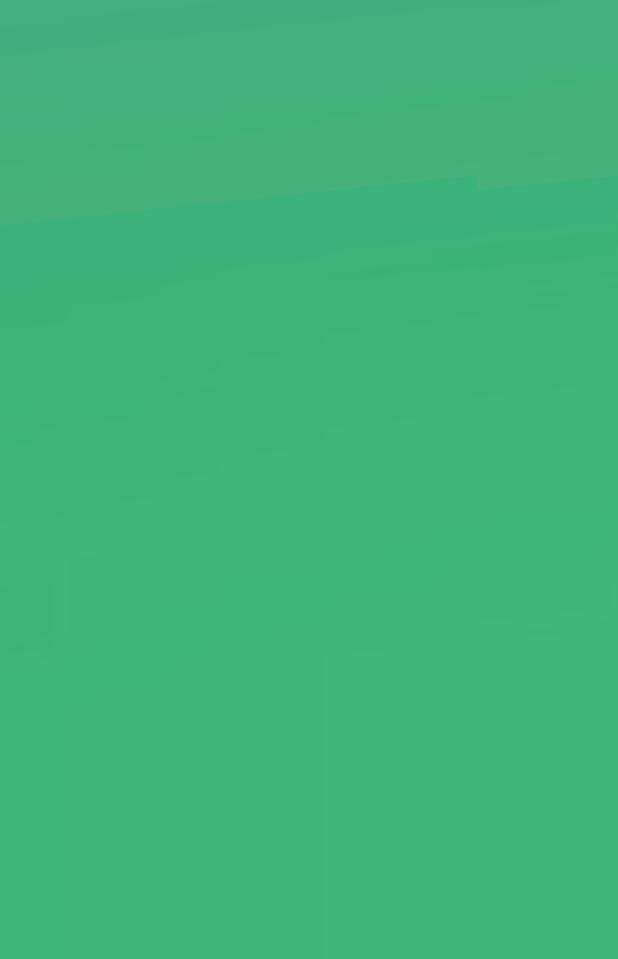
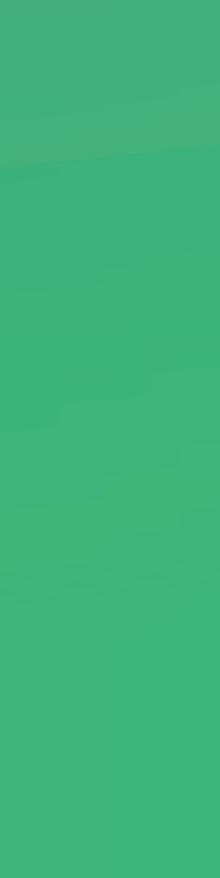

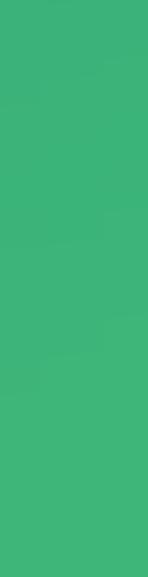


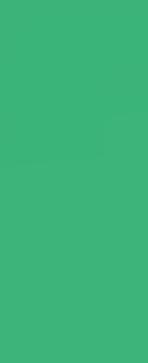
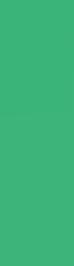
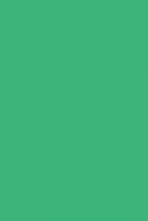
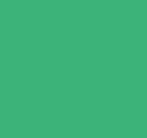
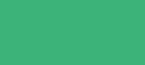
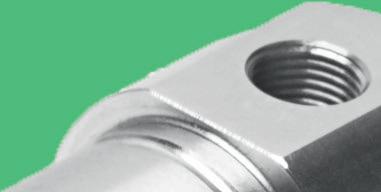
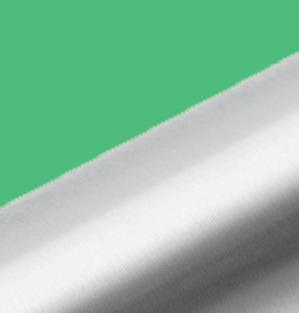
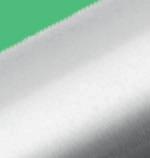

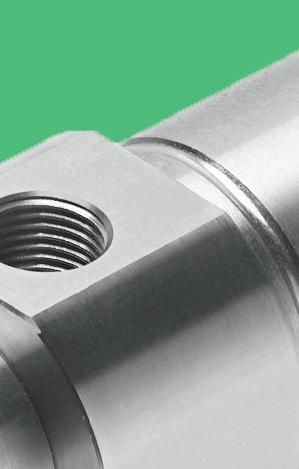
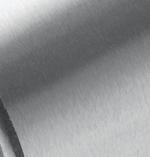
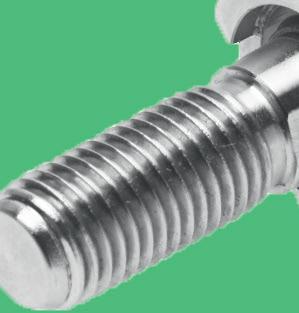
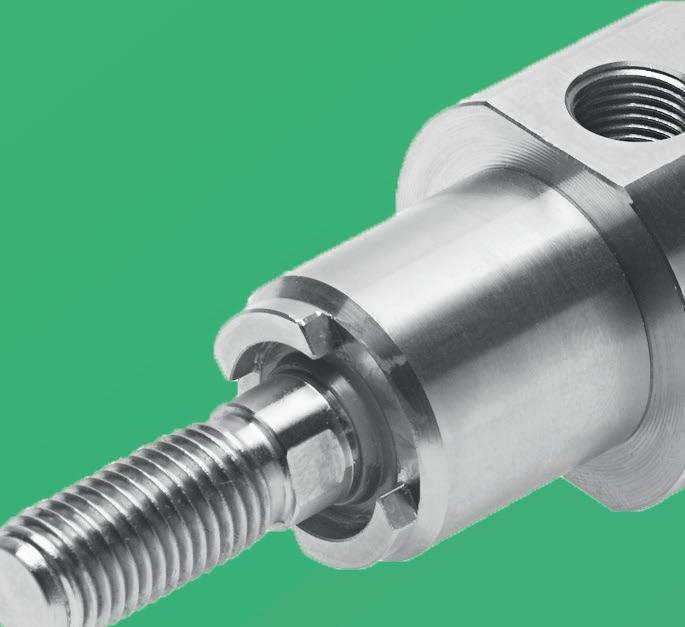
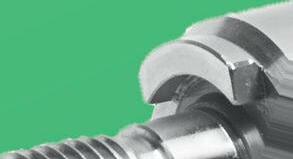
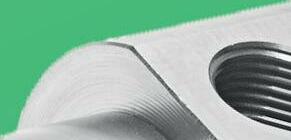

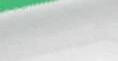

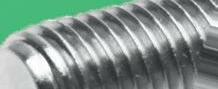

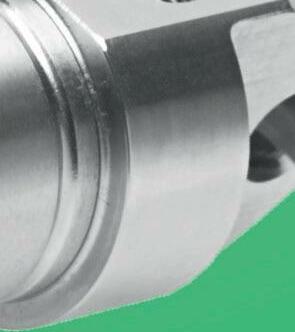
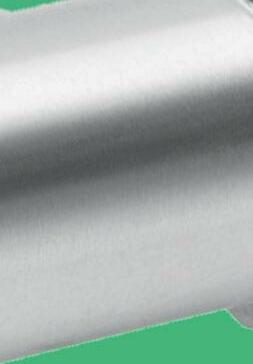
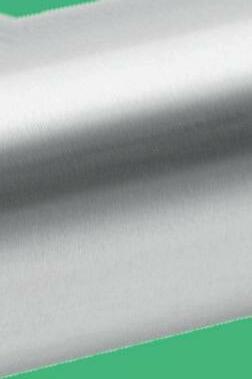
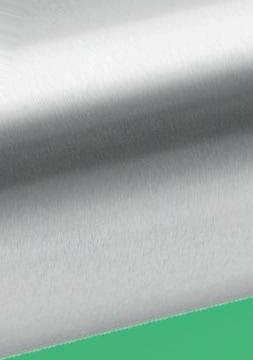
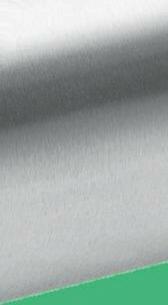
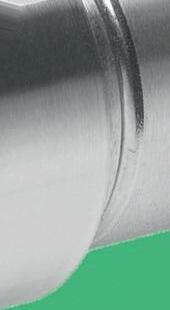
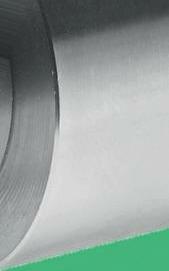

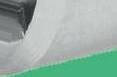
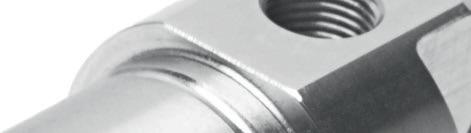





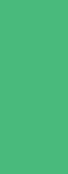
38 FLUID POWER WORLD 8 • 2022 www.fluidpowerworld.com
Tip 4: Shorten tube length between valve and cylinder One of the most important developments of the last several years has been machine mountable valve manifolds rated at IP69K washdown that, like washdown cylinders, conform to clean-design principles. The elimination of cracks and crevices reduces cleaning time for faster changeover and improved machine availability.
costs
The new ability to move the manifold from the control panel to the machine in the food zone cylinder delivers advantages, not the least of which is energy savings. Chart One shows the dramatic energy cost saving of moving a manifold out of the panel and closer to the cylinder – 50% in this example. The shorter the tubing length between valve and cylinder, the faster and more repeatable the cylinder’s cycles. Faster cycles improve performance. In many applications PNEUMATICS
*ASSUMPTIONS: 20 CYCLES/MIN, 16 HOURS/DAY, 300 DAYS/YEAR, 6 BAR PRESSURE, $0.35/1000 smaller Mounting valve manifolds on the machine allows control cabinets to be smaller or eliminated, which can significantly reduce both cost and footprint. Moving the valve manifold outside of the control cabinet also eliminates pneumatic connections installed into the wall of the control cabinet, lowering machining in materials and labor as well as reducing the number of components required. Greater control There are also new opportunities for achieving both the benefits of on-machine mounting and greater control flexibility. The Festo MPA-C IP69K-rated manifold, for example, can be configured with supply and exhaust ports on each valve slice. All ports for every position can be completely independent of the valve next to it. For complex pneumatic situations where several different pressure zones are used, this can be one of the most cost-effective solutions. For some applications, the designer may face the choice of either locating an adjustment point for easy access in a panel or on the machine where it may be difficult to adjust. The latter means losing all the advantages of machine mounting. The MPA-C, in a second example, allows the OEM to plumb each valve slice to a pressure regulator. This solution achieves both objectives: easy adjustment and machine mounting. There are other design considerations for food and beverage packaging applications such as selecting tubing materials that withstand harsh chemicals and resist plastic transfer to food. Hydrolysis-resistant polyurethane (PUN-H) and Polytetrafluoroethylene (PTFEN) tubing are ideally suited for use in the food and beverage industries. Both resist cleaning agents, microbes, and hydrolysis and are FDA compliant. PUN-H is more flexible and economical, while PTFEN is ideal for the harshestDesignersenvironments.canuse one of the many free online tools offered by Festo to size the pneumatic system appropriately so that the system runs as energy efficient as possible. And of course, specifying air filtration units to achieve 0.01 µm filter with 99.9999% efficiency is a must. It is the four tips, however, that lay the foundation for compliance, utilization, and performance in food and beverage packaging applications. FPW Festo | festo.com
SCF such as filling, more precise cycles achieve better control of the process leading to higher consistency in product volume and weight and lowerThewaste.trend today is for
THE SHORTER THE TUBING LENGTH THE FASTER THE PRESSURIZATION, LOWER LEFT IN THE CHART, MEANS HIGHER CYCLE RATES AND MORE REPEATABLE CYCLES. | COURTESY OF FESTO Scenario Manifold in a panel Machine Mounted Manifold Tubing length 20 ft 6 ft Tubing volume 75 cm3 23 cm3 Cylinder volume 25 cm3 25 cm3 Total volume/cycle 200 cm3 96 cm3 Annual energy cost* $85.43 $41.01
machines.
THE MPA-C MANIFOLD, TOP CENTER, IS INSTALLED IN A HARD TO ADJUST POSITION. PROPORTIONAL PRESSURE REGULATORS, LOWER LEFT, PLUMBED TO THE MANIFOLD, SOLVE THE ADJUSTMENT PROBLEM. | COURTESY OF FESTO
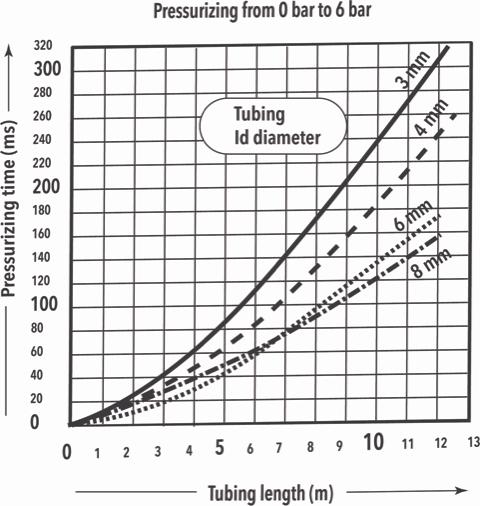
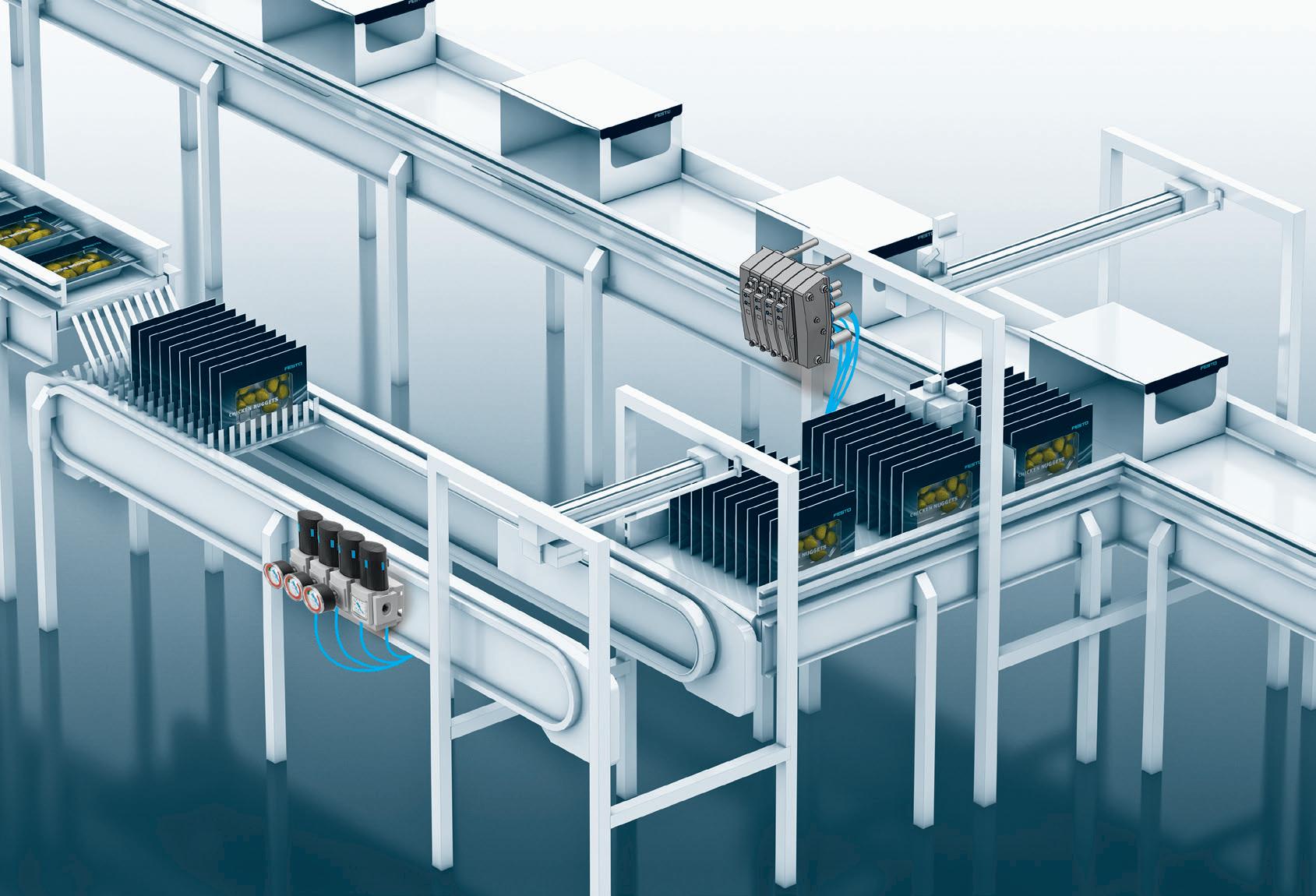

AMERICAN CHAMP SERIES LightDMD400andMedium Duty Dump Trucks and Trailers Go with the dump pump that works as hard as
ADVERTORIAL
17-month, hybrid program, offering online and on-site learning. “I liked that the program was hybrid, so I wouldn’t have to travel all the time,” said Rotman, who lives on the West Coast. “And Weatherhead has a very good reputation in organization
cohortcocktailclassroom.”shehuddlewesomeonebeingRotman,onfromTheperson’stosittingprofessoraroundcohort’swesaid.myBecausedevelopment.”ofpandemicrestrictions,Rotman’scohortwasn’tabletomeetinpersonuntiltheirlastscheduledresidencythisspring.Unfortunately,thiscoincidedwithherbeingsevenmonthsintoadifficultpregnancy. “TherewasnowayIwouldbeabletomakeitonowntocampuswithouthelp,”she“IthoughttheywouldZoommeinlikedidwithourothercourses.” Instead,Rotmanshoweduptoherfirstin-personclass,glidingtheroomtotalkwithherpeersandasatelepresencerobot. TherobotlooksequivalenttoaniPadontopofalongpoleattachedwheels.TheiPadscreenshowsthefacewhoisusingtherobot.personcaneasilymovetherobotlefttoright,orforward,byclickingdirectionalarrowsontheirscreen.Totheexperiencewasasclosetoinpersonasshecouldimagine.“WiththerobotIcouldgochatwithindividuallyintheroomandwhenhadgroupworkIwouldsitthereandwiththegroupinthisrobotbody,”said.“IfeltlikeIhadapresenceintheBeyondclass,Rotmanattendedareceptionthisspringwithherasarobot.“Icouldlookaround and drive the robot over to whoever wanted to chat. It opened up a host of different possibilities way beyond what Zoom could offer,” said Rotman, who graduated this spring with her master’s degree. Other professors who have taught courses with a student robot share similar sentiments. Professor of Organizational Behavior Chris Laszlo said the use of the robots are, “very similar to having a student in the front row,” he said. “They’re at the same height as a student who would be sitting at a desk and the screen is filled with their face.” If a student using a robot wants to ask a question in class they can do so by raising the height of the stick of the robot, similar to if a student was raising their hand. “It’s pretty realistic,” said Department Chair and Professor of Accountancy Tom King. “What is really cool is when class ends and students disperse into groups a robot rolls right up to a group and joins the conversation.”Kingsaidthe partnership with Permco provided a solution for hybrid learning. “We have to figure out hybrid learning and the use of robots is very helpful in this journey,” he said. “This is a school that’s based on innovation and we try new things.”
Home of the American Champ 1500 Frost Road Streetsboro, OH 44241
Precision-Engineered Fluid Power Products
No problem, says Permco and Case Western Reserve University
AMERICAN CHAMP
Recently, Case Western Reserve University’s Weatherhead School of Management students in Cleveland have had the opportunity to attend class in-person — even from thousands of miles away, thanks to the efforts from Permco Inc. In the fall of 2021, Permco supplied Weatherhead School with 12 telepresence robots — at no cost to the school — which have been used by Permco employees, as well as other students and faculty members who were in need of a robot. The conversation to use robots came about during the winter of 2021 when Permco, a hydraulic pump manufacturer in Streetsboro, Ohio, wanted to send a few of its employees to receive their Master of Business Administration (MBA) degree from Weatherhead School. Because of the pandemic safety measures Permco was taking, the student employees were not allowed to come to class in person. “After some wonderful conversations with the creative minds at Case Western Reserve, we were able to come up with a way that would make it possible for students to attend class without losing that in-class feel,” said Bryce Dalton, director of talent development at Permco, and one of the part-time MBA students who uses a robot to attend class. “This is what led to the beginning of this game changing pilot program. These robots areReesaamazing.”Rotman started her first semester in Weatherhead School of Management’s Master of Science in Positive Organization Development and Change (MPOD) program in January of 2021. The program is a
Permco’s American Champ Dump Pump works as hard as you do - even under extreme conditions. It’s the only dump pump built entirely in the USA with the highest quality globally sourced products. The American Champ minimizes down time and maximizes productivity so you can always get the job done. To nd the best solution for your needs, call 330-626-2801 or visit permco.com
Virtual learning?
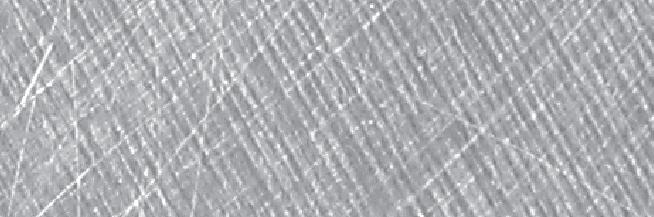






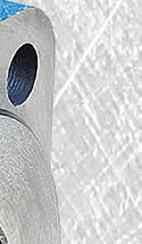
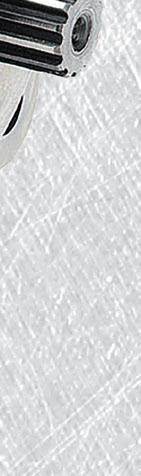
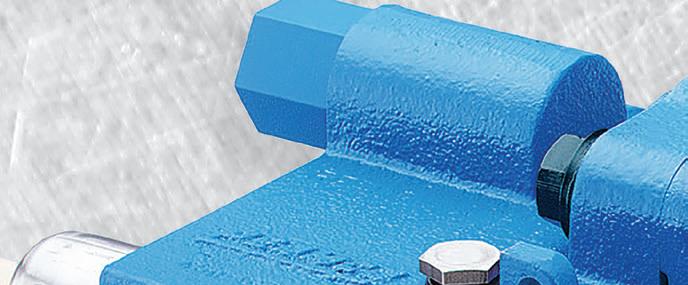
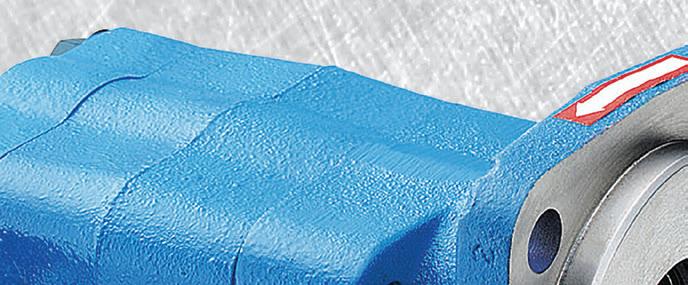
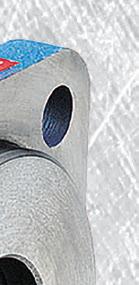

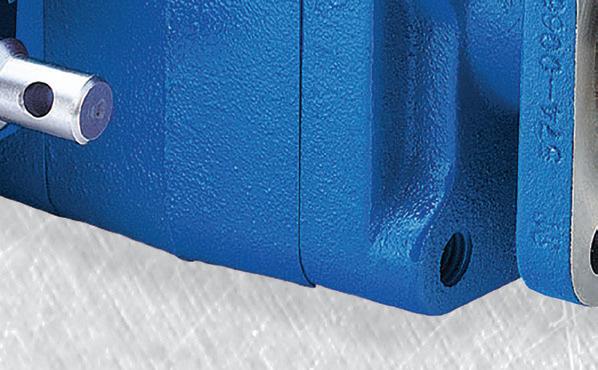
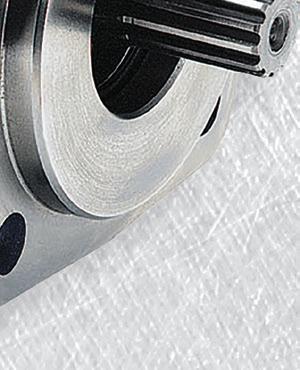
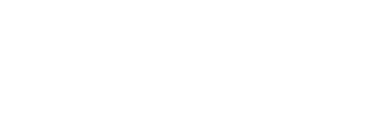
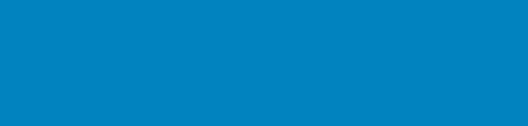
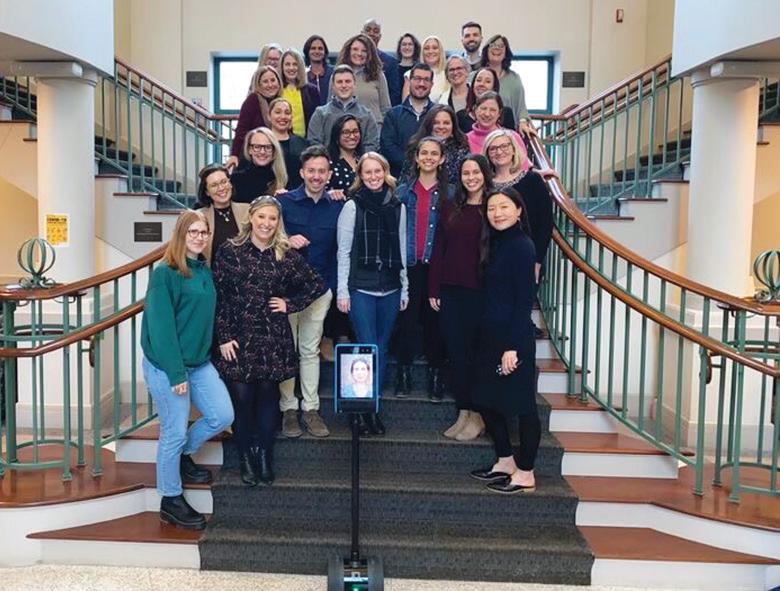


heads back to the Midwest Pack Expo
Pack Expo is scheduled to run from October 23-26 at McCormick Place Convention Center.
40 FLUID POWER WORLD 8 • 2022 www.fluidpowerworld.com PACK EXPO SHOW PREVIEW
By Paul J. Heney, VP, Editorial Director
www.fluidpowerworld.com 8 • 2022 FLUID POWER WORLD 41 Pack Expo International, the annual Fall tradeshow and conference dedicated to packaging machinery and related technology, always features a broad variety of pneumatic components and applications. The show, which alternates each year between locations in Las Vegas and Chicago, is back in the Windy City for 2022, and is scheduled to run from October 2326 at McCormick Place Convention Center. Pack Expo, which is run by PMMI, The Association for Packaging and Processing Technologies, bills itself as “the most comprehensive packaging and processing show in the world.” In response to the unprecedented demands on the industry, this year’s version of Pack Expo will offer more features than ever before, according to show management. PMMI explained that it is vital for the packaging and processing industries to come together and share innovations, connect with colleagues, hear from experts, and see machinery-in-action.
Show features
The trade show and convention is certainly the most efficient and effective way to do all of this, with solutions for more than 40 vertical markets. PMMI said that no other event this year will showcase entire production line solutions and offer attendees everything needed to compete in a changing marketplace.
The interactive “Pack to the Future” exhibit celebrates the role of packaging and processing through history and the impact it is poised to have on our future. Accompanied by an educational component, the Pack to the Future Stage will provide free industry-expert presentations on cuttingedge industry advancements. Pack Match at Pack Expo International also debuts this year, providing attendees complimentary personalized, one-on-one guidance with Pack Match Advisors to connect attendees with the right suppliers.
“There has been so much innovation in our industry since this show’s last in-person installment in 2018 that end users can’t afford to miss this opportunity to see the latest breakthroughs live, in-action,” said Jim Pittas, president and CEO, PMMI. “No other show in the world this year will offer what Pack Expo International offers. We can’t wait to return to Chicago to debut our brand-new show features, reinstate show favorites, and continue to drive the industry forward.”
The Emerging Brands Summit will launch at Pack Expo International 2022 and will be a one-day event featuring educational content, tabletop exhibits and expert advisors. This new program is aimed at founders and leaders of startup manufacturing
• The Logistics Pavilion — A crucial part of the product journey is from manufacturer to consumer. With the boom in e-commerce, The Logistics Pavilion in the North Building will be the place to find targeted solutions related to the supply chain, including warehousing, fulfillment, distribution logistics services, and transportation providers.
42 FLUID POWER WORLD 8 • 2022 www.fluidpowerworld.com
• The Package Printing Pavilion features digital printing and converting, labeling, coding, and marking technologies.
• The Containers and Materials Pavilion is the prime destination for companies looking for innovative containers and materials to meet sustainability goals, refresh a brand or launch new products. It also houses award-nominated packaging solutions in The Showcase of Packaging Innovations, sponsored by WestRock.
• The Reusable Packaging Pavilion, sponsored by the Reusable Packaging Association, showcases reusable packaging solutions to help reduce waste, cut costs, and gain supply chain efficiency.
• The Association Partner Pavilion houses leading associations dedicated to advancing the packaging and processing industry, offering significant resources, insights, and expertise all in one central location.
Pack Challenge is a brand-new packaging competition that brings high school teams together for a head-to-head machine-building competition. The winning school will be awarded $5,000 with an additional $2,000 split between individual team members. Afterward, the teams will take the machines back to their school, providing future students the opportunity for hands-on experience.
Programs and activities In addition to Pack Challenge, Pack Expo International offers additional programs and activities aimed at getting students excited about careers in packaging and processing. The Future Innovators Robotics Showcase is where high school robotics teams from across the country showcase their
The new Industry Speaks Stage features expert sessions from the Pack Expo Partner Program, addressing the latest hot button topics and industry trends across multiple industry verticals.
The Processing Zone returns in 2022 along with the Processing Innovation Stage — focusing on the latest breakthroughs in processing. In today’s manufacturing environment, processing and packaging are integrated systems, making it critical to bring both solutions under one roof.
• The Education and Workforce Development Pavilion is Pack Expo International’s one-stop-shop for resources to strengthen and grow the current workforce.
Brand new pavilions at Pack Expo International are:
Returning favorites include unmatched show floor education on three Innovation Stages and at The Forum. The Forum will feature interactive sessions, including small group discussions and Q&A sessions. The Innovation Stages on the show floor provide quick presentations on breakthrough technologies and techniques focused on a wide range of industry-specific solutions. These returning pavilions will include:
PACK EXPO SHOW PREVIEW companies looking to scale their brand to larger production through either in-house facility build out or outsourced relationships with contract manufacturers and packagers. Exhibitors will include packaging machinery, packaging materials, processing equipment and contract manufacturing and packaging.
• The Healthcare Packaging Pavilion The name is the only thing that’s changed about this gathering ground for life science industries. Innovations for pharmaceuticals, biopharmaceuticals, nutraceuticals, and medical devices will be front and center in this targeted show floor destination.
• The Confectionery Pavilion, sponsored by the National Confectioner’s Association, highlights candy trends and technologies, and also offers The Candy Bar Lounge for casual networking and idea-sharing.

design, engineering and troubleshooting skills. The Amazing Packaging Race is a fun, educational event where teams from colleges and universities in North America race around the Pack Expo International show floor to complete tasks at the booths of participating exhibitors. CareerLink @ Pack Expo is an opportunity for PMMI members and consumer packaged goods companies to meet with students and veterans pursuing careers in packaging and processing during one-on-one informational interviews to take place at the show. PMMI will also be offering popular training workshops in Chicago to coincide with Pack ExpoTheInternational.eventalso offers high quality connections through specialized networking events such as the Packaging & Processing Women’s Leadership Network Event, which tackles timely issues facing women in the industry. Pack gives Back is Pack Expo’s annual benefit concert and returns to Chicago in 2022. And immediately following Pack gives Back, the Emerging Leaders Network will host an evening event for young professionals at an exciting venue in downtown Chicago. Finally, The Technology Excellence Awards will recognize the most innovative technologies not yet shown at a previous Pack Expo. Attendees will be able to vote onsite, on the app, or online for their favorite finalists selected in specific market segments.
toSeptemberRegistrationvisit packexpointernational.com.fortheshowis$30until30th,afterwhichitincreases$130. 8 • 2022 FLUID POWER WORLD 43
FPW To learn more and to register,
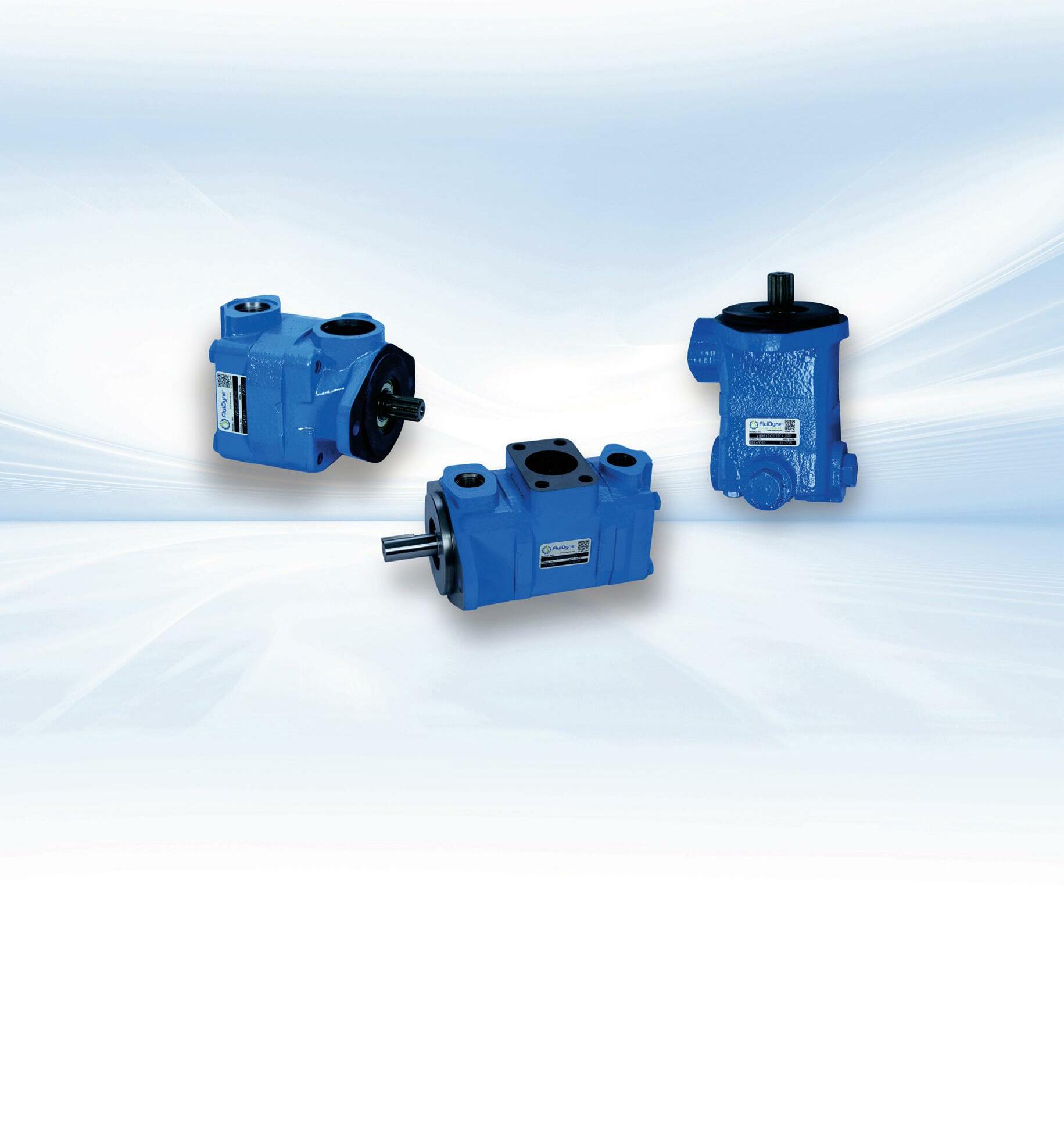






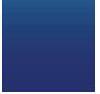













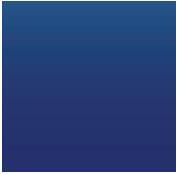
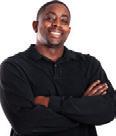
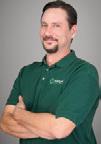
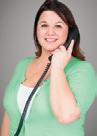
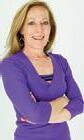









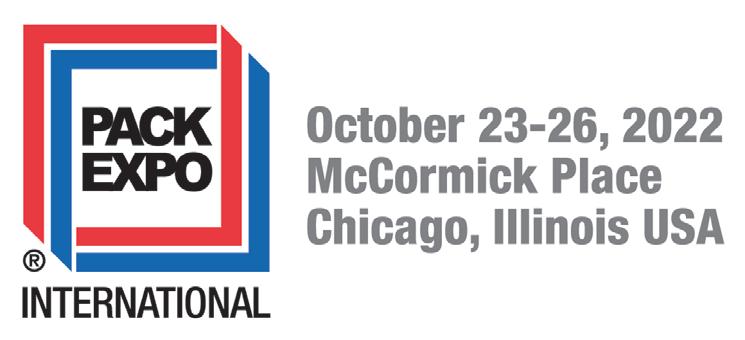
• Metal removal • Quality assurance, and • Tooling and workholding systems.
The IMTS 2022 Conference is composed of multiple sessions throughout the week. Topics include process innovation, plant operations, quality/ inspection, automation, improving productivity, improving part quality, and developing a competent workforce to improve the competitiveness of manufacturing in the United States.
AS RECENT MONTHS HAVE SHOWN, engineers are ready to get back to in-person meetings and conferences, from the Automate Show in Detroit to the Robotics Summit and Expo in Boston. And few are larger or more important to OEM design engineers than the biennial IMTS that’s held in Chicago’s vast McCormick Place complex. IMTS, or the International Manufacturing Technology Show, is held in even-numbered years, and the 2022 edition is scheduled for September 12-17. IMTS 2022 will be the 33rd edition of the show. The 2018 IMTS was impressive in scope — it hosted the highest number of exhibiting companies ever (2,563) and was the largest event as far as the number of registrations (129,415) as well as net square feet of exhibit space (1,424,232) at the McCormick Place complex.
According to The Association for Manufacturing Technology (AMT), which runs the tradeshow, IMTS attracts buyers and sellers from 117 countries. While the 2020 event was cancelled due to the Covid-19 pandemic, as so many other trade shows were, the 2022 edition is moving full-steam ahead. This Fall’s show will feature multiple pavilions to help guide attendees throughout the massive amount of floorspace. The pavilions are divided into:
• Machine components / cleaning / environmental
• Abrasive machining / sawing / finishing • Additive manufacturing • Controls and CAD-CAM • Fabricating and lasers
A busy conference schedule Education is always an important part of the IMTS show, and this year’s event will be no exception. A total of 12 different conferences will be co-located at the show, all within Chicago’s McCormick Place. “Content is key in the information era, and we have organized the widest array of conference topics ever at IMTS 2022 to help visitors move their people, business, and technology forward,” said Bonnie Gurney, VP –Strategic Partnerships for AMT. New events include the IMTS Women Make Manufacturing Move program to inspire women, the IMTS Investor Forum, and The Smarter Sourcing Symposium. After an impressive 2018 debut, the Job Shops Specialty Program returns this year with a focus on ready-toimplement digital technologies that will help job shops address their most pressing issues.
Additional partner conferences cover subjects such as additive manufacturing, 3D printing for job shops, lasers, parts cleaning, interoperabilityindustrialstandards, and technology“Conferencesleadership.atIMTS 2022 offer a deeper dive into the technologies exhibited on the show floor, the chance to network with subject matter experts and like-minded peers, and the opportunity for professional growth,” said Gurney. “Plan to take advantage of these learning opportunities for a few days, then add another day to your itinerary to walk the show floor. There is no more efficient way to gather more information in one location, plus
IMTS SHOW PREVIEW
BYCOMEBACKPAULJ.HENEY,VP,EDITORIALDIRECTOR
• Gear generation
44 FLUID POWER WORLD 8 • 2022 www.fluidpowerworld.com
IMTS IS READY FOR ITS CHICAGO
IMTS, OR THE INTERNATIONAL MANUFACTURING TECHNOLOGY SHOW, RETURNS TO CHICAGO SEPTEMBER 12-17.
IMTS Investor Forum: The IMTS Investor Forum connects visitors with advanced manufacturing experts who will demystify the estimated $65 billion manufacturing technology industry. Guided tours of the trade show floor afford an inside experience with the industry, firsthand from startups and industry insiders. The Smarter Sourcing Symposium at IMTS 2022: The inaugural Smarter Sourcing Symposium at IMTS 2022, presented by IMTS and The Onshoring Project, will deliver direct strategies for sounder and more financially beneficial North American part production.
Parts Cleaning Conference: Environmental limitations are becoming stricter, and manufacturers demand high-quality clean parts. The Parts Cleaning Conference will detail how to make it all happen while staying within compliance and on budget. Hannover Messe USA 2022 Conference: The 2022 Hannover Messe USA Conference will offer five topic tracks, including Motion & Drives, Cybersecurity, Industry 4.0, Automation, and Supply Chain. It will provide solutions to manufacturing concerns.
www.fluidpowerworld.com 8 • 2022 FLUID POWER WORLD 45 Exhibitors of Note Booth Number Absolute Machine Tools Inc. 338519 AirTAC USA Corporation 134882 Allegheny York 134892 Atlas Copco Compressors 121151 Balluff Inc. 134637 Brush Research Manufacturing Co. Inc. 237148 Camel Precision Co. Ltd. 237163 CAPLUGS 121368 Deublin Company 121003 Dura-Bar 432172 Dynatect Manufacturing Inc. 121012 Emerson 134113 Festo Didactic Inc. 215000 Grainger 432091 HBC-radiomatic Inc. 121465 Hunger DFE GmbH 236759 igus Inc. 134812 ITT Enidine 121045 Kaeser Compressors Inc. 121246 Nachi America Inc. 432024 Newall Electronics 135354 Quaker Houghton 431949 RÖHM Products of America 432346 Rosedale Products Inc. 121035 Rotary Precision Instruments Ltd. 135932 Schmalz Inc. 431154 SCHUNK 432010 Smalley 236300 SMC Corporation of America 215520, 236249 Sunnen Products Company 237330 it gives you a chance to rest your feet while stretching your mind.” IMTS 2022 Conference: With a slate of product experts selected entirely from IMTS exhibiting companies, the IMTS Conference will equip attendees with tangible solutions that they can put into practice immediately. IMTS Specialty Program: Job Shops Workshop Day 1: Designed exclusively for job shops stakeholders, this event features an industry roundtable and panel discussions with job shops implementing digital manufacturing technologies and other best practices that improve their efficiencies. This features a session from the Technology & Manufacturing Association.
IMTS Specialty Program: Job Shops Workshop Day 2 featuring Modern Machine Shop’s Top Shops: This half-day program offers visitors a look into this year’s annual Top Shops benchmarking survey. Attendees will learn from industry experts and current and past Top Shop award winners to find out what makes a shop rise to the top.
OPC Foundation Conference: The OPC UA Seminar is about industrial interoperability scaling from sensor to IT and Cloud and back. Learn about the one harmonized solution OPC UA FX for process and factory automation. Learn why MQTT-only is not enough and why the biggest six big IT companies support OPC UA over MQTT. Technology Leadership Summit: Powered by ASME, this conference focuses on digital transformation. Leaders will discuss big data, digital twin, robotics, additive manufacturing, and tour the show floor with an industry expert. FPW To register for this year’s IMTS, please visit www.imts.com/show/reg.cfm.
IMTS Specialty Program: Women Make Manufacturing Move: The IMTS Women Make Manufacturing Move program will inspire women in the manufacturing technology community through curated sessions, networking, and business. This includes a Monday night reception, Wednesday luncheon, and a Friday Take 5.
Additive Manufacturing Conference: Focused exclusively on additive technologies for industrial part production, the AM Conference will take a practical, applications-based look at the machines, materials, and methodologies being used to create end-use tools and components.
3D Printing Workshop for Job Shops: 3D printing’s biggest potential lies in the hands of manufacturers — those that can see the intersections between CNC machining and additive manufacturing and innovate ways to evolve part production. This event will help job shops learn how 3D printing can help them with prototyping, tooling, production, and more.
Industrial Laser Conference: This conference, presented by the Laser Institute of America, focuses on laser processing for manufacturing, including marking, cutting, welding, heat treating, remote welding, cleaning, additive manufacturing, and more.

46 FLUID POWER WORLD 8 • 2022 www.fluidpowerworld.com BAUMA SHOW PREVIEW construction and mining machinery industry prepared for bauma 2022 , set for october 24 - 30 . mobile machinery makers head to munich

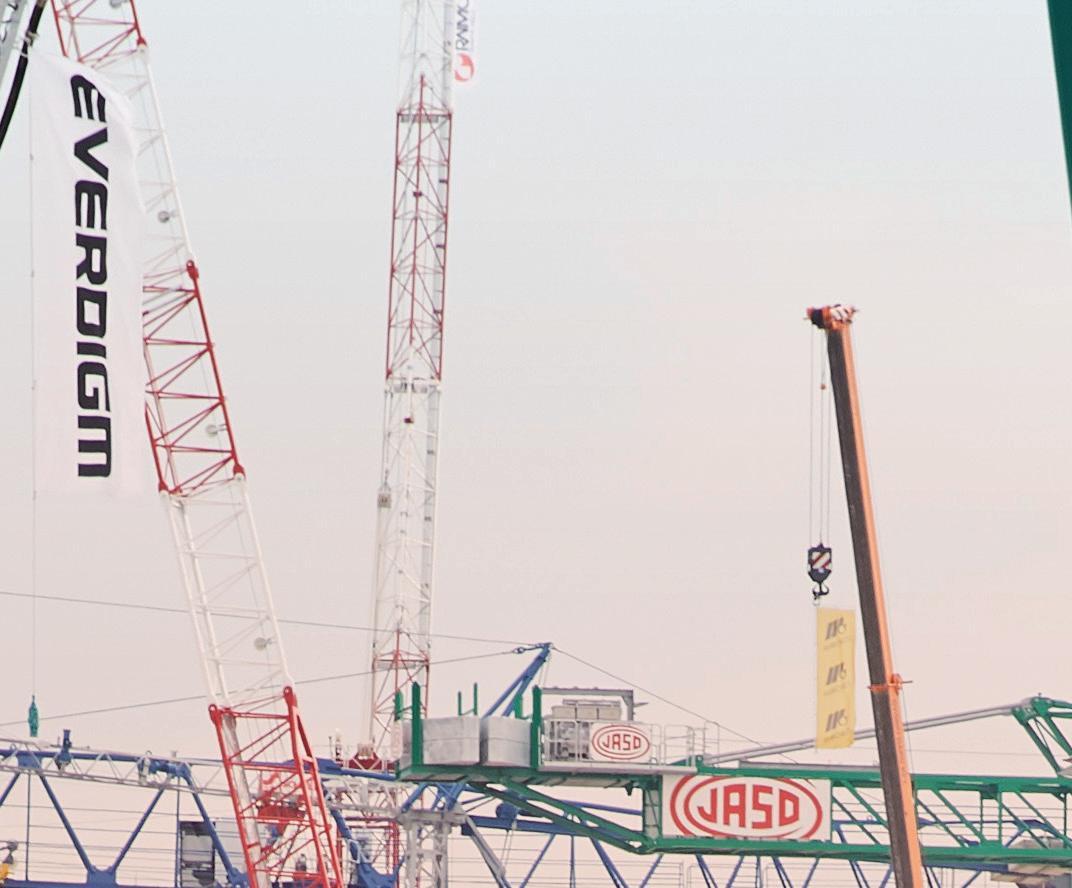

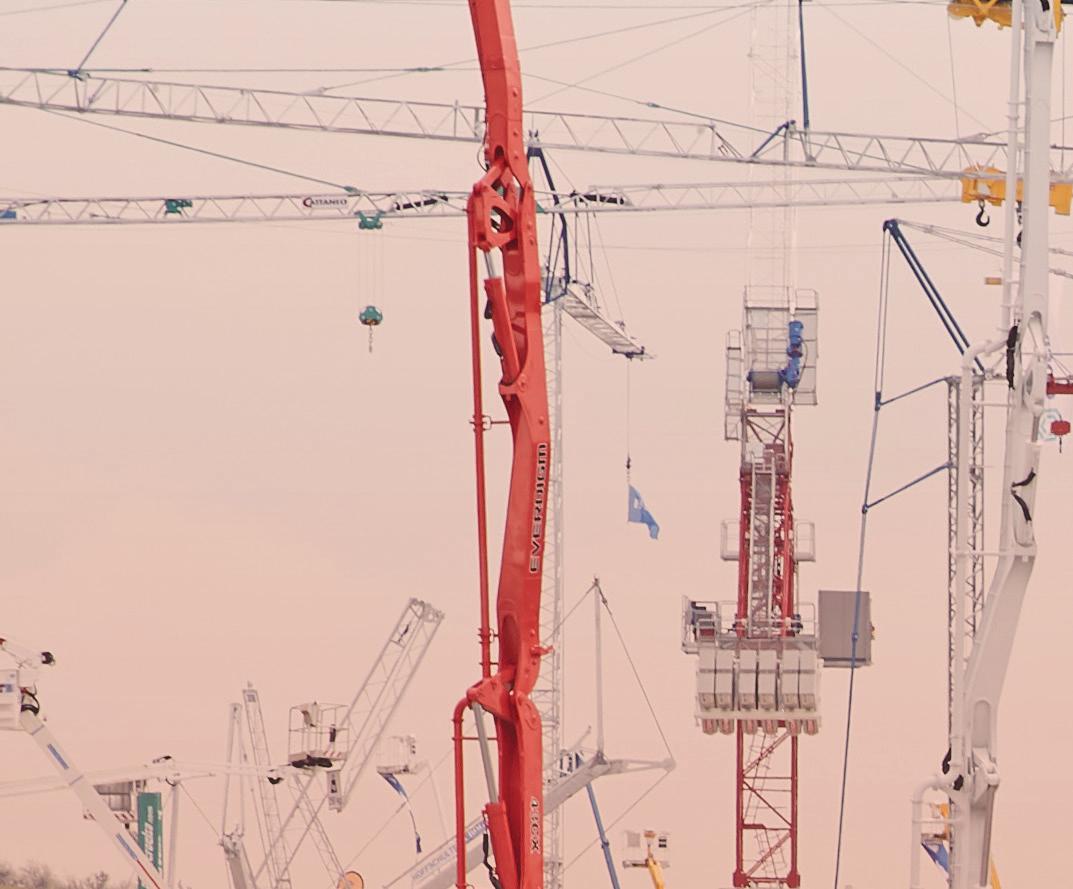
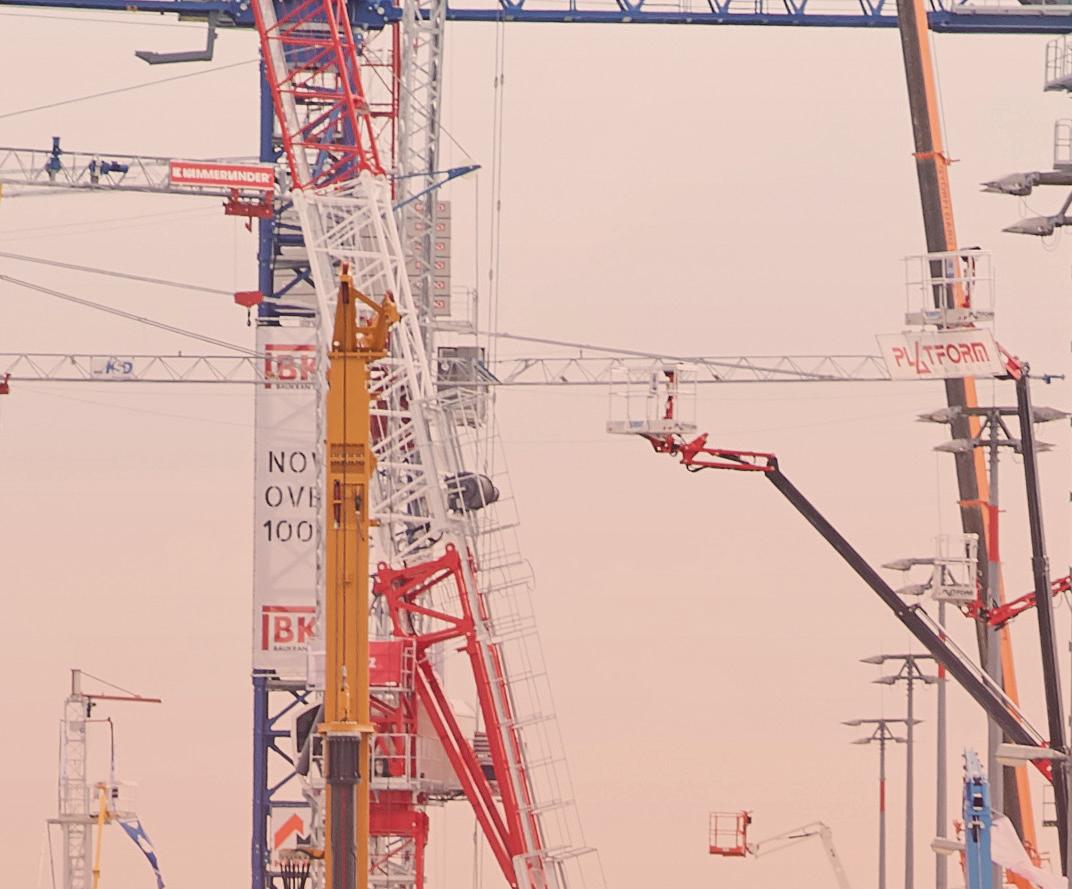

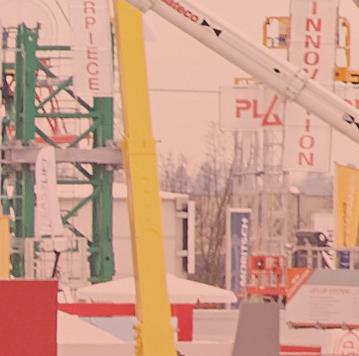


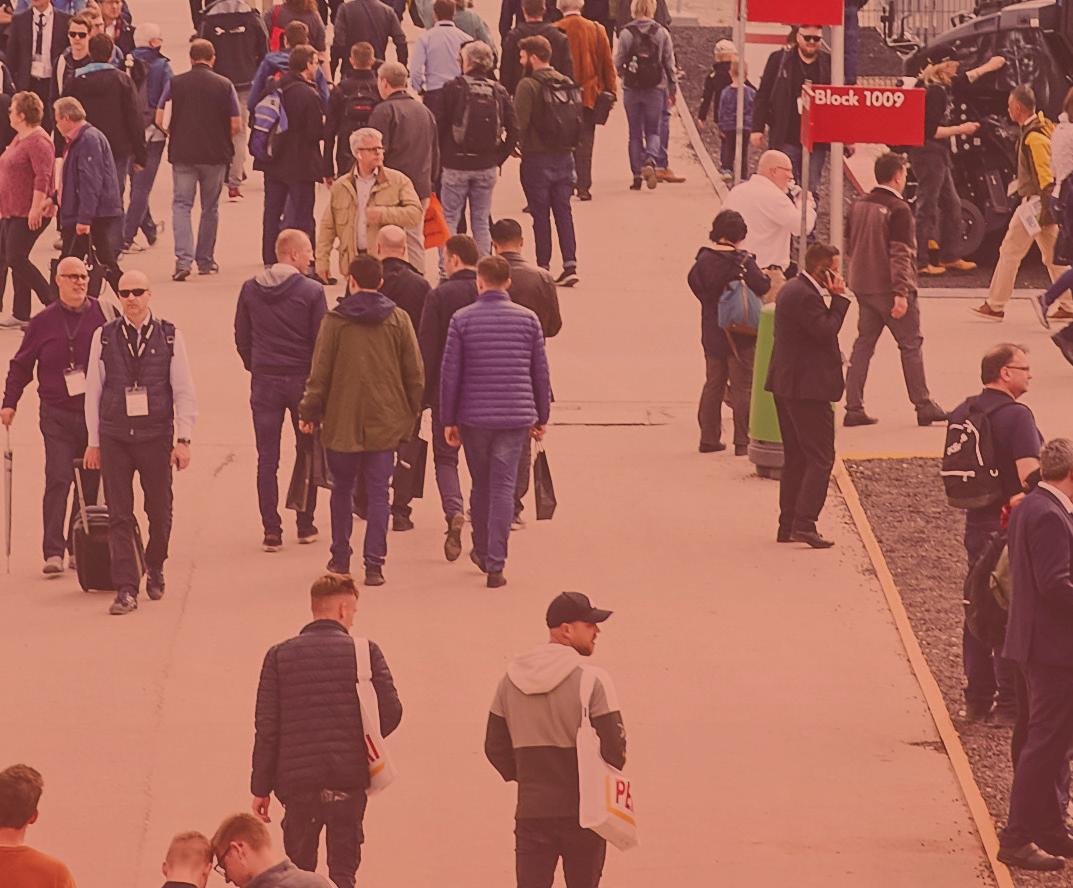
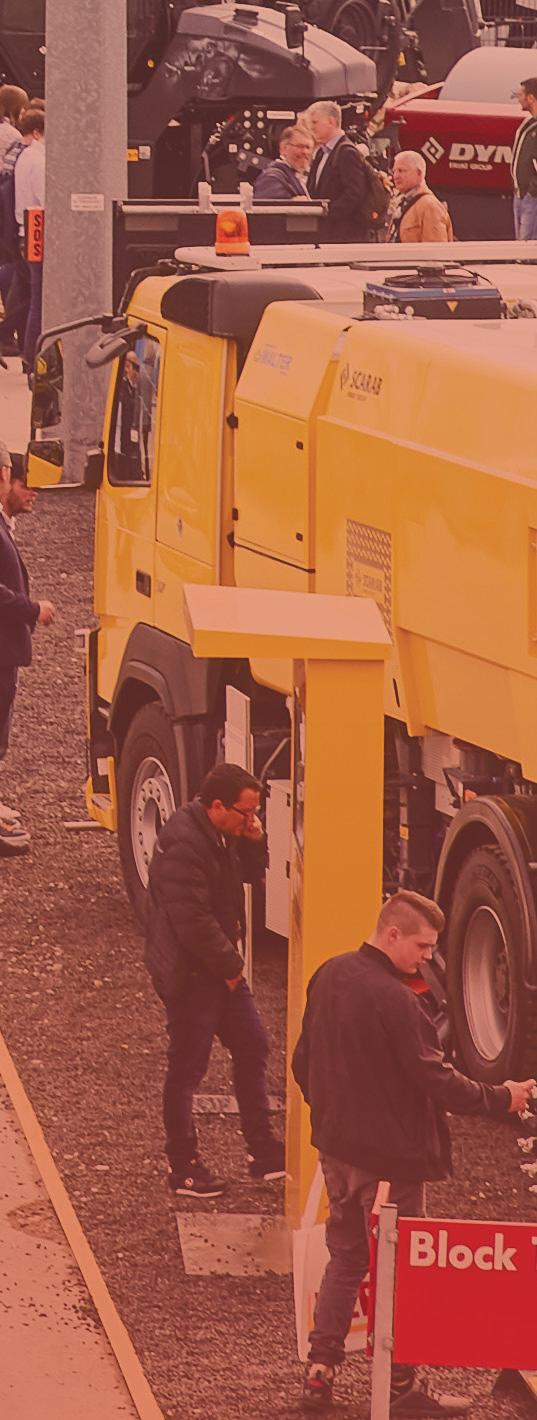
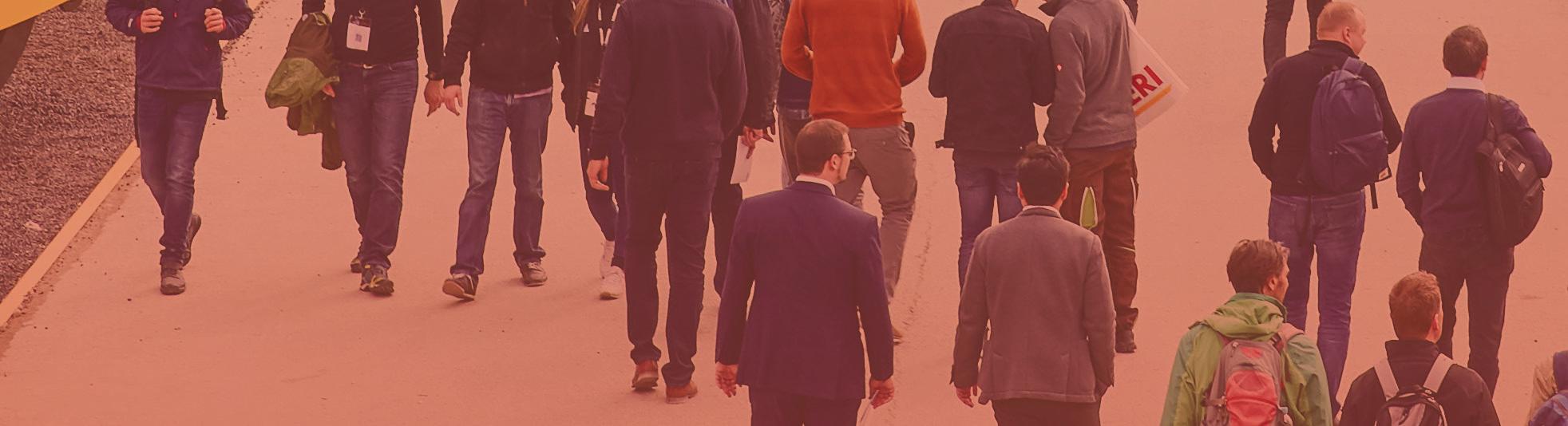

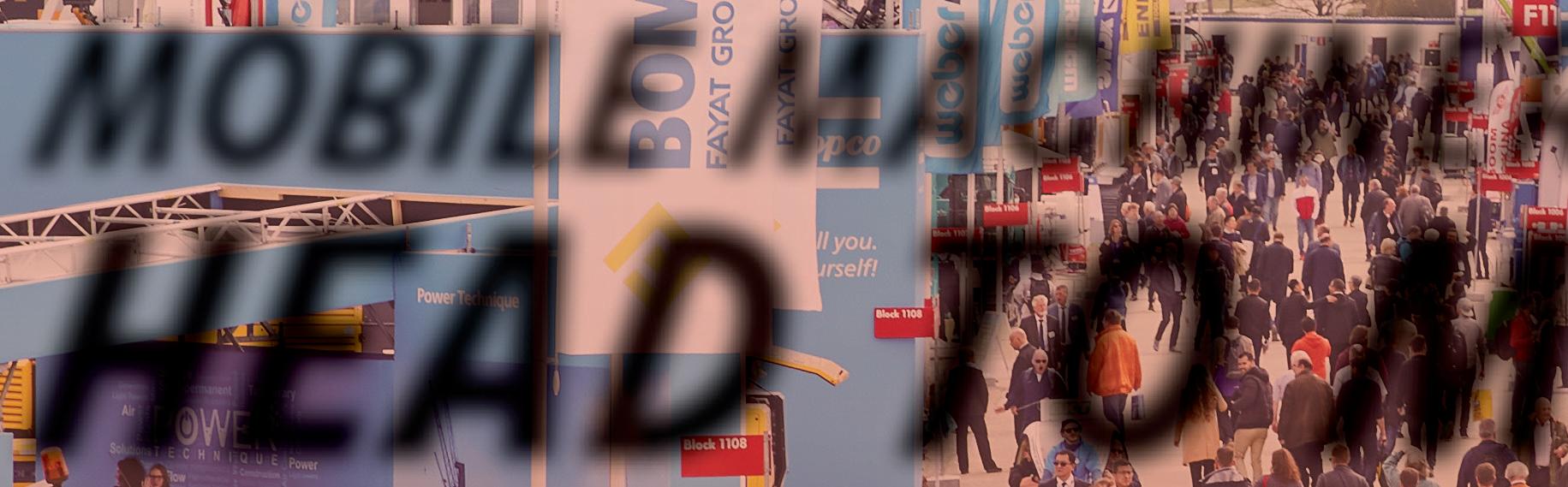

Innovation hub
AKON HIDROLIK VALF SAN. VE TIC A.S.
ALFAGOMMA Germany GmbH
Aliauto Italia S.r.l. A4.342 ARGO-HYTOS GmbH A3.403 Argus Fluidtechnik GmbH A3.215 asa technology Produktions- und Vertriebs GmbH A3.533 Autokühler GmbH & Co.KG A4.448 Bondioli & Pavesi GmbH Deutschland A3.349 Bosch Rexroth AG A3.327 Bosch Rexroth AG A5.326 Bucher Hydraulics GmbH A3.103 Carlisle Brake & Friction A5.531 Casappa S.p.A. A3.239 CEJN-Product GmbH A3.313/J Cogito SP. ZO.O. A5.331 COMER INDUSTRIES S.p.A. A3.225 Continental AG C5.403 Danfoss Power Solutions ApS A3.125 Dunlop Hiflex A Division of ALFAGOMMA GERMANY GmbH A3.215 Eberspächer GmbH A4.351 EBI Motion Controls s.r.l. A3.128 Eckerle Technologies GmbH A3.144 Elsässer Filtertechnik GmbH A4.302 EUROMAT SRL A3.145 Euroswitch SPA A2.542 FLODRAULIC GmbH A3.128 FUCHS LUBRICANTS GERMANY GmbH A5.137 Gürmaksan Hidrolik Devre Elemanlari San. Ve Tic. Ltd. Sti. A3.212 GUVEN ENDUSTRI MAKINA IMALAT A.S. A2.425 HAWE Hydraulik SE A3.348 HBE GmbH Hydraulik-Komponenten A5.100 Hengst SE A4.103 Hidromec srl A4.104 HKS Dreh - Antriebe GmbH A6.239 HKS Dreh - Antriebe GmbH FN.815/1 Hoses Technology Spa A5.A5.139A
bauma is preparing to open its doors in munich october 24 30 as the world’s leading trade fair for construction machinery, building material machines, mining machines, construction vehicles and construction equipment is expecting a very high level of participation. The event, which was postponed from earlier this year, will host more than 3,500 exhibitors and nearly 630,000 visitors. Event organizers are excited about the event. According to Klaus Dittrich, Chairman and CEO of Messe München, “In the personal conversations we have with exhibitors and visitors, we hear one thing over and over again: They are really looking forward to having face-to-face discussions and, of course, to experiencing the special atmosphere that only bauma can create.” Mining sector to be widely represented again
www.fluidpowerworld.com 8 • 2022 FLUID POWER WORLD 47
In addition to mining, for years now, the trade fair has been viewed as the world’s unmistakable innovation hub thanks to the tremendous number of innovations that exhibitors present there. This special position will be underscored this year by the innovation hall LAB0, an area that will include such special areas as the bauma Forum, virtual reality, MIC 4.0, startups and a science hub. Think Big, a program that promotes talented young people, will also be included as a key issue for the industry. Electricification will be a hot topic at the event, with several key products being introduced in this area. A unique electrohydraulic innovation comes from Japanese manufacturer Tadano, with its E-Pack, an electrohydraulic system with an integrated 32 kW electric motor providing low-noise and emission-free crane operation. This solution was presented at the last bauma in 2019. At that time, it was only available for a single crane vehicle. Tadano now will show that, in the meantime, five of its AC cranes can be ordered with the E-Pack or existing cranes retrofitted with it. As one of the largest shows in the world for construction and mining machinery, bauma will host a great number of fluid power exhibitors. More than 125 hydraulics manufacturers will be at the event — a list of fluid power exhibitors is included here. Five key focus areas will be the highlight of the event, with the following: Construction methods and materials of tomorrow Around the world, the construction machinery industry is tackling the challenges of today. The primary goal is to lower the amount of carbon dioxide released during the production of cement. Demolition materials should be better processed and reused in the future. New materials are also appearing on the scene. A6.512 A2.645 A3.450 A3.215
The mining industry, an area where bauma is the leader in Europe, will be well represented once again. Exhibitors will include such industry heavyweights as BHS Sonthofen, Herrenknecht, Komatsu, Liebherr, Schulte Strathaus and Zeppelin Baumaschinen. Other companies attending the fair will be the Matrix Design Group from the United States, Resemin from Peru, Roco9 from Great Britain, Tesab Engineering from Great Britain and Weber Mining & Tunneling from France. Another returning company will be Minearc Systems from Australia, a key market for the mining industry.
Company Hall A.M.A. S.p.A.
ACTIA

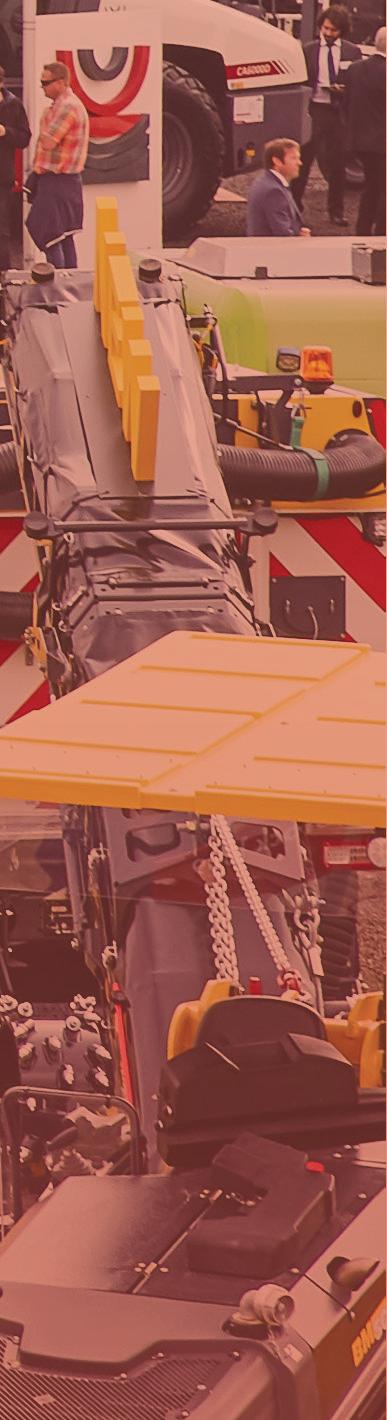
JUNG Hebe- und Transporttechnik GmbH C4.324 Kawasaki Precision Machinery UK Ltd. A4.536 KAZELOGULLARI SAN. VE TIC. LTD. STI. A4.544 KLEIN GmbH FS.1006/1 KYASHIF EOOD A3.511 Linde Hydraulics GmbH & Co. KG A3.149
Oleotec
Olsbergs Hydraulics AB A3.126 OMFB
MP FILTRI SPA
Parmafluid S.r.l.
ILGOM TUBI Srl A4.100 Infraserv Vakuumservice GmbH A4.547 Italgroup S.r.l. A4.114
MCS Mobile Control Systems SA A2.540 Meta Hydraulic s.r.l.
Hydraforce Hydraulics Ltd. A4.450
HYDRO LEDUC GmbH A4.101 HYDROMA, spol. s r.o. C1.415-6
HYDRONIT SRL A3.526 Ikron S.r.l. A3.239
LMC MAKINA SAN.TIC.A.S. LTD. STI. A6.401 Lösing, Willibrord, Filtertechnik e. K. A4.443 Magnet-Schultz GmbH & Co.KG A2.204
Neumeister Hydraulik GmbH
PERFORATOR GmbH
Motrac Hydraulik GmbH
Hydraulic Components A4.202 OMSI Trasmissioni
Parcaci Construction Machinery Spare Parts A6.335 Parker Hannifin GmbH
Miba Frictec GmbH
48 FLUID POWER WORLD 8 • 2022 www.fluidpowerworld.com BAUMA SHOW PREVIEW Company Hall PIRTEK Deutschland GmbH A6.337 PMP Pro-Mec S.p.A. A4.150 PONAR Wadowice S.A. A3.527 Reco Italia SpA A5.115 Rima S.p.a. A4.218 Rotary Power Vertriebsgesellschaft mbH A4.107 RT-Filtertechnik GmbH A3.451 Schmitter Hydraulik GmbH A5.105 Shinn Fu Europe B.V. A1.219 SIKO GmbH A2.415 Slanzi Oleodinamica Srl A4.128 SLP Swedish Lorry Parts AB A5.215 SPIR STAR AG A1.144 SRP SADID OTOMOTIV ANONIM SIRKETI A5.426 STUCCHI S.p.A. A4.213 SUCO Robert Scheuffele GmbH & Co.KG A5.212 Sunfab Hydraulics AB A3.515 Sure Grip Controls Inc. C4.342 Tecnord S.r.l. A3.239 Thomas Magnete GmbH A4.319 TongMyung Eng. Europe GmbH A3.146 Transfer Oil S.p.A. A4.208 Transfluid S.p.A. A3.307 Tries GmbH & Co. KG Hydraulik-Elemente A4.538 USCO ITR A5.249 VTS Track Solutions A5.218 Wandfluh AG A3.350 Wandfluh GmbH A3.350 Weber-Hydraulik GmbH A3.312 Welte Cardan-Service GmbH A3.513 Wikov MGI a.s. A4.543 WingFan Ltd. & Co.KG A4.525 Yee Young Industrial Co., Ltd. A1.530 ZEC SPA A5.109 3D printing, modular construction and new materials
OP Srl
HYDRA SRL FN.523/1
The construction machinery industry and the mining industry are developing innovative construction methods and material solutions. These will be highlighted at the event and in preshow talks. The way to autonomous machines The development of autonomous machinery for construction sites and mining operations is taking huge leaps forward, even if there is still a long way to go until full automation is reached. Automating and digitizing construction processes and machinery will reduce greenhouse-gas emissions and ensure productivity in this age of skilledworkerHumanshortages.machine interfaces (HMI), assistant and safety systems, construction site robots and the downsizing trend: There are many milestones that still must be reached on the way to developing autonomous construction machinery and autonomous underground mining equipment.Theexhibitors and speakers at bauma 2022 will explore these issues during bauma TALK 2 and during the trade fair itself. Mining – sustainable, efficient, reliable How can mining profit from its digitalization and automation edge in the future? The mining industry already has a standard that is being used in the manufacturing process: open platform communication – unified architecture, or OPC UA. At the same time, environmental compatibility and recultivation are creating new challenges for the industry. As the leading platform for the mining industry, bauma will focus intensely on the questions of the future for the mining industry. Live demonstrations will be complemented by the presentation of new research findings. bauma TALK 4 and the focus day Company Hall HYDAC International GmbH A3.449
GmbH &
Montanhydraulik GmbH
MANN+HUMMEL GmbH A4.248 Marzocchi Pompe S.p.A. A4.414 Maschinenfabrik Wagner Co.KG A5.351 A3.251 A3.418 A4.415 A3.313/E A4.338 A4.512 S.L. A4.507 A3.136 S.r.l. A5.100 S.p.A. S.p.A. A3.514 A4.308 A4.215 A3.529 C3.247
Nexo Fittings,
OILCOMP srl
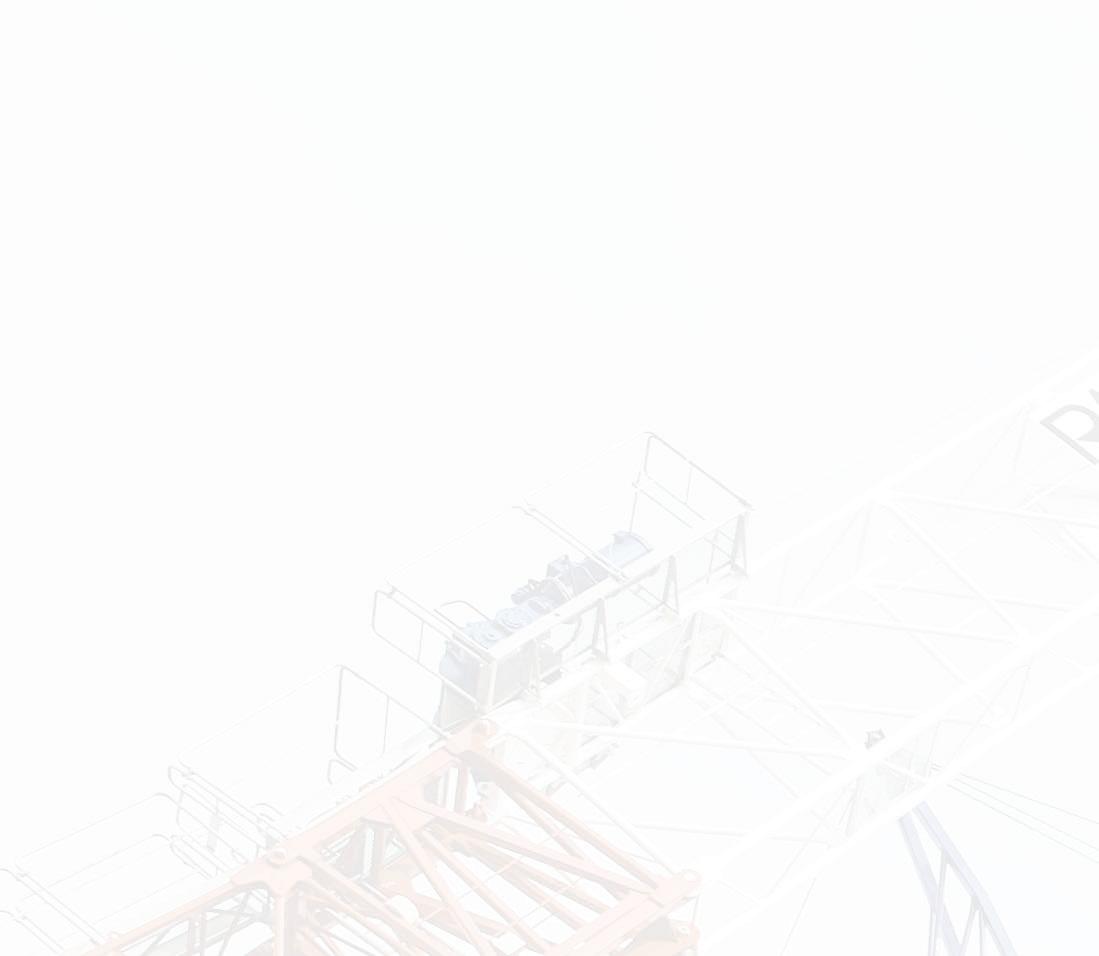
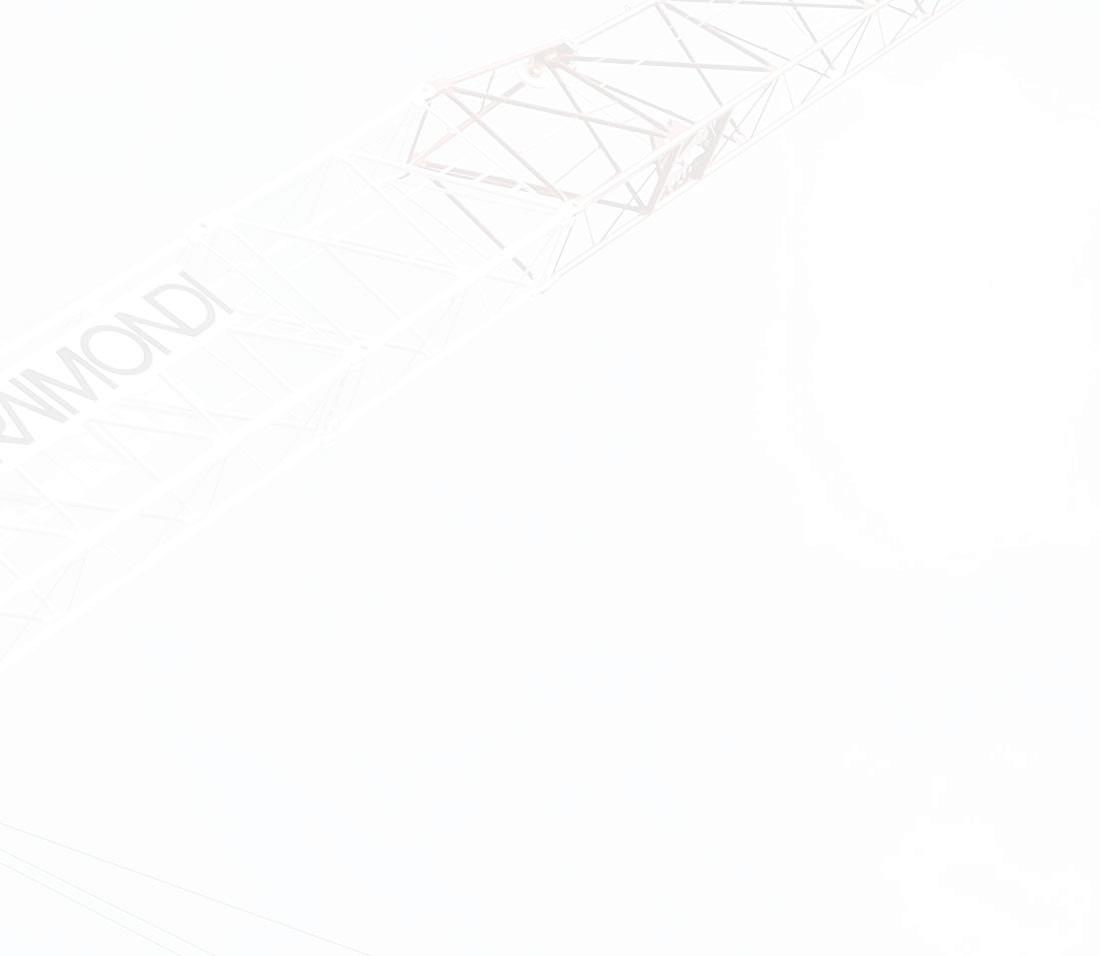

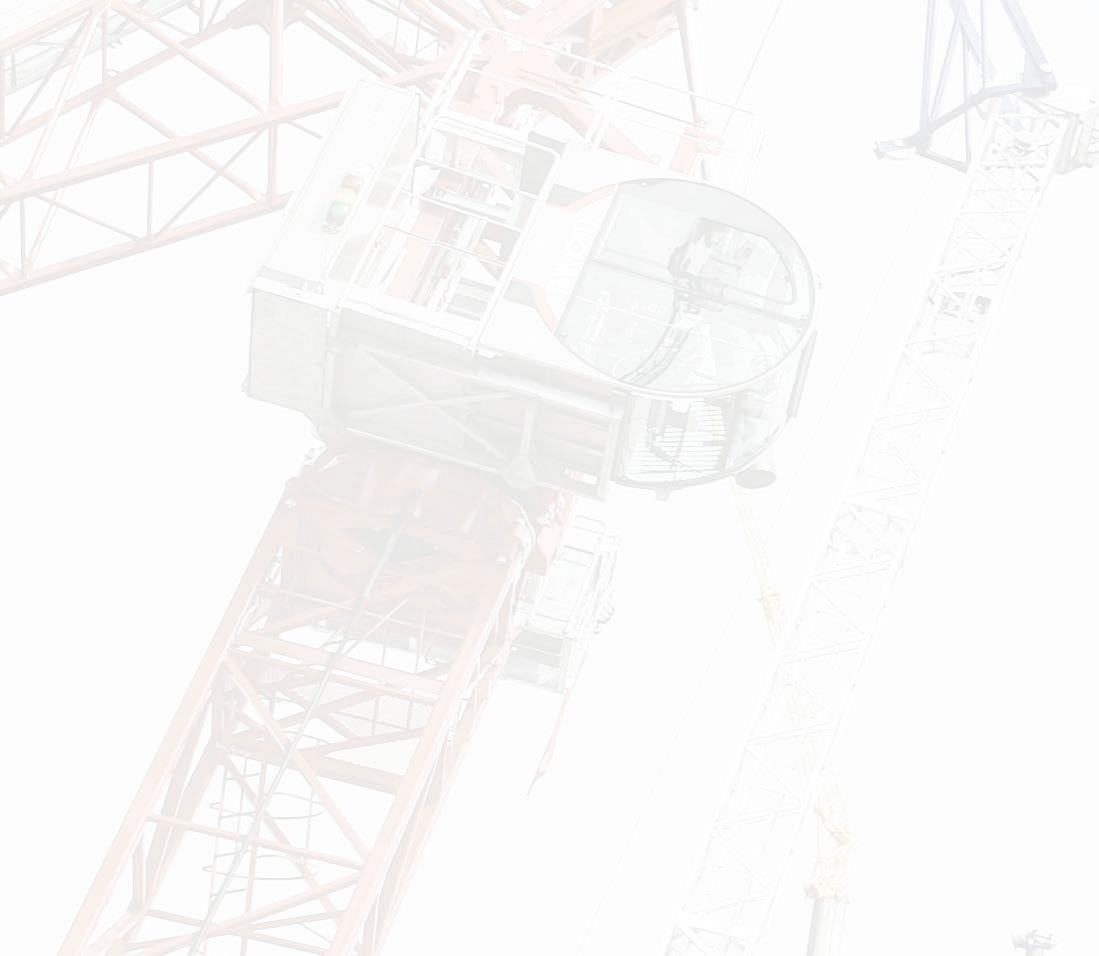
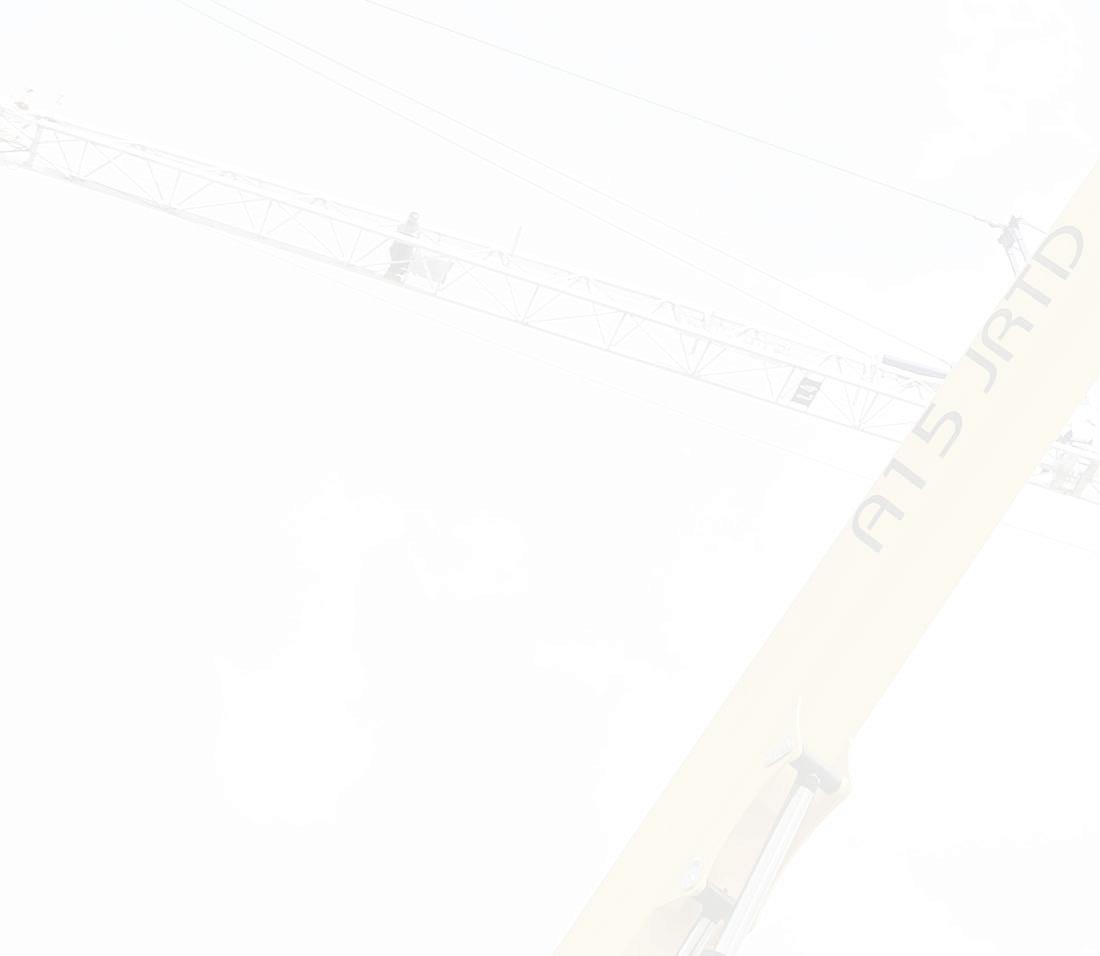
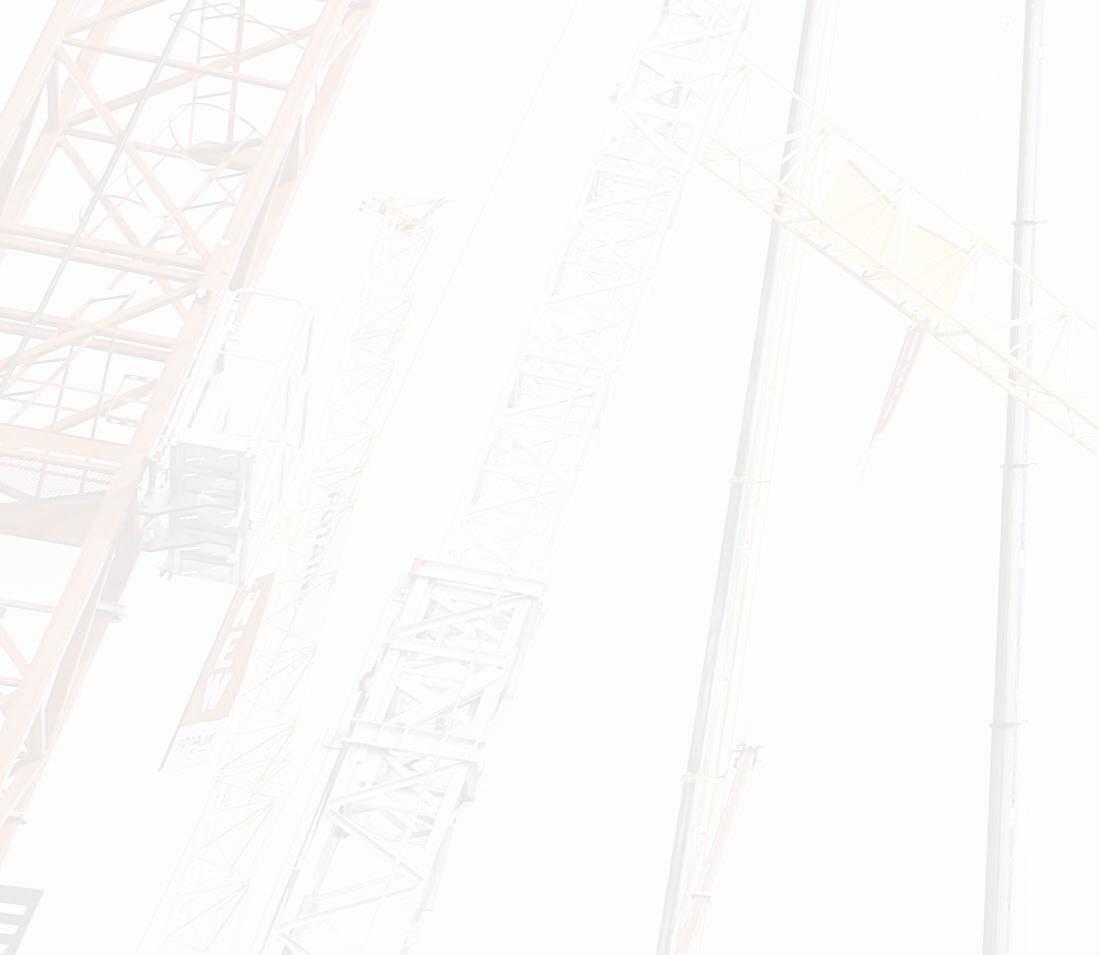

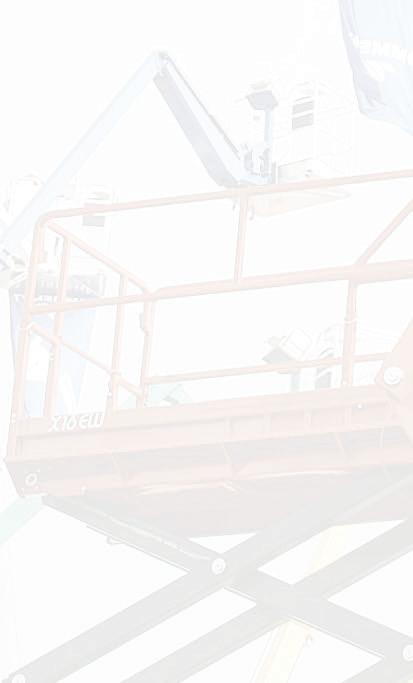


Driving and working with hybrid and allelectric vehicles and construction machinery are two of the high-potential ways to cut emissions in the construction business. This is also the case with the development of CO2reduced construction materials.
Speakers and discussion groups will delve into the vision of “zero emissions” during bauma, in the bauma FORUM and during bauma TALK 5, and examine the road that leads to this destination. FPW For more information, visit bauma.de.
The key pre-condition for these gains is a manufacturer-independent communication standard for communicatimachine-to-machineons(M2M).Datamanagement,BIM,virtual and augmented reality and digital twins are increasingly playing a crucial role in the successful digital work on construction and mining sites. At bauma, you will be able to see real-life examples, attend a thematic day at the bauma FORUM and view the presentation of the latest developments discussed previously at bauma TALK 3. MiC 4.0 - The Machines in Construction 4.0 working group is celebrating its premiere at bauma in the Innovation Hall bauma LAB0. Eleven member companies will present the results of their MIC 4.0 BUS project - a milestone in the direction of ‘attachment as IoT device’.
www.fluidpowerworld.com 8 • 2022 FLUID POWER WORLD 49
HBC radio remote controls. Your #1 choice for safe and efficient machine operation. Quality in Control.
HBC-radiomatic, Inc. 1017 Petersburg Road • Hebron, KY 41048 • USA Phone: +1 800 410 4562 • sales@hbc-usa.com www.hbc-usa.com in the bauma FORUM will investigate solutions that various actors are developing under the umbrella term “Mining 4.0” to meet this broad array of challenges. Digital construction site Digital planning and construction processes promise to create increased environmental protection, safety and, not least, cost effectiveness to go along with efficiency.
The way to zero emission One goal for everyone – reducing greenhousegas emissions in the construction and construction machinery industry to zero.
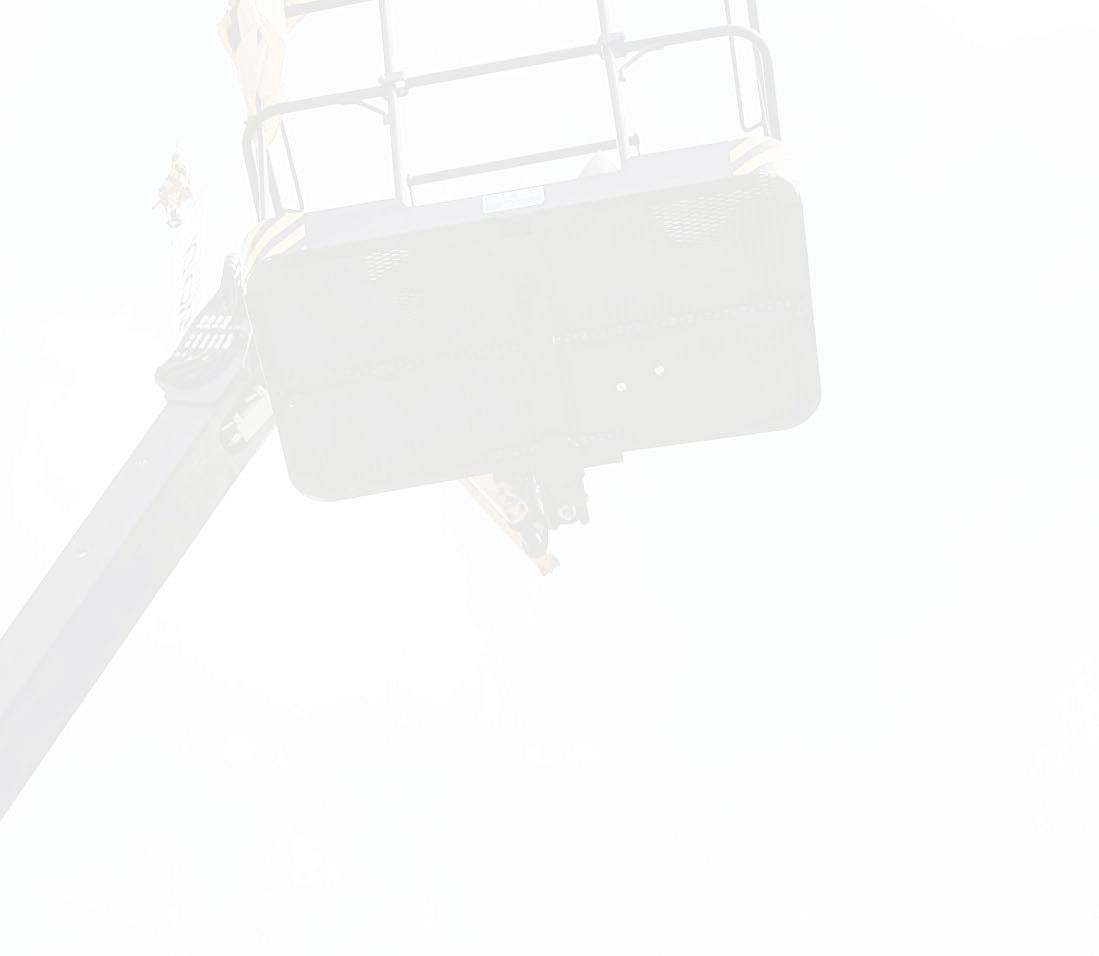

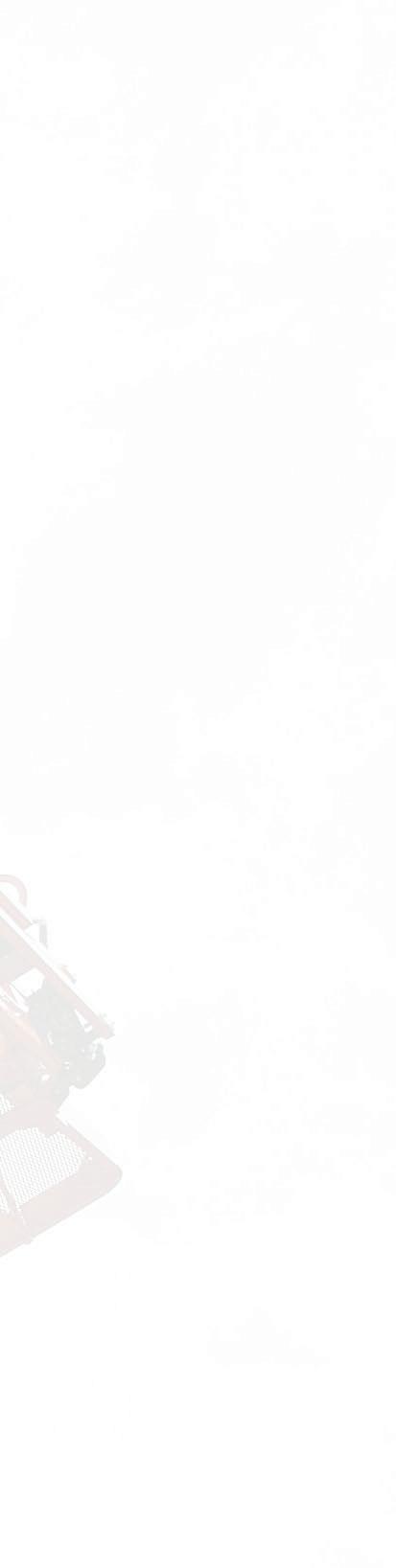

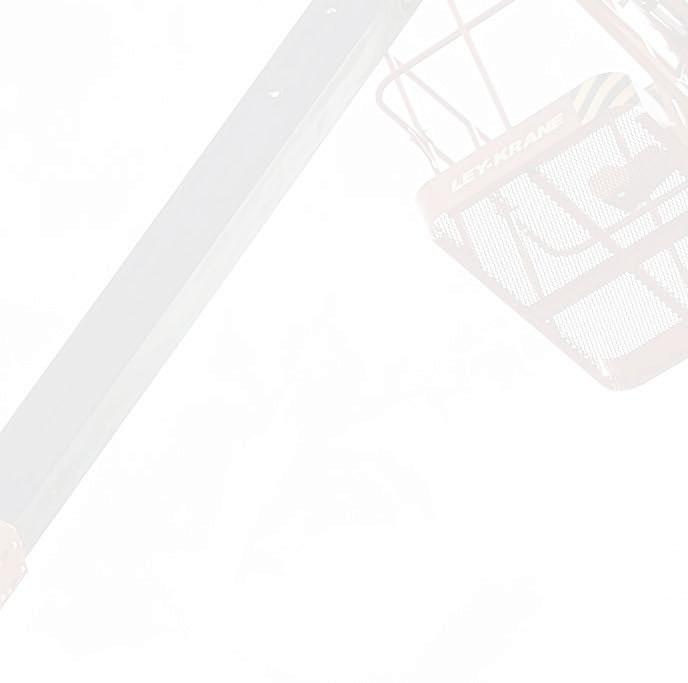
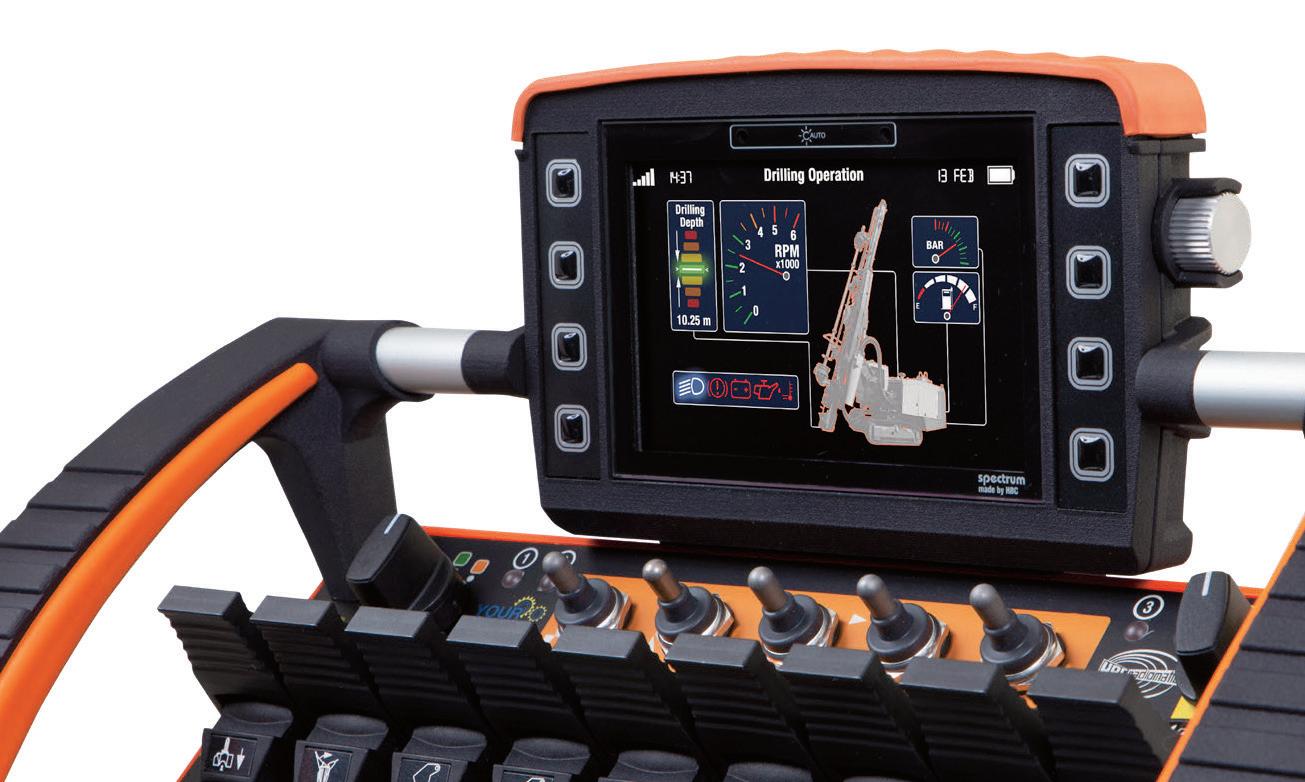
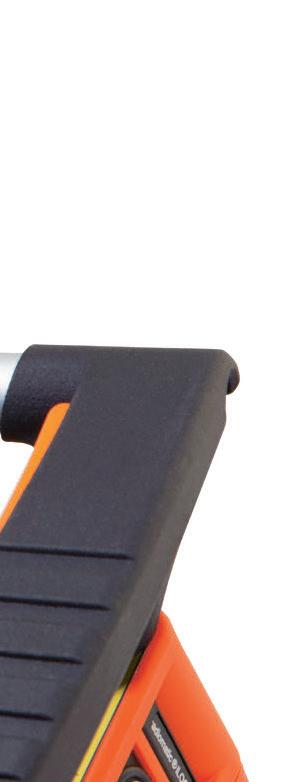
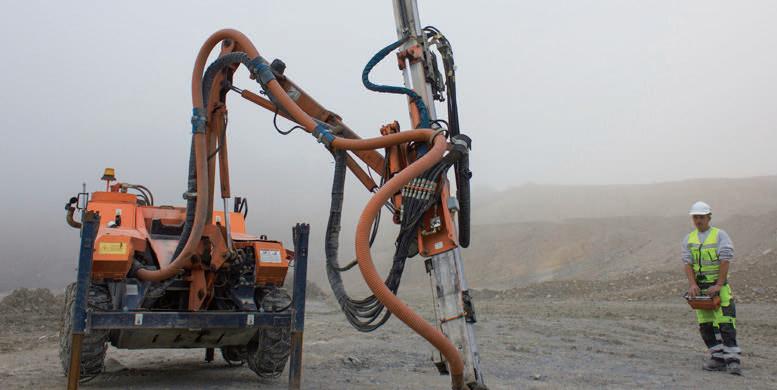
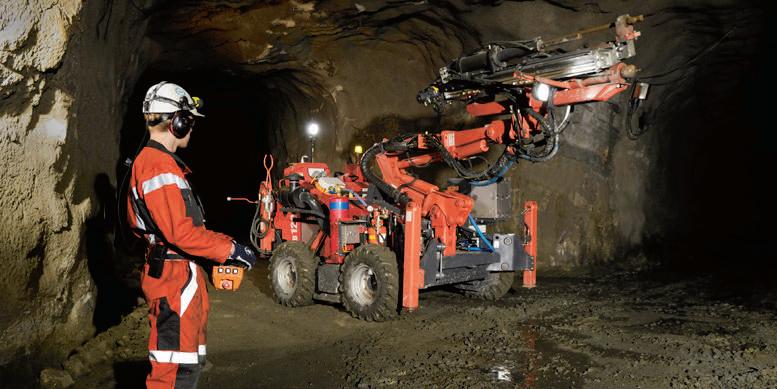
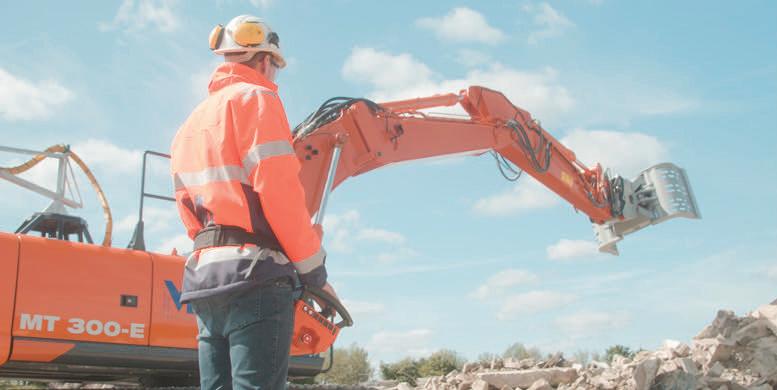
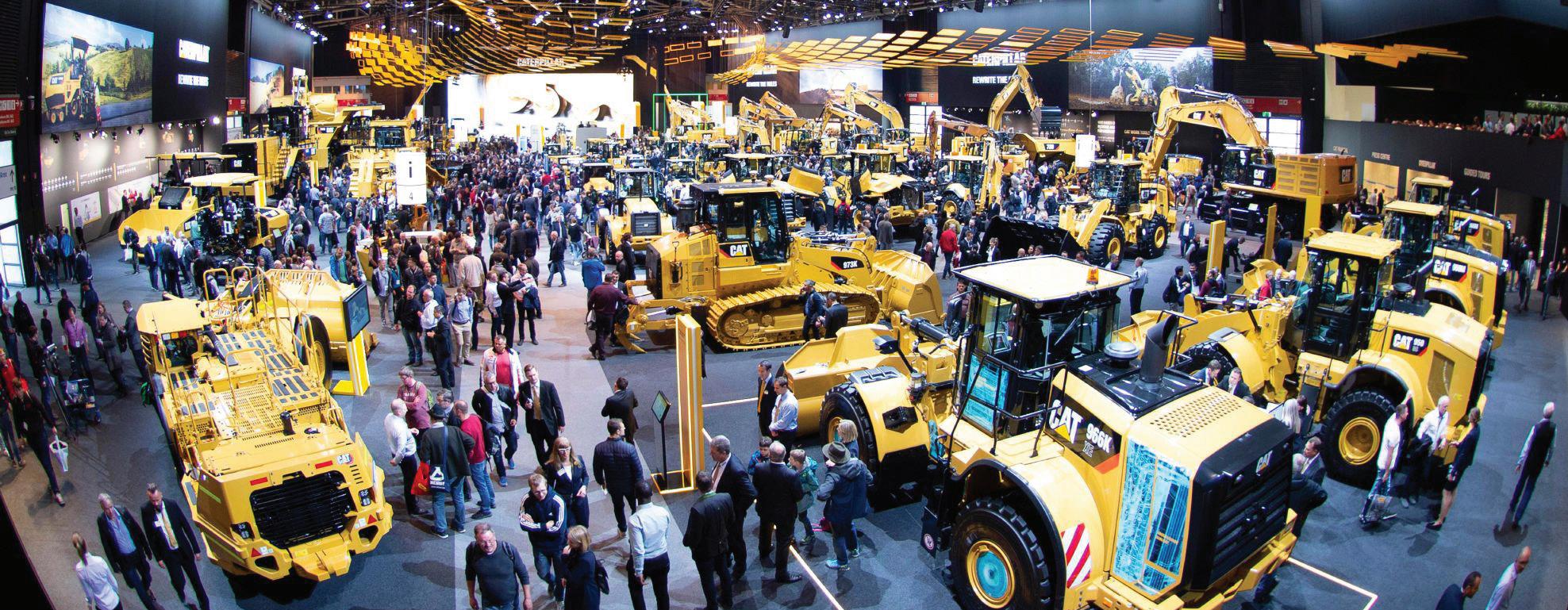
FLUIDINTERNATIONALPOWEREXPO MARCH 14-18, 2023 LAS VEGAS, NV, USA The International Fluid Power Exposition (IFPE) is the place where engineers meet to: “ There’s no other show in the world I think that brings the OEM machine manufacturers and the suppliers as close together as this show. It’s a good place to meet and learn about what’s going on. In the Americas, in the Western Hemisphere, this is the show for fluid power.” KEN ROSENBECKER SALES MANAGER NORTH AMERICA | WIPRO INFRASTRUCTURE ENGINEERING IFPE only happens once every three years! REGISTRATION OPENS EARLY AUGUST See why IFPE is the can’t-miss fluid power event of 2023! Learn more at IFPE.com Discover solutions current suppliers can offer to your unique challenges. Find new partners among suppliers pushing the envelope on what fluid power can do. CONNECT WITH TOP MANUFACTURERSCO-LOCATED WITH CONEXPO-CON/AGG (two shows, one price) Including Bosch Rexroth , Danfoss Power Solutions , Parker Hannifin , Poclain , IFM Efector , Hawe Hydraulik , Husco , and 375+ more! Join your peers from these OEMs: ∙ Caterpillar Inc ∙ Volvo EquipmentConstruction ∙ Liebherr ∙ CASE EquipmentConstruction ∙ Komatsu ∙ John Deere Construction ∙ Doosan Bobcat ∙ KOBELCO Construction Machinery USA ∙ LBX Company Spark new ideas with in-depth technical conversations with other engineers. The #1 Trade Show & Conference for Fluid Power, Power Transmission, and Motion Control
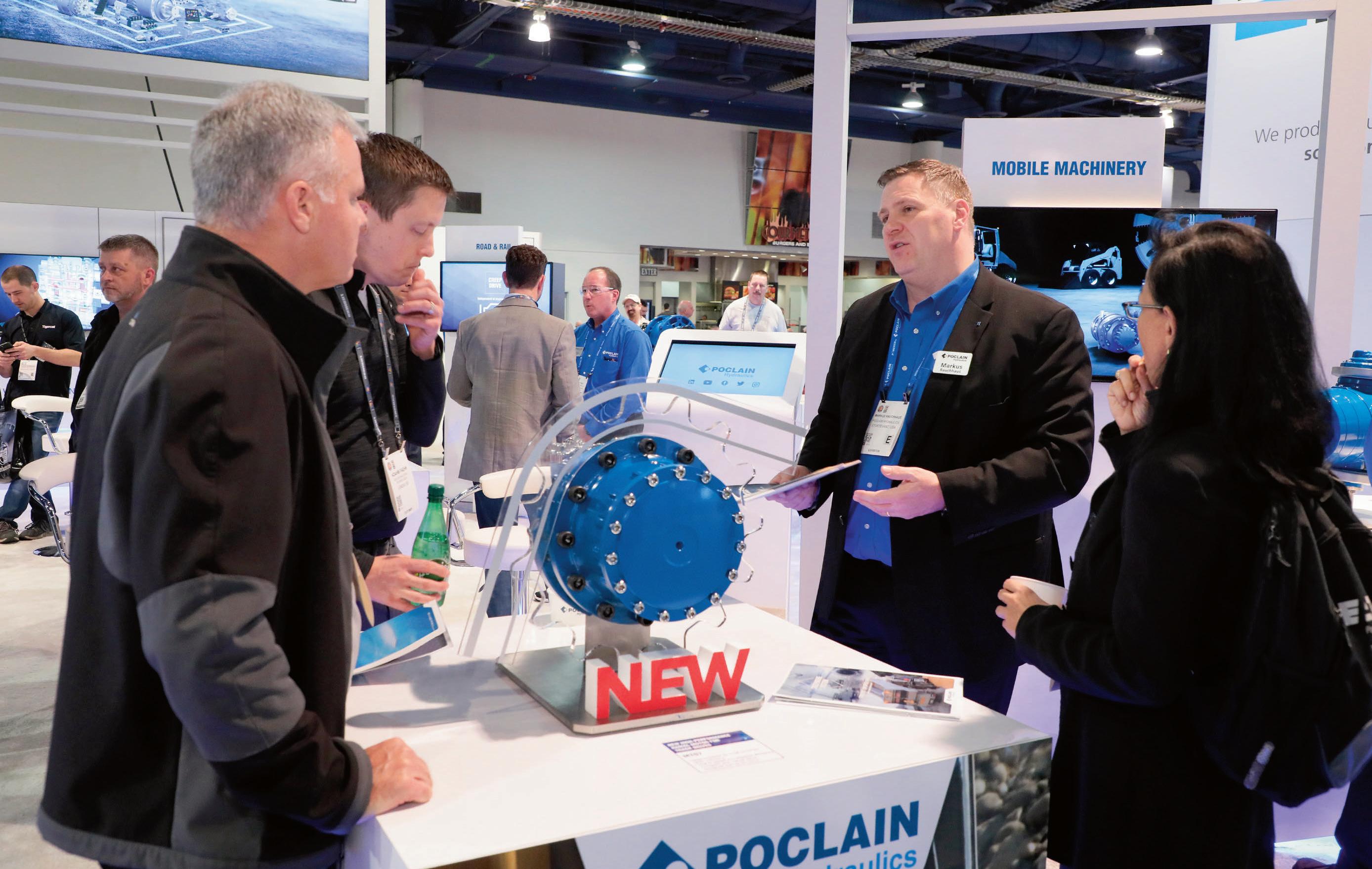
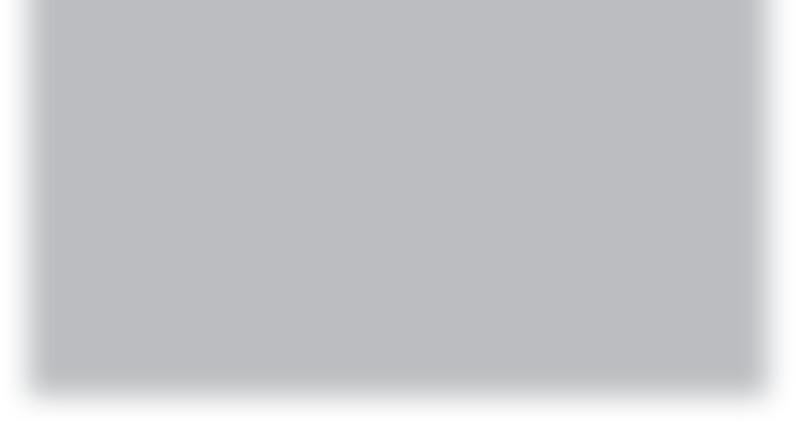
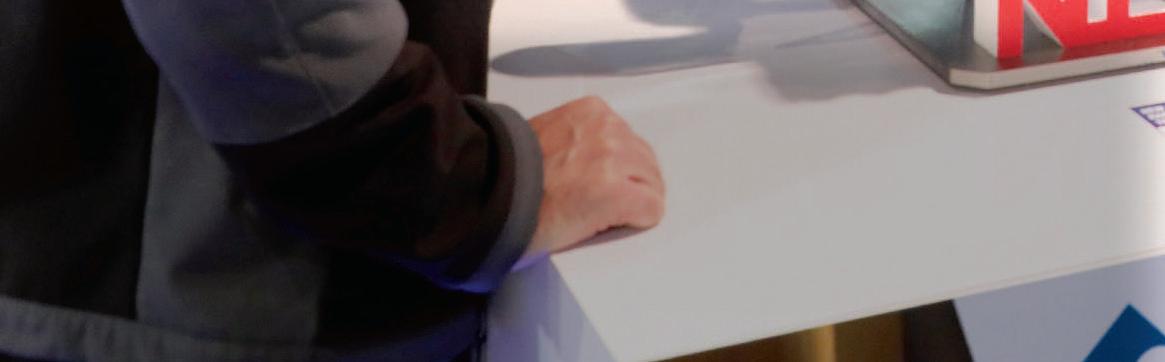
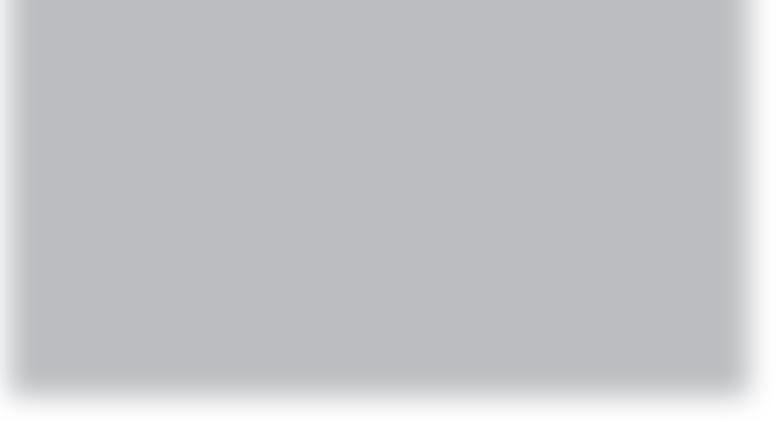
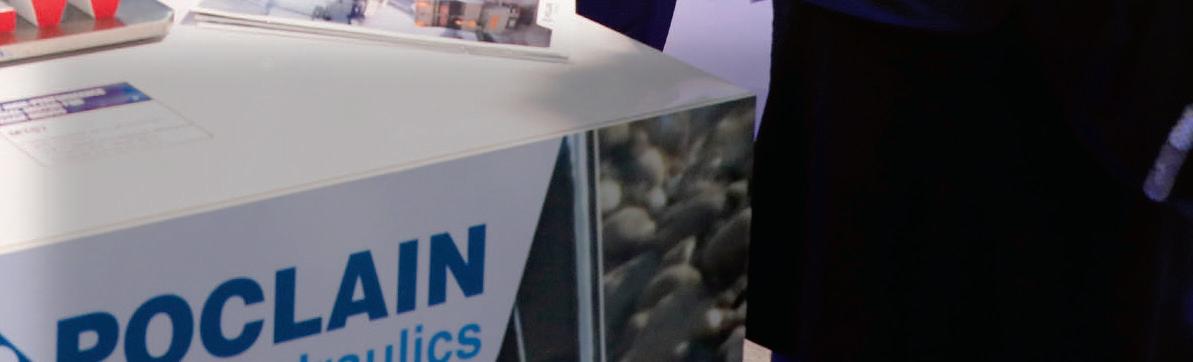


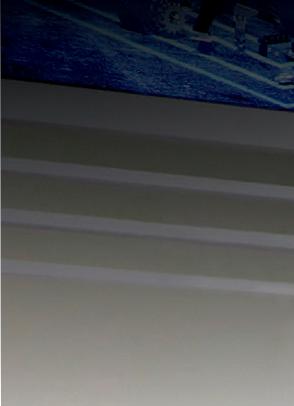
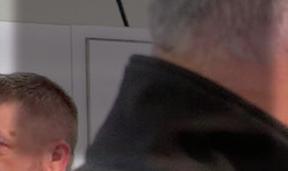
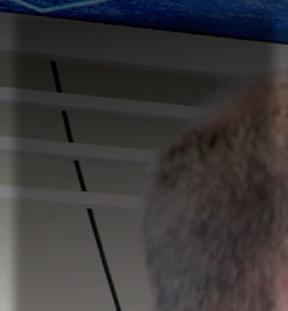
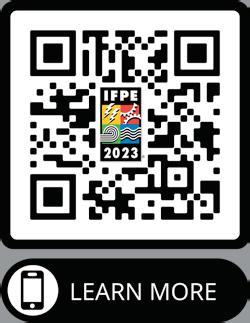
The S1 has been designed for high-volume manufacturing, which allows Ashcroft to offer a high-quality transducer at a low cost with quick lead times to meet OEM needs. This transducer features all stainless-steel thin film pressure CVDbased sensor technology for exceptional cycle life and repeatability. It also offers Ashcroft ’s TruAccuracy performance, which ensures rated accuracy out of the box so it’s ready for installation with no additional calibration adjustments required. Other features include outstanding humidity resistance, IP65 and/or IP67 levels of ingress protection (depending on electrical connection used) and the ability to operate in temperatures from –40° to 257° F (–40° to 125° C).
The new Surseat P51B flare lapping tool features improved usability and additional collets for metric sizes. The new shape and size of the tool make it easier to work in tight spaces and the lock-spring system secures the tube seamlessly in the tool’s cavity. Another addition to the P51B is the easy-to-use clip mechanism for the interchangeable 37° and 45° lap heads. The Surseat P51B removes irregularities in flared tubing, leaving a suitable sealing surface. A precision 37° or 45° lap head coated with diamond dust literally polishes steel, stainless steel and copper nickel tubing to perfection.
www.fluidpowerworld.com 8 • 2022 FLUID POWER WORLD 51 PRODUCT WORLD OEM pressure transducer
The S1 pressure transducer is specially made for mobile hydraulics, performance racing, agriculture and refrigeration applications, and is thus a reliable solution for harsh environments.
Surseat P51B flare lapping tool
Pneumatic clamps
The pneumatic clamps product family has now been reworked — primarily to increase its lifespan and reliability. The most significant improvement concerns the pneumatic cylinder, which now operates with a magnetic piston and has T-slots on the housing. Thanks to this slot, it is now much easier to attach sensors, while the magnetic piston permits more precise querying of the current position by the new, modern sensor GN 3380, which entirely replaces the previous sensors. Other sensors can also be precisely installed in the slot. The pneumatic clamps of the GN 860 series now have hardened, ground bearing bushings and tempered bearing pins for significantly reduced wear. No meaningful alterations were observed in testing for over 250,000 cycles. Structural reinforcement of the sheet steel housing reduces wear-inducing vibrations during operation, which makes a difference even under lower loads. And, finally, the new one-way restrictor in the cylinder enables smoother travel to extend the lifespan of the piston. The new pneumatic clamps are available in versions for horizontal (GN 860) and vertical (GN 862) installation. With GN 862.1, Winco also has a version that additionally permits manual operation.

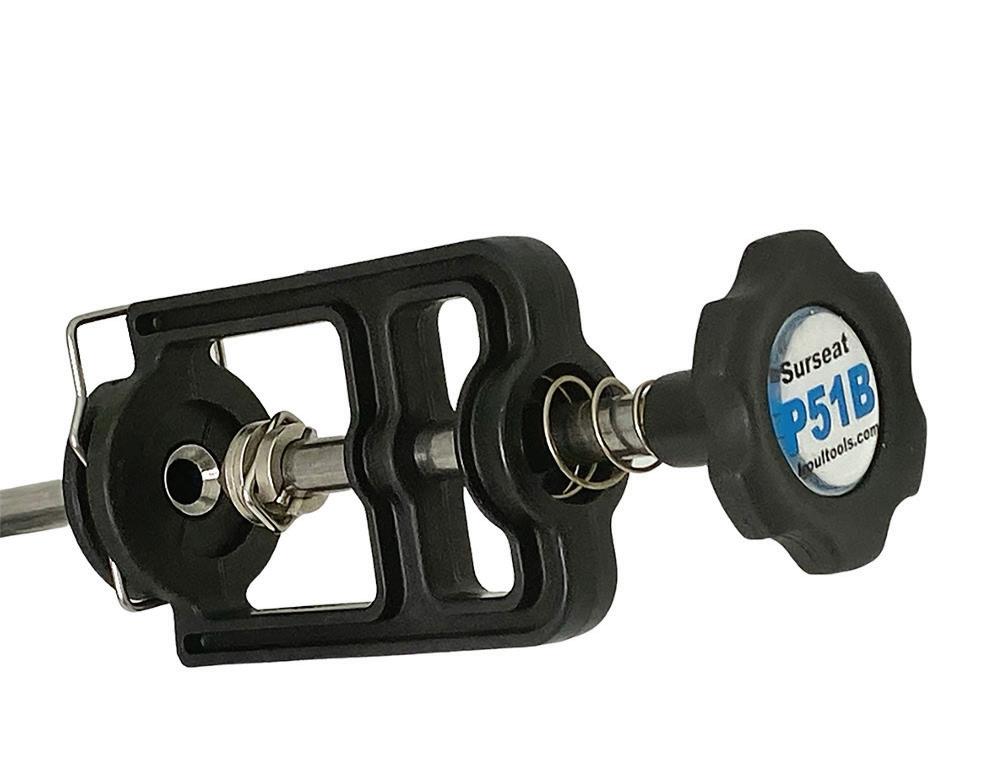

The SDBT-MSX is the first programmable proximity switch with an automatic switching point setting. With an initial detection range of 20 mm, the SDBTMSX is easy and reliable to install and commission, especially in applications where mounting is difficult. The switch is suitable for all standard applications, including factory automation and the electronics industry/small parts handling.
proximityProgrammableswitch
Only two steps are required for installing an SDBTMSX. The user simply fits the switch in the approximate end stop position within the 20 mm detection range (which is marked on the sensor) and connects the cable to the controller (PLC). No power supply is needed during installation. During first operation, the proximity switch detects the end position of the piston stroke and automatically learns and remembers the switching point. This is an industry first for a solid-state positioning switch. Alternatively, the switching point of the SDBTMSX can be taught manually using the capacitive control button. This button also allows the user to select PNP, NPN/ NO, or NC, and the switching window can be set from 2 … 15 mm. This flexibility can also reduce the variety of sensor types needed to be kept in inventory.
PRODUCT WORLD 52 FLUID POWER WORLD
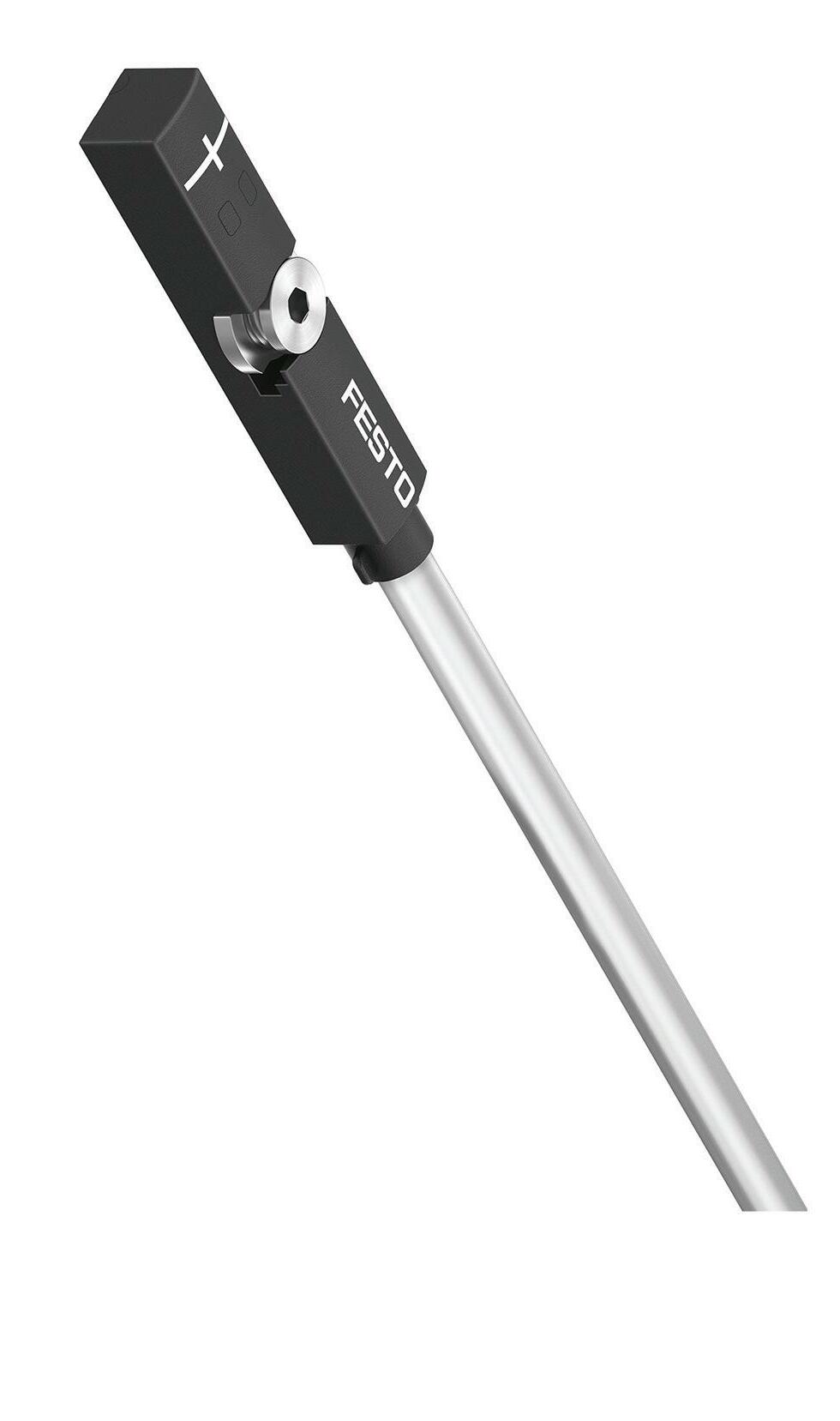

Schroeder Industries strives to keep hydraulic systems running at optimum performance. With the BestFit element series, the replacement elements are engineered and tested to the highest quality standards. With over 40,000 crosses currently offered online, Schroeder continues to expand the BestFit element series to meet customer’s needs. New Schroeder BestFit element series replace Competitor P’s 15CN, 40CN, and 80CN medium pressure coreless filter elements. The new series will replace the Ecoglass III series with a stronger and better performing coreless element. With high-performing Excellement Z-Media utilizing epoxy wire mesh for support structure, a stronger media pack is ensured for not only greater dirt holding capacity, but beta efficiency and stability as well compared to the plastic mesh support of the Ecoglass III series. element. dirt holding capacity, but beta efficiency and
www.fluidpowerworld.com 8 • 2022 FLUID POWER WORLD 53 Simplified hose configuration, less hose and adapters combine to reduce repairs and downtime, cutting the overall cost of hydraulics. www.SuperSwivels.com1-763-784-5531 No Kinks No Hose Twisting Full Flow Quality Products Made In The U.S.A. Patent No. 5547233 Fax: Email:1-763-784-7423sales@superswivels.com AvailableInBSPP InlineLiveHydraulicSwivels&90° Heavy Duty Ball Bearing Design • Also In 304 & 440 Stainless Steel • Rated To 10,000 P.S.I. • Heat Treated • Custom Design & Sizes Available • Rebuildable Ball Bearing Design • Full Flow —Low Pressure Drop • Superior Quality Alloy Steel • Side Load Resistant Sw i tc h Y o u r S w i v ®le S w i t c h Y o u r S w i v ®le CytroMotion self-contained actuator Bosch Rexroth has expanded its range of standardized self-contained actuators by adding the CytroMotion system solution. With the help of the new compact actuator, linear movements involving forces of up to 110 kN can be achieved in a range of machines and systems in smaller spaces, more efficiently and more sustainably. These benefits can be seen over the entire life cycle. Thanks to fully electric control, CytroMotion also makes engineering and commissioning easier. The efficient power-on-demand drive and the maintenance-free, hermetically sealed design help to save CO2 and minimize operating costs.
Expansion of filter element crossovers
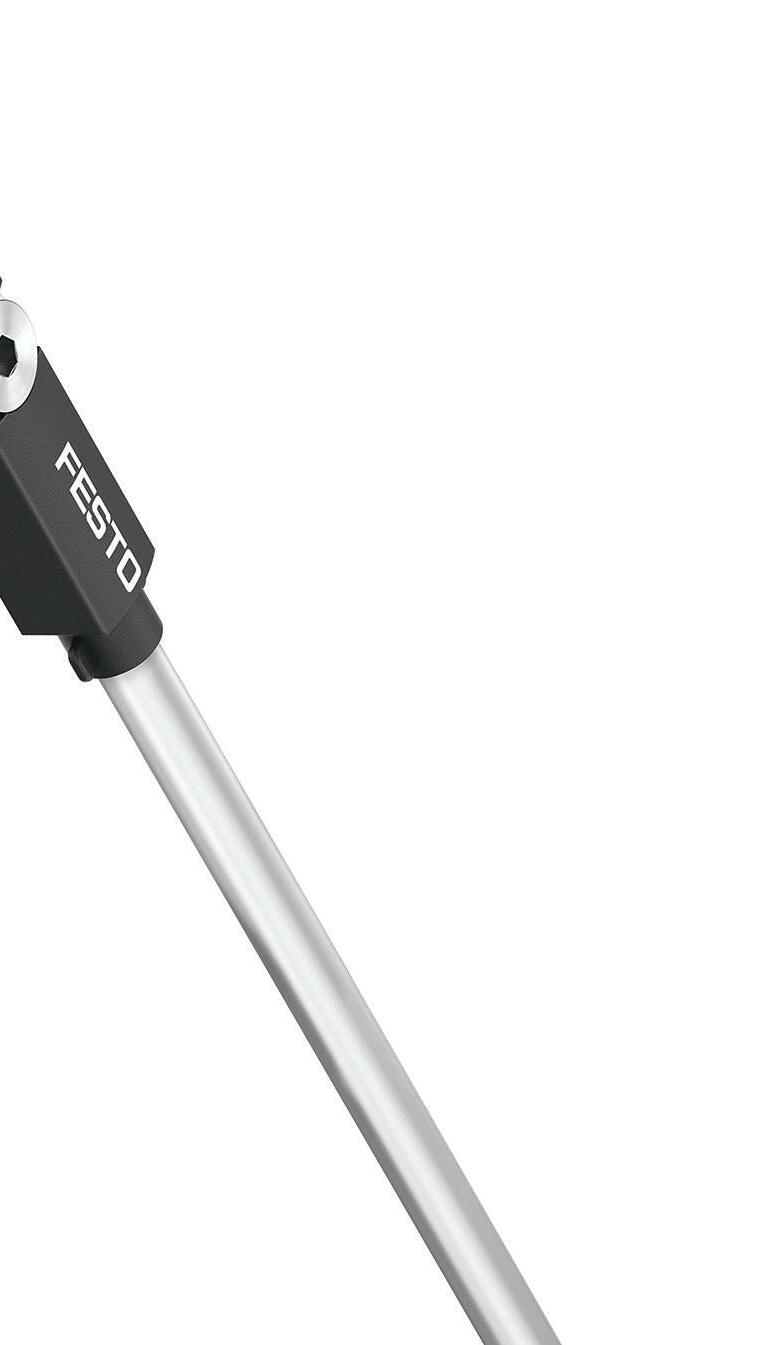
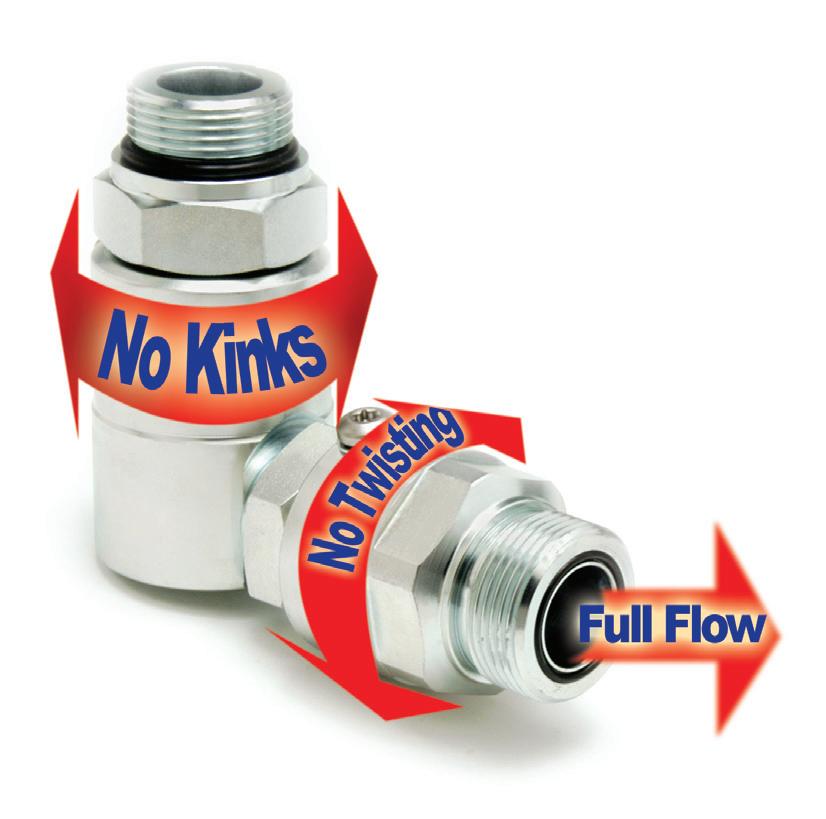
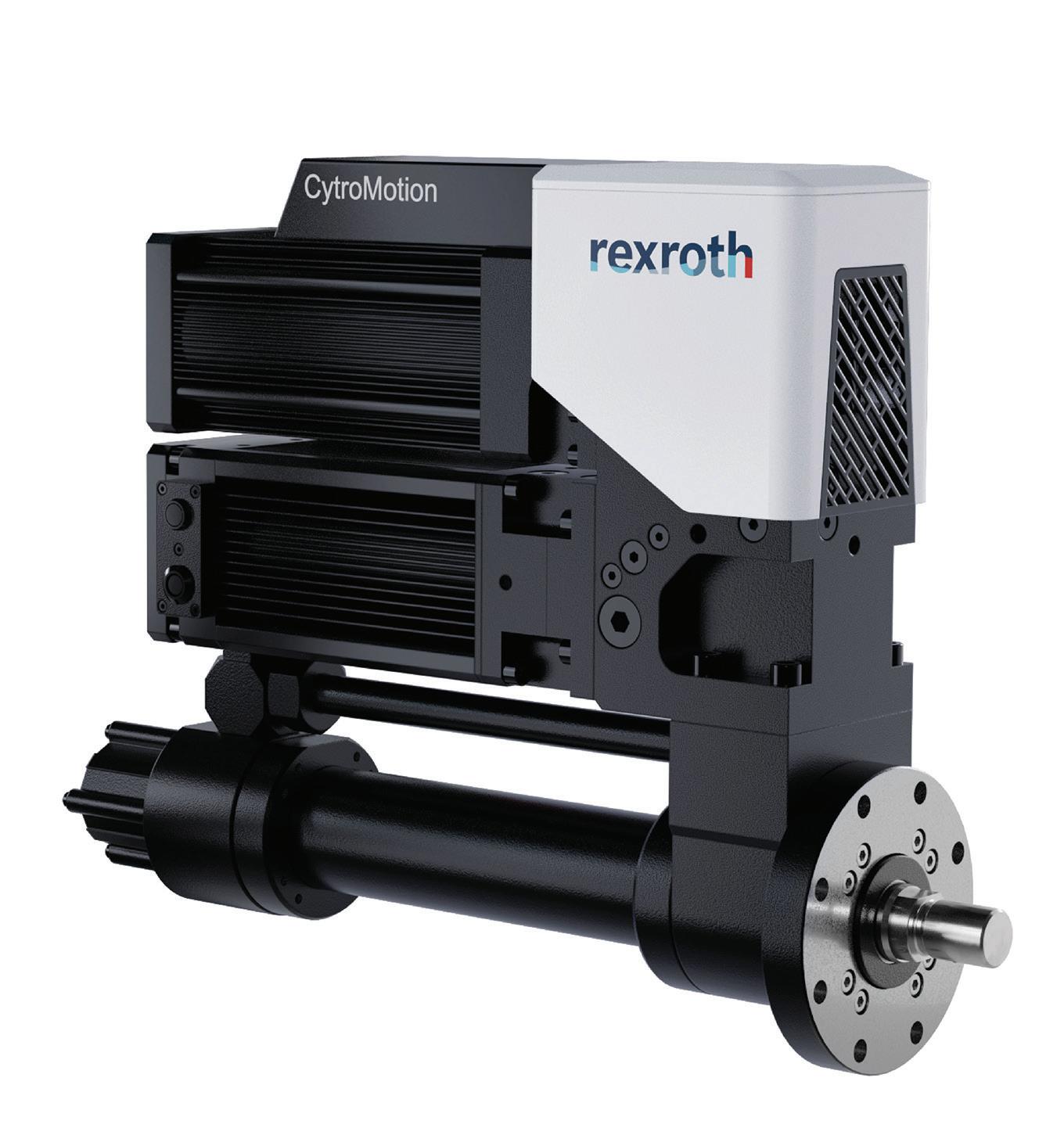
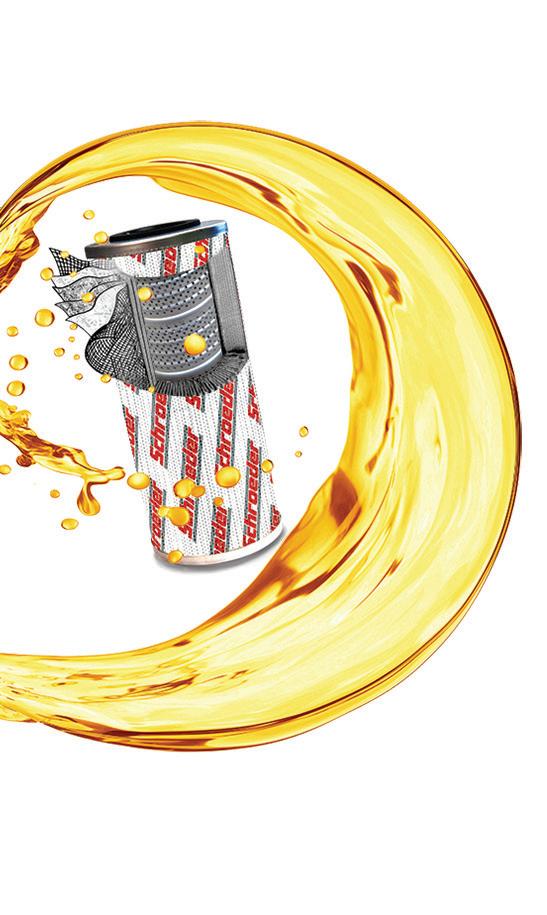
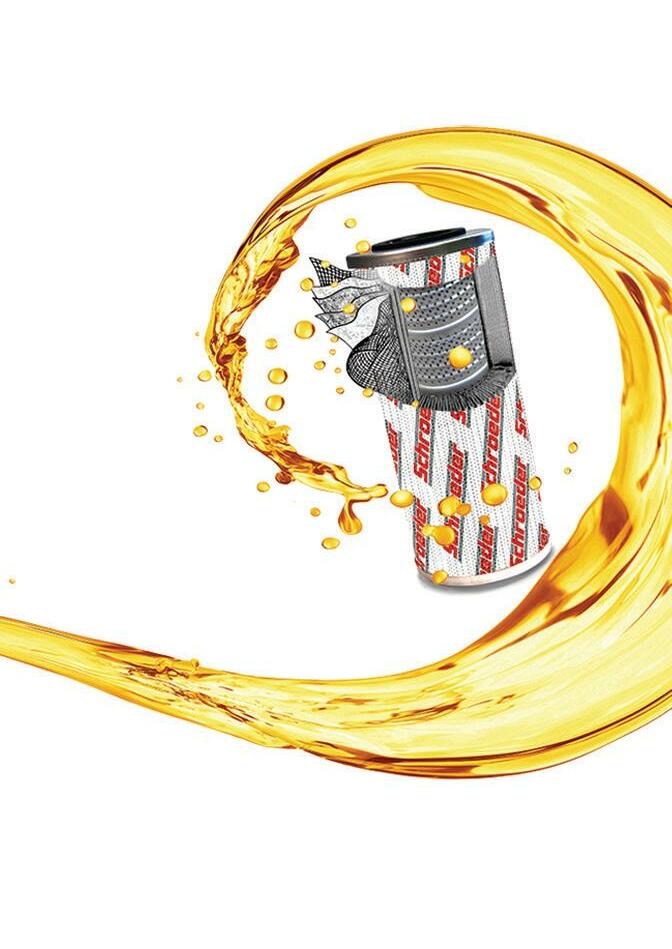



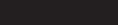







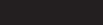

SGDR Toothed couplings made of C40 steel with Nylon PA66 drive ring, suitable for mounting with electric motors and internal combustion engines.
TEAMWORKPERFECT PASSION TO PERFORM ELIXIR In-line return filter with Spin-onserviceguaranteescartridgepatentedelementOEMelementVSstylefilter
MPTX Return filter with optional breather & dipstick for lower flow mobile applications where space is a premium pumps, with or without centering ring, for external and internal tank mounting.
sales@mpfiltriusa.com(215)www.mpfiltriusa.com529-1300
FMM In-line High pressure filter. Light-weight, ideal for forapplications,mobilesuitablevariousfluidtypes.
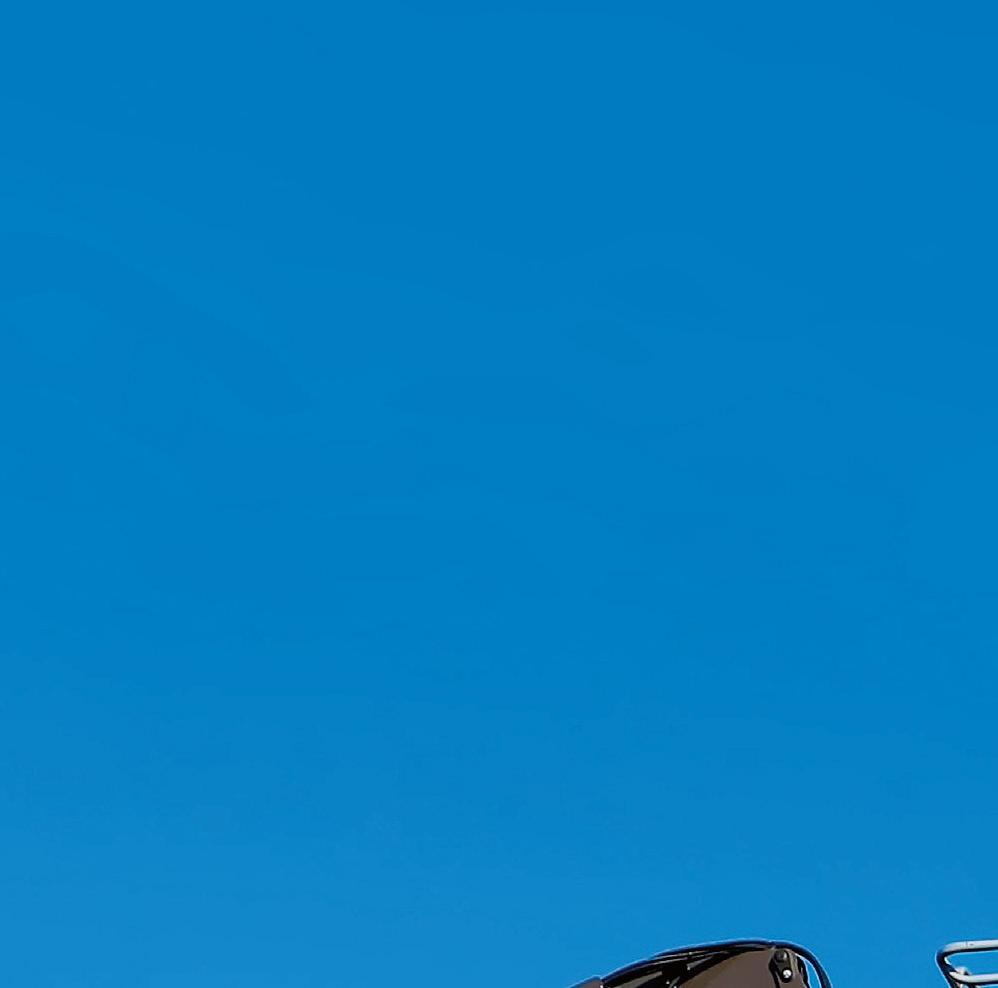
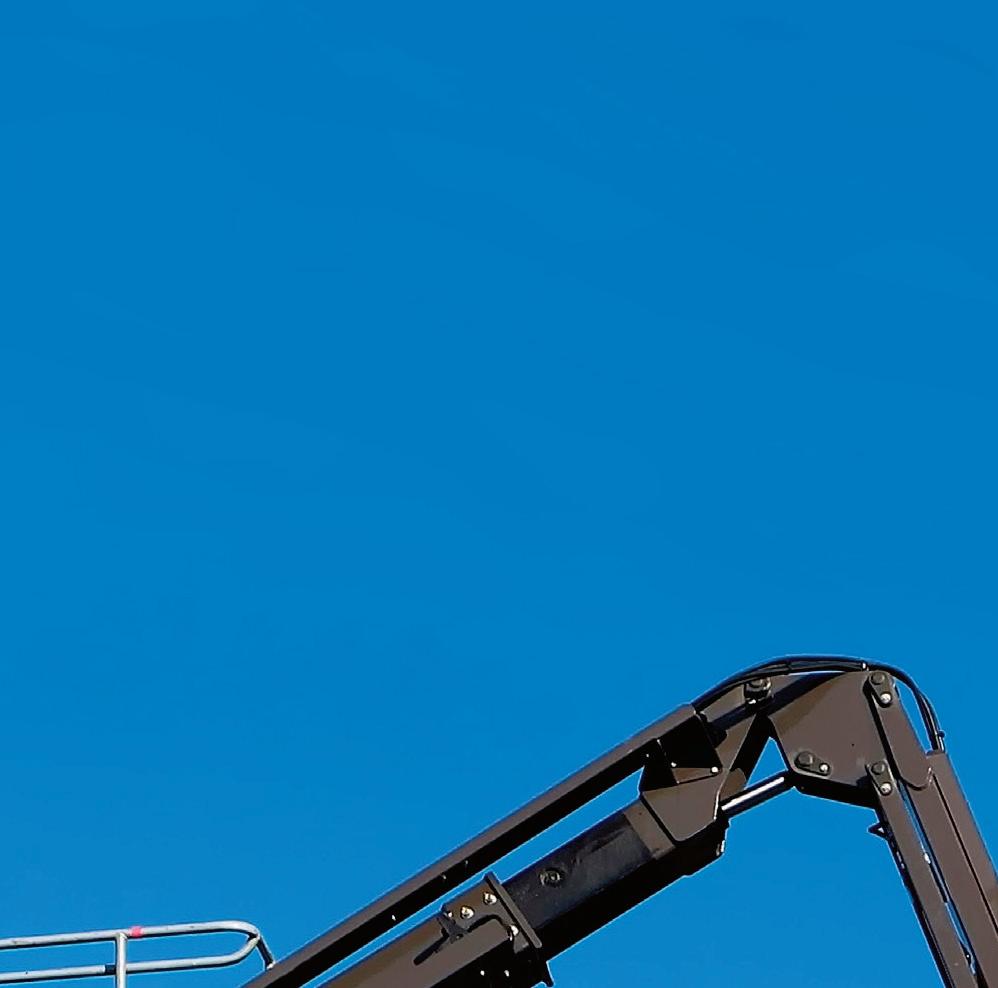

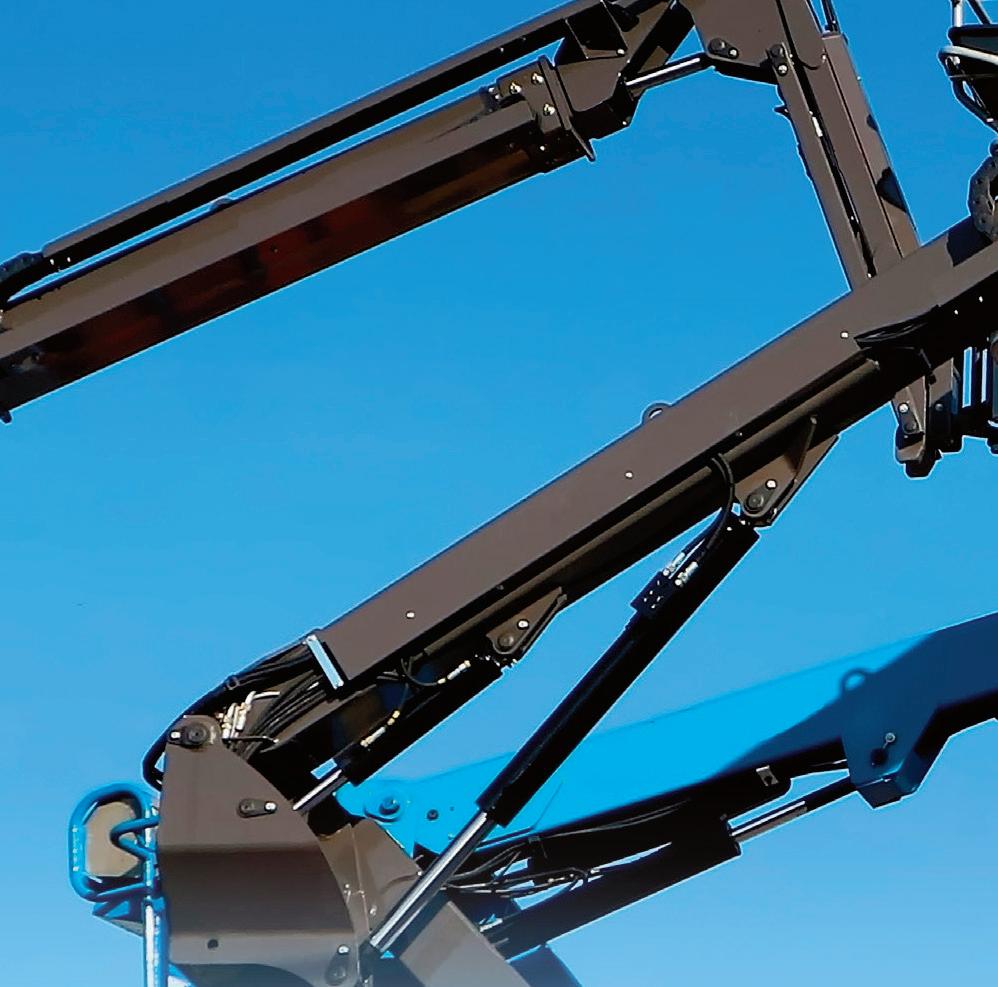
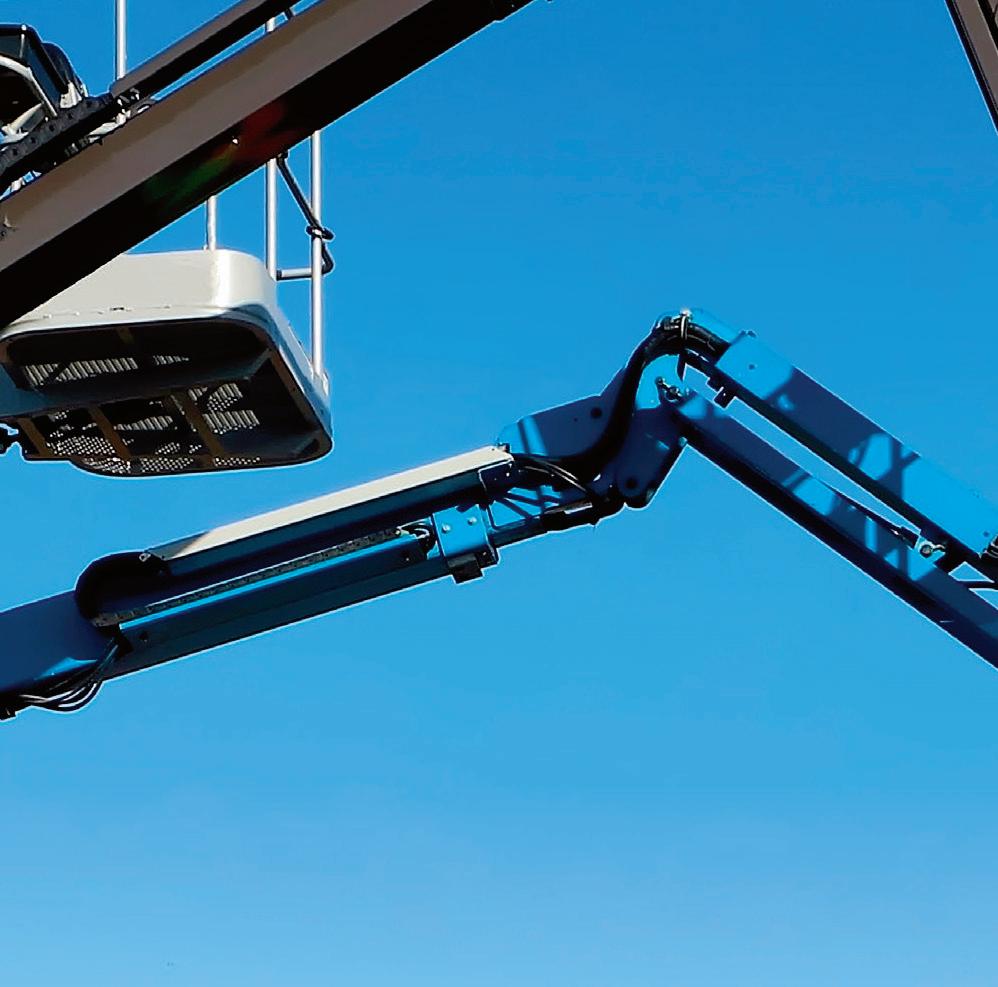
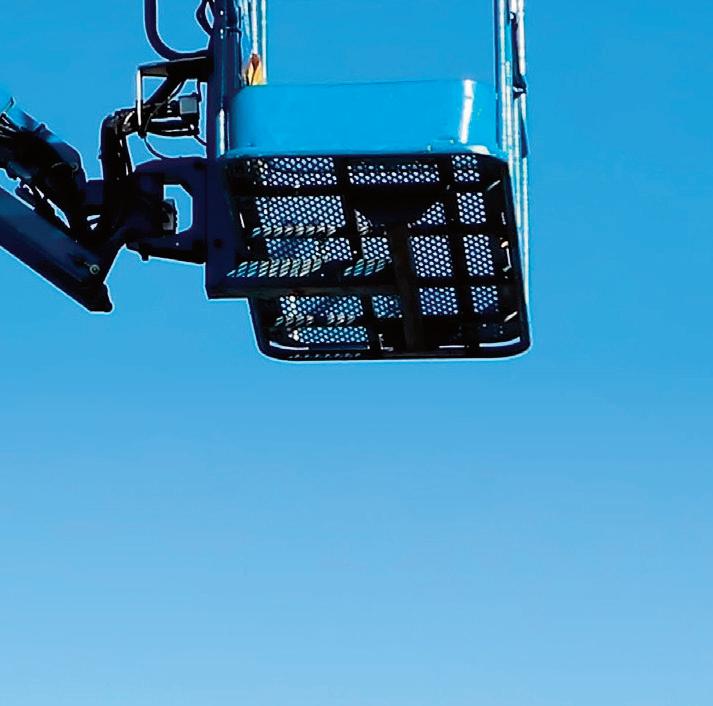
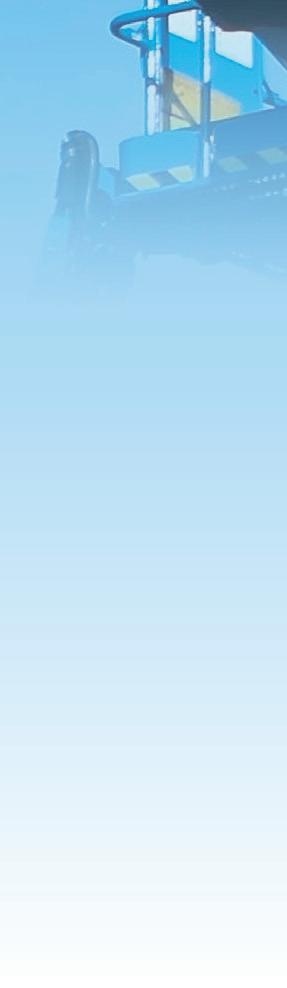


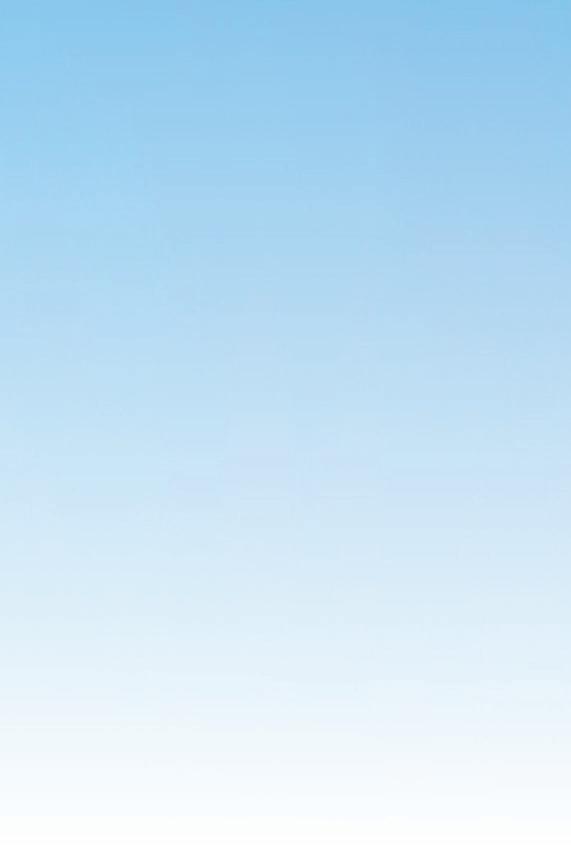
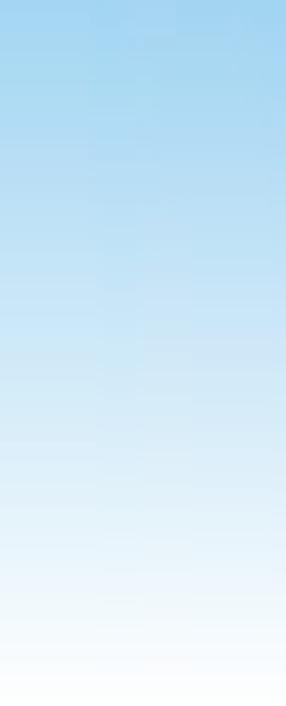
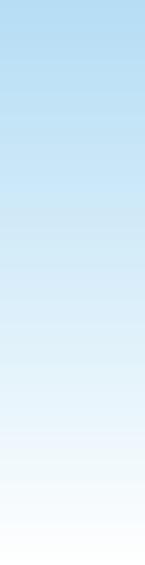
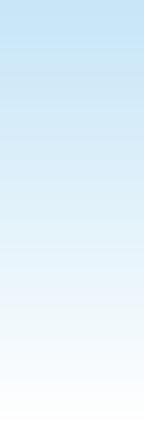
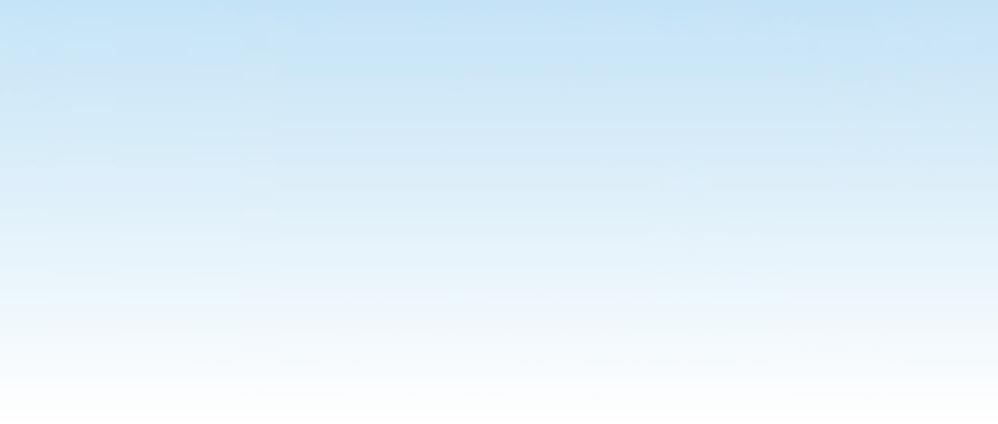

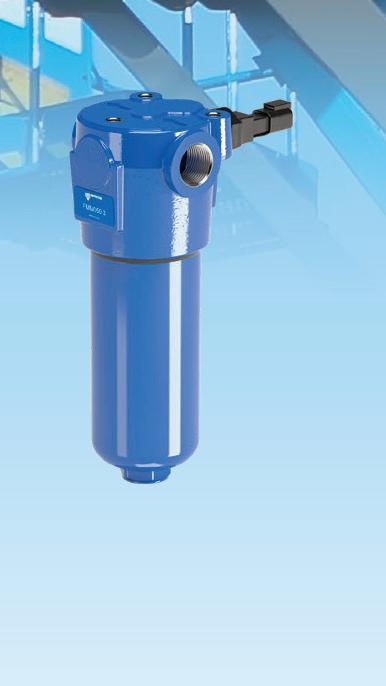
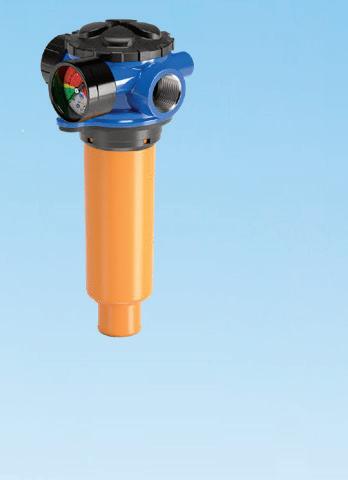
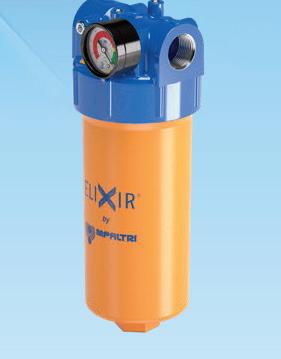

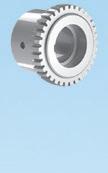
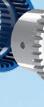
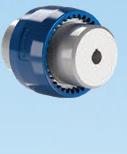
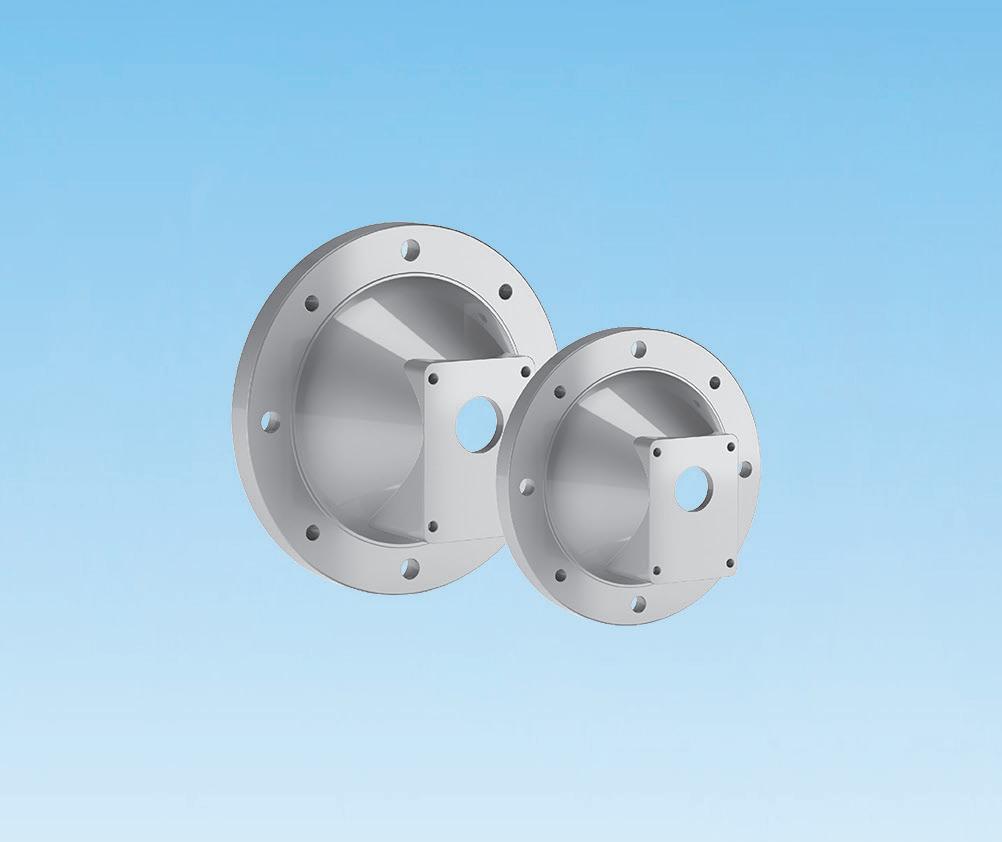




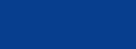
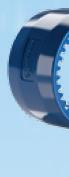





| Courtesy of Twiflex, Altra Industrial Motion
However, rather than a master cylinder and human-created force, a hydraulic power unit provides the power and control to braking systems. A full complement of redundant valves, pressure switches and accumulators intelligently plumbed offers precise control over the braking system to ensure they never fail, even in the absence of pump power. Not all brake applications are springapplied, operating more like the advanced-control older brother to vehicle brake systems. It’s reasonable to expect brake force up to 1,000 kN (225,000 lb), which holds a load equal to that force plus the radius of the brake disc with a whole lot of safety factor involved. Smaller hydraulic brakes get by with compact hydraulic power units, while more sophisticated systems operate more in line with what’s done in the mining industry. From mountain bikes to skyscraper elevators, hydraulic brakes exemplify what makes hydraulic technology so durable.
GMR series spring-applied disc brake, caliper style.
Braking systems take advantage of the textbook offerings given by hydraulics — power, controllability and safety. Hydraulic brakes are simple on the cover, requiring a hydraulic pump and a brake actuator. Vehicle braking systems may get by with what are essentially two cylinders, one at the pump and other at the brake. Depressing the brake pedal transfers force from the operator to the brake caliper actuator with force multiplication equal to the ratio of brake caliper area to the master cylinder area. For example, if the square area of the brake caliper cylinder is 3 in.² and the master cylinder is 0.5 in.², then the force multiplication is six times the effort of the operator’s leg. Hydraulic brake applications go above and beyond the typical brakes of mobile machinery. Although it should be noted that mobile hydraulic machines employ braking technology so much more advanced than the above description, brakes are used in more machines than those with wheels or tracks. Any machine with a load to be controlled safely may take advantage of a hydraulic braking system.
One of the standout applications is the braking systems for mine hoists. These advanced systems are powerful and sophisticated, which you would expect from machinery meant to keep both persons and equipment safe for long journeys up and down a mine. However, the mining industry puts safety ahead of all else, especially in underground mines, and this philosophy is evident with the braking systems used to hold the hoist cable drums. When complete machine failure occurs, the brake actuators must default to the closed position to hold the drum stationary in the absence of power. Powerful springs inside large brake calipers maintain a braking force to hold the large drums and their subsequent loads stationary. Hydraulic pressure releases the brake, and at any time the hydraulic system fails, the brakes will automatically apply to slow and hold the hoist. The force generated by industrial braking systems, such as those used in anything from amusement park rides to shipyard gantry cranes, is based on your standard area/pressure/force triangle.
FPW
Twiflex T40 disc brake caliper is split caliper design suitable for use with a minimum disc thickness of 20 mm.
COMPONENT FOCUS By Josh Cosford • Contributing Editor www.fluidpowerworld.com 8 • 2022 FLUID POWER WORLD 55
How do hydraulic brakes work?

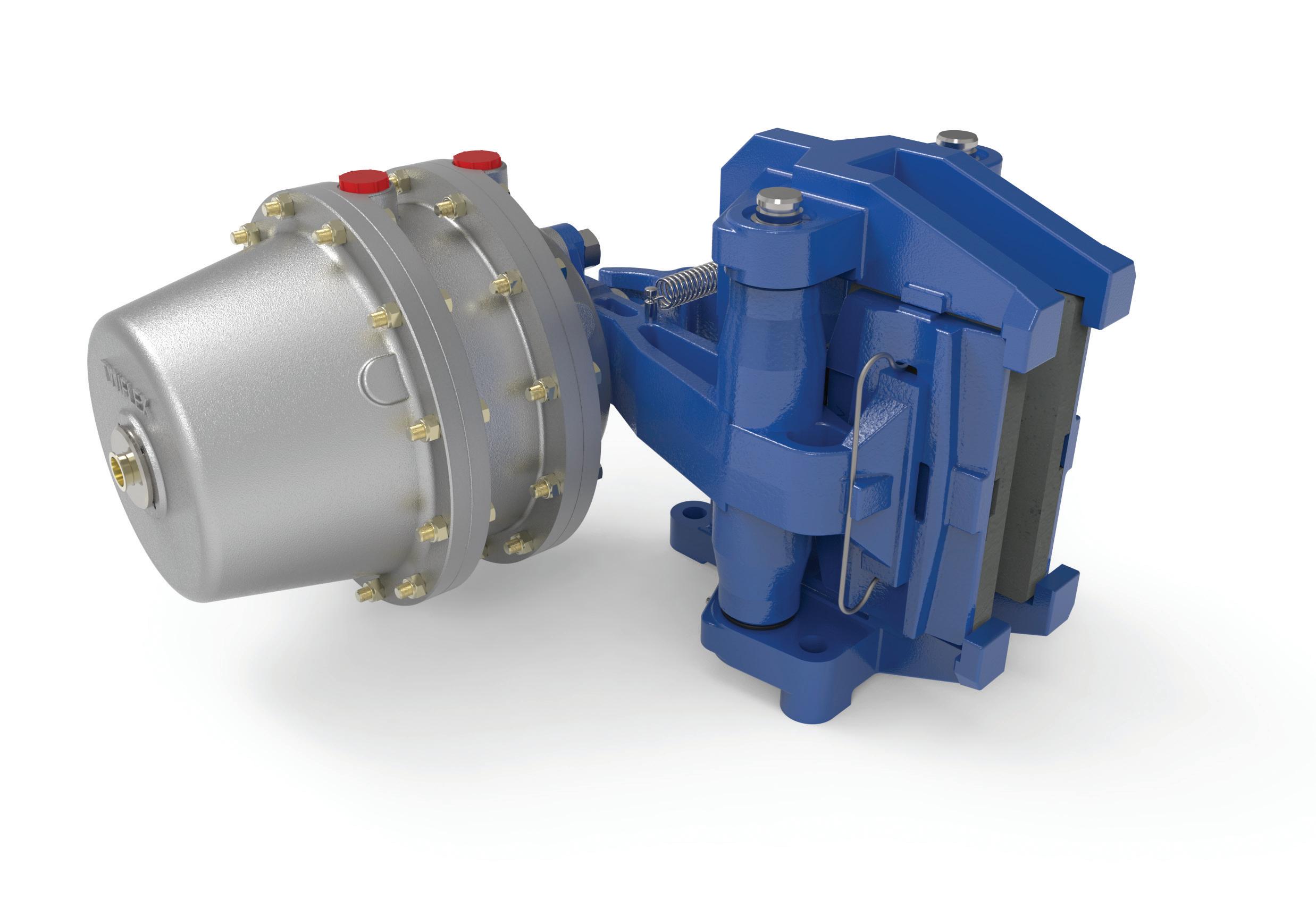

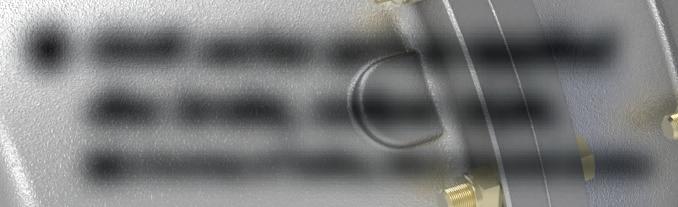
LEADERSHIP TEAM Co-Founder, VP Sales Mike Emich @wtwh_memicmemich@wtwhmedia.com508.446.1823 Co-Founder, Managing Partner Scott McCa erty 310.279.3844 @SMMcCaffsmccafferty@wtwhmedia.comerty MarshallEVP Matheson @mmathesonmmatheson@wtwhmedia.com805.895.3609 Follow the whole team on twitter @FluidPowerWorld@FluidPowerWorld FOLLOW US ON AD INDEX Ace Controls ...........................15 AutomationDirect ....................1 Barb-Tech Tools ......................35 CFC Industrial Training .............4 Clippard ................................. BC DMIC ........................................9 FluiDyne Fluid Power .............43 GRH Power .............................27 HAWE .....................................23 HBC - Radiomatic 49 HYDAC USA 5 Hydraulex Global 13 IFPE (AEM) 50 Kawasaki Precision Machinery . 19 Main Mfg ..................................8 Motion ...................................11 MP Filtri USA ..........................54 Permco ........................... 39, IBC Rota Engineering ....................52 Seco Seals ...............................31 SIKO ..........................................2 Super Swivels .........................53 Terzo Power Systems 3 Tompkins Industries IFC, 8 Veljan Hydrair 7 fluidpowerworld.com CHECK US OUT on ISSUU.COM! CONNECT WITH US!
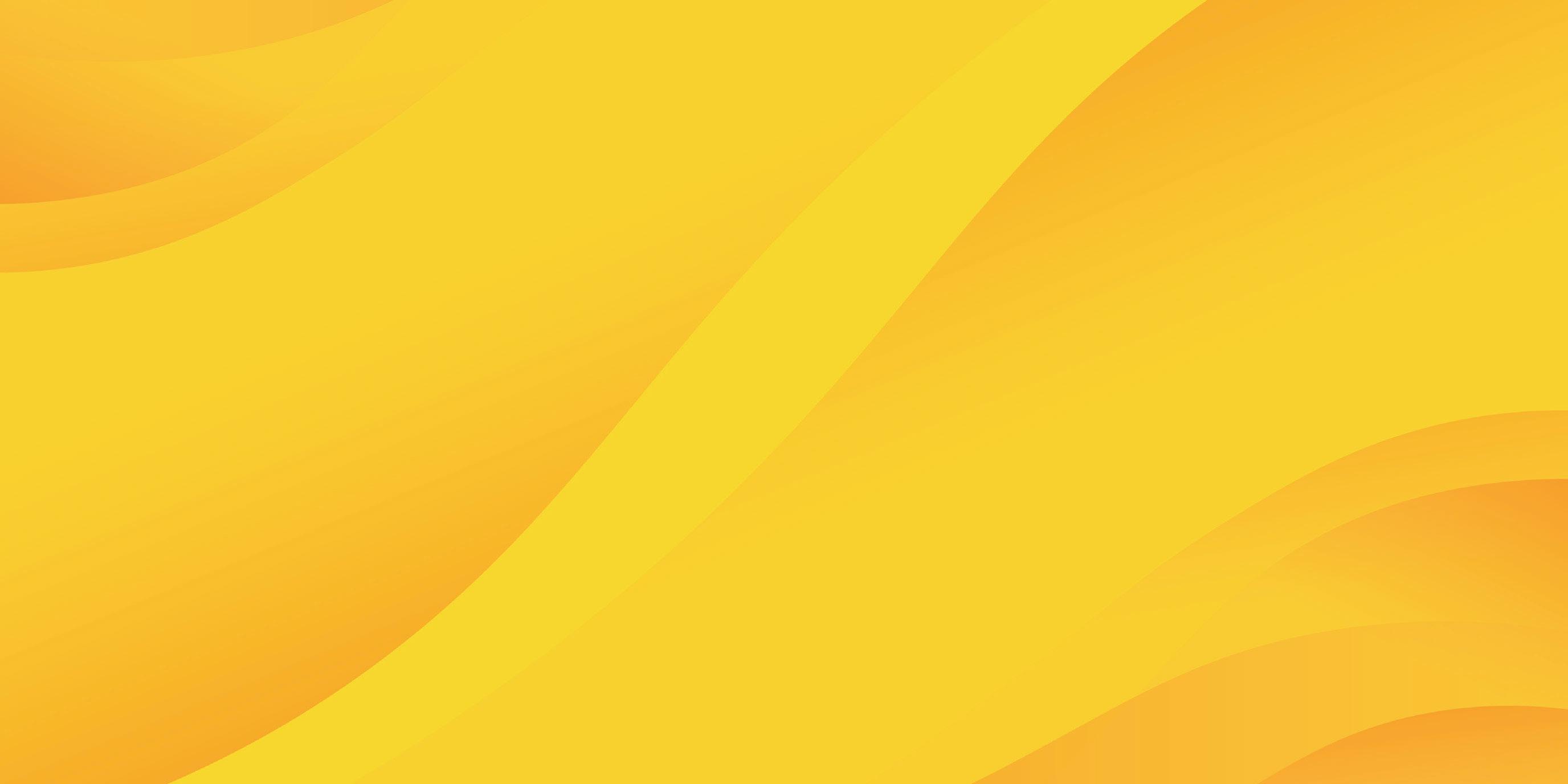

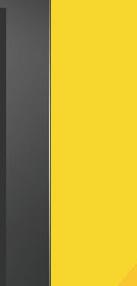

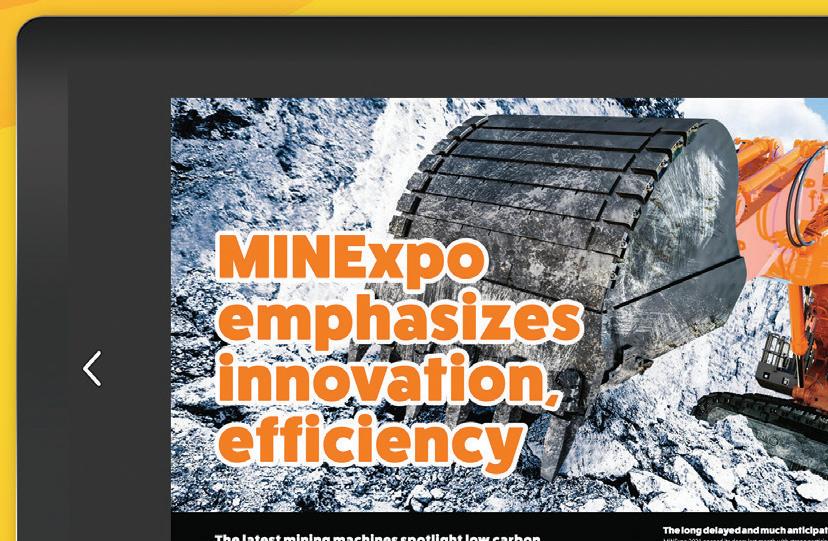




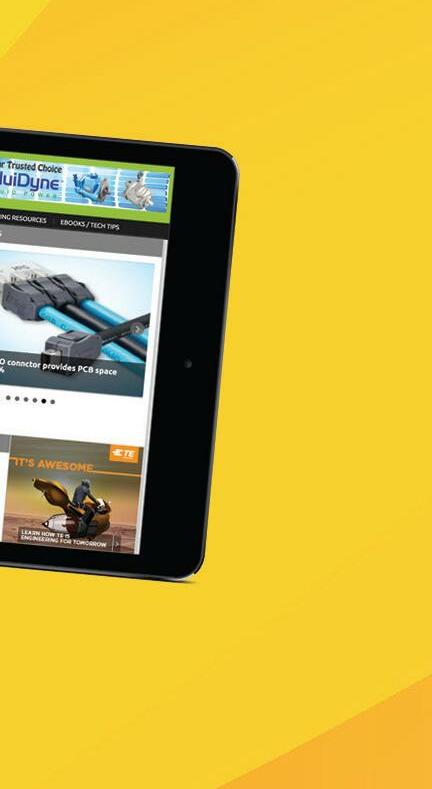
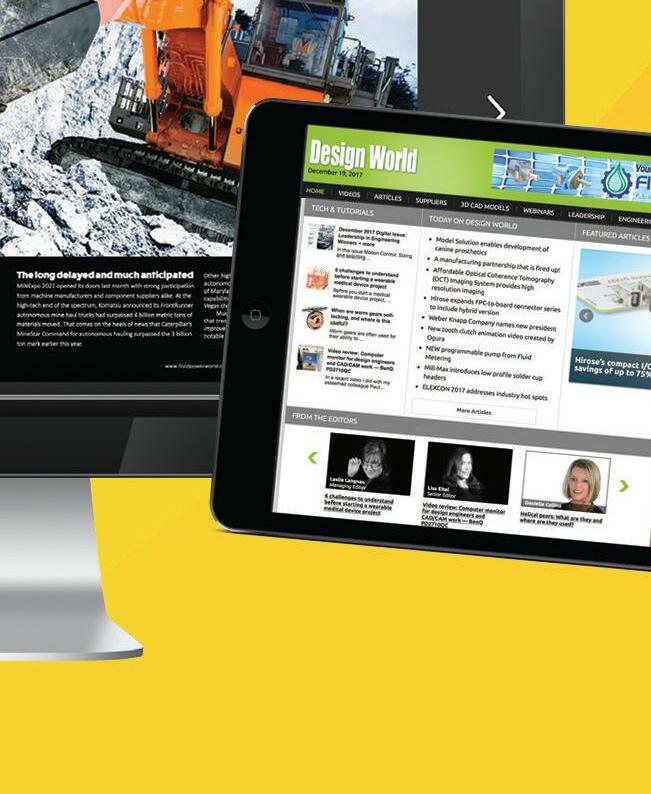
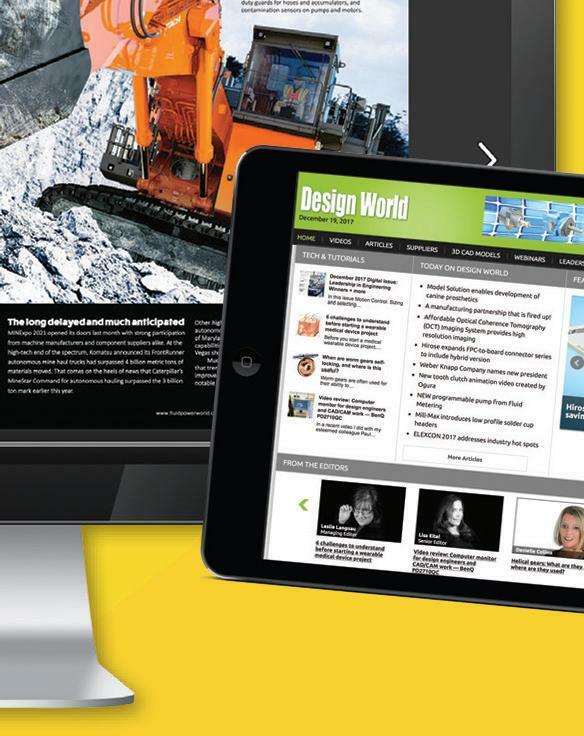



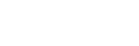
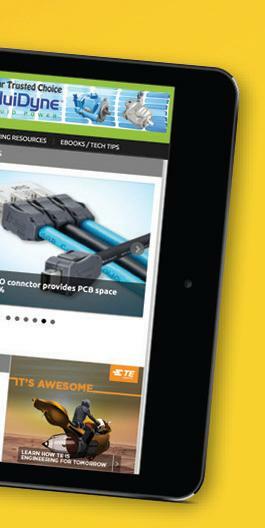
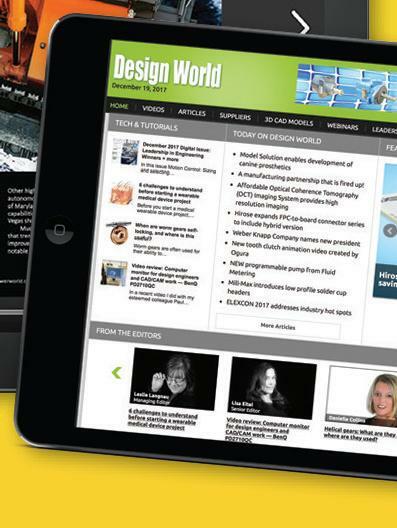
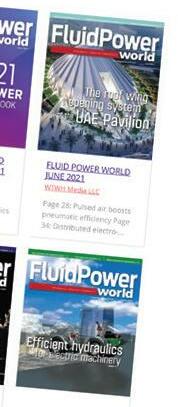


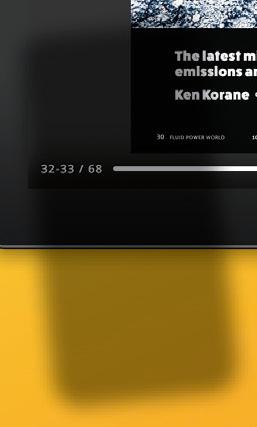





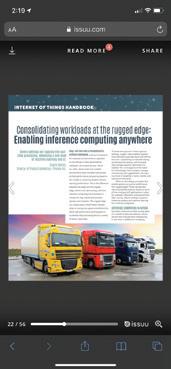

Home of the American Champ 1500 Frost Road Streetsboro, OH 44241 PERMCO MVP The Permco MVP is the only pump that fits all 5 manufacturers of Allison Brand Transmissions. It takes an MVP to get the job done. Contact us today. permco.com | 800.626.2801MVP Designed to be used in Heavy & Medium Duty Trucks & Trailers. Pump and cylinder protected in the “Raise” and “Neutral” position of the spool. It takes an MVP to get the job done. Saves you money. Saves you time. Saves you hassle.

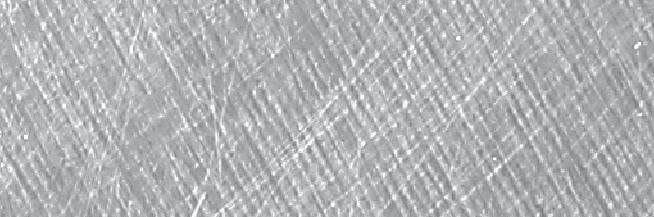


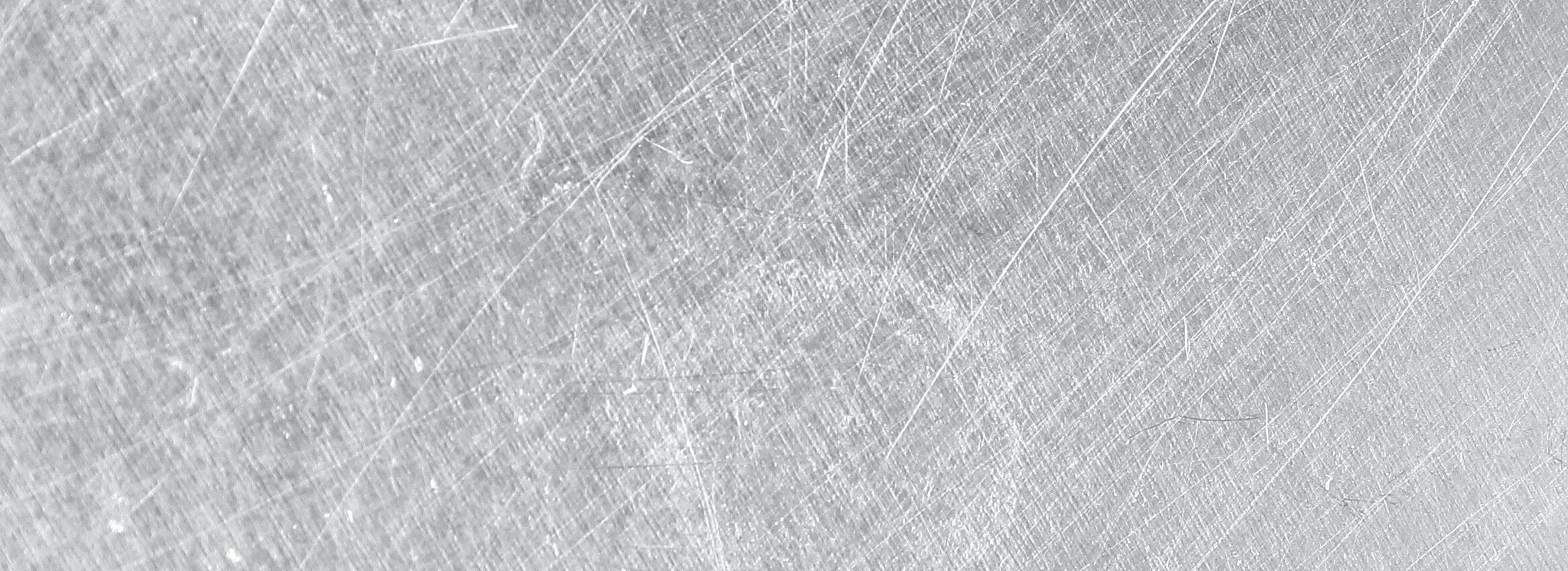
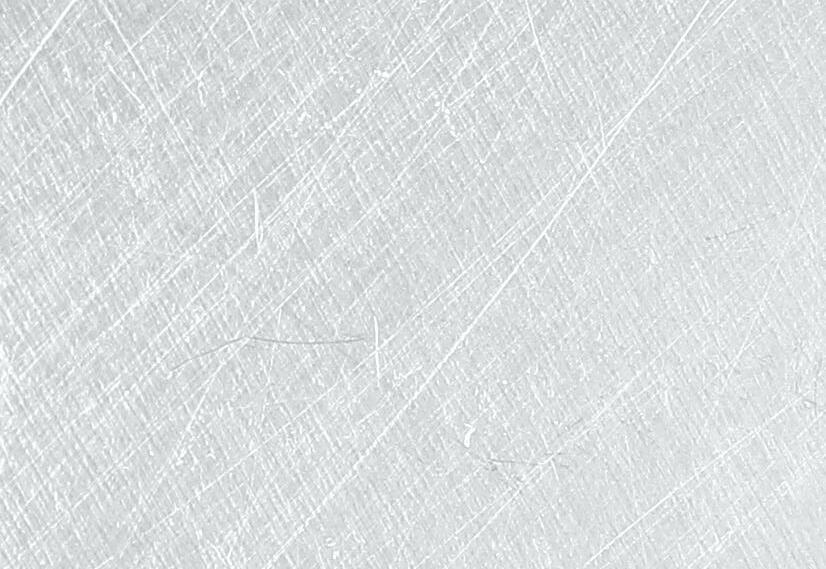


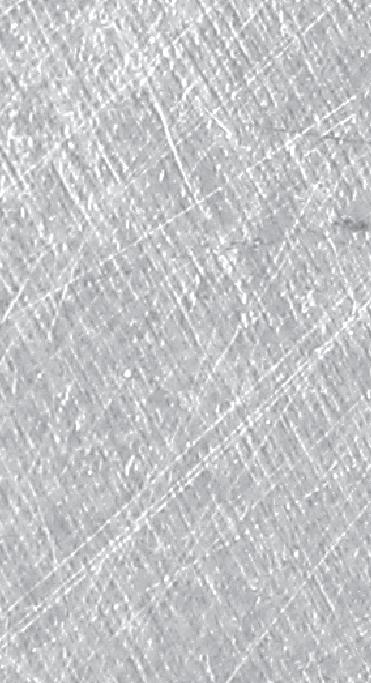
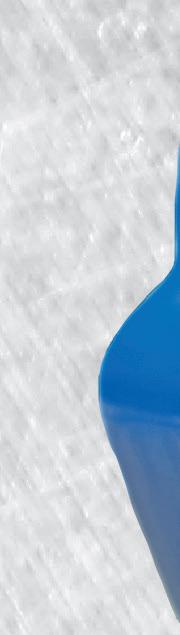
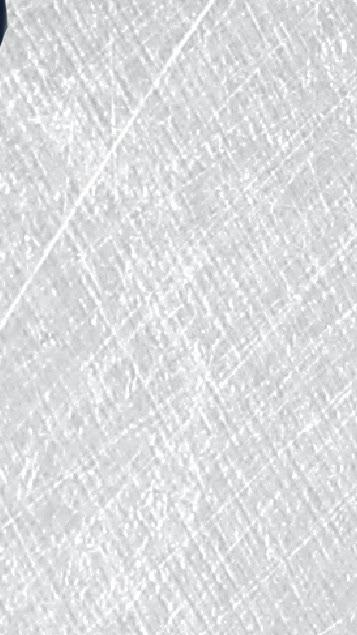

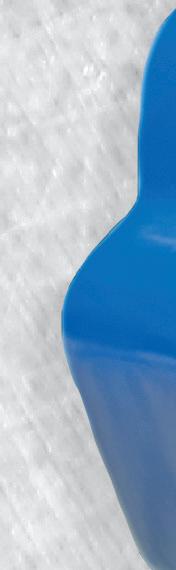
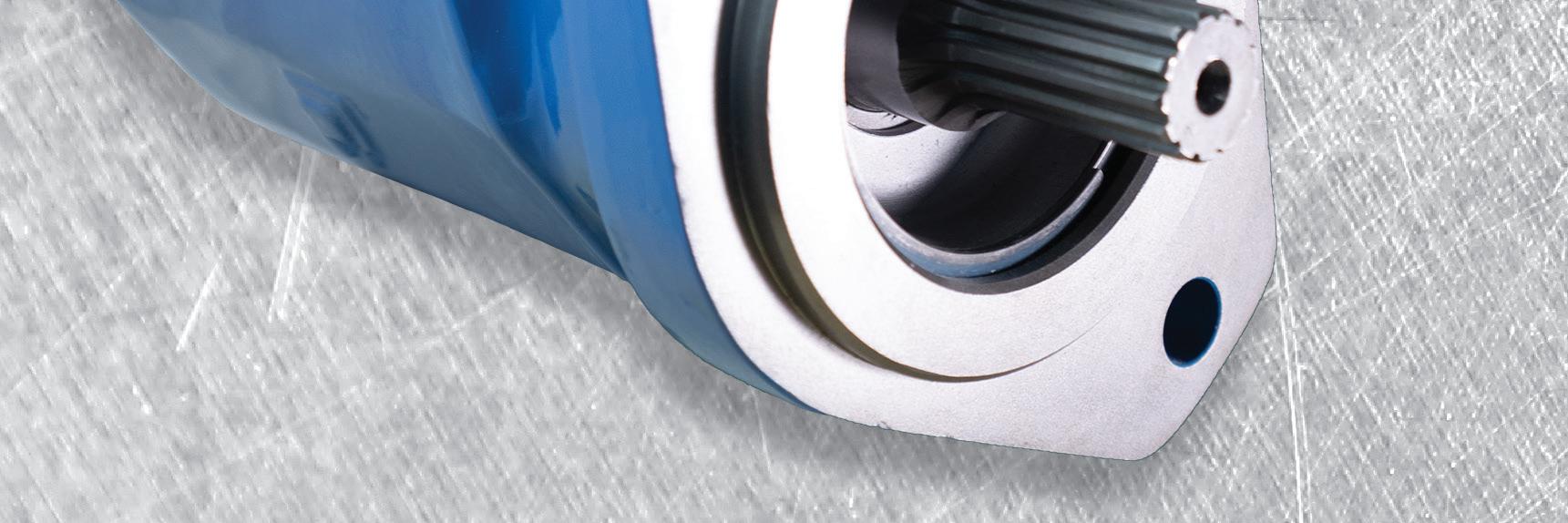
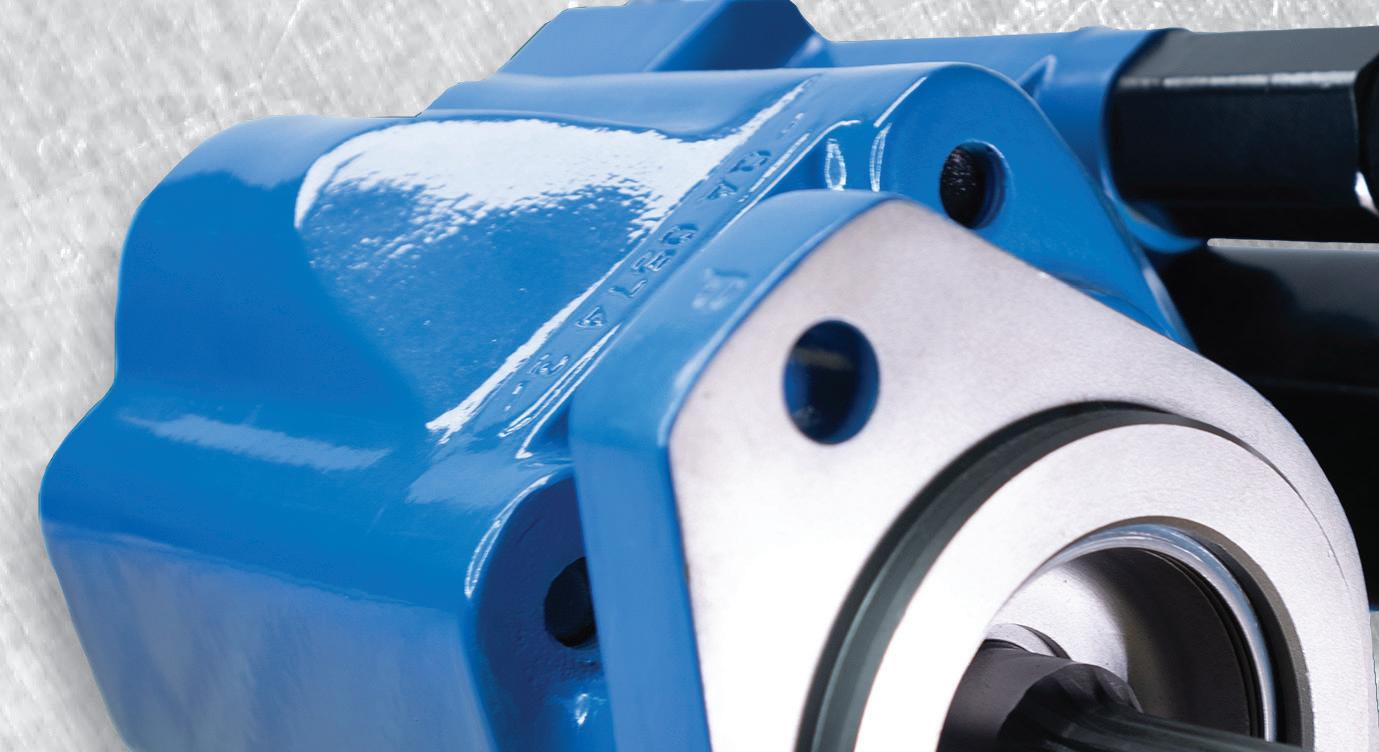
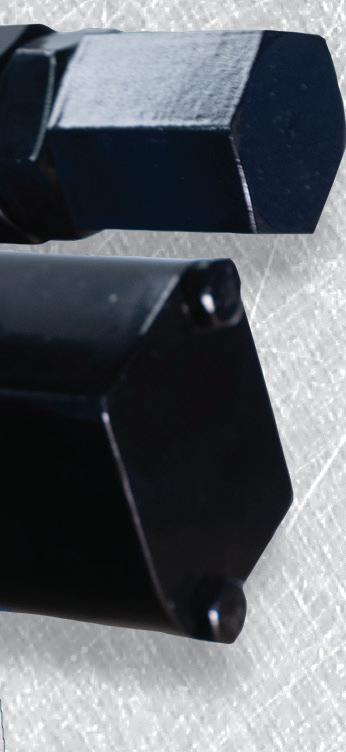

Take Control with Cordis The future of proportional control has arrived— and it’s digital. The Clippard Cordis is a revolutionary microcontroller primed for escape velocity from a proportional control market that has grown stagnant. With unparalleled performance and flexibility not possible with current analog proportional controllers, the Cordis makes everything from calibration, to sensor variety, to future development opportunities more accessible and less complicated. Precise, Linear Digital Pressure Control • Resolution ≤5 mV • Accuracy ±0.25% of full scale • Real-time adjustable PID control • Integrated 0 to 10 VDC, 4-20 mA signal, or 3.3 VDC serial communication • 0 to 10 VDC feedback pressure monitor • Virtually silent • No integral bleed required • Multiple pressure ranges from vacuum to 150 psig • 2.7 to 65 l/min flow control 877-245-6247 CINCINNATI • BRUSSELS • SHANGHAI Contact your distributor today to learn more about how the Cordis can provide precise, real-time control for your application, or visit clippard.com to request more information. ELECTRONIC PRESSURE REGULATION



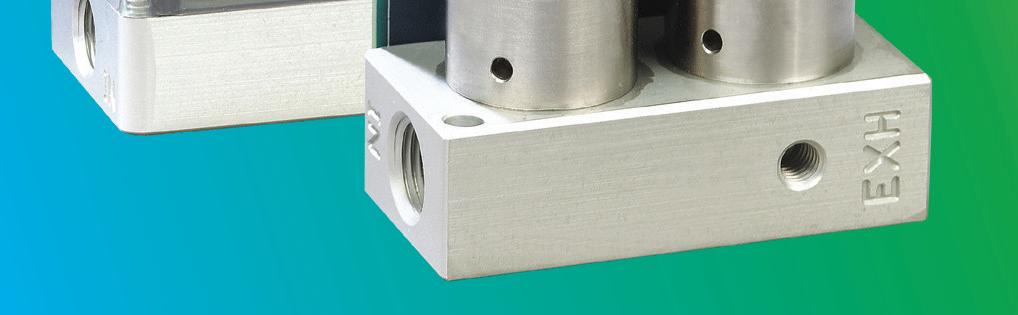



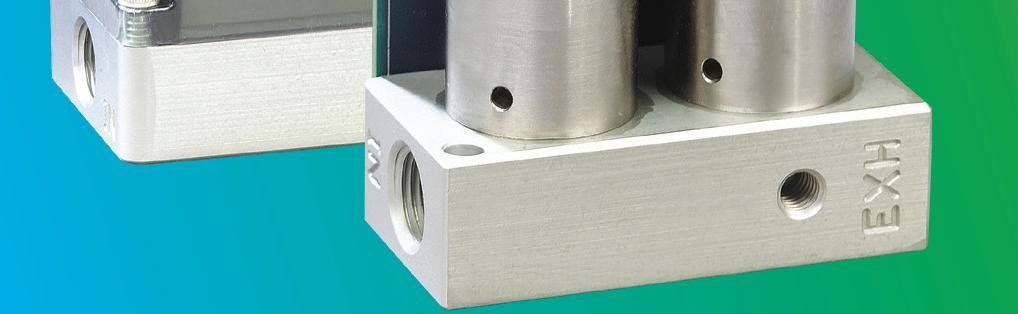
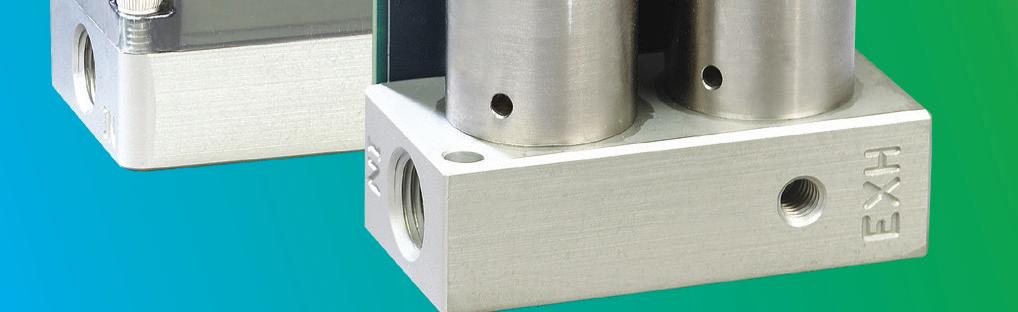
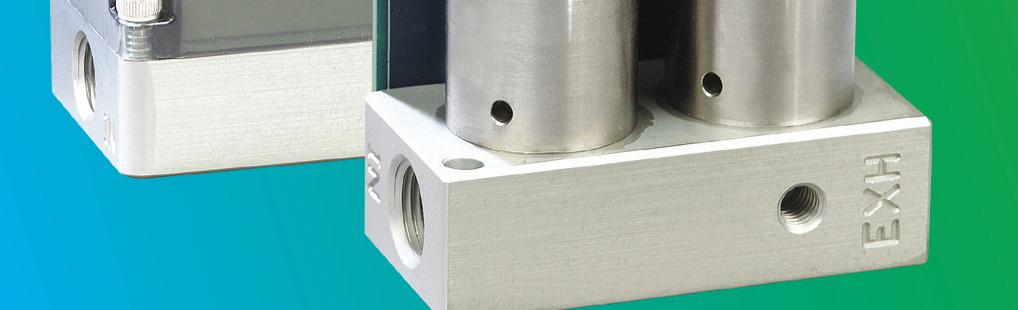
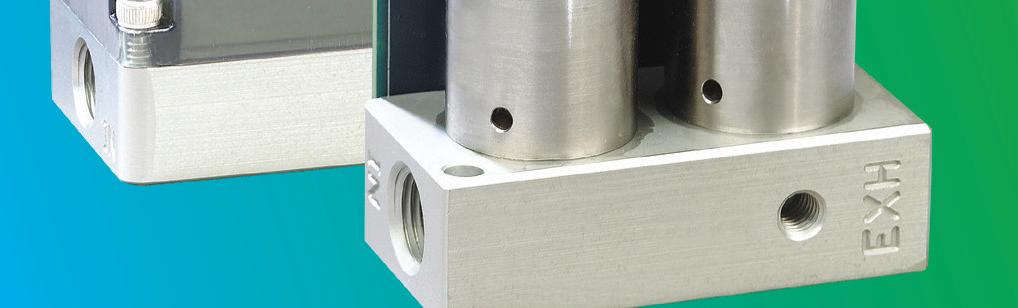
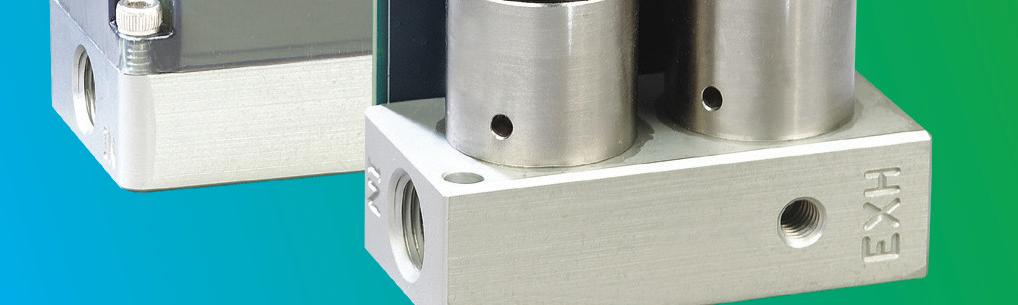

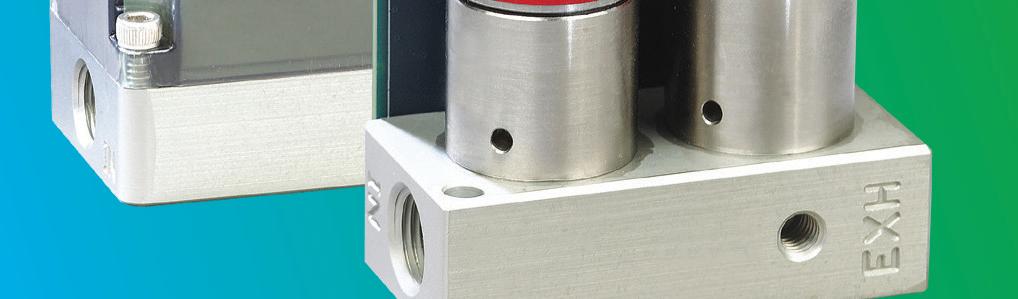
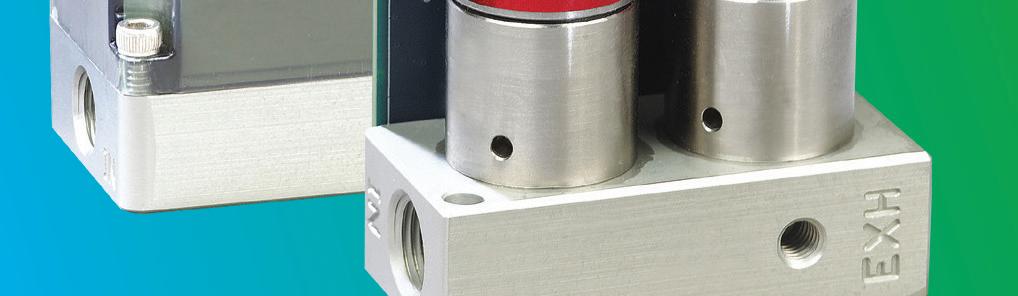
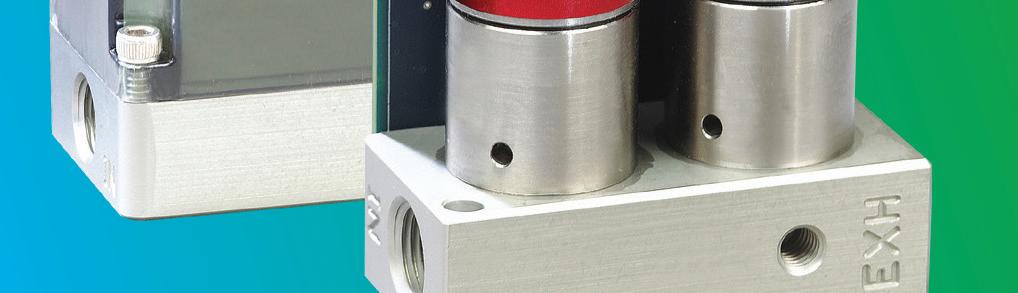
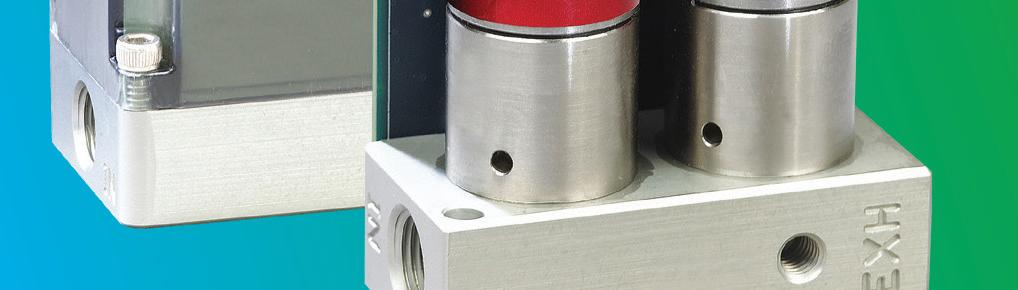
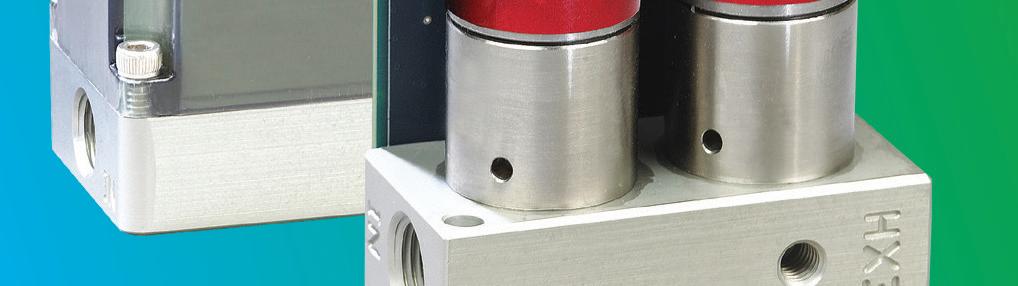
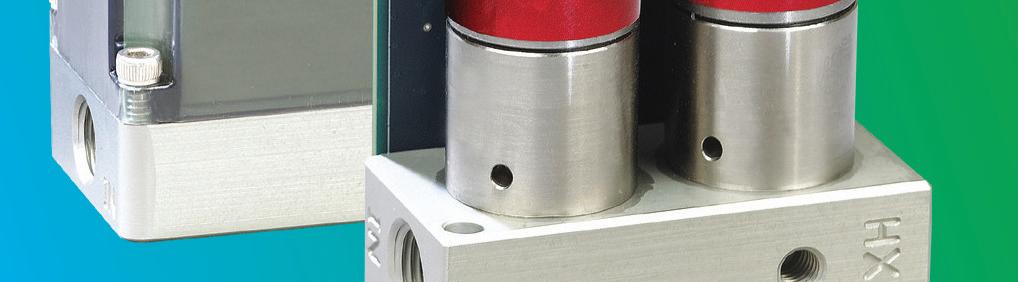
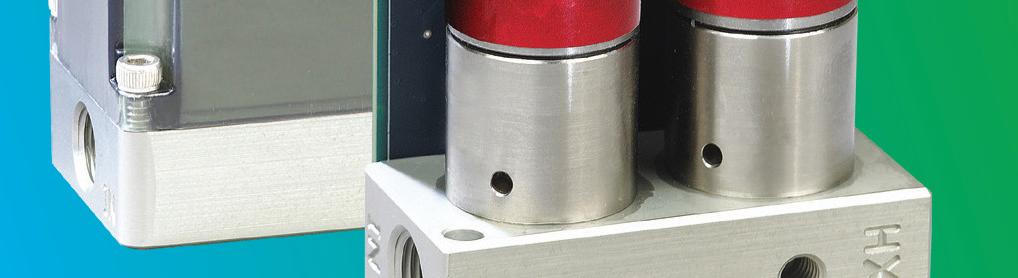


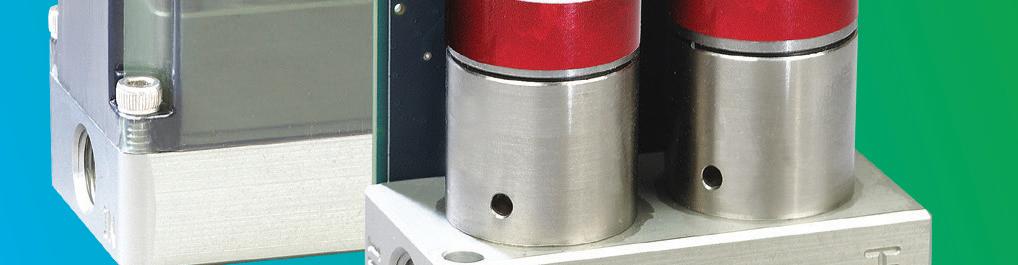
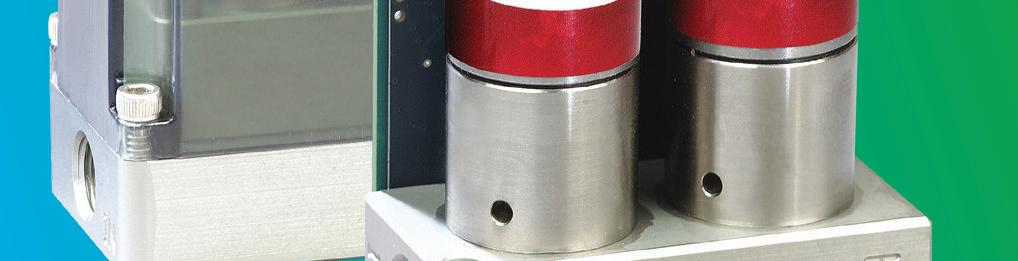

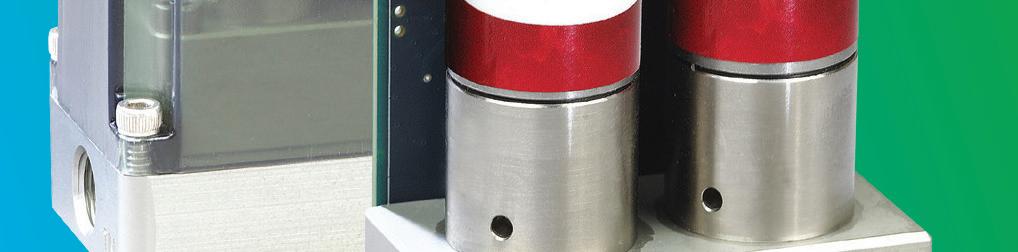
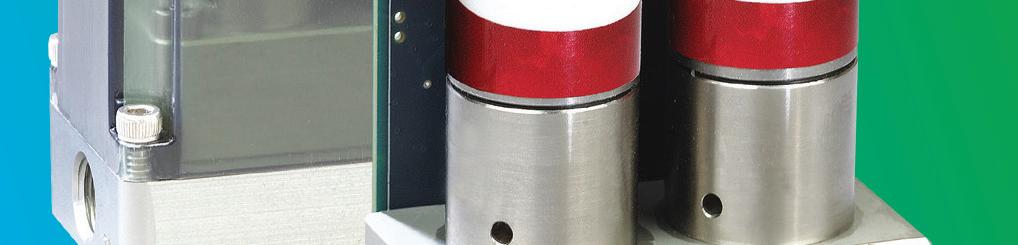
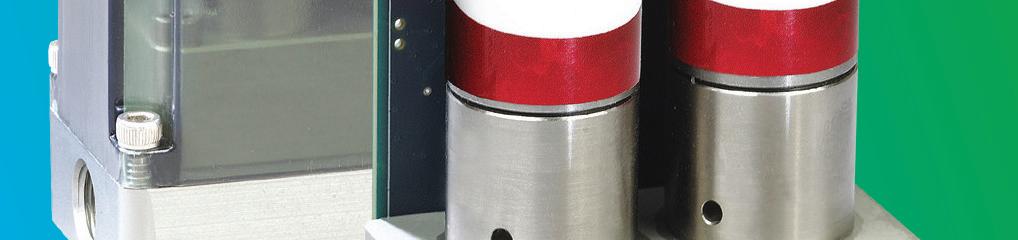
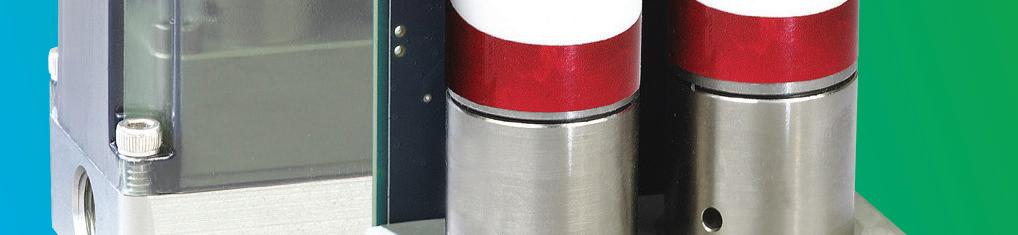
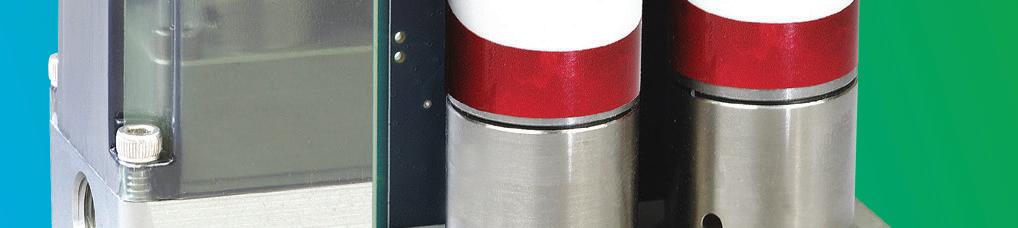
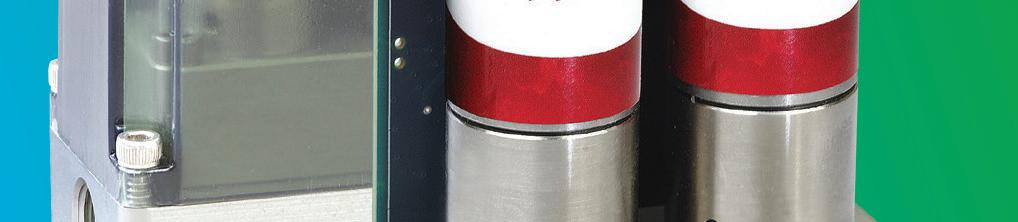
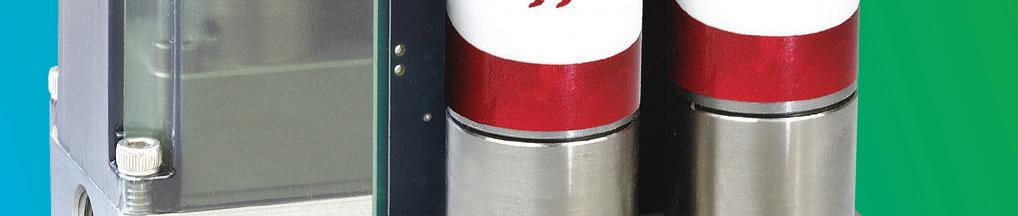
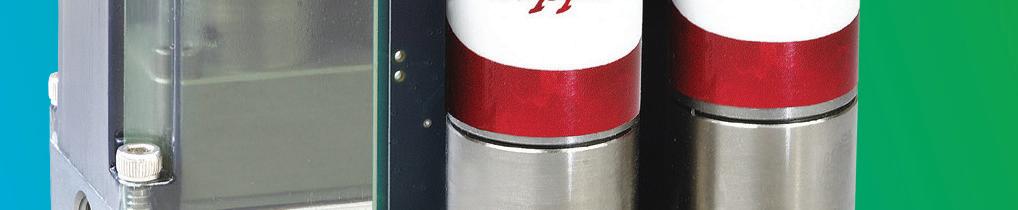
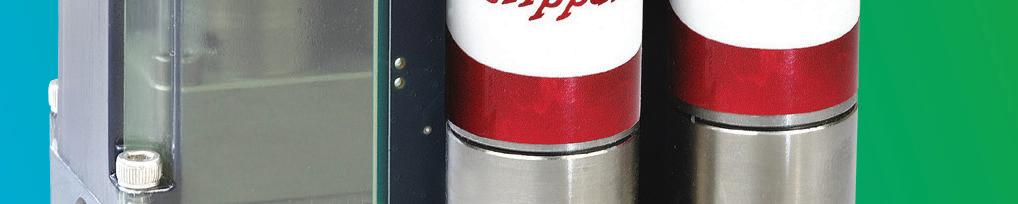
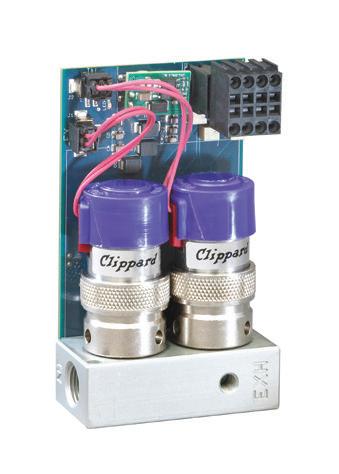
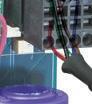
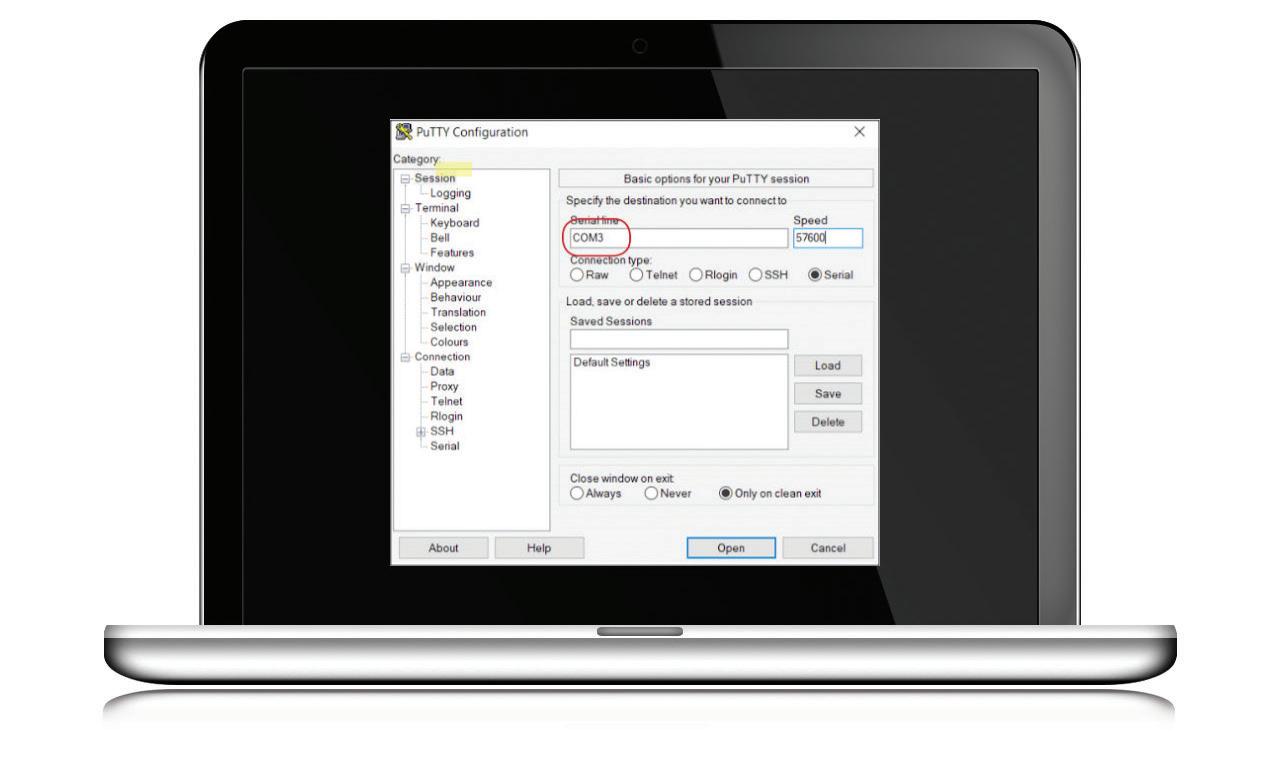
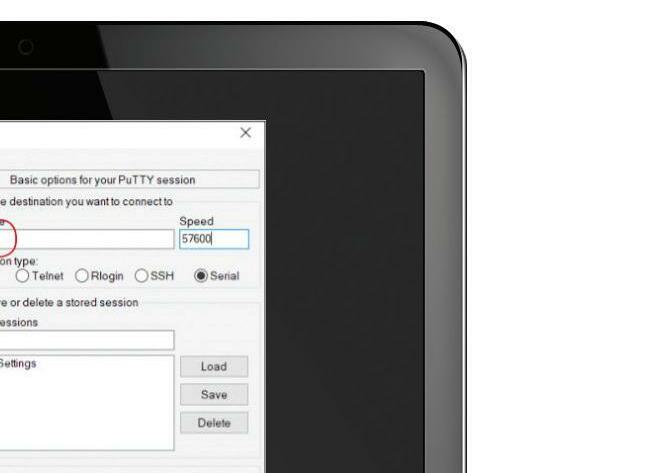

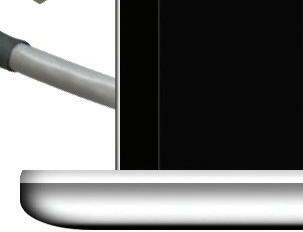
