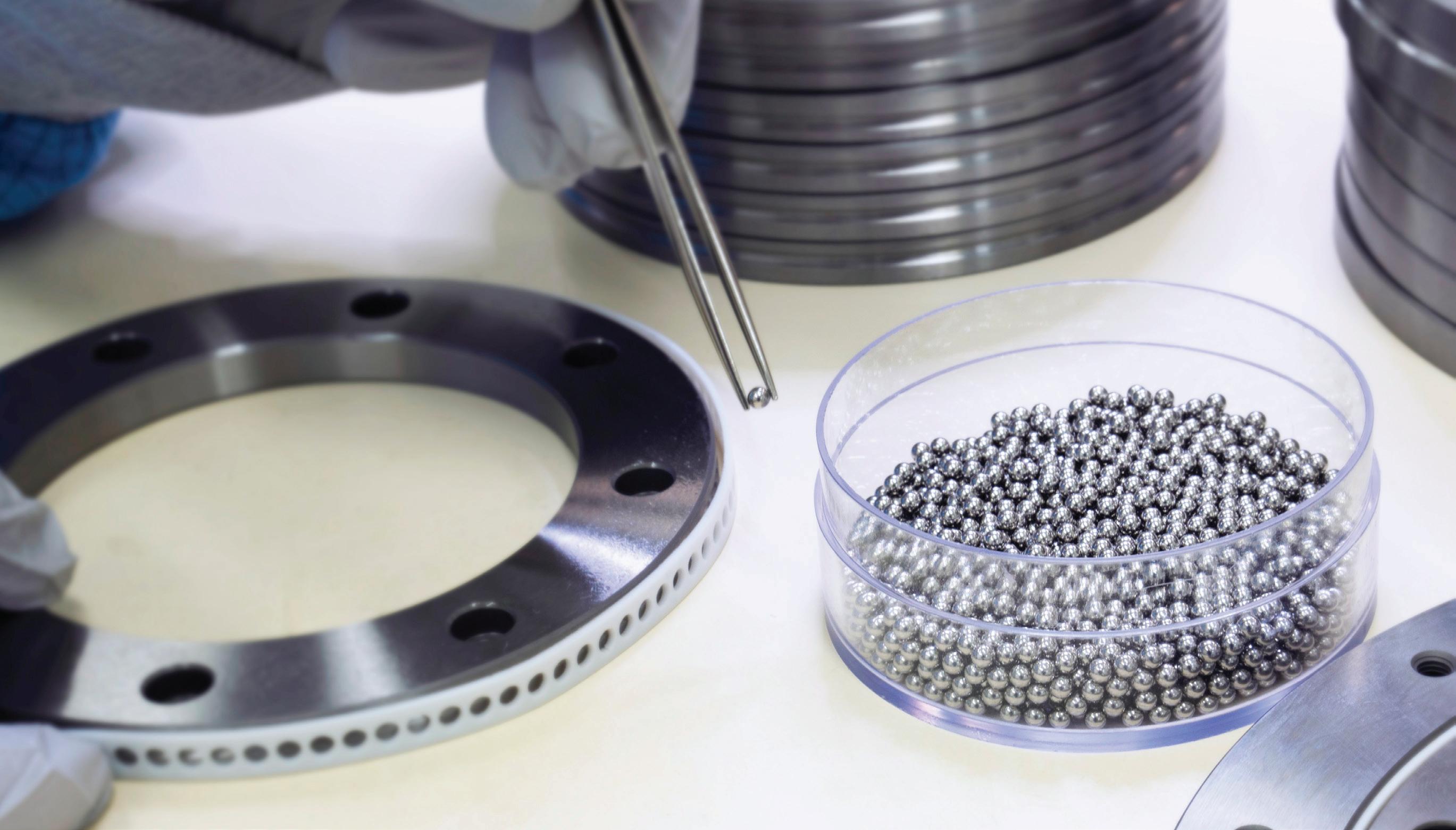
2 minute read
Rotary bearings in everything — from miniature tables to railcars
Bearing variations abound to satisfy an array of loads, environments, speeds, expected design life, and more. Consider the bearings and slewing rings in wind turbines. These can reach 2 m in diameter and must sometimes bear hundreds of tons. In contrast are miniature bearings for medical applications. These often go into tiny handheld devices and other compact equipment necessitating bearings of just a couple millimeters in diameter (with rollers that are even smaller).
Some bearings going into equipment subject to washdown have treated steel subcomponents; others for disposable or quiet designs are made of plastic. Industrial machines that endure hot, fast, or lubrication-starved conditions pose their own bearing-design challenges. Some of these benefit from the use of hybrid bearings — those with steel raceways and rollers or balls made from ceramic. No matter the design, each bearing type satisfies specific parameters.

This FMB rotary table bearing is specifically developed for high-precision rotary-motion tables. It’s less costly than other rotary bearings because it contains fewer components — and necessitates consideration of fewer less tolerances for installation. Image courtesy of PM B.V.
Ball bearings use balls to provide low-friction motion between bearing races. When selected properly, they require little maintenance. This feature and their limited heat generation make them indispensable. They are found in everything from skateboard wheels to turbine engines — in aerospace applications, medical equipment, and home appliances.
Roller bearings have cylindrical rollers instead of balls to transmit loads and reduce friction. Thanks to this shape, roller bearings have greater surface contact than ball bearings, so handle larger loads without deforming. Their shape also allows for a moderate amount of thrust load because weight is distributed across cylinder line contacts instead of point contacts. These bearings are common in conveyor belt rollers, turbine engines, transmissions and gearboxes, as well as the mining, food and beverage, pulp and paper, waste-water and marine industries.
Needle roller bearings have rollers with lengths at least four times their diameter. The large surface area accommodates high radial loads even in compact designs. Needle bearings often go in compressors, rocker-arm pivots, pumps, transmissions, and other automotive designs. Needle bearings are also common in construction and agricultural equipment, two-cycle engines, outboard engines, and paper-moving equipment.
Thrust ball bearings go in applications with mostly axial loads and can handle shaft misalignment. These bearings excel in high-speed aerospace, automotive, and oil and gas applications. Thrust ball bearings also work in machine tools, fluid-control valves, and spindles.

Shown here is the FMB rotary table bearing once installed. Image courtesy of PM B.V.
Thrust roller bearings transmit load from one raceway to the other to accommodate radial loads. Bearings like these also have a self-aligning capability that makes them immune to shaft deflection and alignment errors. Typical applications include crane hooks, pulverizers, cone crushers and other heavy-load, mediumspeed applications.
Tapered roller bearings have tapered inner and outer ring raceways with tapered rollers between them. The rollers are angled so their surfaces converge at the bearing’s axis. These bearings can handle axial and radial loads. Common applications include helicopter transmissions, fuel pumps, and agricultural equipment.
Plain bearings don’t have rolling elements. They’re compact and lower-cost bearings for many applications, but automotive and construction are some of the most common. Plain bearings go in automated machine axes and more rugged applications such as hydraulic excavators and more.

On the opposite end of the application spectrum is this SMB188 stainless steel bearing for railway applications — one that includes a magnetic pulsegenerator ring for IIoT functionality. In the railway industry, adding smart bearings will provide operators with real-time, on-board information on bearing health, and allow the detection of early bearing damage. Because train bearings are key elements in the integrity of railway wheelsets, the integration of condition monitoring can significantly impact railway operating costs and train safety. Image courtesy of SMB Bearings