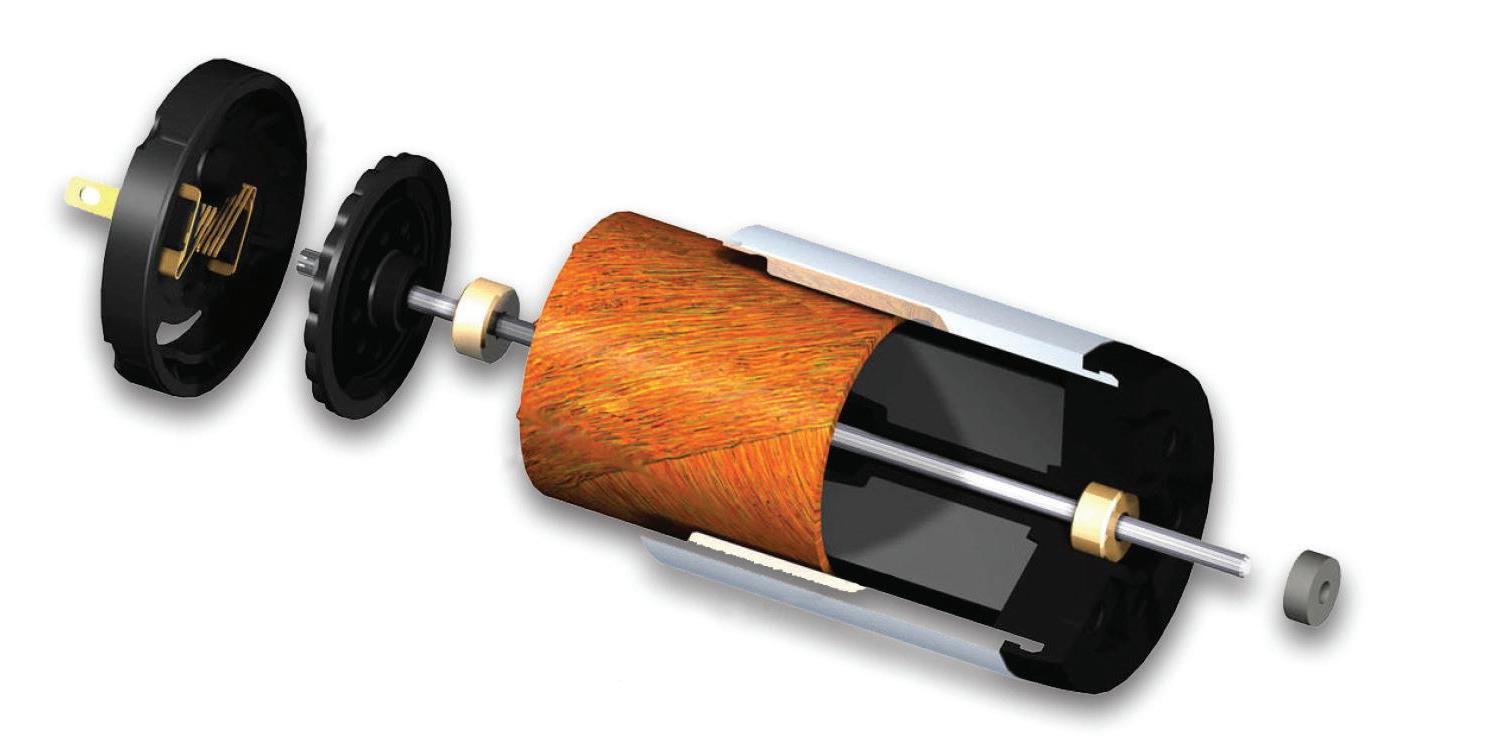
7 minute read
Brush DC versus brushless DC motors in disposable tools
By Clémence Muron Applications engineer | Portescap
Disposable medical hand tools are seeing increased use due to their cost and hygiene benefits. Engineers who design these tools usually specify brush DC or brushless DC motors. Here we compare these two options.
An early step of surgical power tool engineering is to determine whether the design will be disposable or reusable. Recent component design and manufacturing advances have rendered many single-use power tool designs for complex surgery a cost-effective option. Nowhere is this more apparent (or significant) than with today’s brush DC and brushless DC (BLDC) motors both of which have lower price points and higher performance than in the past.
Reusable and disposable surgical tools often have equivalent motor-performance requirements. However, their design life and cost requirements are vastly different. Reusable tools must often last hundreds or even thousands of surgeries — so must integrate premium components. In contrast, the components in disposable tools only need to perform for one surgery — which necessitates that these components be available in high volumes and at a competitive price.

Shown here is an exploded cutaway of a slotless motor from Portescap. Notice (in copper) the ironless rotor-coil windings. Also notice the brushes (on flat springs) mounted on the black motor endcap (the rightmost subcomponent in this illustration). Portescap sells this motor with either sleeve or ball bearings for the output shaft support.
BRUSHLESS DC MOTORS FOR REUSABLE TOOLS — BRUSH DC MOTORS FOR SINGLE-USE
Though they may be too costly for disposable power tools, BLDC motors offer top reliability — so are the most common motor type in reusable power tools. Brushless motors are capable of speeds up to 100,000 rpm over a long design life. Contact-free BLDC commutation (usually via magnetic Hall sensors or a sensorless drive with a brushless motor controller) limits all mechanical wear to that of the motor-shaft support bearings … so with precision bearings, these motors can operate at high rpm over (in some cases) hundreds or thousands of surgeries.
In contrast, DC-motor brushes (whether graphite or precious metal) physically contact the rotor’s commutators, so wear over time. That means these brushes are the primary limiter of brush DC motor life — with higher speeds accelerating wear. That’s acceptable in disposable tools, even some requiring high rpm … though ultimately the motors’ suitability heavily depends on the tool’s duty cycle and exact speed requirements.

Shown here is a cutaway of a Portescap Ultra EC 35ECS slotless brushless motor. The magnet on the rotor (in grey) is precision balanced; the PCB that controls the electronic commutation (green) is embedded inside the motor housing.
Depending on the exact design and materials, brush DC motor performance also varies. For example, certain coreless brush DC motors have lower inertia for higher performance regarding acceleration and efficiency than comparable motors of a different construction. Recall from a previous Design World editorial that most lower-cost brush motors have an iron core … but coreless motors have rotors consisting of only a coil and shaft. Besides the aforementioned benefits, these coreless motors also eliminate detent torque (cogging torque) for smooth rotation even at slow speeds. No wonder brush DC motors of this type are finding increased use in disposable power tools.
Depending on the exact design and materials, brush DC motor performance also varies. For example, certain coreless brush DC motors have lower inertia for higher performance regarding acceleration and efficiency than comparable motors of a different construction. Recall from a previous Design World editorial that most lower-cost brush motors have an iron core … but coreless motors have rotors consisting of only a coil and shaft. Besides the aforementioned benefits, these coreless motors also eliminate detent torque (cogging torque) for smooth rotation even at slow speeds. No wonder brush DC
MOTOR-POWERED TOOL COST-ANALYSIS EXAMPLE
Once performance requirements are met, cost is often the next-most critical design consideration. We’ve covered how motors with a BLDC construction are relatively expensive … and in fact, the controllers they require (for commutation) and embedded electronics (for tracking rotor position) further increase overall system cost. The additional cost for these subcomponents (along with premium bearings, dynamic shaft seals, or high-grade magnets) can be justified where the application demands top performance … but not usually for disposable tools.

With disposable tools, cost incurred for a single surgery includes the full purchase price of the tool. With reusable surgical tools, a small portion of the purchase price is amortized for each procedure … although the cost of re-sterilizing these power tools incurs additional cost that should be considered in per-surgery cost assessments.

A costlier reusable tool (perhaps using a higher performing BLDC motor instead of a low-cost brush DC) will necessitate uses in more surgeries to be less expensive than a disposable tool. Sterilization costs also increase the number of procedures needed to break even — so much so that disposable tools are in some cases preferable no matter the number of surgeries.
In contrast, DC motors with their brushbased commutation only need a cost-effective PWM circuit for speed control … and motor-construction advances have made for unprecedented performance increases with only negligible cost increases. That’s made today’s more advanced brush dc motors particularly suitable for short-life surgical tools.
Refer to the charts accompanying this article for average-cost analyses of various tool options. These don’t account for how high-end reusable tools typically offer superior performance and additional capabilities. Such factors may make tools based on BLDC motors the best design choice for surgeons and patients even if a breakeven surgery quantity isn’t reached. However, the analyses also don’t account for one unpredictable cost of the sterilization process — the potential risk of infection from inadequately sterilized reusable tools. Wellenforced sterilization methods and tool design features can certainly facilitate proper and reliable sterilization, and sterilization has been proven safe and effective. However, inadequate tool sterilization between surgeries is a risk that should also be considered by surgical-tool design engineers. Disposable tools can be sterilized and packaged by the tool OEM, and this approach boosts patient safety for some applications and hospital systems.

Case in point: Consider a new design being developed by an R&D team at a medical-device company. This is a handheld surgical power tool that can cause grave complications if it stops working during a procedure. The engineers prefer a disposable tool, but a reusable tool may be acceptable. The battery-powered device requires that the motor be 80% efficient (or better) and run off 6 to 9 V at 1.5 A (maximum). The motor (not to exceed Ø17 mm) must deliver 5 mNm (continuous) at 15,000 rpm. The procedure is cost sensitive, so the motor mustn’t contribute more than $20 to the cost of each surgery.
The engineers first engage with a motor supplier offering both brush DC and BLDC motors as well as extensive experience in the surgical power tool market. The supplier suggests motors that are Ø17 mm or smaller and best matching the design’s performance and power requirements: Both motors satisfy the 5 mNm torque requirement, but the maximum continuous torque rating for the DC brush motor is only slightly higher at 5.7 mNm. This reduces motor life — though not enough to be a concern for a single surgical procedure. The bigger problem is the 15,000 rpm speed requirement, which is higher than the brush DC motor’s top speed. Though possibly acceptable for a single procedure, it increases the risk of failure during surgery. The cost of the motor is low enough that it can be thrown away after each use.
The BLDC motor can easily meet the speed and torque requirements and could continue to do so for many surgeries. Efficiency doesn’t quite meet the 80% target, and the price is much higher than $20 … so for the BLDC motor to be viable, it’d require use in at least eight surgeries.

The increasing popularity of disposable surgical power tools (such as surgical staplers) has prompted more demand for higherperformance brush DC motors. These are more suitable than BLDC motors where cost effectiveness is the top design objective.
In short, the design constraints force the design engineers to choose between a brush DC-motor-based disposable tool or a BLDC-motor-based reusable model. A reusable brush DC motor isn’t viable (because of the unacceptable risk of failure if used in more than one surgery) and cost precludes a disposable BLDC motor model.
The top design question then becomes: Is the potential failure of a brush DC motor in its first surgery (due to high rpm) acceptable? If not, then engineers can reduce the speed requirement — and build lowerperformance tool. The other option is to build the reusable tool and accept its lower efficiency. They will also have to design the rest of the tool to be sterilizable and will need their end users to sterilize the tool between uses — two factors that increase the total cost per surgery.
BRUSHLESS MOTORS IN ROBOT WHEELS

ElectroCraft Inc. now offers an MPW wheel drive built around a high-torque-density brushless dc motor with a heavy-duty integrated planetary gearbox. These motion components mount inside the hub of a lightweight aluminum wheel with custom tread. Designed for mobile robot applications, the MPW combines performance with high efficiency, quiet operation, and long life.
The MPW52 (150-mm wheel) delivers up to 12.4 Nm at 2.4 m/sec while carrying up to 68 kg per wheel. The MPW86 (200-mm wheel) provides a peak torque to 35 Nm at 1.9 m/sec while carrying up to 227 kg per wheel.
The MPW provides a complete motorized wheel-drive solution for mobile platform OEMs, eliminating the need for robot builders to design a solution using disparate components from different suppliers. The ElectroCraft MPW is engineered for integrated efficiency ... as the motor, gearing, hub, wheel assembly, and optional accessories provide a single-source solution for efficient battery-powered AGV and mobile-robot applications.