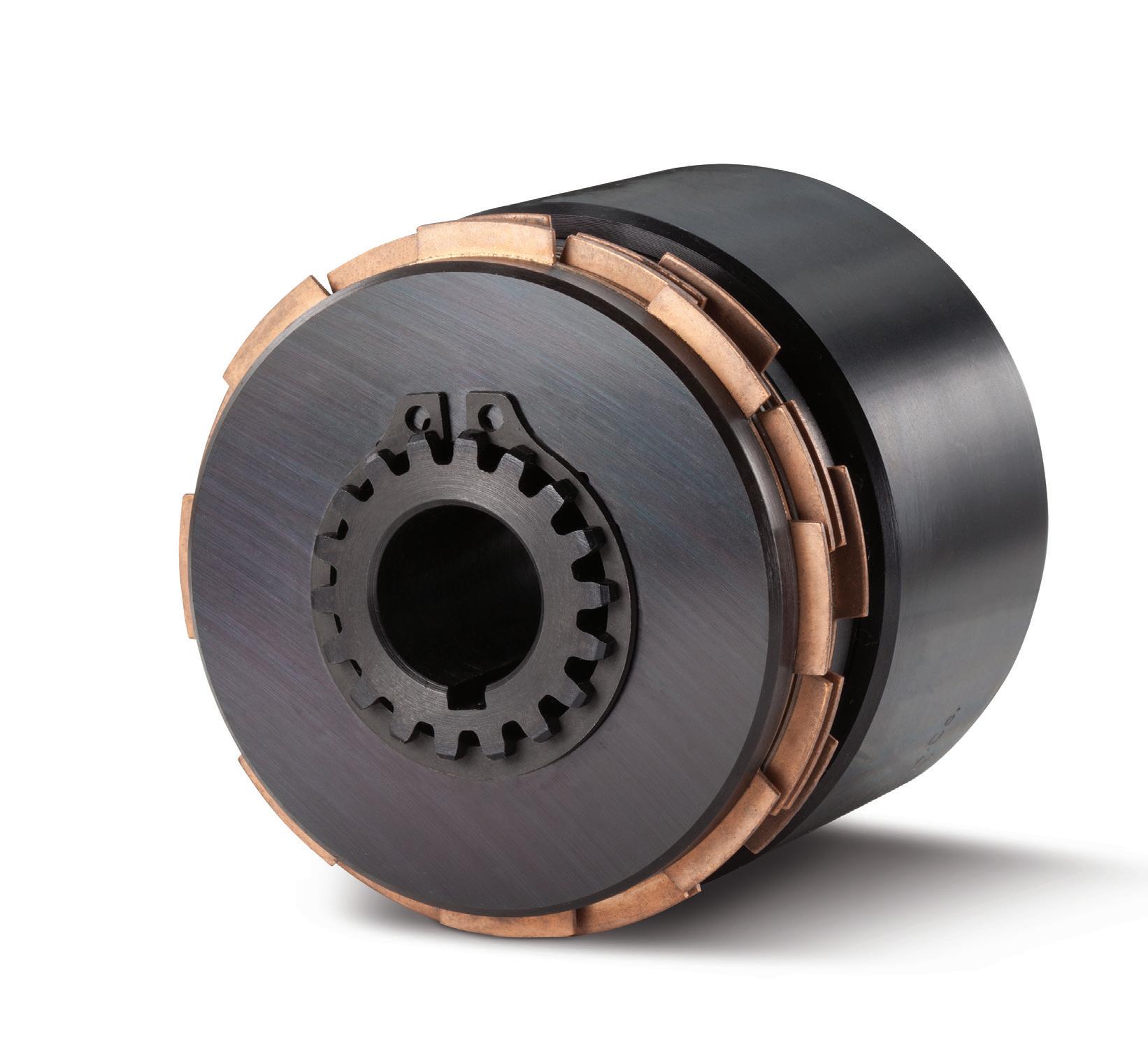
1 minute read
Retaining rings keep assemblies together
Motion system designs make use of retaining rings in everything from electric motors and gear retainers to solenoids to aircraft to door handles and sports equipment. These fasteners hold together components on a shaft or in a housing when installed in a groove. In fact, the automotive industry may make the most use of retaining rings, especially for assemblies in air bags, timing-belt pulleys, radiator hoses, turbo chargers, door locks, carburetor assemblies, drive shafts, and brakes.
Used in an array of oil-and-gas and other industries’ designs, tapered section rings have decreasing thickness from center to ends. They mount axially or radially, and the taper keeps full contact with the installation groove.
Common in assemblies for lawn mowers, hand and power tools, agricultural machinery, nuclear equipment, and even computer equipment, constant-section retaining rings have a constant width around the circumference of the ring. When installed, these rings do not maintain uniform contact with the entire component. They take on an elliptical shape and make contact with the groove at three points. Spiral retaining rings go into housings or on shafts with full contact with groove or component. Their grooves are shallow, so have less load bearing capability. So, spiral rings often go into applications that prioritize full contact with the retained component or lower axial profile.

MAXITORQ AHA25 clutches and brakes from Carlyle Johnson are rated from 15 lb-ft dynamic to 60 lb-ft of static torque ... and torque can be regulated by adjusting system pressures. These components have a stationary cylinder assembly mounted on deep-groove ball bearings to accommodate thrust loads. Notice the retaining ring on the face of the unit.
Spiral rings find use in torque converters, speed reducers, lamp assemblies, clutches, hinge pins, home appliances, robotic toys, pumps, couplings, valves, hydraulic equipment, and photography equipment. They don’t have protruding ears to interfere with mating components; they also eliminate the need for machining and threading. Spiral retaining rings don’t necessitate special tools for removal and come standard with removal notches for extraction.
When selecting a retaining ring for an application, factors that dictate which retaining ring is most suitable include application environment (including temperature, speed, and thrust) as well as critical dimensions (including the assembly’s housing or shaft diameter and the installation groove’s dimensions.
In fact, maximum thrust is one of the most critical application parameters, as it dictates whether there’s risk of groove deformation or ring shear. Applications that run in corrosive environments also may also need retaining rings made of specialty material.