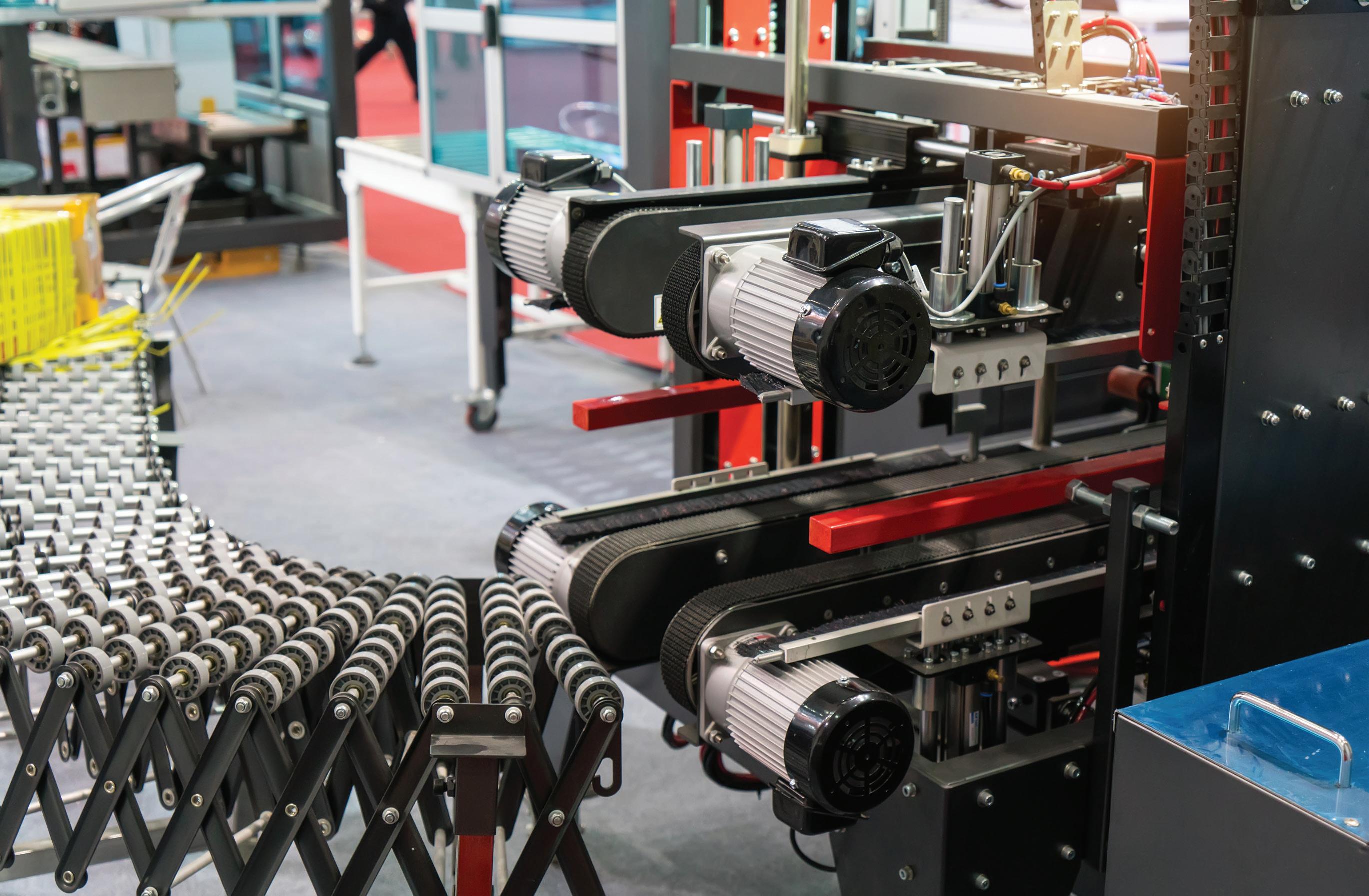
3 minute read
Conveyor functions as varied as applications
Conveyors are core to material handling … for transporting packages as well as improving workflows and even interfacing with other automated systems. Just consider the requirements placed on zero-pressure accumulation conveyors — systems with precision controls to prevent products from bumping or even touch while conveying for the prevention of damage to expensive workpieces and fragile products. Such designs require IoT connectivity for data sharing as well as precision motion and optimized efficiency.
These and other conveyors for discrete product transport benefit from customization to satisfy requirements — including support frames; chain and belt size, morphology and material; controller, drive, and motor or motors; mode of engagement with the drive; encoder, vision, and switch feedback; tracks, bumpers, and gates; and HMIs and plant-level IT integration.

For example, warehouse automation requires ultra-fast sorting and tracking … and conveyors with servomotor functionality integrated with inspection stations fitted with machine vision. Or consider pharmaceutical manufacturing — now a trillion-dollar industry and expected to grow to address COVID-19 — with especially stringent regulations. Here, conveyors must deliver top-notch warehouse automation functions and have stainless and aluminum parts to pose no risk of contamination to expensive pharmaceutical products such as pills. Likewise, medical-device manufacture must adhere to FDA regulations that dictate equipment-sterilization schedules so conveyors in these applications withstand harsh washdowns.
Another example is how some highly engineered flat-top conveyors streamline still other material handling. Among the many varieties of conveying systems, flat-top conveyor chains perform like belts but can also convey, transfer, accumulate, meter, elevate, and lower items of various sizes and shapes. The VersaFlex conveyor from mk North America is one such flat-top chain conveyor system for complex design needs. It replaces the company’s SBF-P 2254 conveyor line … and excels as a pallet-handling conveyor system in many industries. Conveying the product on a pallet achieves a more streamlined approach to material handling which in turn maximizes manufacturing productivity, flexibility, and product quality.

The DC Platform from Interroll is a series of 24-V or 48-V components to build power-roller-based conveyors for operation flexibility. Installations based on these offerings can precisely position totes and goods to complement robotics … or work as conveyors commissionable without a PLC. The 48-V systems cut the need for power supplies in half (compared to comparable 24-V installations). The RollerDrive EC5000 in the lineup comes in 20-W, 35-W, and 50-W versions for the transport of light or heavy goods. Other large-diameter, IP66, Deep Freeze, and CANOpen-connectible roller options abound.
Consider another way in which conveyors improve upon traditional arrangements — in production. Here traditional work areas are separate from parts warehouses — and external logistics integrate only with warehousing operations. In some instances, automatic guided vehicles (AGVs) might travel the plant floor and feed assembly or finishing lines at regular intervals. Then personnel at stations execute fairly specific operations — picking pieces and finishing assemblies, for example. But automated plants today are looking to satisfy end-user demand for increasingly customized product. Just consider how amazon.com offers a huge array of choices for nearly any product type imaginable. That demands far more items in any given warehouse than in the past — and facilities that can handle the exponential rise in item numbers.
Here and in similar operations with comparable complexity, overreliance on manual labor adds too much cost into the final delivered-product cost. Using AGVs to supply all the items or parts to work or assembly stations would quickly choke even expansive operations with unsafe and insufficient traffic. Totally automating finishing processes using robots is often unsuitable or impractical.

VersaFlex coveyors from mk North America are available in three different chain width sizes. They can also convey small pallets. Key benefits include the ability to easily and cost-effectively integrate into existing production processes and expand as needed.
Conveyors are a great solution to these limitations. Conveyors free personnel from rote jobs so they can focus on more complicated factory tasks — supplanting bins, AGV part racks, and a mishmash of unergonomic pallets and boxes around a work cell with more efficient presentation of parts to be processed.
Pioneered by the Toyota’s World Class Manufacturing (WCM) concept, conveyors complement use of what’s called the Golden Area — the immediate area around a worker in which no time is wasted. In addition, conveyors support operations with exceptionally numerous item variations and delivery requirements as well as those that need automated order tracking.