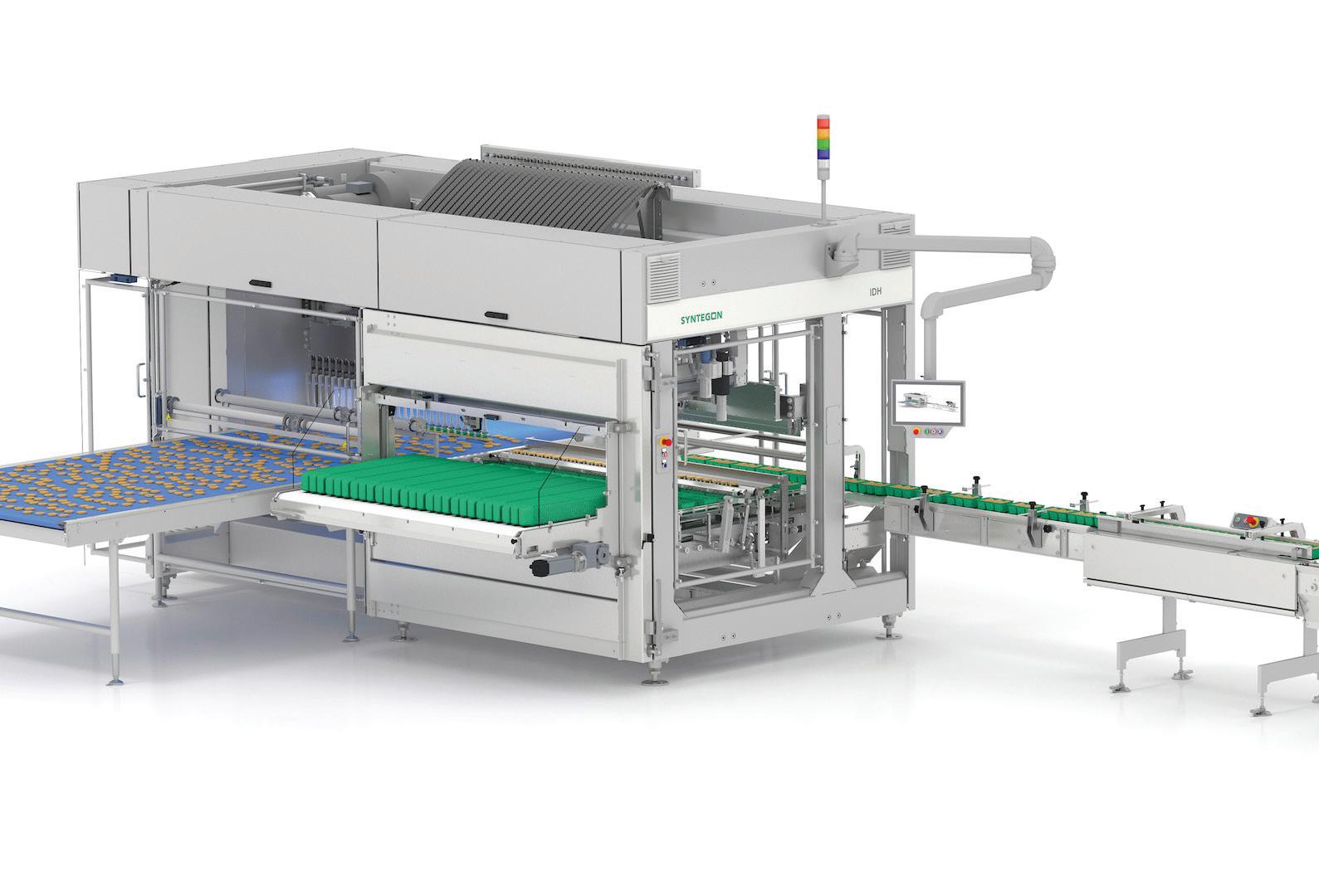
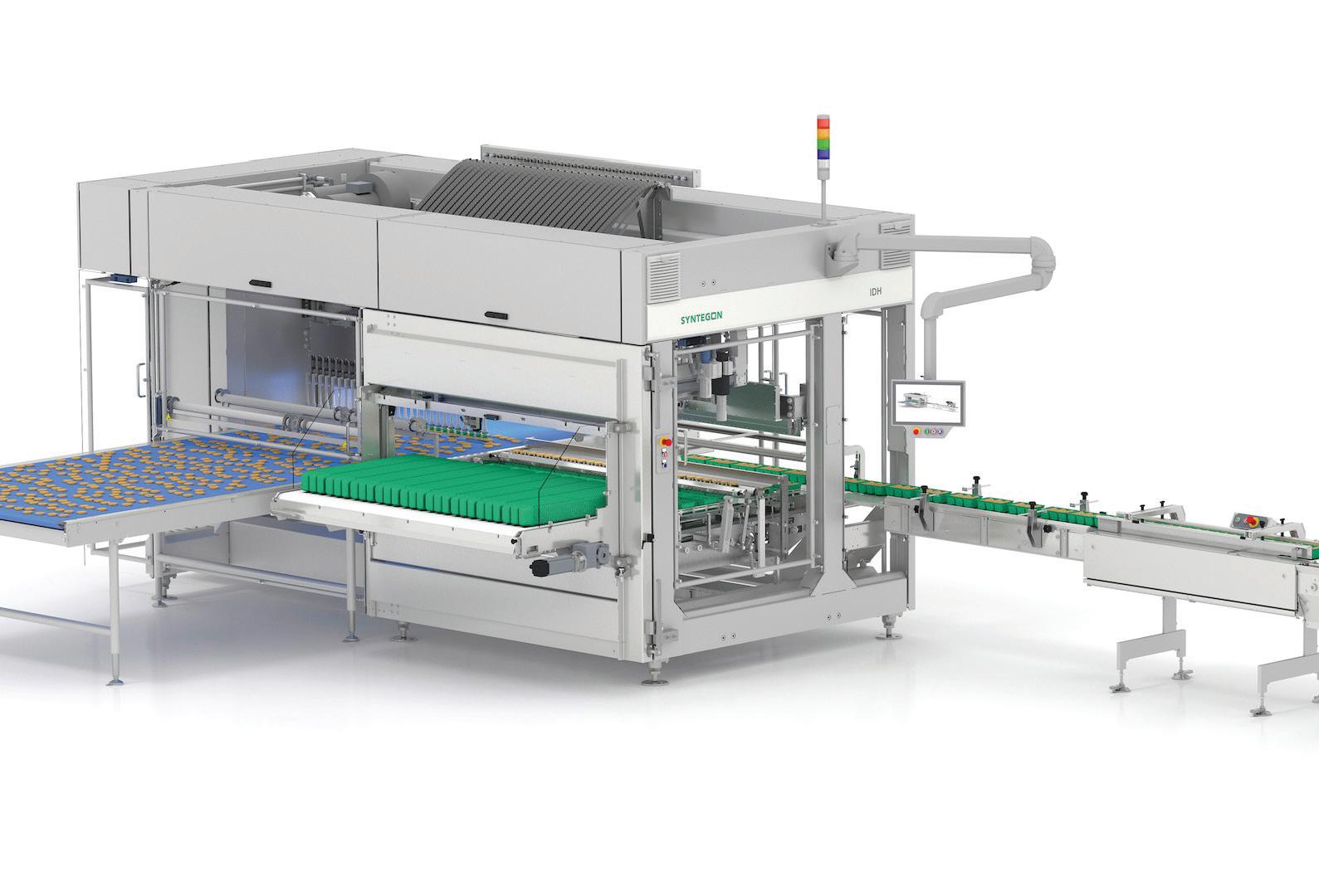
packaging automation in perspective
Packaging machinery uses cutting-edge automation, and it’s no wonder. Facilities that parcel products need to deliver high throughput, but modern consumers demand smart packaging in the form of no-fuss containers that protect everything from M&Ms to patio furniture. What’s more, there’s a continuous drive to customize packages and let consumer-facing companies wrap products for bulk distribution, single-item sales, and everything in between.
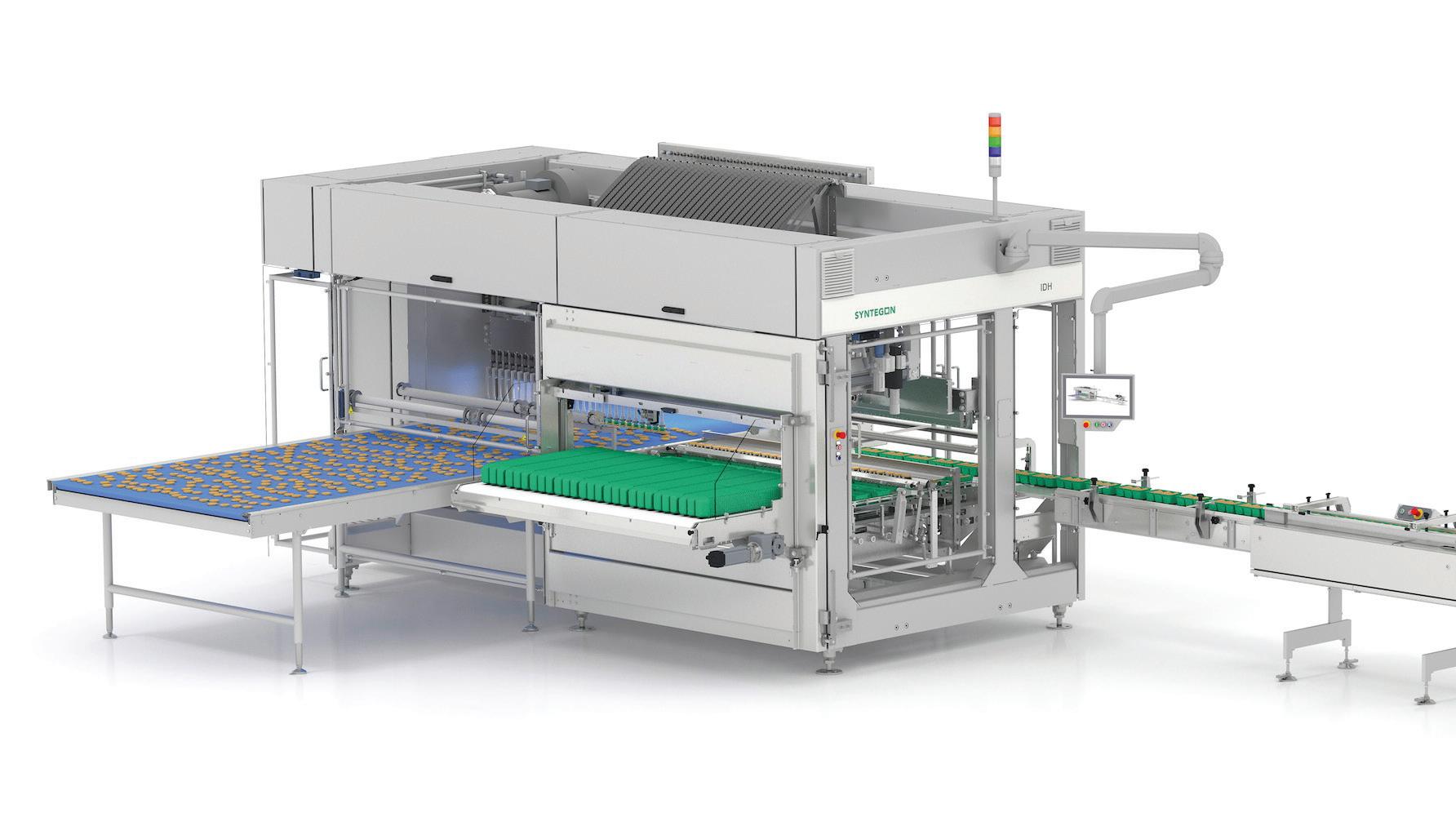

To satisfy these design objectives, packaging machinery over the last decade has become increasingly adaptive. That’s been evident in a range of motion components and fully integrated designs at recent Pack Expo events. More specifically, the newest adaptive machines are:
• Modular (so they can be reprogrammed if not physically reconfigured on the fly)
• Fitted with HMIs (to let operators feed high-level operational data into machines as needed)
• Based on components that satisfy the efficiency, safety, and networking standards of multiple regions.
At the core of all these sophisticated elements are motion-control and power-transmission mainstays. Most all packaging machines include mechanical frame and powertransmission elements (including linear motion drives and guides); motors and drives; and motion controllers not unlike those used for the last 40 years in mechanizing and automating equipment. However, the accuracies and other performance characteristics of these machines’ power-transmission elements have steadily evolved and improved to complement the latest servomotor offerings (synchronous ac and otherwise) as well as increasingly advanced electronic control capabilities.
Though the accuracy and repeatability requirements of packaging equipment can be more modest than those for medical or semiconductor manufacture, the need for throughput is unrivalled — with many machines processing thousands of items per minute. Accompanying this need for high output is a need for reliability and consistency. That’s true whether discrete product pieces are of some consistent mass or (in the case of filling and packing) variable.
Consider the retail-ready packaging that some machines assemble — the product-packed pallets increasingly common in club stores such as Costco and BJs. The machines that put these shelf-ready displays together rely heavily on servo-driven stations and robotic arms that usually interface a conveyor. In a typical setup, the conveyor takes product to a station that orients individual units for grouping; then the modules travel on the conveyor to subsequent stations that group packs into patterns that let retailers use larger cartons for shipping, stacking, and displaying items once they’re in stores. Setup of such machines is almost always through HMIs.
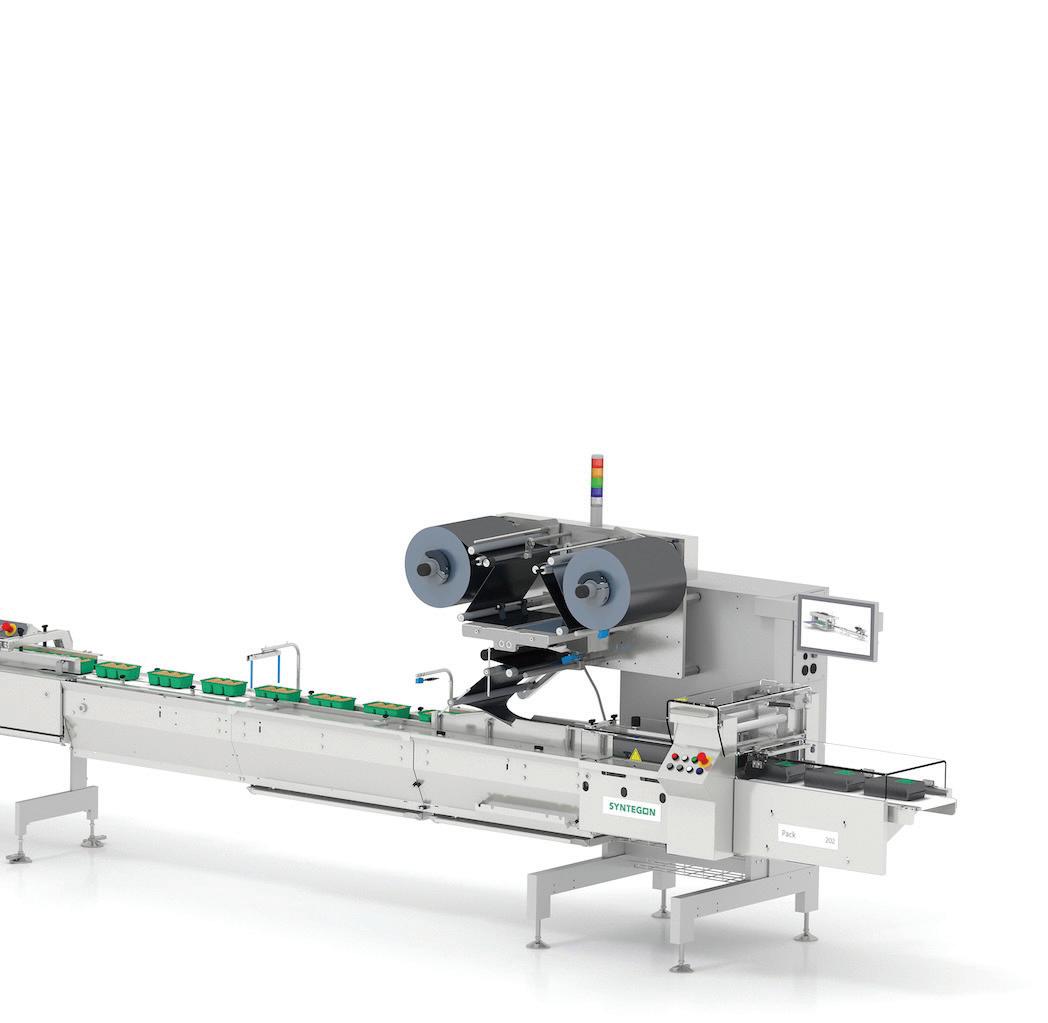
In many cases, next-generation machines capable of assembling retailready displays must also incorporate sensors and networking fast enough to log dozens of mixed stock keeping units (SKU product codes) per minute.
For example, a maker of pita bread and sandwiches might employ servodriven cartoning machines to boost productivity and flexibility. For this application, vertical cartoner arrangements can assemble cartons having different item counts. For large retailers and club stores, this might involve four, six, 12, and 14-count cartons … necessitating a machine design that lets operators (via a touchscreen HMI) make speedy changeovers to different carton sizes — typically a dozen or more times a week. With modern drives and controls, such changeovers can take as little as 10 to 15 minutes.
In many cases, even the OEMs who build such cartoner packaging machines benefit from the automation and reduced mechanical part counts of servodrive-based equipment.
Considering the conveyors of packaging applications
Automation in packaging has reduced labor costs and boosted efficiency for large makers of consumer goods. Now, smaller operations up and down the supply chain have also found ways to leverage automation’s benefits.
Just about any product made of metal, food, cosmetics, medical supplies, plastics, or boxes moves on a conveyor during manufacture. No wonder that conveyors come in all shapes and sizes — from belt widths of less than 2 in. (for moving extremely small parts) to several feet wide for transferring bulk substances.
Conveyors are classified by both their conveyance media and application: Some conveyors serve to transport bulk or discrete product in a steady stream with little interaction with transported goods along the way. These are ruggedized units optimized for high throughput. Slightly more demanding conveyor installations shuttle product between locations or machines. Still more demanding are

conveyors to move materials into or out of machines or stations. These actually require positioning capabilities to ensure proper handling of product. The most demanding conveyors run workpieces and other goods through assembly or other workstations and machinery without break. Many such conveyors for this demanding task employ custom workpiece pucks to steady product while machines perform work on the items.
Conveyors for moving arrays of discrete product — applications associated with motion control — take various forms. Some employ thin flat belt made of engineered fabric with nylon, PVC, styrene-butadiene synthetic rubber (SBR), or other durable synthetic materials.
Specially shaped motor-driven pulleys engage (with tensionmaintained friction) the conveyor belt and make it (and any product riding on it) advance. Benefits of this design include simplicity and costeffectiveness; thinness of conveyance medium for easier transfers off and onto the conveyor-belt ends
even for very small objects; the ability to withstand a wide range of temperatures; and customizable surfaces — for easy release of baked confections, for example.
In other instances, conveyors consist of a series of both unpowered and powered cylindrical rollers. These roller-based conveyors work best for transporting flat-bottomed objects such as carboard boxes or molded part pucks.
Simple conveyors with only unpowered rollers work as manual conveyors (to let personnel push items along the low-friction conveying surface) or gravity conveyors which incorporate downward slopes — often as diverting-conveyor offramps to feed items to their final workplace or collection destinations. Here a competitive conveyor option is the ball-table conveyor — studded with freewheeling spherical rollers to let conveyed product freely glide along. The motorized rollers on roller-based conveyors can either couple to a gearmotor on the conveyor flank or directly integrate motors called drum
motors inside their cylindrical bodies — in turn usually made of steel or (if intended for washdown settings) stainless steel.
Conveyors to position items with moderate accuracy (say, for simple spacing of boxes) might employ only motorized rollers. In contrast, systems or sections of conveyor with laxer requirements (or relying on peripheral systems for final positioning functions) might gang a few unpowered rollers to each powered roller via cords or bands made of round polyurethane belt. These bands loop around and nestle into grooves on the powered and unpowered roller ends; tension keeps the round bands firmly set in their grooves and facilitates the transmission of power from motorized roller to ganged passive rollers.
Smart transport and planar motor systems for packaging
Linear-motor conveyors, also called smart transport systems by those who aim to differentiate the offering, are costly but enable very sophisticated applications. Some modular linear-
LEVEL U and then
Constant Force Lead Screw applies uniform pressure to the nut at all stages of travel along our quality CNC rolled lead screws. World class NEMA motors combined with an integrated lead screw make for one of the most accurate lead screw assemblies on the market.
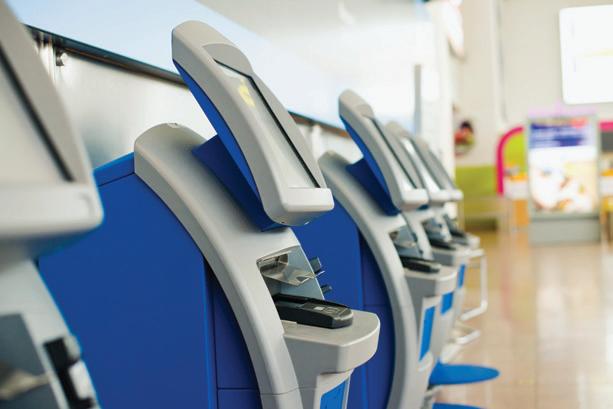
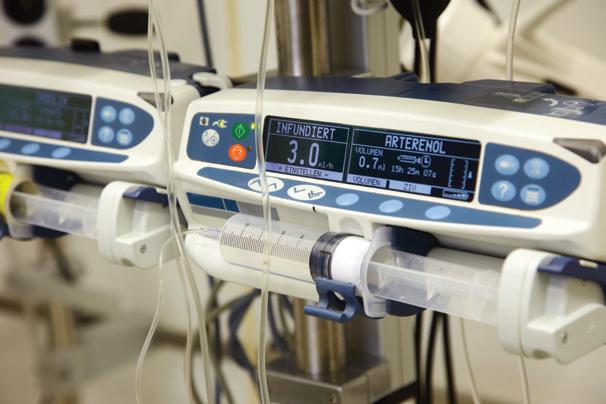



Our miniature ball screw assemblies combine fine leads with small screw diameters, and utilize a compact internal ball return system to yield high precision linear motion for a range of small-scale applications. In addition, our ball screws are precision-rolled, making them a critical asset to laboratory machines, medical devices, and mechatronic applications.
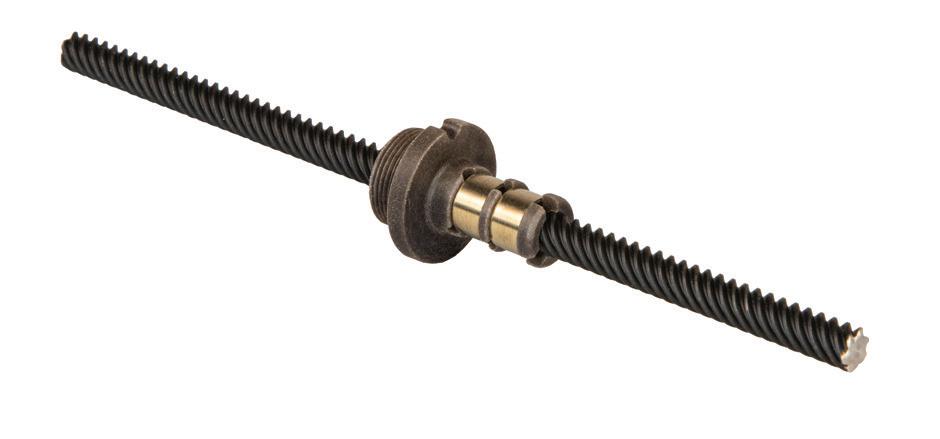
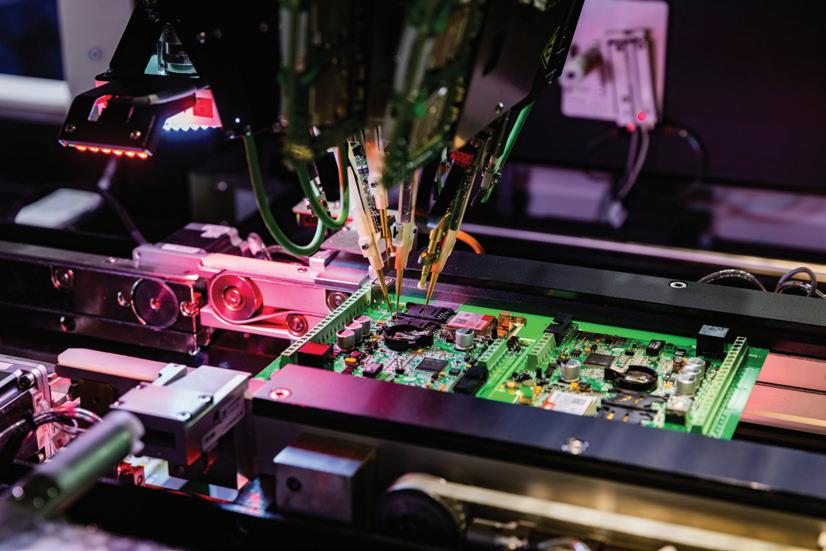
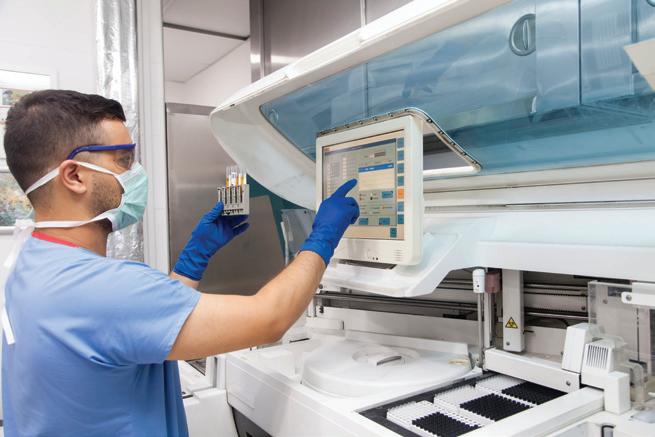
packaging oem
transport systems can trim machine footprints by half when used to replace indexing and conveying equipment.
The movers on some such systems can travel independently of one another or in groups along several customizable rail systems. High dynamics and precision help the system excel in gapping and diverting applications — and a new hygienic version is aimed at pharmaceutical, biotech, packaging, and food and beverage environments.
Modular linear transport systems are not designed to replace other conveying systems. However, traceability with the system can reduce the scans required for each piece through an operation. Because movers are mapped as individual servo axes, controls never lose track of items being transported. Such
traceability in traditional architectures can require innumerable scanners ... so the component and labor reductions of intelligent transport systems are worthwhile in some cases.
Other options for conveyance of specialty goods are two-axis airbearing stages and planar motors. Air-bearing stages suspend the carried load on a cushion of air and for motion rely on linear motors— often with an ironless forcer design for smooth actuation. Driving is typically centered near the center of mass to maximize the straightness and minimize the angular errors of each motion. In contrast, planar motors use the electromagnetic behavior of its motors for both the movement and suspension of loads … which is why they’re occasionally called magnetic levitation or maglev stages. Some such
systems levitate the magnetic movers with six degrees of motion up to 5 mm above planar motor tiles.
Flexible packaging evolution
Future packaging machines will also be judged by how well they integrate into so-called connected industry concepts. Here, the idea is to let design engineers build machines and networks to connect operational technology or OT — the drive, control, and even process and manufacturing components and software that they integrate everyday — with those of information technology or IT … here, the managerial, sales, ERP, supplychain, and inventory tools of an organization.
Several motion-component suppliers have over the last 15 years purchased or developed software to
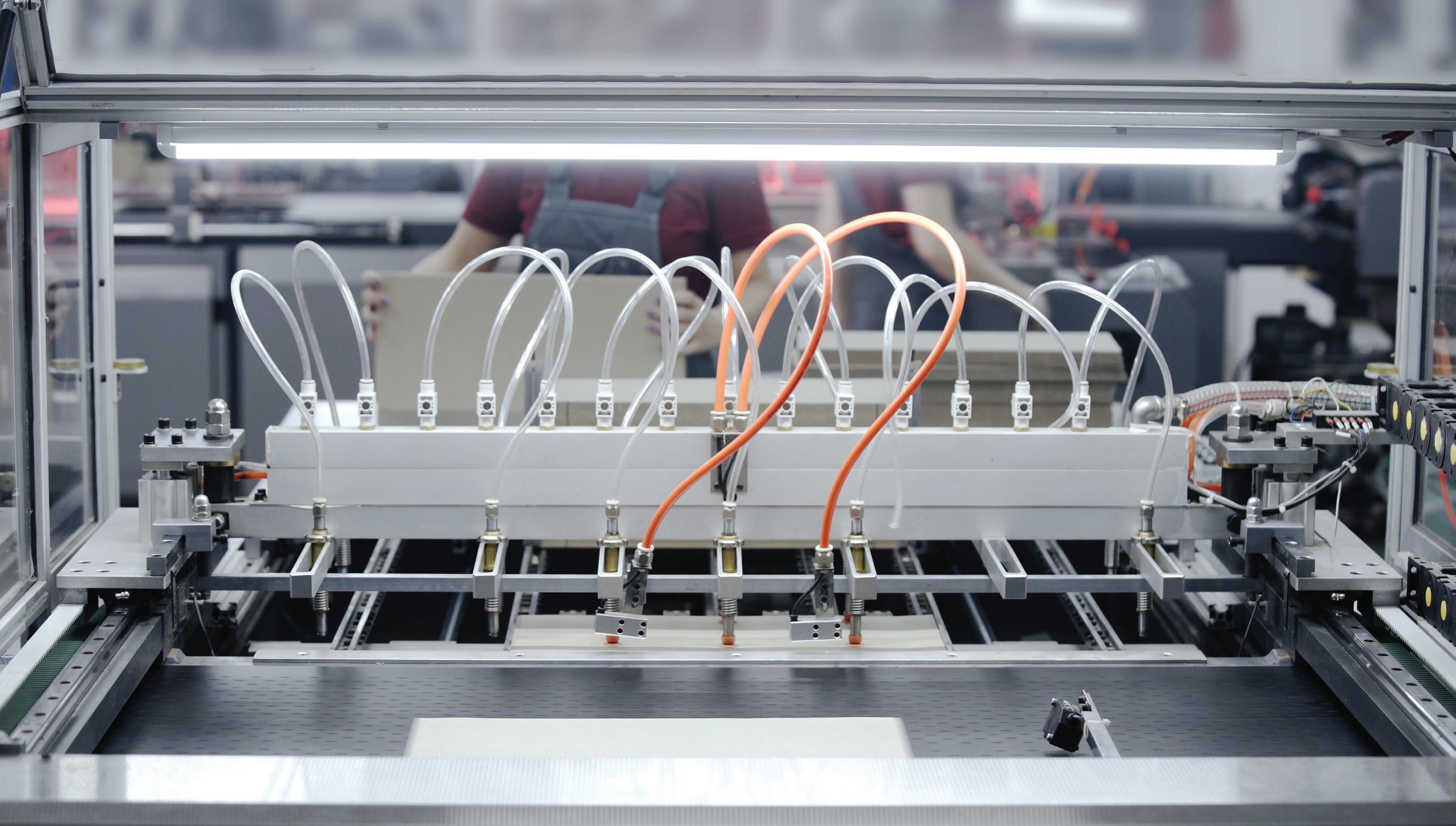
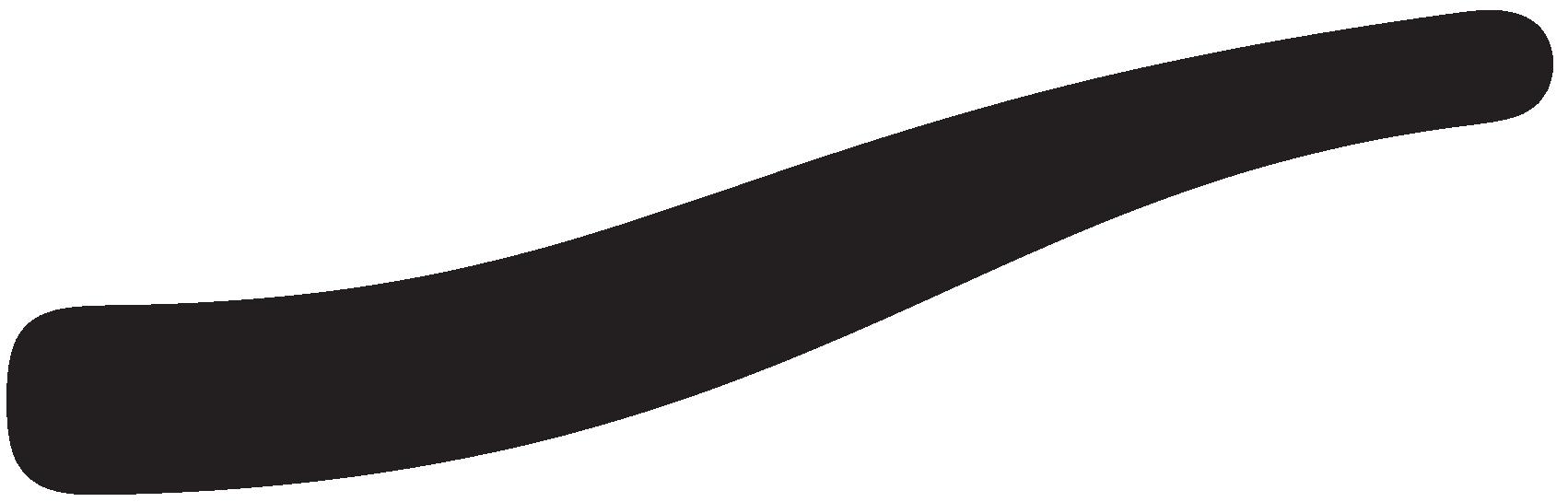


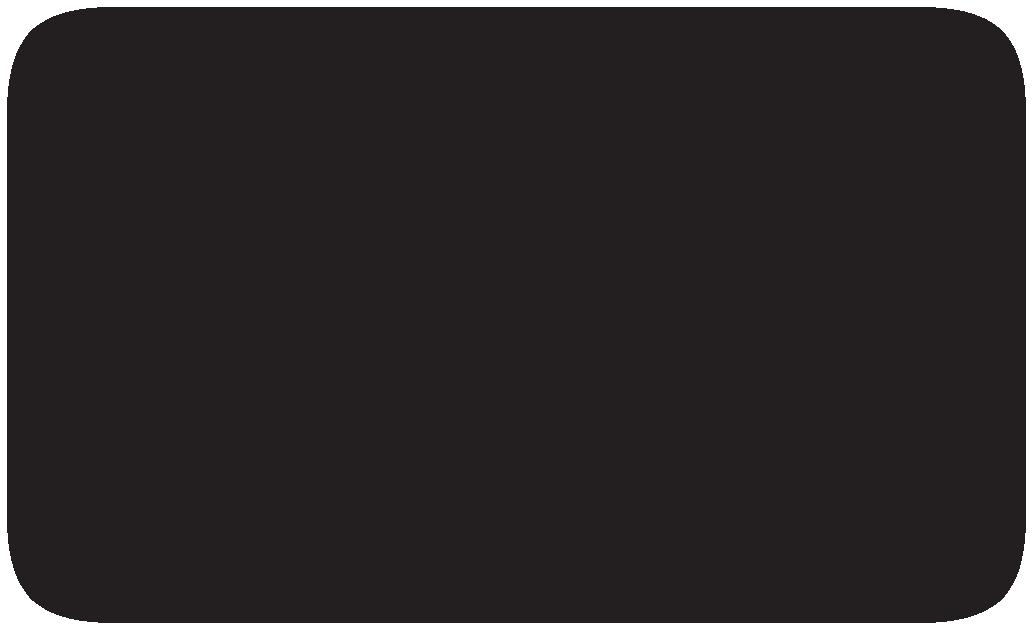
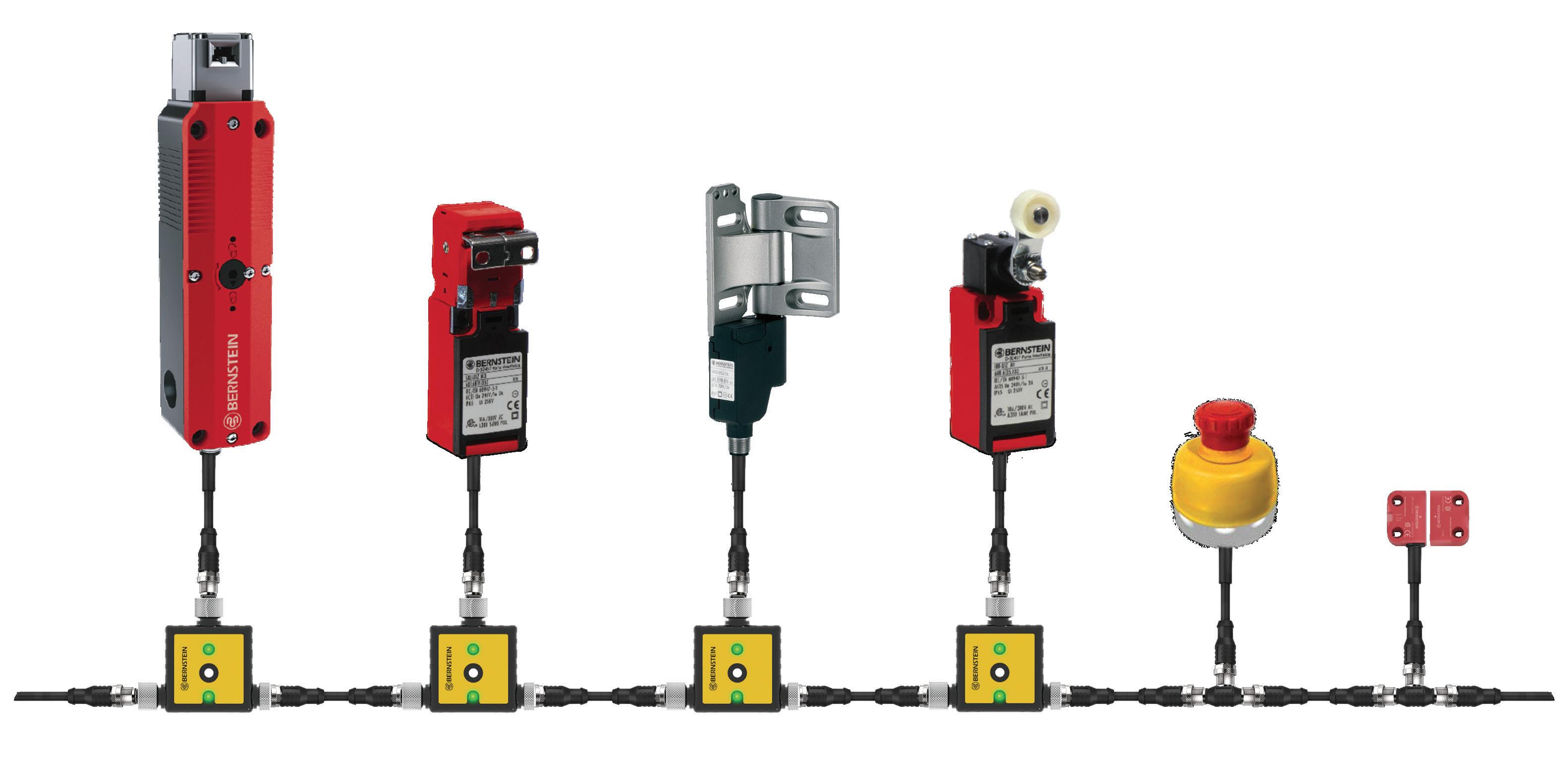
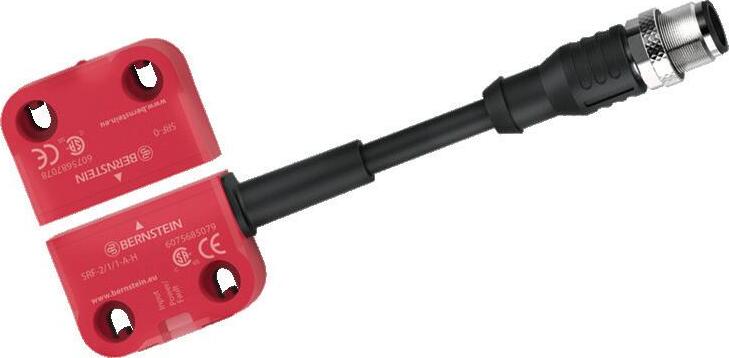

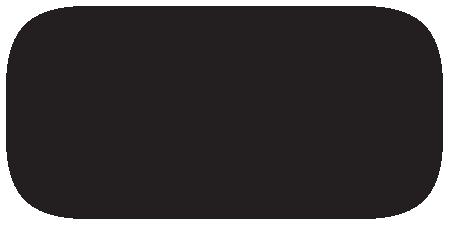
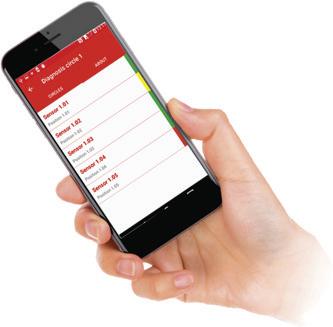
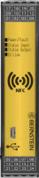
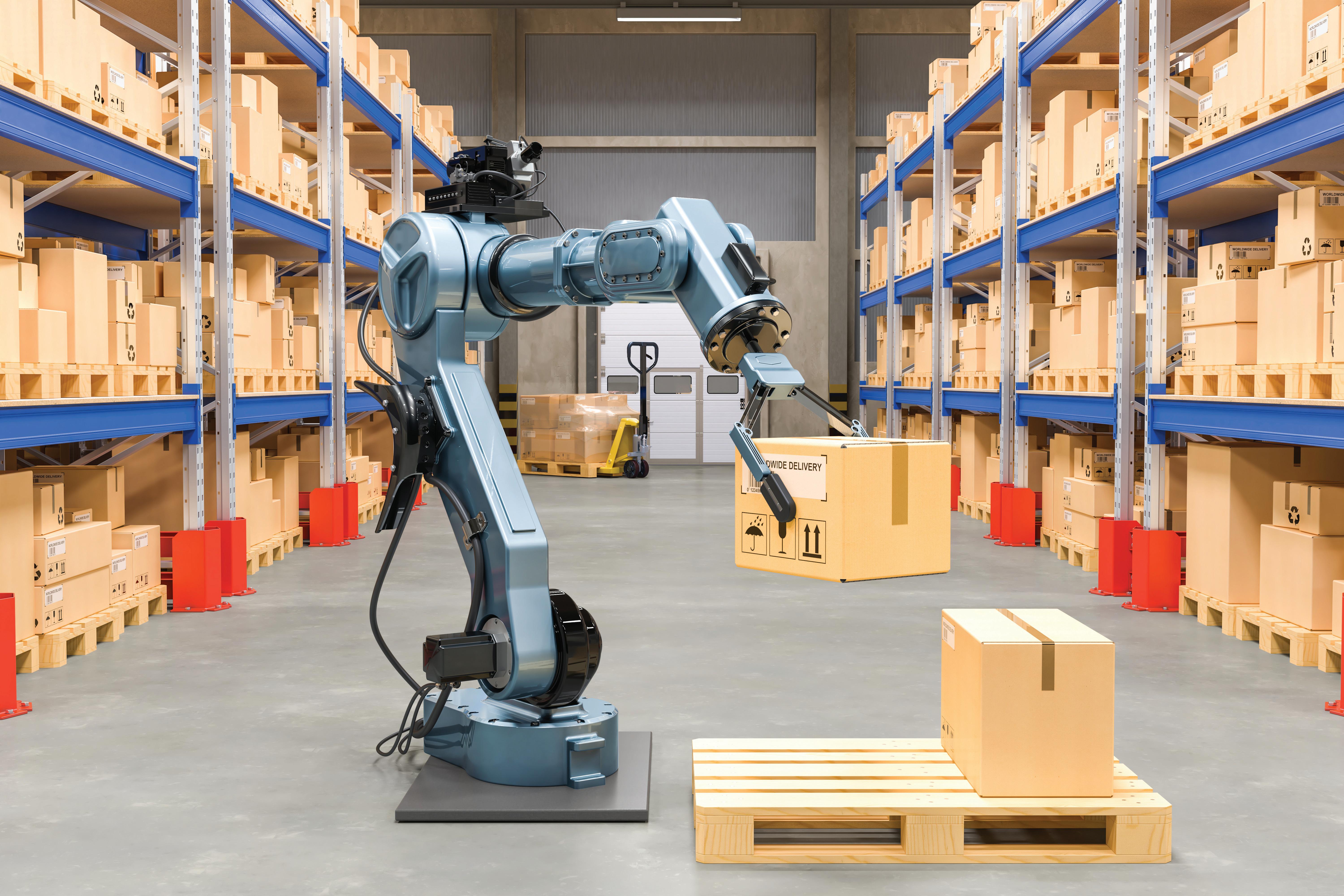
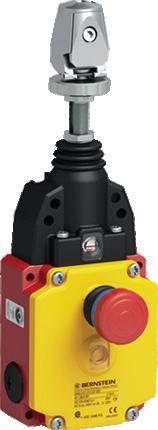

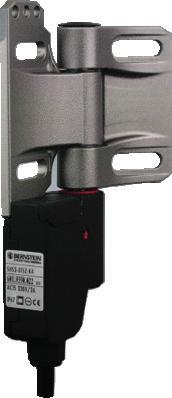


let packaging-plant management and ERP-level data dictate what happens on factory floors. Others have established partnerships with Cisco and similar companies to offer these functions to OEMs and end users. Much of the integration here uses Ethernet to connect to IT data for IT/ OT convergence — relevant to many industries but particularly beneficial to packaging for the regulation of output to better meet demand … as well as product safety through tracking.
Formats for individual products— stand-up pouches, child-resistant (CR) packaging, anti-bacterial wraps, multifunction container lids, and custom-sized cartons — also continue to proliferate. In fact, market reports from the Flexible Packaging Association, a trade
association for converters of flexible packaging and industry suppliers, global use of specialty packaging has grown unabated over the last decade and now exceeds $30 billion. That’s thanks to better automation as well as advances in materials and processes. For example, some OEMs that build form-fill-seal machines for pouch products are switching from heat sealing to ultrasonic sealing, as the latter is more forgiving and efficient. Ultrasonic welding also improves beverage packaging. One technique from Germany-based Xolution (not to be confused with OXO) ultrasonically welds polypropylene lids to aluminum cans for a portable mug design that otherwise lets beverage companies can drinks by traditional means. OEM
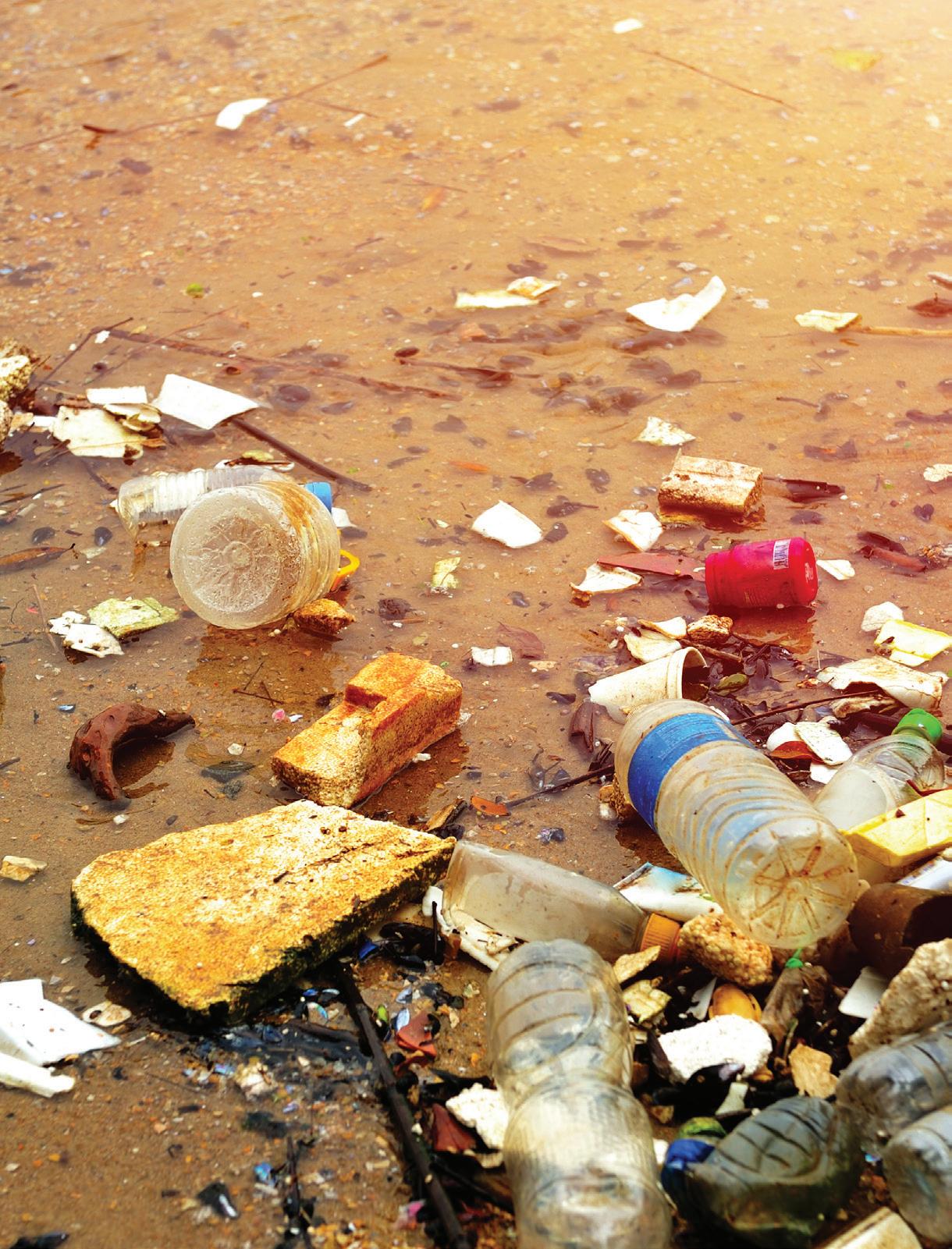
The SMART Safety System
This system offers plug-in convenience allowing up to 32 switches to be run in series. The system features redundant cascading OSSD outputs which eliminates the possibility of fault masking (TR24119) and offers superior diagnostics and communication via IO-Link, NFC or PLC.
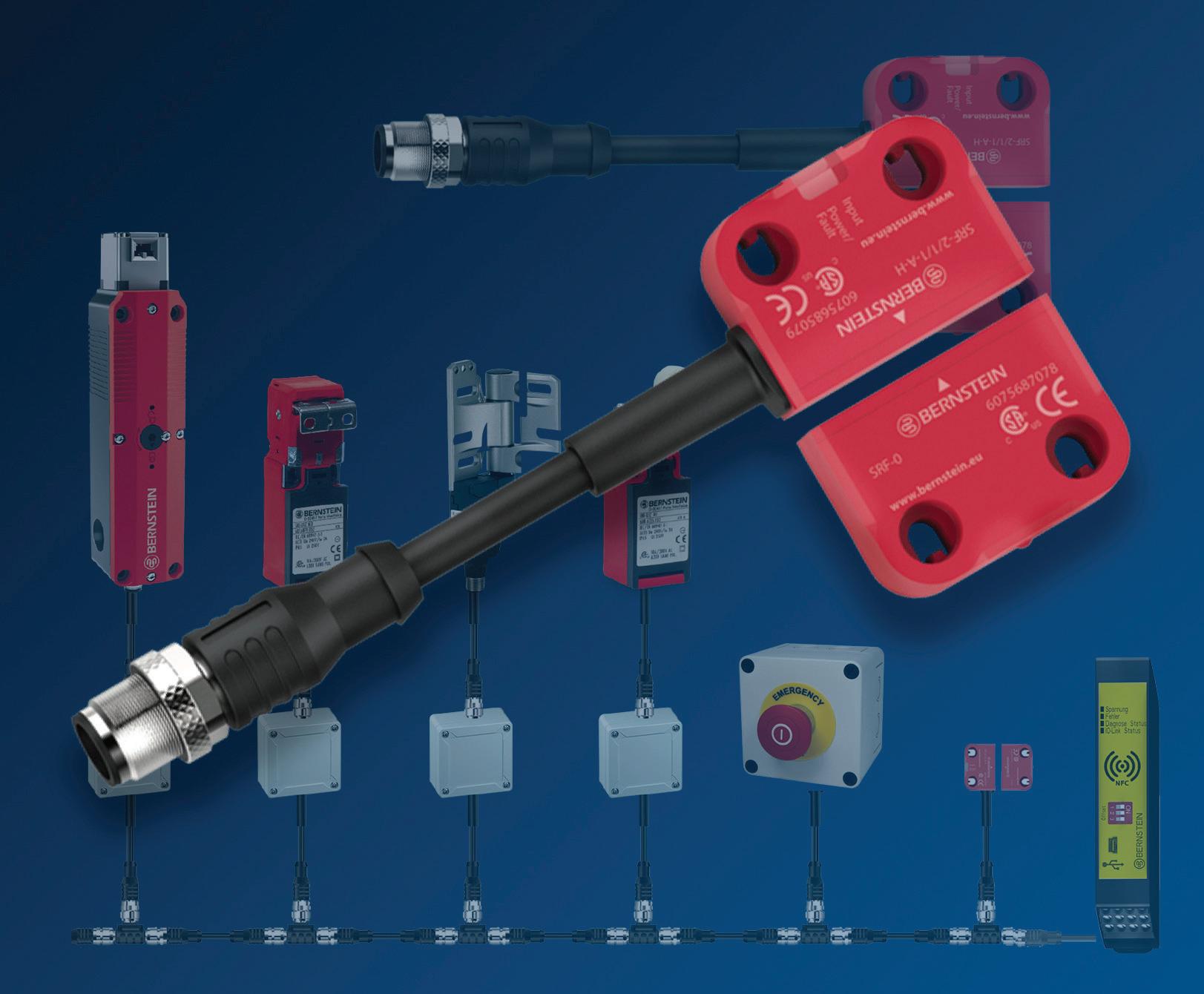
908-806-9400
908-806-9490 (FAX)
info@altechcorp.com
www.altechcorp.com
