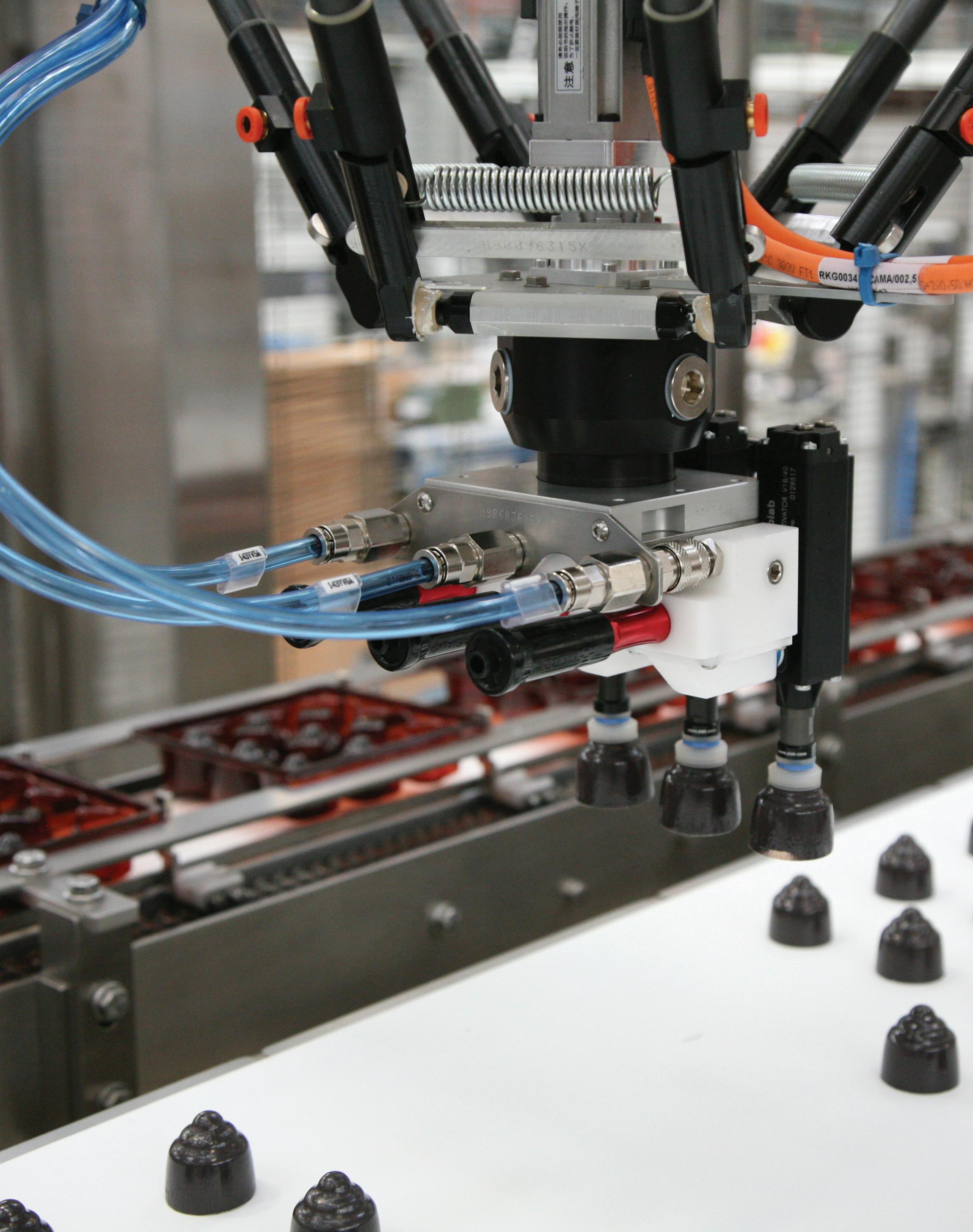
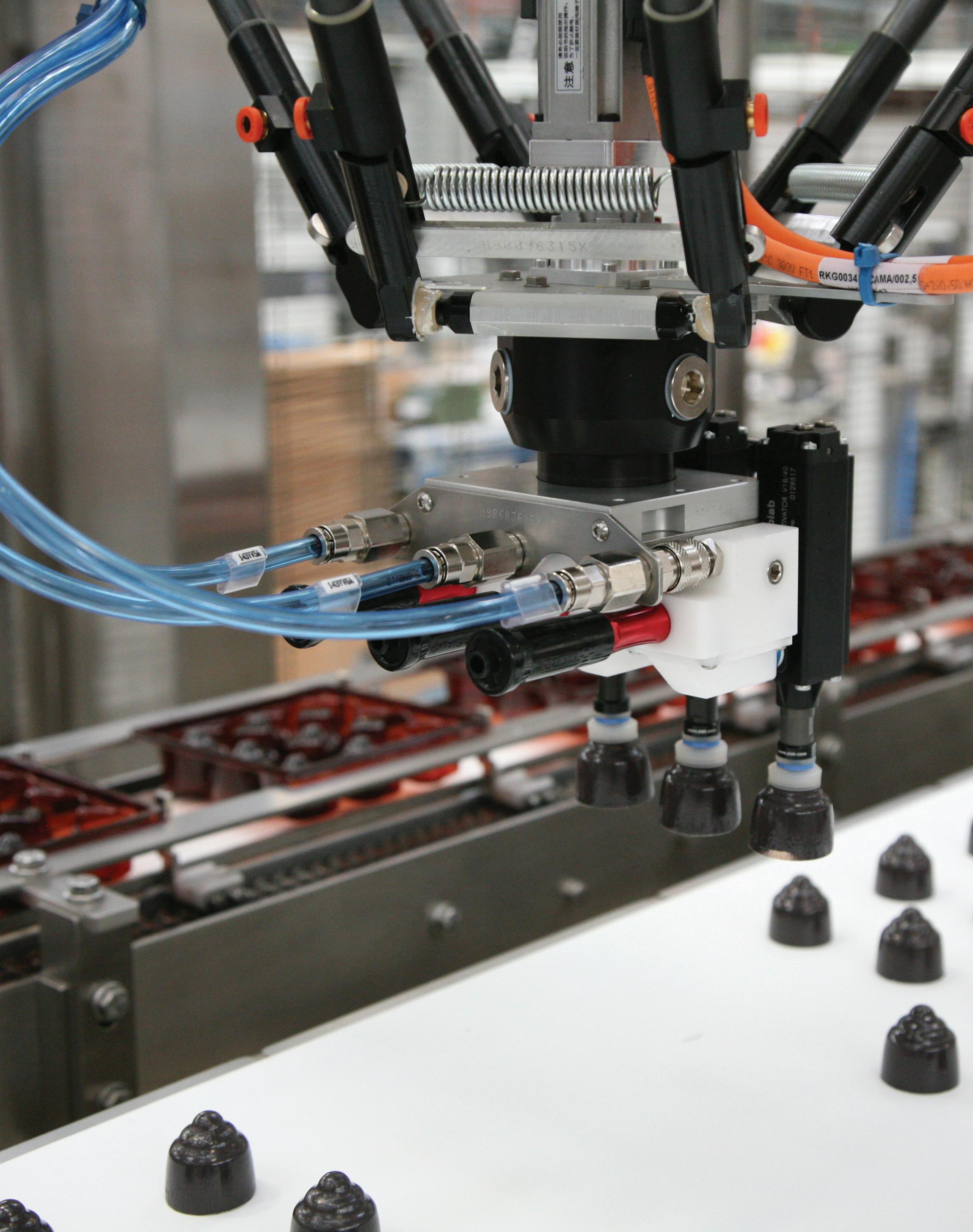
A SWEET, FLEXIBLE SOLUTION FOR
A SWEET, FLEXIBLE SOLUTION FOR THE FROZEN TREAT INDUSTRY
Cama Group’s adaptable secondary packaging automates operations to boost productivity in frigid temperatures.
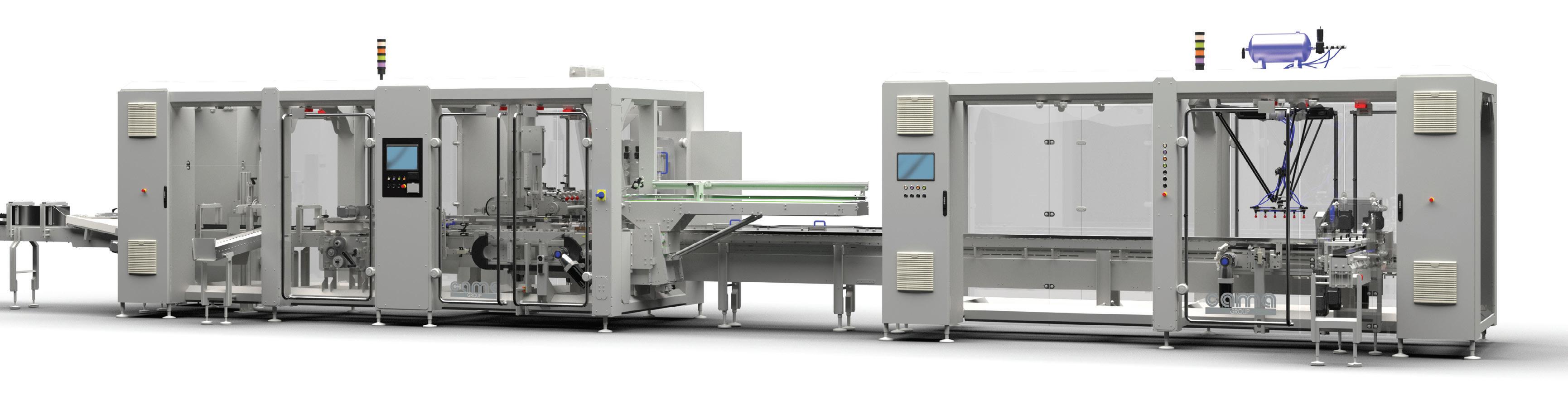
Supplying machinery for the ice cream and frozen treat category comes with its own set of challenges, including speed, efficiency, and ever-changing product needs. With Cama Group’s automated equipment, companies can quickly pump out frozen treats, while meeting the packaging industry’s need for changing demands and formats, such as sustainability and flexible packaging.
Cama Group, headquartered in Molteno, Italy, is known for designing and manufacturing secondary packaging systems such as cartoners, case packers, and robotic loading systems. It specializes in integrated packaging lines that ensure products get to customers in the most effective and appealing way possible. Its machinery adapts to various frozen treat products that require a variety of packaging formats, mixes, and materials.
When a Polish frozen treat manufacturer approached Cama Group with two needs — to implement automation and reduce
materials — the Italian OEM got to work and set the client up with proper PLC controllers and robotic flexibility.
Adapting to formats & temperatures
Cama Group’s machinery can withstand a large assortment of packaging formats, including flow cups, wraps, cones, sticks, and the traditional ice cream carton. This equipment can also work with packaging made from both traditional and ecofriendly, sustainable materials.
Additionally, there’s another factor that this machinery must adapt to – it must be able to work and maintain its production in frigid temperatures required by the product.
Customer challenges
When the frozen treat client, which specializes in private-brand products for retailers, approached Cama Group, they needed two major solutions: automation and material savings.
First, the client needed to enhance speed, efficiency, and reduce reliance on low-skilled seasonal labor. With eight operators working across three different shifts, automation offered significant improvements in productivity.
Second, the customer needed to save on materials as they had been using cartons that were designed for manual loading. This made it a more complicated option because they required specialist handling.
Solution #1: Advanced controllers
To satisfy both client requests, Cama Group provided automation solutions. The core of the system include primary controllers, which work in conjunction
Sarah Wynn • Digital Editor
The Cama Group secondary packaging solution includes an IT280 robotic loading machine and a CL169 continuous-motion cartoning machine. Cama Group


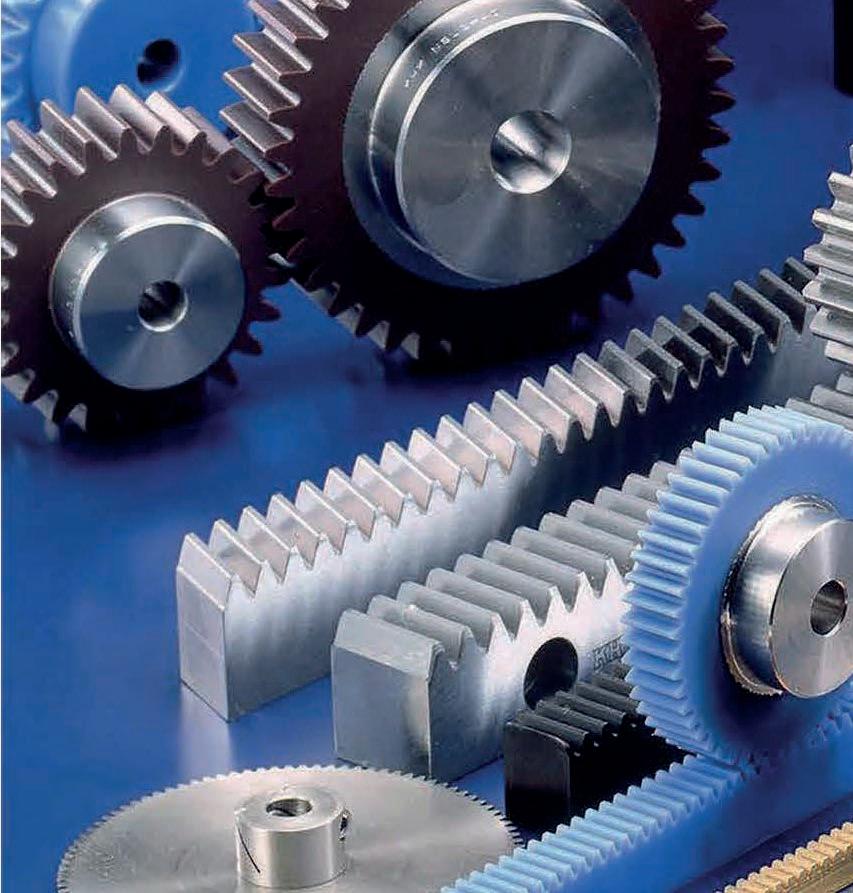


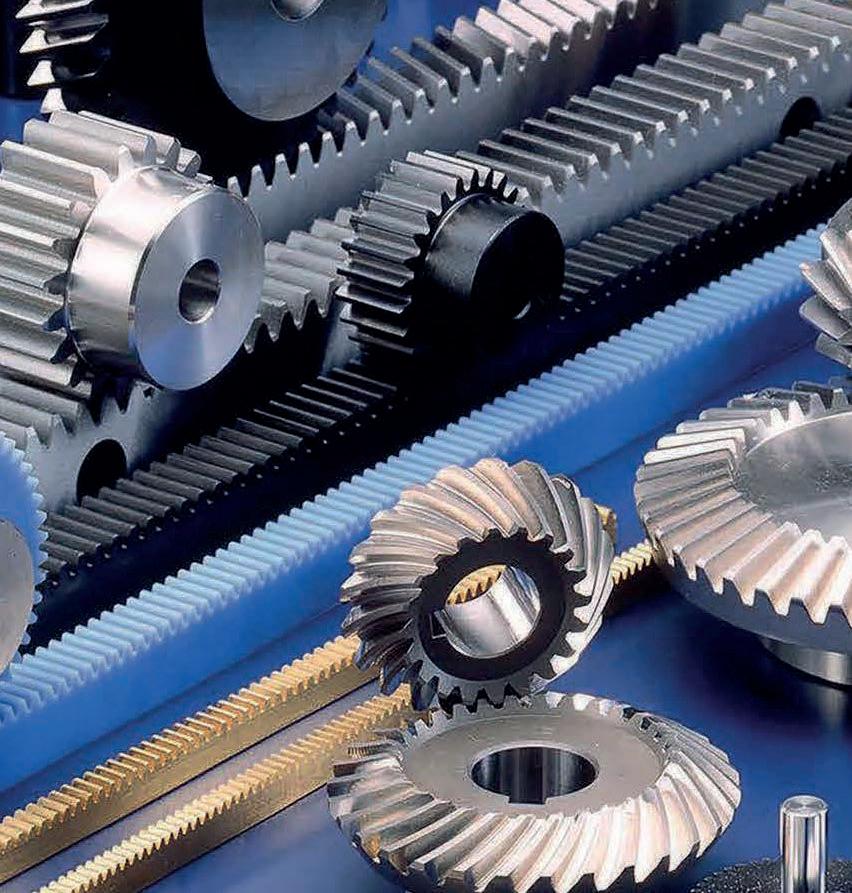

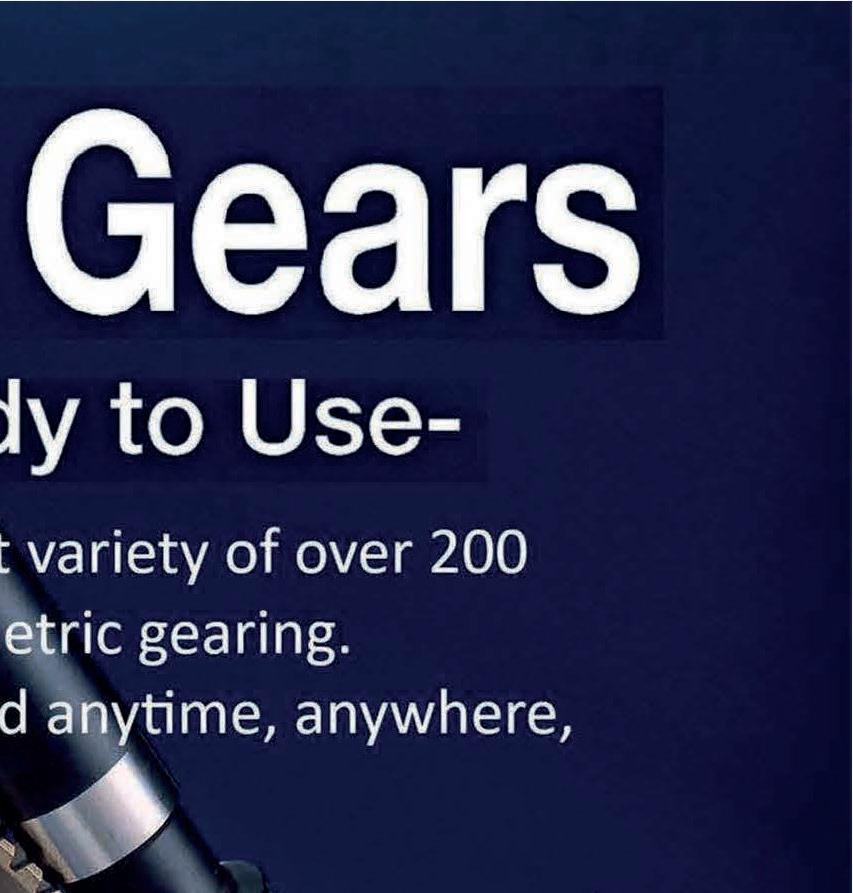
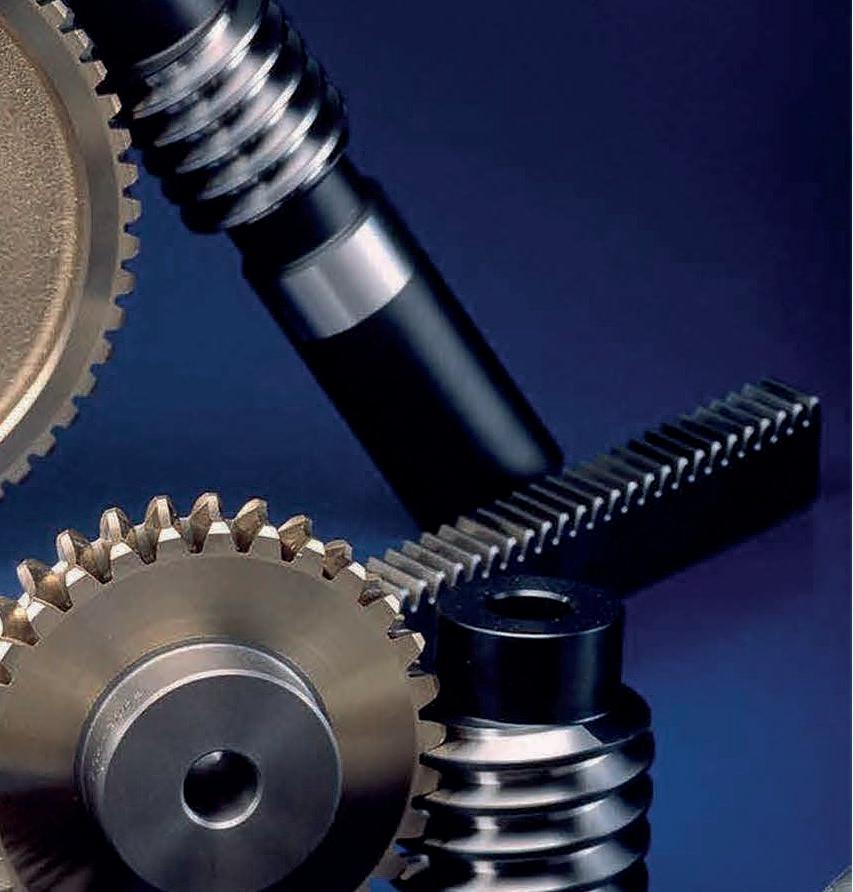
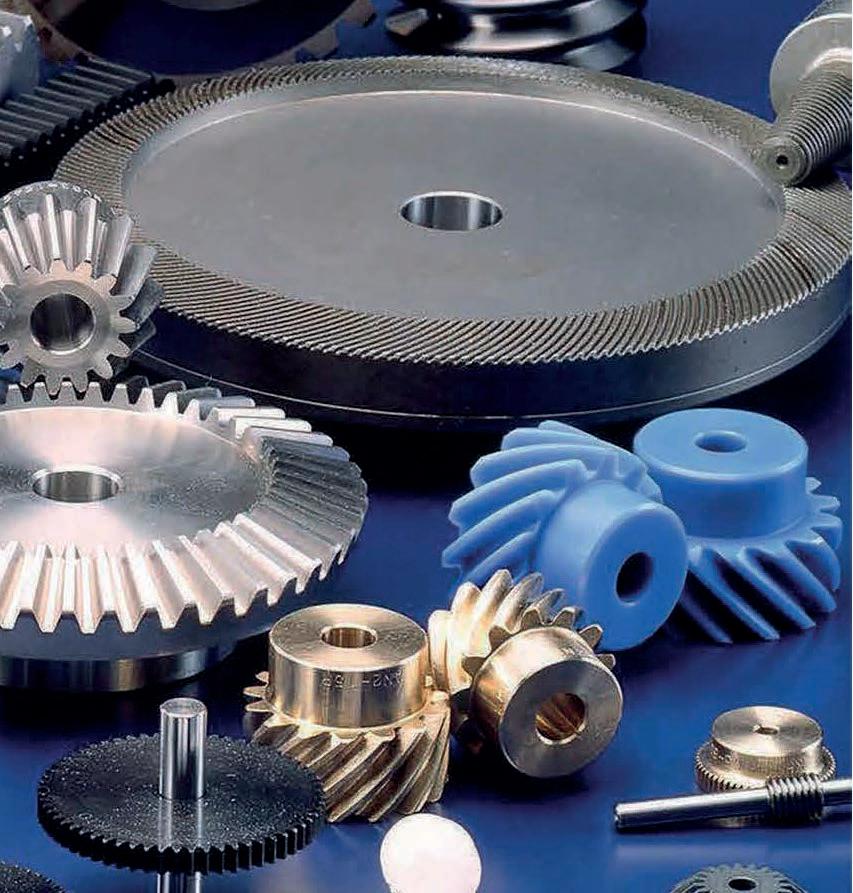

packaging oem
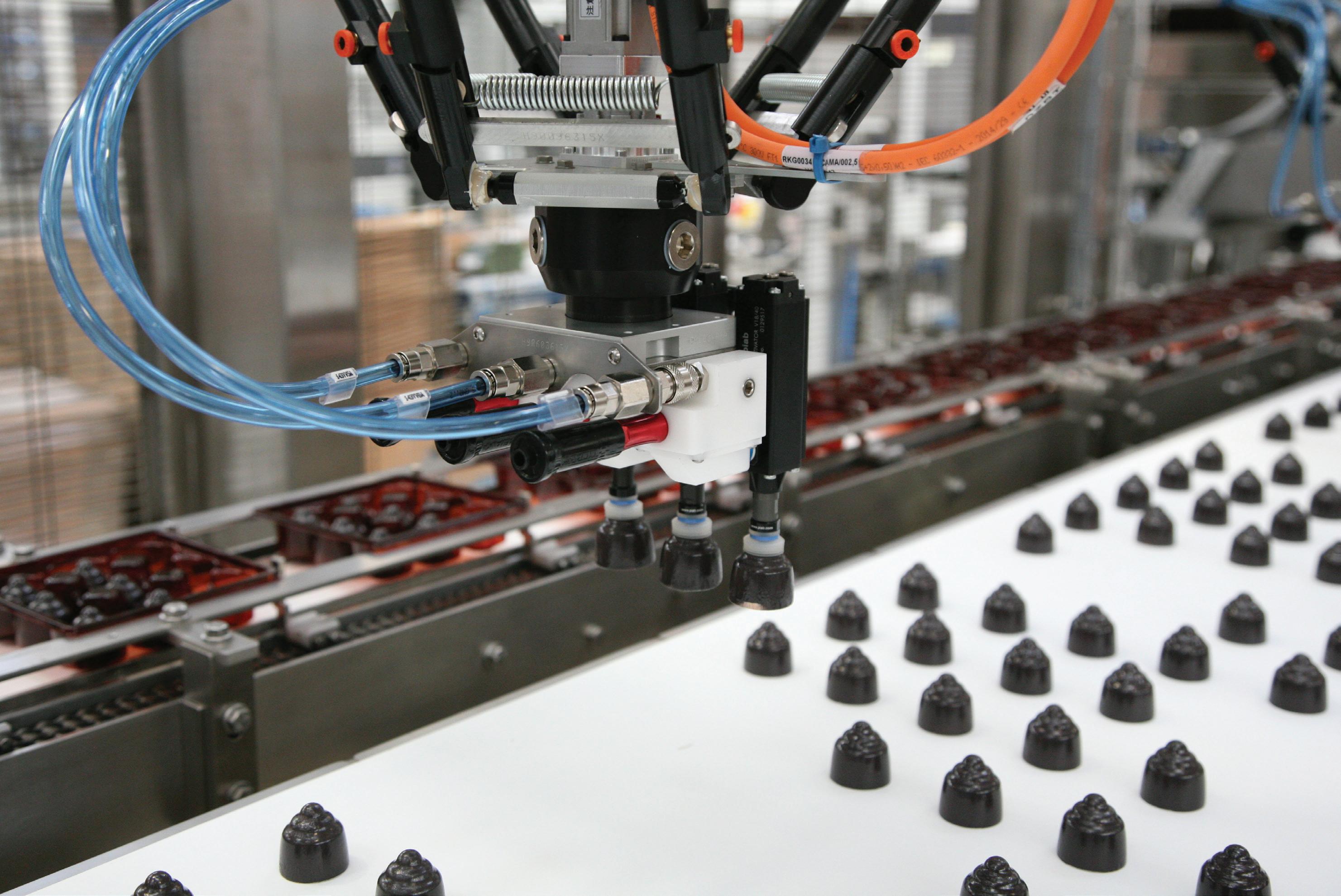
The cyclical and seasonal ice cream industry presents a unique set of challenges to secondary packaging OEMs. It’s a market that is heavily dependent on brand and packaging appeal.
Cama Group
Manufacturers of frozen treats require gentle yet fast, flexible, and agile packaging technology that can keep pace with changing demands.
with additional automation components to ensure precision, accuracy, and scalability. For this project, Cama Group selected Rockwell Automation controllers, including:
• Allen-Bradley GuardLogix: Part of the ControlLogix family, this controller is known for its integrated safety features, flexibility, and simplified programming.
• Compact Logix PLC: This controller offers high-performance processing, scalability, and flexibility, along with an integrated control system.
According to Cama Group, the controllers were selected because they offered seamless integration with the customer’s management software, machine onboarding, and robotic control needs.
This type of application isn’t new for Cama Group, as they offer a variety of machinery that work in cold temperatures.

“Our machines are designed for multienvironment applications and feature open easily cleanable frames and no trap points,” said Alessandro Rocca, sales engineering director at Cama Group, in a statement. “We have a range of machines that can fulfill the packaging needs, but being able to mix and match our solutions to best fit the customer’s needs is definitely a very powerful and highly desirable capability.”
Solution #2: Robotic flexibility
Cama Group’s solution also included its IT280 robotic loading machine and CL169 continuous motion cartoning machine.
• IT280 robotic loading machine: Features flexible infeed configurations, scalable robotic integration, compact, and hygienic design. This machine is designed to enhance efficiency in the packaging process and can be utilized for
Cama Group
industries such as food production and pharmaceuticals.
• CL169 continuous motion cartoning machine: Capable of adaptable product handling, highspeed operation, carton opening, flexible loading system, and carton closing options. It’s designed for high-speed packaging across several industries, including food.
Cama Group's packaging solution for this client included four feeds moving into the equipment, followed by accelerating conveyors spacing out the products. Each product is then placed into an intermittently moving pocket conveyor where products are gathered.
A delta robot picks up the products and places them into a bucket conveyor. The products are sideloaded into cartons by the CL169 and transferred to a flap-folding station, closed with hot melt, and conveyed to the machine's outfeed.
According to Cama Group, both the IT280 robotic loading machine and CL169 cartoning machine feature scalable, hygienically designed frameworks to house automation solutions, including advanced rotary and linear servo technology. The company says both machines are part of Cama’s Breakthrough Generation (BTG).
“Our BTG range, with its multiapplication, multi-environment capabilities, was designed specifically to address these needs,” Rocca said in a statement. “Thanks to its electronic backbone, it is also fully Industry 4.0 compatible, a capability that has been exploited extensively during the pandemic, where we have been able to undertake a huge array of remote operations and interactions, including full [factory acceptance tests]. These capabilities are set to stay commonplace as many end users begin to realize the outstanding capabilities that datacapable machines can deliver.”

KHK USA offers the broadest selection of stock metric gearing in North America. Designed for use in industrial automation applications, conveyor systems, packaging equipment, robotics, and general machinery applications, KHK’s selection of spur gears, helical gears, internal ring gears, gear racks, bevel gears, screw gears, worms & wormwheels, ratchets & pawls, gear couplings, right-angle gearboxes, and gear lubrication systems are available in various materials and sizes. KHK’s website offers free 3D CAD models for all gear products, complete product specifications, and 24/7 shopping. With KHK USA, stock gears are delivered from stock, with no minimum order or credit card surcharges.
khk usa inc.
259 Elm Place, Mineola NY 11501 516-248-3850
Enhancing packaging with flexibility
Frozen treat manufacturers can leverage secondary packaging to improve product quality, reduce costs, and support sustainability initiatives while keeping pace with the industry’s evolving trends, like flexible packaging.
When compared to traditional, rigid packaging, flexible packaging is lightweight, cost-effective, and offers consumer convenience. It’s being called upon more as consumers and businesses request eco-friendly packaging. Flexible packaging comes in many formats like roll stock, liners, pouches, and bags.
For its part, Cama Group offers clients the ability to leverage flexible packaging for the frozen treat industry in the form of stand-up pouches and flow wraps. OEM
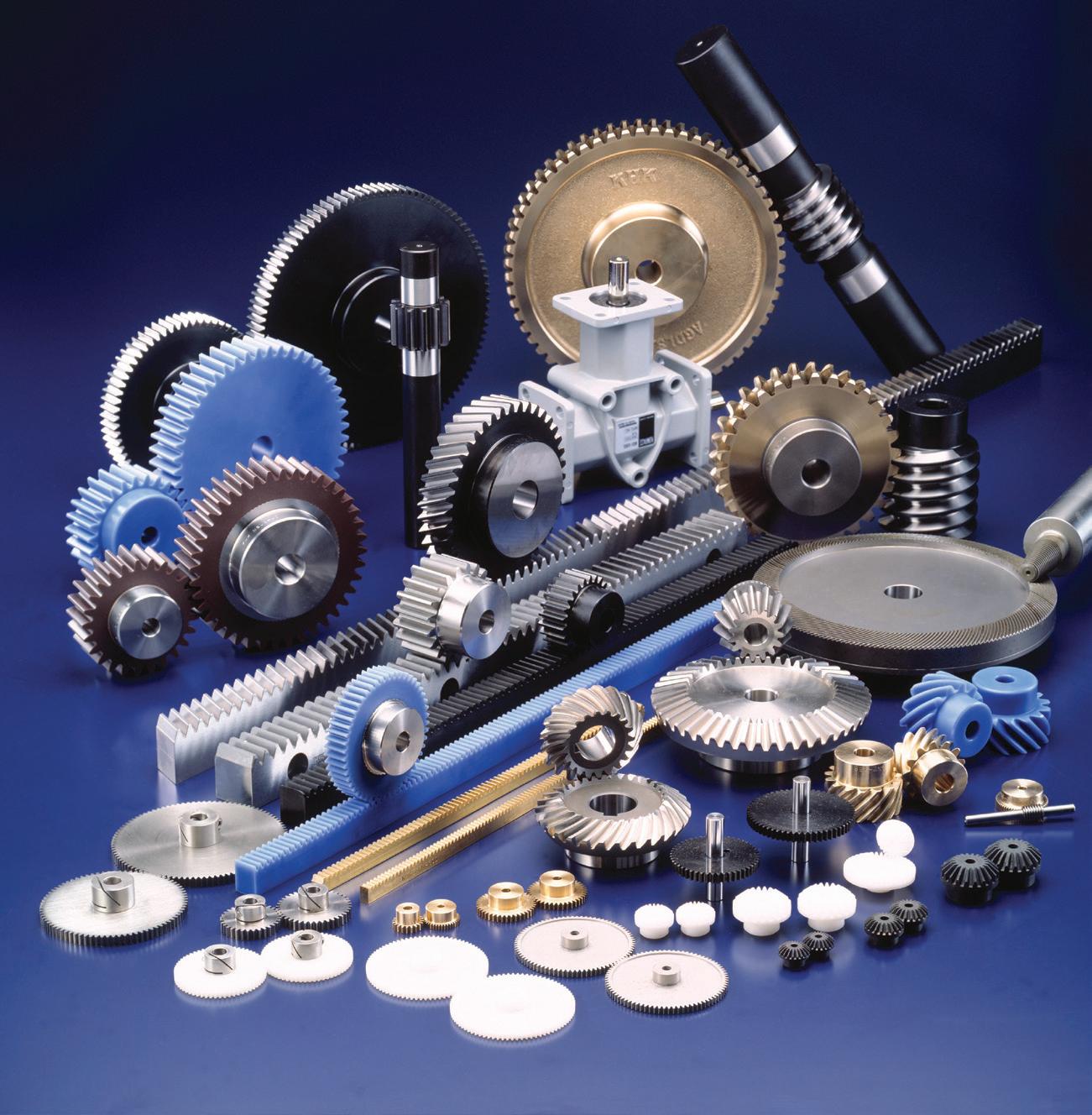