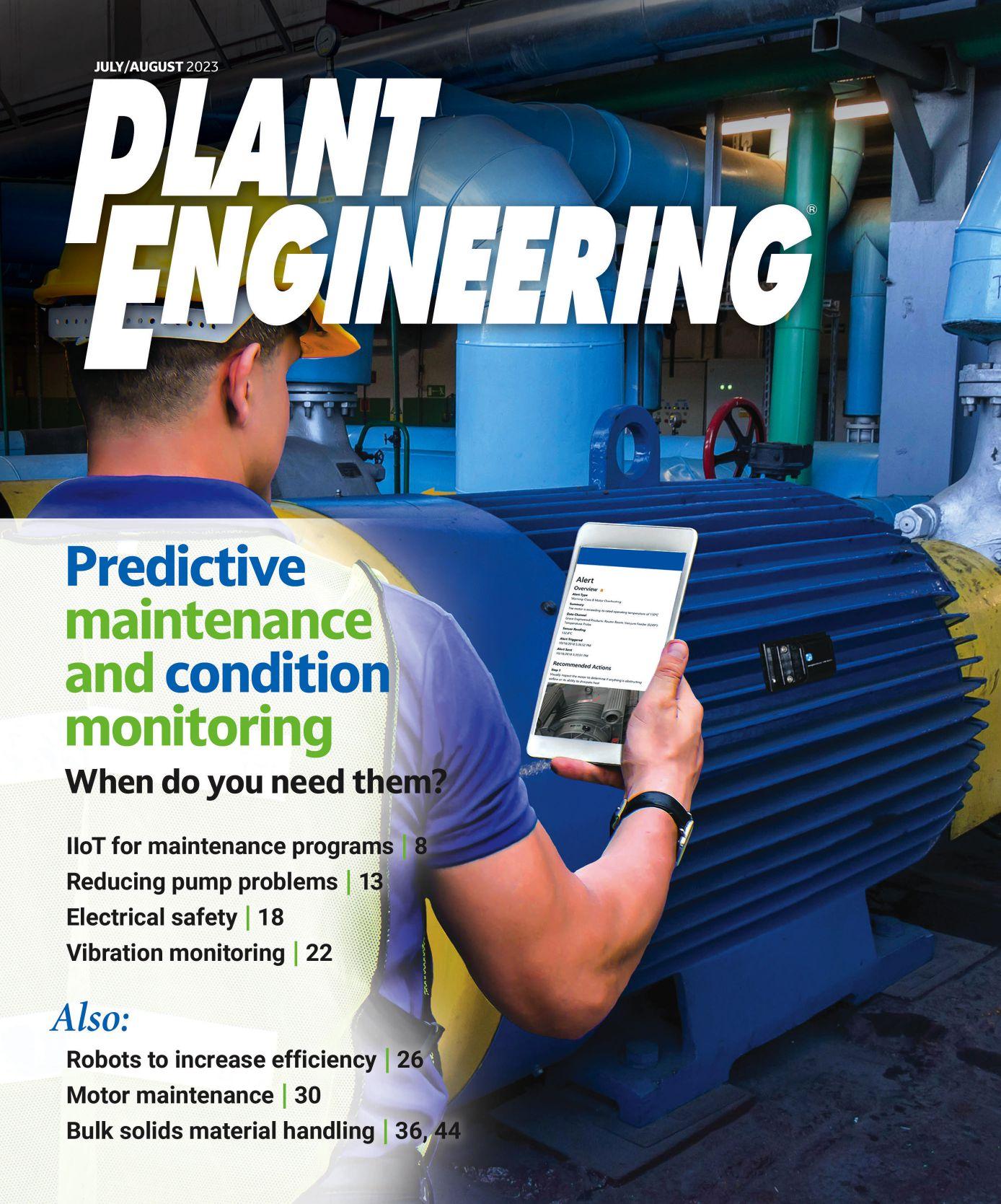

AutomationDirect has thousands of cost-effective motor control products that can easily start, control, and protect your motors...FOR LESS!
Starting at $17.50 (HMC-9B30-11-BS)
Starting at $513.00 (BRY420MI9W)
Interlocked motor disconnects use matching pin and sleeve connectors with keyways to conveniently connect and disconnect mobile equipment safely. They are suitable for use as manual motor controllers, provide an OSHA lockout/tagout point, prevent the connection of devices with different voltage and current ratings, and prevent the installation and removal of a plug when the switch is in the on position. ratings, and prevent the installation and removal
Starting at $98.00 (XTOE1P6CCSS)
The IronHorse series of IEC contactors, overload relays, and manual motor protectors, in sizes up to 300 hp (at 480 VAC), offers a dependable and cost-effective solution for your motor control needs. A wide variety of accessories provides considerable flexibility for any motor control configuration you might need at a price you can afford. Research, price, buy at: www.automationdirect.com/motor-controls
Eaton XT series electronic overload relays are the most compact, high-featured, and economical products in their class. The XT is a self-powered electronic overload relay, available in ratings up to 175A, and designed to cover the entire power control spectrum including NEMA, IEC and definite purpose contactors. These relays can be used with any brand or style of contactor, and accessories provide remote reset capability.
At Dodge ®, innovation is in our DNA. That’s why we make the best solutions possible. Our new OPTIFY™ Performance Sensor includes enhanced features to unlock your operation’s potential and maximize uptime, even in the most extreme conditions.
Enhanced features
Tri-axis accelerometer captures data with improved accuracy Magnetometer captures advanced measurements in motors
Extended battery life provides hassle-free, lasting performance
Widest temperature range for wireless sensors on the market
Extreme conditions call for extreme performance. Learn more about how the intrinsically safe, OPTIFY-compatible sensor can save you time and money at info.dodgeindustrial.com/optify-performance-sensor or by scanning the QR code.
Stainless steel servos motors from SEW-EURODRIVE keep things moving wherever machines and systems are subject to particularly intensive cleaning. Whether used for material handling, intralogistics or sanitary applications, their hygienic properties, long operating life, and maintenance friendliness make them optimally suited in permanently wet environments like food and beverage and pharmaceutical industries.
5 | Where are trends headed for the rest of the year?
In the Plant Engineering state of the industry report, several trends affect plant managers and industrial experts
7 | What are the trends in hazard protection and safety?
Companies must do all they can to ensure their workers stay safe
8 | The benefits of IIoT predictive condition monitoring for maintenance programs
The use of IIoT predictive maintenance technology is becoming increasingly important
13 | Reduce dreaded pump problems or failures with condition monitoring
To avoid downtime, leveraging condition monitoring in a reliability plan is essential
18 | Predictive maintenance best practices improve electrical safety
Predictive maintenance can ensure electrical systems are designed correctly and operated safely
22 | Compressed air vibration monitoring best practices
Vibration monitoring can help providing information on industrial air compressor equipment and prevent unplanned downtime
26 | How working with robots helps a team increase efficiency
Incorporating robots into daily routines had a surprising impact at a semiconductor facility
30 | Maintenance and management strategies for electric motors
Developing a strong motor maintenance strategy can provide companies with many benefits
36 | Scaling up green hydrogen and production
Green hydrogen can be an effective and clean energy source, but there are challenges ahead
44 | Best practices to overcome bulk solids material handling challenges
There are several different types of bulk solids material handling equipment available
48 | Bulk handling system cuts dust, improves accuracy at graphite plant
A graphite and carbon processing plant used a bulk bag filling specialist to reduce dust
A maintenance technician using a web-based browser to see real-time insights provided by a motor condition monitoring device.
AMARA ROZGUS, Editor-in-Chief/Content Strategy Leader ARozgus@CFEMedia.com
CHRIS VAVRA, Web Content Manager CVavra@CFEMedia.com
MICHAEL SMITH, Creative Director MSmith@CFEmedia.com
AMANDA PELLICCIONE, Director of Research APelliccione@CFEMedia.com
SUSIE BAK, Production Coordinator SBak@CFEMedia.com
H. LANDIS “LANNY” FLOYD, IEEE Life Fellow JOHN GLENSKI, President, Automation Plus
Are you a subject matter expert in one of these topics? Would you like to author an article on one of the topics below? If so, please submit an idea to: https://tinyurl.com/PlantEngineeringSubmissions
• Expert Q&A: VFDs and VSDs
• Expert Q&A: Plant automation
• Gears and bearings
• Material handling
• Networking systems and edge computing
• Pneumatic and hydraulic controls
• Predictive maintenance
• Process piping
• The rise of services in manufacturing
Content For Engineers. That’s what CFE Media stands for, and what CFE Media is all about — engineers sharing with their peers. We welcome content submissions for all interested parties in engineering. We will use those materials online, on our Website, in print and in newsletters to keep engineers informed about the products, solutions and industry trends.
* https://tinyurl.com/PlantEngineeringSubmissions gives an overview of how to submit press releases, products, images and graphics, bylined feature articles, case studies, white papers and other media.
* Content should focus on helping engineers solve problems. Articles that are commercial in nature or that are critical of other products or organizations will be rejected. (Technology discussions and comparative tables may be accepted if nonpromotional and if contributor corroborates information with sources cited.)
* If the content meets criteria noted in guidelines, expect to see it first on the website. Content for enewsletters comes from content already available on the website. All content for print also will be online. All content that appears in the print magazine will appear as space permits, and we will indicate in print if more content from that article is available online.
* Deadlines for feature articles vary based on where it appears. Print-related content is due at least three months in advance of the publication date. Again, it is best to discuss all feature articles with the content manager prior to submission.
LEARN MORE AT: https://tinyurl.com/PlantEngineeringSubmissions
In the Plant Engineering state of the industry report, several trends affect plant managers and industrial experts
We recently conducted a study of the Plant Engineering audience, and the results are interesting. Nearly 200 people gave feedback on a variety of topics, from their primary role at work to where their company stands versus competitors to challenges at work.
The challenges are vast. Many cannot be controlled, which makes it exceptionally difficult to plan or make business decisions. Take supply chain delays, for example. When asked, “What are some engineering challenges you are currently experiencing or have encountered in the very recent past?,” 64% said they experienced supply chain delays. And when asked, “What are the current trends and challenges facing the engineering industry?,” 67% indicated they experienced supply chain problems obtaining raw materials.
tries, and the manufacturing and industrial sector is no different.
Cross-training and using technology like artificial intelligence (AI) could help mitigate some of the staffing issues, though it’s not an instant fix. In the case of the Plant Engineering study respondents, 63% see AI as a way to “remove tedious or repetitive tasks.” On the flipside, 63% of respondents said new graduates need people skills just to thrive in the current landscape.
Amara Rozgus, Editor-in-Chief
So where does that leave workers, both those fresh out of school and the more seasoned employees? The majority (66%) feel their company is ahead or just pulling ahead of the competition. Many (49%) say that “increasing complexity of projects and systems” is a trend that others should watch.
Finally, the manufacturing industry is adapting to the changing needs and expectations of clients in many ways:
According to Deloitte’s 2023 Manufacturing Industry Outlook, supply chain delays continue to be one of the top challenges in 2023. They reference exactly what Plant Engineering respondents did: sourcing bottlenecks and logistics backlogs.
Some of these supply chain issues are directly connected to the second engineering challenge: not enough people working on a project (46% indicated this was an issue). Finding talent is a problem in many indus-
• Offering customizable and scalable solutions: 45%
• Emphasizing sustainable and environmentally friendly practices: 41%
• Implementing agile project management methodologies: 34%
• Providing comprehensive life cycle support and services: 34% PE
• The Lead Flexicon Project Manager supervising your system offers you a single point-of-contact through every phase of development, streamlining your communications
• Strict adherence to your unique standards, documentation requirements and timelines
• Commitment to the successful performance and cost effectiveness of your project by serving as your dedicated advocate
• Engineering teams on four continents relieve your staff of overloading
• Over 25,000 bulk handling installations worldwide provide the breadth and depth of experience essential for seamless integration with your upstream and downstream processes
• Ability to work with the engineering firm managing your entire project, or directly with your team
• As one of the world’s largest manufacturers of bulk handling systems, Flexicon can provide the engineering, manufacturing, outsourcing, integration, programming and validation of your project—eliminating the risk of coordinating multiple suppliers
• Greater efficiency and control than available through diversified engineering firms, dedicated equipment makers or in-house engineering departments with limited time and/or bulk handling experience
Safety in manufacturing facilities takes many forms and it is critical companies do all they can to ensure their workers are safe.
Plant Engineering: What are some of the current hazard protection trends for industrial and manufacturing facilities?
Zack Mitchell: Training, personal protective equipment (PPE), safety equipment (eyewash, handwash, etc.), housekeeping and ventilation are among some of the trends we see.
PE: What future trends should engineers, plant managers and designers expect for hazard protection?
Zack Mitchell: Fire protection systems will continue to evolve with advanced technologies and improved detection systems. Ventilation systems will see advancements to enhance air quality and remove hazardous substances more effectively. The incorporation of permanent fixtures for constant waterflow, such as eyewash and handwash stations, will become more prevalent to ensure immediate access to emergency decontamination.
PE: What types of computer applications are in use to support your hazard protection functions?
Jeanie Downs: We use a system that divides our risk categories by module (environmental, etc.) It then assists in tracking our incidents and near misses as well as our corrective actions, requiring completion of the corrective action(s) before we can close out the incident. It also helps us track that our contractors — and their employees — are up to date on safety requirements.
Zack Mitchell: We utilize various computer applications within our enterprise hazard protection systems. These include safety auditing software for regular inspections, a document management system for administrative records,
daily activity logs for tracking man hours, and a training credential database to manage employee certifications.
PE: What are some of the key challenges for improving electric hazard protection at your facility and what strategies/best practices have you implemented to help ensure success?
Zack Mitchell: Some of the key challenges for improving electric hazard protection at our facility include the proper implementation of lockout/ tagout procedures and ensuring effective communication and awareness among personnel. To address these challenges, we have implemented strategies and best practices.
PE: What measures do you take to ensure all employees are adequately trained and aware of the hazards they may encounter in their specific roles within the facility and how often does this occur?
Jeanie Downs: Newer generation workers learn differently. We have begun retooling our training to better equip employees once they get to the shop floor. Originally, we conducted our training in the classroom only. We have since added a hands-on element to appeal to our younger recruits. We also remind employees, not just shop workers of the importance of safety. Everyone receives weekly safety trainings delivered online.
Zack Mitchell: All new-hire employees undergo training courses that are specifically tailored to their scope of work. These training courses cover the hazards they may encounter and the necessary safety protocols to mitigate those hazards effectively. Additionally, we prioritize ongoing training and awareness by retraining employees on an annual basis. PE
FIGURE 1: The biggest challenge to a safety culture is employee turnover. Keeping safety top-of-mind is critical to achieving safety goals. Courtesy: Hitachi Global Air Power
PREDICTIVE AND PREVENTIVE MAINTENANCE
Nick Schiltz, Grace Technologies, Davenport, Iowa
The use of industrial internet of things predictive maintenance technology is becoming increasingly important for businesses that rely on rotating equipment such as motors, pumps and fans
Maintaining equipment is essential to ensure optimal performance, reduce downtime and avoid costly repairs. Traditionally, maintenance programs have relied on periodic inspections and reactive repairs, resulting in lost productivity and increased costs. However, with the advent of industrial internet of things (IIoT) predictive condition monitoring, businesses can now use data to
proactively identify potential issues and address them before they result in downtime.
Many businesses still rely on periodic inspections and reactive repairs as their primary maintenance strategy. This approach is time-consuming and inefficient, as it requires shutting down equipment and manually inspecting components. In addition, it is not always effective at identifying potential issues before they cause downtime, leading to lost productivity and increased costs.
Unplanned downtime due to equipment failure is a major risk for businesses, resulting in lost revenue, decreased productivity and increased repair costs. For example, a motor failure can result in the shutdown of an entire production line, causing delays and lost revenue. The longer the equipment remains offline, the greater the cost to the business. In addition, reactive repairs are typically more expensive than proactive maintenance, as they require emergency repairs and expedited shipping of replacement parts.
IIoT predictive condition monitoring can help businesses address these risks by proactively monitoring equipment and identifying potential issues before they cause downtime. By adding smart devices to equipment such as motors, pumps and
‘
downtime due to equipment failure is a major risk for businesses, resulting in lost revenue, decreased productivity and increased repair costs. ’
fans, businesses can collect real-time data on equipment performance and use advanced analytics to identify potential issues before they cause equipment failure. This proactive approach can result in significant cost savings, increased productivity and extended equipment life.
Enhancing maintenance teams to be more responsive: IIoT predictive condition monitoring can enhance the responsiveness of maintenance teams by providing real-time data on equipment performance. This data can help teams identify potential issues and address them before they result in downtime, reducing the need for reactive repairs and emergency shutdowns. In addition, the use of advanced analytics can help maintenance teams prioritize their workload and focus on the most critical issues, improving efficiency and reducing downtime.
Extending the life of equipment: IIoT predictive condition monitoring can help businesses extend the life of their equipment by identifying potential issues before they result in equipment failure. By proactively addressing issues such as vibration, temperature and fluid levels, businesses can reduce wear and tear on equipment and avoid costly repairs. In addition, the use of predictive maintenance can help businesses schedule repairs and replacements at a time that is most convenient, reducing downtime and lost productivity.
Return on investment (ROI) for condition monitoring devices: While the initial investment in IIoT predictive condition monitoring devices may seem significant, the long-term ROI can be significant. By reducing downtime, avoiding emergency repairs and extending the life of equipment, businesses can save money in the long run. In addition, the use of predictive maintenance can help
businesses optimize their maintenance schedules, reducing the need for periodic inspections and reactive repairs. This can result in significant cost savings and increased productivity.
Despite the benefits of IIoT predictive condition monitoring, some customers may still have concerns or misconceptions about the technology. Common concerns include cost, complexity and reliability issues.
Addressing cost concerns: The initial investment in IIoT predictive condition monitoring devices can be significant, but the long-term ROI can be significant. By reducing downtime and extending the life of equipment, businesses can save money in the long run. In addition, many IIoT predictive condition monitoring solutions offer flexible pricing models, allowing businesses to scale their investment as needed. This can help businesses to manage their costs and ensure that they are only paying for what they need.
Addressing complexity concerns: Some businesses may be hesitant to adopt IIoT predictive condition monitoring due to concerns about complexity. However, many IIoT solutions are designed
2: A maintenance technician using a web-based browser to see real-time insights provided by a motor condition monitoring device.
• Understand the basics of industrial internet of things (IIoT) predictive maintenance and its potential benefits for businesses that rely on rotating equipment.
• Learn about the risks and costs associated with unplanned downtime due to equipment failure and how IIoT predictive maintenance can help prevent these issues.
• Explore common questions and hesitations associated with adopting IIoT predictive maintenance solutions and learn strategies for overcoming these concerns and making a strong business case for implementing this technology.
‘ In addition to these challenges, it is important to recognize that IIoT options are not a one-size-fits-all solution. It is important to work with a provider who can help select the right solution for specific needs and provide ongoing support as needed.’
to be easy to install and use, with minimal technical expertise required. In addition, many solutions offer user-friendly interfaces and dashboards that provide real-time insights into equipment performance. This can help businesses to quickly identify potential issues and take proactive measures to prevent downtime.
Addressing reliability concerns: Reliability is a key concern for businesses when it comes to adopting IIoT predictive condition monitoring. However, many IIoT solutions are designed with reliability in mind, using advanced analytics and machine learning algorithms to detect potential issues before they become critical. In addition, many solutions offer redundancy features, ensuring that data is always available even in the event of a system failure.
Predictive condition monitoring
uPredictive condition monitoring technology can help companies avoid costly unplanned downtime, increase productivity and safety and improve the return on investment for their maintenance programs.
u This article will explore the benefits of industrial internet of things predictive condition monitoring for maintenance programs, address common questions and hesitations that customers may have and provide insights on how businesses can integrate this technology into operations.
While IIoT predictive condition monitoring can provide many benefits for businesses, it is important to recognize that there may be challenges associated with implementing these solutions. Here are some key challenges businesses may face and how they can be overcome:
Integration with existing systems: One of the biggest challenges businesses may face is integrating IIoT predictive condition monitoring solutions with their existing systems. To overcome this challenge, it is important to choose a solution that is compatible with your current infrastructure. Many IIoT solutions offer application programming interfaces and other integration tools that can help streamline the integration process.
Data management: Another challenge businesses may face is managing the large amounts of data generated by IIoT predictive condition monitoring solutions. To overcome this challenge, it is important to have a clear data management strategy in
place. This may include setting up automated data collection and analysis processes, as well as investing in data storage and analysis tools.
Training and adoption: Finally, businesses may face challenges related to training and adoption. While IIoT predictive condition monitoring solutions are designed to be easy to use, it is important to ensure that maintenance teams are trained on how to use them effectively. This may include offering training sessions and providing ongoing support to ensure that teams are comfortable using the new technology.
In addition to these challenges, it is important to recognize that IIoT options are not a one-size-fits-all solution. It is important to work with a provider who can help select the right solution for specific needs and provide ongoing support as needed. While there may be challenges associated with implementing these solutions, these can be overcome with the right strategy and support. By choosing the right solution and working with a provider who can offer ongoing support, businesses can maximize the benefits of IIoT and gain a competitive edge in today's rapidly changing industrial landscape.
The benefits of IIoT predictive maintenance go beyond just preventing downtime and extending the life of equipment. These solutions can also have a significant impact on safety and productivity. Here are some statistics that demonstrate the ROI of IIoT predictive maintenance:
Improved safety: According to a study by the National Safety Council, workplace injuries cost businesses more than $161 billion per year. By adopting IIoT predictive maintenance, businesses can reduce the risk of equipment failure and associated accidents, improving overall workplace safety.
Increased productivity: Downtime caused by equipment failure can have a significant impact on productivity. According to a study by Aberdeen Group, unplanned downtime can cost businesses up to $260,000 per hour. By preventing downtime through IIoT predictive maintenance, businesses can increase productivity and reduce the risk of lost revenue.
Cost savings: Finally, IIoT predictive maintenance can provide significant cost savings for businesses. According to a study by Deloitte, companies
that implement predictive maintenance can expect to see a 10%-20% reduction in maintenance costs, a 20%-25% reduction in equipment downtime and a 5%-10% increase in production capacity.
These statistics demonstrate the significant ROI that IIoT predictive maintenance can provide for businesses. By preventing downtime, improving safety, increasing productivity and reducing costs, businesses can gain a competitive edge in their industry and improve their bottom line.
IIoT can be a powerful tool for preventing equipment failure, improving safety and increasing productivity. By leveraging advanced analytics and machine learning algorithms, these solutions can detect potential issues before they become critical, enabling businesses to take proactive measures to prevent downtime. In addition to the benefits of preventing downtime, IIoT predictive maintenance can provide significant cost savings, improving the overall ROI of these solutions.
By choosing the right solution and working with a provider who can offer ongoing support,
businesses can maximize the benefits of IIoT predictive maintenance and gain a competitive edge in today's rapidly changing industrial landscape.
IIoT will provide businesses with a proactive approach to maintenance, enabling them to identify potential issues before they result in downtime. By enhancing the responsiveness of maintenance teams, extending the life of equipment and providing a strong ROI, IIoT predictive condition monitoring can help businesses to reduce costs, increase productivity and improve overall performance. Despite concerns about cost, complexity and reliability, many IIoT solutions are designed to be easy to use and reliable, providing businesses with a simple, stress-free integration process. By adopting IIoT predictive condition monitoring, businesses can gain a competitive edge, ensuring that their operations are running smoothly and efficiently. PE
Nick Schiltz is a Content Specialist for Grace Technologies.
Mike Durbin | Market Segment Manager, Pharmaceutical and Data Centers, Sherwin-Williams Protective & Marine
Paul Pineda | Market Segment Manager, Aerospace-Aviation and Semiconductors, Sherwin-Williams Protective & Marine
The right coating solutions can play a crucial role in facility management, offering asset protection and enhanced safety without disrupting daily operations. By partnering with experienced MRO coatings representatives, managers can ensure compliance with regulatory standards and develop comprehensive approaches to facility maintenance.
In addition, emerging coating technologies offer cost-effective options for facility managers to control expenses and prevent unplanned maintenance shutdowns. These innovations can also promote cleanliness, which is essential for maintaining a safe and efficient facility. Moreover, the use of advanced coating systems can help attract skilled labor by enhancing the overall appearance and functionality of the facility.
By leveraging the right coating solutions, partnering with MRO coatings representatives, and incorporating emerging technologies, facility managers can achieve a harmonious balance of safety, efficiency, compliance, and cost management. This comprehensive approach helps ensure optimized facility performance and long-term success in a dynamic business landscape.
Download the paper here.
E-mail: swprotective@sherwin.com
Lubriplate’s ultra-high-performance, 100% synthetic lubricants have been engineered to provide unsurpassed performance in the most demanding plant environments. They provide a wide range of benefits designed to make your plant run better. Benefits include: extended lubrication intervals, lubrication consolidation through multiple application capability, reduced friction, extended machinery life and reduced downtime. Products include...
HIGH-PERFORMANCE SYNTHETIC GEAR OILS
SYNTHETIC AIR COMPRESSOR FLUIDS
SYNTHETIC HYDRAULIC FLUIDS
HIGH-PERFORMANCE SYNTHETIC GREASES
NSF H1 REGISTERED FOOD GRADE LUBRICANTS
ECO-FRIENDLY SYNTHETIC LUBRICANTS
SPECIALTY LUBRICANTS
Kristi-Jo J.H. Giba-Reiss, Motion, White City, Saskatchewan
Pumps perform critical liquid transfer applications in many industrial facilities, from heavy industry like mining and pulp and paper to lighter industry, such as municipal recreation. An unplanned critical pump outage can be costly in resources and downtime.
Failure pattern studies show that industrial equipment, including pumps, have only a small percentage of equipment failures due to aging — the vast majority occur early in the asset’s life. Thus, time-based maintenance will rarely be the most effective method for improving plant reliability.
Plant managers can use condition monitoring to help identify precursors to common pump failures and allow a maintenance program to move from preventive maintenance to proactive maintenance.
Condition monitoring is the process of observing machinery, such as pumps, to detect any signs of potential failure before it occurs. This is done by collecting the machinery’s performance data and analyzing the trends to detect anomalies. It has been in practice since the 1850s when railway engineers would inspect and monitor the conditions of locomotive wheels using a small hammer. Compromised wheels have a different sound from intact wheels, so by tapping the wheels with the hammer, engineers could analyze the state of each wheel and provide corrective action, such as replacing a wheel.
Throughout industrial history, there have been several evolutions of condition monitoring, beginning with walkaround routes that depended heavily
on resources and having the same people working at the same facility for years to gain familiarity with the equipment.
Facilities now take advantage of the decreasing cost of smart sensors and the improved connectivity within plants. The current goal is to capitalize on plant staffing to make the best use of resources while working to minimize downtime. Combining more modern techniques — such as oil analysis, vibration analysis and thermography — will maximize the ability to identify abnormalities well before problems occur. The potential failure (P-F) curve (see Figure 1) shows the P-F interval, where various condition monitoring techniques are performed early to maintain the equipment in the “P” portions of the curve.
Condition monitoring is practiced at various levels at most industrial facilities in North America. Its power comes from how the data is trended and analyzed. One can employ a route-based maintenance system to monitor the health of critical assets on an annual/quarterly/monthly basis.
However, that requires consistency and dedicated, well-trained resources to ensure that data is collected properly. This method identifies trends as a snapshot in time.
For more powerful trending, plants have begun to employ online condition monitoring. Online monitoring programs collect data at certain intervals throughout the day and can have alarms to alert the appropriate personnel when the asset is
• Learn about condition monitoring and its techniques and benefits.
• Understand the most common pump failure causes and how condition monitoring can help prevent them.
• Determine which technologies are most effective for specific failure modes.
operating outside of preferred conditions. These programs can be set up completely inside existing plant data infrastructure by connecting to a human-machine interface or a programmable logic controller (PLC) to push data into a plant distributed control system or historian. The data can then be sent to the cloud via Ethernet or cellular. Many companies have analysts to provide insights on the data; this can be included as part of the program.
Prevalent online monitoring methods used in centrifugal pump preventive maintenance include:
sis kits (to be used in-house or by a reputable thirdparty lab), handheld oil analysis devices (such as particle counters) and online monitoring systems.
Ultrasonic data identify early signs of wear and abnormalities in slow-moving equipment. Ultrasonic greasing is invaluable in determining the correct amount of grease to apply — increasing the asset’s life. Ultrasound can be performed with various handheld devices (depending on the application) or online monitoring.
FIGURE 1: In a potential failure (P-F) curve, oil analysis is used early to reveal if the oil is degrading or contaminated, to avoid issues that will cause the equipment to begin failing. If needed, it also can be used later in the interval to identify wear metals. Courtesy: Motion
Vibration analysis detects abnormal vibration patterns in machinery, indicating problems such as misalignment, unbalanced components, lubrication issues and bearing failure. Vibration analysts can review vibration trend plots to pinpoint the problems by comparing the patterns that develop in the frequencies captured against known patterns associated with common failure modes (see Figure 2). The most common techniques for vibration analysis are route-based data collection using handheld vibration collectors and online monitoring, either wired or wireless.
Thermography is a technique that uses specialized cameras to detect upset temperature patterns in machinery, such as bearing failure, lubrication issues (i.e., over or underlubricating), seal flushing issues and overloading. Thermography can also identify process issues like plugging in piping, performed with handheld or online monitoring.
Oil analysis identifies abnormalities in the oil, indicating problems such as contamination, wear and water ingress. Tools include handheld oil analy-
Electrical monitors, such as current transmitters, identify how much load the motor is pulling. If a motor is working too hard or not hard enough, there could be a performance issue with the pump or the motor may be sized incorrectly. Electrical monitoring can be performed via handheld clamp-style devices, inline measurement devices or online monitoring.
Common failures among centrifugal pumps include:
Seals are critical to the performance of many centrifugal pumps. Depending on the pump type and application, various seals can be chosen, such as packing and mechanical seals, including component and cartridge types. Seals can fail for many reasons, including improper installation (such as misalignment), upset conditions in the pump and contamination; another factor could be improper application of a seal, such as the seal not being designed for abrasive applications.
The more sophisticated the seal, the more likely condition monitoring will help us identify anomalies. While severe seal failures can be identified visually if leakage comes from the pump, online monitoring can identify anomalies before they become full-on failures. Leaks from seal failures can damage the pump and surrounding equipment.
Vibration analysis and thermography can identify seal failures. A compromised seal will have an identifiable vibration pattern detectable by vibration analysis and could cause the pump to overheat, identified by thermography.
For seals with an auxiliary flush system, oil analysis can ensure the new oil is clean and dry before application. This will provide optimal life for the seal faces. Oil analysis can also identify wear on the seal faces by monitoring for wear metals.
Bearing failure is another common pump prob-
lem stemming from roots like mechanical seals, including assembly misalignment, improper lubrication and upset process conditions. Pump bearings provide the primary support to position the impeller and maintain the concentricity of the running clearances. Centrifugal pumps typically have two bearings but may have more. Journal, rolling element, tilting pad, magnetic and hydrostatic bearings are all used in various scenarios. Depending on the size and speed of the pump, bearings may be oil lubricated or greased.
For greased bearings, ultrasonic greasing is an excellent tool to ensure the correct amount of grease is applied. Many companies offer grease guns with integrated ultrasonic testing. It is a relatively simple process for technicians to be trained to use properly and can dramatically increase the life of greased bearings.
Regardless of the lubrication method, vibration analysis and thermography are instrumental in identifying bearing faults. By monitoring the vibration spectrum, bearing faults can be identified well before needing to replace the bearings. A skilled vibration analyst can often catch situations like misalignment or looseness that demand correction to maintain bearing integrity and ensure the equipment continues running.
Corrective actions include tightening baseplate fasteners, adding/reducing lubricants and realigning the shaft. If corrective actions cannot be applied, the advanced notice from monitoring allows for scheduling the repair during a convenient planned outage.
Cavitation is a common problem when the pressure in the pump drops below the vapor pressure
of the fluid being pumped. This causes the fluid to vaporize, creating bubbles that collapse and damage the impeller and other pump components; this could be either suction cavitation, where there is not enough net positive suction head for the application, so the pump is starving for water or discharge cavitation, where the pump is not designed to meet the actual discharge conditions
Aggressive cavitation often sounds like rocks moving through the pump, and vibration analysis can identify collapsing air bubbles before one can hear it with the naked ear. Corrective actions for cavitation can include lowering the pump suction or raising the feeding tank.
Impeller damage can be caused by cavitation, corrosion and erosion. Impeller damage can result in reduced pump performance and increased vibration, damaging the surrounding piping. While performance loss is a notable indicator of impeller damage, it is a lagging indicator. Leveraging online vibration analysis gives a leading indicator, allowing us to correct impeller damage before it causes performance loss.
Motor failure resulting from overheating, overload and bearing failure can reduce pump performance and increase downtime. It can be detected using a current transformer to identify anomalies in the motor draw. Vibration analysis and thermography can also identify motor failure.
If there is interest in monitoring pumps continuously, deciding where to place the sensors depends on the size and configuration of the pump and motor combination.
FIGURE
2: Vibration trend plots pinpoint developing problems. Courtesy: Motion
‘ Regardless of the lubrication method, vibration analysis and thermography are instrumental in identifying bearing faults. ’
Condition monitoring
uCondition monitoring is part of a larger proactive maintenance strategy to identify potential problems while still manageable.
u As the heart of a system, pumps are critical for efficient operation and a smart application for this costsaving tool.
Each motor and pump bearing should have at least one vibration sensor, potentially more depending on the size, speed, criticality and maintenance philosophy. For example, for smaller motors (below 50–75 horsepower) that don’t get rebuilt, a single sensor could identify when to start planning for a replacement. Motors sent out to rewind shops for complete rebuild should have a sensor on each end to detect failures as soon as possible.
In rare cases, such as where there are redundant lines, there may only be a single sensor on the motor. More data points are better for vibration analysis, so having sensors at each bearing will allow experienced analysts to identify concerns more accurately.
Auxiliary lubrication systems benefit from lubrication monitoring (particle counter, moisture sensor, oil quality sensor) placed upstream of the filter and a vibration monitor each on the pump and motor. An additional layer of protection is flow
control connected to a PLC to shut down the main pump if the seal isn’t getting fluid. Auxiliary cooling systems would be like auxiliary lubrication systems, except the fluid monitoring may change depending on the fluid in the system.
Condition monitoring is an essential tool to include in a reliability plan. It can increase operating profits by decreasing repair and downtime costs. Given the criticality of pumps in industrial settings and companies’ continuous supply chain problems, unplanned downtime can prove very costly. Many cases show that the return on investment of a well-designed condition monitoring system is as short as four months. That means that the cost of not using condition monitoring could be three times (or more) than the startup costs of the system. PE
Kristi-Jo J.H. Giba-Reiss serves the Canadian market as Application Specialist for Motion’s On-Site Solutions Team.
ARC FLASH AND ELECTRICAL SAFETY
Carsten Baumann, Schneider Electric, Larkspur, Colorado
Predictive maintenance can ensure electrical systems are designed correctly and operated safely
Managing maintenance and operating electrical systems in facilities without proper controls can lead to safety and financial risks, including unplanned outages that can cause harm to on-site personnel and equipment damage. Such outages can also cause exorbitant financial losses to businesses.
Uptime Institute research data found that around a third of all reported outages cost more than $250,000, with many exceeding $1 million. Data center outages are some of the costliest, with a quarter of respondents in a survey indicating that their most recent outage had cost more than $1 million in both direct and indirect costs.
Digital twins are virtual replicas of physical objects, processes or systems that are created using real-time data and simulations. These digital representations can help improve the understanding, design and operation of complex systems by providing insights into their behavior, performance and potential problems.
For example, a digital twin of a power distribution system could monitor the flow of electricity through various components, identify potential areas of overload or overvoltage and predict the likelihood of equipment failure.
Digital twin technology can be employed during the design phase of an electrical system and the life cycle's operations and maintenance phases to significantly increase safety. Intelligent single-line diagrams using digital twin technology can create active blueprints of single- and three-phase power systems. These tools facilitate seamless collaboration and the application of real-time insights, which can streamline diagnostics and troubleshooting.
• Learn how to tap into the power of digital twins to run “what if” safety scenarios.
• Know how to use audits and smart sensors to improve safety and electrical system performance.
• Review methods to proactively reduce arc flash threats. Objectives
Power systems engineers working in plants often rely on static paper or PDF-based electrical single-line diagrams to prevent these outages and maintain their facilities. This introduces limitations that increase operational risks and create challenges in maintaining and updating the documentation for electrical systems. Adopting predictive maintenance best practices to mitigate these risks, such as digital twins, safety audits, smart sensors and arc flash solutions, can help ensure electrical safety and reduce unplanned downtime.
Operators and engineers can improve their understanding of existing electrical systems by using digital twins as a comprehensive digital learning environment. New generation predictive tools use real-time and archived data as a simulation platform that enables power systems engineers to run “what if” scenarios. This online predictive simulation is a potent analytical tool that allows engineers to anticipate the system’s response to operator actions.
Such an approach offers several advantages, including the ability to experience emergencies and precarious situations without actual danger, resulting in fewer safety exposures. Additionally, precise “what if” scenarios can illustrate how to improve
FIGURE 1: ETAP is an analytical engineering solution company specializing in the simulation, design, monitoring, control, operator training, optimizing and automating of power systems. ETAP's integrated digital twin platform offers the best comprehensive suite of enterprise solutions.
Courtesy: Schneider Electric
operational efficiency and enhance decisionmaking. The practical post-mortem analysis and event playback capabilities facilitate faster incident response times.
Audits can be another valuable tool for promoting safety and enhancing the performance of electrical systems. Having the capability to identify technical deficiencies and anticipate potential failure risks in a facility's electrical system is vital. By conducting audits organizations can identify potential hazards and areas for improvement, allowing them to implement corrective actions before accidents or failures occur. Audits can also help ensure that electrical systems are operating efficiently, identify areas of noncompliance and verify that maintenance programs are being executed effectively. This proactive approach can improve safety, reduce downtime, extend equipment life span and save costs.
However, detecting these shortcomings can be daunting, particularly when faced with limited resources. Collaborating with expert consultants and the operations team can help identify critical areas for improvement. Using nonintrusive stateof-the-art technology, an on-site audit assesses the electrical installation and builds a single-line diagram of the devices, quickly identifying potential weak points that could compromise system safety and performance. This process helps uncover potential vulnerability hazards and recommends optimal performance and safety improvements. Experts equipped with specialized software provide a comprehensive modernization plan, including 10-year maintenance, monitoring and management plans, spare parts and technical documentation management. Following the audit, debrief sessions with all stakeholders highlight observations, risks and recommended next steps. Comprehensive reports relay vital, actionable insights and standardized deliverables across locations, segments or coun-
‘ Digital twin technology can be employed during the design phase of an electrical system and the life cycle's operations and maintenance phases to significantly increase safety. ’
tries to ensure multisite or country consistency and develop ongoing monitoring and management strategies for maintenance plans.
Arc flash is one of the most potentially destructive and hazardous forces in the field of electrical installation, operations and maintenance. It is extremely complex, dangerous and difficult to avoid and contain. An uncontrolled arc has the potential to generate extreme heat exceeding 35,000°F and a blast force with pressure waves up to 1,000 pounds per square foot. The result-
ing noise can reach 160 decibels and high-velocity projectiles from the arc can travel up to 700 mph. The toxic gases produced can expand by a factor of 67,000, posing a significant risk to workers, equipment and facilities.
Arc flash mitigation and arc flash hazard analyses have been difficult until recently. Although many empirical formulas and significant testing have been developed, the algorithms and formulas available are still challenging for engineers to solve without a computing tool and nearly impossible for people in the field to apply.
However, with an increased industry focus on electrical safety, arc flash hazards are now more broadly recognized.
Mitigating the risk of arc flash is complex and typically requires collaboration between multiple parties, including facility owners, electrical system designers and equipment manufacturers. However, obtaining accurate information can be challenging, especially in traditional design-and-build project environments. Information exchange may be limited, such as the system short circuit level, the composition of electrodes, enclosure sizes or standard operating procedures. Failure to consider these factors can undermine even the most well-conceived mitigation solutions.
Compliance with Title 29 of the Code of Federal Regulations Part 1910 is required to reduce the risk and severity of arc flash incidents and ensure worker safety. A proactive approach to electrical system design can eliminate the risk of arc flash hazards. Engineered solutions can reduce the likelihood of accidental contact with energized components by using a safety by design methodology during a new system's design and specification stage.
Understanding the arcing current's magnitude, path and duration is necessary for effective mitigation. Incident energy level is a parameter used to quantify the arc flash hazard. Eliminating the hazard or reducing the arc flash incident energy is possible through de-energized work, arc-resistant switchgear or removing personnel outside of the arc flash boundary.
However, these solutions do not necessarily prevent equipment damage. Alternatively, arc fault detection solutions can clear arc faults by upstream overcurrent protection devices. However, these solutions can be risky and require auxiliary power, system design or operator intervention, which introduces the possibility of human error. Additionally, these solutions are one-time use and require inspection or replacement of failed components.
A straightforward and reliable solution for controlling arc flash hazards can be achieved with a passive, repeatable and always-on system that does not require complex engineering. An always-on arc flash prevention and containment system works to minimize the chances of an arc occurring. If a sustained arcing current does occur, the system will extinguish it within one cycle or less, which is faster than any other active or reactionary protection system.
This approach eliminates the need for operator intervention, does not rely on auxiliary power
and significantly reduces the risk of harm to people and electrical equipment. With the implementation of a passive arc flash protection system, managing arc flash hazards becomes more straightforward and mitigation strategies become more accessible. Unlike many active solutions, an always-on arc flash prevention and containment system does not cause tripping, leading to zero downtime or disruption of upstream devices while still containing the arc fault.
It is worth noting that the initial cost of implementing a passive, repeatable, always-on arc flash control solution may be approximately 15% more than standard equipment. However, the return on investment over the equipment life cycle is significant. The benefits of this system include a reduction in additional arc flash engineering controls, lower installation, commissioning and ongoing maintenance costs, decreased need for personal protective equipment and associated costs. Furthermore, businesses can avoid direct and indirect arc flash-related expenses, such as medical and legal costs, fines, increased insurance premiums and business continuity interruptions.
Smart sensors, breakers and electrical panels with shared visibility offer significant benefits to various stakeholders along the risk-management value chain. Smart sensors can be used to monitor plant conditions and alert engineers to potential safety hazards by monitoring air quality, temperature, humidity and other environmental conditions in the plant. If levels exceed safe limits, alerts can be sent to engineers or safety personnel, allowing them to take appropriate action. Smart sensors can also detect the presence of gases that can be hazardous to human health or safety, as well as detect the presence of smoke or fire in the plant.
When circuit breakers and electrical panels are equipped with built-in smart sensor monitoring capabilities, they can provide operational data right from the moment they are installed. These novel capabilities have numerous advantages, such as reducing risk for insurers and supporting testing, inspection and certification providers to offer value-added services to their clients throughout the year, not just during annual inspections.
‘ Compliance with Title 29 of the Code of Federal Regulations Part 1910 is required to reduce the risk and severity of arc flash incidents and ensure worker safety.’
Smart sensors can be used to monitor critical plant equipment and processes in real time, allowing engineers to quickly detect any anomalies or potential problems and take corrective action before they escalate into more serious issues. By analyzing data from smart sensors, engineers can predict when maintenance is required for plant equipment. This allows maintenance to be scheduled in advance, minimizing downtime and reducing costs. These capabilities are continually evolving and hold the potential to provide even more comprehensive insights into electrical operations in the future.
Ultimately, state-of-the-art predictive maintenance best practices are all about accomplishing the four broad dimensions of safety: reduction, avoidance, prevention and containment. Ensuring safety and reducing unplanned downtime in electrical systems is essential to minimize financial risks and safeguard personnel and equipment. Adopting predictive maintenance best practices such as digital twins, safety audits and arc flash solutions can significantly enhance safety and reduce unplanned downtime.
Digital twin technology can be employed during the design, operations and maintenance phases to streamline diagnostics and troubleshooting. Audits can identify potential hazards and areas for improvement, allowing organizations to implement corrective actions before accidents or failures occur. Mitigating the risk of arc flash is necessary to reduce the risk and severity of arc flash incidents and ensure worker safety. Adopting these proactive measures to ensure electrical safety and prevent unplanned downtime can lead to financial benefits, increase safety and extend equipment life span. PE
Carsten
Baumann is Director Strategic Initiatives and Solution Architect at Schneider Electric.
uElectrical system safety is always the No. 1 priority and engineers are aware of the four basic tenets of achieving it: reduction, avoidance, prevention and containment.
uWhat if engineers were equipped with a crystal ball that could tell them how, why and when that safety would be jeopardized? Predictive maintenance can be the answer.
Tony King, Hitachi Global Air Power US, LLC, Vincennes, Indiana
Vibration monitoring can prove to be an essential predictive tool providing information regarding the health of industrial air compressor equipment and can help prevent unplanned downtime.
For most manufacturers keeping an operation up and running, downtime is what keeps them up at night. And well it should. Interruptions to operations can be expensive and have consequences beyond lower output — from supply chain and inventory impacts, to workforce challenges to investor and customer relations.
A key element of most (approximately 80%) of manufacturing is air power. Considered the fourth utility for its ubiquitous role, keeping compressed air flowing is critical to an overall operation. To ensure air power is reliable, proper maintenance of a compressed air system is imperative. A step beyond proper maintenance is predictive maintenance. Knowing the compressor’s health throughout its life span helps keep operations running smoothly.
faults, poor installation or may be caused by normal functioning of the machine.
• Understand what vibration monitoring and analysis is.
• How vibration monitoring is performed and what is included in the final report.
• What the benefits of vibration monitoring are as a part of regular air compressor maintenance.
One of the easiest and most cost-effective predictive maintenance steps is vibration analysis. When done regularly, vibration analysis monitors the health of a compressed air system from installation and provides an in-depth view of what is ailing the system – and more importantly, what might causes problems in the future.
Vibration analysis is a predictive way of determining a machine’s health and is the testing and tracking of an air compressor’s vibration profile to aid in diagnosing any current or future faults. Vibration can come from electrical or mechanical
In this way, vibration can be normal or indicate an issue. Every compressor has its own vibration signature and documenting and tracking that unique vibration allows the owner to “see” a number of performance issues. As the compressor runs, bearings in the air end and motor as well as gears and other mechanics emit a vibration frequency. That frequency, when tracked over time, tells a story.
At certain known or documented frequencies, a skilled analyst can tell (and then predict) when a bearing or gear is failing. The analyst can even discern details like the difference between the rolling element, the inner or outer race, or the cage in a bearing that has or is beginning to fail. In addition
to bearings, the issues that may be diagnosed through vibration analysis include mass unbalance, misalignment, mechanical looseness, gear issues, motor faults and more.
In addition to helping prevent catastrophic compressed air machine failure, there are many benefits to vibration analysis such as reduced maintenance costs, less standby equipment, lower energy costs and enhanced safety.
Vibration analysis is ideally started as soon as the air compressor is installed. Collecting a baseline vibration profile will help the analyst see, over time, when the integrity of the various components begins to break down. It can also determine if the compressor was installed correctly and identify any balance issues, etc. And, while vibration analysis can begin after installation and even midlife (or later) of a compressor, the readings are best if trended from installation startup. Collecting readings from machines in a faulted state doesn’t allow the analyst time to alert a customer on possible downtime from what’s creating the issue as baseline readings are captured on an already faulted machine.
After the initial baseline analysis, a vibration profile should ideally be collected at quarterly preventive maintenance visits — depending on the usage of the air compressor, but at a minimum annually. The route and data collection usually only takes about 20-30 minutes to complete.
To conduct the analysis, a small handheld vibration tool with an accelerometer is placed (via magnet) to various areas of the air end as well as the motor and other select areas of the compressor. The technician will then take readings in up to three directions-- vertical, horizontal and axial along the measuring points – and may even take several readings from one measuring point. Some vibration accelerometer devices read in all three directions – vertical, horizontal, and axialat the same time, but some analysts prefer using a single direction as it tends to be more accurate. Additionally, the data collected can be more dependable if the measuring points of the routes are marked so that the future routes are taken in the same locations. Once the machine reaches its operating temperature and stabilizes, the compressor will then need to run at rated pressure and full load for the entire time the readings are being
FIGURE 2: Charted vibration data can help reveal a compressor’s health and pinpoint failing parts, including predicting when those parts may fail.
Courtesy: Hitachi Global Air Power US, LLC
taken — with the usual environmental conditions and temperature. The handheld analyzer along with the accelerometer measure the machine’s vibration in the Fast Fourier Transform (FFT) spectrum and converts the data gathered into the FFT spectrum by the algorithm. This FFT data is recorded at each measuring point of the compressor and route and sent to an analyst to evaluate the readings.
The analyst will view the collected data on spectrum and time wave form plots and render a report. The vibration levels recorded on the graph will indicate what components are performing normally, which are changing (if historical data is available), and what is beginning to fail.
Every component from the ball bearings to the gears and rotors has its own frequency. By reviewing the frequency readings and studying the peaks and valleys on the graph, analysts can pinpoint an issue by a shift or abnormal component frequency as vibration peaks will become more pronounced or elevated when there is a problem. The process is extremely accurate. If the analyst can’t determine exactly what is at issue, they can come very close to providing a strong indication of the issues brewing.
The final vibration report provides an overview of the health of the compressor and includes a detailed summary of where the various parts and components are in their life cycle. Most importantly, the report can inform the user when an issue will become serious or a failure is likely. This will allow the user to schedule maintenance at a time most convenient to the overall operation. Instead of a bearing failing during a busy or critical production
Vibration monitoring
uVibration monitoring is a critical tool in predictive maintenance and can help users examine when compressed air systems aren’t working.
uVibration monitoring reports provide analysts a comprehensive picture on what’s happening in a compressed air system, but it’s not the only tool companies have. Oil sampling and examining the compressor’s foundation also can help find potential issues.
‘Vibration analysis is a predictive way of determining a machine’s health and is the testing and tracking of an air compressor’s vibration profile to aid in diagnosing any current or future faults.
window, plant management can shut down operations at a pre-determined time and coordinate repairs to other areas of the factory at the same time. Scheduling this kind of maintenance also ensures that the parts needed for the repairs are in-house. Unplanned shutdowns can stretch into days or even weeks if parts are unavailable.
Oil sampling is another predictive maintenance tool that, when used with and at the same time as vibration analysis, can provide a detailed and accurate picture of the health of a rotary screw compressed air system. Both tools are inexpensive and, when performed on a regular schedule, can predict and prevent costly and untimely breakdowns. With oil sampling, metals and other particulates found in the machine’s lubricant can signal an issue. Combine that with vibration analysis and it’s easier to identify the culprit before catastrophe strikes. Oil sampling is also
often necessary to keep a compressed air system in warranty.
Users also should examine the compressor’s foundation and the addition of non-shrinking epoxy grout to help reduce vibrations from the frames of the machines. Some compressor foundations are not designed and reinforced properly to carry the compressor’s load. It’s also possible the compressor’s foundation has weakened over time. Ensuring the foundation has not been compromised after years of heavy, vibrating machinery sitting on top can help reduce the overall vibration of the air compressor and reduce repairs and extend the life of the compressor. Vibration analysis is an important tool to regularly utilize to ensure keep air compressors maintained and running as efficiently as possible. When paired with oil sampling and grout upkeep and performed consistently, it can provide invaluable information and provide the user peace of mind. PE
Tony King, C&I technical service supervisor, Hitachi Global Air Power US, LLC
MECHANICAL AND ELECTRICAL
Samantha Garrison, GlobalFoundries, Essex Junction, Vermont
Incorporating robots into daily routines at has had some surprising impacts on the teams’ day-to-day work at a semiconductor manufacturing facility
Mobile robots are among the most intriguing new technologies to enter the workplace. Once the stuff of science fiction, they are now rapidly integrating into a wide range of industries. More people are adding robots to their ranks of new co-workers, ultimately changing the way we work, though maybe not quite in the ways many of us had feared or even imagined.
Technology has a long history of evolving the way we work and the tools we use to accomplish everyday tasks. Telephones and interoffice mail gave way to computers, email and smartphones.
1: Spot, which is a robot outfitted with a Spot CAM + IR (an integrated radiometric thermal camera) payload, at GlobalFoundries' Essex Junction, Vermont, facility. Courtesy: Boston Dynamics
Data logs that were once recorded by hand on pen and paper are now transmitted instantly and stored digitally. GlobalFoundries’ (GF) site in Essex Junction, Vermont, has been manufacturing semiconductors for more than 65 years and embracing change and technology has been key to the site’s decades of success. New technology offers new ways to achieve results, usually with higher accuracy and better efficiency, but it also often comes with a learning curve.
GF started rolling out an entirely new form of automation — mobile robots — to support the operational efficiency of its production facility, which manufactures semiconductors used in communication devices, radio frequency technology and more. A team oversees the deployment of automated material handling and robotic solutions, including Boston Dynamics’ Spot, an agile mobile robot that traverses rough terrain, climbs stairs and autonomously navigates the 209,000-square-foot facility.
As a semiconductor manufacturer, GF is hyperfocused on product quality, maintenance efficiency and ensuring production uptime. Integrating robotic technology helped improve on these key metrics and the early results are promising. Working daily with a robot has also come with some surprising perks.
It’s no secret that data can unlock important insights in any organization, but sometimes capturing it can be a massive challenge. GF’s facility uses more than 1,000 computers and peripheral equipment that require timely monitoring and inspection.
‘ The robot takes the exact same images from the exact same angle at the exact same times and its work is creating entirely new, critical data streams for the team. ’
With that many assets needing inspections, it’s not economically feasible to add fixed sensors to each piece of equipment or have staff walk through the massive facility doing inspections all day long. The sheer size of the facility means relying on other lagging process signals to detect changes in equipment performance.
Spot is now regularly helping and systematically collecting valuable data about the thermal conditions of the equipment. The robot takes the exact same images from the exact same angle at the exact same times and its work is creating entirely new, critical data streams for the team. The challenge then becomes how best to use the information.
Making this data actionable required integrating it with an existing system, which aggregates data from equipment, including fixed sensors and now data collected by Spot. The team has one place to see all the signals from the equipment, providing a holistic view of operations. Because most of the equipment has a long life cycle and slow rate of change, it does not require a continuous data stream, but with periodic inspections by Spot, the team can better monitor these assets over time, resulting in more informed decisions to keep the facility running efficiently.
Using robots has also influenced how the team tackles responsibilities. Previously, when equipment failed, an engineer or technician responded to address the problem tactically. Sometimes it was a quick fix, but oftentimes the parts needed weren’t immediately available or there was a short-
age due to supply chain constraints. Every minute and hour that a machine is down ultimately costs valuable production time, so the team was often forced to make trade-offs to minimize the impact of downtime.
By feeding all the new data Spot is capturing into the existing analytics system, the team can now see trending analysis and identify patterns over longer periods of time. That means they now can predict equipment failures before they happen. The workflow can be adjusted to support this new approach; the team is now responsible for identifying potential failures and planning predictive maintenance accordingly. Additionally, they can also make sure they have the right parts in advance and can schedule maintenance at the most efficient times to avoid interrupting production.
Simply walking around the facility with a robot like Spot catches a lot of attention. The expectation was that the team would receive questions from colleagues who saw the robot. There was some worry that people might think it was a robot takeover. It turned out the questions were right, but the concerns about fears were wrong.
• Robots enable more consistent data capture, which must be integrated into existing operations to have a real impact.
• With new data streams from robots, reactive maintenance can shift to predictive maintenance, which in turn increases operational efficiencies.
• Technology can have a surprising impact on not just operations, but culture and the ability to foster collaboration across teams.
‘ There are hundreds of engineers that work on-site and as soon as they see the robots their wheels start turning on how it can support their work. ’
u
Robot insights
uThis example of robots used at a semiconductor manufacturing facility showcases how productivity can increase.
uUsing robotic technology ultimately helped increase efficiency and collaboration in a production facility.
Interest in the robot and its work has surprisingly increased engagement across a wide variety of departments and has had a positive impact on the facility’s culture. The team receives numerous requests from other departments to collaborate, hoping to put the robot to work. The focus has been deploying Spot for the original thermal monitoring business case, but there is a long list of additional applications to add to Spot’s workload. There are hundreds of engineers that work onsite and as soon as they see the robots their wheels start turning on how it can support their work.
The team is working hard to ensure everyone in the organization can be a part of this exciting new technology.
Demonstrating Spot’s ease of use has become a favorite pastime for the team and is contributing to the companywide interest. Within 30 minutes, users can confidently drive Spot around the facility, which seems to be a shared experience at the company, regardless of previous experience with robotics. Driving a robot, it turns out, is really entertaining.
Naturally, any new technology introduced in the workplace will take time and energy to perfect. But the best tools ultimately improve both the job itself and the workers’ experience. Based on the work thus far, mobile robots have a bright future in industrial manufacturing, especially in modernizing existing sites in the United States. The initial learning curve is far surpassed by the benefits — both operationally and culturally. PE
Samantha Garrison is Deputy Director, Factory Automation at GlobalFoundries.
experts in bulk solids handling get stuck sometimes.
Not sure how to handle products that leave behind unwanted residue? Moving friable materials where you are concerned about breakage? Unlike those materials, we don’t crumble under pressure. We’ve got over 50 years of industry expertise in building processes that are efficient and effective. Our team of engineers is here to handle your complex challenges so you can focus on what you do best — designing systems that work.
Timothy Albers and Scott Hopkins, Nidec Motor Corporation, St. Louis
Developing a strong motor maintenance strategy can provide companies with many benefits long-term as it reduces downtime and can help companies avoid large repair or replacement costs.
Electric motors are the drivers for most equipment from factories to commercial building HVAC systems. Developing a strategy for the lifecycle of the motor makes good operational and business sense. A good motor management strategy must consider the motor life from receipt to repair to recycle. Planning for the motor’s life will pay dividends versus just letting it happen.
When a motor is first received, it will need to be inspected for any damage that may have occurred in shipping. Remove any plastic covering used to protect the motor during shipment because this could cause condensation to build up while the motor is waiting to be installed. If the motor is not going to be installed right away, energize the motor space heaters, if installed, to keep condensation out of the motor windings, and fill oil reservoirs with oil to protect the bearings.
Every motor should come with an instruction manual with installation and maintenance instructions. The requirements and recommendations should be integrated into the facilities maintenance and management practices as much as is practical.
If a motor is not going to be installed within a short time after receiving it, refer to the motor’s operations manual for the correct procedures for storing the motor. The procedures may vary due to the length of time a motor will be in storage. The storage area will need to be a space that will have a minimal amount of ambient vibration as this
can damage the motor bearings. Periodic maintenance will need to be performed on the motor as well. This maintenance may consist of rotating the motor shaft, performing winding inspections such as megger checks, and oil or grease analysis.
When it is time to install the motor, couple of steps need to be completed. If the motor has been filled with oil, it will need to be drained before moving. Moving a motor full of oil could cause the oil to slosh around and wind up inside the motor. If the motor has been in storage for an extended period of time, it may need to go to a service shop to be inspected and brought back to “as new” condition.
A motor’s installation location is an important consideration. It is important to keep a motor clear of obstructions to not restrict ventilation. Unless otherwise specified on a nameplate, a motor is designed for operation in accordance with National Electrical Manufacturers Association (NEMA) MG1 "Usual Service Conditions," which states an ambient temperature range of -15° to 40° C (5° to 104° F). Standard grease lubricated units are suitable for operation within this temperature range. Special lubricants may be required for ambient temperatures outside of this range.
Motors operating under rated load and allowable ambient conditions may feel hot when touched; this is normal and should not be cause for concern. When in doubt, measure frame surface temperature and confer with the motor manufacturer.
Enclosed motors often have condensation drain openings. Ensure drain openings are properly located and open (plugs removed) for the motor mounting position. Drain openings should be at the lowest point of end brackets, frame housing and terminal housing when the motor is installed.
Mount the motor on a firm, flat surface sufficiently rigid to prevent vibration. Drive belts and chains should be tensioned in accordance with supplier recommendations. Couplings should be properly aligned and balanced. For belt, chain and gear drive selection refer to the drive or equipment manufacturer. For application of drive equipment refer to applicable information in NEMA MG1.
Motor to equipment alignment is important to motor and equipment bearing life. Refer to the motor’s installation manual or driven equipment’s manual for the alignment specifications. For horizontal motors, check for soft foot conditions when
performing motor alignment. When using shims use a size that will cover approximately 80% of the foot area. Use no more than 5 shims under each foot with no more than one shim being thinner than 0.003” and the sum of the thinnest three must be greater than 0.010.” Shaft alignments will vary depending on speed. Two pole motors (3600 RPM) will have the tightest alignment requirements.
‘ Motor connections should be made by following instructions on the motor connection diagram.’
For vertical motors, alignment will depend on what type of shaft the motor has. For vertical motors with hollow shafts, the pump shaft and coupling must be aligned within 0.003” and for vertical motors with a solid shaft, alignment must be within 0.002.”
Motor connections should be made by following instructions on the motor connection diagram. The direction of rotation should be determined before connecting to the driven equipment. Rotation may be reversed on three phase motors by interchanging any two-line connections. On single phase motors interchange leads per connection diagram on motor. The wiring of units, controls and grounding should be in accordance with local and National Electrical Code (NEC) requirements.
• Understand the importance of motor maintenance and the different steps involved in the process.
• Learn how to develop a motor maintenance plan and determine whether to repair or replace a motor.
3: Example of a 700hp 3600 rpm WP2 methane compressor pulling methane out of dairy farms and compressing for a pipeline in California.
A key element of motor management is analyzing the health of the electric motor. Electrical and mechanical health can be measured over time based on resistance, amps and vibration. After initial installation it is good to perform baseline electrical and vibration checks. These initial values for resistance, amps and vibration are critical as a baseline to compare future checks to determine the health of a motor.
Equipment to perform a baseline measurement includes a “megger” to test resistance of the motor windings, an ammeter and a vibration measurement device. Periodic checks of the motor system using the equipment over time provides good insight into the health of the motor. Resistance and amps indicate how the insulation of the windings are holding up to the environment. Steady vibration values indicate the motor's mechanical and some electrical elements are healthy. With this information, trended over time, maintenance, repair and replacement has a much better opportunity of being scheduled instead of occurring without warning.
Maintenance is key to keeping the motor healthy. Cleanliness and lubrication are key maintenance activities to be completed. At a basic level, an initial start to maintenance is a basic inspection of the motors at regular intervals. Motors should be kept clean and ventilation openings clear of dust, dirt or other debris.
One of the key factors in long electric motor life is ensuring it is fed by high quality power. Small imbalances in the voltage or frequency could cause major damage to the windings. It is important to regularly check the voltage and frequency of your plant’s power supply to make sure it falls within the motor manufacturer’s specifications. Running a motor with low quality or the wrong voltage or frequency can cause damage and shorten the motor’s life.
TABLE 1: Efficient Motor Management will increase uptime and lower total cost of ownership but it must start with procurement and does not end until recycle.
Courtesy: Nidec Motor Corporation
Source:NidecMotorCorporation
Winding resistance can be measured using a “megger” test. Completing this check on a periodic basis helps provide an understanding of how the insulation of the windings is holding up to the environment and allows the user to build a history of the motor. It also is beneficial to visually inspect the motor windings during a scheduled maintenance event for signs of damage, discoloration or dirt and debris.
As a safety precaution, a motor should be disconnected from any power source before any maintenance or servicing. Periodic vibration or ultrasonic inspections can let you know if there are changes in your bearings and can let you plan for a bearing replacement instead of an emergency repair.
Bearings should be lubricated per the manufacturer’s operating instructions and any additional instructions found on a motor mounted plate. Lubrication is critical, but excessive grease may damage the motor. Following lubrication instructions, including process, periodicity and volume is important to maintaining the life of the motor.
Motors with grease lubrication are pre-lubricated at the factory and do not require initial lubrication. Relubricating interval depends upon speed, type of bearing and service. Refer to Table 1 for suggested regreasing intervals for some common size motor bearings. Harsh operating conditions such as high humidity or dirty environments may dictate more frequent lubrication.
Vertical high thrust motors are often used in pumping applications and require some special considerations to protect the bearings. For example, certain motor enclosures have screens that must be cleaned. Also, accessory parts for these motors such as lubrication and water-cooling systems for the high thrust bearings should be included in maintenance.
If the equipment the motor is driving is a critical component to plant operation, then decreased intervals with more check points should be implemented in the maintenance schedule.
Inspections should always include the cooling system, whether it is making sure the fins of a totally enclosed fan cooled (TEFC) motor are clear, the cooling fans of the motor are not damaged, or there are not outside factors increasing the ambient temperature. Always check to make sure the motor cooling system is operating correctly.
If air filters are installed on the motor, check them regularly to make sure they are not clogged and blocking airflow to the motor. Clogged air filters can cause a motor to overheat.
A repair or replacement plan is needed for each motor. Of course, every good plan can change if conditions warrant it, but creating a plan will decrease the cost of keeping an operation running.
A motor plan should include several elements. First is the decision to repair or replace the motor. The larger the motor, the cost to purchase and maintain a spare or the likelihood a replacement motor would be in stock locally drives the decision toward repair rather than replacing it. Of course, if the motor’s criticality to the operation is very high, a spare may be the correct decision.
If repair is the intended solution, then a plan should be in place. The plan should include the shop or location for repair and, if possible, have motor winding information on file to speed up the repair process.
If replacement is the intended course, then a spare motor should be purchased or a replacement motor model should be identified including the manufacturer and the location and contact information for a local supplier. All of this planning speeds up the process of getting equipment back
Motor maintenance
u A good motor management strategy must consider the motor life from beginning to end and having a consistent plan will reduce downtime and repair or replace costs.
uMotor maintenance involves many steps including inspection, installation, commissioning and more and the maintenance strategy must be consistently followed throughout to avoid potential issues.
‘ Maintenance is key to keeping the motor healthy. Cleanliness and lubrication are key maintenance activities to be completed.’
up and running. Creating a plan like this can seem daunting, but it can be completed over time.
Spare motor inventory can be a challenge for companies. With the average life of a motor at approximately 17 years, a spare could be a spare for a long time. That spare requires maintenance of its own as well as protection and it is an investment. Those factors add to the spares challenge.
To minimize spares a few processes and procedures can be implemented. The first step is standardizing motors being acquired across the facility. Having a consistent specification for multiple installations will allow for a single spare to be utilized in multiple applications. The second step is
identifying reliable primary, secondary and even tertiary local motor distributors that can supply common replacement motors. With confidence in outside supply, spares can be focused on more unique installed motors. The third step is evaluating repair. In some cases, the spare investment may be too expensive or not practical. If that happens, have a repair plan in place with motor repair data ready to use. These three factors should assist in determining a reasonable spares plan.
A motor management plan should be holistic from receipt to recycle. Having procedures and proactive plans in place will lead to greater uptime and lower overall costs for the motors installed to run the facility. PE
Tim Albers is the director of product management for Nidec Motor Corporation’s Commercial and Industrial Motor Division. Scott Hopkins is manager product service; Nidec Motor Corporation US Motors St. Louis. He has 20 years of industry experience in motor manufacturing, testing, repair and service.
PREDICTABLE PERFORMANCE. CONSISTENT DATA.
Spot helps increase your uptime by enabling your team to collect high quality data more frequently and efficiently with automated robotic inspection.
bosdyn.co/automate-inspection
Rob Lindquist, Emerson, Pompton, New Jersey
Green hydrogen is a growing industry with a lot of potential for manufacturers as an effective and clean energy source, but there are challenges ahead.
Green hydrogen is one of the most promising alternative fuel sources. There has been tremendous global investment in green hydrogen technology as the zero-emissions fuel source is a path to decarbonization. With many well-funded projects in the works, the green hydrogen industry is well-positioned to grow.
Success will depend on reliability across the entire supply chain from production to storage and transportation to dispensing. The future of safe, efficient green hydrogen can become reality with the right solutions and processes in place today.
Green hydrogen is attractive as an alternative source of energy because it can provide sufficient and reliable power with zero emissions. Countries have developed policies, programs and projects to accelerate green hydrogen production and use. Many governments have developed hydrogen road maps and are setting ambitious targets. Energy companies are responding by making investments in large-scale green hydrogen projects.
Many of these projects are large and ambitious, and the infrastructure and processes still need to be built. Although scale-up is a challenge, there are technological and digital transformation solutions that have already been proven in related applications and industries, including the greater hydrogen industry. These established solutions can help solve many of the challenges companies face across the value chain.
The process of producing hydrogen using water and electricity is called electrolysis. Electricity breaks water down into its base elements, hydrogen and oxygen, in a unit called an electrolyzer.
These electrolyzers can range in size from small devices to large-scale, central production facilities. For example, skid electrolyzers can be placed outside of factories to replace public utility electricity, or they can be used to power entire communities. By combining electrolytic cells and stacks, green hydrogen production can be scaled according to the application’s needs.
However, within the great advantages of scalable clean energy lie a few challenges. R&D efforts are being made to increase electrolyzer system efficiency overall, as well as electrolyzer operating life, power density and stack size. These improvements will reduce material costs and lead to more flexible systems adapted to intermittent and fluctuating power supplies.
Because of the great scalability of electrolyzers, manufacturers need to consider how they access the components necessary for the full range of electrolyzer sizes.
Hydrogen’s nature adds even more complexity because there are severe consequences if it’s handled improperly. Electrolyzer components need to be reliable and built for hazardous environments to keep people and property safe.
Working with a technology supplier that has an extensive portfolio specifically designed for hydrogen applications can simplify the supply chain, saving time and money. And, in many cases, it can be much easier to work with one supplier with a complete portfolio, especially as companies scale their production. This frees up equipment manufacturers and producers to focus on developing and delivering their products.
It’s important to work with an expert supplier equipped with a wide range of measurement, control and electrical equipment specifically designed to improve reliability and safety in the hazardous areas of electrolyzers. In addition to valves, valve systems, flow meters, regulators and pressure transmitters, they should also have smart technologies, such as scalable process control and safety solutions that can reduce operational complexity, lower risk and improve the performance of green hydrogen facilities, from electrolyzers to balance of plant (BoP) assets, while providing sitewide safety system capabilities. An integrated control and safety sys-
FIGURE 2: The TESCOM HV-3500 Series Hydrogen Onboard Regulator provides consistent pressure and continuous flow, maximizing fuel cell efficiency in industrial and commercial light and heavy-duty hydrogen fuel cell vehicles. Courtesy: Emerson
tem (ICSS) is also a critical tool to ensure optimized start/stop sequencing with embedded sequence diagnostics.
Before hydrogen can be used for power, it has to be converted, stored or transported. With pressures of up to 15,000 psi in the value chain, hydrogen must be effectively controlled. There can’t be any inboard or outboard leaks due to integrity issues with static
‘ There has been tremendous global investment in green hydrogen technology as the zero-emissions fuel source is a path to decarbonization. ’
or dynamic seals. Even some metals can be negatively affected by prolonged exposure to H2, a process called hydrogen embrittlement. There also are risk assessments and strict regulations to meet.
Working with hydrogen requires serious, dependable control to ensure systems operate safely. Companies need to know they don’t have any loss across their systems, and they need to know how much hydrogen is passing through any transmission/transfer points. Integrating components that monitor and measure hydrogen into systems is essential.
Every system includes certain final control elements (FCEs), such as shut-off and metering valves, high-pressure regulators, pneumatic actuators and solenoid valves. Reliable, high-quality control and safety circuits provide the precision necessary to maintain appropriate pressure and flow rates and preserve hydrogen purity and can be monitored remotely. Sensors should be integrated to monitor pressure, temperature and flow rates. If smart
Learningu
• Learn about the rise of the green hydrogen industry as an alternative fuel source.
• Understand green hydrogen’s benefits and current limitations as a fuel source.
• Discover how digital transformation and other technologies can help the industry break through and benefit manufacturers.
a few of our many abilitites
We constantly work to ensure both the availability of raw material and manufacturing capacity to provide our distributors with critical products needed.
equipment is used, data can be collected to improve productivity and ensure high operational yields.
Hydrogen insights
uGreen hydrogen is a new industry and not mature yet, but there are many companies looking to harness and improve the technology to make economically viable and profitable.
uDigital transformation and other technologies can help this process along, but the companies looking to invest will benefit most from working with a specialist who knows the technology.
This also is where it’s important to have a supplier with a complete portfolio. What’s even more important is working with partners with extensive hydrogen experience and expertise, familiar with the regulations and certifications. They understand the plantwide ecosystem and have the safety and controls equipment needed to monitor, measure and control hydrogen effectively and efficiently. They also should have the flexibility to address many designs and applications.
A key element of the transition to hydrogen-powered vehicles is the fuel cell. Fuel cell power systems can be used to power passenger cars, commercial vehicles and more.
For fuel cells, that portfolio should include high-reliability flow control, pressure regulators, safety junction boxes and flameproof cable glands. Designs should be compact and lightweight to enable manufacturers to create systems with high-power density and extended cell life. Manufacturers can lower risk of fuel cell system failure
with solutions that provide stable pressure regulation, safe distribution and equipment connectivity. Drivers will need to fuel hydrogen-powered vehicles as they populate the road. As fueling stations transition to green hydrogen, they face several challenges, such as sustainability, safety and maintenance. First, there’s the concern of accurately monitoring the hydrogen flow to ensure customers dispense the right amount of fuel, every time, quickly and safely. Accurately maintaining the condition of fueling stations and their critical components can ensure stations are available for users at any given time, whether they’re deployed in dense or remote areas. Fueling station equipment can leverage digital transformation to solve some of these critical challenges.
Starting at the device level, smart sensor technology and the data it provides can lay the foundation on which digital transformation is built. Building on this foundation, utilizing a programmable logic controller (PLC) with integrated edge gateway capabilities can provide complete control and turn aggregated data into real-time information/analytics of the fuel-dispensing process or the condition of the system itself.
‘ A key element of the transition to hydrogenpowered vehicles is the fuel cell. ’
The power of digital transformation can be scaled beyond to a vast network of fueling stations. Information can be aggregated to help optimize the entire network. Dispensing accurate fuel volumes at the highest flow rates as well as reducing the probability of leaks and monitoring the condition of the fueling station helps ensure operation and optimal yield.
The PLC, combined with an edge gateway, also can perform analysis and visualization of diagnostic and process data. Providing this to the fuel station operator and remotely to the hydrogen supplier helps simplify supply chain logistics. Having remote access to filling rates
and preventive maintenance information means hydrogen suppliers are filling tanks only when necessary and providing maintenance only when needed.
From storage tanks to tube trailers to dispensers, fueling station systems must also be safe and easy to maintain, as well as meet the highest performance and regulatory standards. And as we’ve seen throughout the value chain, hydrogen’s explosive nature must be taken into consideration.
To protect personnel, customers and property, ultrasonic gas leak detection systems continuously monitor fueling stations for ultrasound generated from the release of pressurized gas. Pressure
Price your requirement then place your order online.
Use our secure shopping portal to calculate your quantity discount and place your order today!
Your order ships in 5 days or less.
Quantity Discounts Available Built in the USA
transmitters designed for high-pressure measurement and flow meters specifically designed for hydrogen-dispensing applications can accurately measure pressure and gas flow. Connecting these devices that monitor critical parameters to a higher-layer gateway can be used to deliver real-time warnings and alerts to staff on, providing further safety enhancements.
Building the infrastructure and processes needed to transition to green hydrogen requires a partner who can support companies at each stage of their scale-up. Taking a scalable approach will reduce risk while making meaningful progress.
Because green hydrogen is still a relatively new business, companies must rely on partners with broad knowledge and expertise that have already proven themselves in the hydrogen industry, from production and storage to conversion, transportation and mobility. These expert partners already know the regulations and certifications needed and how they change depending on region. And they likely already have a physical presence to manufacture close to customers and their markets.
Green hydrogen is clean and efficient, but building the infrastructure, controlling the gas and making it available for consumption requires expertise. Companies are better equipped to forge ahead if they partner with a specialist that already has a strong presence and relevant experience, holds deep industry and regulatory knowledge and can provide the needed solutions. This strategic partnership will give them a strong position and long-lasting competitive advantage as they make the promising future of green hydrogen a reality. PE
Rob Lindquist is director of global marketing at Emerson.
Optimize warehouse capacity and slotting flexibility with a truck specifically designed for the demands of today’s on-demand economy. Capable of facilitating order picking a full rack higher than models currently on the market, Raymond’s High Capacity Orderpicker is an industryfirst, with an elevated height of 456” –delivering market-leading capacity at height and reducing annual cost per pallet stored by 19% compared with competitors.
www.raymondcorp.com/POY2023
Andy Forrester, Spiroflow, Monroe, North Carolina
There are several different types of bulk solids material handling equipment available; learn tips and tricks here
Bulk solids material handling equipment plays a crucial role in industries that process dry and bulk solids in either powder or granular forms, including pharmaceuticals, chemicals, food and beverage. Bulk material handling solutions providers offer a wide range of equipment for conveying, loading and unloading material.
Efficient material handling is a critical aspect of any industrial process, and selecting the right equipment can help maximize productivity while minimizing downtime and accidents. Choosing the right equipment can be confusing with so many different types of material handling equipment available on the market.
and energy costs and minimize product degradation or contamination.
Some of the more common types of conveyors available include aero mechanical, belt conveyors, bucket, cable drag, flexible screw and pneumatic. Each of these conveyors has unique features and benefits that suit different applications.
For instance, flexible screw conveyors are a great and economical choice for a wide range of materials. Cable drag conveyors are ideal for handling materials that need to be moved long distances and handled gently to avoid breakage. Pneumatic conveying systems can quickly move products over long distances and complex routes, however, they often require expensive and heavily regulated air power units, fans and filters. Aero mechanical conveyors are a unique hybrid technology that allows for near-total material transfer without the additional complexity of pneumatic systems.
Totally enclosed conveying options such as cable drags and aero mechanical conveyors also have advantages over the open belt and bucket style conveyors when it comes to hygienic conveying and minimizing the risk of product contamination.
• Understand different types of bulk solids material handling equipment and their uses.
• Learn to develop safe material handling practices.
• Gain insights about commonly asked questions. Objectives
Throughout the processing line, some key pieces of material transfer equipment will include conveyors, bulk bag fillers and bulk bag unloaders.
Conveyors are an essential part of most bulk solid processes, and there are various conveyor technologies on the market. Automating the movement of materials from one part of a process to another can have a huge impact on the speed and efficiency of an operation. Through careful conveyor selection, companies can improve process safety and productivity, make significant savings on labor
Selecting the right conveyor system is critical to optimizing material handling processes. Each conveyor type has unique features and benefits that suit different applications and choosing the right one can help increase efficiency, productivity and safety.
Due to the convenience, versatility and relatively low cost of flexible intermediate bulk containers, sometimes known as bulk bags, the industry has experienced significant growth in the use of this medium for handling bulk solids across a wide range of industries. To reap the benefits of this technology, end users need to understand and select the most appropriate features to incorporate
into their bulk bag handling equipment.
Bulk bag unloaders are designed to discharge large quantities of materials while minimizing the risk of accidents, spills and material waste. They come in different sizes, shapes and configurations to suit specific applications and can be customized to meet different requirements.
An increasingly popular style of bulk bag unloader incorporates a dedicated hoist, which allows for quick, easy and accurate bag positioning over the unloading station. This eliminates the need for a forklift truck to load the bags reducing the amount of manual labor required and minimizing the risk of employee injuries.
Bulk bag unloaders should also be designed to discharge material safely and efficiently, minimizing the risk of dust escaping to the environment and operator exposure. To achieve this, the unloading station can be customized with a variety of bag and spout seals that may include a spout untie chamber with an integrated dust collection system. Bulk bag unloaders may also include mobile options to move to various locations in a plant, low headroom designs for areas with limited space and integral bag dump stations to unload small bags in your process.
Bulk bag unloaders can be integrated with downstream equipment such as hoppers, conveyors or other material handling systems. They can incorporate weighing systems automated and controlled by a programmable logic controller for accurate dosing or batching operations. All of these features can help to streamline the material handling process, reduce material waste and improve overall efficiency.
Bulk bag fillers are another essential piece of equipment in many industries where there is a requirement to package large quantities of powders, granules or pellets. These systems should be designed to fill bulk bags efficiently and accurately while producing a safe and stable package that can be handled and stored easily and safely.
The filler also can weigh the materials as they are being filled, ensuring that each bag contains the desired amount of material. Semi-automatic bulk bag filling systems can help improve efficiency by automating the filling process, minimizing the amount of manual labor required and reducing the risk of material spills or waste.
An advantage of using a semi-automatic bulk bag filler is that it reduces the need for manual labor and minimizes the risk of errors or injuries associated with manual handling. Instead, the system can automatically fill bags with the desired amount of material, reducing the risk of spills, waste and contamination.
With automated filling and weighing capabilities, the system can accurately fill bags at a rate of up to 40 or more bags per hour and significantly increase weighing accuracy resulting in less product being “given away” in overfilled bags. Some
manufacturers also offer sophisticated densification systems that can be incorporated and automated during the filling cycle. A well-designed densifying bulk bag filling system can result in significant cost savings by increasing production rates, reducing shipping and packaging costs, minimizing product waste (giveaway) and safer storage and stacking of bags.
By working with a company that has a comprehensive understanding of the different types of fillers, unloaders and conveyors available and how to apply them correctly, manufacturing facilities can make informed decisions that help improve their bottom line.
Material transfer points that require an operator, such as manual bulk bag unloading or semi-automatic bag filling, can introduce the risk of injury or accidents if proper safety protocols are not followed. Training employees to operate material handling equipment correctly is crucial in ensuring safety. This includes training on potential hazards associated with the equipment and proper procedures to follow in an emergency.
The next step is to identify potential hazards before any material handling activity occurs. This can involve conducting a risk assessment to identify potential risks and taking measures to mitigate them. This is especially critical when handling powders which can be hazardous to personnel or even become explosive in certain conditions.
Employees should be given appropriate personal protective equipment — such as gloves, goggles and respirators — as required. Equipment should also be regularly inspected, cleaned and maintained to ensure it is in good, safe condition.
Creating a culture of safety within the workplace is also critical. This can be done by conducting regular training sessions, establishing safety committees and encouraging employees to report any potential hazards or safety concerns. Adhering to industry regulations and standards, such as those set by Occupational Safety and Health Administration, is crucial to ensure all safety protocols are met.
Prioritizing safety in material handling practices not only protects employees from potential harm but also ensures the smooth and efficient operation of the workplace. It helps prevent accidents and breakdowns, leading to costly downtime and lost productivity. A safe workplace also promotes employee morale and job satisfaction, leading to improved performance and better results for the company.
Selecting the right material handling equipment is crucial for any industrial setting. Various factors must be considered, including material properties, production rate and desired throughput. Consulting with an expert in manufacturing material handling solutions can help identify the appropriate equipment for a specific application. It's also essential to consider the equipment's capacity, durability and ease of operation and maintenance when selecting the right solution.
Taking the time to find the right conveyor for operations can be a very worthwhile investment. Not only can it be customized, but by finding the most suitable conveyor, it can improve safety, reduce labor costs and increase efficiency. Key points to consider when auditing conveying options include:
• Conveying distance.
• Volume.
• Energy requirements.
• Material challenges (hydroscopic, abrasive, friable, like to segregate).
Can complex bulk bag fillers really save money?
Yes, bulk bag fillers with high fill rates, accurate weighing systems and optimal densification systems can fill bulk bags faster, more accurately and efficiently. Below are a few of the cost savings that can result from a well-designed bulk bag-filling system:
• Reduced bag costs. Savings can come from either filling more material in each bag, reducing total bag usage or from the ability to use shorter, lower-cost bags.
Reduced material waste/giveaway. Less “free” product is given away by avoiding overfilling bags to ensure they are not underweight.
• Savings in storage costs and floor space due to needing fewer bags to hold the same amount of material, oftentimes with the additional benefit of being able to safely stack bags due to their more consistent, square, stable shape with firmer, flatter tops.
• Reduced shipping costs. Using an efficient densification bulk bag filler, more weight can be shipped in the same footprint on each truck, often significantly reducing shipping costs.
What type of bulk bag discharger should be used for a specific material?
It depends on the material's properties, such as its flow characteristics, moisture content and particle size. In narrowing down the decision, it's important to factor in headroom, space constraints, how the bags will be handled, downstream process requirements and dust containment. A reputable manufacturer will test the equipment for safety and efficiency.
While the life span varies depending on several factors, including the equipment type and frequency of usage, proper maintenance can significantly extend its life. For instance, selecting a conveyor built to handle expected wear and tear for more abrasive
materials can prolong its life span. Regular cleaning and upkeep can also prevent equipment failure and keep it operating at peak efficiency.
Clean-in-place systems are becoming increasingly popular as they allow for quick and efficient cleaning without disassembling the equipment. For instance, a food manufacturer can switch between different flavors without worrying about flavor contamination. Proper maintenance and cleaning can ensure that material handling equipment lasts longer and operates efficiently.
The expected life span of material handling equipment depends on various factors, including the type of equipment, usage frequency and maintenance. Proper maintenance can significantly extend the equipment's life span. For more abrasive materials, selecting a conveyor built to handle the expected wear and tear is crucial to ensure the equipment lasts as long as possible. It's important to choose equipment specifically designed to handle the type of material being transported, as using the wrong equipment can cause premature wear and tear, leading to costly repairs or replacements.
‘ Selecting the right material handling equipment is crucial for any industrial setting.’
Regular maintenance, such as cleaning and inspection, can also help extend the equipment's life span. Some providers may offer maintenance and repair services as part of their product offerings, so it's important to consider these factors when choosing a material handling equipment provider.
When selecting a material handling equipment provider, it's important to consider various factors beyond the equipment itself. Look for manufacturers offering material testing services to help customers find the best solution for their applications. It’s helpful to work with a manufacturer that offers a wide range of equipment and custom design solutions for any unique challenges, ensuring that operations are optimized for safety and efficiency. PE
Andy Forrester is VP of Sales at Spiroflow.
MATERIAL HANDLING
David Boger, Flexicon, Bethlehem, Penn.
A graphite and carbon processing plant used a bulk bag filling specialist to reduce dust and other particles escaping in their Netherlands facility.
Asbury Graphite & Carbons is one of the largest global processors of graphite and other carbon materials used in the plastics, automotive, lubrication, powder metallurgy, petroleum and coatings industries. Its European installation in the Netherlands opened in 2014 to take in raw graphite from around the world, reduce it into fine particles through a variety of milling and screening processes and fill 2,200 lb bulk bags and smaller bags, based on customer needs.
The plant operators had experienced problems with inaccurate fill weights of milled graphite, as well as issues with dust control.
“We hadn’t decided what equipment we should go with,” said Marc Stassen, former general manager of European operations. The existing equipment was rudimentary and produced off-weight bags. “We would only find out when the product reached the shipping department that we filled 2,024 lb instead of 2,200 lb, for example.”
The bulk bag filler frames operated with a poorly designed bag spout seal that wasn’t reliable. “Very often, the seal inflated incorrectly or wasn’t strong enough or exploded,” Stassen said.
As a result, dust and fine particles escaped, putting the plant’s compliance with Dutch health and safety guidelines at risk. Spills were also occurring with the original bulk bag dischargers. “We had to do something else,” Stassen said.
On the recommendation of Dutch distributor Matec Techniek, the company turned to Flexicon (Europe) Ltd., which specializes in bulk bag filling and discharging systems.
“We tried one bulk bag filling station, and that reduced our dust big time,” Stassen said. “So we chose to go forward with Flexicon for all 11 stations, followed over the years by nine bulk bag dischargers and numerous flexible screw conveyors. They reduced dust tremendously in the plant.”
The bulk bag fillers are arranged in pairs beneath bins holding the finished graphite product. An operator inserts the bag loops into the fill head’s
FIGURE 1: Pairs of forklift loaded bulk bag dischargers feed raw graphite into tubular cable and flexible screw conveyors which transport it to silos and the milling process. Courtesy: Flexicon
‘ The bulk bag fillers are arranged in pairs beneath bins holding the finished graphite product.’
four retractable hooks and pulls the inlet spout of the bulk bag upward over a heavy-duty flexible collar, which inflates to create a dust-tight seal. A filtered air displacement vent at the fill head prevents escape of dust during filling.
The operator sets the target weight on the programmable logic controller (PLC) and initiates the filling cycle.
A slide gate opens above the filling chute and a rotary valve meters product from the bin above. Load cells beneath the deck are linked to the PLC, which closes the slide gate when the bag reaches the target weight. As the bag fills, a densification/deaeration deck vibrates to stabilize the bag for storage and shipment. The operator deflates the bag spout seal, ties off the bag and removes it with a forklift.
Each operator runs two fillers side by side, connecting a second bag while the first one is filling. When the first bag is full, the PLC automatically signals the system to begin filling the empty bag.
“The operator is continuously busy hanging new bags and taking away full bags,” Stassen said.
The plant unloads incoming raw materials with nine bulk bag dischargers, designed to eliminate dust during discharging, collapse and removal of empty bulk bags, increasing plant safety.
Bulk bags of incoming material are loaded by forklift into the discharger frames. Operators create a dust-free bag/hopper interface by connecting the bag spout to the clamp ring which sits atop the telescoping tube. During discharge, the telescoping tube lowers the clamp ring as the bag empties, applying continual downward tension to keep the spout taut.
Promoting evacuation, extension arms on the dischargers’ upper frames automatically raise the bulk bag into a steep V shape. Bulk bag activator plates raise and lower the opposite bottom edges of the bag, directing material toward the bag outlet spout.
introduce raw graphite into a tubular cable conveyor, which gently moves it to a jet mill on the mezzanine. Courtesy: Flexicon
“In the past,” Stassen said, “we hung the bag from a frame and let the material gravity fall. The bag would look empty but still had 44 or 66 lb. inside and, when we removed the bag, the material ended up on the floor. Now no material remains.”
From the 5-cu ft floor hopper below each bulk bag discharger, a fully-enclosed flexible screw con-
• Understand how accuracy improved in filling fine particles into bulk bags at a graphite plant
• Learn about the conveying and filling process and the equipment needed to ensure the bags are filling accurately.
FIGURE 3: A rotary valve beneath each hopper feeds graphite to a tubular cable conveyor, which gently moves it dust-free to a jet mill for fine grinding. Courtesy: Flexicon
‘ The operator sets the target weight on the programmable logic controller (PLC) and initiates the filling cycle.’
veyor ranging in length between 26 to 52 ft moves the material to several silos.
The conveyors specified are designed to propel difficult-to-move materials that tend to pack, cake, smear, plug or fluidize — or break and slip in the case of graphite — without crushing or grinding material against the tube wall.
Feeding the jet mill line, a tubular cable conveyor moves graphite and coke powder from a dedicated bulk bag discharger. The fine particles exiting the bag flow into a rotary valve that meters them into the conveyor, which consists of ultra-high molecular weight polyethylene conveying discs attached to a steel cable and enclosed inside a polymer tube.
The convey line is a continuous circuit, kept under tension by a wheel near the inlet end and driven by another wheel at the discharge end. The material rides gently in the spaces between the discs. The convey line makes a 90° turn past the inlet and moves vertically to 30 ft (9 m) in height before turning 90° again to the discharge point above the feed hopper and downspouting to the jet mill. The gentle movement reduces risk of abrasion and the enclosed circuit ensures dust-free operation.
After processing, another set of flexible screw conveyors, ranging from 13 to 26 ft, transfers the materials to the bins above the bulk bag filling stations. PE
David Boger is executive vice president, The Flexicon Corporation.
Bulk handling insights
uAsbury Graphite & Carbons plant operators experienced problems with inaccurate fill weights of milled graphite, as well as issues with dust control.
uThey changed their bulk bag discharging and filling systems, reducing dust in the plant and obtaining clean fills at the target weight.
Education and personal development are vital to the advancement of the engineering community.
We invite our readers to explore and utilize the educational efforts of this year’s participants in our annual Educating Engineers program.
pe202308_leadHLF_EduEng.indd 1
ABB Motors and Mechanical
Assured Automation
AutomationDirect
Dewesoft
Digi-Key Electronics
Dodge Industrial
Flexicon
Flowserve Corporation
Lubriplate Lubricants
Motion
SEW Eurodrive
Spiroflow
UW–Madison, College of Engineering
Assured Automation’s automated valve configurator uses a powerful, rules and constraint-based configuration and pricing management technology to deliver complete solutions quickly and accurately.
The online configurator steps the user through the build process, guiding them to select compatible options for optimal pricing and area classifications.
Once the configuration is complete the valve assembly can be viewed in an interactive 3D viewer. CAD models are downloadable in over 150 file formats. A pdf datasheet is generated for the configured valve assembly which includes an embedded 3D model viewer, full page dimension drawing, part numbers and key specifications for valves, actuators, and accessories.
Click here or scan QR to watch our video.
Improve system efficiency, reliability and sustainability by pairing an inverter duty motor with a variable speed drive
About 45% of the electricity used in industry is consumed by the 300 million industrial electric motors at work around the world, many of them old and inefficient. If 80% of the world’s electric motors were replaced with the most efficient motors available, 160 terawatthours of energy would be saved per year.
Replacing older motors with new, high-efficiency models is one way to improve inefficient systems, and performance can be increased further by pairing motors with variable speed drives. The basic function of a drive is to control the flow of energy from the power supply to the motor, thus controlling speed, power and torque output.
Inverter-duty motor/drive systems provide optimal performance for constant-power, constant-torque and variable-torque applications
As a result, systems can be optimized to deliver the right amount of performance – no more, no less.
Inverter duty motors are designed to be paired with drives, ready to be placed into new applications or as an upgrade to optimize existing systems. If motors in operation were replaced with motor/drive systems, global electricity consumption could be reduced by as much as 10%, resulting in a 40% reduction in greenhouse gas emissions. It’s not enough to wait until a motor needs a replacement — proactively replacing
older motors with new motor/drive systems will result in reduced power consumption, longer equipment life and better process control.
ABB’s ID (inverter duty) motors on demand webinar series provides information about the benefits of pairing motors with drives. The series features an introduction into ID motors and how to choose the correct motors for various applications. Also included with the series, whitepapers, podcasts and videos.
Click here or scan QR for more information
utomationDirect provides free online PLC training to anyone and everyone with no purchase necessary.
As the world around us becomes more and more automated, an understanding of electrical control systems becomes more and more vital. Because of this, the demand for training in industrial controls has grown exponentially over the years.
Luckily, AutomationDirect has decided to meet this demand head-on by offering absolutely FREE online PLC training –no purchase necessary!
This online video training course encompasses various levels of training from entry level programming to advanced PLC functions, and is available 24/7/365 so you can learn at your pace and at your convenience.
Some of the general topics covered include:
• Logic circuits
• Basic switches
• Sinking and sourcing
• PLC scan time
• I/O fundamentals
• PLC memory addressing
Scan the QR to view video about training opportunities.
A wide variety of free training videos can be found at automationdirect.com.
Also available are over 200 videos specifically covering AutomationDirect PLCs and include topics on how to use their rung editors, logic instructions, internal control relays, subroutines, communication, data view windows and many other functions.
• CLICK PLC Family Video Library
• Do-more\BRX PLC Family Video Library
• Productivity PLC Family Video Library
This training is provided by AutomationDirect’s education and training partner Interconnecting Automation who has been training automation professionals for more than 20 years. Interconnecting Automation’s instructors pride themselves on providing a “no hype”, “no sales pitch” type of instruction and aim to thoroughly help others learn about PLC products so they are ready to use these products to their fullest potential.
To get unlimited access to the FREE online PLC training or to see more about what is provided, head on over to www.automationdirect.com/plc-training.
Wherever you are, no matter what you are doing, whatever you need, we try our best to cover almost any training need.
There’s a diverse and almost unlimited selection of classes, seminars, tutorials and short courses available today, but how do you avoid getting bogged down with theoretical approaches and get the fundamentals?
DEWESoft believes an approach using how and why, provides a basis for the inevitable conclusion of understanding if your results are correct. By using known and accepted principles and theories to confirm the outcome.
We offer on-line, in person or regional training and seminars which typically start with a ‘hands-on’ approach, where you can become familiar with an entire process.
We believe this helps with better appreciation for some of the factors that can influence outcomes as well as determine the appropriate theories which could or should be applied to ultimately validate your results.
At DEWESoft that is a subset of what we offer, we also have a team of field based application Engineers as well as industry experts that are available if you want to progress further into deeper subject matters. They are supported by a team of front-line support Engineers located at our headquarters in Ohio who
“we encourage what we call the power user status and we will do everything we can to ensure success”
Al Hoge Automation
would be able to walk you through many of the stages to get you started.
We realize that our users are critical to our success, and we know that when tools such as those provided by DEWESoft are used to their fullest potential, others will see and want to follow. So we encourage what we call the power user status and we will do everything we can to ensure success.
Cli Ck or scan QR to learn more
One of the best avenues of education for engineers and designers is DigiKey’s TechForum, a collaboration space where they can search for answers previously asked by other industry members or answers generated by our team of technical staff based on direct interactions. Together with other TechForum participants, we do our best to answer any technical question posted on our Forum.
Additionally, scalable approaches to value-added learning like DigiKey webinars have gained traction because they are focused and targeted vehicles that are presented by subject matter experts for a very specific topic that enable participants to interact, ask questions and get answers in an extremely timely format.
DigiKey publishes hundreds of articles and blogs on our website and makes engaging video content to help people understand how to use technology to turn their ideas
into products. We are also seeing the adoption of new tools that enable collaboration across various platforms and we continue to push communication across a variety of social channels. Today’s younger engineers want easily digestible nuggets and information. Shorter form videos like YouTube shorts or Instagram reels have enabled key topics and messages to be absorbed in these newer formats.
Combining the elements of our training and experience is critical to offering content that can get engineers past design hurdles. We tend to hear from engineers at the most common crossroads
in a design — the initial selection, hardware design, software design, integration, testing or certifications.
To be able to deliver in all these areas requires a combination of not only supporting the technical elements but also having the right products in stock, the right relationships in place and the experience to navigate issues that can stall a design.
Scan the QR code to learn more.
Building on PT Wizard’s legacy of more than 25 years, the platform guides you through product selections, system design, and competitive interchanges.
Like magic, PT Wizard seamlessly connects to PT Place, the Dodge eCommerce platform, to deliver pricing and convert your selections into orders to save time and stay within budget.
PT Wizard is the easy-to-use tool to find the best solution for your application requirements—continuing to honor the Dodge legacy of innovating the future of mechanical power transmission design.
Capabilities:
• Mounted bearing selection and dimensions
• Enclosed gearing selection
• Conveyor pulley assembly design
Create your account to get started at ptwizard.com
• Belt conveyor design
• Product competitive interchange
• Grease calculator for mounted bearings
Learn more at https://info.dodgeindustrial.com/PTWizard
Scan the QR code to learn more about PT Wizard.
bulk material? Understand the fundamental differences between Flexicon Flexible Screw Conveyors, Tubular Cable Conveyors and Pneumatic Conveying Systems
Several conveyors can move your bulk material, but only one is likely to offer the greatest efficiency, dependability and cost effectiveness for your requirement.
Flexible Screw Conveyors can move the greatest diversity of bulk materials, including those that pack, cake or smear, with no separation of blends. Economical to purchase and maintain, they convey at any angle over short to medium distances in low to medium capacities. The removable inner screw is the only moving part contacting material, and is driven above the point at which material exits the conveyor, eliminating contact with seals.
Tubular Cable Conveyors gently slide fragile food and nonfood products through smooth stainless steel tubing routed at any angle over short or long distances in low to high capacities using low-friction polymer discs attached to stainless steel cable.
Flexible Screw Conveyors, Pneumatic Conveying Systems and Tubular Cable Conveyors from Flexicon offer unique attributes relative to individual requirements.
These conveyors are available with single or multiple inlets and outlets, prevent the separation of blends and evacuate material from the tubing circuit, preventing waste and allowing rapid cleaning.
Dilute-Phase Pneumatic Conveying Systems with single or multiple inlets and outlets move bulk materials vertically and horizontally in low to high capacities over short to long distances using pressure or vacuum generated by a blower. Material enters the system through rotary airlock valves, pick-up adapters and wands (vacuum systems), and is separated from the airstream using filter receivers or cyclone separators. Material exits the system through rotary airlock valves or fill/pass valves, or discharges directly into process vessels—with no residual.
While these generalizations may help narrow your conveyor choices, Flexicon recommends running your material in its test laboratories equipped with full-size conveying systems and upstream/downstream equipment to simulate your process.
+1 888 353 9426 sales@flexicon.com www.flexicon.com
Flowserve’s Energy Advantage Program (EAP) helps achieve carbon and efficiency goals with proven engineering expertise and a data-driven optimization of flow loop operations. EAP personnel perform engineering analysis, project management, and execution of aftermarket upgrades, tailored to the industry, application, and other site variables.
The EAP improved the steelworks’ safety, ergonomics, and MTBR; it also reduced unplanned downtime, water, and chemical usage. Estimated Annual Savings/Reductions
• Power Consumption 7200 MWh
• CO2 4320 mt
• Electricity Costs £431,000 | $520,000
• OPEX £242,000 | $292,000
As an example, a UK-based steelworks identifiedopportunities to maximize uptime and Mean Time Between Repair (MTBR) while reducing energy and maintenance costs. EAP engineers conducted an extensive engineering assessment on several key hot rolled products and processes for their water pump applications, observing processes around flume flushing, furnace feed, cross spray, and several other pump-related processes. Using Distributed ControlSystem data, in-situ performance testing and system walk-downs, EAP engineers established actual needs for each of these pumping services.
By taking a holistic view of the system requirements, theteam identified improvement opportunities related to sub-optimal thermal balances, excess throttling, and off-design operation. Extensive failure mode and effects analyses were conducted for each of the pumping services. Flowserve’s expertise as a pump and control valve OEM helped define numerous design, operation, and maintenance improvements to further reduce the TCO for the steelworks.
Flowserve’s EAP helps companies realize measurable results in a wide variety of industries and applications — naphtha cracking, coal-fired power plants, pipeline, and nuclear, just to name a few. Achieve sustainability goals and lower TCO with an enhanced, holistic flow control approach. CLICK here or scan the QR Code to get in touch with Flowserve’s EAP engineering team.
Log on to our website and find all the information you need about industrial lubricants. From mineral based greases and oils to the latest high grade synthetic fluids, the data is compiled in our Lubriplate Lubrication Data Book that you can download at no cost to you.
Also available in digital format are important specification and product information sheets on H1 Food Machinery Lubricants, Environmental Lubricants and more.
Complete data on drop points, cold tests, viscosity indexes, ISO grades, AGMA numbers, etc. is included. There is lubricant information available regarding compressor fluids, hydraulic fluids, bearing lubricants, power transmission fluids, specialty lubricants, high grade greases and more.
If you have a specific question you may also talk with one of our lubricant representatives at 1-800 733-4755 or e-mail lubeXpert@lubriplate.com
Maintaining engineers’ critical skills should be a top priority for any company. Engineers are often involved with various activities, such as plant layouts, productivity enhancements to existing equipment, determining if new equipment costs are warranted, implementations and product designs. To obtain the best results, your engineers must be up to date on the latest industry innovations. Fortunately, keeping your engineers current on their skills is not daunting if you keep these simple suggestions in mind:
1. Encourage your engineers to belong to and participate in engineering-related professional organizations. Many of these organizations offer training and development and provide resource materials to members. In addition, these organzations provide networking opportunities for your employees to exchange best practices with others in their field. Lastly, train your engineers to look out for good talent when attending networking events, and you just may find yourself landing some great new team members for your company.
2. Develop a relationship with a local university with an engineering school. Most universities have ongoing development opportunities, and many are more than willing to customize training for your employees. Like professional organizations, this route also gives your engineers a good chance to network.
3. Collaborate with your key suppliers to discover learning and development opportunities they can provide or coordinate for you. Well-established suppliers either have their own content or work closely with manufacturers to offer training for end users.
Remember, if you take care of your engineers, they will take care of you!
For more information, visit Motion.com/plantengineering and Motion.com/learning-development.
Want to learn about engineering topics pertaining to gearmotors? We have the information at your fingertips!
Tired of looking up multiple sources for answers to common engineering questions about gear units or gearmotors? We have the solution.
SEW-EURODRIVE’s online
Technical Notes can be a real life-saver when you need answers. Technical Notes provide quick access to many engineering topics such as how to properly mount a torque arm, how to determine and design for inertia, or how to properly design your machine to use a hollow shaft gear unit.
Need answers on how the speed, mounting position, environment, and duty cycle can affect the thermal rating of a gear unit and how to protect against too much heat? That’s one of many in-depth documents you can find by visiting www.seweurodrive.com and clicking Technical Notes
Scan QR code to access Technical Notes on your smartphone.
Our technical white paper, Maximizing Gearmotor Speed Range shows you how to operate VFDs above 60Hz to widen speed range, improve stability and reduce cost.
In this white paper, you’ll learn why it can be a good idea to operate gearmotors above 60Hz. Through a common example, we will show you how to select the proper gearmotor that will significantly enhance performance in the following ways:
• Increase stability by reducing inertia mismatch
• Widen the available speed range
• Eliminate a costly ventilator fan at low speed
• Eliminate motor overheating at low speed
• Enable the use of a smaller motor
Visit www.sewwhitepapers.com/vfd to download the PDF.
mktg@seweurodrive.com 864-439-7537 www.seweurodrive.com
When it comes to material conveying systems, selecting the right solution is crucial for maintaining operational efficiency and product integrity. By understanding what criteria is most important to you, you can make an informed decision on the ideal solution for your material conveying needs.
Some Key Features and benefits of Flexible Screw Conveyors to consider:
Design Simplicity: Look for systems that have straightforward designs, like those with an electric motor-driven spiral as the sole moving part and easy to adjust inlet configurations. These features enhance reliability and performance and make maintenance easier.
Dust-Free Operation: To prevent hazards and product contamination, choose a system that ensures fully sealed operations. A fully enclosed Flexible Screw Conveyor can help prevent dust contamination, eliminating the need for additional filtration and dust collector maintenance.
Easy Cleaning: Ensure you are looking at systems that offer easy cleaning procedures. For example, some systems allow for quick disassembly or include clean-in-place options. With some Flexible Screw Conveyor designs you can reverse the motor to empty any residual material, this is then followed by quick disassembly options for thorough wet or dry cleaning.
Constant Remixing: Certain conveying technologies can cause blends of products to separate during transfer while others, such as the Flexible Screw Conveyor, allow for constant remixing of materials. If maintaining a uniform mix is a key consideration, the Flexible Screw Conveyor may be a good option for you.
To help you determine when a Flexible Screw Conveyor might be the best option, Spiroflow has launched a comprehensive to help you decide if it is the right solution for your needs. The Flexible Screw Conveyor guide is designed to educate you on the various features and benefits of the system. Click here to download the guide.
sales@spiroflow.com • 704-215-4624 Spiroflow.com
Keep pace with the latest innovations and technology with our Maintenance and Reliability Management (MRM) courses. Each course features practical, problem-solving strategies, designed to help new and experienced maintenance and reliability professionals.
The certificate program is designed for those who are involved in their company’s asset or maintenance management program, part of the change process in their maintenance and reliability transformation, new to the field, and senior members of the maintenance team who are tired of doing the same thing and getting the same results, constantly putting out fires, and never having the time to do things right.
“I think Sub-Zero [benefitted] right away, because there are takeaways from the classes. Even a couple days later there will be an issue or question in this department, and you have that little lightbulb moment ‘Oh, I just talked about this the other day in class, and now I can use my skills I just learned.’”
— Callie Pankow, Sub-Zero
Handle complex maintenance challenges, network with individuals experiencing similar problems, and learn from instructors with decades of practical experience.
“It’s been incredibly helpful to utilize some of the things that I’ve learned up there and bring it back here, and actually get to work on implementing some of the things that I got excited about hearing in the classes. So at least in my company, [the MRM Certificate] is held in high regard.”
— Carl Kottke, PCI Pharma Services
Scan QR to view course offerings and learn more.
Enroll in one required course and take four additional courses to achieve your MRM Certificate. Your participation in courses is tracked and you may verify your progress at any time by requesting a UW Transcript.
Learn in-person and online
Interdisciplinary Professional Programs
432 North Lake St. • Madison, WI 53706
Learn more, view available courses, and register now to begin your journey with the MRM Certificate from Interdisciplinary Professional Programs (InterPro) at UW–Madison’s College of Engineering. Go to interpro.wisc.edu/MRM Maintenance and Reliability Management Cer ficate
custserv@interpro.wisc.edu
800-462-9876 • interpro.wisc.edu
ABB Motors US .C-4 .https://baldor .abb .com/ec-titanium
AssetWatch .25 .www .AssetWatch .com
AutomationDirect .C-2 .www .automationdirect .com
Boston Dynamics .35 .https://bosdyn .co/automate-inspection
CARLTON .16 .www .carltonusa .com
CFE Media GSI Database .34 .https://gspplatform .cfemedia .com/si/home
CFE Media LLC .24 .www .cfemedia .com
CFE Media NPE Database .34 .https://gspplatform .cfemedia .com/pe/home
ContiTech .41 .www .continental-industry .com
Digi-Key ELECTRONICS .17 .WWW .DIGIKEY.COM
Dodge Industrial .1 .www .dodgeindustrial .com
Flexicon Corp .6 .www .flexicon .com
Industrial Cybersecutiy Pulse .28 .www .industrialcybersecuritypulse .com
Lubriplate Lubricants Co .12 .www .lubriplate .com
MAPCON .16 .www .mapcon .com
MOTION .4 .www .Motion .com
Raymond Corporation .43 .www .raymondcorp .com/POY2023 ROYAL PRODUCTS .64 .www .mistcollectors .com
SEW-EURODRIVE, Inc .2 .www .seweurodrive .com
SHERWIN-WILLIAMS .11 .www .sherwin .com
spiroflow .29 .www .spiroflow .com
Standard Time .16 .www .stdtime .com/shop-floor
WELDBEND .38, 39 .www .weldbend .com
Workbenchmarket .42 .www .workbenchmarket .com Yaskawa America, Inc .C-3 .www .yaskawa .com
Publisher/Midwest
Matt Waddell MWaddell@CFEMedia.com
3010 Highland Parkway, Suite #325 312-961-6840
Downers Grove, IL 60515
Account Manager
Robert Levinger RLevinger@cfetechnology.com 630-571-4070 x2218
West, TX, OK
Aaron Maassen AMaassen@CFEMedia.com Integrated Media Manager 816-797-9969
Northeast
Richard A. Groth Jr. RGroth@CFEMedia.com 12 Pine Street 774-277-7266 Franklin, MA 02038
Director of Content Marketing Solutions
Patrick Lynch PLynch@CFEMedia.com 3010 Highland Parkway, Suite #325 847-452-1191 Downers Grove, IL 60515
Marketing Consultant
Brian Gross BGross@CFEMedia.com
3010 Highland Parkway, 630-571-4070 x2217 Suite #325
Downers Grove, IL 60515
Jim Langhenry, Co-Founder and Publisher, CFE Media JLanghenry@CFEMedia.com
Steve Rourke, Co-Founder, CFE Media SRourke@CFEMedia.com
McKenzie Burns, Marketing-Events Manager MBurns@cfemedia.com
Courtney Murphy, Marketing and Events Manager CMurphy@cfemedia.com
Paul Brouch, Director of Operations 630-571-4070 x2208, PBrouch@CFEMedia.com
Rick Ellis, Audience Management Director 303-246-1250, REllis@CFEMedia.com
Michael Smith, Creative Director 630-779-8910, MSmith@CFEMedia.com
Michael Rotz, Print Production Manager 717-422-3622, mike.rotz@frycomm.com
Maria Bartell, List Rental Account Director Infogroup Targeting Solutions 847-378-2275, maria.bartell@infogroup.com
Claude Marada, List Rental Manager 402-836-6274, claude.marada@infogroup.com
Letters to the Editor: Please e-mail your letters to ARozgus@CFEMedia.com
Letters should include name, company, and address, and may be edited for space and clarity.
Information: For a Media Kit or Editorial Calendar, go to www.csemag.com/connect/advertising
Marketing consultants: See ad index.
Custom reprints, electronic: Paul Brouch, PBrouch@CFEMedia.com
TM Technology and
From fractional to 600 HP, Yaskawa industrial drives cover all of your application needs, with an array of features that improve your operations.
Intuitive Mobile-Friendly Interaction
Fast Connection to Any Major Network Protocol
Functional safety rated - Standard
Best-in-class Efficiency
And don’t forget about everything else Yaskawa provides you with.
World-Class Quality and Reliability
Award Winning Customer Service
Product Lifetime Training
Free 24/7/365 Technical Support
Life getting too complicated?
Contact Yaskawa for help today.
Sustainable non-toxic environmentally friendly components —
Plug and play
Quick and easy motor and drive set-up
A greener solution
Reduce your power consumption with industry leading rotor technology
Upgrade to ABB’s Baldor-Reliance® ultra-premium EC Titanium™ integrated motor drive, and lower your overall energy cost. These motors are specifically designed for VFD operation that help optimize overall performance at reduced speeds and loads, ideal for fans, pumps, and compressors.
• More than 10% efficiency gains compared to NEMA premium
• Reduce power consumption by 25%
• Higher power density for a smaller footprint
Efficient. Innovative. Environmentally friendly. baldor.abb.com/ec-titanium