
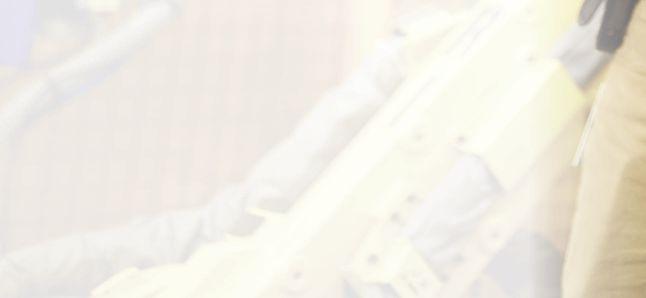
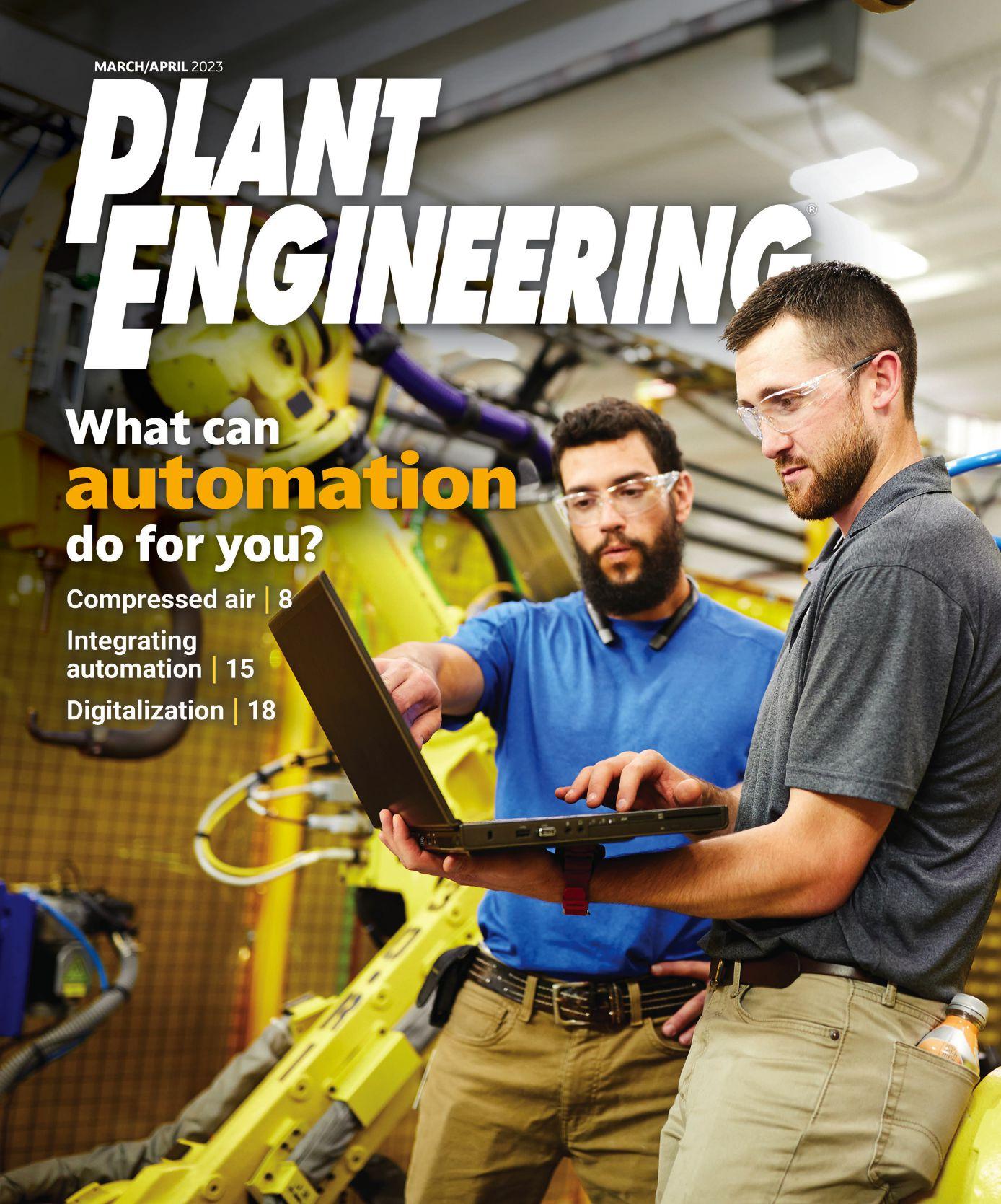
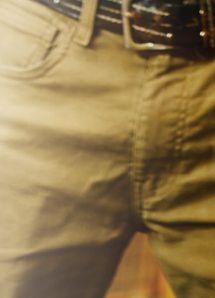
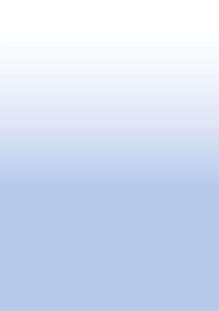

Ventilated Drive Isolation Transformers (NEMA Rated)
Hammond HPS drive isolation transformers are designed to withstand the mechanical stresses, voltage distortions, and heating associated with motor drives. They provide all of the bene ts of a line reactor; the extra reactance reduces harmonics and the e ects of voltage and current distortion caused by the variable speed drive.
• They provide isolation between the drive system and the power source
• When the wye connected secondary is grounded, it prevents the transfer of common-mode noise and transients between the voltage source and the drive system
• They localize the effects of drive-induced ground currents and prevent them from being passed upstream to the power system
Ventilated Distribution Transformers
Hammond Power Solutions (HPS) Sentinel G series ventilated distribution transformers o er high e ciency and lower heat emissions, which result in lower operating ownership and air cooling costs.
• Dry-type 3-phase distribution transformer
• Open coil/core ventilated
• Meets DOE and NRCan requirements
• VA range from 15 to 75kVA
• Electrical grade silica sand and resin compounds enclose core & coil, which eliminates moisture, contaminants and corrosion
• 100VA to 25kVA (HPS) and 3kVA to 15kVA (ACME)
• 120 to 600VAC ACME 1-ph transformers
• 120 to 480VAC (HPS 1-ph) and 480VACΔ to 600VACΔ (ACME 3-phase)
• 240 and 120VAC (HPS) and 208Y/120VAC, 480Y/277VAC, 240Δ/120VAC (ACME)
• Used to power loads requiring a higher/lower voltage than the available line voltage
• Can buck (lower) or boost (raise) line voltage from 5 to 20 percent
• Single-phase units from 0.25 to 5.0kVA at 60Hz operation (individual units required for multiple phases)
• Encapsulated with electrical grade resin with cores of high-quality electrical steel
• Maximize inrush capability and provide reliable output voltage regulation when an electromagnetic device is energized
• VA range from 50VA up to 1500VA at 50/60 Hertz
• 600V class, machine tool rated
Servo motors and gear units offer a high degree of dynamics and performance with a compact design, making them excellent for confined spaces. Multiple frame sizes and torque ratings makes them the perfect fit in material handling, hoist and gantry
applications, and a wide variety of machine automation applications. Their modular design allows for direct gear unit mounting without adapters or couplings. Pair that with the option of single-cable technology and you’ve got a flexible, precise servo drive solution.
5 | How will artificial intelligence change the job of the plant manager?
Will you lose your job to artificial intelligence? How AI is changing the game
8 | Leveraging the future of compressed air through automation
Automated, remote and integrated monitoring all play a role in the efficient “smart plant”
15 | Create a strategic plan when integrating automation in manufacturing facilities
Plant owners must develop a strategic plan about their integration process
18 | Three pillars for digitalization success
The path to a digital production facility starts with capturing benefits by tying lean practices to data collection 22 | Enhanced Ethernet benefits for manufacturing operations
Time-sensitive networking (TSN) is having a major impact on future operations
| Considerations for choosing the right flyback diode and rating
There are several important considerations when selecting flyback diodes
| Condition-based maintenance keeps a facility up and running
Learn how to protect facility assets with condition-based maintenance
34 | Minimizing the oil and gas workforce skills gap with cloud connectivity
Oil and gas companies are integrating IIoT cloud-based automation to mitigate the skills gap
39 | Pneumatic line abrasion resisted with deflection elbows
Waupaca Foundry deployed deflection elbows to reduce pneumatic line abrasion at two of its facilities
PT Wizard is the easy-to-use platform to find the best solution for your application requirements with a guided experience to help you select Dodge products quickly and easily.
Product selection by application, dimension, or assembly design
Belt conveyor system design
Mounted bearing grease calculator
Single-part interchange tool info.dodgeindustrial.com/ptwizard
AMARA ROZGUS, Editor-in-Chief/Content Strategy Leader ARozgus@CFEMedia.com
CHRIS VAVRA, Web Content Manager CVavra@CFEMedia.com
MICHAEL SMITH, Creative Director MSmith@CFEmedia.com
AMANDA PELLICCIONE, Director of Research APelliccione@CFEMedia.com
SUSIE BAK, Production Coordinator SBak@CFEMedia.com
H. LANDIS “LANNY” FLOYD, IEEE Life Fellow JOHN GLENSKI, President, Automation Plus
Are you a subject matter expert in one of these topics? Would you like to author an article on one of the topics below? If so, please submit an idea to: https://tinyurl.com/PlantEngineeringSubmissions
• Efficient motor management
• Expert Q&A: VFDs and VSDs
• Expert Q&A: Hazard protection and hazardous environments
• Material handling
• Pneumatic and hydraulic controls
• Power and electrical systems maintenance
• Predictive maintenance
• Process piping
• Pumping and liquid movement
Content For Engineers. That’s what CFE Media stands for, and what CFE Media is all about — engineers sharing with their peers. We welcome content submissions for all interested parties in engineering. We will use those materials online, on our Website, in print and in newsletters to keep engineers informed about the products, solutions and industry trends.
* https://tinyurl.com/PlantEngineeringSubmissions gives an overview of how to submit press releases, products, images and graphics, bylined feature articles, case studies, white papers and other media.
* Content should focus on helping engineers solve problems. Articles that are commercial in nature or that are critical of other products or organizations will be rejected. (Technology discussions and comparative tables may be accepted if nonpromotional and if contributor corroborates information with sources cited.)
* If the content meets criteria noted in guidelines, expect to see it first on the website. Content for enewsletters comes from content already available on the website. All content for print also will be online. All content that appears in the print magazine will appear as space permits, and we will indicate in print if more content from that article is available online.
* Deadlines for feature articles vary based on where it appears. Print-related content is due at least three months in advance of the publication date. Again, it is best to discuss all feature articles with the content manager prior to submission.
LEARN MORE AT:
https://tinyurl.com/PlantEngineeringSubmissions
Will you lose your job to artificial intelligence? How AI is changing the game
Artificial intelligence (AI) is transforming every industry and manufacturing is no exception. In the past, manufacturing was a tedious and labor-intensive process, but with the advent of AI, the sector is becoming more efficient and streamlined. AI technologies can help plant engineers and managers achieve higher levels of productivity and quality. Here, I will explain — using ChatGPT, the AI chatbot tool — how AI will aid manufacturing plant engineers and plant managers in their job.
end customer. In turn, this will lead to higher customer satisfaction and fewer returns.
Amara
AI can also help plant managers optimize their production processes. By analyzing data from machines and sensors, AI can identify areas where efficiency can be improved. This information can then be used to optimize production schedules and reduce waste. The result is a more efficient manufacturing process that can produce more products with fewer resources.
One of the main advantages of AI in manufacturing is predictive maintenance (PdM). PdM involves analyzing data from machines to predict when they are likely to fail. This information allows plant engineers to take preventive measures before the machines break down, saving time and money. By implementing AI technologies, plant managers can reduce downtime and maintenance costs, leading to increased productivity and efficiency.
Another way that AI can aid plant engineers and managers is through quality control. Quality control is an essential aspect of manufacturing and AI can help improve it by detecting defects and anomalies in products during the production process. This means that plant managers can catch problems early, preventing them from reaching the
Moreover, AI can help plant managers manage their inventory better. By analyzing customer demand, AI can predict which products will sell the most and which ones will be less popular. This information can be used to adjust inventory levels, ensuring that the right products are always in stock. This will prevent overstocking or understocking, leading to more satisfied customers and higher profits.
However, some critics argue that AI will replace human workers in the manufacturing industry. While it is true that some jobs may become obsolete, AI will create new jobs in the industry. According to a 2020 report by the World Economic Forum, AI was predicted to create 133 million new jobs globally within two years (too bad it didn’t predict COVID-19). This content was enhanced with ChatGPT. Due to the limitations of AI tools, all content was edited and reviewed by our content team. PE
• The Lead Flexicon Project Manager supervising your system offers you a single point-of-contact through every phase of development, streamlining your communications
• Strict adherence to your unique standards, documentation requirements and timelines
• Commitment to the successful performance and cost effectiveness of your project by serving as your dedicated advocate
• Engineering teams on four continents relieve your staff of overloading
• Over 25,000 bulk handling installations worldwide provide the breadth and depth of experience essential for seamless integration with your upstream and downstream processes
• Ability to work with the engineering firm managing your entire project, or directly with your team
• As one of the world’s largest manufacturers of bulk handling systems, Flexicon can provide the engineering, manufacturing, outsourcing, integration, programming and validation of your project—eliminating the risk of coordinating multiple suppliers
• Greater efficiency and control than available through diversified engineering firms, dedicated equipment makers or in-house engineering departments with limited time and/or bulk handling experience
Don Orban, Sullair LLC, Valparaiso, Indiana
Automated, remote and integrated monitoring of systems and machines all play a role in the efficient “smart plant” and automating compressed air systems through remote monitoring plays a key role
Big data, cloud computing, the Internet of Things (IoT) and Industry 4.0 are part of a larger movement where everything is interconnected. In business and manufacturing, IoT means connecting machinery to edge devices that collect and share data with any web-enabled device that can access the internet and has permission.
This allows businesses to leverage technology to improve products and services or streamline business processes. This includes assembly automation, process design, controls engineering, software integrations, remote monitoring and more.
With automation advances and machine learning (ML), the Industry 4.0 revolution provides companies with an opportunity to create a unified, real-time view of their business that can be used for better strategic decisions at all levels.
As budgets and workforces tighten and specialized expertise is exchanged for more generalized, jack-of-all-trades skill sets, the need for automation in manufacturing facilities and the enhanced insight has increased. From the production floor up to the C-suite, employees can now have actionable insights at their fingertips. Whether it is one system or the integration of the entire facility, the future is here and the IoT is changing how we build, design and maintain our equipment and processes in many ways.
Compressed air is the life blood of nearly 80% of all manufacturing in the world and accounts for 10% of all electricity in manufacturing in the United States according to the U.S. Department of Energy. Compressed air is often referred to as the fourth utility because of its ubiquitous role in manufacturing. Despite its important role in manufacturing, at the end of the day, most users of compressed air just want consistent, clean, dry air.
The IoT’s opportunities for automation include compressed air systems. Remote monitoring features, which are available on most modern air compressors, can help maximize the system’s efficiency and reliability in several ways:
• Capturing historical performance data. Monitoring controls collect data points on functions such as pressure changes, compressor flow, discharge temperature and run hours. Plant personnel can monitor performance and other metrics right
from their computer. The data is stored, providing a historical snapshot of a system’s performance over time. This allows users to track trends and make data-driven capacity decisions as a facility’s air power needs change.
• Providing timely maintenance and service alerts. Customized alerts delivered to the user’s dashboard can signal when it is time to change a filter or perform other maintenance. Alerts also can indicate if a potential issue such as a loose bearing or reduced pressure due to dirt or foreign material in the system needs to be investigated. These alerts help avoid costly and often devastating downtime by indicating and even predicting when maintenance is needed. Because this dashboard is online, plant personnel can monitor the system’s performance while away from the plant for added peace of mind.
• Maximizing efficiency. Many systems waste up to 30% of compressed air through leaks, misuse, poor maintenance and improper system control according to the U.S. Department of Energy. Remote monitoring allows a user to see when air demand has increased without a corresponding increase in output. Users can make necessary repairs or adjustments to the compressed air system and eliminate wasted air and wasted energy.
Another type of remote monitoring is managed or outsourced air. Managed services are some of the fastest-growing sectors of the technology industry. Limited skilled labor, an unreliable supply chain, uncertain inflationary pressures and the rising cost of financing are just a few factors that make managed air power an exciting and attractive option. Managed air is different from remote monitor-
ing because the data points and alerts on the compressed air system go directly to the compressed air supplier. The supplier remotely manages the compressed air without involving on-site plant personnel. Most importantly, the compressed air supplier delivers not only the monitoring service, but the actual compressed air machinery.
The customer pays a simple service fee each month for an agreed-upon time period (often seven to 10 years) and the equipment, monitoring and backup air are managed for the customer. If maintenance or service is needed, the compressed air supplier takes care of the repairs or service, which is often included in the air supply contract. The supplier also monitors the entire compressed air system’s efficiency and can even make recommendations on how to adjust the system as the customer’s needs evolve.
In addition to the hands- and headache-free supply of compressed air managed air provides, there is also an efficiency factor. With managed air, the compressed air supplier will conduct a thorough air audit at the start of the contract to determine the current and potential needs for the customer. They then design and install the most efficient compressed air system for that operation, which is based on data-driven analysis.
Another key difference with managed air is there is no capital expenditure required. Funding for capital expenditures and new projects can be a long and arduous process in many organizations. With
solve customers’ key operational and productivity challenges.
• Learn how the Internet of Things (IoT) is leveraged in plant automation.
• What compressed air remote monitoring and outsourced air are and what benefits each provide manufacturing facilities.
• How and why integrating all systems in a manufacturing facility can facilitate data-driven decision making.
managed air, the customer pays a monthly fee without having to endure lengthy approval processes, internal budging constraints and more.
Because the monthly fee for outsourced air can be classified as an operational expense, there may be tax advantages to this option, as well. What the customer gets at the end of the day is a modern compressed air system with an uninterrupted supply of compressed air without having to pay a high upfront cost.
Compressed air monitoring and managed air’s future lies in what and how much is monitored to facilitate predictive analysis. While many key functions of the air compressor can be monitored, the next generation of compressed air remote monitoring will be in expanding what functions and to what extent those functions are monitored. Using data to go deeper into predictive maintenance to synthesize action plans, based on aggregated information will be standard in the future.
Added service alerts and parts ordering based on activated alerts are tools that will likely become commonplace with compressed air systems. Think of a car’s low gas gauge warning that prompts the driver to head to the nearest gas station. The same will be true for compressed air; monitoring systems will direct users with links to parts or to request service calls, ship filters or other aftermarket parts providing added convenience, tracking and speed.
When it comes to automating the rest of the plant, producing actionable machine performance data requires integrating many levels of company data from a variety of processes and machinery — not just the air compressors powering the plant. From machines on the floor up, smart factories must bring those disparate data points into a single source of truth. This can now be done by tapping into existing monitoring features and software tools, minimizing the need to make major upgrades to a system.
“Digital applications are designed to give a person a view and allow each one to make a different decision about what they are interested in seeing — bottlenecks, downtime, equipment failure. Customers want their data transformed into something that a CEO, an engineer, maintenance and more can understand in real time,” said David Vitale, chief engineer of digital solutions for JR Automation, an integrator of manufacturing automation systems.
Custom technology solutions for every application, process and industry are now the norm in modern manufacturing facilities. Once the data from the varying systems is brought together onto one screen, many improvements can be made.
Perhaps the most important is keeping the company’s operations in motion. Having access to the health of the equipment not only allows teams to quickly respond to potential bottlenecks and downtime, but engineers can also have up-to-date analysis that allows for planning repairs, improvements, expansion or upgrades.
Real-time data also opens the door to anticipating issues before they happen throughout the system.
“The ability to take raw data from the manufacturing process and turn that into insightful, proactive and perhaps even predictive capabilities has been a game-changer for the industry,” said Bob Hynes, JR Automation director of sales for digital solutions.
Benefits extend beyond the equipment on the floor. Customers integrating their data can improve their inventory control and traceability, supply chain visibility, production planning and scheduling. At an organizational level, the
benefits can be significant. Companies report improvements in the overall equipment effectiveness, throughput, uptime, speed to market and asset use. It also can result in significant reductions in labor costs, energy usage and overhead requirements.
In the end, the biggest results come from remembering why those systems were created in the first place. When data and equipment are integrated, it’s crucial to know how to use it in a way that actually improves the business. This means understanding the big picture of what problem the customer is trying to solve.
From productivity improvement to quality enhancement, understanding that motivation provides better transparency when it comes to how the operator works with the equipment. This enables better use of data to resolve the issue in a collaborative manner.
Plant automation is here to stay and the future is exciting and boundless. From optimized efficiency to performance transparency and pre-
‘ Real-time data also opens the door to anticipating issues before they happen throughout the system.’
dictive maintenance, the benefits of automated systems are numerous. And the ability to make data-driven decisions has repercussions beyond the bottom line. It allows manufacturers to do more with less and do it more efficiently. IoT has made our personal lives easier and is now providing the convenience in our working lives. PE
Don Orban is product manager - IoT and digital commercial solutions, Sullair LLC. He is a technical leader with more than 25 years of experience in IT and product management including building and managing SaaS solutions for the U.S. Government.
Advertorial
Compressed air
uCompressed air is often referred to as the fourth utility because of its ubiquitous role in manufacturing.
uImproving compressed air in a facility can be done by companies making insightful and data-driven decisions.
Protect: heat exchangers, spray nozzles, instrumentation, pump seals, I.E. & R.O. units,aircompressorsandtheenvironment.
Remove: airborne particles, sand, gravel, algae, pollen, silt, scale, rust, microbiological growth, zebra mussels and other dirt particles down to micron size.
Applications: anywhere that dirt is a problem–cooling water, process water, reclaim water, effluent water, intake water, waste water, wash water, potable water.
213 S.Van Brunt St., Englewood, NJ 07631 (800) 567-9767
(201)568-3311 • Fax(201)568-1916 www.orival.com • filters@orival.com
Users: U.S. government, municipalities, big 3 automakers, steel mills, major oil companies, commercial buildings, food, chemical, pharmaceutical, plastics, paper, car/rail washes, mines, power.
In 2023, Atlas Copco celebrates our 150th anniversary. From the United States compressed air and gas team, we want to say a heartfelt ‘thank you’ to all our employees, customers, and suppliers who have been part of our journey –we could not have achieved it without you! As we pass this milestone, our unwavering commitment is to continue to provide innovation which empowers our customers to grow and drive society forward.
Perma automatic lubricators provide clean, safe, reliable and consistent machinery lubrication every day around the clock. They are fully programmable and deliver the right amount of lubricant consistently, day after day, week after week. A wide range of types and sizes are available to meet your exact needs. All come ready to install pre-filled, available with a wide variety of Lubriplate Quality Greases and Oils. They save time, lower maintenance costs and improve workplace safety.
Plant owners must develop a strategic and comprehensive plan about their integration process to optimize production long-term
Modern automation technology is transforming the food manufacturing landscape. New advancements can mitigate safety risks, increase productivity, reduce downtime, and improve quality and accuracy with fine-tuned precision.
Of course, these solutions require capital investment upfront, but the long-term return on investment is hard to ignore. The good news is technology is getting cheaper and easier to implement with every year that passes. While the barrier is shrinking, manufacturers still face another challenge: What happens when these sophisticated systems need maintenance or repairs?
According to the U.S. Bureau of Labor Statistics, the average turnover in the manufacturing industry at 40%. As the data suggests, hiring, training and retaining skilled technical workers who can service a plant’s automated processing lines isn’t as straightforward as it may appear.
A system integrator (SI) can help companies achieve their goals with comprehensive solutions. An SI partner can offer tried-and-true ideas to mitigate risk and build efficiencies into new and existing processes.
Vetting qualified SI professionals is a demanding, critical process. The greatest value lies in establishing a partnership with an SI who will evaluate the facility’s unique system, layout and objectives to develop a tailored, long-term strategy
for integrating systems and technology to achieve performance goals.
Consider the following questions to help make the decision easier:
1. Can the integrator demonstrate a list of executed projects and/or clients with examples of challenges they helped overcome?
2. Do they understand the short — and long — term corporate and plant goals?
3. What is their implementation methodology?
4.Do they have a consistent team? Who does it include?
• Automation provides substantial ROI in manufacturing settings, but there’s a shortage of skilled technical workers to support sophisticated facilities. Investing in more automation can be the answer.
• System integrators can help plants identify opportunities for improving their processes with the latest technology and recommend strategies to mitigate risk.
• Facility owners should consider the maintenance needs of their technology upfront and invest in preventative solutions to minimize maintenance time.
5. Do they offer startup support and to what extent?
6. How do they handle system knowledge transfer to plant personnel?
7. How do they approach migrating a complex system with minimal downtime?
Owners also must be wary of SIs who want to implement sweeping changes without regard for the existing process, plant and personnel. Each recommendation, especially when it involves modifying existing standards, must have a reason behind it and the SI should be prepared to explain it to stakeholders.
Automation is an integral component of a modern facility’s competitive advantage. In addition to
enabling rapid throughput, robotics and automation solutions can help minimize production issues stemming from fluctuating factors like labor availability, supply chains and material prices. Even small adjustments can result in significant savings and greater ROI.
If a piece of technology fails, there are proactive strategies facilities can integrate to mitigate risk and reduce downtime. Being proactive is general best practice, but it is especially useful when running a plant with sophisticated systems and automation.
When owners embark on a new project — whether it’s building something new, expanding or upgrading – they’re often so focused on the design and construction aspects they don’t consider the resources needed to support and maintain the facility’s ongoing operations.
Companies don’t often hire and train mechanical and technical control personnel until they’re ready to start production. This timeline creates unintended knowledge gaps that can slow down the ramp-up process because critical knowledge is exchanged during the design, startup and installation phases.
Embedding key operators and maintenance staff in early phases and allowing them to provide input about improving processes and operations can be extremely beneficial. Automation design is increasingly sophisticated to maintain and operate. Why wouldn’t you want staff to know exactly how a new piece of equipment is built and wired before issues occur? With this approach, you’ll already have a trained and knowledgeable crew who can support the plant without delay as soon as the startup phase is complete.
Bringing a facility up to speed with the digital era requires legwork. There are many facilities where operators still use paper and pencil for record-keeping. If there’s a problem, it might take the person troubleshooting many hours to locate the right documents and sort through stacks of paperwork to figure out what went wrong. Worse yet: The handwriting may be illegible. Going offline to address administrative issues like these can cost a facility millions of dollars.
AutomationDirect is a non-traditional industrial controls ideas from the consumer world to serve your automation quality products fast for much less than traditional suppliers, every step of the way. See below . . .
Our campus is located about 45 minutes north of Atlanta, GA, USA. We’re all here - our sales and technical support teams, purchasing, accounting, and of course our huge warehouses and speedy logistics team.
You want complete product information to make the right purchase decision.
Whether you’re deciding on purchasing our products or learning our products after you buy, why jump through hoops or even pay for the information you need?
We have exhaustive documentation all freely available online, including overviews, technical specifications, manuals and 2D and 3D CAD drawings.
We have over 1,200 videos online to get you up to speed quickly. We even provide FREE online PLC training to anyone interested in learning about industrial controls.
http://go2adc.com/videos http://go2adc.com/training
For over 25 years, we’ve been offering a better by running our direct business efficiently and you. No complex pricing structures or penalty everyday prices on everything from fuses to Programming software for controller products can be costly, so we help you out by offering FREE downloadable software for all our latest PLC families and C-more HMIs. No license or upgrade fees to deal with!
http://go2adc.com/why
You don’t want to wait for your
We have fast shipping, and it’s FREE if your order is over $49.*
At AutomationDirect, we strive to have what you it. We’ve invested heavily into infrastructure, inventory, automation so that we can continue to provide you products, at great prices, extremely fast!
*Order over $49, and get free shipping with delivery in 2 business the U.S. (Certain delivery time or shipping cost exceptions may Conditions online for complete details. http://go2adc.com/terms
You insist on getting better service and you want it FREE.
Our technical support team provides superior assistance and has consistently received high ratings from satisfied customers. And it won’t cost you a cent!
Before, during, and after any sale, contact us with questions and we’re glad to help, http://go2adc.com/support-ss
company using the best automation needs. We deliver suppliers, and support you
great prices.
better value on industrial controls and passing the savings on to penalty for small orders, just low motors.
Our primary focus has always been customer service — practical products, great prices, fast delivery, and helpful assistance. But the intangible value of customer service is something that cannot be faked, automated or glossed over.
Our team members here at AutomationDirect approach every day with one goal in mind - serve the customer. If the answer to any decision is “Yes, this is good for our customers”, then we do it, whether personally or via self-serve features on our site.
need, when you need inventory, and warehouse you with quality
business days (or less) within may apply; see Terms and http://go2adc.com/terms) your order.
You want to be confident in our products and our commitment to you. We stand behind our products and guarantee your satisfaction. We want you to be pleased with every order. That’s why we offer a 30-day money-back guarantee on almost every stock product we sell. (See Terms and Conditions online for exclusions.)
BRIAN in CLEVELAND, TN:
“Automation Direct has a great website with in-stock visibility. Everything I’ve ordered has been great quality parts and definitely better value than other brands. Customer service is prompt on emails and I love the free 2-day shipping!!”
CODY in MOORESVILLE, NC:
“Excellent customer support and fast shipping. These guys are the best for automation equipment!!!” We’ve shopped around to bring you the most practical, reliable industrial control products at the best prices!!
JASON IN DODGE CENTER, MN:
“Automation Direct always has great quality electrical & pneumatic components at a fraction of the cost. Orders are always correct, packaged well and Free 2nd day shipping is an added bonus!”
JOHNNY IN NEW CANEY, TX:
“Excellent company. Use it regularly and highly recommend it to others.”
JASON in RENSSELAER, NY:
“We turned to Automation Direct due to previous suppliers having a “more-than-profound” impact with the 2022 supply chain issues. We’re sure glad we did! Automation Direct offers competitively priced products, many directly swappable with competitor brands, and has a very robust inventory allowing us to see their inventory in real time.”
Hayk in CLAREMONT, CA:
“Competitive prices on most of their selection. Easy to order on the web, no sales rep or middle man needed.”
Amy in MOFFAT, ON:
“Very easy to deal with, technical support is the best in the industry.”
Transitioning from analog to digital automation yields numerous benefits such as enabling personnel to better troubleshoot and address problems in critical moments. It also lets manufacturing execution systems (MES) collect and analyze data to produce detailed diagnostic reports that can pinpoint precisely when, how and why an error or malfunction occurred.
Developing standard procedures for documentation and diagnostic screenings takes time, but the payback is instantaneous.
The IIoT connects subsystems in industrial equipment — such as sensors, programmable logic controllers (PLCs) and human-machine interfaces (HMIs) — to the internet to enable real-time data collection and remote monitoring. This technology can be leveraged to proactively monitor a system’s health and streamline maintenance.
For example, designing a machine with vibration or temperature sensors can alert key operators to discrepancies in critical equipment before failure and help them pinpoint where an issue originated. These features may have once been considered “nice-to-haves,” but they are quickly becoming “must-haves” as plants become more automated.
There are some limitations to integrating IIoT in existing facilities. It’s challenging to install sensors for data collection in plants that do not have existing PLCs or a robust network infrastructure. In these situations, it’s necessary to schedule downtime in order to perform equipment upgrades and installation. Integrating IIoT technology during the design phase of equipment development is the most cost-effective approach overall.
An SI can also help mitigate risk by coordinating and integrating remote monitoring capabilities between individual equipment and their respective original equipment manufacturers (OEMs). Providing OEMs with virtual private network (VPN) access allows them to remotely support the facility. Consider a situation where a piece of equipment goes down in a Florida plant. If the OEM is in California, the integrator would need to travel across the country to troubleshoot and repair. Between making the decision and traveling, a facility could
lose two or three days of production time before resolving the issue. However, downtime is significantly minimized if the same OEM can access the equipment remotely via VPN.
Be mindful that setting up a network infrastructure is a specialized process that involves properly designing the system to minimize cybersecurity risks. The savings are significant and can make the difference between losing thousands of dollars versus millions.
Typically, plant owners and managers hire full-time IT professionals to maintain their servers. When it’s time to upgrade, however, facilities must buy additional servers and train their employees again.
Using a cloud service provider is an easier solution because it helps ensure new and existing servers remain up to date as time passes. These companies maintain and troubleshoot servers through a monthly subscription. Technology evolves quickly and this is a great way to access the latest technology without added work.
While robotics and automation technology are becoming more affordable, it’s still a considerable investment. Racing to become the most technologically-advanced facility in the industry without a plan is never advised.
A good system integrator will identify opportunities to optimize processes throughout a facility first and then develop a long-term strategy. Fiscally, it’s not always realistic to upgrade every component upfront.
Establishing a 3- to 5-year strategy can help stakeholders prioritize how to replace and update critical systems and subsystems and set up a game plan for efficient execution. Having a blueprint for a plant’s long-term automation strategy provides sufficient training and ramp-up time while still delivering ROI. PE
Rao Kolla, PE, PMP, CSCP, MBA, is director of process electrical/controls engineering at Stellar, a design, engineering, construction, refrigeration and mechanical services firm serving commercial, industrial and public sector markets across the United States and around the world. Stellar is a CFE Media and Technology content partner.
‘ A good system integrator will identify opportunities to optimize processes throughout a facility and then develop a longterm strategy. ’
uInvesting in automation and using system integrators (SIs) can help plants identify ways to improve processes and safety at the same time.
uFacility owners should consider the maintenance needs of their technology upfront and invest in preventative solutions to minimize maintenance time.
David Skelton, Phoenix Contact, Harrisburg, Pennsylvania
The path to a digital production facility can be incremental, capturing benefits along the way through the proposed approach of tying lean practices to data collection so users throughout the facility have access to visualization and analytics
Phoenix Contact's facility in Bad Pyrmont, Germany, is an electronics production facility that implemented factory digitalization. This location has been operating as a smart production facility for several years. While digitizing, the plant operators identified and implemented projects that improved efficiency by more than 10% per year. They also found they could go from idea to execution up to five times faster. Wrapping digital production information around existing lean and agile processes helps make this data easily accessible to employees. This creates a feedback loop that can increase production.
Phoenix Contact's U.S. production facility, located near Harrisburg, Pennsylvania, has 70,000 square feet of production space divided into electronic and electromechanical production. U.S. manufacturing operations formally started in 2003, with custom products for the U.S. market. Development capabilities were added incrementally and production grew to include standard catalog products for global distribution.
In 2021, Phoenix Contact started a five-year, $19 million investment program to better serve organic growth in the North American market, reduce supply chain risk and better use the facility's overall assets.
The program consists of nine projects divided into 39 subprojects. Six subprojects are focused on creating a fully digital factory. The effort has been planned as a part of daily work, with existing production staff implementing the activities. The same team is also responsible for deploying the new machines in the expansion projects. This makes prioritization of floor activities critical. While it slows the speed of the journey, it is a practical approach. Short "sprints" on pilots or events allow experimentation, proof of concepts and quick feedback about new activities.
The Bad Pyrmont electronics production facility became a template for potential success. The U.S. facility is different, which meant Bad Pyrmont’s approach couldn’t be copied. In addition to electronic and electromechanical production, Harrisburg has a legacy manufacturing execution system (MES) on many workstations and most automated machinery. The different production areas run almost independently and all information systems and key performance indicator (KPI) reporting were established in the same way. While Bad Pyrmont's approach could be followed, the project team needed to adjust for the equipment and reporting tools already in place.
The digitalization approach consisted of three pillars: Shop floor management, data collection and analytics and visualization.
Shop floor management is the institutionalization of the lean process. The team has been practicing lean techniques for more than a decade.
Phoenix Contact typically held Kaizen events when identifying issues or installing new product lines. The shop floor management program makes these activities daily habits.
This subproject began in mid-2021 when the project team expanded the daily Gemba walks to all production areas and shop floor management meetings using near real-time data from the process (Figure 1). The walks and the meetings focused on addressing issues immediately with the personnel as close to the events as possible. Regular 5S events (sort, straighten, sweep, standardize and sustain) occur, with results being tracked. Process improvement activities run continuously.
Data collection activities began in June 2022. Data is required from three unique categories of equipment: The MES, equipment that is connection-enabled primarily through Open Platform Communications (OPC) or an application programming interface (API) and stand-alone legacy machines and workstations.
The MES was initially deployed for shop floor scheduling in one of the electromechanical production areas. All automated machinery built internally also includes connectivity to the MES. It measures operational equipment effectiveness (OEE) and benchmarks operations with similar machines
globally. These two applications will be merged to expand shop floor scheduling to automated machinery and measurement of the entire process value flow. All data is available only through centralized enterprise applications.
It also is possible to make this data available to visualization tools for KPI reporting and analytical tools selected by the end user. Standardized APIs provide access to user-specific applications and visualization.
Connection-enabled equipment provides access through a standard interface, primarily OPC UA. Most of this equipment is purchased from machine manufacturers that provide connectivity as standard. Examples of this equipment include surfacemount line modules, automatic test equipment and semiautomated packaging. New custom or semicustom locally sourced machines have an opensource controller, which also acts as an message queuing telemetry transport (MQTT) server. This provides the same connectivity as the stand-alone machines and workstations (Figure 2).
Stand-alone machines and workstations make up a large portion of existing assets in production and include manual, semi-automatic and fully automatic machines or work areas. These are controlled by industrial computers or earlier-generation
FIGURE 2: PLCnext Control, Phoenix Contact's opensource controller, collects operational data from the wave soldering machine. Courtesy: Phoenix Contact
‘ Regular 5S events (sort, straighten, sweep, standardize and sustain) occur, with results being tracked. Process improvement activities run continuously.’
• Learn an approach to developing and implementing industrial Internet of Things in a production facility.
• Tie lean practices to actual data collection enhances decision-making.
• Understand the importance and opportunity of ongoing communication for all activities.
programmable logic controllers (PLCs). The machines are part of daily production, so the project team needed a low-risk, noninvasive approach to connect the equipment. The inputs are often parallel wired in the control cabinet, to the sensors with the desired data. These are wired back to an open-source controller, which acts as an MQTT gateway to the production network.
The analytics and visualization were in place at those workstations with automated machinery or MES. Operators use these tools to call up, open, track and close work orders. Machine OEE and statistical process control tools are also accessible. Additional access to the enterprise resource planning, MES and product life cycle management provides production KPI data at the direct production, supervisory and manufacturing engineer levels or at the machine or workstation level. The intent is expanding information access the enterprise.
‘ While there are different ways to collect data, making that data available to all users is important. ’
The method chosen to link all of this together is a microservice architecture. Each data source or the analytical program collecting data resides in containers accessed through APIs. Applications, or individuals with access rights through the API, have near real-time data without other preprocessing or storage. Open-source tools support this effort.
The benefits of this architecture are flexibility, speed and expanded use of the existing workforce. It also does not tie anyone to a single supplier. Applications can be created as required and piloted. If successful, internal specialists then harden and release them to the larger community.
Developers create applications using programming environments they are familiar with. The structure is not supplier-specific, so tools from different suppliers can be used and mixed within the architecture.
The MES is an enterprisewide application; however, through the API, data can be accessed to allow other user-defined applications. For example, the digital twin obtains machine status from the MES to display in a separate visualization tool (Figure 3). This architecture fit into the IT security infrastructure while allowing personnel to work within production network guidelines.
The digital twin was the first step toward this, providing situational awareness. Here is one way to explain it: A user finds something on the operator interface in the same place located on the production floor. If a particular machine is located outside of the production entrance and to the right, the user will find it there on the digital twin graphic. The machine graphic allows access to basic information: whether on or off, the number of units produced or rejected and more. It also includes any current process improvement projects, with status in the process or production area. The KPI board locations in production can be accessed electronically through the digital twin, as well.
Direct and continuous communication has empowered employees to share ideas for process improvement. All employees in the Phoenix Contact U.S. organization are updated on high-level activities at least quarterly. The leadership team is updated monthly and all production and project personnel receive weekly updates.
This communication and engagement allows greater participation. For example, a mechatronics-technician apprentice involved in one of these updates expressed interest in programming some of the apps outside of PLCs. He was paired with a manufacturing engineer with programming experience to deploy the first MQTT gateway on-site.
In another example, a second-shift mechatronics technician made a hack using a QR code taped to a machine to help him remember the frequently used spare part numbers. He shared this with his supervisor, who recognized the benefits and the risks.
They worked with the IT department to build a custom augmented reality (AR) solution.
They built an application to scan the machine using an authorized cellphone or tablet so they could identify and immediately access all machine documentation, including the parts lists (Figure 4). This pilot was successful and is now being scaled throughout the department. Having the data server across the enterprise allows more user access to individuals who are not reliant on others to create reports or access data. This is a soft gain, but it provided real results.
The shop floor management program has provided significant gains. Despite supply chain issues, production output grew by 23% in 2022. The Kaizen events improved efficiency between 7% and 33%. The production floor's new layout has optimized floor space, creating room for the addition of two new product lines. The effort has also resulted in updated value-stream maps, which will help prioritize the data collection activities.
Data collection is moving forward. To date, 30% of all machines and workstations have been conneted. The MES API integration has allowed a pilot project to collect and display machine status through the digital twin. That success qualified the concept and has kicked off a project to automatically display real-time KPIs overall. From there, the project team can drill down to individual machines for daily production management. The company has piloted a new pick-and-place machine with their standard interface and developed a schedule for the remaining equipment. Two stand-alone machines have piloted the MQTT data collection concept and scheduled the remaining workstations.
The digital twin is active and it’s been kept updated with new equipment installations and plant relayout activities. The current digital machine status is available. Several machines' data can be displayed through open-source software. A digitalization steering committee comprising operations and IT personnel has been formed to lead the qualification, deployment and standardization of applications involving analytics and visualization. The first programs involved the expansion of the existing MES applications across all areas of production. This is almost complete.
Two more pilot applications have been rolled out. The first involves labor management and the second involving process quality. Each is in a different production area, but multiple projects can be run simultaneously to help expand knowledge across the site. If successful, both pilots will be deployed throughout the facility.
Two pilots involving AR have been completed and are beginning to scale these to other areas. One is a vendor-specific solution to help onboard new employees. The other is the machine troubleshooting application.
All production facilities and their specific activities are unique, but other organizations can use this approach if they follow a few best practices.
First, the facility needs to define a clear direction or overall purpose of the production digitalization and communicate that to the organization regularly.
Tying lean to the digital effort is important. Actual machine data allows better and faster decision making. Collecting data along a process value stream provides a starting point and immediate feedback following a change. While there are different ways to collect data, making that data available to all users is important.
Run pilots first and don't try to be perfect. If the pilot will get 80% of the initial scope, it’s good enough, which will help prevent companies from getting stuck. Build on those successes and communicate them to the entire organization. PE
David Skelton recently retired as vice president and general manager of Phoenix Contact Development and Manufacturing Inc.
uses an augmented reality application to locate instructions and part lists and to log maintenance activities on an automated machine. Courtesy: Phoenix Contact
uCompanies incorporating digitalization and digital transformation into their facilities can glean more insights and improve efficiency in their production facility.
uUsing a lean approach to this process and using short sprints can help companies make small, but incremental, gains where they are needed and use them as a proof of concept when expanding its scope.
Thomas Burke, CC-Link Partner Association (CLPA), Vernon Hills, Illinois
Fundamentally, Ethernet is a nondeterministic technology, letting devices on the network take turns in sending messages. Devices listen for a quiet moment at which to transmit a message. If two devices transmit at the same time, they recognize a collision and back off for varying periods to avoid another collision. Ethernet has been applied to applications requiring communication determinism, but it is up to the devices on the network to work in unison toward the outcome, not something that is possible in an “open” network.
• Understand how determinism and convergence in timesensitive networking (TSN) enhances network communication.
• Learn how TSN can provide a competitive advantage in industrial manufacturing.
• Learn what capabilities TSN provides to machine builders.
In 2018 that changed with the addition of time-sensitive networking (TSN) specification additions. TSN delivers functionality for device clock synchronization, traffic prioritization and traffic shaping. These features enable devices to coordinate their communication schedules, preempt traffic as necessary and break up large transmissions to intersperse higher priority messages. This combination enables Ethernet to be applied to one of the most demanding areas of communication.
Ethernet’s benefits include low-cost cabling, ease of use and flexible architectures. With all devices on one network, the real benefit is data access. Adding TSN delivers a whole new dimension.
TSN’s main benefits are determinism and convergence.
Determinism is fundamental to supporting time-critical communications on the factory floor, as it ensures the predictable delivery of data by minimizing latency and jitter. This requires that the Ethernet specification is enhanced in three areas:
• Delivering an accurate time synchronization to all devices on the network can communicate intelligently and in a coordinated fashion.
• That traffic can be shaped — large transmissions can be broken into many smaller transmissions to enable preemption by higher priority traffic.
• The ability to define prioritization to communications between devices. This supports realtime applications and provides the foundation for convergence.
Convergence, the second key benefit of TSN, enables companies to merge different traffic types onto a single network without affecting the performance of shop floor communications. This is fundamental to sharing operational insights and hence increasing process transparency across an enterprise, which can then be used to derive insights to optimize manufacturing facilities and entire organizations.
Because TSN is an extension of Ethernet, it also is interoperable with existing network technologies and devices. Hence it can be used alongside existing devices, reducing system investments. Converged networks provide users with four benefits:
• Control devices that have previously been isolated to separated control networks –required to ensure deterministic performance, can now be addressable and accessible to other applications for use in advanced analytics and digital twins,
• Devices are becoming smarter and more complex and require management that can now be accomplished over one connection,
1: Time-sensitive networking (TSN) allows multiple networks to exist on a single wire. Courtesy: CC-Link Partner Association (CLPA)
• Architectures are simplified through the use of one network, improving deployment and troubleshooting and
• Costs are reduced, through the simplification of architectures.
Leveraging TSN enables the development and use of smarter machines and has many benefits for users. Three, in particular, stand out:
1. Provide external access to all machine variables: In the past, this has been one of the greatest challenges, primarily because communications within a machine fall into various categories and have differing requirements. There is typically a control network and a supervisory network. There can be a bridge to an external network. Some communications require deterministic performance for processes such as motion control or high reliability for safety. Other communications are less demanding and are for informational purposes. The gateway for these communications often becomes the controller. There should be a common backbone for all machine communications. With new products on the market that support TSN, machine builders can now deliver machines with a common Ethernet TSN backbone, enabling direct data access with the entire machine, from controller to sensors and actuators.
2. Instrumenting a machine with additional sensors to enable greater context: Greater access to machine data means the opportunity to better understand the machine operation, provided there is enough context to enable an understanding of the data.
For example, a piece of equipment may be running hotter than usual because it is running harder, under greater load or because the ambient temperature is higher that day. Startup performance will vary based on a cold or warm start. If a machine
‘ Leveraging time-sensitive networking enables the development and use of smarter machines and has many benefits for users. Three, in particular, stand out. ’
isn’t properly instrumented for context, making sense of data will be more challenging. This also requires a loosening of alarm levels, which is the early warning system to machine failures. A common backbone enables the introduction of more sensors. These sensors might be unrelated to the machine’s operation, but they are critical to understanding the context of a machine’s operation.
‘ By selecting state-of-the-art
with TSN capabilities, machine designers can increase their market coverage and gain a competitive advantage. ’
3. Adding capabilities that can deliver a competitive advantage. As a machine user, competitive advantage is making the product as efficiently and of the highest quality as possible. A smarter machine will certainly help. As a machine builder, what is the competitive advantage? In an Industry 4.0 world, competitive advantage may well be in the machine analytics the user can provide.
Users should also ask many questions for better insights such as:
• Is maintenance is being scheduled based on operations or a scheduled timespan?
• Are you able to view similar machines and identify which will provide the best rate of return and schedule appropriately?
Time-sensitive networking (TSN) insights
uEthernet has continued to improve and broaden its reach and has been expanding into industrial automation applications.
uTime-sensitive networking (TSN) delivers functionality for device clock synchronization, traffic prioritization and traffic shaping and can help manufacturers improve communication and scheduling.
uTSN is part of a larger initiative by manufacturers looking to improve their supply chain and maintenance schedules and reduce potential logjams.
• Are you able to connect remotely and have access to enough data and context, to properly troubleshoot a machine and eliminate the need for travel and coordinated visits?
• Can you add sensors to unlock a greater understanding to the operation of your machine, when needed?
• Are you delivering digital twin analytics, modeling machine operations and dynamically adjusting alarm levels based on the current context of operation?
Industry 4.0 technologies are unleashing waves of innovation that will increase performance, improve quality and reduce costs. With new technology such as Ethernet TSN, machines will shift from their original designed for purpose delivery to those that can offer quantified performance, quality and cost metrics. This will improve over time,
based on original equipment manufacturer (OEM) analytics and feedback.
TSN is recognized across different sectors as the future of industrial Ethernet and industrial communications. Technology companies have delivered silicon and firmware to enable the development of new TSN-based devices and infrastructure components. Leading automation suppliers have already adopted those new components into their automation equipment offerings, including PLCs, input/ output and motion controls.
Proof of concepts have been on display for several years now at trade shows around the world, demonstrating new levels of motion control determinism that leads to higher quality products. Users can now combine video and deterministic control communications on the same wire.
This technology trend offers potential opportunities for machine designers and builders. By selecting state-of-the-art products with TSN capabilities, machine designers can increase their market coverage and gain a competitive advantage.
To tap into this market, machine designers are selecting products from leading suppliers to produce TSN-based solutions. Thanks to software and straightforward hardware modifications, it is often possible to update existing industrial controls to support next-level capabilities.
To enable future-proof industrial communications and next-level performance, machine designers and builders should think outside the box and embrace this new technology, ahead of their competition, to achieve a clear and measurable competitive edge. They need to act now to deliver TSN-compatible products or upgrade existing machines with TSN capabilities. By doing so, they can help their customers to create factories of the future while enhancing their own competitiveness in a fast-growing market. PE
Thomas Burke is global strategic adviser for CC-Link Partner Association (CLPA). He is the founder of the OPC Foundation and spent much of his career developing software, hardware and firmware for industrial automation, including at Rockwell Automation. CCLink Partner Association (CLPA) is a CFE Media and Technology content partner.
Michael Wrinch, Ph.D., Hedgehog Technologies, Burnaby, British Columbia
There are several important considerations when selecting flyback diodes that can make the difference in reliable design and extending the life span of the system
• Understanding flyback diodes and why it is important to choose the right product.
• Learn the calculations to determine reverse voltage, current and energy.
• Review the alternative options for the basic rectifier diode.
lyback diodes are a simple, essential protective component that impacts the overall life of a semiconductor and other mechanical switches. They are commonly found in the terminals of 24 volts direct current (Vdc) industrial contactors or relays.
Sometimes the supplier will have a suggested product, but this is not always true. Some exceptions include legacy products or applications in unique locations. A situation may occur where users need to select the right diode for an application. When this is the case, three major considerations need to be front of mind.
1. Overvoltage protection
A flyback diode protects the circuit from overvoltage if the contactor is switched off from a controller. Without it, the magnetic field around the inductor collapses and produces harmful voltage levels. Aside from damage, higher voltage generates noise that confuses the controllers, which can trigger false trips.
The basic configuration of a flyback diode for industrial applica-
tions is to use a classic rectifier in reverse polarity across each contactor terminal.
2. Four flyback diode considerations
Flyback diodes relieve the magnetic circuit of its energy in a reverse flow system. When inserted into a circuit, the diode creates a reverse current path to flow through it .
While the application is simple, there are four parameters to consider when choosing a diode that helps mitigate damage to the diode, controller and contactor:
• Selecting a proper reverse voltage (V) that is suitable for the application.
• Selecting a current (I) that can support the application.
• Selecting a repetitive energy (J) dissipation for the application.
• Ensuring that the diode is as close to the target as possible.
Several factors must be considered before committing to the purchase of a diode. These include reverse voltage rating, current and energy, which will prevent long-term damage to the contactor.
3. Reverse voltage rating
When determining reverse polarity rating for a 24 V system, it should be 10 times the nominal voltage of the system when selecting a diode, though it is advisable to go higher if possible. Reverse polarity voltage adds stress to the diodes reducing its reliability and lifetime.
Reducing the voltage stress ratio is critical to the health of the system. The ratio is applied voltage versus rated voltage. Selecting 10 times the nomi-
nal voltage is useful because the system voltage can spike from external influences such as noise, reflections and other circuit interferences.
Consider a 120/208 volts alternating current (Vac) circuit that operates at higher voltage levels. The nearby 24 Vdc-powered line becomes corrupted by the radiated noise from the higher voltage circuit causing damage to the diodes.
Choosing the right current setting is just as important as selecting the voltage rating. Overvoltage can destroy the internal P-N junction in the diode while overcurrent can result in the diode overheating.
STEP 1: Determine the average current rating and multiply by 10
The average current listed by the contactor manufacturer is a reliable source for choosing a rectifier diode. When a listing is not available, the safest parameter is to use the coil resistance and apply Ohm’s law (V=IR) or power ratings and use the power equation (P=IV) to determine the average current. Then multiply the result by 10.
If the solenoid nominal current’s consumption rate is known, a flyback diode is only required to carry 10 times the nominal solenoid for a limited time during the turn-off period. The reason for this is that the flyback diode current decays similar to the RL circuit current. Diodes also have a shortterm surge current that is much greater than the average current, which offers additional protection.
A powerful analysis tool is using the approximate rectifier diode repetitive I^2 t values. It can be used with either repetitive switching or a flyback diode without a sufficient average current rating.
The diode datasheets provide an approximate number of equivalent amplitude half-cycle current pulses (N) versus peak current in chart form. The half-cycle pulses are based on a 60 Hz wave and last about 10 milliseconds (ms).
If the system is constantly switching, this may help to understand what the peak current should be adjusted to. Apply the I^2 t using the value “t” as 10 ms and “I” as the peak current. Ensure this number is well below the max A^2s value.
‘ A situation may occur where users need to select the right diode for an application. When this is the case, three major considerations need to be front of mind. ’
Flyback voltage can reach levels of up to 10 times in a high impedance circuit. To minimize the potential for a voltage spike, place the diode in the terminals of the contactor. There are suppliers that offer adaptors for adding flyback diodes that can be clipped to relay or contactor terminals. While users might want to place flyback diodes in a control panel when a terminal block is easily accessible, this should only be done if the contactor is located inside the same panel.
There are several options that can be considered as alternatives to a basic rectifier diode and each are useful in specific applications.
• Metal oxide varistors are used in ac circuits operating as logarithmic functioning devices. They are useful in protecting them from severe spikes that occur in events such as lightning strikes.
• Transient-voltage-suppression diodes are fastacting diodes that can be bi-directional or monodirectional to protect electronics from transient spikes. While they can be used in flyback applications, they cost more than a basic rectifier diode and may not be required in a typical contactor situation.
u
u A flyback diode protects the circuit from overvoltage if the contactor is switched off from a controller and can damage semiconductors and other mechanical devices in the process. uPicking the right flyback diode will extend the life span of the system and improve its overall reliability.
• Zener diodes are reverse triggered for a set voltage. Though they are not intended for surge protection, they can work if a suitable part is selected.
• Schottky diodes carry a low forward voltage drop thus increasing the opening time of the contactor. This diode is not recommended as the reverse voltage tolerance is lower than typical rectifier diodes.
Flyback and current suppression with contactors are essential components to most industrial designs. Making the right decision when selecting a circuit will extend the life span of the system and improve its overall reliability.
Consider alternate designs such if the application requires it. If the system is sensitive and demands high reliability, take a moment to test performance with each option and compare the voltage, current and energy using a datasheet. PE
Michael Wrinch, Ph.D., is the founder and president of Hedgehog Technologies. Hedgehog Technologies is a CFE Media and Technology content partner.
Tank linings are crucial to ensure the safety and quality of food and beverage products during storage and transport. These coatings provide a protective barrier that shields tank interiors from the corrosive effects of the products they contain and prevents any unwanted contamination from affecting the stored goods. Proper linings are also critical for meeting regulatory compliance and chemical resistance requirements.
In the food and beverage industry, hygiene, safety and quality assurance are essential to success. Therefore, lining materials must be non-toxic, non-reactive and resistant to bacterial growth, so products remain safe and consumable.
Choosing the right tank lining material is crucial in any setting, as it helps safeguard products, protect consumers and ensure that applicable regulations are being met. This white paper discusses the importance of choosing an optimal tank lining material among new innovative technologies – including high-performance corrosion-resistant materials, antimicrobial options and self-healing linings – that deliver unprecedented levels of quality and durability.
Download the paper HERE swprotective@sherwin.com SCAN CODE AT RIGHT FOR SMARTPHONE ACCESS
We
When
Jeffrey R. Jowett, Megger, Valley Forge, Pennsylvania
What if there was a way to protect facility assets and ensure little to no downtime of plant machinery?
No matter the industry, when it comes to equipment and machinery, the goal is to keep it up and running with little to no downtime. When equipment fails, so does your production and ultimately your bottom line. Preventive maintenance, while good, isn’t always good enough.
• Explore what conditionbased maintenance is and how it works with your equipment maintenance strategy.
• Gain a broader understanding of the different ways data is collected through a condition-based maintenance program depending on what type of machinery you are monitoring.
• Learn how condition-based maintenance not only decreases downtime, but also saves your facility time and money.
FIGURE 1: Performing a predictive/preventive insulation test on a transformer. Courtesy: Megger
Maintenance needs are predicted in advance and maximum downtime of equipment can be reduced, but oftentimes equipment that is on a scheduled maintenance routine is getting “maintained” when
it doesn’t need to be. This is a waste of company time and resources. In truth, preventive maintenance has companies overspending on maintenance when they don’t need to.
What if there was a way to protect assets and ensure little to no downtime with another maintenance strategy? What if time and money wasn’t being wasted? This is an opportunity for conditionbased maintenance (CBM).
What is condition-based maintenance?
CBM is a maintenance strategy that monitors the real-time condition of an asset to determine what maintenance needs to be performed. Unlike preventive maintenance, which is based on some sort of schedule, CBM dictates that maintenance only be performed when real-time indicators set up on the asset being monitored show irregularities or signs of decreasing performance. Its goal is to continuously monitor equipment to spot impending failure. By doing this, maintenance teams are given enough time to react before failure occurs.
Because CBM is done by taking real-time measurements, maintenance is only done as needed while machinery is running. Because of this, there are fewer unplanned downtime events, which is extremely beneficial for production efficiency and resources.
Data can be collected in several different ways through a CBM program depending on what type of machinery being monitored. Some include vibration analysis, infrared thermography, ultrasonic analysis, oil analysis, electrical analysis and pressure analysis. By collecting information this way, it is remarkably precise, indicating not just that the machine is failing, but also exactly what is wrong
with the asset by identifying the root cause. Electrical analysis is key in condition-based maintenance.
Electrical analysis is extremely important when it comes to large industrial machinery, like those found in petrochemical, mining and pulp and paper. Interruptions in production or reduction in output are extremely costly — for example, losing barrels of oil or tons of minerals in the petrochemical industry. CBM isn’t just to head off breakdown in machinery at the pass. It is also used to slow down loss of capacity.
By constantly monitoring the electrical condition of critical equipment, engineers and plant managers can hold production losses to a minimum or even to zero. In addition, conditions that could lead to catastrophic failure later can be spotted early and corrected with minimal or no loss of production.
An example would be if an unrecognized moisture source in a nearby industrial process causes a motor to fail. If a CBM program is in place, someone could recognize that insulation values were dropping at a rate beyond normal wear. This would allow them the time to look for the source of the problem and remedy it before it is too late.
‘ What if there was a way to protect assets and ensure little to no downtime with another maintenance strategy? ’
Monitoring for insulation resistance is paramount in CBM and is very easy to test. It monitors the condition of equipment in that it can alert the tester to water ingress, contamination and physical breakdown from things like vibration and electrical disturbances, as well as general long-term wear. With a good quality tester, test results are easy to interpret because the range of measurement is vast — from Tera-Ohms continuously down to Megaohms. The person reading the measurement has a window that can be easily checked at any time and provide a look at where the equipment is on its life cycle. This allows for an early warning of anything happening beyond normal wear — like excess moisture ingress.
Condition-based maintenance insights uCondition-based maintenance lowers maintenance costs and decreases downtime of a manufacturing plant.
uSelecting the correct equipment can ease the challenges of condition-based maintenance.
Ground testing is easily overlooked by many because the grounding system seems to be a passive part of the electrical plant, unlike motors and lights. However, a corroding or eroding ground can affect everyday operation in a plant. Failure to ground can cause noise interference and lightning strikes. So, ground testing needs to be a part of a condition-based maintenance plan.
For ground testing a four-terminal tester is needed because there is a good chance a resistivity test may be necessary at some point in order to install another ground or to improve what is already in place. Generally speaking, a clamp-on tester for continuous testing is not the best option; however, it may be useful to have on hand to use for a quick backup test.
Courtesy: Megger
A quick and easy way to regularly check for different kinds of problems on an electrical system is
equipment provides an early warning of future breakdown. Courtesy: Megger
using a thermal camera. They are particularly good for production lines because the operator can find hot spots where some flaw or problem is interfering with current flow. Once found and isolated, the issue can be readily corrected before it interferes with production or ignites a fire.
The performance of a transformer is rated by and critically dependent on the ratio of turns in the primary and secondary. Electrical stresses cause insulation breakdown, possibly no more than a tiny pinhole, where current can short across from one turn to an adjacent turn. This effectively reduces two turns to one and the cumulative effect can significantly change the transformer’s rating.
Industry standard is tight; no more than 0.1% change from rated is allowed before the transformer should be serviced. In this same area are winding resistance testers. These are applied to both transformers and motors. Winding resistance
changes along with turns ratio. An ordinary ohmmeter is not useful because it lacks the power to readily overcome the capacitance and inductance of large windings. A dedicated winding resistance tester is required to produce the power necessary to test quickly and efficiently.
Partial discharge is also a concern, especially in transformers. Deterioration of bushings and other components can cause electrical leakage to the atmosphere. Partial discharge testers are specifically designed to meet this challenge, identify and localize partial discharge. These can be used in CBM.
CBM is well worth the time, effort and money spent in implementing it. It helps to improve system reliability as well as increases productivity. CBM lowers maintenance costs and decreases downtime of a plant. It is a much quicker and more efficient way to diagnose problems within a system. PE
Jeffrey R. Jowett is a senior application engineer at Megger with more than 40 years of experience in electrical testing and measuring instruments.
VelocityEHS
The use of temporary workers and contractors is on the rise and this trend shows no signs of slowing. Yet, many employers are still relying on paper-based systems and basic spreadsheets to manage Control of Work functions like contractor prequalification, onboarding, permit-to-work processes, site access, and performance tracking. These outdated systems introduce unnecessary administrative burdens, bottlenecks that hold up productivity, and unacceptable safety risks to workers.
Download this complimentary eBook that breaks down the core elements of an effective Control of Work system— what it is, why you need it, and how it keeps people safe and processes running smoothly.
Register to download the paper here.
• www.ehs.com Contact VelocityEHS
experts in bulk solids handling get stuck sometimes.
Not sure how to handle products that leave behind unwanted residue? Moving friable materials where you are concerned about breakage? Unlike those materials, we don’t crumble under pressure. We’ve got over 50 years of industry expertise in building processes that are efficient and effective. Our team of engineers is here to handle your complex challenges so you can focus on what you do best — designing systems that work.
WORKFORCE DEVELOPMENT
Shane Persad, Machfu, Germantown, Maryland
The oil and gas industry is facing a skills gap and companies are integrating industrial Internet of Things cloud-based automation to mitigate this problem
According to the report, Science & Engineering Indicators 2018, prepared by the National Science Foundation, “The demographic composition of the science and engineering workforce in the United States is changing. The baby boom portion of the S&E workforce continues to age into retirement. Mirroring U.S. population trends, the science and engineering labor force (worldwide) is aging.”
• The industrial Internet of Things (IIoT) is creating new methodologies to collect, process and push data from the network edge to back-end servers using cloud-based systems.
• Data from multiple devices can be correlated using real-time cloud processing and analytics to create prescriptive and actionable outcomes on the well pad, while extending traditional supervisory control and data acquisition systems with actionable intelligence and adaptive analytics.
The oil and gas industry is at risk due to its dependence on oil price fluctuations. In the 1970s, thousands of baby boomers studied petroleum engineering and other energy professions when oil prices were high. However, layoffs in the 1990s discouraged an entire generation from joining the industry.
This great crew change is a phenomenon where high retirement rates and a widening employee demographic gap have created a significant skill shortage in the oil and gas industry. The pool of open skilled jobs in oil and gas is growing as employers are finding these positions more difficult to fill with younger qualified candidates.
Retiring engineers, technicians and workers take decades of experience and expertise and knowledge of oil and gas process operations with them. Much of this equipment was installed at the oil field and in processing facilities 40 to 50 years earlier.
Maintaining robust and effective maintenance and upgrade of this equipment and securing its reliability is crucial as the equipment continues to age.
Oil and gas companies are implementing new ways to recruit and train young engineers, technicians and field workers in the skills needed to bridge the gap. This is a vital and proactive step forward, but it is not enough.
Oil and gas companies are starting to turn to automation to alleviate the skills gap problem by using industrial Internet of Things (IIoT) cloudbased automation. Wireless data collection sensors on edge processes are used to maintain, upgrade and extend longevity of their key assets in the oil field and in downstream processing facilities.
Employing specialized gateways capable of connecting data from edge assets to the cloud, they are interacting in real time to new machine learning and application services interface applications, without interrupting existing supervisory control and data acquisition (SCADA) functionality.
A broad base of recorded engineering and maintenance knowledge on these systems and processes is recorded and available for immediate condition and predictive analysis.
Contrast this with the data collected from manual condition monitoring and noncloud-based automation techniques, which is often undertaken by oil and gas maintenance and engineering personnel, where not all equipment is accessible, sometimes due to hazardous locations. An oil and gas producer also may have many wells being maintained by a small number of instumentation engineers and workers in the field.
While existing noncloud-based automation may provide some insight into issues, it is often reactive, informing operators of what went wrong after the problem has escalated to critical failure. Operators often do not have the time to inspect and study the data from wells that appear to be operating properly to discover what may go wrong. The instincts of a career oil worker is often used to identify or determine what action should be taken. As the crew change evolves, much of this experiential practical knowledge that took years to acquire will disappear, making manual and noncloud-based automation increasingly less effective.
Subsequent data analysis for system faults is only be as good as the consistency of collection protocols and continuity over time of the data collection. Infrequent condition monitoring, as well as personnel transfers or leaves, interrupt this continuity.
In view of these circumstances, cloud-based, real-time monitoring is not only an ideal and proven method of capturing data from these assets, but it also has the tangible effect of reducing oil and gas companies’ reliance on the transfer of knowledge from an experienced to a novice workforce to help compensate and minimize the workforce skills gap.
The IIoT is creating new methodologies to collect, process and push data from the network edge to back-end servers using cloud-based systems. One system that simplifies the complex landscape of the IIoT and connects valuable assets to new cloud solutions is an IIoT platform, which can provide tools that can bridge traditional 1980s control technologies to real-time IIoT edge appliances.
An IIoT platform provides actionable operational intelligence that improves decision intelligence, provides risk assessment and generates prescriptive outcomes leveraging IIoT and artificial intelligence technologies to optimize operations across the well pad.
FIGURE 1: The latest IIoT gateways provide secure connectivity to industrial controllers, process automation and smart grid assets in the field using legacy and modern protocols without disrupting existing legacy SCADA platforms.
Courtesy: Machfu
The platform scales to support private or public cloud-based visualization platforms and does not interfere with existing SCADA operations. The open, standard-based platform enables vendor agnostic data models, controls and management.
The IIoT platform uses a gateway, which provides a rich set of edge functionality, collecting data by polling critical infrastructure and industrial application sensors at the edge, assessing the system state every second.
‘ The IIoT is creating new methodologies to collect, process and push data from the network edge to back-end servers using cloud-based systems.’
The platform is designed to run secure, device-specific applications at the edge, similar to a smartphone enabling data from existing legacy devices, to support edge processing and analytics. Data from multiple devices can be correlated using real-time cloud processing and analytics to create prescriptive and actionable outcomes on the well pad.
The gateway provides secure connectivity to industrial controllers, process automation and smart grid assets in the field using legacy and modern protocols without disrupting existing legacy SCADA platforms.
An IIoT gateway provides many features designed to simplify the development of edge applications by reducing the time to create and integrate them. This enables innovative edge applications to be created and integrated to existing infrastructure and IIoT applications.
Continued on page 38
FIGURE 2: Mach-IO provides standards-based wireless data collection for IIoT sensors in the oil field, working with the MACHGateway. Together, they simplify connecting and managing sensors and controllers and provide a secure connection to transmit data real-time to oil and gas companies.
Courtesy: Machfu
Continued from page 35
Oil and gas insights
uThe oil and gas industry and particularly oil field operations, is facing an imminent shortage of talented and trained workers, putting production performance and equipment reliability at risk.
uTo mitigate the impact of this problem, a growing number of oil field sites are integrating IIoT cloudbased automation, using wireless data collection from edge assets and employing intelligent gateways capable of connecting data from edge assets to the cloud.
Wireless connectivity provides data collection for IIoT sensors in the oil field, working with the gateway. These help simplify connecting and managing sensors and controllers and provide a secure connection to transmit data real-time to oil and gas companies.
An IIoT cloud platform exchanges data from the edge gateway and input/output devices. It provides cloud computing capability across a set of correlated assets analyzing process flow to assess risk and provide prescriptive outcomes to issues.
The IIoT cloud platform is designed to process real-time insights and extends SCADA with actionable intelligence and adaptive analytics. It leverages low-code solution templates and lets users rapidly build digital apps and automate critical workflows. The platform creates action from data and extends analytics with personalized workflows, automated rules and alerts that solve unique business challenges. It also integrates with existing IT systems, cloud platforms and external systems from ecosystem partners.
The IIoT cloud platform uses IIoT-based automation, consisting of its edge gateway and standards-based wireless I/O connectivity, to instrument and model the entire process flow. Its
cloud-based backend provides real-time processing to correlate the sensor data and create meaningful time-series data of the entire well process, including artificial lift, test separator, well-pad separator, tank storage, gas flow measurement, water disposal and custody transfer of the oil from the pad.
The time-series data can be monitored using a risk model, with actionable intelligence and adaptive analytics that include economic impact across the fleet wells. The end result is a risk-weighted list of potential problems and prescriptive measures that may remedy them.
Industries engaged in oil and gas production are losing know-how and experience through the loss of seasoned engineering and other technical personnel. Poor systems in place for the acquisition of asset data and performance such as manual and noncloud-based data collection result in inadequate knowledge and learning to facilitate cost-efficient oil field performance.
Within the IIoT cloud-based, real-time data collection framework, well site process information can be collected to a big-data cloud database, which is designed to provide information for different applications that are requiring data. This means a much higher volume of data can be gathered from the well pad metrics and made available in a common format, to allow for broader usage and analytics.
An IIoT cloud platform can provide a sustainable resolution to the oil and gas industry’s skills gap. PE
Shane Persad is vice president of business development at Machfu.
Waupaca Foundry, a Hitachi Metals company, casts automotive, semi-truck, home-heating and agricultural parts of gray iron, ductile iron, austempered ductile iron and compacted-graphite iron in seven plants.
At plants two and three, a shared cupola furnace melts 120 tons of iron per hour. To maintain that pace, several pneumatic conveying systems are routed throughout the 665,850-sqare-foot facility.
“We use pneumatic conveying systems to move metallic additives into ladles, and transport sand and sand additives to our core rooms,” said Mike Hemmila, plant manager. “We also use pneumatic conveying to transport metallic waste and waste sand back into the silos, and we use it in our dust collection systems.” The pipelines are 2 or 4 inches in diameter and 30 to 300 feet long.
With a near-constant stream of abrasives moving through the lines at high speed, wear is a major design and maintenance consideration. Line integrity is especially critical at the bends, where a change in direction can cause the material to impact and wear-through elbow walls resulting in blowouts.
To extend the service life of the pipeline bends and minimize downtime, Waupaca deployed deflection elbows from HammerTek Corp. The company’s smart elbow design features a spherical vortex chamber protruding from the elbow. When material passes into the elbow, part of the flow is automatically diverted into the vortex chamber, where it forms a loosely packed mass that slowly
rotates in the direction of flow. This gently deflects incoming particles around the bend.
“We’ve found applications where the HammerTek elbow works really well and is the better solution (over other types of short-radius bends and 90-degree sweeps),” said Hemmila. “For the system I designed for moving waste sand, I put in the HammerTek deflection elbows because they worked really well with that particular material.”
Hemmila also noted that this system has provided reliable service since 2004.
The smart elbows also are suited to applications at Waupaca in which materials are diverted downward into silos and bins. “Dead-end stops are a good application for them as the material absorbs the impact as direction changes,” he said.
Dale Harris, maintenance foreman at Plant 2/3, said, “We have some HammerTek 45-degree elbows that can last two years.”
Replacing a smart elbow bend is simple, Harris said, being a matter of changing eight bolts, with most jobs taking several minutes. If the leak occurs in a very high area or is otherwise difficult to access, it might take an hour to replace because of the time needed to round up a lift, hoist and other equipment.
Whatever the application, the goal is to minimize downtime, and Hemmila said his company will always opt for the bend that lasts the longest. “If we can find something that is going to last longer and save us the trouble of changing it out, we will choose that product without even thinking about it.” PE
Charles Williston is the national sales manager at HammerTek Corp.
FIGURES 1 AND 2: Waupaca Foundry deploys Smart Elbow deflection elbows to avoid leaks, blowouts and downtime from wear by abrasive materials speeding through the pneumatic lines. Courtesy: Waupaca Foundry
• Learn how line integrity in facilities is critical and how deflection elbows can help maintain operational efficiency.
• See how Waupaca Foundry used deflection elbows and the process involved.
John Malinowski, IEEE Fellow, NEMA MG1 Past Chairman; and Tim Albers, IEEE Senior Member, NEMA MG1 Technical Committee Chairman
Advantages of using adjustable speed drives vary, and different applications may require different options
What are the advantages of using adjustable speed drives? The combination of a motor and adjustable speed drive (ASD) is called a power drive system (PDS). Specifying adjustable speed drives can help a manufacturing process become more energy efficient and productive. On variable torque applications (pumps and fans), one can expect energy savings of 20% to 40% with a PDS when compared to an application using a valve or damper for flow control.
PE: Name two factors that are important to optimize peak efficiency on a motor with a variable frequency drive (VFD).
Tim Albers: Two factors:
• Finding the best efficiency point (BEP) of the pump or fan.
• Providing system feedback (temperature, pressure, flow, level) to the VFD to maintain.
PE: Is a microdrive and three-phase motor the same as an electronically commutated motor (ECM)?
John Malinowski: A Microdrive is usually a pulse width modulation inverter paired with a three-phase induction motor where an ECM is a synchronous motor.
u
VFD insights
uThis Q&A helps readers learn the energy savings and process control available with adjustable speed drives
uAfter watching the webcast and reviewing these questions, readers will learn when to specify inverter ready or inverter duty motors.
u It is important to understand what advantages a synchronous motor provides over an induction motor.
During this live webcast entitled “Motors and drives: Advantages of using adjustable speed drives” on Feb. 16, 2023, several questions were left unanswered. The presenters take on several audience questions here.
Presenters:
• John Malinowski, IEEE Fellow, NEMA MG1 Past Chairman, JMAL Consulting, Fort Smith, Arkansas
• Tim Albers, IEEE Senior Member, NEMA MG1 Technical Committee Chairman, Chair of the Associate Member Council, Hydraulic Institute, St. Louis
Plant Engineering: What hp range of synchronous motors are available in the North American market?
John Malinowski: 0.5 – 500+
PE: Does VFD come with integral or external fused disconnect for short circuit/fault current protection? Is it required by code?
Tim Albers: Most locations code will require a fused disconnect for a VFD. Some VFDs (smaller and then very large panel built) do have an internalw fused disconnect, most do not.
PE: Is there any established practice of running the VFD at a frequency higher than 60 Hz to gain some additional process control and/or more horsepower out of a motor?
Tim Albers: I would say that there is not an established practice. It is pretty common to run a motor over base speed to increase output and increase the available horsepower. The tricky or most important item is that to increase the hp above 60 hz, the voltage must be set up to peak at the high-
Power drive systems (PDS), electronically commutated motors (ECM), adjustable speed drives (ASD) and variable frequency drives (VFD) were all highlighted in this webcast. Courtesy: Plant Engineering
er frequency and not at 60 hz. So, if, for example, a pump is going to be run at 75 hz instead of at 60, then the 460 volts would have to occur at 75 hz. So, the voltage at 60 hz is going to be the ratio below 75 hz. The 60 hz volts will be 368 and the 75 hz volts is then 460. The motor must be designed for this or it will not work. If a motor is a 230/460volt motor, then (for example) a 4-pole motor could be connected at 230 volt and then run up to 120 hz at 460 volts. The motor then would be a 3,600-rpm motor that would double in horsepower.
PE: What is a “KPI”?
PE: What are the largest variable speed drive? I have a scope in an RFP that indicates it includes a 20,000 hp synchronous compressor drive motor with variable speed control.
John Malinowski: Medium voltage drives are available to 100 MW from several manufacturers. Larger sizes may be available on a custom basis.
PE: Could manufacturer supply harmonics spectrum, as many applications request harmonics mitigation?
—John Malinowski, IEEE Fellow, NEMA MG1 Past Chairman, JMAL Consulting, Fort Smith, Arkansas
Tim Albers: Key performance indicator (what do you want to measure?).
PE: What about soft start?
John Malinowski: A soft start is a type of control that ramps up the voltage to a motor when starting to reduce the inrush current and starting torque. On many applications it is bypassed once the motor reaches speed so there are no additional losses.
PE: How does the cost of cooling, HVAC equipment, maintenance and power consumption of cooling equipment play into this?
Tim Albers: In many cases, no extra cooling is required. A VFD will have about 3% total losses, so that heat does need to be taken into account, but the VFD does not have to be in a cool location. Most VFDs are rated for 40C so they can be in nonconditioned air. If they are placed in the conditioned air, then those 3% of losses in watts must be taken into account
PE: How is energy efficiency related to motor size?
John Malinowski: Lower horsepower NEMA Premium motors have nominal efficiencies starting around 82% and the larger ones are 96.2%.
Tim Albers: This is difficult as many items come into play on harmonics. How large is the power supply system? What is the cabling like? Are there any magnetics added such as a line reactor? For the cost of evaluating the harmonics, in most cases, a line reactor will fix most issues and not cost that much. I strongly recommend talking to a VFD rep, distributor or manufacturer about your specifics.
PE: Grounding rings need to be installed to protect bearing?
John Malinowski: Shaft grounding systems are helpful in installations where there is poor grounding or where common mode voltage is present.
PE: What are some considerations that need to be incorporated in an electrical power design if the distance from the VFD to the motor exceeds 100 feet or more?
John Malinowski: Where long cable runs are present between the drive and motor, line reactors are often used in the system. Check with the drive manufacturer for recommendations.
PE: How come a system, such as a fan, cannot have both damper and VFD? The damper changes the
—Tim Albers, IEEE Senior Member, NEMA MG1 Technical Committee Chairman, Chair of the Associate Member Council, Hydraulic Institute, St. Louis
‘Shaft grounding systems are helpful in installations where there is poor grounding or where common mode voltage is present.
—John Malinowski
duct system curve, while the VFD varies the fan curve, until they both meet at a “mutual” operating point? What is wrong with that to make a system work?
Tim Albers: You absolutely can do this, but the VFD on its own can do 99% of the work and save a significant amount of energy. Having both in the system will require a fairly complex control system to make sure they two work together to save the most energy. Again, it is possible but a VFD alone is much easier to program and control.
PE: Ground currents through the bearings?
John Malinowski: Shaft grounding systems are helpful in installations where there is poor grounding or where common mode voltage is present.
PE: In my experience, a drive working under a 60% to 50% nominal horsepower, efficiency and harmonics become much worse than nominal values? Could such values could be supplied by manufacturers?
Tim Albers: Harmonics are really an individual installation discussion. I agree that lightly loaded systems, without any mitigation, can have harmonic issues. I think this should be a discussion with the suppliers of the VFD. The installation is a part of this so the VFD alone will not have a harmonic that you can just apply.
PE: Are there guidelines/estimates for the increase in motor losses for large low-voltage motors (i.e., 300 hp) driven by standard VFDs?
Tim Albers: IEC Standard 60034-31 provides calculations that are used for estimating the incremental losses of a motor while running on a VFD. For larger motors it is an incremental 25% of losses over the base motor losses. For 1-125 hp it is 15%. So, if a 300 hp is 95% efficient, then the remaining losses are 5%*0.25% is 0.0125%. So, the new motor efficiency is 93.75% instead of 95%. On smaller VFDs it is 15%. Those values are now incorporated into a number of Department of Energy efficiency rules and the European efficiency rules as well, so they are well accepted.
Topog-E® Gasket Company, formulates and mixes its own rubber manufactures superior moldedrubber handhole and manhole gaskets for steam, hot water boilers, water heaters, softeners, deaerators, make-up tanks, and other selected pressure vessels.
Topog-E® Gaskets have become an industry standard since 1956. Topog-E® Gaskets seal quickly, completely, preventing seepage, corrosion and pitting. They peel off easily leaving clean surfaces for inspection.
Topog-E® Gasket Company offers a FREE Technical Specification and Usage Guide containing useful information about boiler maintenance safety.
Also, FREE a pocket slide rule that charts steam temperature versus pressure.
For more information contact:
Topog-E Gasket Company 1224 North Utica Fax: 918-587-6961 Tulsa, OK 74110 www.topog-e.com Tel: 800-587-7123 info@topog-e.com
PE: When do we need to spec line and load side reactors? What do they do for us?
Tim Albers: Line reactors protect the plant/location electrical from harmonics the VFD sends to the system, load reactors (I strongly prefer load filters over reactors) lower the spikes going down the line to the motor from the VFD. A filter versus a reactor on the load side of the VFD also will have less losses in efficiency which is another reason I prefer them.
PE: When do we specify shaft grounding rings?
John Malinowski: Shaft grounding systems are helpful in installations where there is poor grounding or where common mode voltage is present.
PE: When do we specify ceramic bearings in the motors?
John Malinowski: Ceramic bearings are an alternative to shaft grounding systems. They are more expensive than standard stainless bearings and may be difficult to get in larger sizes.
PE: When do specify both shaft grounding rings and ceramic bearings?
John Malinowski: Such a system would be like having a belt and suspenders, a backup system.
Tim Albers: On larger hp motors such as 100 hp and up, circulating currents become an issue. An insulated bearing of some type (could be ceramic or a coating on the shaft or in the end shield) will stop circulating currents which may not have anything to do with the VFD. The grounding ring then still serves the purpose of taking away the shaft voltage.
PE: Examples of when to use a vector flux drive?
John Malinowski: A flux vector drive controls current to the motor better than a simple volt/hertz inverter. Vector drives are most often used for constant torque applications and accurate speed operation down to zero speed. Adding feedback with an encoder will allow the vector drive to do positioning like a servo.
PE: Can a capacitor-start, single-phase motor be run on a drive?
John Malinowski: No but a permanent split capacitor motor is sometimes used with a triac control for fan applications.
PE: What class of motor insulation will result in an acceptable operation with a drive?
John Malinowski: Most industrial motors are manufactured with a Class F insulation system and operate at Class B rive online power. This gives them the margin for additional losses when operated with a drive.
PE: Inverter duty rated versus normal motor?
John Malinowski: General purpose motors are usually capa-
ble of operation with an inverter and often termed as “inverter-capable.” CSA Group makes manufacturers mark these as inverter duty motors and show the constant and variable torque speed ranges on the nameplate. These motors are identified in NEMA Part 30.
Inverter only motors have different commercial names from each manufacturer. These motors are designed for use with inverters or vector drives only and not designed for line start. Such motors are meant for wide constant torque speed use.
PE: Synchronous motors have low starting torque. I've witnessed problems starting a 600 hp pump with a synchronous motor. How is this problem addressed?
Tim Albers: Many synchronous do have lower staring torque. A few ways to address are designing the motor and system for the torque. Sound simple, but important. Some synchronous are designed with more robust start systems. Also, for larger hp synchronous, an induction pony motor is also a good idea. It engages at start and during accel and then drops off closer to full load speed. It is a fairly inexpensive way to fix a big problem (used it before and it still working over 20 years later).
PE: Do permanent magnet (PM) motors rely on rare earth magnets? Will they become difficult to obtain?
John Malinowski: PM synchronous motors with high power densities like servo motors use rare earth magnets, most other PM synchronous motors use ferrite magnets like PM DC brush type motors.
The government has identified rare earths are a critical material and are working to develop domestic sources.
PE: Does soft start qualify as a variable torque application?
John Malinowski: A soft start only gives reduced torque and inrush current and not variable speed.
PE: What are the biggest challenges you see in VFD installs? Too long cables? Are shunt trips required if a remote disconnect is installed on the load side?
Tim Albers: Shunt trips should not be required. Proper fusing is. Correct grounding from the motor back to the VFD and the cabling required for a good installation are a couple of challenges.
PE: We've seen some instances of instability in VFD speed control due to high electromagnetic interference/radio frequency on the encoder signals. What are your recommendations to mitigate encoder noise issues?
Tim Albers: There are encoders with more isolation. Also, be very sure the encoder feedback signals and cabling are well isolated from the motor cables. The motor cables will overwhelm the control cables for sure. Cannot get commercial, but I do know of some encoders with high isolation for higher electromagnetic frequency locations.
PE: Is there a 120 V 1 hp catalogue I'm looking at fractional horsepower range under 1 hp for a closed loop heating system instead of closing valves to allow heat gain in the boiler.
John Malinowski: Some manufacturers have single phase ECMs in their product lines.
PE: What is the recommended high frequency grounding method for the motors?
Tim Albers: This comes down to the connection. A cable with an external shielding that is designed to capture and transmit the high frequency currents. From motor to ground a strap instead of a cable is better. This is a potential long answer so I can also say to recommend talking to a VFD manufacturer.
PE: How to determine if a blower fan can run direct-online using contactor-overload combo or a motor soft-starter is required?
John Malinowski: Drive bypass systems are sometimes used to eliminate drive losses if the motor will be operated only at full speed.
PE: What method should be used to ground the motor for high-frequency grounding? Assuming that the standard electrical grounding conductor is already connected to the motor electrical junction box.
Tim Albers: Standard grounds will not capture and transmit high frequency currents. Specific cables that are designed with an external braided jacket are the best. That is what would be used to ground the motor back to the VFD. From motor to earth ground, a strap is good as it captures the high frequency as well.
PE: Do you have to do something different if motor is a distance for drive?
John Malinowski: Where long cable runs are present between the drive and motor, line reactors are often used in the system. Check with the drive manufacturer for recommendations. PE
John Malinowski, IEEE Fellow, NEMA MG1 Past Chairman, JMAL Consulting; and Tim Albers, IEEE Senior Member, NEMA MG1 Technical Committee Chairman, Chair of the Associate Member Council, Hydraulic Institute.
Flowserve’s Energy Advantage program is a holistic flow control approach aimed at helping operators reach their sustainability objectives of carbon reduction and lowering total cost of ownership. The program provides you with Flowserve engineering expertise, a systematic data-driven evaluation process, and a complete offering of products and services to help you:
• Reduce carbon emissions.
• Increase energy efficiency through optimization of pump and valve power consumption.
• Improve plant productivity and reliability.
• Achieve operational savings.
Contact us today to see how the Energy Advantage program can accelerate your energy transition plans to achieve net-zero. EnergyAdvantage@Flowserve.com Flowserve.com/EnergyAdvantage
Maintenance programs range from simple to complex. Either choice is correct, as long as it’s followed
—Paul Lachance Industrial Operations Technology Evangelist On behalf of Brightly Software Cary, North Carolina
—Brent Nelson Director of Product ManagementAftermarket and Service Donaldson Bloomington, Minnesota
Plant Engineering: What’s the current trend in maintenance for industrial and manufacturing facilities?
Paul Lachance: Given challenging headwinds in the economy, supply chain and labor force — as well as other uncontrollable factors — industrial and manufacturing leaders are being forced to constantly reevaluate how to stay profitable. And while you can’t control inflationary pressures, you can do the next best thing — operate “lean,” or efficiently, by leveraging technology and other best practices to control cost factors while keeping up with desired quality, safety and team morale.
Using enterprise asset management (EAM) or a computerized maintenance management system (CMMS) and turbo-charging these systems by harnessing asset operational data (otherwise known as the Internet of Things, or IoT), will be essential in this environment. The current trend is to find ways to “do more with less” so your business can stay competitive and profitable in these challenging times — computerize maintenance management systems (CMMS) can help you control costs and stay profitable.
Brent Nelson: More facility management teams continue to move to a condition-based maintenance model and away from traditional periodic or fixwhen-broken maintenance approaches. The desire for condition-based maintenance is driving the need for more connected machines and real-time data and alerts. This is increasing deployment of local control systems and IoT connectivity to a variety of machines.
PE: What future trends should engineers, plant managers and designers expect for predictive and/ or preventive maintenance?
Brent Nelson: More original equipment manufacturers (OEMs) are offering connectivity built into their machines. This data is useful for facility maintenance teams, but it also allows OEMs to offer full-service packages where they can monitor a facility’s equipment remotely and advise end-users on maintenance needs. In addition to monitoring, you’ll start to see more OEMs have the capability and scale to deploy service technicians when they detect a potential performance issue while monitoring from their mobile Paul Lachance: Given the rapid entrance of lower-cost, easier to install sensors — combined with the ability to easily access existing data from supervisory control and data acquisition (SCADA), building automation systems (BAS), smart assets and IoT platforms — engineers and plant managers should expect to see a continued shift away from traditional calendar-based and manually managed usage-based maintenance toward more condition-based or predictive maintenance. It’s more accurate, less evasive on operations and now has viable return-on-investment — even for smaller and less technology-savvy manufacturers.
PE: When considering your most effective maintenance strategies, what are the advantages?
Paul Lachance: The most effective maintenance strategies are the ones that the team embrace, see the value in and promote throughout the organization. Fancy technology serves no purpose if it’s not properly implemented and used. Also, it is not just technology that’s supporting optimized operations: it is a combination of tech and best-practice methodologies. Using best-prac-
‘The desire for condition-based maintenance is driving the need for more connected machines and
real-time data alerts.
’
tice methodology tools such as total productive maintenance, 6-Sigma, 5S and others to promote a continuous-improvement, lean-focused environment complimented by CMMS/EAM is key. If you have operational challenges, software won’t fix them. Understanding and solving those problems before automating will yield the best results.
PE: What are the leading causes of unscheduled downtime and how do you overcome these?
Brent Nelson: The most common issue we see with our customers is a lack of understanding of the equipment and how frequently certain elements should be maintained and replaced (typically filters). Monitoring equipment in real time via a control system or IoT application can identify these needs for service before they lead to production downtime.
Paul Lachance: The main cause of unplanned downtime is the lack of commitment to a proactive maintenance/operations environment. If you ignore simple little issues with assets, they will come back to bite you with profit-killing unplanned downtime. Periodic inspections and, better yet, using sensors to continuously monitor your assets’ health will allow you to avoid unplanned downtime.
It’s not rocket science, it is simply using the core capabilities of CMMS. As you use CMMS more and more, you’ll get amazing analytics that uncover exactly where your sources of downtime are (i.e., identifying the “bad actors”). Analytics, IoT and other advanced CMMS capabilities can help avoid those disruptive issues, leading to lower costs and increased profitability.
PE: What tips would you offer to someone newly tasked with maintenance duties?
Paul Lachance: Honor and learn from the veterans that came before you (and hopefully still work with you). You can learn a ton from these people who have been fixing assets with far less sophisticated tools for possibly decades. Pair
The trend of monitoring and managing connected facility equipment on-the-go from mobile devices and laptops will continue to increase and become the standard.
Courtesy: Donaldson
up with these men and women where possible, capture their skills and park it in your CMMS. Capture a video of that person fixing a bearing set so you can recall later when performing a PM. Get good instructions and pictures for all tasks, again harnessing the skilled work they do. Once these veterans retire, you will still have the next best thing: a great record of their work in your CMMS so the next generation can use this resource.
Brent Nelson: Leverage your outside partners, including dealers, service companies and OEMs to supplement your maintenance teams. While there is some key production equipment your team needs to have full knowledge of, there are a lot of other machines, such as dust collectors, where leveraging specialized expertise can help supplement your team and benefit the company’s bottom line.
A second tip is to invest in regular training and continuing education for your maintenance team. While learning on the job is a given, increasing your team’s knowledge, skill set and capabilities by investing in their professional development will help increase the plant’s overall safety, efficiency and output. Plus, they’ll find more satisfaction in their roles. Helping your team modernize and automate plant processes will free up their time to tackle more strategic and impactful projects for your company. PE
The installation process for dust collection equipment monitoring through Donaldson is simple, using several standard sensors integrated into a cellular gateway. Courtesy: Donaldson
Maintenance
u By using technology wisely, maintenance programs in manufacturing facilities can save time and money.
uThe break-fix model does not work as well as measuring the conditions of systems and then reacting accordingly.
ABB Motors US .C-4 .https://baldor .abb .com/ec-titanium
Atlas Copco Compressors .12, 13 .www .atlascopco .us
AutomationDirect .C-2, 16A-16D .www .automationdirect .com
CARLTON .42 .www .carltonusa .com
DEWESoft .29 .www .dewesoft .com
Digi-Key ELECTRONICS .25 .WWW .DIGIKEY.COM
Dodge Industrial .4 .www .dodgeindustrial .com
Flexicon Corp .6 .www .flexicon .com
FLOWSERVE .45 www .Flowserve .com/EnergyAdvantage
Industrial Cybersecutiy Pulse .44 www .industrialcybersecuritypulse .com
Lubriplate Lubricants Co .14 .www .lubriplate .com
MAPCON .43 .www .mapcon .com
Marketing To Engineers 2023 .7 .www .cfemedia .com/m2e
MOTION .1 .www .Motion .com
Orival, Inc .11 .www .orival .com
ROYAL PRODUCTS .48 .www .mistcollectors .com
SEW-EURODRIVE, Inc .2 .www .seweurodrive .com
SHERWIN-WILLIAMS .28 .www .sherwin .com
spiroflow .33 .www .spiroflow .com
Standard Time .42 .www .stdtime .com/shop-floor
TOPOG-E GASKET COMPANY .42 .www .topog-e .com
VelocityEHS .32 .www .ehs .com
WELDBEND .36, 37 .www .weldbend .com
Yaskawa America, Inc .C-3 .www .yaskawa .com
REQUEST MORE INFORMATION about products and advertisers in this issue by using the www.csemag.com/information link and reader service number located near each item. If you’re reading the digital edition, the link will be live. When you contact a company directly, please let them know you read about them in Consulting-Specifying Engineer.
Publisher/Midwest
Matt Waddell MWaddell@CFEMedia.com
3010 Highland Parkway, Suite #325 312-961-6840
Downers Grove, IL 60515
Account Manager
Robert Levinger RLevinger@cfetechnology.com 630-571-4070 x2218
West, TX, OK
Aaron Maassen AMaassen@CFEMedia.com Integrated Media Manager 816-797-9969
Northeast
Richard A. Groth Jr. RGroth@CFEMedia.com 12 Pine Street 774-277-7266
Franklin, MA 02038
Director of Content Marketing Solutions
Patrick Lynch PLynch@CFEMedia.com 3010 Highland Parkway, Suite #325 847-452-1191 Downers Grove, IL 60515
Marketing Consultant
Brian Gross BGross@CFEMedia.com 3010 Highland Parkway, 630-571-4070 x2217 Suite #325
Downers Grove, IL 60515
Jim Langhenry, Co-Founder and Publisher, CFE Media JLanghenry@CFEMedia.com
Steve Rourke, Co-Founder, CFE Media SRourke@CFEMedia.com
McKenzie Burns, Marketing-Events Manager MBurns@cfemedia.com
Courtney Murphy, Marketing and Events Manager CMurphy@cfemedia.com
Paul Brouch, Director of Operations 630-571-4070 x2208, PBrouch@CFEMedia.com
Rick Ellis, Audience Management Director 303-246-1250, REllis@CFEMedia.com
Michael Smith, Creative Director 630-779-8910, MSmith@CFEMedia.com
Michael Rotz, Print Production Manager 717-766-0211 x4207, Fax 717-506-7238 mike.rotz@frycomm.com
Maria Bartell, List Rental Account Director Infogroup Targeting Solutions 847-378-2275, maria.bartell@infogroup.com
Claude Marada, List Rental Manager 402-836-6274, claude.marada@infogroup.com
Letters to the Editor: Please e-mail your letters to ARozgus@CFEMedia.com
Letters should include name, company, and address, and may be edited for space and clarity.
Information: For a Media Kit or Editorial Calendar, go to www.csemag.com/connect/advertising
Marketing consultants: See ad index.
Custom reprints, electronic: Paul Brouch, PBrouch@CFEMedia.com
From fractional to 600 HP, Yaskawa industrial drives cover all of your application needs, with an array of features that improve your operations.
Intuitive Mobile-Friendly Interaction
Fast Connection to Any Major Network Protocol
Functional safety rated - Standard
Best-in-class Efficiency
And don’t forget about everything else Yaskawa provides you with.
World-Class Quality and Reliability
Award Winning Customer Service
Product Lifetime Training
Free 24/7/365 Technical Support
Life getting too complicated?
Contact Yaskawa for help today.
Sustainable non-toxic environmentally friendly components
Plug and play
Quick and easy motor and drive set-up
A greener solution
Reduce your power consumption with industry leading rotor technology
Upgrade to ABB’s Baldor-Reliance® ultra-premium EC Titanium™ integrated motor drive, and lower your overall energy cost. These motors are specifically designed for VFD operation that help optimize overall performance at reduced speeds and loads, ideal for fans, pumps, and compressors.
•More than 10% efficiency gains compared to NEMA premium
•Reduce power consumption by 25%
•Higher power density for a smaller footprint
Efficient. Innovative. Environmentally friendly.
baldor.abb.com/ec-titanium