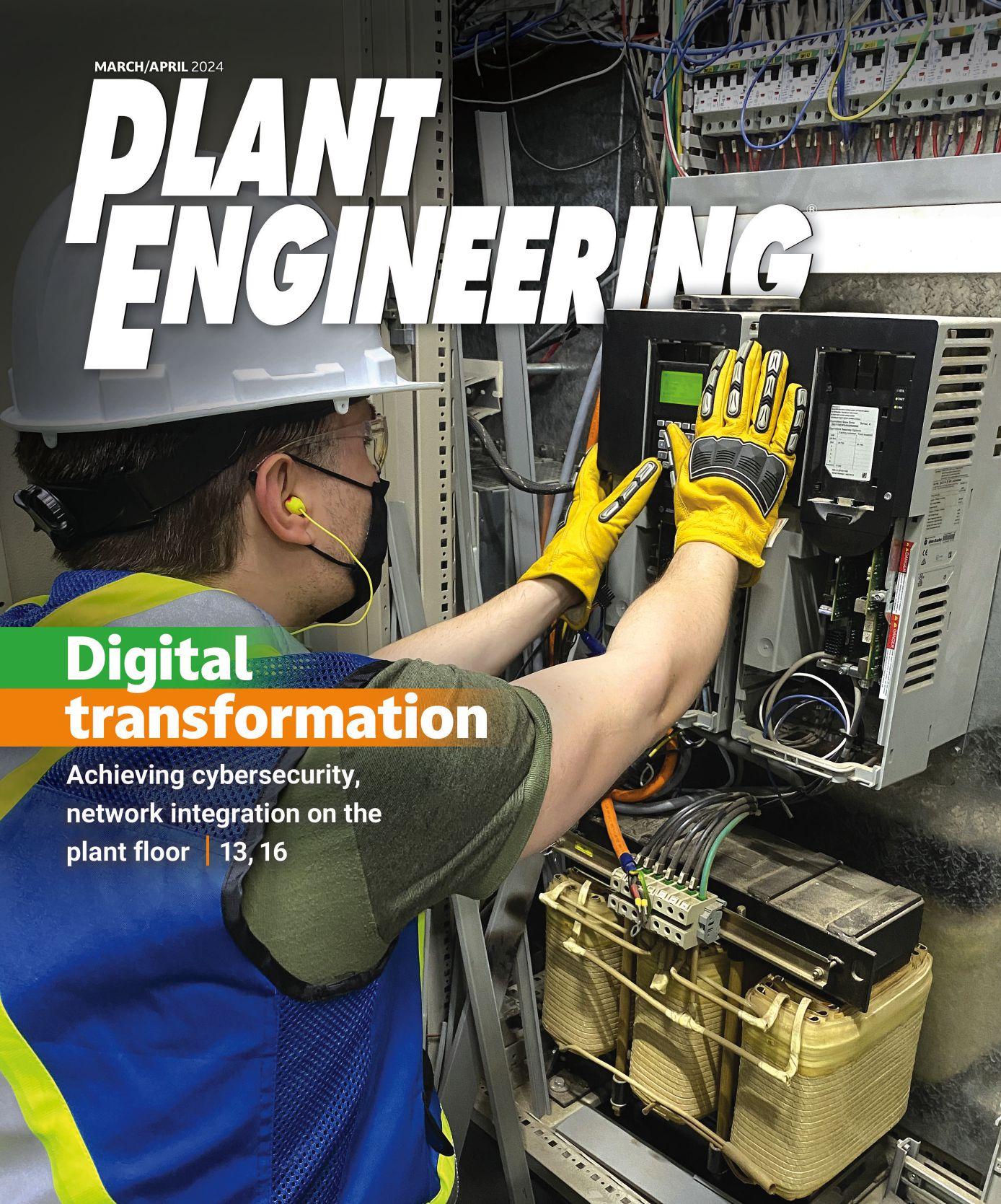
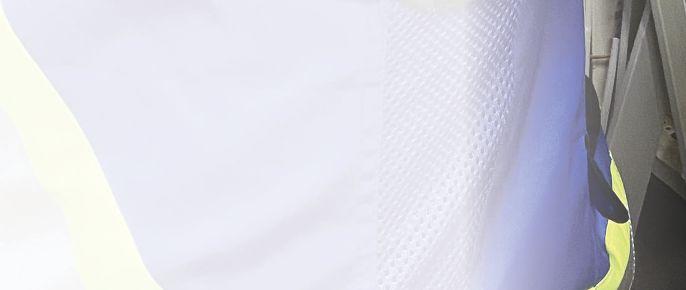
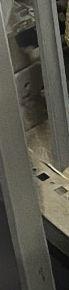


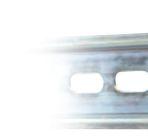
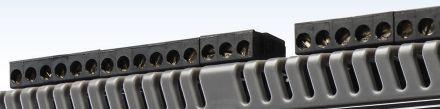
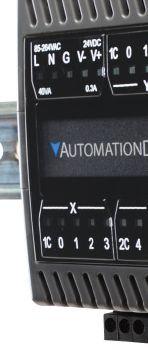
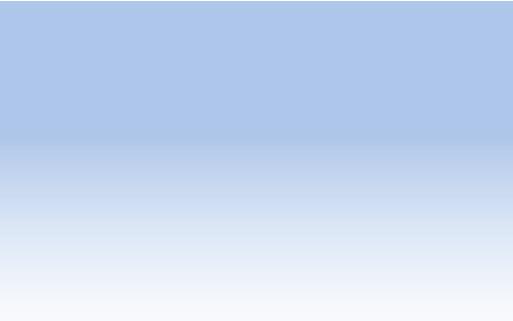
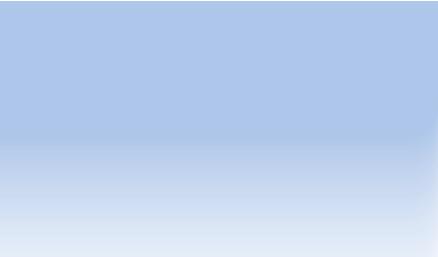
The BRX PLC has advanced features that allow it to easily take on the role of an edge computing device - gathering, re ning, and delivering control system data to upstream IT collection and BIG DATA analysis programs. devicecatalog.azure.com
With BRX’s embedded Web server, you can instantly access system status, diagnostic information, and monitor memory usage from any Internet-ready device.
The integrated Rest API and secure HTTPS protocol allow BRX to work with ow control tools like Node-RED® in order to supply high-level IT systems with the plant- oor data they need.
With the growing number of IIoT platforms and cloud computing services, BRX controllers utilize the industry-standard MQTT(S) and FTP protocols to seamlessly integrate with asset management/ IIoT platforms including:
• Microsoft Azure®
• IBM Watson®
With robust task management and a variety of interrupt styles for task prioritization.
Discrete, process, and multi-axis motion control instructions to support even complex applications, executed with familiar ladder logic programming.
Enabling scripted math and algebra, to support rich data pre-processing right at the edge.
NEW! AchieVe PSA Series DC Power Supplies starting at $25.50
AchieVe PSA series value power supplies offer prices well below the competition and are ideal for price-sensitive users who require basic yet reliable power output for general industrial applications. Their overcurrent protection is designed to operate in constant current mode, making the PSA series suitable for inductive and capacitive loads.
• Universal 85-264 VAC/120-375 VDC input voltage
• 12, 24, or 48 VDC adjustable output options
• 75, 120, 240, and 480 Watt models
• Rugged plastic or aluminum housings
NEW! WAGO Eco2 Series DC Power Supplies starting at $60.00
WAGO Eco2 series power supplies offer performance and value, featuring high efficiency and a compact design. These economical power supplies provide reliable performance and long service life for a variety of applications, such as industrial automation, machine control, and robotics.
• Universal 90-264 VAC input voltage
• 24 VDC adjustable output
• 30, 120, and 240 Watt models
• Rugged plastic or aluminum housings
Available Enclosed Chassis Mount Rugged Machine Mount Value Series
NEW! LUTZE Compact DC Power Supplies starting at $97.00
LUTZE DIN rail mounted compact switching power supplies are high efficiency units that offer space and cost savings. These smaller-than-industry-standard power supplies are offered in four series:
• ECO series power supplies are low-cost single-phase units with an adjustable output voltage
• Ultra series power supplies are single-phase models that reduce space requirements even further with their extremely small size
• 3-phase series power supplies provide an integrated power boost function and remote ON/OFF capability to significantly reduce energy consumption
• Universal series power supplies provide the flexibility of 1-, 2-, or 3-phase inputs, allowing these units to be used in many diverse applications
Pre-configured software modules for motion control
Would you rather enter parameters, or code? MOVIKIT ready-to-use automation modules are pre-configured software elements for many common motion control tasks ranging from simple speed control and positioning to complex multi-axis sequences. These intuitive, user-friendly modules are hardware independent, and can save commissioning time and costs. Simply enter paramters, and GO! Download
Plant Engineering salary survey respondents reported high salaries, bonus compensation
Maintenance best practices have evolved and are changing how workers stay safe 5 | Are you worth more than your peers?
How maintenance trends are affecting, changing manufacturing facilities
Selecting a drive doesn’t have to be a traumatic experience
Piping, valves and fittings all play a role in the overall health and efficiency of a compressed air system
Choosing the right freeze protection can prevent damage from water supply disruptions
Proper design and installation of relief valves can keep industrial fluid systems operating efficiently
AMARA ROZGUS, Editor-in-Chief/Content Strategy Leader ARozgus@CFEMedia.com
CHRIS VAVRA, Web Content Manager CVavra@CFEMedia.com
MICHAEL SMITH, Creative Director MSmith@CFEmedia.com
AMANDA MCLEMAN, Director of Research AMcLeman@CFEMedia.com
SUSIE BAK, Production Coordinator SBak@CFEMedia.com
H. LANDIS “LANNY” FLOYD, IEEE Life Fellow
JOHN GLENSKI, Principal, Automation & Digital Strategy, Plus Group, A Salas O'Brien Company
MATTHEW GOSS, PE, PMP, CEM, CEA, CDSM, LEED AP, Senior Vice President, CDM Smith
Are you a subject matter expert in one of these topics? Would you like to write an article on one of the topics below? If so, please submit an idea to: https://tinyurl.com/PlantEngineeringSubmissions
• Efficient motor management
• Expert Q&A: Hazard protection and hazardous environments
• Expert Q&A: Variable frequency drives (VFD) and variable speed drives (VSD)
• Fall protection
• Material handling
• Predictive maintenance
• Transformer efficiency
Content For Engineers. That’s what CFE Media stands for, and what CFE Media is all about — engineers sharing with their peers. We welcome content submissions for all interested parties in engineering. We will use those materials online, on our Website, in print and in newsletters to keep engineers informed about the products, solutions and industry trends.
* https://tinyurl.com/PlantEngineeringSubmissions gives an overview of how to submit press releases, products, images and graphics, bylined feature articles, case studies, white papers and other media.
* Content should focus on helping engineers solve problems. Articles that are commercial in nature or that are critical of other products or organizations will be rejected. (Technology discussions and comparative tables may be accepted if nonpromotional and if contributor corroborates information with sources cited.)
* If the content meets criteria noted in guidelines, expect to see it first on the website. Content for enewsletters comes from content already available on the website. All content for print also will be online. All content that appears in the print magazine will appear as space permits, and we will indicate in print if more content from that article is available online.
* Deadlines for feature articles vary based on where it appears. Print-related content is due at least three months in advance of the publication date. Again, it is best to discuss all feature articles with the content manager prior to submission.
LEARN MORE AT: https://tinyurl.com/PlantEngineeringSubmissions
Plant Engineering salary survey respondents reported high salaries, bonus compensation
According to the U.S. Bureau of Labor Statistics, the average U.S. annual salary in Q4 of 2023 was $59,384. This is up 5.4% from the same period in 2022, when the typical American was making $56,316 per year. Average weekly earnings reached $1,142, while the average American made $4,949 per month in Q4 of 2023.
Many respondents are at smaller facilities, with 78% at companies that have fewer than 500 employees, and 30% at companies with fewer than 50 employees.
The Plant Engineering audience is ahead of that curve. According to the 2023 Plant Engineering salary survey results, the average base salary in 2023 was $106,312 and the average nonsalary compensation was $19,105. The numbers show that the average professional earned a 3.9% increase over last year.
Amara Rozgus, Editor-in-Chief
Also according to the Bureau of Labor Statistics, the unemployment rate in the manufacturing sector remains historically low at 3.0% in February 2024. In comparison, unemployment was 2.8% in 2023 and 3.0% in 2022.
TM Technology and
When reviewing the average salary data since 2010, average total compensation in 2023 was highest it has ever been at $125,417. In the 14 years of data collection, this is slightly higher than the average total compensation of $116,052.
Bonus compensation was up year over year, due to a host of reasons (respondents could select several options):
• Company profitability: 53%.
• Personal performance: 52%, up from 44% last year.
• Safety metrics, 19% (new to the list).
• Quality metrics, 19% (new to the list).
• New business, sales increase: 16%, down from 23% last year.
The average workweek for those in the entire manufacturing sector (all job titles) is 39.8 hours, according to the Bureau of Labor Statistics. For the 2023 Plant Engineering salary survey study, the average was 46 hours. Again, this may directly relate to those with management titles, or the fact that respondents are from a varied background with a wide variety of responsibilities.
To improve in their profession, respondents shared details about skills they or others in similar positions could use to get ahead:
• Engineering: 76%, up from 71% last year.
• Project management: 68%, down from 70% last year.
• Communication/presentation: 59%, up from 54% last year. PE Register for the full research study online at www.plantengineering.com /research
Your piping system could be key to big savings. With an air leak estimated to cost you in the region of $2,500 per year, those pipes are a potential goldmine when it comes to savings. Keep in mind that not all air leaks are audible, and so ultra-sonic equipment might well be needed to inspect those pipes thoroughly. If you’ve never had an AIRScan, then make 2024 the year to put that right. www.atlascopco.com/tagit
Did you know that an air compressor could also be the key to reducing your fossil fuels usage? By reusing the heat of compression you can get a head-start on the need for warm water, as one example, and save thousands on your heating bill. In many instances, Energy Recovery systems can also be fitted to existing compressors and don’t require much space. www.atlascopco.com/ER
In simple terms, do you have the tools to make your equipment work perfectly in harmony? A central control system will do the critical thinking for you and ensure your system is working efficiently. Most control systems can also work with multiple brands of air compressors. Remote connectivity, diagnostics, and early detection of any issues is a must for any production site as we embark on 2024. www.atlascopco.com/optimizer
Your make your own compressed air, so what about nitrogen or oxygen too? The good news is that if you have a compressor, you are likely already 50% of the way there. By adding a small generator, you have built the system you need to enable you to take control of your gas availability, delivery, purity and price! www.atlascopco.com/nitrogen-usa
‘What if’ is a question we have all asked ourselves on multiple occasions. Since compressed air is critical to any site, what happens if your compressor is not working? Do you have a backup? Do you have a plan to allow essential predictive maintenance to happen? How will I cope if my production doubles or if I need to reduce my capacity? A compressed air plan is essential to your production facility and let us help you make one.
www.atlascopco.com/air-usa
It’s a well known fact that chillers are an essential part of the manufacturing process and effectively removing excess heat is essential to a wide-variety of industrial applications and ensuring product quality. Atlas Copco has brought their own, unique innovation stamp to the range, including remote connectivity, advanced controllers, and exceptional efficiency – with multiple ranges to meet the exact needs of every customer. The chiller ranges follow the principle of “integrated design”. Meaning the hydraulic and refrigerant circuits, condensers, compressors, fans, and superior control systems are always included. Our products are easy to install, with “plug and play” connections.
and applications and stamp to the – with the condensers, are easy to
The process filtration range is focused on liquid, steam, and sterile air, extending our filter product portfolio by increasing its reach into multiple industries, including pharmaceutical, electronics, life sciences and food. The product portfolio includes bags, filters, and cartridges with the goal of preventing microbial contamination and ensuring that the quality of the final product is protected. These filters can be steam sterilized and used with a wide-range of mediums. The stainless-steel housings holding these products are sanitary, and therefore inhibit the growth of bacteria and allow for easy disassembly for inspection and cleaning.
Atlas Copco offers a complete range of aeration blowers, with multiple technologies on offer, including positive displacement technologies (screw blowers and lobe blowers) and centrifugal technologies (high-speed turbo blowers and multistage blowers). All our oil-free air blower technologies are designed to offer you quality air and maximum uptime of your process, safeguarding the quality of your end product. Having a complete range ensures customers can selecting the best blower technology for their application over its lifetime; when the cost of purchase, electricity usage, and service is all factored in.
Maintenance best practices have evolved and are changing how workers stay safe and improve their operations.
Question: What’s the current trend in maintenance for industrial and manufacturing facilities?
John Gaddum: The current trend for manufacturers is to rely more heavily on outsourcing of the expertise and knowledge of their equipment directly from the OEM's or manufacturers (software/hardware) when there is a need.
Lance Gilbert: The current trend in maintenance for industrial and manufacturing facilities is leaning towards adopting software-as-a-service (SaaS) subscriptions for master data management (MDM). This approach acts as an upfront data governance tool that seamlessly integrates with enterprise resource planning (ERP), enterprise asset management (EAM) or computerized maintenance management systems (CMMS), ensuring efficient and standardized data management across operations.
• Understand and learn about the current maintenance trends manufacturers are dealing with.
• Learn how different thought leaders are developing their maintenance strategies to evolve with a changing manufacturing landscape.
Pratibha Pillalamarri: Manufacturing facilities are adopting data driven maintenance strategies by leveraging advancements in data analytics, Internet of Things (IoT) sensors and machine learning algorithms. This shift allows for real-time monitoring of equipment condition, enabling proactive identification of potential failures before they occur.
There is a growing emphasis on incorporating predictive maintenance into existing preventive maintenance programs to optimize maintenance schedules and resource allocation by considering equipment criticality & failure mode severity. The overall goal for asset intensive industries is to enhance equipment reliability, minimize downtime
and maximize operational efficiency, driving down maintenance costs and improving productivity.
Q: What future trends should engineers, plant managers and designers expect for predictive and/ or preventive maintenance in the next 1-2 years?
Gaddum: Budgeting for transition and support planning. Transfer of budgeting from training their own employees, to the outsourcing of external experts with a plan in place to support the production demands of their equipment.
Gilbert: in the next 1 to 2 years, engineers, plant managers and designers should anticipate a surge in future trends for predictive and preventive maintenance. This includes the widespread integration of artificial intelligence (AI), IoT, inspection technologies, digital twins, predictive analytics and the emergence of predictive-maintenance-as-a-service. Additionally, there also will be an increasing adoption of an array of immersive technologies on the shop floor, collectively shaping a tech-driven landscape to enhance maintenance strategies and overall operational efficiency.
Pillalamarri: There's a shift towards proactive, data-driven methods that aim at optimizing asset performance, reducing downtime, and promoting sustainability. Asset performance management (APM) solutions are crucial, offering comprehensive coverage of asset and process health. They aid sustainability efforts by minimizing downtime, product loss, resource and energy waste and expenses.
They also provide early warnings for process and mechanical issues, enabling timely adjustments to maintain yields and product quality. Predictive alerts facilitate proactive maintenance, avoiding unplanned breakdowns. APM solutions also promote sustainable practices, optimizing maintenance schedules and minimizing energy waste. This integrated
AutomationDirect is a non-traditional industrial controls ideas from the consumer world to serve your automation quality products fast for much less than traditional suppliers, every step of the way. See below . . .
Our campus is located about 45 minutes north of Atlanta, GA, USA. We’re all here - our sales and technical support teams, purchasing, accounting, and of course our huge warehouses and speedy logistics team.
You want complete product information to make the right purchase decision.
Whether you’re deciding on purchasing our products or learning our products after you buy, why jump through hoops or even pay for the information you need?
We have exhaustive documentation all freely available online, including overviews, technical specifications, manuals and 2D and 3D CAD drawings.
We have over 1,500 videos online to get you up to speed quickly. We even provide FREE online PLC training to anyone interested in learning about industrial controls.
http://go2adc.com/videos http://go2adc.com/training
You need quality products at great
For over 25 years, we’ve been offering a better by running our direct business efficiently and you. No complex pricing structures or penalty everyday prices on everything from fuses to Programming software for controller products can be costly, so we help you out by offering FREE downloadable software for all our latest PLC families and C-more HMIs. No license or upgrade fees to deal with!
http://go2adc.com/why
You don’t want to wait for your
We have fast shipping, and it’s FREE if your order is over $49.*
At AutomationDirect, we strive to have what you it. We’ve invested heavily into infrastructure, inventory, automation so that we can continue to provide you products, at great prices, extremely fast!
*Order over $49, and get free shipping with delivery in 2 business the U.S. (Certain delivery time or shipping cost exceptions may Conditions online for complete details. http://go2adc.com/terms
You insist on getting better service and you want it FREE.
Our technical support team provides superior assistance and has consistently received high ratings from satisfied customers. And it won’t cost you a cent!
Before, during, and after any sale, contact us with questions and we’re glad to help, http://go2adc.com/support-ss
company using the best automation needs. We deliver suppliers, and support you
great prices.
better value on industrial controls and passing the savings on to penalty for small orders, just low motors.
Our primary focus has always been customer service — practical products, great prices, fast delivery, and helpful assistance. But the intangible value of customer service is something that cannot be faked, automated or glossed over.
Our team members here at AutomationDirect approach every day with one goal in mind - serve the customer. If the answer to any decision is “Yes, this is good for our customers”, then we do it, whether personally or via self-serve features on our site.
need, when you need inventory, and warehouse you with quality
business days (or less) within may apply; see Terms and http://go2adc.com/terms) your order.
You want to be confident in our products and our commitment to you.
We stand behind our products and guarantee your satisfaction. We want you to be pleased with every order. That’s why we offer a 45-day money-back guarantee on almost every stock product we sell. (See Terms and Conditions online for exclusions.)
We’ve shopped around to bring you the most
industrial control products at the best prices!!
BRIAN in CLEVELAND, TN:
“I love having a single website that I can use for selecting and purchasing everything I need for our industrial automation projects. With fast shipping times, an active support forum, and competitive prices, there’s nothing else that compares. Thanks!”
CODY in MOORESVILLE, NC:
“Best phone support I’ve gotten from a supplier yet, answers the phone quickly and has a very knowledgeable staff.”
DAVE IN MITCHELL, SD:
“In 10 years of using the company products and services I’ve only had a few returns. The products are reliable and the customer service has always been second to none. I plan to continue using the company into the future.”
JOHNNY IN NEW CANEY, TX:
“Excellent company. Use it regularly and highly recommend it to others.”
BEN IN PAHRUMP, NV:
“We use AutomationDirect as a standard supplier for many of our UL508 control panel components, and have never had a single issue! Automation Direct has an incredible stock of inventory and product selections, and the two day shipping gets us the parts we need right on time!”
Mark in AYLMER, ON:
“We have been buying from Automation Direct for quite a few years now and we have been really happy with the service and range of products available and the prices are usually as good or better than elsewhere.”
Daniel in ALLIANCE, OH:
“They are the best game in town for industrial PLCs”
approach enhances operational efficiency, reliability and environmental leadership in industrial and manufacturing sectors.
Q: What are the fundamental distinctions between predictive and preventive maintenance, and how do these approaches complement each other in an ideal maintenance strategy?
Gaddum: Preventive maintenance is the time-tested practice of the scheduling of periodic maintenance in order to keep equipment from premature wear and tear. Preventive maintenance does not warn you, guarantee or prevent failures from occurring. It's just good practice, similar to regular oil changes for your car, but certain electronic and mechanical hardware have a certain life expectancy. Predictive maintenance involves the monitoring of equipment, in real-time, to help identify or predict potential failures due to changes in the operation of equipment.
Gilbert: The fundamental distinctions between predictive and preventive maintenance lie in their timing and approach. Predictive maintenance operates as needed, relying on real-time data collection and analysis of machine operation to detect issues at their early stages, preventing production interruptions. Repairs in predictive maintenance occur during machine operation, addressing actual problems.
In contrast, preventive maintenance involves scheduled routine inspections and tasks aimed at preventing potential issues. These approaches complement each other in an ideal maintenance strategy by combining proactive measures with just-in-time interventions. Predictive maintenance minimizes downtime by addressing issues precisely when needed, while preventive maintenance establishes a preventive framework to minimize the likelihood of issues arising in the first place. Together, they create a comprehensive strategy that maximizes equipment reliability and operational efficiency.
Pillalamarri: Preventive maintenance involves regularly scheduled inspections, servicing and replacement of parts to prevent equipment failure. These tasks are calendar-based regardless of whether there are signs of impending failure. Predictive maintenance uses data from sensors and maintenance records and applies advanced analytics and other monitoring techniques to predict when equipment is likely to fail accurately. In an ideal world, these two strategies can complement each other.
The data gathered from predictive maintenance can inform and refine the preventive maintenance schedule, ensuring tasks are performed when they're most needed.
Predictive maintenance helps prioritize tasks based on actual equipment condition, while preventive maintenance ensures that essential maintenance tasks are not overlooked. By combining both approaches, organizations can allocate resources more efficiently.
Q: Describe the successes from using programs that incorporate predictive, preventive, reliability-centered or reactive maintenance.
Gilbert: Programs incorporating predictive, preventive, reliability-centered and reactive maintenance demonstrate success through systematic preventive schedules, efficient real-time interventions in predictive maintenance, optimized focus on critical components with reliability-centered approaches and swift issue resolution in reactive maintenance. This holistic strategy results in enhanced equipment reliability, prolonged asset lifespan and minimized downtime, contributing to improved operational efficiency and cost-effectiveness.
Q: Tell us about a recent maintenance project you’ve worked on that’s innovative, large-scale or otherwise noteworthy. Please tell us about the location, plans your team engineered, key players, interesting challenges or solutions and other significant details.
Gilbert: We recently led an innovative maintenance project within St. Gobain's Building Products Division, collaborating closely with key stakeholders such as engineering and maintenance teams, inventory personnel and C-level executives.
The project aimed at achieving significant outcomes, including a remarkable 10% increase in maintenance productivity, a 12% improvement in machine downtime and a 10% boost in storeroom productivity. Our strategy also targeted enhanced PO accuracy and the elimination of 3-way match errors.
Despite an investment of $1.4 million, the project demonstrated exceptional efficiency, reaching breakeven in nine months. The success of this large-scale initiative underscores our commitment to innovation, collaboration and tangible improvements in maintenance operations.
Q: What percentage of your team is focused on maintenance? What percentage of your entire operation is focused on maintenance? How will this change in the next 12 months?
Gaddum: As part of the service group, our help desk and field service engineers are always supporting customer maintenance personnel, but not necessarily focused on predictive or preventive maintenance. We help guide customers on the practices but were more reactive to the causes of failure.
Gilbert: As an MDM vendor, our entire team is dedicated to maintenance and inventory levels, constituting 100% of our focus. Our operational structure revolves entirely around providing comprehensive solutions in these domains.
Looking ahead, over the next 12 months, our commitment to maintenance and inventory management remains steadfast, with no anticipated changes in our strategic focus. We continue to prioritize excellence in MDM services to further support our clients in optimizing their maintenance operations and enhancing overall efficiency.
Q: What are the leading causes of unscheduled downtime, and how do you overcome these?
Gaddum: Not having any predictive or preventive maintenance plan. We see this a lot at our customers
when their production overrides the need for taking good care of the equipment.
Gilbert: The leading causes of unscheduled downtime often include not having the right part at the right time, missing or incomplete bill of materials (BOM) parts lists, an excessive number of emergency orders and spot buys, and unplanned outages exceeding acceptable tolerances. These challenges can be effectively addressed through the implementation of a robust MDM system.
By centralizing and managing critical data related to parts, inventory and maintenance processes, an MDM system ensures accurate and up-to-date information, minimizes errors in BOMs, optimizes inventory levels and streamlines the procurement process. A well-implemented MDM system becomes a proactive solution to mitigate the causes of unscheduled downtime, promoting operational efficiency and reducing disruptions.
Q: What new or increased technologies do you plan to implement at your facility?
Gilbert: We recommend a comprehensive MDM platform. This platform will encompass software solutions, a robust data dictionary, integration with EAM and a SaaS model. Additionally, we aim to incorporate services and reliability information into the MDM framework. This approach harnesses the
power of artificial intelligence and machine learning, streamlining data management processes, enhancing system reliability, and ultimately contributing to the overall success of any facilities that deploy.
Q: How have artificial intelligence (AI) and machine learning (ML) changed maintenance in the last few years and what have the results been like?
Pillalamarri: Artificial intelligence (AI) and machine learning (ML) have transformed maintenance practices, enabling predictive and prescriptive approaches. By analyzing data from sensors, equipment logs and historical records, these technologies predict equipment failures, optimizing maint enance schedules based on actual condition rather than predetermined time intervals. This minimizes downtime and maximizes asset performance. Integrating AI and ML can yield significant results such as reduced unplanned downtime, improved reliability, and enhanced efficiency. These technologies can extend equipment lifespan, cut maintenance costs, and enhance asset management strategies. They also can facilitate the shift from reactive to proactive maintenance, improving resource allocation and productivity. As AI and ML evolve, their impact on maintenance is expected to grow, driving further improvements in reliability, efficiency, and cost-effectiveness across industries.
2: Aspen Mtell Alert Manager. Courtesy: AspenTech
‘ Artificial intelligence (AI) and machine learning (ML) have transformed maintenance practices, enabling predictive and prescriptive approaches.’
Q: What tips would you offer to someone newly tasked with maintenance duties?
Gaddum: Put a preventive and predictive plan in place and plan to provide remote access to your equipment from reliable resources for support.
Gilbert: For someone newly tasked with maintenance duties, my key tip would be to thoroughly examine the need for implementing an MDM system at your plant. A robust MDM system can significantly streamline maintenance operations by centralizing and maintaining accurate data related to assets, parts and maintenance processes. It enhances data reliability, reduces errors, and ensures consistency across various systems. By adopting MDM early on, you establish a strong foundation for effective maintenance management, ultimately contributing to increased operational efficiency and improved decision-making. PE
Lubriplate’s ultra-high-performance, 100% synthetic lubricants have been engineered to provide unsurpassed performance in the most demanding plant environments. They provide a wide range of benefits designed to make your plant run better. Benefits include: extended lubrication intervals, lubrication consolidation through multiple application capability, reduced friction, extended machinery life and reduced downtime. Products include...
HIGH-PERFORMANCE SYNTHETIC GEAR OILS
SYNTHETIC AIR COMPRESSOR FLUIDS
SYNTHETIC HYDRAULIC FLUIDS
HIGH-PERFORMANCE SYNTHETIC GREASES
NSF H1 REGISTERED FOOD GRADE LUBRICANTS
ECO-FRIENDLY SYNTHETIC LUBRICANTS
SPECIALTY LUBRICANTS
Younes Rashidi, Hedgehog Technologies, Burnaby, British Columbia
The integration of networking systems and edge computing is revolutionizing data processing and enhancing real-time decisionmaking across key industries
The digital world is on the verge of a revolutionary transformation, mainly driven by the integration of networking systems and edge computing. This shift goes beyond conventional methods of processing data, pushing boundaries to enable more efficient and real-time decision-making.
It's a critical moment for businesses across all sectors, where adapting to this evolving landscape is not just a strategic move but a necessity to remain competitive. This transformation is changing industries, setting a new standard for technological advancement and positioning those who embrace it as pioneers in the field.
The integration of networking systems and edge computing marks a significant milestone in recent years. This convergence is not just about combining technology but represents a substantial shift in how data is processed and used.
Networking systems, traditionally central to data transmission and communication, are now intertwined with edge computing's capability to process data closer to its source. This integration is transforming the way we manage vast amounts of data, reducing latency and enhancing data processing efficiency in a rapidly expanding digital world.
For instance, real-time data processing using edge computing is becoming crucial in autonomous
vehicles where, in a split second, an enormous amount of data needs to be processed locally.
The integration of these technologies has greatly improved the ability of organizations to make informed decisions in real time. This ability is particularly valuable in industries where prompt decision-making can have a huge impact on outcomes.
For example, in health care, instant analysis of patient data can lead to rapid diagnosis and treatment plans, potentially saving lives. In financial services, it allows for faster transaction processing and fraud detection, thus protecting both the institution and its clients.
In manufacturing, this integration enhances operational efficiency and predictive maintenance, leading to reduced downtime and increased productivity. The automotive industry benefits from advancements in autonomous driving systems.
• Understand the significance of integrating networking systems and edge computing in transforming data processing, reducing latency and enhancing efficiency in various industries.
• Explore the potential benefits and challenges of this technological convergence.
• Evaluate the opportunities and challenges businesses face in adopting networking systems and edge computing.
Digital insights
uThe ongoing integration of networking systems and edge computing is revolutionizing data processing digitally, enhancing efficiency and enabling real-time decision-making in a rapidly expanding digital world.
uBusinesses that strategically adapt to the evolving digital landscape — seizing opportunities presented by integrating networking systems and edge computing — can gain acompetitiveadvantageand thrive in today's market.
Although technological convergence has numerous advantages, it also presents various challenges. One of the most critical challenges is ensuring data security in a more distributed computing environment. Moreover, it is crucial to have a robust infrastructure to support these technologies.
The demand for skilled personnel capable of managing and optimizing these integrated systems is another significant challenge. One of the biggest barriers remains the investments required for this transformation. To fully harness the potential of this technological convergence, businesses must address these challenges.
Integrating networking systems and edge computing presents numerous opportunities for innovation
and efficiency. Businesses can harness this technology to improve operational efficiency, enhance customer experiences and create new opportunities.
However, seizing these opportunities requires strategic adaptation. Organizations need to invest in the proper infrastructure, develop new skill sets among their workforce and foster a culture of innovation to stay ahead.
In a fast-paced digital economy, businesses must embrace technological transformation to gain a competitive edge. Companies that successfully integrate these technologies can expect to see improvements in efficiency, agility and customer satisfaction, positioning themselves as leaders in their respective industries. In short, embracing and adopting these technologies is no longer just beneficial, it is an essential competitive advantage for businesses to thrive in today's market.
The future of networking systems and edge computing is on the verge of a transformation marked by promising innovations. As these technologies continue to evolve, the horizon is expanding with excess innovative applications and enhanced efficiencies. This advancement is involved with emerging trends like the internet of things, industrial internet of things, artificial intelligence and machine learning, which are expected to weave more profoundly into the fabric of networking and edge computing, forging systems that are not only more sophisticated but increasingly autonomous in nature.
This ongoing integration is far more than a fleeting technological trend; it represents a fundamental paradigm shift, redefining the shapes of the digital landscape. For businesses, this change is not just an option but a requisite adaptation to stay relevant and competitive. Those who embrace and harness the power of this convergence will likely find themselves at the forefront of digital transformation, using these advances to fuel innovation, drive efficiency and carve out a competitive edge. This transformative journey promises a future where embracing technological convergence is synonymous with driving business success and innovation. PE
Younes Rashidi is the VP of engineering operations for Hedgehog Technologies.
CYBERSECURITY
Scott Dowell, Wesco, Pittsburgh
The industrial Internet of Things (IIoT) has the potential to deliver positive outcomes to the industrial industry, but protecting the facility from new cybersecurity threats is critical.
The industrial Internet of Things (IIoT) revolution is well underway. From small manufacturers to global powerhouses, industrial businesses are coming to understand the power and potential of connected devices and systems. According to a 2021 report from Microsoft, 90% of organizations cited the adoption of IoT as a critical element for success in manufacturing. From operational efficiency to safety, cost containment to productivity, IoT has the potential to deliver positive outcomes in an industrial market where margins are historically razor thin.
However, there is a potential roadblock to successfully digitizing your operations and executing your vision for Industry 4.0: If a system is connected to the internet, it’s vulnerable to cyber attacks.
From access controls to the electric grid, smart buildings to industrial control systems (ICS), end points and opportunities abound for hackers to exploit and they are building automated, credential-based attacks to do that. For those with information technology (IT) and operations technology (OT) infrastructure to safeguard, understanding the convergence of those systems and protecting them from nefarious actors is a critical and daunting task.
Cybersecurity attacks also are becoming more sophisticated. According to Symantec, IoT devices are faced with an average of 5,200 cyber-attacks each month. Further research has found ransomware is one of the hottest approaches when it comes to exposing plant floor vulnerabilities.
Ongoing research from Marsh Insurance’s cybersecurity division found that ransomware remains the number one cyber threat. Two-thirds of cyber-attacks are facilitated by ransomware-as-a-service. These schemes aim to create a larger web of opportunities for cyber criminals to exploit by paying “affiliated” hackers to execute pre-developed ransomware schemes and hold data hostage.
These hackers are searching for cracks in your connected infrastructure and once exploited can lead to extended system downtime and lost revenue. Vulnerabilities and weaknesses in your industrial controls network are areas that could most compromise operations or system availability. These include outdated hardware or software, unpatched systems and inadequate security controls.
It's not all doom and gloom, however. There are strategies that can increase network performance
and availability while building a more secure, robust and resilient network. For example, consider preventive and predictive plant services that help illuminate the current state of what’s installed on the plant floor. Once the risk is understood, companies should work to ensure the security roadmaps are aligned with industry standards and best practices, which is an effective and straightforward way to stay on top of evolving threats.
Having an OT-specific cybersecurity plan is essential to protecting critical assets and mitigate risks on the plant floor. Most companies know this is important, but don’t know where to start. That’s where the NIST Cybersecurity Framework comes into play.
The National Institute of Standards and Technology (NIST) is an offshoot of the U.S. Department of Commerce, the agency’s mission is to promote “innovation and industrial competitiveness” through science, technology, and standards. There are six key tenants:
1. Identify – Understand which operational processes and critical assets need protection.
2. Protect – Adopt and deploy safeguards to protect those entities.
3. Detect – Identify systems that can alert the organization to an active cyber threat.
4. Respond – Plan and execute for the best ways to contain a threat.
5. Recover – Restore functions and services to their pre-attack mode.
6. Govern – Emphasize that cybersecurity is a major source of enterprise risk and a consideration for senior leadership.
The NIST Cybersecurity Framework helps businesses of all sizes better understand, manage and reduce their cybersecurity risk and protect their networks and data. NIST also makes it easy for everyone to work toward the same goal, talk in the same language and streamlines the process to bridge the IT/OT gap and shore up a company’s security posture.
FIGURE 2: Consider implementing preventive and predictive plant services to help illuminate the current state of what’s installed on the plant floor and what needs to be protected.
Courtesy: Wesco
For example, a food supplier experienced a cybersecurity incident on their IT network in 2021. While the situation was contained and didn’t impact production, the company was aware the risk for another such incident was likely around the corner and were interested in further reducing their OT risk.
As a result, the company deployed a more robust cybersecurity program aligned with NIST. They started by conducting cybersecurity health checks. This included an audit to identify vulnerabilities which enabled them to mitigate potential risks that were uncovered during the process and shore up their cybersecurity posture.
As a result, they were able to address the vulnerabilities, gain greater insights into the plant floor networks and minimize cybersecurity threats to meet compliance goals. They also gained insight into asset utilization, were able to optimize operations, and reduce downtime from cyber-attacks saving them thousands of dollars. Today, the organization can monitor threat detection in real-time and has expanded their capabilities to two other manufacturing facilities.
Manufacturers need to be proactive in preventing possible risk and damage to their business. Ensuring IT and OT systems are safe and secure requires all-hands-on-deck engagement. By following industry best practices and leaning on established frameworks such as NIST, organizations can continue securely down the path towards IIoT. PE
Scott Dowell is senior vice president and general manager, industrial and CIG at Wesco.
• Learn why manufacturers need to be proactive to manage cybersecurity risk.
• Understand the sophisticated attacks and threats that are being perpetrated right now.
• Learn how the National Institute of Standards and Technology (NIST) and their Cybersecurity Framework can help address vulnerabilities.
u
Cybersecurity insights
u The industrial Internet of Things (IIoT) brings immense potential for manufacturers, but cyber threats pose a significant risk to their safety.
u Adherence to frameworks like NIST aids in fortifying networks, enabling real-time threat monitoring, minimizing downtime, and enhancing operations.
David Kennedy, VAC-U-MAX, Belleville, N.J.
Automation of bulk powder handling is a natural step for companies that consider current powder handling tasks as a danger to worker health or to ongoing plant operations, product quality and consumer safety and more.
Bulk powders are used at some stage in almost every industry: Fwood, pharmaceutical, confectionary, chemical, plastics, aerospace, nutraceutical, packaging, additive manufacturing (3-D printing) and energetics. Even liquid end-products will have powdered ingredients that give those liquids an identity or function: sports and energy drinks, alcohol, soups and sauces, lubricants, and paint.
• Identify tangible and quantifiable benefits that automation of bulk powder handling can bring to every company.
• Automation can range from very basic to very sophisticated technology depending on the size and nature of the company’s operations.
• Automation makes laborers and other process equipment work better.
However, powder handling means different things to every company, generally based on the volume and type of powders they introduce to their manufacturing process or the ultimate end-product which is in the form of a powder.
Small family-owned businesses and the largest companies in the world, as well as government-owned facilities, have different concepts of “bulk powder handling”. Some focus on the “bulk” part: They have powders supplied in non-consumer-sized containers such as 50-lb. bags, 55-gal. drums, 2,000-lb. bulk bags or supplied from silos.
Others focus on the “handling” part, which is an engineered process with equipment to transport the product from point A to point B.
The benefits of automating the bulk powder handling process will provide varying benefits depending on the user’s perspective, but there are several that will often come to the forefront.
1: Vacuum conveying allows change from manual bag dumping to bulk bags for lower cost of materials. Courtesy: VAC-U-MAX
Manual container dumping or filling of bulk powders can be a repetitive, physically demanding, and mind-numbing activity that leads to musculoskeletal disorders, which the Bureau of Labor Statistics of the Department of Labor defines as “musculoskeletal system and connective tissue diseases and disorders when the event or exposure leading to the case is bodily reaction (e.g., bending, climbing, crawling, reaching, twisting), overexertion, or repetitive motion, from bending, twisting, pushing, pulling…
National Safety Council data shows the average (direct) worker’s compensation costs of a lower back injury was almost $40,000 in 2021, arms/shoulders at $50,000 and hip/thigh/pelvis injuries at almost $60,000. That’s not counting the indirect costs, which can be several times greater than the direct costs. Indirect costs can include lost time, increased worker’s compensation insurance premiums, recruiting costs or repositioning a substitute worker, new worker training, slower productivity of replacement worker and more. Vacuum-assisted lifting devices also can reduce repetitive motion tasks when they’re part of a vacuum conveying system. Vacuuming materials from drums or bulk bags also helps reduce heavy-lifting and lower-back strains.
Personnel also need to be safe from inhalation hazards from fugitive dusts. Manual dumping and filling can expose workers to allergens such as sesame seed dust and milk powders. Other powders
such as super-absorbent polymer (SAP) will dry out mucous membranes in the eyes and nose of workers if over-exposed. Workers in certain industries can be exposed to carcinogenic materials such as silica sand through inhalation.
Automation via vacuum conveying of these powders in lieu of manual handling reduce fugitive dusts and unhealthy or life-threatening exposures.
However, if bag dumping cannot be avoided, devices such as bag dump stations with integral dust collectors at the entry point of a vacuum conveying system will draw dusts away from the worker when dumping bags of powder.
Workers also are at risk in combustible dust environments. Despite the known dangers of combustible dust explosions, workers continue to be injured or killed in plant environments with poor
Vacuum conveyor keeps auger-filler packaging machine full with constant head pressure of powder for accurate filled containers. Courtesy: VAC-U-MAX
dust control and lax housekeeping which often result from manual powder handling operations and lack of automation of the powder handling tasks.
Most organic materials and many non-organic materials such as plastics will be found to be combustible when in powder form. Manual filling of process equipment will result in accumulations of fugitive dust on floors, machine surfaces, walls and overhead building structures. These conditions make a facility ripe for a combustible dust explosion if an ignition source such as static electricity discharge or an overheated bearing is initiated. NFPA standards regarding combustible dust, and OSHA’s enforcement of the standards are focused on life safety and continuing operations by preventing dust accumulations and conditions that lead to catastrophic combustible dust events. Powder handling automation with an enclosed vacuum conveying system will reduce, if not eliminate, fugitive dusts escaping into the plant environment. It has been said in hazard and operability (HAZOP)
evaluations that “training is not an acceptable safety device.” The possibility of human error remains and automation via vacuum powder conveying is suitable as an engineering control and a device that reduces the chances of operator error.
The enclosed nature of a vacuum conveying system will prevent opportunities for accidental or intentional contamination of the ingredient stream. Food and pharma products, nutritional and cosmetic products and the like have increased risk of recall or injury from contamination if their powder handling process has gaps due to manual handling. Again, vacuum conveying of powders will protect product and brand integrity and maximize consumer safety and confidence.
Contamination and inconsistent delivery of powders into a manufacturing process will ruin quality control plans. Automation of powder handling via vacuum conveying, or specifically batch
‘ Automation via vacuum conveying can eliminate the forklift tasks and laborer from the process time allocation. ’
weighing vacuum systems, will deliver consistent and unadulterated finished product. Recipes can be accurately followed and ingredients are not wasted. Segregation of allergen-containing products is best accomplished with an enclosed vacuum conveying system. Enclosed vacuum conveying systems reduce the chance of pest infiltration as well. Packaging equipment such as auger fillers require consistent feed of powders in the packaging machine supply hopper. An automated vacuum conveyor maintains the consistent “head pressure” to make the auger filler perform at its best.
Other powder processing equipment such as loss-in-weight (LIW or gravimetric) feeders are most accurate when the refill time is minimized. Gravimetric feeders convert into volumetric (non-weighing) mode during its fill cycle. Minimizing the refill time maximizes the accuracy of a gravimetric feeder.
A vacuum conveyor accomplishes this by holding the next batch of powder waiting for the refill signal from the feeder and immediately discharging the powder. This is known as discharge-on-demand and is a form of immediate gratification in the bulk powder handling industry.
5. Increased worker productivity
Manual handling of bulk powders can work until the need for increased throughput outpaces the
human body’s ability to keep up. Automated powder handling can take a production rate to the next level and not be limited by the human’s physiology. Today’s powder packaging lines can demand up to 10,000 lb. (4,500 kg) of powder per hour. Workers cannot climb ladders and dump boxes fast enough to meet that rate. Automation via vacuum conveying is the best answer to refilling today’s bottling lines, stick-pack fillers and vertical form-fill-seal (VFFS) machines.
Productivity is also improved when time-consuming steps are removed and replaced with higher-output solutions like automated powder handling. Many powder handling operations require forklifts and operators in production suites to raise pallets of bags up to mezzanine level. Automation via vacuum conveying can eliminate the forklift tasks and laborer from the process time allocation.
Ingredients can stay on the ground floor and forklifts can stay outside of the production suite thus saving time and space. Automated powder handling such as direct-charge blender loading not only reduces material handling via forklift, but it also stops workers from climbing on mezzanines to dump those bags into tumble blenders.
Bulk powder handling insights
uAutomation in bulk powder handling enhances worker safety by reducing musculoskeletal disorders, inhalation hazards and the risk of combustible dust explosions, minimizing direct and indirect costs.
uAutomated powder handling not only improves operational safety and consumer confidence but also boosts productivity, quality control and inventory management.
Automation of bulk powder handling can make other process equipment perform better. A vacuum conveying system can increase the throughput of batch equipment such as rotary blenders and ribbon blenders by staging ingredients above the blenders/mixers for immediate filling when the previous batch is completed. Automation cannot shorten the mixing process, but it can shorten the loading and unloading times to complete more batches in a day.
The current and foreseeable labor shortage can also be solved with automation of powder handling tasks. Seasonal increases, or
FIGURE 9: Volumetric and gravimetric feeders are big beneficiaries of automated vacuum conveying for refill.
Courtesy: VAC-U-MAX
long-term production increases are accommodated using vacuum conveying or powders. Vacuum conveyors won’t complain about repetitive tasks, and they don’t take vacations, and they help achieve higher output goals when new hires are in short supply.
Automated bulk powder handling increases productivity, reduces potential costs and liabilities from employee workplace injuries, ensures ongoing operations in a safe plant environment, reduces the risk of product recalls, and builds consistent brand strength, provides better inventory management and reduces product loss.
It also can reduce ingredient costs by transitioning from smaller manually dumped containers to larger bulk material containers such as bulk bags and silos. Vacuum conveying is the only bulk powder handling technology that is “container agnostic” and works with any original ingredient container. PE
David Kennedy is business development manager at VAC-U-MAX.
Nord-Lock created the original wedgelocking technology that secures bolted joints, even when exposed to severe vibration and dynamic loads. It is impossible for our products to loosen unintentionally due to the wedge created underneath the bolt head and nut, thus reducing the risk of production failures or property damage.
www.nord-lock.com
Log on to www.stle.org/ annualmeeting for registration and hotel information.
May 19-23
Minneapolis Convention Center Minneapolis, Minnesota (USA)
Whether you work in the field or lab—in industry, academia or government—STLE’s Annual Meeting has programming designed specifically for you. Please join your peers from around the globe for five unique days of technical training and indus try education that could change your career.
Program Highlights:
• 500 Technical Presentations and Posters
• 13 Lubrication-Specific Education Courses
• Sustainable Power Generation Track including Fossil Fuels, Hydropower, Nuclear, Solar and Wind
• Discussion Round Tables – An Idea Exchange Event
• Electric Vehicles Track and Course
• Trade Show
• Commercial Marketing Forum
• Business Networking
Joe Wagner, Red Lion, Sacramento
For data to have real value to today’s automated manufacturing plants, industrial networks need critical tools to access and deliver the data to critical operational and analytical platforms.
• Understand how digital transformation helps manufacturers realize the value of their industrial data.
• Learn how information technology and operational technology (IT/ OT) convergence helps companies better manage their data.
he promise of Industry 4.0 is rapidly being realized across many manufacturing segments. A wide range of sensors, smart components and advanced automation drives and controls are routinely integrated into production machines and processes, furthering the growth of automated manufacturing.
These systems are now generating large amounts of industrial data. The challenge for many manufacturing operations invested in this digital technology is how to efficiently access and utilize this data, leveraging its full value with networking systems that are reliable, secure and scalable to meet both current and future needs.
Several key technologies provide the critical building blocks of high-performance industrial
data networks. Systems integrators, original equipment manufacturers (OEMs) and manufacturers are seeking strategies to use these tools to gain more complete access and control of companies’ industrial data and bridge existing gaps between information technology (IT) and operational technology (OT) within the manufacturing enterprise. The goal is accessing that data to improve operator performance, plant safety, predictive maintenance processes and manufacturing productivity.
Today’s manufacturing platforms constantly generate mountains of data related to the performance of individual machine components, subsystems and production lines. It’s being generated by sensors, pneumatic valves, control devices, electric drives and other components. The volume of this data constantly grows.
However, in many production environments, the data is isolated. This complicates manufacturers’ efforts to use the data to improve productivity and return on investment (ROI). In many cases, this isolation is unintentional. For example, temperature and valve performance data are fed through input/output (I/O) channels to a machine controller, but may not go any further without manual intervention, limiting its value.
Industrial data is a manufacturer’s most valuable asset. Data’s true value is only realized when it can be easily accessed, aggregated with other machine and line data and analyzed. These “islands of data” exist because many factory automation plants have multiple generations of equipment installed — in
FIGURE 1: Leverage the full value of your industrial data through Red Lion’s product portfolio. Courtesy: Red Lion
FIGURE 2: Platforms such as Red Lion’s FlexEdge provide a versatile and full-featured solution to bridge the worlds of information technology (IT) and operations technology (OT) to realize the total value of a manufacturer’s industrial data more efficiently and completely. Courtesy: Red Lion
some cases, decades-old systems that still provide productive performance.
Incompatible communications protocols are a major reason why full industrial data networking can be so challenging to implement. Many older machines will be using protocols such as Modbus RS-232. At the same time in the same plant, a newer production system added to the line will use more current, open protocols such as OPC UA. To compensate, some companies building out their networks may try to create specialized software patches on a case-by-case basis.
The most effective solution to this challenge is a robust set of protocol conversion capabilities that can be implemented as part of investments in new data access and connectivity systems.
Rise of edge computing systems
Edge computing platforms, sometimes called edge gateways, are playing a fast-growing and critical role in solving the challenges of disconnected islands of data. Edge computing often refers to hardware/software networks and devices located at or near the end user. It enables data access and processing closer to where the data is generated, for faster processing speeds and higher data volumes that supply actionable data in real time.
Edge computing platforms are widely used for critical, real-time protocol conversion to bridge legacy and current generation production systems. Leading providers of these edge platforms are designing them to be powerful networking devices, engineered to supply critical data access and management tasks.
Leading suppliers offer platforms that can simultaneously process up to 20 protocol conversions
‘ Data’s true value is only realized when it can be easily accessed, aggregated with other machine and line data and analyzed. ’
from over 300 supported drivers. These platforms are designed to be all-in-one edge devices that support other critical functions, such as data logging, easy access to MQTT-based cloud servers and remote access.
Edge systems are being offered by many different technology suppliers, so picking the right one calls for careful assessments. In some operations, manufacturers are reluctant to invest in edge platform technology out of concern that implementing these systems will be costly and time-consuming.
Look for systems that feature user-friendly software and feature efficient, drag-and-drop programming platforms that make it easy to set up protocol conversion, cloud connections and data logging features. There also are advantages to utilizing scalable platforms. For example, one leading platform can serve as a protocol converter, a networking gateway or an automation controller via software upgrades.
FIGURE 3: Red Lion’s N-Tron series NT5000 switches are designed to keep your network connected, protected and provide ease of use, security and reliability today’s manufacturers and industrial operations need. Courtesy: Red Lion
It’s also important to weigh potential yearly software fees and costs for external support services. Costs also could escalate beyond established budget parameters unless properly accounted for when purchasing multiple systems to upgrade networks.
Digital transformation insights
uDigital transformation is providing manufacturers with unprecedented amounts of data related to production system performance; however, many older manufacturing sites use platforms that keep the information siloed and separate from other systems.
u A new generation of scalable edge computing platforms is providing a critical solution to this challenge, incorporating key capabilities such as robust protocol conversion libraries and user-friendly programming interfaces that make it easier to build bridges between those data islands.
uImproving industrial data networking capabilities can also help manufacturers more fully and efficiently integrate the worlds of information technology and operational technology (IT/OT).
In many cases, today’s automated manufacturers are multi-location operations, with multiple plants situated across the globe. To be competitive and productive, they need to operate as fully integrated enterprises. This means eliminating data communications barriers between facilities and leveraging cloud-based analytical tools.
Along with edge computing platforms, a new generation of remote access systems is now being launched to meet these needs. These systems provide a dedicated platform to advance remote system monitoring, making it possible to remotely access and interact with production systems in a secure and reliable way from anywhere in the world.
Just as legacy production tools in a plant can become islands of industrial data without effective protocol conversion capabilities, geographically separated plants can also become islands. With one remote access device, users can access multiple other connected network devices and obtain realtime insights and comparisons about how similar production systems and plants are performing. These devices are useful as more multi-location companies use cloud-based analytical tools to conduct deep dives into their industrial data, extract
trends, modify production or supply chain processes, improve enterprise-wide predictive maintenance programs and guide long-term planning. It is impossible to carry out these kinds of high-level analysis without having robust remote access to help ensure real-time data is accurate and current.
Cloud-based data management and analysis depend on secure and efficient data communications from the plant to the cloud. One emerging technology in plant automation that is shaping the future of manufacturing is the message queuing telemetry transport (MQTT) protocol. MQTT was designed for connections with devices in remote locations with resource constraints or limited bandwidth, making it very lightweight and efficient at moving data to and from a data broker (either locally or in the cloud).
MQTT is capable of “report by exception,” which means data is only transmitted when it has changed. This feature can provide significant bandwidth savings for both internal and external networks. Specifically configured topics can be stored by the database during a network outage and forwarded to users once reconnected, which guarantees delivery of messages about critical topics. MQTT is not necessarily “new” but is still new to the world of manufacturing with many companies starting to adopt this powerful technology. Automation companies seeking to bridge the remote data islands between their production facilities will benefit from selecting edge computing platforms that support MQTT.
Connecting industrial data with enterprise-level analytical platforms is crucial to gaining deep insights into automation system efficiency and performance. However, that data has equal value (in some cases greater value) for operators and managers on the factory floor.
Actionable data needs to be presented in real time to help operators visualize the information they need to maximize productivity and throughput. The latest generation of human-machine interfaces (HMIs) and operator panels are designed to deliver that data in clear and compelling formats. They incorporate features that let them integrate data across multiple devices and, in conjunction with edge computing platforms, acquire and display
data that has been converted from multiple legacy protocols.
Newer generation panel meters feature large, easy-to-read displays that include a broad range of user-selectable graphics and intuitive screen libraries that are simple to configure and customize to specific plant and production line requirements.
With this new generation of visualization technology, operators and line personnel are able to respond to issues faster, process critical information immediately while having one person monitor multiple machines and processes. These tools let operators see more than just information. They also see what the information means and are able to react faster with the right steps.
One of the biggest challenges factory automation companies face to leverage their industrial data is finding smarter ways to integrate the worlds of IT and OT. These two worlds have, until recently, functioned independent of each other.
OT’s goal is keeping the plant running smoothly while IT manages all the business applications within the enterprise. However, as digital transformation continues evolving in factory automation plants, these two worlds are uniting.
Successful IT and OT convergence depends on enterprise connectivity solutions between the systems that create the data and the users that consume the data. In order to extract any actionable insights from this OT manufacturing data, it needs to be packaged in an interchangeable and flexible format that can be shared between IT and OT applications.
This is one of the key capabilities that edge computing platforms are providing. Software that collects, organizes and contextualizes OT data — and then makes it available to higher-level IT applications and databases — can unlock actionable plant- and enterprise-level insights to guide critical decisions about ways to improve manufacturing processes, increase energy efficiency, reduce machine downtime and provide a more flexible and productive manufacturing enterprise.
This data exchange between IT and OT also needs to be as secure as possible. Hackers and ransomware criminals will try and target industrial
‘ One of the biggest challenges factory automation companies face to leverage their industrial data is finding smarter ways to integrate the worlds of IT and OT. ’
systems for vulnerabilities so they can access enterprise IT networks through OT systems. It is critical to select edge computing platforms with top-ofthe-line security features, including a stateful firewall, access control list capabilities, packet filtering and fully secured virtual private network (VPN) connections.
These edge devices deliver valuable, long-term insights into plant floor operations. With the data collected from OT, operations can transition to proactive and develop predictive and prescriptive maintenance strategies.
FIGURE 4: The latest generation of HMIs and operator panels incorporate features that let them integrate data across multiple devices and, in conjunction with edge computing platforms, acquire and display data that has been converted from multiple legacy protocols. Courtesy: Red Lion
‘ Industrial data is a company’s most valuable and useful asset. ’
For example, these devices can automatically alert operators to any changes or events that could lead to a machine shutdown, allowing them to stay ahead of — and avoid — costly production issues. Finally, thanks to powerful remote access capabilities, users from anywhere in the world can add alarms or improve logic and data collection processes or even monitor traffic on the OT network.
Digital transformation has woven a wide range of data-generating components and systems into automated manufacturing systems. Many manufacturers continue to struggle with accessing that data, particularly from older legacy equipment.
Sophisticated edge computing, remote access systems and smart visualization systems can provide solutions to these challenges, bridging per-
sistent “data islands” so that each company’s most valuable resource — its industrial data — can be accessed, connected, visualized and analyzed to help drive operational improvements and longterm decision-making.
Finding and implementing the right technology for each plant and manufacturer can be challenging. Today’s leading industrial data networking suppliers are experienced at analyzing each plant’s unique infrastructure and a company’s data needs. They can apply their expertise to develop strategies to meet those needs, based on an in-depth appreciation of where data is isolated, as well as insights into future needs as companies grow and evolve.
Industrial data is a company’s most valuable and useful asset. The right technologies, combined with smart approaches for using those technologies to improve day-to-day operations and long-term business strategies, can play a critical role in helping realize the full potential of digital transformation in factory automation. PE
Joe Wagner is a field application engineer for Red Lion.
Control room environments put incredible stress on the equipment and employees in them. To truly satisfy today’s heightened ergonomic standards, console design has experienced a dramatic shift to deliver solutions that are smaller, with improved functionality and more appeal than ever before. Current console design is done with a more comprehensive, top-down approach to control room planning, examining every element of the console itself, as well as the overall layout of the room.
Control room planners are now incorporating every aspect of human, machine and environment interaction, from monitor tilt and indirect lighting to air temperature and movement, to create the optimal working conditions and comfort level.
Control room design considerations include:
• Overall room architecture which includes room size and layout, shape, materials used, window placement and aesthetics.
• Technical furniture consoles and general functionality.
• Equipment and technology such as monitors.
• Environmental factors such as lighting, sound and air quality.
Since the control room acts as a person’s “eyes and ears,” the design of it is extremely important. When designing a control room, it’s critical to consider all factors, for example, equipment selection, operating practices, working environments and furniture choices. In addition to the design of a workstation, operators within the control room must be considered. The overall system will fail if operators are overloaded, undertaking tasks for which they are poorly trained or straining to read displays that are illegible. It is necessary to identify the limitations of the operator to minimize potential mismatches between user capabilities and system demands.
Download the paper at: https://tinyurl.com/4ypxaa5t
Don Congdon, SEW-EURODRIVE, Wellford, South Carolina
Selecting a drive, whether for a new application or to replace an existing one, doesn’t have to be a traumatic experience
If an electrically powered industrial machine moves, chances are that a drive — an electronically controlled gearmotor — orchestrates that motion. While ordinary gearmotors have moved industry for more than a century, inexpensive electronic drives have been mainstream technology for just a few decades. Consequently, plant engineers and maintenance personnel may feel uncomfortable about selecting a drive. Traditionally, drive manufacturers guided this process through their sales engineers, but many now offer online selection tools or smartphone apps as an alternative. While these certainly make the selection process more convenient, they can be daunting to use correctly.
Happily, there’s a simple solution to this problem: Ask the right questions before sitting down to the selection tool. Thoughtfully defining the problem and organizing the application’s requirements paves the way to a smooth and successful selection experience.
The drive train contains everything that powers the application, including the drive itself. The drive (see Figure 1) has three core components: a gearbox, an electric motor and a variable frequency drive (VFD). It may connect directly to the application or it may deliver power through additional transmission elements, such as a belt, chain or spindle. In either case, the drive must have appropriate coupling and mounting devices. These include flexible couplings, flanges, feet or torque arms.
The motor may require a brake, either to stop the load or hold it in place. If the application requires precise speed control or accurate positioning, a motor encoder will be necessary. When a programmable logic controller (PLC) or other industrial controller manages the application, the VFD will probably need a suitable fieldbus interface or some extra inputs and outputs.
The questions you’ll be asking define the drive. They flesh out the main components and tease out the specialized accessories required. The questions broadly divide the drive into its electromechanical and electronic components.
Begin by identifying the application’s motion.
Is it rotary or linear? With linear motion, is it horizontal, vertical or angled? Vertical and angled applications usually require a brake, while horizontal ones may or may not. Be sure to identify the motion’s duty cycle too. Continuous duty applications, like simple conveyors or a blower, can work well with an ordinary alternating current induction motor. Cyclic applications performing repetitive sequences, such as packaging machines, may benefit from a more dynamic permanent magnet synchronous motor.
While you’re thinking about the application’s motion, identify the expected loads. Besides their magnitude, also determine whether they’re predominantly static or dynamic. Sizing a drive for an application with relatively static loads is simple. If the load varies widely or can change abruptly, the drive will need a larger service factor.
Be sure to identify the application’s acceleration requirements too. In cycling applications, the motor must deliver sufficient torque to accelerate the load within the time constraints. Permanent magnet synchronous motors can handle aggressive acceleration better than ordinary induction motors. Determine the application’s speed, torque and horsepower requirements. These help size the motor and gearbox. The speed and torque requirements also determine the appropriate gearbox ratio. Be sure to identify how the drive will connect to the application. List appropriate details like shaft diameter, flange and feet requirements and coupling type. Finally, if the application needs a brake, identify the required braking torque.
Application efficiency has progressively become more important in recent years due to rising energy costs and legislation mandating efficient motors. Questions that you’ve already answered may steer the selection tool toward a particular motor efficiency rating.
For example, a continuous duty application requires a premium efficiency (IE3) motor. You can improve efficiency even further by requesting a particular gearbox style and mounting position. Gearboxes based on helical or bevel gears tend to be much more efficient than those containing worm gears, so they’re preferable when efficiency is paramount.
Similarly, the gearbox mounting position influences efficiency since position determines how much oil the housing must contain to keep the gear stages lubricated. Vertical mounting positions
often require more lubricant, which leads to higher churning losses as the gears plow through the oil. Whenever possible, select a mounting position that requires the least lubricant. Every manufacturer has its own mounting position identification scheme (see Figure 2). Be sure that you understand it, so you can correctly specify the gearbox mounting position.
You’re past the most difficult electromechanical questions. Those that remain help identify additional factors needed to ensure a good match between the drive and the application. Begin by describing the application’s operating environment. Is it indoors or outdoors? Clean or dirty? Wet or dry? Are there harsh or corrosive chemicals involved? Will the drive require regular wash-down?
The answers to these questions determine the drive’s materials, protective coatings, seals and cabling. A drive operating in a poultry processing plant, for example, requires multiple wash-downs per day with hot water and caustic cleaning agents. Ordinary protective coatings won’t survive these conditions for very long. A stainless steel drive with potted motor windings and conduit box connections is a much better choice.
FIGURE 2: Gearbox mounting position identifiers vary among manufacturers. This is SEW-EURODRIVE’s system. Courtesy: SEWEURODRIVE
FIGURE 3: Control cabinet (left) and decentralized (right) variable frequency drives perform the same task but in completely different ways. Courtesy: SEW-EURODRIVE
On the other hand, the environment can be dry but still very harsh. Drives powering ore or rock crushing machines must endure heavy dust and abrasive grit. These will probably require multiple shaft seals or ones specifically designed to keep abrasives out. The drive may also need bearing relubrication fittings to make regular grease changes simpler.
Identify the application’s expected temperature range. Is it unusually hot or cold? Temperature affects lubricant choices. Mineral oils and greases perform well at everyday temperatures, whereas specialized synthetics are better choices for hot and cold extremes. The gearbox and motor may require auxiliary heat in a cold environment or more aggressive cooling in a hot one. While you’re thinking about lubricants, remember that food processing and pharmaceutical machines often need foodgrade lubricants.
ing questions help select the VFD and its accessories. These may be unfamiliar territory if you’ve not worked with VFDs before. While all VFDs do much the same thing — control the motor — they vary widely in their features and intended applications. Again, asking the right questions will help you decide which one is right for you.
You’ve already answered an electromechanical question that is equally important for selecting the VFD — the application’s horsepower requirement. Additionally, determine the available power supply voltage and phase (single- or three-phase). These answers size the VFD and identify possible models. In most cases, a drive manufacturer will offer several VFDs that will satisfy your application’s basic electrical requirements. Listing additional application requirements will help you choose from among these.
ing
Begin by identifying the application’s operating mode — whether it’s speed-, position- or torque-based. Speed-based applications are the simplest, so almost any VFD can handle them capably. Do determine the accura-
4: A highly efficient electronic gearmotor integrating a motor, a helical-bevel gearbox and a variable frequency drive. Courtesy: SEW-EURODRIVE
cy required, however. Entry-level VFDs can handle applications with modest requirements — fans, pumps and blowers, for example. Applications requiring higher accuracy must use a VFD that supports closed-loop control via a motor encoder. While many VFDs can operate in closed-loop mode, not all come with built-in encoder interfaces. Those that don’t will require an add-on interface board. This must match the motor encoder’s communications standard.
electronics questions
At this point, you’ve asked enough questions to specify the motor and gearbox. The remain-
By their very nature, positioning applications require a more advanced VFD. It must run the motor at a specific speed while monitoring one or more encoders to determine the application’s position. Upon reaching the specified position, it must stop the motor cleanly and accurately. If your application requires positioning, determine its type (linear or angular) and the required accuracy. These answers will also influence the encoder selec-
tion. Precise positioning will require an expensive, high-resolution encoder, while basic positioning can get by with a more economical choice.
Applications requiring torque-based control are the least common, so not all VFDs support this mode. They require the VFD to maintain a specific tension on the load by adjusting the driving torque. A wire winder is an example, as is the paper feed system in a web printing press. In each case, the VFD monitors the tension on the wire or paper with a sensor, such as a dancer potentiometer. The VFD uses this feedback to generate the torque required to maintain the target tension. If your application is torque-based, be sure the VFD supports this mode and can interface with the required sensors.
For the final core electronics question, determine how the VFD will integrate into the application. Many VFD manufacturers offer their products in two styles: control cabinet and decentralized (see Figure 3). A control cabinet VFD, as its name implies, lives in an electronics cabinet. Wires enter and exit the cabinet, connecting power, the motor and any sensors to the VFD. The cabinet protects the VFD from the environment, especially important when operating under harsh conditions.
Decentralized VFDs approach control differently. They mount either on the motor itself or very close to it. Because they’re exposed to the application’s operating environment, decentralized VFDs usually have relatively high ingress protection (IP) ratings, such as IP66 or higher. A decentralized VFD integrates more seamlessly into the application and typically requires less wiring because it mounts very close to the motor.
Decentralized VFDs are becoming increasingly popular in many industries. Some drive manufacturers even offer “electronic gearmotors” — an all-in-one gearbox, motor and VFD (see Figure 4). These offer an especially elegant solution to many drive challenges. As a bonus, some are exceptionally efficient because they combine a super premium efficiency (IE4) motor with an efficient gearbox and VFD.
Once you’ve identified the core electronics requirements, ask questions that will reveal special features affecting the VFD. For example, many
applications include controls or sensors that the VFD must monitor. These may be digital devices like toggle switches, pushbuttons, limit switches or a referencing cam. Alternatively, they may be analog devices, like temperature sensors, a speed-control potentiometer or a voltage that represents a process variable. Most VFDs include at least a few digital inputs and outputs, but not all support analog signals. In some cases, the VFD may require an expansion card to augment its built-in inputs and outputs.
Finally, consider the control method that the application will use to manage the VFD. Simple applications like fans and pumps may rely on the VFD’s front panel for control and status display. More sophisticated applications might operate the VFD in terminal control (binary) mode via switches, a potentiometer and digital indicators.
The most sophisticated applications use a PLC or similar industrial controller to manage the VFD. These usually communicate with the VFD over a fieldbus — a robust industrial network. Fieldbus control provides maximum flexibility and sophistication but adds an extra layer of complexity. If the application requires fieldbus control, you’ll need to identify the controller brand and model, as well as the fieldbus standard it uses.
Newer controllers use Ethernet-based fieldbuses such as EtherNet/IP, Modbus TCP or PROFINET. Older controllers use legacy standards such as PROFIBUS or DeviceNet. Most VFD manufacturers support multiple fieldbus standards. The VFD may have a built-in fieldbus interface or may require an add-in card.
At this point, you’ve gathered everything necessary to use the drive manufacturer’s selection tool. Fire it up and answer its questions, supplying the information that you’ve gathered. You’ll discover that thinking things through in advance will give you confidence as you work your way through the selection process, as well as afterward when the tool generates its recommendations. Far from being a worrisome experience, drive selection will become a routine task that gives plenty of satisfaction. PE
Don Congdon is a corporate trainer at SEW-EURODRIVE.
‘If your application is torque-based, be sure the VFD supports this mode and can interface with the required sensors.’
Drive selection insights
uThis article outlines the questions you should ask yourself as you prepare to use a drive manufacturer’s selection tool.
uThe key to successfully selecting the correct drive lies in asking a logical sequence of thoughtful questions.
COMPRESSED AIR
There is more to an efficient compressed air system than the compressor itself. Piping, valves and fittings all play an important role in the overall health and efficiency of a compressed air system.
Alot of time is spent sourcing and properly installing the right air compressor for a facility, setting the maintenance schedule and working out the intervals for regular oil sampling per the original equipment manufacturer’s (OEM’s) recommended service intervals.
However, there are other often overlooked components in an optimized compressed air system that are critical to helping get the most out of the compressed air system: Pipes, valves and fittings. If one part of the compressor system’s supporting components isn’t installed, operating or designed correctly, there is a major risk of lowered efficiency or, in the worst-case scenario, a shutdown.
Pipes are the conduits that carry the compressed air to the process once it leaves the compressor. All compressors come with a discharge pipe connection sized by the manufacturer to have the proper and minimal pressure drop for the best compressor operation. Added to this connection is a manual (or automatic) shut-off valve. This disconnects the compressor from the compressed air system in times of maintenance.
The system piping to the plant after the shut-off valve, needs to be at least the size of the discharge connection at the compressor. The size of the pipe at the discharge of the compressor should never be reduced. Increasing the pipe size, however, is often beneficial to a compressed air system from a control reliability standpoint. The piping should also have the least number of 90-degree elbows as possible. In a good installation, sweeping piping radius bends are the best solution. This helps reduce the pressure drop every 90-degree elbow affords. As the piping connects to the main header, it is always good practice to connect the air at the top of the main header. If this is not done, then the pipe com-
ing from the compressor can act as a “drip leg” and allow condensation to drain into the compressor.
In terms of piping materials, there are several options. Each comes with their own advantages and disadvantages. A compressed air specialist can help determine which type works for the specific application.
Aluminum piping is often used because it is lightweight, non-corrosive and easy to work with. Galvanized piping is sometimes used but is heavy and challenging to fit. Copper piping is also used but can be expensive. Older systems often have iron pipes which should be replaced. Over time, the residual water from the compressed air system can react with the iron pipes, causing a buildup of corrosion and reducing air flow.
In addition to the shut-off valve, a 3-valve bypass should be installed around each added and maintained piece of equipment, such as filters and dryers in the compressed air system. At some point, the in-line filters will need to be changed and maintenance will need to be performed. Another good practice to follow is when the piping contractor is onsite, have the installer add a pipe with a ball valve before the filters and dryer somewhere near the compressor room or penetrating an outside wall. At times, the compressor will need maintenance and to be shut down.
‘ Pipes are the conduits that carry the compressed air to the process once it leaves the compressor. ’
This additional connection allows the customer to hook up a rental compressor so maintenance can be completed without interrupting the air flow. This helps prevent unplanned downtime due to emergency maintenance situations.
Quality air compressors are designed with safety in mind. For the most part, users normally do not have to worry about a safety issue arising. In fact, to prevent a potential issue, air compressors come equipped with an air pressure relief valve (PRV), sometimes called a safety relief valve, which is designed to work if other safety features fail.
The pressure relief valve protects the compressor component it is attached to from being exposed to a pressure above its rated maximum operating pressure. This rating, called the maximum working pressure (MWP), is the pressure at which the sump has been certified to continuously operate safely. When a compressor is running at or below its maximum working pressure — when it’s running “normally” — the relief valve doesn’t do anything. However, when the air pressure inside a compressor exceeds its MWP, the pressure relief valve will activate to “blow off” the excessive pressure within the compressor. Without a relief valve, the storage tank could rupture from the excessive pressure, damaging the compressor, other property near it, and maybe causing injuries (or worse) to anyone standing nearby.
Under normal circumstances, the air pressure in a compressor is controlled by a pressure switch in an electro/mechanical control system or, in the case of an electronic controller, a pressure transducer and controller settings. When the cut-out
Continued on page 38
• Types of piping and the role piping plays in a compressed air system.
• Understand how bypass valves help with maintenance needs to avoid downtime. Pressure relief valves keep the compressor, storage tanks and other components from being damaged should an error occur.
• The impact air leaks have on the efficiency of a compressed air system (and the corresponding costs) and how to best remediate any leaks or issues.
a few of our many abilitites
We constantly work to ensure both the availability of raw material and manufacturing capacity to provide our distributors with critical products needed.
FIGURE 3: Compressed air system air leak auditing
should be an on-going maintenance task. A good practice is to check the entire system annually. Courtesy: Hitachi Global Air Power
Continued from page 35
set pressure for the pressure switch is reached, the compressor will stop compressing air until the cutin set pressure is reached at which time it will start compressing air again.
If the pressure switch fails, the compressor would not be able to start compressing air again, or potentially worse, not be able to stop. Most compressors also have a high-pressure safety switch that should stop the compressor if the pressure exceeds the unload set point.
A pressure relief valve is a straightforward safety backup to the pressure switch and high-pressure switch, or the controller set points, should any of these components fail with the compressor running. The safety relief valve is set above the high-pressure safety switch and at or below the vessel’s maximum operating pressure. Inside the valve
‘ And the leak doesn’t have to be large to start dragging down efficiency levels. ’
is a spring, and the pressure created by compressing the spring keeps the valve closed under normal operating conditions. However, as the air pressure increases in pressure vessels (like the storage tank), it may exceed the rated pressure of the relief valve, causing the relief valve to open and the excess pressure to be blown off to the atmosphere.
What happens when the pressure relief valve fails depends on whether it fails with the valve open, or the valve closed? There are two key scenarios to consider.
1. Failing with the valve open
If the pressure relief valve fails to open, air will keep venting to the atmosphere, preventing the air stream from becoming fully pressurized. The compressor should be shut down and the relief valve replaced before the compressor is restarted. The open relief valve may cause a loss of production and possible danger to personnel as a result of the flow of high-pressure air potentially with flying debris. The open valve can also produce an unsafe sound level.
2. Failing with the valve closed
A pressure relief valve failing closed presents a potentially more dangerous situation. As noted earlier, the relief valve exists to allow excessive pressure to be “blown off” so the air pressure inside the compressor’s pressure vessels don’t exceed their rated specifications. If the valve fails closed, it is a malfunction. It is not a setting or normal mode of operation and this pressure venting can’t happen. Unless compressed air demand matches the compressed air supply, the pressure inside the compressor will continue to build. Eventually, the pressure increase would cause the storage tank to rupture, damaging the compressor and causing additional damage and injury to property and people nearby.
If the pressure relief valve is opening and whether that is because of excessive pressure in the compressor or because the valve is failing, users should have an air compressor service technician inspect it before running it again for two reasons:
1. The certified technician can determine whether the valve opened due to a failing relief valve or excessive compressors pressure and perform any needed maintenance or service to get the compressor safely running again.
2. Regardless of why the pressure relief valve opened, replacing it may be recommended to ensure safe compressor operation, depending on the valve manufacturer.
Running the compressor after the relief valve has opened can put property at risk and workers in danger.
If pipes are leaky, the system is losing air and efficiency. Checking for leaks in a compressed air system should be an on-going activity. One approach to managing leaks is to segment the plant into 10 to 12 relatively equal areas, based on the distribution of production equipment using the compressed air power. Assigning one segment per month for a leak audit allows the entire plant to be audited each year.
And the leak doesn’t have to be large to start dragging down efficiency levels. Even small leaks can become expensive. By some reports, up to a third of compressed air is lost due to leaks and the corresponding elevated system pressure to compensate for that loss.
If an industrial user has 200 HP online (approximately 1,000 acfm capacity), the leaks and inappropriate uses of compressed air consume a significant quantity of electrical power, which add to the cost of electrical power for the plant and unnecessarily contribute to carbon emissions.
Piping leaks usually happen over time due to vibrations, hose and tubing degradation and failed compression fittings. To root out the sources of leaks, most OEMs recommend a leak audit. These audits often find inappropriate uses and loss of compressed air, so the exercise is absolutely worth the effort.
TABLE 1: Impact of leaks and inappropriate uses of compressed air for an industrial user with system specific power of 20kW/100 cfm, paying $0.0771/kW-hr operating 8,000 hours/year. Tons of CO2/year based on coal-fired utility. Courtesy: Hitachi Global Air Power
Most air auditors use an ultrasonic leak detector since most leaks are small and are not audible to the human ear, particularly in a noisy production environment.
A best practice is to document each leak when it is identified. Many ultrasonic leak detectors include cameras so the leak can be photographed allowing the user to include a description such as the location in the plant. And, along with documenting the leak information, attaching a two-part tag to the leak makes locating the leak for repair easy for the maintenance team.
Logging the intensity of the leak is also a good practice to follow. The leak intensity can be used to estimate the power cost of the leak and allows the maintenance team to determine if a leak is worth fixing. For example, the packing gland and seat in a valve are found to be leaking, but the leak cannot be repaired without replacing the valve. The cost of the valve, plus the labor associated with the repair, could cause the repair to be more expensive to fix than letting the leak continue.
While an air compressor is the largest and most important part of an efficient compressed air system, the piping, valves and fittings that carry the air from the compressor can have a huge impact on the cost to run the system and the operation’s safety.
Utilizing the right parts and connectors and remembering to regularly check these often-overlooked components can mean significate savings and a more optimized compressed air system. PE
Peter Modrow is senior product manager at Hitachi Global Air Power. Brian Mann is product manager, service plans & warranty at Hitachi Global Air Power.
uNeglecting the maintenance of supporting components like pipes, valves, and fittings in a compressed air system risks efficiency loss and potential shutdowns.
uSmall overlooked leaks in pipes and fittings significantly reduce efficiency, leading to increased power costs and unnecessary carbon emissions over time.
Christine Tarlecki, ThermOmegaTech, Warminster, Pa.
Choosing the right freeze protection can prevent damage from water supply disruptions, which can have adverse effects on a plant facility.
Maintaining water-bearing equipment in a facility can be tricky, especially in wintertime. Ensuring piping, safety showers, condensate systems and pumps are kept from freezing conditions comes with several challenges. When these systems are exposed to freezing temperatures, they become vulnerable to damage and water supply disruptions, which cause hazardous working conditions. Freeze protection is critical in applications such as:
• Piping, valves and fittings
• Pumps
• Filtration systems
• Holding tanks
• Condensate systems
• Fire lines
• Freeze-sensitive equipment
• Identify freezevulnerable areas, assessing criticality, climate severity for tailored freeze protection strategies in facilities.
• ifferentiate between insulation, electric tracing, and valve-based methods for effective freeze safeguarding systems.
• Evaluate the effectiveness and cost efficiency of Thermostatic Freeze Protection Valves for diverse industrial applications.
• Backup protection on traced systems/ equipment.
A common misconception is the system will continue functioning when water is at freezing temperatures as long as the water is "moving," which is untrue. Water expands and freezes at 32°F, regardless of flow rate and pipes can burst.
Factors to consider are the location of the machinery, temperature variations, the presence of outdoor or exposed sections and the criticality of the water supply. Assessing the facility's specific machinery and water systems is vital to
determining the most appropriate freeze protection methods. Different areas of the facility may require different strategies or multiple approaches. The severity of the winter climate should also be considered.
There are various ways to protect water lines:
1. Pipe insulation: Pipe insulation is a commonly used method to help protect pipes from freezing by wrapping the pipes with insulating material, such as foam or fiberglass, to provide a barrier against the cold. Insulation reduces heat transfer and helps maintain a more stable temperature within the pipes. This is good practice but is not always enough protection to prevent freezing in extreme weather conditions.
2. Electric heat tracing: This process installs electric heating cables along the length of the pipes. These cables generate heat that keeps the pipes warm, preventing freezing. This method can be expensive and vulnerable to power outages.
3. Pipe taping: Pipe taping involves wrapping the pipes with specially designed heat tape or heating cables, generating heat to keep the pipes warm. Pipe taping is suitable for smaller pipes or localized freezing areas.
4. Pipe-heating cable systems: Pipe-heating cable systems require electricity to function and consist of versatile, self-regulating cables that automatically adjust their heat output based on the surrounding temperature. The cables are installed on the pipes and provide constant heat to allevi-
‘Once freeze protection is in place, facility maintenance personnel have a better chance of working safely and protecting their equipment from freeze damage.’
ate freezing. In very cold conditions, pipe-heating cable systems could struggle to keep up with the demand for heat, especially if the system is not designed for extremely low temperatures.
5. Backup generators: In the case of power outages, backup generators can provide additional protection for freeze-prone areas. They ensure essential equipment, such as heat tracing systems or pipe-heating cables, continues functioning even during power failures.
6. Space heaters: Using space heaters to warm the air around the pipes can provide temporary freeze protection. This method is suitable for small, localized areas or temporary setups.
7. Manual valves: By providing a means to control water flow in a piping system, these valves are manually operated, allowing users to open, close or partially restrict the water flow.
8. Thermostatic freeze protection valves: Freeze protection valves are a specialized type of valve that prevents freezing in piping systems. These valves automatically open when the temperature drops below a certain set point, allowing a controlled water flow to prevent freezing. When the temperature rises, the valves close.
Low temperatures can turn worst-case scenarios into reality without adequate protection. Upholding diligent maintenance and awareness during cold weather can avert expensive and inconvenient repercussions from frozen pipes. Even heat-traced systems risk freezing in the event of an electric tracing malfunction.
Once freeze protection is in place, facility maintenance personnel have a better chance of working safely and protecting their equipment from freeze damage.
Manual valves are an easy solution for freeze protection to implement, but this introduces the risk of human error (forgetting to turn the valves on or off). Choosing a self-actuating, non-electric freeze protection method can offer superior protection for water systems compared to other techniques.
Thermostatic freeze protection valves prevent water from freezing within pipes and systems by monitoring temperatures and adjusting flow. Utilizing thermal actuator technology, they sense the water or air temperature and will open to bleed off the cold water until it reaches a safe level. Because the valve functions without power, it is ideal for explosion-proof and remote areas.
Pipes and pumps insights
uProtecting waterbearing equipment in winter involves assessing risks, employing insulation, heat tracing, and thermostatic valves for safeguarding.
uEmploying diverse freeze protection methods — from insulation to specialized valves — mitigates freezing risks and ensures uninterrupted facility operations.
‘
Different areas of the facility may require different strategies or multiple approaches.
’
Freeze protection valves are useful in intermittent water flow or when power is not readily available for heat tracing systems. They are used in industrial settings such as oil refineries, chemical terminals and processing facilities to forestall freezing within their systems.
Water line thermostatic freeze protection valves use a specifically designed thermostatic wax actuator technology with an "install it and forget it" approach, simplifying the management of freeze protection.
A HAT/FP valve allows flow when the thermostatic actuator senses 35°F and will remain open as long as the discharge water temperature is below 40°F. Installed in the standard flow direction, the actuator will sense the ambient temperature and open to initiate flow, then respond to water temperature.
Installed in the reverse flow direction, the wax actuator will always sense and respond to the
water temperature to control the flow. Once the water temperature is above the freeze danger zone, the valve will modulate closed to conserve water.
The main benefit is cost savings; once installed, they require no additional power source and only activate when the water temperature is near freezing. Thermostatic freeze protection valves operate independently. They also help prevent frozen piping with the facility's systems and offer the convenience of a low-maintenance, long-lasting solution, protecting against freeze damage for all applications.
"If systems are left unprotected, damage in piping can occur, so safeguarding your machinery with freeze protection valves offers a sense of security, knowing your systems are protected and won't freeze due to unpredictable weather or a sudden cold snap," said Tim McCollum, ThermOmegaTech OEM sales manager. PE
Christine Tarlecki is marketing coordinator at ThermOmegaTech.
sales@procoproducts.com www.procoproducts.com
Shaji Arumpanayil, Product Manager, Swagelok Co., Solon, Ohio
Proper design and installation of relief valves can keep industrial fluid systems operating efficiently and effectively for years to come
Chemical plants and refineries build extensive networks of small-bore tubing to move industrial fluids throughout their facilities. This web of tubing and pipes brings mission-critical fluids to the areas where they are needed to perform important functions.
Safety threats can unexpectedly occur because of the complexity of these systems, placing an undue burden on plant managers and operators to keep up. Making the right decisions in system design
and component choices upfront can help relieve this burden and make the facility safer for everyone. Additionally, effective system design can avoid unplanned downtime, which can cost up to $100,000 an hour if components in the system fail.
Installing pressure relief valves in high-risk areas of a fluid system will enhance facility safety and prevent unforeseen downtime (see Figure 1). Venting excess pressure prevents blowouts, equipment damage or complete system failure and relief valves play a vital role in maintaining system pressures within acceptable limits.
Safety depends on properly installed relief valves
Set pressures within critical industrial fluid systems can affect the safety and efficiency of a facility.
Objectives Learningu
• Learn the importance of installing safety relief valves in critical areas of a fluid system.
• Review the three most common types of relief valves and how they work.
• Determine where to place relief valves in a system to enhance safety.
uChemical plants and refineries use intricate networks of tubing to transport industrial fluids, presenting safety challenges due to system complexity.
uEffective initial design decisions, including the installation of pressure relief valves, can mitigate safety threats, prevent unplanned downtime and ensure the overall safety of facilities by managing overpressurization risks in fluid systems.
While many chemical plants and refineries employ pressure regulators to manage pressure levels throughout the entire system, they are often not enough. Other fail-safe measures must work in conjunction with system components because unexpected pressure changes can lead to dangerous liquid or gas leaks, which could put employees at risk of exposure.
FIGURE 2: Coordinating with a reliable valve supplier to determine the appropriate relief valves to use for an application and where to install them will help system designers prevent unnecessary downtime and eliminate leaks for safer operations. Courtesy: Swagelok Co.
One such fail-safe strategy is to install relief valves at specific points throughout the system as part of the initial design. Operators can set relief valves to open and release pressure if it exceeds certain parameters. The released pressure can either be captured if it is potentially toxic or allowed to dissipate into the air if it is not.
Reliable relief valves are essential for keeping industrial fluid systems operating at peak performance. Finding a supplier that produces high-quality components and can commit to servicing them when necessary can prevent unnecessary downtime and eliminate leaks, keeping facilities and employees safe from harm (see Figure 2).
Any fluid system, no matter how well designed, can experience overpressurization, which is why it is important to have relief valves installed as a fail-safe measure. The complexity of fluid systems means there is no single cause of overpressurization.
However, the conditions leading to it can be generally grouped into one of four categories:
• Procedural errors: Because people are responsible for operating chemical fluid systems, the systems themselves are inherently subject to common human error. For example, a technician may have opened the wrong valve in a system, leading to a pressure rise downstream. System conditions may
have been improperly calibrated. The wrong type of pressure regulator may have been installed during routine fluid system maintenance. Robust fluid system training can help prevent these issues from happening, but it is still important to incorporate relief valves in case of operational error.
‘ While
many chemical plants and refineries employ pressure regulators to manage pressure levels throughout the entire system, they are often not enough.
’
• Component wear: Fluid system components naturally wear over time. Particularly in fluid systems that handle aggressive chemicals, corrosion can cause premature wear. In any case, component wear may compromise pressure control, making relief valves a necessity for chemical plant safety.
• Contamination: Pressure regulators can reliably reduce pressure to desired levels, but dirty or otherwise contaminated fluids can compromise their performance. Particulates have the potential to compromise a regulator’s seal, allowing unwanted pressure to creep past the seal, which leads to rises in downstream pressure. Here, a relief valve would be able to vent off that unwanted pressure.
• Loss of power: Some fluid systems may rely on the electronic control of certain components
for operation or pressure control. If a system experiences an unexpected loss of power, compromising the ability of certain components to function as intended, relief valves will help manage any overpressurization that occurs.
Relief valves come in multiple shapes and styles depending on what their purpose is and how they are meant to work. The three most common types of relief valves include:
Proportional relief valves (PRV): PRVs provide overpressure protection with a variety of set pressures available (see Figure 3). They open gradually as the pressure increases and close when system pressure falls below the set pressure, with the resealing pressure always being lower than the set pressure. Consequently, they do not have a capacity rating at a given pressure rise (accumulation) and they are not certified to American Society of Mechanical Engineers or any other codes.
Some system applications require relief valves to meet specific safety codes. The system designer and user must determine when such codes apply and whether these relief valves conform to them. PRVs often come in a variety of set spring pressure ranges with the selected set pressure factory-set, tested, locked and tagged to ensure the desired setting.
Bleed valves: Bleed valves can be used on instrumentation devices such as multivalve manifolds or gauge valves to vent signal line pressure to the atmosphere before removal of an instrument or to assist in calibration of control devices.
When installing a bleed valve, position the vent tube to direct system fluid away from the operator. Always open bleed valves slowly. These valves contain no packing, so some fluid leakage will occur when the valves are opened. Operating personnel must therefore protect themselves from exposure to system fluids.
Purge valves: Purge valves are manual bleed, vent or drain valves. The knurled cap is permanently assembled to the valve body for safety. Onequarter turn with a wrench after finger tightening provides leak-tight closure on first makeup. Snugging with a wrench ensures closure to the rated pressure with subsequent makeups.
For many purge valves, the vent hole rotates with the cap, changing the direction of discharge as the cap is turned. Therefore, operating personnel should pay attention to the direction of the vent to avoid standing in front of any potential discharge. Like bleed valves, purge valves should be opened slowly and may leak fluid, so operators should be aware of these potential hazards and behave accordingly.
Typically, chemical plants and refineries must employ relief valves in particular applications to maintain the overall safety of the employees and the environment, including the following applications:
• When system pressure is high: In fluid system applications that exceed a certain pressure — usually measured in pounds per square inch, or psi — relief valves are an essential safety element that can help prevent potential accidents. Choosing highquality small-bore tube fittings for such applications is a good way to protect against the potential dangers of overpressurization, and relief valves are a good supplemental safety measure for high-pressure applications.
• When applications use toxic fluids or chemicals: In applications in which escaping system media would cause an immediate plant safety threat — toxic or hazardous chemicals, for example — relief valves are an essential safety measure. In the event of overpressurization in these applications, relief valves can be set up to capture vented pressure and media instead of releasing it into the atmosphere. Escaped fluid can then be safely disposed of.
LEARN the STAMPED method, which provides valve selection guidance
Whether you need a relief valve or other type of fluid system valve, a variety of considerations abound when making a selection. You want to get that selection right, as choosing an improper valve could lead to avoidable safety risks, poor performance and even increased downtime (see Figure 4).
A helpful tool when choosing a valve for your system is the STAMPED method, which stands for size, temperature, application, media, pressure, ends (or fittings) and delivery. This method provides a framework to help fluid system designers pick the proper valve and entails:
Size: The size of valve to use is dependent on the required flow rate needed for the system to operate as intended. Choose a valve that makes that rate possible by consulting the manufacturer’s published flow coefficient (Cv). This data shows the relationship between the pressure drop across a valve and the resulting flow rate. A reputable supplier should be able to provide guidance on the right-sized valve for the situation. Some even offer a Cv calculator to help.
Temperature: The temperature at which the valve will be operating is also important to know, as well as whether that temperature will be constant or fluctuate, to ensure compatibility. That includes both the temperature of the media the valve will control as well as the ambient operating temperature of the environment. Temperature fluctuations can cause seals to expand and contract, causing rapid wear that may lead to failures and leaks.
Application: System designers must know the specific function of a valve to make the right selection. In the case of a relief valve, it will need to allow the system to release pressure to avoid overpressurization. Other valves may need to start or stop flow or perhaps regulate flow levels instead. For example, most two-way ball valves only allow for on/off operation, so if the system needs to throttle or regulate flow, a needle or metering valve would be a better choice.
Media: Compatibility with system media and the ambient environment is key for a valve to operate as expected. All materials of construction, including bodies, seats, stem tips and other softer materials, must be compatible since valves are made from a variety of materials. Otherwise, corrosion, embrittlement or cracking may occur.
Pressure: Pressure limitations are determined by the lowest-rated component in a system, with valves being a common factor. It is important for the valve to be compatible with the normal operating pressure — or working pressure — of the system. In addition, system designers need to ensure the system never exceeds the design pressure of the valve, which is its manufacturer-provided maximum pressure limit.
FIGURE 4: When making valve selections, it is important to make the right choice to ensure safety, performance and uptime. Courtesy: Swagelok Co.
FIGURE 5: Choosing the right end connections can help technicians perform easier and speedier installations, while also enhancing leaktight valve performance. Courtesy: Swagelok Co.
End connections: End connections are crucial to how well a valve will resist leaking. They include integral tube fittings, pipe threads, pipe flanges, welded ends and other options. Choosing the appropriate end connections for a valve that meet the pressure, temperature and size of a system will make installations easier and reduce the number of potential leaks (see Figure 5).
Delivery: Once the above factors have been considered, it’s important to ensure you can actually get your valves in hand. Look for suppliers that can source your valves on time, including specialty ones that may require more lead time.
Using the steps outlined in the STAMPED method will help system designers create safe, efficient fluid systems.
‘
By taking all these factors into account,
c hemical plants and refineries can design safer industrial fluid systems from the ground up. ’
• When sensitive equipment is involved: One of the most important roles pressure relief valves can play is helping to protect sensitive analytical equipment from overpressurization. Higher pressures than the equipment is rated for can easily damage expensive systems, including online analyzers. This is especially important because analyzers are deployed to sample fluids directly from your main processes. An optimal regulator should be paired with a properly rated and set relief valve to ensure that pressure is sufficiently reduced from the main process by the time fluids are delivered to the analyzer.
In addition to relief valves, other important factors play significant roles in making a chemical plant or refinery safer. These include avoiding tube fitting intermix, eliminating unnecessary complexity and taking note of specific operational stressors like vibration and heat. By taking all these factors into account, chemical plants and refineries can design safer industrial fluid systems from the ground up.
Choose a supplier that can guide the plant or facility team through the design process with inhouse system design specialists who are familiar with the chemical and refining industries. They should be up to date on the latest developments in safe system design and can provide the proper expertise to allow all systems to perform effectively in any operational environment. PE
Shaji Arumpanayil is a Product Manager for Swagelok Co.
Michael C. Durbin and Rita Kamoutsis | Sherwin-Williams Protective & Marine
Adherence to government standards is critical for product safety, quality and worker well-being. Plant audits, whether conducted internally or by third parties, play a vital role in identifying areas of improvement before regulatory visits. However, navigating the complex regulatory environment amidst audits by agencies like USDA, OSHA and FDA presents ongoing challenges for plant managers.
Coatings professionals offer invaluable expertise in optimizing operational efficiency and safety protocols. They deliver tailored evaluations and recommendations, helping facilities select the right coatings to mitigate risks, enhance safety measures and ensure compliance.
Ahead of audits, proactive repair specifications and collaboration with coatings professionals streamline maintenance programs, minimize stress and pave the way for uninterrupted operations. During audits, coatings professionals assist in identifying safety hazards and ensuring regulatory compliance. By embracing a proactive approach and leveraging partnerships with coatings professionals, plant managers can maintain compliance, avoid penalties, and foster long-term operational efficiency and regulatory success.
Download the paper at: https://tinyurl.com/yc99jbvy
James Nyenhuis, Emerson, Pittsburgh
Many of today’s power generation facilities are at an inflection point. Whether it is a commercial generation plant supplying power across half a state or one within the fence of an industrial manufacturing facility, external forces are exerting pressures that complicate operations.
But while the complications of modern power operations may seem insurmountable, few truly are. A combination of a clear understanding of the challenges of modern power generation management and the strategic implementation of modern automation software can help any organization make the most of what they already have for more efficient and effective operation.
• Understand the current challenges faced by modern power generation facilities, both commercial plants and those integrated within industrial manufacturing facilities.
• Gain insight into the need for modernizing power system operations.
• Acquire knowledge about the benefits of implementing advanced automation and simulation in power facilities.
First and foremost, power facilities are seeing a massive shift in the personnel they employ. Operations teams can no longer rely on the expertise of longtime employees who have worked at the facility since the concrete for the foundation was poured. Those personnel are now retiring in droves and plants are seeing the practical ramifications of their departure. Decades of institutional knowledge disappear with each retirement. Simultaneously, complex operations are being handed over to newer personnel who have limited experience with aging assets and decades-old technologies.
Properly training new staff typically takes two to five years, but today’s plant personnel are commonly staying for only two to three. Often, as soon as a new person knows where all the equipment is and has a handle on the quirks of taking the plant
through intricate operations such as startup and shutdown, they move on and that knowledge is lost once again.
Moreover, even if an organization can retain personnel, they are getting harder to find. Plants need modern technology to attract the most talented personnel of the new digital-born generation, as they expect to work with advanced systems that provide decision support and mobile access.
In tandem with the complexities of a worker shortage, power generation facilities are faced with mature assets needing to operate in ways that do not align with their original operating specifications. When many of today’s plants were designed and commissioned, they were engineered to support a profile of running turbines at full output for as long as possible to maximize their efficiency of power production. The rise of the wholesale power market, coupled with a global push toward more renewable energy generation, has changed this dynamic (see Figure 1).
Modern power generation systems connected to the grid are changing how much and when power is available. Renewable energy sources like solar and wind are changing the game with difficult-to-predict power fluctuations based on changing weather patterns.
To meet demand, thermal and other power plants must ramp their output up and down in response to the variability, causing them to operate away from their most efficient operating point, typically at or close to full output. This results in more complex operations for plant personnel to balance the cost of generating power with varying output and price conditions. If those operations are not performed properly, efficiency is reduced and more wear and tear is encountered on the assets, shortening their life span.
Twenty years ago, plant startups and shutdowns were handled by a deep bench of expert personnel, not only because such operations were more uncommon and required extensive expertise, but also because the control systems did not have the computational horsepower to fully automate coordinated plant process operations. There was not enough memory in the real-time controllers to store the historical data and complex algorithms necessary for advanced process control and automation.
Some organizations ran advanced automation on secondary workstations, but those setups typically required complicated custom engineering. Such solutions were fragile and hard to support, so they were often only suitable for the most confident and well-resourced operations teams.
In contrast, modern advanced control software is designed to simplify this connectivity, empowering teams to leverage the best automation technologies with the control systems they already have in place. Teams might employ Emerson’s Boundless Automation vision of seamlessly integrated data mobility to break away from the complex, custom engineering of the past.
The best advanced control solutions available seamlessly layer sequential automation directly on top of a plant’s existing control architecture, providing teams with the tools they need to easily build institutional knowledge directly into their control systems (see Figure 2).
Not only does this built-in knowledge help operators make better decisions as they guide the plant through changing operational states, it also helps ensure that the plant’s best practices are applied every time, through every stage of a workflow, regardless of who is working in the control room. Operations teams are also linking these advanced control solutions with simulation software to build digital twin replicas of their power operations to test new operating strategies and improve training across the workforce for faster upskilling.
These software solutions are easier to implement than ever before because they are making it possible to seamlessly move information from field to edge to cloud to unlock new advanced control technologies and because successful organizations are implementing them using four proven strategies for improved success.
A team implementing modern advanced control strategies cannot be successful without a good grasp of its starting point. Typically, this starts with an evaluation of two key elements: operator loading and alarm management. Teams should explore and document how many times an operator needs to interact with the control system on an hourly basis and then compare that number against widely recognized standards for best-practice operation.
In addition, the team needs to look at the alarms designed to provide operator awareness. When
FIGURE 1: North American combined cycle gas turbine fleet cycling metrics show an increase in conventional plant starts and stops associated with growing renewable energy penetration and evolving coal unit retirements.
Courtesy: Emerson
considering alarm management, teams should evaluate not only the number of alarms coming in, but also the quality of those alarms. Operators can only process so much information. If the control system is constantly overwhelming them with alarm floods, operations will be far less safe and effective.
FIGURE 2: When embedded into the plant control system, advanced process control reduces variability to deliver better dynamic performance closer to operating limits. Courtesy: Emerson
FIGURE 3: Solar energy penetration is changing traditional operating profiles, calling for more active response to compensate for variable renewable generation during the daytime, along with increasing plant demands at night when solar is not producing and winds typically decrease. Courtesy: Emerson
Fortunately, nearly every control system records alarms and user interactions and then stores that historical data for later access. An experienced automation partner can help the team filter and process that data for clarity into the effectiveness of operator interactions with the control system to build a critical baseline for current operational efficiency.
For example, a large North American power producer recently wanted to centralize operations across its network and recognized it would need to streamline, standardize and automate many parts of its operating procedure. In researching best practices, the team discovered industry studies showing the ideal target to optimize operational decision-making is 6-10 control system interactions per hour.
The power producer’s team partnered with its automation provider to collect historical data and discovered that between changing setpoints and moving operations from automated to manual, their personnel were interacting with the system significantly more — at 5-10 times the ideal limits. Knowing the baseline helped the team develop goals for their advanced automation project because they knew if they could bring operators into the 6-10 interactions per hour range, they would be more successful at managing multiple facilities.
Trying to implement advanced control on top of an unstable automation foundation is a recipe for frustration. After a team has identified its baseline and targeted goals, the next step is to find the parts of the process where the team can true up the base level control strategies.
The need to revisit basic automation strategies is not uncommon. Many plants find that control strategies implemented decades ago were not engineered to today’s best practices or were not as robust as they need to be for operation in the modern industrial manufacturing marketplace. But even optimally engineered plants change over time as their range of supported operations increases. Meeting new goals with aging infrastructure will nearly always require some reconfiguration. Leveraging specific advanced process control techniques for drum level, emissions, steam temperature, unit response and other systems helps optimize control of plants with a more dynamic operating profile.
Additionally, implementing adaptive, advanced software that continuously assesses process performance, identifies degrading conditions and adapts to ever-changing conditions helps increase production and ensures optimal efficiency over a wide range of operating states.
Once the plant has its core automation systems running as expected and in line with best practices to the greatest extent possible, the team can consider adding advanced automation strategies to lock in best practice controls and help operators of any skill level more efficiently and effectively drive their power generation processes. Step-by-step automated operator guidance through normal operations — and process aberrations — helps to ensure procedures are performed the same way consistently, regardless of which shift is on duty.
The best software solutions for sequential automation integrate seamlessly with the control system, so automated operations feel like a normal extension of operational procedures. And even more importantly, they integrate seamlessly with the best modern simulation tools to provide operators with testing and training platforms that look and feel just like the actual plant controls in the control room. Empowered with decision support at every stage of operations and a safe sandbox in which to learn and improve strategies for uncommon operations, operators are elevated to higher-level process managers, more focused on driving continued efficiency and equipment health than on firefighting.
The aforementioned North American power plant looking to improve operations identified a common issue in its operations that, if remedied, could dramatically improve efficiency, safety and uptime. Due to fluctuations on the grid, both from an increase in renewables and from constantly shifting electrical demand, the team had units starting and stopping almost daily to manage the change in load from daytime to nighttime and from on- to off-peak.
When the team needed to reduce load, they would have to stop their gas turbines — large, highly refined pieces of equipment. After the turbine cooled down, the team would have to perform a very complex startup procedure to safely heat the metal up again and get it started (see Figure 3).
4: Integrating operating procedures into a control system using advanced strategies drives operational consistency, resulting in cost savings and a potential return on investment of 1-2 years. Courtesy: Emerson
Not only did the startup and shutdown processes introduce complexity and risk into operations, they also added extra wear and tear on equipment that was designed for continuous operation. By layering automated sequencing technology over their existing automation, the plants were much better equipped to support more cyclical operations. The team gathered data on best practices for the startup and shutdown process and then built those strategies into automated workflows for turbine operation.
‘ Step-by-step automated operator guidance through normal operations — and process aberrations — helps to ensure procedures are performed the same way consistently, regardless of which shift is on duty.’
But even more importantly, they were able to seamlessly connect operational data with real-time digital twin simulation to help identify patterns of operation from a wide range of variables. Using these predictive patterns, the team layered in new automation strategies to more gradually adjust load to meet operational requirements, reducing the number of times operators needed to stop and start equipment.
Few, if any organizations achieve operational excellence by implementing a single change and
Automation insights
uToday's power generation facilities face complex challenges due to external pressures, requiring a strategic approach to modern automation software.
uAdapting to the changing landscape of power system operations is crucial for efficiency and competitiveness, with advanced automation and simulation offering predictive strategies that enhance safety and efficiency, without requiring a complete infrastructure overhaul.
then stopping their improvement program. Once a team sees success with their new automation systems, they will likely want to implement more enhancement. To sustain continuous improvements, it is critical to determine the right metrics to track performance against an original baseline, confirming the value created for the plant with each change. Utilities can get additional support in determining the best metrics to meet their plants’ objectives by working with a trusted partner with decades of global industry and operational experience.
As teams gather metrics and identify success in their key performance indicators, they should not only share those achievements with management — but also with the maintenance, operations and engineering teams to generate buy-in across the organization — as operational excellence requires support from the entire enterprise. Demonstrating success is the fastest way to leverage wins into future projects and more effective personnel (see Figure 4).
Modern power system operations — whether in a power utility or a small plant supporting other industrial manufacturing operations — have changed dramatically, even in just the past 5-10 years. Continuing to run these operations using strategies developed decades ago makes it difficult, if not impossible, to compete in a modern, global economy. Fortunately, most teams can improve operations without a complete rip-and-replace overhaul of their infrastructure.
Modernizing a power facility’s operations with advanced automation and simulation unlocks predictive strategies that keep maintenance and operations teams safer, while increasing their efficiency. And because the key steps to implementing those technologies are process improvements every team should already be considering, there is no reason to avoid starting the journey toward advanced automation. PE
James Nyenhuis is manager of performance consulting for the power industry at Emerson.
The IMO Series Jacketed C324A pumps have a double suction design, essentially making it two pumps operating in parallel. This means the pumps are very compact for their flow range. C324A pumps are especially suitable for higher temperature operation, including the transfer of asphalts, vacuum tower bottoms, and more, as there are no antifriction bearings requiring separate cooling. All of these threescrew pump solutions from IMO feature excellent suction lift, long service life, low horsepower consumption, and high contamination tolerance. These benefits mean less downtime, lower energy costs, and lower total pump life cycle costs for the user. Circor International, www.circor.com
The TIDALFLUX 2300 is an electromagnetic flowmeter with a patented, capacitive level measurement. This meter provides an ideal solution for flow measurement of municipal and industrial wastewater in pressureless transport lines. It also id designed to measure effluent brine and slurries in gravity pipelines and sewers, as well as dredging, mining, or sea and well water injection applications. The TIDALFLUX 2300 sits inline as a closed measuring solution without obstructions, allowing it to achieve much better accuracy at lower total costs of ownership than channel systems such as Venntury and V-notches. Krohne, www.krohne.com
The PZ 2.5 S is the smallest professional crimping tool on the market for wire end ferrules. In control cabinet construction, cables of the most diverse cross-sections are fitted with wire end ferrules. Ninety percent of these connections are in a cross-section range of AWG 14 (2.5 mm2) and smaller. A focus on this cross-section range makes the PZ 2.5 extremely compact and ergonomic – the small handle width and the opening angle, as well as the weight, make the tool easy to use without incurring fatigue in the hand, wrist or arm. The PZ 2.5 tool features a length of 160mm with a small grip width so it can easily fit in the palm of the hand. This compact tool is light to carry around for ergonomic advantage. Weidmuller, www.weidmuller.com
The FlexEdge Intelligent Edge Automation Platform, powered by Crimson, gives industrial organizations the complete, scalable access they need to take full advantage of all the industrial data embedded in your operations. This enhancement features strain gauge modules and J1939 and CAN protocol sleds. The strain gauge modules are easily installable and configurable and come in both SSR output and relay output options.
Both offer single loop PID capabilities to monitor, measure, and control equipment. Designed to thrive in harsh environments, the modules accept signals from load cell, pressure, and torque bridge transducers. With a software-selectable 5 or 10 Vdc stable bridge excitation voltage, each strain gauge module can drive up to four 350W bridges.
Red Lion Controls, www.redlion.net
The Raymond High Capacity Orderpicker is the first-of-its-kind forklift that delivers market-leading capacity at all heights and reduces annual cost per pallet stored by 19% compared with competitors. Designed to facilitate order picking a full rack higher than models currently on the market, the orderpicker features an industryleading elevated height of 456-in., which allows for increased rack storage access to 11% more pick slots. The increased elevated height enables operators to optimize storage capacity for more usable space and improved SKU count without increasing a facility’s overall footprint. It integrates Lithium-ion battery technology, in-aisle detection system and zoning and positioning technology.
The Raymond Corporation, www.raymondcorp.com
78th STLE Annual Meeting & Exhibition .23 .www .stle .org/annualmeeting
Atlas Copco Compressors .6, 7 .www .atlascopco .us
AutomationDirect .C-2, 1, 8A-8D .www .automationdirect .com
CFE Media GSI Database .43 .https://gspplatform .cfemedia .com/si/home
CFE Media LLC .43 .www .cfemedia .com
CFE Media NPE Database .43 .https://gspplatform .cfemedia .com/pe/home
Dodge Industrial .4 .www .dodgeindustrial .com
Hertz Kompressoren USA Inc .28 .www .hertz-kompressoren .com/en-us
Industrial Cybersecutiy Pulse .49, 54 .www .industrialcybersecuritypulse .com
Lubriplate Lubricants Co .12 .www .lubriplate .com
MAPCON .54 .www .mapcon .com
MOTION .C-4 .www .Motion .com
Nord-Lock, Inc .22 .www .nord-lock .com
Proco Products, Inc .42 .www .procoproducts .com
ROYAL PRODUCTS .56 .www .mistcollectors .com
SEW-EURODRIVE, Inc .2 .www .seweurodrive .com
SHERWIN-WILLIAMS .48 .https://tinyurl .com/yc99jbvy
Sullair Industrial Products .15 .www .sullair .com
WELDBEND .36, 37 .www .weldbend .com
Winsted Corporation .29 .https://tinyurl .com/4ypxaa5t
Yaskawa America, Inc .C-3 .www .yaskawa .com
VP Sales
Matt Waddell MWaddell@CFEMedia.com 312-961-6840
Sales Account Manager
Brian Gross BGross@CFEMedia.com 847-946-3668
Sales Account Manager
Dick Groth RGroth@CFEMedia.com 774-277-7266
Sales Account Manager
Diane Houghton DHoughton@cfemedia.com 508-298-9021
Sales Account Manager
Robert Levinger RLevinger@CFETechnology.com 516-209-8587
Sales Account Manager
Dean Morris 513-205-9975 DMorris@cfemedia.com
Sales Account Manager
Judy Pinsel 847-624-8418 JPinsel@cfemedia.com
Sales Account Manager
Mike Worley MWorley@CFEMedia.com 331-277-4733
Jim Langhenry, President, Co-Founder, CFE Media JLanghenry@CFEMedia.com
Steve Rourke, Co-Founder, CFE Media SRourke@CFEMedia.com
Patrick Lynch, CEO, CFE Media 847-452-1191, PLynch@cfetechnology.com
McKenzie Burns, Marketing-Events Manager MBurns@cfemedia.com
Courtney Murphy, Marketing and Events Manager CMurphy@cfemedia.com
Paul Brouch, Director of Operations 708-743-5278, PBrouch@CFEMedia.com
Rick Ellis, Audience Management Director 303-246-1250, REllis@CFEMedia.com
Michael Smith, Creative Director 630-779-8910, MSmith@CFEMedia.com
Michael Rotz, Print Production Manager 717-422-3622, mike.rotz@frycomm.com
Custom reprints, print/electronic: Paul Brouch, PBrouch@CFEMedia.com
Jeff Mungo, List Rental Account Director, DataAxle 402-836-6278, Jeff.Mungo@data-axle.com
Information: For a Media Kit or Editorial Calendar, go to www.controleng.com/mediainfo.
Marketing consultants: See ad index
Letters to the editor: Please e-mail us your opinions to MHoske@CFEMedia.com or fax 630-214-4504. Letters should include name, company, and address, and may be edited.
Your time is valuable. The new, easy-to-use GA800 AC Drive from Yaskawa gives you the power to make all of your operations better.
• Rest easy with legendary Yaskawa quality and embedded functional safety.
• Experience ultimate ease-of-use with DriveWizard® Mobile and optional Bluetooth® connectivity.
• Enjoy incredible torque production and network connectivity.
Your days are complicated enough. Let us help simplify them. To learn more, visit or call Yaskawa today at 1-800-YASKAWA. FOR MORE INFORMATION: https://www.yaskawa.com/ga800
Email: info@yaskawa.com | yaskawa.com