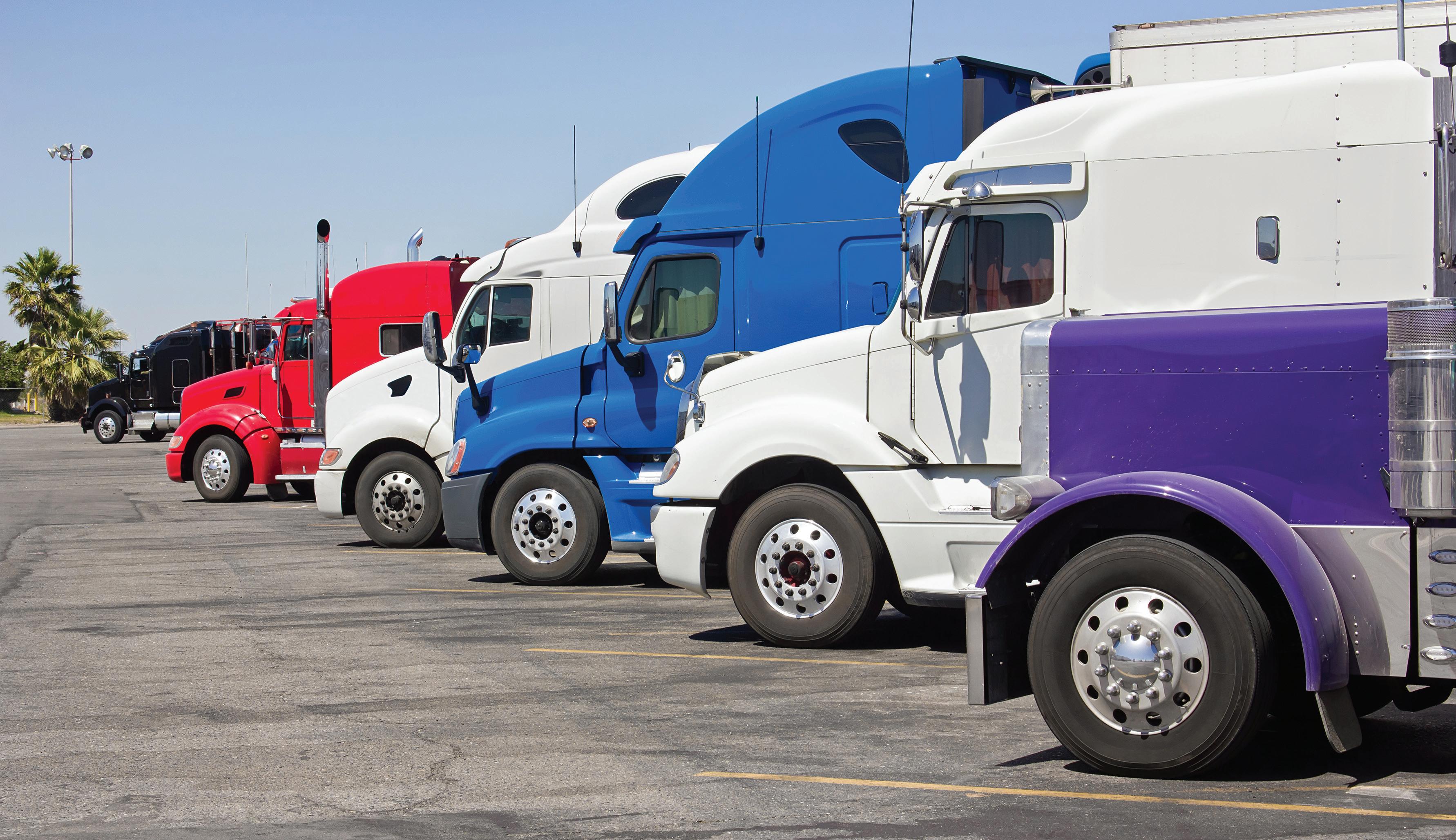
7 minute read
The move to synchronous power supplies in smart factories
Anthony "Thong" Huynh • Maxim Integrated
The need for high efficiency is pushing industrial power supplies toward synchronous topologies that minimize the need for heat sinking and cooling.

Compact power circuits help trucking companies manage their fleets with vehicular asset-tracking devices. Image courtesy of JohnnyH5/iStock
Buildings, factories, and industrial equipment are getting more space efficient, driving a move toward miniaturizing the underlying components that enable intelligence and automation. This trend challenges the power supplies for these designs. The power ICs must, of course, provide the necessary output voltages, and also must be small and capable of performing well in thermally difficult environments.
There are several techniques and technologies that can ensure power supplies will meet the efficiency and size requirements of industrial equipment. They help realize the high efficiency, low power dissipation, and small form factor needed to address modern design targets.
The task of reducing analog IC size hasn’t been easy—particularly because power management components consume a significant portion of PCB area. To illustrate this point, let’s examine the power supply requirements of some typical application areas, as well as what’s needed to address their demands.
First consider vehicular asset-tracking devices. These aftermarket items let companies managing large vehicle fleets keep close tabs on their cars, trucks, and vans. Data collected can enhance fleet efficiency, ensure vehicles undergo regular maintenance, and locate vehicles in the event of theft or other issues. The devices themselves are usually powered by the vehicle battery (12 V for cars and 24 V for many trucks) and have a rechargeable backup battery. They’re typically installed under the dashboard, so heat dissipation is critical to keeping the device in its proper temperature range.
The power circuit for asset-tracking devices can include step-down dc-dc converters and LDOs (low dropout regulators) to convert 12 and 24-V supplies to lower voltages for powering various digital logic and analog ICs. LDOs are, indeed, an option, as they’re typically easy to use and inexpensive. However, LDOs dissipate appreciable power when used directly from the main battery voltage, the primarily means by which these asset-tracking devices are powered. This application would be well served by highly integrated power ICs. Among today’s dc-dc regulators, there are devices that integrate the power MOSFETs, compensation circuit, and other external components, minimizing the discrete parts. In fact, new technologies push the envelope even further for efficiency and space savings.

Small, efficient power ICs support intelligence at the edge of automated factories such as this car manufacturing plant. Image courtesy of onurdongel/iStock.
As intelligence continues to move to the edge of the digital factory, installations require a plethora of high-performance sensors, actuators, I/Os, and programmable logic controllers (PLCs). The insights they deliver allow factory equipment to become self-aware and deliver benefits such as greater productivity and up-time, predictive maintenance, and adaptive manufacturing. The power ICs for this equipment must be small, efficient, robust, and able to handle conditions such as drops, shock, and vibration.
Industries that require noncontact level sensing--such as oil and gas, mining, and waste water processing--are driving demand for ultrasonic sensors. These types of sensors emit frequencies ranging from 30 kHz up to a few megahertz and interpret reflected signals as a sensing method. For level sensing, a single transducer is sufficient. After the transducer emits the ultrasonic signal, it measures reflection time from the surface of the liquid. Flow sensing typically relies on two transducers because this process uses the time-of-flight of the ultrasonic wave and its variation (depending on the flow rate of the medium).
Ultrasonic sensors include an analog front-end that encompasses transmission, receiving, and control circuits, plus an MCU for the calculations. Increasingly, these sensors must be small enough to fit into compact quarters and in narrow openings. Their power supplies, therefore, must be small, rugged, and dissipate minimal heat. There are a few other power considerations to note. Fan-less ultrasonic sensors are typically powered by a supply of 10 to 30 V and consume a few hundred milliamps of load current. With system operating temperatures up to 70°C, the power components should be rated for at least 125°C. These systems also need protection from reverse polarity connections, over-voltages, and electromagnetic interference (EMI).
Today’s smart buildings are defined by intelligence that controls the lighting, temperature, security systems, access mechanisms, and more. The sensors, controllers, and interfaces that make these capabilities possible are often tiny and, thus, require small, efficient power sources. Sensors generally receive power from 24-Vdc sources and must be able to operate in environments where there will be high-voltage transients. Non-critical industrial equipment typically demands a maximum operating range from 36 to 40 V. Critical equipment-- which includes controllers, actuators, and safety modules--must support 60 V. On the output-voltage side, you’ll commonly find 3.3 and 5 V with currents from 10 mA in small sensors up to tens of amps in applications such as motion control. These parameters point to use of a stepdown voltage regulator that can withstand voltage transients (42 or 60 V, typically) for building and industrial control applications.

Industries such as waste water processing rely on ultrasonic sensors for level sensing. Image courtesy of BKhamitsevich/iStock.
ENHANCING POWER SUPPLY EFFICIENCY
Clearly power supplies for these applications share qualities that include small size, power efficiency, wide input-voltage range, and reliable operation in harsh and thermally challenging environments. Board space is often limited in these industrial designs, making it impractical to dissipate heat via techniques such as heatsinks. Forced-air fans also aren’t viable where sealed industrial enclosures prevent ingress of dust and pollutants. The only real option is a power supply with high efficiency.
The input and output voltages involved in these industrial designs make it necessary to use a step-down, or buck, voltage regulator. The most common type of stepdown architecture is the nonsynchronous buck converter, with the low-side rectifier diode external to the IC. These devices are fairly easy to design for high voltages. In a design with a 24-V input and a 5-V output, the buck converter works with a duty cycle of approximately 20% and the external rectifier diode conducts the remaining 80% of the time (this accounts for most of the power dissipation). To greatly minimize the power dissipation, synchronous topologies replace the rectifier diode with a synchronous rectifier (such as a low-side MOSFET).
Consider an example with a 4-A load and a Schottky rectifying diode that has a voltage drop of about 0.64 V. At 80% duty cycle, the conduction loss is roughly:
(0.64 V) ×(4 A) × (0.80) = 2 W
Replacing the diode with a low-side MOSFET serving as a synchronous rectifier replaces the 0.64-V drop with a drop across the MOSFET transistor’s on-resistance, RDS(ON). The MOSFET’s RDS(ON) is just 11mΩ. As such, the voltage drop is:
(11 mΩ) × (4 A) = 44 mV
And the power loss is:
(0.044 V) × (4 A) × (0.80) = 141 mW
In our example, the MOSFET power loss is about 14× smaller than the Schottky power loss at full load. Such are the power-efficiency benefits of synchronous rectification.
A cautionary word about handling maximum input voltage: Though 24 V is the nominal rail for factory applications, it would be prudent to choose from the 28-V, 36-V, 42-V, or 60-V input power management modules now available. In fact, unless you know or will be able to model all possible surge scenarios that can stem from long cables and PCB traces, devices with a 42-V or 60-V maximum operating range should be the best bet—28 V is too close to 24 V to provide a reliable margin, and 36 V is risky when working with sensors and encoders on a 24-V rail. (This approach could expose equipment to excessive voltages, even with surge protection in place.)
Integrated power modules can handle such demands while reducing overall circuit size by eliminating the need for many discrete components. For example, the Maxim Himalaya uSLIC dc-dc power modules integrate a synchronous wide-input Himalaya buck converter—including built-in FETs, compensation, and other functions—together with the output inductor. These modules reduce the power supply size by up to 2.25× compared to discrete approaches. The family of power modules supports input voltages from 2.9 to 60 V and, as such, can support low-voltage applications such as consumer devices as well as higher voltage industrial applications.

Smart building applications such as automated lighting, security, and temperature control benefit from step-down voltage regulators that can withstand voltage transients. Image courtesy of zhudifeng/iStock.
All in all, integrated power modules help meet the input voltage, heat dissipation, and size requirements of the industrial applications that are bringing greater operational efficiency to our factories, vehicle fleets, buildings, and more.
References: Maxim Integrated Himalaya power modules, https://www.maximintegrated.com/en/ products/power/power-modules.html