www.therobotreport.com A Supplement to Design World - AUGUST 2022 powers the UR20 cobot How a new joint design Redesigned from the ground up, the UR20 is the fastest and strongest collaborative robot arm ever built by Universal Robots. page 68 • What’s the di erence between a servo drive and motion controller? ................................................................. 74 • How precise motion systems drive AMRs 78 • How the mini cheetah robot learns to run 86 INSIDE:

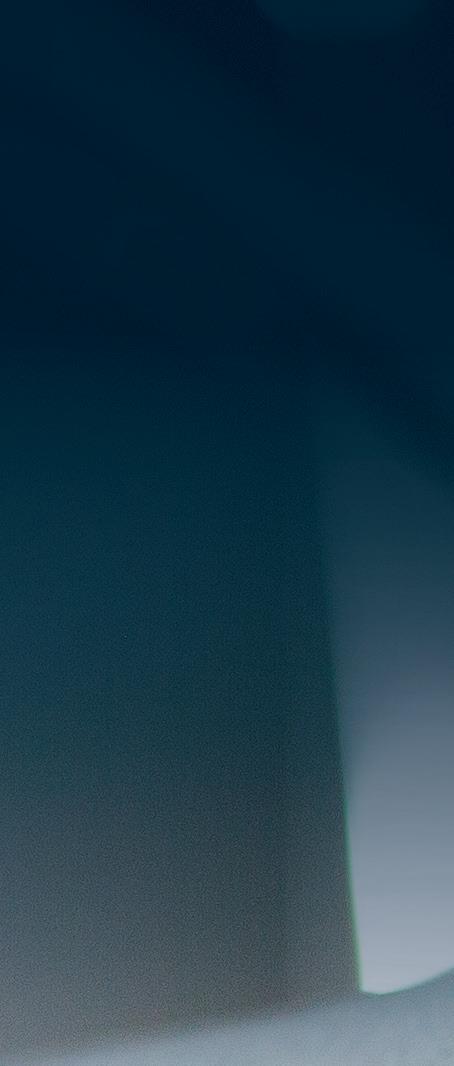
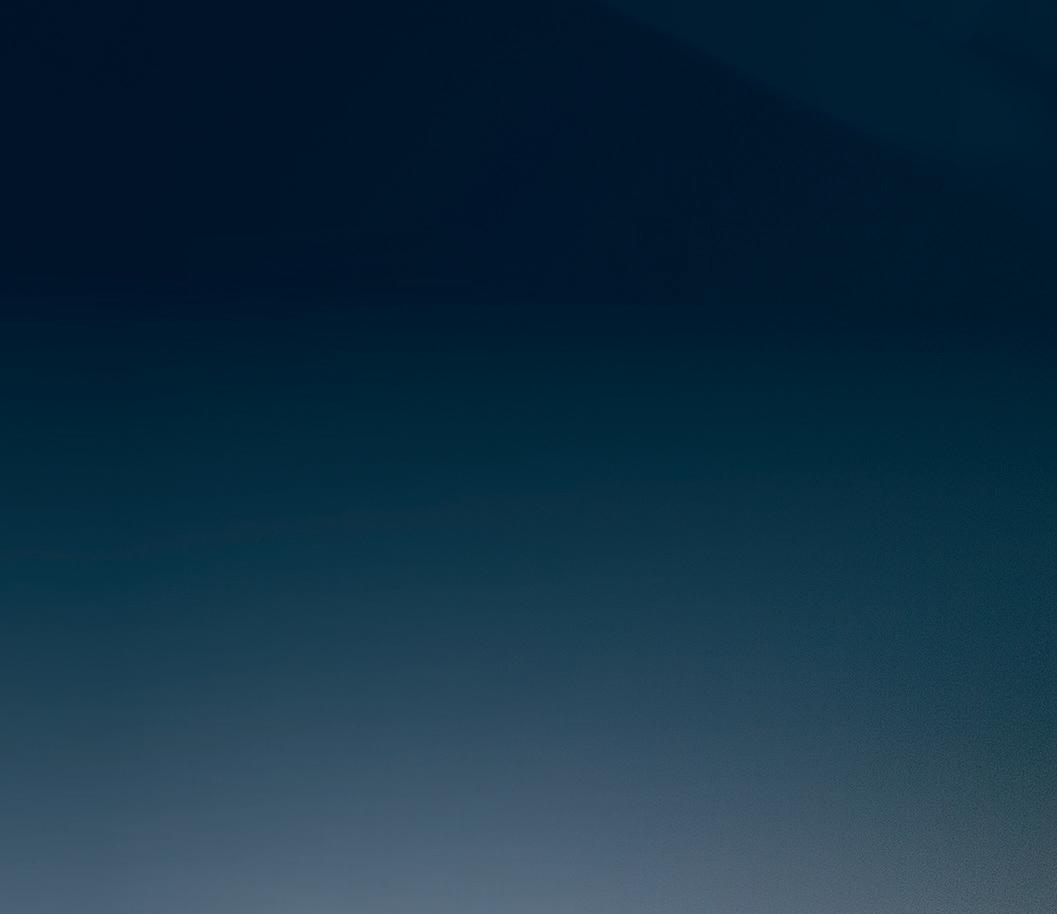
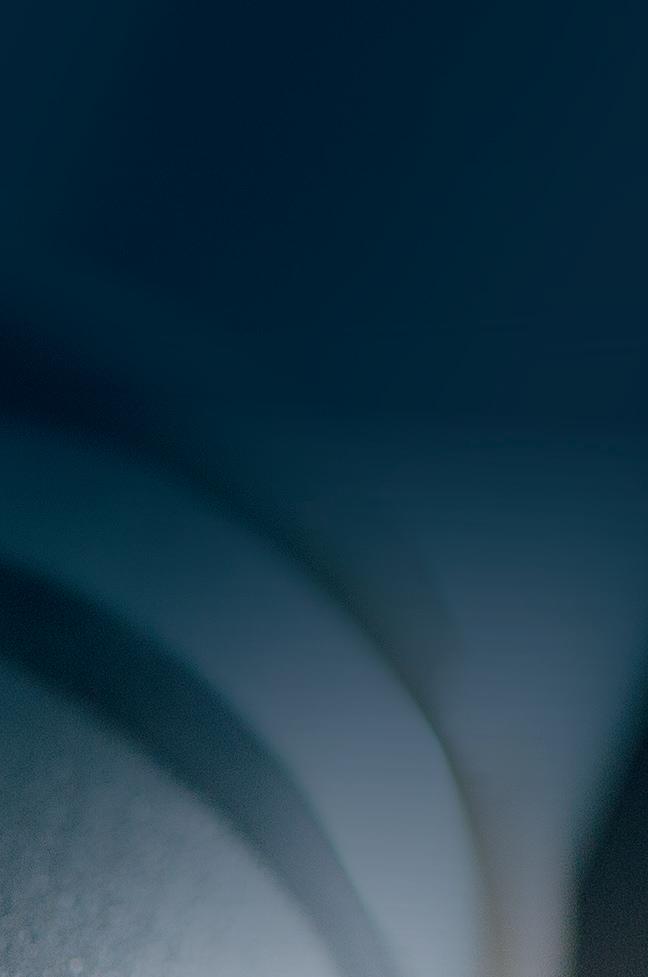
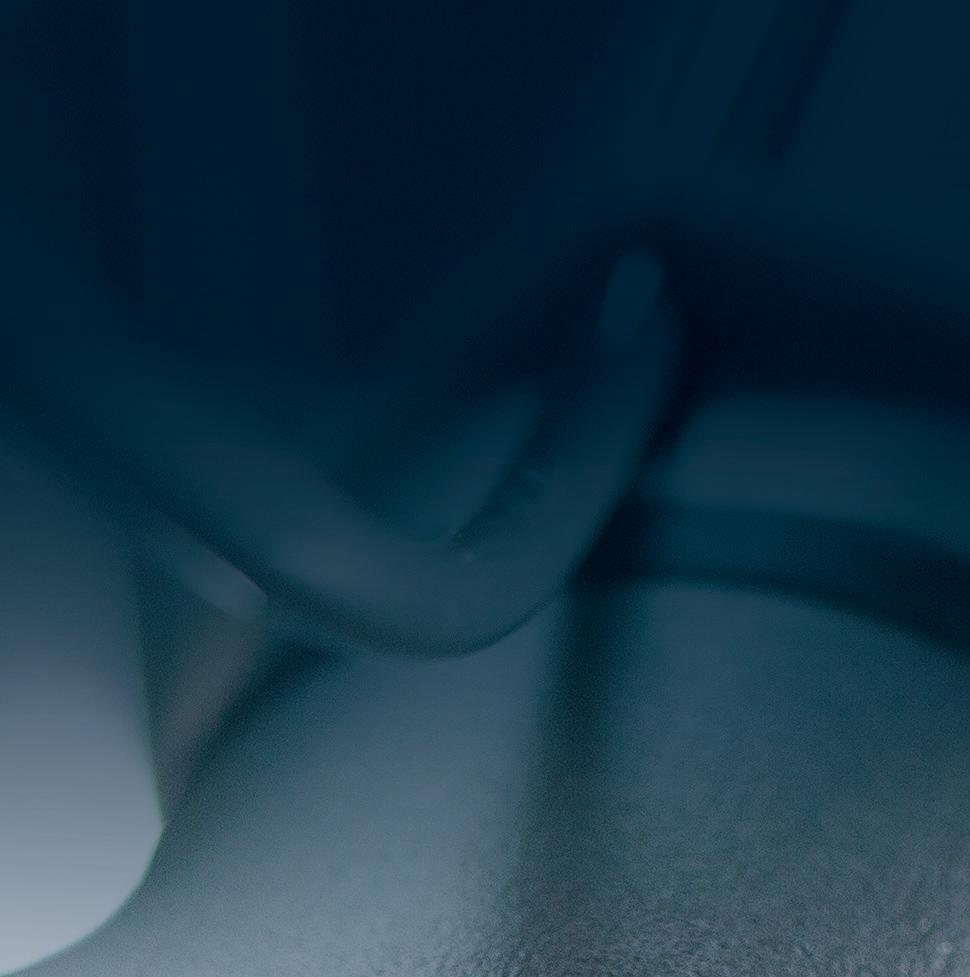
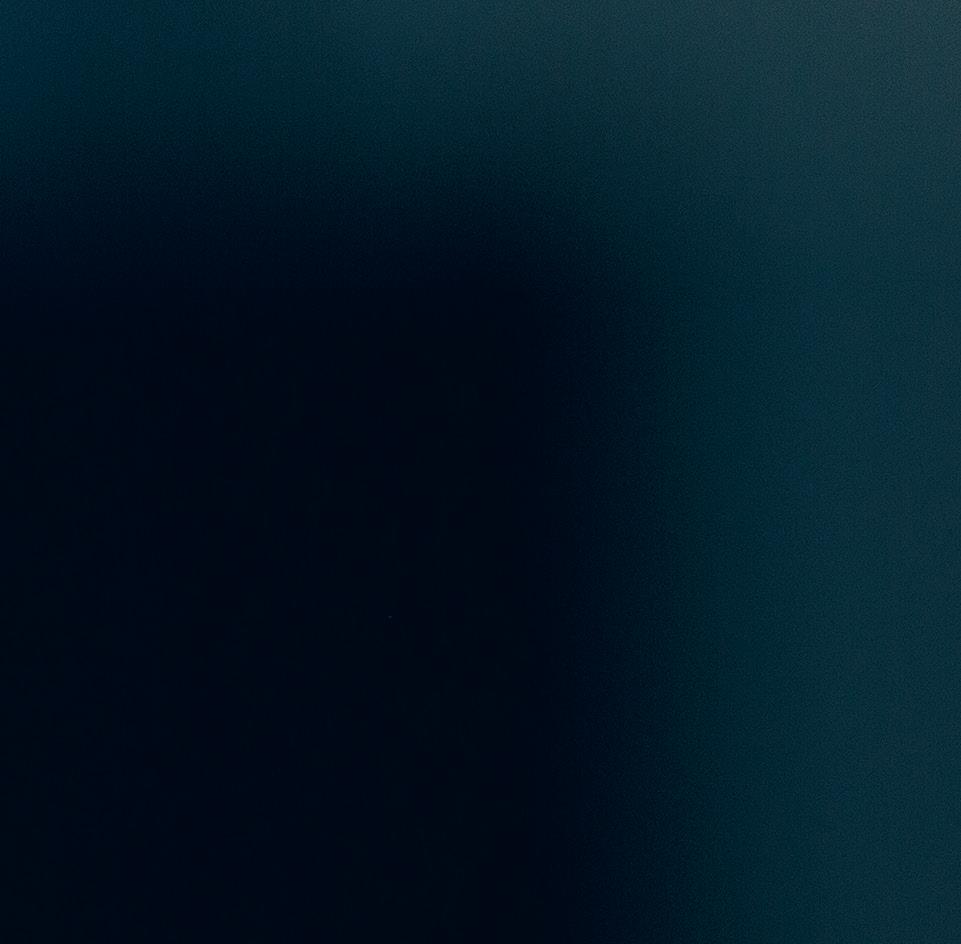
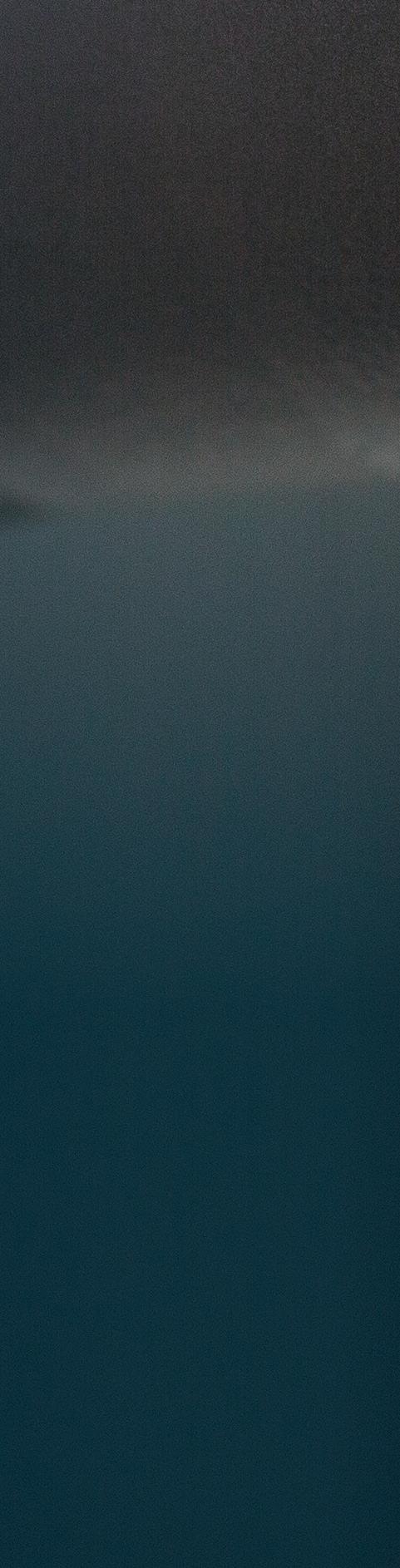
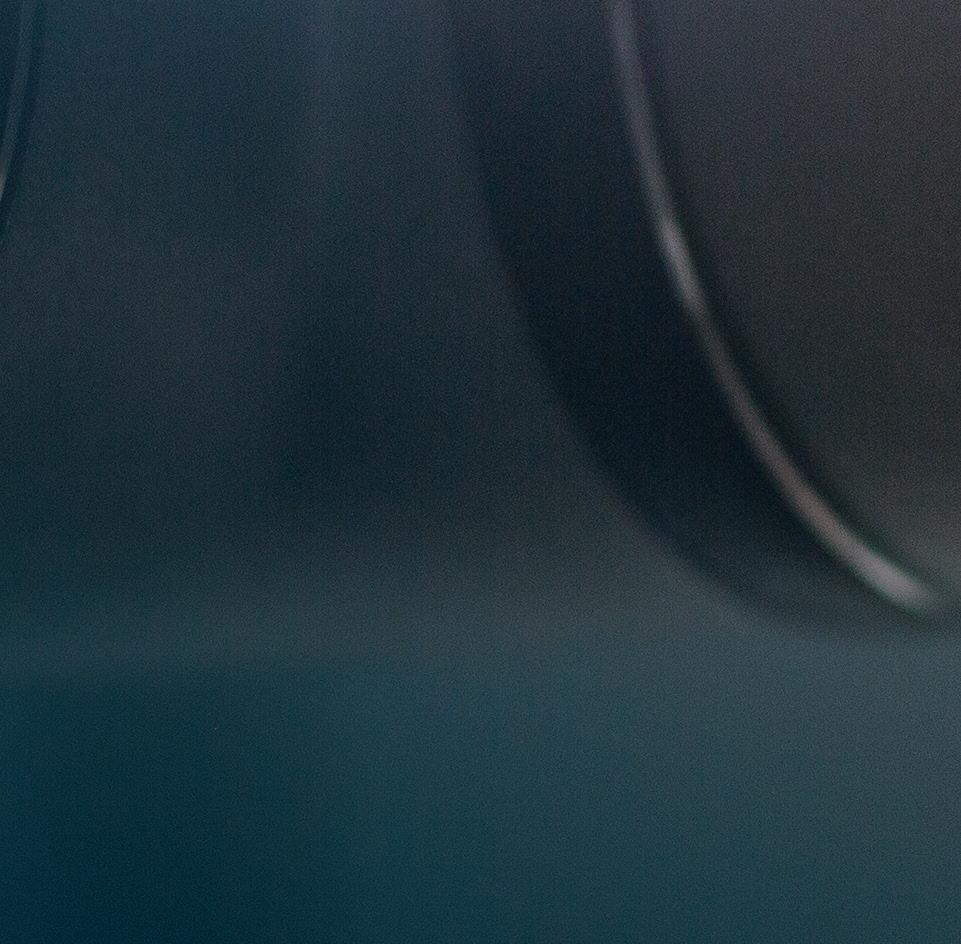
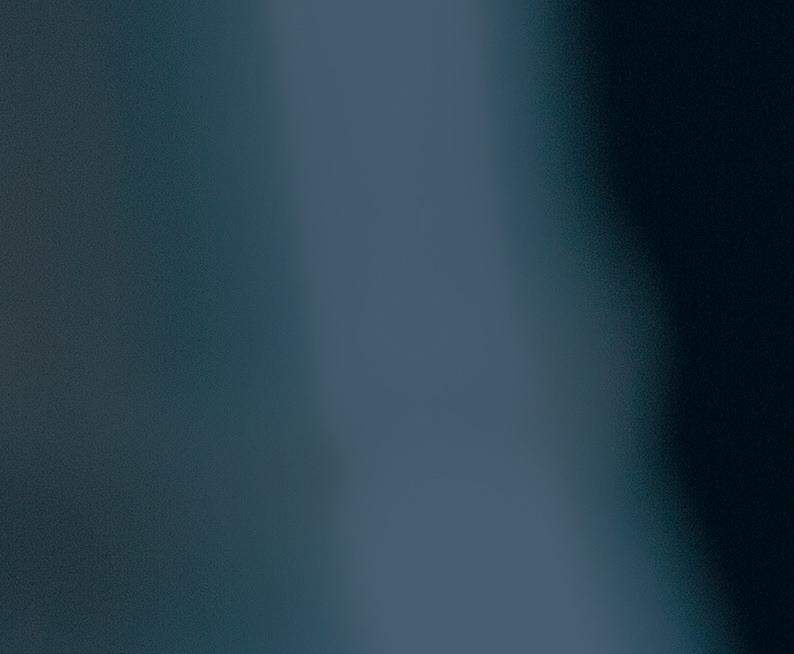
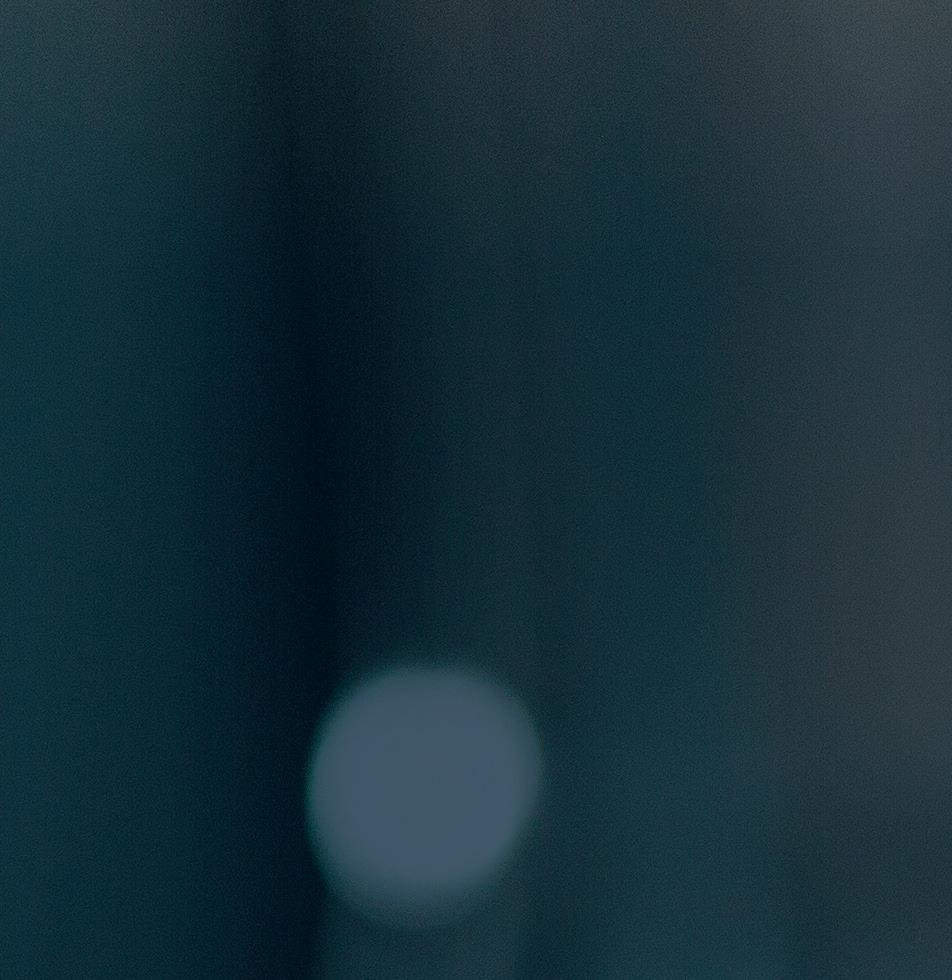
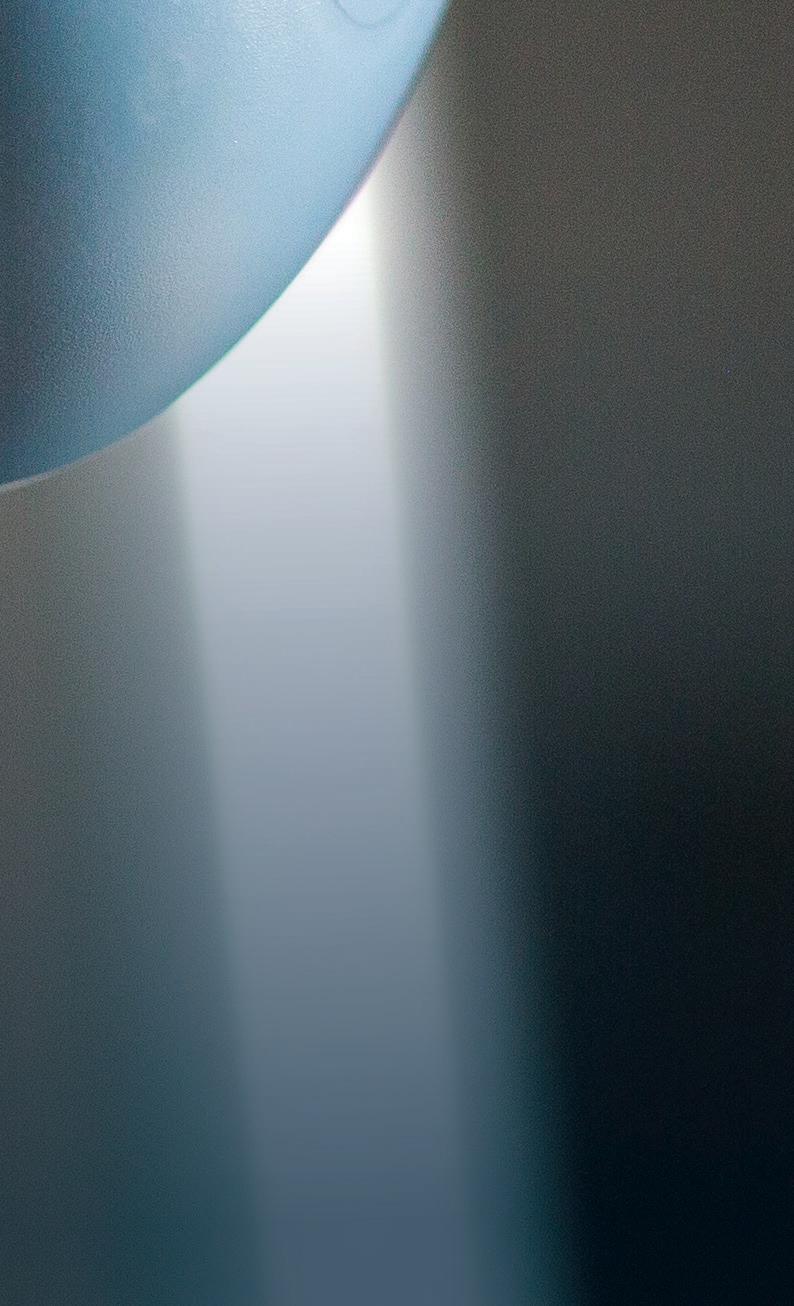



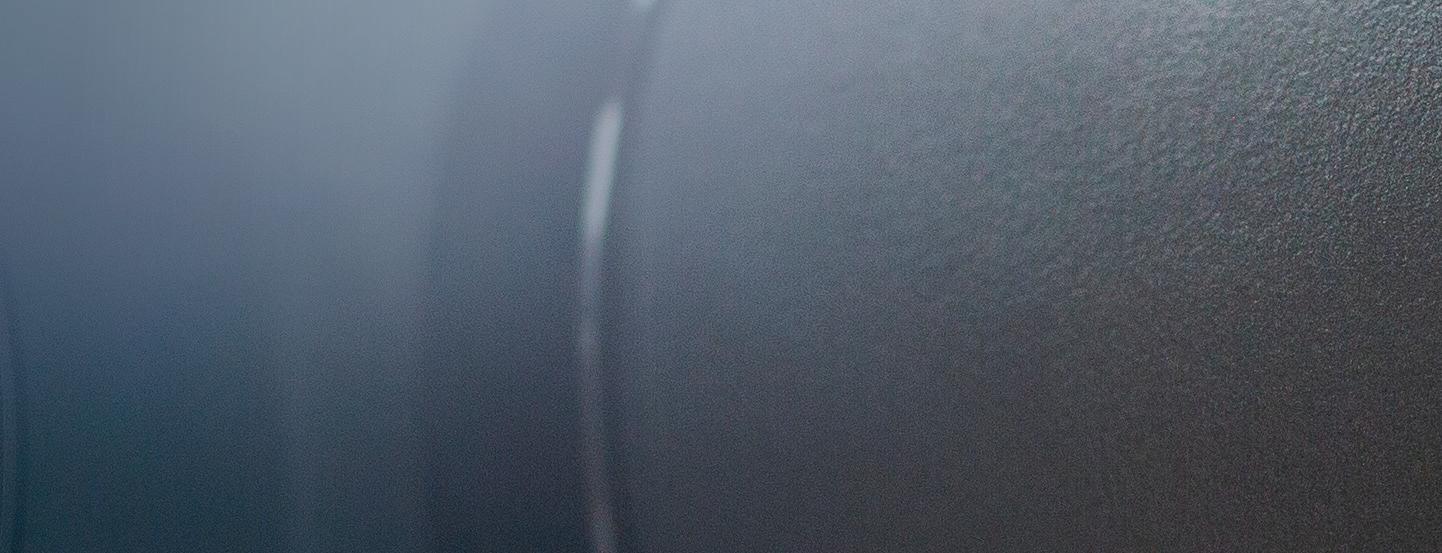
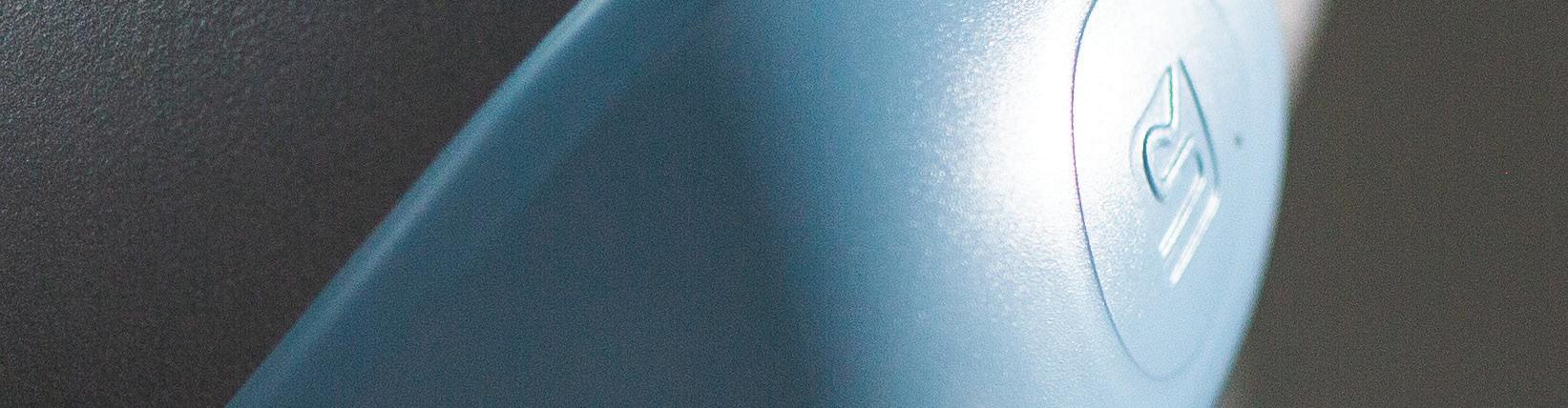
68 August 2022 www.therobotreport.com THE ROBOT REPORT The Robot Report the UR20 cobot How a new

joint design Redesigned from the ground up, the UR20 is the fastest and strongest collaborative robot arm ever built by Universal Robots. powers
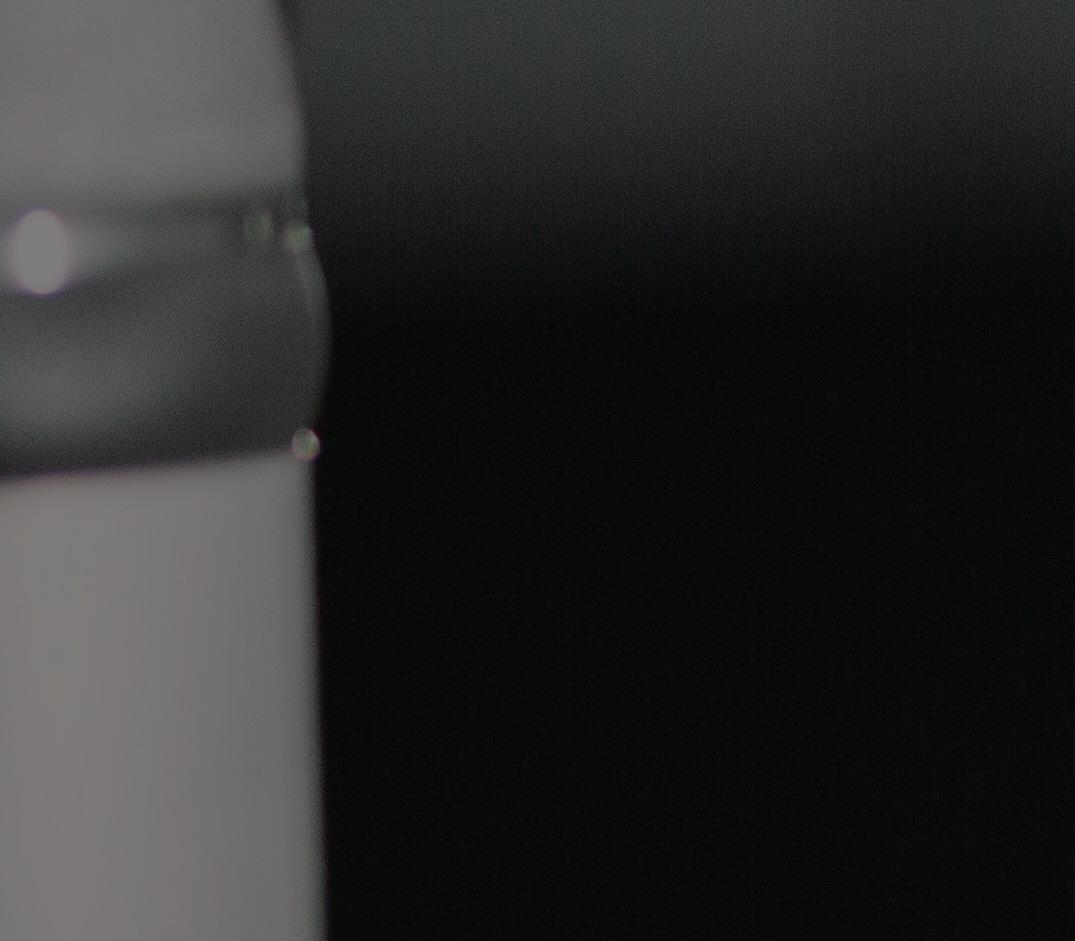

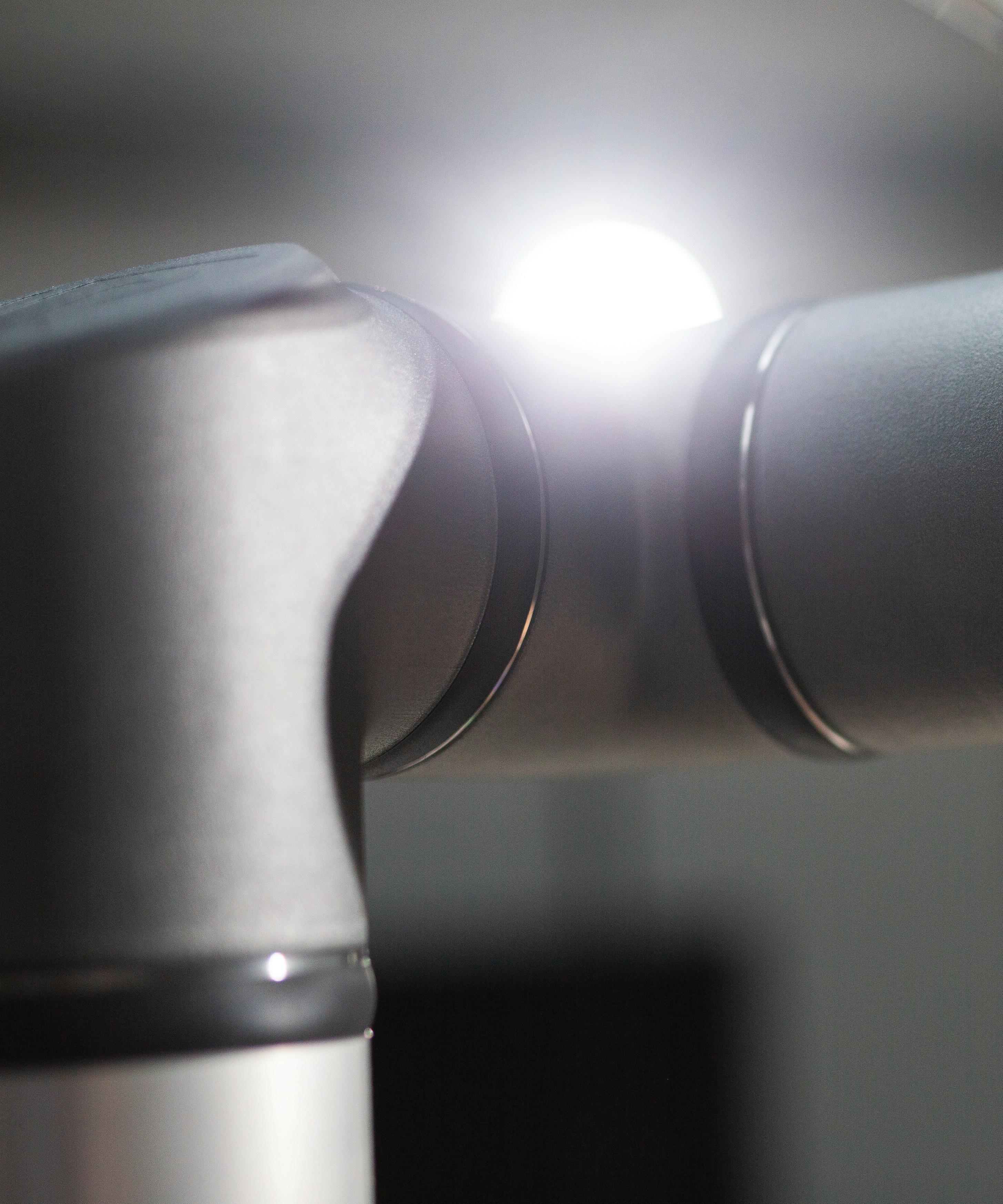
Robot
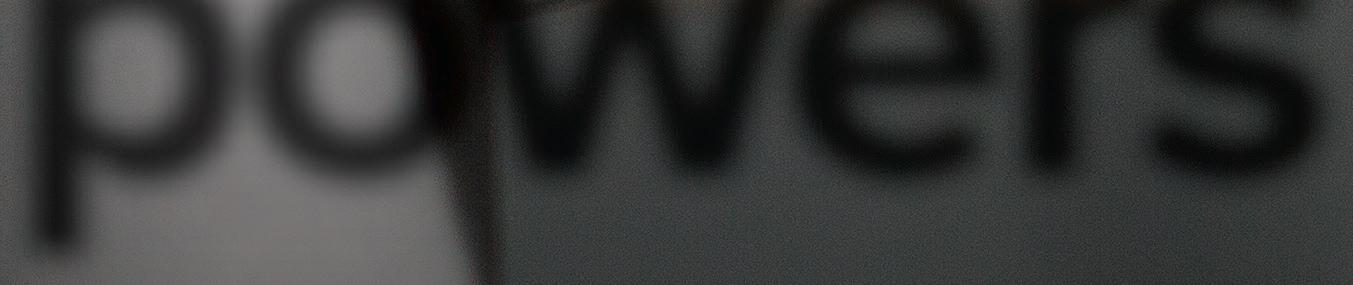


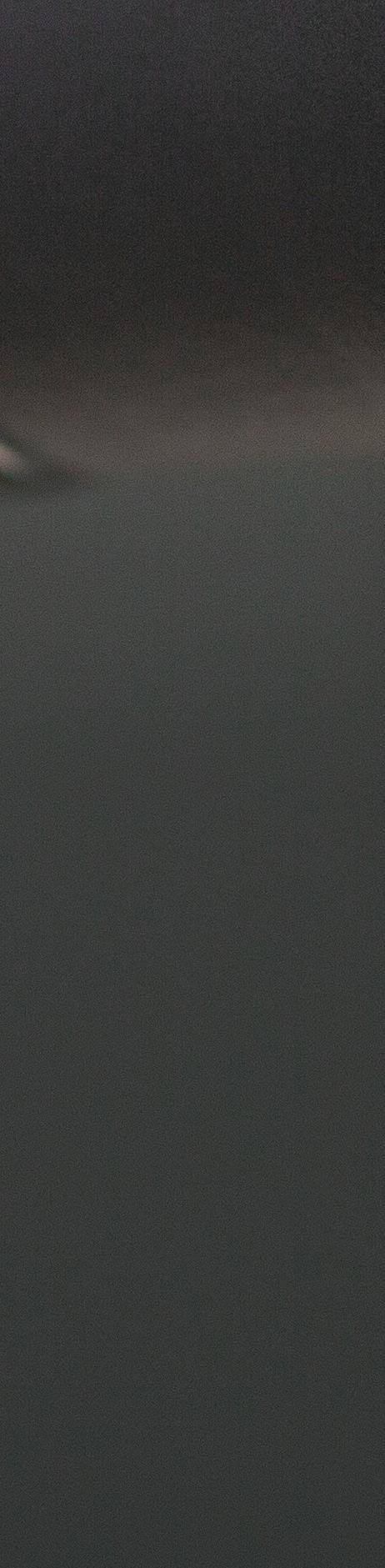

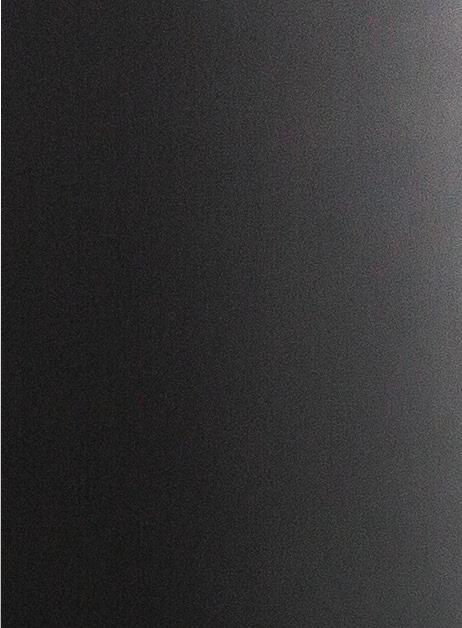
By Steve Crowe • Editorial Director, The Report

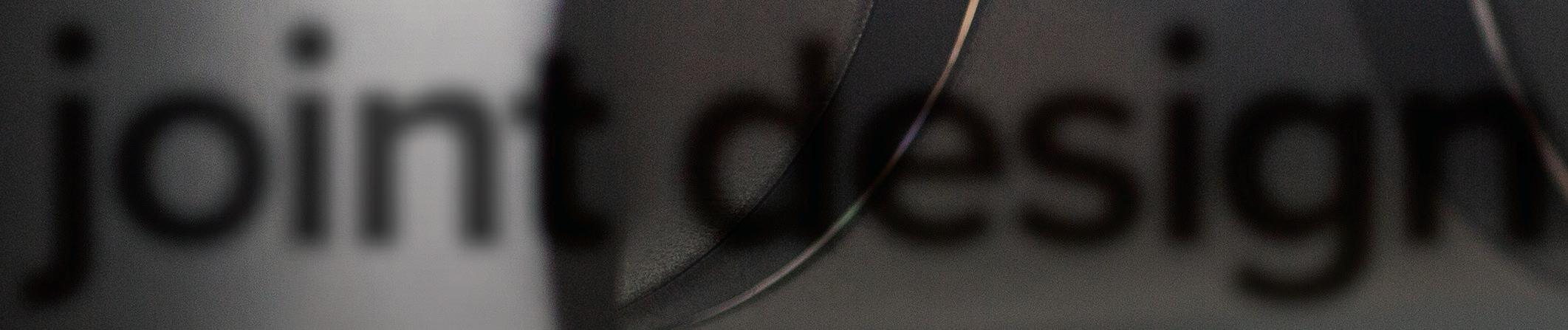
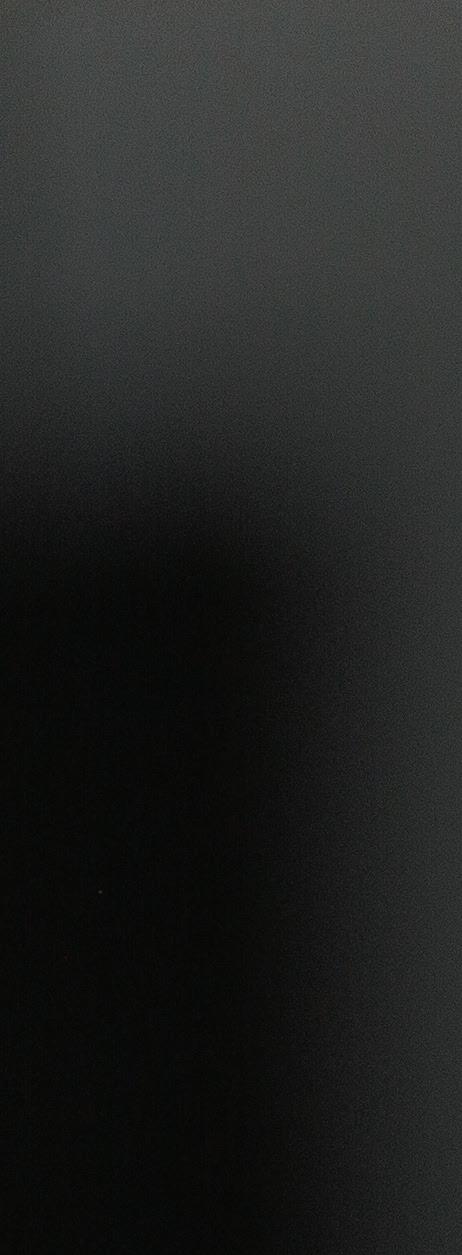

Universal Robots (UR) finally unveiled at Automatica 2022 what it’s been teasing the last few months. It introduced the UR20, the Danish company’s fastest and strongest collaborative robot arm ever. The UR20 is expected to be available for pre-order in late Q4 2022 and will begin shipping in Q2 2023 for an undisclosed price. The UR20, which has been redesigned om the ground up, is the first model in a new series of next-generation cobots that will complement the e-Series. The UR20 features a 20 kg payload, 1750 mm reach, ± 0.05 mm repeatability and up to 30% more speed and torque when compared to other UR cobots. According to the company, the UR20 is well suited for applications such as machine loading, machine tending, materials handling, palletizing and welding. UR told The Robot Report additional new cobots will be introduced in late 2023 or early 2024. The last time UR introduced a new cobot was 2019 when it added the UR16e. It offers a 16 kg payload and is designed for heavy-duty applications. UR’s cobot portfolio also includes the UR3e (3 kg payload), UR5e (5 kg) and UR10e (12.5 kg). At Automatica in Munich, Germany, the UR20’s palletizing capabilities were demonstrated with UR+ partner Robotiq. The new extended reach was demonstrated stacking to the height of 1800mm, covering two standard European (40in x 48in / 1200mm x 800mm)) pallets. The demo showed how the kinematics can cover both the pallets and an infeed at the same time. www.therobotreport.com August 2022 69
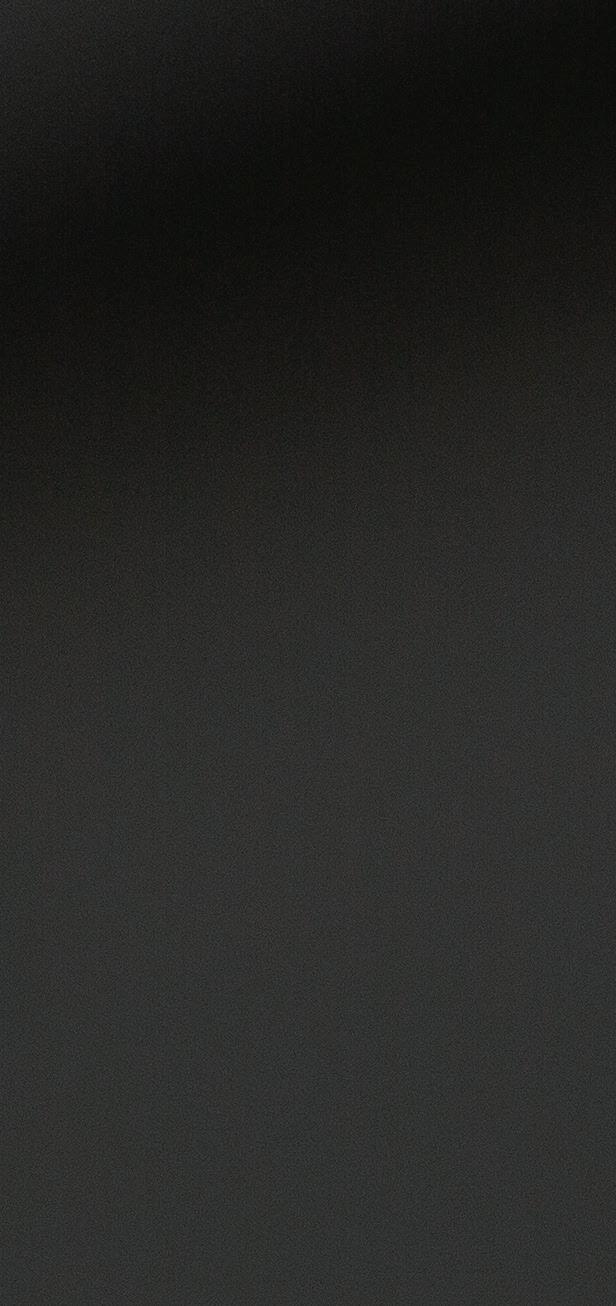
THE ROBOT REPORT

|
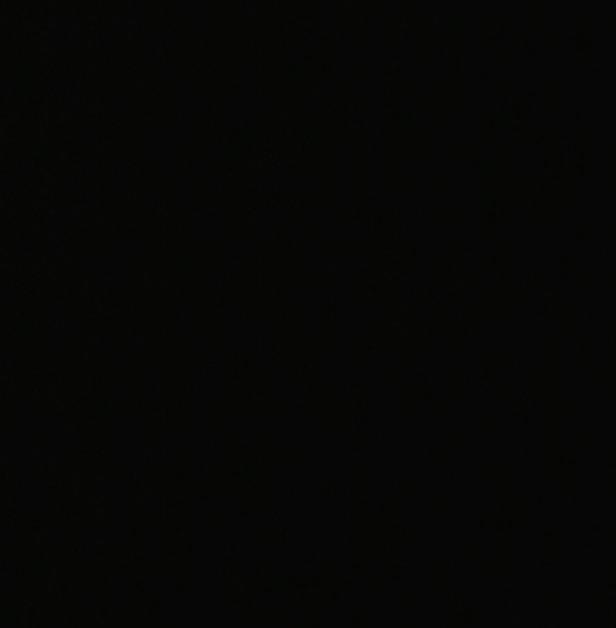

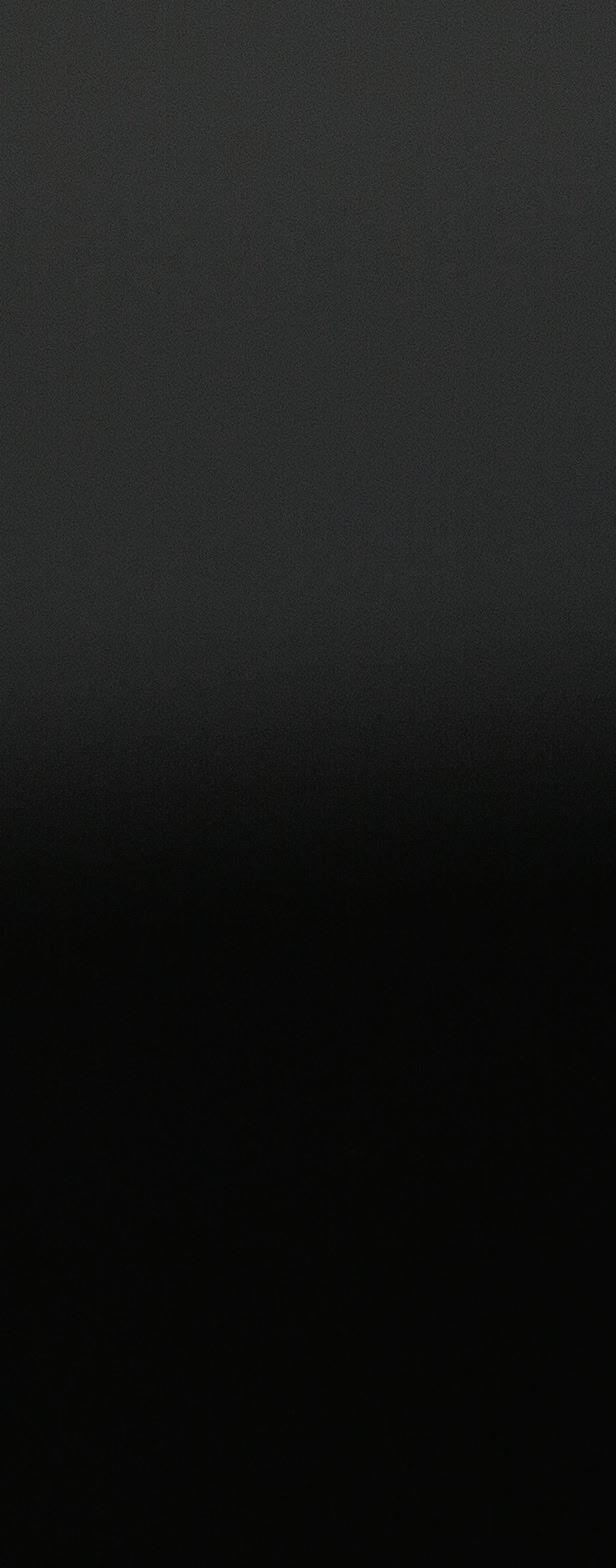
Credit:RobotsUniversal
A close-up of the new joint on the UR20 cobot.
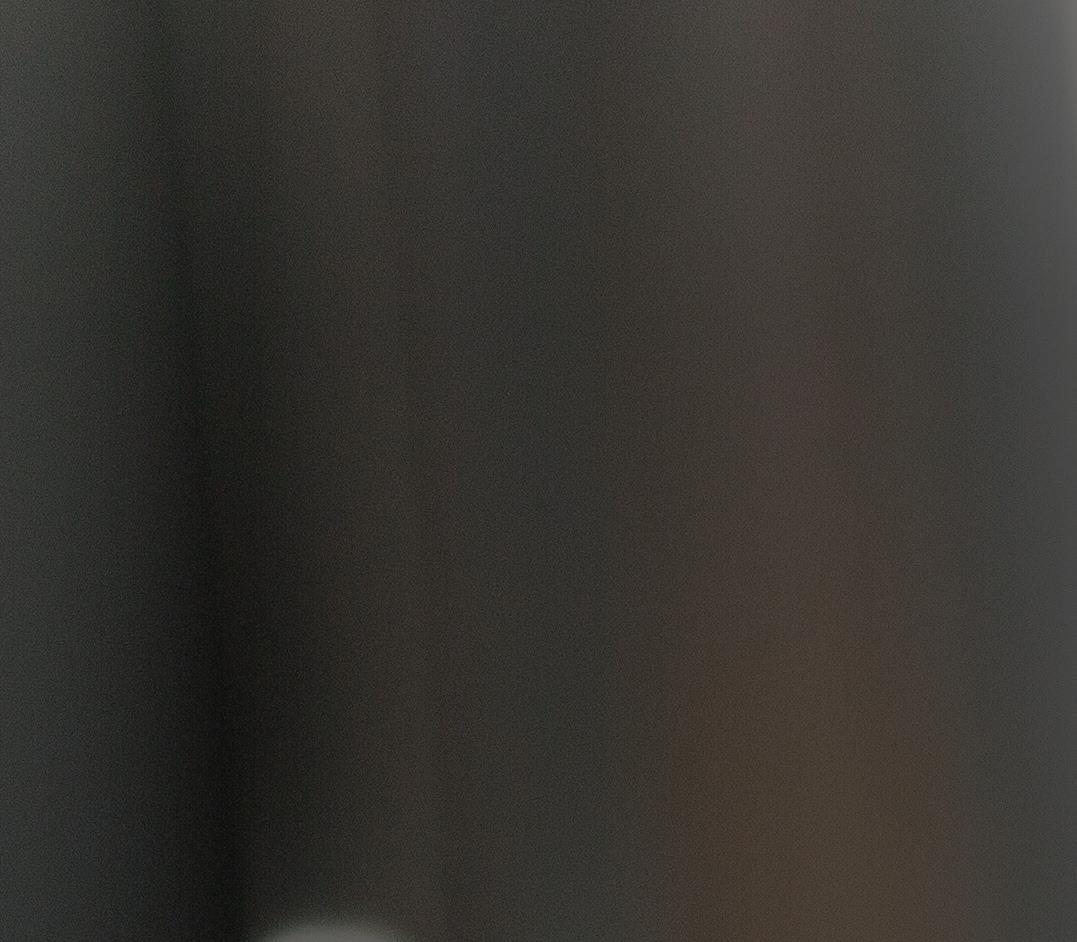
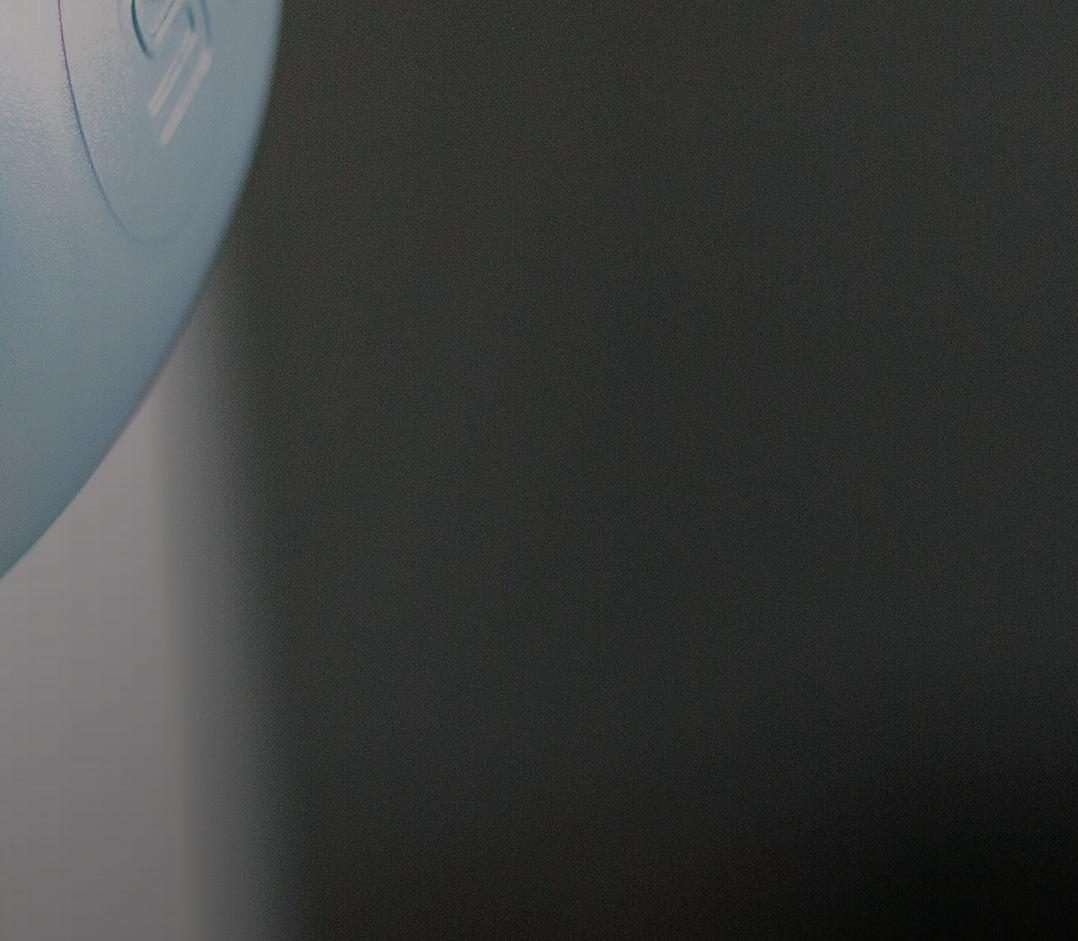


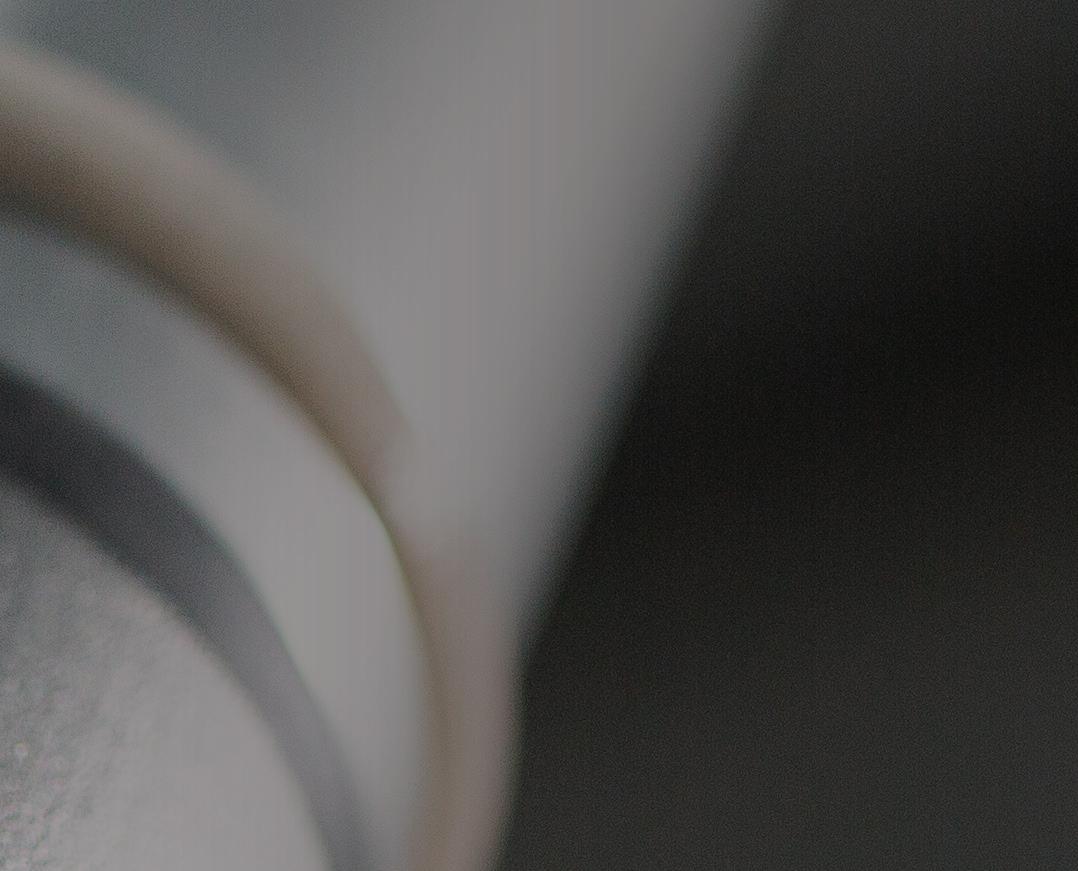
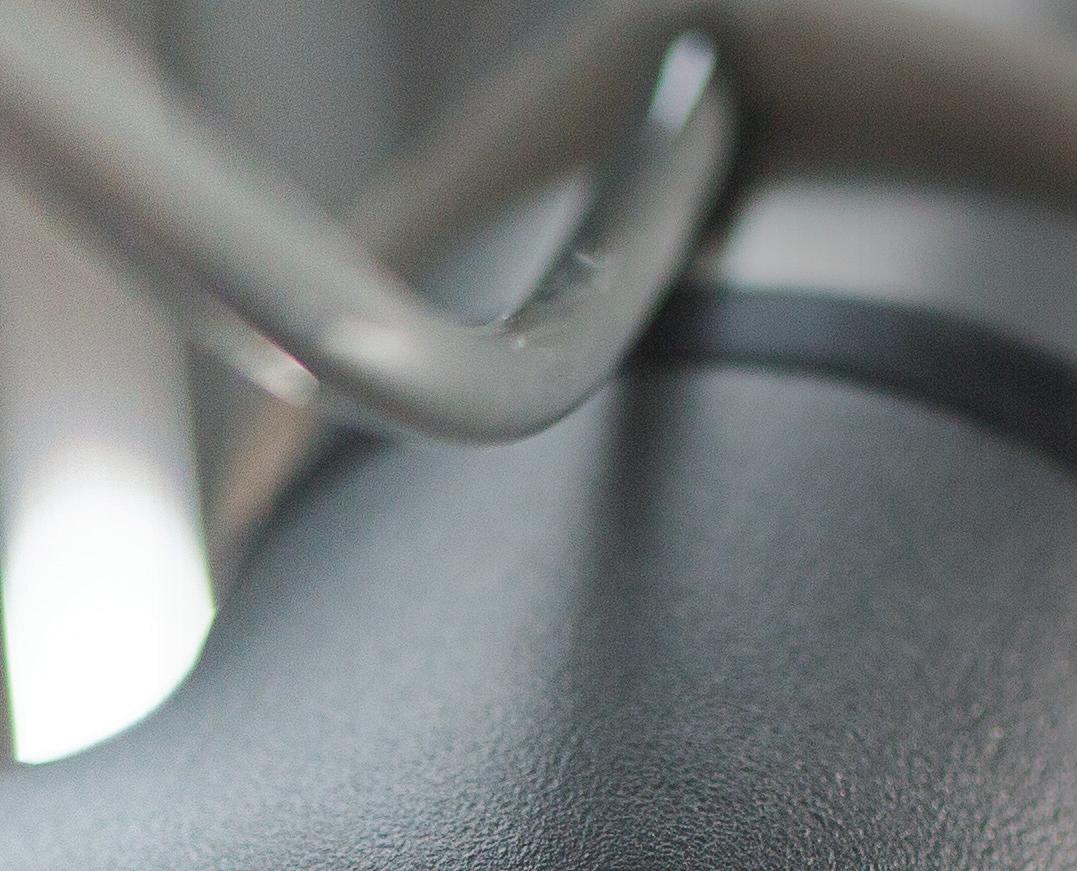
All of UR’s cobots are power and force limited (PFL) robots. Just like the e-Series, the UR20 will be certified to both EN ISO 13849-1, Cat. 3 PLd and ISO 10218-1 by TÜV Nord. UR also said that like the e-Series, the UR20 has 17 customizable safety functions so far, including having stopping time limiting and stopping distance“Innovationlimiting.had to happen across the board,” Povlsen said. “Joints and gears aren’t our core competency. We collaborated with vendors on different parts in the joints to iterate our way here. We needed more reach, more payload, and more speed. We have smart engineers who cracked the code to still make sure it’s a safe cobot to be around.” The UR20’s base offers the traditional flange design that gets bolted down. But in a change of appearance for UR, none of the joints have external screws. So it could be easier for UR to do a scrubbable version of this cobot than with the current e-Series.Povlsen told The Robot Report the entire control software has been rethought on 70 August 2022 www.therobotreport.com
THE ROBOT REPORT
Smith said the primary purpose of cobots is to help manufacturers solve labor shortages. “They have trouble hiring people. If you look at what people can practically lift, it’s 15-20 kilograms,” he said. “So we had a gap above 16 kg in tasks that people want to do, in particular machine tending and palletizing.”
sameworkinghavedevelopincludePovlsenimprovements,SomePolyScope.ofthemajorsaid,howtoURcapsandmultipleURcapstogetheratthetime.“Anythingwecando
Universal Robots unveiled the UR20 at Automatica in Munich, Germany. The new extended reach was demonstrated stacking to the height of 1800mm, covering two standard European pallets. | Universal Robots the UR20; although it is compatible with the latest version of

to simplify the path for customers to be more innovative, that’s something we’re investing in.” Why the UR20? UR certainly is not the first company to offer a 20 kg cobot. There are at least several others, including Fanuc and Yaskawa; Fanuc also has the CRX-25iA with a 25 kg payload. Povlsen said UR learned from its customers that there was a gap in its product portfolio.
“There were a number of applications that our portfolio didn’t cover [before the UR20],” said Povlsen. “But specifically packaging and palletizing. Moving 40-lb boxes onto a pallet over and over again, day after day, is a task that you should not be doing. We had lots of conversations with customers about how we can help them deal with these challenges.” UR was acquired by Teradyne for $285 million in 2015. Teradyne president Greg Smith, who runs the company’s industrial automation group, said UR’s cobot sales have been trending towards heavier payloads. “Over the last three years, the UR10e and above have accounted for about half of our unit volume,” he said. “So it made sense to augment the product line at the high end.”
The Robot Report Inside the new joint design UR president Kim Povlsen said a new joint design is the key to the increased speed and torque. “We needed a new mechanical joint design to have more torque. We’ve been working on this for a while, and it’s hard to do. But it won’t take long for people to take apart the joint and see that it’s completely different inside.” On the UR20, the base and shoulder have a maximum speed of 120˚/s, while the elbow can move up to 150˚/s. The three wrist joints can move up to ± 210˚/s. On the UR16e cobot, for comparison, the base and shoulder offer a maximum speed of ± 120°/s, while the elbow and three wrist joints each have a top speed of ± 180°/s.“Wereduced the number of loose parts going into a robot joint by almost half,” said Anders Beck, vice president of innovation and strategy, Universal Robots. “From a quality engineering standpoint, just reducing part count leads to intrinsic quality improvements.”BecksaidUR also moved to a new encoder type on the UR20. “We even made encoder structures that grow with the joints. As the joints become larger, they often get placed further away from the tool flange. And that’s where accuracy matters the most in terms of repeatability. So this allows us to maintain good accuracy; the UR20 has similar accuracy to the UR10, and we might be able to supersede that when we’re ready to ship.
“Because we made this decision, it takes away concerns from customers that if they move into a different robot size it will behave differently or require different things to get the job done. We were quite deliberate in the engineering to make sure none of the design decisions we made came in the way of building robot applications that just work.”
Harmonic Drive®, Harmonic Planetary®, Harmonic Gearhead® and Quick Connect® are registered trademarks of Harmonic Drive LLC. Harmonic Drive LLC | 42 Dunham Ridge | Beverly, MA 01915 | 800.921.3332 | www.HarmonicDrive.net Servo Gearheads for AMR/AGV Propulsion
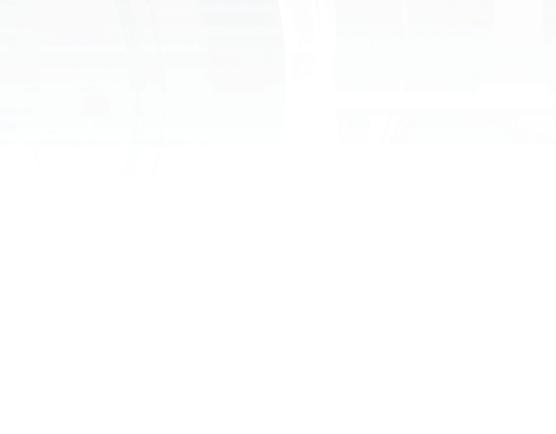
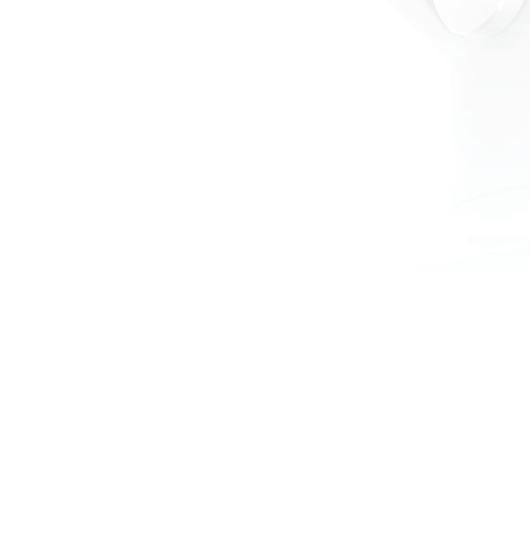
HPG Gearheads Low Backlash for Life
A Cross-Roller bearing is integrated with the output flange to provide high moment stiffness, high load capacity and precise positioning accuracy.
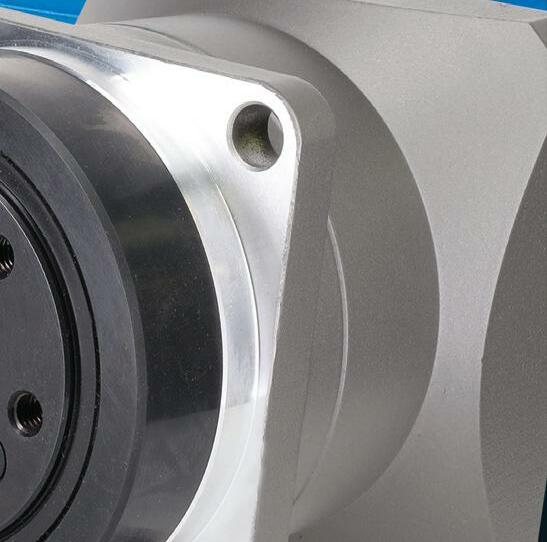
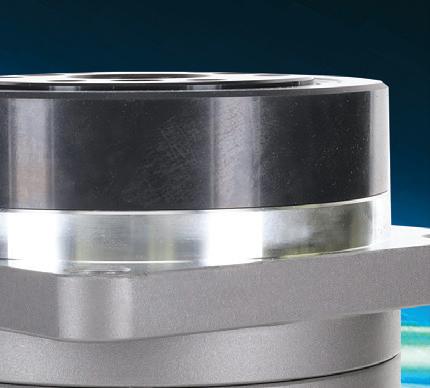
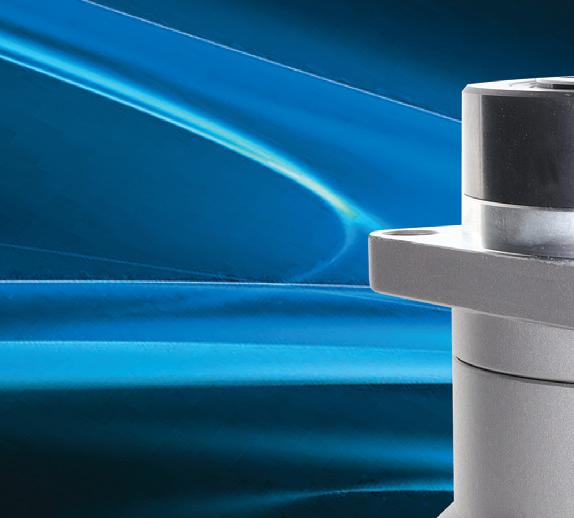
includes a clamshell style servo coupling and piloted adapter flange.
Innovative ring gear inherently compensates for interference between meshing parts, ensuring consistent, low backlash for the life of the gearhead.
Easy Mounting to a Wide Variety of Servomotors system
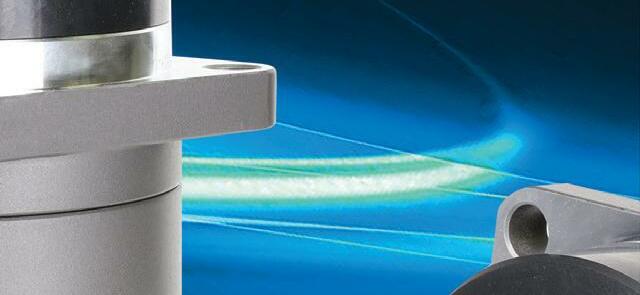
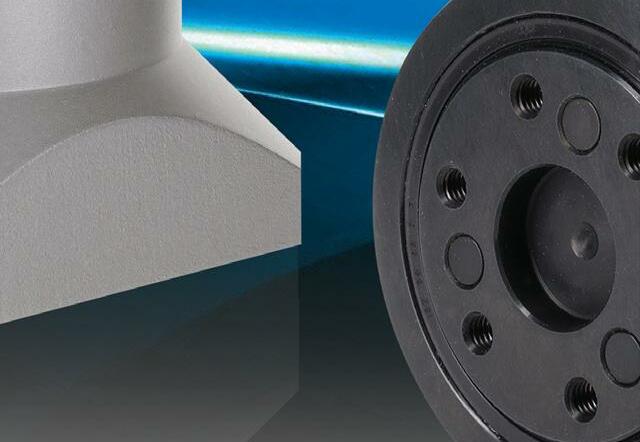
standard for convenient, stable wheel mounting. The Harmonic Gearhead® gearbox design allows for backdrivability while ensuring highefficiency performance, maximizing elapsed operational

High Efficiency Up to 95% Efficiency
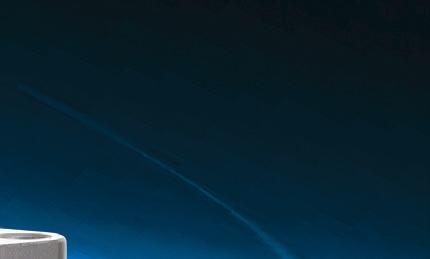
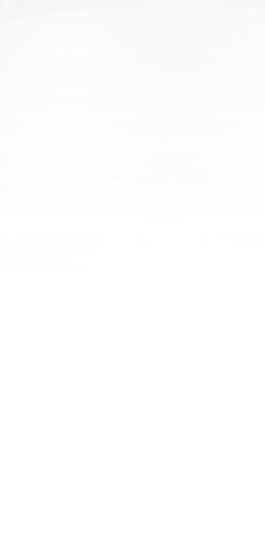
Quick Connect ® motor adaptation
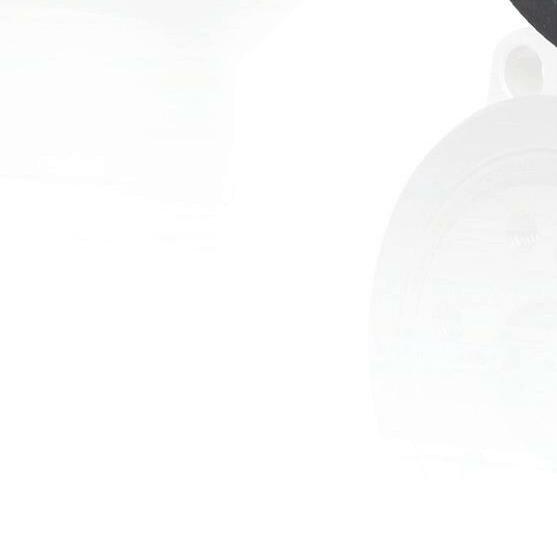

Flanged

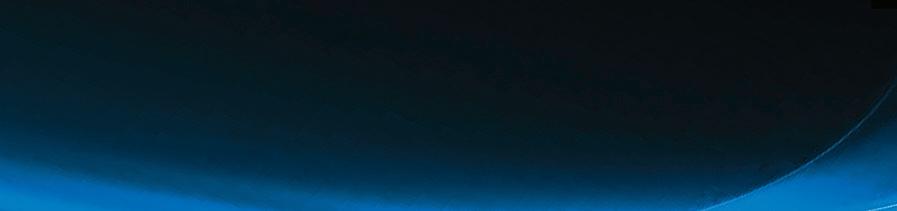
Flange Output Standard output is time
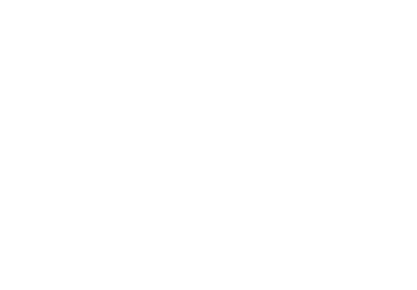

before recharging is necessary. High-capacity cross roller bearing supports heavy payloads.
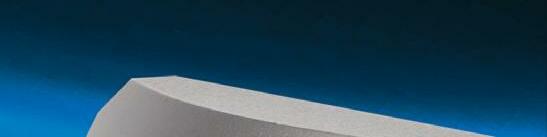
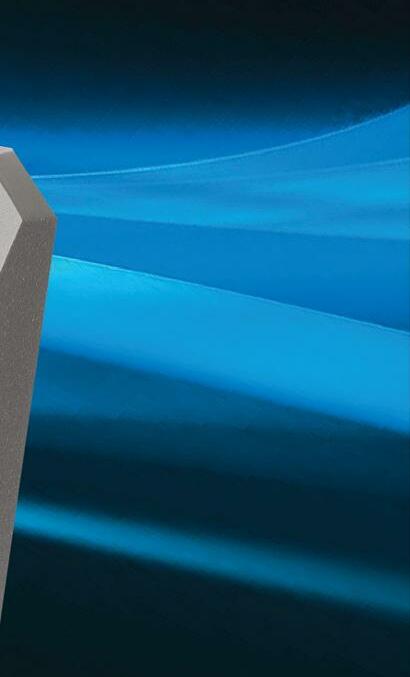
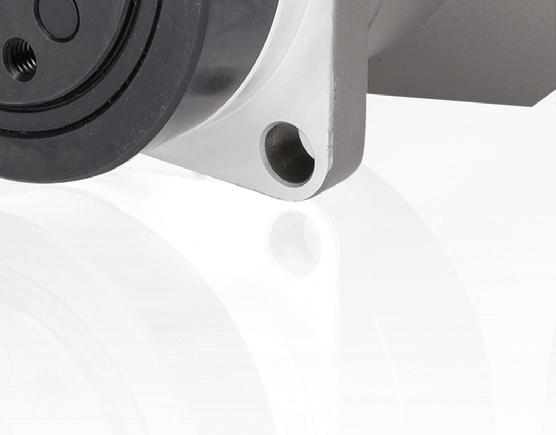
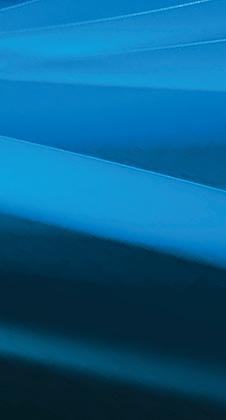
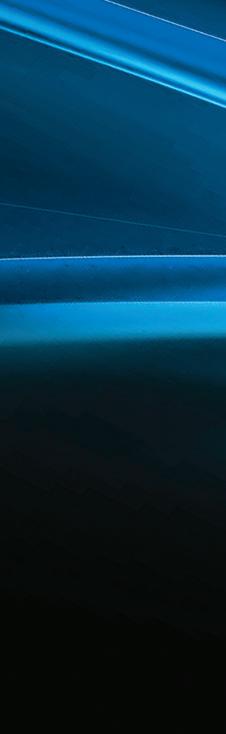
High Load Capacity Output Bearing
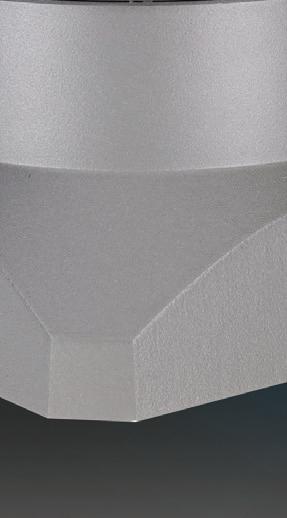
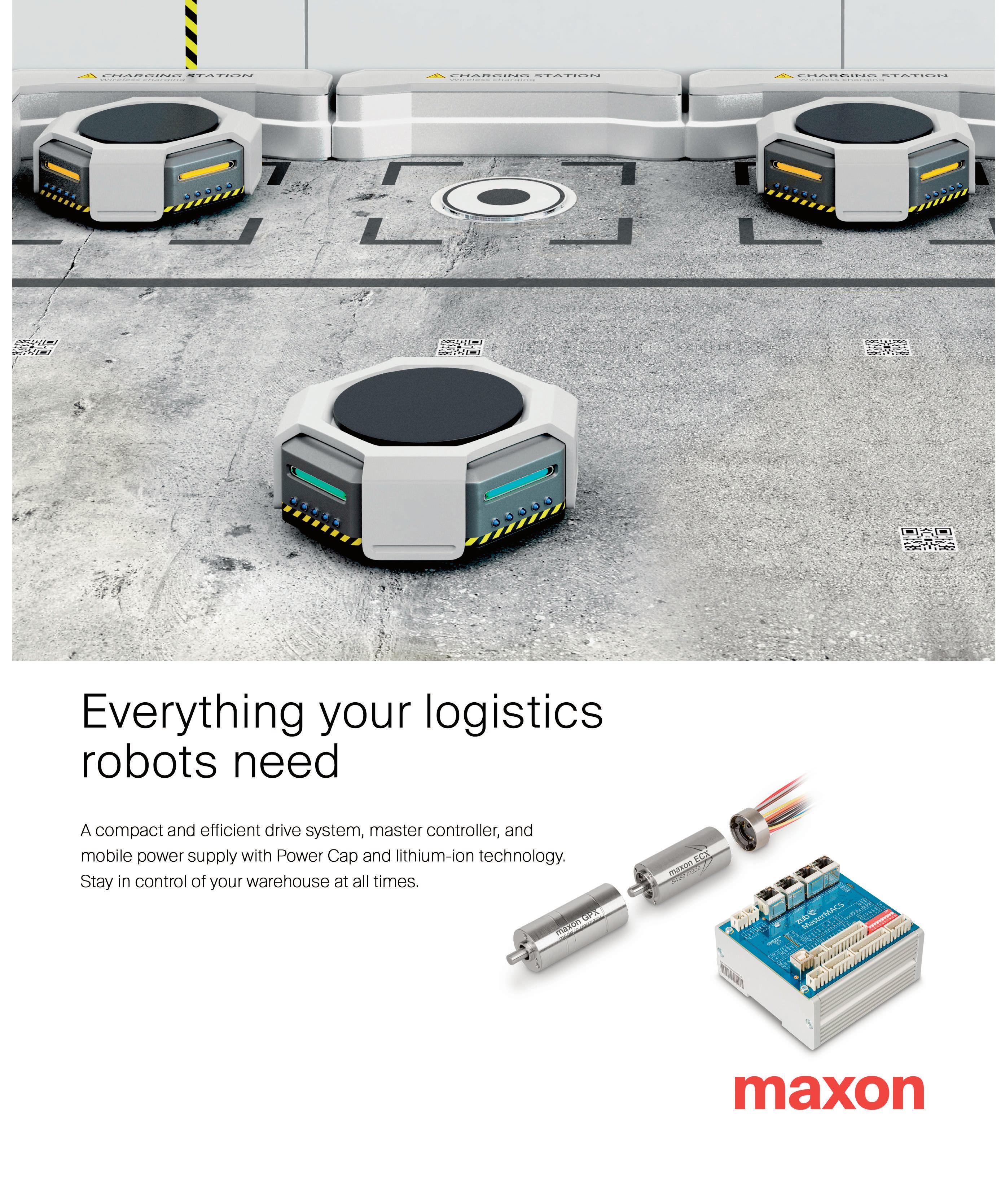
In the automation world, there can be a fine line between what is considered a motion controller and what represents a basic servo drive. It is critical to understand the functionality and intelligence of each device since, in many applications, both a motion controller and a servo drive are required to complete the system.
There can be a fine line between what is considered a motion controller and what represents a basic servo drive. It is critical to understand the functionality and intelligence of both. The Robot Report Staff
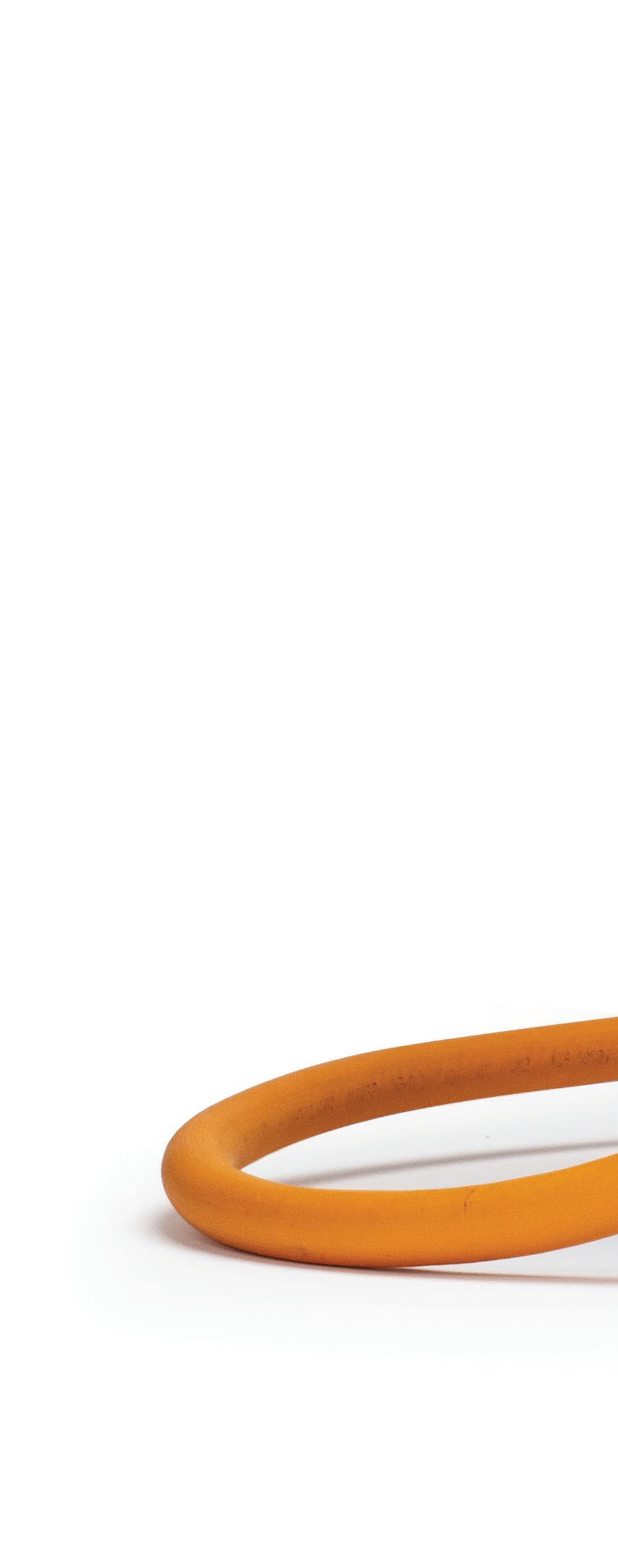
A servo motor is powered by a servo drive that supplies voltage and current to the motor coils and then monitors feedback to close the servo loop. In most cases, the servo drive consists of three embedded servo loops - the current (or torque) loop, velocity loop, and position loop - that interact with each other to create precision motion. The expected motor operation will determine which loops are required.
The Robot Report between a servo drive and motion controller?
The servo system
74 August 2022 www.therobotreport.com THE ROBOT REPORT
What’s differencethe
• Finally, a position loop application employs a feedback sensor coupled to the motor that sends position information to the servo drive or motion controller, which in turn signals the velocity loop to increase or decrease velocity, which then relays the information to the current loop to regulate torque.
Defining the drive and controller roles
• With velocity control applications, it is common to find both current and velocity loops. The velocity loop monitors a sensor that provides velocity information to the servo drive and then uses this data to adjust the current loop to increase or decrease torque.
|
In a torque control application of a brushless dc servo motor, a “device” supplies current and voltage to a motor based on a commanded input measured against the current feedback. The apparatus that provides the power to the motor is called, in proper terms, a servo amplifier or servo drive. A current or torque drive is useless unless it receives a specific command to tell it what torque to produce. The command can come from a variety of sources that essentially act as the “controller”. The command may be as simple as a person, functioning as a controller, Kollmorgen’s 2G Motion Systems consists of the AKD2G servo drive (left) and AKM2G servo motors. Kollmorgen
THE ROBOT REPORT www.therobotreport.com August 2022 75
• In a torque control application, which requires a specific torque, only a current loop is needed. Since torque is directly proportional to current, torque is regulated by a sensor that provides current feedback to the servo drive.

In a typical brushless dc servo system, three embedded loops with various compensation and filtering elements are present. | Kollmorgen
THE ROBOT REPORT
The Robot Report manually adjusting a potentiometer to apply a +/- 10 Vdc signal to the drive based on the desired output torque. In a typical brushless dc servo system, three embedded loops with various compensation and filtering elements are present. The inner loop (the current loop) is controlled by the velocity loop, which in turn is controlled by the position loop. The current loop always resides in the drive, while the velocity and position loops reside in either the drive or controller. The current loop uses a motor current sensor to measure current in the motor windings, while the velocity loop uses a speed sensor (typically an encoder) to measure motor velocity, which also provides position information to close the position loop. Motion controllers are microprocessorbased devices with complex algorithms that generate Pulse Width Modulated (PWM) waveforms. Power transistors within the servo drive transfer the current and voltage waveforms to energize the motor. The motion controller typically processes the feedback information from the various servo loops. Controllers use feedback information to commutate the motor to behave precisely as commanded by the microprocessor. In essence, the intelligence provided by the microprocessor acts as the controller, while the electronics associated with the power devices acts as the drive. Basically, a controller is the element that applies a specific command to a position, velocity, or current loop, while a drive provides the voltage and current to the motors as demanded by the controller.
The controller is typically a programmable device that stores and runs code provided by the programmer. Programming is developed in a variety of languages, such as BASIC, C+/C++, VB, and languages specified in IEC 61131-3 standards. Controllers have numerous safety elements to prevent overloads or stop motion in the event of component failures. Drives, on the other hand, tend to focus on receiving the input commands of the controller and switching the power transistors on and off. This creates the current and voltage required to meet the commanded torque and speed. With advances in microprocessors and new switching devices, controllers and drives are becoming more and more intertwined - mostly in centralized systems where all electronics are colocated in a single control cabinet. In decentralized solutions, the motion controller resides in the cabinet while the drives are collocated near the motors and communicate with the centralized motion controller through a motion field bus. RR 76 August 2022 www.therobotreport.com
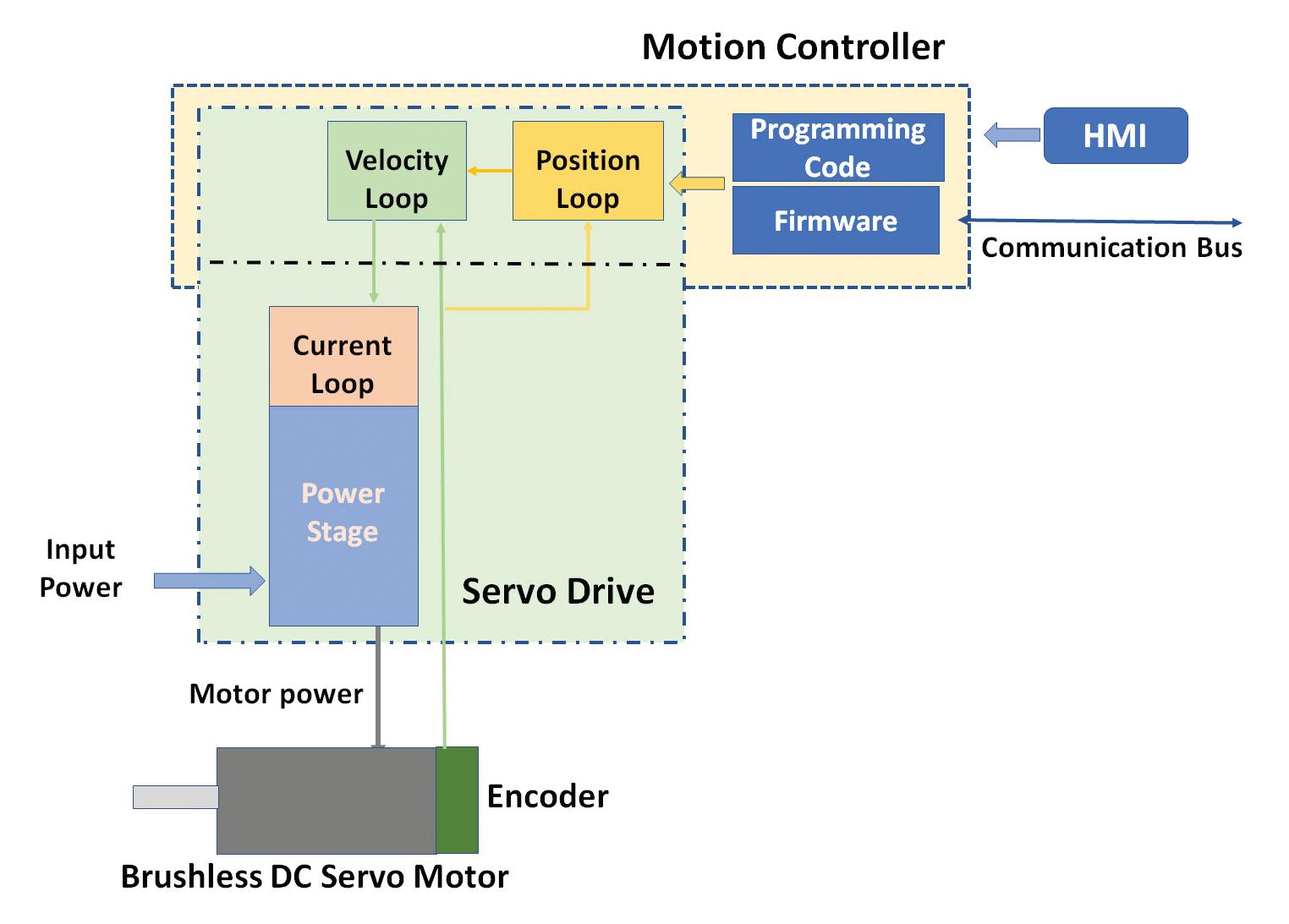
CGI Motion standard products are designed with customization in mind. Our team of experts will work with you on selecting the optimal base product and craft a unique solution to help di erentiate your product or application. So when you think customization, think standard CGI assemblies. Connect with us today to explore what CGI Motion can do for you. copyright©2021 cgi inc. all rights reserved. YOUR CUSTOM SOLUTIONS ARE CGI STANDARD PRODUCTS Advanced Products for Robotics and Automation 800.568.GEAR (4327) • www.cgimotion.com
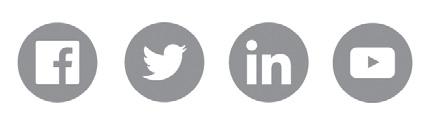
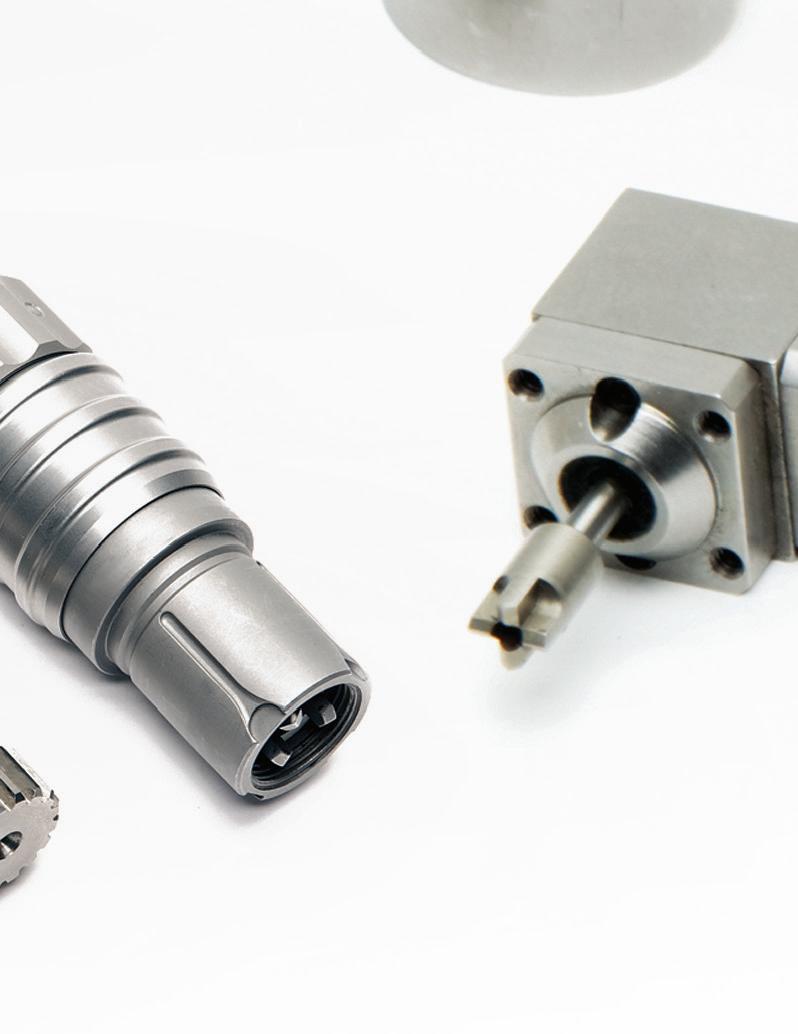
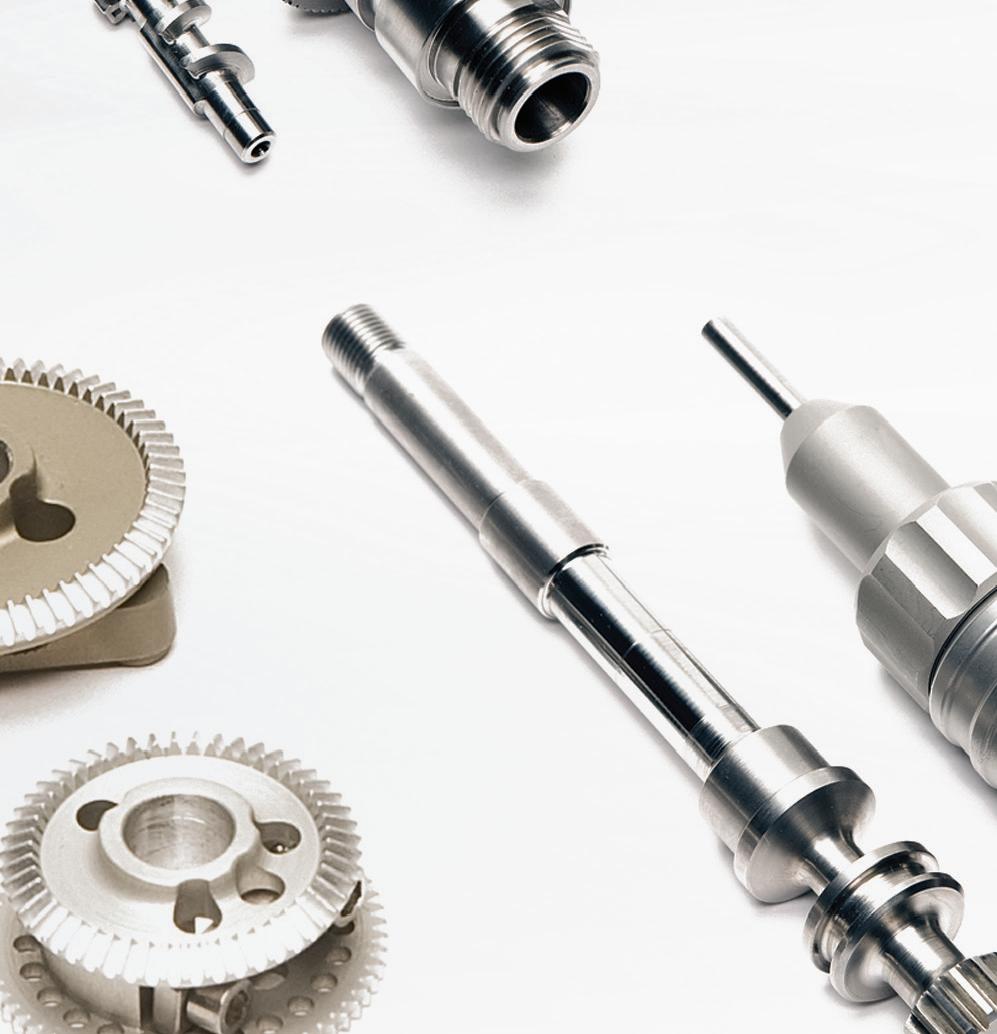

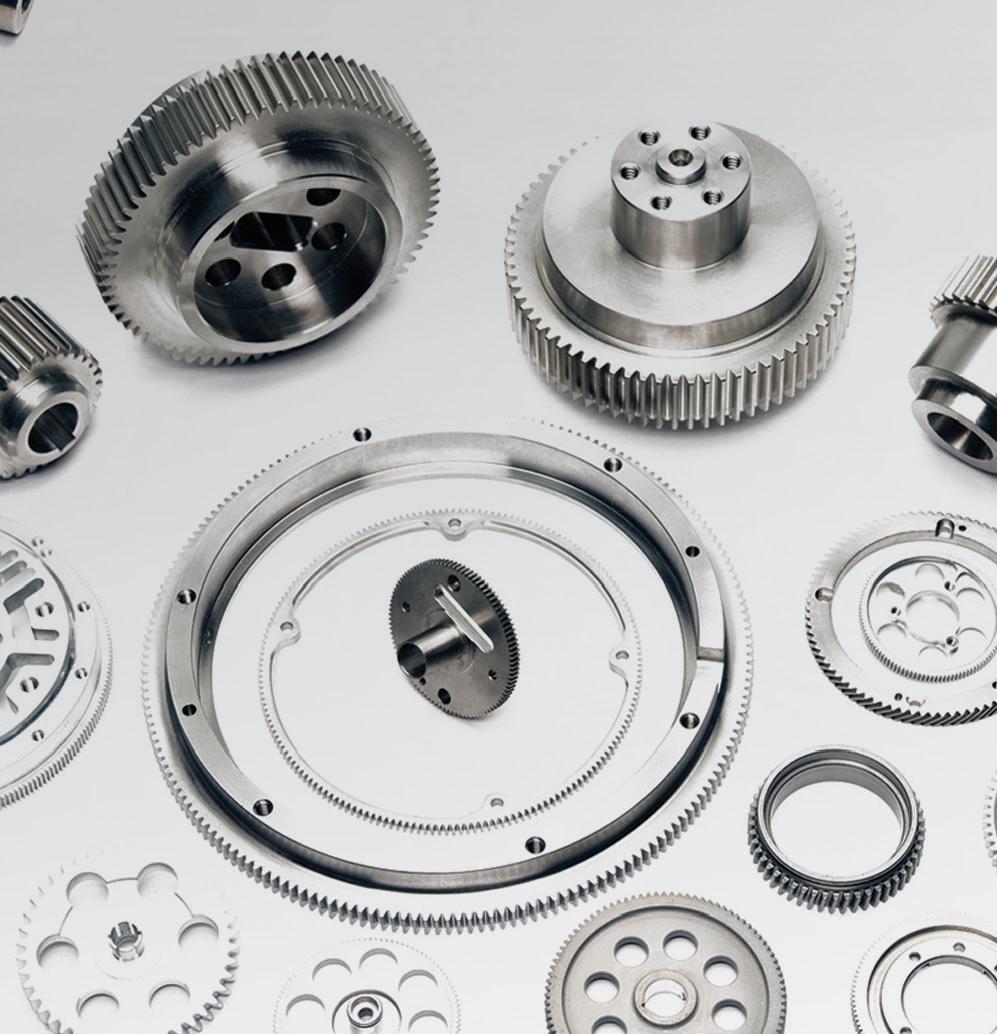
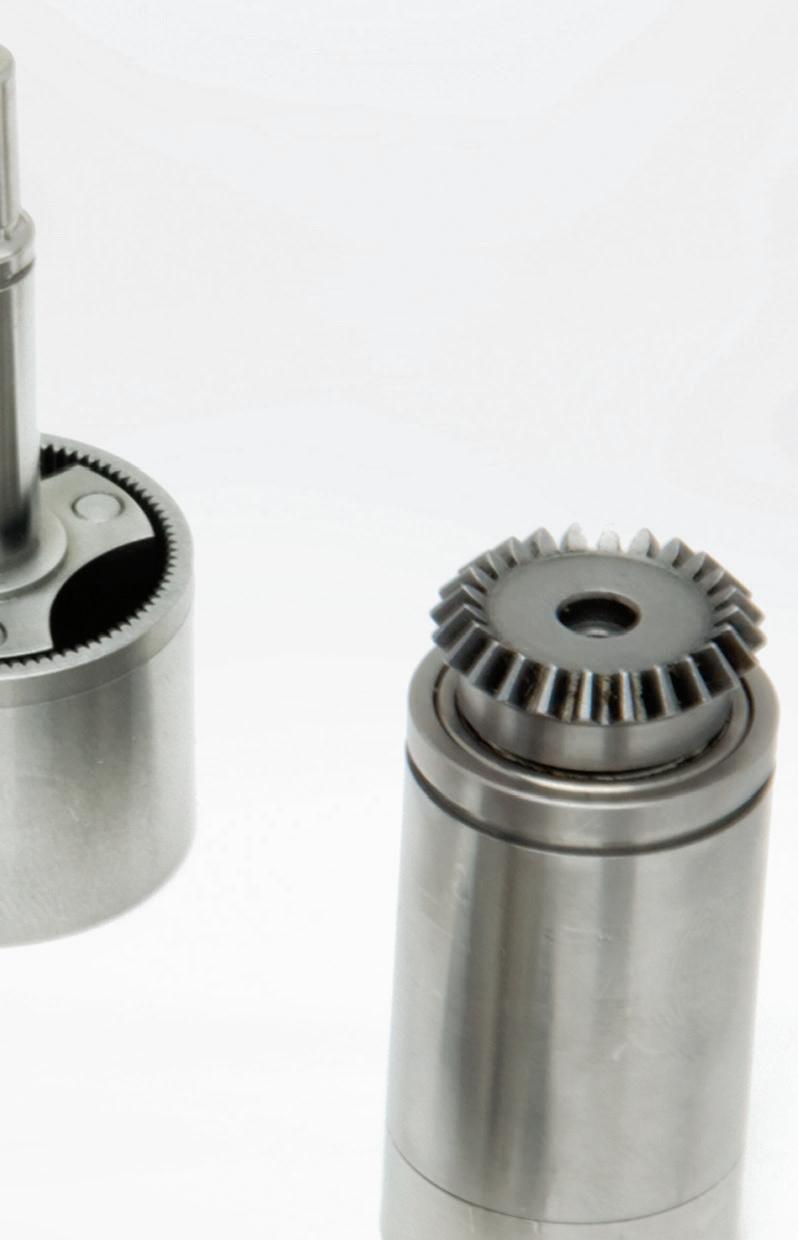
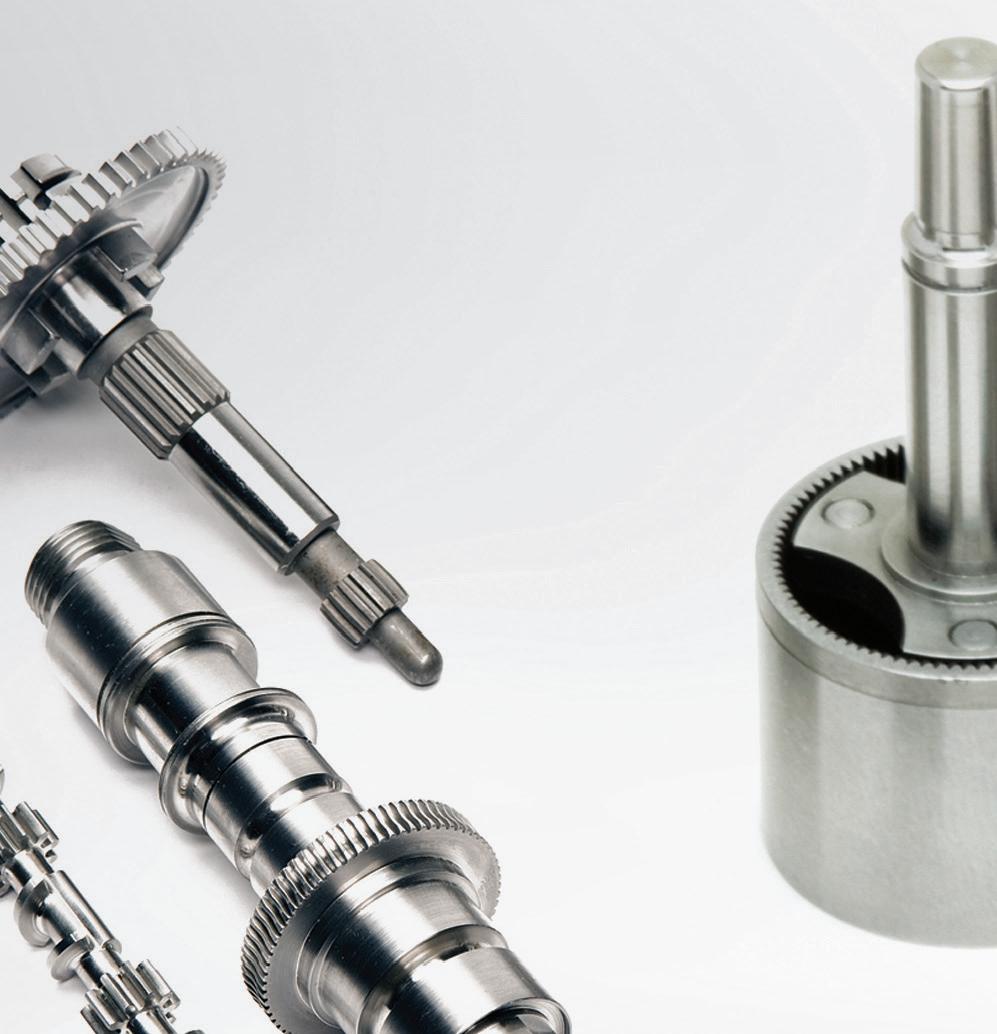
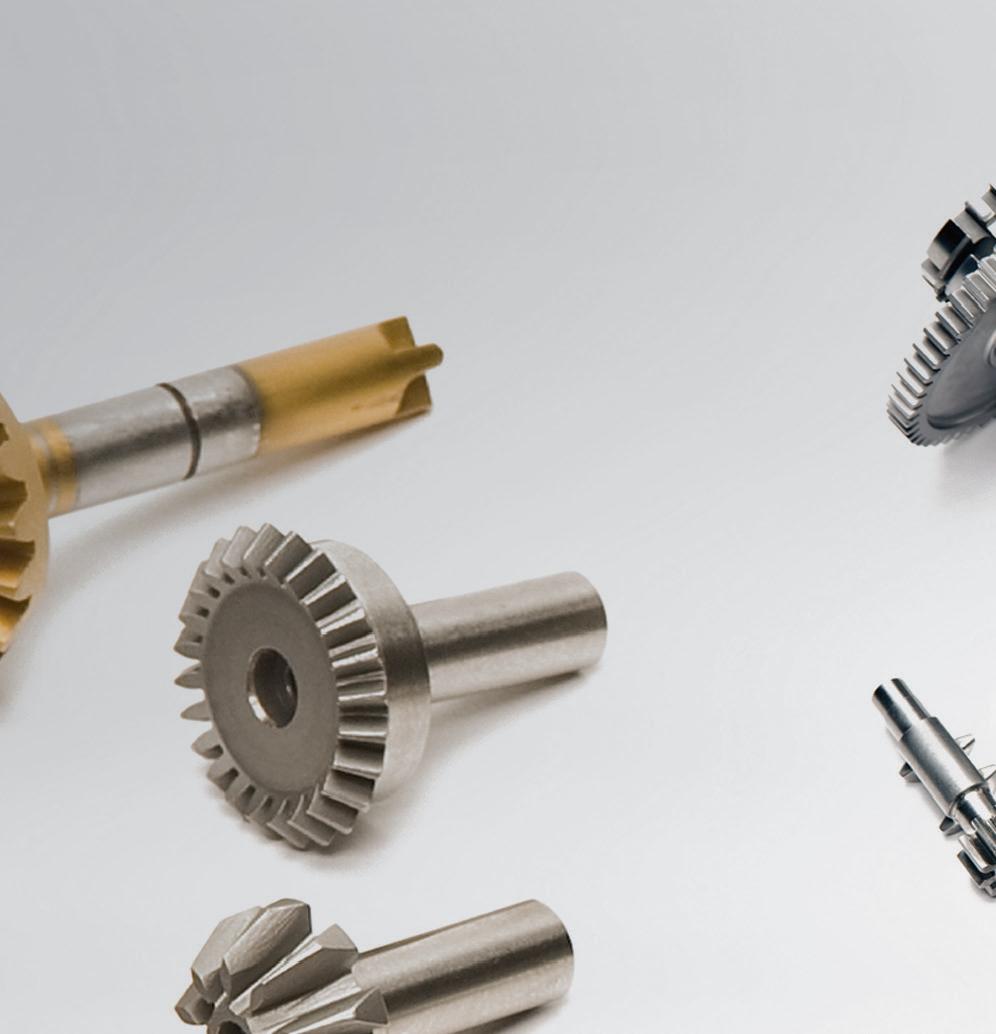
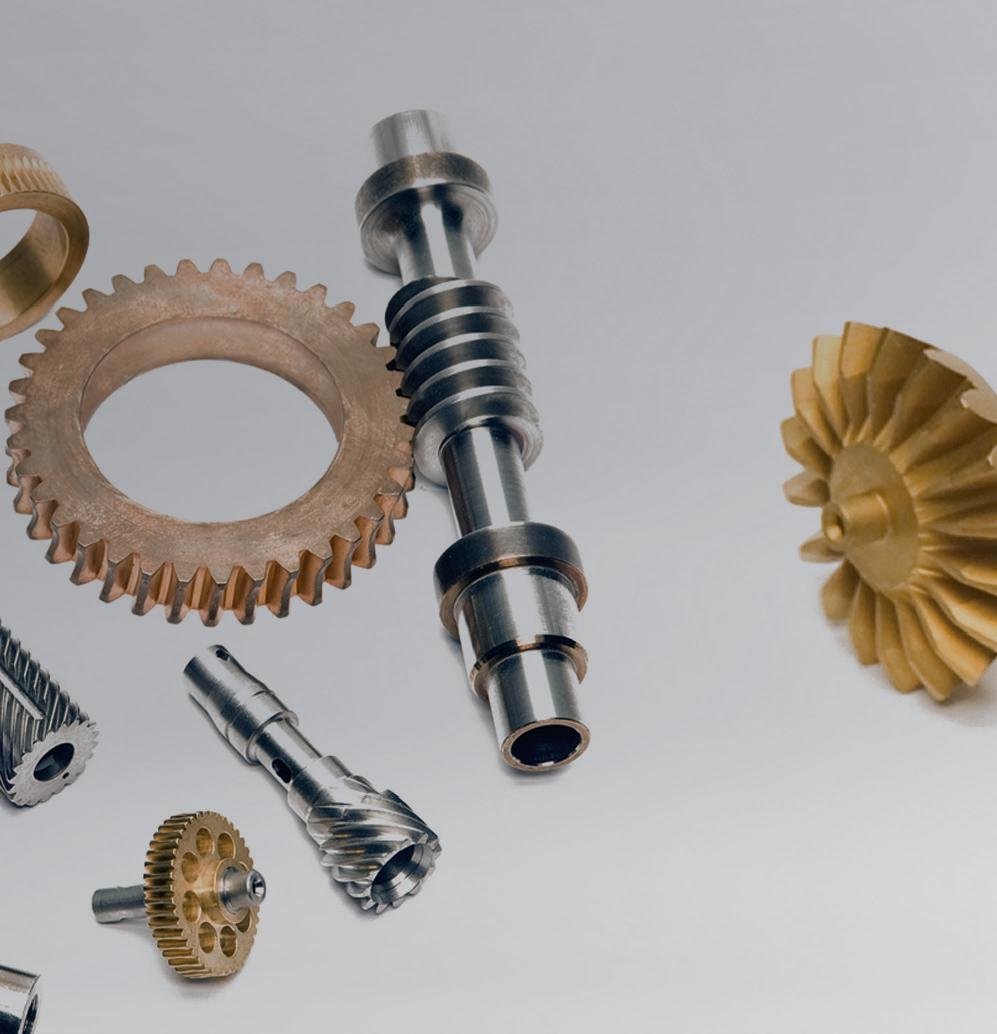



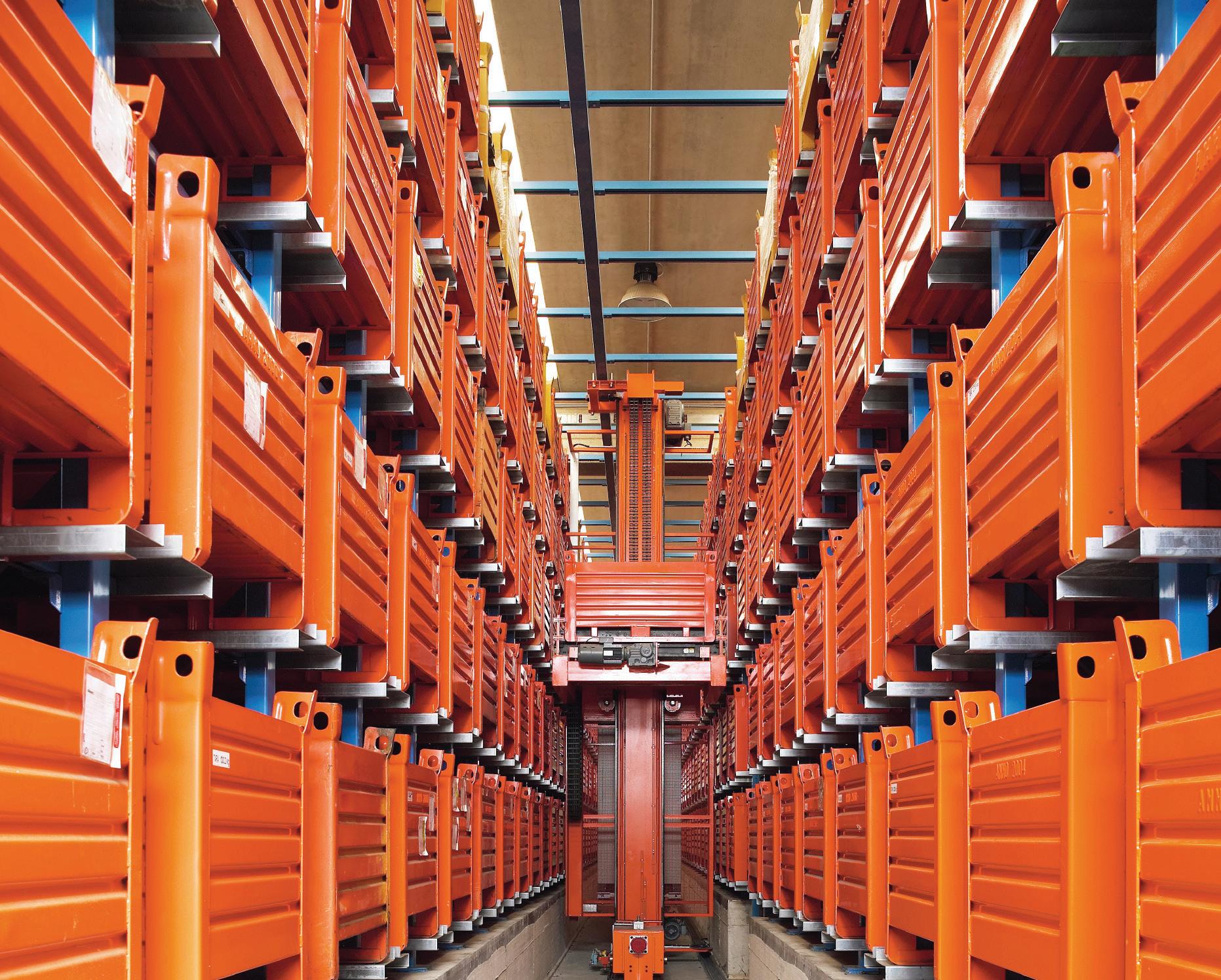
78 August 2022 www.therobotreport.com THE ROBOT REPORT The Robot Report precise AMRssystemsmotiondrive How Selecting the correct motor is critical to overall performance for autonomous mobile robots. Pradeep Deshmane and Manoj Pujari | Portescap
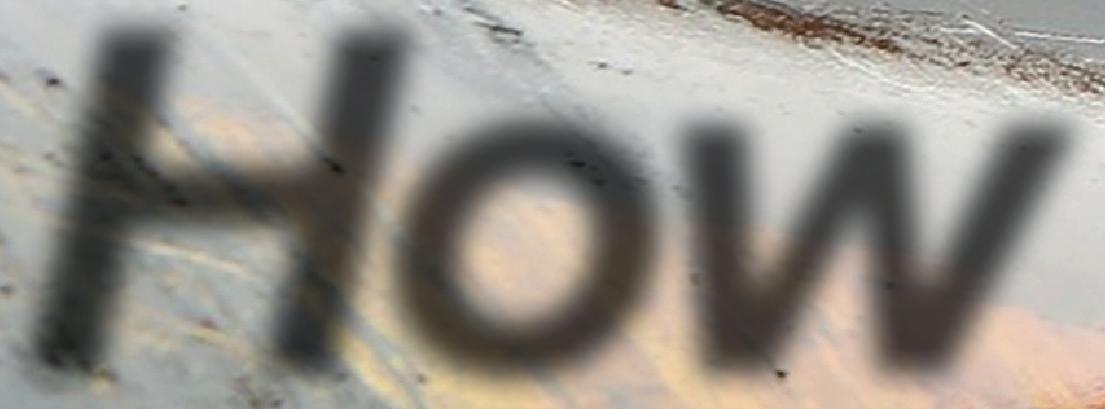

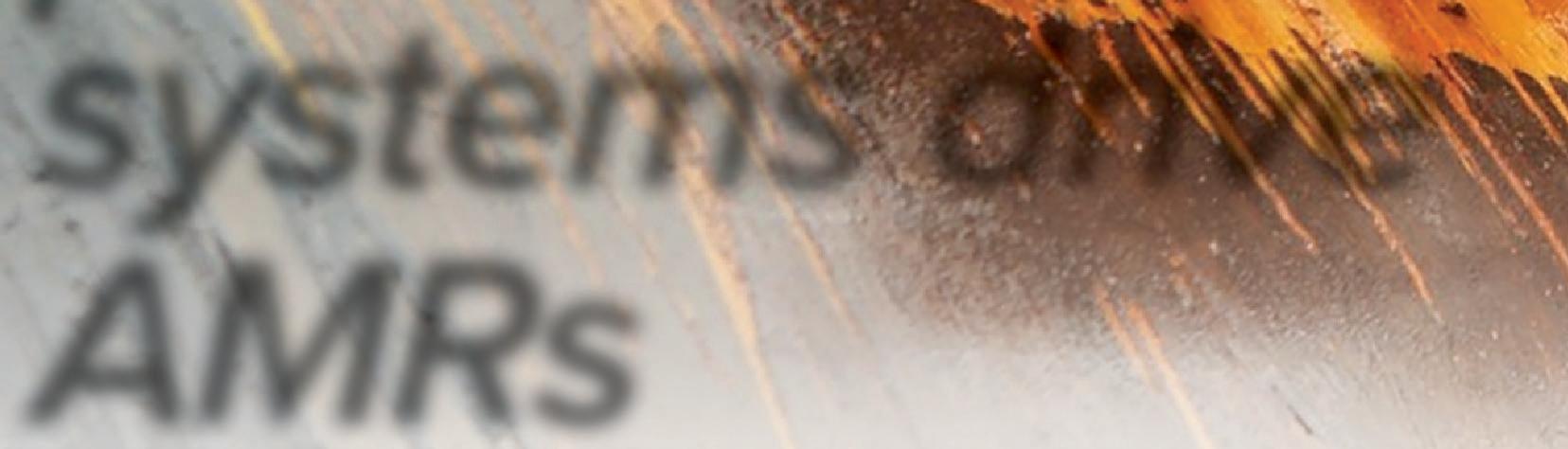


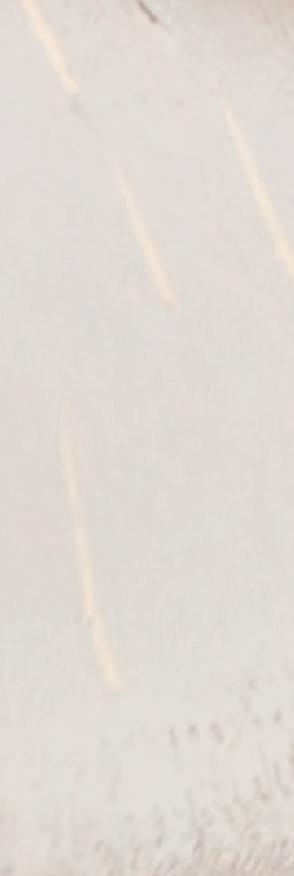
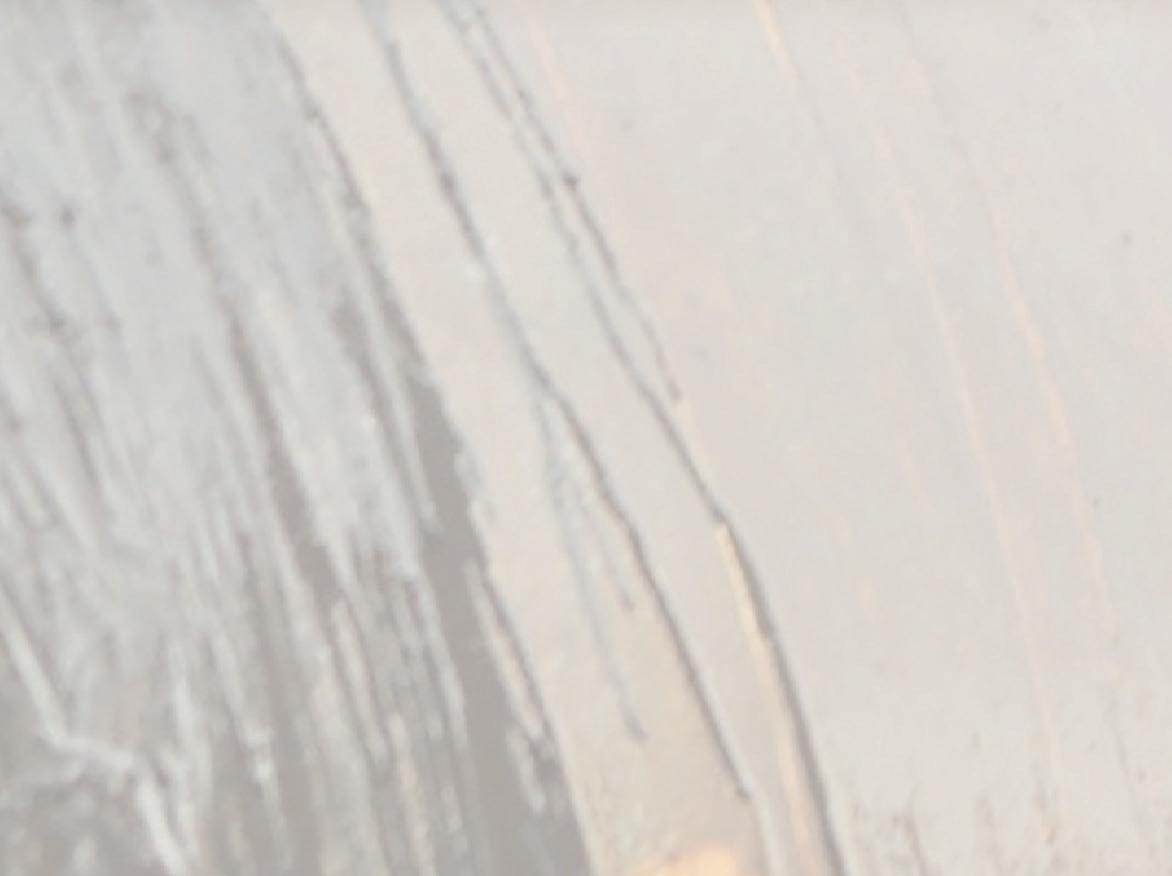
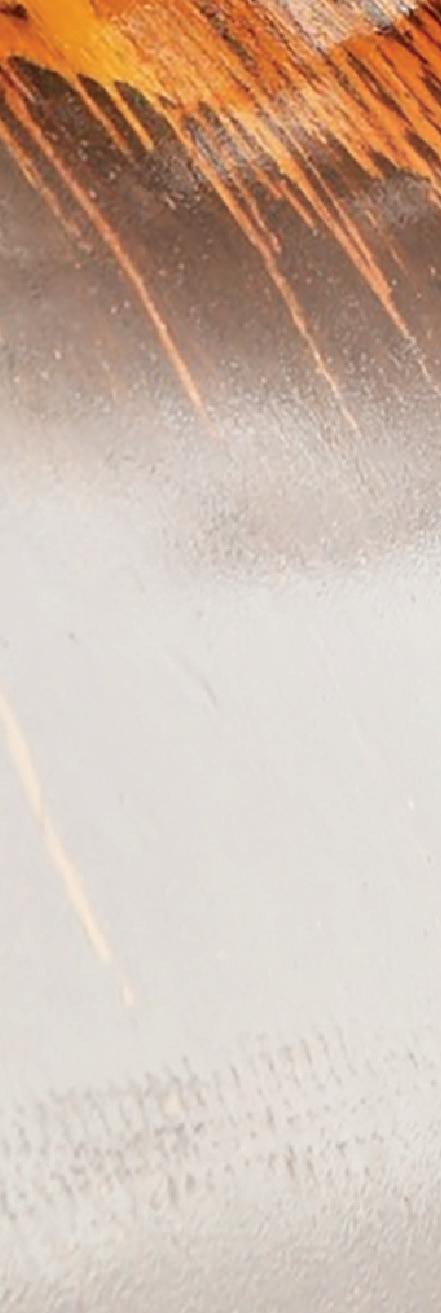

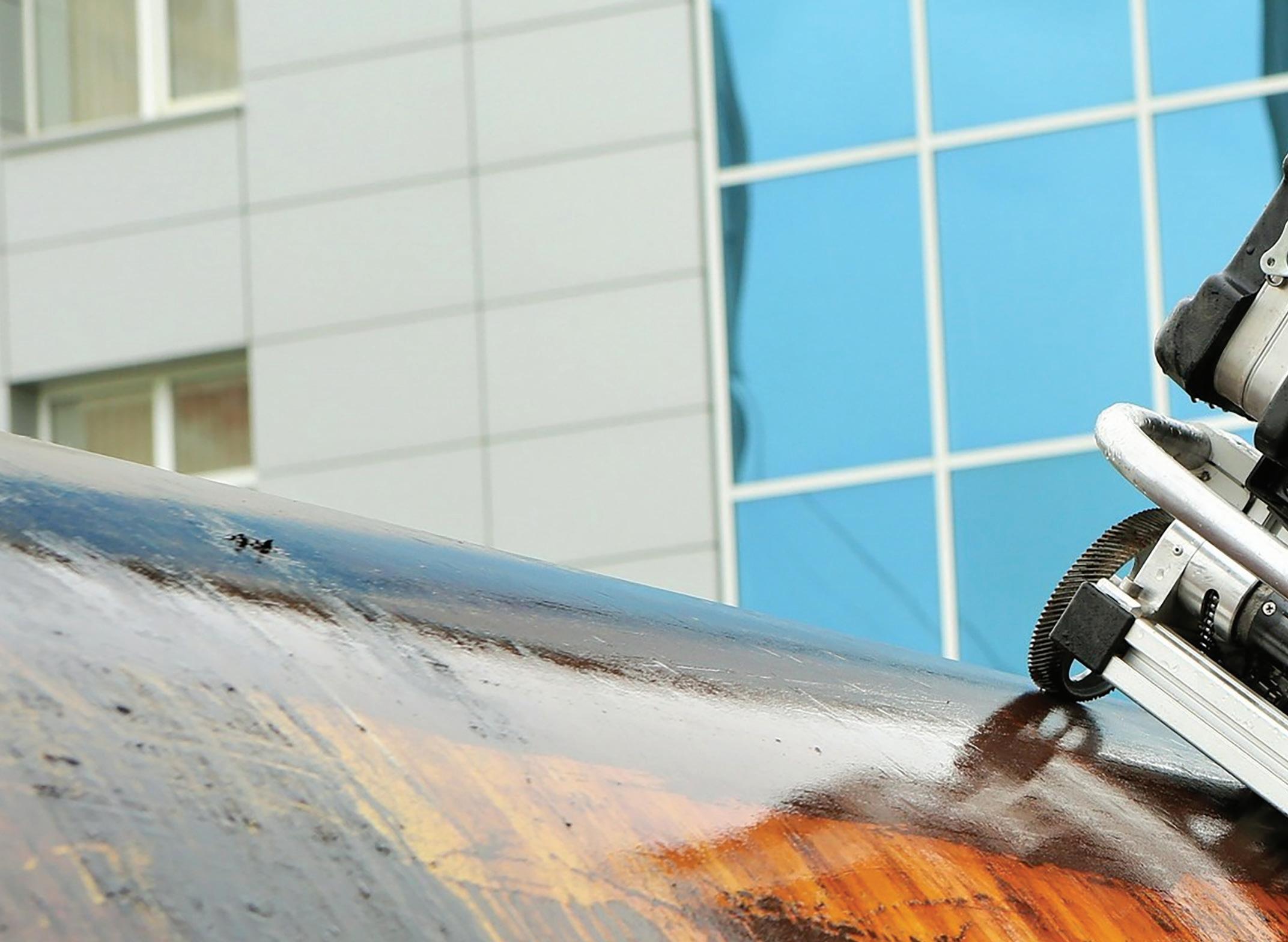
Shutterstock.com
program for movement in flat, not-so-rugged terrain. They are particularly popular in the logistics market. The motion system consists of motors coupled with gearboxes driving the wheels, which increases the torque capacity for better drivability.
AMRs can also be found in hospitals performing infection control, medical services, medical waste delivery, biochemical specimen delivery and general medical tasks. They’re also being deployed in the worldwide fight against the COVID-19 pandemic.
THE ROBOT REPORT www.therobotreport.com August 2022 79
Whether moving or positioning objects, accessing dangerous environments, handling hazardous materials like medical waste or simply helping out around a warehouse, there is a tremendous demand for autonomous mobile robots (AMRs). Not only do they perform tasks that are di cult, repetitive or inconvenient for human labor, they carry them out correctly and are especially effective where precision is required.
This article provides an overview of AMRs, describing their operation, market need and demand, application requirements, selection criteria, design optimization and future advancements. Autonomous mobile robot applications AMRs navigate on the ground using motorized wheels to propel themselves. Unlike robots that use treads or legs, AMRs are easier to design, build and
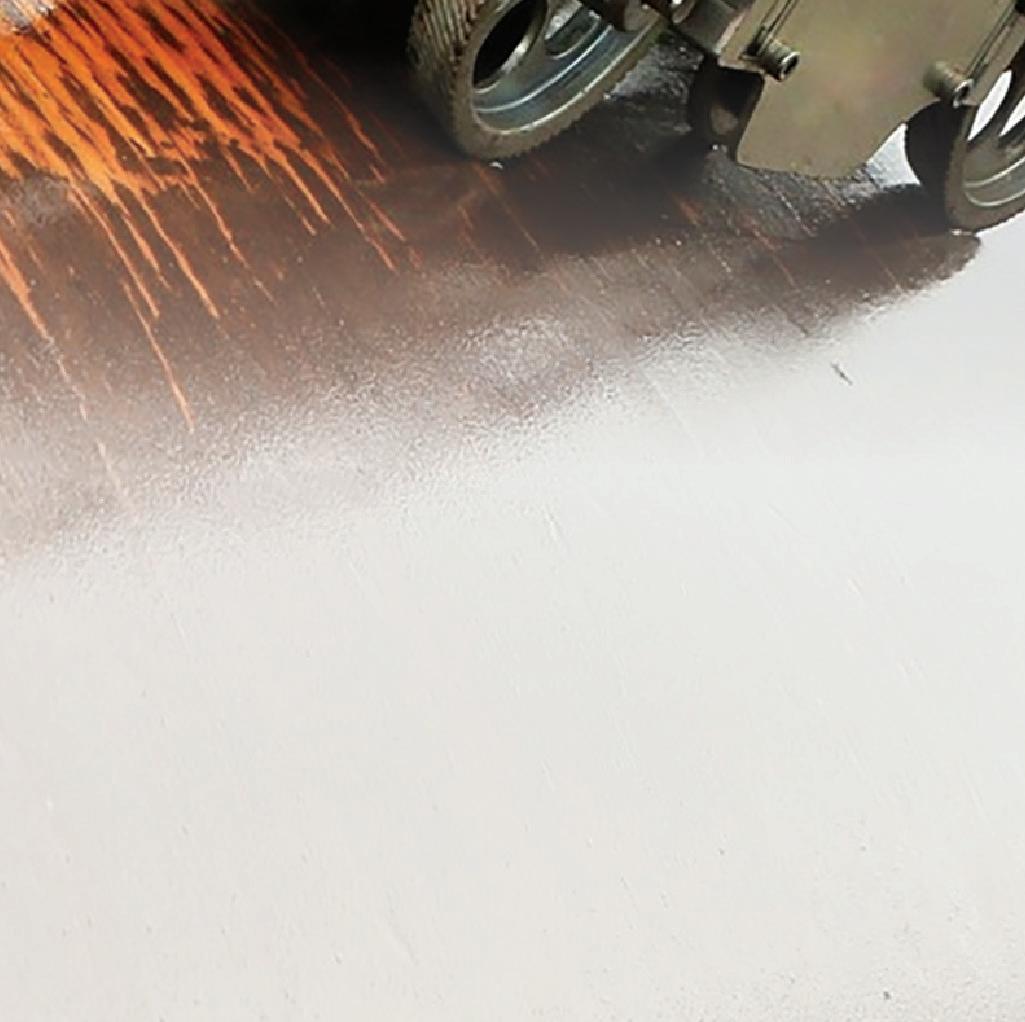
Another growing market is in the aerospace and defense (A&D) industry where robots play a crucial role in surveillance and military operations. In the oil and |

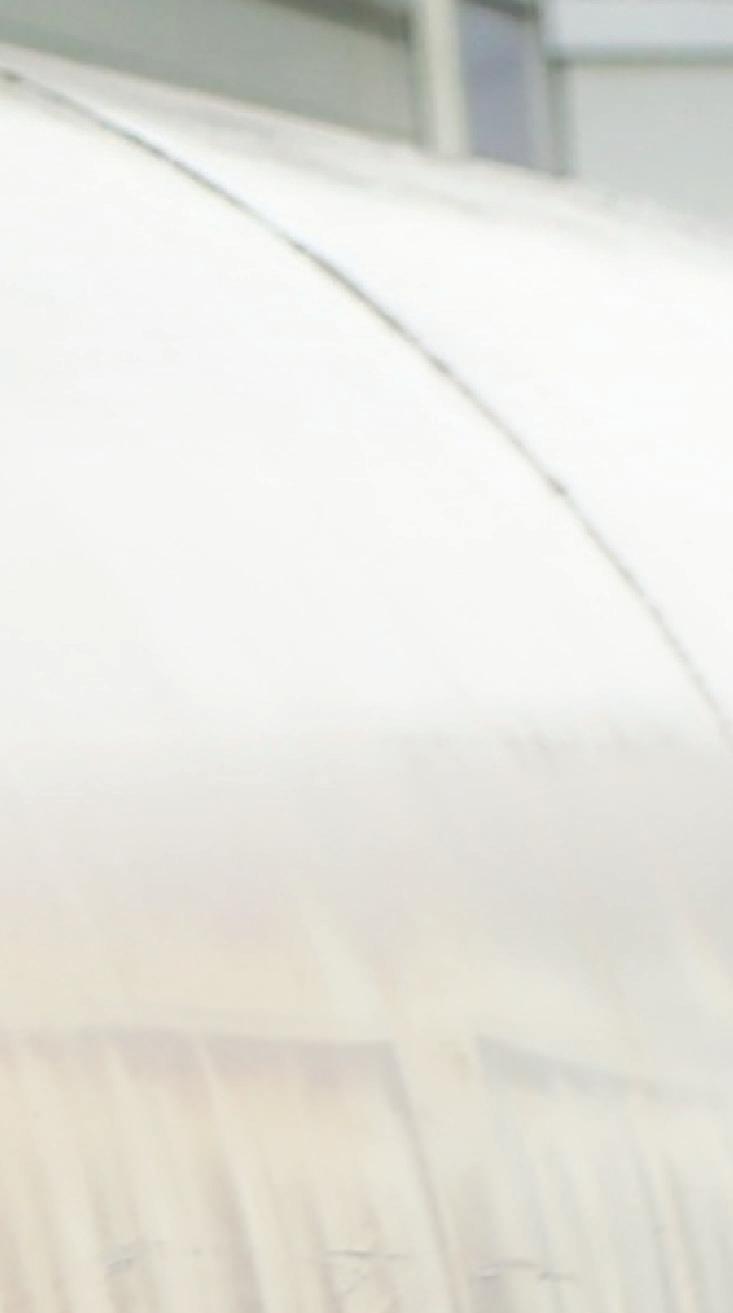
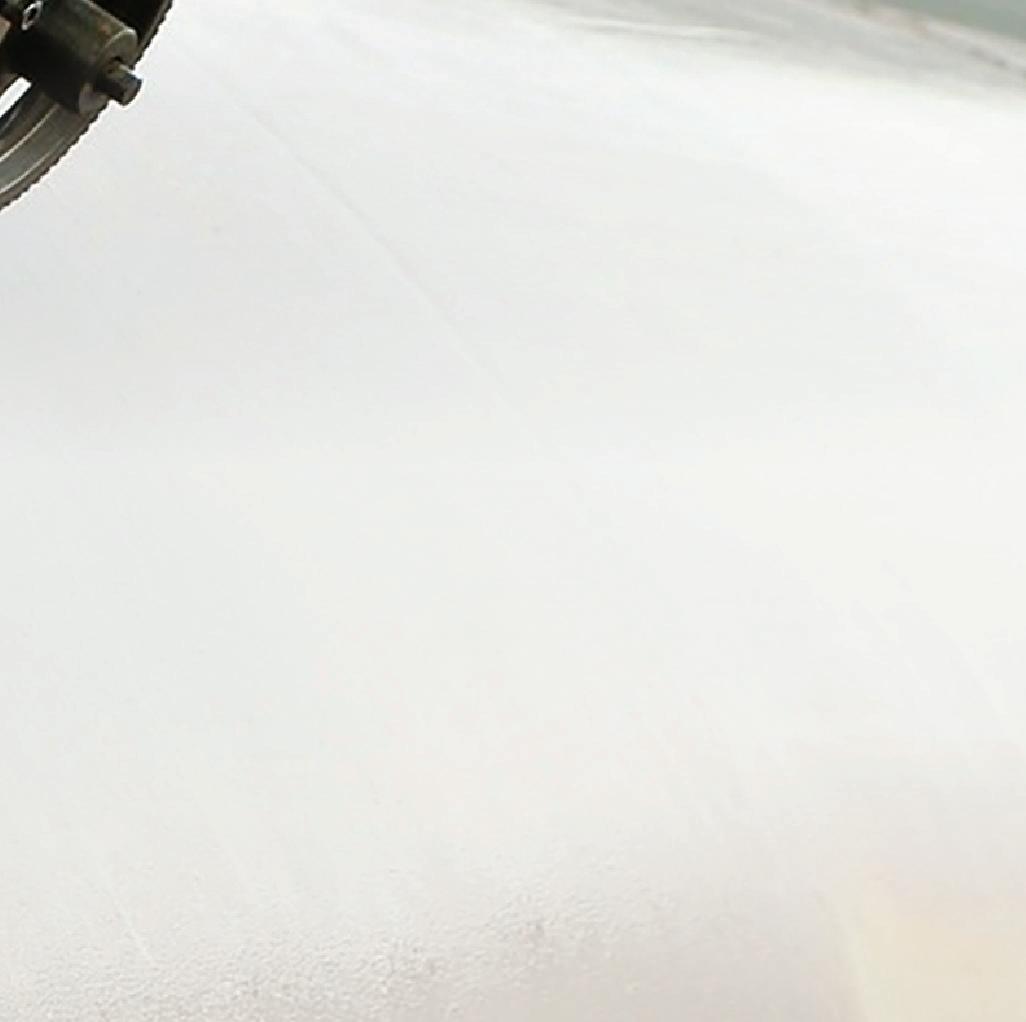

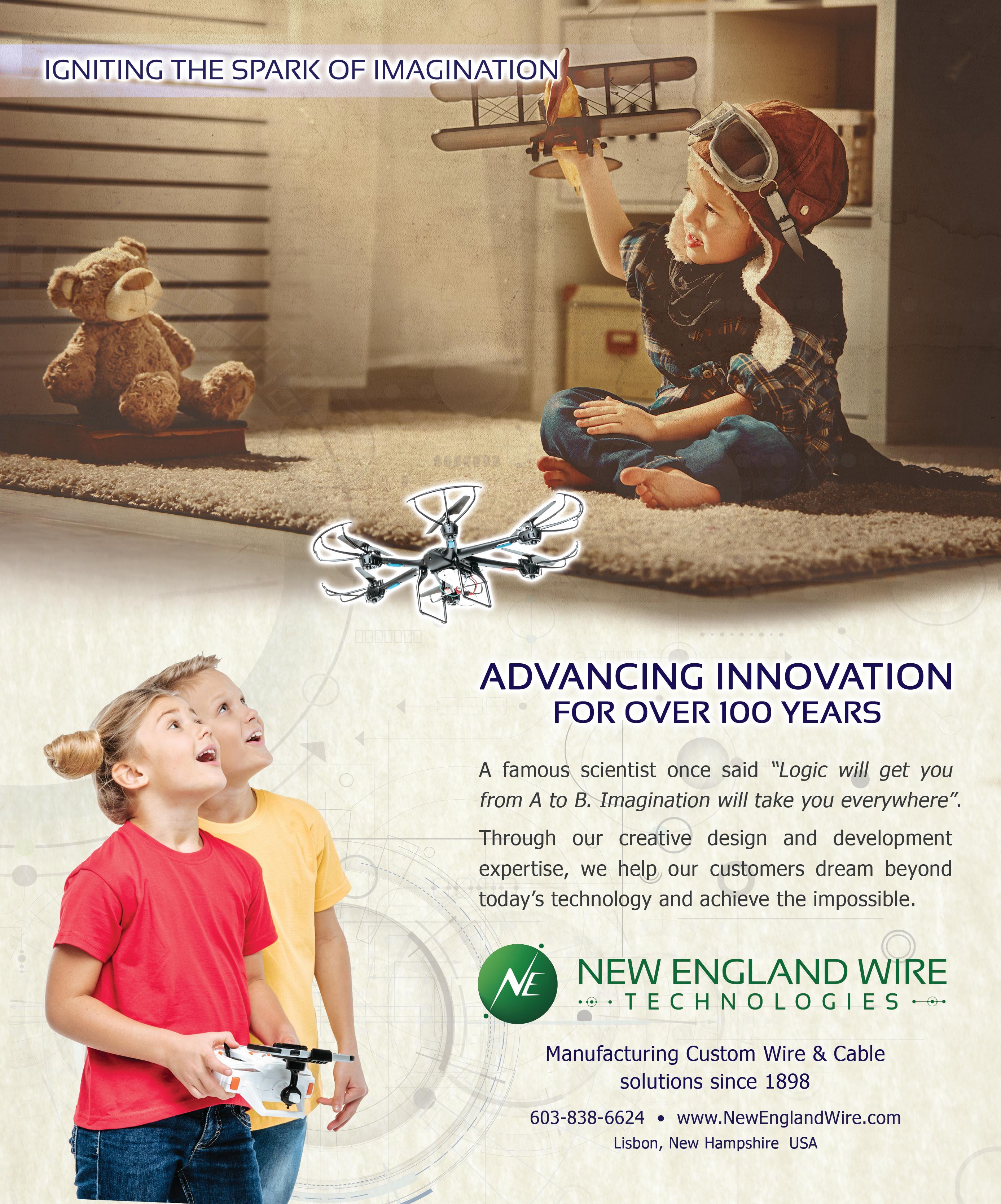
In most applications, the motion systems typically must satisfy the following: • Compact size and lightweight • High torque • Durability and long life • Low noise, especially when used in medical and A&D equipment • High efficiency and low current. Motion systems in AMRs usually consist of brushed or brushless DC motors coupled with compact planetary gearboxes. This requirement may differ slightly from application to application, but the motion systems typically have the following specifications:•Motor:coreless brushed DC or brushless DC motor
Important aspects to consider when selecting a motor and gearbox for an autonomous mobile robot design. | Portescap Torque
Application requirements
Precision, accuracy and efficiency: How much lag can you afford in your gearing? Often, wheel motor robot applications can allow a little less precision and accuracy depending on the terrains and torque profiles involved. And, since not all applications
Selection criteria
Weight: The mass of the load also determines the torque for motor selection. Therefore, you will need to estimate the mass, or know the actual mass, to choose a motor. If you base your design on a mass estimate, we recommend applying a 25 percent safety margin. Refer to the torque constant provided on the motor datasheet to calculate how much torque output you will achieve per amp.
THE ROBOT REPORT www.therobotreport.com August 2022 81
• Gearbox configuration: planetary; ⅔ stage, 30:1 to 120:1 ratio • Packaging size: <40 mm2 • Gearbox output torque: 4 to 8 Nm • Gearbox output speed: 50 to 150 rpm
Torque: First, determine the output torque required and then work backwards to find your motor and gearing. The torque on the wheel should be based on robot acceleration, wheel diameter and carrying capacity. Be sure the carrying capacity accounts for pulling the entire robot in case some actuators fail or wheels slip, as well as the minimum slope and potential obstacles to overcome. Friction and efficiency also should factor into the final torque calculation. Speed: To calculate the speed at which the wheel needs to rotate, you must define your desired speed - or final output - for the wheel. Based on that information, you can choose the motors and gearing. The robot manufacturer generally finalizes the robot’s drive speed, and the wheel diameter determines the required speed at the wheel output.
Packaging space: Make sure the motor stack, which consists of the encoder, brake, motor and gearing, fits into the robot and can be packaged cleanly. The encoder allows you to measure how much the motor shaft turns, and the brake system helps to hold the torque and provide dynamic stopping in case of an emergency.
Operating temperature: Although temperature often is not an issue, it is still important to make sure your motor stack does not overheat — particularly if it is enclosed. The gearbox is another area of concern since temperature can affect its lubrication life and performance over time.
Cost: While building a gearbox from scratch may be less expensive, the time and effort required to design, assemble and test the new gear can make a standard gearbox the more economical option.
VoltagePrecision/Accuracy/Efficiency Packagingspace
The first step in selecting a motor and gearbox is to determine both the product’s operating and maximum conditions. Therefore, you will need to confirm the required speed and torque experienced at the wheel output.
Motor+GbxSpeedandselectioncriteriaReliabilityandNoiseCost Operatingtemp
Weight
Voltage: The operating voltage is used to power the motor. Typically, the higher the voltage, the higher the speed capability of the motor. The motor’s datasheet will provide the voltage constant - also known as back EMF constant - so you can calculate how fast the motor will rotate per volt.
The Robot Report gas (O&G) industry, they are expected to be invaluable tools in pipeline inspections thanks to their ability to photograph the interior of the structures to help identify cracks or faults.
Meeting Customer Needs with Diverse Product Categories and Customized Products Linear Piezo Motor DC Brushless Servo Motor Canon Precision proprietary technology and internal production systems provide our partners with micro-motor design flexibility, quality control and rapid delivery. Canon Precision motors can also be equipped with optional gear units and encoders and can be optimized to meet your size, speed, gear ratio and reliability requirements. CANON U.S.A., INC. Motion Control Products 3300 North 1st Street • San Jose, CA 95134 TEL: 1-408-468-2320 • Email: motors@cusa.canon.com www.usa.canon.com/ Canon is registered trademark of Canon Inc. in the United States, and may also be registered trademarks or trademarks in other countries. All other referenced product names and marks are trademarks of their respective owners. Specifications and availability subject to change. Not responsible for typographical errors. ©2021 Canon U.S.A., Inc. All rights reserved.
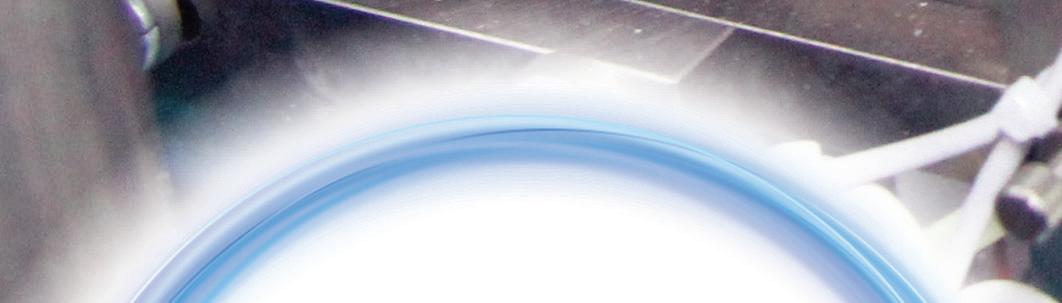
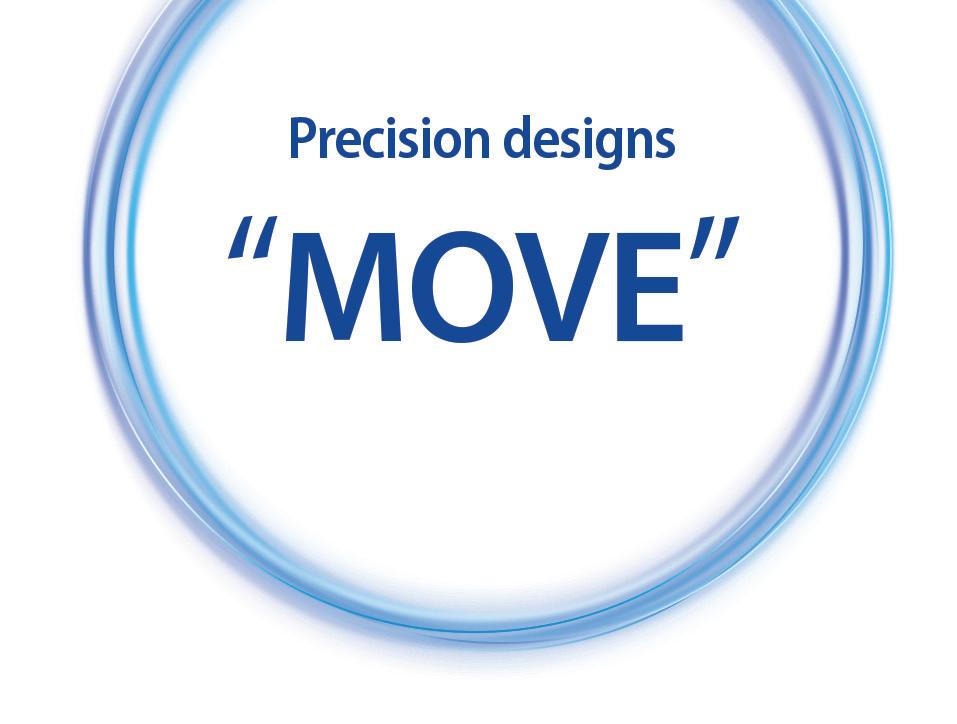
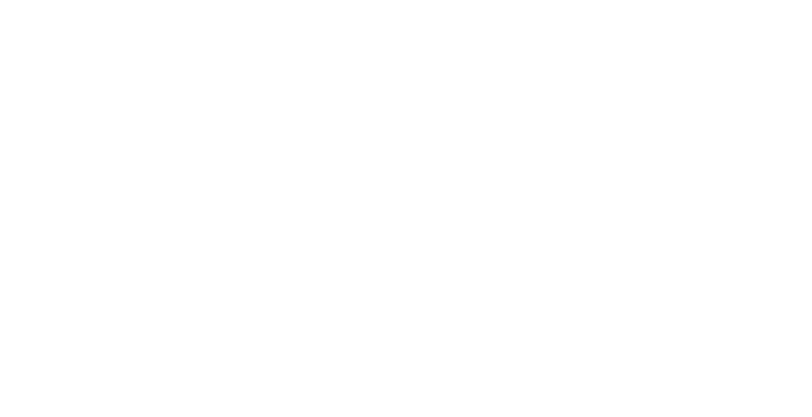
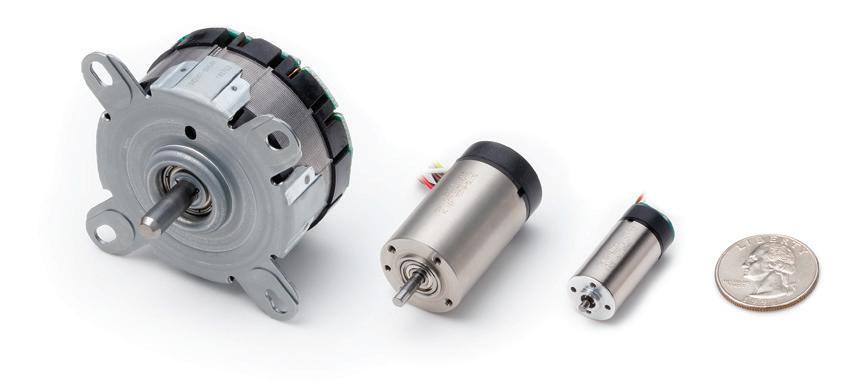

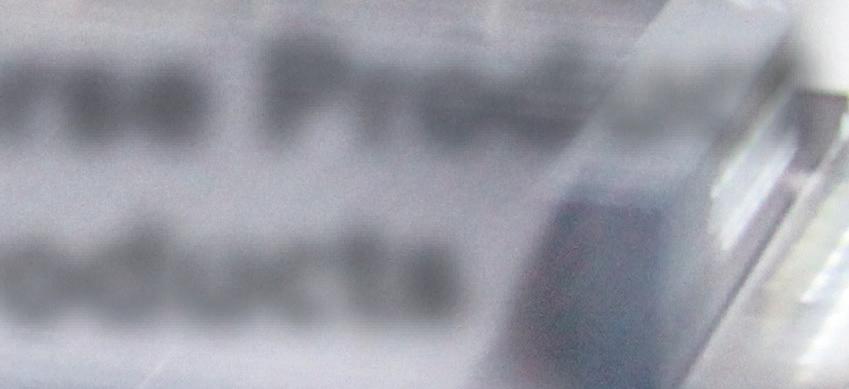

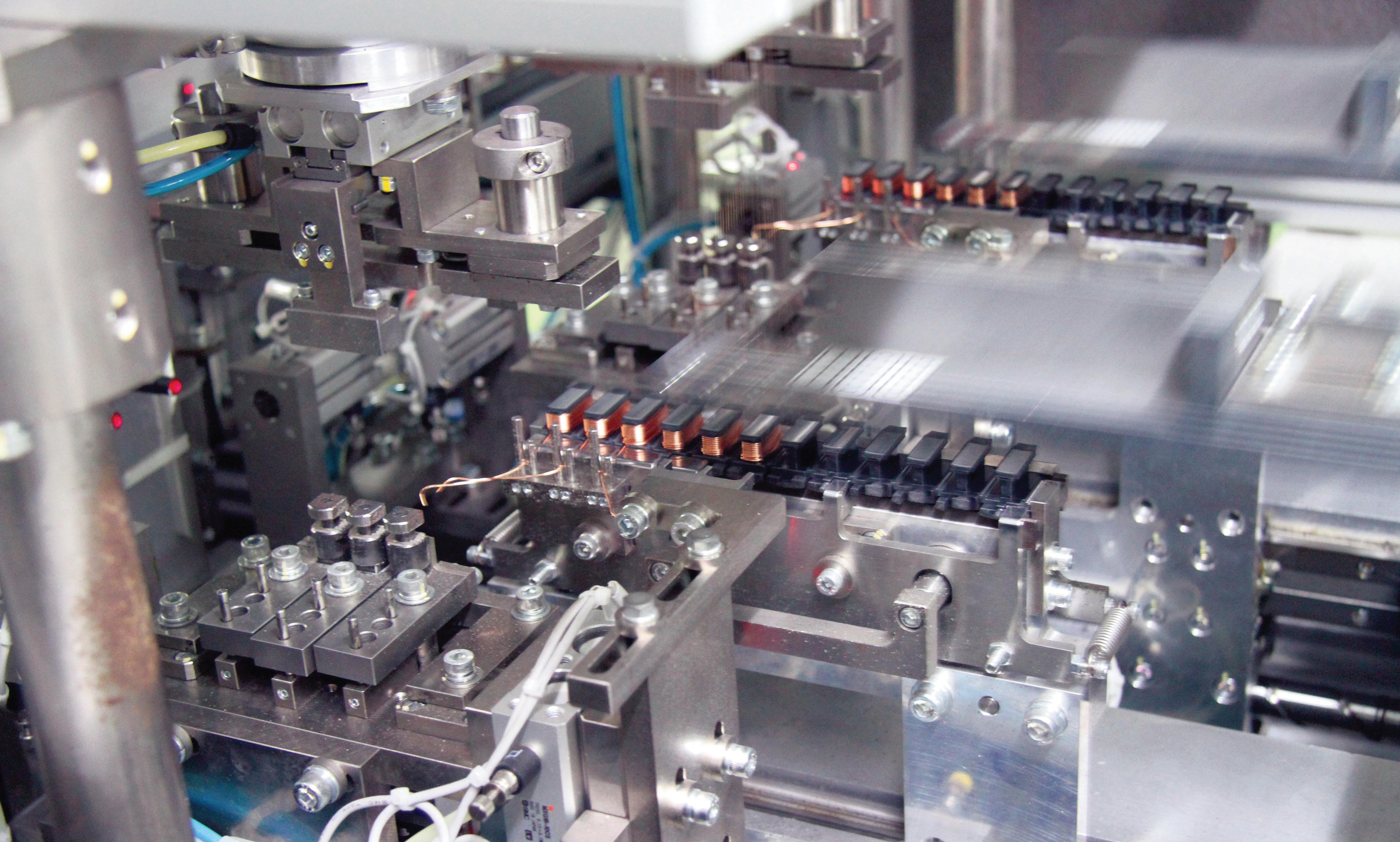
Choose an optimal design Here’s an example of an AMR application using a motion system designed by Portescap: • Motor: brushed DC 35 GLT • Main gearbox: planetary gearbox, 3 stage, spur, 99.8 total gearbox ratio Many AMRs employ differential steering, which relies on separately driven wheels for movement. Another design, a four-wheel drive robot with two pairs of powered wheels, offers more balance since each pair can turn in the same direction. However, if the pairs do not run at the same speed, the robot will move slowly and cannot drive in a straight line.
The Robot Report THE ROBOT REPORT August 2022 83 Hall Sensor Option High Torque Density Low Cogging Torque Adapted for Robot Joints AK SERIES ACTUATORS: Built-in reducer Input & Output Encoders Small Size & Large Torque Support Servo & MIT modes Multi Reduction Ratios (Up to 64:1) WWW.CUBEMARS.COM INFO@CUBEMARS.COM demand high performance characteristics like low noise or vibration, lower precision can be tolerated. However, robotic arms or instruments often need low backlash systems that are more precise and accurate.
A needle roller bearings can avoid scuffing failures and ensure smooth rotation of planet gears on planet pins. | Portescap
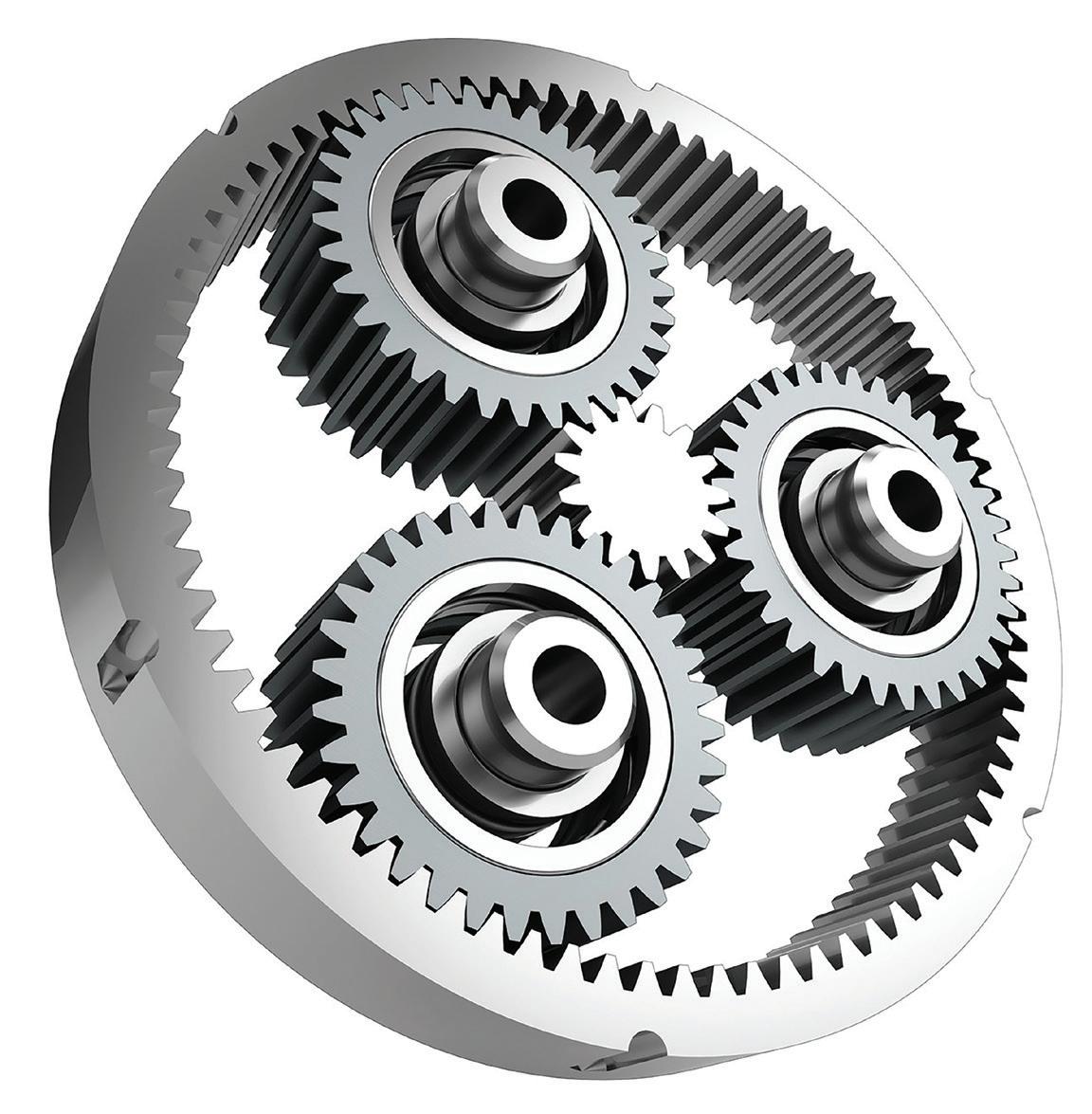
Reliability and noise: Most applications require higher reliability, so the motor stack must survive the required working points. Some critical applications like surveillance robots demand both low noise and higher reliability, and the motor and gearbox have to satisfy both criteria.

• Widest
•
•
MODULAR MOUNTING SYSTEMS

•
Ruland Manufacturing is proud to support the FIRST Robotics Competition as a Gold Supplier of precision shaft collars couplings.
QUICK CLAMPING
&
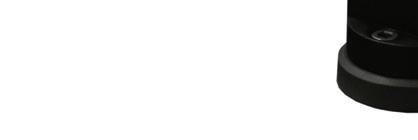
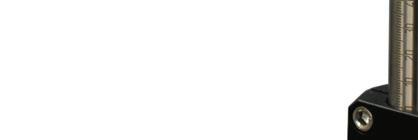
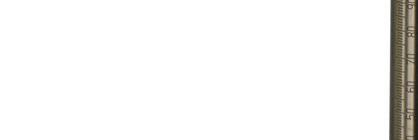
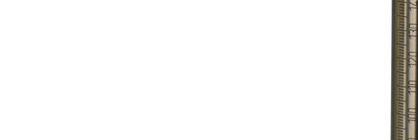
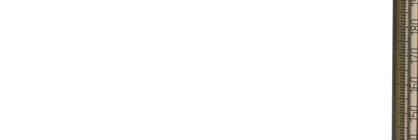
• Yokes,
TOOL-LESS ADJUSTMENT COMPONENTS • Adjustable handles and knobs replace standard hardware and can be used to torque components without tools. • Levers can be used with Ruland shaft collars for quick installation and adjustment.
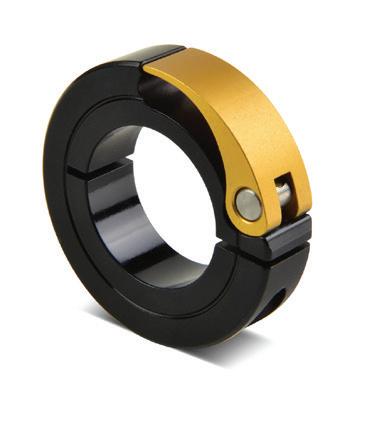
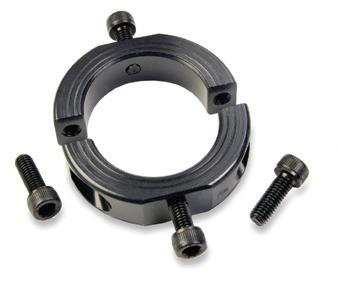
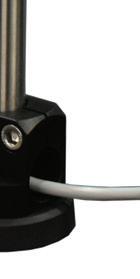
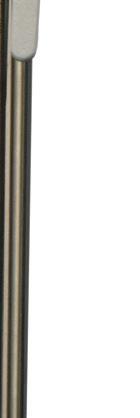
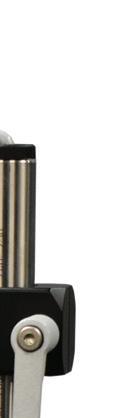


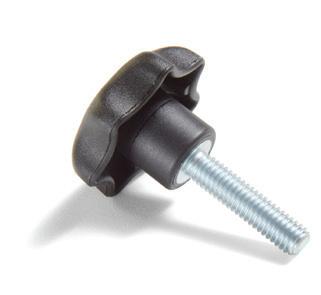
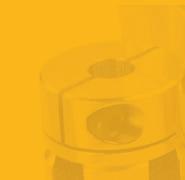
UNIVERSAL JOINTS selection in the industry: over 3000 standard single and double universal joints to start your next design with. Available from Ruland in 2 weeks or less for the shortest lead times in the industry. pins, and blocks are precision machined, ground, and selectively heat treated for smooth operation at high operating angles.
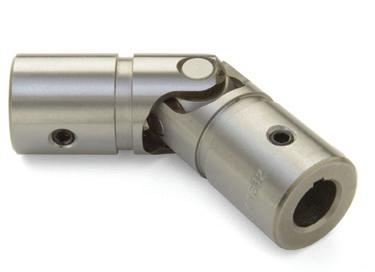
•
• Assortment of components that allow users to build small assemblies for mounting sensors, conveyor rails, machine guards, and more. • Optional pre-designed kits make it easier to select the right system for your application.
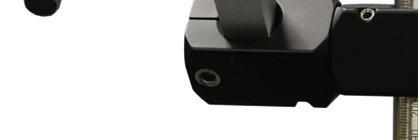
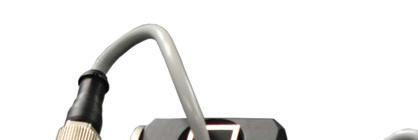
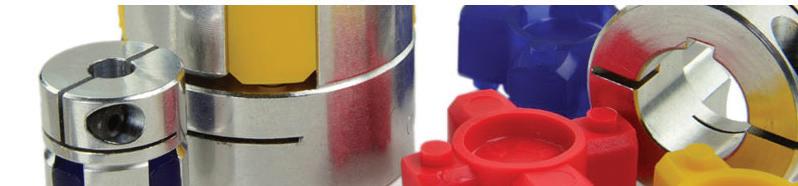
SLIT AND CONTROLFLEX COUPLINGS Slit couplings are available in short and long styles giving designers a variety of body sizes to choose from to t application envelope and performance requirements. Control ex is a highly exible encoder coupling designed for applications with high speed, low torque, and wide differences in shaft sizes (up to a 4:1 small to large ratio). Slit couplings are available in bore sizes from 1.5mm to 12mm (1/8” to 1/2”) and control ex couplings are available in sizes from 6mm to 40mm (1/4” to 1-1/2”). COLLARS

• Hand operated: no tools required to install, remove, & adjust. • Best suited for systems that require adjustments.application.frequent All products available directly on RULAND.COM www.ruland.com | sales@ruland.com MOUNTABLE SHAFT COLLARS • Available with OD ats and holes for direct mounting of the collar to other components. • Proprietary manufacturing processes ensure superior t, nish, and holding power. • Manufactured in a variety of sizes, styles, and materials.NEWWHAT’S RULANDfrom Adjustable Handle Star Knob Shaft Collar with Lever Slit Coupling Control ex Coupling

The Robot Report
• Life expectancy: 1,000 hours
Future AMR advancements AMRs are not without drawbacks. For example, they do not navigate well over rocky terrain, sharp declines or areas with low friction. For AMRs to overcome these limitations, driving architectures must be modified to include mechanisms like a differential drive system with tracks, a skid steer four-wheel drive system or two wheels plus passive casters differential drive system. However, these architectures add more complexity and require detailed studies about their cost impacts.Without a major change in the overall architecture, robot designers must focus their efforts on optimizing the motion system. The following advancements can help improve autonomous mobile robot performance with respect to durability, efficiency and noise reduction: Advanced components: Needle roller bearings avoid scuffing failures and ensure smooth rotation of planet gears on planet pins. In addition, certain gearboxes feature gear teeth arranged to lower torsional forces for reduced noise.
• Maximum temperature: 125°C
Advanced acoustic simulation: Using software to predict noise, helps optimize the design for critical applications requiring low noise. RR
Realize your vision with Festo‘s approach to smart automation for electronics manufacturing. Partner with Festo today.
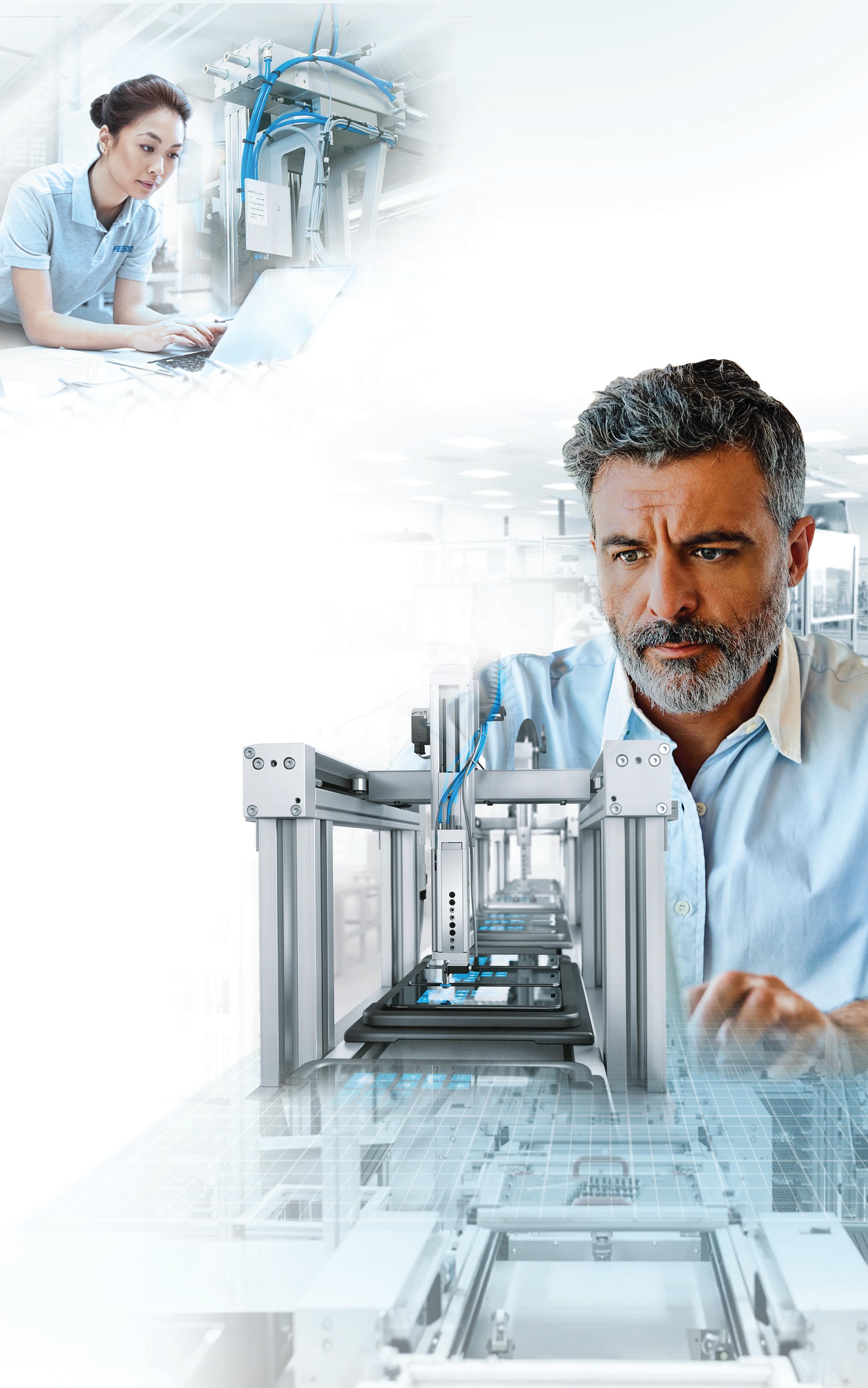
www.festo.us Industry Leadership Superior Quality Products Global Training & Support
THE ROBOT REPORT 85
• Packaging: 32 -mm2 x 115 mm length • Gearbox output torque capacity: 8 Nm • Gearbox output speed: 80 rpm
Innovate today for a new tomorrow
Advanced FEA-based analyses: A structural analysis helps to identify potential failures and eliminate them early in the design process.
An optimum design has a differential steering mechanism similar to those used in a car, which allows the robot to turn left or right, requiring only one motor. Another common configuration of robots uses motors that drive wheels independently instead of differential steering. In this case, separate motors are required to drive each wheel. The overall system specifications are:
It’s been roughly 23 years since one of the first robotic animals trotted on the scene, defying classical notions of our cuddly four-legged friends. Since then, a barrage of the walking, dancing, and door-opening machines have commanded their presence, a sleek mixture of batteries, sensors, metal, and motors. Missing from the list of cardio activities was one both loved and loathed by humans (depending on whom you ask), and which proved slightly trickier for the bots: learning to run.
The Robot Report the cheetahmini robot learns to run How
86 August 2022 www.therobotreport.com THE ROBOT REPORT
Researchers from MIT’s Improbable AI Lab, part of the Computer Science and Artificial Intelligence Laboratory (CSAIL) and directed by MIT Assistant Professor Pulkit Agrawal, as well as the Institute of AI and Fundamental Interactions (IAIFI) have been working on fast-paced strides for a robotic mini cheetah — and their modelfree reinforcement learning system broke the record for the fastest run recorded. It bumped its peak indoor velocity from 12 feet per second before training to 13 feet per second after.
MIT’s mini cheetah, using a system,reinforcementmodel-freelearningbroketherecordforthefastestrunrecorded. | MIT
MIT developed a learning pipeline for the four-legged robot that learns to run entirely by trial and error in simulation. The Robot Report Staff
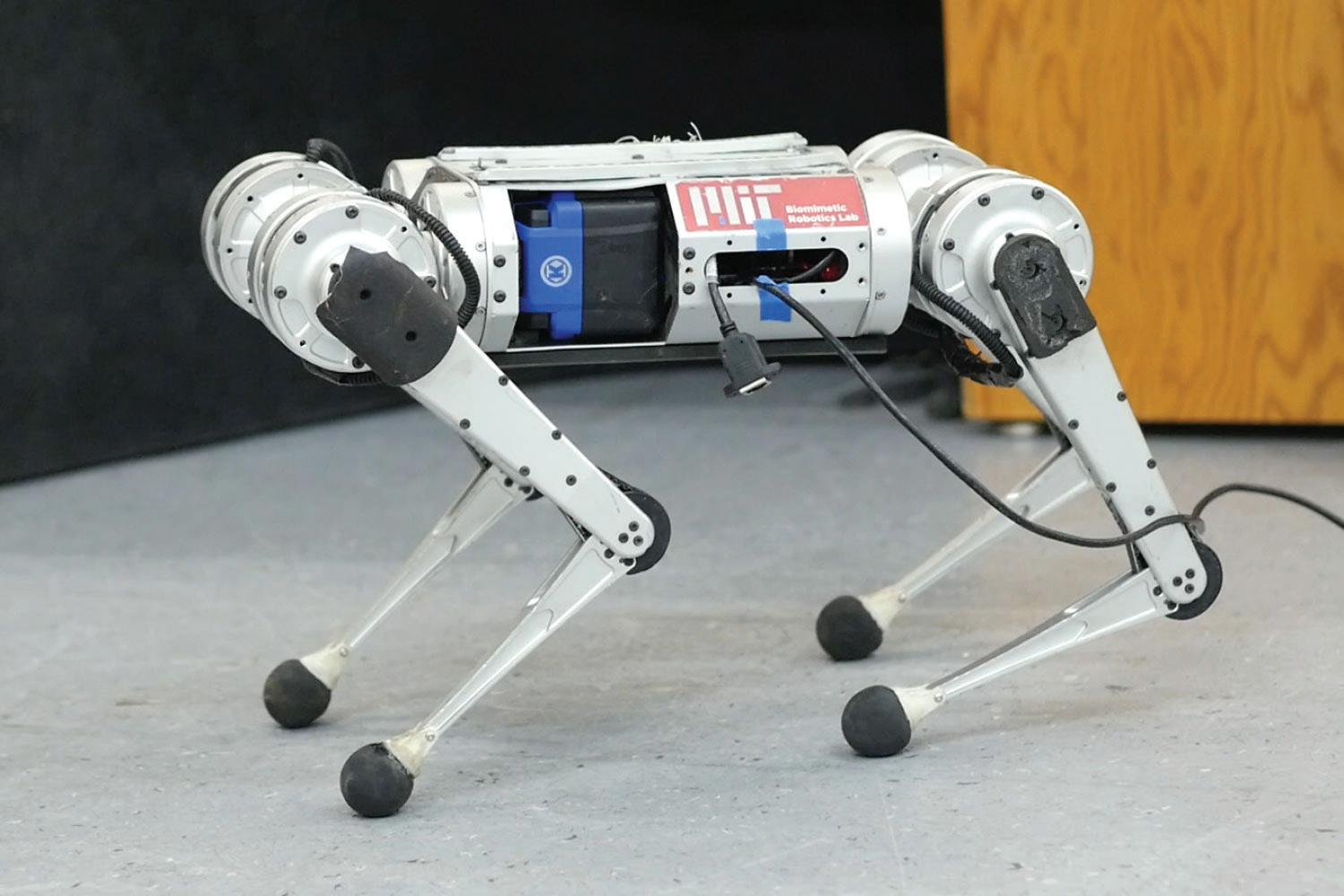
THK is committed to meeting the worldwide demand for linear motion products. At THK Manufacturing of America, Inc (TMA), we manufacture, assemble, and ship all over North America from our location in Hebron, Ohio. We’ve also ramped up our automating processes at existing facilities including our U.S. manufacturing plant where over 70% of THK Robotics Components are manufactured. Automated processes at this state-of-the-art facility enable increased production while maintaining the high standard of precision associated with our products. To learn more, call us at 1-800-763-5459 or visit www.thk.com. Quality Linear Motion Solutions from THK LOCAL MANUFACTURING WORLD-CLASS LINEAR MOTION 1–2 Week Delivery of Select LM Guides and Actuators QUICK SHIP COMPONENTS THK Manufacturing in Hebron, Ohio See us at: IMTS 2022 • September 12-17 Chicago • Booths 134802 & 134803
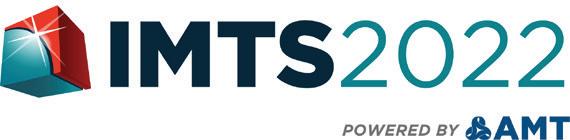

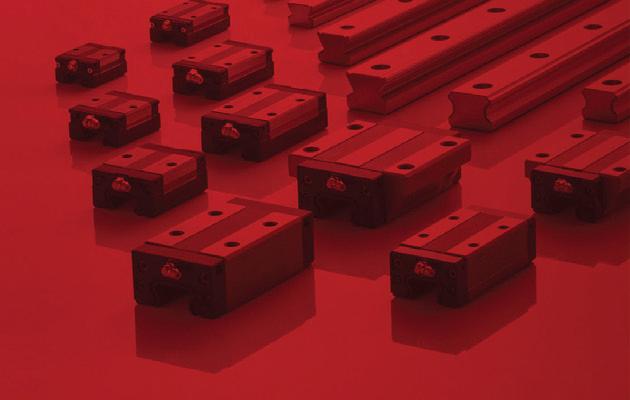
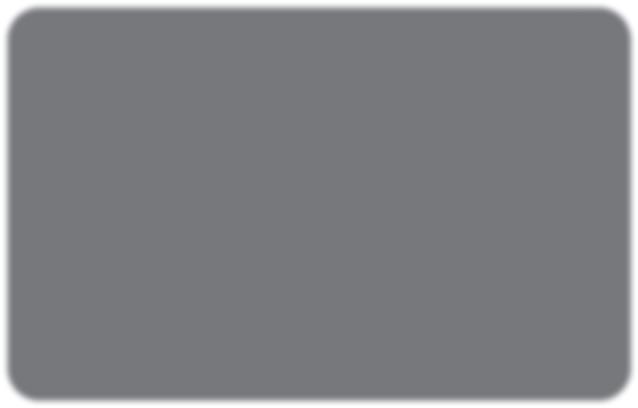


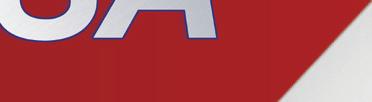
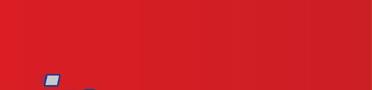
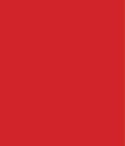

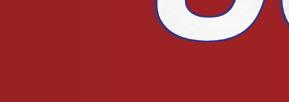
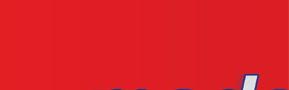
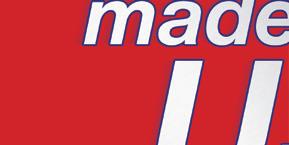
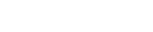
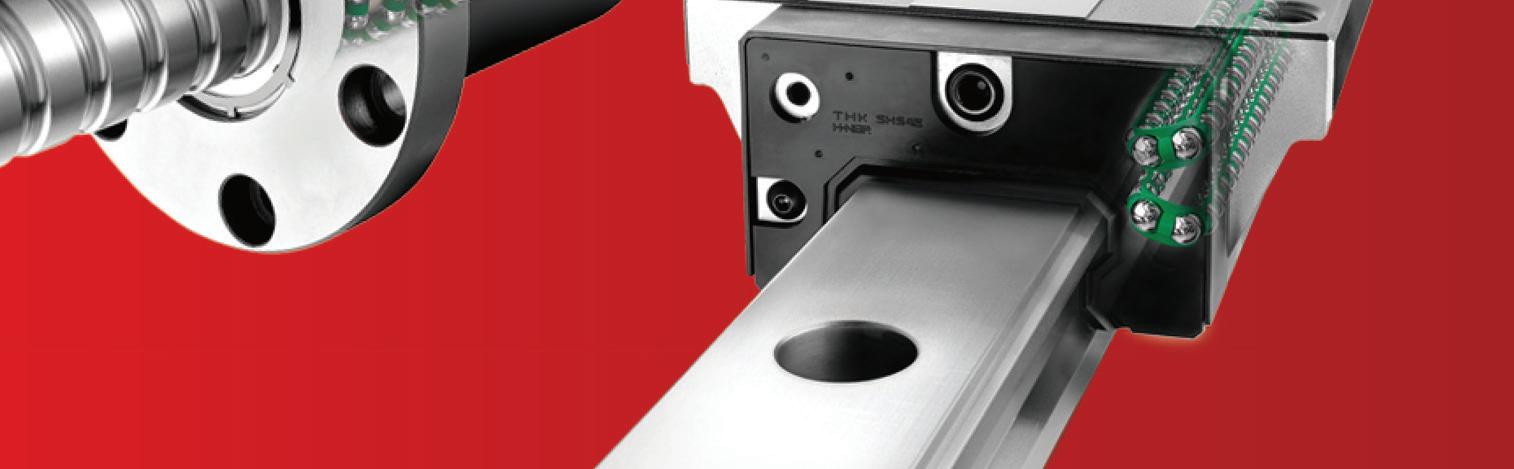


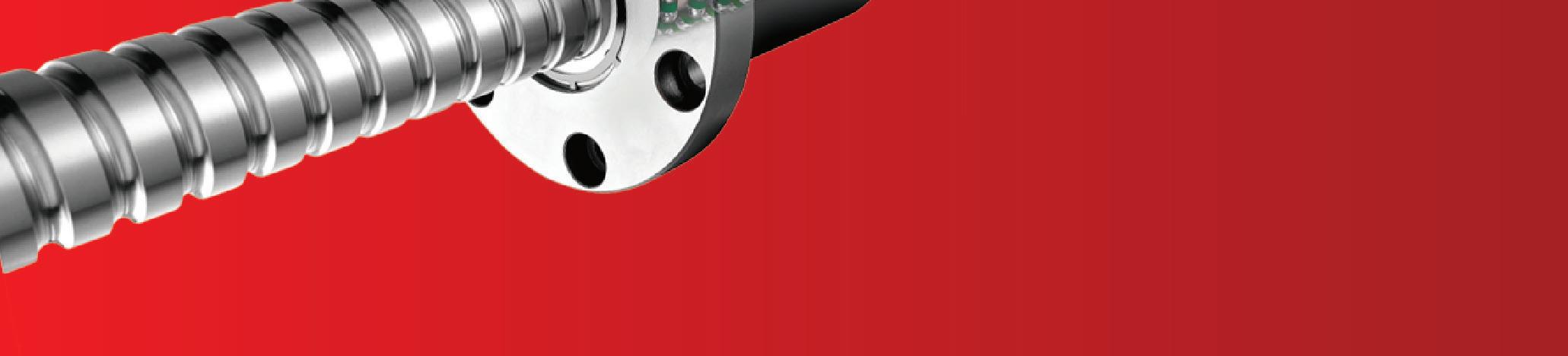



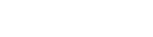
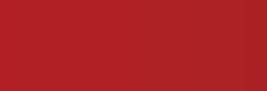
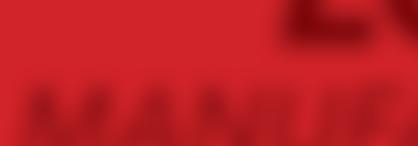

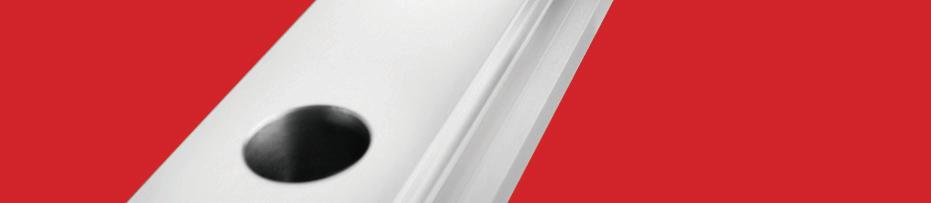


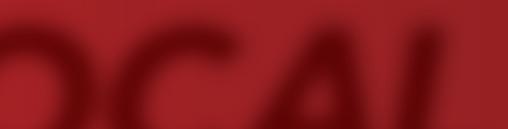
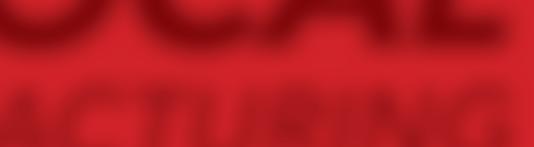
www.therobotreport.com THE ROBOT REPORT
Reinforcement learning mimics the fundamental way in which humans learn. Here, MIT PhD student Gabriel Margolis and IAIFI postdoc Ge Yang discuss just how fast the cheetah can run. We’ve seen videos of robots running before. Why is running harder than walking?
Today’s robots face an analogous problem. The problem is that moving on all terrains as if you were walking on ice is very inefficient, but is common among today’s robots. Humans run fast on grass and slow down on ice — we adapt. Giving robots a similar capability to adapt requires quick identification of terrain changes and quickly adapting to prevent the robot from falling over. In summary, because it’s impractical to build analytical (human-designed) models of all possible terrains in advance, and the robot’s dynamics become more complex at highvelocities, high-speed running is more challenging than walking.
At the heart of artificial intelligence research is the trade-off between what the human needs to build in (nature) and what the machine can learn on its own (nurture). The traditional paradigm in robotics is that humans tell the robot both what task to do and how to do it. The problem is that such a framework is not scalable, because it would take immense human engineering effort to manually program a robot with the skills to operate in many diverse environments. A more practical way to build a robot with many diverse skills is to tell the robot what to do and let it figure out the how. Our system is an example of this. In our lab, we’ve begun to apply this paradigm to other robotic systems, including hands that can pick up and manipulate many different objects.Thiswork was supported by the DARPA Machine Common Sense Program, the MIT Biomimetic Robotics Lab, NAVER LABS, and in part by the National Science Foundation AI Institute for Artificial Intelligence Fundamental Interactions, United States Air Force-MIT AI Accelerator, and MIT-IBM Watson AI Lab. The research was conducted by the Improbable AI Lab. RR 88 August 2022
The robot needs to respond quickly to changes in the environment, such as the moment it encounters ice while running on grass. If the robot is walking, it is moving slowly and the presence of snow is not typically an issue. Imagine if you were walking slowly, but carefully: you can traverse almost any terrain.
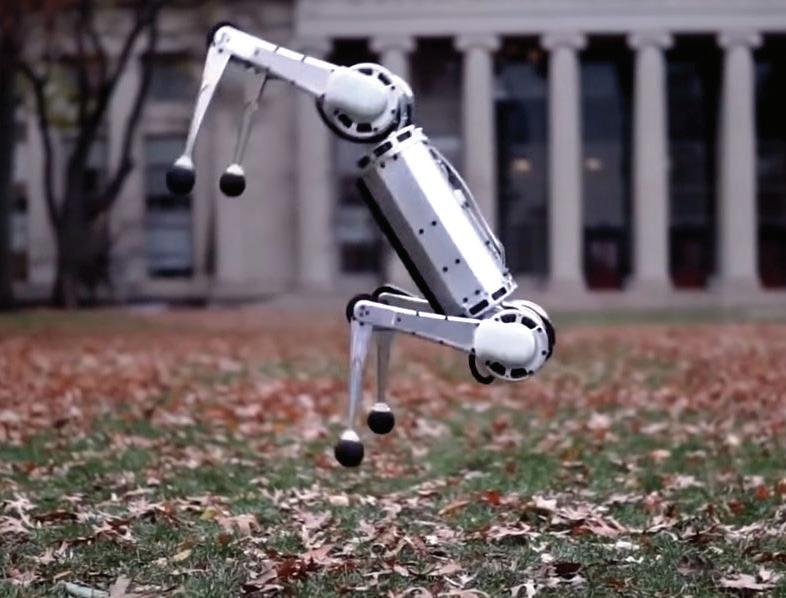
Reinforcement learning is a goal-driven form of machine learning where an agent, in this case mini cheetah, learns by interacting with its environment, observing the results of these interactions and receiving a reward (positive or negative) accordingly.
Programming how a robot should act in every possible situation is simply very hard. The process is tedious, because if a robot were to fail on a particular terrain, a human engineer would need to identify the cause of failure and manually adapt the robot controller, and this process can require substantial human time. Learning by trial and error removes the need for a human to specify precisely how the robot should behave in every situation. This would work if: 1. The robot can experience an extremely wide range of terrains 2. The robot can automatically improve its behavior with experience Thanks to modern simulation tools, our robot can accumulate 100 days’ worth of experience on diverse terrains in just three hours of actual time. We developed an approach by which the robot’s behavior improves from simulated experience, and our approach critically also enables successful deployment of those learned behaviors in the real world. The intuition behind why the robot’s running skills work well in the real world is: Of all the environments it sees in this simulator, some will teach the robot skills that are useful in the real world. When operating in the real world, our controller identifies and executes the relevant skills in real-time. Can this approach be scaled beyond the mini cheetah? What excites you about its future applications?
Previous agile running controllers for the MIT Cheetah 3 and mini cheetah, as well as for Boston Dynamics’ robots, are “analytically designed,” relying on human engineers to analyze the physics of locomotion, formulate efficient abstractions, and implement a specialized hierarchy of controllers to make the robot balance and run. You use a “learn-by-experience model” for running instead of programming it. Why?
Achieving fast running requires pushing the hardware to its limits, for example, by operating near the maximum torque output of motors. In such conditions, the robot dynamics are hard to analytically model.
The Robot Report
• ITAR SIX SIGMA AND LEAN PRACTICES ARE EMBRACED DAILY WITHIN THE CULTURE
THE ROBOT REPORT www.therobotreport.com August 2022 89
Robotics
Today’s increasing demands of automation and robotics in various industries, engineers are challenged to design unique and innovative machines to di erentiate from their competitors. Within motion control systems, flexible integration, space saving, and light weight are the key requirements to design a successful mechanism.
CGI’s diverse customer base and wide range of applications have earned us a reputation for quality, reliability, and flexibility. One of the distinct competitive advantages we are able to provide our customers is an engineering team that is knowledgeable and easy to work with. CGI is certified to ISO9001 and ISO13485 quality management systems. In addition, we are FDA and AS9100 compliant. Our unique quality control environment is weaved into the fabric of our manufacturing facility. We work daily with customers who demand both precision and rapid turnarounds.
Canon’s new high torque density, compact and lightweight DC brushless servo motors are superior to enhance innovative design. Our custom capabilities engage optimizing your next innovative designs. We are committed in proving technological advantages for your success. DC brushless Servo Motors Canon U.S.A., Inc.
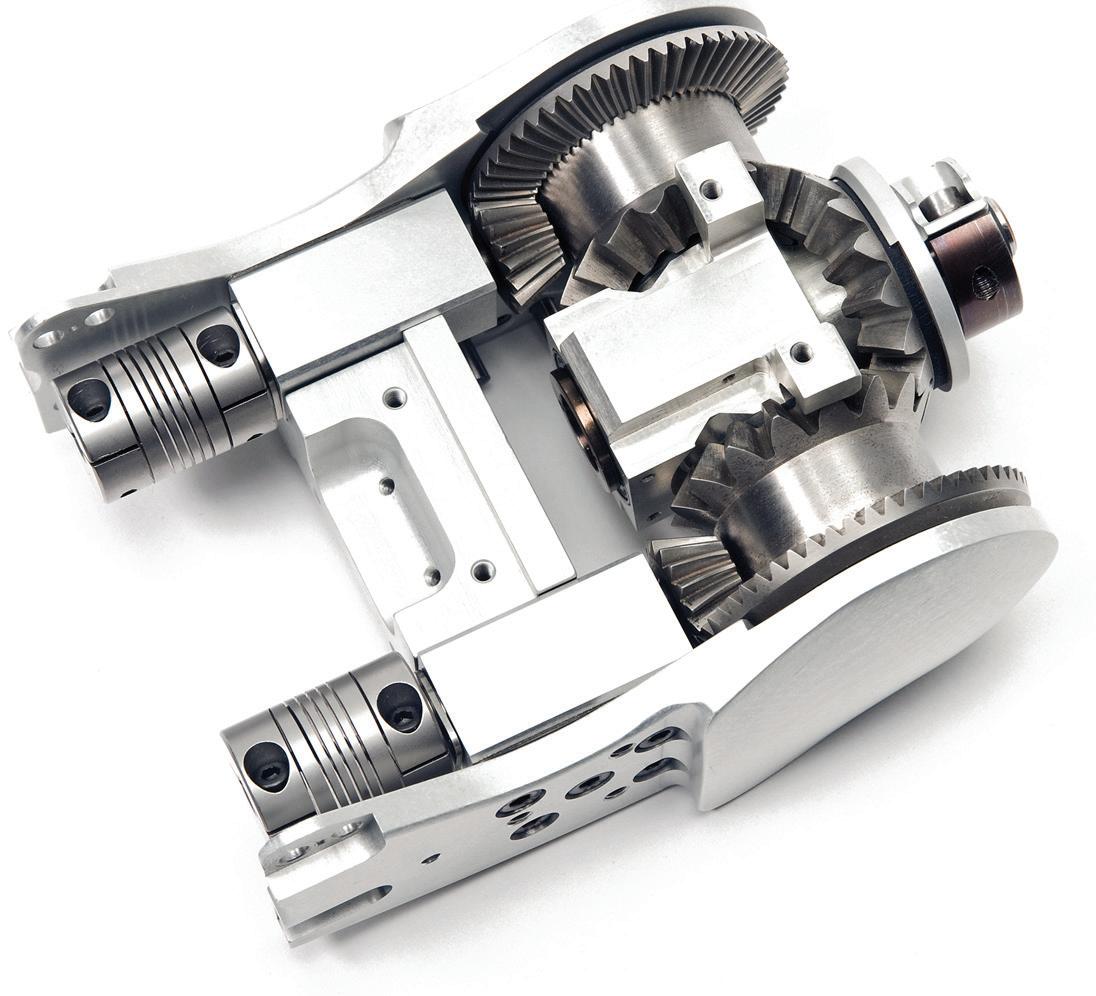
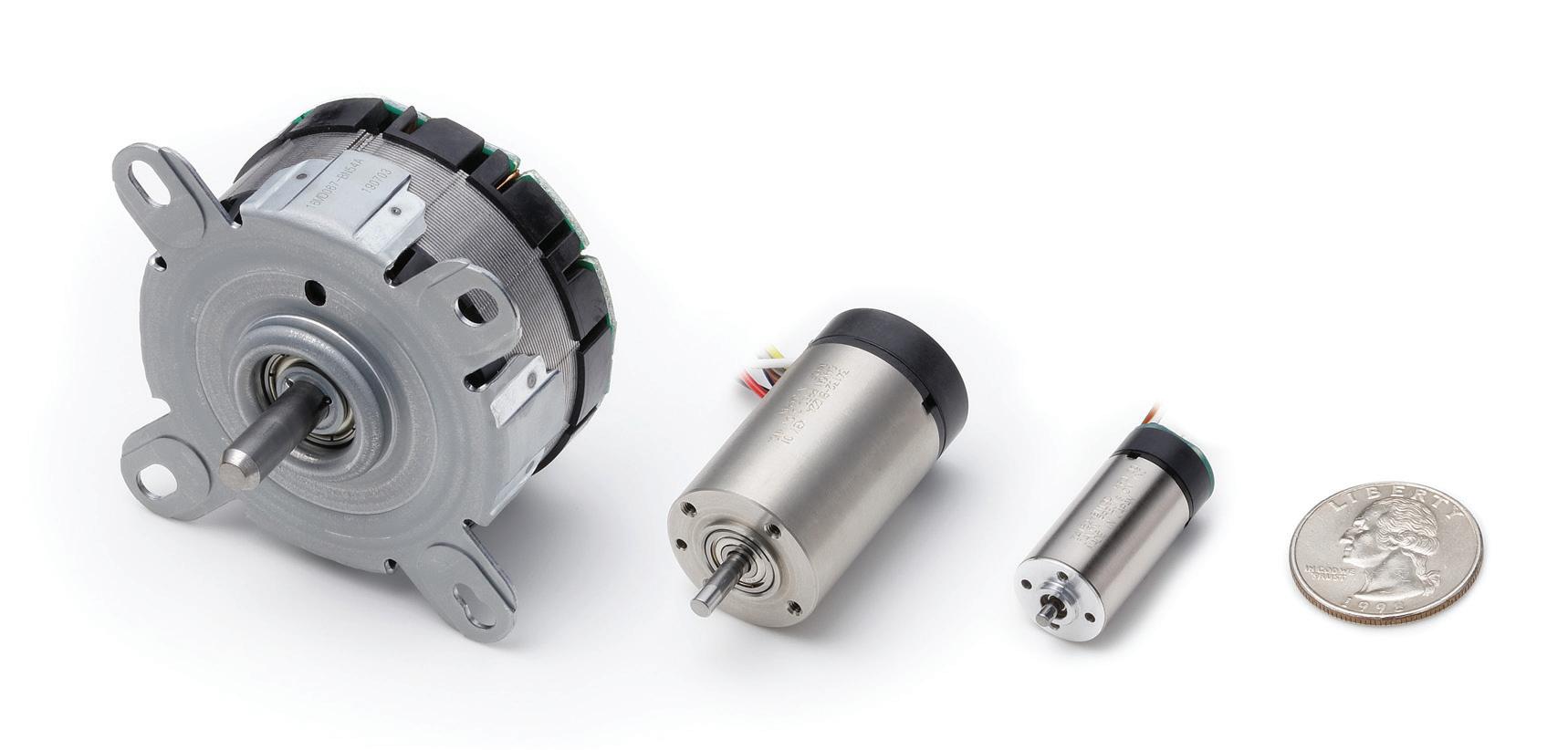
Robotics
Advanced Products for Robotics and Automation CGI Inc. CGI Inc. 3400 Arrowhead Drive Carson City, NV 89706 Toll Free: 1.800.568.4327 Ph: 1.775.882.3422 Fx: 1.775.882.9599 WWW.CGIMOTION.COM ISO QUALITY MANAGEMENT SYSTEMS: ISO 9001• ISO 13485 • AS9100
At CGI we serve a wide array of industries including medical, robotics, aerospace, defense, semiconductor, industrial automation, motion control, and many others. Our core business is manufacturing precision motion control solutions.
Canon U.S.A., Inc Motion Control Products 3300 North First Street San Jose, CA, 408-468-232095134 www.usa.canon.com
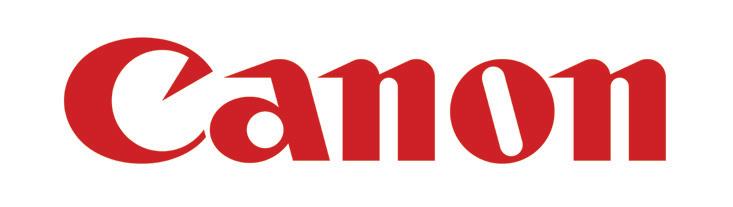
01915 United
Robot
42
The drive wheels on Autonomous Mobile platforms benefit from the inherent characteristics of harmonic planetary technology; primarily, smoothness of travel, backdrivability, and an e ciency curve that does not degrade over time. The integral cross roller bearing construction contributes to an excellent balance of torque density, sti ness, and radial load support in a compact and reliable package. Available in dozens of standard reduction ratios, these low backlash drive trains include motor adaptation as required. Dunham Ridge Beverly, MA States
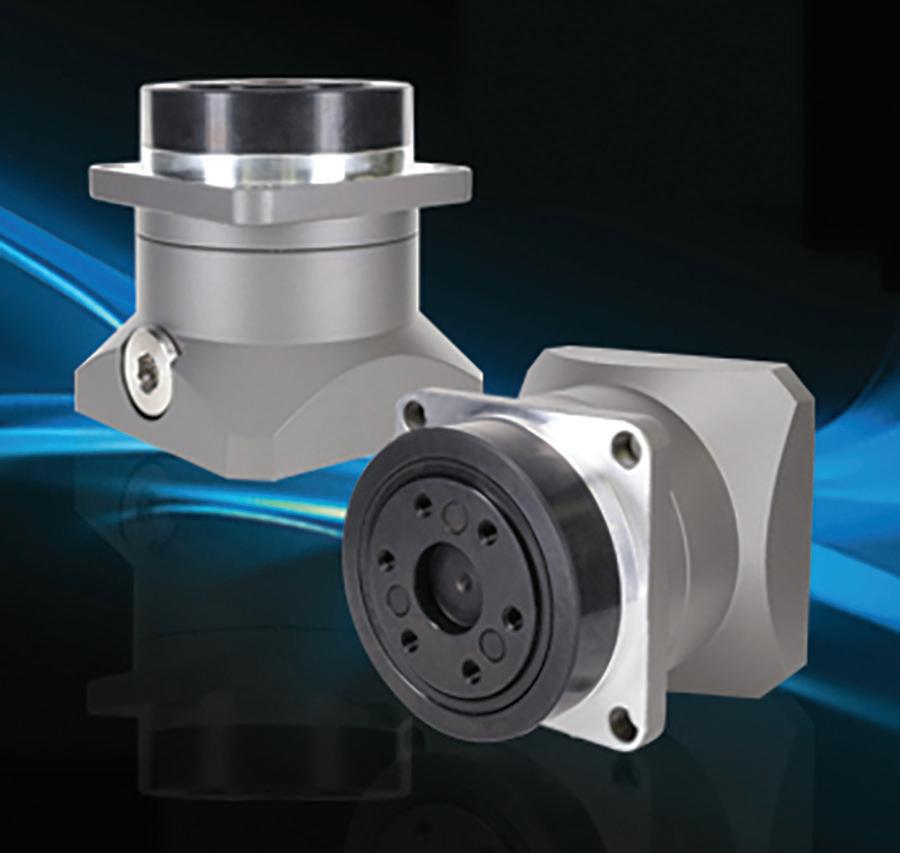
www.harmonicdrive.net Harmonic Drive is a registered trademark of Harmonic Drive Systems
90 August 2022 www.therobotreport.com THE ROBOT REPORT Robotics Machine Vision Systems from Festo From inspection to identification, barcode reading to robotic guidance, measurement to color analysis, Festo provides machine vision solutions to suit your needs. With higher resolutions, more powerful software tools, easier integration and more flexibility, the latest generation of SBS vision sensors provide the right features and tools to meet your demanding machine vision requirements. Machine Vision Software The SBS Vision sensor software is used to configure and program all aspects of the SBA and SBSX vision sensors. Discover a New Vision Software! FESTO Corporation Festo Corporation 1377 Motor Pkwy. Islandia, NY 11749 www.festo.us Robotics Harmonic Drive Servo Grade AMR Propulsion Drive Trains
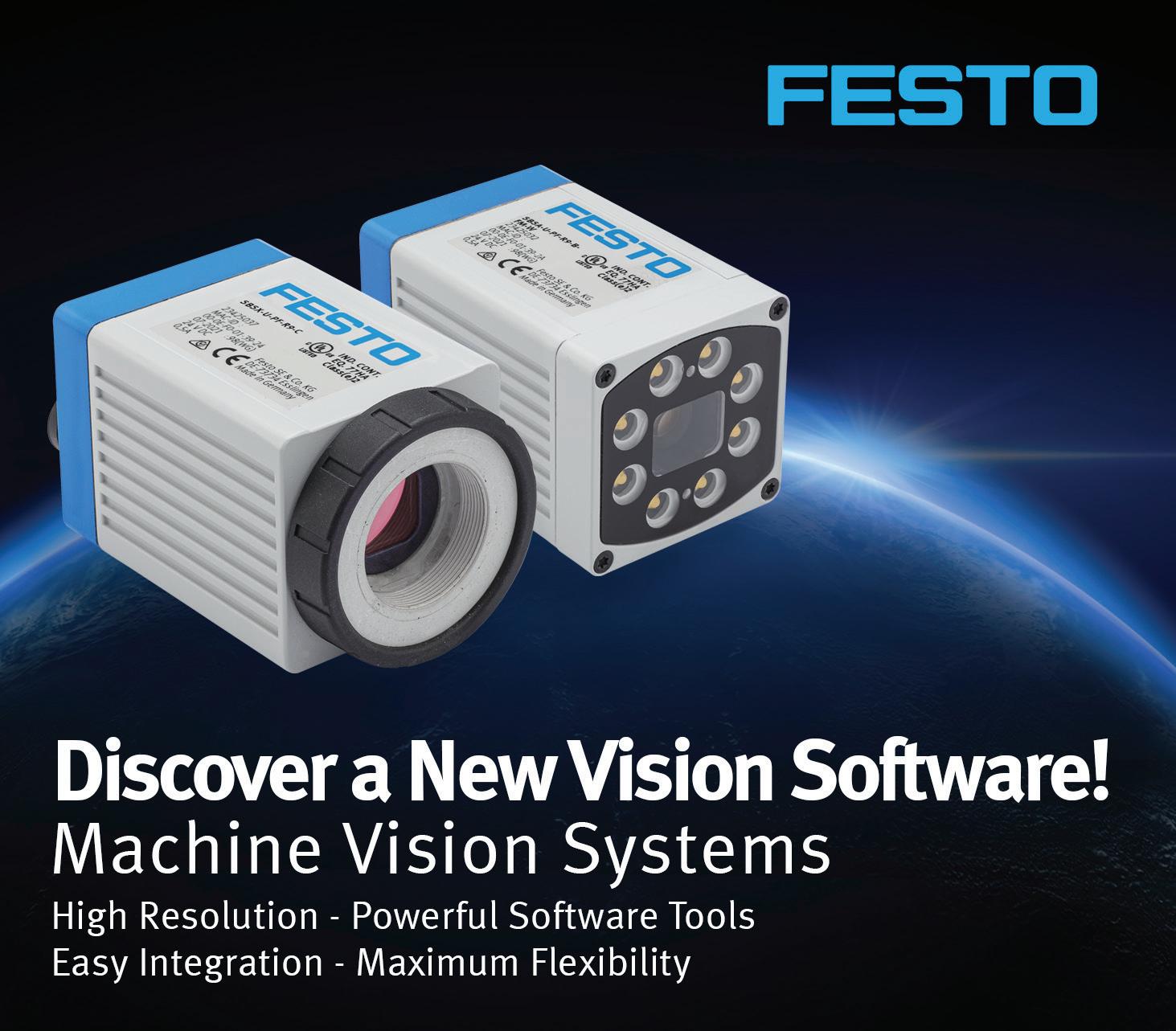
NEWENGLANDWIRE TECHNOLOGIES

Robotics
1. Choose compact motorization where possible - Drives must fit into restricted spaces, as they are sometimes integrated into existing trucks. A small footprint is critical for applications in logistics.
THE ROBOT REPORT www.therobotreport.com August 2022 91 Robotics
Today’s AGVs must be compact and functional robots which are able to move vertically and carry heavy loads. These AGVs cannot fail, and so the choice of their motorization is crucial. There are 5 key points to consider when motorizing an AGV.
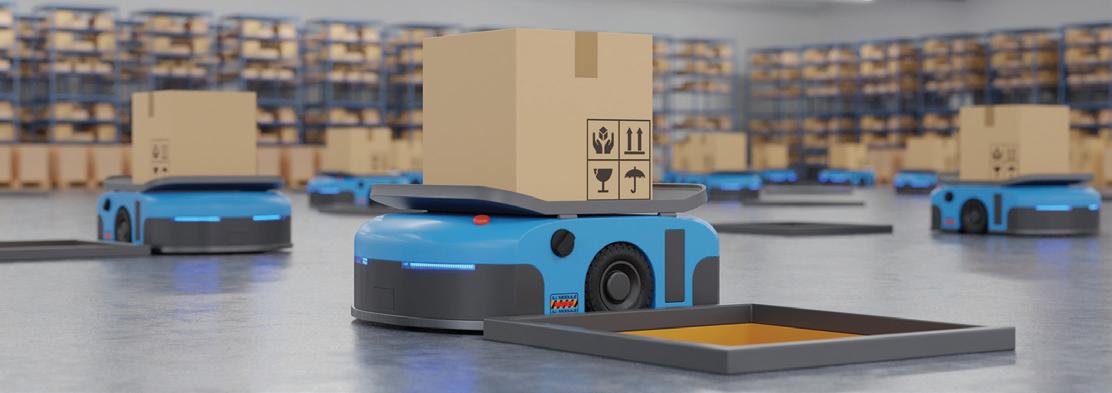
New England Wire Technologies Advancing innovation for over 100 years Contact info: New England Wire Technologies 603.838.6624www.newenglandwire.com
3. Opt for fast delivery of your motor solution
4. Base the design on modularity - Not all AGVs do the same job and therefore having the flexibility to select a solution to match needed specifications is essential.
Phone: info.us@maxongroup.comwww.maxongroup.us508.677.0520
5. Prioritize safety – select motor options with integrated sensors. maxon’s IDX motor has a diameter of only 56 mm, its performance is equivalent to that of a motor with a footprint 25% larger. The IDX motorization thus combines performance in a compact size and ideal for AGVs. Go to Drive.tech for more details. Visit www.maxongroup.us for more maxon solutions.
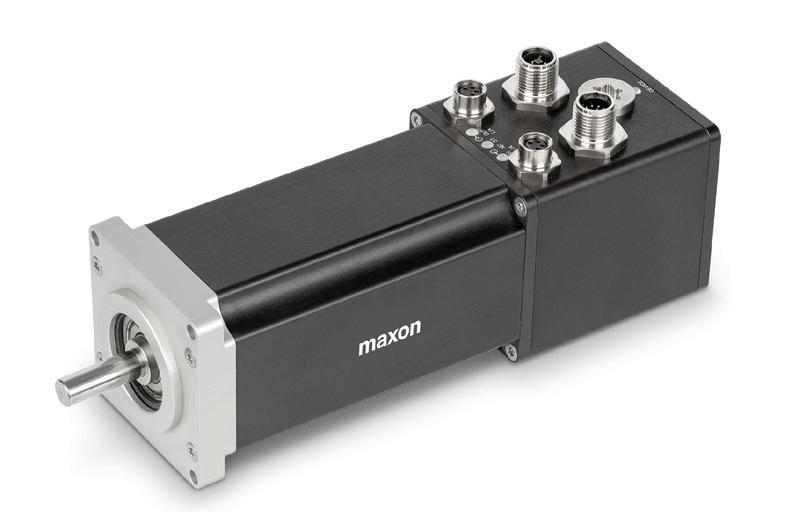
Why accept a standard product for your custom application?
Motorizing an AGV maxon precision motors, inc. 125 Dever Drive Taunton, MA 02780
2. Focus on ease of use – select a plug-and-play solution.
NEWT is committed to being the premier manufacturer of choice for customers requiring specialty wire, cable and extruded tubing to meet existing and emerging worldwide markets. Our custom products and solutions are not only engineered to the exacting specifications of our customers, but designed to perform under the harsh conditions of today’s advanced manufacturing processes. Cables we specialize in are LITZ, multi-conductor cables, hybrid configurations, coaxial, twin axial, miniature and micro-miniature coaxial cables, ultra flexible, high flex life, low/high temperature cables, braids, and a variety of proprietary cable designs. Contact us today and let us help you dream beyond today’s technology and achieve the impossible.
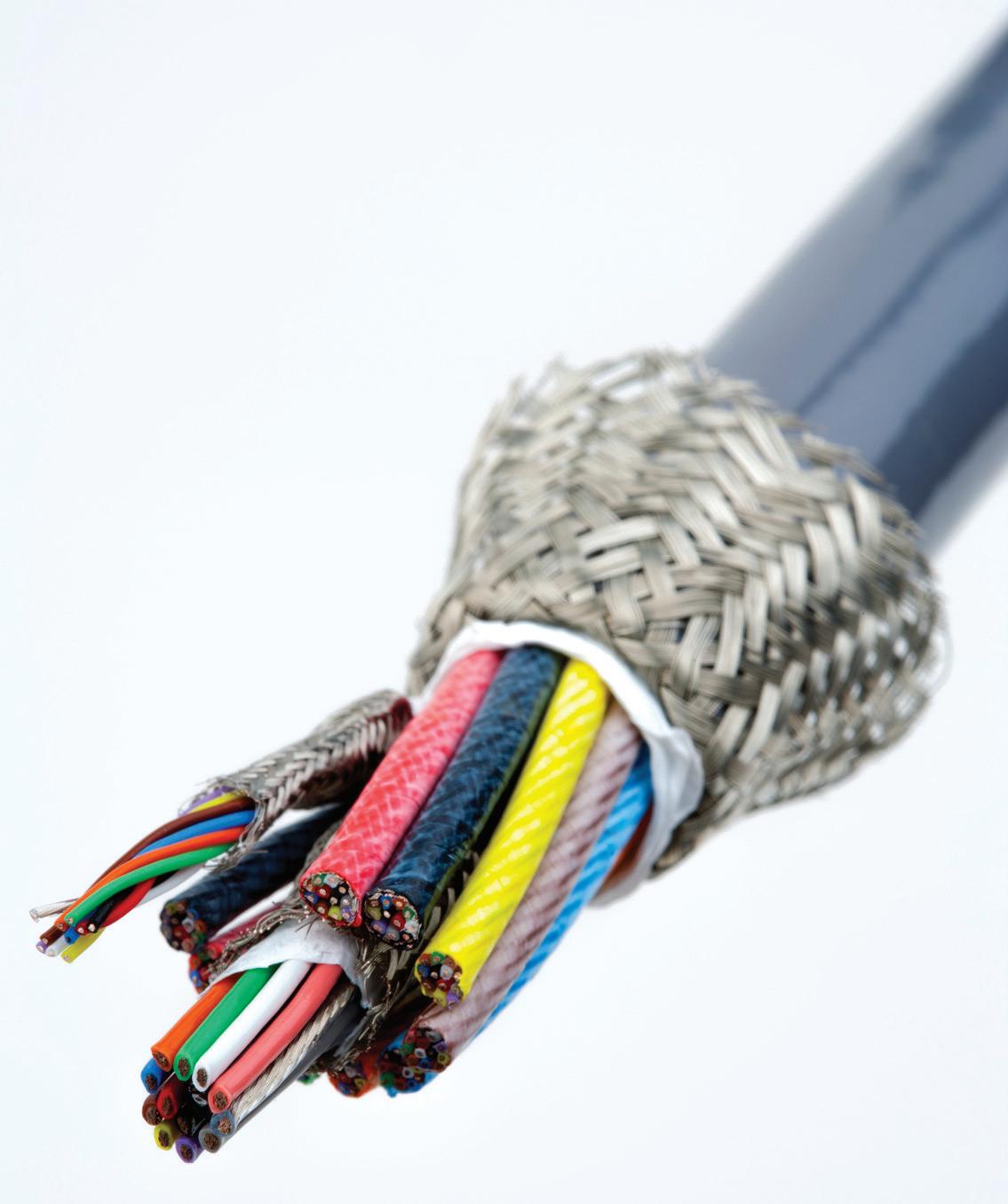
Ruland Manufacturing 6 Hayes Memorial Dr. Marlborough, MA 01752 508-485-1000 www.ruland.com email: sales@ruland.com
Robotics
THK America, Inc. 200 East Commerce Drive Schaumburg, IL 60173 Phone: 847-310-1111 www.THK.com
92 August 2022 www.therobotreport.com THE ROBOT REPORT Robotics
THK Micro Cross-Roller Ring Series RAU The THK micro-size Cross-Roller Ring RAU features a 10mm inner diameter and a 21mm outer diameter. It is more compact, lightweight and rigid than a double row angular contact ball bearing type. RAU rollers travel on V-shaped raceways ground into the inner and outer rings. Alternating rollers are arrayed orthogonally so that one bearing can support loads and moments in any direction. Spacer retainers enable smooth movement and high rotation https://www.thkstore.com/products/rotation/cross-roller-rings/rau.htmlaccuracy.
Zero-Backlash Couplings for Robotic Systems Ruland Manufacturing
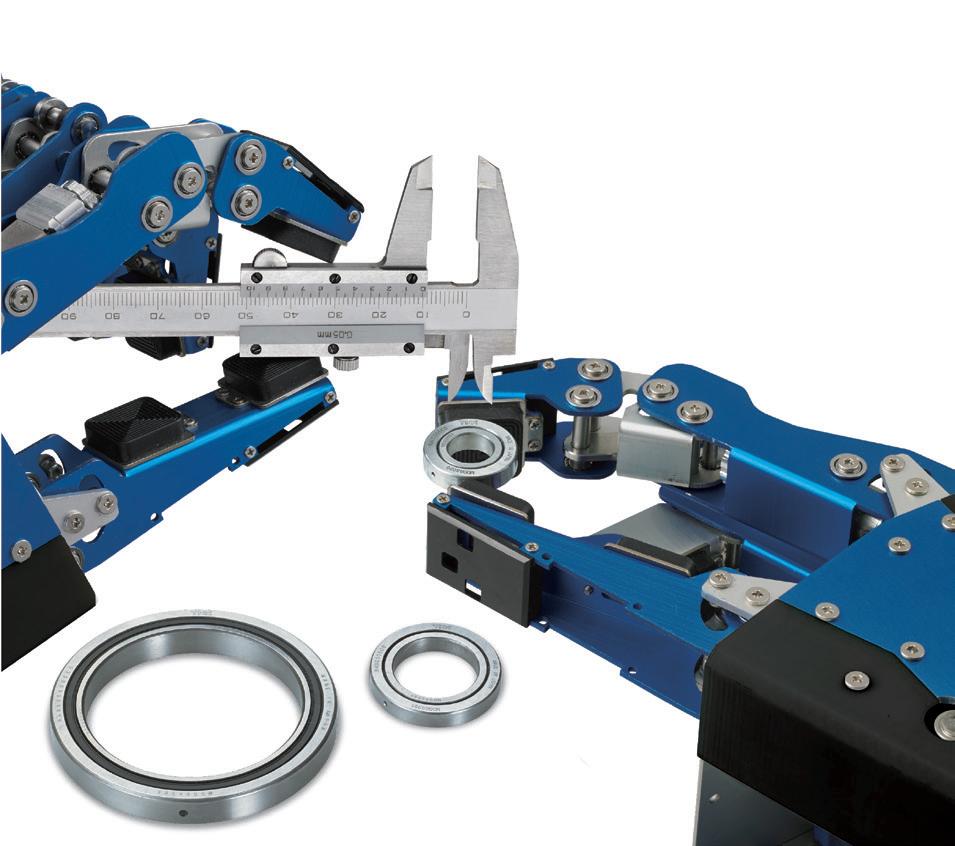
Ruland Manufacturing o ers a variety of zero-backlash servo couplings designed for use in high precision applications like automation and robotics. Ruland o ers beam, bellows, disc, oldham, jaw, and newly-released Controlflex couplings in thousands of o -the-shelf combinations and sizes to help designers optimize their systems. Robotic vision systems, material handling robots, and automated guided vehicles have infamously strict requirements that require engineers to balance torque, weight, dampening, and more, all while retaining extremely precise power transmission. Ruland servo couplings excel in demanding applications and can be selected based on a wide variety of performance characteristics. Visit Ruland.com for access to everything you need to make a coupling design decision including: full technical product data, 3D CAD models, installation videos, and eCommerce to make prototyping easy.
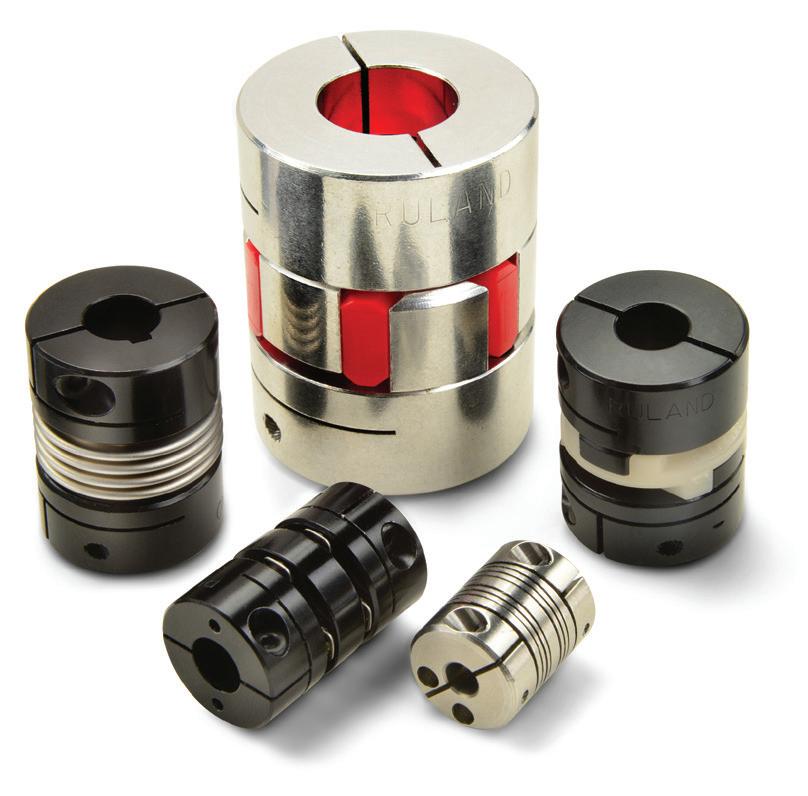