ENGINEERING SIMULATION SOFTWARE CAN INCREASE OFFSHOREWINDADOPTION SEPTEMBER 2022 www.windpowerengineering.com The technical resource for wind profitability PLUGGING OFFSHORE WIND POWER INTO OUR ENERGY GRID PAGE 22 aztecbolting.com







































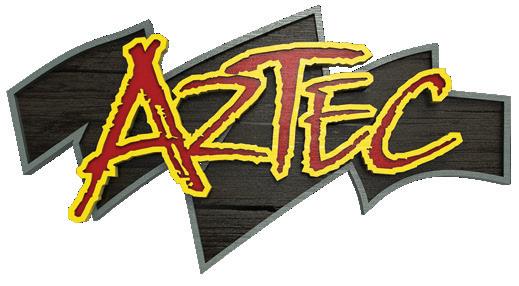
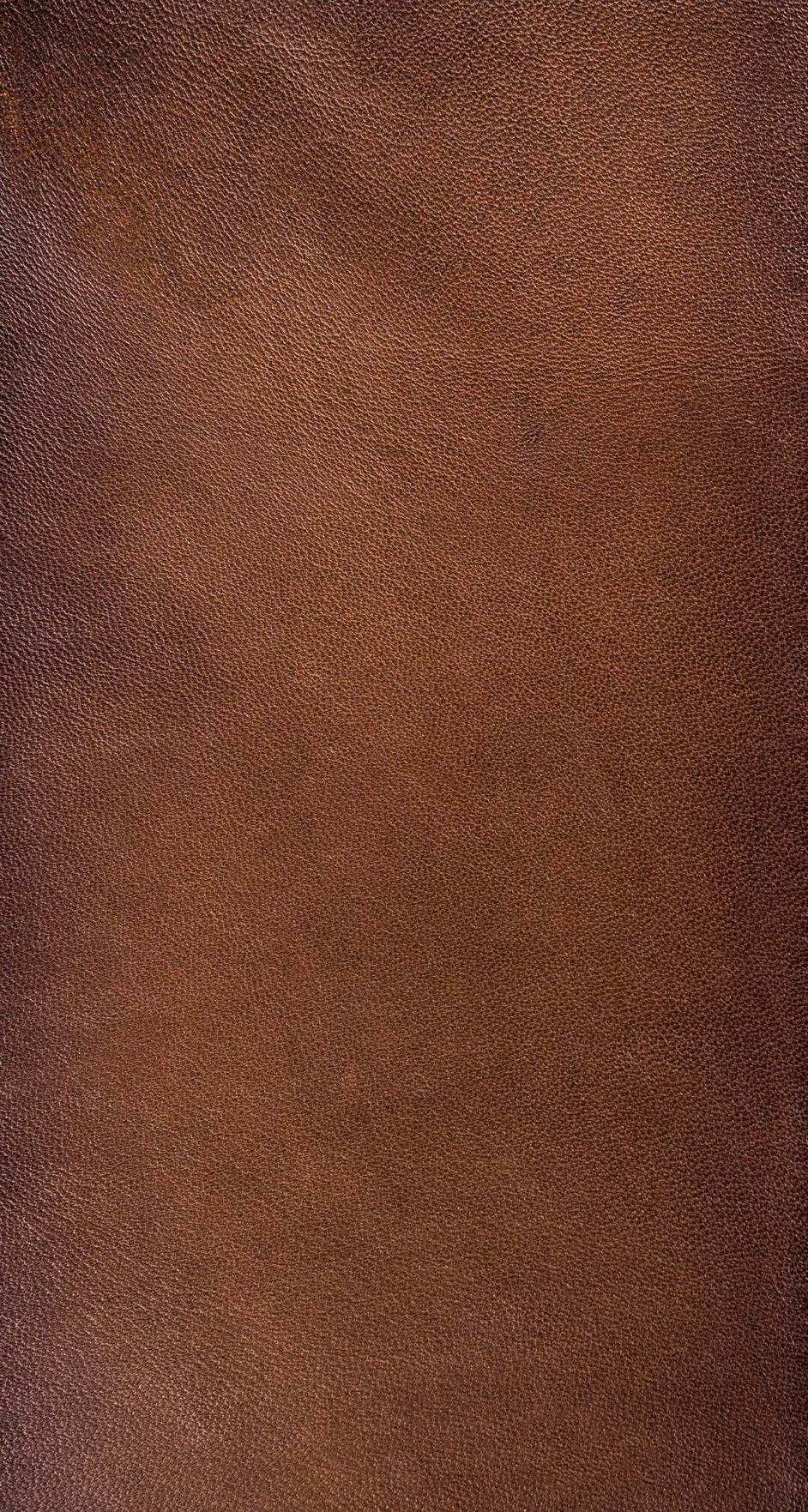

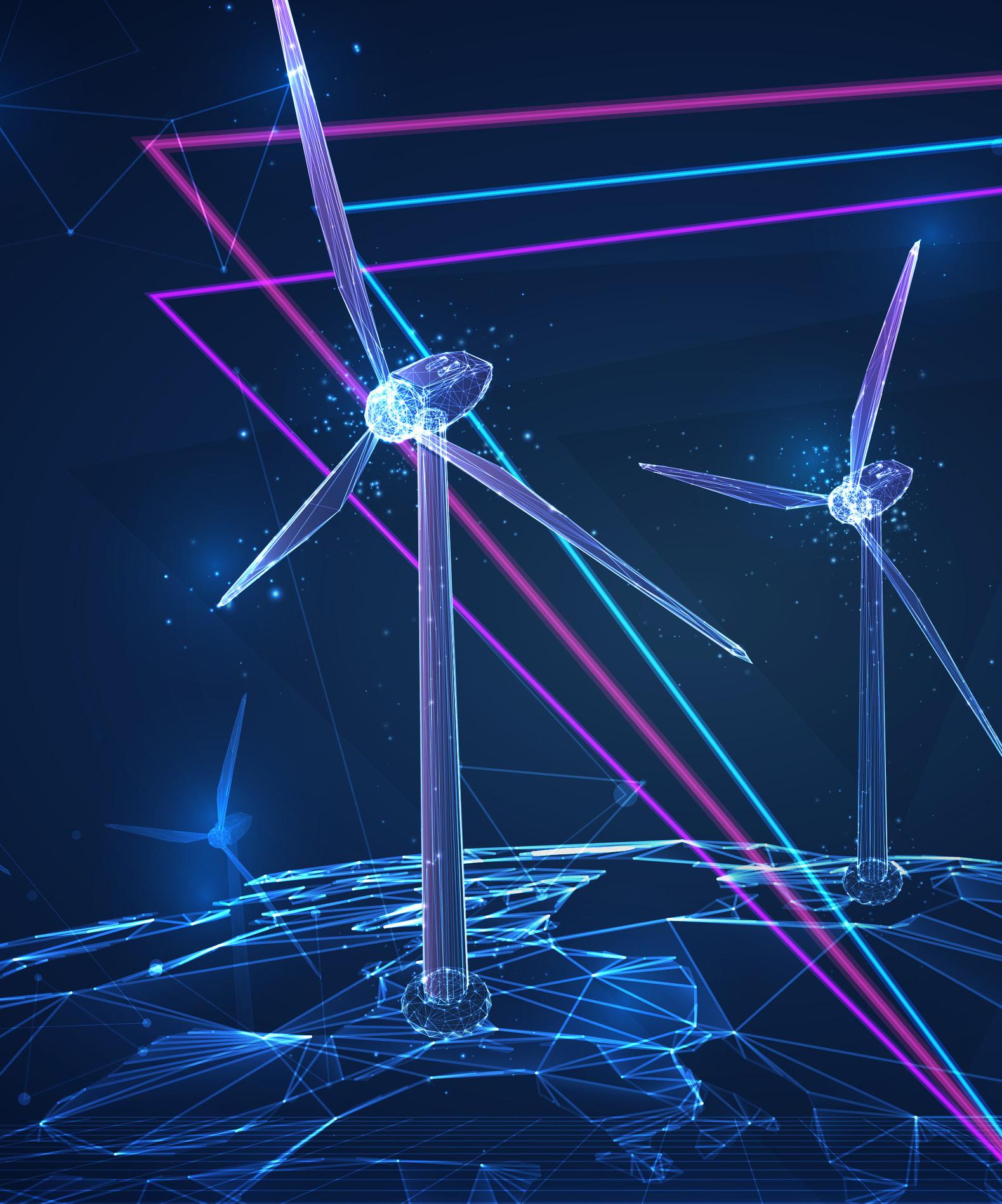
Yuken is the most trusted name in the US Wind industry for pitch control valves. Since 2014: • Over 4,000 valves installed • No warranty claims or returns since 2014 • 3 year warranty guarantee ALA Industries Limited 3410 Delta Dr • Portage, IN 46368 Tel: 877-419-8536 Fax: www.alaindustrieslimited.com219-762-2066
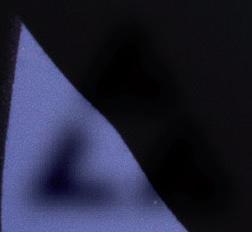
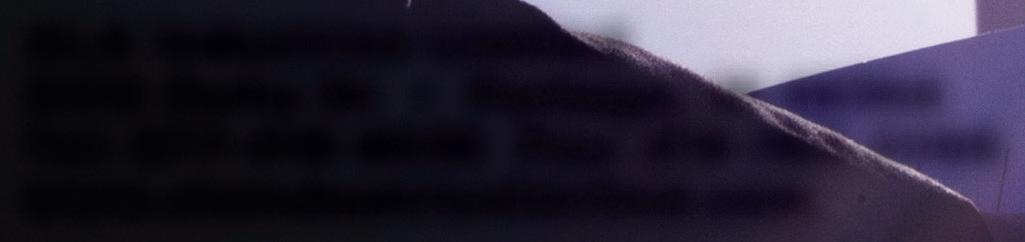
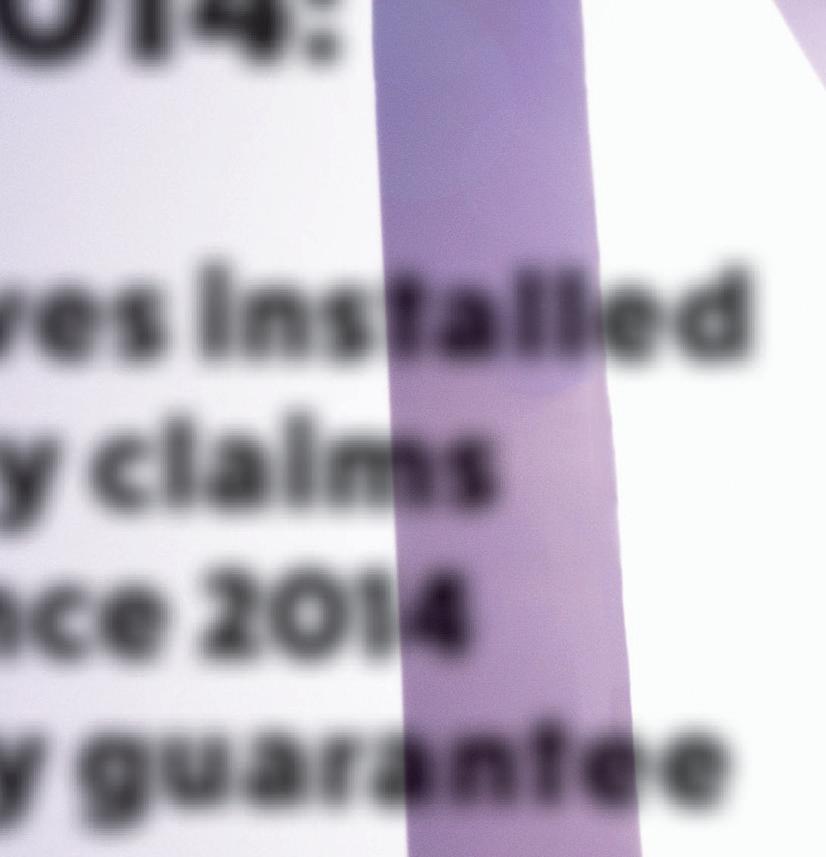

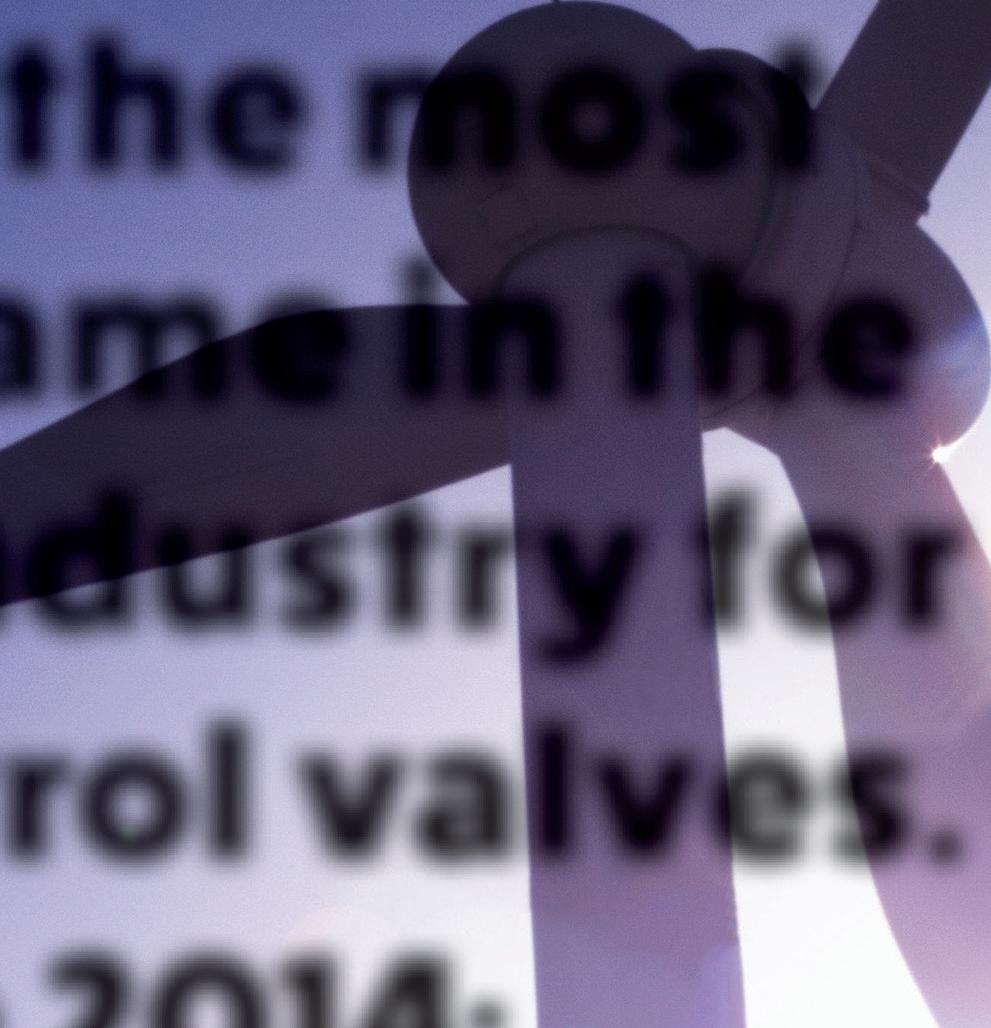
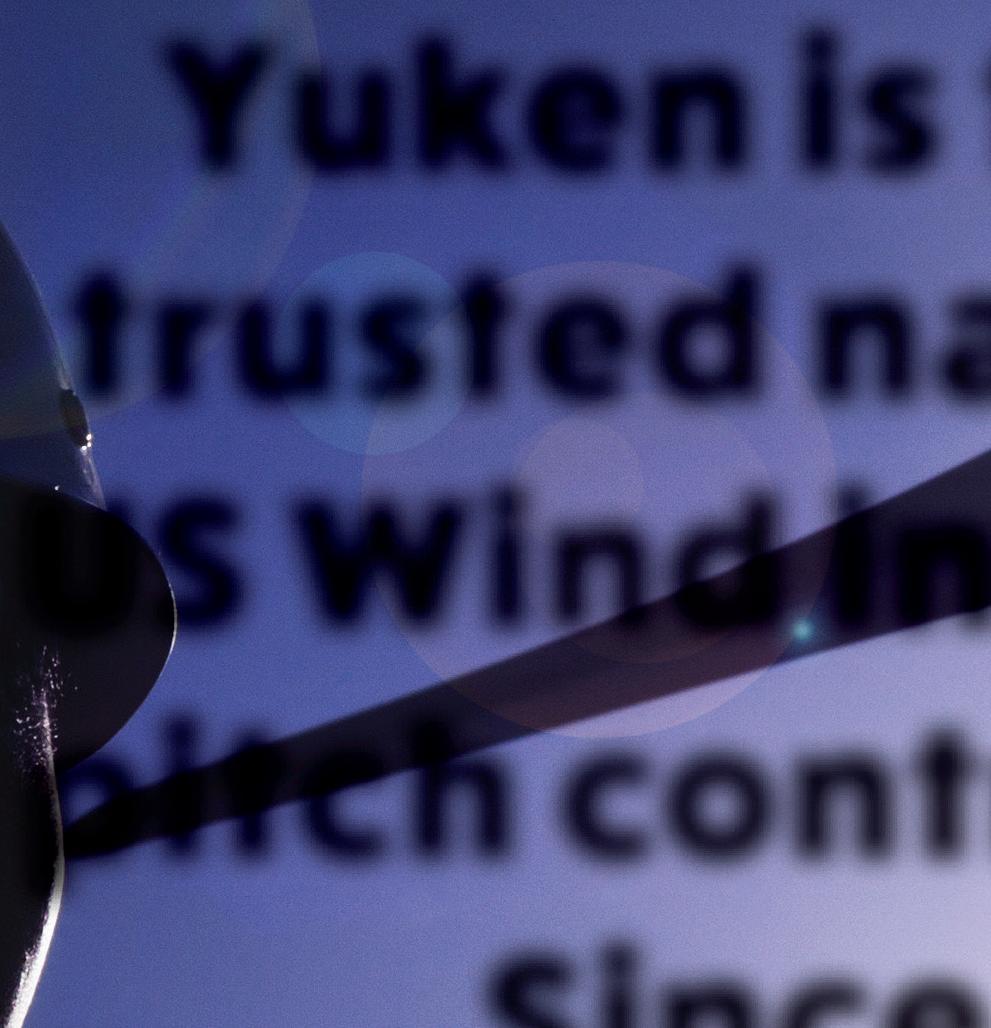
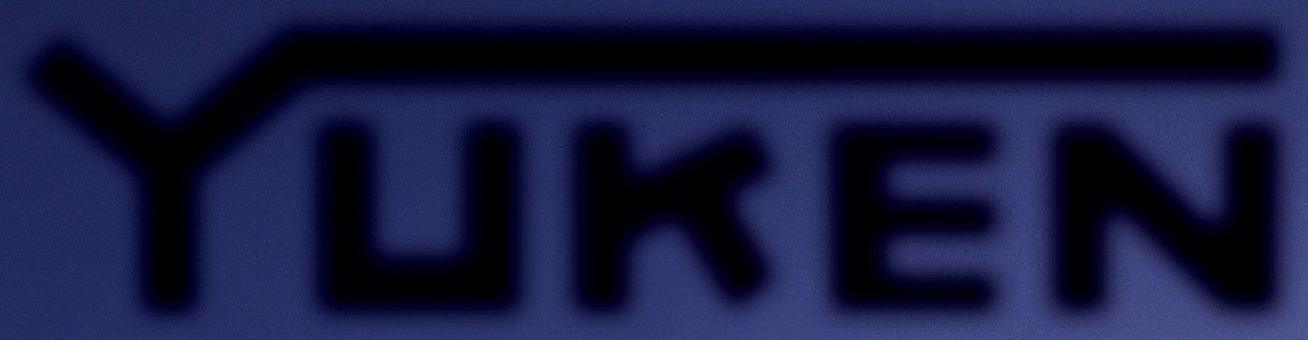

What better way to test resistance than with Megger’s quality instruments? We make testing safe, accurate, and easy.
Reference Code: DLRO2_WP_FEB
The DLRO2 handheld 2 Amp low resistance ohmmeter, coupled with the new KC-C series test leads, is perfect for testing wind turbines. The DLRO2 measures the resistance between the turbine’s blade tip to the ground connection using the KC-C long test leads.
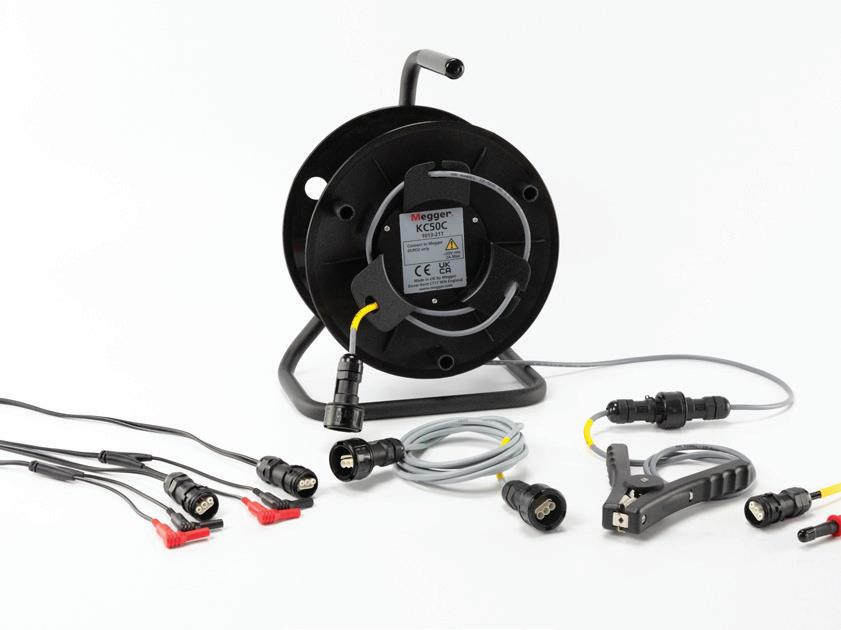
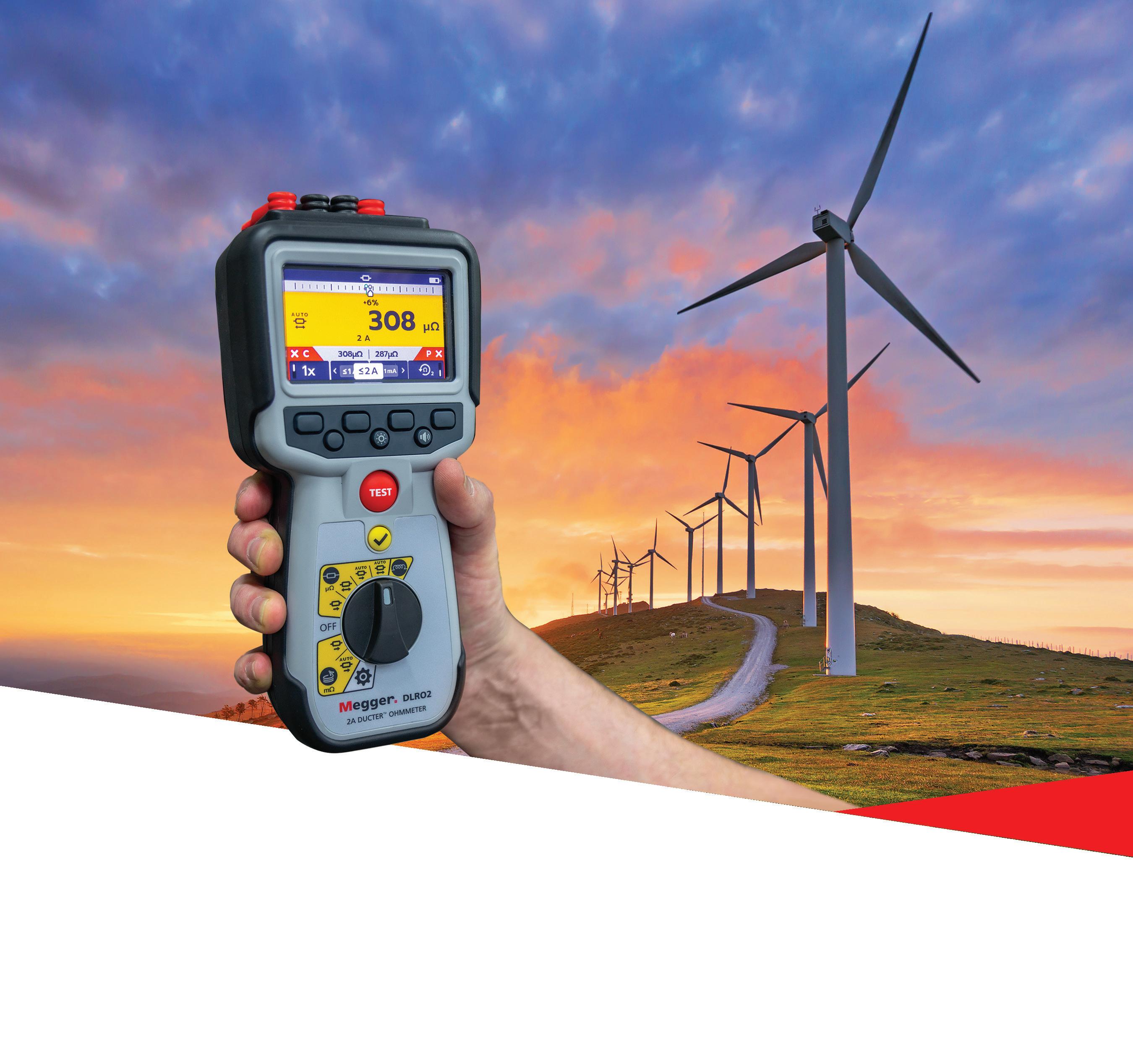
With a combined weight of less than 20 pounds, the DLRO2 and KC-C leads are the perfect tools when testing at heights. Lightweight tools are a necessity for the safety and comfort of wind technicians.
KC-C long test leads
Testing lightning protection on wind turbines?
Visit our website: US.MEGGER.COM
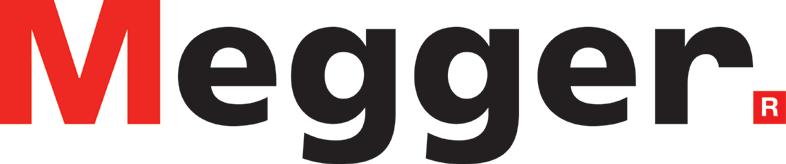
For a FREE VoltclawTM non-conductive tool visit us.megger.com/getbook
Megger has the right tools for you!
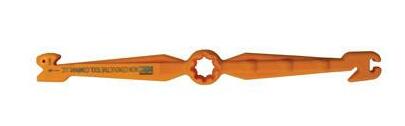
Marketing Graphic Designer Hannah Bragg hbragg@wtwhmedia.com
Events JenniferManagerKolasky jkolasky@wtwhmedia.com
PUBLISHER
Accounts Receivable JamilaSpecialistMilton jmilton@wtwhmedia.com
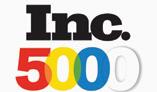
IN-PERSON EVENTS
Videographer Manager Bradley Voyten bvoyten@wtwhmedia.com
Web Development Manager B. David Miyares dmiyares@wtwhmedia.com
Senior Graphic Designer Allison Washko awashko@wtwhmedia.com
Event Marketing Specialist Olivia Zemanek ozemanek@wtwhmedia.com
KaraVideographerSingleton ksingleton@wtwhmedia.com
egillespie@wtwhmedia.com
Digital Production Specialist Elise Ondak eondak@wtwhmedia.com
VP of Creative Services Mark Rook mrook@wtwhmedia.com
Digital Production Manager Reggie Hall rhall@wtwhmedia.com
Front End Developer Melissa Annand mannand@wtwhmedia.com
kpickerel@wtwhmedia.com
Digital Production Specialist Nicole Lender nlender@wtwhmedia.com
EDITORIAL
WINDPOWER ENGINEERING & DEVELOPMENT does not pass judgment on subjects of controversy nor enter into disputes with or between any individuals or organizations.
Art MatthewDirectorClaney mclaney@wtwhmedia.com
VIDEO SERVICES
WINDPOWER ENGINEERING & DEVELOPMENT does not endorse any products, programs, or services of advertisers or editorial contributors. Copyright© 2022 by WTWH Media, LLC. No part of this publication may be reproduced in any form or by any means, electronic or mechanical, or by recording, or by any information storage or retrieval systems, without written permission from the publisher.
SUBSCRIBER SERVICES: To order a subscription or change your address, please email: please visit our web site at www.windpowerengineering.com
Customer TracyRepresentativeServicePowers tpowers@wtwhmedia.com
Editorial KellyRenewablesDirector,Pickerel
Webinar Coordinator Kim Dorsey kdorsey@wtwhmedia.com
Customer JoAnnRepresentativeServiceMartin jmartin@wtwhmedia.com
CREATIVE SERVICES & PRINT PRODUCTION
BrianControllerKorsberg bkorsberg@wtwhmedia.com
WTWH Media, LLC 1111 Superior Avenue, Suite 2600, Cleveland, OH 44114 Ph: Fax:888.543.2447888.543.2447
Graphic Designer Mariel Evans mevans@wtwhmedia.com
FINANCE
POSTMASTER: Send address changes to: Windpower Engineering & Development, 1111 Superior Avenue, Suite 2600, Cleveland, OH 44114
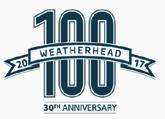
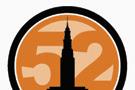



Customer ReneeRepresentativeServiceMassey-Linston renee@wtwhmedia.com
CUSTOMER SERVICE
Associate Editor
Customer Service StephanieManager Hulett shulett@wtwhmedia.com
ONLINE DEVELOPMENT & PRODUCTION
WINDPOWER ENGINEERING & DEVELOPMENT is also an independent forum for the expression of opinions relevant to industry issues. Letters to the editor and by-lined articles express the views of the author and not necessarily of the publisher or publication. Every e ort is made to provide accurate information. However, the publisher assumes no responsibility for accuracy of submitted advertising and editorial information. Non-commissioned articles and news releases cannot be acknowledged. Unsolicited materials cannot be returned nor will this organization assume responsibility for their care.
VP of Digital Marketing Virginia Goulding vgoulding@wtwhmedia.com
SUBSCRIPTION RATES: Free and controlled circulation to qualified subscribers. Non-qualified persons may subscribe at the following rates: U.S. and possessions, 1 year: $125; 2 years: $200; 3 years $275; Canadian and foreign, 1 year: $195; only U.S. funds are accepted. Single copies $15. Subscriptions are prepaid by check or money orders only.
AudienceDirector, Development Bruce Sprague bsprague@wtwhmedia.com
Digital Media Manager Patrick Curran pcurran@wtwhmedia.com
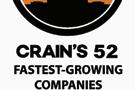
WINDPOWER ENGINEERING & DEVELOPMENT (ISSN 2163-0593) is published four times per year in February, May, September and a special issue in December by WTWH Media, LLC, 1111 Superior Avenue, Suite 2600, Cleveland, OH 44114. Periodicals postage paid at Cleveland, OH and additional mailing o ces.
Digital EmilyCoordinatorMarketingGillespie
Billy Ludt bludt@wtwhmedia.com
Digital SamanthaMarketingProduction/DesignerKing sking@wtwhmedia.com
Webinar Coordinator Halle Sibly hkirsh@wtwhmedia.com
GarrettVideographerMcCafferty gmcca erty@wtwhmedia.com
MARKETING
Customer TrinidyRepresentativeServiceLonggood tlonggood@wtwhmedia.com
Courtney Nagle 440.523.1685cseel@wtwhmedia.com
WINDPOWER ENGINEERING & DEVELOPMENT2 SEPTEMBER 2022www.windpowerengineering.com 2011 - 2021 2014 Winner 2014 - 2016 2013 - 2017 asbpe.org BRONZE REGIONAL AWARD 2022
Digital Marketing Manager Taylor Meade tmeade@wtwhmedia.com
How lidar powers wind energy in environmentsoffshore
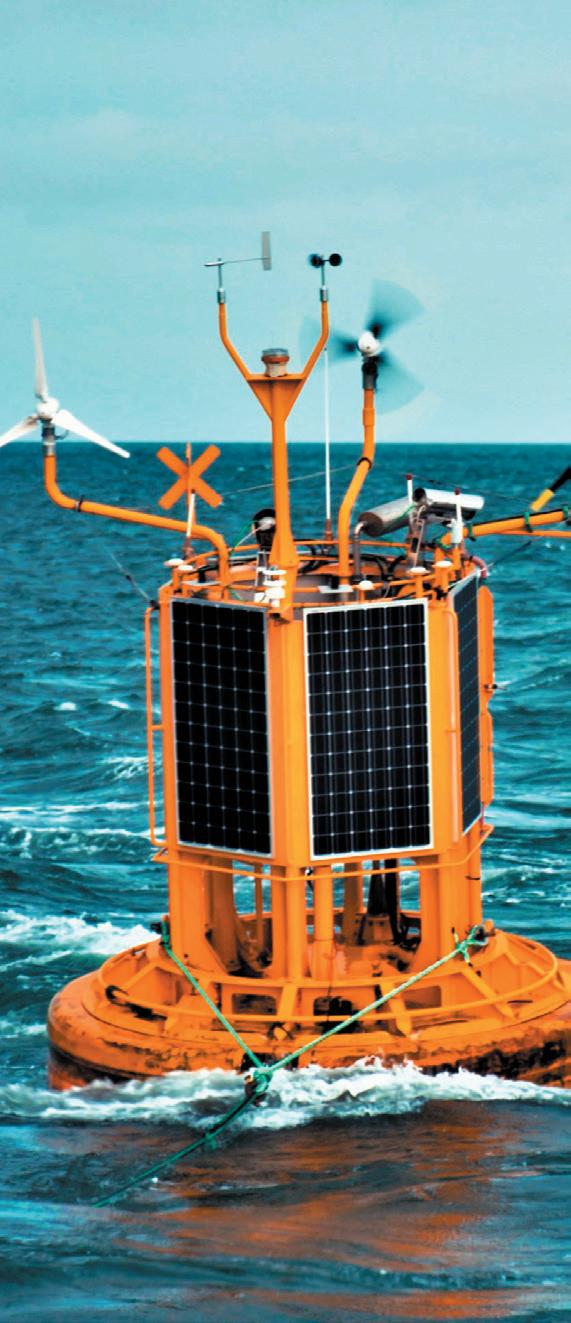
and offshore wind project announcements from across the country. WINDPOWER ENGINEERING & DEVELOPMENT 3SEPTEMBER 2022 www.windpowerengineering.com INSIDE See the latest wind power developments and U.S. project news as well as expert webinars and more on our website today. FIND US ONLINE WINDPOWERENGINEERING.COM
Considered by many to be the most critical step of any wind farm project, wind resource assessment establishes the foundation for determining a project’s business case and acquiring financing.
A
Setting the standard for wind maintenanceenergy
0408 0814 22190507 22 26 14
On-
FEATURES
Prioritizing innovation over process is hurting manufacturing

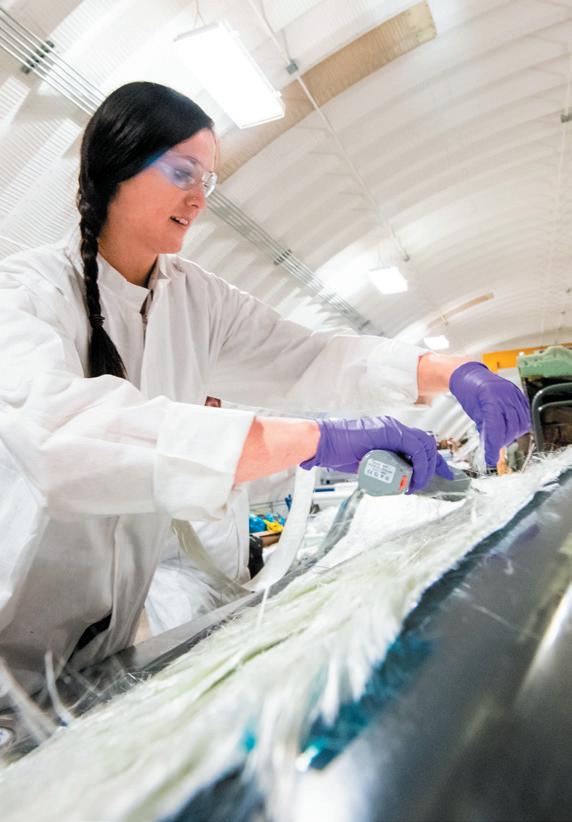
How engineering simulation software can increase offshore wind adoption
Given the scale and importance of the task, it is essential for the wind industry to unite around an agreed set of standards and practices. Best practice standards can help turbine operators enhance operations.
WIND WORK AROUND THE UNITED STATES
selection of product and policy news from our website.


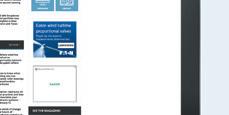
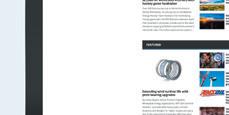
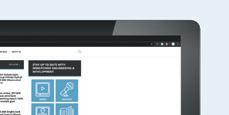
WINDPOWER ENGINEERING & DEVELOPMENT // VOL. 14 NO. 3
A 30-GW offshore goal by 2030 in the United States is ambitious and will require detailed engineering. One thing that shouldn’t be overlooked is the cabling needed to get this wind energy to shore and into communities.
Using simulation software, engineers can create detailed models of wind turbines to analyze performance under different conditions. These models can lead to lower costs and shorter time frames to design and build turbines. Cover image: iStock
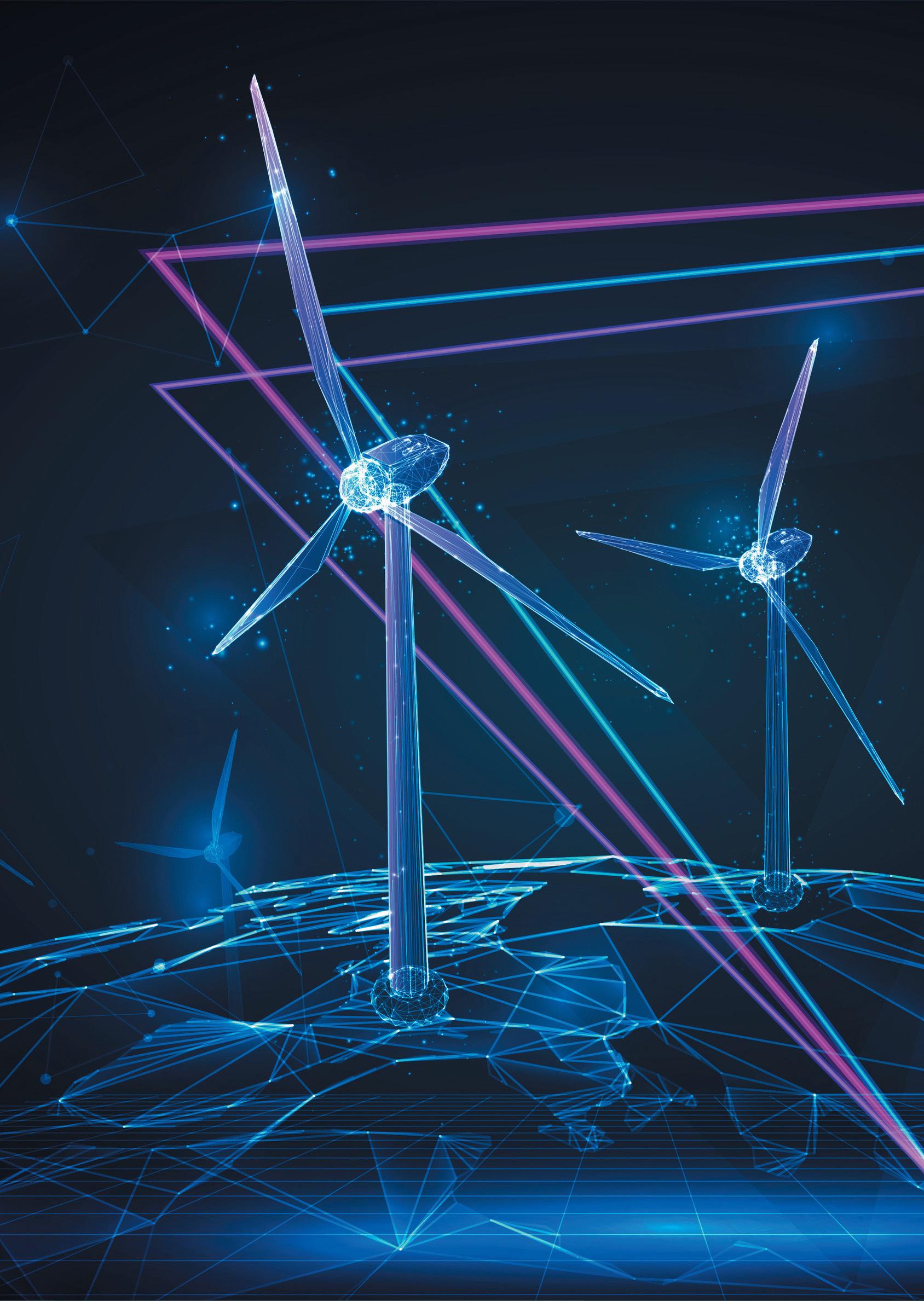
COVER STORY
IN EVERY ISSUE
The failure to capture and communicate engineering processes and knowledge to nonspecialists prevents companies from streamlining and automating more of their manufacturing processes.
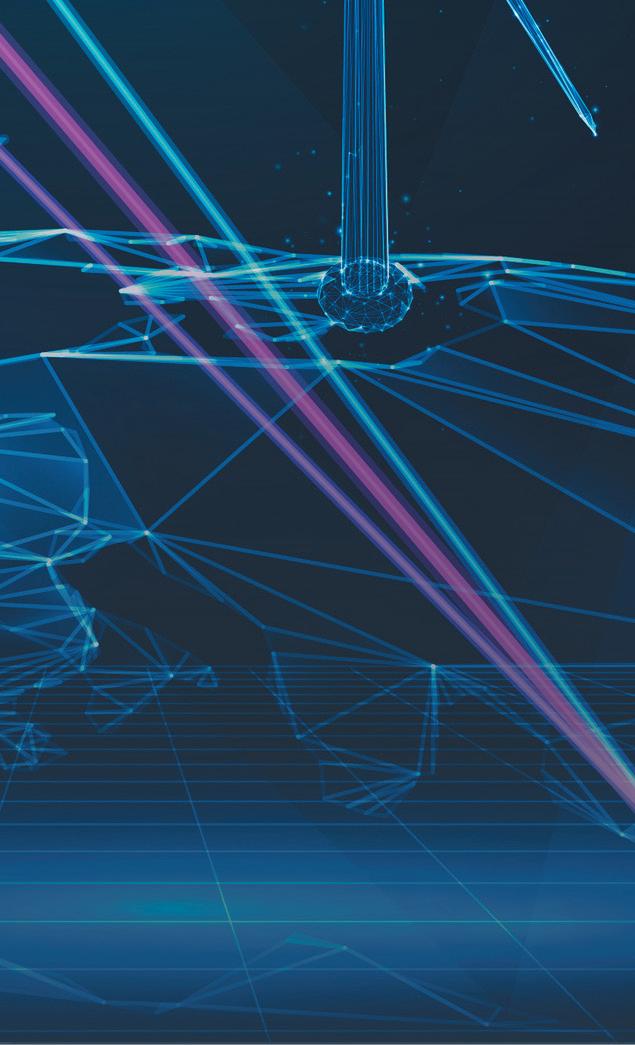
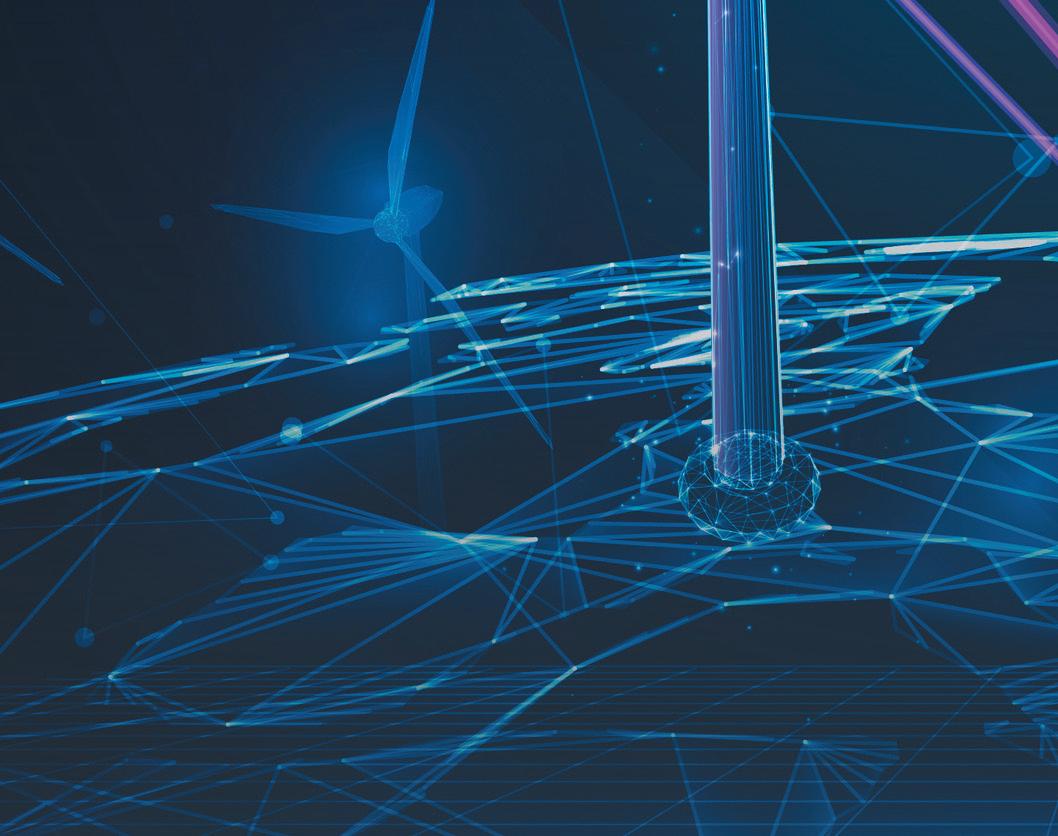
Plugging offshore wind power into our energy grid
WINDWATCHCONTRIBUTORS
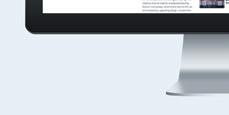
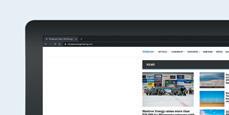
JOHN CROWTHER is Senior Principal, Environmental Services, for Stantec. John has over 35 years of environmental consulting experience. A geologist by education and training, John applies his diversified experience in the geologic and physical environment as well as the marine ecological environment. John brings together Stantec’s environmental services and power engineering groups to deliver integrated solutions to Stantec’s offshore wind clients.
MATTHIEU BOQUET
RALPH KURTH
CONOR WILKINSON is the EAME Commercial Brand Manager at ExxonMobil, responsible for a range of Mobil solutions for the commercial sector. Conor has extensive experience in brand marketing, strategic planning, technical solutions and sales management and was formerly the Europe Energy Sales Manager with a customer base across conventional, renewable, and decentralized power generation. Conor began his career in 2009 as a field engineer in the UK, providing technical services to customers in the energy and manufacturing sectors. He is a native of Ireland and graduated from Queen’s University Belfast with a Masters of Chemical Engineering.
WINDPOWER ENGINEERING & DEVELOPMENT
RALPH KURTH is Senior Principal, Energy, for Stantec. With more than 35 years of experience, Ralph has worked on a range of power system projects. His focus is currently on HVDC transmission systems, AC substations and their automation systems. While his assignments are wide ranging and complex, his goal remains the same — to provide solid advice to project teams and clients.
JAMES MONTGOMERY, VP of Solutions at Andea, has over 25 years’ experience in creating innovative solutions for the manufacturing sector across various industries. He has worked at companies including SpaceX, Apriso and ProDB Business Systems in positions including Lead Product Manager, Solution Architect, Business Analyst, Project Manager and Software Development Team Lead. James is responsible for managing Andea’s key functions in North America, including operations management, team management, customer and marketing relations, services and project delivery activities.
WINDPOWER ENGINEERING & DEVELOPMENT4 SEPTEMBER 2022www.windpowerengineering.com
GUILLAUME LECHATON JAMES MONTGOMERY
CONOR WILKINSON
JOHN CROWTHER
GUILLAUME LECHATON is Akselos’ Sales Director for Wind and New Energies, driving global sales and business development in the offshore wind industry. Guillaume has over 11 years of experience in the wind industry, having worked for a world-leading asset owner and a top three wind turbine manufacturer.
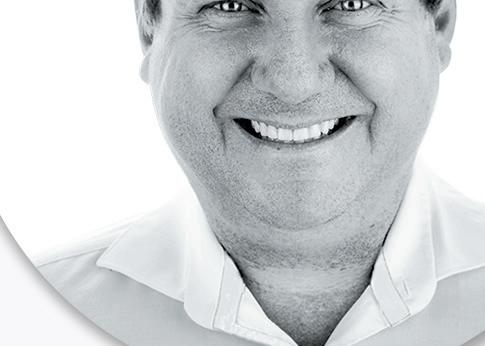


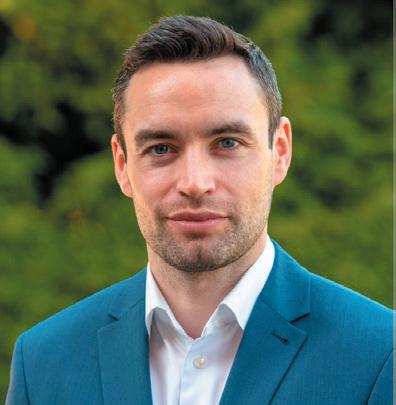
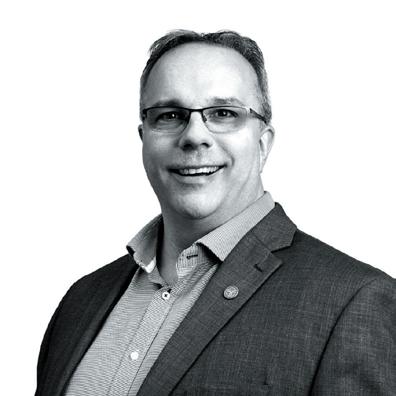
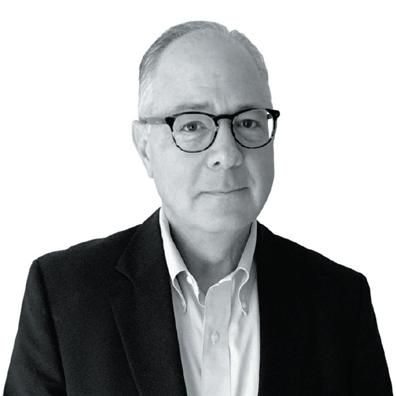
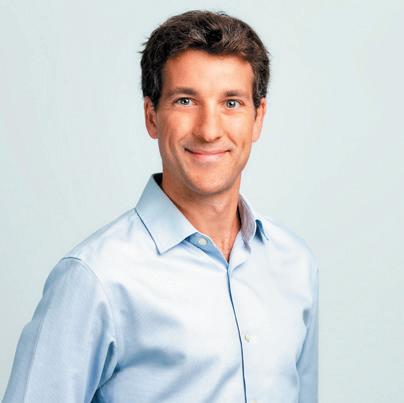
CONTRIBUTORS
MATTHIEU BOQUET is Head of Market and Offering – Wind Energy at Vaisala. In this role, he drives Vaisala’s renewable energy offerings to meet the industry’s high-level expectations while helping customers continually generate value from their projects.
SEPTEMBER 2022
Wind power provides more than 9% of the country’s electricity supply
The U.S. Department of Energy released three reports in mid-August detailing wind energy deployment in the country. According to the reports, wind accounted for 32% of U.S. energy capacity growth in 2021, employs 120,000 Americans and is providing more than 9% of total electricity nationwide. Wind accounts for more than 50% of the electricity generated in Iowa and 30%
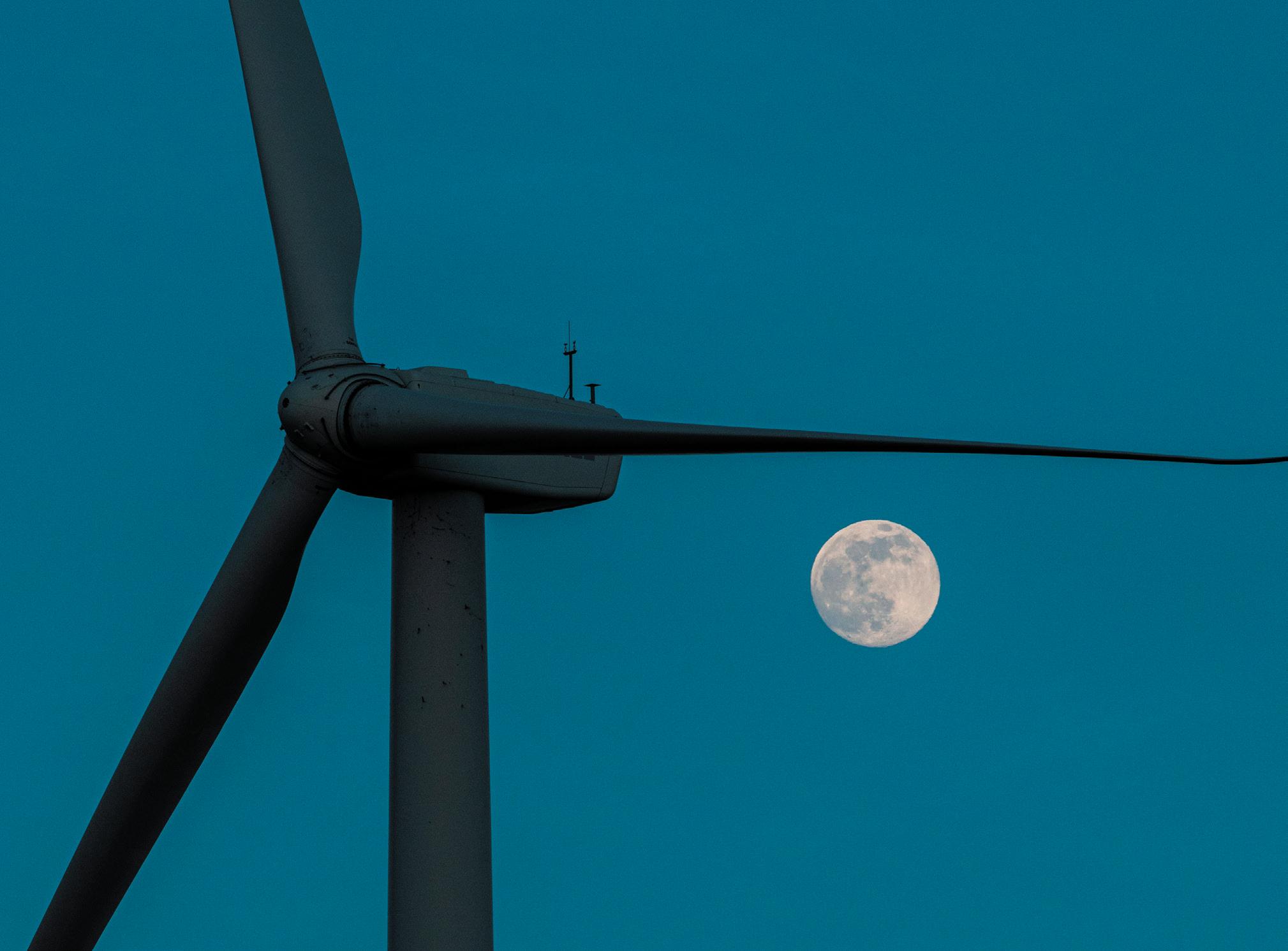
WIND WATCH
NREL
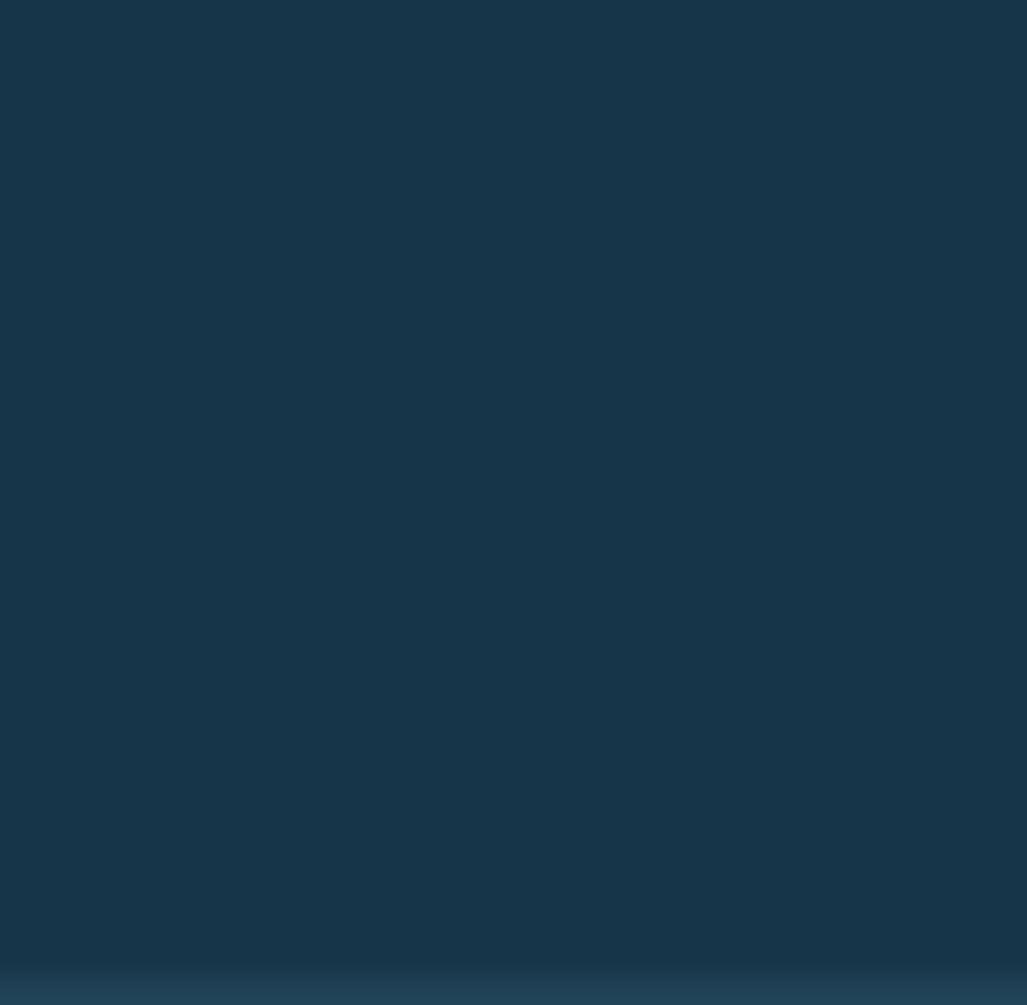
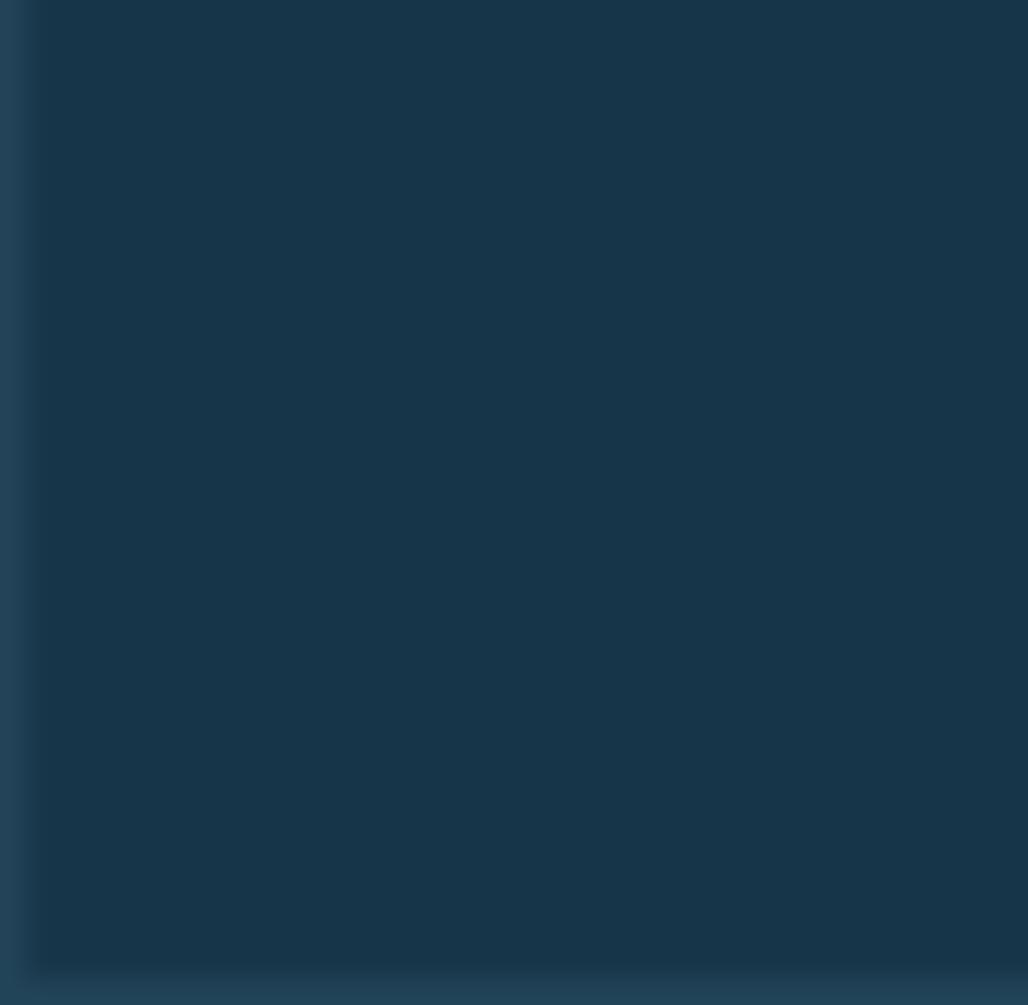
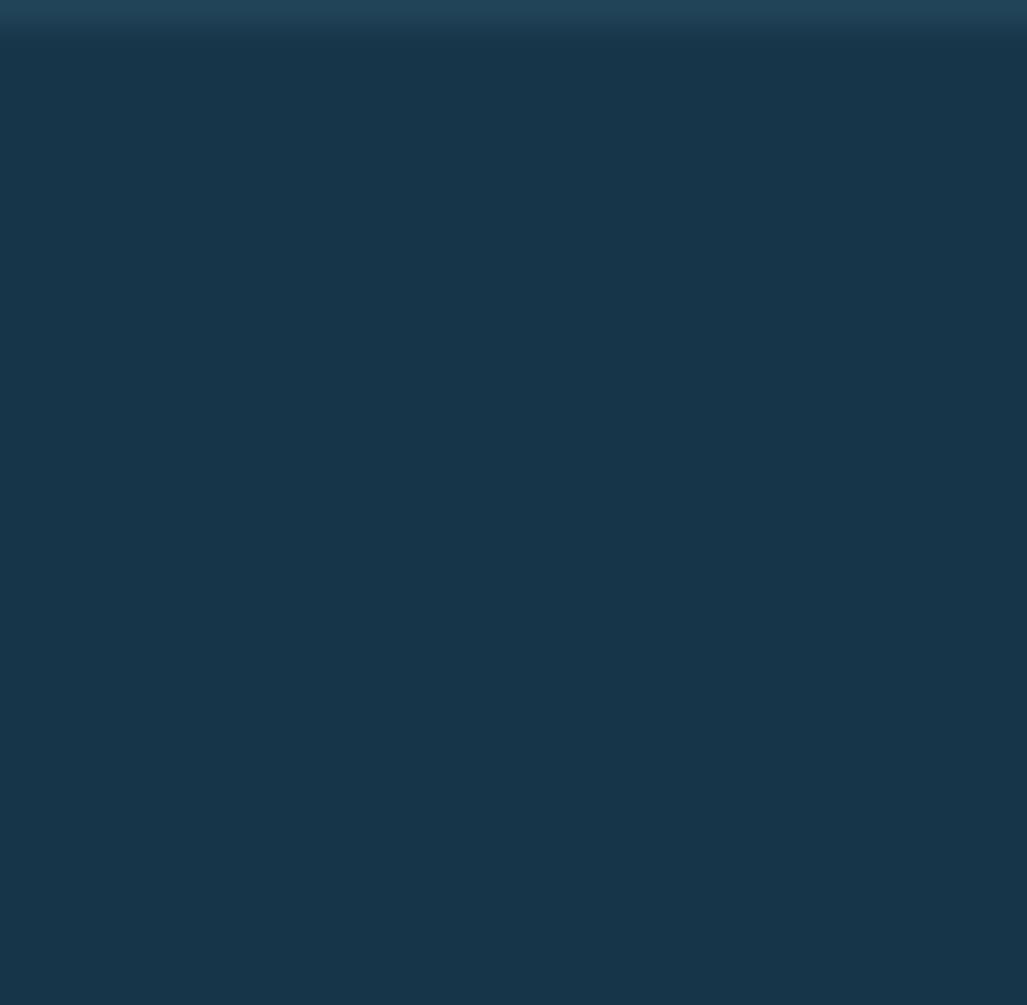
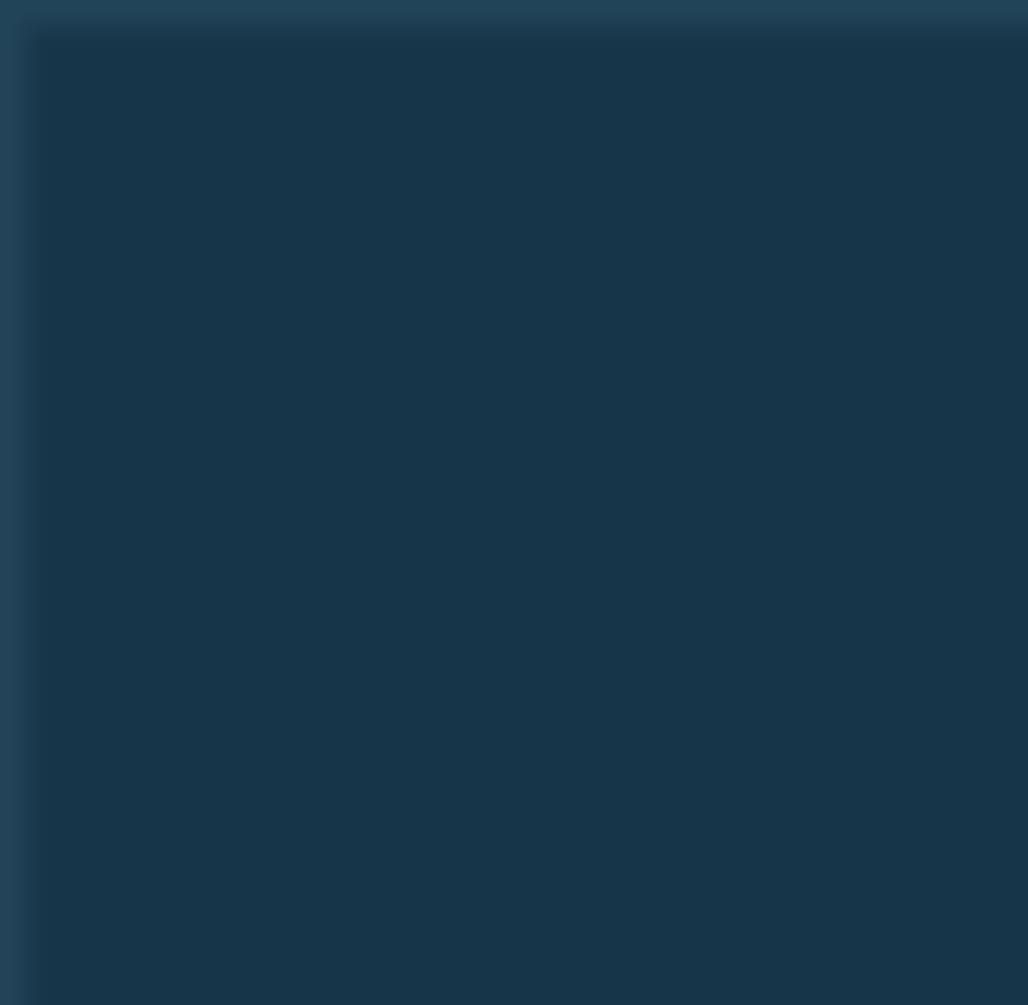
WINDPOWER ENGINEERING & DEVELOPMENT SEPTEMBER 2022
in Kansas, Oklahoma and North Dakota. That means wind is supplying enough electricity to power 40 million American homes. The Inflation Reduction Act, which includes long-term extensions of critical tax incentives supporting the deployment of land-based, offshore and distributed wind projects, should encourage more growth over the next 10 years.
WHAT’S NEW
WINDPOWER ENGINEERING & DEVELOPMENT 5SEPTEMBER 2022
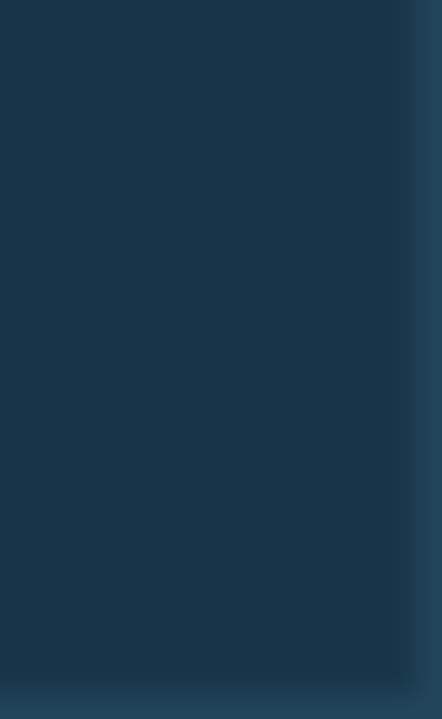
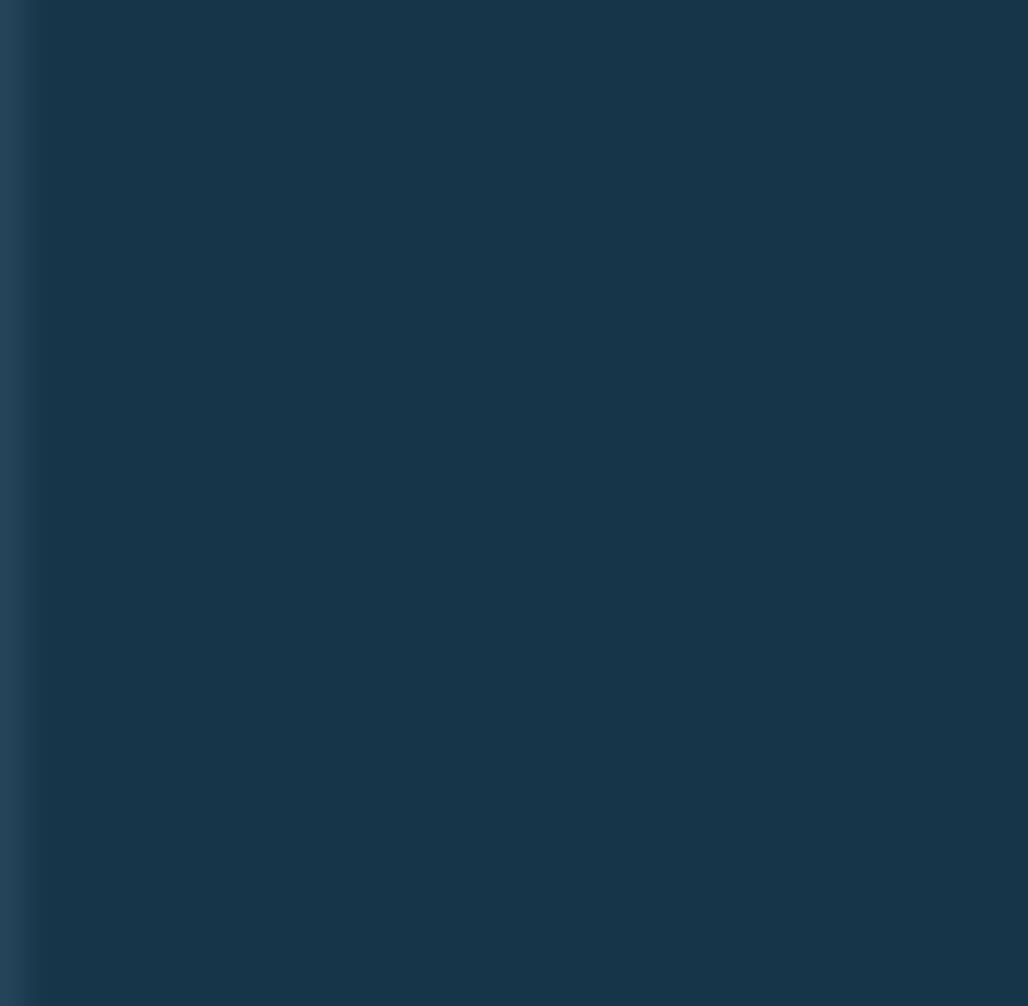

The Biden Administration joined 11 governors of East Coast states to launch a federal-state offshore wind implementation partnership to accelerate the offshore wind industry. The collaboration will identify elements of the supply chain that require expansion, like manufacturing facilities, ports and vessels.
WANT MORE NEWS? VISIT US AT WWW.WINDPOWERENGINEERING.COM/CATEGORY/NEWS
New York solicits third offshore wind solicitation application
WINDPOWER ENGINEERING & DEVELOPMENT SEPTEMBER 2022
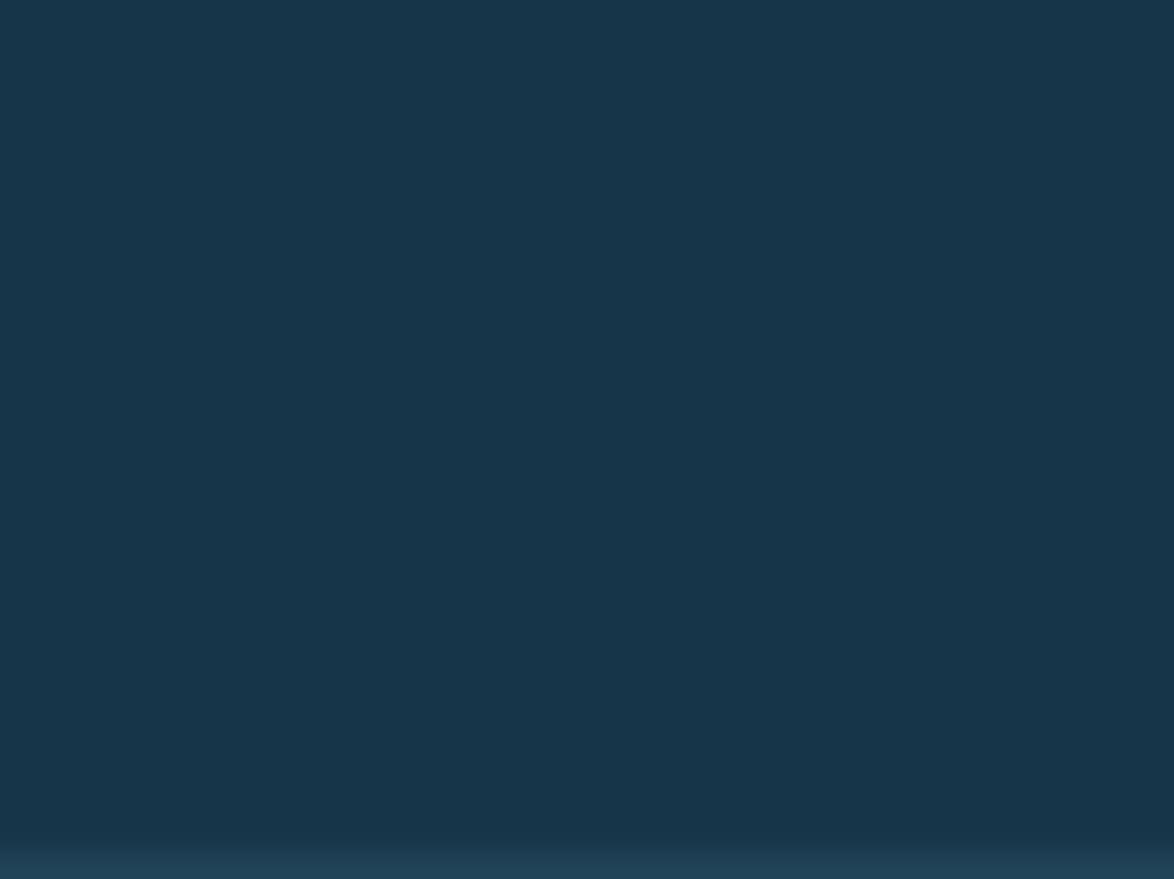
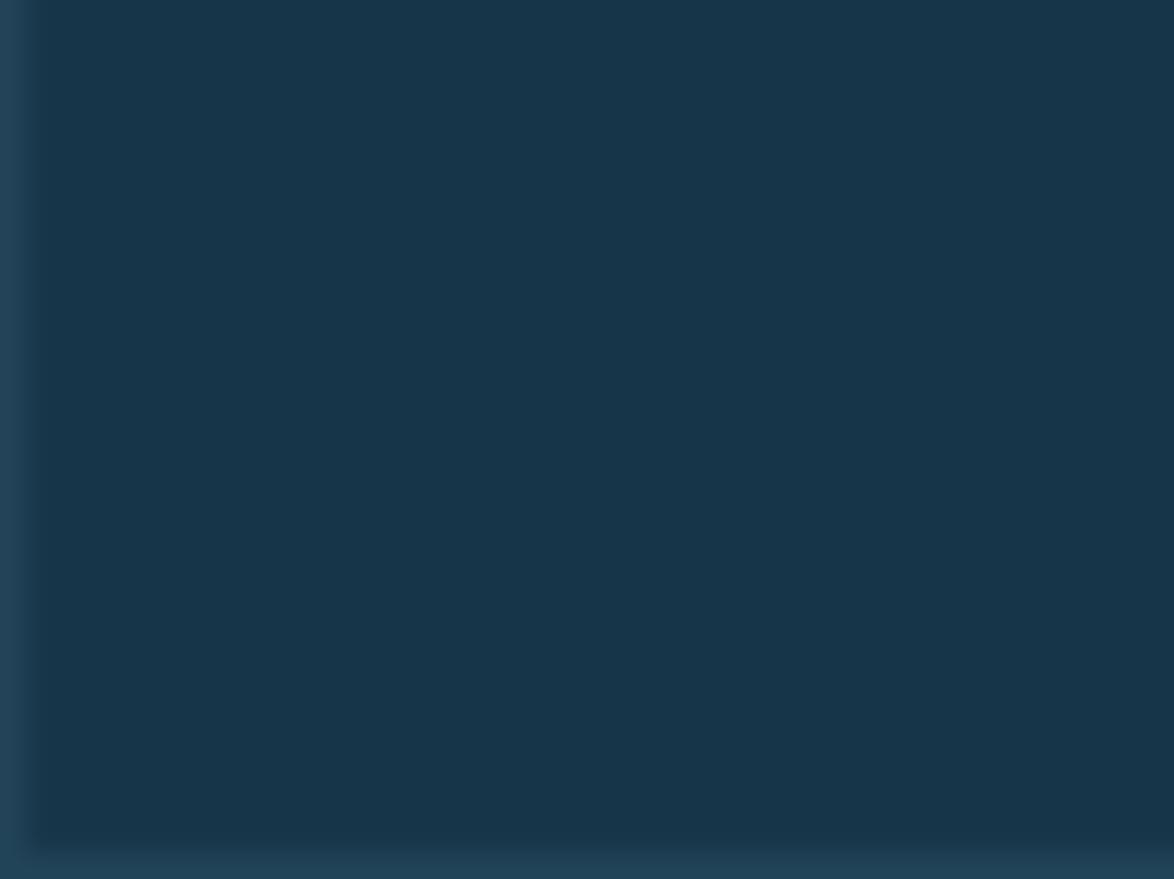

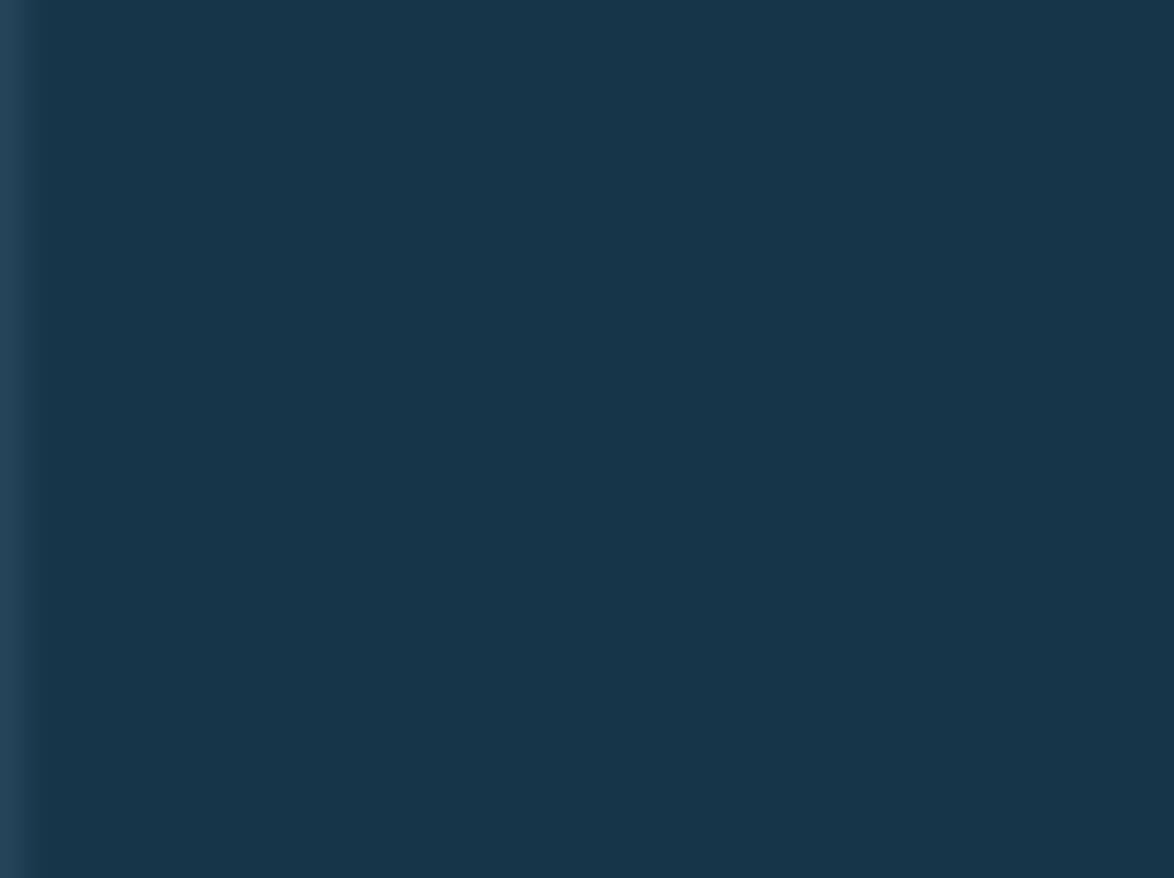
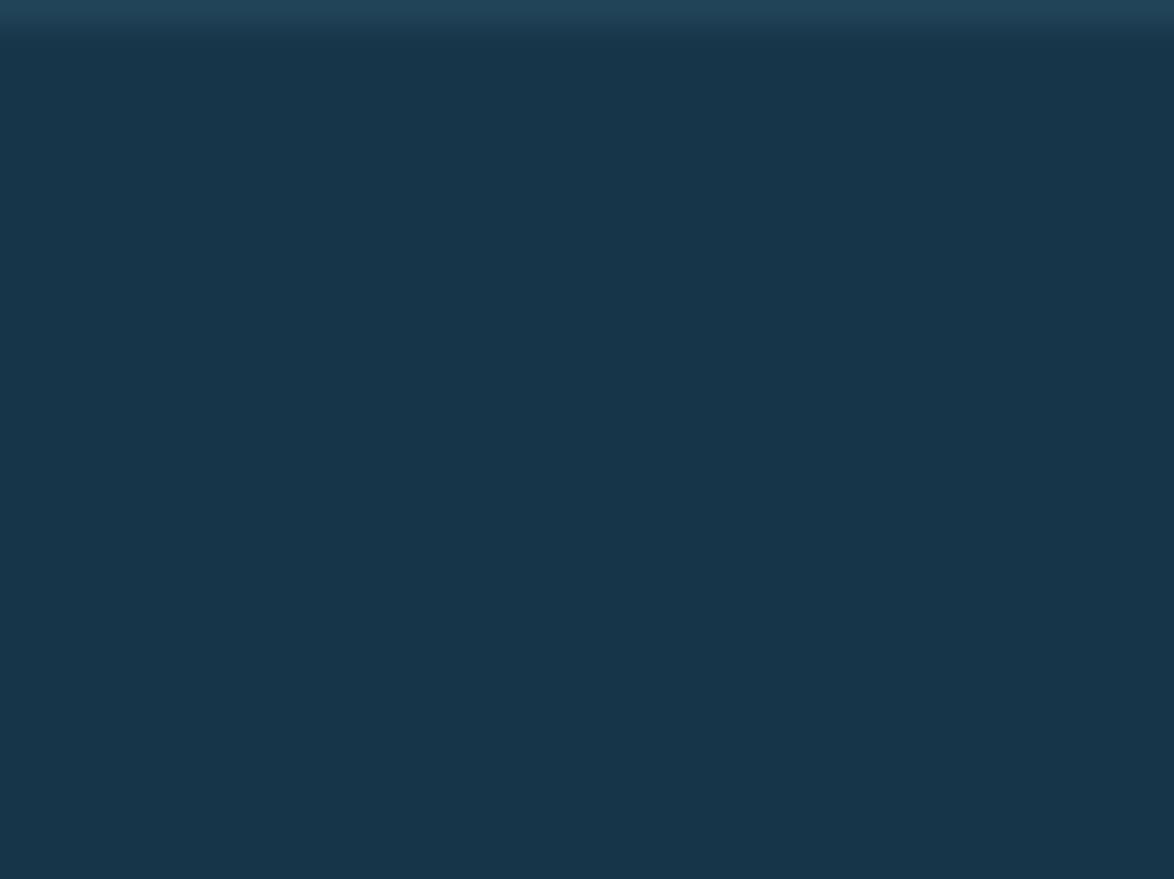
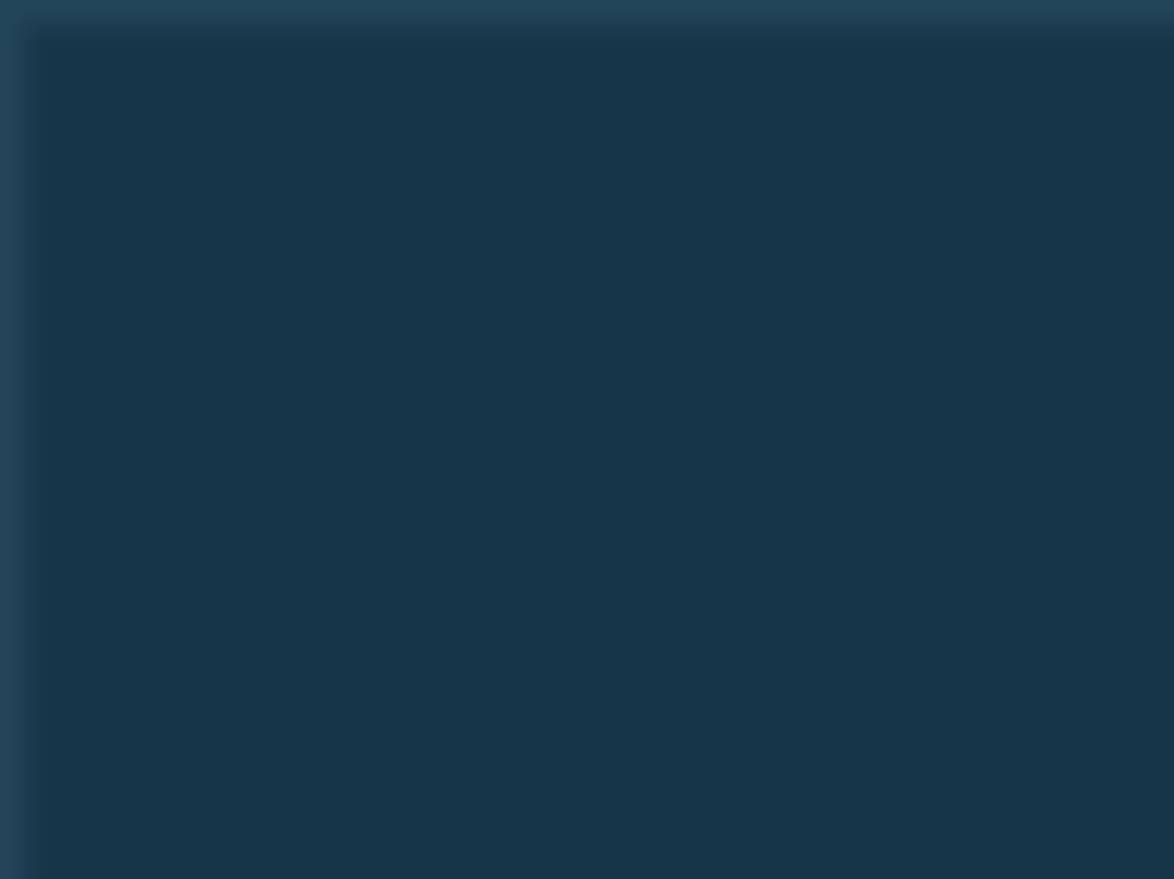
President Joe Biden announced three executive actions in July related to the climate crisis, and in response, the DOI has disclosed plans to explore the Gulf of New Mexico for offshore wind development. The first two areas for review are off the coasts of Galveston, Texas, and Lake Charles, Louisiana.
BOEM considers offshore wind development off Oregon coast
President Biden pushes for offshore wind in Gulf of Mexico
New York State released its third competitive offshore wind solicitation, seeking to procure 2,000 MW of offshore wind energy. The procurement includes the first phase of the state’s $500 million investment in offshore wind ports, manufacturing and supply chain infrastructure.
Offshore project South Fork Wind will undergo environmental review to enhance protection measures for endangered aquatic species native to the New York coastal region. South Fork wants to mitigate impacts to critical habitats, especially to the North Atlantic right whale, an endangered species.
The California Energy Commission established offshore wind energy construction goals of 2 to 5 GW by 2030 and 25 GW by 2045, as announced in a report in August. The report was created in collaboration with local Tribal governments, fisheries and other frequent ocean users.
East Coast governors tapped for offshore wind implementation goals
South Fork Wind project expands protectionsenvironmental
WIND WATCH
WHAT’S NEW | CONTINUED
California sets offshore wind deployment goal of 5 GW by 2030
WINDPOWER ENGINEERING & DEVELOPMENT6 SEPTEMBER 2022www.windpowerengineering.com
With the California coast pushing closer to development, the Bureau of Ocean Eenergy Management is exploring the potential of offshore wind power in waters off the Oregon coast. Two areas are being explored – Coos Bay Call and the Brookings Call – which begin about 12 nautical miles from the state’s shore.
RWE Renewables powers on 200-MW wind farm in ERCOT territory Texas
El Algodon Alto, a 200-MW onshore wind farm in San Patricio County, Texas, is operating and supplying power to the Electric Reliability Council of Texas south market. RWE Renewables completed construction of the 91 Vestas turbines in May.
WIND WORK AROUND THE UNITED STATES
200-MW wind project completed across 28,000 acres of farmland Oregon
Meta commissions 112-MW Michigan wind project Michigan
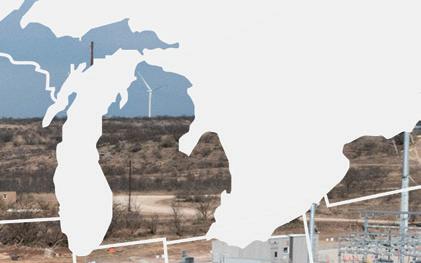
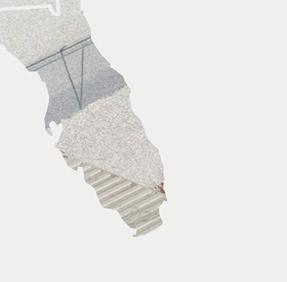
200-MW wind project completed Oregon
Algonquin Power & Utilities subsidiary Liberty is developing a 112-MW wind project in Huron County, Michigan, that will supply electricity to Meta’s operations in the state.The Deerfi eld II wind project will be adjacent to Liberty’s Deerfi eld I project and fi nish in 2023.
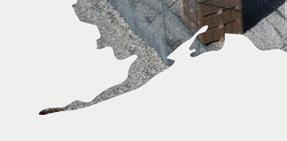
145-MW Panorama wind project supports interstate utility Colorado

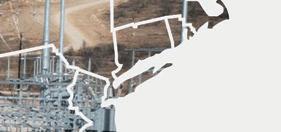


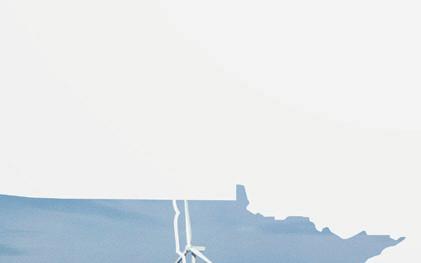
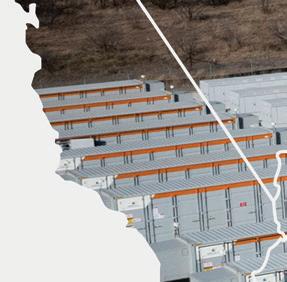

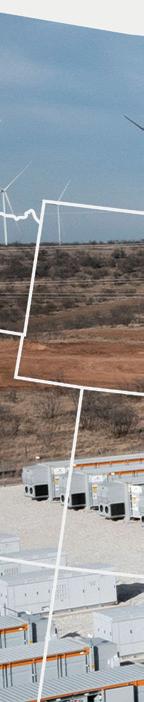
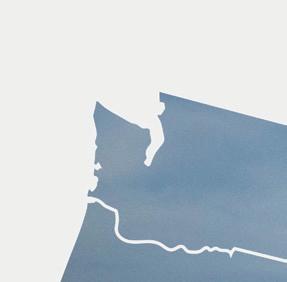
The 200-MW Golden Hills wind farm in Sherman County, Oregon, reached
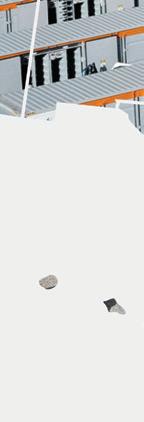
Great Pathfinder Wind nears commercial operations Iowa


Great Pathfinder Wind, a 224-MW wind project, should reach commercial operations in Q4 2022. Apex Clean Energy and IEA Constructors are involved on the project that will support Facebook parent company Meta’s operation under a long-term PPA for the full capacity of the project.
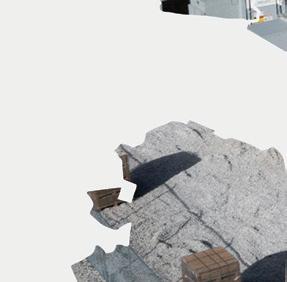
Construction has been approved for North America’s first freshwater offshore wind project. Icebreaker Wind is a proposed six-turbine site about 10 miles off the coast of Cleveland in Lake Erie. The project will test the viability of offshore wind farms in the Great Lakes.
A selection of recently completed wind projects.
Ohio Supreme Court approves Lake Erie offshore wind project Ohio
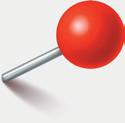

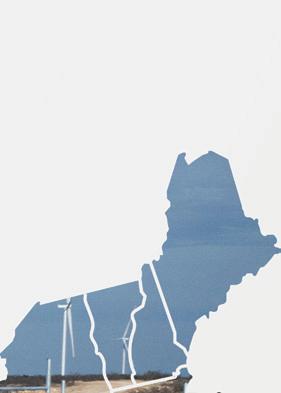
WINDPOWER ENGINEERING & DEVELOPMENT 7SEPTEMBER 2022



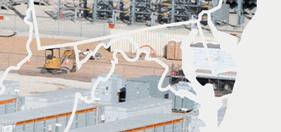

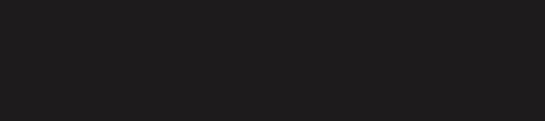
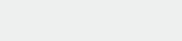
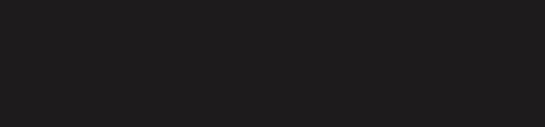

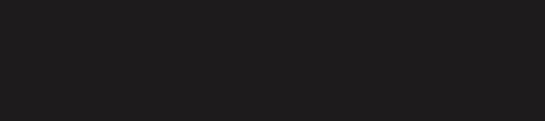
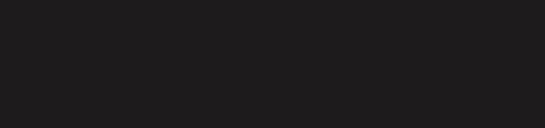
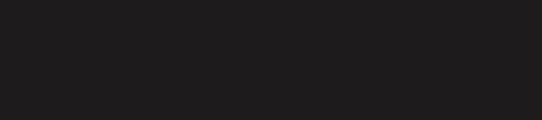
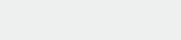


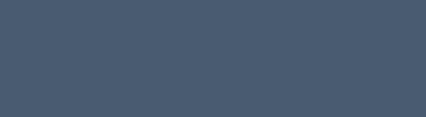


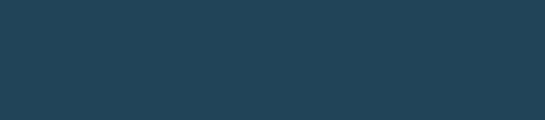
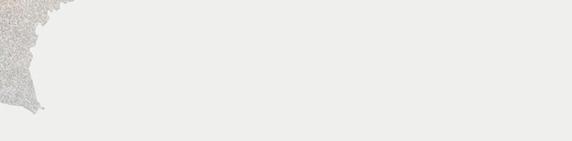


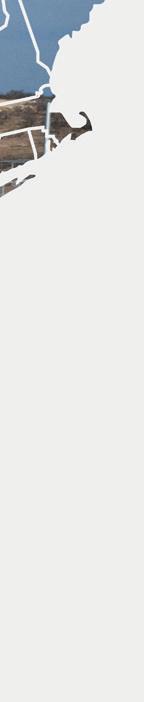
Enel Green Power finishes 350-MW wind + storage project Texas


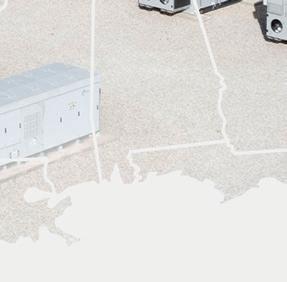

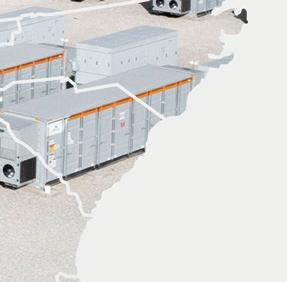

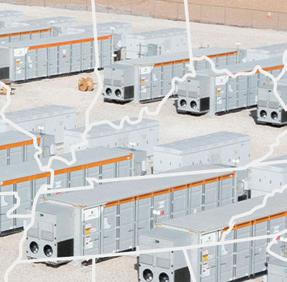
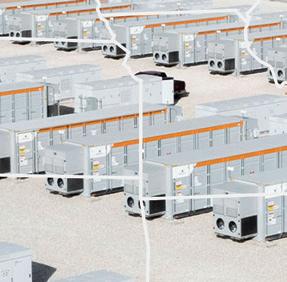
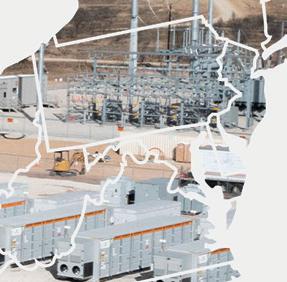

Leeward Renewable Energy completed construction of the 145-MW Panorama Wind Farm in Weld County, Colorado. Panorama will generate enough electricity to power approximately 53,000 homes in Colorado and New Mexico in the Guzman Energy utility territory.
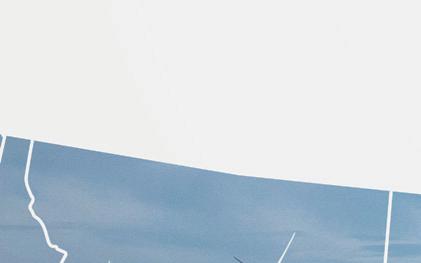
Enel Green Power completed the 350MW Azure Sky wind farm paired with a 137-MW/205-MWh battery storage facility. Located in Throckmorton County, Azure Sky’s energy output is relegated to several corporate customers through power purchase agreements.
The 200-MW Golden Hills wind farm in Sherman County, Oregon, reached commercial operation in Mayfor Puget Sound Energy. Golden Hills is built across approximately 28,000 acres of grazing and dry-land wheat farmland held by 37 landowners.
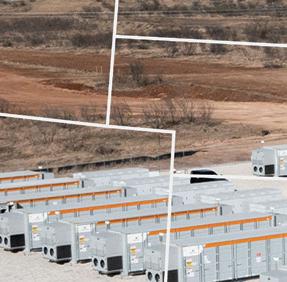
BY MATTHIEU BOUQUET
WINDPOWER ENGINEERING & DEVELOPMENT www.windpowerengineering.com LIDARENVIRONMENTSINWINDPOWERSHOWENERGYOFFSHORE
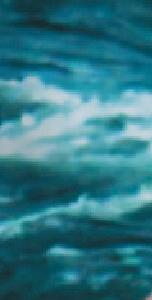
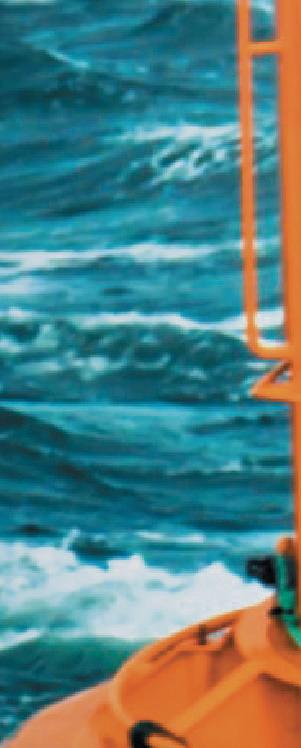
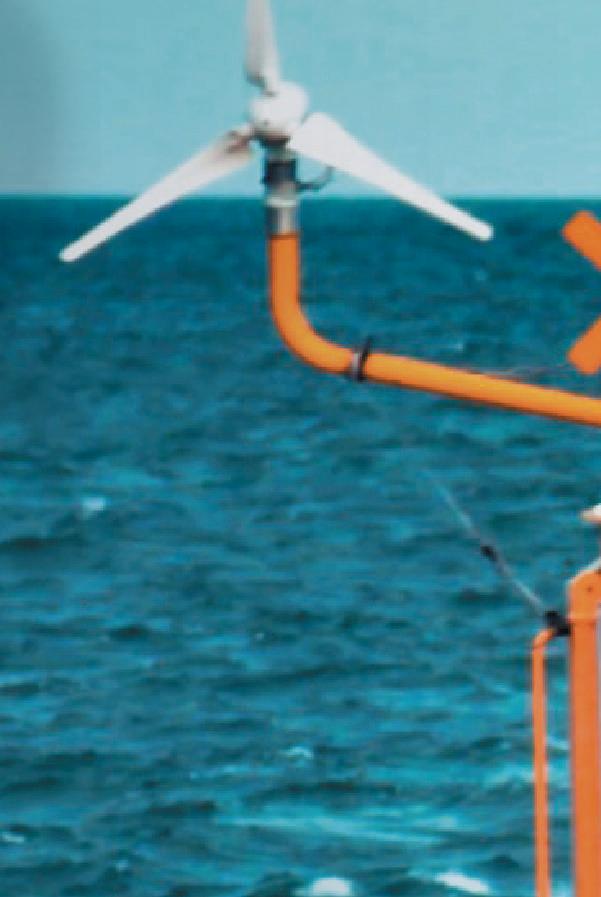
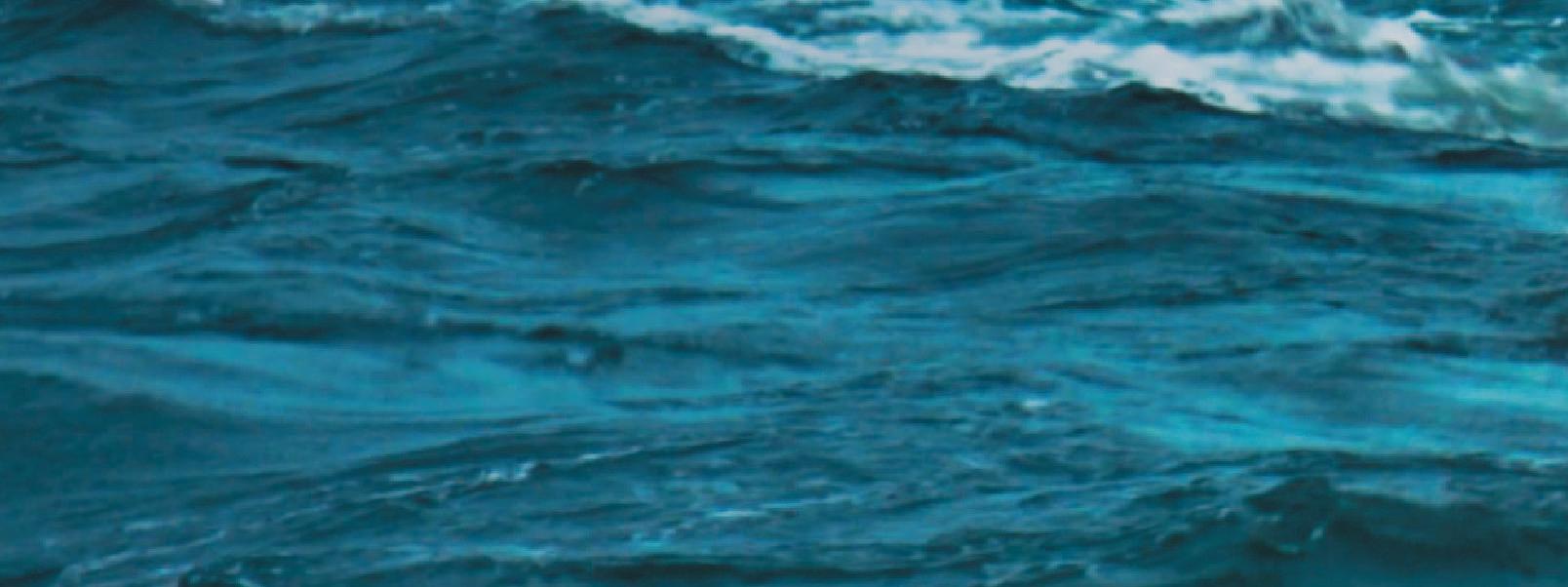
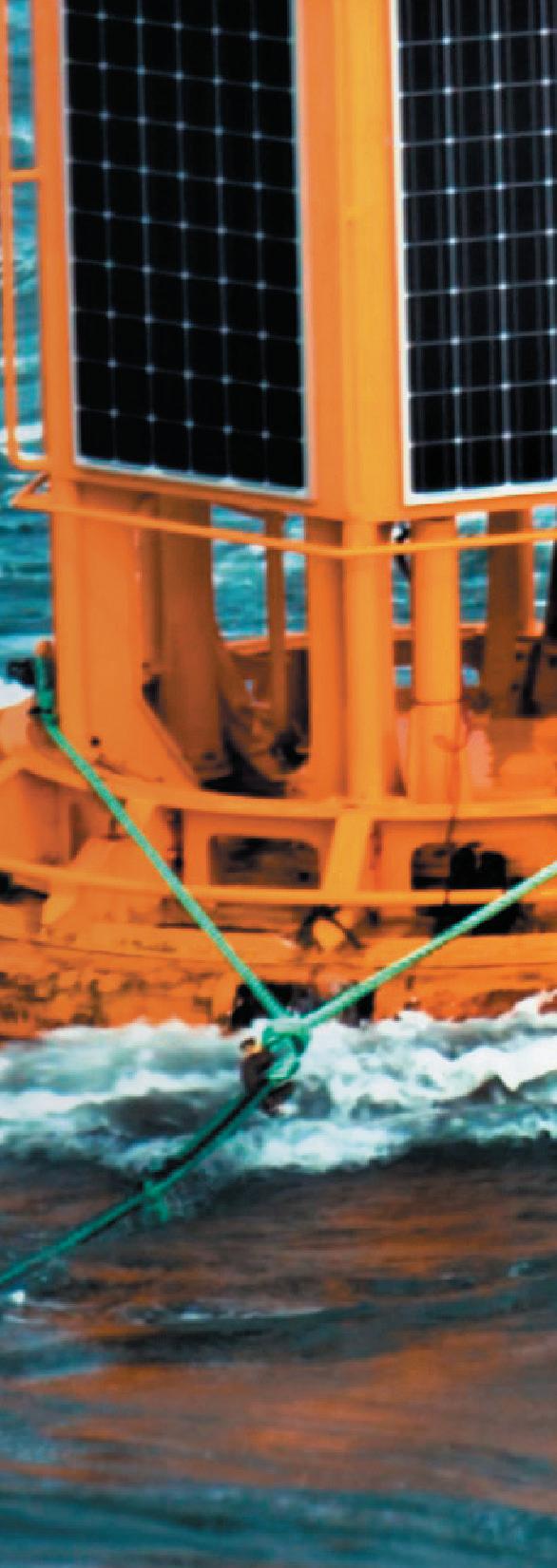
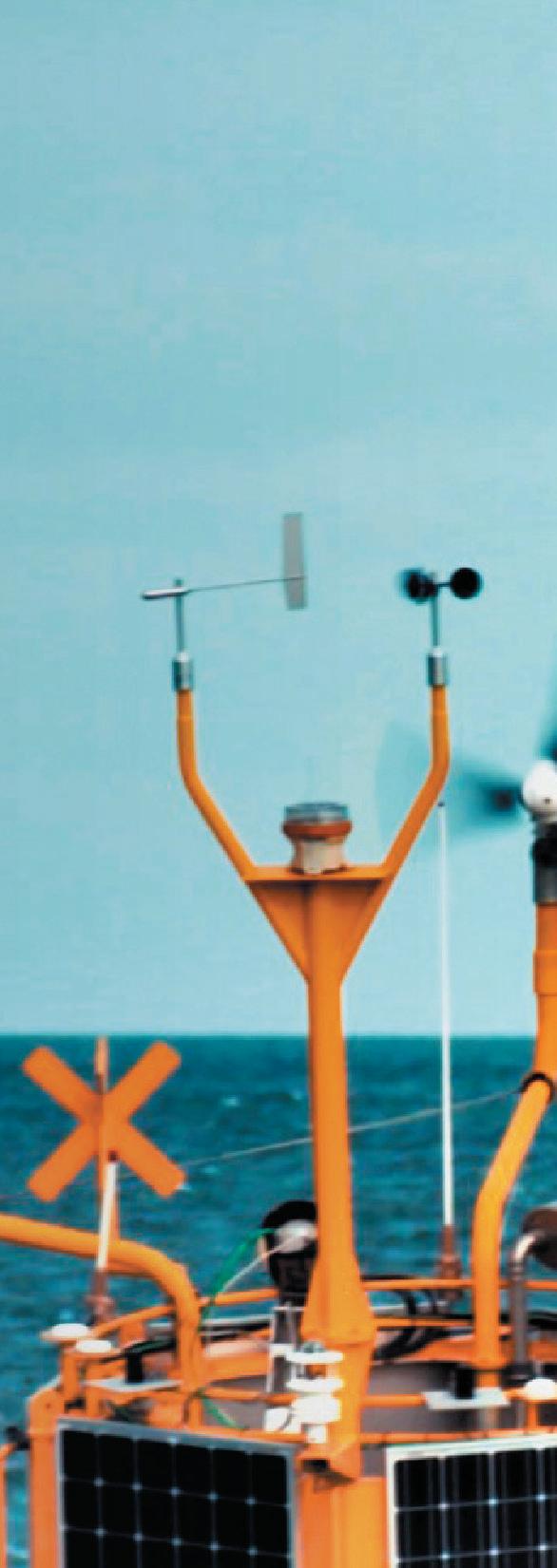
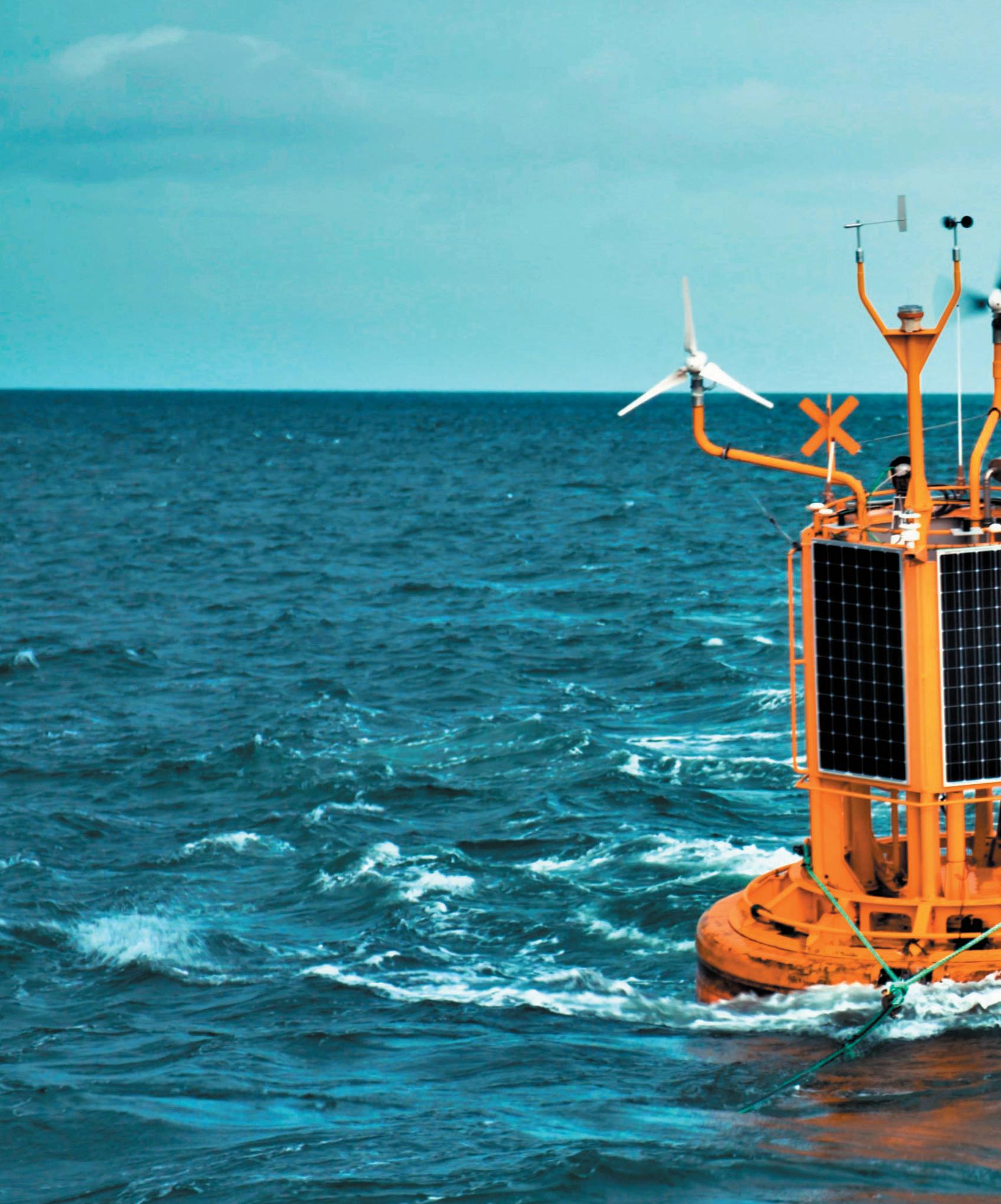
• HEAD OF MARKET AND OFFERING • WIND ENERGY • VAISALA 8 SEPTEMBER 2022
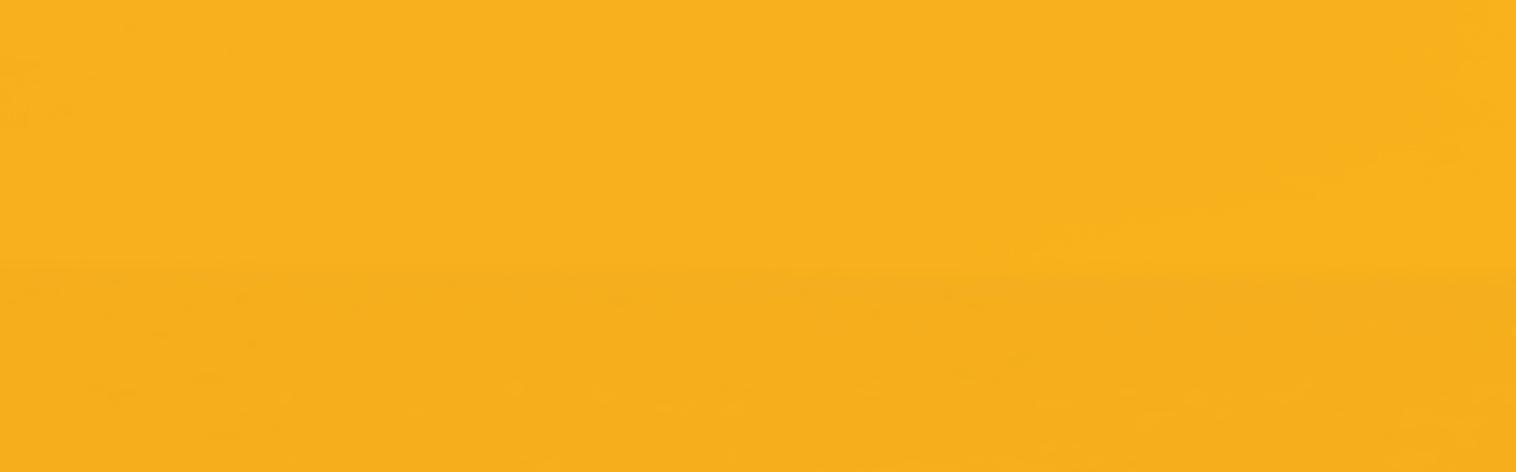


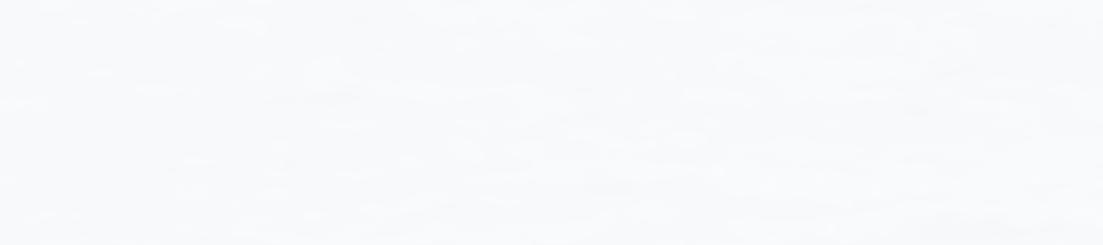
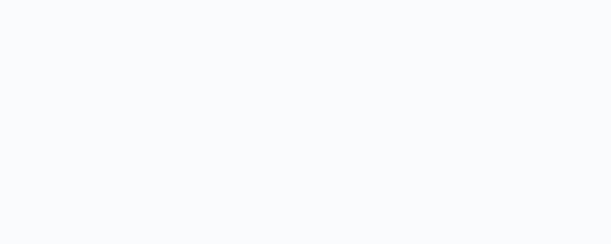
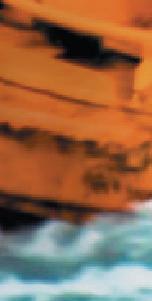


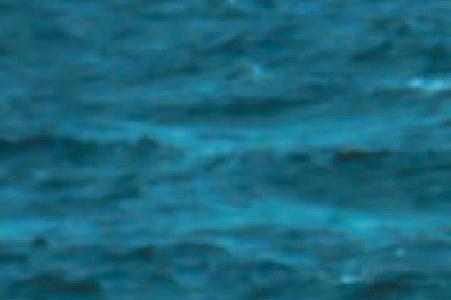
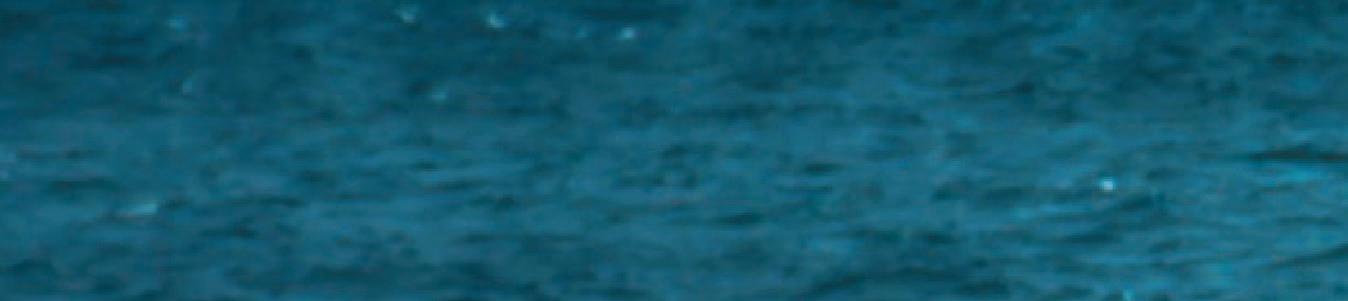
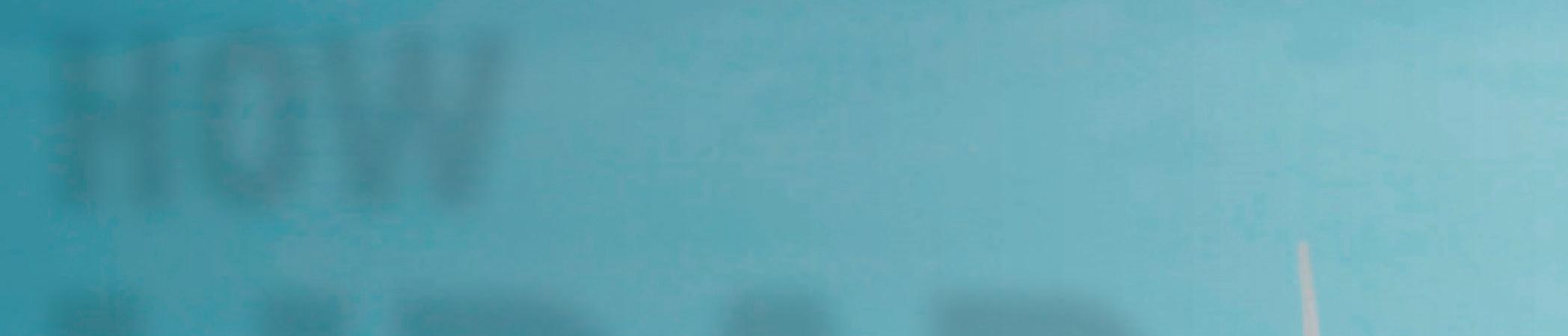
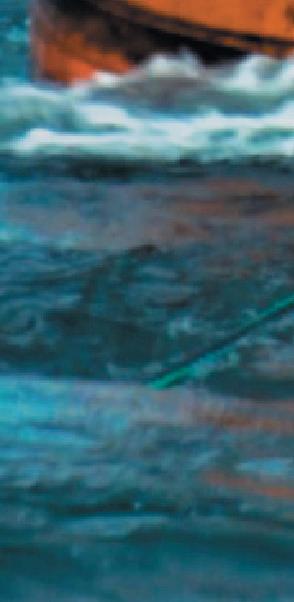
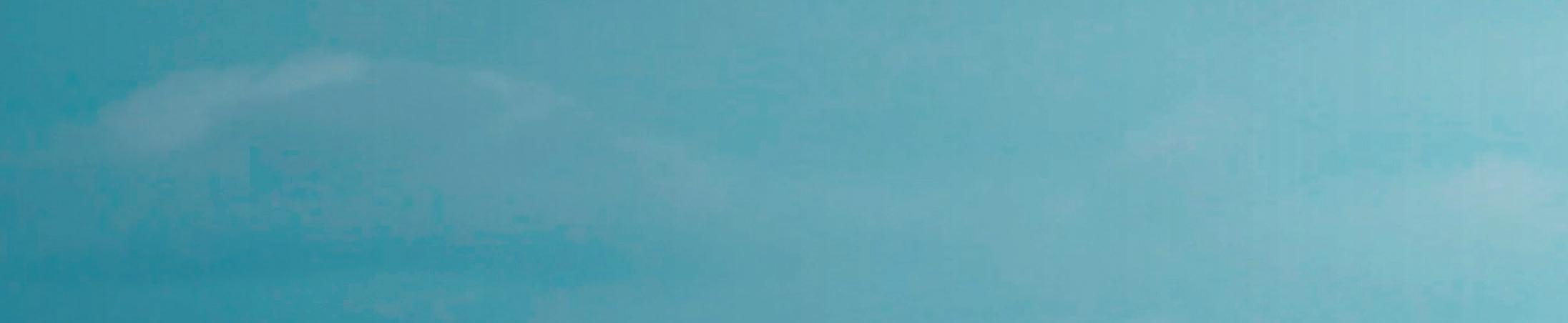
Before the first turbine begins spinning and producing energy, significant amounts of time and effort are invested in wind farm projects. Considered by many to be the most critical step of any wind farm project, WRA establishes the foundation for determining a project’s business case and acquiring financing.
organizations around the globe are increasingly implementing policies and programs aimed at increasing the number of wind turbines and the amount of power generated from wind energy. To meet this demand, there is continued innovations in the design, development, performance testing, operations and ongoing optimization of wind farms to generate electricity from wind energy. Consequently, wind energy is rapidly becoming one of the planet’s fastest-growing renewable energy segments — and an essential element of building a healthier, greener, more innovative future.
Each wind farm is unique and accordingly presents its distinct challenges. Wind flow patterns and wind speeds vary greatly worldwide and are impacted by bodies of water, vegetation and differences in terrain. Offshore wind farm development is challenging due to strict environmental standards and operating in harsh, salted environments far from maintenance resources, as well as significantly high costs surrounding the support structure, ongoing operations and maintenance (O&M), electrical infrastructure and ever-growing turbines.
As more countries expand their windgeneration capacities — both onshore and offshore — it is vital that wind energy decision-makers understand how to accurately define, measure and forecast the world’s wind resources so that projects can take advantage of the increasing size and capacity of wind turbines — especially in offshore environments. By recognizing the critical importance of wind resource assessment (WRA) and evaluating how several recent offshore projects leveraged recent wind energy industry innovations and evolving best practices, the entire sector can help propel renewable energy to new heights.
Why wind resource assessment?
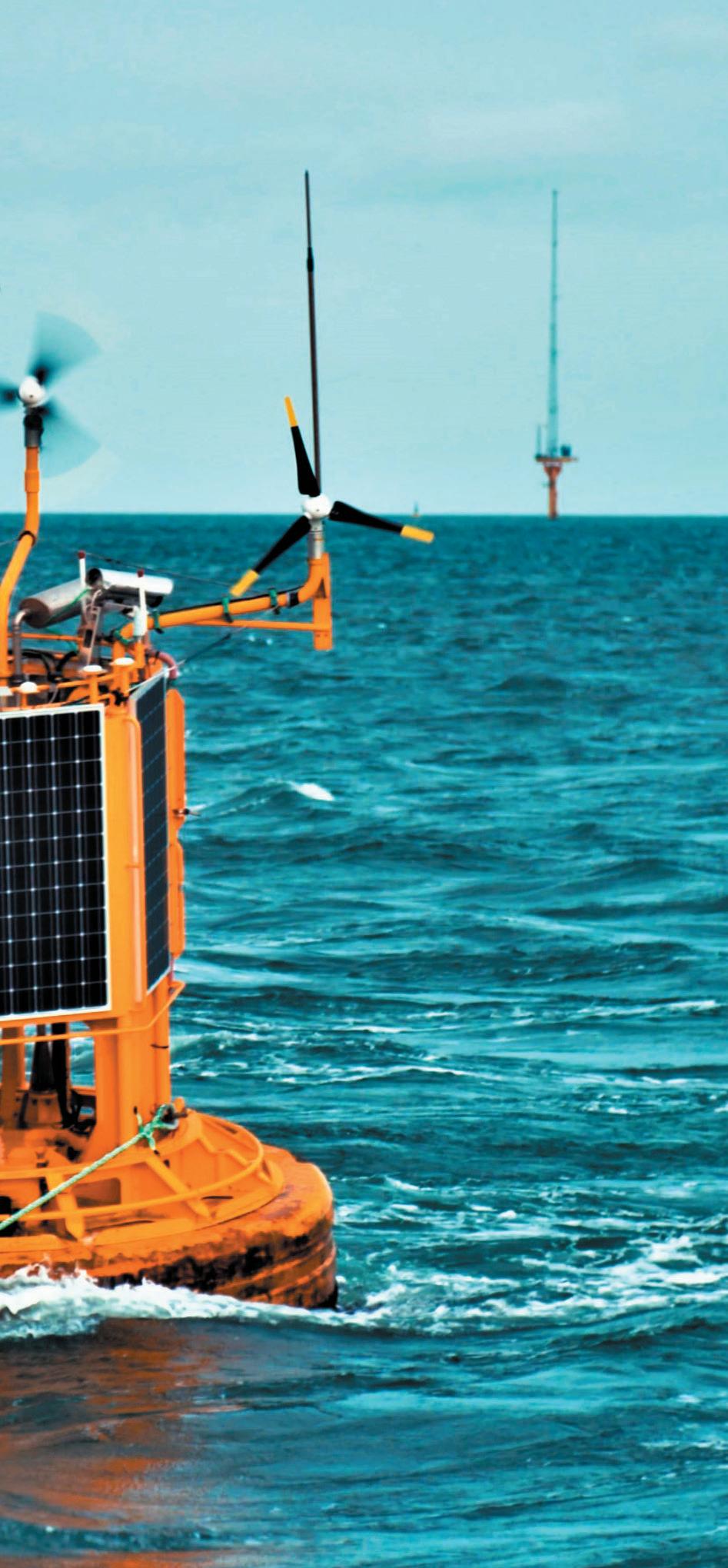
WINDPOWER ENGINEERING & DEVELOPMENT 9SEPTEMBER 2022
GOVERNMENT
Accurasea, EOLFI
Jacques Vapillon, Akrocean
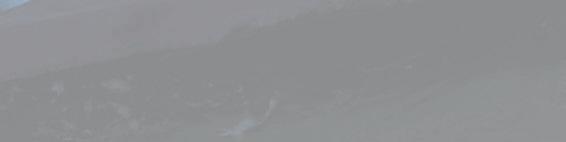

Leveraging lidar for offshore WRA
With advances in lidar technology, the assessment of an offshore wind farm site can be completed more swiftly and accurately, as the technology’s mobility, ease of deployment and offshore-ready measurement prowess provides a solution for almost any need in offshore development and operations.
Different lidar devices easily measure up to the full height of today’s turbines without mathematical extrapolation; move around the site for additional measurements (or to support another campaign); can be positioned to increase coverage, accuracy and efficiency; can be deployed for greenfield assessment
WITH ADVANCES IN LIDAR TECHNOLOGY, THE ASSESSMENT OF AN OFFSHORE WIND FARM SITE CAN BE COMPLETED MORE SWIFTLY SITEOFFSHOREACCURATELY.ANDWINDFARMCANBECOMPLETEDMORESWIFTLYANDACCURATELY.
As offshore wind farms leveraging larger turbines than ever continue to be built in deeper waters farther from the shore, the ability to quantify the wind resources at a given offshore site is invaluable in determining what kind of equipment is needed at that location as well as a project’s overall financial and practical viability. Today, meteorological (met) masts — the traditional standard of wind measurement — struggle to keep up with wind turbines’ constantly increasing hub heights in offshore environments. Also, most met masts fail to cover the entire operating region of an offshore wind farm, and the significant majority of today’s masts greatly rely on data extrapolation, which can introduce error and uncertainty into the measurement.Inadditionto high permitting and construction costs, obtaining siting permits for met masts can take months. Worse yet, met masts cannot be easily moved around an offshore site, and they are susceptible to mechanical failure, lightning strikes and high winds, which creates insurance risks for project developers. Finally, considering the incredibly high level of investment required, met masts can be prohibitively expensive — and potentially dangerous to install, maintain and repair — for offshore projects.
Constructing a sound financial model for investment requires decision-makers to accurately assess and characterize available wind resources. For bank engineers who judge a wind farm project’s viability, lidar has replaced met mast as a primary measurement device for offshore WRA are being used in many applications to ultimately supply clean, renewable power to businesses and homeowners at lower costs.
WINDPOWER ENGINEERING & DEVELOPMENT 11 LIDAR POWERING OFFSHORE WIND
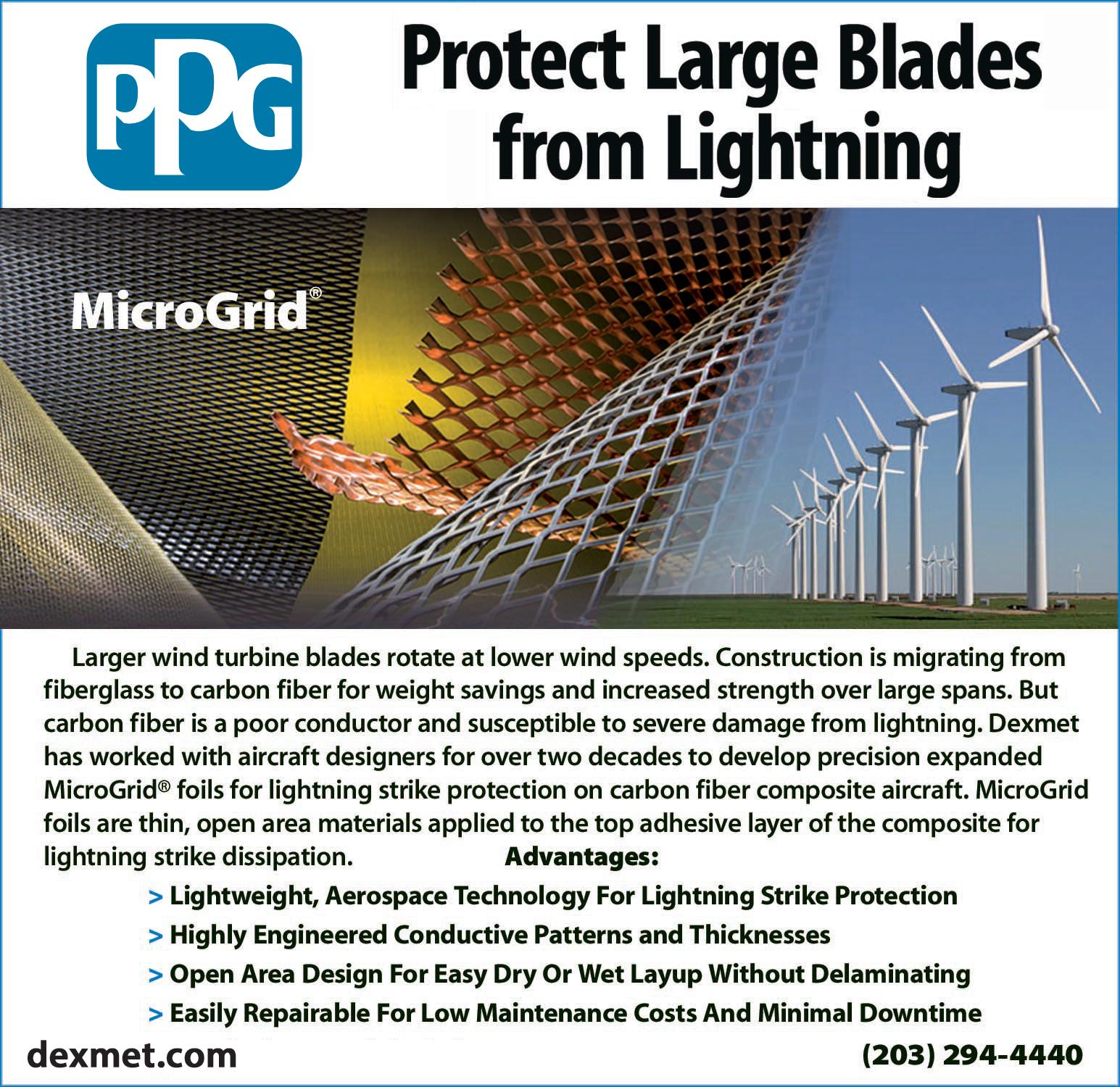
Today, offshore developers are increasingly turning to dual scanning lidar for a fuller, 3D understanding of the wind environment, especially for near-shore wind farm development. Consider the Green Power Investment’s project as an example.AGreen Power Investment (GPI) project required wind speed measurements covering the area where all future turbines will be located. With each scanning lidar placed in a strategic location, GPI observed an offshore area from two positions and created several “virtual met masts,” reducing uncertainties and increasing bankability.
WINDCUBE DUAL LIDAR IS A GAME-CHANGER: WE CAN GET THE WHOLE WIND PICTURE WITH SCANNING LIDAR.
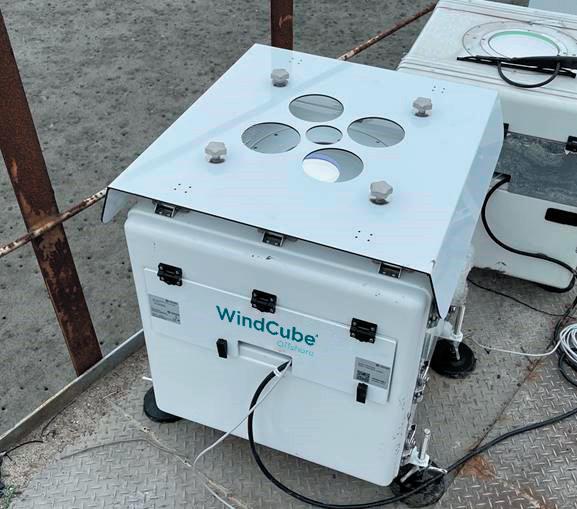
Dual scanning lidar
LIDAR POWERING OFFSHORE WIND WINDPOWER ENGINEERING & DEVELOPMENT12 SEPTEMBER 2022www.windpowerengineering.com
As organizations continue to develop and deploy offshore wind technologies that can capture the abundant, stronger and more consistent than land-based wind resources available off the coasts of countries around the globe, WRA becomes increasingly tricky at sites where there are no available fixed platforms.EnterFloating Lidar Systems (FLS). Rugged and versatile, lidars are often integrated onto a standalone floating structure, such as a buoy, to collect offshore wind data. With a robust, marinized casing that ensures wave movement does not create data errors, floating lidar instruments deliver reliable insights vital to construct an offshore wind farm.
offshore locations and several heights, this solution’s unique configuration provides the precise, reliable wind measurements that GPI needs to reduce measurement uncertainty, meet ClassNK requirements and ultimately create a feasible project and competitive bid for the upcoming wind farm development auction.
nearly anywhere; and new breakthroughs are even enabling instruments to achieve the lowest measurement uncertainty.
“WindCube Dual Lidar is a gamechanger: We can get the whole wind picture with scanning lidar. We can create site conditions for wind turbine design load using dual scanning lidar without an offshore met mast or floating lidar system,” said Atsushi Yoshimura, manager at GPI.By creating “virtual met masts” that collect accurate data at two to three
Floating lidar systems
GPI was able to set up the duallidar configuration faster and more cost-effectively than a met mast. The lidars’ beam crossing and high sampling frequency also enabled the collection of turbulence intensity measurement.
As lidar technology advances and scientific breakthroughs are achieved, new lidar innovations are seeing increased measurement ranges of up to 300 meters, which enable dozens of simultaneous measurement heights, and unmatched accuracy in meeting wind industry standards. The improved measurement range can cover the wind profile of even the largest wind turbines, enabling even more accurate WRAs and data-driven decision-making. The algorithmic combination of scalar and vector averaging called hybrid wind reconstruction reduces turbulence sensitivity and provides a cup-equivalent 10-minute wind speed measurement. Manufacturers are garnering industryleading classification and validation to help developers save time and money on third-party, on-site verification and ensure validation continuity.
With offerings and turnkey solutions that increase efficiency and uptime, as well as validation and certification
Lidar is limitless
With the French government eager to accelerate its offshore wind industry, it needed to quickly and accurately conduct preliminary site assessments of large offshore areas. Deploying FLS over a four-year collaboration in South Brittany, France, it began a campaign to help the French Ministry of Energy define the capacity of future wind farms and clarify needs for the public tenders that will go to developers. As a result of assessing these potential offshore sites with two buoy-integrated lidar units, all bidders will now have accurate data sets to provide quality plans.
LIDAR POWERING OFFSHORE WIND WINDPOWER ENGINEERING & DEVELOPMENT 13SEPTEMBER 2022
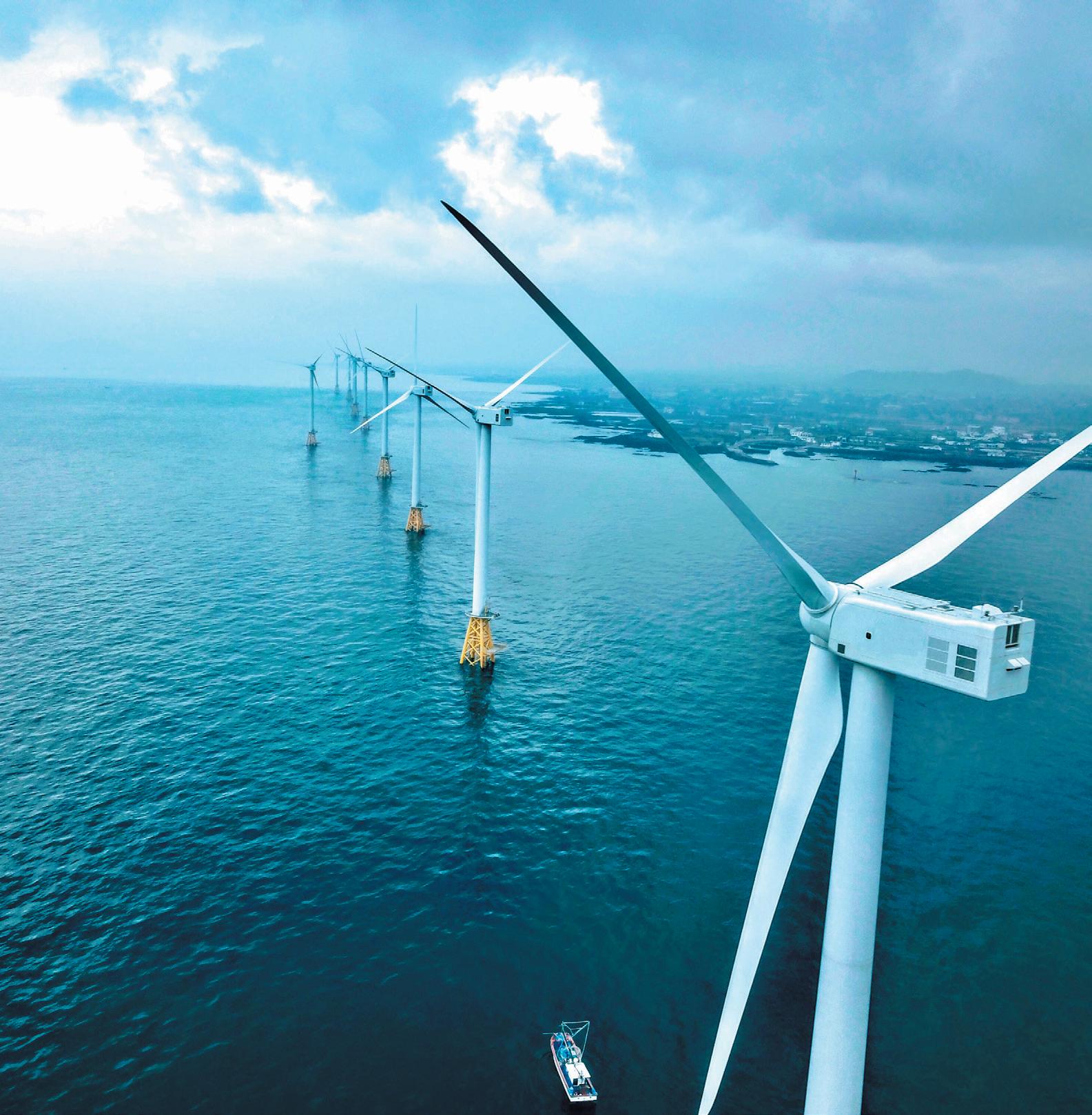
Lidar enhancements
While remote sensing has fought an uphill battle for acceptance in the wind industry, the wind industry is finally embracing lidar solutions for onshore and offshore applications in both the wind development and operational phases. As the cases assessing the evolving offshore wind frontier in this article illustrate, lidar innovations provide developers, operators and manufacturers with better, bankable
Adobe Stock
To increase data accuracy, operational continuity and bankability of wind energy campaigns both on land and offshore, lidar manufacturers are delivering lidar solutions with increased measurement capabilities, premium services and turnkey options.
data in a more agile and straightforward manner. Offshore wind resources must be properly assessed to ensure reliable and efficient construction of wind energy infrastructure — and lidar has made this process faster, easier and more costeffective than Empoweredever.with the necessary guidelines and standards that create global confidence, knowledge sharing and standardization of lidar as an essential and expected part of most standard wind energy processes, the wind energy industry can more easily meet the growing demand for green energy and a more sustainable future. WPE
services that save time and increase trust, lidar manufacturers are empowering customers to harness wind energy in new ways.
WINDPOWER ENGINEERING & DEVELOPMENT14 SEPTEMBER 2022www.windpowerengineering.com OVERINNOVATIONPROCESS THE PRIORITIZATION OF IS HAMPERING MANUFACTURING
BY JAMES MONTGOMERY • VP OF SOLUTIONS • ANDEA
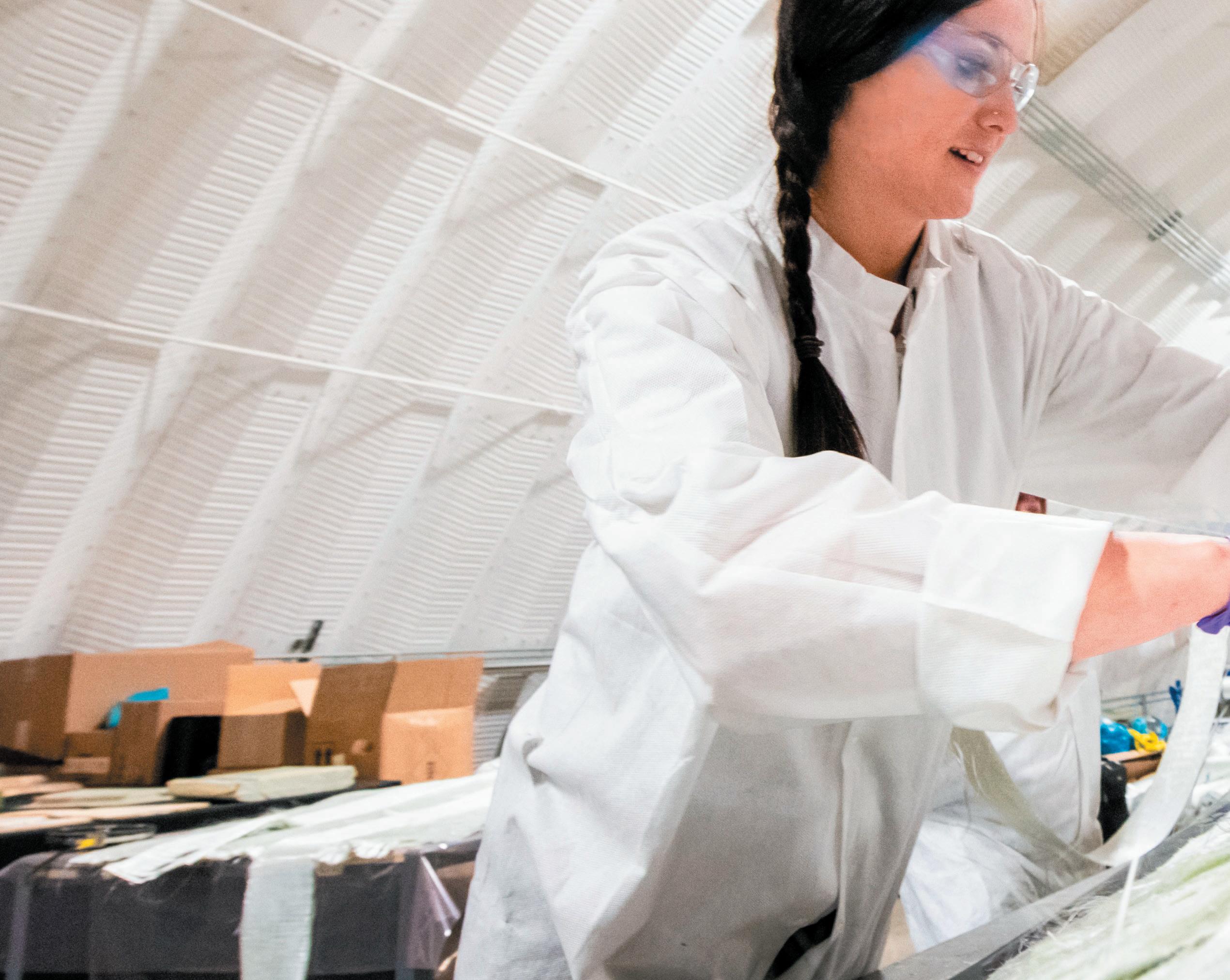
A failure to align product innovation and shopfloor operations also means that vital lessons learned during development and manufacturing are not being
A deep disconnect between R&D and manufacturing is jeopardizing efforts to increase speed to market and achieve economies of scale for complex new technologies while harming safety and sustainability standards. The hand-off from product design and development to production creates significant risks as engineers prep the shopfloor to ramp-up the rate of production.
are inaccessible on the shopfloor. The increasingly high cost of opening this high-tech engineering knowledge to non-specialists also means that shopfloor workers are often being left without all the necessary knowledge required to complete their job without significant engineering oversite. The cost of not converting engineering knowledge into practical, accessible workflows often creates an additional risk that this invaluable engineering expertise could be lost to future retirements or resignations of key personnel. Failure to do so typically means manufacturing processes cannot be easily reproduced or standardized on
NREL
a large scale, impeding companies from ramping up manufacturing at speed.
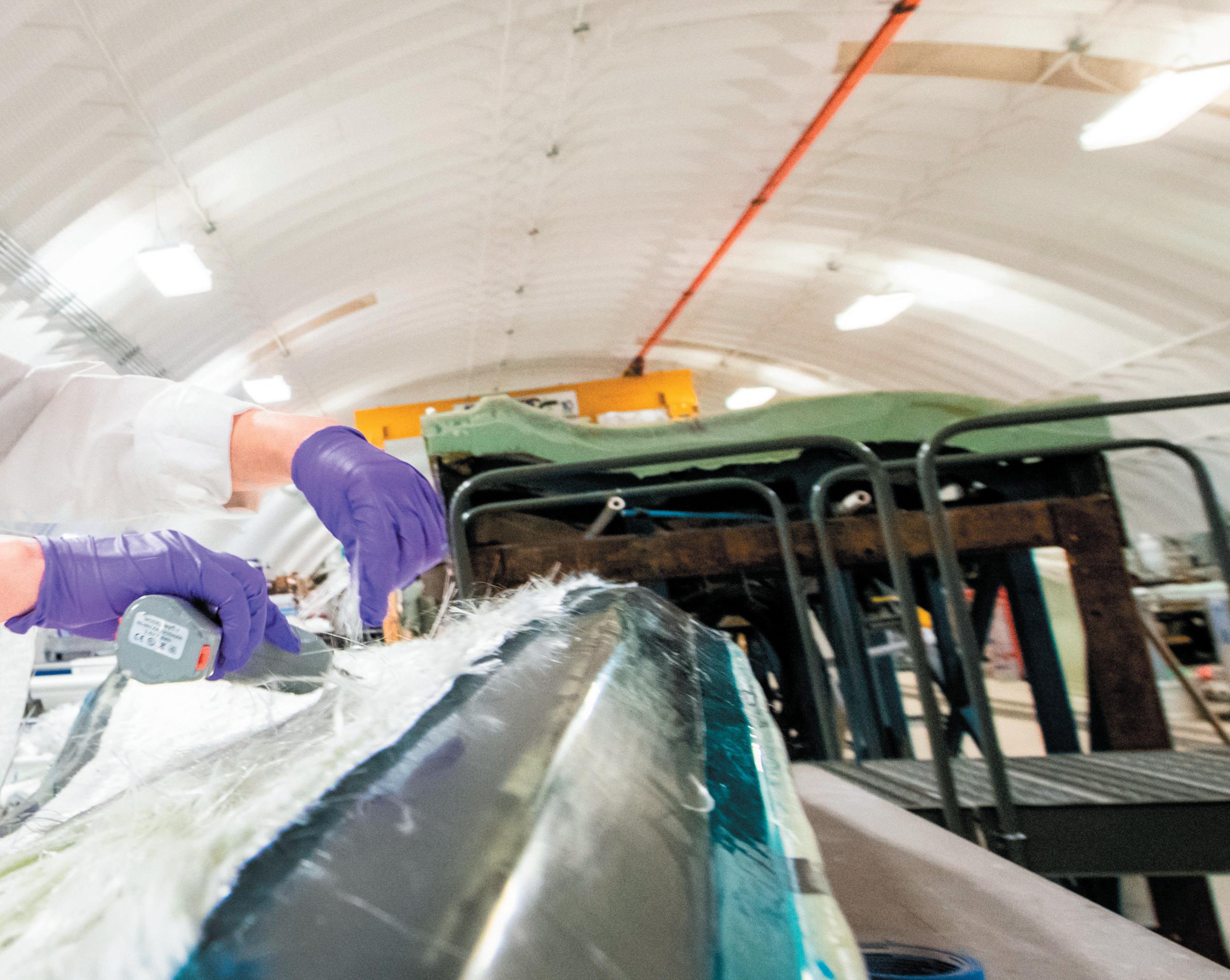
The failure to democratize engineering knowledge and bridge the gap between design and the first few articles being produced, to what is required for higher volume manufacturing means many production instructions
The failure to capture and communicate engineering processes and knowledge to non-specialists also prevents companies from streamlining and automating more of their manufacturing processes and adopting “Industry 4.0” innovations. Crucially, there is a growing risk of defects creeping in once more nonspecialists are brought in to accelerate the manufacturing process.
WINDPOWER ENGINEERING & DEVELOPMENT 15SEPTEMBER 2022
INNOVATION VS. IMPLEMENTATION WINDPOWER ENGINEERING & DEVELOPMENT16 aztecbolting.com 520 Dallas St. League City, TX 7757324/7 Service - Call Us 832-271-5120 Wield Absolute Power on the Job Site We also provide some of the most sophisticated bolting products from other leading brands in the world including: • Skidmore Bolt Testers • Norbar Electric Torque Wrenches • Norbar Electronic Calibration/Measurement Equipment We are always adding the newest Enerpac tools to our lineup of equipment available to rent, lease-to-own and buy. Shop our entire selection of torque wrenches, tensioners, hydraulic pumps and more. With Enerpac tools, you know you’re ready for the job ahead. | Enter the Enerpac Ecosystem The Highly TorqueHMT1500VersatileModularWrench • Lightweight and powerful • Job-site flexibility • Simple and durable design Get Any Job Done With The EPulse Pump • Autocycle and Multiport • Brushless DC motor • Speed variability control • Fully-enclosed, aluminum extruded shell


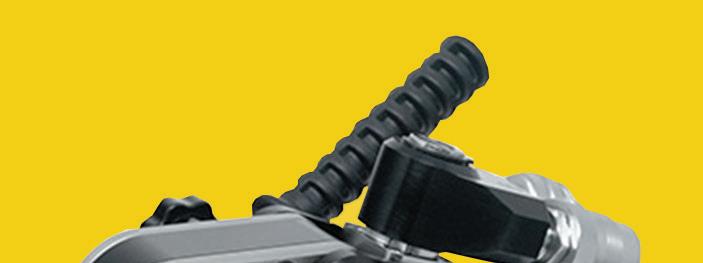
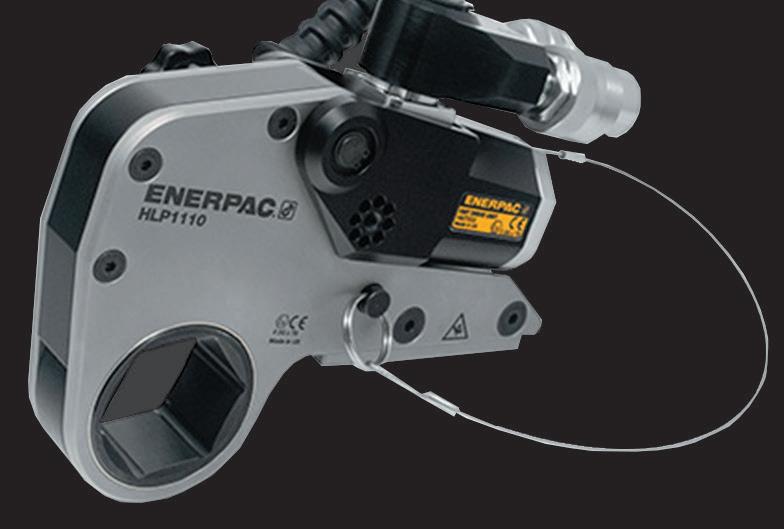
TRANSPARENCYINADEQUATE AND TRACEABILITY IS HAMPERING QUALITY CONTROL HAMPERINGCOMPLIANCEAND.QUALITY COMPLIANCEAND.


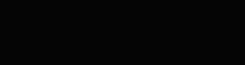
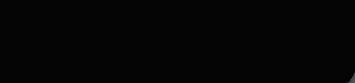
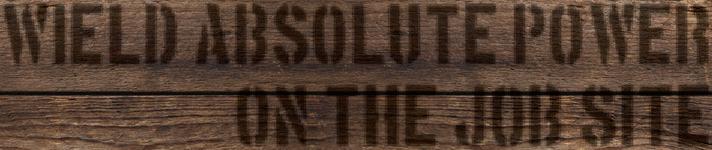
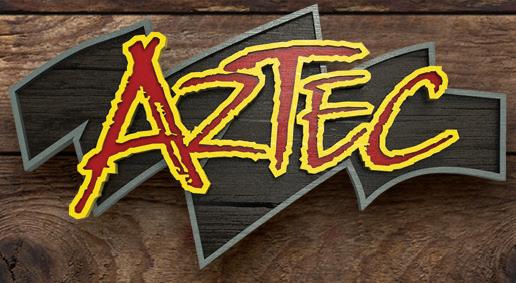
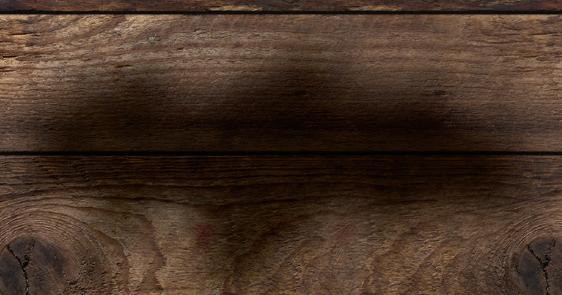

The disconnect between innovation and implementation Manufacturing processes are perceived as an administrative cost rather than a competitive advantage while R&D is seen as the true money-spinner. This means companies often fail to invest in the cost of converting new innovations into practical manufacturing plans so that production instructions are often inaccessible to those outside the engineering department, preventing manufacturers translating complex concepts into mass-manufactured technologies.Forexample, it is often prohibitively expensive to convert complex new designs into accessible, actionable manufacturing plans with clear steps expanded and explained, buyoffs added and data collection embedded at every stage. This impedes the necessary transparency and traceability needed
harnessed to improve future products. It is critical that anyone who touches the part or product has a feedback loop to the design and manufacturing engineers with any issues or ideas to make the part better. Furthermore, inadequate transparency and traceability is hampering quality control and compliance. Cumulatively, this is delaying the introduction of crucial new technologies from renewable energy to satellite communications systems.
in fi ve manufacturers prioritize advanced analytics for either short-term savings or long-term structural improvements to costs and 61% have failed to scale datadriven production processes beyond a single product.
to detect and correct errors at an early stage. Lack of visibility and traceability over manufacturing changes is causing excessive scrap rates and product recalls while creating safety and sustainability risks with new technologies. For example, the Space Shuttle Challenger Disaster was famously caused by engineering mistakes in designing two O-rings, while a recent tragedy involving a Red Arrow aircraft was caused by a single overtightened ejector seat bolt.
Scaling to high-speed, large-scale manufacturing

NREL
INNOVATION VS. IMPLEMENTATION WINDPOWER ENGINEERING & DEVELOPMENT 17SEPTEMBER 2022
to manufacture complex high-value technologies at speed and scale, this creates a dangerous disconnect between design and improvements.datamanufacturingfrominsightssilos.systemssolutionsMutuallyimplementation.incompatiblepointandproprietarymanufacturingfurtherreinforcethesedataAfailuretosharemanufacturingwidelyispreventingcompaniesreplicatingandautomatingpresentprocessesorharnessinganalyticstodrivefutureprocessAsaresult,lessthanone
production by hiring non-specialist factory workers, sometimes from other industries and see them struggle to understand the intricacies at play. This is not only due to the tasks given but because they had been created by engineers for engineers.
Accelerating speed to market for complex technologies will require companies to bridge the gap between innovation and implementation to create a mutually beneficial feedback loop from factory floor to design. Manufacturers need to embrace open, interoperable systems that enable data sharing across the manufacturing process from concept to completion. Everything from product design to process plans should be democratized and decentralized, creating collaborative processes continually
Even worse, many changes are not centrally recorded due to the cost or challenges in ensuring traceability across manufacturing areas and product lines, resulting in these being left in issue systems or ticketing systems such as JIRA. While the change or nonconformance is tracked, it often does not control or prevent defective or untested parts from fl owing through production, into the warehouse and shipping areas, and on to the real world. Any production errors or unanticipated changes can also cause a ripple effect across complex multi-tiered assembly processes, leading to costly delays or even dangerous defects going unnoticed.
There is signifi cant pressure to accelerate the speed to market which falls on the shoulders of overworked design and manufacturing engineers. This pressure, combined with the cost of continually making changes to the manufacturing processes, often means work instructions are frequently misaligned to the needs of production teams and can overlook real-world production requirements. A lack of communication during production means that engineers are missing vital shopfl oor feedback from unexpected challenges to part changes which could drive more effi cient production and smarter future designs.Asproduction increases, it is untenable to confi ne production knowledge to a small group of skilled engineers, and companies often have to bring in technicians of varying skill levels who may not have comparable engineering and product expertise. With the market being so hot in many industries and with massive pushes to develop workforces, ramp up of knowledge is often a luxury. We see companies trying to rapidly scale
Crucially, the accelerating pace of innovation and complexity of assembly makes it progressively harder for engineers to track and trace components
training@abaris.comwww.abaris.com+1.775.827.6568

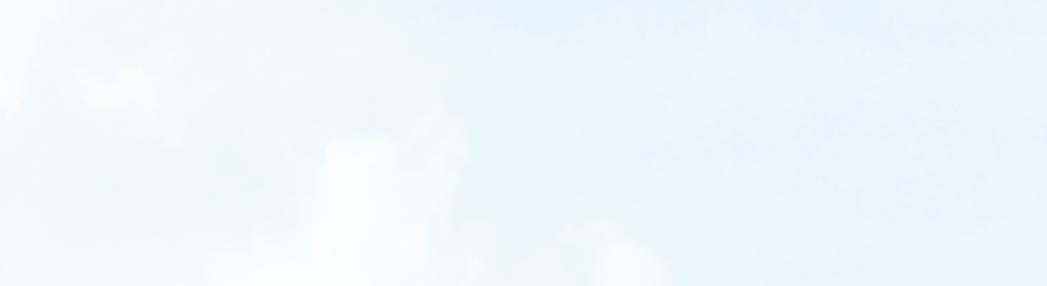
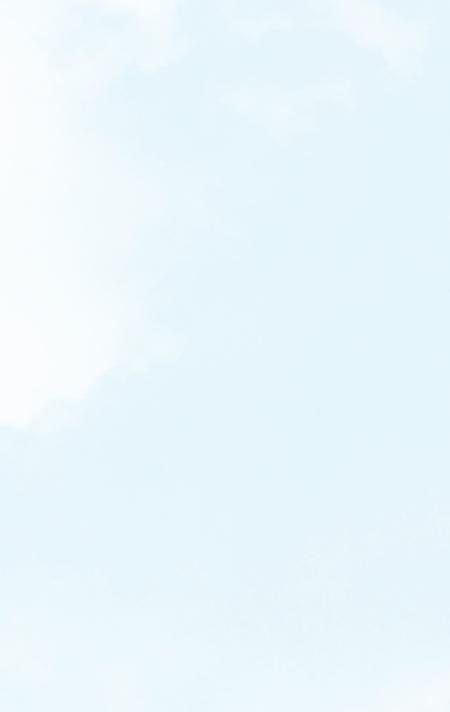
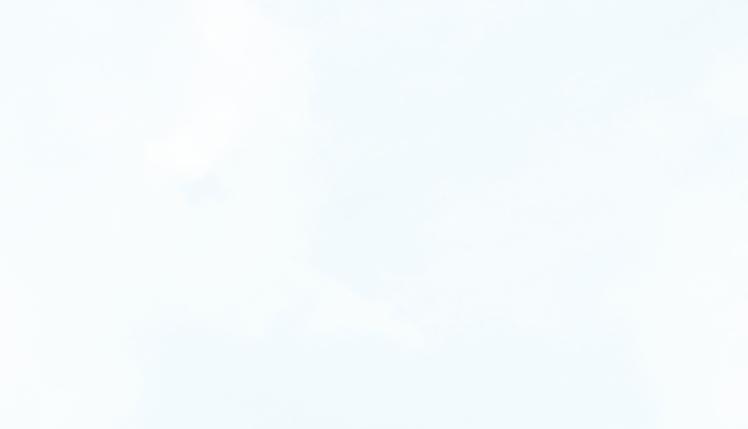
A follow-on to our Composite Windblade Repair course, this course is for those directly involved in providing high performance repairs to large area spars,damage,andtips.
INNOVATION VS. IMPLEMENTATION
ENROLL TODAY
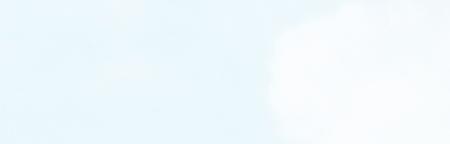
Pioneering manufacturers from high-tech industries, including solar and aerospace, are now adopting decentralized, data-driven planning solutions, that incorporate everything from real-time redlines to equipment alerts from the factory
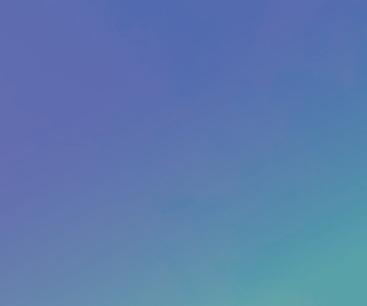
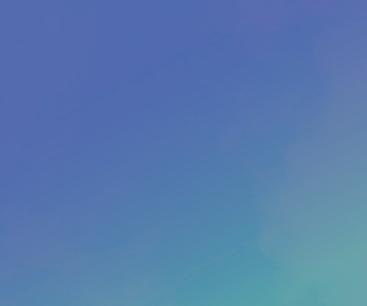
R-15: Advanced Windblade Repair
For those responsible for performing structural repairs to composite windblades, this course covers fundamentals necessary to understanding aerodynamic skin, core, and trailing edge repairs.

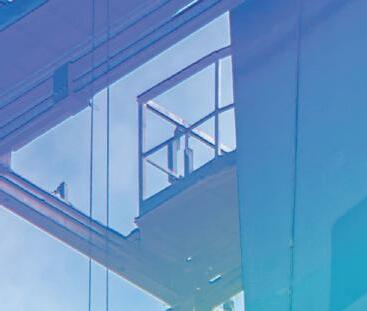
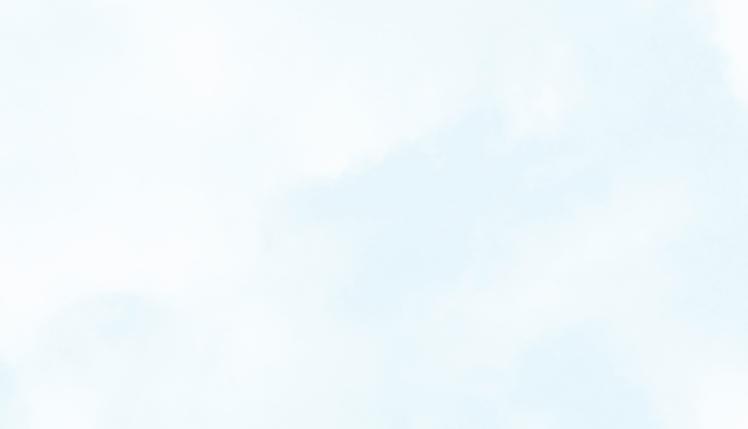
R-5: Composite Windblade Repair
Digitally integrating the factory floor with design would also create a digital feedback loop capturing and cross-fertilizing insights across projects to optimize future processes. Integrating processes into a single common planning solution to help centrally synchronize and optimize all manufacturing processes.
adjusted to reflect operational realities. Process plans should be made accessible and configurable so that shopfloor teams can remotely adjust work instructions in real-time to make changes or correct errors.
Crucially, these companies are moving away from a narrow focus on R&D over the process and instead engaging shopfloor workers in everything from design reviews to approvals. The key to rapidly scaling from R&D to mass manufacturing is bridging the gap between engineering and operations, moving from linear to adaptable processes, and shifting from top-down to twoway information flows. WPE
trace their cause, reducing safety or sustainability risks without excessive scrap rates. Engineers of various types can dig into all facets of the process to analyze risk and areas of opportunity.
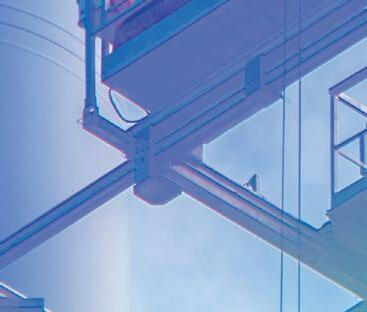
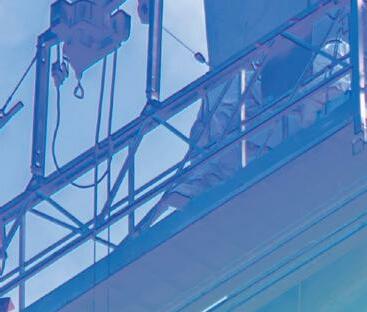

floor — but there is an urgent need for other emerging energy industries, such as wind, to establish better manufacturing processes now. This creates end-to-end visibility over changes and enables processes to be rapidly reconfigured to real-time manufacturing requirements.
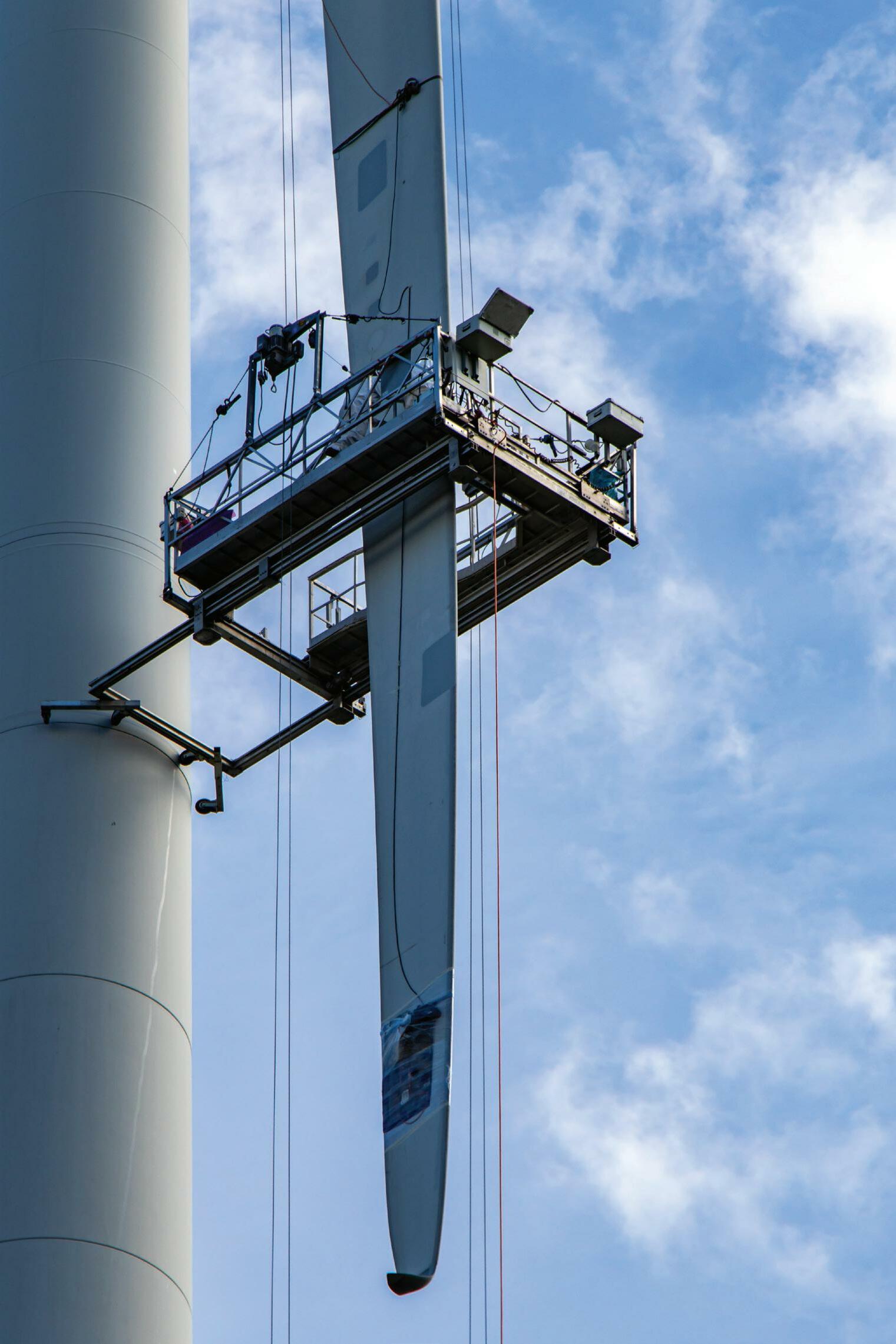
Real-time inline collaboration and communication between engineering and operations creates agile manufacturing and engineering capable of adapting processes to ramp up production of complex new technologies. With centralized engineering, and a system optimized for change and execution allows for significantly easier reporting, analysis and machine learning. Live data on excessive downtime or unresolved defects could also help adjust maintenance procedures to quickly contain and correct defects and
Aerospace Methods Applied to Windblade Repairs

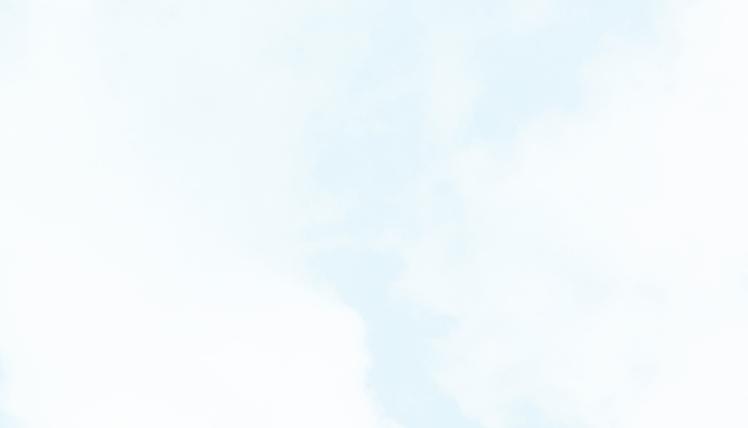
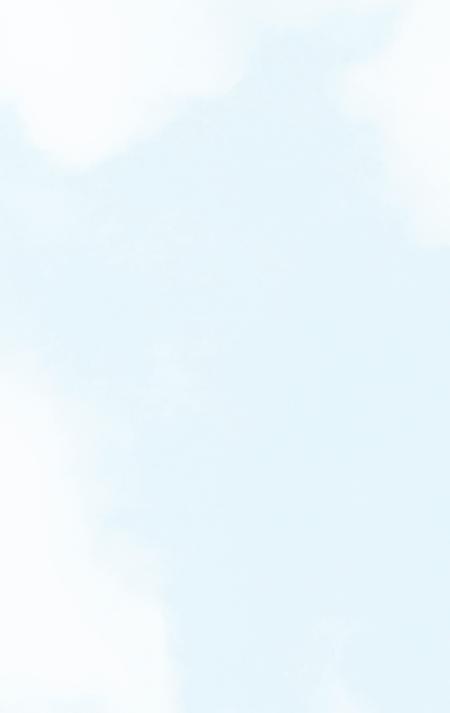
High HigherExpectations,LevelofSkill
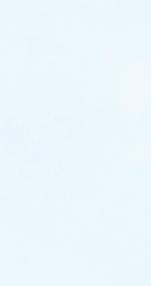
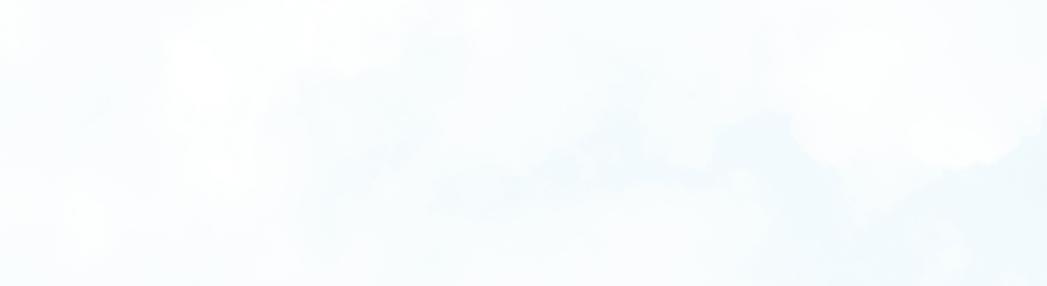
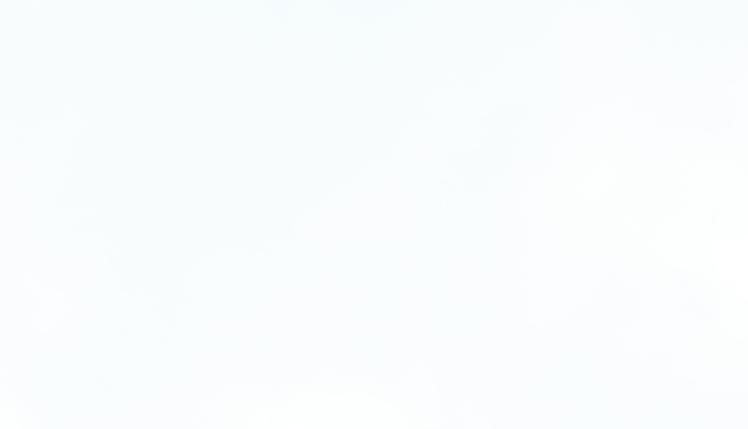
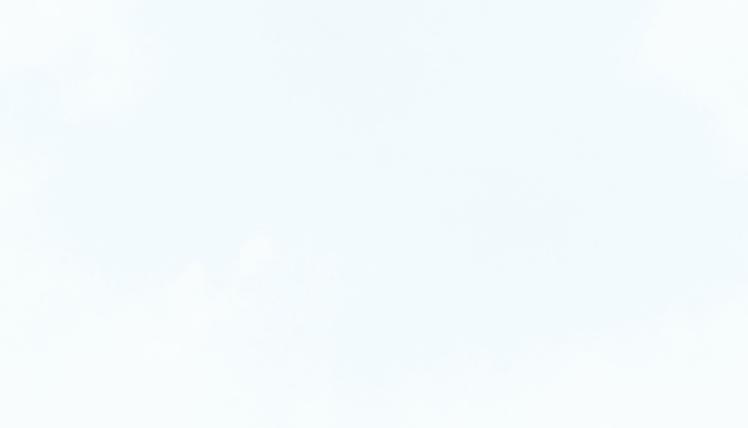
and practices, which is where Denmarkbased APQP4Wind comes in. The nonprofit organization was founded by worldleading wind turbine manufacturers and suppliers to help ensure that performance improvements keep pace with the downward trend in the levelized cost of energy
All this activity is having an impact: the offshore wind industry is on the cusp of a major transformation, fueled by increased demand for clean energy, technological advances and improved efficiencies.
are headline topics – soaring gas and electricity prices and growing concerns about climate change have guaranteed that. Part of the answer is an increased focus on wind power; as a result, it is significantly growing in importance as part of the UK and the world’s overall energyThemix.UK government has committed to a major expansion of offshore capacity by 2030, raising the target from 40 GW to 50 GW, with 5 GW from floating offshore wind sources. Good progress is already being made. In July this year, the
Advanced(LOCE).product quality planning (APQP) is a well known concept within the automotive industry and has been the backbone for improving quality performance for manufacturers and suppliers for decades. In the context of APQP4Wind, APQP has been adapted to deliver a standardized framework of
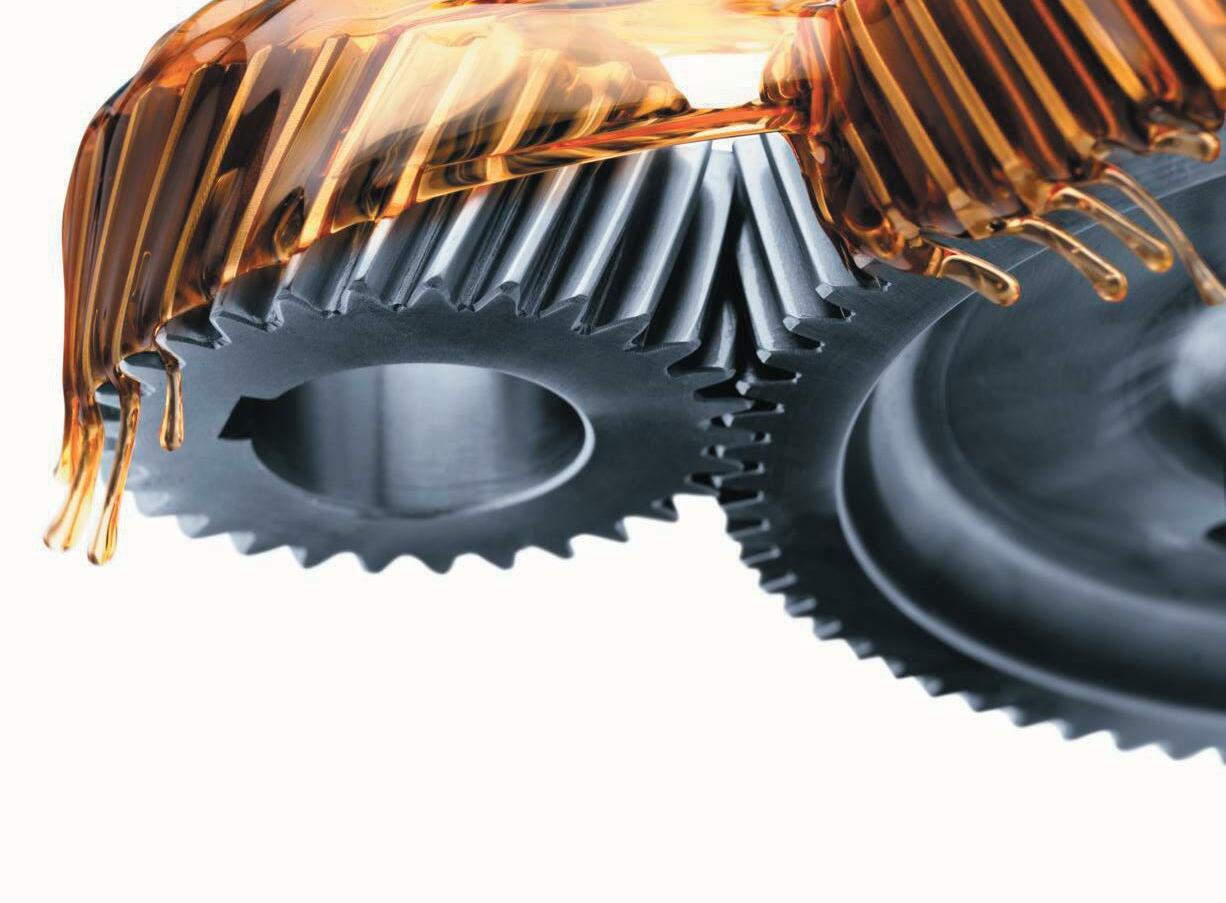
government approved 8 GW of offshore wind capacity – a major milestone for renewable energy and a significant step toward the UK meeting its net zero and energy security commitments.
WINDPOWER ENGINEERING & DEVELOPMENT 19SEPTEMBER 2022
Given the scale and importance of the task, it is essential for the wind industry to unite around an agreed set of standards
One good turn deserves another – setting the standard for wind energy maintenance
Keeping pace with industry trends
Energy security sustainabilityand
By Conor Wilkinson • EMEA Commercial Brand Manager • ExxonMobil Fuels & Lubricants
That’s why the Mobil brand joined APQP4Wind; we support its championing of common quality standards across the industry and embrace its framework in our ongoing product and service development. Our close collaboration with the world’s leading OEMs helps us understand equipment trends and lubricant requirements, consult on lubrication system designs and troubleshoot field lubrication challenges, expertise that we are sharing with APQP4Wind.
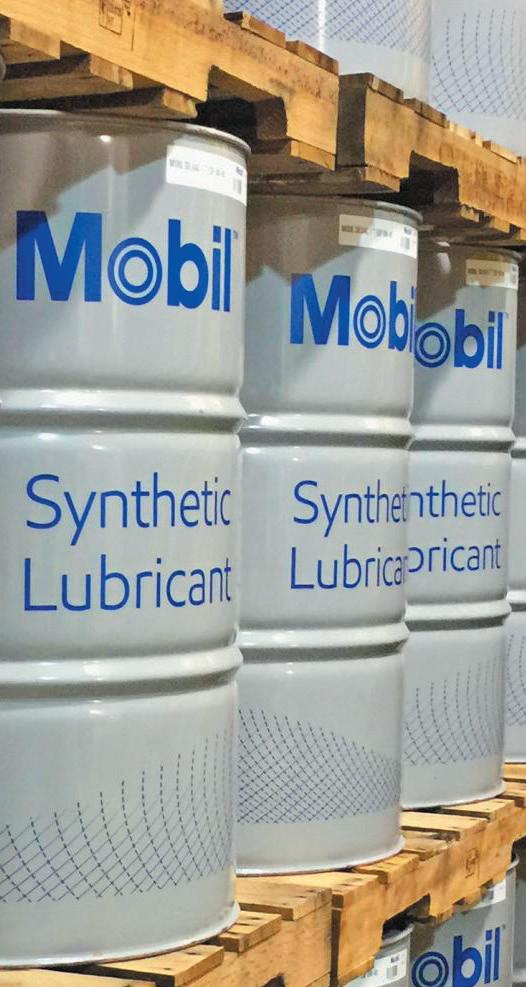
Optimizing turbine performance
procedures and techniques that fit the specific conditions of the wind industry. As a result, APQP4Wind has become an important seal of quality in the wind energy sector.
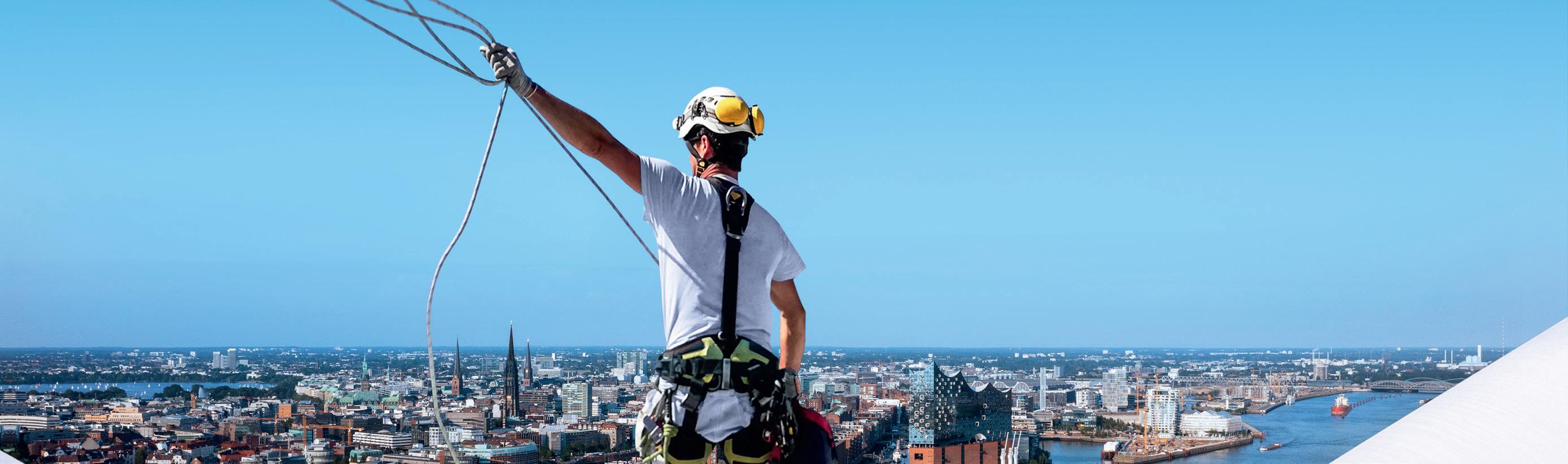
Unlike other industries, wind turbine operators are well aware of the critical role played by lubricants in machine performance. To sustain maximum power output, it is critical to reduce unscheduled and costly downtime for maintenance and repairs. And to do this with ever more extreme temperature, load and water contamination conditions that are common in offshore installations.
WINDPOWER ENGINEERING & DEVELOPMENT20
Mitigating bearing failures
THE INDUSTRYWIND IS SET FOR GROWTH.
For example, white etching cracking (WEC) is a common cause of bearing failure in the gearboxes of wind turbines. The condition, which gets its name from the appearance of the white fissures in the microstructure of steel, can result in critical parts failure. Given that the cost of repairing a wind turbine gearbox is expensive, compounded with the
Be sure to take part in the world’s biggest and most important business platform for the onshore and offshore wind industry!
To date, no definitive trigger has been established, although WEC is most likely the result of a complex interaction between mechanical, electrical, operational and chemical factors. This tribochemical reaction — the chemical changes that occur to a lubricant and a lubricated surface — is not well understood, so the Mobil team and a major bearing manufacturer set out to compare a range of lubricant formulations to a reference oil that has been reported to generate WEC in bearings.
A new spin on wind turbine performance
Checking a lubricant’s formulation and ensuring it is the most effective could help enhance the overall reliability and protect individual components. Operators
The wind industry is set for growth. To maximize the opportunities this will bring, operators need to observe optimum maintenance standards to help safeguard uptime. Best practice standards, in combination with advanced lubricant solutions, can help turbine operators enhance operations and deliver the renewable energy we all need. WPE
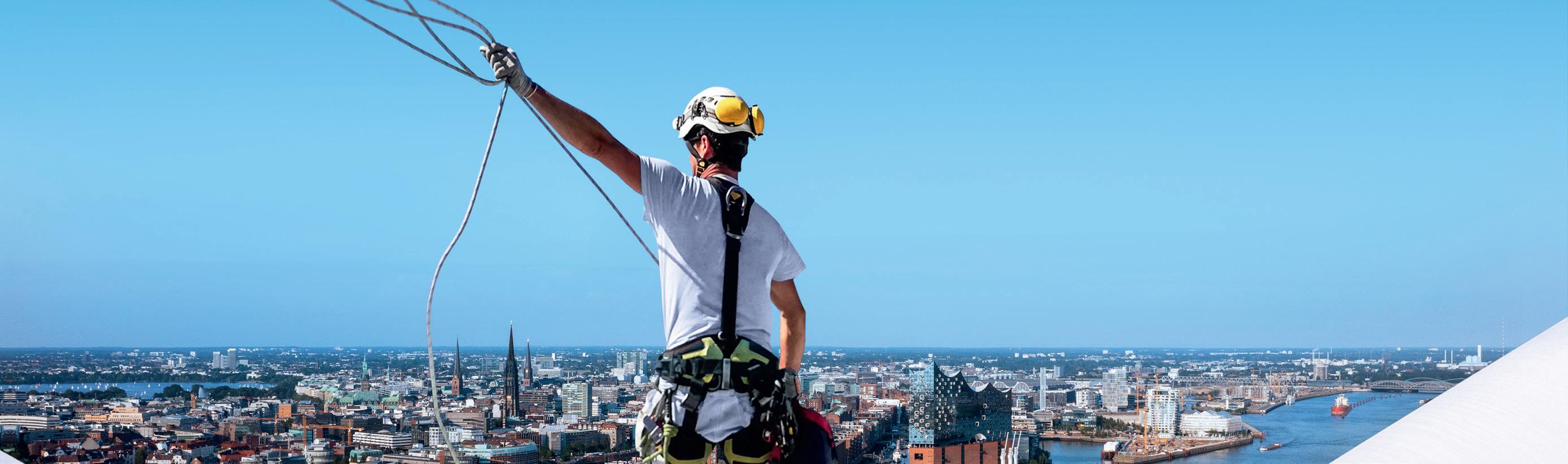
awarded a Conformity Statement by DNV GL, verifying that it does not contribute to the formation of WEC. It is also supplied with a 10-year warranty.
The findings were then used to help formulate Mobil SHC Gear 320 WT, a synthetic gearbox oil that has been
associated loss of productivity, it is little wonder why multiple investigations have been conducted to determine the cause of WEC.
Held in parallel with HamburgWindEnergy Exploring new horizons: It’s time to put climate first! 27 30 September 2022 Organised by: In co-operation with: European Partner: Partners:Global Partner: windenergyhamburg.com
should also ask for gearbox flush and fill guidance, as well as start-up and cleanliness advice from their lubricant supplier. Used in combination with dedicated wind turbine oils and greases, these can help wind farm operators achieve superior equipment protection and long service intervals, generating safety, environmental and operating cost benefits.
The wind industry also requires longlasting greases that protect against wear, rust and corrosion, even in extreme conditions. Formulations using a metallocene polyalphaolefin (mPAO) base stock have demonstrated superior lowtemperature performance compared with greases made with mineral and cPAO base stocks in lab tests.
& DEVELOPMENT www.windpowerengineering.com
ENERGYOUR GRID
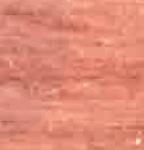
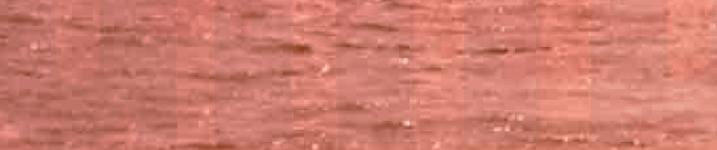
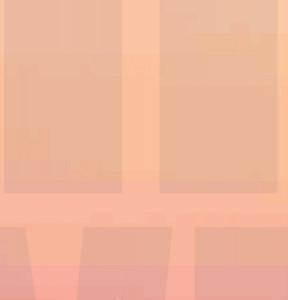
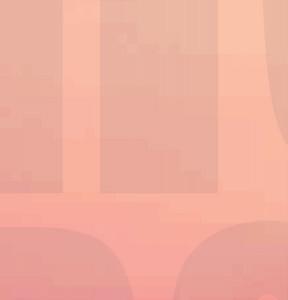

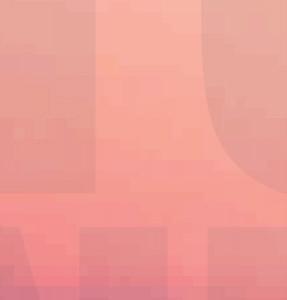

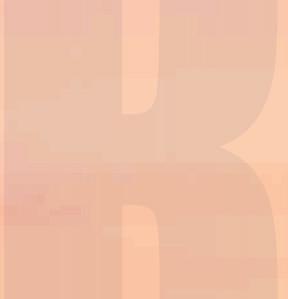
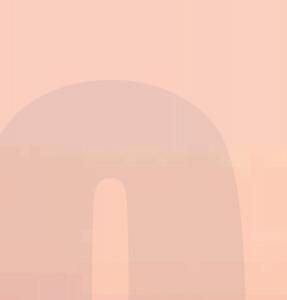
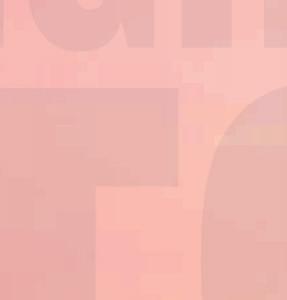
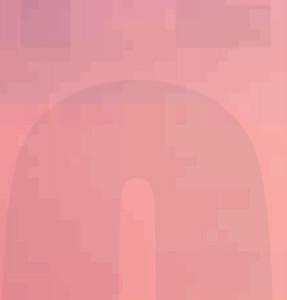
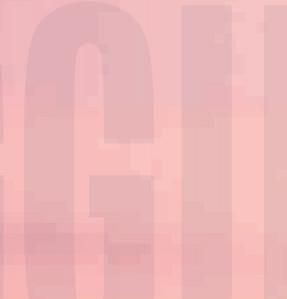

BY RALPH KURTH SENIOR PRINCIPAL, JOHN
OFFSHORE PLUGGING WIND POWER INTO
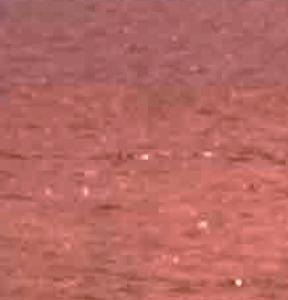
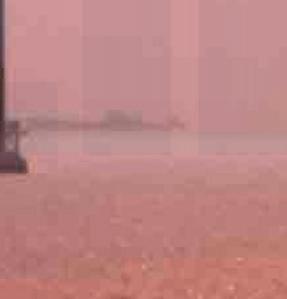
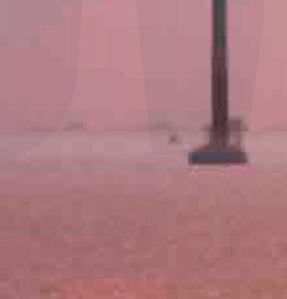
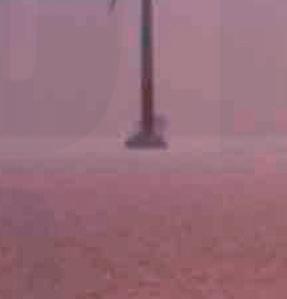
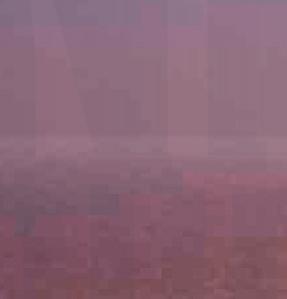
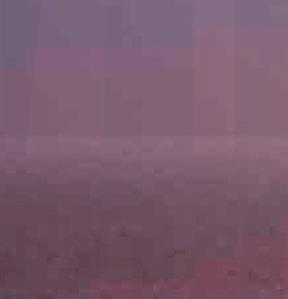
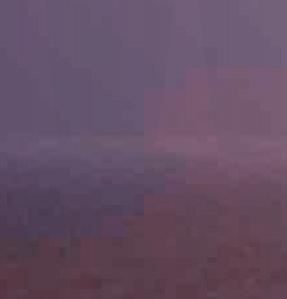

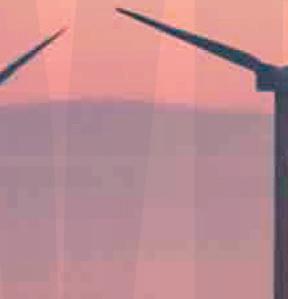
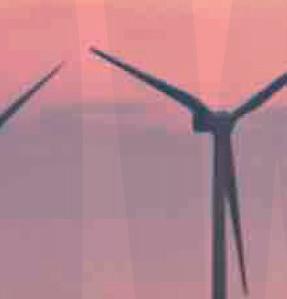

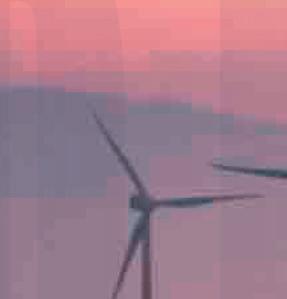
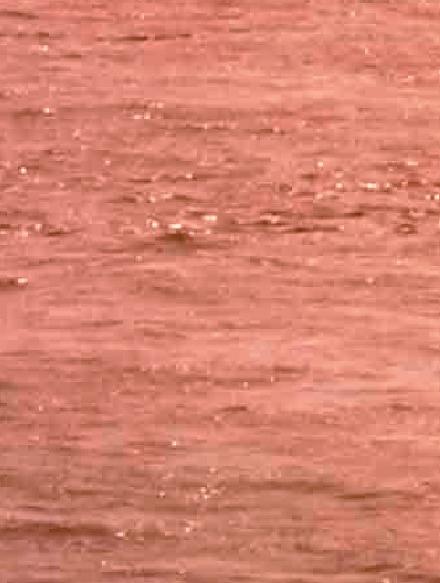

CROWTHER • SENIOR PRINCIPAL, ENVIRONMENTAL SERVICES •STANTEC 22 SEPTEMBER 2022
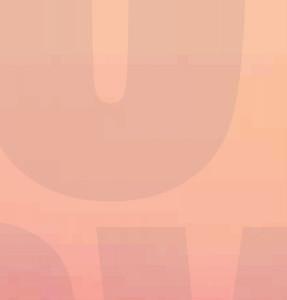
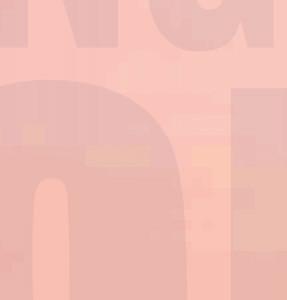
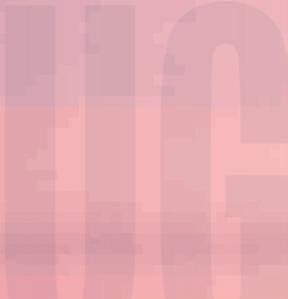
•
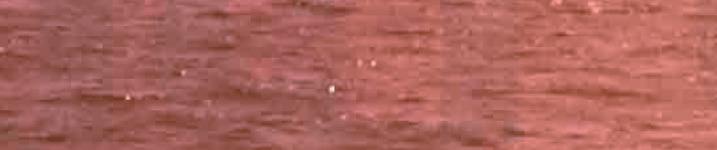
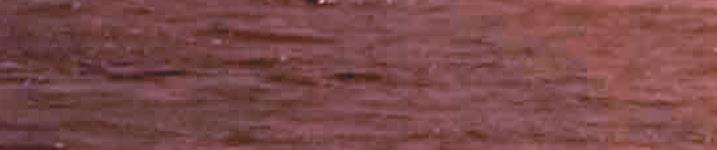
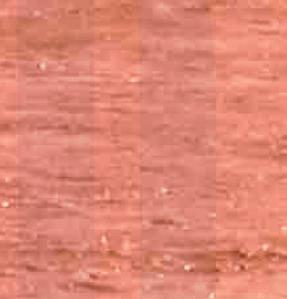


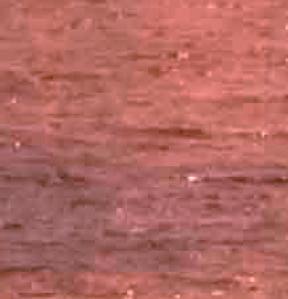
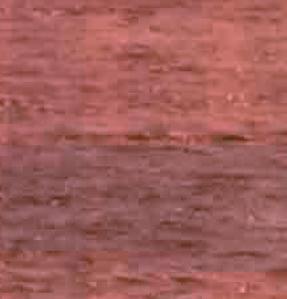

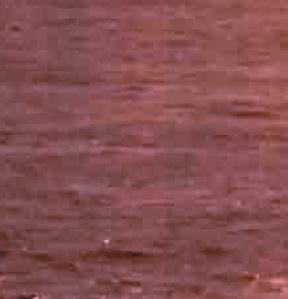
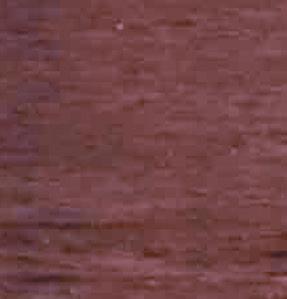

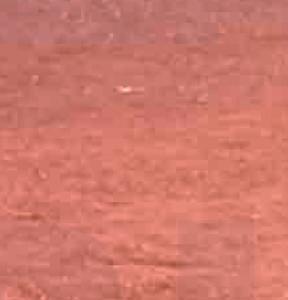

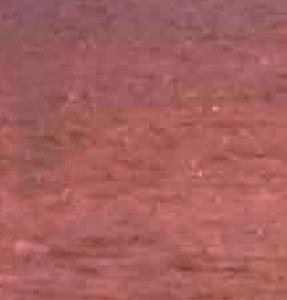
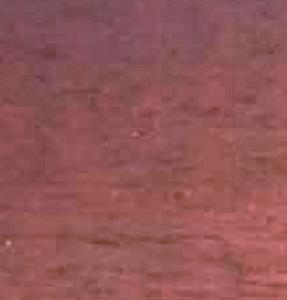
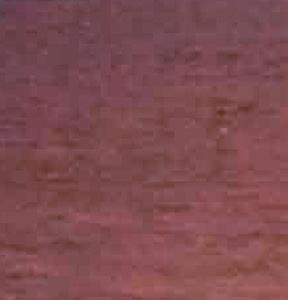
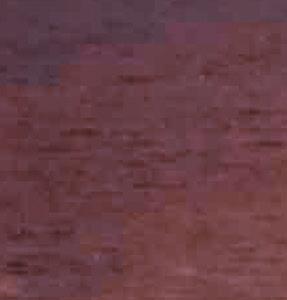

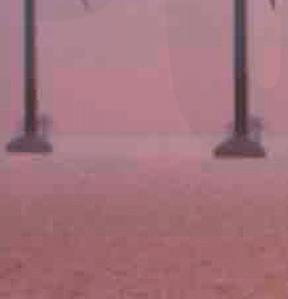
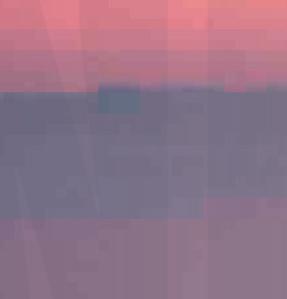
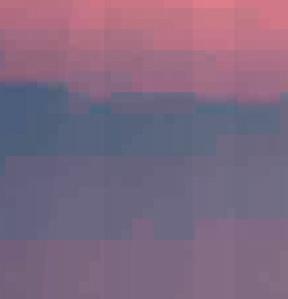
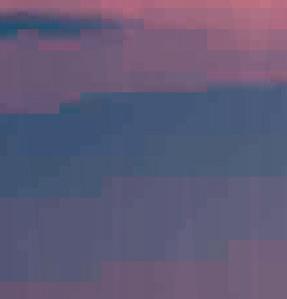

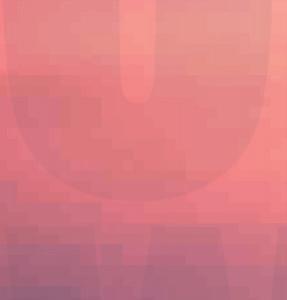
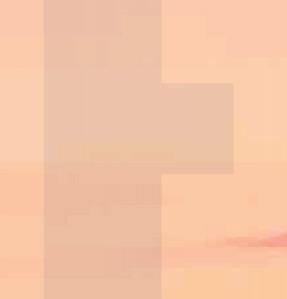
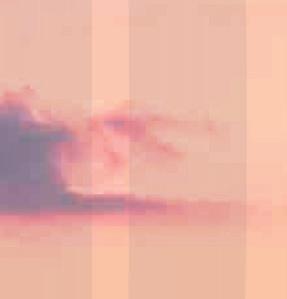
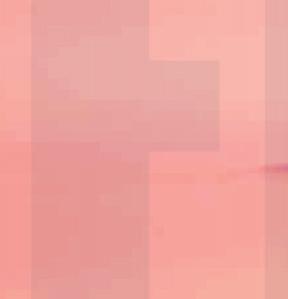
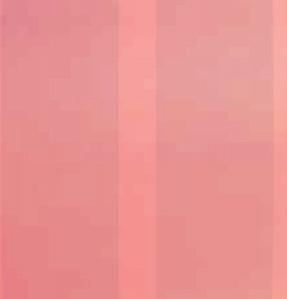

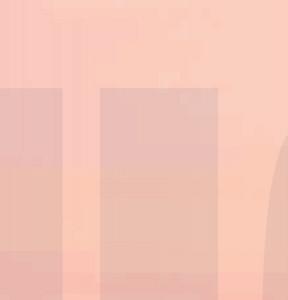
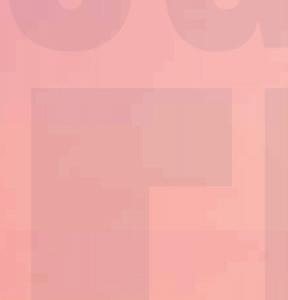
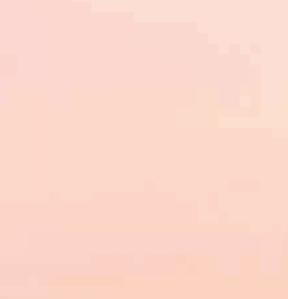
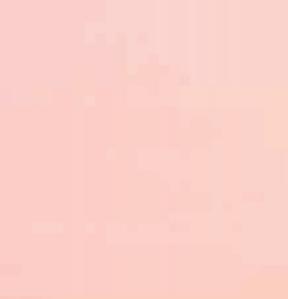

ENERGY; AND
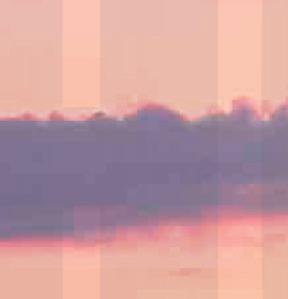

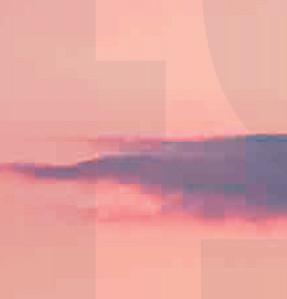
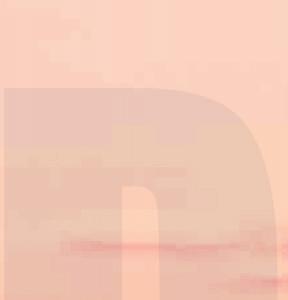
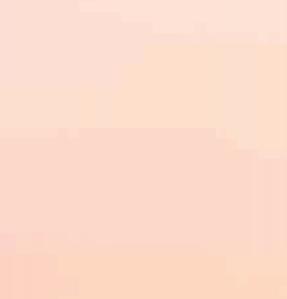
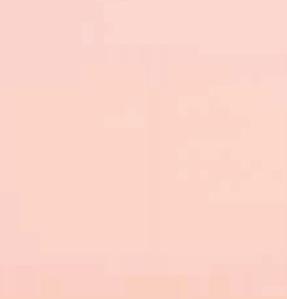
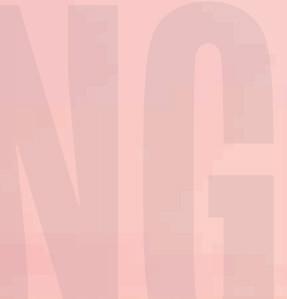
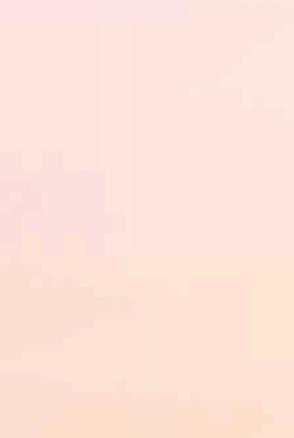
Siting and connecting offshore wind farms
Offshore wind from the ground up
WITH President Joe Biden setting a 30-GW offshore wind goal by 2030 for the United States, the industry is ready to take off. This massive development is a very ambitious goal that will require detailed engineering and planning. One thing that shouldn’t be overlooked is the cabling needed to get this wind energy to shore and into communities.
Offshore wind turbines require thousands of kilograms of precious materials, including copper, nickel, manganese, chromium and zinc. Beyond the turbines, offshore wind farms require high-voltage cables to connect to the grid. These cables will require even more precious materials that need to be mined.
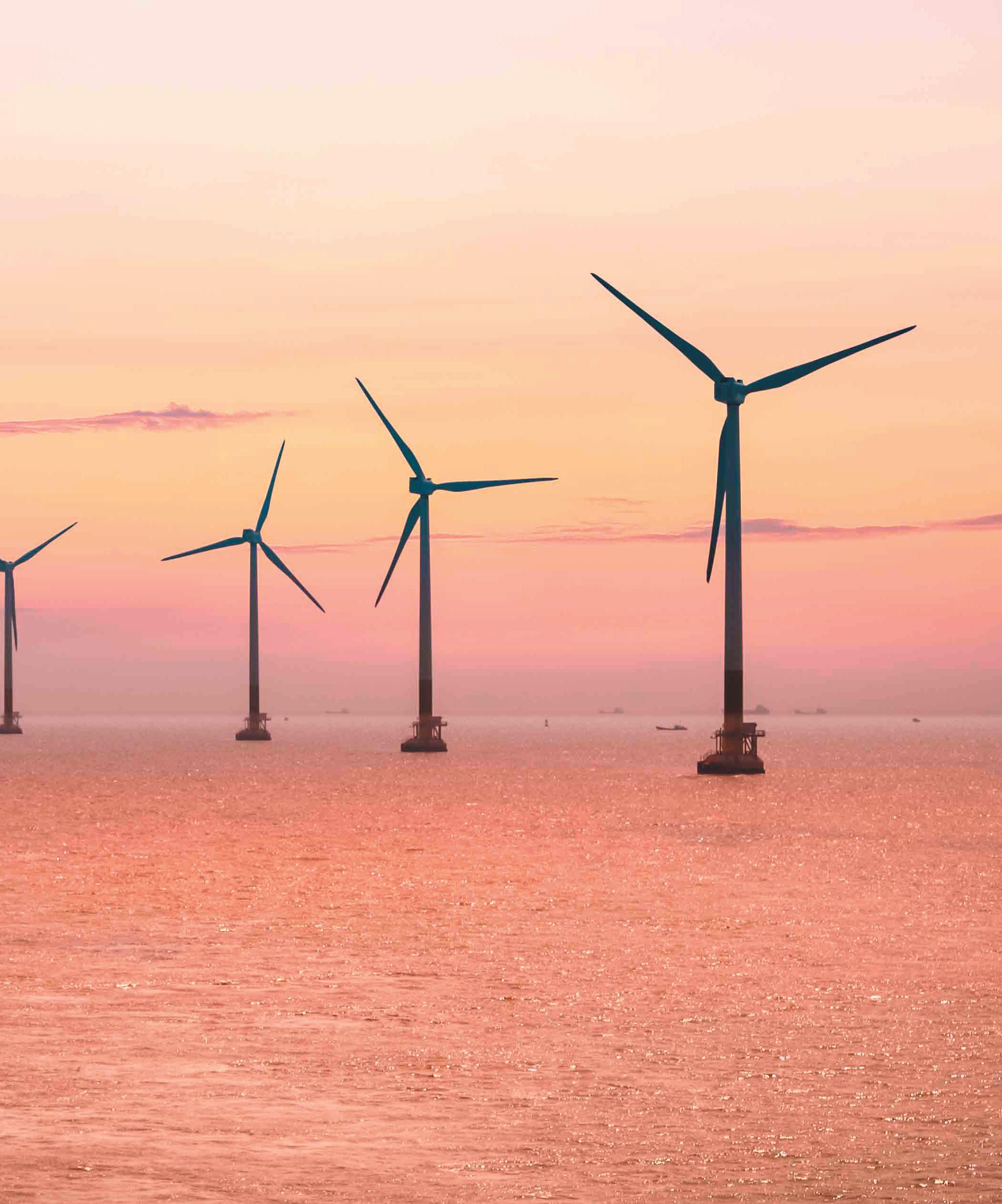
WINDPOWER ENGINEERING & DEVELOPMENT 23SEPTEMBER 2022
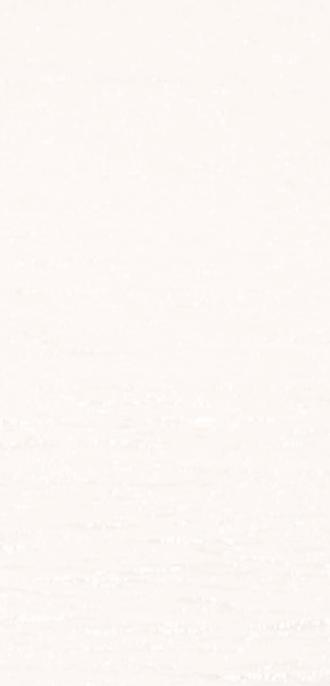
wind technology. And it all starts with the mining industry.
Offshore wind farms currently being proposed in the United States are mostly located approximately 15 to 30 miles from shore. This distance will increase as the industry grows and more turbines are needed further offshore. The size of these offshore
Before designing and executing offshore wind projects, first comes the procurement of offshore
so too will the demand for cables. That means procuring cables will take longer than usual. It’s critical to engage cable manufacturers as early as possible in the project’s life cycle.
Currently, there is a huge global demand for these cables as well as limited production capacity — and as the offshore wind industry grows,
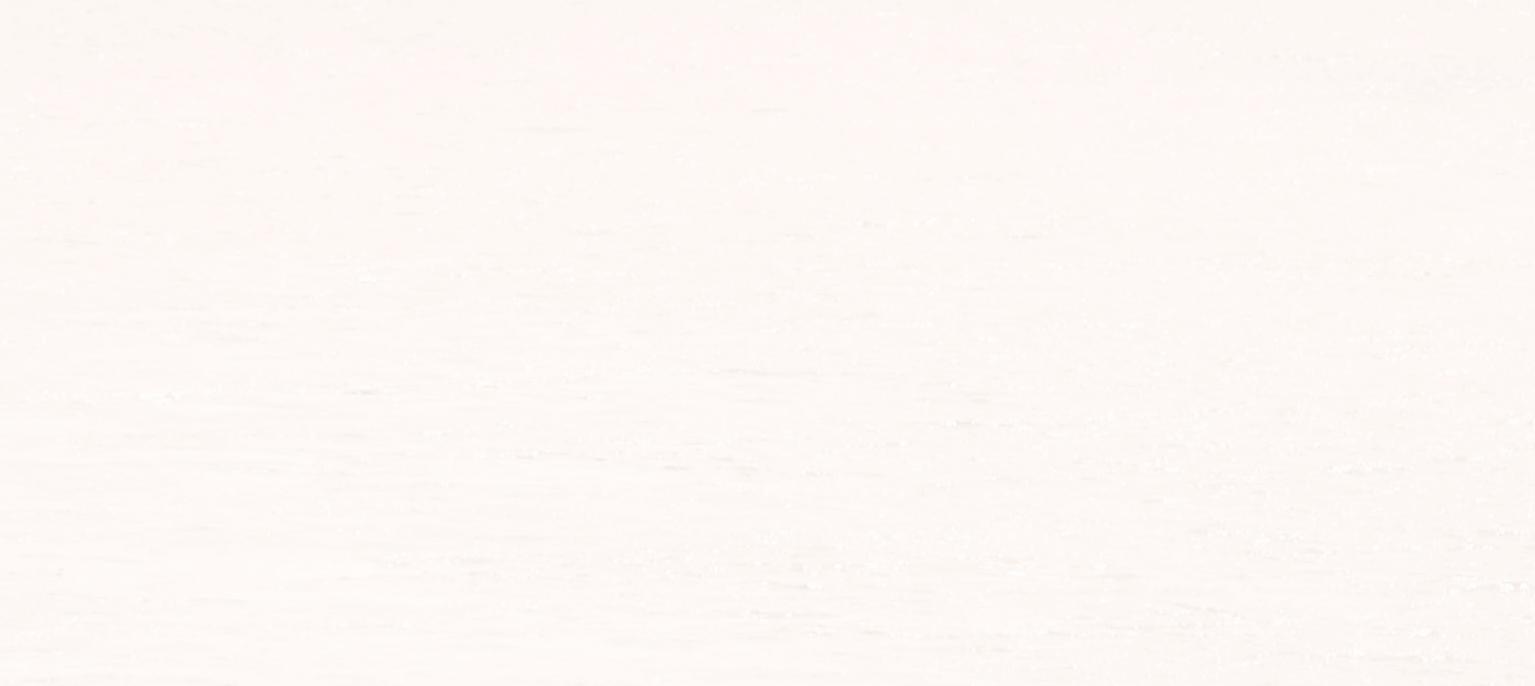
Another thing to consider is finding an effective way to protect the cables. According to reports from insurers, approximately three-quarters of all offshore wind insurance claims are related to cables. And 88% of those cable-insurance claims are related
the utility that owns the substation where the connection is being made.
underwater canyons and high shipping traffic areas. We also must consider the design of the onshore electrical transmission system. It may not be ready to accept offshore wind power at shore locations that are already congested.
PLUGGING IN OFFSHORE WIND
The points of interconnection in the electrical system need to be determined by conducting power system studies. Having knowledge of the electrical system is important, as transmission capacity may be available in the future where there are non-renewable generating plants planned for retirement. In many areas, the electrical system close to the coastline is not sufficient to carry large amounts of power from the offshore wind farms further into the grid. These instances require additional onshore transmission upgrades. This calls for coordination with the local planning authority and
wind farms will grow too — both in terms of the number of turbines and the generating capacity of each turbine. Further developments in turbine generating capacity will drive the industry to higher capacity farms, especially in locations farther from shore. Both floating and fixed offshore wind farms are turning to high-voltage direct-current (HVDC) transmission lines as projects move further away from the shore.
Routing offshore wind cables
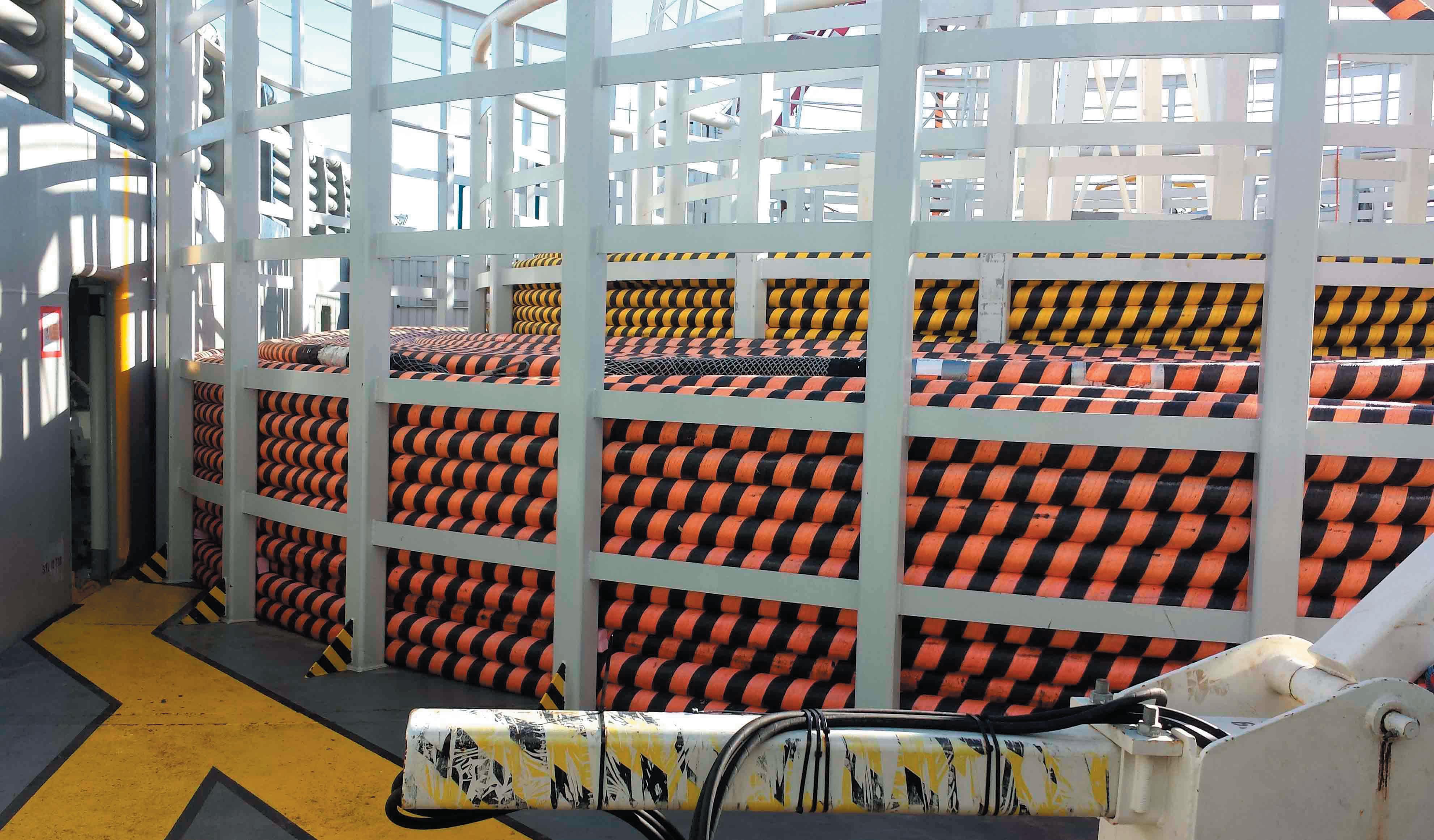
Landfall locations for the cables need to be selected carefully. It’s important to consider environmental constraints, coastal protection requirements and construction requirements. Generally, horizontal directional drilling is used to install the cable from a location a few hundred meters off the coast. This allows contractors to bypass — and not disturb — the shoreline.
Protecting offshore wind cables
It’s essential to find the right route for transmission cables. It would be optimal to route the cables from the offshore wind farms directly to the shoreline and immediately connect into the electrical grid at the closest substation. But this is not always possible due to constraints in the water, such as marine-protected areas,
Installing cables can create a temporary disturbance of the seabed and may cross through sensitive environments. Benthic resources are documented, and the impacts must be minimized through the permitting process for construction. The same is true for other methods such as dredging in high relief areas or protecting surface laid cables.
The submarine cable route may also need to cross over other linear infrastructure assets such as communications cables, other power cables or pipelines. In these instances, it is important to engage with the asset owners as early as possible to develop cable crossing requirements and agreements.
Once the cables reach shore, there is a need for more infrastructure and more cables to transmit the power, either underground or overhead, to the designated substation. Both transmission cable options can have an impact on the environment and must be addressed. Public outreach is important. The electrical substations and equipment needed to tie into the points of interconnection will require more land. Ideally, the point of interconnection is as close as possible to the submarine cable landing point.
Offshore wind power into our energy grid
Mechanically protecting submarine cables can assist with reducing damage from anchors, fishing gear, dredging and more. This requires detailed geophysical and geotechnical surveying of the cable route, along with a cable burial risk analysis.
to the export cables, which transport the power to shore. Damaged cables can be very costly to repair — it’s not only the cost of the cables, but the cost of the outage.
While it is critical to protect the cables, it’s also important to minimize impacts to the environment. The primary environmental concerns with offshore wind transmission are the impact to the seafloor, sensitive coastal environments and other marine life. There is also concern with potential conflict with other ocean users.
interface comes into play. This helps avoid sensitive shoreline resources and habitats by drilling at depths below them.
Cables are an important part of offshore wind, and having an upfront knowledge about the challenges developers may face will assist in successfully delivering bountiful offshore wind energy into our communities. WPE
REQUEST YOUR FREE Catalog! Quality &StampingsWashers SERVING A WORLD OF INDUSTRIES SINCE 1919 bokers.com (888) -WASHERS
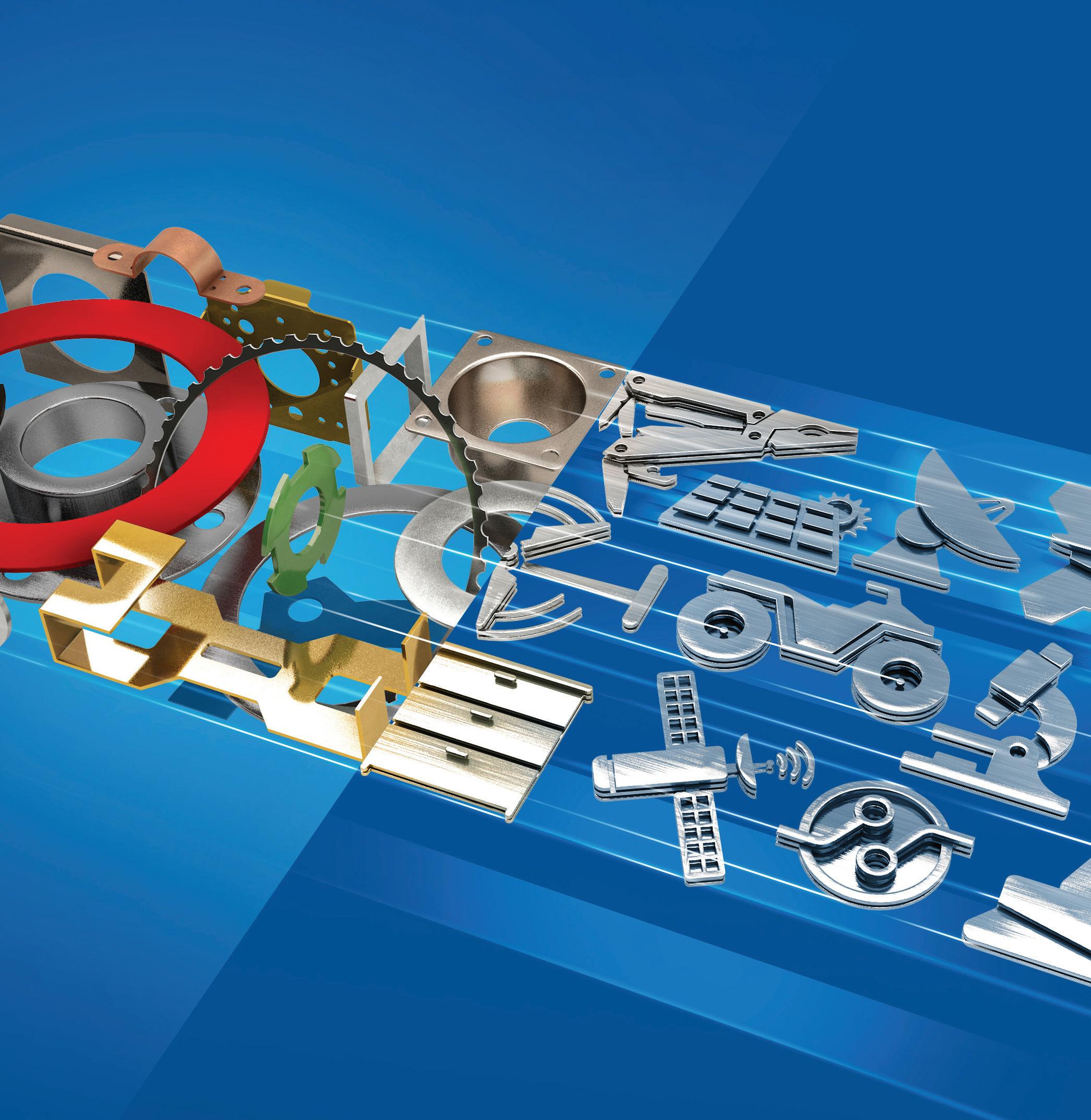
Offshore wind projects also must consider avoiding sensitive habitats wherever possible. This is where horizontal directional drilling at the ocean/land
Cable installation must also account for other ocean uses such as fishing interests, sand borrow areas, artificial reefs and navigation channels. Burial must be at sufficient depth in or around these areas to avoid direct contact and potential impacts.
A lot of work goes into protecting transmission cables. Having a repair preparedness strategy in place can help to minimize the outage time if damage occurs. Those strategies ensure that all documentation, permits and framework contracts are in place for all aspects associated with cable system repair.
WINDPOWER ENGINEERING & DEVELOPMENT 25 PLUGGING IN OFFSHORE WIND
Mitigating impacts to the surrounding environment
OFFSHORE wind is going from strength to strength.
BY GUILLAUME LECHATON • SALES DIRECTOR FOR WIND AND NEW ENERGIES • AKSELOS
HOW SIMULATIONENGINEERINGSOFTWARE CAN
Offshore wind has a critical role to play in the transition to a clean energy economy. To hit the International Energy Agency (IEA) target of net-zero global emissions by 2050, 80 GW of new capacity must be built annually from now until 2050. Therefore, while impressive, current growth rates are insufficient, and we need to add capacity at an unprecedented speed and scale to hit net zero.
2021 was a record year for the industry, with almost 21 GW of capacity added globally, up from 6.1 GW in 2020. Total offshore wind capacity is now at 57 GW and is expected to reach 630 GW by 2050.For the fourth year in a row, China led the world for offshore wind installations in 2022, adding almost 17 GW. During the same period, Europe’s capacity grew by 3.1 GW, and the continent pledged to increase its capacity to 150 GW by 2050 as part of the REPowerEU Action Plan. The
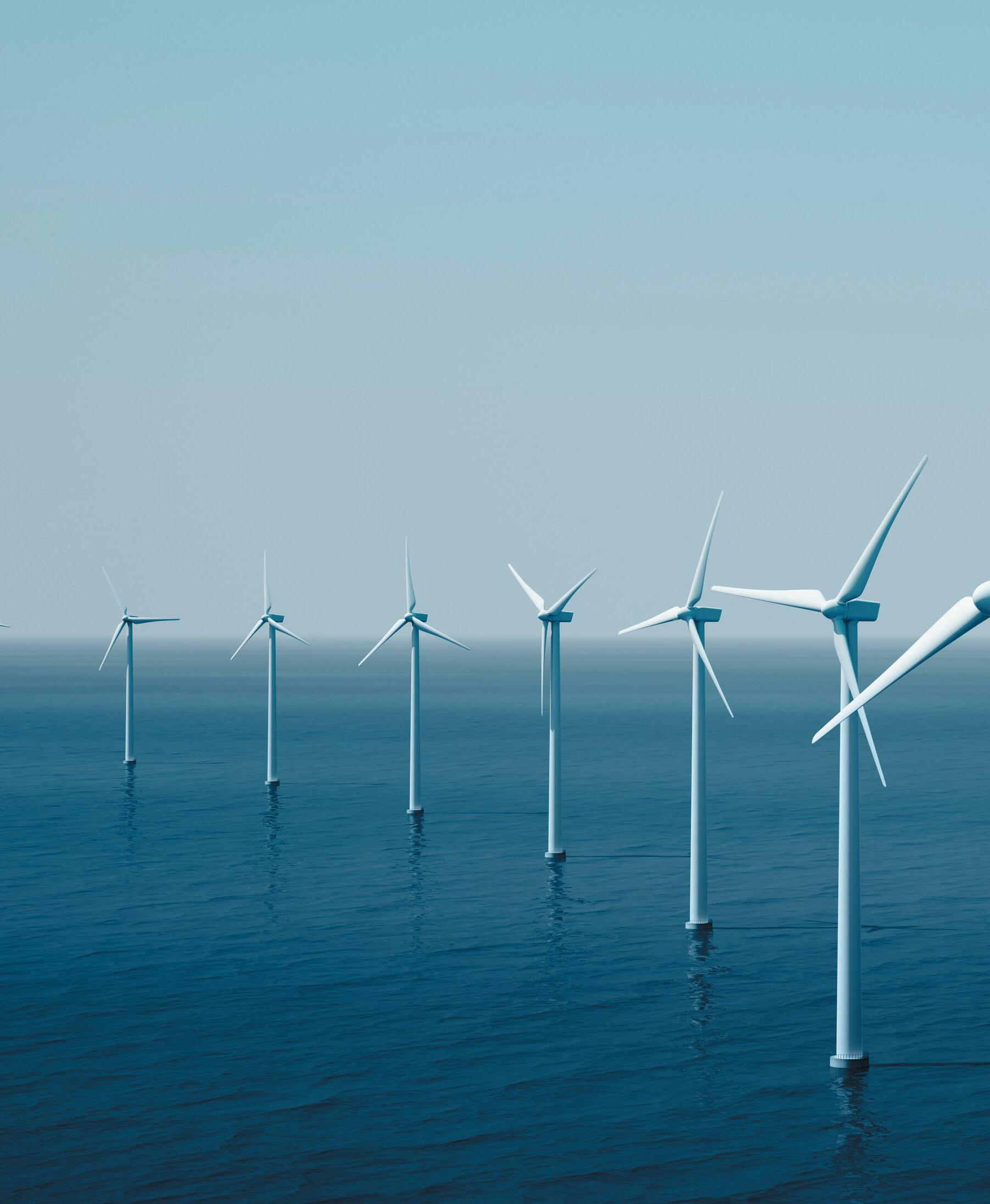
United States added no new offshore turbines in 2022 but identified 700,00 acres of potential offshore wind development in the Gulf of Mexico.
WINDPOWER ENGINEERING & DEVELOPMENT26 SEPTEMBER 2022www.windpowerengineering.com
INCREASE OFFSHORE WIND ADOPTION
WINDPOWER ENGINEERING & DEVELOPMENT 27SEPTEMBER 2022
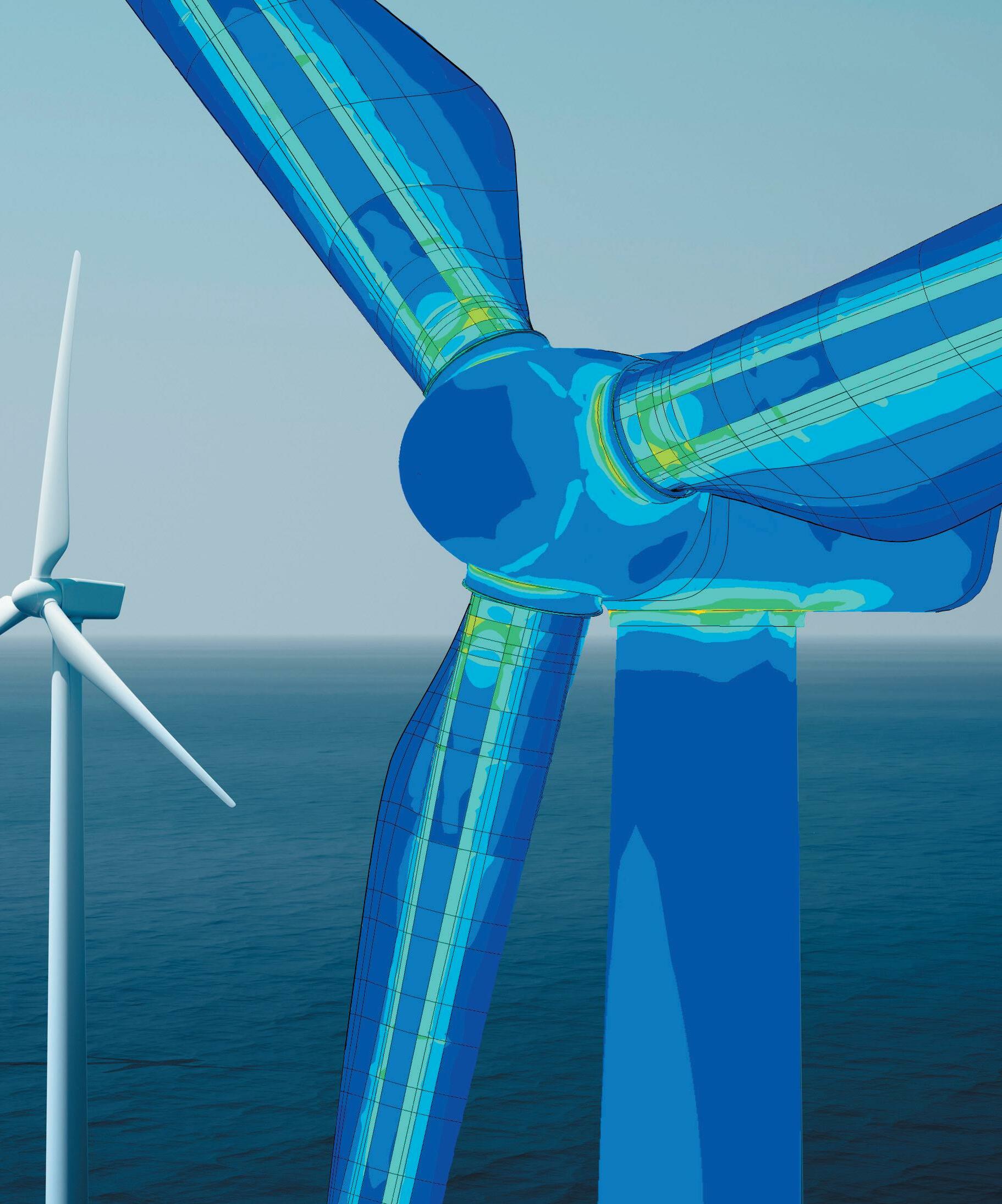
Engineering simulation technology offers an innovative solution

With its enormous global potential, the offshore wind industry should be leading the charge to hit the IEA's net-zero 2050 target. Unfortunately, it is being held back by barriers to growth that are preventing it from reaching its full potential.
California • Colorado • Florida • Georgia • Hawaii • Illinois • Louisiana Massachusetts • North Carolina • Ohio • Pennsylvania • Texas • Washington Corporate Office: 216-831-6131 Offshore Dynamic Foundation Testing • Pre-construction driveability wave equation analyses • Monitoring of pile driving stresses and hammer efficiency • Assessment of pile capacity, shaft resistance and end bearing GRLWEAP wave equation analysis For additional information on testing and analysis services, visit www.grlengineers.com. USING ENGINEERING SIMULATION SOFTWARE
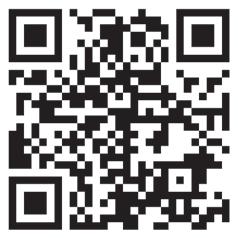
THE OFFSHORE WIND INDUSTRY CAN OVERCOME BARRIERS TO GROWTH BY EMBRACING ENGINEERING SIMULATION SOFTWARE.
WINDPOWER ENGINEERING & DEVELOPMENT28
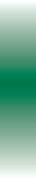
For example, permitting is a slow and cumbersome process. As a result, wind farms currently take around 11 years to move from lease to installation. By the time engineers install turbines, the industry has developed superior technology, and the installed turbines are outdated.
The offshore wind industry can overcome barriers to growth by embracing engineering simulation software. Using simulation software, engineers can create detailed models of wind turbines to analyze performance under different conditions. These models can lead to lower costs, shorter time frames to design and build turbines, and increased renewable energy adoption. Savings achieved by improved designs can be re-allocated to different areas of the supply chain, creating more profit.
The positive news is that the industry has the potential to hit and even surpass net-zero targets. According to the IEA, it could generate more than 18-times today's global electricity demand. In the United States, offshore wind has the potential to provide more than 2,000 GW of energy – two-times the current generation of the entire grid.
Barriers to growth
For example, in a recent project, Akselos modeled offshore wind jacket foundations to identify specific stress hotspots for optimization. The modeling results showed that the software could reduce the steel weight of offshore wind
The offshore wind industry also relies on expensive raw materials for construction, such as copper, iron and steel. The price of these raw materials is soaring. Globally, the cost of steel has risen by 215%, while global iron and copper prices rose by around 50% last year. Such steep increases have been driven in part by the war in Ukraine driving up the cost of raw materials, especially since Russia and Ukraine are significant producers of steel.
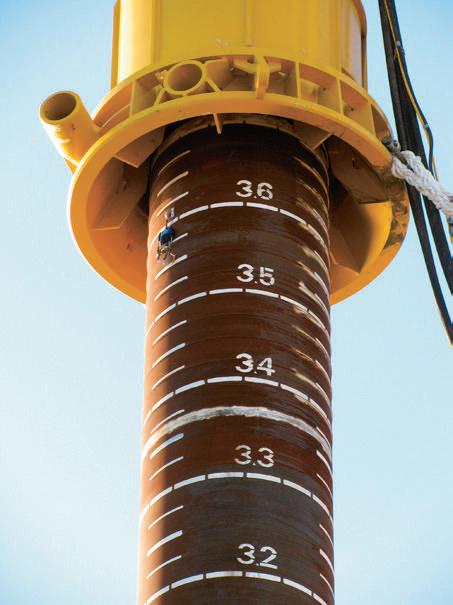
iStock

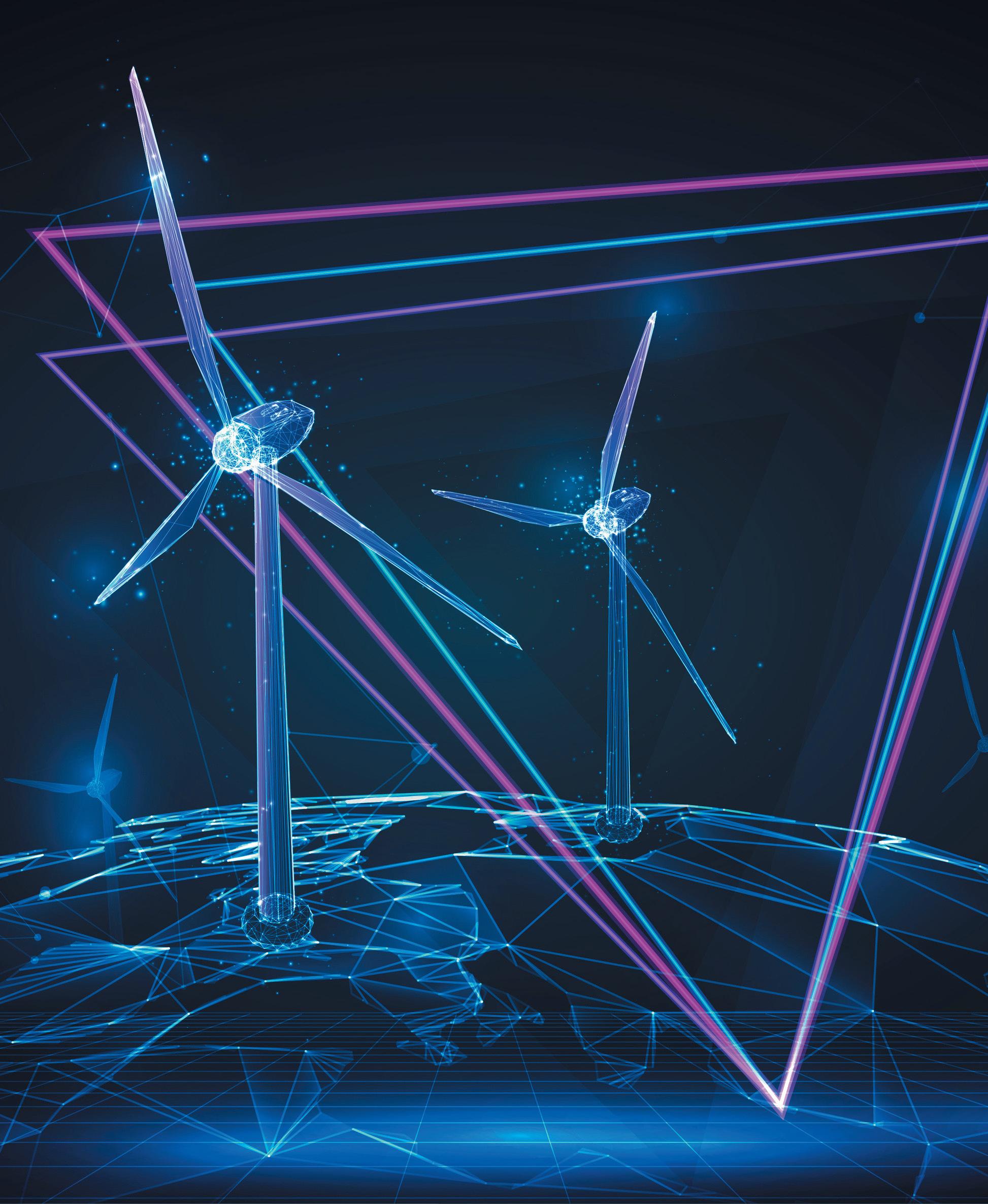
The reduction in steel weight achieved is significant as it could help the industry overcome its two main barriers to growth. Using less steel offsets the high cost of the raw material, bringing down the price of the technology and increasing deployment. Also, the less raw material required, the quicker a turbine can be built, which somewhat reduces the time necessary to get a turbine from conception to installation.
Adobe Stock
Global implications
Finally, by creating more efficient turbine designs and lowering prices, simulation software can help us overcome two further fundamental challenges of our time: Energy security and affordability. Engineering simulation software lowering the cost of renewable energy and increasing its adoption help diversify countries' energy mix and reduce the reliance on fossil fuel exports. This diversification is crucial as Russia is threatening to cut off European
jacket foundations by up to 20% while meeting the exact design requirements and without impacting the scale of wind generation output.
From a global perspective, the results of this project could have far-reaching implications. As many in the wind industry believe, bigger turbines are not automatically better. Leaner designs removing unnecessary weight are superior
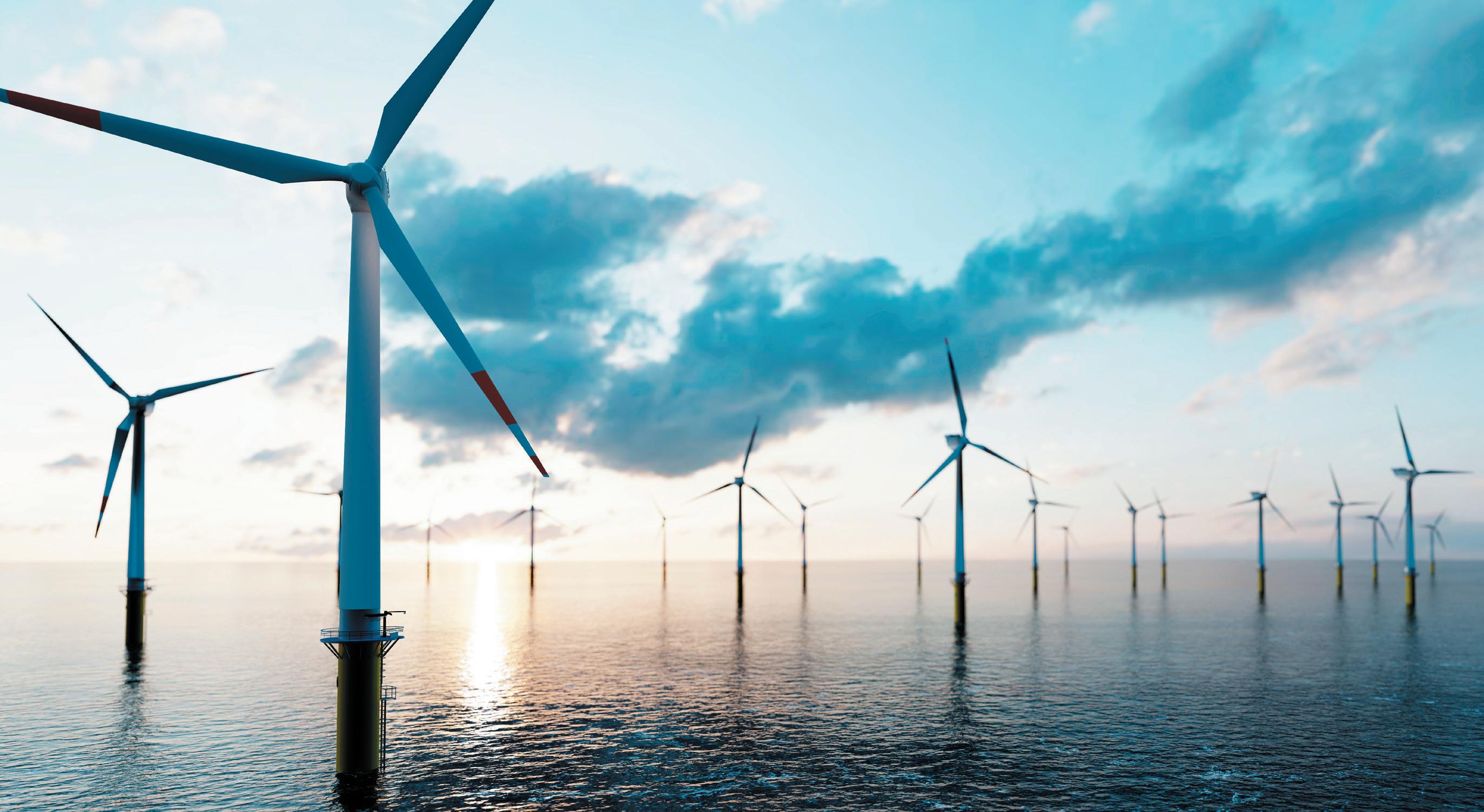
USING ENGINEERING SIMULATION SOFTWARE
WPE
gas supplies, and there is a growing requirement to incorporate renewable energy into the electrical grid. Lower renewable energy costs can also help ease the global cost of living crisis that we are currently facing.
as they use less raw material, speeding up the building process and increasing adoption.Moreover, if simulation software can significantly reduce the weight of offshore jackets, there is room for improvements elsewhere. Engineers could use simulation software to optimize more wind turbine components — such as the tower and rotor blades — to find other inefficiencies and reduce costs.
A solid base to build on Offshore wind is in a strong position, with capacity increasing globally and plans to expand. However, the industry is falling short of its net-zero targets and must grow quickly to help avoid the worst of climate change. Offshore wind has enormous potential to grow at the speed and scale required to achieve net-zero emissions by 2050. Combining this potential with engineering simulation software could drive the industry towards net-zero while increasing energy security and affordability.
KEEP UP WITH US ON TWITTER! Connect with Industry Experts everythingcovering in wind energy from turbine design to installation to maintenance. Looking for more ways to connect? Follow along @Windpower_Eng



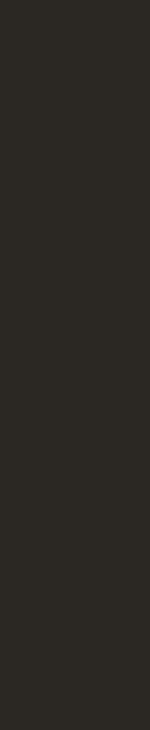
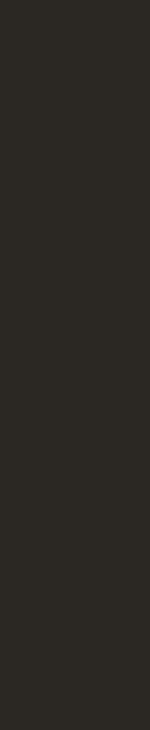



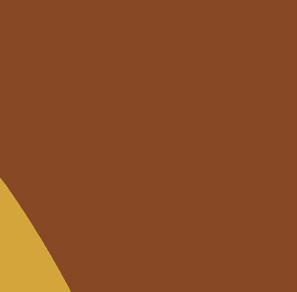
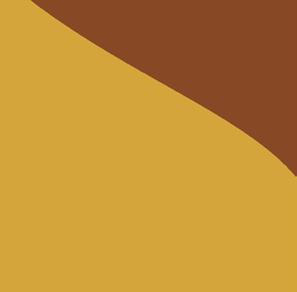
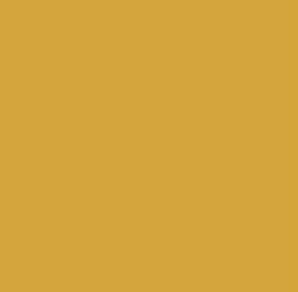

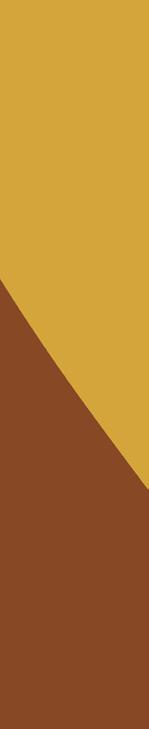
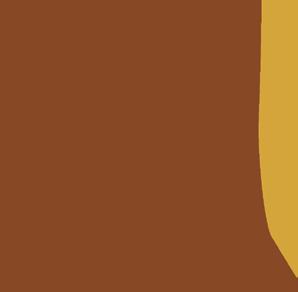
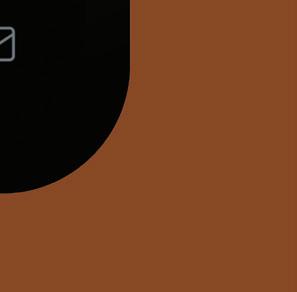
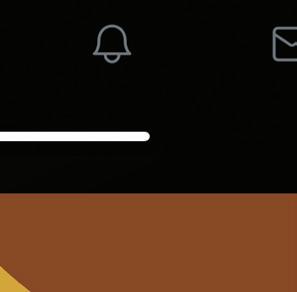
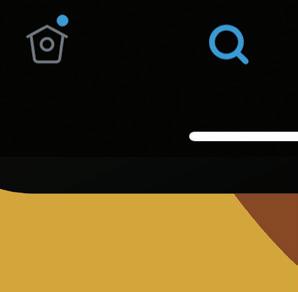
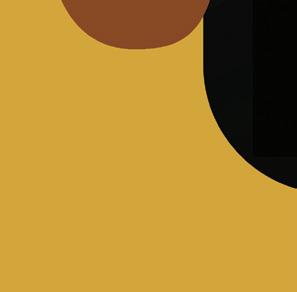

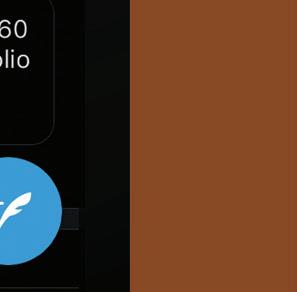
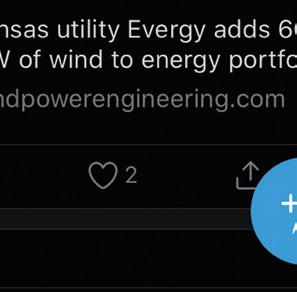
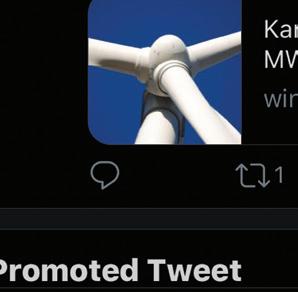
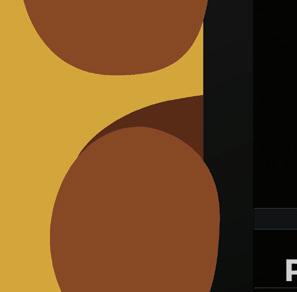
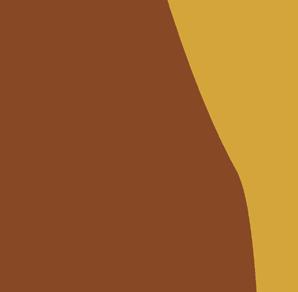
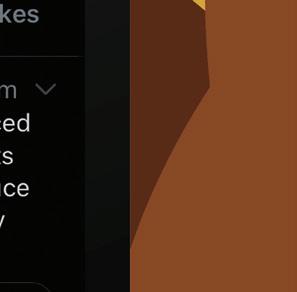
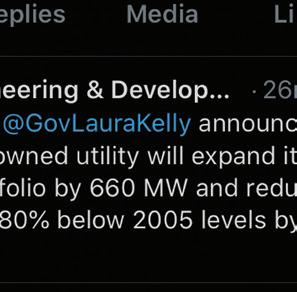
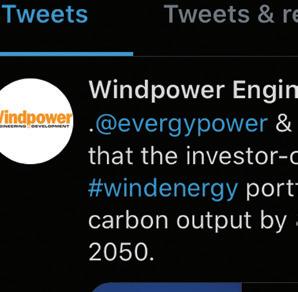
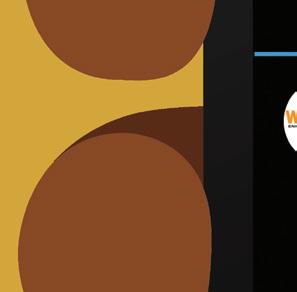
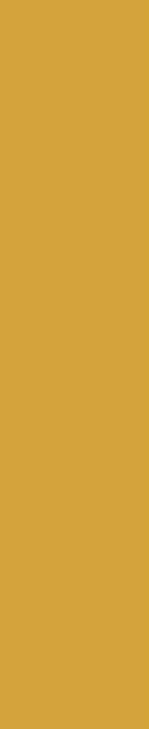

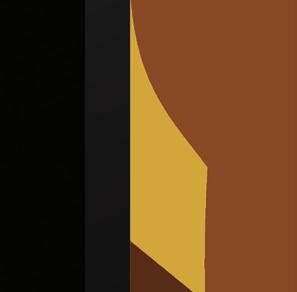
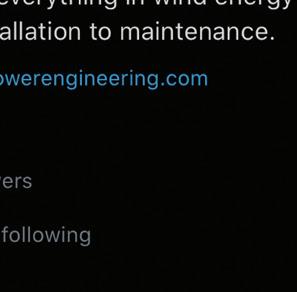
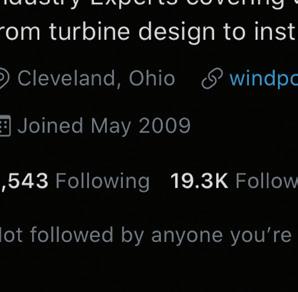
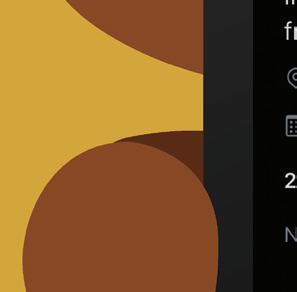

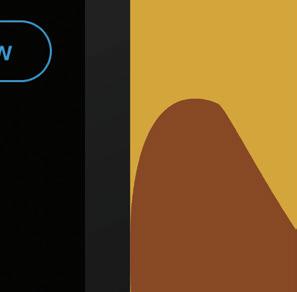
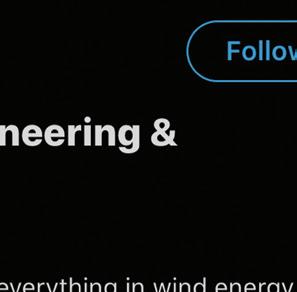
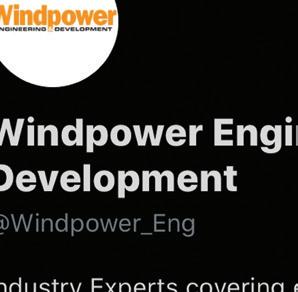
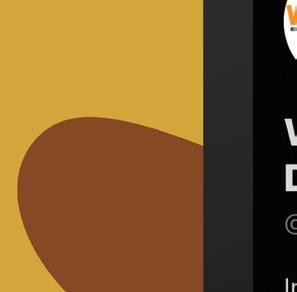
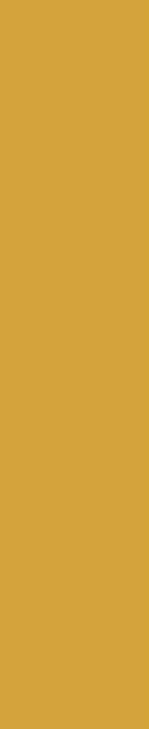
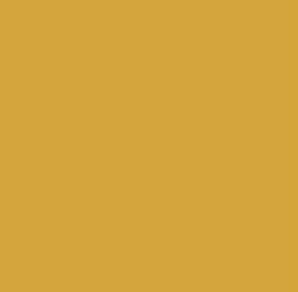
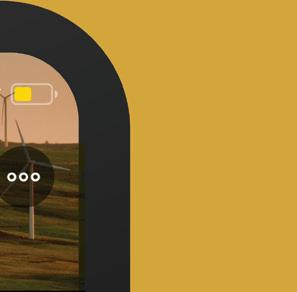

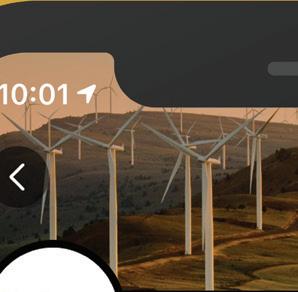

Abaris 18 AZTEC Bolting Services Inc. ................................. Cover, 16 Boker’s, Inc. 25 Dexmet ........................................................................... 11 GRL Engineers ................................................................. 28 Megger 1 Norbar ............................................................................ BC WindEnergy Hamburg ...................................................... 21 Yuken IFC WINDPOWER ENGINEERING & DEVELOPMENT32 SEPTEMBER 2022www.windpowerengineering.com Follow the whole team on Twitter AD INDEX CONNECT WINDPOWER ENGINEERING & DEVELOPMENT Looking for more ways to connect? LEADERSHIP TEAM VP of Sales Mike Emich memich@wtwhmedia.com508.446.1823 Managing Director Scott McCafferty smcca310.279.3844erty@wtwhmedia.com MarshallEVP Matheson mmatheson@wtwhmedia.com805.895.3609 CourtneyPublisher Nagle 440.523.1685cseel@wtwhmedia.com SALES Jami Brownlee jbrownlee@wtwhmedia.com224.760.1055 Ashley Burk aburk@wtwhmedia.com737.615.8452 Jim Powers jpowers@wtwhmedia.com312.925.7793 WITH US @Windpower_Eng
Looking for more ways to connect?
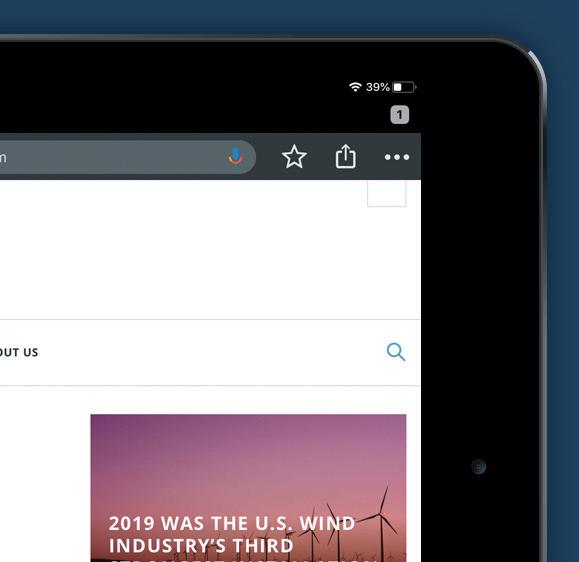
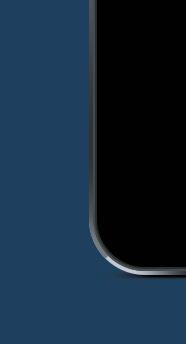
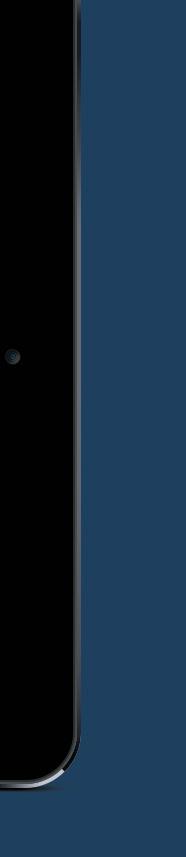

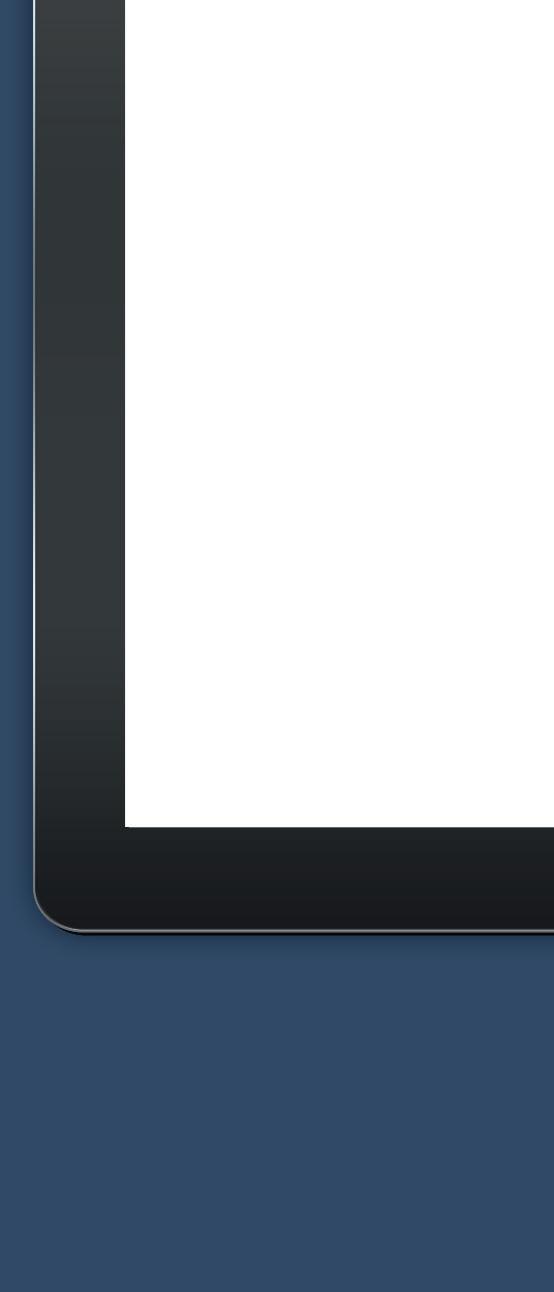

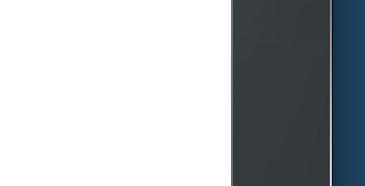
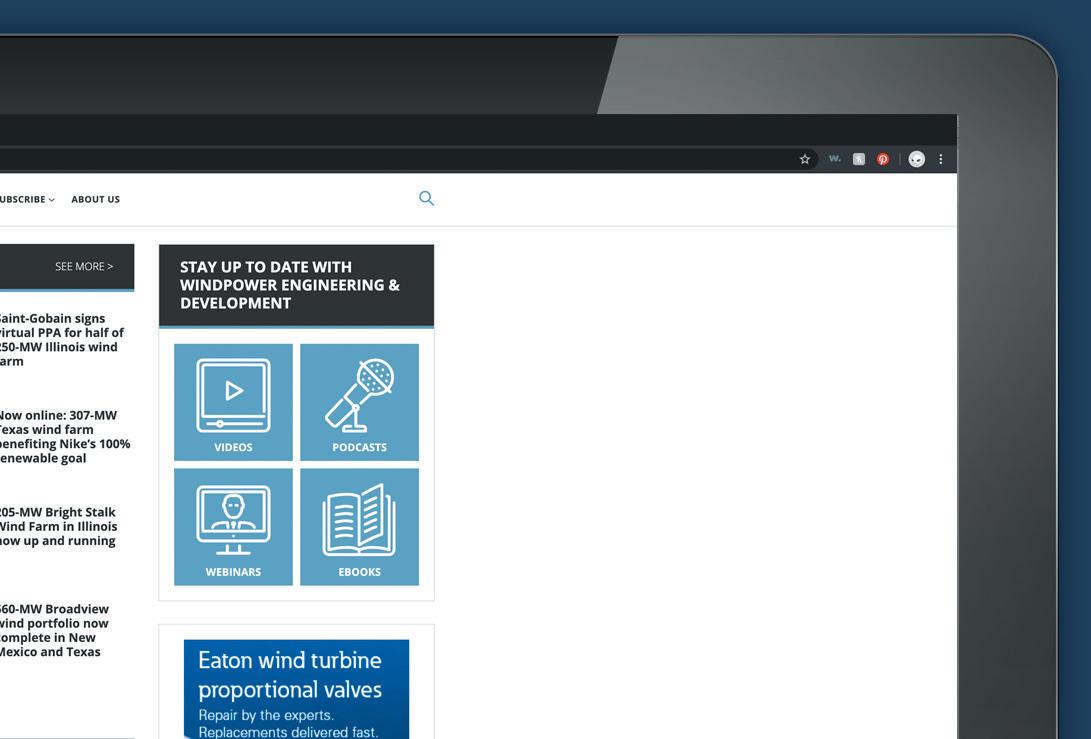
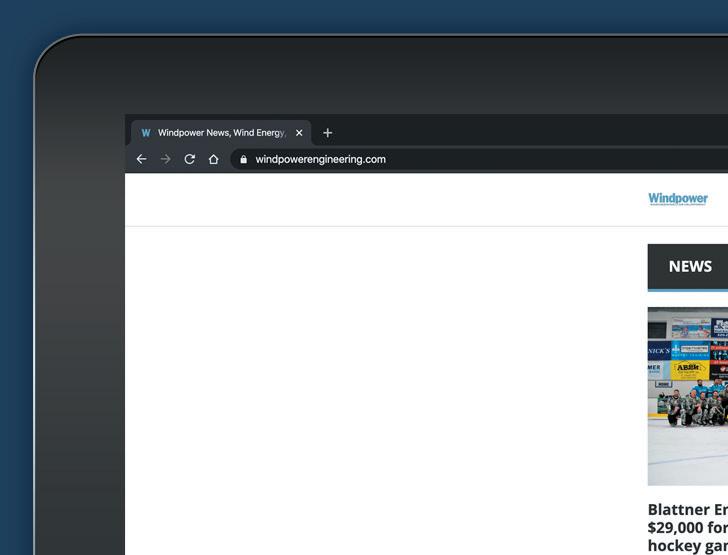


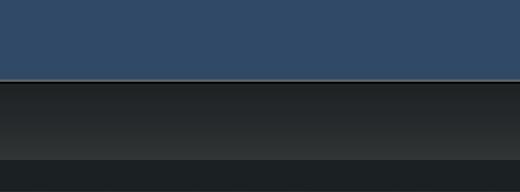
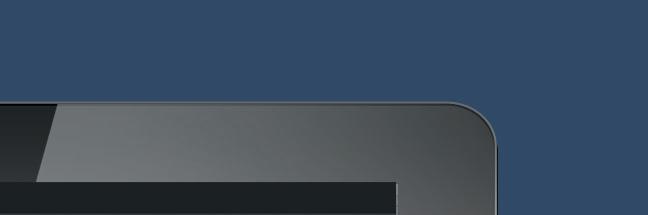

FIND US WINDPOWERENGINEERING .COM
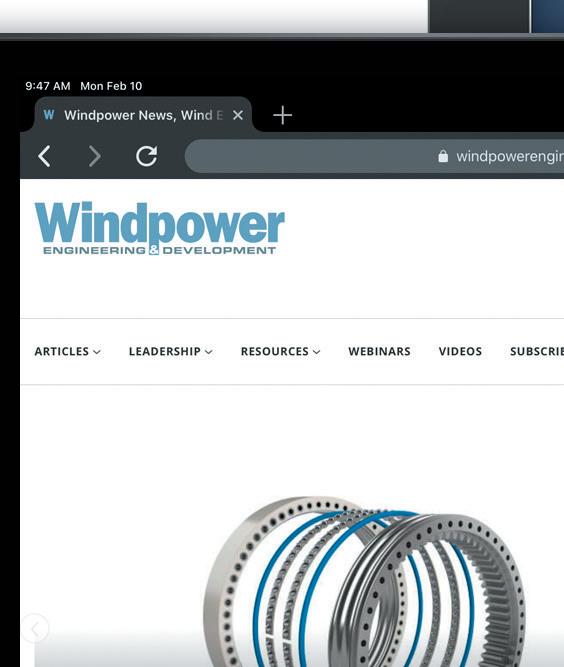
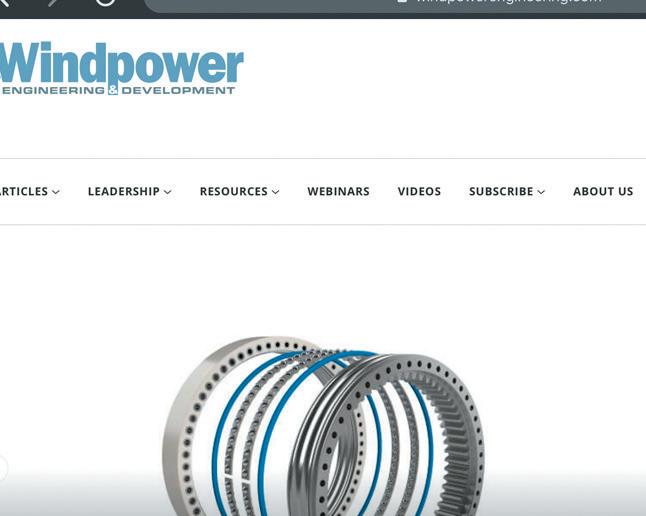



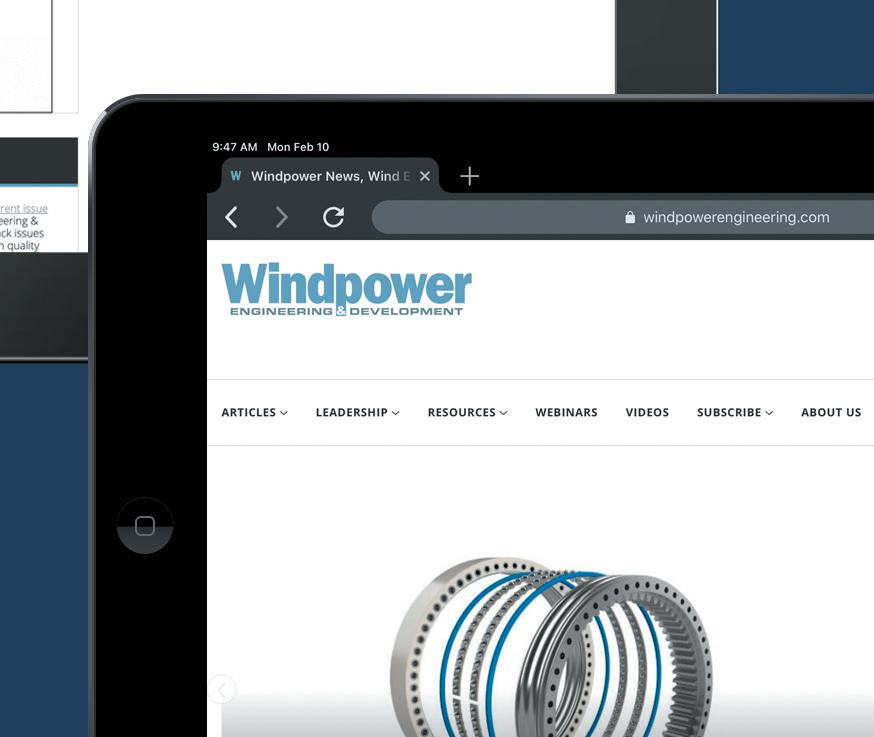
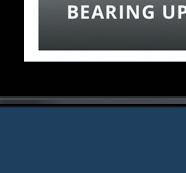

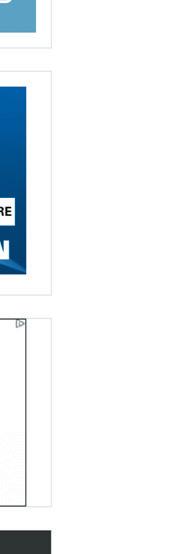

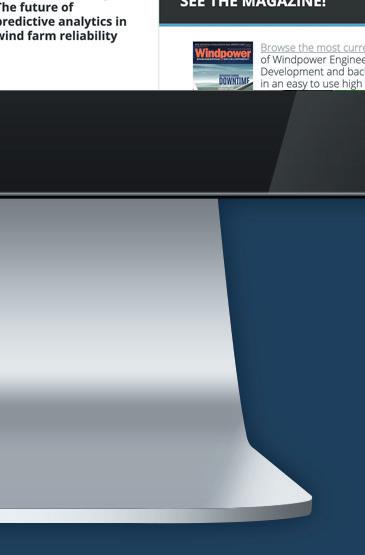
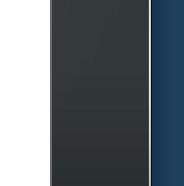

See the latest wind power developments and U.S. project news on our website. Also fi nd expert webinars and more from the leading wind power engineering magazine today. ONLINE!
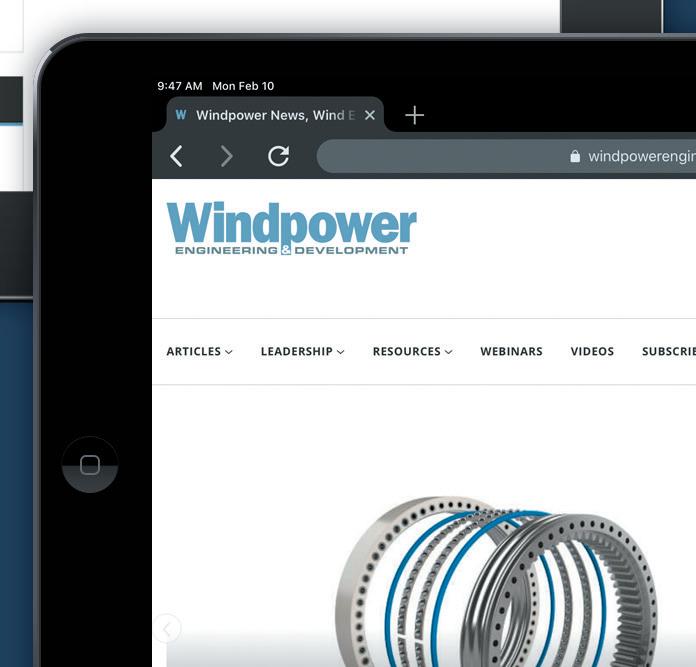



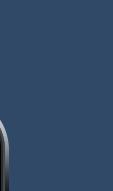
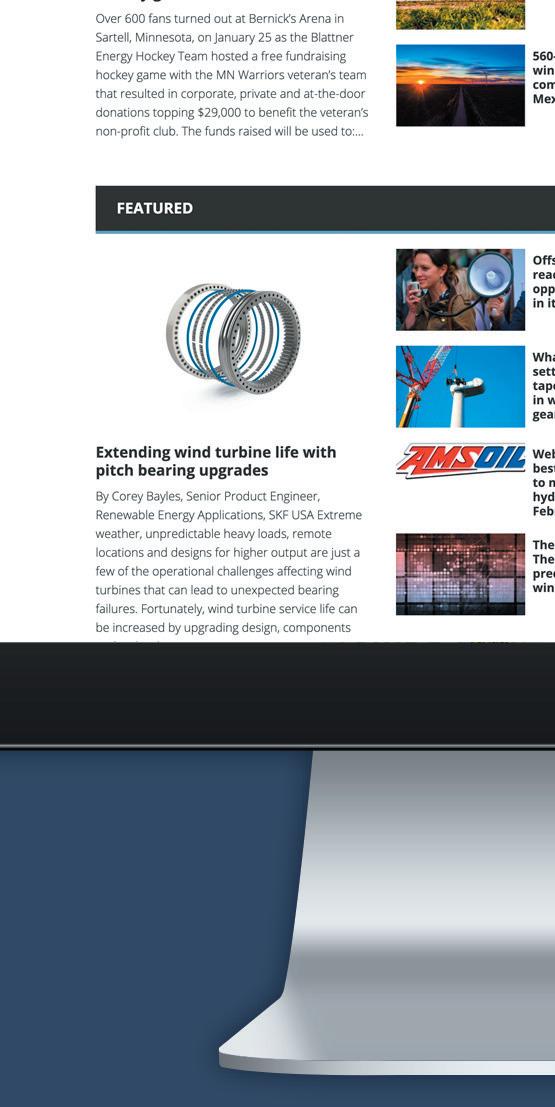
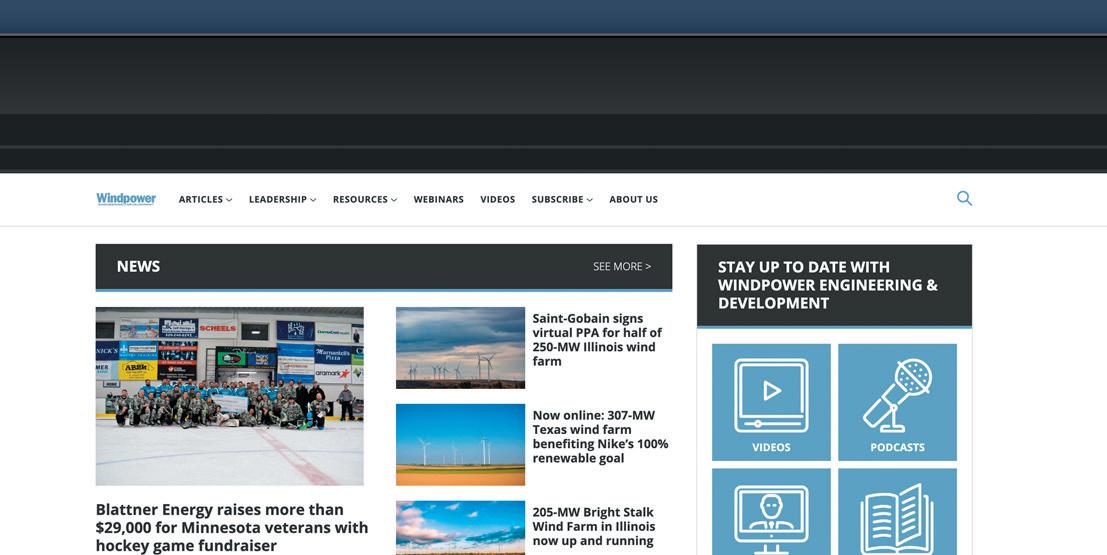
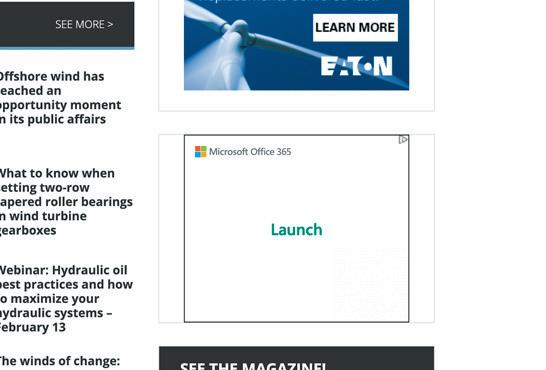
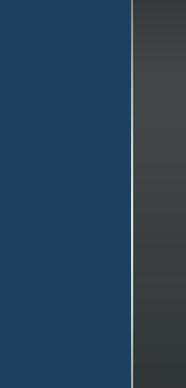
A Radical Change in Bolting is Coming Your Way Norbar Torque Tools Introduces a New Generation in AC Powered Torque Multipliers EvoTorque®2Let’sTalkTorque It’s Time to Change the Way You Think About AC Powered Torque Multipliers • Operating ranges from 100 lb-ft to 4500 lb-ft • Measures in Torque, Torque and Angle, and Torque Audit mode for pre-tightened bolts • Versions for 110 VAC or 230 VAC • Lightweight at only 23lbs. • Factory calibrated and certified to ± 3% accuracy regardless of fluctuating voltages • USB and Bluetooth® 4.0 data transfer (also called Bluetooth® Smart) • 3,000 readings in internal memory, time and date stamped • Includes PC software ‘EvoLog’ for data management and tool configuration • From factory to field; for fabrication, installation, verification and maintenance Norbar Torque Tools, Inc. 440.953.1175 PH 440.953.9336 inquiry@norbar.usFXnorbar.com
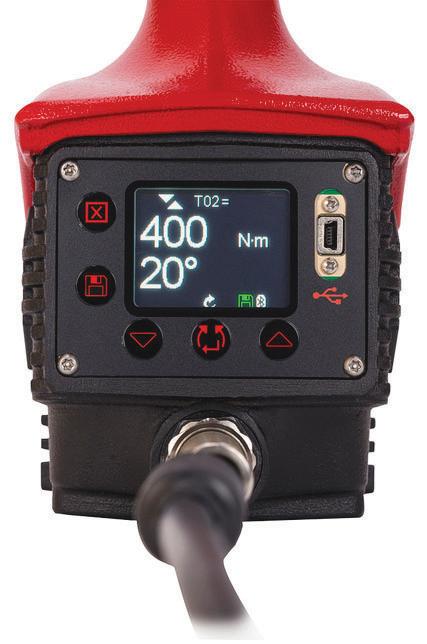
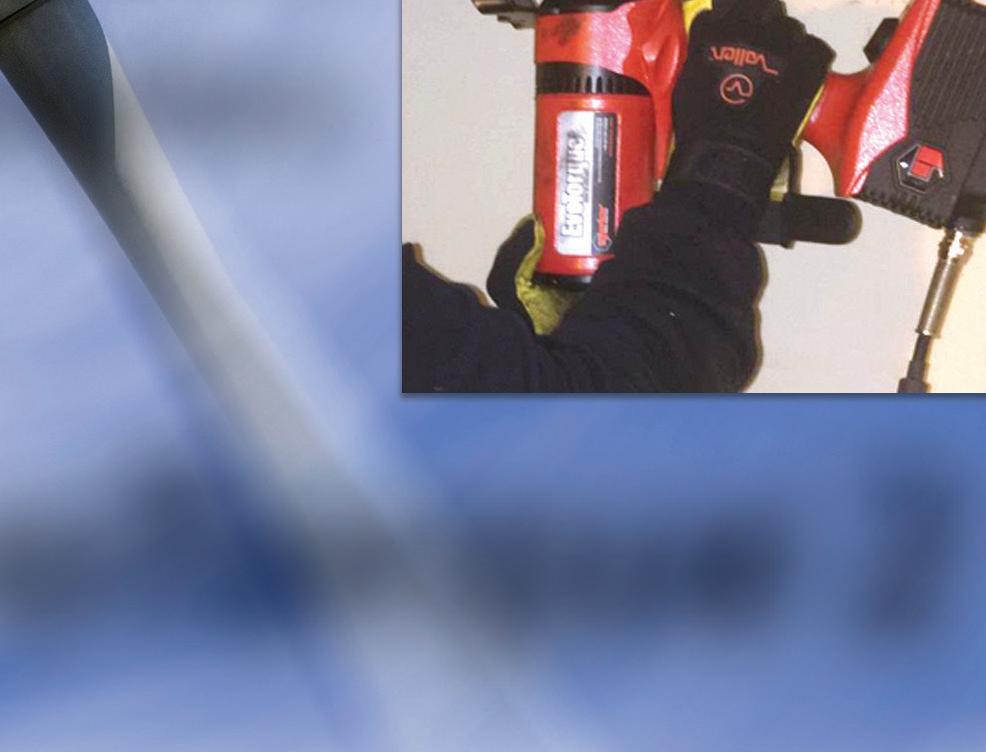
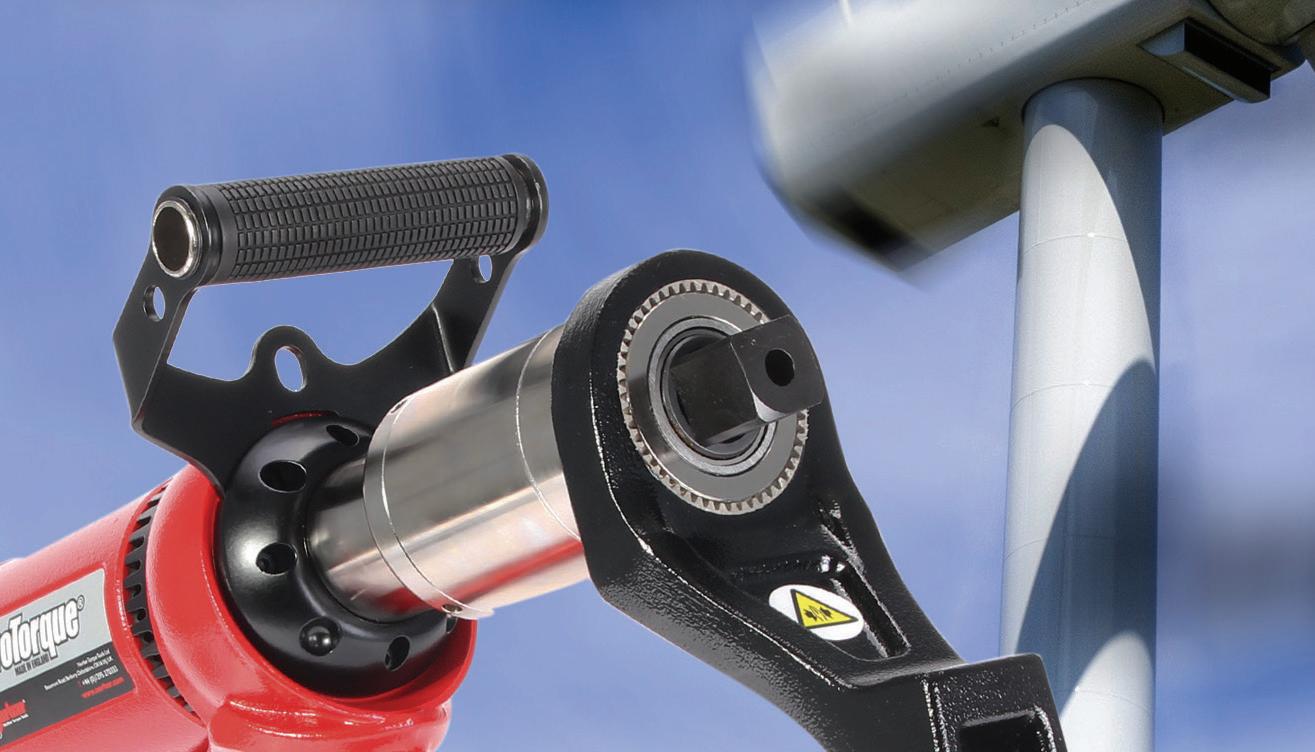
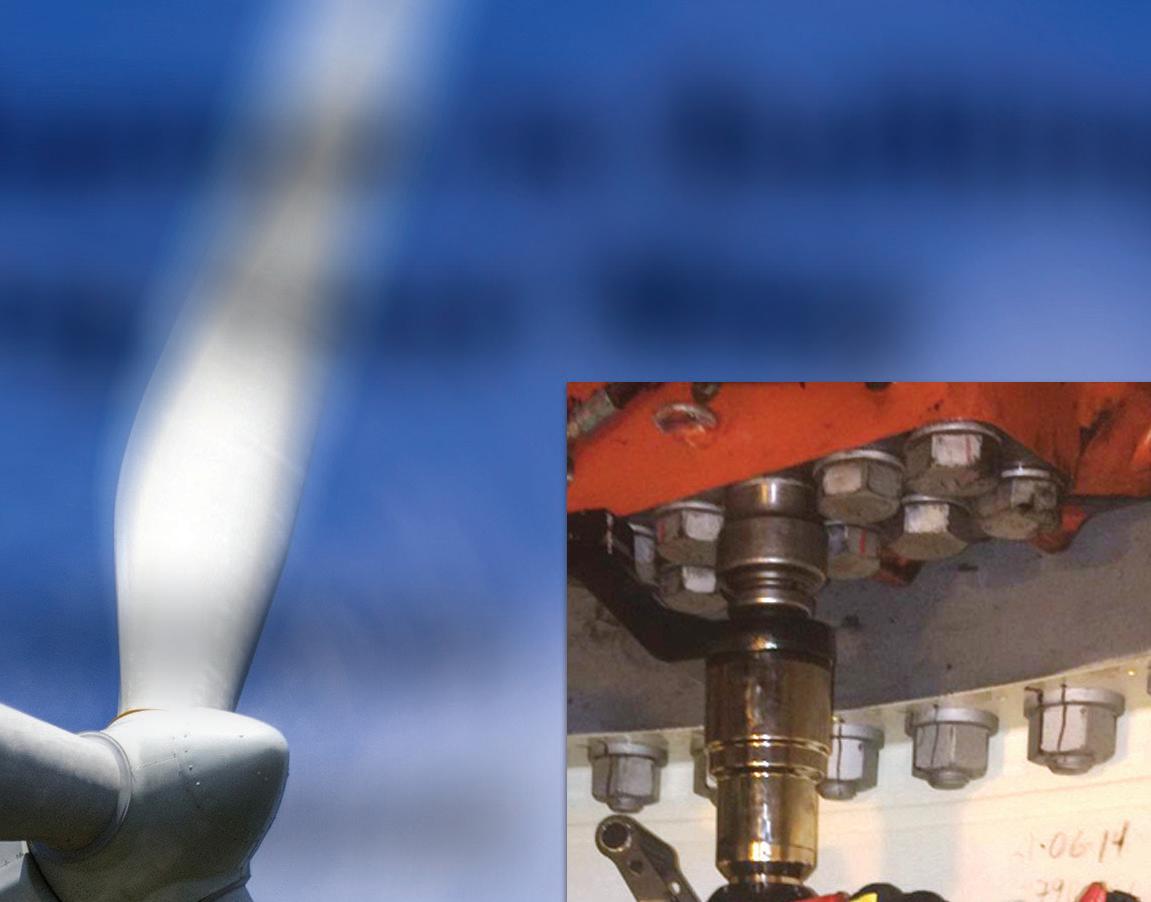

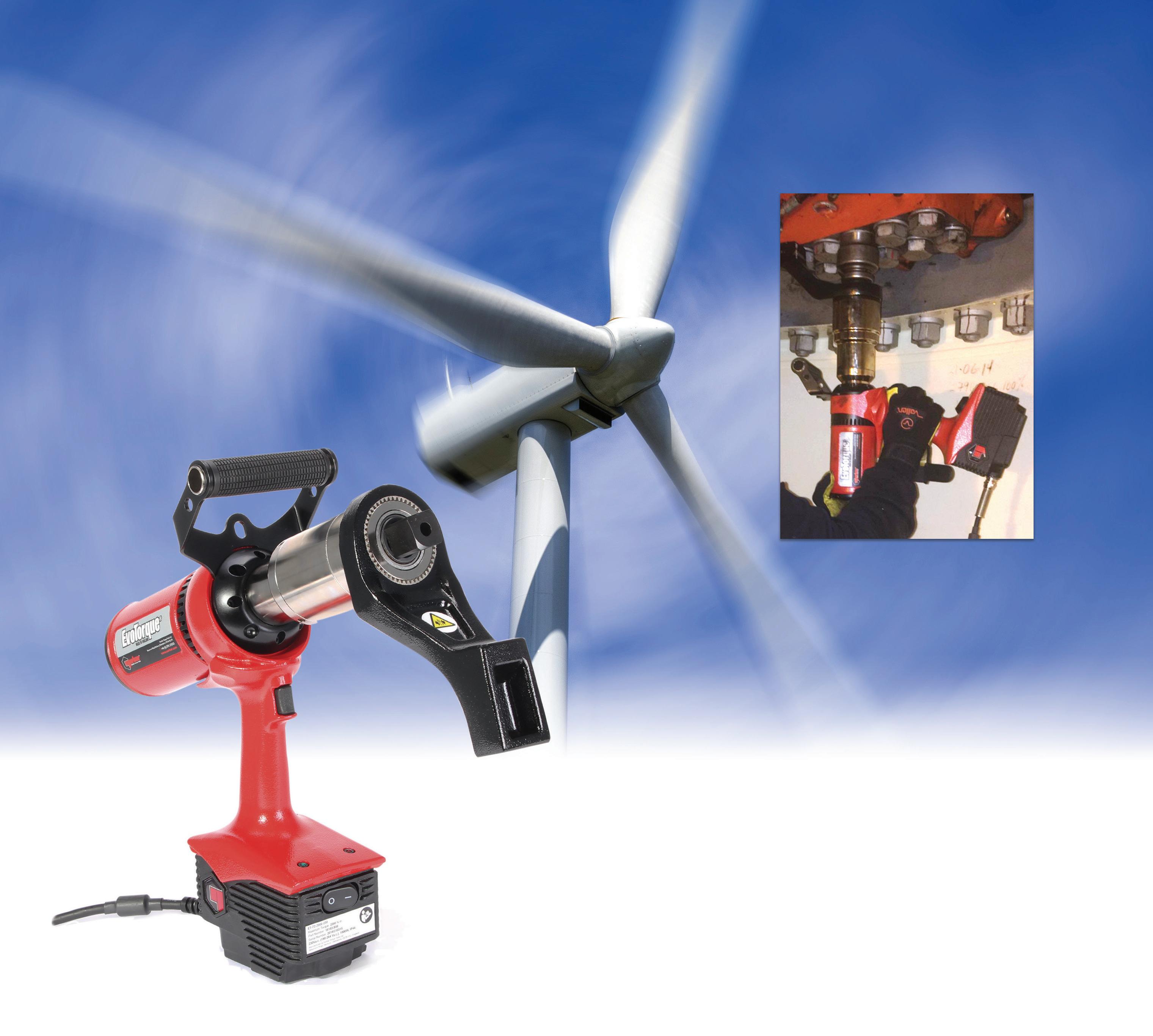