

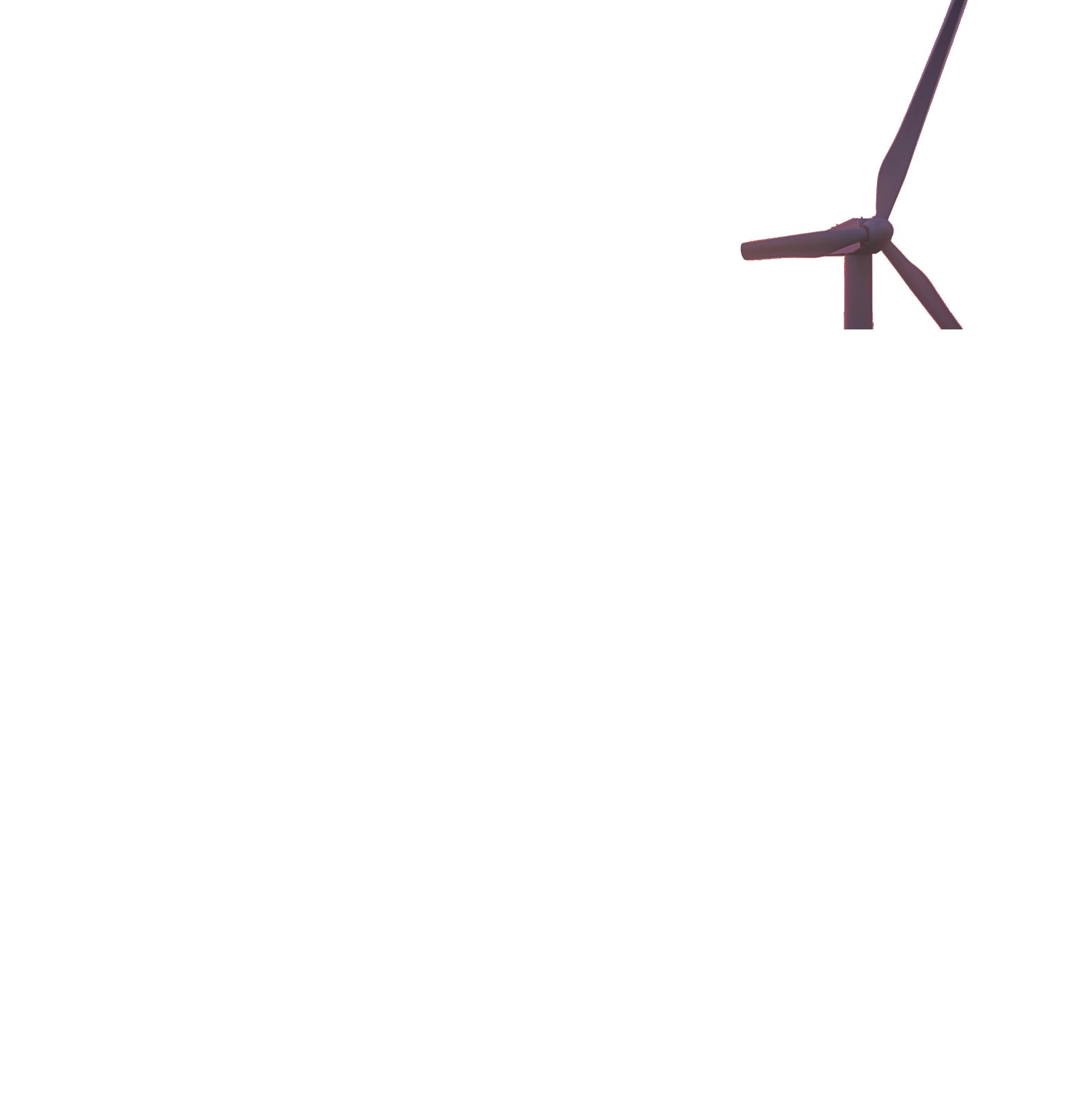
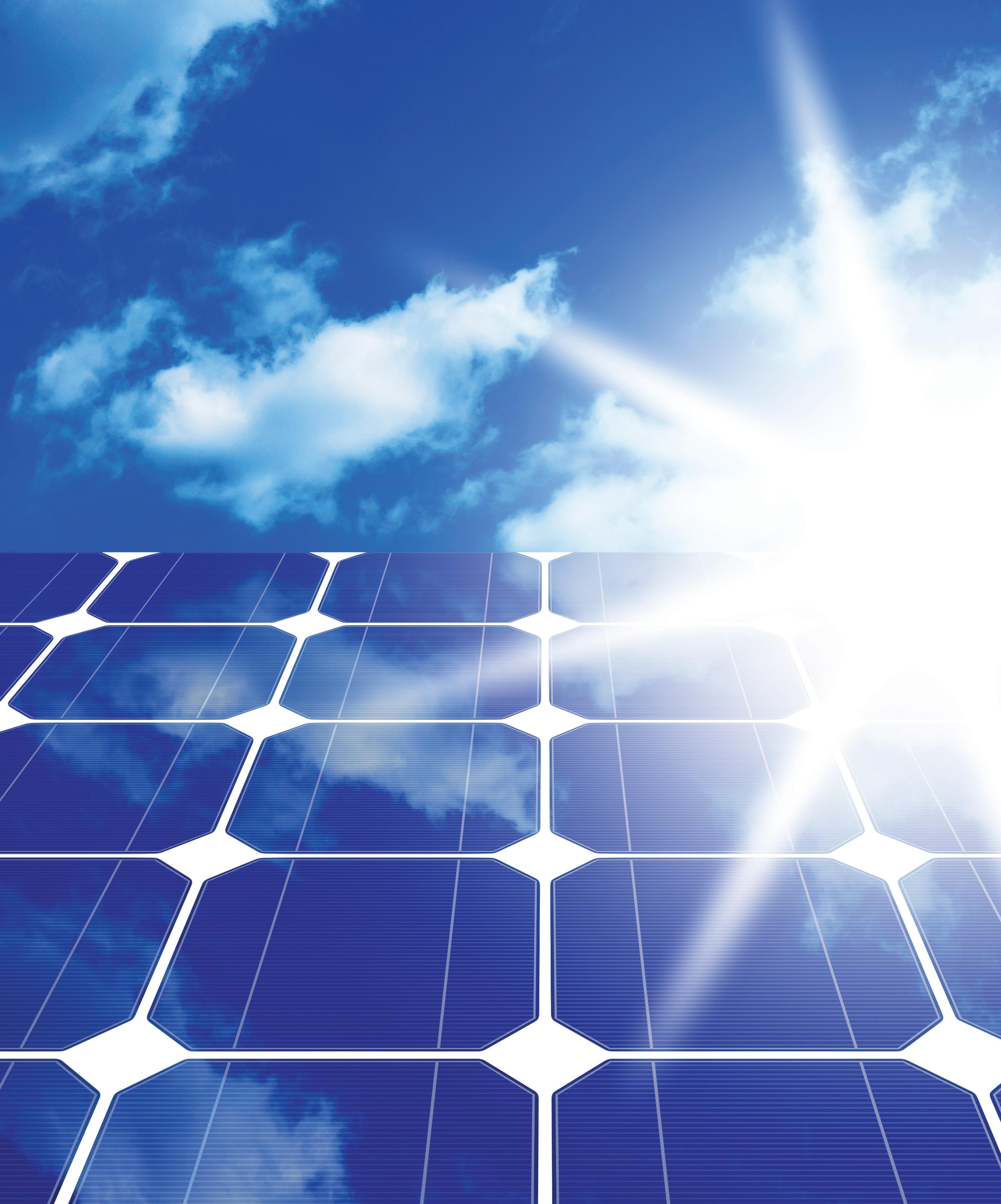






Scale Your Business
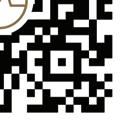
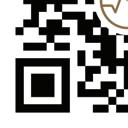
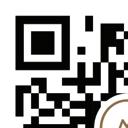
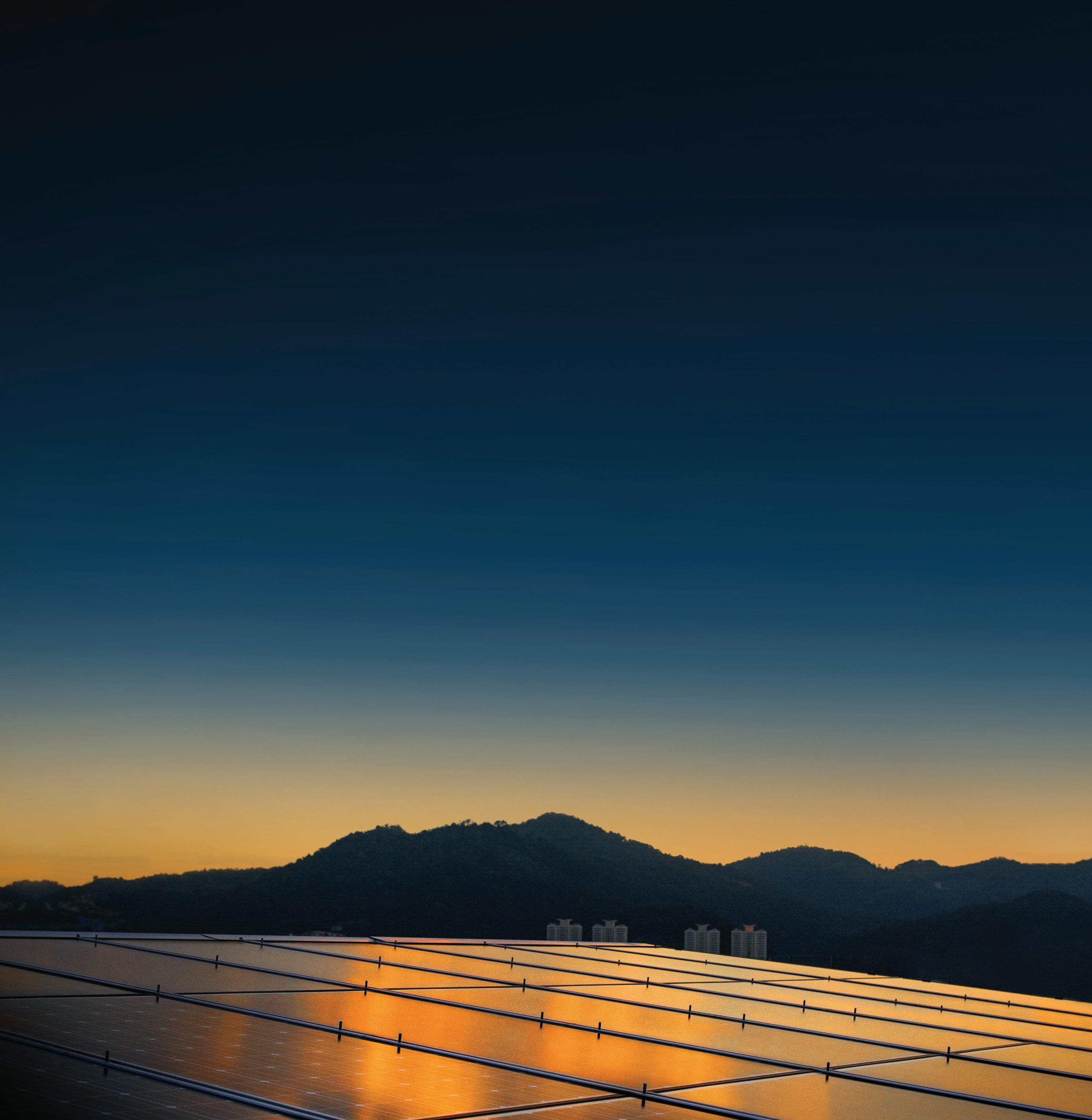
One-stop
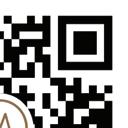

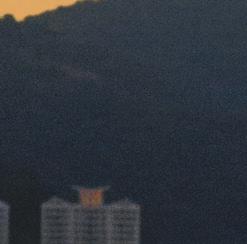

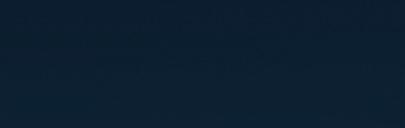


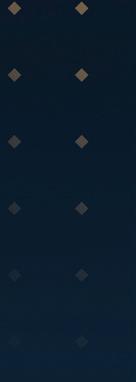
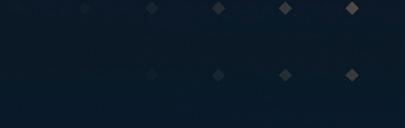
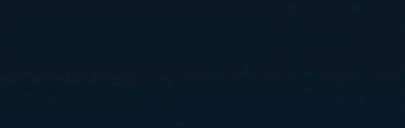
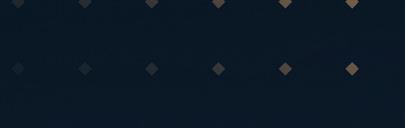
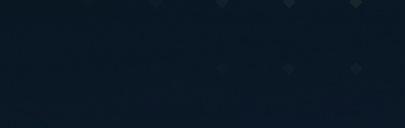
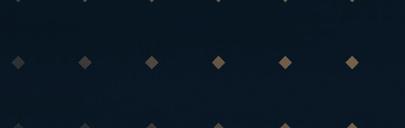
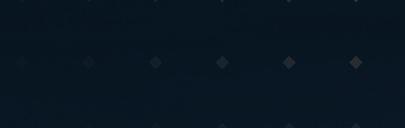



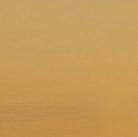

Nationwide Field Service Network


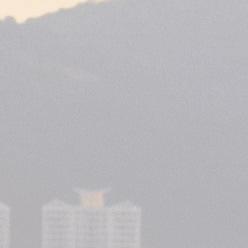
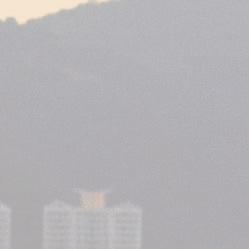
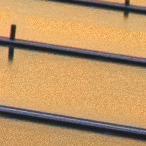
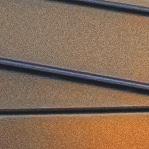
One-stop
We’re wrapping up another hectic year for renewable energy policy in the United States. And as busy as everyone has been, we’re sure a few standout stories missed your eyes this year. Don’t worry, this handbook reviews what has been trending in both the solar and wind industries in our sister publications Solar Power World and Windpower Engineering & Development. In addition to installation tips, service guides and O&M best practices, the 2023 Renewable Energy Handbook offers our
editors' picks for the top solar products released in the last year as well as the top wind projects recently brought online.
The country will be going through a major transformation in 2023 as incentives in the Inflation Reduction Act are released to the renewable energy markets. Be sure to check our two websites for the absolute latest on how the solar and wind industries will shake out in 2023. We’re ready for more solar, storage and offshore wind project announcements!
Courtney Nagle cseel@wtwhmedia.com 440.523.1685
Editorial Director, Renewables Kelly Pickerel kpickerel@wtwhmedia.com
Senior Editor Billy Ludt bludt@wtwhmedia.com
VP of Creative Services Mark Rook mrook@wtwhmedia.com
Art Director Matthew Claney mclaney@wtwhmedia.com
Senior Graphic Designer Allison Washko awashko@wtwhmedia.com
Graphic Designer Mariel Evans mevans@wtwhmedia.com
Director, Audience Development Bruce Sprague bsprague@wtwhmedia.com
Videographer Manager Bradley Voyten bvoyten@wtwhmedia.com
Videographer Garrett McCafferty gmcca erty@wtwhmedia.com
Videographer Kara Singleton ksingleton@wtwhmedia.com
VP of Digital Marketing Virginia Goulding vgoulding@wtwhmedia.com
Digital Marketing Manager Taylor Meade tmeade@wtwhmedia.com
Digital Marketing Coordinator Emily Gillespie egillespie@wtwhmedia.com
Digital Production/ Marketing Designer Samantha King sking@wtwhmedia.com
Marketing Graphic Designer Hannah Bragg hbragg@wtwhmedia.com
Webinar Coordinator Halle Sibly hkirsh@wtwhmedia.com
Webinar Coordinator Kim Dorsey kdorsey@wtwhmedia.com
WTWH Media, LLC 1111 Superior Avenue, Suite 2600, Cleveland, OH 44114
Ph: 888.543.2447 Fax: 888.543.2447
Web Development Manager B. David Miyares dmiyares@wtwhmedia.com
Digital Media Manager Patrick Curran pcurran@wtwhmedia.com
Digital Production Manager Reggie Hall rhall@wtwhmedia.com
Front End Developer Melissa Annand mannand@wtwhmedia.com
Digital Production Specialist Nicole Lender nlender@wtwhmedia.com
Digital Production Specialist Elise Ondak eondak@wtwhmedia.com
Events Manager Jennifer Kolasky jkolasky@wtwhmedia.com
Event Marketing Specialist Olivia Zemanek ozemanek@wtwhmedia.com
Customer Service Manager Stephanie Hulett shulett@wtwhmedia.com
Customer Service Representative JoAnn Martin jmartin@wtwhmedia.com
Customer Service Representative Tracy Powers tpowers@wtwhmedia.com
Customer Service Representative Renee Massey-Linston renee@wtwhmedia.com
Customer Service Representative Trinidy Longgood tlonggood@wtwhmedia.com
FINANCE
Controller Brian Korsberg bkorsberg@wtwhmedia.com
Accounts Receivable Specialist Jamila Milton jmilton@wtwhmedia.com
WINDPOWER ENGINEERING & DEVELOPMENT does not pass judgment on subjects of controversy nor enter into disputes with or between any individuals or organizations.
WINDPOWER ENGINEERING & DEVELOPMENT is also an independent forum for the expression of opinions relevant to industry issues. Letters to the editor and by-lined articles express the views of the author and not necessarily of the publisher or publication. Every e ort is made to provide accurate information. However, the publisher assumes no responsibility for accuracy of submitted advertising and editorial information. Non-commissioned articles and news releases cannot be acknowledged. Unsolicited materials cannot be returned nor will this organization assume responsibility for their care.
WINDPOWER ENGINEERING & DEVELOPMENT does not endorse any products, programs, or services of advertisers or editorial contributors. Copyright© 2022 by WTWH Media, LLC. No part of this publication may be reproduced in any form or by any means, electronic or mechanical, or by recording, or by any information storage or retrieval systems, without written permission from the publisher.
SUBSCRIPTION RATES: Free and controlled circulation to qualified subscribers. Non-qualified persons may subscribe at the following rates: U.S. and possessions, 1 year: $125; 2 years: $200; 3 years $275; Canadian and foreign, 1 year: $195; only U.S. funds are accepted. Single copies $15. Subscriptions are prepaid by check or money orders only.
SUBSCRIBER SERVICES: To order a subscription or change your address, please email: please visit our web site at www.windpowerengineering.com
WINDPOWER ENGINEERING & DEVELOPMENT (ISSN 2163-0593) is published four times per year in February, May, September and a special issue in December by WTWH Media, LLC, 1111 Superior Avenue, Suite 2600, Cleveland, OH 44114. Periodicals postage paid at Cleveland, OH and additional mailing o ces.
POSTMASTER: Send address changes to: Windpower Engineering & Development, 1111 Superior Avenue, Suite 2600, Cleveland, OH 44114
Up to 2000A, up to 1500 VDC
The first true motorized 2 pole 1500 VDC Innovative Application tested design Reduced total cost of ownership
SIRCO MOT DC & DC ESS are remotely operated multipolar load break switches. They make and break under load conditions and provide safety isolation for any low voltage circuit dedicated to DC applications with high short circuit capabilities up to 1500 VDC.
Robust federal clean energy policy has laid the groundwork for a decade of explosive growth for the solar and storage industries. A 10-year extension of the investment tax credit, new incentives for domestic solar product manufacturing and many other provisions will help solar and storage meet the increasing demand for home-grown, clean energy.
The industry has already seen U.S. manufacturing expansion and groundbreaking announcements directly triggered by the Inflation Reduction Act at the end of 2022, with developers eager to collect the 10% ITC adder for sourcing domestic content. From mounting companies like Nextracker, with an expanding manufacturing facility in Pennsylvania, to panel makers like Heliene, with expansion plans at a Minnesota facility, the legislation is delivering more solar manufacturing to U.S. soil.
"For decades, it simply did not make economic sense to build solar manufacturing facilities in the United States," wrote Heliene president Martin Pochtaruk in an op-ed for Solar Power World. "Fortunately for energy consumers and the nation’s climate goals, this has started to change. There’s never been a better time to invest in domestic solar manufacturing."
2022 marked a return to relative pre-pandemic normalcy with solar
tradeshows back in business, including the largest in the United States, RE+. The show in Anaheim, California, brought a record-setting number of more than 27,000 people together to attend sessions and see new products in person for the first time in years.
“This was the first time we were able to host RE+ in person since 2019. It was clear that the industry was eager to get back together to network and conduct business, in a way that’s hard to replicate online,” said Stephen Miner, president and CEO of RE+ Events, in a press release.
On the regional policy front, utilities and solar advocates continued to clash in 2022, but some compromises gave the industry hope for a more collaborative future. In Minnesota, the public utilities commission approved a new cost-sharing program for residential solar interconnection upgrades that requires new solar customers to pay $200 into the program to cover any necessary expensive grid upgrades that ordinarily would be expected from one homeowner. And in California, the utilities commission released a new version of net metering 3.0, which didn't include the "solar tax" that the solar industry rallied against in the original version. Although utility outcomes are rarely perfect, the solar industry has had a seat at the table in an increasing
number of important energy discussions.
In markets large and small, the industry celebrated many milestones over the past year. More utility-scale solar was installed in the first nine months of 2022 than all other forms of energy, according to a SUN DAY Campaign review of FERC data. The number of residential solar homeowners adding storage to their projects reached an all-time high, according to EnergySage. One in 10 of all K-12 schools in the country have gone solar, according to Generation180. And the job market recovered from pandemic lows, adding 21,500 jobs in 2021, according to IREC.
The stage is set for a dramatic ramp-up of solar and storage deployment over the next 10 years, but the industry must stay engaged to get the most out of the opportunities ahead.
“SEIA helped deliver the most transformational clean energy bill in history, and now the real work begins,” said SEIA president and CEO Abigail Ross Hopper in a press statement. “SEIA is keenly focused on implementation and is well-positioned to tackle the challenges that remain, including land use, recycling, ethical supply chains, workforce and more. Addressing these issues will require a thoughtful, comprehensive vision, and it’s incumbent upon the entire solar and storage industry to build support for this new clean energy era.” SPW
Whether connecting panels to the inverter/charge controller and monitoring units or providing the infrastructure cable to transfer the electricity to the power grid, HELUKABEL provides electrical system expertise throughout the solar farm. Our copper and aluminum solar cable solutions can be used in environments that can range in temperature from -40°C to + 90°C, resist UV, ozone, abrasion, oil and hydrolysis, and have multiple global approvals such as UL 4703, CSA, IEC 62930, EN 50618, VDE, TÜV, and EAC, to name a few.
For OEM and MRO customers, pre-assembled cable solutions are available for reliable termination and quicker installation on the factory floor or in the field.
The editorial team at Solar Power World had the great opportunity to mingle with 27,000 friends at this year’s RE+ tradeshow in Anaheim, California. Besides stopping by happy hours and food truck lunches, we filled our time visiting as many booths as possible on the show floor to check out the newest products on display.
The solar and storage industries have evolved quite a bit since the last major tradeshow in 2019. Solar
panels are bigger, trackers are more accommodating and inverters are smarter. There have been many great developments in the last few years to make solar and storage easier to deploy. We tried our best to pick a few of our favorites from 2022.
Be sure to visit our online database for an even more extensive list of the top products from 2022.
SPW editors have only chosen a battery once in the five previous years of compiling our favorite products. That’s because batteries used in energy storage systems, especially in the residential market, are mostly just gray boxes with nothing exciting on display. The highest capacity available was usually reached by Tesla with its 13.5-kWh Powerwall, but its 5-kW inverter often leads most households to default to two or more units to meet power needs. Tesla’s nickel manganese cobalt (NMC) chemistry works great, but many safety-conscious installers and homeowners are demanding more lithium-iron phosphate (LFP) brands that can easily be installed outdoors.
Enter the truly customizable and modular EP Cube energy storage system from Canadian Solar. The easy-to-expand single unit has a 7.6kW inverter on top, stackable battery modules in the middle and all the wires condensed in the bottom plate. Each battery module averages about 3.3 kWh, making expandable capacity more affordable when someone needs a bit more than 13.5 kWh but not quite 27 kWh. The LFP-based system can be floor- or wall-mounted, and the entire unit is NEMA 4X rated — the highest outdoor rating we’ve seen for any ESS.
Each 3.3-kWh battery module in the EP Cube weighs around 70 lbs, which is much easier to install than the Powerwall’s 250-lb system. This means fewer installer hands needed to get batteries hooked up and commissioned. It’s still a gray box — but the EP Cube’s metallic tint makes this ESS attractive enough to display outside anyone’s home.
One stubborn roadblock for solar installers looking to expand into new geographic areas is the amount of variation in permitting and design requirements in local building departments. It can take time and resources to learn each department’s intricacies — with inevitable delays if there are errors on permitting documents.
Solar software companies continuously attempt to reduce these soft costs that hurt the bottom line of solar installers big and small. One provider has created a marketplace to connect solar companies with design and engineering firms across the country that already have experience with the nuances of local building departments.
"Having design expertise in all of those areas helps the installer to basically jump into it without having to
have extensive understanding of that side of it," said Matt Rea, VP of revenue operations at GreenLancer.
GreenLancer is a platform that allows installers to pay for permit drawings, interconnection applications and other documents from a network of design and engineering firms at prices standardized by the software company. GreenLancer's in-house support team assists throughout the process, serving as the facilitator between contractor and design firm and solving any issues that arise in the process.
Some contractors use GreenLancer as their entire design and engineering branch. Others use it as an overflow — they have an in-house design team, but need some help during the busy season.
"With the ebbs and flows of the solar industry, there are certain times
where they need to tap our shoulder and say, 'Hey, we need to send you some projects.' We're happy to fill that gap," Rea said.
Moving forward, GreenLancer plans to expand into field services too — not only connecting installers to design firms, but also connecting project owners with installers if they want to add batteries to an existing project or need O&M assistance.
"That is really the vision — an installer can come to us and get this design and engineering work done, but also they can look on our platform for work," Rea said.
In this increasingly digital age, online marketplaces like GreenLancer help installers fill gaps in design and engineering and grow without adding new departments. SPW
One of the highest barriers to deploying single-axis solar trackers has been hilly terrain. Hiring a civil engineering service to grade land and produce a flat worksite can significantly increase the cost of a solar project. However, this was necessary to allow the driving mechanisms on solar trackers to rotate panel rows that previously could not compensate for undulating land. Now, that’s changing.
One manufacturer building single-axis solar trackers for these environments is Nevados Engineering. The company’s All Terrain Tracker (ATT) has a built-in slope tolerance up to 37% overall and can work with up to 26% slope change at each foundation. The key feature making this possible is an articulating bearing that installs atop each foundation, letting each bay of panels install at different slopes, all while maintaining panel row rotation.
The Nevados solution reduces grading costs for large-scale solar installations and opens the possibility of single-axis tracking in hillier regions that have previously been confined to fixed-tilt racking. In addition to its slope tolerance, the ATT underwent environmental testing on uneven terrain and is rated to perform in up to 80-mph winds, but will stow at 45 mph. Its row controls are wireless and self-powered. ATT can safely handle up to 50 psf snow loads, and the system has a 10-year extendable structural warranty and a five-year warranty on its drive and controls.
With new products like the ATT, single-axis solar trackers can continue to adapt to new topographies and grow in structural strength. SPW
•
Aluminum has treated the solar industry well. Its light weight and corrosion resistance has made it the dominant material choice for solar panel frames and accessory installation products. But in an era where people are paying closer attention to the carbon footprint of all materials, more sustainable framing and support options are gaining traction.
Steel is the first material to make some inroads. Risen Energy has introduced steel frame options for its Titan crystalline silicon solar panel line, and First Solar plans to use steel back rails on its new Series 7 thin-film modules. Both companies cite the smaller carbon footprint of steel as a primary reason for
switching from aluminum. According to Risen Energy, producing one tonne of aluminum exerts 11.2 tonnes of CO2 vs. only 1.8 tonnes of CO2 per one tonne of steel. And switching to steel affects the end-product very little — a steel-framed Titan panel is only 3 lbs heavier than an aluminum-framed model.
Solar panels using steel rather than aluminum get the added benefit of strength, which comes in handy on larger solar panels entering the utility-scale market. First Solar’s Series 7 module is longer and has a larger surface area than the Series 6 module, so the steel back support rails provide more structural support for the frameless Series 7 solar
panel. First Solar is also tapping into the local steel industry for an even smaller carbon footprint, and all of its new U.S. manufacturing plants will be entirely dedicated to the Series 7 module with no aluminum parts.
With the cost of the solar-generating portion of panels decreasing, frames and supports become the biggest cost on a finished solar module. Aluminum is on average 2.6-times more expensive than cold-rolled steel on the global markets, so cutting this big-ticket item out will make solar panels cheaper — and greener. SPW
Energy storage is becoming more accessible thanks to regional and federal incentives, but it's still not economically viable for all homeowners. New inverters give solaronly homeowners some benefits of backup energy with the ability to easily add a battery later on.
SMA America has included a "Secure Power Supply" feature in its Sunny Boy
inverters since 2015. These inverters include terminals for installers to add either a quad or dual electrical outlet underneath the unit or by the main critical load in the home. In the event of a daytime power outage, homeowners can plug their critical load, like a refrigerator, into that solar backup outlet and keep it running on up to 2 kW of power until the electric grid is fixed.
As the leader in solar charge controllers since 1993, SureSine is the inverter line our customers asked us to build. And our competitors will wish we hadn’t.
ureSine starts with the same industry-leading quality and performance standards of our charge controllers and adds a long list of advanced inverter features and technologies: full communications capabilities, wireless utility apps, seamless system integration, multiple AC wiring options, and more. We also built-in the safety, noise and performance standards required to achieve industry-leading NRTL conformance certifications—a unique advantage in this class of inverters.
With six power classes ranging from 150 to 2500 Watts offering models with 120, 127 or 230V output and 12, 24 or 48V DC input options, there’s a Morningstar SureSine perfect for your next project
Now, the company is changing names and adding new options to the system in its updated Sunny Boy Smart Energy inverters, which are expected to start shipping in mid-2023. That entry-level solar backup version is now called "Backup Secure," but the company is now offering two more robust backup options. The first is "Backup Select," which requires installation of an additional SMA accessory but can double the power capacity to almost 4 kW of backup energy without a battery when the sun is out. Backup Select inverters come with a dedicated electric panel with up to six breakers prewired, so when the power goes out during the day, those circuits are automatically backed up.
The most advanced iteration of the Sunny Boy inverter is "SMA Backup Home," which is a full backup solution paired with a battery to provide auxiliary power
in the day or night. This system can tie into the main electric panel of the home to back up numerous circuits.
SMA's tiered solutions are all based in its flagship Sunny Boy inverter, so homeowners have flexibility as demand, electric costs and incentives change over time.
"For a low-cost entry, they can have automatic backup during the day using clean energy, and if a year or two later their utility starts to offer incentives for adding storage, they can easily add a battery to that same platform without changing anything," said Rob Lamendola, product manager for home solutions at SMA America.
Future-proofing solar arrays is getting easier as hybrid inverters with built-in backup options become the norm. SPW
Out of the box, GenStar is an overachiever —an all-new design with “lithium DNA.” Standard features include advanced communications and control, powerful load control, and oversized PV array input capability. On top of that, our innovative ReadyRail architecture makes it easy and cost-effective to add a solar professional’s “wish list” of advanced features and control technologies, including battery metering/monitoring, lithium battery communications and control, signaling and advanced load control, and more. Our snap-in ReadyBlocks make GenStar fully futureproofed for evolving system needs.
With three models up to 100A maximum current GenStar’s ready to bring success your next critical project
Shown with optional ReadyBlocks installed
Snap-in ReadyBlocks enable advanced features to be built-in and fully integrated, instead of wired outside the system as accessories
Solar panels continue to increase efficiency, but along with that leap in generation comes an increase in size and weight. Manufacturers producing complementary technologies must adapt to these new dimensions and outputs. For one, racking and mounts must be fabricated with greater consideration to keep these large-format panels in place. But the ones feeling the greatest impact of heavier panels are solar installers themselves — especially contractors working on rooftops, hauling modules up ladders.
Solmetric is known for producing shade analysis and other field solar array testing equipment, and now the company has developed a pulley system that attaches to ladders to bring panels to the roof. The Module Lift is designed to work with fiberglass ladders, a common and necessary tool for residential rooftop solar installation. A pulley is attached to the top of the ladder and a patented hook latches onto the solar panel’s frame. The operator pulls the rope and hoists the panel up the ladder along a ramp that prevents the panel from colliding with anything along the way. A brake stops any backward motion as the panel is lifted to the roof.
For solar installers working at heights, there are safety measures to mitigate worksite accidents, like wearing protective equipment and anchoring to the roof surface to prevent falls. But there are always risks involved with climbing a ladder. Solar panels have never been light, but they can now weigh upwards of 50 lbs. A tool like Module Lift reduces the risk of working at heights with heavy materials and gives residential module makers a bit more freedom to continue to increase the size of panels. SPW
With 1 person and 30 minutes on-site, Scanifly equips your entire team with a photorealistic 3D model and all the data they need to plan and design every project. 98% of contractors go on-site before install - why not make it your only visit?
Striking the right balance between risks and rewards lies at the heart of solar success. Ideal sites with flat, soft terrain come at a price premium, while rocky, sloping land can offer discounted leases and higher margins — but at a price of time and development complexity.
EPCs and developers, especially in the Northeast, are constantly juggling complex ground-mount construction risks that can easily derail margins and project schedules. Whether it’s punishing winds, heavy snow loads, frost heave or extended mud seasons, managing Northeastern environments can be tough. Undulating topography doesn’t help, with rock-strewn hills posing ongoing threats of refusals.
For PV success in the region, consider these actionable strategies to minimize risks, keep projects moving at a good clip and safeguard margins for the strongest possible returns.
risk
Refusals are often the biggest unknown factor that can turn a good project bad. They pose a threat for obvious reasons: You don’t see them coming.
There is a host of testing to quantify and measure a site’s refusal risk, starting with geotech reports and pull testing. If the site has a constant ledge, refusals are to be expected. Lands with
predominantly cobbled soil contain rocks of various sizes and require more testing to help make a foundation choice between driven piles and ground screws.
Five tests can help guide the right foundation decision. While not all tests are required for every site, consider performing thorough testing on difficult sites to better predict issues before installation.
• Pull test and geotech report: Pull tests are done with screws and piles at various locations throughout a site. To prepare a geotech report,
soil samples are analyzed to reveal the site’s overall properties and glean insights about potential refusals.
• Compression testing: A compressive load is applied to various locations throughout the site to determine how the soil responds, particularly to heavy snow loads.
• Pull-out testing: Also known as tension testing, this helps assess the foundation’s anchorage or pull-out capacity, which is particularly helpful in regions that experience frost heave.
Below is a portion of Sungrow’s Solar Spotlight podcast with Solar Power World, but be sure to listen to the full episode on your favorite podcast app.
What is the footprint of the new SG4400UDMV station and what does it include?
We have been able to stay basically with the same footprint as we’ve had in previous generations over the last five, six years. So it’s a standard shipping container format. It’s 8 ft wide by 20 ft long. Its height is a standard format, so it’s 9 ft 6 in. tall. Basically, we’ve been able to increase the power with this new model to 4,400 kVA vs. the old 3,600 kVA, so a 20% increase in this same footprint.
The unit is a complete skid which it includes a medium-voltage transformer for connection to 35.5 kV, as well as the power conversion system — the inverter. And we also have an auxiliary power unit, which could either be a 5 kVA or a
40 kVA optional unit depending on what you power as far as trackers and weather station, switches, etc.
So, the new Sungrow inverter is “modular." Can you explain this further?
Traditionally, our inverters have been a single large inverter, which also makes it somewhat sensitive to in case you have an internal fault. You basically would lose that whole complete unit. What we have done now in this latest generation is we have split the unit up into four identical 1.1 kVA modules. So in total 4,400 V. But what this gives us is basically partial redundancy, so in case, for example, you have a single cooling fan fault, in the whole unit it would take down the complete 3.6 MW. In this case, you would basically just lose 25% or just 1.1 MW.
That is an improvement for the reliability and the uptime on the site. We also have the option to size the system a little bit di erent. We have the option now for a three-module unit. That would basically be a 3.3-MW system, which could be useful in certain corner cases.
Also, with four independent units, we have four MPPTs. We have a single MPPT, or maximum power point tracker, in the past unit, and the advantage of having more of these is that you can have potentially uneven terrain, where you know there is some shading and
some things like that. You can further optimize it now when you have multiple MPPTs.
Are there any performance di erences in the SG4400 when compared to previous inverters? We have improved the processing power. So we basically have a more powerful CPU in the new unit. This will lead to an increase in performance when it comes to response time. For example, reactive response time is less than 20 milliseconds or simply almost a single-cycle response compared to multiple cycles in past generations of product. So that whole area of improved power support and grid support functionality is something that has been improved. It also comes with direct compliance with the IEEE 15472018. It’s also prepared for the new IEEE standards that are coming out, which is the IEEE 2800.
Sungrow describes the new SG4400 inverter as having easier O&M considerations. We talked earlier about the modular approach. This doesn’t only go for the main inverter itself, but also internally in each section more modularity has been achieved. What this means is that when you remove, for example you have a semiconductor fault, you can remove that whole package and it is just basically a unit you remove and slide it out. Or if you have a fan issue, you replace the full cooling fan package. So there’s no need to go in individually and do a certain part. We’ve basically made it sections of power parts, which will lead to faster replacement and also you don’t need so much training to replace these as they are basically big chunks or sections you slide out and replace.
US.SUNGROWPOWER.COM
• Lateral load testing: foundation’s lateral capacity is critical for sites that experience high winds.
• Refusal testing: A geotech report limits insights only to the three or four areas assessed across a site, leaving room for risk during installation, especially on larger sites. Instead, refusal testing at the site’s most challenging location — sinking a foundation to its refusal limit — can better predict issues that may arise.
When evaluating a challenging site, pre-drilling the foundations can offer a risk-free solution. This is especially relevant when facing end-of-year schedule pressures. Contractors should talk to the racking partner about pre-drilling for ground screws as well as driven piles to ensure projects stay on track.
In cases where larger rocks and boulders impinge on a site’s design, consider adopting a novel approach: a hybrid foundation model which combines a mix of screws and piles. Piles can be used in softer soil while ground screws can eliminate refusal risks on the site’s rockier areas. While this may add some complexity in the project’s testing and design stages, a hybrid model offers substantial advantages during installation — the blend leverages the cost benefits of driven piles while taking advantage of the risk mitigations inherent to using screw foundations. The goal is to optimize each unique site’s profile to formulate the winning risk/ reward formula. Consider a partner that can offer both options and is well-versed in such hybrid foundation systems.
Racking structures built on slopes require additional adjustability to account for the undulating terrain. For example, when installing on a hard, straight ledge, it takes two to three minutes longer per foundation than installation on a
soft site. With slopes of 30 to 36%, particularly in high snow areas, the installation process is slower, too. When evaluating slope options, look for fixed and singleaxis tracking solutions with high slope tolerances to reduce construction risks; the highest fixed tolerance we have seen on the market offers 36% in all directions. The same consideration goes for trackers. Some systems are designed specifically for arduous soils and undulating terrain and can be used interchangeably with different foundation options. Flexible trackers with slope tolerances up to 20% north-south can help account for misalignments in the field. Look for systems that allow for east-west and vertical adjustment to minimize land grading and other civil work and keep construction costs down and schedules tight.
If you are considering ground screws or a combination of screws and piles, look for adaptable racking that can be used seamlessly with both.
Northeast construction risk No. 3: Weather Although not a construction risk per se, weather factors are key to ensuring system performance and must be thoroughly evaluated in the design phase. Local codes for managing snow, wind and frost heave can guide design parameters and component selection.
• Snow: Racking must be able to withstand and shed heavy snow loads. Building codes written for roofs tend to ignore solar projects. Snow shed from a solar module only has about 3 ft in which to accumulate, while roofs can slough off three-times as much snow load. But adding height to the module forces crews to do more awkward, elevated construction work. Additionally, to bear additional snow load on the modules, purlins have to be bigger or spans smaller. Racking partners should conduct robust load testing with artificial snow in the winter or tons of bricks in warmer months.
• Wind: This is a key consideration on the coast and along larger inland lakes, where hurricane-force gales often blow through. Assess the varying angles of force possible on the project site and be certain that designers have done thorough wind tunnel testing to account for these stresses. Some racking manufacturers use advanced software to simulate the most costeffective design for a site’s unique wind profile.
• Frost heave: Northern latitude installers know firsthand the devastating impact frost heave can have on a project’s long-term LCOE. Remediating heaved foundations after installation is costly and can destroy
Technology evolves quickly. Keep up with CPS America 250/275kW 3-phase string inverters designed to work with solar sites from 2MW to 2GW.
Significant design flexibility for solar plants of all sizes
More granular data analytics and monitoring
Available now, without the long lead time
When maintenance is required, only 275kW is impacted versus 5MW, minimizing harvest loss. Get back up and running quickly with service performed by local electricians instead of waiting for highly specialized manufacturer’s technicians.
Welcome to a new era in solar with CPS America string inverters. www.chintpowersystems.com
the project’s overall returns. Ground screws offer proven reliability against frost heave. Because their threads are embedded below the frost line depth, ground screws are most effective at resisting the upward force of ice lenses. Their smaller diameter reduces frost heave forces, while the screw’s threaded portion mobilizes significantly more tension against heaving than a driven pile.
Ultimately, developers and EPCs have much to gain from integrated partners ready to handle the entire scope from foundation and racking design to manufacturing, installation and electric BOS. Opt for manufacturers that self-perform the entire build with their own experienced installers and specialized equipment. Pick a partner that will absorb refusal risks on your behalf. Ultimately, clear the path to project success with a team offering proven experience delivering results in the challenging and unpredictable Northeast. SPW
www.socomec.us
As a member of Socomec Group, Continental Control Systems designs and manufactures metering devices, current transformers and custom energy measurement. Socomec and CCS offer a wide range of low-voltage electrical equipment designed and suitable for solar applications, including power metering & monitoring, power switching and energy storage.
Discover
As the demand for solar systems explodes across the country, so does the need for technicians who can troubleshoot PV systems efficiently and effectively.
Solar system troubleshooting typically focuses on four parts of the system: PV panels, loads, inverters and combiner boxes. Here is a checklist for locating and addressing common problems in those areas.
Before you begin troubleshooting, check the output of the entire system at the metering system or inverter, and record the inverter’s input voltage and current level from the array. One
of two conditions is the most likely: either the entire PV system, or a portion of it, is down or not producing power (possibly a problem with the inverter), or the PV system output is less than expected (could be an issue with one of the arrays or modules).
• Trace out the individual branch wiring backward from the concentrator. Check the entire system visually for any obvious damage or accidental disconnections. Once you find the failed module or array, check all wires, switches, fuses and circuit breakers. Replace blown fuses. Reset the breakers and switches. Watch for loose connections between the
modules and replace or clean broken wires and loose or dirty connections.
• Check the combiner box. This is a good place to troubleshoot the system, since the individual wires from the modules come back to it. Each module may have a fuse that you should check with your clamp meter.
• Watch for low voltage and check wiring connections. If a module’s output is too low, it may mean that an individual section of cells is bad.
Trace these through the wires, the connections, or potential ground fault issues until you find the problem.
• Test the open circuit voltage (Voc). If the polarity is reversed, it may mean that other circuits in the combiner
box are unintentionally connected in series, resulting in voltages over the maximum inverter input voltage.
• Inspect the modules for obstructions. Although PV modules are usually designed to be maintenance-free for years, they may still need to be cleaned. Contaminants like dirt, pollen or dust, or obstructions like shade on the modules themselves can cause reduced output.
The PV system is used to operate electrical loads, so any problems with the loads will affect the PV system as well.
• Measure voltage on the solar array at the combiner box, load switches, fuses and breakers to see if the proper voltage is present at the load’s connections.
• Check the fuses and circuit breakers. If you find blown fuses or tripped breakers, locate the cause and fix it, or replace the faulty component.
• Check for and repair any ground faults. If any fuses or breakers are blown, there’s a short that you need to locate and repair.
• Check for broken wires and loose connections. Replace any broken or damaged wiring and clean all dirty connections.
The inverter converts DC power coming from the solar system into AC power for use in a building or connected to the grid, and a failure there can cause problems. If the inverter isn’t producing the right amount of power, it may have a blown fuse, a tripped breaker or broken wires.
• First, check and record the inverter’s operating DC input voltage and current level, and then check the inverter’s output voltage and current levels on the AC side. Many systems have a display that indicates current inverter and system performance.
If your meter produces a true-RMS reading, you can use the voltage and current to measure and record the kilowatt output. If possible, use the inverter display to show the current total kilowatt-hours. You can then record that value and compare it to the one measured during the last inspection.
• Use your clamp meter to measure the output/AC side of the inverter. Confirm that the output voltage and frequency is correct for the demand.
• The inverter may be tied into the local utility. As the AC current output from the inverter fluctuates with the level of solar input on the array, the inverter maintains the correct output voltage and phase to the utility. Any voltage problems from the utility may cause the inverter to shut down. In that event, contact the utility for repairs.
Amperage measurements and calculations are crucial to establishing whether the PV arrays are operating correctly.
• Confirm that all wiring connections are tight. A loose connection could cause fluctuating voltage or current output to the inverter.
• Validate all fuses in the box. Check that they have correct resistance and continuity.
• Make your calculations. Measure and calculate incoming current and
voltage from the arrays and validate the combined current and voltage output to the inverter. Measuring current on individual arrays or combining current measurements will help you determine if a cell has malfunctioned.
Troubleshooting PV systems efficiently is about being methodical, thorough and using tools that are rated for the job. As solar systems and loads become bigger and more complex, it’s also about safety. The best all-around tool for working in most areas of a solar installation today is a CAT III 1,500-V rated AC/DC clamp meter with features — such as DC power, audio polarity, visual continuity and a thinner jaw design for tight spaces — that are tailor-made for test and measurement in solar PV applications. SPW
Workplace safety is important in any field. Knowing how to use tools, equipment and machinery properly, as well as suiting up in all the necessary safety gear to perform your job can keep you from damaging equipment or getting seriously injured. This is especially true when dealing with the electrical grid, such as when installing and maintaining PV systems. When designing, installing and maintaining PV systems, workers should pay close attention to strict guidelines and directions to help reduce or eliminate installation errors, electrical
errors and injuries. Current coming from these systems can sometimes be erratic, and dangers can be hidden in things like ground faults or wiring. Knowing best practices and what to look for will help mitigate risk.
Workers in the solar energy industry are exposed to a multitude of serious hazards while working with PV systems. These hazards include arc flash, which is when there is a high-power discharge of electricity between two or more conductors that can cause burns or even
death; as well as insulation deterioration that can cause a fire; electric shock from a system’s loose wiring or tools and wiring that are not grounded or double insulated; thermal burns that can cause serious injury or death; as well as falls.
When it comes to solar electric systems, there are two sources of electricity: the utility and the solar electric system. Simply turning off a main breaker doesn’t stop a solar electric system from producing power. Modules always have some sort of voltage, even in low light. If handled improperly, it can lead to a shock or arc flash, which could cause serious injury or death.
In PV systems, most issues arise in the combiner box, PV source and output circuit conductors, and the equipment grounding conductor. But issues can be avoided if workers take the time to install and maintain them properly. After installation, at least bi-annual maintenance is needed, especially if the modules are tilted. When modules are moved out of alignment due to natural events like weather and damage from human or animal contact, the efficiency of the string/array is affected. Misalignment can lead to adverse production in the array regarding maximum power delivery to the grid. Alignment must be corrected with an irradiance tool like the Megger PVM210 in order to bring the
module back into maximum efficiency alignment. There are monitoring apps that can help owners track the amount of solar energy the modules are producing. If there seems to be a dip in production, it’s either time to clean the modules or look further to see if there are other issues going on.
Identify a problem before it happens O&M technicians can use a variety of tools to investigate problems with an array. These include a digital clamp meter, irradiance sensor, insulation resistance tester, as well as a thermal camera. Each tool has a specific job in identifying areas of concern, helping to correct the issue and keeping workers safe.
A digital clamp meter measures the voltage output of PV modules to verify the performance of a PV array. It also provides solar technicians the ability to test higher voltages and current values with greater flexibility using a single tool. By using this tool, technicians can measure the intensity of the sunlight striking the arrays. This measurement is very important when validating the performance of a PV system.
Irradiance
This handheld tool measures the intensity of the sunlight striking an array. Measuring solar irradiance provides knowledge in making important decisions regarding future energy yield, efficiency, performance and maintenance.
An insulation resistance tester helps to perform insulation resistance testing during startup and maintenance activities to verify the integrity of conductors associated with a photovoltaic array. This tool can be used in residential, commercial and industrial rooftops, as well as large-scale ground-mount solar applications.
Periodic testing of the electrical cabling and components associated with solar PV systems helps to indicate the health of the system, identify potential issues early, ensure the safe operation of the system and reduce the risk of fire associated with potential or existing electrical faults.
A thermal camera helps to quickly and safely assess the PV modules as well as the junction boxes, combiner boxes and electrical connections for abnormal heat with a quick scan. The camera is used to locate bad cells, wiring or
diodes. Each of these plays an important role in having the PV array run properly.
Cells are connected in series. When one cell in the series does not work, no current passes through that entire series, resulting in no electricity being generated. If an array is wired improperly or has failed, it might not deliver the appropriate voltage and fail to power up electrical units or result in the battery bank’s failure to charge fully. If a diode has gone bad, users will notice a drop in output.
Megger offers a Solar Test Kit with each of these tools to make a technician’s job easier.
Understanding PV systems, the dangers that lurk and how to safely test and maintain them is key in protecting workers and end users alike. SPW
There’s an anecdote that I share with nearly every installer because it illustrates the challenges facing smaller solar businesses. The story goes like this:
A homeowner explained that she had two homes, both with solar. With her first home, she installed with Tesla and had a horrible experience. For her second home, she decided to try a local solar company and had a great experience. Unfortunately, she couldn’t remember the name of her second installer.
This anecdote illustrates the sheer power of a brand name, and when it
comes to solar, there’s no stronger name than Tesla. There’s a cache that has been built by its EVs and, of course, the recognition of its CEO, Elon Musk.
So how can your solar business compete with Tesla, Sunrun or any big national player? Below are six concrete ways to put your business on top and ensure your customers always remember your company name.
Instead of thinking of Tesla or Sunrun as competitors, you need to go toe-to-
toe with, and take advantage of their marketing efforts. Companies that are big and expanding into new regions are spending astronomical amounts of money to penetrate this new market. This means that, really, they’re doing the work of market education for you.
Use their marketing and sales efforts as a springboard for your own initiatives. Start thinking about your sales process as two distinct phases: There’s convincing people to go solar, which is where Tesla can do the heavy lifting. Then there’s convincing people to go solar with you.
The latter is where you should focus your marketing efforts.
People shop around for solar these days. It’s in the comparison stage where your business can both be discovered and truly shine. Instead of trying to outshine Tesla’s brand — which is almost impossible — focus on efforts that will help you win in the proposal stage.
Make yourself easy to find on Google under the search term “solar installers near me.” Highlight your differentiators and tighten up your proposal process. These efforts are all much more likely to yield noticeable results to help you win against national players.
Embrace the ‘Buy Local’ brand
Did you know that 93% of consumers prefer buying local? Use this to your solar company’s advantage. The buy local movement offers an easy network for you to tap into and rally support for your business over bigger brands like Tesla and Sunrun.
Differentiate yourself as a local player by emphasizing your community roots. On your website, share your founding story and talk about your involvement in the local community. Participate in events that are iconic in your community — from sponsoring local sporting events and exhibiting at fairs or events.
People are drawn to solar because it makes them feel like they’re a part of something bigger. You can affirm that feeling by reminding them that they’re a part of a local community of forward-thinking energy consumers.
Use your local knowledge
While you can’t outspend Tesla or Sunrun, you can be more strategic than them. I guarantee that you’re more in tune with what happens in your local market than a national player. Tesla’s sales and marketing may be well-financed, but it’s generic.
Adapt your messaging and sales practices to match your customers’ unique likes and dislikes that are particular to the regional culture. For example, Austin company
Freedom Solar Power hired Willie Nelson for its marketing to appeal to its customer base in Texas.
You should also use your understanding of your region to give yourself a leg-up on other fronts. You probably know the right people in the permit and inspection office to give a little nudge to an application ahead of the opportunistic visitors. Keep a constant eye on the local hiring market, so you can scale up as needed.
Tesla must acquire local knowledge — you have it built into your business.
Be more nimble Tesla is a giant corporation. No matter how whimsical its leader Elon Musk may seem on Twitter, to expand into new regions, they need an aligned growth and marketing strategy. This takes time — often a lot of it. The same goes for Sunrun. With over 11,000 employees, nothing goes quickly.
In the same way that you can use local knowledge to get ahead of national installers, you can also use speed as a weapon. Be nimbler across every department and at every stage of the solar process. From delivering proposals on tighter timelines to being faster to
respond to customers, you should be able to accommodate a reasonable customer request without going through tons of red tape. There’s a reason Tesla has bad reviews.
Solar installation is never a cookiecutter process (as much as we wish it was), and the big companies will be much slower at responding to changing conditions.
Earlier this summer, Tesla quietly cut their solar roof referral program from $500 to $300 per referred installation. If you have
a more competitive referral program, bring it up as a differentiator.
Referral programs also work best when there’s a high density of customers, an advantage local companies will have over larger national installers. When a prospect hears about your company multiple times from the people around them, they’ll trust you more.
You should also use your customers as referrals for whenever their friends or neighbors get a quote from Tesla. Our customer Lighthouse Solar won a homeowner’s business specifically because Tesla, then Solar City, originally knocked on the customer’s door. The Tesla prospect had a happy Lighthouse customer in their network, and they made the decision to trust their friend’s referral and go with Lighthouse instead.
Big companies like Tesla like to build their own software, keeping everything from proposal and site design to customer experience in-house. To do this, they employ an army of product managers, UX researchers, designers and software developers — not to mention all the managers needed to handle that employee base.
However, for small to midsize solar companies, building instead of buying software is a mistake. Thirdparty software companies are more effective and efficient than anything you could build in-house. They’re also always improving their product based on how the solar landscape is evolving. These companies focus 24/7 on the niche area that they service so you can focus on what you do best: Selling and installing more solar.
Finally, these software companies will often have a branded app and a digital experience that delivers on the expectations that your customers are bringing to their solar journey. For example, my company Bodhi has done extensive research on what the ideal post-install experience is for homeowners so that solar businesses can generate more reviews and referrals. Take advantage of these kinds of platforms so that you can meet your customers’ digital expectations.
By following these six tips, you can ensure that your business gets the customer consideration it deserves. More and more homeowners are choosing to go solar — now is your chance to beat out the competition and create a community of loyal customers who never forget your name. SPW
In competitive residential solar markets, a solar sales and installation company competes with an average of 20 solar businesses for customers, referrals and market share. For many companies, the pressure to stay competitive has emphasized a new need to reduce system costs.
While overall system costs in the United States have declined by 25% since 2014 largely due to technology advancements, customer acquisition and overhead costs have increased by 31% during the same time. According to SEIA, soft costs in the United States represent 60 to 70% of the total cost of residential-scale solar PV systems.
This disparity between rapidly falling system hard costs and the
generally increasing percentage of soft costs point to the importance and opportunity of soft cost reductions.
Soft costs represent the costs outside of hardware equipment associated with selling, designing and installing a solar PV system – including customer acquisition, design, permitting, installation, inspection, interconnection, business overhead and profit.
Overhead (general and administrative) and profit make up a project’s largest expense, representing 21% of the total system cost. Sales and marketing come in a close second with 18% of the total system cost.
Rather than sacrificing profit margins to narrow costs, companies have an opportunity to evaluate their sales and
operations workflow to first pinpoint inefficiencies and then identify high-impact solutions to streamline operations. Customer acquisition and related sales and design activities, in particular, are a great place to start.
Prioritize accurate site assessment data
Site assessment data is foundational to the solar sales and installations process. Roof size, usable square footage and sun exposure are all data points used throughout a project’s sales, planning, installation and close-out phases.
Inaccurate site measurements result in less profitable jobs in the best case, and canceled contracts and lost referrals in the worst.
On the flip side, high-quality site measurements result in a quick sales cycle from lead through installation, which speeds payment and cash flow.
Fortunately, new advancements in remote measurement allow solar companies to bypass inefficient and error-prone site visits to measure and record roof dimensions, azimuth, pitch and localized shading at a given site. Additionally, some remote measurement technology, such as those that derive from aerial imagery, captures thousands of measurement points. In comparison, the same rooftop measured manually with a hand-held device captures perhaps only a few dozen values.
Traditional solar sales processes begin with sales representatives using preliminary system designs from a do-it-yourself software to develop an initial proposal that estimates how many solar modules will fit on various roof facets. In this preliminary design process, many contractors purposefully underutilize roof space to avoid issues at final design or installation. (Under-sizing a solar PV system may help mitigate risk but doing so adds to soft costs, leaves money on the table for the contractor and negatively impacts return on investment for the homeowner.)
Once the contract is signed, a technician then performs a site visit to collect the necessary measurements and information to validate a final system. Unfortunately, the chance for human error when using a hand-held device to log measurements is high and can lead to costly mistakes down the line.
With remote measurement technology, however, virtual site assessments employ satellite or aerial imagery to capture data – including all roof measurements, pitch angles and even obstacles such as plumbing vents and skylights – to output a detailed 2D or 3D roof model. Energy production estimates and visual rooftop solar layouts can be developed before any direct customer engagement. Not only does this prepare the salespeople for a well-informed first communication with a potential customer, it also optimizes outbound sales efforts by prioritizing homes with favorable roof facets and solar access values in the sales queue.
Coupling high-accuracy remote measurement and high-resolution imagery with solar design and layout software tools efficiently delivers installation-ready designs on the front end of the sales cycle, eliminating the need Pexels
As North America’s most diversified steel and steel products company, Nucor is committed to delivering world-class reliability and results to your solar projects. We partner with you to develop innovative solutions that cost less, last longer, and simplify installation.
Let’s work together to make your next project a success.
for “preliminary” designs altogether. These designs are also optimized to fit more modules on the average rooftop and maximize annual solar energy production.
of an optimized workflow Inefficiencies in traditional solar sales and operation workflows often begin with inaccurate roof measurements that lead to overly conservative designs, excessive truck rolls and change orders, and result in longer timelines that ultimately dig into a project’s profitability. There’s also a greater risk of canceled contracts, unhappy customers and lost referrals.
Fortunately, implementing highaccuracy data tools that facilitate virtual site assessments and installationready designs at the proposal stage offers solar companies significant opportunities to streamline workflow and gain a competitive advantage and market share within their service area. By optimizing available roof space, shortening project timelines, reducing labor and the opportunity for human error, companies can increase profits, customer satisfaction and their ability to scale.
Competitive and growing solar installers that target customer acquisition costs through virtual assessments and installation-ready designs on the front end of a project will significantly improve workflow efficiencies that in turn support better business processes across the board. Changes such as these, which accelerate sale-to-install time and optimize system performance, are ultimately what will be needed to scale the solar industry to achieve global clean energy goals. SPW
Advanced Green Technologies credits good design and preventative maintenance as keys to success.
BY KELLY PICKEREL • EDITOR IN CHIEF • SOLAR POWER WORLDHurricane Ian, the fifth-strongest hurricane on record to make landfall in the contiguous United States, barreled across Florida in late September 2022. The Category 4 storm hit Fort Myers, Florida, particularly hard, contributing to over 125 deaths, mostly due to prolonged flooding.
Millions were without power, but a bright point came from Babcock Ranch, a 100% solar powered community outside Fort Myers that survived the hurricane mostly unscathed. The neighborhood made national news and showcased the strength and success of well-engineered solar projects when tested in the middle of an incredible natural catastrophe.
More solar projects successfully came out the other side of the storm after experiencing 155-mph winds. Florida solar company Advanced Green Technologies has been assessing the damage (if any) to its portfolio of projects in the Fort Myers area, and VP Clint Sockman talked to Solar Power World about what the team has seen.
Two AGT projects described here did experience some damage. Mercola Market in Cape Coral is a three-story health food store and office building that has a flat-roof array and a solar carport. The carport had no visible damage, but one corner of the flat-roof project had panel uplift. J.J. Taylor Distributing in
Fort Myers is a beverage distribution warehouse that also had panel and rail uplift on one corner of its flat-roof array. The O&M team was able to isolate the damaged portions to keep the rest of the arrays producing power.
SPW: As a solar installer and postconstruction maintenance provider, how do you react when extreme weather is announced in the area?
Stockman: We try to get an email out ahead of the storm and let people know it’s coming. It could be prudent to go ahead and power the system down and ride it out, depending on the severity of the storm. We suggest checking
THE SOLAR CARPORT market is expanding, meaning this high-profile racking is entering new territories. Canopies are viable structures for energy resiliency; they can deploy atop parking lots and commercial garages and are more frequently meeting financing requirements for power purchase agreements. We’re joined by Finn Findley, CEO, and Danny Kraft, director of customer development, at Quest Renewables, a commercial and utility racking company specializing in carports. Finn and Danny are here to discuss how the market is changing for solar canopy systems and how EPCs and developers can anticipate those changes and include carports in their portfolios.
Below is a portion of Quest Renewables’ Solar Spotlight podcast with Solar Power World, but be sure to listen to the full episode on your favorite podcast app.
How have you all seen the solar carport market change over the past several years?
FF: There’s no doubt the canopy market is growing really quickly, and the growth is really durable, meaning there’s a lot of tailwind supporting it. So even when you come up with the big headwind we did in the last year, with the supply chain challenges that a ected everybody, we still had our biggest year. We built our biggest project.
On the other hand, folks in the industry know the growth is geographically inconsistent, meaning one market is doing a lot of carports and another is not. That’s at least how I see it.
DK: I agree that it’s geographically inconsistent. A lot of that is policy-driven, weather-driven, customer-driven, really. The Northeast and the Southwest, opposite ends of the United States, the lower 48 seem to be the most advanced when it comes to canopies and it’s the sunny Southwest and it’s the snowy Northeast, and a lot of that being policy driven.
What causes the market to be geographically inconsistent?
DK: It really seems to be feast or famine and there’s really three factors that we look at to assess if there’s an opportunity and what drives this inconsistency. One of them being the cost of energy. Where energy is expensive, companies and consumers in general are looking to reduce their power costs, so they go
to solar largely based on what the incentives are. Massachusetts with the SMART program, having carport incentives; the new IRA is going to help the broader U.S., I believe. But it’s cost of energy, it’s policy, wind and snow conditions. When you get into the Midwest, you’re looking at 50-lb snow, you’re looking at some significant steel costs to hold up panels.
Another driver is really land use, which a lot of times drives policy, where states and areas don’t want to take agricultural land out of use or chop down woods to support panels. So you see developers vying for space where rooftops are unavailable and there’s a lot of impervious surface that’s already been taken out of its natural condition, it’s a perfect situation for a canopy. You don’t really see solar canopies outside of an urban environment. So, I think those are the biggest drivers for geographical inconsistencies.
In what ways can EPCs predict which markets are likely to develop favorable incentives?
FF: It seems like they’re really “willy-nilly.”
But there is some rationale as to where the incentives take place, and I think the key is really to understand the perspective of the utilities. If we change our mindset about how we can work in conjunction with the utilities, it
really helps us get into their minds and think about where do carports help them? And carports help them in places where there’s, like Danny said, a shortage of land, and also where the grid isn’t particularly strong. So if you look at places like that, the utility can really use some help with distributed generation.
What can EPCs do if they are in a less-than-ideal market?
DK: Whether you’re in a less-than-ideal or ideal market, where we see EPCs and developers strike success is when they have customer focused approach. They’re working very closely with their customer who has renewable energy targets to begin with. Sometimes it could be a third-generation business owner who wants to take their company into the future with renewables through canopies, roof mounted solar, lighting, etc. SPW
drains and other good practices if it’s a rooftop system to make sure nothing’s clogged. We’ll check in with the people who were under the direct path.
Two of our larger C&I projects took a direct hit — Mercola Market and J.J. Taylor Distributing. We emailed and called both of them. As soon as NOAA starts posting their satellite or aerial imagery, which they were very quick this year, we can start assessing damage virtually, literally the next day.
Once the storm passes, what do you do with damaged solar arrays under AGT’s care?
The first order of business is to always protect life safety and the safety of the building. We get up there and if there is
any damage, we get things safe for everyday operation. Then we look into final repairs and getting it put back together, if needed. If the asset is fine, you still need to look at all your connections and terminations, inverters and enclosures. These events have an enormous amount of vibration. The carport at Mercola went unscathed — when you look at it, there’s nothing that happened. But as we started looking deeper, we had bolts that had vibrated loose and were clearly disengaged from their torque marks and mechanical settings. While they certainly took the punch, they couldn’t take it again if it wasn’t addressed.
While there were panels and rails damaged on the two flat-roof projects, I noticed that the roofing membrane itself had no damage. Commercial roofing will typically fail as a perimeter breach or a window being breached and causing negative pressure to blow up from inside the building. These two buildings didn’t have any breaches to the perimeter. The solar projects were designed to modern code, either MiamiDade or Florida code. We used enhanced fastening patterns and looked at the sheet metal details on the perimeters to prevent interior pressure failure.
A lot of the modern stuff that was designed to current building code fared pretty well. A lot of the more aged assets and at-risk assets really didn’t. The devil’s in the details. Good design typically will work — whether it’s roofing or solar.
J.J. Taylor was rebuilt from a prior catastrophe. It was new construction and the general contractor built [solar] and a Category 1 hurricane hit about four years ago and blew the entire thing off. We were hired to come in and rebuild. It performed obviously a lot better, but it still had that isolated corner pick up, and we lost about 40
modules out of a couple thousand. We’re looking at forensics on how those rooftop breaches happened. We don’t know if the prevailing winds were strongest from that corner, but it will be interesting to see.
The sections on the two arrays will be replaced. Both are minor in the grand scheme of the array. Most of the modules now are no longer commercially available, so that changes engineering. It’ll probably take a month or two to work through design and permitting. They’re both up and running at 90% capacity. We were able to simply take that inverter offline. The J.J. Taylor project was one inverter out of 30. That’s the great thing about redundant design and using modern string inverters. You’re able to take out
a small portion of the array and keep the asset up and producing energy.
PanelClaw performed very well. We used PanelClaw racking systems on both projects. We have a lot of faith in their wind tunnel testing and their panel qualification. A lot of people will design racking systems and not make sure that the module has the frame strength that correlates to the racking system. You can’t treat them as individual components, it has to be an integrated system. We’ve stressed that a lot in the last 10 years, being in Florida and exposed to high winds.
Beyond that, it’s just being prepared for the storm and going through your annual maintenance. Both of these systems are under a preventative maintenance agreement. Our techs come out pre-hurricane season every year to inspect all the bolts for proper torque settings, inspect all the enclosures, preemptively getting in front of this. We’re in Florida. We’re exposed to what would be considered severe wind several times a year. A 70-mph heavy thunderstorm may not cause blow-off or severe damage, but it does put stress on the array and can cause things to come loose. We’re really encouraging all our customers to look at preventative maintenance at least once a year. SPW
Shingled roofs are reliable and a roofing classic, but that doesn’t mean they are a flawless solution. Their installation allows for and often requires more roof penetrations compared to other roofing materials like tile or metal roofing. Despite all those nails and staples in the mix, shingles do their part in keeping the surfaces underneath them dry.
Solar mounting manufacturers often hear the question, “What about the roof warranty?” Most installers are just covering their bases, seeing what assurances they can get beyond their own quality of labor. What seems to trip everyone up is that most roof warranties are only an assurance for the quality of manufacturing; assurance that the product was manufactured to the standard the manufacturer intended. So where do the lines get blurred?
To provide insight into the issue, we gathered warranty documentation from the nation’s most popular shingle manufacturers. First, we will dive into common types of warranties.
Any supplier worth its salt will offer a manufacturing or product warranty, ideally for a period matching how long it’s been in business; anything longer and the warranty period length is speculation. Most solar mounting manufacturers offer a 25-year warranty on their mounting solutions — this means they will replace products with defects attributed to the manufacturing process for up to 25 years past the manufacturing date.
A service warranty is a different type of offering that covers forms of labor. Truck
rolls, crew size and subsequent warranty coverage are each a common component of service warranties. It’s rare to see a manufacturer offer a service warranty. That’s left to the secondary market full of insurance/solar warranty providers (like SolarInsure) that cover parts-and-labor on warranty claims.
Now we’ll run through some manufacturers alphabetically and break down their warranties. Anyone not listed either could not be reached, does not provide explicit documentation addressing the question or fell outside the scope of our search.
Atlas Roofing seems to be the first roofing company to address the issue of solar installations and roofing warranties. The company published an article in 2014 explaining how its warranty is impacted by solar installations.
Atlas recommended homeowners check with their home insurance providers to see if solar is covered, and for installers to offer a third-party warranty/insurance plan.
CertainTeed is the rare case that offers a combined manufacturing/service warranty — under the right conditions. Its warranty coverage is tied into its credentialed installer program by benefitting contractors with two levels of coverage. When installed by “Credentialed” or “Master Installers,” Certainteed’s warranty covers any manufacturing defects and defects in workmanship for 15 or 25 years respectively. This makes for a very flexible offering only if you are a credentialed installer.
GAF warranties will remain in place if a solar system is installed over its roofing products. GAF released a technical bulletin a few years ago detailing the coverage and its limitations: If you need to remove the solar system for GAF to inspect the defective shingles, that cost is not covered by its warranty.
Malarkey offers a straightforward breakdown of its manufacturing warranty in a handy technical bulletin. Solar installations are allowed on Malarkey roofing and do not void its manufacturer warranty. But the bulletin states that “damage resulting from installation of a solar/PV system does not constitute a manufacturing defect and is not covered by the warranty.”
Owens Corning’s warranty is simple — the shingle warranties remain in place even when a solar system is installed. That warranty only covers manufacturing defects in Owen Corning’s own products, and the standard warranty doesn’t cover other manufacturer’s products.
Like GAF, Owens will not cover the cost of removing a solar system to replace a defective roofing product covered by their standard warranty.
TAMKO doesn’t have any documentation addressing solar installation, but its technical team’s answer over a phone call was, “The roof warranty will remain intact” if PV is installed.
So, will your solar installation void the roof warranty? Most likely, no, but that warranty never protected you or the homeowner from anything other than a defective roof product. At the end of the day, manufacturing warranties are not nearly as important as the quality of your own labor.
If you come prepared for the roof, then you can increase your chances of getting it right the first time. Taking direction from manufacturers is key to successfully using their products and installing a cohesive solar system. If you think you’ve got a better method, then let them know so they can develop a better product or adjust their instructions using your field experience.
Other ways to plan for a successful installation are by taking advantage of innovative mounting solutions — solutions that work with the roof and not against it. QuickBOLT has produced minimally invasive mounting solutions for a decade, and most of our peers in the mounting industry now offer their own top-mounted solutions.
The last three years have seen a major boon to over-theshingle, top-mounted solar attachments which work to decrease the impact to the roofing materials beneath them. The fewer penetrations you make in the roof and the less you lift shingles, the better the roof integrity remains.
Someday soon we will witness the rapid decline of ripping up shingles, destroying the roof’s existing integrity and forcing installers to wonder with a pry bar in their hand, “Will this void the roof warranty?” SPW
Almost half of U.S. states have now adopted the 2020 National Electrical Code, which includes specific fire safety requirements for rooftop solar projects. If a fire should break out at a home or commercial building, the code ensures firefighters won't be harmed by an energized solar array on the rooftop.
Installers now have multiple options to satisfy this measure in the code, including the use of module-level rapid shutdown devices and PV Hazard Control systems — listed as UL 3741.
To achieve PV Hazard Control certification under UL 3741, products must pass a series of tests designed to simulate situations firefighters may encounter on a solar rooftop. The testing analyzes what happens when first responders fall on damaged solar panels while wearing typical protective gear. There’s no prescribed combination of solar products to satisfy this new rating; the merits of each submitted product or product combination are scrutinized during testing.
Rapid shutdown devices are also certified by UL, but most units can work with numerous string inverter brands. Small units are affixed to either one or two solar panels to reduce the voltage to 80 V within 30 seconds once the shutdown switch is activated at the inverter, which the codemaking body decided was a safe voltage for firefighters to work around.
An increasing number of manufacturers are bringing rapid shutdown devices to market, so installers now have multiple choices when it comes time to choose this small but important part of solar systems.
The main rapid shutdown devices on the market in 2022 include:
• APsmart package includes the rapid shutdown receiver and inverter-agnostic transmitter
• The rapid shutdown unit is small and can be buckled to the module frame or applied to module backsheet using adhesive
Our wide range of NEMA rated enclosures are built to protect your electronics in the harshest of conditions and look great doing it.
To learn more about our quality products visit integraenclosures.com
The compact design of WAGO’s TopJob® S Mini Rail-Mount Terminal Blocks makes them ideal for work in tight spaces. Various mounting and actuation variants are also available for maximum flexibility; allowing you to select terminal blocks based on your critical application needs. Thanks to the reliability of Spring Pressure Connection Technology, safely landing wires in the field is simple, and easy to service.
WAGO offers a full range terminal blocks and connection solutions to meet the requirements of residential, industrial, and utility grade solar energy applications
• Works well in bifacial applications because it doesn’t block the underside of the module
JMS-F
• SMA says the JMS-F device features up to 50% fewer internal components than alternatives, resulting in greater lifetime reliability
• Uses the existing DC lines between the inverter and PV array for power line communications
• Technical support available from SMA’s extensive O&M program
• Inverter-agnostic
TS4 rapid shutdown suite - Tigo Energy
• Tigo says its devices work with the largest network of inverters and module types
• Tigo works closely with many inverter partners to integrate its Rapid Shutdown System Transmitters into their inverters, which simplifies installation
• Tigo’s rapid shutdown suite gives customers the freedom to choose other features they need in modulelevel power electronics
• SolarEdge’s Power Optimizer is a DC/DC converter connected to each module with built-in SafeDC rapid shutdown feature
• SafeDC automatically reduces module voltage to a safe level whenever the inverter or grid power is shut down
• Only works with SolarEdge inverters
• IMO Automation’s FireRaptor is a solid-state switch that doesn’t require powerline communications
• Comes with a 20-year warranty and works with all inverter types
• FireRaptor can automatically shut down if the temperature sensor on the device detects a rise above programmed trigger level SPW
•
It’s easy to become an industry leader when you’re committed to designing and developing solar battery storage solutions equipped with groundbreaking innovations. Work with a solar battery supplier you can support and a partner that offers personalized OEM service, technical training, and 24/7 global support. That’s BSLBATT.
Test that PV systems are performing to their optimal power output as well as operating safely with the Fluke SMFT-1000 multifunction tester with I-V curve tracing. Designed for PV professionals that provide installation, commissioning and maintenance services to systems that operate at 1000 V DC or under, the SMFT-1000 provides a complete PV testing solution that conforms to IEC 62446-1 standards. While taking an I-V curve reading in the field, the SMFT1000 will display the curve as it loads in the test data in real time. This makes it easy to immediately confirm measurements without the use of a laptop or tablet. Through Fluke’s TruTest™ Software, measurement data from solar site installation and commissioning testing can be easily imported, organized and analyzed for effortless reporting.
The Fortress Power Guardian is a gateway device that connects Fortress Power Batteries to the cloud. Paired with the companion app, the Guardian will automatically discover connected Fortress Power batteries. This enables battery-level monitoring of key values such as State of Charge, Voltage, Current and Battery Temperature as well as faster, more accurate technical support. Remotely update battery firmware, submit support tickets, chat live with technical support, complete warranty submissions, and securely share installation and monitoring data directly with support engineers– right from the companion app.
FranklinWH is focused on energy management solutions providing safety, reliability and energy independence for homes. Franklin Home Power (FHP) is a wholehome energy management system integrating solar, battery, grid and generator power sources and managing them to optimize the safety, reliability and efficiency of home energy. The FHP is designed for simplicity and is easy to install, maintain and operate.
>> SOFTWARE
Solar installer, reduce your time on support phone calls with the Fronius Solar.SOS app, the online troubleshooting tool for Fronius installers.
(877) 376-6487 Fronius
Growatt provides the whole system solution of MIN 3000-11400TL-XH-US battery ready inverter and ARO lithium battery. MIN XH-US series is the most cutting-edge residential hybrid inverter integrated with smart EMS software, it can be used as a standard on grid PV inverter, and easily extend to an energy storage system by installing ARO extra battery pack. Combined with Growatt’s new 200A microgrid interconnection device SYN 200TL-XH-US, it supports whole home backup capacity with alternative port for generator and EV charger.
• Whole Home Backup and Partial Home Backup diverse options
• Support DC-Coupled and AC-Coupled energy storage systems
• Support 4 working modes to customize your energy management
• Integrate diesel generator to charge battery for optimal energy management
• LFP modular battery, capacity range from 6.6-19.8kWh
• Comply with UL1741SA/SB, CA Rule 21 & HECO
GROWATT USA INC
9227 Reseda Blvd. #435 Northridge, CA 91324.
www. growatt-america .com
>> STAGE COMPONENTS & EQUIPMENT
Integra Enclosures has you covered
From solar battery boxes in the west coast heat to remote monitoring in the snowy Midwest, Integra enclosures are built to handle it all. Our high-quality NEMA rated enclosures are trusted by OEMs around the world to protect sensitive electronics from all weather conditions. So what makes a box so special?
Quality materials: Integra uses impact and UV resistant polycarbonate to make enclosures that far outlast the competition.
Attention to detail: Each product is meticulously designed and tested for optimum performance. Plus, quality checks at every step of production means you’ll get the best enclosure. Every time.
Modification: Integra offers in house machining, printing and a wide range of accessories to meet your exact needs.
8989 Tyler Blvd. Mentor, OH 44060
www. integraenclosures .com • 440-269-4966
Inxeption Energy is proud to support reliable U.S. manufacturers, including Solar4America–America’s solution for quality, performance, and reliability. All Solar4America products are manufactured locally in the U.S. under the highest quality standards.
Introducing Solar4America 410W All-black Mono Perc Module
Solar4America’s 410W all-black mono perc module is known for world-class mono efficiency and can withstand high winds in areas such as Miami-Dade.
• 20.64% module efficiency
• 420W high power output
• Strong 40mm frame
• Wind and snow load of up to 5400PA
• Excellent Anti-PID performance
• Improved shading tolerance
• Certified for salt/ammonia corrosion resistance
For dependable products and reliable expertise, choose Inxeption to guide you through your next solar project and experience the American-made difference of Solar4America.
The CanDuit™ securement clamp by S-5! easily and affordably secures the PV system’s home run conduit and other wire management to the metal roof in combination with any S-5! clamp, bracket or the GripperFix® Strut to create on-site wire chases.
Corrosion resistant CanDuit comes with an EPDM liner pad to protect against abrasion and a threaded M8 stud for easy attachment to S-5! products without scratching or other damage to the roof.
CanDuit is available in 14 sizes with overlapping diameters ranging from .79 – 4.6 inches. Adjustability within each clamp enables minor size adjustment.
Colorado Springs, CO
www. s-5 .com • 888-825-3432
775 Fiero Lane Suite
#200 San Luis Obispo, CA 93401 SnapNrack www. snapnrack .com
Socomec
switching • Reduced total cost of ownership • Application tested design 9 Galen Street, Suite 120 Watertown, MA 02472 Tel. (617) 245-0447
The ACR-1000 by Solar Recombiner is a creative, cost-effective solution to recombining AC string inverter outputs on rooftop solar. Thoughtfully designed for the rooftop C&I market, this unique AC recombiner allows for a fast, clean installation that is O&M friendly throughout the life cycle of the asset. Key innovations include a gas spring cover, integral heat shield, and universal mounting rails all packed within a durable, powder-coated enclosure with generous wire bending area. The ACR-1000’s low profile of less than 14 inches allows for a compact installation. With a 10-year warranty and short lead times, the ACR-1000 is the new standard for rooftop AC recombiners.
Discover all of the advantages of WAGO’s TOPJOB® S terminal blocks, but with a smaller footprint. At a size 60% smaller than our standard terminal blocks, the TOPJOB® S Mini features the same industry-proven, Push-in CAGE CLAMP® connection technology used throughout our TOPJOB® S series.
These blocks are available in open tool slot or the easy-to-identify orange push buttons and can be mounted via miniature rail, snapin mounting foot or direct mount with fixing flange.
The TOPJOB® S Mini terminal blocks are a perfect solution where space is limited or where use of DIN rail is not possible.
The wind market continues to be the silent powerhouse in the renewable energy space in the United States. Through the first nine months of 2022, electrical generation by wind increased by 18.64% and provided 9.75% of total U.S. electrical generation. The next closest renewable energy electrical source was solar at 5% of the country’s output. But wind’s steady trajectory threatened to be stalled by supply chain issues and long offshore project timelines if some positive action wasn’t taken quickly.
A shot in the arm came with new and extended incentives for wind in the Inflation Reduction Act (IRA), which was signed by President Joe Biden in August. The wind production tax credit (PTC) was extended for projects that start construction before January 1, 2025, and a 10% PTC adder can be applied for wind projects that use domestic content. Wind projects can also now elect to take an investment tax credit (ITC) in lieu of the PTC — a clear benefit to expensive offshore wind development.
“This unprecedented investment in clean energy will supercharge America’s clean energy economy and keep the
United States within striking distance of our climate goals,” said Heather Zichal, then-CEO of the American Clean Power Association (ACP). “This is a generational opportunity for clean energy after years of uncertainty and delay. The IRA will lower consumer costs, enhance grid reliability and strengthen the nation’s energy security. It will expand our domestic manufacturing base, inject nearly half a trillion dollars into U.S. GDP over the next decade and create more than half a million new jobs — more than doubling today’s clean energy workforce.”
Consulting firm Rystad Energy quickly predicted the IRA would lead to an additional $160 billion of investments in onshore wind, which would double installed capacity over the next 10 years to 280 GW. The silent powerhouse will continue its leadership in U.S. renewable energy.
The IRA includes the new Advanced Manufacturing Production Credit, which will encourage domestic production of wind components like foundations, nacelles, blades and towers. The bill also provides nearly $40 billion in clean energy manufacturing that would directly benefit
offshore wind production and develop an advanced electrical transmission outline.
Those investments are much needed, as President Biden has amended his 30 GW of offshore wind by 2030 goal to require 15 GW of floating offshore wind capacity by 2035.
“California and Oregon have some of the best wind resources in the world, and floating offshore wind is crucial to harnessing these resources due to the depth of the ocean floor along the West Coast,” ACP’s Zichal said. “Innovation in floating wind turbines will make offshore wind more efficient, grow a more robust American supply chain, and bring down the cost of energy for consumers.”
The Dept. of the Interior held the first-ever offshore wind lease sale on America’s west coast in December as it opened California waters to floating offshore wind development. Even before 2022 closed out, major progress spurred by the IRA was in motion. The next year should prove to be another exciting development in the U.S. wind industry.
HELUKABEL provides cable system expertise throughout the wind turbine — rotor tip to tower base. We focus on control and data cables in the nacelle, torsion-rated cables in the drip loop, and flexible control and power cables in the down tower.
Our UL (WTTC)- and CSA (FT4)-approved copper, aluminum and fiber optic cables provide superior performance in climates ranging from -40°C up to +90°C, and can withstand the harsh environmental factors found in both on- and offshore environments.
For OEM and MRO customers, pre-assembled cable solutions are available for reliable termination and quicker installation on the factory floor or in the field.
1-GW wind project portfolio built by Blattner Energy New Mexico
Pattern Energy Group started commercial operation of Western Spirit Wind, a group of four wind farms totaling more than 1,050 MW located in Guadalupe, Lincoln and Torrance counties in New Mexico. The four projects are made of 377 GE wind turbines ranging from 2.3 to 2.8-MW. Pattern Energy developed the projects and Blattner Energy served as the construction contractor. The wind farms were built over 15 months and required more than 1,100 workers. Mike Garland, CEO of Pattern Energy, said Western Spirit demonstrates that large-scale renewables can be built and deployed in the United States.
EDP Renewables repowers phase of 423-MW Oklahoma wind farm Oklahoma
EDP Renewables North America repowered the second phase of Blue Canyon Wind Farm in Kiowa and Caddo counties, Oklahoma, extending the project’s lifespan by 20 to 30 years. In total, the repowering project brings Blue Canyon to 423 MW. EDPR NA replaced 73 of 84 turbines at Blue Canyon II, replacing each turbine’s nacelle, blades and top tower sections, upgrading from V80 1.8 MW to V110 2 MW.
Single-largest wind project in North America comes online
Oklahoma
AEP constructed the single-largest wind farm built at one time in North America, the 998-MW Traverse Wind Energy Center in Blaine and Custer counties in Oklahoma. Developed by Invenergy, the project delivers power to Oklahoma, Arkansas and Louisiana customers.
Construction underway on New York’s first offshore wind farm New York
New York legislators held a symbolic “groundbreaking” ceremony for the South Fork Wind offshore project to mark the start of construction. South Fork is the state’s first offshore wind project and the second commercial-scale offshore project approved in U.S. federal waters.
1st cross-border wind project between US and Mexico completed California
Sempra Infrastructure started operations on Phase II of Energía Sierra Juàrez, the first cross-border renewable energy project between Mexico and the United States. The expansion added 26 new wind turbines for a total of 263 MW.
Invenergy building 250-MW Illinois wind project Illinois
Invenergy completed construction on the 250MW Sapphire Sky Wind Energy Center in McLean County, Illinois, in December 2022. Sapphire Sky created 300 jobs during its 12-month construction period.
Great Pathfinder Wind constructs 224-MW wind project Iowa
Great Pathfinder Wind, a 224-MW wind project in Iowa, reached commercial operations in Q4 2022. Apex Clean Energy and IEA Constructors were involved on the project that supports Facebook parent company Meta’s operation under a longterm PPA for the full capacity of the project.
The Seven Cowboy wind project started operations before the end of 2022. Additionally, Enel is planning a new office space outfitted with facilities to simulate working inside wind turbines. Coursework will cover topics on safety, ladder rescues and turbine repair.
Renewables powers on 200-MW wind farm in ERCOT Texas
El Algodon Alto, a 200-MW onshore wind farm in San Patricio County, Texas, is operating and supplying power to the Electric Reliability Council of Texas south market. RWE Renewables completed construction of the 91 Vestas turbines in May 2022.
200-MW wind project completed across 28,000 acres of farmland Oregon
The 200-MW Golden Hills wind farm in Sherman County, Oregon, reached commercial operation in May 2022 for Puget Sound Energy. Golden Hills is built across approximately 28,000 acres of grazing and dry-land wheat farmland held by 37 landowners.
Cordelio Power completes Glacier Sands wind farm Illinois
Cordelio Power constructed a 185-MW wind project in Mason County, Illinois. Glacier Sands wind farm is composed of 43 Vestas V150.43 wind turbines and reached commercial operation. The wind farm is selling 100% of its power to tech giant Microsoft.
Enel Green Power finishes 350MW wind + storage project Texas
Enel Green Power completed the 350-MW Azure Sky wind farm paired with a 137-MW/205-MWh battery storage facility. Located in Throckmorton County, Texas, Azure Sky’s energy output is relegated to several corporate customers through power purchase agreements.
Gear-driven wind turbines are the heart and soul of sustainable, green energy generation from wind. With the urge to maximize efficiency and reduce costs, engineers strive to build bigger, safer and more powerful turbines. Eaton’s customized TWF Twinfil filter systems enable designers to reduce weight of the gearboxes significantly while maintaining top-level filtration quality that results in lower maintenance needs and downtime.
Green, clean but demanding wind power generation Wind energy is one of the fastest-growing renewable energy resources globally; it is free, sustainable and inexhaustible. However, due to their continuous energy production and often remote locations, both onshore and offshore, gear-driven wind turbines are demanding applications that require extreme reliability and durability. At the same time, manufacturers strive to build bigger, safer, more efficient and powerful turbines to provide the world with more affordable electricity.
At the top of the wind turbine’s tower is the nacelle, which houses all the generating components such as the generator, gearbox, drivetrain and brake assembly. For gear-driven wind turbines, the gearbox is a critical system. It steps up the relatively slow rotational speed of the blades, or extruders, to a higher speed, roughly 60-times more, needed to
generate electricity. Generally, turbines start producing energy at wind speeds above 5 to 7 mph. At speeds below this threshold, the turbine is not generating electricity, and the rotor is just idling.
On top of the nacelle are wind instruments, such as an anemometer and wind vane, which work out where the rotor has to point into the wind, and the correct pitch angle of the blades. For optimal performance of the turbine in any wind condition, the pitch of each of the common three blades is controlled independently by a gearbox.
Reducing weight and optimizing safety
Pitch control is essential, especially in very windy conditions, to keep the gearbox from getting overloaded and to avoid imbalance. Depending on the direction and strength of the wind, the gearboxes rotate each of the extruder blades to optimize power generation. There is usually a shock sensor inside the nacelle to measure vibration, which increases with wind speed. If the vibration reaches a specific limit, the turbine goes into a safe "pause"mode until the wind dies down. However, large moments and forces are
applied by the turbine rotor onto the drivetrain. To prevent stress points and failures, designers adjust the gearbox to support the loads and stress. Therefore, seals and lubrication systems must operate consistently, even in wide temperature variations; otherwise, dirt and moisture may collect and buildup inside the gearbox. Since oil contamination can cause gear failure and lead to breakdowns, potentially resulting in high repair costs, lost energy production or even destruction, the maintenance, monitoring and filtration of gear oil is an essential part of preventive maintenance programs.
The need to continuously optimize the powerto-weight ratio and energy yield of wind power gearboxes while simultaneously reducing the cost of producing wind energy led a global designer, manufacturer and supplier of gearboxes for wind turbines to reach out to Eaton for a customized solution. Known for its robust research and development operations, strategic partnerships and technological leadership, the company has installed thousands of gearboxes with a total capacity greater than 50,000 MW. The main objectives were to reduce the weight of the filter system, reduce the number of components and interfaces needed while providing full filtration quality and corrosion protection. Serviceability and low initial investment were equally important factors.
Anodized aluminum, fewer sealed connections and reliable filter elements
Eaton’s custom-designed TWF Twinfil filter system was engineered to meet the requirements. The result was a new generation of a gear lubricant filtration system that reliably met performance specifications.
The previous generation filter system was made from carbon steel and cast iron, which was C4H painted. Any paint damage, therefore, would result in severe corrosion — a particular problem for offshore installations where maintenance and replacements cost are incredibly high. By using anodized aluminum instead, the corrosion risk was minimized. Also, with a density of 168 lbs/ft³, anodized aluminum in place
of carbon steel and cast iron, with a density of 491 lbs/ft³, reduced the weight of the TWF Twinfil filter system by at least 882 lbs, depending on the size. With the lower weight of the filter system the overall weight of the nacelle, a key design parameter in this project, was reduced significantly.
The custom design combines the filter’s four mounting blocks into a single connection, virtually eliminating misalignment issues. The simplified mounting design also uses fewer sealed connections to reduce the risk of leaks. In addition, the new design integrates all valves into the system and connects the mounting plate to the manifold block. The new bayonet closure that replaces the previous flange cover permits rapid filter element changes, which improve serviceability by minimizing both maintenance and operating costs.
The TWF Twinfil filter system relies on glass fiber fleece 01.NR.1000 return-line filter elements and a 2-stage Twinfil filter element. The latter combines a fine 10 μm filter made of high-performance glass fiber fleece with a coarse filter made of stainless steel wire mesh with a nominal fineness of 25 μm. These two parts are separated by a bypass valve that allows an opening pressure of 51 psi. The valve is designed to protect the fine filter from any damage due to high viscosity at low temperatures or provides permanent filtration by the fine filter when closed. In the end the TWF Twinfil filter system provides up to three different levels of fineness
depending on the used filter elements, is suitable for a working pressure up to 263 psi and effectively removes particles from lube oils down to 6 µm, reliably and consistently throughout the filter’s life at a maximum flow rate of 66 gal/min. All system components work properly from a cold start to the +158°F maximum operating temperature without any adverse effect on the overall gear-oil supply. The flow dividing valve reliably controls the flow rate to the cooler or directly back to the gearbox.
Maintaining filtration quality while reducing weight by 78%
The custom designed TWF Twinfil filter system is fulfilling the requirements of the gearbox manufacturer. Essential was the success in reducing the weight of the filter systems by 78%, which was key to reducing the overall weight of the gearboxes.
In this pilot project Eaton was providing more than 80 units of TWF Twinfil 4000 and 6000 filter systems for the different wind turbines in the park. Both have proven to de-aerate oil under all operating conditions, enhancing the reliability and efficiency of the gearbox and its lubrication system by assisting users in maximizing output while minimizing downtime and operating costs. An additional benefit for the gearbox manufacturer is that the new TWF Twinfil filter system meets all the relevant safety certifications for both on- and offshore wind turbine applications worldwide.
“A ll models are wrong, but some are useful,” the statistician George Box wrote in 1976. This familiar aphorism sheds light on the fact that models cannot capture the complexities of the real world. Whether we use models to study financial market mechanisms, predict optimal healthcare strategies or, for any other use case, they can be useful but never truly accurate.
The same goes for numerical weather prediction. As most of us have experienced watching the weather on TV, weather forecasts are rarely perfect. Like all forecast models, weather models are only an approximation of the world that tries to predict the conditions of the atmosphere by collecting quantitative data and relying on advanced calculation methods.
Recent technological advancements, however, promise to improve the accuracy of weather forecasting. Today, advanced machine learning techniques and increased computing power can reduce weather forecast errors, ultimately helping meteorologists develop better predictions.
This is good news for the offshore wind industry, as the weather plays
a critical role in the construction, maintenance and productivity of offshore wind farms. Wave height determines the working windows of wind farm installation vessels and limits the accessibility of wind turbines for maintenance. Lightning and thunderstorms can endanger the safety of maintenance crews working on the turbines. And strong winds can reduce the operability of cranes and thereby limit the working windows during installation.
With more accurate weather forecasts at hand, offshore wind players can efficiently reduce downtime and costs while simultaneously increasing the safety of personnel and maintenance crews.
As a global partner for the offshore wind industry, StormGeo strives to improve its weather forecasts to help offshore wind developers and operators ensure safer and more efficient wind farm installations and maintenance. That is why StormGeo has developed DELFI, a weather forecasting algorithm that leverages the power of machine learning to improve offshore wind operations and maintenance worldwide.
DELFI: Machine learning for offshore weather forecasting
DELFI (deep learning forecast improvement) is StormGeo’s machine learning system, raising the quality of weather forecasts by correcting forecast errors adaptively. It leverages a broad range of advanced machine learning techniques, from linear models to deep neural networks, to automatically improve forecast quality by learning the error patterns from the forecast systems.
Every week, DELFI compares the forecasts produced by the different methods with all available observation data and chooses the method with the highest score. That method is then used in the forecasting for the next week. The process is repeated every week, always adding last week’s observations to its verification process.
DELFI differs from traditional weather forecasting in that it reduces the need for manual intervention in position-based forecasts. Where we often needed to rely on forecasters to learn, remember and act on the model’s weaknesses in the past, DELFI now learns these weaknesses and automatically reduces most of these errors. DELFI,
then, provides a more accurate starting point than any of the input forecasts.
Machine learning-based forecast improvement methods, such as DELFI, are, in principle, not that different from conventional weather forecasting. In both cases, somebody or something must understand and learn the forecasting system weaknesses and leverage this knowledge to improve the accuracy. The main difference, however, is that the machine learning system more efficiently identifies errors compared to a traditional weather forecaster. DELFI, then, provides a more accurate forecast baseline that helps the forecaster work more efficiently and make better decisions.
DELFI, and machine learning in general, not only improves the accuracy of weather forecasts but also improves efficiency by automating tasks traditionally performed by human weather forecasters. The forecaster’s role will change accordingly, moving away from detailed intervention of position-based forecasts to focus more on decision support for offshore wind clients, optimizing the forecasts, identifying potentially breaching thresholds and providing advice when observations do not match the forecasts.
In other words, DELFI reduces the subjective element of weather forecasting, which in turn creates more consistent and efficient predictions
that are less dependent on the inclinations of individual forecasters. For some offshore wind developers and operators, a more objective forecast may yield more confidence during decision-making processes.
StormGeo has successfully used DELFI to improve weather forecasts for several offshore locations — even though the machine learning system is still in its early development stages.
For example, a multinational energy company recently leveraged DELFI to improve its understanding of metocean characteristics on one of its offshore locations in the North Sea. By relying on DELFI’s machine learning capabilities, the offshore site improved its results significantly compared to traditional weather forecasting methods.
The figure below shows an improved forecast accuracy at the offshore location (figure 1). The blue curve indicates observations, showing measured wave height for nine days during Autumn 2021. The orange line represents the numerical weather prediction model. The green line represents the DELFI forecast — and catches the variability correctly.
For some offshore clients, the difference between 1.9 and 2.2 meters of wave height is critical to their operations and their ability to ensure safety and
efficiency and reduce operational downtime. And offshore operators, in general, increasingly focus on the costbenefit of having more accurate forecasts. Leveraging machine learning techniques helps us adapt to these changing business needs by increasing weather forecasts’ quality, accuracy and efficiency.
The first use cases for DELFI are promising, and the system will keep on improving and extending to improve forecast quality in even more industries and for more advanced situations. And DELFI will only enhance its accuracy as it gets more use cases to learn from. StormGeo currently trains DELFI to improve the forecasts weekly, using a full range of machine learning techniques, as new and updated observation data from offshore wind farms and other offshore installations come in.
Once implemented, DELFI can result in significant weather forecast accuracy improvement, ultimately helping offshore wind developers and operators safely plan their operations and improve operational spending. WPE
Figure 1: Time series of signifi cant wave height forecast from 2021-10-30 to 2021-11-07. The time series of model and DELFI forecasts shown here are based on a 0 to 12 hours lead time.
In their quest to lead the fight against climate change, clean energy industry stakeholders have had to overcome no end of challenges. And in doing so, huge progress has been made; the levelized cost of solar and wind energy has tumbled in the last decade, technology has evolved rapidly and now — at such a critical time for our planet — renewable energy sits right at the heart of the energy transition. It is undoubtedly seen as
the weapon of choice for governments seeking to rapidly decarbonize their energy systems while enhancing their security.
But one very significant challenge to the clean energy sector is increasingly coming into focus: greenflation.
What is greenflation?
Defined in simple terms, greenflation is the sharp rise in the price of materials like
metals, minerals like lithium, and other resources such as labor, energy and fuel that are used in the creation of renewable energy technologies and projects.
There is presently no single trend behind price increases experienced by wind sector stakeholders. The COVID-19 pandemic has placed global supply chains under strain, leading to rising raw material costs and global labor shortages. The war in Ukraine and subsequent sanctions
on Russia has compounded this — particularly when it comes to the costs of energy needed to produce and ship materials.
In turn, this has meant higher manufacturing and logistical costs throughout the value chain, including for components, capital equipment and technical resources.
According to various outlooks, forecasts and indices, commodity prices are surging — in spite of renewable energy development. Energy commodity prices published by The World Bank in March 2022 have surged 63.4% over the last 12 months, while non-energy commodities, including metals and minerals, increased 22.7%. Increases in both energy and non-energy commodity prices are causing renewable energy project development costs to rise.
The Refinitiv CoreCommodity CRB Index, a composite measure of commodity prices, was up 46% on the year at the end of January, the largest one-year increase since 1995, when comparable data became available.
There are also demand-led causes. A push for new wind projects as countries seek to reach their net-zero goals, alongside a scramble to install as government subsidies begin to disappear, has stoked fierce competition for limited assets and services. The supply chain, including maritime and maintenance service providers, has been stretched to capacity, even as their own costs increase.
International Monetary Fund research published in November 2021 stated that “the world’s historic pivot toward curbing carbon emissions is likely to spur unprecedented demand for some of the most crucial metals used to generate and store renewable energy in a net-zero emissions by 2050 scenario.”
It found that costs of these metals will surge, with the potential for lithium
to rise from its 2020 level of around $6,000 per metric ton to about $15,000 late this decade — and stay elevated through most of the 2030s. Cobalt and nickel prices, the IMF says, could also see similar surges in coming years.
And a report published by Wood Mackenzie in August last year — prior to the Q4 gas price surge — highlighted that commodity price increases, coupled with a four-fold rise in logistics costs, would see turbine prices go up by 10%.
Greenflation is hitting OEMs hard OEMs have been particularly impacted, with many reporting profit warnings last year and posting huge losses through the first half of 2022. This situation is unsustainable — OEMs are the lifeblood of the wind industry and without them nothing can be done.
It isn’t all bad news. These are temporary growing pains, arising partly from wider inflationary pressures, but also due to growing demand. Renewable energy is scaling rapidly, with lower cost financing available to green businesses from environmentally minded financiers. That is cause for celebration.
Wind energy will overcome this challenge, as it has many others. However, while greenflation has a more immediate and significant effect on developers and OEMs, owners and operators will inherit projects with tighter margins within the decade.
That is why building a robust understanding of efficient operations is key to mitigating the effects of today’s greenflation, while continuing to drive down costs and improve efficiencies in years to come.
With O&M accounting for almost 60% of total operational expenditure, wind project owners and operators
can mitigate against the impacts of greenflation by optimizing their O&M strategies.
“Wind Power’s Greenflation
Frustration,” a recent report by ONYX Insight, takes operators through the four steps they can take to bolster predictive maintenance programs, in turn reducing costs and safeguarding profits as greenflation begins to bite. A best practice predictive maintenance program could reduce OPEX costs by 17% on average.
Despite greenflation, operators can boost their portfolio’s long-term profitability by thinking holistically — reducing labor and logistical costs, and component replacements.
Four steps that could ease operators’ future greenflation pain
There are four steps — underpinned by a series of self-analytical questions — that operators can take to safeguard against the long-term impacts of greenflation.
The first way to do this is by looking at base level capability. A robust and reliable predictive maintenance strategy involves understanding the risks and opportunities for improvement across a wind portfolio. Most asset owners already have various software products deployed across their fleet. They can start with gap analysis to identify areas for improvement.
The second is to build a greenflationproof business case. Greenflation is an evolving trend, but the risk profile of a wind portfolio also changes with time. The historical performance of a wind farm does not reliably indicate the future performance since failure rates are not static.
By utilizing accurate, turbine-specific technology to predict failure rates, asset owners can forecast and implement solutions before reliability issues start to surface.
Third, operators should carefully select predictive maintenance technology.
Specific technologies that enable predictive maintenance include software tools such as analysis dashboards and data management platforms, sometimes enhanced by additional hardware such as vibration, oil quality/contamination and audio sensors.
Operators need to assess track record, accuracy and reliability, what components are covered and lead time on fault detection and the technology’s ability to manage diverse data streams (SCADA, sensors, non-structured data).
And finally, they need to implement and integrate a program. The relatively slow adoption of digital technologies in wind is in part due to owners and service providers relying on case studies instead of backing operational decisions with statistical analysis. Performance statistics
are key to a systematic approach, enabling operators to create KPIs at the implementation stage that track the ability of digital technologies to achieve and maintain desired business outcomes, such as production-based availability, climbs per wind turbine per year, labor hours per component, and so on.
Enabling a holistic data-led O&M strategy allows operators to identify opportunities to pool resources, such as consolidating transport costs and technical resources or maintaining a joint inventory. Data integration — and sharing — is key to achieving this.
Fail to prepare, prepare to fail So the old adage goes. Greenflation is not a short-term consideration. It represents a rebalancing of costs across
the wind industry in line with wider macroeconomic trends. It sits alongside critical challenges such as the looming skills gap and increased exposure to merchant markets.
Wind farm owners globally are demonstrating that digital technologies are essential in improving asset profitability, reducing uncertainty in energy production and optimizing operational efficiency. Now they need to ensure that as they inherit the challenges currently being posed to the wind industry by greenflation, they have the capabilities to deal with it by being forensic in their approach to operations cost management. WPE
Scaling renewable energy capacity is critical to the global energy transition and the decarbonization of difficult-to-abate industries. While it is widely recognized that offshore wind can play a key role in increasing this renewable energy capacity, many people do not appreciate that for this ambition to become a reality, floating wind will have to play a significant role.
The ability of floating wind technology to open new offshore sites for high-capacity wind farms is key. For the United States, the incentive to “go deep” exists because almost two-thirds of its offshore wind resources are found in waters that would require floating platforms.
Meanwhile, the UK has increasingly ambitious offshore wind targets that floating wind farms can help the country achieve. The UK government recently announced its goal is to build 50 GW of operating offshore wind capacity by 2030, of which 5 GW will be floating wind.
A recent report by the Global Wind Energy Council (GWEC), aptly called floating offshore wind a global opportunity, highlighting that the U.S. West Coast, Ireland, Italy, Morocco and the Philippines would likely closely follow the small group of pioneers already installing the first commercial-scale floating wind farms.
However, while the offshore wind market enjoyed its best year ever in 2021, with 21.1 GW of capacity commissioned, only 57 MW of that was floating wind. So, what barriers are preventing the commercialization of floating wind technology?
As with most nascent technologies, there are still commercial barriers to overcome for floating wind technology to mature as needed. One such barrier is floating foundation structure selection.
The four main structure types (spar buoy, tension leg platform, semi-submersible platform and square barge) are well known at this point, but decisions on which platform or variation to use are rarely underpinned by data or analysis. Demonstrators have often been driven by the floating structure designers themselves, mostly to prove their technology rather than to provide developers with an objective demonstration of each technology.
Therefore, there is still a fundamental need to identify the best
technical solutions for each planned floating site to minimize costs, risk and inefficiency for developers. It’s highly unlikely that there will be a single definitive foundation type. Rather, developers will need to go beyond purely reviewing the site to identify the most suitable option for each location and specific set of conditions.
Advanced floating foundation analysis involves comparing a combination of technical and operational factors and, arguably, the latter will have a bigger impact throughout the asset’s lifecycle.
Location, infrastructure, water depth, available space for fabrication and storage are all key for ports that will support a new development. Taking the UK as an example, current options are limited. Individual ports do have plans
IN THIS EPISODE of the Wind Spotlight podcast from Windpower Engineering & Development, we are joined by Brian Warmerdam, product manager at RAD Torque Systems, to discuss the company’s latest o ering in torque wrench. RAD Torque is a Canadian Manufacturer producing battery-powered torque wrenches used in a range of industries, including mining, aerospace, and, of course, wind power.
RAD Torque will be exhibiting at the international construction machinery trade show, bauma 2022 in Munich, Germany. The company encourages attendees to stop by RAD Torque’s booth to test out its range of tools.
Below is written excerpt of this episode of Wind Spotlight, but be sure to listen to the entire episode here or on your favorite podcast app.
RAD Torque systems will soon be launching an exciting new tool called the B-RAD Xtreme. Tell me about it and why it’s going to revolutionize the torque wrench industry?
Well, the B-RAD Xtreme is going to launch with the highest torque output models available anywhere in the world. We’re
launching with a 5,000, 8,000 and 11,000 ft lb models, making us the biggest battery tool available in any market.
The B-RAD X also includes a bunch of safety features that are new to our battery tooling. There’s a secondary trigger to prevent accidental operation or prevent any pinch points that may occur. We also are launching the tool with a bunch of ergonomic accessories. But most importantly is performance.
RAD Torque Systems is well known for its innovative gearbox. What makes the RAD gearbox unique?
We have 25 years of experience designing and manufacturing these gearboxes across five distinct generations of design. All that experience, all that knowledge has really put us in a position to bring that together and be able to provide the strongest, smallest gearboxes possible. That’s really where we take our pride in our tools, is being able to provide something that’s ergonomic, safe to use and isn’t as cumbersome as most of the solutions on the market right now.
The E-RAD Blue torque wrench is a preferred tool in the wind industry as well. Tell me about the E-RAD Blue and why so many wind turbine manufacturers and maintenance contractors make it their go-to tool.
It’s definitely two-fold. In manufacturing, the features that seem to be successful from the E-Rad are the data collection, process control integration with open protocol and other software that uses that technology. And it’s a bit of a workhorse. It’s an AC-powered tool, so you can plug it in and use it two shifts a day, every day. On the maintenance side, up a tower, the E-RAD provides a lot of benefits over some of our competition because the tool system is fairly lightweight. It’s easier to pack up a tower in order to do flange maintenance or generator maintenance or whatever needs to be done. And that’s proven to be very successful for us. WPE
to invest, but none will be sufficient to cover all options, so there is a risk that significant parts of the manufacture could go to Europe or Asia.
This lack of port infrastructure seems to be driving the choice of concrete over steel foundation. It would appear easier to manufacture concrete structures because it requires a less skilled workforce. You only need the molds and raw materials, and not the specialized welding equipment or qualified welders. Steel can be prefabricated elsewhere and assembled, but that builds in additional fabrication risk and requires additional transport of large components, increasing costs and carbon footprint.
Operations and maintenance (O&M) is an even bigger challenge facing the industry. Floating foundations are currently towed back to port for maintenance and repairs. However, this cannot be viable or economical as wind farms are located further offshore and the distance to O&M ports increases. The ability to conduct O&M on-location
must be developed, because the risk and costs associated with connection and disconnection and transportation of the wind turbine generator (WTG) will prove too high over time.
A combination of modifying the WTG, as well as developing the tools and vessels required to support this O&M phase is crucial to the success of floating wind. Having the right expertise and advice available in the initial phase of the project ensures that developers gain a holistic understanding of the processes, equipment, vessels and operations involved from the outset.
The latest targets in Scotland are to deliver up to 11 GW of (fixed and floating) offshore wind capacity by 2030+, aligning with the government’s ambition to challenge Norway and China as a leader in floating wind.
The recent ScotWind leasing round awarded 24.8 GW of offshore wind, 15 GW of which is floating. Meanwhile the
upcoming Innovation and Targeted Oil & Gas (INTOG) leasing round could deliver a further 5.7 GW, and the Celtic Sea Lease would deliver 4 GW.
The total capacity of floating offshore wind in the UK including ScotWind, INTOG and Celtic Sea currently amounts to 25 GW, which equates to 1,250 floating units, assuming each project uses 20-MW turbines and that one foundation per turbine if required. ScotWind is assuming mostly to use 18- and 20MW turbines, however these are not yet available, so it’s a bold assumption on the developers’ part. For a 10-year period (2029-2039) for manufacturing and installations, this requires 125 units to be made per year.
Supply capacity for ScotWind is capable of exceeding demand. However, the actual realized capacity will likely be lower, as, due to competition with other marine activities for port use, limited areas will be available for wet storage that may hinder productivity. For this reason, not all expansion plans will be realized.
Onshore crane availability may also be a bottleneck, and immature supply chain and installation infrastructure may slow progress further. Critically, many Scottish ports do not have the required areas to deliver commercial-scale floating offshore wind without significant investment and infrastructure development.
What ScotWind is still missing is a decision on which floating foundation each developer will select for a given site. Until that is known the supply chain cannot form, and investment cannot be made in the port infrastructure. There are many floating foundations to choose from, but only a handful that are practical for use with the constraints of ScotWind.
While many challenges remain, it’s not all doom and gloom; the industry is at the dawn of commercialization. The Hywind Scotland project was the first commercial-
scale offshore floating wind farm in 2017. Now, there are 14 floating ScotWind projects in the pipeline.
There is no shortage of companies lining up to form the supply chain and people ready to invest. At Houlder, we believe that the challenges in Scotland, and globally, can be overcome with the right collaboration and investment. Independent marine and offshore design and engineering specialists can provide consultancy on the costs, timeframes, emissions and risks of each floating wind technology — supported by technical analysis.
Lessons will also be learned from INTOG, as well as ScotWind over time. The industry will evolve, and it is likely that future leasing rounds will have improved technology and foundations. Although this does rely on increased
transparency on foundation choice and reasoning.
Vertical access turbines, or selferecting nacelle systems such as SENSEWind’s concepts, as well as power to X will influence the direction of foundation type. But we need to put those evolutions to one side for now and choose a conservative base that can work for a site and press on to avoid major delays to ScotWind and the UK’s environmental targets.
Only the offshore wind industry and its experts can decide if floating offshore wind will be an endless dawn or a global opportunity which can drive the global energy transition. Let’s make the right decisions, supported by engineering, to ensure that renewable energy ambition is fulfilled. WPE
WTWH Media, LLC
1111 Superior Ave., Suite 2600, Cleveland, OH 44114 Bruce Sprague (888) 543-2447
WTWH Media, LLC 1111 Superior Ave., Suite 2600, Cleveland, OH 44114
Courtney Seel; WTWH Media, LLC
1111 Superior Ave. Suite 2600, Cleveland, OH 44114
Kelly Pickerel; WTWH Media, LLC
1111 Superior Ave., Suite 2600, Cleveland, OH 44114
Billy Ludt; WTWH Media, LLC
1111 Superior Ave., Suite 2600, Cleveland, OH 44114
WTWH Media, LLC 1111 Superior Ave., Suite 2600, Cleveland, OH 44114
Scott McCafferty 1111 Superior Ave., Suite 2600, Cleveland, OH 44114
Mike Emich 1111 Superior Ave., Suite 2600, Cleveland, OH 44114
Marshall Matheson 1111 Superior Ave., Suite 2600, Cleveland, OH 44114