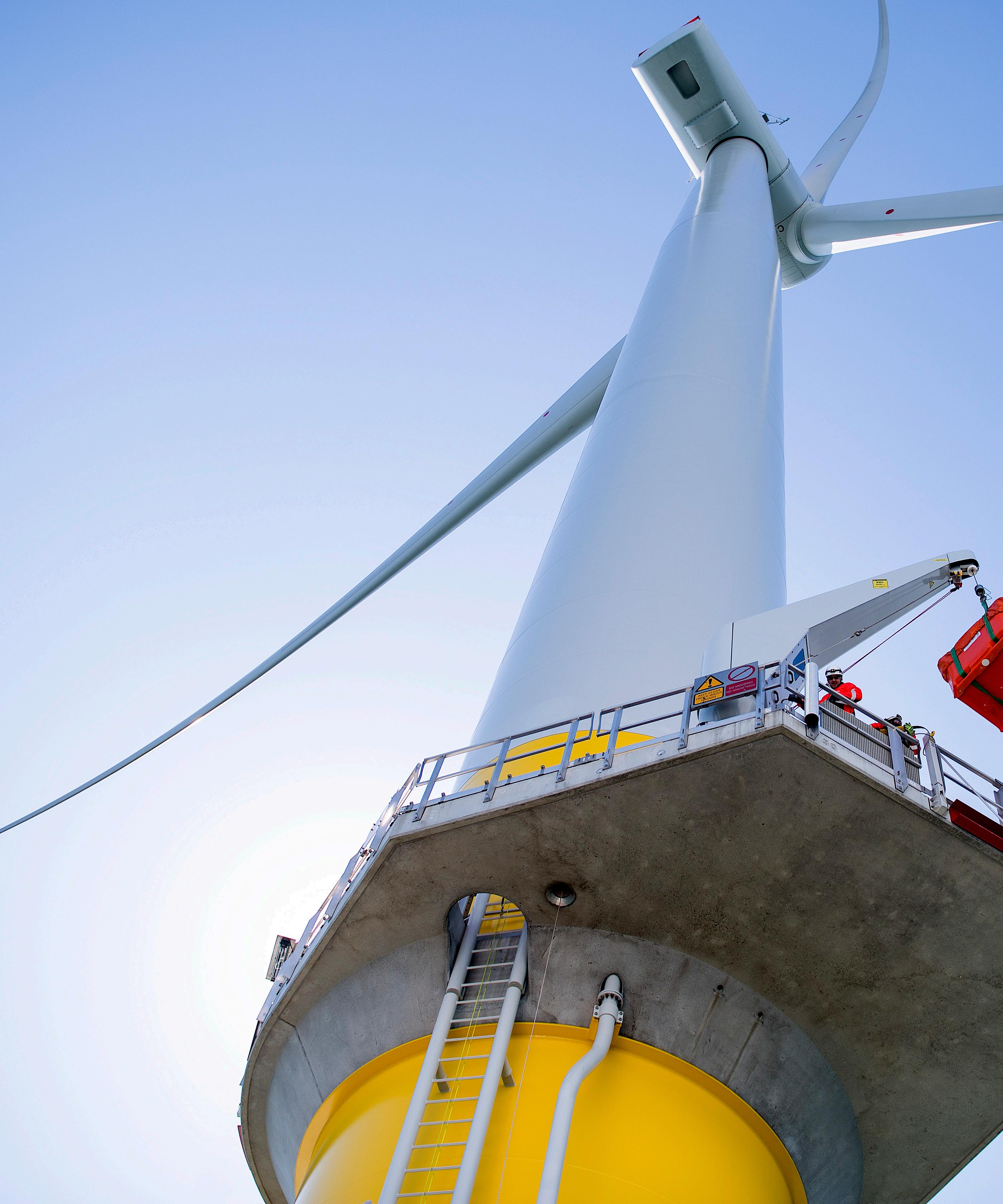
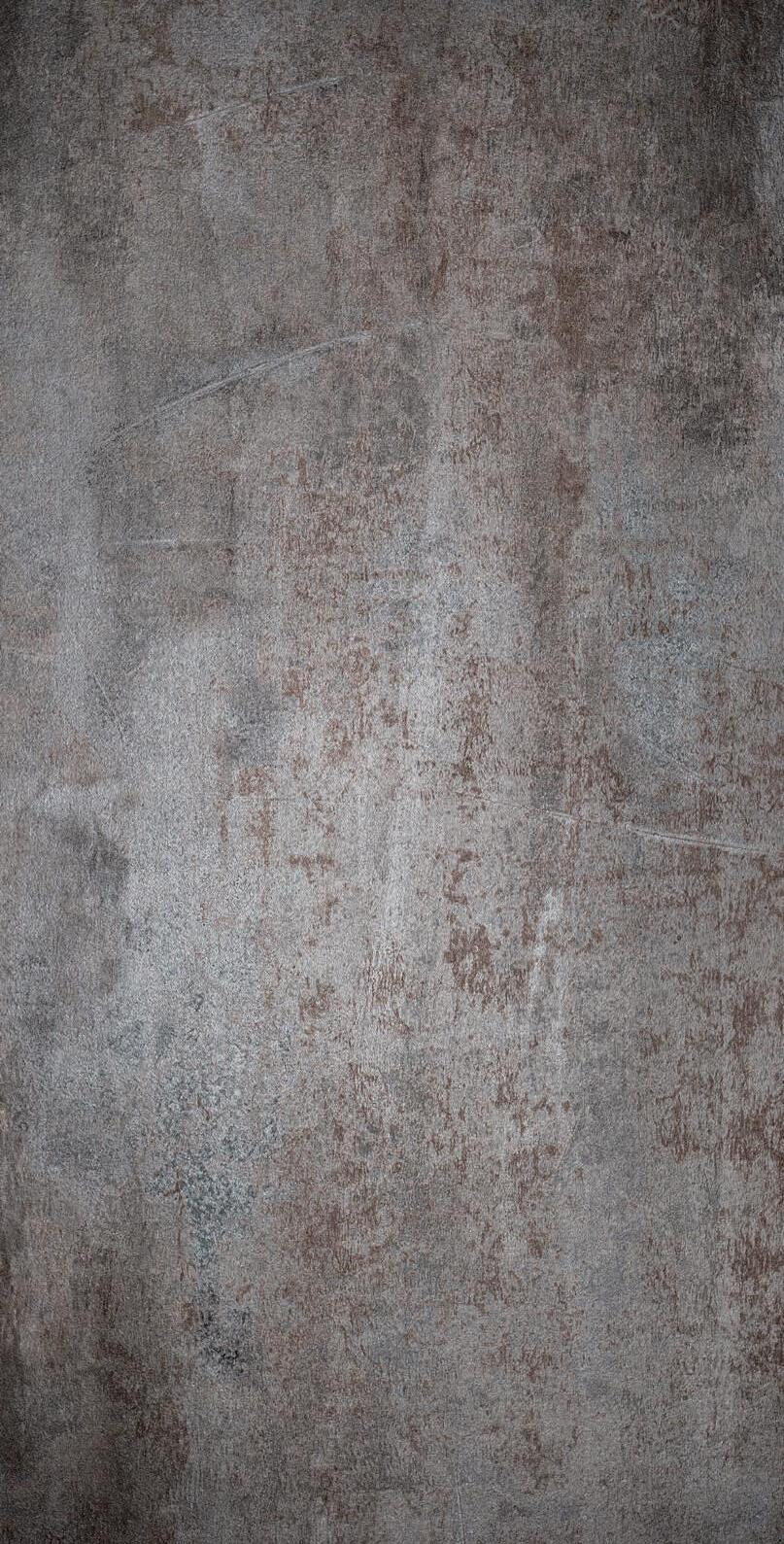
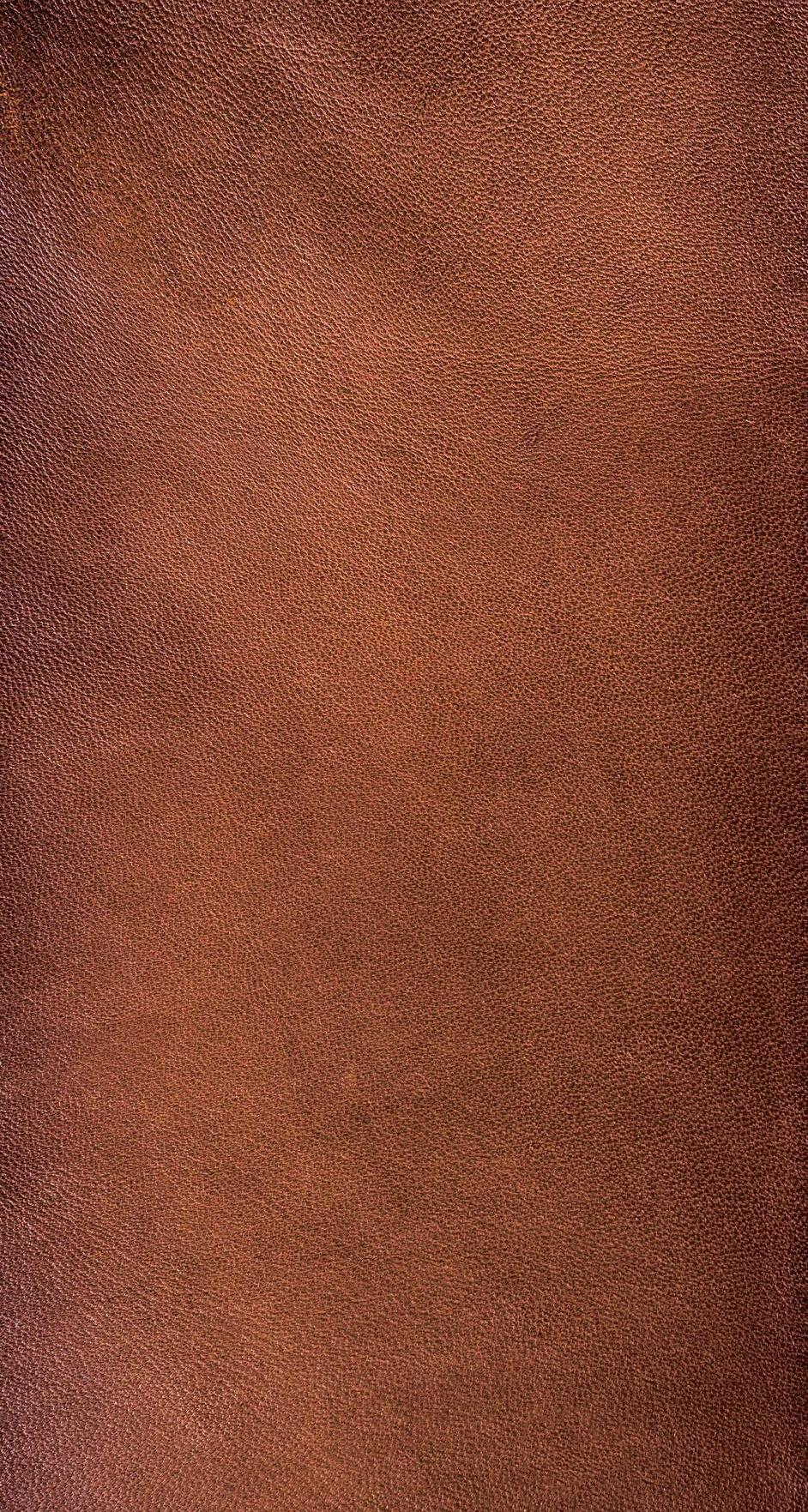
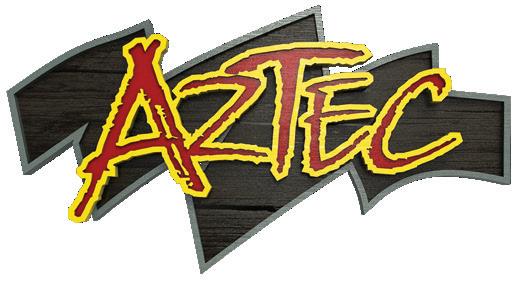







































PUBLISHER
Courtney Nagle cseel@wtwhmedia.com 440.523.1685
EDITORIAL
Editorial Director, Renewables Kelly Pickerel kpickerel@wtwhmedia.com
Senior Editor Billy Ludt bludt@wtwhmedia.com
CREATIVE SERVICES & PRINT PRODUCTION
VP of Creative Services Matthew Claney mclaney@wtwhmedia.com
Art Director Allison Washko awashko@wtwhmedia.com
Senior Graphic Designer Mariel Evans mevans@wtwhmedia.com
Graphic Designer Shannon Pipik spipik@wtwhmedia.com
Director, Audience Development
Bruce Sprague bsprague@wtwhmedia.com
WTWH Media, LLC
1111 Superior Avenue, Suite 2600, Cleveland, OH 44114
Ph: 888.543.2447
Fax: 888.543.2447
VIDEO SERVICES
Videographer Manager Garrett McCafferty gmcca erty@wtwhmedia.com
Videographer Kara Singleton ksingleton@wtwhmedia.com
Videographer Cole Kistler cole@wtwhmedia.com
MARKETING
VP of Digital Marketing Virginia Goulding vgoulding@wtwhmedia.com
Digital Marketing Manager Taylor Meade tmeade@wtwhmedia.com
Digital Marketing Coordinator
Emily Gillespie egillespie@wtwhmedia.com
Digital Production/ Marketing Designer Samantha King sking@wtwhmedia.com
Marketing Graphic Designer Hannah Bragg hbragg@wtwhmedia.com
Webinar Coordinator Halle Sibly hkirsh@wtwhmedia.com
ONLINE DEVELOPMENT & PRODUCTION
Web Development Manager
B. David Miyares dmiyares@wtwhmedia.com
Digital Media Manager
Patrick Curran pcurran@wtwhmedia.com
Digital Production Manager Reggie Hall rhall@wtwhmedia.com
Front End Developer Melissa Annand mannand@wtwhmedia.com
Digital Production Specialist Nicole Lender nlender@wtwhmedia.com
Digital Production Specialist
Elise Ondak eondak@wtwhmedia.com
IN-PERSON EVENTS
Events Manager
Jennifer Kolasky jkolasky@wtwhmedia.com
Events Manager
Brittany Belko bbelko@wtwhmedia.com
Event Marketing Specialist
Olivia Zemanek ozemanek@wtwhmedia.com
CUSTOMER SERVICE
Customer Service Manager Stephanie Hulett shulett@wtwhmedia.com
Customer Service
Representative JoAnn Martin jmartin@wtwhmedia.com
Customer Service Representative Tracy Powers tpowers@wtwhmedia.com
Customer Service Representative Renee Massey-Linston renee@wtwhmedia.com
Customer Service Representative Trinidy Longgood tlonggood@wtwhmedia.com
FINANCE Controller Brian Korsberg bkorsberg@wtwhmedia.com
Accounts Receivable Specialist Jamila Milton jmilton@wtwhmedia.com
HUMAN RESOURCES
VP of Human Resources Edith Tarter etarter@wtwhmedia.com
WINDPOWER ENGINEERING & DEVELOPMENT does not pass judgment on subjects of controversy nor enter into disputes with or between any individuals or organizations.
WINDPOWER ENGINEERING & DEVELOPMENT is also an independent forum for the expression of opinions relevant to industry issues. Letters to the editor and by-lined articles express the views of the author and not necessarily of the publisher or publication. Every e ort is made to provide accurate information. However, the publisher assumes no responsibility for accuracy of submitted advertising and editorial information. Non-commissioned articles and news releases cannot be acknowledged. Unsolicited materials cannot be returned nor will this organization assume responsibility for their care.
WINDPOWER ENGINEERING & DEVELOPMENT does not endorse any products, programs, or services of advertisers or editorial contributors. Copyright© 2023 by WTWH Media, LLC. No part of this publication may be reproduced in any form or by any means, electronic or mechanical, or by recording, or by any information storage or retrieval systems, without written permission from the publisher.
SUBSCRIPTION RATES: Free and controlled circulation to qualified subscribers. Non-qualified persons may subscribe at the following rates: U.S. and possessions, 1 year: $125; 2 years: $200; 3 years $275; Canadian and foreign, 1 year: $195; only U.S. funds are accepted. Single copies $15. Subscriptions are prepaid by check or money orders only.
SUBSCRIBER SERVICES: To order a subscription or change your address, please email: please visit our web site at www.windpowerengineering.com
WINDPOWER ENGINEERING & DEVELOPMENT (ISSN 2163-0593) is published four times per year in February, May, September and a special issue in December by WTWH Media, LLC, 1111 Superior Avenue, Suite 2600, Cleveland, OH 44114. Periodicals postage paid at Cleveland, OH and additional mailing o ces.
POSTMASTER: Send address changes to: Windpower Engineering & Development, 1111 Superior Avenue, Suite 2600, Cleveland, OH 44114
WINDWATCH
A selection of product and policy news from our website.
CONTRIBUTORS
See the latest wind power developments and U.S. project news as well as expert webinars and more on our website today at WINDPOWERENGINEERING.COM
MV wind converters help wind operators maintain profitability by offering higher efficiency, lower total cost of ownership and greater reliability at the higher turbine power levels now demanded by new offshore wind projects.
The demand for wind turbine maintenance is increasing. Borescope inspections of gearboxes are a cost-effective way to shorten the downtime of wind turbines and prevent early detection of defects leading to gearbox replacement.
Wind power operators face a unique set of risks that can be effectively managed to protect wind farm assets and ensure the viability of the operation. Whether facing required upgrades to an aging equipment fleet or incorporating new technology into the operation, wind operators can plan for associated risks with the support of healthy, vetted OEMs and an experienced insurance broker.
The American Clean Power Association released a report in May on the U.S. offshore wind market, revealing a pipeline of projects across 32 leases totaling 51.3 GW of capacity — enough electricity to power more than 20 million homes. The U.S. offshore wind industry is expected to create 83,000 jobs by 2030
and invest up to $25 billion annually, according to an ACP report from 2020. Other highlights from this latest report include more than 30 new sea vessels being built domestically to support offshore wind development; and at least 14 facilities related to the offshore supply chain have been announced or are under construction.
Tech Safety Lines opened its brand-new Blade Repair Training Center that will provide educational opportunities for blade repair technicians. The center will cater to both seasoned technicians seeking to enhance their expertise and newcomers looking to embark on a rewarding career in blade repair. Trainees will have access to hands-on experience using actual blade sections, replicating real-life scenarios and challenges they might encounter in the field.
The U.S. federal government approved construction of the 1.1-GW Oceans Wind 1 project located 13 nautical miles southeast of Atlantic City, New Jersey, and the 704-MW Revolution Wind project, located 15 nautical miles southeast of Point Judith, Rhode Island. These are the third and fourth offshore wind projects that the Biden Administration has approved, preceded by Vineyard Wind offshore Massachusetts and South Fork Wind offshore New York.
Several organizations in education and the maritime industry signed a memorandum of understanding to bolster Maine’s workforce for offshore wind development. The Maine Community College System, Maine Maritime Academy (MMA) and Diamond Offshore Wind participated in roundtable discussions in July at the MMA’s Center for Professional Mariner Development to discuss initiatives related to future offshore wind farms off New England’s coast. This collaboration is the first of its kind in Maine.
The U.S. Dept. of the Interior held an auction in late August to lease nearly 300,000 acres offshore in the Gulf of Mexico for wind development. The department stated that the lease area has the potential to generate approximately 3.7 GW of power from offshore wind. Following a 60-day period for public comments,
the Dept. of the Interior included requirements that bidders must support workforce development, build a domestic supply chain, mitigate impacts to local fisheries and routinely engage with regional Tribes and ocean users that could be affected by offshore wind construction.
Pattern Energy contracted Stantec to serve as owner’s engineer for the SunZia Transmission Project, an infrastructure project that will provide transmission capacity for 3 GW of clean energy facilities to communities in Arizona and California. This infrastructure upgrade opens Pattern Energy to developing up to 3.5 GW of wind power in New Mexico that will serve Southwest communities. SunZia will be composed of a 525-kV high-voltage direct current transmission system with 550 miles of overhead power lines traversing federal lands. Stantec will be responsible for electrical, civil, structural, building and mechanical engineering services on the project.
AES Corp. started commercial operation for phase one of its Chevelon Butte wind farm located in Coconino and Navajo counties, Arizona. This first phase is 238 MW in a 454-MW total project, with the remainder of capacity expected to reach commercial operations in 2024. The project was built to continue a century-long tradition of raising livestock on the land and matches Arizona’s dark sky characteristics by using lighting that only activates when low-flying aircraft is in its vicinity.
The first monopile foundation was installed in June on the South Fork Wind offshore project being built off the coast of New York. With the foundation in place, the offshore substation could be installed, followed by tower erection. Upon completion, the project will reach 130 MW. The site will feature 12 Siemens-Gamesa 11-MW wind turbines, which are being carried 35 miles offshore from Montauk. South Fork is one project in a more than 4.3-GW pipeline of offshore wind projects slated off the New York coast.
GE Vernova, General Electric’s portfolio of energy businesses, invested $50 million at its Schenectady, New York, facility to establish a new manufacturing assembly line for its onshore wind business. This will spur the hiring of approximately 200 new full-time employees including union operators, manufacturing engineers and front-line leadership that will assemble three components for GE Vernova’s 6.1-MW turbine.
JOAO AMARO is a Partner in the McGill and Partners’ Renewables, Power and Energy team, specializing in offshore wind. Joao has over 10 years’ experience in the insurance market, most of which has been exclusively dedicated to the renewable energy sector. With a background in civil engineering, Joao has specialized in advising offshore wind projects throughout the full scope of the project lifecycle, including risk allocation, insurance program design, and placement for construction and operational phases. During this time, Joao has gained broad knowledge and experience on fixed-bottom and floating offshore wind projects in Europe, U.S. and Asia.
TIM HALPERIN SMITH is the Head of Renewable Energy at McGill and Partners, specializing in renewable energy asset risks throughout their lifecycle. Tim has worked exclusively within renewable energy sectors for the last 13 years, dedicated to advising developers and operators in risk identification, contract risk allocation, and the placement of suitable insurance solutions for renewable energy projects worldwide, specializing in solar, onshore and offshore wind. Tim has previously worked at Willis and Aon. He has become recognized as one of the leading
insurance advisers within the offshore wind sector, having been involved in the design and placement of over 60 GW of offshore wind construction and operation across Europe, Asia and the U.S.
EDWARD STEWART is a Senior Vice President at Alliant Insurance Services, based in Seattle, Washington. Focused on the renewable energy industry, Edward works to derisk innovation, support growth and enable complex and challenging project development using insurance and risk transfer strategies to lower the cost of risk.
JUNKO UEHARA has held various positions providing remote visual inspection solutions since joining Evident Scientific in 2002. She has experience in global marketing, marketing communications, and videoscopes and their applications.
JONAS WAHLSTRÖM is Head of Product Management, Wind Converters at ABB. Jonas has more than 20 years’ experience in international business, including product management, product development, business development, and strategy development and implementation.
across the globe have embraced wind power, recognizing its potential to reduce carbon emissions and foster sustainable development.
China, the United States and Germany have all made substantial investments in wind power, while the United Kingdom, Denmark and the Netherlands are all pioneering offshore wind projects, demonstrating the immense possibilities of this clean energy source.
What’s more, the cost of wind energy has significantly reduced, enhancing its competitiveness in the global energy market. Ongoing innovations and economies of scale have resulted in reduced production
costs, making wind power increasingly affordable compared to traditional energy sources. This positive trend has encouraged substantial investments in wind projects and has motivated governments to set ambitious renewable energy targets. There are some present concerns about inflation and the availability of raw materials, but these are likely short-term phenomena.
Emerging technologies and leadingedge engineering — some of which has been years in development — is now reaching the market in practical, scalable form. Larger wind turbines, with larger capacity, can harness more
power from the wind than ever before.
But as wind turbines become larger and more powerful, their component requirements must change in order to bring the optimal benefits. Medium voltage (MV) converters are a good fit because they provide many benefits at higher power levels.
The higher voltage level of MV converters means lower currents in the electrical drivetrain, along with an easier integration of the converter into the turbine. As a result, a lower number of lighter and less expensive cabling can be used. Then these converters have a more compact footprint and are lighter in weight. They also feature high-efficiency integrated gate-commutated
thyristor (IGCT) technology, as well as an advanced control algorithm that optimizes the operation of the generator while minimizing losses. The converter’s low part count and fuseless design ensure high availability and reduced maintenance requirements. This, in turn, results in a lower total cost of ownership. All these advantages help wind park operators to achieve a good return on their investment.
In the near future, ABB’s MV wind converters will have ratings of up to 20 MW and beyond. Designed for utilityscale wind turbines, they will be able to deliver an estimated 33% uplift in power with the same number of components as their lower power predecessors.
The right choice of wind converter also has a significant impact on grid stability. Rated to handle higher power output and better able to stabilize voltage and frequency fluctuations caused by changing wind conditions, the new generation MV converters enable a higher
penetration of renewable energy into the grid without compromising on stability.
By maintaining a low part count despite delivering more power, MV wind converters’ compact nature allows for easy customization and fewer points of failure, minimizing downtime. Plus, the new generation of MV wind converters have built-in intelligent software and digital features. This enables monitoring and diagnostics to be carried out remotely, better preparing engineers for an efficient service intervention when they arrive on site.
As we strive toward a low-carbon society, increasing the availability of renewable energy equipment for use within the power grid is key. But we also need to establish how to operate this equipment as safely, reliably and, of course, as efficiently as possible. This is where rigorous testing comes
in, to ensure grid performance, stability and regulatory compliance.
Right now, the growing number, power and size of offshore wind turbines is pushing current testing facilities, and their procedures, to the limit. Yet power grids still need to maintain total stability and performance while integrating ever increasing amounts of intermittent renewables like wind and solar. That’s why more advanced testing facilities are needed.
ABB has partnered with the Fraunhofer Institute of Wind Energy Systems (IWES) to develop what’s set to become the world’s largest mobile grid simulator.
The new mobile grid simulator will assess renewable energy equipment, including components of wind turbines, in real-world conditions. Its mobile capability has the flexibility to be used in the field or on test benches to simulate dynamic and steady-state grid conditions.
The test program will verify that a renewable project connecting to a
a public power network is fully compliant with stringent local grid codes and will not compromise grid performance and stability.
The mobile grid simulator will use the ACS6080 Power Electronics Grid Simulator (PEGS) technology developed by ABB to create an artificial power grid on site. Fraunhofer IWES will use the system to simulate different grid operating modes, including fault conditions, as well as validating compliance with all standards.
Its flexible and modular structure allows for almost unlimited configuration potential. In addition to its practical testing application, the mobile simulator will play an important role in research and development, particularly for various grid-of-the-future scenarios.
As the largest of its kind in the world, the mobile grid simulator will have a power rating of up to 28 megavolt ampere (MVA) and a shorttime capability of up to 80 MVA. For additional flexibility, it will also be able to operate as two independent units of 14 MVA. In addition to the PEGS technology, the full package solution delivered by ABB will include transformers, filters, e-houses, cooling equipment and power and auxiliary distribution equipment.
Summing up
MV wind converters help wind park operators to maintain profitability by offering clear benefits, including higher efficiency, lower total cost of ownership and greater reliability, at the higher turbine power levels now demanded by new offshore wind parks.
There may be challenges, such as sourcing suitable materials to construct high-power MV converters, the availability of advanced testing facilities and supply chain delays. But heavy investment in offshore wind turbine research and development is helping to leap these hurdles, enabling the construction of even larger offshore wind turbines and even better fuel economy. This will surely speed the journey to net zero. WPE
Theglobal shift to renewable energy and expanded use of wind power has significantly increased the number of wind turbines, both onshore and offshore. The demand for wind turbine maintenance is also increasing, especially for critical components such as gearboxes. Borescope inspections of gearboxes are a cost-effective way to shorten the downtime of wind turbines and prevent early detection of defects leading to gearbox replacement.
Why wind turbines need regular inspections
Wind turbine gearboxes, generators and blades require intensive maintenance because wind turbines face significant stress and wear. Maintaining these parts helps prevent expensive repairs and downtime. Gearbox failures are relatively rare (once every 10 years on average), but wind turbine downtime can last as long as six months while waiting for this part to be repaired.
A typical 2.4-MW wind turbine generates about $1,000 worth of electricity per day, so a several-month downtime can be costly in terms of lost revenue. Gearbox failures can also cause catastrophic damage to the gearbox, such as a fire due to overheating, which could cause a turbine to permanently go out of service.
The condition of wind turbines is typically monitored using supervisory control and data acquisition (SCADA) systems and condition monitoring systems (CMS) before and after inspections are performed at the top of the tower for oil sampling and noise checks. SCADA or CMS equipment can collect inline vibration and oil data from wind turbines to predict or detect blade, main bearing and gearbox failures up to 30 days in advance of the potential failure date.
However, SCADA and CMS error information does not indicate the exact location of the defect or specify the failure conditions. Even if you receive a 30-day warning about a gearbox failure, your wind turbine could be out of service for weeks until the parts arrive. Complementing preventive maintenance strategies with remote visual inspection (RVI) equipment that looks inside the gearbox can help identify failing components more quickly and accurately.
With a nearly six-month delay in the delivery and replacement of certain
gearbox components, the sooner the required part is determined, the less downtime the wind turbine will have. In addition, knowing the status of potential failures lets you make proactive and informed decisions about parts procurement and maintenance planning. For example, regular borescope inspections during low wind season can help monitor internal gearbox deterioration and possibly prevent equipment failure.
Observation images taken with a borescope or videoscope (an advanced
borescope with video imaging) help identify deterioration and defects in specific locations at an early stage. Operators can use this data to direct maintenance activities and part replacement plans.
The interior of the gearbox consists of a series of transmissions that convert the low-speed rotation driven by the blades into a high-speed rotation that drives the generator. Components can
be damaged by vibration, foreign matter mixed in lubricating oil or excessive stress. A visual check of defects, such as fatigue, wear, corrosion and fractures, is recommended.
The planetary stage bearings and planetary gear provide support to the lowspeed shaft. The planetary stage absorbs high stress from the slow stage in variable weather conditions. The structure of the planetary gear teeth is complicated and its location within the gearbox makes it difficult to access with inspection equipment.
Intermediary stage bearings support the intermediary shaft and are located at the front and the back — directly below the other shafts. Intermediary bearings are difficult to inspect, mainly due to their location.
High-speed stage bearings are easier to access during an inspection but are more likely to be damaged due to their high speed of between 1,500-1,800 rpm. This high speed also means that damage to the high-speed bearings is more likely to affect other parts of the gearbox.
The planetary stage has two planetary carrier bearings and nine cylindrical planetary bearings. You can access the planetary stage through small hatches on the rotor side of the gearbox, usually located at around the 2 o'clock and 10 o'clock positions.
Ring gear, planetary gears and sun gear: These gears can be easily inspected with a borescope through the rotor-side hatches. You will want to check the surface condition of their gear teeth, so a near-focus, forwardviewing videoscope is recommended.
Planetary bearings: Thread the scope through the space between the planetary carrier and planetary wheel to reach the planetary bearings. Using a bent guide tube will help you prevent the lens from touching the oily surfaces inside the gearbox, and an oil-clearing lens adapter can also improve
your view. Since there are three planetary wheels, you must rotate the rotor to access the two other sets of planetary bearings.
Rotor side carrier bearings: Insert the scope between the planetary carrier and the gearbox’s rotor side wall to inspect the rotor side carrier bearings. The generator side carrier bearing inspection is sometimes difficult as it is located far from the front hatch. Try the parallel stage hatch on top of the gearbox, as some gearboxes have a large opening between the planetary and parallel stages. If that is impossible, use a long guide tube from the front hatch to reach the generator side carrier bearing. The two parallel stages have three shafts, each with one cylindrical roller
bearing and two tapered roller bearings for shaft axial load and guidance. You can access the parallel stages through the large hatch on top of the gearbox.
High, intermediate and low-speed gears, pinions and bearings: The access hatch on top of the gearbox is large enough to use a regular digital camera to take photos of these gears and pinions. However, you need a borescope to check the condition of the bearings.
High-speed shaft (HSS) bearings: These bearings are usually located near the access hatch on top of the gearbox. You can hold the borescope with your hand to insert the scope head between the roller bearings.
Intermediate-speed shaft (IMS) and low-speed shaft (LSS) bearings: Use the access hatch on the top. You will need a guide tube to insert the borescope far enough to reach them.
To perform a gearbox inspection accurately and efficiently, select a borescope with the performance and functions that match the inspection environment and purpose. Consider the following points when selecting a borescope.
The equipment inside the gearbox is covered with lubricating oil. When observing with a borescope, lubricant often gets inside the optical adapter attached to the borescope tip and makes the view unclear. Inspectors can waste half of their gearbox inspections cleaning and repositioning the scope lens. Even with a borescope that does not have an interchangeable optical adapter, lubricating oil adhering to the lens at the tip of the insertion tube causes the lens to become colored, impairing the observation performance of the borescope. As a result, inspectors will need to repair or replace the borescope.
Therefore, it is essential that the borescope used for gearbox inspection is resistant to lubricating oil and can prevent oil from adhering to and entering the lens surface and inside of the borescope tip.
The gearbox inspection requires checks for defects such as scratches, flaking and dents on the bearing surfaces, as well as defects such as cracks, pitting and discoloration of the gear teeth.
Near-focus observation is important for detecting initial defects on bearing surfaces such as micropitting. Deep observation of the entire gear is important for gear teeth inspection. Choose a borescope that meets both observation needs to perform inspections efficiently.
3. Durability suitable for bearing inspection
Borescope durability is important, as damage of inspection tools during gearbox inspection can undermine your wind turbine inspection plan. In particular, when inspecting bearings, the borescope is placed in the gap between the bearings to observe their surfaces. Physical stress tends to be applied to the scope insertion tube during this inspection, posing a risk of damage to the scope articulation section. It is recommended to choose a borescope with a durable scope bend.
4. Designed to work inside the confined nacelle
The space inside the nacelle of a wind turbine is narrow, so there is limited space for equipment placement and movement during inspections. Choose a handheld borescope that is highly portable to reduce stress during work and shorten the inspection time.
Regular gearbox inspections are a cost-effective way to shorten the downtime of wind turbines and prevent early detection of defects leading to gearbox replacement.
The scale of wind power generation is expected to continue expanding as demand for renewable energy increases worldwide due to climate change issues, the finite nature of fossil fuels and geopolitical risks. The importance of borescopes and videoscopes will continue to grow for the stable operation of wind power generation facilities. WPE
See the latest wind power developments and U.S. project news on our website. Also find expert webinars and more from the leading wind power engineering magazine today.
Wind power operators face a unique set of risks that can be effectively managed to protect wind farm assets and ensure the viability of the operation. Whether facing required upgrades to an aging equipment fleet or incorporating new technology into the operation, wind operators can plan for associated risks with the support of healthy, vetted original equipment manufacturers (OEMs) and an experienced renewable energy insurance broker.
Here are some emerging topics when it comes to managing risk in the wind energy segment and developing a successful risk management program.
In the wind power segment, the importance of vetting EPC contractors cannot be overstated. Wind energy operators should always request credentialing information from tier-one contractors and verify the contractor’s experience and track record of successful development and completion of projects.
It will prove valuable to ensure the OEM has access to a reliable supply
chain with inventory and contingency for spares, especially when sourcing components from overseas. When sourcing international equipment, wind operators should request details around the OEM’s supply chain and their contingencies around Plan B’s outside traditional domestic content. Specifically, transformer availability is currently a widespread industry issue, spanning wind farms to utility applications. Lead time is also a major consideration factor for acquiring components, from blades and nacelles to transformer batteries. It’s critical that the OEM is proactive in managing the supply chain queue to ensure the timely availability and delivery of parts when they are needed.
Once a project is underway, what capability does the OEM have to replace broken and damaged equipment? There are significant solvency and profitability concerns around major OEMs in today’s wind market. As wind assets come out of warranty, how does the solvency of OEMs impact the validity of warranties and the likelihood that the manufacturer of components will be sustainable to honor those
warranties? From the carrier perspective, they are concerned with the validity of warranties going forward, which will be reflected through the underwriting process. M&A activity presents an additional challenge and whether acquired OEMs can remain financially viable to fulfill their provided warranties.
Technology is spurring advancements across all industries, and the wind market is seeing the rapid evolution of larger turbines and blades. It’s important to stay ahead of the insurance and risk management factors associated with technology evolution to ensure new projects continue to be insurable at economic levels.
Considering the overall field experience of newer, larger parts, carriers may have concerns that as projects grow larger, so too does the possibility for greater downtown caused by losses. For OEMs producing newly constructed parts, this circles back to the importance of vetting — will the OEM remain viable to satisfy their obligations to the buyers of their equipment?
As smaller wind fleets cross multiple decades in production, this aging equipment may require repowering action, which brings its own insurance considerations. For instance, to utilize newer technology-driven equipment, one may need to upgrade foundations for a 4-MW turbine vs. the older, 2-MW model. When upgrading equipment for aging fleets a broker can spec the correct coverage to support the associated engineering upgrades.
As weather events grow more significant in scale and in their levels and paths of destruction, an experienced insurance broker can determine how to value wind project equipment. Tornadoes present an increasingly frequent threat to wind farms, especially in susceptible areas. Lightning protection is also crucial, and lightning protection systems should be installed to protect against catastrophic fires. Wind power operators typically take a broad-brush approach when determining estimated costs for replacement
and expected business interruption. Wind customers specifically need to account for coverage for each equipment component under the policy, as they may run into issues when trying to file a claim for a single turbine, for instance.
Insurers may try to cap the cost of what a wind operator can declare in the statement of values (SOV). It’s important to have discussions around policy language when forming the original SOV to ensure proper coverage in the event of a claim — whether it’s one turbine or a whole site.
Alliant’s renewable energy insurance experts help ensure customers in the wind energy segment can secure ironclad renewable energy insurance coverages that address the unique risks facing each operation. From traditional solutions to a full range of innovative specialty solutions custom designed for the renewable energy space, Alliant provides seamless project coverage, from inception to completion and continued operation. WPE
ZF is a global technology company supplying gear systems for vehicles and industrial technology. ZF Wind Power designs modular gearbox platforms and produces complete powertrains for wind turbines. Sivakumar Jayapal, Chief Service Officer at ZF Wind Power, talks with Windpower Engineering & Development about its new interactive service Thrive.
Below is an excerpt of ZF's Wind Spotlight with Windpower Engineering & Development, but be sure to listen to the full episode on your favorite podcast app.
What is Thrive, and what does it stand for?
Thrive is ZF Wind Power's new service brand, which we launched in 2022. As a global leader in the wind industry for the gearbox and powertrain, we aim to empower a sustainable future with our partners by our service offerings. Our unique service concept helps our wind park operators, consumers and customers to get the most from the wind power to generate limitless green energy. “Thrive” means to prosper, to be fortunate. We embody that definition to the power of our service. For us, service is not reactive, but rather being proactive. It is not only about maintaining and keeping the wind turbines alive, but about continuously optimizing to thrive and prosper.
What does Thrive’s tagline ‘For continuous availability’ mean?
With Thrive, we strive for continuous availability for our partners and their wind projects. Thanks to our customercentric mindset, availability of the gearbox and the spare parts along with our global footprint, we can ensure the wind power continues to reach consumers 24/7 through the year.
How do you guarantee this availability? Thrive offers a complete service package. We bundled everything together, including worldwide field support, workshop repairs in 90 days, global replacement pool, spare part management, and we also train our partners. All these are supported by our unique digitalization approach, a service powered by analytics. This includes different digital offerings like ZF’s customer dashboard, intelligent powertrain, spare part optimization. We also work as partners with our customers and tailor our offerings to their preference. That’s key because it's not that they have to get the full package. There is no standard or a fixed approach. We always develop a personalized package together with our partners, which suits their business model, they have a choice to select in any six of our offerings.
What do you mean by ‘Services Powered by Analytics’?
This is a unique concept of the digital support for Thrive. The state-of-art analytical tool combines the data from the gearbox manufacturing and the lifecycle monitoring with advanced reliable models to enable the spare parts optimization. Spare parts are replaced on a plant, should they need maintenance, before the turbine suffers
any downtime. This guarantees multiple benefits like reduced downtime, fast return to operation, increased availability and more energy production from the wind turbine without compromising the operational lifetime. In fact, our predictive maintenance philosophy actually extends the lifetime of the gearbox. This helps to reduce the levelized cost of energy. The combination of the low-cost, optimized energy output per wind turbine and extended gearbox lifetime contributes to a significant low overall cost of ownership for the wind farm in the coming years.
Thrive offers an international pool for its partners. This gearbox pool contains new and refurbished gearboxes from all major brands and multiple turbine models. Using the digital Thrive platform, customers can go into zfthrive.com and order a gearbox of their choice, which will be shipped within five days. The gearbox pool provides many opportunities for our partners such as low personal stock, less downtime and replacement gearboxes when a gearbox needs service. WPE
2023, the offshore wind insurance market will support over 5 GW of offshore wind construction along the U.S. East Coast. Considering the existing development pipeline in the United States, this number is expected to grow to approximately 50 GW within 10 years. While considered an emerging sector in North America by many, the reality for many insurers is that this is a well-established industry they’ve been supporting for over 30 years — albeit the entire project in 1991 was 11 MW using 450-kW turbines. The insurance market has played a critical role in this growth by providing coverage to operators, contractors, finance parties and suppliers and offsetting risks from stakeholders’ balance sheets. Traditional insurance products purchased to protect
is expected to grow to approximately 50 GW within 10 and offsetting risks from stakeholders’ balance sheets. these parties predominantly cover three key areas:
1. Property damage to the wind farm,
2. Revenue loss at the wind farm resulting from property damage and
3. Liability associated with third-party property damage, death and/or bodily injury during the construction or operation of wind farms.
The insurance market providing these coverages
is extensive, with the appetite of over 50 insurers to provide capacity. Over the last 10 years, these property damage and revenue loss to wind farms, where amount received in premiums. These claims have and can be attributed to the following root causes: Planning/execution errors: The industry’s rapid growth has led to larger equipment and vessels, operations in deeper water depths and increased
insurers have paid substantial claims associated with including many where the claim value exceeded the been mainly attritional rather than large one-off losses distance from shore each year. As a result, it is perhaps inevitable that mistakes will be made as the industry learns. This steep learning curve is particularly evident in projects built in new locations or in countries with
in projects built in new locations or in countries with
no prior offshore windfarm exposure, using new technologies or installation methodologies and involving new operators, contractors and suppliers.
Errors are one of the key reasons insurance is ultimately purchased, to protect those parties against the losses associated with such mistakes. However, insurers will not accept corner cutting, lack of due diligence and weak quality assurance/quality control. To keep insurers engaged, the industry must demonstrate that lessons are learned from each
instance of negligence, and steps are taken to prevent recurrence. In some cases, this has happened. In other cases, “learning” has taken longer, like with cable installation, and insurers have had to take definitive actions to address claims being made, by increasing deductibles, implementing stricter marine warranty surveyor protocols or limiting coverage in specific areas or for specific perils.
Defects in design: Wind turbines have gotten bigger, foundations are longer and heavier, cables have lengthened
and shifted to higher voltages and direct current circuits, and offshore substations have reached the size of football stadiums. With this evolution, there have been examples of the technology containing defects in design. These defects range from series-wide basis (gearbox issues on a certain wind turbine model), issues impacting the entire industry (cable protection systems) or one-off defects (a specific manufacturing defect bespoke to a project). In each of these cases, insurers have played a crucial role in compensating
the affected party, alongside warranty provisions provided by the supplier.
In the current challenging supply chain environment, risk allocation between the insurer, the operator and supply chain will remain difficult to agree upon. In addition, gaps may emerge if parties wish to engage with insurance advisors without significant offshore wind experience, insights and a track record of designing and placing offshore wind insurance solutions over the last 10+ years. Allocating risks to the party
best able to manage them is crucial, as insurers cannot be the sole backstop for warranties or technology evolution.
Weather: Most weather-related losses in offshore wind have been caused by operating in extreme offshore conditions, such as a vessel caught in a difficult sea state during cable installation. However, the biggest concern for insurers as offshore wind goes into new territories across Asia and the United States is the projects’ exposure to natural catastrophes such as hurricanes and earthquakes.
While the industry hasn’t experienced significant natural catastrophe losses to date, the data shows that weather patterns are becoming more extreme, leading to significant losses across insurers’ broader portfolios. For example, global (re)insurer Munich Re confirmed that global H1 insured natural catastrophe losses exceeded the 10-year average of $34 billion, hitting $43 billion in 2023.
The development of typhoon class (T-Class) wind turbines is a necessary and important step, but the reality is that the
data is still limited on the survivability of offshore wind farms in extreme weather-related events. Insurers face challenges due to their lack of modeling data specific to such extreme weather. For years, insurers have relied on weather models to set their limits and pricing. However, these models do not consider the specifics of offshore wind. As a result, insurers rely on onshore calibrated models, which can lead to potentially inaccurate results. Insurers need to consider their exposure at both a single offshore wind farm site, and their accumulation to a large area of offshore wind activity such as the U.S. East Coast. As their accumulation grows, their ability to deploy capacity will be reduced and the supply/demand balance will shift into more expensive natural catastrophe capacity for the industry. Understanding offshore wind’s resistance to earthquake is even less understood. Therefore, as floating fixed projects are developed in locations like California, there is a lot of work still to be done before insurers will deploy significant capacity.
In addition to the industry-wide features outlined above, the U.S. offshore wind industry faces additional challenges that are inherent to a new offshore wind geography. The restrictions to vessels and crew imposed by the Jones Act require alternative installation methodologies. These alternative methods introduce additional interfaces beyond the traditional scope of offshore wind farm installation (e.g., the use of feeder barges). Insurers are closely examining these activities and the implications to the overall risk profile of a project. Limitations in the capacity of the offshore wind industry supply chain, especially regarding vessel availability, are expected to increase lead time of components and overall repair time in the event of a loss. This has an immediate impact on the insurance market’s exposure to revenue losses, and insurers are looking carefully at this exposure and trying to limit their liabilities through cover restrictions and/or increases in deductibles. Additionally, supply chain constraints would impact repair costs, with higher expenses in the United States compared to Europe (known as claims inflation). This has an impact in the total amount of medium/large losses but also in the number of smaller losses that can potentially exceed the deductible, which is driving insurers to increase deductible levels for U.S. projects. While the development of
a local supply chain is welcomed as it should have a positive impact on lead times and replacement costs, this is also perceived by insurers as an increased risk due to the potential lack of experience of the workforce around the local content.
The insurance market is very well positioned to support the emerging U.S. offshore wind industry, as it has done for many countries and developers moving into new locations, but insurers cannot be expected to assume all the risks associated with errors, defects in design and extreme weather. Along the U.S. East Coast, adapting to intensifying hurricane events is inevitable. The supply chain needs to work closely with developers and insurers to be transparent about the technologies design tolerances to such events, working closely with modeling companies and associated analysts to ensure insurers can adequately review and manage their exposure, to charge reasonable, consistent and sustainable premiums for such perils.
If the United States and developers intend to move into locations like the Gulf of Mexico, this becomes even more acute. The current supply chain is not designed to robustly survive hurricanes, which frequent the Gulf of Mexico each year at Category 4 and Category 5. As a result, insurers will not provide capacity until facilities are designed to such wind speeds. Therefore, the key to insurance (and consequently financing) comes from the supply chain’s ability to give insurers comfort that the technology they are supplying can withstand environments like that of the Gulf of Mexico. In addition, comparison must be drawn with the oil and gas operators in the Gulf of Mexico who have self-insured the exposure of hurricanes for many years due to the cost and extremely limited capacity offered by insurers in the Gulf for these weather events. Offshore wind developers and the supply chain must proceed on the assumption that this will be the case for offshore wind as well if they do operate in this location. When a risk is present that is so significant like natural catastrophe perils, it needs to be shared. If the offshore wind industry is to grow at the projected levels, insurers cannot be expected to hold these extreme weather risks on their own. An open and ongoing dialogue among developers, operators, supply chain and finance parties, including insurers, is necessary to find a balanced allocation of risk between the interested parties. WPE
LEADERSHIP TEAM
VP of Sales
Mike Emich 508.446.1823 memich@wtwhmedia.com
Managing Director Scott McCafferty 310.279.3844 smcca erty@wtwhmedia.com
EVP
Marshall Matheson 805.895.3609 mmatheson@wtwhmedia.com
SALES
Jami Brownlee 224.760.1055 jbrownlee@wtwhmedia.com
Ashley Burk 737.615.8452 aburk@wtwhmedia.com
Publisher Courtney Nagle cseel@wtwhmedia.com 440.523.1685
CFO
Ken Gradman kgradman@wtwhmedia.com 773-680-5955
Jim Powers 312.925.7793 jpowers@wtwhmedia.com
WTWH Media's webinars offer:
- Coverage of a wide range of topics
- Help engineers better understand technology or product related issues and challenges
- Present educational material related to specific topics
The STX40 is the most powerful and modern portable fault location system on the market. It is ideal for testing, analyzing, pre-locating and identifying faults in low voltage and medium voltage extruded cables insulated with XLPE and EPR. The lightweight and rugged construction make the STX40 ideal for challenging environments and the compact size provides increased mobility in adverse terrain.
Learn how to improve your testing strategy and return equipment to service quickly in this newly released case study. Scan the QR code or visit: https://us.megger.com/stx40