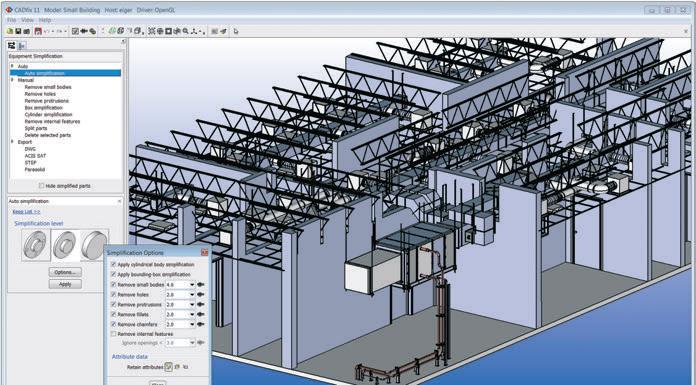
12 minute read
CADfix PPS
With a reputation for solving the most challenging 3D geometry wrangling problems, ITI takes on the process plant workflow with its new, easy to use CADfix PPS system, writes Al Dean
When it comes to process plant there are key data translation issues that are regularly encountered across the entire industry. Many of these are caused simply by the sheer size of the datasets typically found in process and plant design.
Consider what the typical dataset contains; framework, skids, equipment assemblies, sub systems and all of that glorious pipe work. If each area of work is held in its native, unsimplified and full resolution form, we could be talking about 100,000s of faces and gigabytes of data. However you cut it, whatever format you use, this is going to cause problems when you’re looking to communicate and collaborate based on that data.
Then you have the requirement of the different design systems used by various teams and disciplines. Moving data between 3D design systems is fraught enough, but trying to shoehorn a gigabyte of data from one system to another can provide more than a few headaches.
It’s into this arena that International TechneGroup (ITI) has recently launched its CADfix PPS system (PPS standing for Plant and Process Simplification). If you haven’t come across ITI and its CADfix tools before, the global firm has an excellent reputation for providing robust and reliable tools for data repair, repurposing, translation, migration and validation for some of the biggest names in manufacturing.
The first stage in the CADfix PPS process is to read in your dataset. Here, ITI’s experience and long-standing relationship with all of the major vendors pays dividends as the import options are pretty rich. You have the usual array of standard formats, including DXF/DWG, STEP, JT, ACIS and Parasolid. There are also a range of good quality native formats including Catia, Creo, Inventor, Siemens NX, SolidWorks as well as CADDS 5i (a legacy system that is still particularly useful for those in the shipbuilding game).
CADfix PPS is able read in and quickly display these datasets, even in the large, complex forms that they typically arrive in.
2
Reducing complexity Once the data is loaded in, the system can be used to remove detail by either deleting or simplifying parts or sub-assemblies to reduce the complexity of the data.
This can happen in one of two ways. Firstly, there are a set of pre-baked, ready to go simplification routines in the CADfix PPS automatic simplification Wizard.
The system can quickly find and remove small parts based on bounding box size (useful for dealing with those assemblies that feature every last nut, bolt and washer). You can also select a part of a certain shape and size and have the system find matching components (useful for dealing with those non-standard components or those that you know you don’t need).
Perhaps one of the most useful tools is the automated removal of internal details. This will inspect your model and find parts or assemblies that contain internal detail which can’t be seen from the outside; consider the internal working of a pump assembly, complex motor or generator, or a small portacabin full of equipment that is not required or seen in the
1 Building model imported into CADfix PPS 2 CADfix PPS display clipping shows internal detail removed from upper container 3 Cooling towers in CADfix PPS

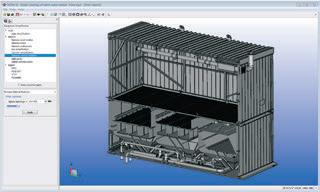
overall layout model for clash detection. carried out manually to provide more con- Conclusion The operation will automatically remove trol over the simplification process. CADfix PPS is a gloriously focussed all of that internal detail, rapidly reducing Once you have arrived at your stripped application. Its goal is to enable the the complexity and size of the data. back, lightweight model, you’ll need to be removal of any extraneous complexity
As well as the removal of whole chunks able to export it to your system of choice. from increasingly complex data and of geometry, CADfix PPS also includes Once again, ITI’s expertise in the data reach a more efficient, more lightweight several tools to help remove geometry translation field comes into play. CADfix model that still conveys the intent to detail (rather than whole parts). There PPS comes with export options for ACIS solve the downstream challenges faced are tools to assist with the removal of holes or bosses as well as design features such as fillets and chamfers. Alongside the automated ‘‘ Moving data between 3D design systems is fraught enough, but trying to shoehorn a by industry. The results, which ITI says can see up to a 95% reduction in data complexity after only a few minutes’ work, tools for the removal of data, gigabyte of data from one system to another will enable your team to there are also a number of operations that can assist with can provide more than a few headachese work more efficiently and get the mission critical data further data reduction through the simplification of complex geometric shapes. In many cases complex (.sat), DXF/DWG, STEP, JT and ’’ to those that need it, in a lightweight optimised form that suits their purposes. equipment represented in mechanical CAD Parasolid. The company is also exploring With ITI’s background of doing this models with the level of detail required for the potential for exporting to a range of for decades in the manufacturing space, manufacturing, can be replaced with sim- faceted model representations such as you know it has the tools to do it in a ple bounding boxes or cylinder primitives the FBX format, that seems to be gaining reliable, robust and repeatable manner. for use in the building layout. These tools some traction in the process plant space, First class stuff. can be used in an automated manner or as well as STL, OBJ, and XGL/ZGL. ■ tinyurl.com/CADFIX-AEC
These are the essential BIM skills you need
Our set of professional BIM training courses offer you expert education and understanding of digital construction methodology – whether you are working domestically or internationally.
BIM Fundamentals BIM for Executives BIM Management ISO 19650-1 and 2 Concepts
Courses are available in the UK and Australia as classroom based and will be available online from 2018.
To find out more, visit digital-node.com/courses.
www.digital-node.com info@digital-node.com +44 (0)203 871 3377 (UK) | +61 420 212 249 (AU)
The connected future
George Broadbent and Dr. Xifan Jeff Chen of global AECO technology consultancy Microdesk explore the potential for connected operations in asset management, harnessing the power of BIM, digital twins, IoT and deep learning
Asset Management essentially is a cost-effective, systematic process of managing assets. It is however, this promise of cost management that is creating market pressure for owners and facility operators to implement an Internet of Things (IoT)based solution. Connected Operations, which is designed to improve the operational efficiency of physical assets, serves as a critical component to complete the root definition of Asset Management.
Connected Operations is developing from a compelling concept used in manufacturing to an AECO industry-wide process. The benefits of Connected Operations implementation include enhanced interoperability efficiency, faster implementation speed, and optimised operation safety. It is triggering the development of several up and downstream sectors, like risk management, supply chain management, and manufacturing services. Connected Operations is stimulating the development and integration of state-of-art technologies such as IoT, Artificial Intelligence, cloud computing, Machine/Deep Learning, big data, and Augmented Reality into the Asset Management process.
Connected operations advances The rapid growth of Connected Operations is a result of both internal and external factors. The AECO industry has been craving new technologies and solutions to increase operational efficiency and enhance asset performance. IoT-led data-driven technologies have sprung up to enable real-time visibility for organisations to overcome these challenges. Cost reduction is another critical motivator that is pushing Connected Operations forward.
The introduction of IoT plays a significant role in redefining the term “connected” in this process. More controllable operational reliability ranks at the top of the capabilities of IoT-enabled Connected Asset Management. Although it is still mission impossible to fully predict operational reliability due to any number of uncertainties, industry as a whole is getting one step closer to utilising the power of IoT-driven data analysis.
Sensor-equipped connected assets automatically log machine performance and operation status. This data is recorded and analysed via a
Computerised Maintenance Management System (CMMS) in combination with cloud-based AI systems to make predictions on system performance. When this is compared to the traditional fixed maintenance schedule (i.e. calendar based), IoT-enabled preventive maintenance can lower operations and maintenance (O&M) costs significantly, while taking maximum advantages of human resources. IoT “weaponises” the existing Connected Operations with a state-of-art data-driven core, to diminish the boundary between tangible assets and their intangible digital constructs. In addition to scheduling preventive maintenance, data collected from connected assets can be used to perform a failure analysis targeting the root cause of unplanned downtime to improve performance in the future. Big data, the idea that the world is replete with more information than ever, is now gradually reshaping existing asset management from passive to a proactive and more sustainable mode.
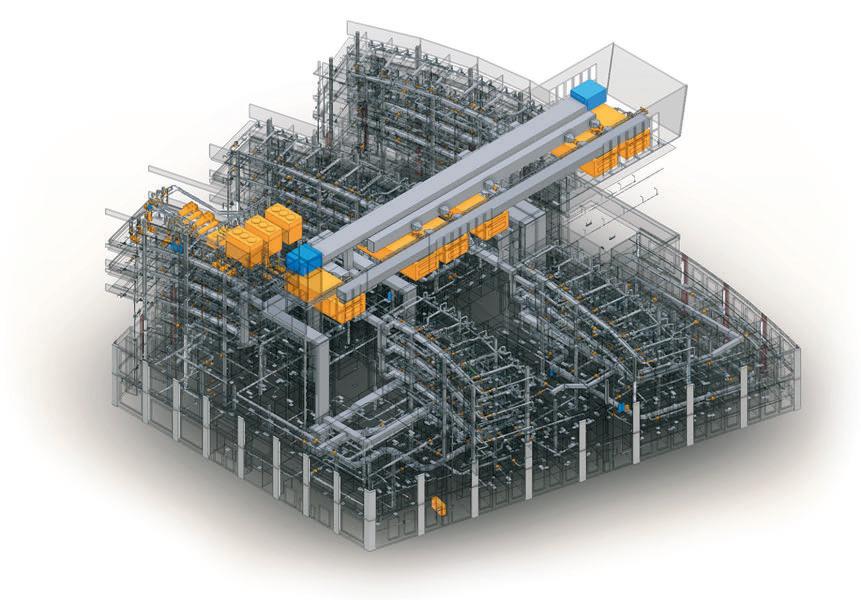
Data leads to major changes The world is converging due to the trends of merging of technologies withinand between-industries that have been changing the way people work, communicate, and interact with the physical world. Data-driven
Connected Operations reveals enormous possibilities to collaborate with other state-of-art technologies. The Artificial Neural Network (ANN) based deterioration model has been widely used in failure analysis, while emergent Artificial Intelligence (AI) became a stronger challenger because it offers more accurate schedule predictive and proactive maintenance of assets. With the availability of big data from connected assets, machine learning can be utilised to detect patterns hidden in collected data to produce actionable insights to increase the accuracy of prediction and benefit decision making.
Looking into the upstream industry, Building Information Modelling (BIM), instead of being described as a threedimensional model, is a pure data presentation of built assets. The nature of datadriven decisions makes BIM and Connected Operations highly compatible and complementary. While owners and
operators were struggling to find a solution to reduce interoperability inefficiency, the BIM and CMMS integrated process emerged from obscurity as an organic workflow. They carry data over through planning, design, construction, commissioning, and into the operations and maintenance stages.
The National Institute of Standards and Technology (NIST) examined US capital facilities and determined that organisations spend $0.23 per square foot annually due to interoperability inefficiency. A well-established as-built BIM model or digital twin that captures as asset information post construction and maintains data consistency and integrity could fundamentally reduce this cost. A BIM and CMMS integrated implementation could follow up to minimise the remaining expenses of interoperability inefficiency.
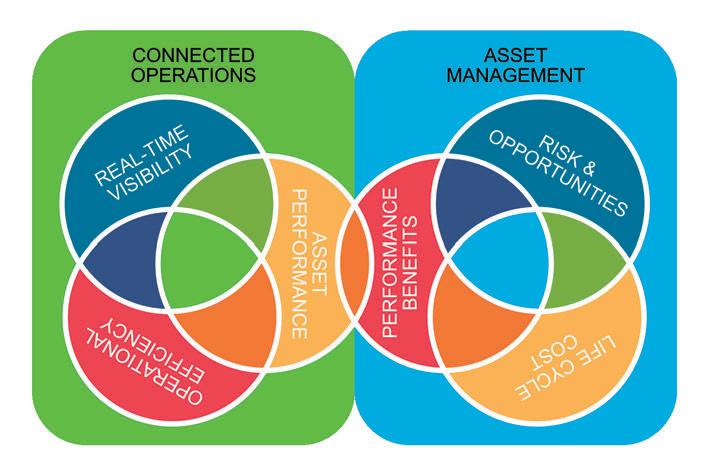
Aligning technical challenges Cycle Benefit/Cost Analysis of Connected tive through real-time alerts, short Although IoT and other Connected Operations exhibits promising a produc- response times, and predictive mainteOperations related strategies and technol- tive Benefit/Cost Ratio (BCR), ROI and nance. It also dramatically expands the ogies carry tremendous potential to Payback Period, it is still a key factor scope of traditional asset management to reshape how asset management is utilised keeping clients from understanding the embrace state-of-art technologies inside for facilities, it is not free from challenges. system at the very beginning. Besides, and outside the AECO field. All stakeholders involved in the policy, execution, adaptability, and other Looking ahead, the future development Connected Operations process must work external influences that also indirectly of AI-based cognitive computing and together to understand the methodology positively or negatively impact system Machine/Deep Learning offers the real to maximise the efficacy of the solution. implementation, it is becoming an accept- promise of more accurate schedule preThis requires coordination between facili- ed method to implement Connected dictive and proactive maintenance of ty operations, IT and business leaders. Operations from the Enterprise Level. assets. The scope of Connected The relatively steep learning curve deter- Once applied, IoT-enabled Connected Operations has been expanded to mines the degree of implementation and Enterprise Asset Management (EAM) embrace the data flow from design stage further affects the system performance. From another point of ‘‘ The future development of AI-based cognitive to supply chain. As the rapid deployment of BIM in the AECO industry continues, view, this emerging topic draws attention to the com- computing and Machine/Deep Learning offers the integration of BIM and CMMS will be better conplexity of maintaining the the real promise of more accurate schedule nected by a unified code and consistency, integrity, and interoperability of data col- predictive and proactive maintenance of assets standardised constructionasset data flow. This will furlected from all sources. It became even more complicated when dealing with roll-in and roll- provides a robust environment for ’’ ther accelerate data exposure and benefit data usage in the asset management stage. out of new data formats and old data for- achieving exceptional value from assets. The Enterprise Asset Management secmats, as well as several different data tor has been described as “the single, bigformats. Potential scenarios include Technology of the Future gest controllable expenditure on the having the ability to merge BIM data Connected Operations is paving a high- planet.” IoT-enabled, data-driven with existing two-dimensional records way to the future with the data of today Connected Operations is fundamentally in CMMS or trying to relate data inputs as the roadbed. The advent of IoT- changing the way that traditional asset from an upstream BIM as-constructed enabled Connected Operations is driven management has been utilised for genermodel with collected IoT data in a bidi- by the industry pressures for operational ations. With this new vision, Asset rectional way. efficiency enhancement, and the gradua- Management, the systematic process of
From a financial perspective, tion of IoT technology from academia to developing, operating, maintaining, Connected Operations may lead to rela- the industry. upgrading, and disposing of assets costtively high capital costs for system imple- IoT-enabled Connected Operations effectively, has been pushed to the forementation, sensor and monitor installa- does everything that traditional solutions front of the trend, and will most likely tion, as-built model and data collection, do while adding intelligence to make hold that position for a very long time. and labour training. Despite the Life existing workflows adaptive and proac- ■ microdesk.com
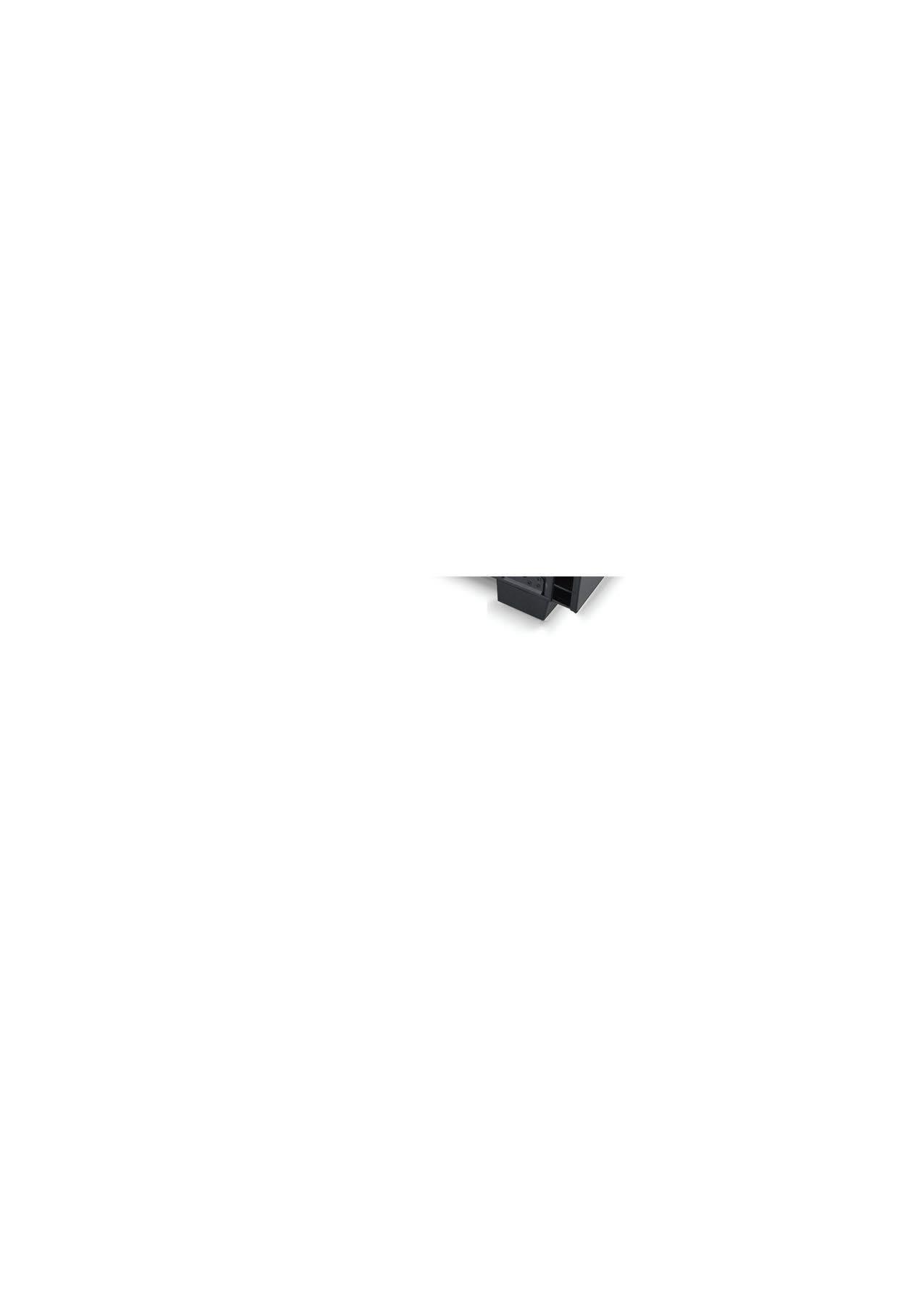

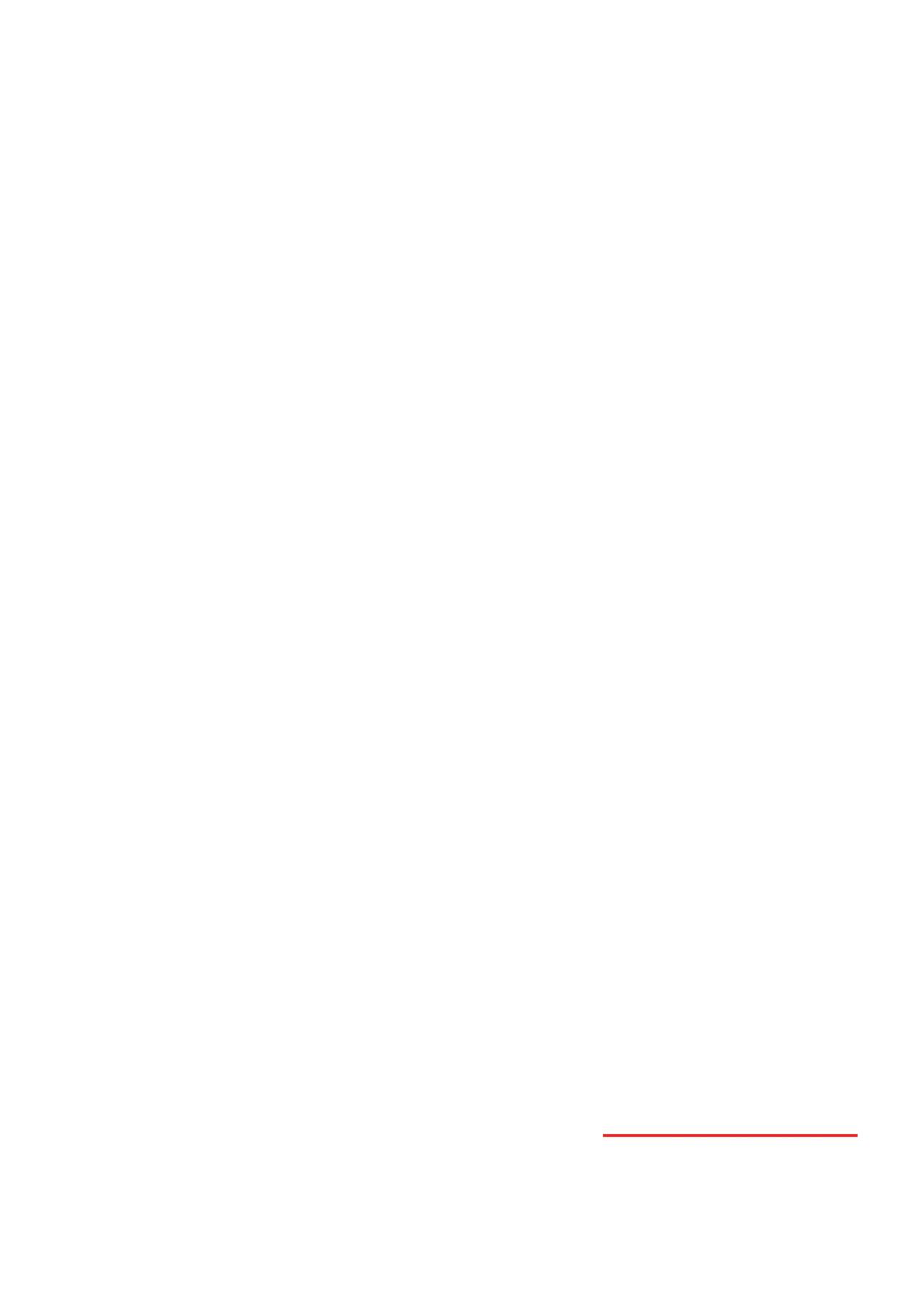
POWER TO ARCHITECTS
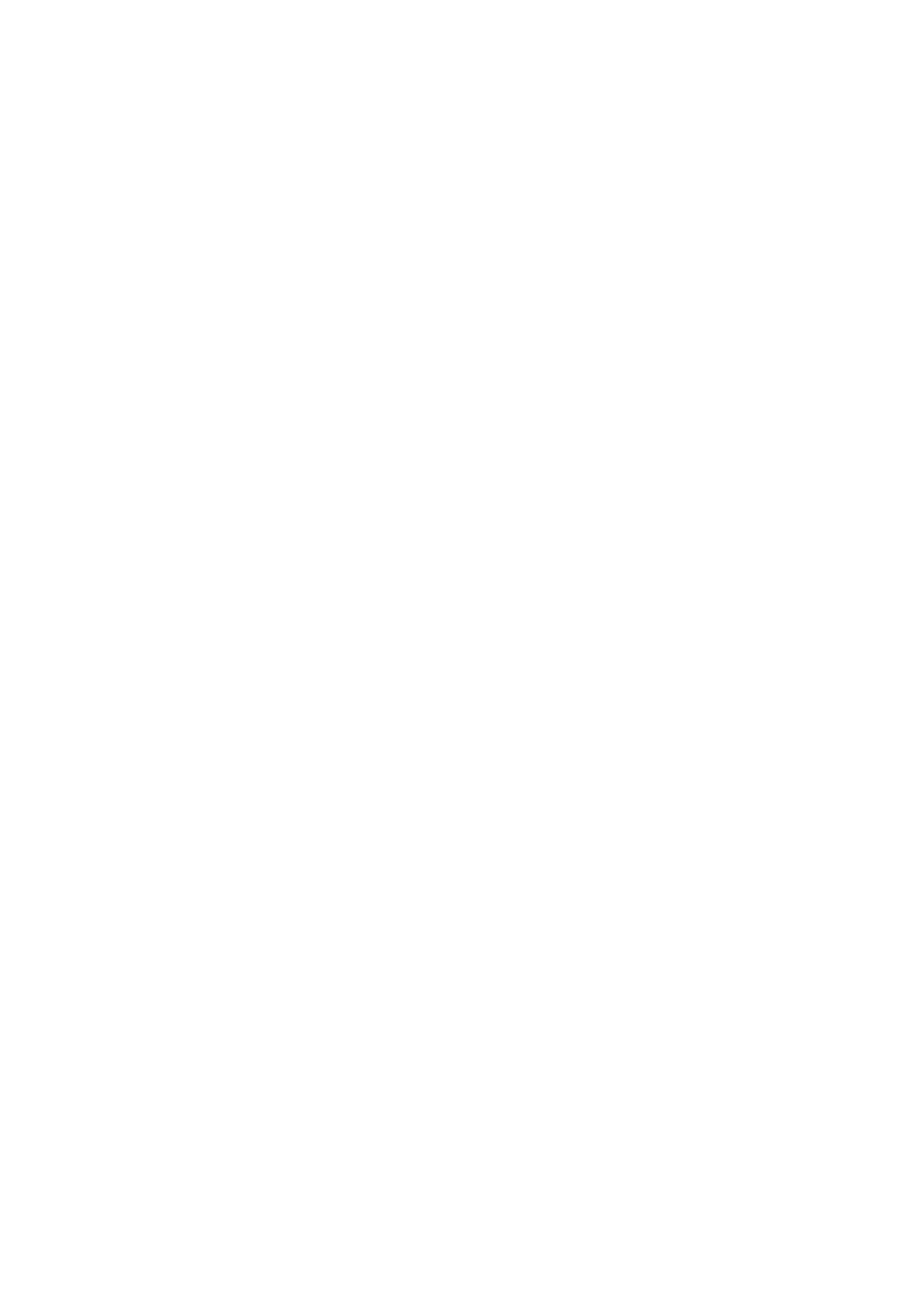
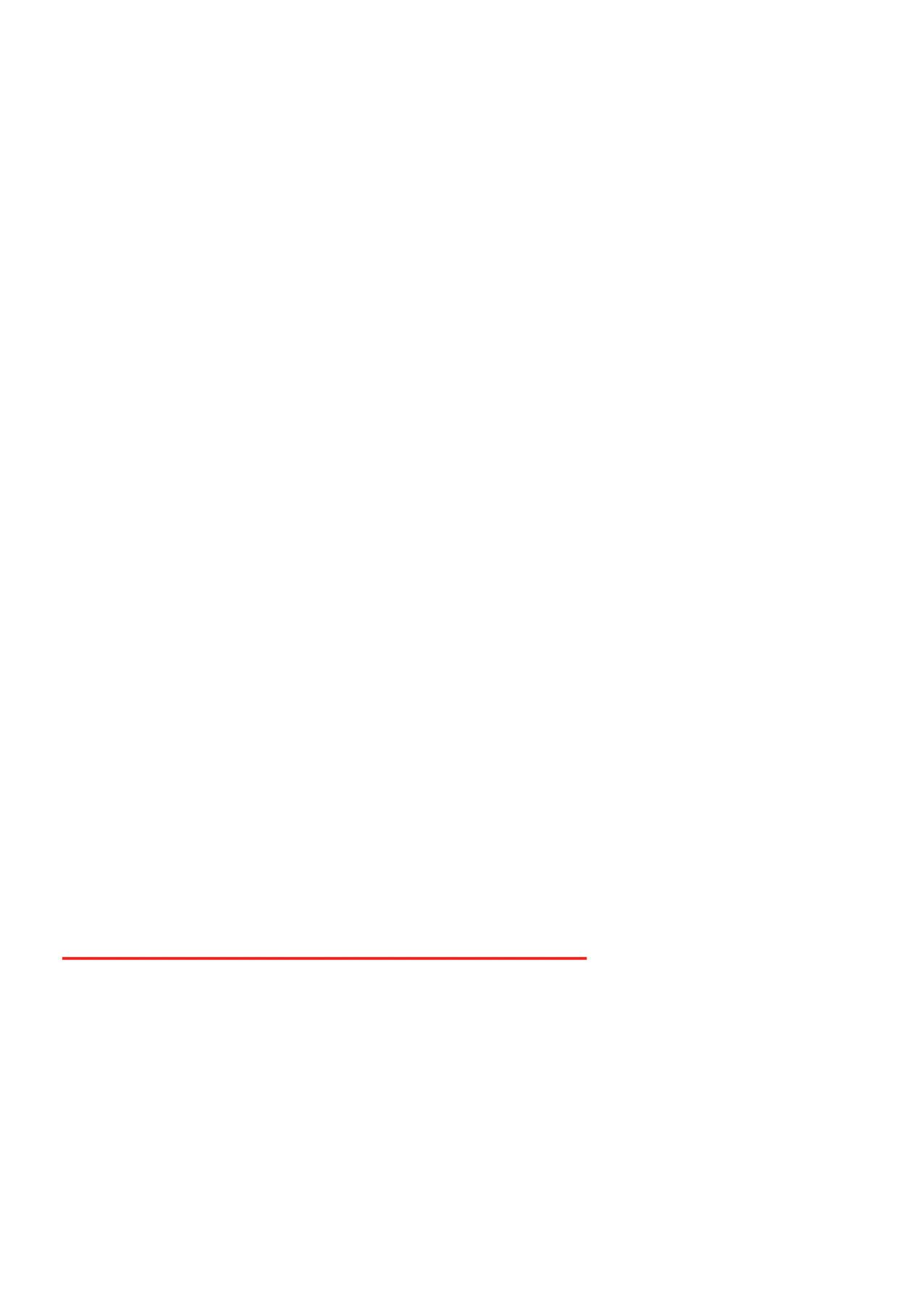
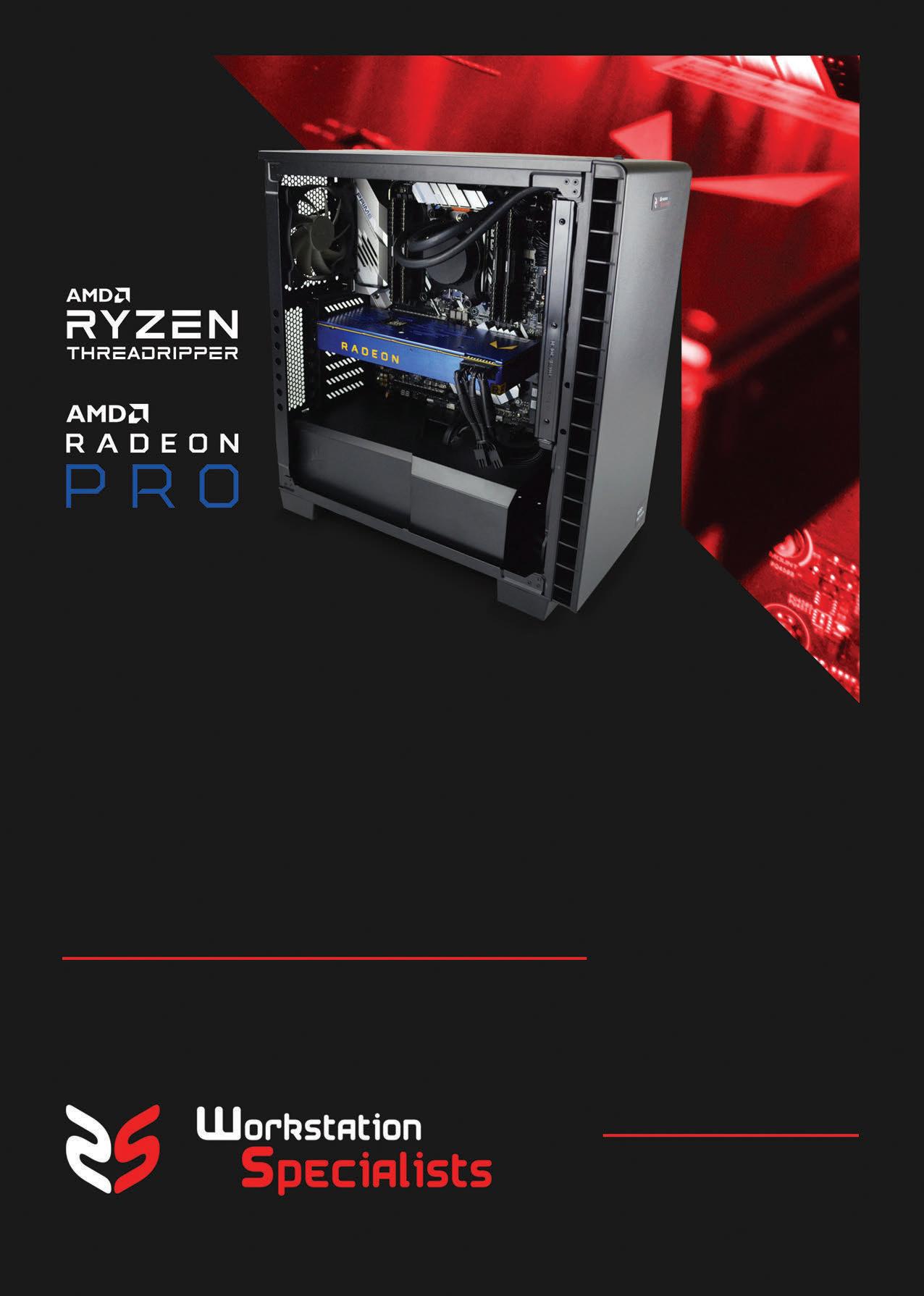
CUSTOM PROFESSIONAL WORKSTATIONS POWERED BY AMD GRAPHICS AND PROCESSORS. BUILT FROM THE GROUND UP FOR OPTIMISED PERFORMANCE AND ROCK SOLID RELIABILITY.
REGISTER FOR A 7-DAY EVALUATION SYSTEM BY VISITING:
www.workstationspecialist.com/power-to-visionaries
Why AMD? Work or Play. Threadripper has the power to overwhelm your most daunting workloads, with TM up to 16 cores and 32 threads for lightning-fast creative workloads. The new Radeon Pro WX series of TM graphics solutions are designed for professionals pushing the boundaries of technology and engineering.
CONTACT A REPRESENTATIVE