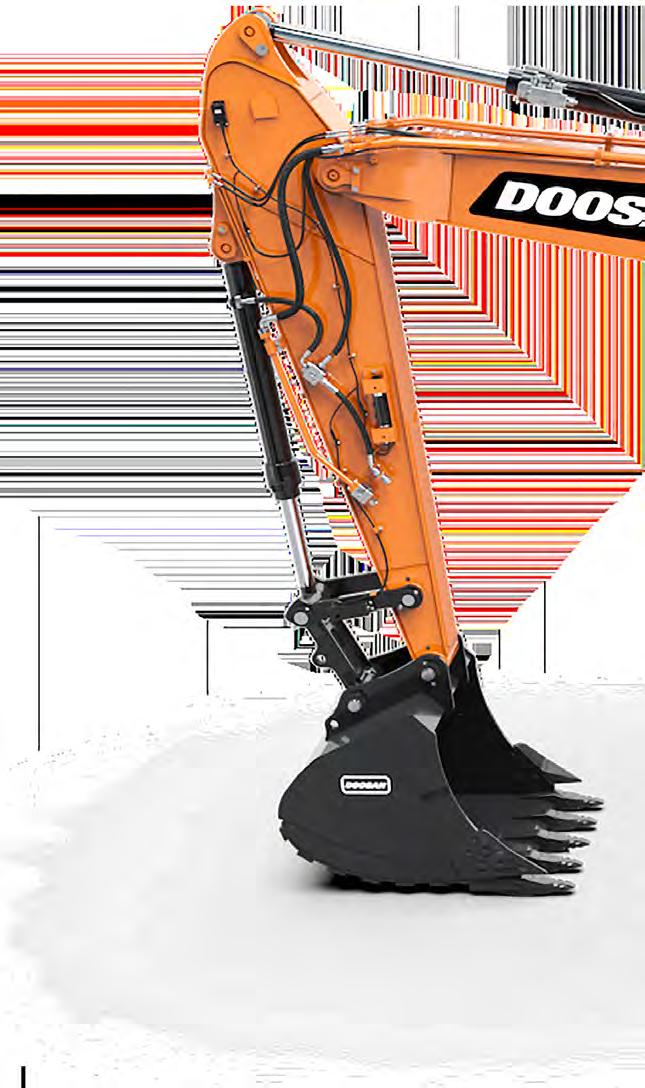
7 minute read
Doosan’s First ‘Smart’ Excavator
Doosan has launched the new DX225LC-7X - the company’s first ‘Smart’crawler excavator, designed to help operators work faster and more efficiently. To facilitate this, the DX225LC-7X offers a number of exciting new features as standard, including Full Electric Hydraulic (FEH) technology.
Doosan excavators are well known for offering more innovativefeatures as standard than other machines on the market.In the standard DX225LC-7 model and the rest of the new Doosan DX-7 medium-sized excavator range, for example, the new features provide major enhancements in machine controllability, versatility, operator comfort, uptime and return on investment, with a strong focus on increased productivity and robustness. But the new DX225LC-7X smart model takes this to a new level. As well as the FEH system, other standard features of the DX225LC-7X include Integrated 2D Machine Guidance; SemiAutomatic 2D Machine Control; Laser Receiver; E-Fence Virtual Wall; and Weighing System. Full Electric Hydraulic (FEH) technology is similar to the D-ECOPOWERVBO (virtual bleed off) system now incorporated on the standard DX225LC-7 model and all Doosan crawler excavators from the DX350LC-7 and above. In effect, the FEH is a VBO system without pilot pressure lines. The joysticks and pedals are fully electric, but give the operator the same feeling as hydraulic joysticks. In the FEH system, an electric signal is sent to the central controller and as such is more precise and provides faster information. Back pressure and energy loss are therefore eliminated, by delivering the exact amount of oil needed. As the system does not utilise pilot pressure, energy is saved and there is a resultant fuel saving. In fact, the FEH system offers a very significant 8% less fuel burn compared to the D-ECOPOWER VBO system. This is on top of the 7% decrease in fuel consumption already achieved in the standard DX225LC-7, compared to the previous DX225LC-5 model. MACHINE GUIDANCE
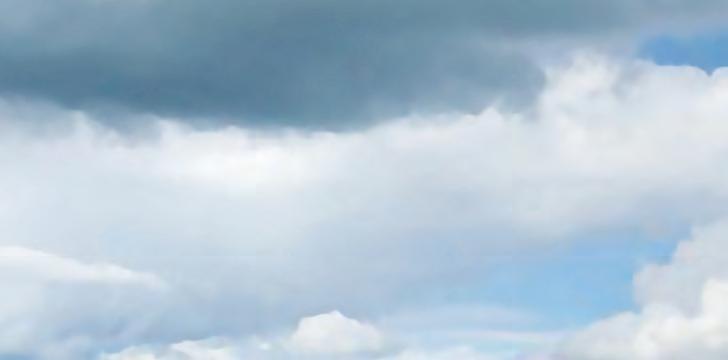
The integrated machine guidance systemon the DX225LC-7X uses sensors mounted on the front and body to recognize the location of each working device andinform/ guide it for the operator.
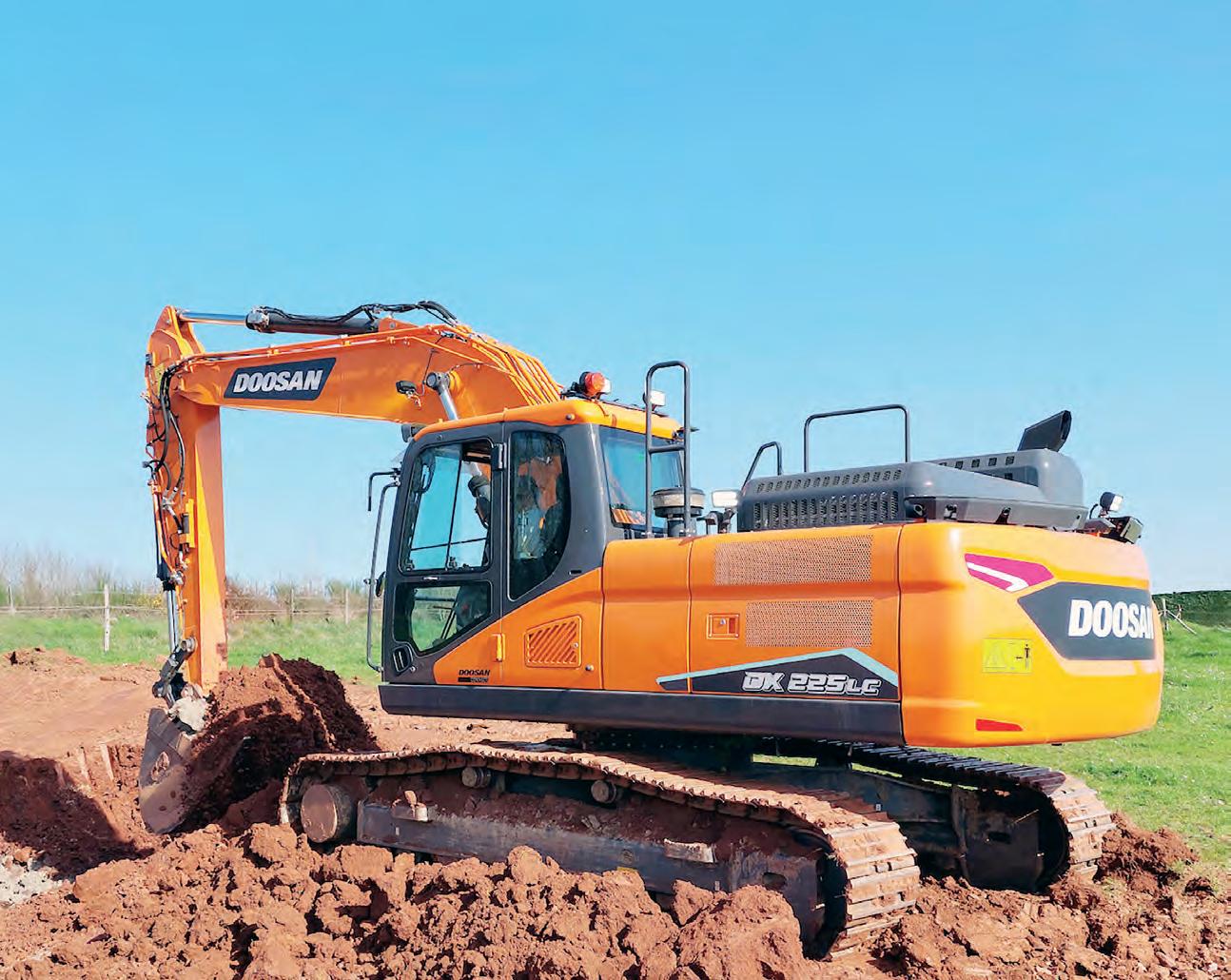
Feedback to the operator is provided through audio and visual displays which allow improved control of the machine in relation to the intended or designed direction of travel. In the on-board machine control system, the sensors mounted on the front and body recognize the location of each working device andsupport/adjust the front operation to the work as planned. In this way, when the operator uses the arm, bucket or boom, they follow the target line. Thanks to the laser receiver, the system will always receive the reference point, even when the machine changes position, without the operator having to reset the reference point every time the machine is moved. When the DX225LC-7X is delivered to the customer, all the sensors are already calibrated. But the buckets to be used by the customer need to be calibrated, and no specific tools are needed for this. The system will ask the operator to enter the required measurements to finalize the calibration process with around an hour needed to calibrate three buckets. CONTROL FUNCTIONS

There are three major Machine Control functions, and they can be activated by pushing the appropriate function button. Grade Assist Mode - On/Off can be set using the instrument panel and joystick. When the Grade Assist mode is set, the boom and bucket are activated in green according to the mode setting in the instrument panel icon. When the Bucket Assist function is activated, the current angle is memorized. When the driver operates the Bucket joystick, the last value is memorized after stopping the operation. When the Bucket Assist mode is on, the Bucket is green on the instrument panel icon. The Weighing System and Lift Assist function measures and displays the current weight of the bucket as the operator is loading materials and warns the driver whenthe total loading weight exceeds the target.

CDE CELEBRATES 30 YEARS IN BUSINESS
Throughout 2022, CDE, a leading supplier of sand and aggregate wet processing solutions for the waste recycling and natural processing sectors, is celebrating its 30th year in business.
It comes as the company reveals its wet processing technologies have, over the past three decades, facilitated the diversion of over 100 million tonnes of construction, demolition and excavation (CD&E) waste from landfill globally. The family-owned business has been at the leading edge of innovation in the materials processing industry since it was founded in 1992 by company Chairman Tony Convery. Since its inception, CDE has successfully delivered over 2,000 proven solutions in over 100 countries, and to this day the Convery family is central to the day-to-day operations of the global firm and the strategic direction of its promising future. Tony said: “When CDE was established three decades ago I was confident that we had something new to offer and that we could be a force to drive meaningful change in the industry. In our relatively short history, we’ve made significant advancements, driven innovation through our technologies, achieved great success, and built a solid reputation for expert engineering that delivers for our customers. Under the direction of our senior leadership team and with the support of the next generation of the Convery family who are already rooted in the business, I’m in no doubt that CDE has a prosperous future ahead of it.” Today, CDE employs a global skilled labour workforce of over 500 people, including over 120 engineers with a combined 1,000+ years of industry experience. FIVE REGIONS
Headquartered in Northern Ireland, CDE operates across five regions – the UK & Ireland, Europe, Middle East & Africa, Australasia and the Americas – with regional headquarters in each. In 2018, to build closer, direct ties with its growing customer base, CDE officially opened its Americas headquarters in Cleburne, Texas, where demand for its cutting-edge solutions is continuing to rise. CDE’s Chief Executive Officer Marc Jennings said: “At CDE, we share a common purpose to create our best world a ton at a time. We’re very proud to announce that in our 30th year, together with our customers, we have diverted 100 million tonnes of CD&E waste from landfill while continuing to support our customers to maximise their natural resources in the most sustainable way possible, with greater efficiency and less waste than ever before. “This accomplishment is testament to the commitment of our pioneering customers, those who have adopted and invested in CDE wet processing technology over the past three decades. “It’s a direct result, too, of the past and present talent at CDE. We know our success is dependent on our people and that’s why we are so focused on developing, promoting, and retaining great talent so that we can continue to develop innovative solutions that empower and equip our customers, and the wider industry, to build a more sustainable future.”
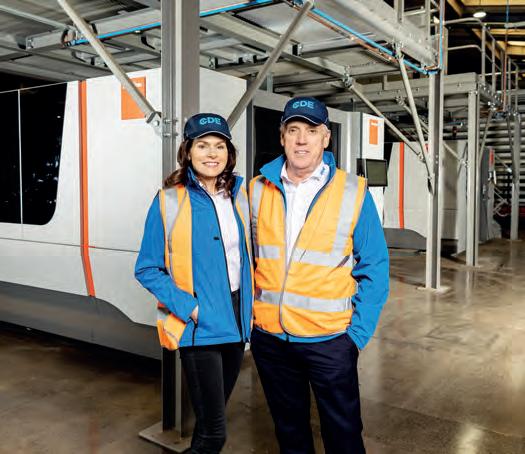
Marking the 30th year in business are CDE Directors Rosemary Convery and Tony Convery at the company’s Monkstown fabrication campus where CDE has made an in new state-of-the-art cutting and automation equipment.
ONGOING EXPANSION
The indigenous Northern Irish firm has big plans to celebrate its 30th year in business, including strengthening its manufacturing capabilities and regional hubs, and expanding its workforce in response to increasing demand. Marc says: “CDE recorded its most successful year to date in 2021; we partnered with more customers than ever before and together we almost doubled our ambitious waste recycling targets for the year helping us surpass 100 milliontonne-diversion from landfill.” In light of demand and to better serve its customers the company has also announced two major investments. CDE recently launched a new website that reflects its global reach. Offering more content and resources than ever before, the new website provides visitors with the comprehensive insight into CDE’s innovative solutions and thousands of projects it has delivered globally. It has also invested in new state-ofthe-art cutting and automation equipment at its Monkstown fabrication campus to boost its manufacturing capacity. “As part of its latest investment, it has installed two new Bystronic high-speed sheet metal laser cutting systems to boost productivity and output in line with growing international demand for its product set. Integrating seamlessly with these is a new 400-tonne steel storage and management system incorporating fully automated loading and offloading of the laser cutters. The new system will improve cutting capacity, efficiency and underpin future growth in manufacturing. Marc continues, “Demand for our solutions continues and our new website will help prospective customers see how CDE technology has transformed operations similar to theirs in terms of challenges, size, sector and material. Investing in our world-class manufacturing campus ensure we can meet that demand as efficiently and timely as possible. “In addition to the launch of the site, we have other ambitious plans in the pipeline, including creating new employment opportunities, launching new products to the market and further supporting our regional bases.” CDE is focused on providing the very best customer experience, Marc explained. “With groundbreaking global customers and pioneering engineering excellence, we are perfectly positioned and 100% determined to lead the future of waste recycling – relentlessly innovating, collaborating, and empowering our customers to transform waste into valuable resources. Laying the foundations for the circular economy and doing our part to protect people and planet.”