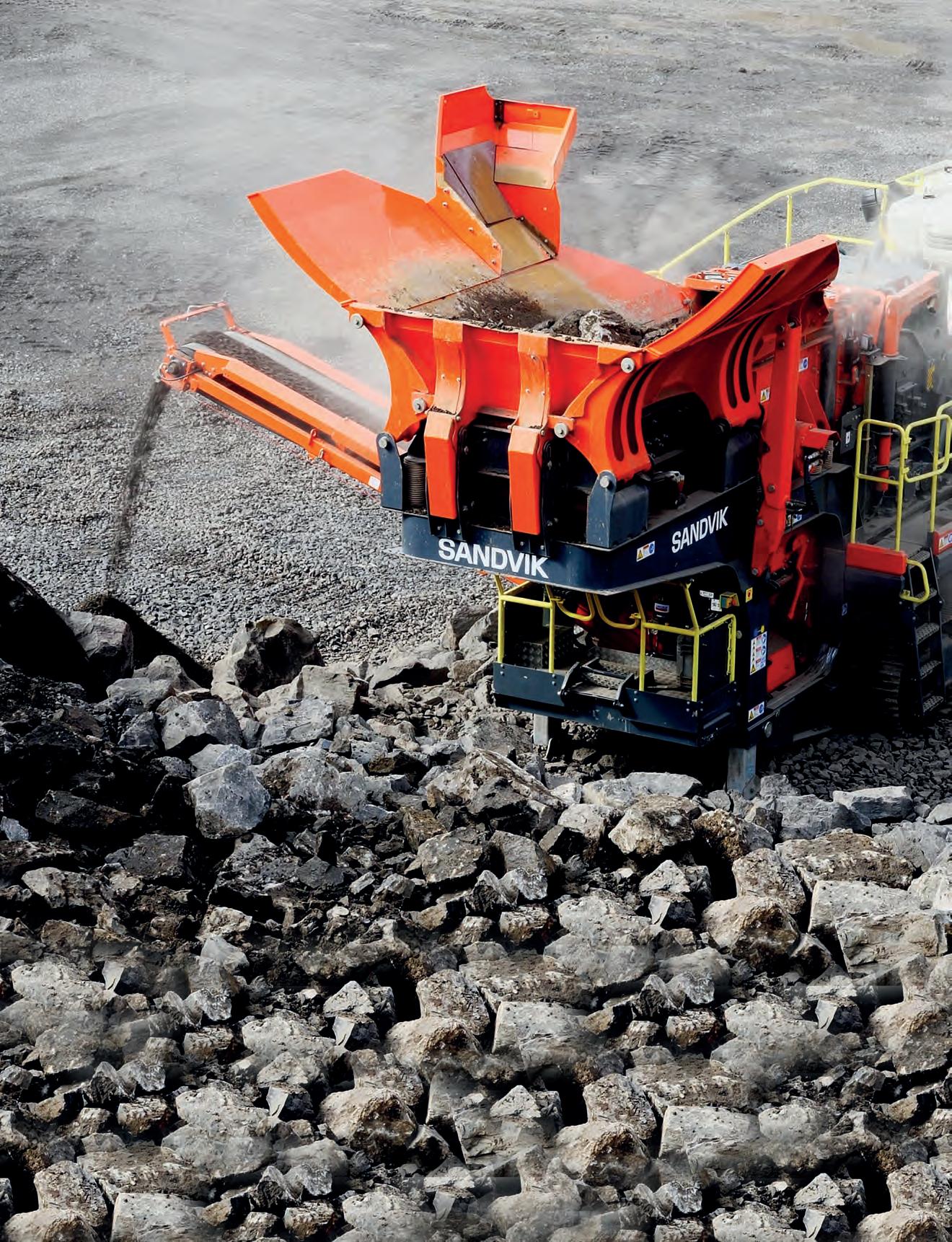
15 minute read
Crushing & Screening
MORE EFFICIENCY, FLEXIBILITY AND PRODUCTIVITY WITH SANDVIK’S 3-SERIES MOBILE IMPACT CRUSHER
Sandvik Mobile Crushers and Screens has unveiled its new QI353 midsize impactor, the first of its New 3rd Generation 3-Series products.
Designed in response to customer research, the QI353 has been built with more productivity, uptime, efficiency, flexibility, connectivity and safety at the forefront of its innovative design. The Sandvik QI353 features a ground-up new mid-size track platform and custom Prisec impact crusher. Targeted at quarry, recycling and contractor segments, the QI353 is the most versatile, mid-sized mobile impactor available today, designed to provide more uptime than any other. With the operator in mind, the QI353 offers a user-friendly mobile solution, with controls and maintenance points located conveniently at ground level. A key highlight is the new automated control system featuring Optik™ intuitive user experience. With colour visual display, easy navigation, and total integration for troubleshooting, diagnostics and support.
More Productivity
The QI353 has been designed with productivity in mind and can process up to 400 mtph / 441 stph. Its feed arrangement includes a new feed hopper with curved heavy-duty sides for greater capacity and tapered feed arrangement to reduce blockages and ensure continuous crushing. It also features a new pan feeder with
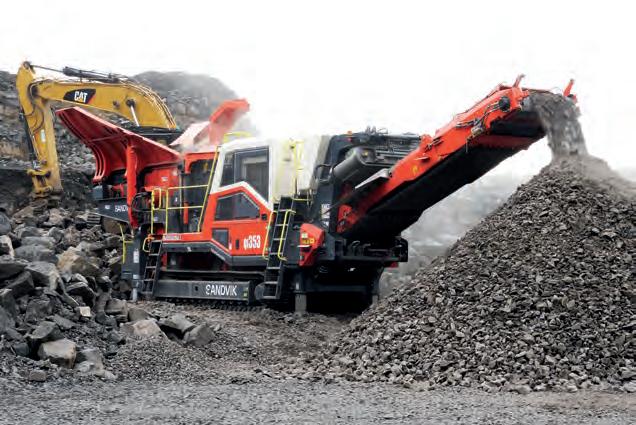
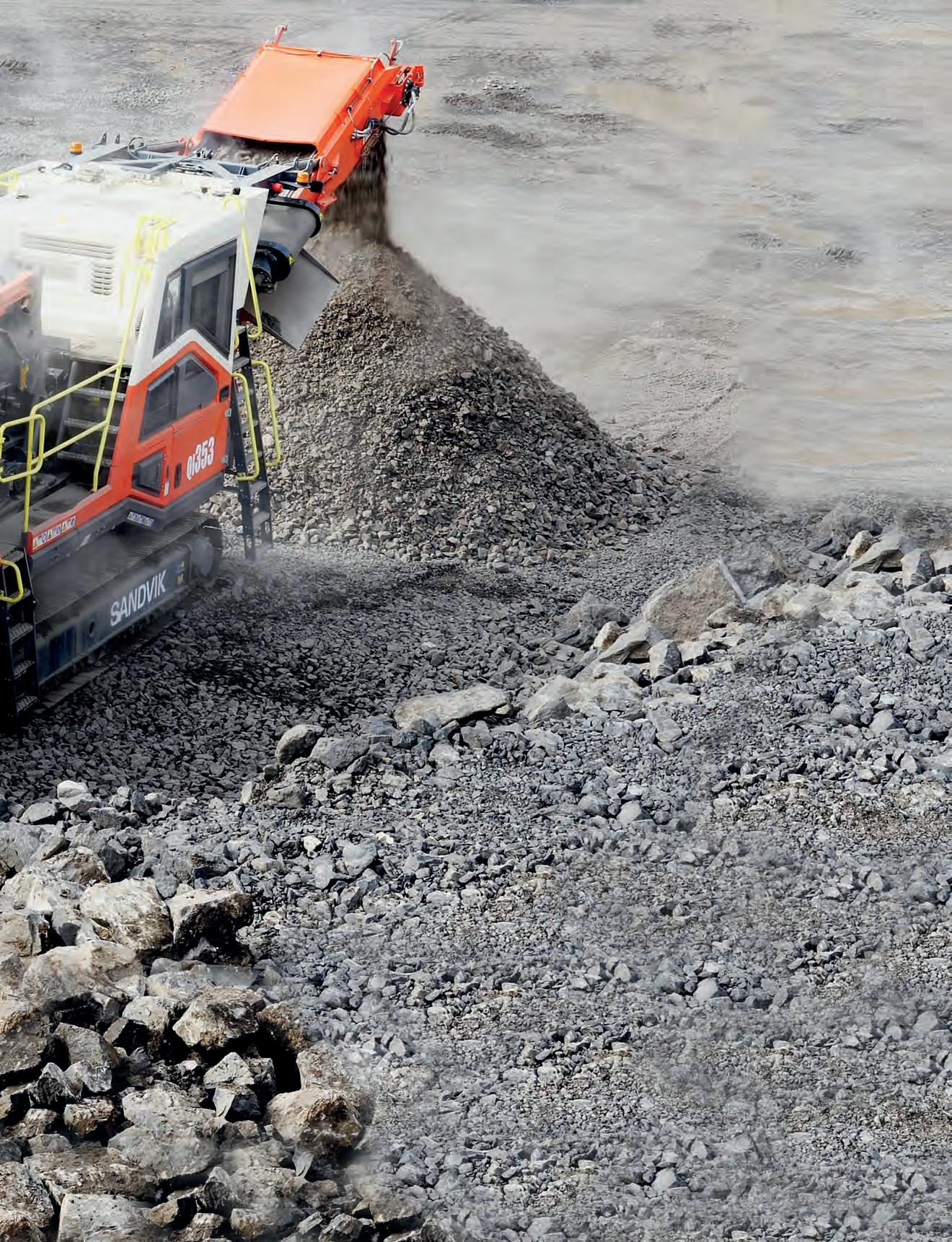
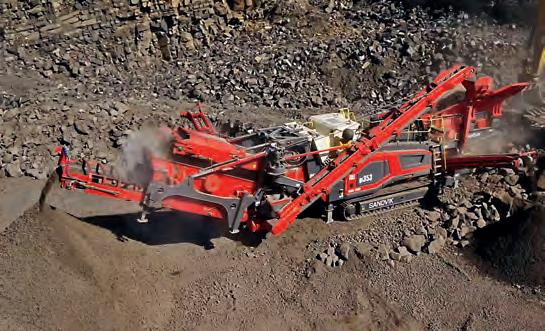
geared drive and a larger pre-screen with improved access to replace media. At the core of the QI353 is a new mid-size Prisec impact crusher, which boasts the largest feed opening 1170 mm x 730 mm / 46” x 29” and largest rotor diameter 1150 mm / 45” in its class, for higher capacity & greater energy efficiency. Adjustable apron curtains and tip speed ensure a wide range of product gradations can be achieved. Also, all plant conveyors have larger discharge heights for increased stockpiling capacity.
More Uptime
The QI353 features a free-flowing feed arrangement where all components in the flow path through the machine get wider, for Improved material flow. A load sensing system for feeder drive, to ensure continuous crushing. A larger pre-screen for effective removal of fines, maximizing throughput and reducing wear. In addition, the QI353 benefits from extended service intervals and larger onboard fuel storage to extend intervals between refuelling.
More Efficiency
The QI353 has been designed to consume less energy, its double-deck pre-screen ensures maximum scalping capability and prevents any undersize material passing through the impactor. This maximizes crusher throughput, reduces wear costs and energy consumption. The machine requires 40% less hydraulic oil per service and benefits from extended hydraulic oil replacement intervals. When combined, this can be up to 64% less hydraulic oil consumed over 10,000hrs of machine usage (subject to oil sampling). The QI353 is also fitted with the latest emissionscompliant power pack for maximum performance and cost efficiency.
More Flexibility
Boasting a high degree of flexibility to suit any application, the QI353 is particularly useful for contractors who change jobs frequently. The natural fines conveyor can be positioned for right- or left-hand discharge with a three-position by-pass chute under the pre-screen allowing you to decide where to send your natural fines. The QI353 comes prepared to accept our new enhanced HS323 hanging screen module, offering the flexibility for the crusher to operate in open or closed circuit. The HS323 enhancements include prepared to accept belt scales for TPH monitoring on fines and stockpile conveyor belts, subframe enhanced for improved screen media access and tensioning and an updated mid-size stockpile conveyor. The unique design enables set-up in less than 30 minutes and can be fitted without the use of additional lifting equipment. The patent pending hanging screen option delivers multi-functionality as a 1, 2 or 3-way split screener, as well as a highly productive and efficient impact crusher.
More Connectivity
The new automation system with Optik™ intuitive user experience, includes simplified operation controls and total integration with our My Fleet telematics solution. Diagnostic support, pre-installed guides for troubleshooting and real time information allows customers to know exactly how their equipment is being utilized. One of the new additions to the plant, is the availability of optional belt scales on the QI353. These are fitted to the product conveyor and will enable productivity data to be displayed on the user interface and via My Fleet for TPH monitoring enabling full control of the machines output.
More Safety Features
With operator safety paramount, we have incorporated a new access platform under the feeder & pre-screen and a spacious 3-sided 270 degree platform for service and maintenance. A lifting beam, jib and tackle are provided, as well as the patented rotor turning device to ensure operator safety, when removing, rotating or installing hammers. A height adjustable overband magnet and all conveyors can be conveniently lowered for inspection and servicing purposes. Enhanced safety features are embedded within Optik™ intuitive user experience, including visual warnings and emergency stop locations.
METSO OUTOTEC EXPANDS LOKOTRACK MOBILE SERIES FOR AGGREGATES
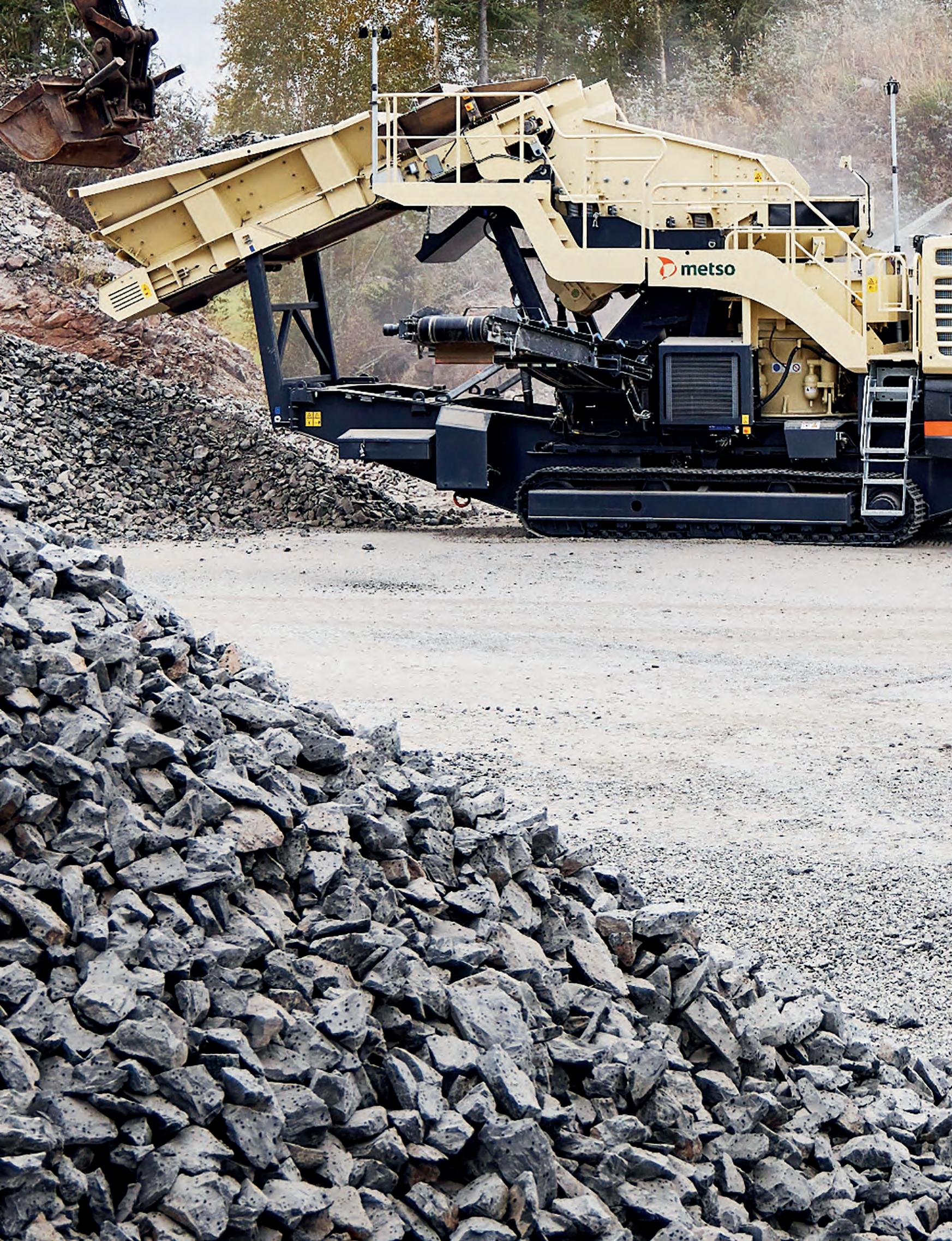
Metso Outotec is launching two new models to the Lokotrack mobile crushing and screening series. The new Lokotrack LT200HPX and Lokotrack LT220GP mobile cone crushers are compact but efficient units ideal for aggregate contractor customers, bringing up to 30% more capacity and added flexibility compared to earlier models.
The new models were premiered during Metso Outotec’s virtual studio events recently, and in the new Lokotrack Liveroom 360 online experience together with services and parts offerings for Lokotrack. The launch models have many new features that are designed to improve the efficiency of customer’s operations. They are built on the same new chassis, allowing customers to choose between the two cone crusher types and various optional features based on their specific needs. The Lokotrack LT200HPX is equipped with an efficient two-deck pre-screen providing more capacity. Heavy duty chassis and wide conveyors facilitate high throughput, and a direct v-belt crusher drive ensures high fuel efficiency. Service and transportation are facilitated with extensive service platforms that fold down for transport. LT200HPX can be combined with Lokotrack LT106 and LT116 jaw crushers and Lokotrack ST3.8 and ST4.8 mobile screens. The Lokotrack LT220GP provides additional crushing power and can be equipped with a pre-screen or with a belt feeder. LT220GP fits well with Lokotrack LT120/LT120E mobile jaw crushers and ST4.10 mobile screen for highcapacity aggregate production. “The new models and our end-to-end offering displayed in the Lokotrack Liveroom, demonstrate our focus on improving aggregates customers’ operations and bottom line,” says Kimmo Anttila, Vice President, Lokotrack Solutions at Metso Outotec. “With these new models of 300 metrics tons per hour capacity
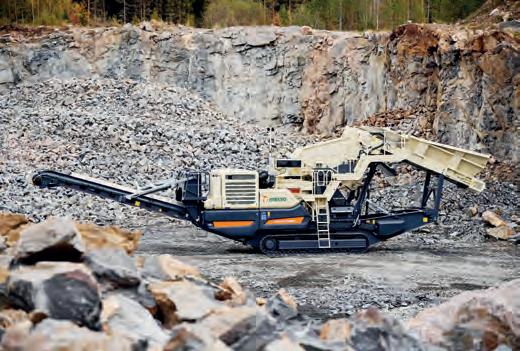
and 40 metrics ton transport weight, the customers have even more choice and flexibility to select from our cone crusher range. Lokotrack is a sustainable and future-proof choice for any type of aggregate production.”
Service and support
Metso Outotec offers extensive services and parts support for Lokotrack, including for example spare and wear parts recommendation lists and kits, full container load parts service, inspections and extended warranties and the Metrics remote monitoring solution. The service portfolio showcased in the Liveroom addresses the needs of aggregates customers in terms of equipment protection, availability, performance, and upgrades. These services are aimed at helping Lokotrack crushing and screening assets operate at their optimal levels.
METSO OUTOTEC LAUNCHES INDEX ONLINE TOOL FOR METAL RECYCLING MACHINES
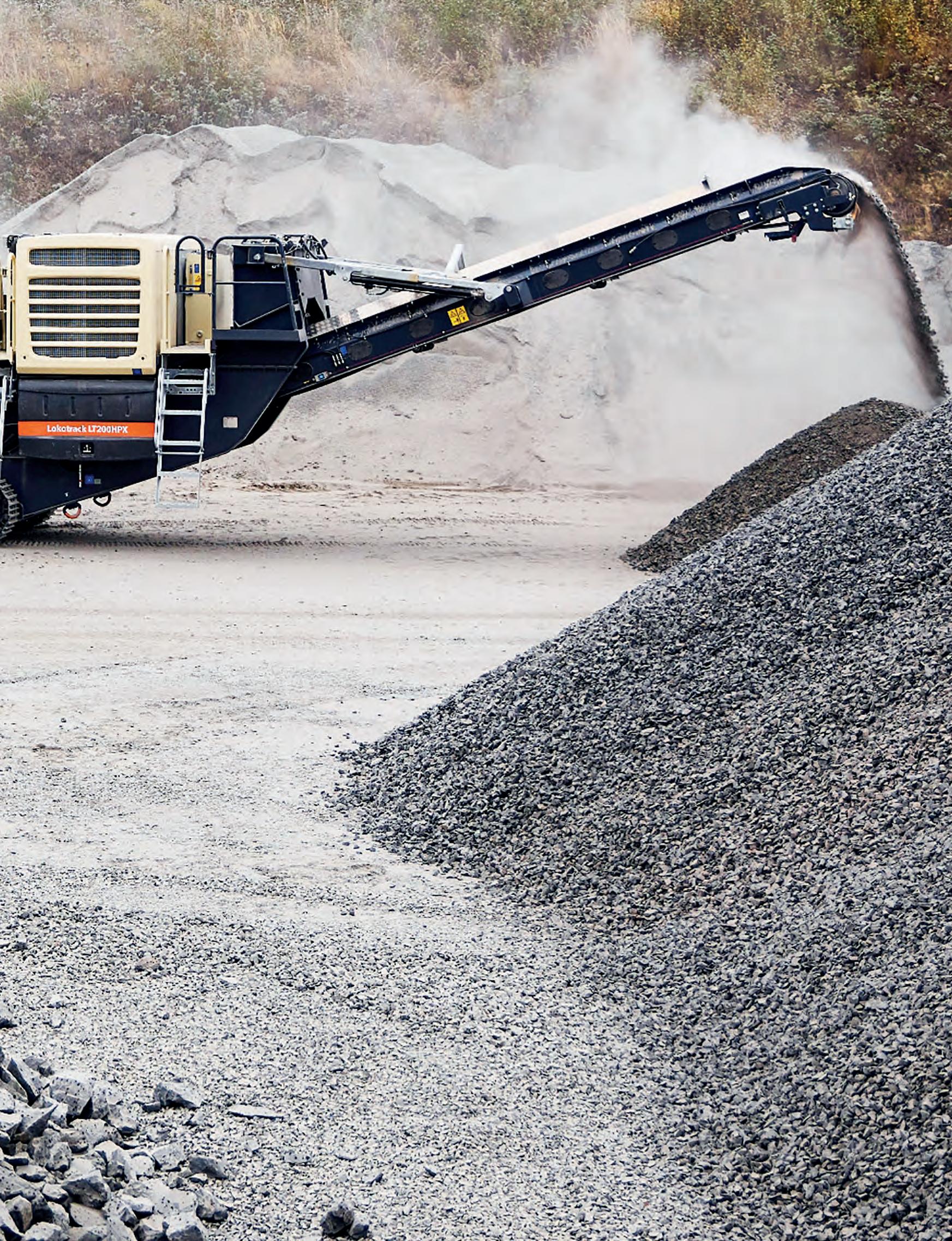
The new Index operating and production data collection system from Metso Outotec’s Metal Recycling business transfers relevant data from the recycling machine directly to the customer’s equipment.
Metso Outotec Metal Recycling has taken the next step in terms of digitisation and, with Index, introduced an intelligent way to increase machine productivity, optimise the costbenefit ratio and identify limiting parameters at an early stage. “Accessible via mobile app or from the dashboard any time, one click is all it takes to find out immediately how high the current capacity utilisation is, which material is currently being processed, how many operating hours the equipment has already been running for, or what the general condition of the metal recycling machine is,” explains Peter Thomas, Director of Products and Technology for Metal Recycling in Metso Outotec. All the equipment data can be visualised, displayed and analysed in the Index web portal and if necessary, transferred to programs and systems designed for controlling purposes. “We are talking about modern workflow and performance monitoring, which serves as the perfect basis for evaluating the various key performance indicators (KPIs),” he continues. The server used to back up data is currently one of the most secure servers on the market. It is located in Europe and is therefore subject to European data protection regulations. Index will be available immediately as standard equipment in these Lindemann shears: EtaCut II, EtaCut, PowerCut/LUC as well as PowerCut Wings/LIS and LU. In addition, customers have the option of retrofitting their current stock shears of the previously mentioned machine types with Index. “Additionally, Index will soon be available for presses and shredder systems for Metso Outotec’s metal recycling customers,” says Peter Thomas.
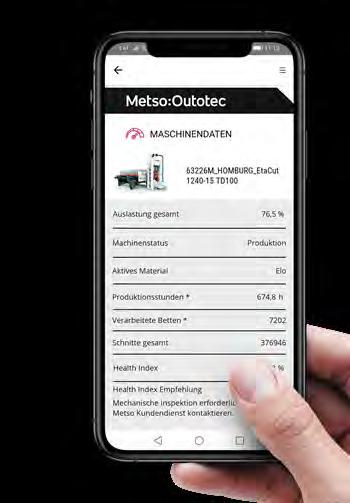
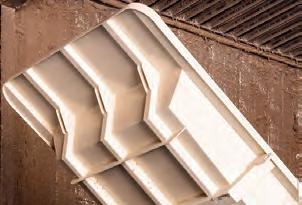
TEREX ECOTEC’S TDS V20 SHOWS ITS POWER AND RELIABILITY AT THE PEUTE GROUP

Peute Recycling, a Dutch company and part of the internationally operating Peute Group, has invested in a Terex Ecotec TDS V20 medium speed shredder to enhance its ability to produce a high-quality and standard of recycled paper at its facility in Alblasserdam, The Netherlands.
Peute Recycling has an established partnership with Terex Ecotec distributor, Troost Machinehandel B.V., having purchased various kinds of machinery from the company and been satisfied with their partnership. Rudolf Peute, Operational Manager at Peute Recycling explains,“A lot of brands make good products, but it is the service partner who determines how well a product is being placed in the market. Additionally, their advice is important for making the right choices. “We needed a diesel-powered shredder, because we don’t have enough electrical power for such tough machines at our current location. We also wanted the paper to be homogenous and compressed in similar dimensions, a requirement from one of our largest customers,” according to Rudolf. After investigating Terex Ecotec’s equipment options with Troost Machinehandel B.V., Peute Recycling opted for the TDS V20, which they found was particularly suited to their operation. Its ability to produce a controlled product size in one pass would prove to be of huge benefit to Peute Recycling, saving both time and fuel. The machine is equipped with a Stage 5 diesel engine of 493 horsepower, reversible hydraulic fan, internal fire suppression system, rubber pads on the steel tracks (because the machine is moved indoors) and a long conveyor belt, with a 5-metre discharge height. The TDS V20 gave the desired results during testing, with Rudolf saying that the team at Peute Recycling were very impressed with the performance of the machine. The TDS V20 mainly shreds industrial types of paper, such as coffee pods, pastry cups, rolls of wrapping paper, packaging material, magazines and newspaper, which often needs to be reduced for a certain field of application. A major application for the company is a semi-finished product for the fibreboard/gypsum industry, where paper compositions are used to make gypsum fibre reinforced boards. Peute Recycling has found the TDSV20 to be a robust machine, an important characteristic for reducing paper. “The machine uses a certain type of cutting technique rather than tearing which gives the right results for us. “Paper is a strange product that releases a lot of forces, which can be problematic. For example, shredders that can process the most difficult materials can struggle when you throw in a pack of paper. Reducing material is a specialist profession.” Rudolf adds: “We have been running for about 600-700 hours to date and see that the wear of the cutting teeth is at a low level—we haven’t had to change teeth yet. Costs are also saved due to lower fuel consumption compared to previous shredders, which is another plus for our bottom line. We haven’t looked back since investing in our TDSV20.”
TEREX WASHING SYSTEMS LAUNCH M1700X MOBILE WASHING SCREEN

Terex Washing Systems has launched its latest innovation - the enhanced M1700X Mobile Washing Screen.
The M1700X is a redesign of the M1700 and improves the M Range of mobile washing screens manufactured by Terex Washing Systems that can produce up to five products (three aggregates and two sands) in applications including; aggregates, recycling, industrial sands and mining. Barry McMenamin, Business Line Director of Terex Washing Systems said, “The addition of the M1700X will enhance an already significant product range offered by Terex Washing Systems, meeting both market and customers’ needs for mobile washing. “Our team of engineers have worked closely with our customers to develop improvements to an already high performing machine, such as the new tracked rinser that features a redesigned high fluidisation wash box, increased standard features and improved washing efficiency.”
Highlights

The improved M1700X features a new integrated high fluidisation wash box to maximise deck efficiency, increase media wear life and have an adjustable spray system. It also boasts increased standard features, including a standard hydraulic raise and lower for quicker service access, standard hydraulic tensioning, and one-piece catchbox for easy machine reconfiguration. Setting new standards in screen box technology, the M1700X has heavy duty bearing arrangement for long service life, higher levels of screening efficiency and throughput, increased serviceability and maintenance access as well as increased screen angle adjustment that is highly adaptable for feed material variation. The model has also been redesigned with a focus on wet processing efficiency, with 16% increase in spray capacity across all decks, industry leading levels of catchbox sealing, innovative configurable catchbox outlets and configurable blending to maintain material specification. Additionally, the M1700X is easily transported, has a quick set up time (typically 15 minutes), and has optional hybrid power available around the world.
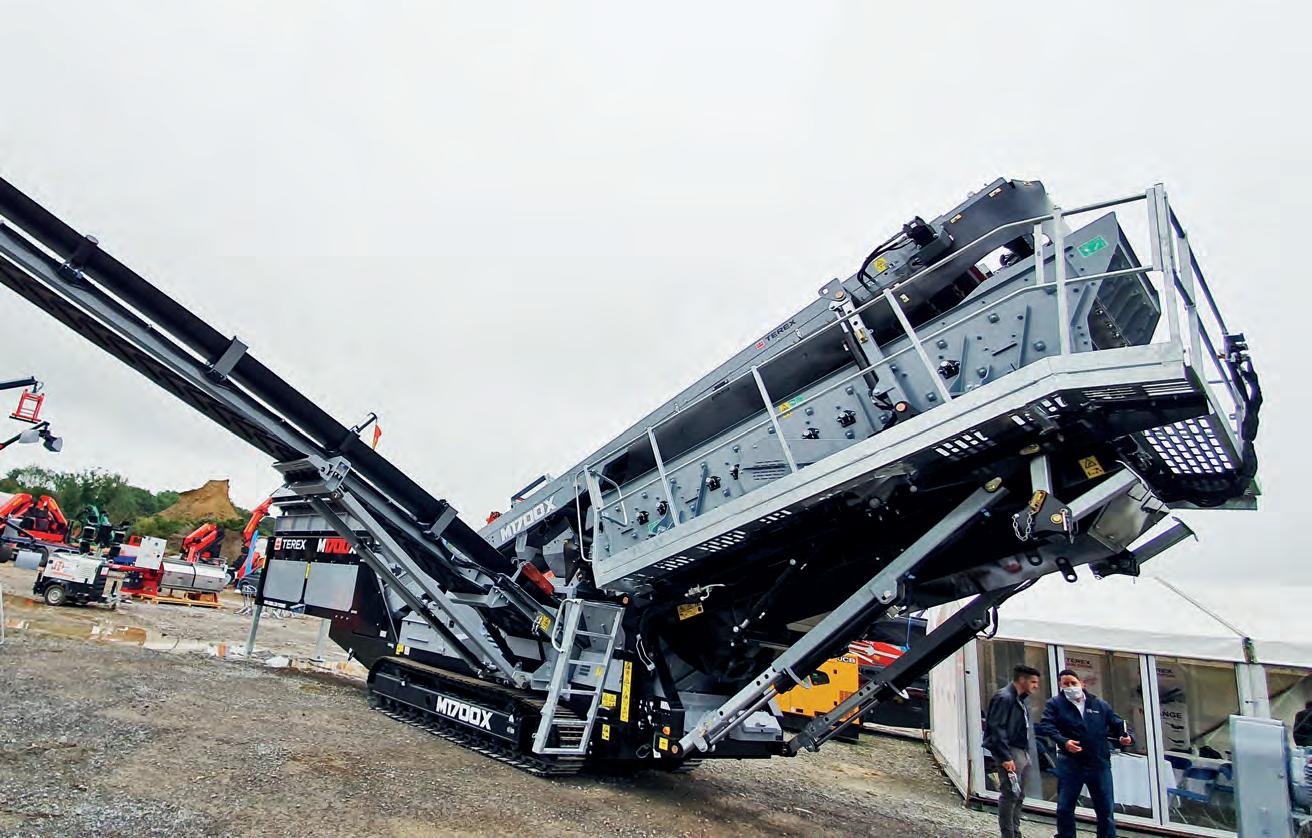
MORE OPERATORS THAN EVER CHOOSING TILTROTATORS FROM ROTOTILT
Tiltrotators from Rototilt have rapidly become one of the leading brands in Ireland and the UK, with the Irish market being served by Cullion Plant since 2014.
The County Tyrone based dealership is fully equipped to handle all sales, service and spare parts for the complete Rototilt range across the island of Ireland. The opening of Rototilt Ltd’s dedicated UK office has gone one step further to strengthen its position in this part of the world; it has given Rototilt a more focused approach to the market here and throughout the UK, while offering an invaluable sales and technical training facility. Tiltrotators from Rototilt virtually transforms an excavator into a flexible machine that opens up the opportunity for operators to take on more challenging tasks; not only can they get them done faster, and more efficient, but with less manpower such is the product’s versatility. Rototilt’s tiltrotators are robust and reliable thanks to their cast rotor housing which is both stronger and lighter than welded alternatives. The worm gear on all models, for example, boasts improved geometry and stricter wheel and screw manufacturing tolerances, providing smoother operation and reduced friction. The worm gear is also equipped with a new worm screw with integrated lubrication channels, which improves and further extends the service life of the tiltrotators. Large bearing surfaces effectively absorb and distribute excavation forces. The specially designed guard for the hydraulic motor is integrated with the cast rotor housing and protects it against impact and shocks from beneath.
Advantages
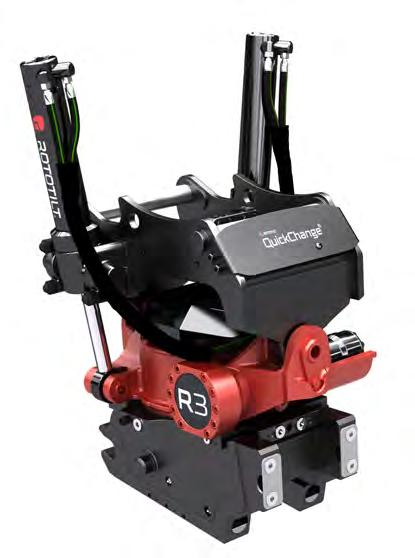
Rototilt’s tiltrotators are oil filled. The advantages of oil over grease are numerous, including continuous lubrication, better heat dissipation, a longer service life, particle removal, fewer lubrication points and cleaner components, the latter simplifying maintenance. Rototilt’s central lubrication system offers convenient tiltrotator lubrication. It is designed to be connected to the machine’s central lubrication system and features an easily accessible interface on the mount. The system also simplifies manual lubrication if the machine lacks a central lubrication system. Self-lubricating bushings on the cylinder attachments mean fewer lubrication points and consequently simpler maintenance. All Rototilt cylinders feature load management as standard, which increases workplace safety; the load is secure, even in the event of a hose rupture, for example
Control systems
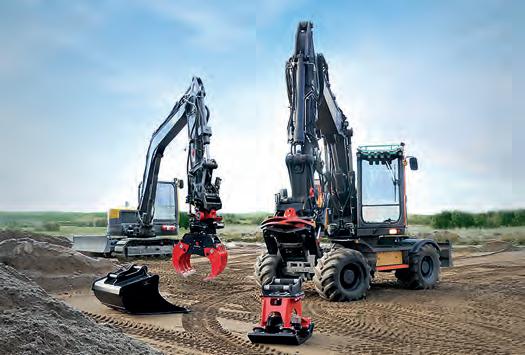
With Rototilt you can choose the control system that optimises your excavator and contributes to increased performance, better handling and more options for settings. The Innovative Control System, ICS, is a smart control system that features a clear and simple display that quickly gives you overview and control. With the ergonomically designed handle you can control tilting, rotation and any extra function during the same excavation movement. Choosing the pulse function, for example, will help you to quickly and evenly spread the material. You can also get individual operator settings and smart troubleshooting that even suggests corrective actions. An important ICS function is the safety solution SecureLock. With a built-in sensor in the quick coupler, you get a warning both on the display and with an audio signal if anything is wrong with the tool coupling. Continuous monitoring ensures that the tool remains locked in place. The safety lock also lets you know when tools are worn and require attention. For dual hydraulic circuits common on smaller excavators, TLE (Tilt Lock Extra) is an attractive and cost-effective control system alternative; it also works with larger excavators with dual circuits and can be complemented with SecureLock.
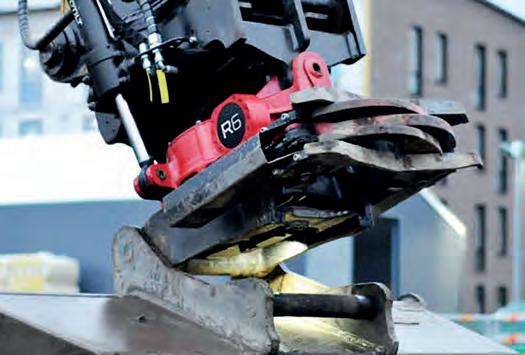