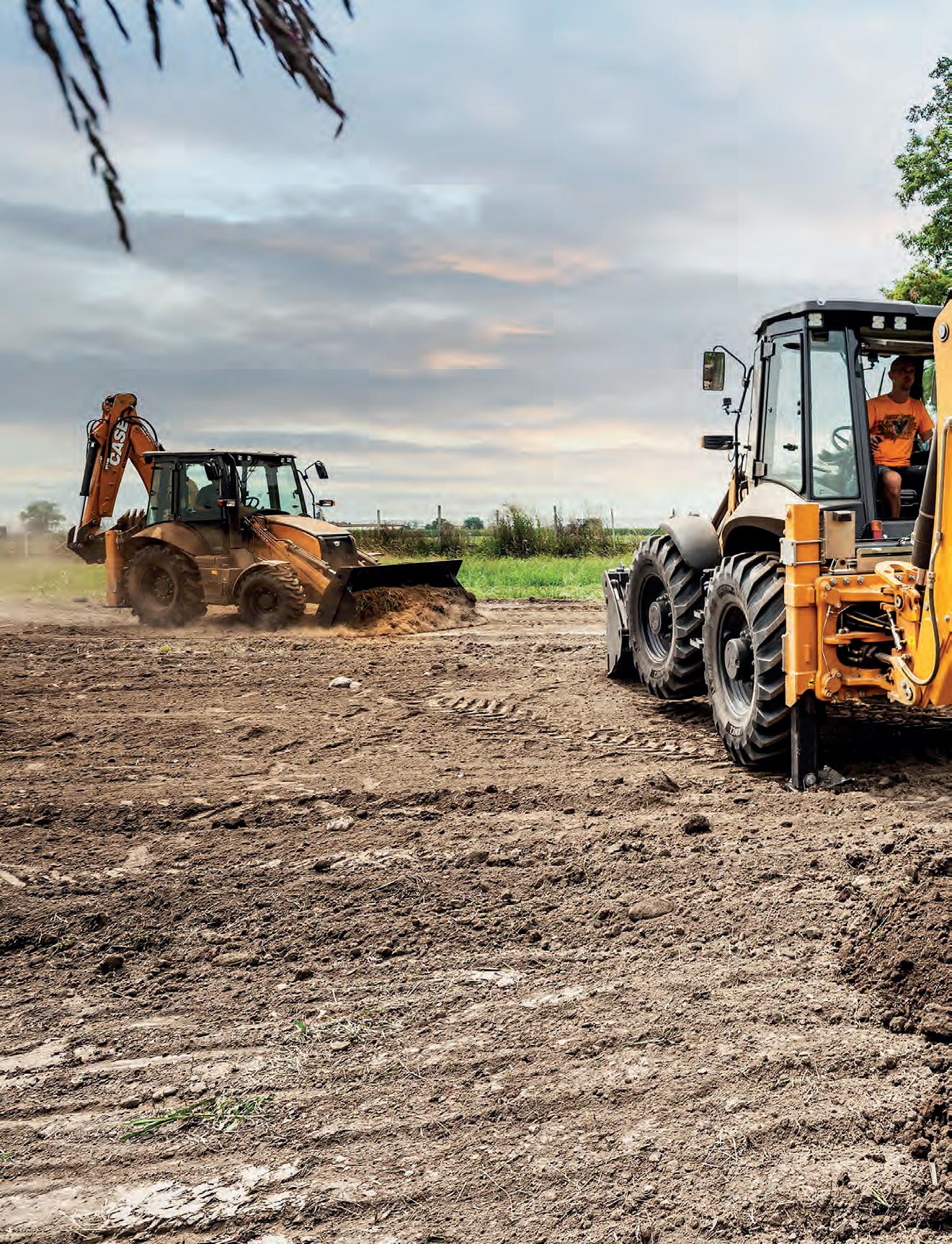
12 minute read
CASE Backhoe Loader SV Series
CASE Construction Equipment recently launched its new Backhoe Loader SV Series, over 60 years in the making and widely acclaimed legendary king of backhoe loaders; Plant & Civil Engineer has been finding out more from Product Manager Umberto Celestini.
The SV Series features a new expanded cab with enhanced controls, new FPT Stage V engine and retains the best in class features and performance - features that CASE say deliver greater operator comfort, increased productivity, reduced emissions and lower total cost of ownership. CASE manufactured the first ever factory integrated backhoe loader in 1957, closely followed by the first diesel powered model in 1959. Many more firsts followed with ride control, powershift transmission and the uniquely flexible integrated quick coupler, a major feature even in today’s models. “With this launch, we believe that the nickname of the King is even more representative, because we have designed a brand new cab with King size space and comfort for the operator,” says Umberto Celestini. So, what prompted the ‘make-over?’ Explains Umberto: “When we took on the challenge of this project to meet Stage V emission regulations, we worked to do it - the “CASE-way”: we accepted no compromise on performance. “We met the stringent Stage V emissions requirements maintaining the same best in class power and torque performances of Stage IV, plus without fuel or urea consumption deterioration vs previous model. Moreover, as we are always aiming for more, we completely redesigned the cab interior and added many productivity, profitability, safety and comfort features. “We did that because with SV Series we wanted not only to give an emission compliant machine, but provide much more added value for our customers, around which the new models have been designed.” Relating how much customer input was there in the new design, he adds: “Customer inputs have been key for the development of this new programme. It started during the creation of the Product Definition at the beginning of the project, continued with regular reviews even at the early stages of it with virtual/3D model reviews and was finalised when the first prototypes/pre-builds were built to try the real machine and confirm the adherence to the agreed upon product definition.”
Optimal Comfort
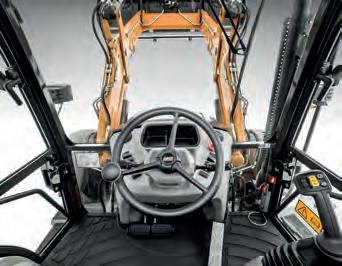
Case have totally re-engineered the cab for optimal operator comfort. The redesigned and restyled interior and exterior cab is wider, providing greater clearance for the operator’s legs when rotating the seat between forward facing and rear facing configuration, and superior accessibility to the cab. The left-hand cab console redesign also places the wiper tank beneath one of the new open tray storage units, enabling convenient refills via the left-hand door. Comfortable operators are productive operators, of course, and the new Backhoe Loader SV Series has many other improvements. A relocated parking brake, new speedometer option, regrouped switches on the right-hand console, new integrated F-N-R switch in the loader control lever on the Power Shift model, new joystick roller switch for extending dipper operation and relocated stabiliser levers all add up to time savings. So, how does it measure up on safety in comparison to previous models?
Comments Umberto: “Our safety standards have been always very high. With the SV series we have added a few significant improvements that make it even higher. “Cab noise has been reduced by more than 3dB. The speedometer has been located on front console, for a safer driving experience. Controls and switches have been repositioned in the most ergonomic way, so that operators can reach them easily in any working position and there’s new rear side glasses for greater visibility in the backhoe position.” Other improvements he outlined include: - Reshaping of front console and Design of Stage V engine and ATS with the same compact dimensions of stage IV to avoid the need to increase the height of
the hood: all for greater visibility to the loader and when driving; - Reshape of front and left console for superior and safe accessibility into the cab; - Wider room for the operator, in particular with a lot of leg and feet clearance when rotating the seat from backhoe to loader position; - Hands free Bluetooth radio for safer phone calls; - One side engine serviceability, all fuses and relays located inside the cab for easy reach and safe maintenance operations. Operators’ comfort and needs have been further accommodated by including 2 USB ports, a 12v port on the instrument cluster, a mobile phone holder, latest Bluetooth technology, and an industry leading storage capacity that is 4 times greater than the previous series. It includes 2 lockable compartments, 2 bottle holders, 4 open trays, and a cooling box, all finished with practical yet stylish injection moulded plastics.
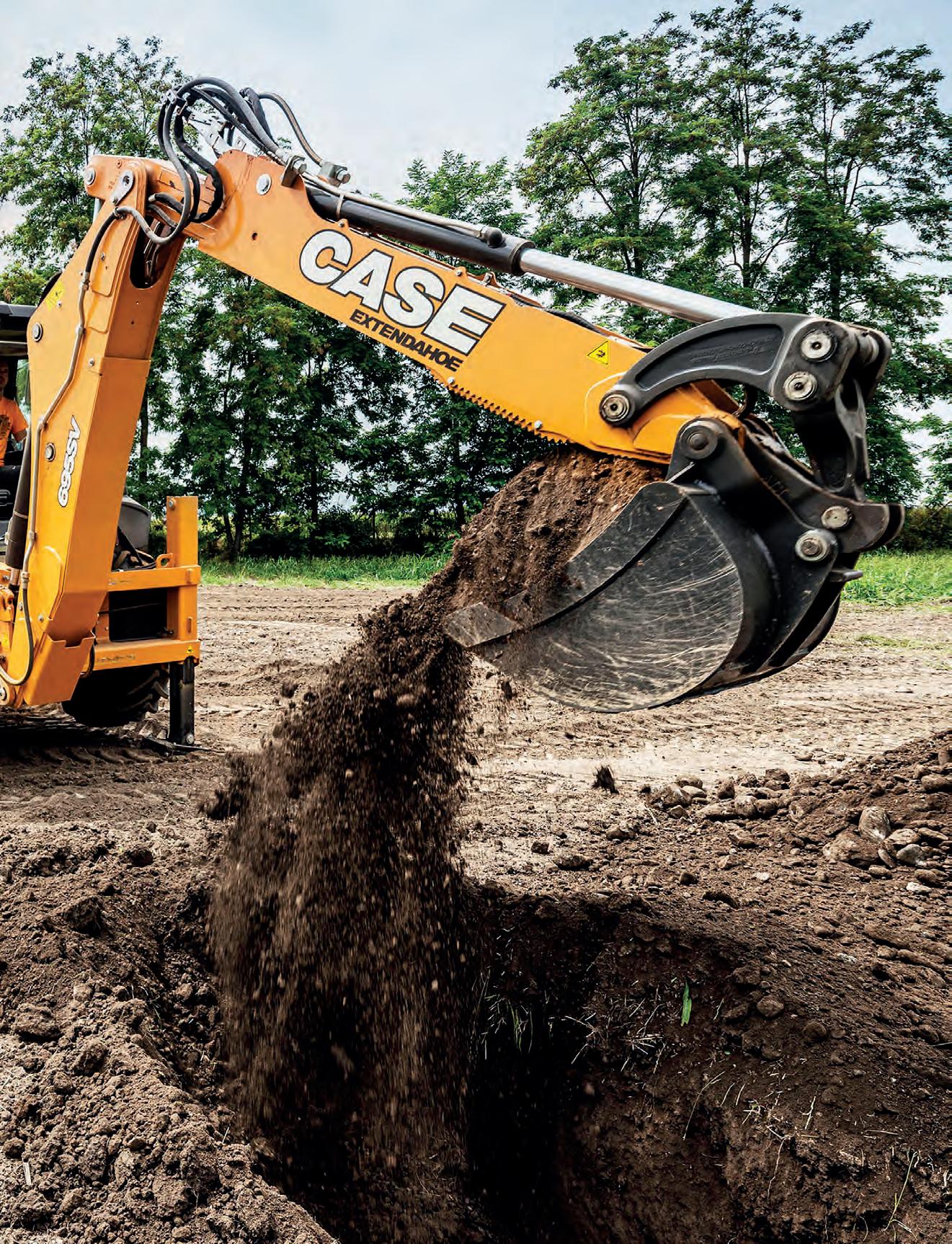
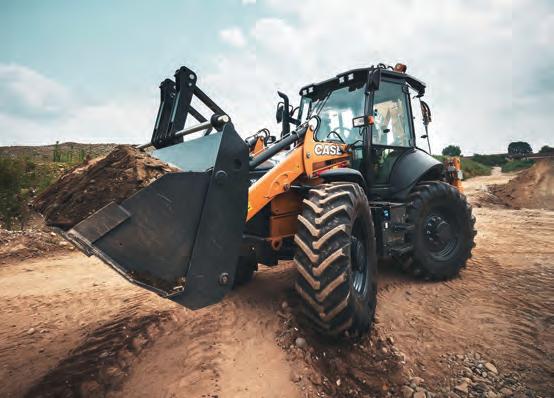
CONTINUED
Advanced Engine
CASE’s partnership with FPT has resulted in a new F36 Stage V engine that delivers the near-impossible – reduced emissions with no loss of performance and improved reliability, reducing total cost of ownership (TCO). The engine has been specifically designed for medium load operations, typical for Backhoe loaders. FPT has, for example, developed a specific after-treatment optimised for compact equipment. Compact High Efficiency SCR2 (Hi-eSCR2) is designed for applications with working cycles that typically generate low exhaust temperatures and include frequent stop and go cycles. Low rate EGR (exhaust gas recirculation) enables NOx reduction with compact SCR (selective catalytic reduction) dimensions while optimised DPF (diesel particulate filter) technology ensures high PM removal at low operating temperatures. All these benefits when combined with the ECO modegenerate fuel consumption savings of up to 10%. The 3.6 litre 4-cylinder 16v 1800 bar common rail injection engine with WG turbocharger, delivers industry-leading performance up to 82 kW and 460 Nm, all in the same highly compact layout as previous models, enabling high manoeuvrability and visibility. Efficient low-rate EGRtechnology and an operator-controlled ECO mode further improve efficiency and productivity. Operating costs have been minimised through a 500-hour oil change interval, variable volume pump that only provides oil when needed, and maintenance free after treatment system (ATS), for reduced operating costs and maximised uptime. The familiar and effective one side serviceability layout is retained for swift and convenient maintenance operations. The unique Hi-eSCR2 is maintenance-free, with low operating costs and no downtime for filter replacement or mechanical cleaning during the first 8000-hours.
Connectivity


There’ve also been improvements in connectivity. Explains Umberto: “We have developed CASE Service Solutions: a new range of services that support operator experience with CASE equipment, to boost productivity and improve machine Uptime. It includes our Connected Services offering.
“Firstly, CASE SiteWatch is a complete Fleet management tool that will help you in your daily work, for example it allows you to geolocate the machine… or to secure your fleet by setting up a geo-fence to be alerted in case of un-authorised use. It also generates a set of reports - easily accessible through the portal- to provide you with information such as fuel consumption, utilisation rate, machine hours, idle time…. very useful for productivity and profitability purposes. “Case SiteConnect, meanwhile, is where we enhance the telemetry data that our Uptime Center team can use to provide your dealer with alerts based on your machine’s parameters. They will be able to remotely access the history of the machine and take corrective action faster. This enables your dealer to be proactive in managing your machine and boost Uptime. Both SiteWatch and SiteConnect are available as options with the new SV range.”
The King
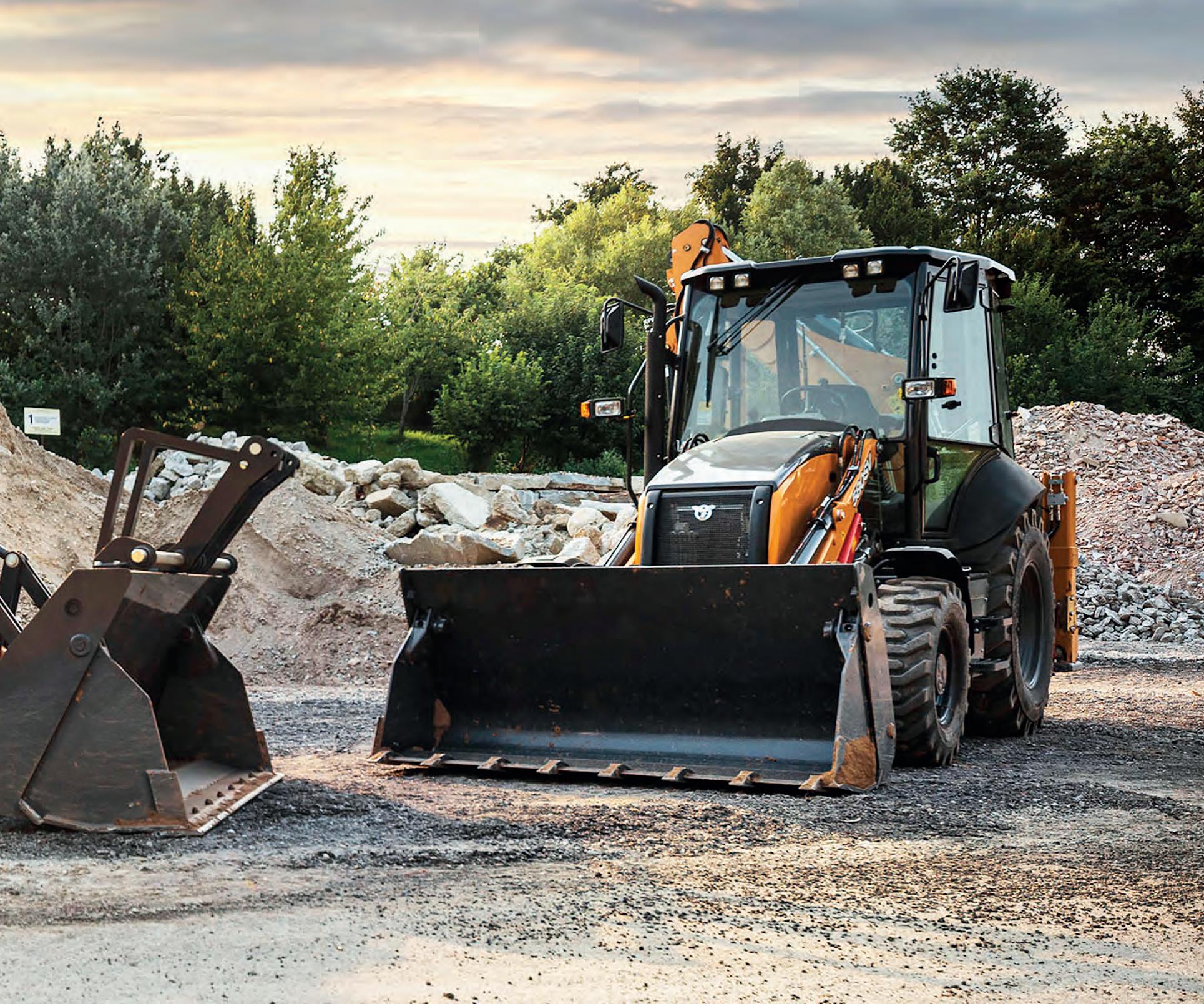
Adds Egidio Galano, Product Management Director, CASE Construction Equipment, Europe: “This latest SV series from CASE follows over sixty years of innovation that have earned all CASE backhoe loaders their unofficial name of The King. “CASE manufactured the first ever factory integrated backhoe loader in 1957, closely followed by the first diesel powered model in 1959. Many more firsts followed with ride control, powershift transmission and the uniquely flexible integrated quick coupler, a major feature even in today’s models. “The game changing features in the Backhoe Loader SV series have been driven by our customers and dealers, alongside the core values of hands-on problem solving that provides reliable solutions and builds communities. When choosing the SV series, our customers will discover new ways of working built on trust, high performance, comfort and cost reductions.”

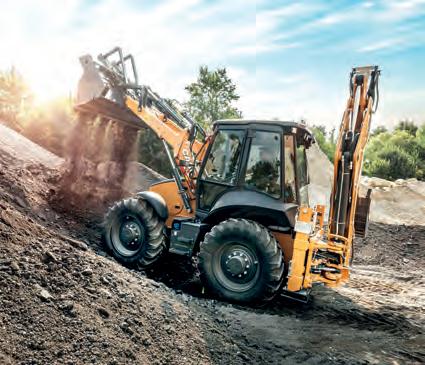
news Knock-On Effect of Pandemic Sees Irish Imports Enter Uncharted Waters
Woodland Group Ireland, one of the country’s leading freight forwarding and supply chain companies, has reported steep price hikes and acute delays for Irish businesses shipping from Asia.
Since October 2020, shipping rates out of Asia have seen a 450% increase. The main source of the surge is due to demand far exceeding capacity, with the industry experiencing reduced vessel, routing, and equipment availability. The situation has been exacerbated by an array of factors: originally set off by outbreak of Covid19 causing cancelled sailings and containers wrongly positioned in US & Europe. The situation was further impacted by the Suez Canal blockage and severe congestion to Southern China ports due to renewed Covid-19 outbreaks. The effect has been significant, resulting in severe disruptions, causing widespread shipment delays with material shortages and great increases in cost as a result for global supply chains, Irish businesses, importers, exporters and has even reached the Irish end consumer. Comments Kevin Brady, Director of Global Business Development at the Woodland Group: “The situation is unprecedented. While we are proud that despite these challenges, we have successfully delivered an 85% success rate in FCL (Full Container Load) liftings compared to the average market rate of 50%-60% and have offered an alternative to FCL for customers through our weekly LCL (less than container load) offering, the impact on the industry and long-term effect is putting significant pressure on everyone importing from Asia and connected supply chains. “There is no quick fix, and we can expect current rate levels to carry on through to at least CNY 2022, while monitoring the situation closely and finding the best possible solutions as we go.”
Research Paper
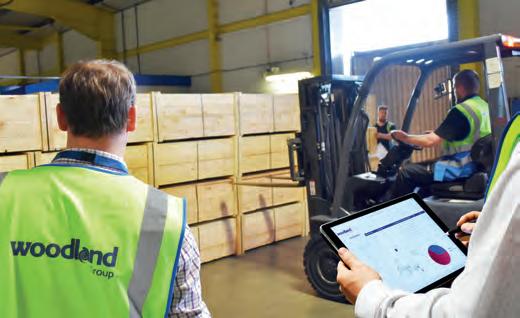
Woodland Group Ireland is currently preparing a research paper on the impact on imported goods from Asia into Ireland. Feedback received so far from Irish clients across five main commodity groups reports a sharp increase in the cost of raw materials as well as a significant rise in shipping costs. Example of such increases: • Bathroom/sanitary ware: 5-12% increase in raw material costs added to the increase in shipping costs resulting in overall cost increase of between 25-30% to the Irish importer • Outside furniture: 10-15% increase in raw material costs added to the increase in shipping costs resulting in overall cost increase of between 25-35% to the Irish importer • Lighting fixtures: 5-8% increase in raw material costs added to the increase in shipping costs resulting in overall cost increase of between 10-15% to the Irish importer • Tiles/stoneware: 5-10% increase in raw material costs added to the increase in shipping costs resulting in overall cost increase of between 25-30% to the Irish importer • Doors: 10-15% increase in raw material costs added to the increase in shipping costs resulting in overall cost increase of between 20-40% to the Irish importer Looking into the future, solutions are lacking, and concerns are increasing. Further outbreaks of COVID-19 remain a worry, with higher shipping costs, delays and a shortage of equipment expected. Unfortunately for customers, it is not anticipated that these issues will be resolved in the short-term. Feedback from Woodland’s Asia teams is that the present situation could result in shortages ahead of Christmas and into the New Year (2022). Retailers purchase seasonal goods from China months in advance, however, the level of backlogs and disruptions will continue to impact importing capacity and thus availability of certain products as we near the holidays.
Superior Operator Safety Drives JCB Site Dumper Deal
A leading agricultural and groundworks contractor has bought the highest specification JCB site dumper ever ordered in Northern Ireland.
Purchased by Co. Down based John Dan O’Hare, the brand-new Stage V 9T-2 dumper has been configured to provide the ultimate in safety and comfort for its operators. Supplied by Dennison JCB, it boasts additional features of a SiTESAFE cab with air chiller, Powershuttle 4 speed transmission, roadlight kit, front screen guard, skip guard, flexible lower Hi Viz step, 360 vision camera kit, SiTESAFE radar, white noise reverse alarm, skip raise warning and LED worklights. John Dan O’Hare Director, Brian O’Hare, said: “We were looking for a new site dumper and the JCB Stage V 9T-2 is a very good machine. The cab is a must for operator safety – with some sites demanding it now. With the weather in Ireland, it’s also essential for operator comfort! “The 9-tonne model holds plenty of material and is easy to use. We added the high specification so it does everything we need it to do and it looks the part too. Dennison JCB are always a pleasure to deal with – they never let us down.” As the largest site dumper in the JCB range, the JCB 9T-2 is an extremely powerful and productive machine that’s designed to shift huge loads of material with class-leading skip strength courtesy of thick steel side walls and heavyduty steel front and base plates. The JCB 9T-2 assures optimal levels of protection and comfort with its innovative JCB SiTESAFE cab which is fitted with a Hammerglass™ front screen and has been designed to withstand a front dump impact and side slewing impact from a 13-tonne excavator and side slewing impact from a 20-tonne excavator. Established for over 50 years, John Dan O’Hare is an agricultural and groundworks contractor based in Co. Down, Northern Ireland. The new JCB Stage V 9T-2 dumper joins five tracked excavators, two 3CX backhoe loaders, four wheeled loading shovels and a Loadall telescopic handler in John Dan O’Hare’s impressive fleet of JCB machines.
