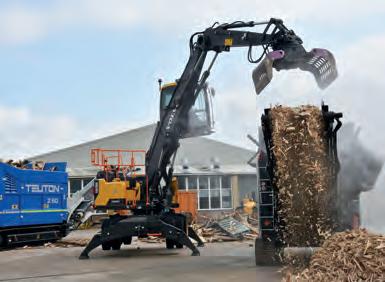
16 minute read
Recycling & Waste Management
A LOOK BACK AT A HIGHLY SUCCESSFUL LETSRECYCLE LIVE SHOW

The UK’s leading live show for the recycling, sustainability and demolition industries, Letsrecycle Live was by all accounts a resounding success, overcoming the challenges of the global pandemic and social distancing.
Held at the NAEC Stoneleigh, south of Coventry, the show was the biggest sector specific event to take place since Covid-19 restrictions were lifted. It featured more than 100 speakers across five conference theatres, live material processing, live vehicle demonstrations, and live fire suppression tests, as well as 200+ exhibitors including included Liebherr, Edge Innovate, JCB, Hitachi, Kiverco, CK International, Ulster Shredders, Neutron Equipment, Mist Air, Terex Ecotec, CRS, and Kinshofer. There was also a range of free to attend networking events including Meet the Material Buyer, Women in Waste, apprenticeship programmes, training sessions and, of course, the infamous ‘Inn on the Green’. The conference programme was split between three theatres: The Keynote Theatre, the Materials Village Theatre and the Local Authority Theatre. There was also a fourth theatre for the Demolition Expo, which was being held alongside Letsrecycle Live. The Keynote Conference Theatre tackled the key issues impacting the sector today and in the future, while at the Materials Village, there was a chance to hear experts deep dive into the issues affecting different material streams. Meanwhile, the Local Authority Theatre was where visitors heard about the latest information and developments in topics related to municipal waste collection.
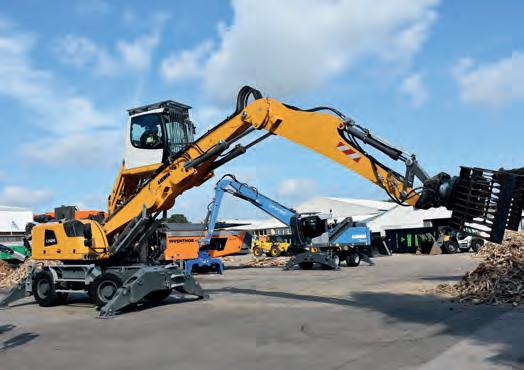

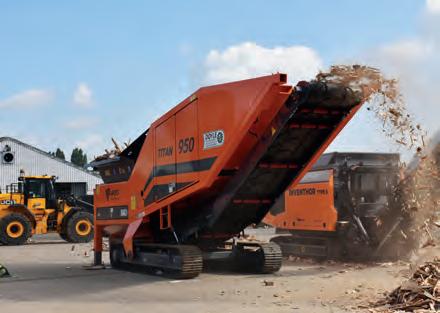
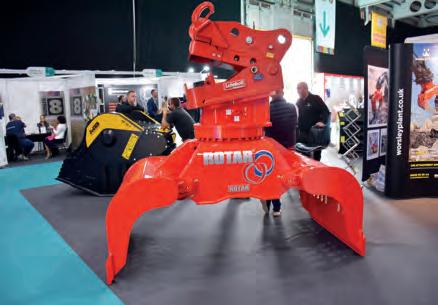
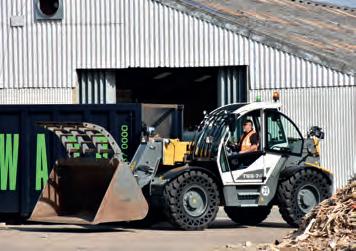
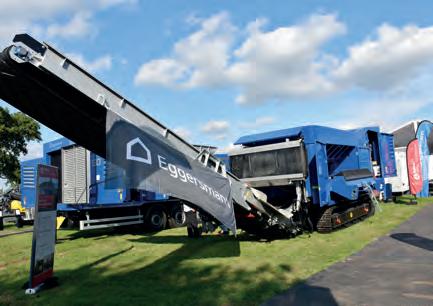
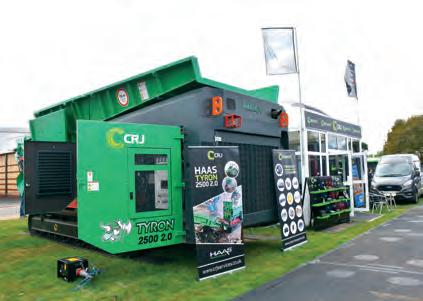
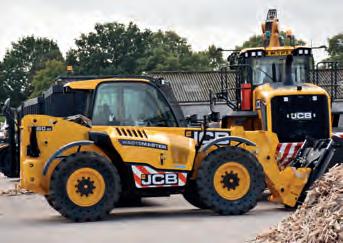
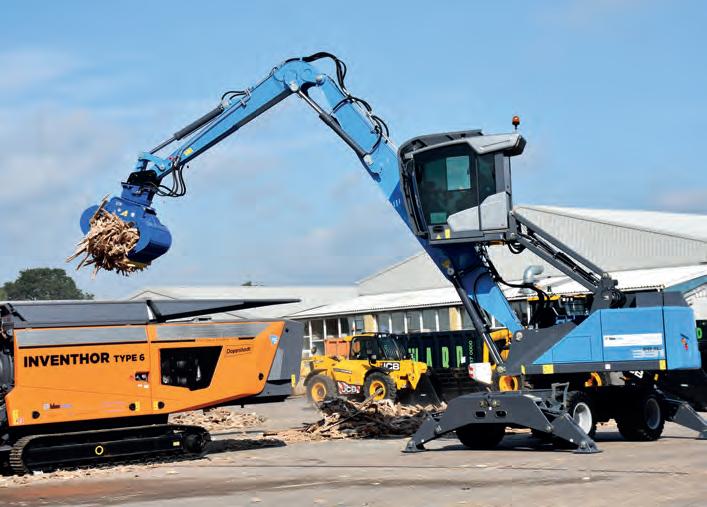
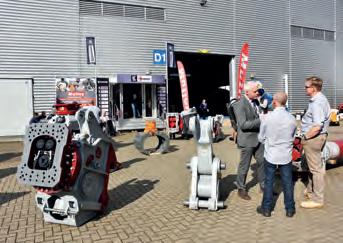

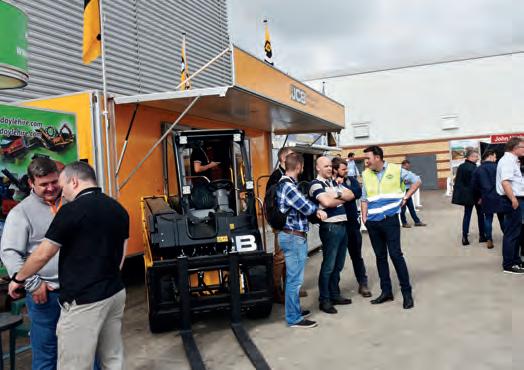
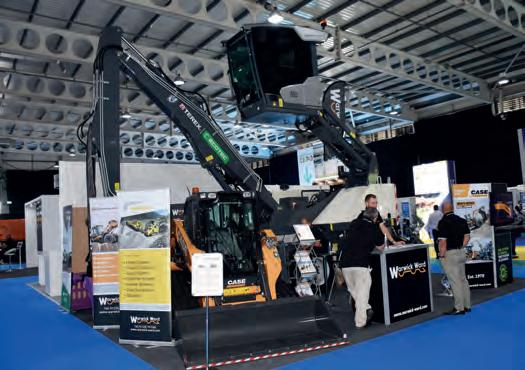
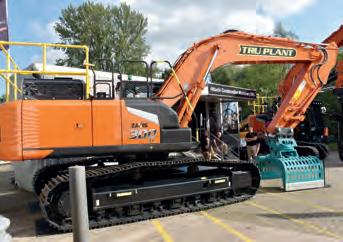
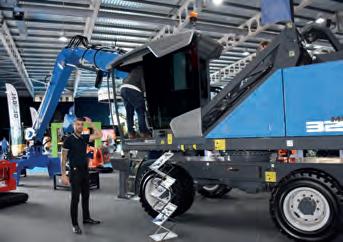
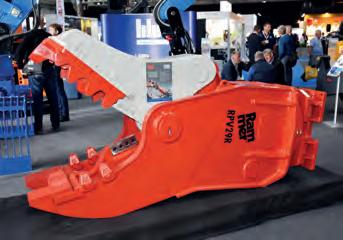
ULSTER SHREDDERS: PRODUCTS THAT ARE INNOVATIVE, VERSATILE & IN GROWING DEMAND
Ulster Shredders hasn’t allowed the Covid-19 pandemic and subsequent lockdowns to stifle its growth; it has been forging ahead with an eye firmly fixed on future expansion, as Plant & Civil Engineer’s David Stokes reports.
It has already been a busy year for the Castledawson headquartered company, which celebrated its 50th anniversary in business in 2020, as it has continued to develop and distribute new innovative commercial and industrial shedders, across both the domestic and export markets – in addition to appointing a new Managing Director. Enda Cushnahan took on the role at the beginning of the year and has already made a significant impact, having previously worked at SDC Trailers for 22 years in both financial and operational roles and more recently was the CEO of the company. He took over from Elliott Martin who has served as Managing Director of Ulster Shredders for 15 years and is now Chairman of the business. Another recent appointment was that of Business Development Manager Brian Baugh who also brings a wealth of knowledge to the role, with over 15 years’ experience in the waste industry. Both have joined the business at what can only be described as ‘an exciting time,’ albeit with the ongoing challenges of the global pandemic. Comments Enda: “Waste management and recycling has never been higher up the agenda, with the circular economy gaining momentum and here at Ulster Shredders we want to help our customers to become more sustainable and more environmentally friendly. To that end, we are continually exploring new opportunities to help companies to re-purpose their waste.” With a global customer base that ranges from SMEs and office centres to large scale industrial plants, Ulster Shredders focus on four main sectors - confidential destruction, production processing, volume reduction and mobile shredding. Their 43,000sq ft state of the art engineering facility houses several complete shredding lines, allowing their engineering team to design equipment, conduct trials, perform testing, and demonstrations of customers’ materials under real production conditions. Ulster Shredders also design and manufacture bespoke systems, which are tailored specifically to meet the demands of each customer’s application, no matter how difficult or complex those requirements might be.


(L-R): Paul Atkinson, Sales and Service Director, Enda Cushnahan, Managing Director and Elliott Martin, Chairman.
Leading Manufacturer of Industrial Shredding Machines.
Working with Customers
“Last year the UK government set out ambitious plans in what
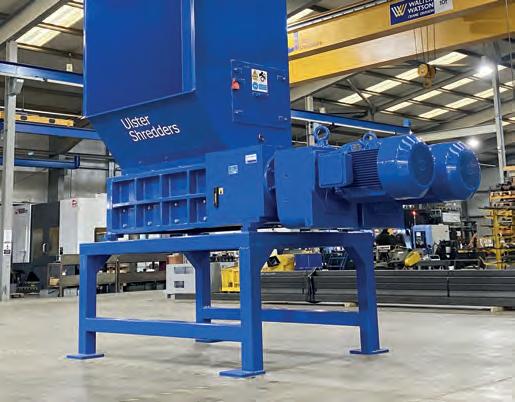

Ulster Shredders engineering capability, from concept design through to final product assembly and performance testing, offers a unique one stop shop solution.
it called its Circular Economy Package that includes a target to recycle 65% of municipal waste by 2035 and reduce the amount of waste sent to landfill or incinerated. It is companies like Ulster Shredders that can significantly contribute towards meeting those targets by working closely with our customers to offer innovative solutions that will help them to better manage their waste and meet those recycling goals.” Comments Sales and Service Director Paul Atkinson: “No two customers are the same, so we take time to sit down with them, find out what their waste management challenges are, consider what materials they want to process and then work towards finding a solution that is fit for their individual purpose.” Adds Paul: “We have invested substantially in a Research & Development Centre, as part of our expansion plans, to demonstrate to our customers what our machines are capable of and how the equipment can be utilised to suit their requirements.” While the company’s domestic market continues to grow, so does its global reach, with some 2,000 shredders of varying sizes and capabilities working for customers around the world. Says Enda: “Having already delivered machines to countries such as Australia, the Middle East, South Africa, the USA and Jamaica, there remains great potential for further growth abroad, and that’s what we will also be targeting in the months ahead.” Recent orders include a machine for an American based company to process waste plastic, another bound for a government department in the Middle East for handling the destruction of confidential material, a third to shred receptacles used in the Covid-19 vaccination programme, and another to reprocess leather for use in the production of shoes and handbags, all of which underlines the sheer versatility of Ulster Shredders’ product portfolio. Not surprisingly, Ulster Shredders enjoy a high level of repeat business for its extensive range of equipment, one of the latest additions being the U-75LB, a slow speed, twin shaft shredder that can handle a variety of challenging material, including food waste; it features a precise and efficient shredding chamber that effectively removes and separates packaging from food waste which later is used for anaerobic digestion. Its development coincided with the company gaining membership of the Anaerobic Digestion and Bioresources Association (ADBA) to support the continued growth of the anaerobic digestion industry. It will also enable the company to showcase its industrial shredders and highlight how its machines can benefit the anaerobic digestion process.
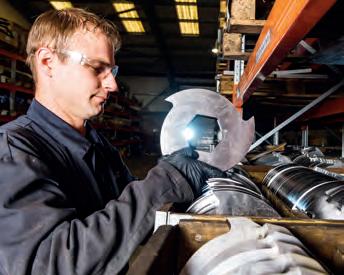
Ulster Shredders also offer a maintenance and support service that is divided into two areas of expertise, Spare Parts and Technical Support.
Focused on Service & Support
As we mentioned, the team at Ulster Shredders has also been strengthened in recent times with a number of key appointments, including Brian Baugh as Business Development Manager who is focusing his time in the southern area of England and Wales, while another new addition is Sales Manager Jude Diamond who will support all shredding enquiries in the north of England and Scotland. Also joining the team is Digital Marketing Executive Jill Sheridan who is responsible for increasing brand awareness, while Johnny McClean, who has been with the company for over 10 years, has been appointed the role of After Sales Manager. Other customer focused developments include a range of asset finance solutions, with a wide choice of flexible and tailored funding options available from the company’s finance partners, including hire purchase, finance lease or operating lease. In addition, Ulster Shredders has introduced a new U-Maintenance package, giving customers the opportunity to receive scheduled maintenance work on their Ulster Shredders equipment. “Customer satisfaction is a key objective that we strive to meet and by introducing the U- Maintenance package, we can support our customers through the lifespan of their shredder. Our highly skilled technicians will carry out all maintenance work, using the latest techniques, providing the best methods and solutions,” says Paul. “We also carry an extensive range of spare parts which we ourselves manufacture inhouse, so availability is never an issue.” Additionally, Ulster Shredders also provide comprehensive training programmes for all machine operators equipping them with the correct skills, knowledge, and methods to operate their machines at the highest level.
Looking to the Future
As the company looks forward to the continued easing of the Covid-19 restriction easing, it is back on the road, recently promoting its products at both Let’s Recycle Live in Stoneleigh in Warwickshire and the RWM exhibition at the NEC in Birmingham. “After over 18 months of restrictions, it’s great to be back in front of our customers and we are looking forward to other opportunities to meet them in the coming months, while we increase our innovative and technically advanced product range and further explore new and emerging markets,” comments Enda. “We have an excellent team of professionals and well qualified personnel around us, and we certainly don’t plan to stand still.”

recycling & waste management
RiverRidge Calls for Urgent Government Action to Address Driver Shortage
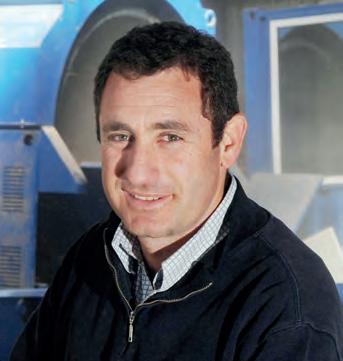
The COVID-19 pandemic has highlighted the importance of maintaining essential services as the backbone to any functioning society and economy. Add to this the complexities of Brexit and the growing significance of the digital economy, and the result is a perfect storm for logistics in Northern Ireland which is leading to a dramatic shortage of drivers.
This shortfall, currently numbering at 5,000 drivers in Northern Ireland, is keenly felt by many industries but none more so than the waste sector which is unique in that it provides an essential service to all businesses and households alike. As Northern Ireland’s leading waste management provider, RiverRidge relies heavily on its drivers as the backbone of the service it provides to local councils and commercial customers – which involves not only the transportation of waste but also the collection and removal of waste for treatment. The process involves some manual handling in the moving of bins to their vehicles for offloading. In recent years, huge progress has been made by the industry to reduce the reliance on landfill, increase recycling rates and improve the carbon intensity of waste processing – all important contributors of Northern Ireland’s zero-carbon aspirations. However, the crisis in availability of qualified drivers is threatening to erode these environmental gains due to the inevitable constraints in waste collection capability. The supply shortage has also put upward pressure on cost, with RiverRidge seeing unprecedented wage inflation for its drivers which will inevitably lead to higher costs for customers. According to Brett Ross, CEO of RiverRidge, “To say that we have reached a crisis point regarding the availability of drivers is no exaggeration. If this situation persists, it will severely impact the enormous gains we have worked hard to achieve at RiverRidge with regard to environmental performance, customer service and pricing, never mind the unimaginable repercussions if waste cannot be collected.” He added, “That is why we are calling on Government to act swiftly and decisively to implement three short and medium-term remedies, which we believe will go a long way in addressing this crisis. These are:1, Address the current delay in turnaround times for driver testing to allow unqualified drivers achieve their professional licence at an accelerated pace; 2, Grant temporary work visas to EU HGV Drivers and 3, Introduce an incentive scheme to attract younger people into a career as a professional driver.” RiverRidge is urgently seeking qualified drivers to join its team. “There has never been a better time to join Northern Ireland’s leading waste management company where you are guaranteed a highly competitive salary, retention bonus and benefits. You will also enjoy other work/life benefits such as stable hours, local work and career development. Above all, we prioritise your health and safety by operating to the highest standards in our industry, ensuring the best possible work environment for every member of the RiverRidge family.”
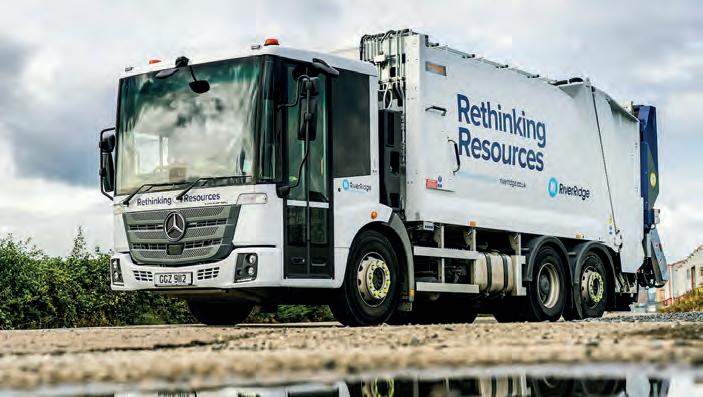
Brett Ross, CEO RiverRidge.
Re-Gen Waste in export deal with Norwegian giant
Newry recycling company Re-Gen Waste has signed a contract which will see the Northern Ireland company supplying 100,000 tonnes of refuse derived fuel to Oslo.
The three-year contract with Fortum is for its combined heat and power facility at Klemestrud in the Norwegian capital. Joseph Doherty, Managing Director at Re-Gen Waste, is delighted to have secured the contract with the Norwegian giant. “We are delighted to work with Fortum. Re-Gen has used its experience and export expertise to send the firstever bulk shipment of refuse derived fuel from the UK to this waste-to-energy facility in Norway,” says Joseph. He adds: “Teamed with the carbon efficiency and cost effectiveness of bulk shipping, this provides maximum value recovery of the energy from waste provided. “Fortum is processing the waste to provide electricity and heat for Oslo city and nearby towns. With the city’s target of 95 per cent reduction of greenhouse gas emissions by 2030 in focus, the Klemestrud facility in Oslo has successfully developed a carbon capture and storage process which recaptures the CO2 emissions. This is part of the Longship project developed by the Norwegian government which will see recaptured CO2 being stored in underground reservoirs. “This cooperation works for Re-Gen, as both partners are committed to reducing, recycling, and reusing materials effectively as we aim to meet government legislation. It is estimated that greenhouse gases account for 25 per cent of current global warming, and we are working with our partners at addressing the issues by maximising energy recovery whilst minimising our carbon footprint.”
recycling & waste management QUANTRON electric waste disposal vehicles impress under test
Quantron AG electrifies commercial vehicles from 3.49 to 44 tons gross combination weight, including waste disposal vehicles such as the Mercedes-Benz Econic. The company’s environmentally friendly solution, called Quantron QHB, has numerous advantages and also impresses in practical tests.
With immediate effect, the company is also offering a fiveyear full warranty on selected models of its Mercedes-Benz Econic, MAN TGS and DAF CF electric waste disposal vehicles, as well as on selected rear-loader bodies. The QHB scores with its power of up to 350kW and a maximum torque of 3500 Nm. The battery of the QUANTRON vehicle also impresses with up to 280 kW storage capacity. This enables the vehicle to either cover a range of up to 240 km (without body activity) or to empty up to 1,000 refuse containers in a 9-hour shift in two refuse tours, without intermediate charging. Further advantages of the QHB are that the e-drive technology and electrification can also be retrofitted to existing vehicles and is also suitable for various attachments and superstructures. The batteries installed are cobaltfree and equipped with extremely flame-retardant lithium iron phosphate (LFP) technology. The environmentally friendly and low-noise QHB waste disposal vehicle has already been proving its worth for many months. The QHB has been in use at leading German waste management companies since May 2020 and has proven its suitability for everyday use in cities such as Frankfurt, Leipzig, Düsseldorf, Nuremberg, Bremen, Ulm, Darmstadt, Constance, Kassel, Halle and Essen. The easy handling for drivers and loaders was rated particularly positively. For example, the operation of the electric QHB differs only minimally from that of a conventional vehicle, and no special handling is required in the fleet. The vehicle could be dispatched and used in all applications, with very few exceptions, in the same way as previous internal combustion vehicles. Up to 1000 refuse containers and two refuse tours in a 9-hour shift were part of the compulsory discipline during the operations of the Quantron QHB 27-280.
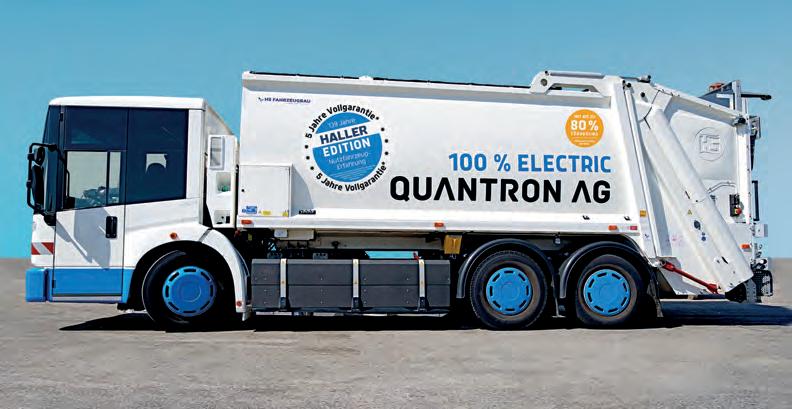
RiverRidge has reinforced its commitment to sustainability by joining more than 200 Northern Ireland businesses to become part of the responsible business network, Business in the Community (BITC).
This is the latest initiative from RiverRidge in its quest to become a more sustainable organisation and showcase the best practices in the waste industry. The company has made remarkable progress in diverting waste from landfill, encouraging recycling over recovery and recently announced plans to utilise waste streams to create vehicle fuel. Members of the Business in the Community network collaborate to advance the responsible business agenda, which includes supporting their people, being a force for good in society and having a positive impact on the environment. Businesses in NI have an important role to play in addressing society’s biggest issues and RiverRidge is proud to play their part by committing to making Northern Ireland a better place in which to live, work and do business. Managing Director of RiverRidge, Brett Ross said, “Business in the Community is a great network and we’re proud to have joined many of Northern Ireland’s leading organisations to become a more responsible business. Over our 10 years in business, we have been passionate about sustainable practices and meeting our environmental goals, and through membership with BITC, we are one step closer. We are looking forward to progressing with the help of BITC and its members.” Kieran Harding, Managing Director, Business in the Community NI said, “We are delighted to welcome RiverRidge into membership. Our members recognise the huge benefits that come from managing their businesses in a responsible and sustainable way, and we look forward to working with all of our members – established and new – supporting them on their responsible business journeys. “We aim to help and inspire companies to address three campaigning areas – their People, the Planet, and the Place in which they operate. By working together to tackle social and environmental issues, businesses in membership with us can truly become a force for good in society.”
PLANT & CIVIL