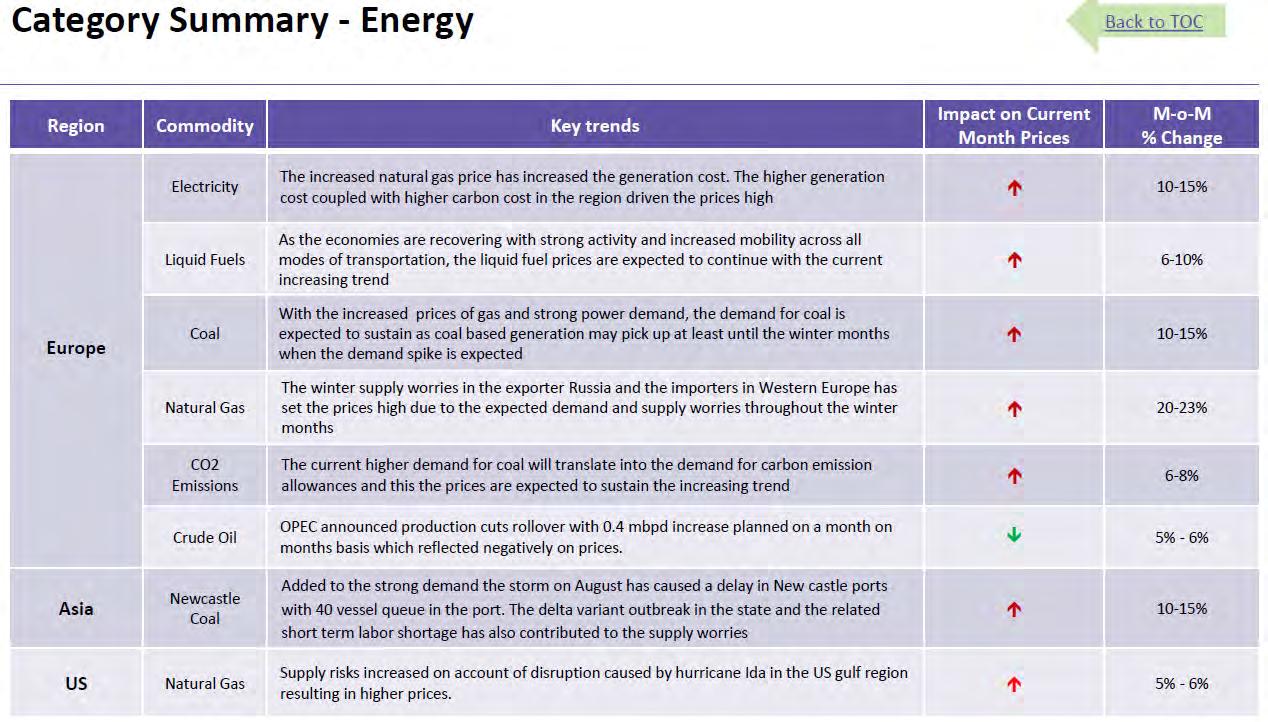
23 minute read
Gordon Best, MPANI
FROM THE DESK OF: GORDON BEST, REGIONAL DIRECTOR, MPANI
CONFRONTING Gordon Best, MPANI CHALLENGES ON ALL FRONTS
The recent Ulster Bank PMI survey revealed again an all too familiar story, with inflationary pressures and lengthening supplier delivery times. Within the UK, Northern Ireland continues to report the steepest rises in input costs, with local firms raising the prices of their goods and services at faster rates than any other region.
Price pressures linked to raw materials, fuel, freight, wages and Brexit continued to be cited by survey respondents. So why is this unprecedented increase in material costs and shortages happening and when is it likely to end from? In January 2021 the Carbon price sat at around £35 per tonne, At the end of September its sitting at £65. Expectation is that it could rise to £100 per tonne by June 2022. The cost of shipping a container from China to Europe has risen from £1,500 to almost £14,000 since January 2021. Wholesale prices for gas has risen 250% since January and 70% since the start of August. 60% of UK Natural Gas is imported. Oil is up from $40/barrel this time last year to $74/barrel, + 85%, and set to remain at $70+ to year end. Gas Oil linked to oil is up over 40% since same time last year. Furthermore, Impact of red diesel changes from April 2022 will see doubling in price. All of the above feeds into the construction supply chain and will continue to make the cost of supply of cement, bitumen, aggregates, admixtures, pigments and transport extremely volatile. UK IMPACT
The construction materials shortage can, in part, be traced back to increased building and home improvement activity in 2020, particularly during the first lockdown. This led to a slowdown in the production of materials from some factories in the EU, and supply chains have remained stretched ever since.
But while construction output reached a 24-year high in June, demand is not being met by supply, and suppliers’ delivery times have lengthened The construction products manufacturing sector posted a fourth successive quarterly expansion in the second quarter of 2021, according to the latest Construction Product Association’s (CPA) State of Trade Survey. Private housing, infrastructure and private housing repair, maintenance and improvement (rm&i), in which activity remains firmly above pre-coronavirus levels, continued to be the main drivers of growth. Material cost inflation, however, remained a prominent feature and supply-side constraints were seen as the key concern for the year ahead. In 2021 Q2, nearly two-thirds of heavy side manufacturers and 44% of light side manufactures reported that sales had increased compared to Q1. With demand in private housing and private housing rm&i expected to be sustained by both government stimulus and increased appetite for properties with more outdoor and office/ study space, 67% of light side firms expected a rise in product sales in the year ahead. On the heavy side, this balance (79%) was the highest in nearly eight years, reflecting work occurring on large infrastructure projects. Plans for hiring also remained on the table, with 61% of light side firms anticipating increasing headcount, the highest balance in seven years. The supply of raw materials and components over the coming year remains the largest concern for manufacturers due to bottlenecks in the global supply chain. Unsurprisingly, raw material prices followed next as a potential constraint for heavy side firms alongside demand, whereas labour availability concerns rose up the agenda for light side firms. The cost of materials for repair and maintenance work rose 6.7% between JuneJuly, and increased by 23% between July 2020 and July 2021, according to the BEIS WHICH MATERIALS ARE AFFECTED?
Timber - There has been a nationwide timber shortage since the first lockdown in March 2020, and imports remain an issue, against a backdrop of high demand for wood and wood products. Steel - Steel is in high demand globally, and shortages could persist until the end of the year. British Steel recently stopped taking orders on structural steel sections due to “extreme demand”. Roof tiles - Roughly half of National Federation of Roofing Contractors members reported a shortage of concrete roof tiles earlier this year. Lead times for concrete tiles are between 20-36 weeks, on average, while lead times for clay times are between 4-8 weeks. Cement - Supplies of bagged cement have been strained since late last year, and Pal Chana, executive director of the Mineral Products Association, warned in July that supplies will not return to normal until the end of the year. Electrical components - Certain electronic components, caused by a shortage of raw materials, could extend into next year. Paints and sealants -Supplies to the UK are restricted due to a global shortage and cost of shipping containers. Plaster and plasterboard - There was a severe plaster shortage earlier this year, and while supplies improved earlier this year, plasterboard has been subject to extended lead times, the CLC said in June.
LABOUR AND HAULAGE
There is now a shortage of more than 100,000 drivers in the UK, out of a pre-pandemic total of about 600,000, according to a survey of Road Haulage Association member estimates. Some suppliers have reportedly been asking builders’ merchants to collect their orders as they cannot get enough drivers to complete deliveries. The demand for construction workers is now close to 20-year high, according to the Office for National Statistics (ONS), with employment in the construction sector falling from 2.3m in 2017 to 2.1m at the end of 2020. This represents a 4% fall in UK-born workers and a 42% fall in EU workers. Jobs website Indeed says construction has seen the highest growth in average advertised salaries since July, while Noble Francis expects 500,000 UK-born workers to leave the industry in the next 10 years as a demographic “bulge” of 50 to 65-year-olds retires. As a result of Industry concerns government has been asked to intervene amid the construction materials shortage which has left the construction sector on its knees.
LOCAL DATA FROM MPANI MEMBERS
Price increases we have experienced over the last 3 years: Cement +15.91% per tonne; Aggregates +14.2%; Steel Coil/rebar +48.1%; Pre-stressing strand +39.2%; Labour costs +19.6%. I couldn’t get an accurate figure for the haulage, but again it would easily be over 15%+ One local company with a turnover of approx. £40 million has reported that based on the same workload volume revenue would need to increase by up to £2 million in the next 12 months to cover increased labour, energy, materials and insurance costs known at this moment in time. CONVEYORTEK VISIT
MPANI are delighted to announce that we have organised a visit to Crumlin based and MPANI Affiliate Member Conveyortek for our Young Leaders Group. The visit and meeting is taking place on Wednesday 20th October. Conveyortek will be demonstrating how immersive design technology is being used to develop automated conveyor systems and bulk handling conveyors. This technology can help to reduce prototyping costs and produce an interactive design experience for customers when designing new conveyors, factories and metal separation centres. The presentation will also cover some key energy saving tips for conveyors and how IOT technology can provide valuable data to assist with planned maintenance schedules. We hope to have some photos in the next Plant and Civil edition.
MANAGERS WORKSHOP
The final Quarry Line Managers Workshop is planned for the 20th October 2021, this will cover County Tyrone. Following this we will be running a further workshop on 3rd November 2021 for Concrete Industry. The date for the event has been set for 17 November, 10.30 to 12.30. The event will have an online format with 4 presentations and an opportunity for Q&A session following each. A number of potential topics have been discussed including managing mental health. We are delighted that in his role as an HSENI Board Member, MPANI Chair Simon McDowell has agreed to Chair the event. MINERALS POLICY
I recently met online with officials from Armagh Banbridge Craigavon Council to discuss the development of their Minerals Policy and the challenges of doing so as a result of limited local information on the minerals sector. Pre-Covid we did engage with a number of Councils and held meetings with local Members to explain the information required to develop local mineral policy, mineral safeguarding areas and ensuring a sustainable supply of construction materials/ aggregates for the length of their local development plan and beyond. It is hoped to start this re-engagement as MPANI have been told by a number of Councils they are struggling to come up with up-to-date accurate data. MPANI members must be aware that any local minerals policy will be intensely scrutinised and must be based on accurate evidence.
MPANI MANIFESTO
There are signs that our local politicians are well into “election mode” with the next NI Assembly Election due to take place in May 2022. With this in mind MPANI will be producing our own Manifesto that we can circulate to the parties and individual MLAs. This Manifesto would cover many of the points we make in our previous “Priorities for NI Government” document. The Manifesto will be high level and support calls from other industry bodies to improve the business environment and growth potential for Northern Ireland. Issues would include: Improving the planning system and adequately resourcing planning decision making including statutory consultees at both
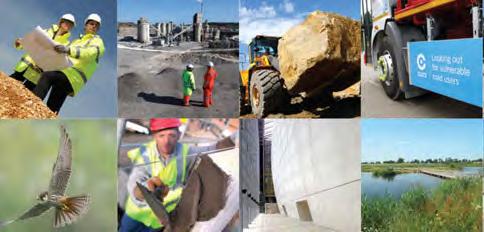
CONTINUED
DfI and local Council Level; Implementation of Multi Year infrastructure and maintenance budgets; Support for an Infrastructure Commission; Further development of apprenticeships and investing in skills of our young people that align with the needs of business; Make industry taxation fairer; Support local business in energy transition; Support responsible operators through the procurement and rating systems. NI PROTOCOL
Last, but by no means least, the ongoing challenges created by EU exit and the implementation of the NI Protocol continue to be addressed by the business community here. NIBBWG continue to engage with all those who will listen to ensure that the arrangements work for both businesses and people in Northern Ireland. The recent extension to grace periods is to be welcomed but is seen by many a “can kicking” exercise and has taken the heat out of the current log jam. Feedback from MPANI members on the impact of the protocol has been few and far between. The results from the recent MNI survey, to which a number of MPANI Members submitted a response, indicated that during the March to June period HMRC introduced the requirement for Supplementary Declarations which was the 2nd stage in completing the full frontier customs declaration between GB and NI. This resulted in a rise of those who say they are currently struggling with the processes from approximately 1/3rd of manufacturers to just over 40%. At the same time the numbers who believed the problems were likely to ease dropped from 20% to 10%. However, there was a drop from 77% to 70% of those who said they experienced some negative impact since the start of 2021. There remains little evidence that HMG have assisted GB firms to get to grips with the new requirements to send goods across the Irish Sea which almost have of firms reporting that their GB supplier remains unprepared. It seems to be left to GB firms to scramble or NI firms to offer support to their supply chains. One in 5 firms continue to report their GB suppliers are unwilling to send goods to NI. There is some evidence that EU suppliers are beginning to understand that goods can freely circulate to NI with now more than half of firms reporting business as usual and a reducing amount saying their EU suppliers are unprepared. One in 5 continue to report that their GB sales are negatively impacted but there is an increasing amount of firms who say their sales are as expected. On EU sales firms report continuing uncertainty in EU customers about the status is NI goods however there is an increasing number reporting that they’ve picked up significant new sales – up from 5% to 11%. 40% of manufacturers say they believe the disruption in supply chains and sales are likely persist through the rest of this year. In April one in 5 firms just wanted the Protocol scrapped but this has grown to almost 30% reflecting the burden of the additional requirements introduced in March. However, more firms want the NI Executive to identify and grasp the opportunity of the Protocol and a half say the Protocol is here and with simplifications we should get on with it. Government recently announced The UKG will be extending the standstill period for UKCA markings for a further 12 months, meaning it will end on 1 January 2023. This means all sectors, apart from medical devices (which has until 30 June 2023), can continue to use CE markings when placing goods on the GB market. Notably for NI qualifying goods - the UKG has legislated for unfettered access to the GB market, without the need for additional approvals before placing goods on the market in the rest of the UK. (i.e. you can place qualifying Northern Ireland goods on the market in Great Britain based on the conformity markings you use in Northern Ireland). In recent times we are starting to see some signs of hope and flexibility coming into the positions of both the UK and EU. Let’s hope common sense solutions, which are there to be grasped, are implemented and we see less ideological and political grandstanding on sovereignty and protection of internal markets.
Best wishes to everyone and continue to stay safe!! Gordon

www.mpani.org
TEEING OFF WITH DENNISONS AT JCB’S EXCLUSIVE GOLF & COUNTRY CLUB
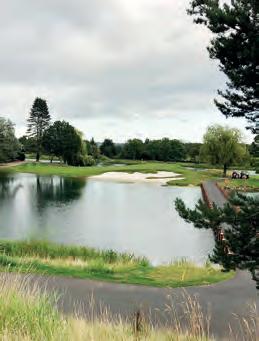
Dennisons recently hosted a day out at the incredible JCB Golf and Country Club in Staffordshire.
Created by internationally renowned Robin Hiseman of European Golf Design, the new 7308-yard par 72 course is certainly a challenge for elite golfers at full distance, while allowing corporate golfers a highly enjoyable experience, as a party of Dennison JCB & Dennison Commercials customers will testify; safe to say all had a thoroughly enjoyable experience. The JCB Golf and Country Club reflects the bold, ambitious vision of JCB Chairman Lord Bamford. Spanning 240 acres of rolling countryside, it has been designed and built using industry-leading technology to create aesthetically appealing tee shots, wide, sweeping fairways and interesting, yet fun greens complexes. It dips in and out of the woodlands and seamlessly brings the existing water features into play. Also on the development is the JCB Golf Academy, a place where students, members and guests of all abilities can learn and hone their skills in a relaxed yet positive environment. It is equipped with cutting-edge technology and boasts some of the latest video analysis coaching studios and custom fitting technology anywhere in the world. Nestled within the course, are 10 luxury lodges, available exclusively to members. Each lodge includes four spacious ensuite private bedrooms with views across the course.
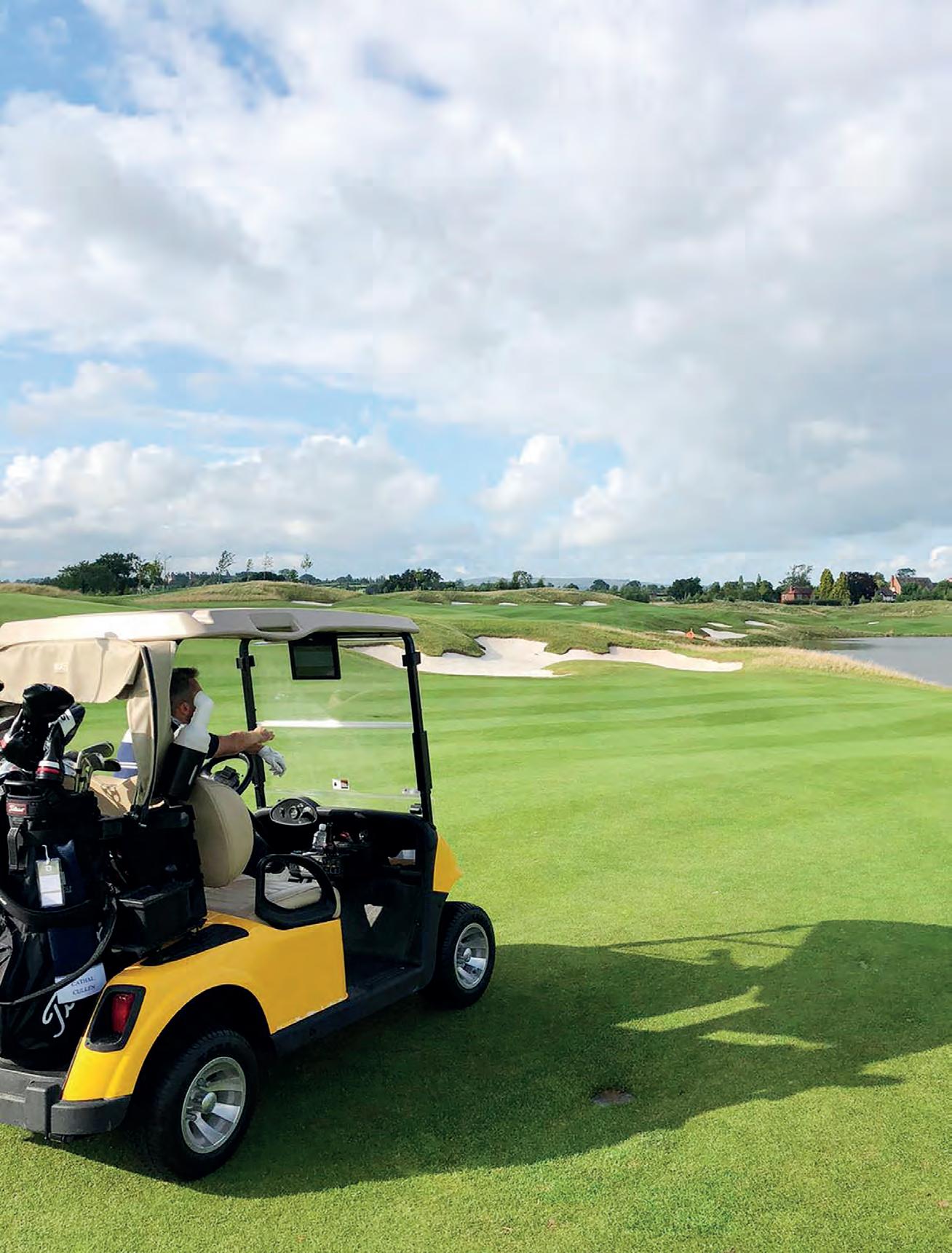
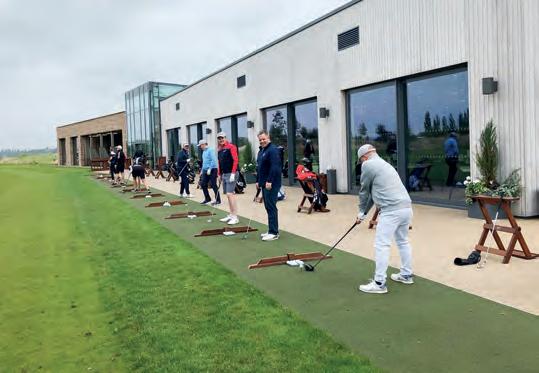
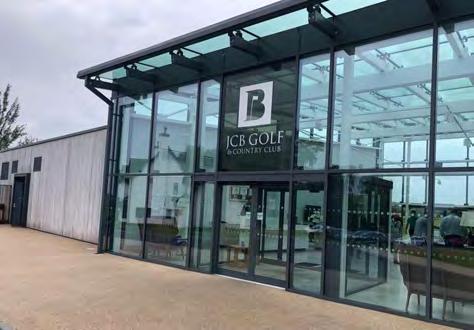
news
Soaring Demand Creates 100 New Welding Jobs at JCB
JCB is recruiting 100 new welders for its Staffordshire factories as demand for its products continues to soar. The recruitment drive has just got underway for the permanent jobs at JCB’s World Headquarters and its plants in Cheadle and Uttoxeter.
JCB has also welcomed an additional 15 new recruits on to its fabrication and welding apprenticeship. In the past three years, almost 70 welding apprentices have passed their courses – and all gained permanent JCB jobs. The news comes as demand for JCB machines reaches historic highs with most products now sold out until next year. It also comes in a year when JCB has recruited 1,350 new shop floor employees and handed permanent JCB contracts to 1,000 agency employees. JCB Chief Operating Officer Mark Turner said: “Over the past five years the number of welders in the UK has shrunk, which presents businesses with a big challenge at times of high demand. “JCB has been working very hard over the past few years to tackle this shortage and attract new entrants to this highly-skilled job with its apprenticeship and training programmes, which have been very successful. “We are delighted to be building on that success with the creation of 100 permanent new welders’ jobs. We offer some of the best conditions and pay rates in the region and with opportunities for nightshift work and overtime, this is great news for welders in the area looking to join a successful global company.”
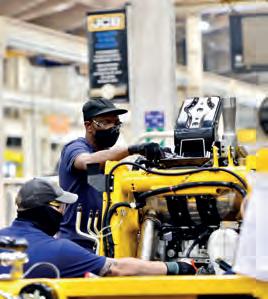
New Generation of Telehandlers from Bobcat
Bobcat is launching the company’s new generation R-Series telehandler range, providing a choice of 12 models with Stage V engines. The new telehandlers cover lifting heights from 6 to 18 m with maximum lifting capacities between 2.6 and 4.1 tonne.
This is the latest phase in Bobcat’s revolutionary ‘Next is Now’ programme, combining innovative product development and diversification with more intelligent, user friendly technologies and services that reshape how work gets done. Commenting on the R-Series launch, Gustavo Otero, President, Doosan Bobcat EMEA, said: “Telehandlers are a fundamental asset of our business strategy and key pillar of our Next is Now initiative. Our new ground-breaking R-Series range offers high performance, robust machines for maximum uptime with a focus on accurate controls and intuitive operation for tackling any job on the construction site. With these new models and the increased investment in our telehandler business, we are aiming to double the production of Bobcat telehandlers by 2025.” The new R-Series telehandlers offer agility on demand, with a newly configured transmission system providing enhanced smoothness to carry out the trickiest jobs at height with surgical precision. These operations are also facilitated by the combination of the Boom Positioning System, the new updated, ultra-accurate joystick, the inching function and the improved visibility from the cab. An enhanced inching pedal design is easier to use and reduces fatigue. A higher engine brake provides a shorter stop distance and increases safety on construction sites. Turtle/ rabbit speeds are standard on all models and operated from the joystick. There is a new DYNAMIC mode for applications requiring rapid transmission response and the new optional hand throttle with FLEX DRIVE function allows for the control of travel speed independent from engine rpm. Bobcat R-Series telehandlers feature a new cab with unmatched ease of use, designed around the operator, offering a unique central control panel for optimized 360° ergonomics. The new high quality, contemporary interior of the cab features stand-out R-Series branding, colours and textures that clearly reflect Bobcat’s DNA. In the ergonomic design, all surfaces have been optimised to offer increased space and visibility. It is based around a new 5-inch LCD display providing interactive and streamlined information, including the feed from the rear camera for easier and more precise operation.
Easy Maintenance
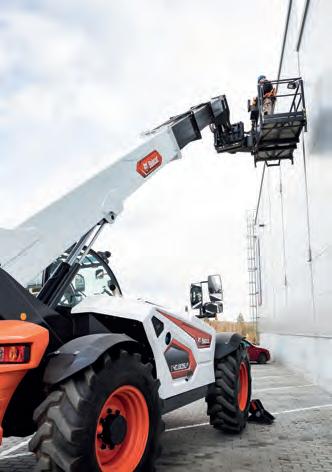
All R-Series telehandlers now feature a new engine hood with a steeper profile that increases visibility and reduces blind spots by 15% on the right hand side of the machines. Together with the new dashboard design, this provides excellent unobstructed visibility from the cab, allowing the driver to move around the job site with ease and minimises accidents or mistakes. Access to the engine compartment has also been improved, enabling easier maintenance. Under the hood, R-Series telehandlers are powered by new upgraded versions of the Bobcat D34 Stage V engine, utilising DPF after-treatment, which is automatically regenerated with no impact on performance and no disturbance for operators. The lack of AdBlue in the 75 HP engine and the absence of EGR in the 100 HP engine provide further advantages. Overall, the decreased number of intervals from five to three in these Stage V models allows for easier maintenance and a lower total cost of ownership. These machines are also connected via Bobcat’s new Machine IQ telematics system further enhancing the efficiency of the ownership experience. For lesser regulated markets, the proven Perkins Stage IIIA engine provides high power and the simplicity of its mechanical injection system. Quentin D’Hérouël, Product Manager Telehandlers at Doosan Bobcat, concluded: “As with all new Bobcat telehandlers, the R-Series offers customers peace of mind with a 3-year warranty (or 3000 hours) on the entire machine as standard from the factory. Bobcat is the only manufacturer to provide a 3-year warranty as standard, allowing customers to focus entirely on growing their business without worrying about their machines. And with regards to the cab interior, we’re now the leaders in the field. As we have constantly involved our customers in their design, we’re confident that the new generation machines will be very well received in the marketplace.”
INSTITUTE OF QUARRYING NORTHERN IRELAND BRANCH GOLF DAY 2021
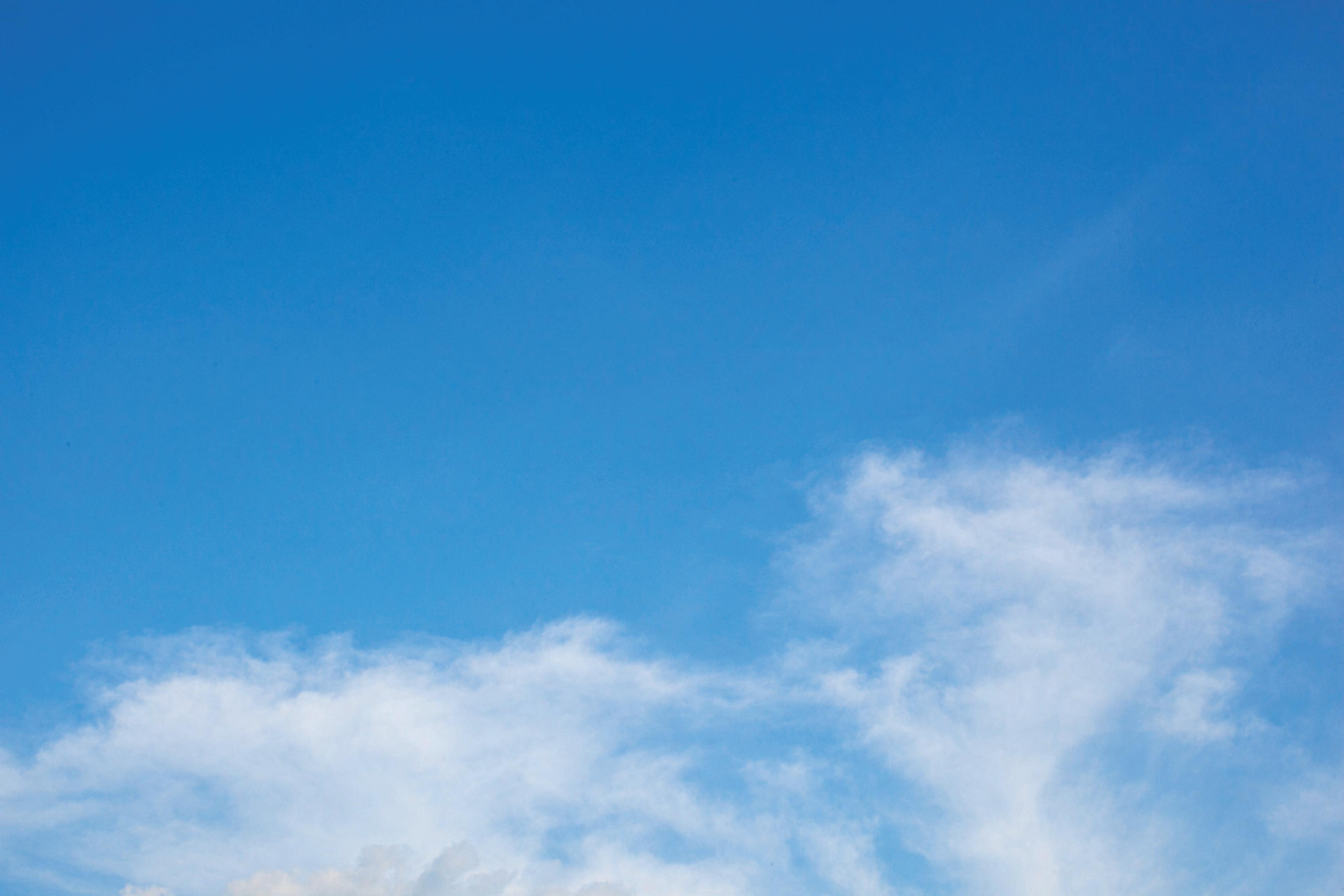
The Northern Ireland Institute of Quarrying held their annual golf day recently at the impressive Lisburn Golf Club, with members and guests having a fantastic day in the Summer sunshine.
It was great to get everyone together again and return to some sort of normality, with all who attended having a tremendous day of golf and networking. Here is a selection of pictures of the 4 ball Teams and winners.
www.quarrying.org
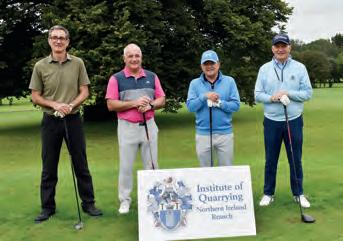
MPANI: Bryan Magee, Steve Morley, Gordon Best and Garfield Harrison
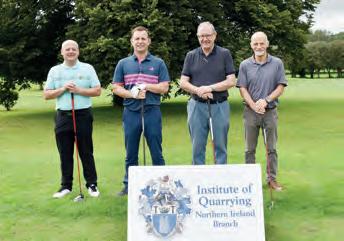
Jabez Safety Solutions: Graham Mitchell, Jason Hopps, David Johnston and Alwyn McCreanor. Mattest: Olcan Kearney, Neil Cook, Colin McGookin and Jordan Hogan.
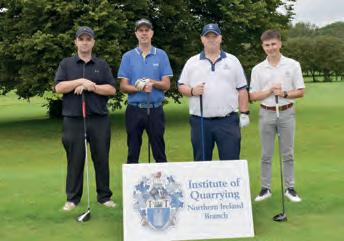

Northstone: David Luke, Paul Adamson, Ryan Nicholl and Andrew Delargy

Gibson Bros: Ken Hood, Michael Gillen, Dennis Davidson and Norman Lamb.
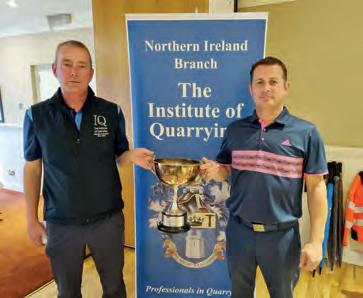

IOQ Chairman John Moore and the winner of the Visitor prize Jason Hopps with 40 points. IOQ Chairman John Moore and the winner of the Members price Roy Wallace with 36 points. Finning: Chris Stevenson, Stefan Barrett, Niall Morris and Colin McCarol.
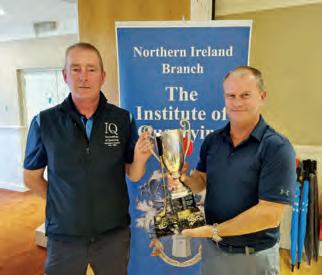
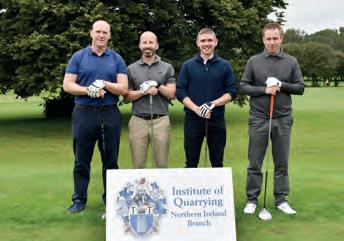
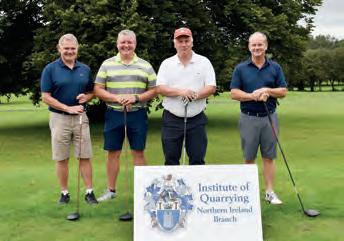
Orica: Mark Orr, Andrew Glover, John McCartan and Roy Wallace.
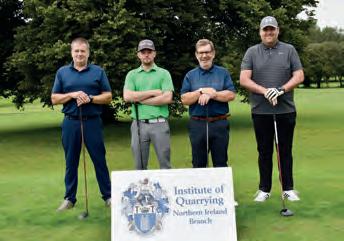
Whitemountain: Alister Jones, Ryan Daly, Gerard Lawless and Pat O’Connor.
IOQ Chairman John Moore with Norman Lamb of the Scotts Fuels Team winner of the Team Prize with an impressive 96 points.
ENGCON TILTROTATOR PROVES WISE INVESTMENT FOR SEAFORDE DIGGER HIRE
BY CHRIS MCCULLOUGH
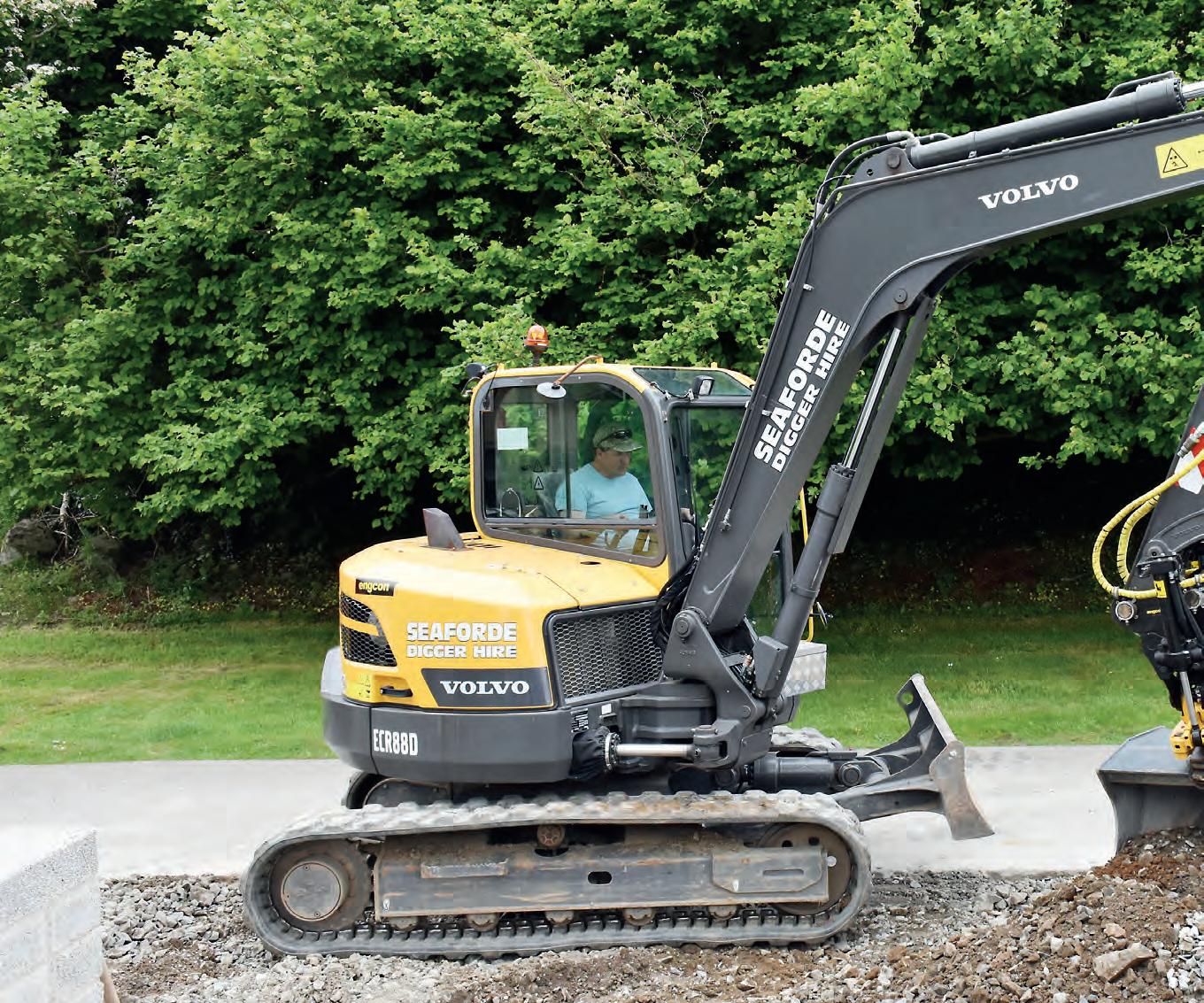

IT’S very true when digger operators say once they get the hang of using tiltrotators they can’t do without them.
That’s exactly the sentiments of Paul Killen, the owner of Seaforde Digger Hire in County Down, who has fitted an Engcon EC209 tiltrotator to his 2018 Volvo ECR88D tracked excavator. Paul carries out all types of digger work mostly for the construction sector running two tracked Volvo excavators and a CAT rubber wheeled backhoe. He already runs another brand tiltrotator on his bigger Volvo EC160E excavator and got so used to running a digger with the tool he decided to put a tiltrotator on the smaller excavator too. Paul decided to invest in an Engcon machine this time and is well pleased with its performance and reliability. Paul said: “I first starting looking at tiltrotators when problems sourcing labour arose. It’s hard to get staff these days and a tiltrotator is like having an extra labour unit on site. “As a one man operator I can do many more additional tasks with a tiltrotator which makes work a lot easier and safer. “It took me around one month to fully get the hang of using the tiltrotator but once I did I couldn’t do without them, hence why I wanted to add one to the smaller Volvo excavator,” he said. Made in Sweden, the Engcon tiltrotators have a well-documented history dating back to the mid-1990s when they were first developed by Stig Engstrom. Paul purchased the Engcon EC209 model from Robert McAlerney at Ballyward Plant Services based near Castlewellan, who has recently taken on selling and fitting the Engcon brand. Paul said: “It was great news when Ballyward Plant Services announced it was selling

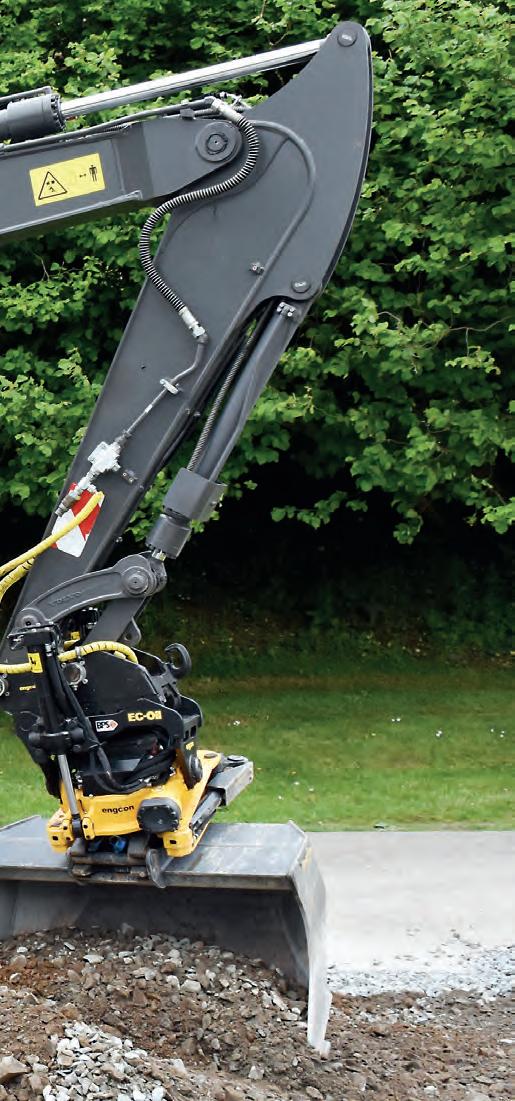
Engcon. The backup service from the company is superb. I have been dealing with them for five years and have bought two diggers off the company in the past. Nothing is a problem for Robert and the team there.” The Engcon EC209 tiltrotator is designed to be suitable for all excavators in the six to nine tonne weight class. If the EC209 is selected with Engcon’s standard quick hitch QS45 and the proportional control system DC2, EC-Oil is offered an automatic quick hitch system as a standard. This means that the tiltrotator and hydraulic tools can be connected and disconnected without the operator needing to leave the cab. The unit comes supplied with hose, quick couplings and electrical installation equipment for one machine. “I choose the Engcon EC209 tiltrotator with a gripper as it fits the Volvo ECR88D nicely being rated at just over nine tonnes,” said Paul. “It was fitted by Robert and the team around March time this year and I have had absolutely no trouble with it at all. It really is a great machine. “I use it for grading and levelling work, where it is extremely useful, and also for pulling out tree stumps. When I use the Engcon tiltrotator on some jobs I get people watching it in amazement and taking videos of it at work. “Using a tiltrotator indeed replaces an extra man. I have seen me doing some quite precise work around a house or a drain where normally you would need that extra person finishing off the awkward parts. However, I can finish off those harder bits myself from the cab now with the tiltrotator,” said Paul. “The secret to having a proper working tiltrotator is to have it installed properly in the beginning and taking enough time to master the controls of the machine. Then you can really see how useful they are,” added Paul. Ballyward Plant Services has been selling the Engcon tiltrotators since the beginning of 2021 and have already sold a number of them to customers in Northern Ireland. Robert McAlerney said the Engcon machines are particularly strong and are very reliable, which is a real testament to their design. Robert said: “We started selling the Engcon tiltrotators early this year after purchasing a EC209 unit to use as a demonstrator in our yard. There is a growing demand for these tiltrotators in Northern Ireland mostly from operators who haven’t used them before. “Paul purchased his EC209 unit with a detachable gripper and he has the DC2 control system with MIG2 controls. This unit can be set up for different users, different oil flows and for different jobs. Operators can use an app on Android phones to set operations up as well. “We have sold and fitted a few of the Engcon tiltrotators and have never received a call out yet to repair one. That says alot. “The tiltrotators must be fitted correctly to the excavator and that process can take two to four days depending on the machine spec and excavator,” added Robert. Robert has plans to use a smaller Engcon EC02B tiltrotator on a 2.5 tonne excavator as another demonstration unit in his yard.
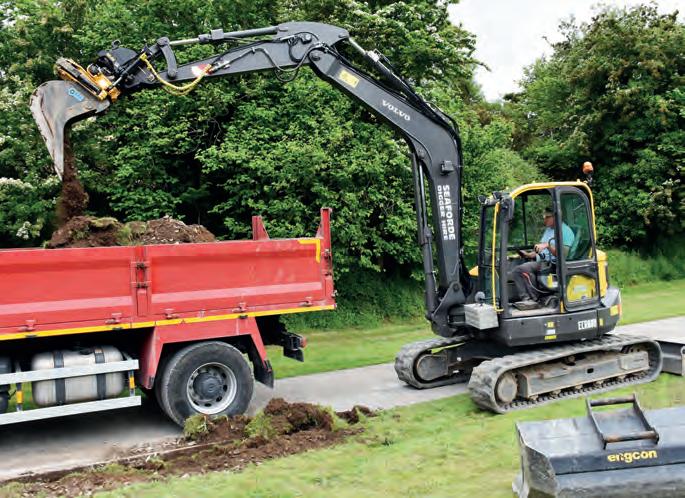
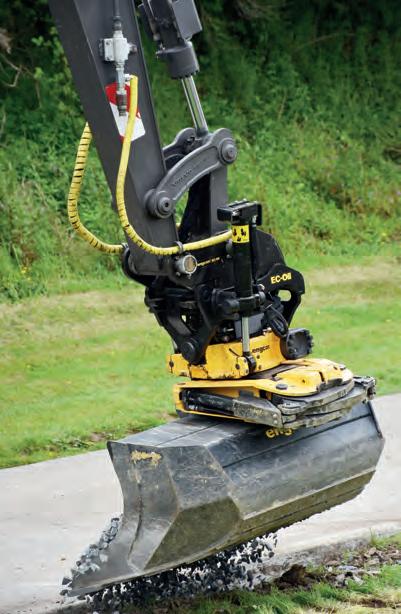