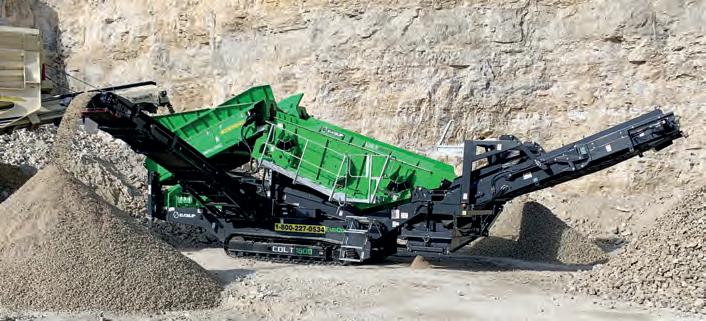
27 minute read
Crushing & Screening
FJS PLANT JOIN EVOQUIP IN CELEBRATING FIVE YEARS OF GROWTH & INNOVATION
Compact crushing and screening brand EvoQuip recently celebrated five years in business with a virtual event that reflected on their phenomenal business growth thanks to continued product development and a loyal global network of distributors that includes FJS Plant Ltd, their authorised dealer for Ireland.
The hour long event attracted almost 100 distributors from around the world and commented FJS Plant’s Managing Director Frank Smyth: “We are delighted to be part of EvoQuip’s global network. We have built up and enjoyed an excellent working relationship with the manufacturer since being appointed Irish distributor last year. “They have been very supportive, have a good marketing team, good aftersales team and a great Territory Manager in Conor Grogan; very easy to work with from a dealer’s point of view. “Their range of crushing and screening equipment has been an excellent fit with our existing range of products and has helped us expand our business. Our customers are very happy with the EvoQuip brand and that has been reflected in a steady stream of sales and enquiries.” Recent sales included a Bison 280, a compact and aggressive portable jaw
Colt 1600.
crusher that utilises an extremely fuel efficient and powerful ‘Direct Drive’ system that provides excellent performance in recycling, contracting and quarrying industries. Its compact size, quick set-up times, ease of transport and user-friendly control system makes it the ideal solution for all small to medium sized operators. Also recently delivered by FJS Plant was a versatile and easy to transport Cobra 290 tracked impact crusher which also features excellent fuel efficiency, quick set up times, and simple intuitive controls. “Currently, we are also dealing with a number of other enquires,” adds Frank, “and with good availability of stock, we are looking to the future as an EvoQuip distributor full of confidence.”
Top Three
Launched at Hillhead in 2016 to bring a simplified range of equipment to the crushing and screening industry, EvoQuip has grown from strength to strength to become one of the top three compact crushing and screening brands in the world.
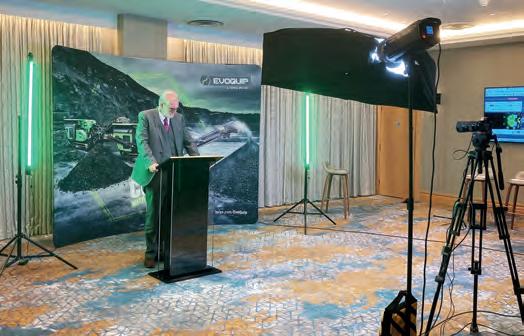


Bison 35.
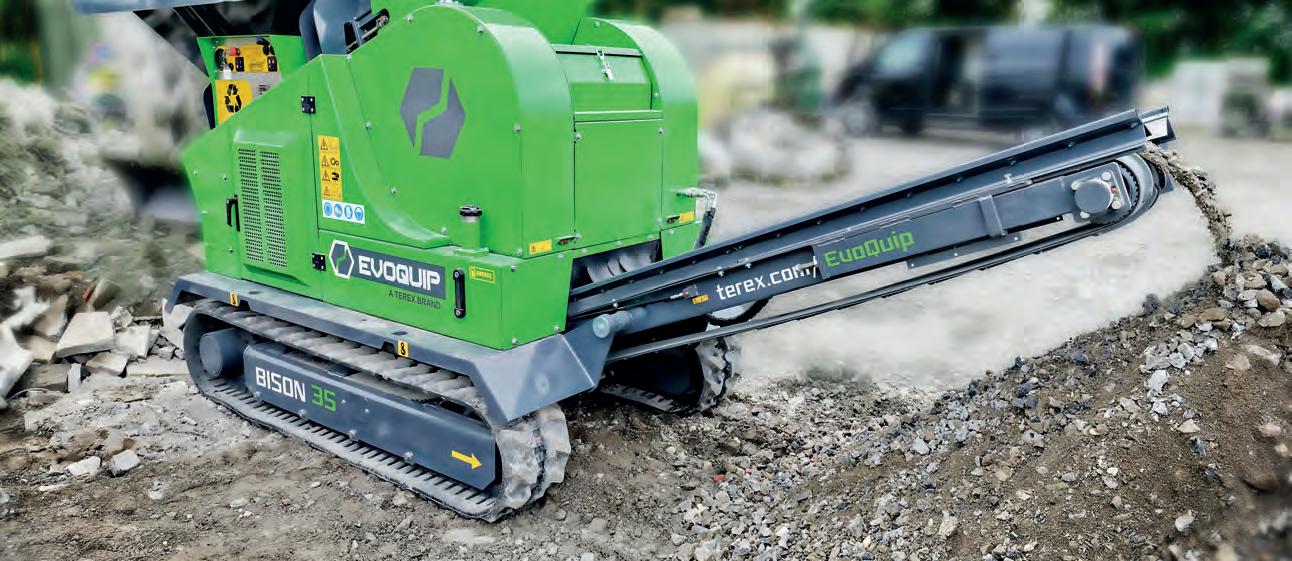
Starting out with the Bison 35 crusher, capable of outputting up to 30 tones per hour, EvoQuip continued to introduce innovative products with the Cobra 290R now being the biggest crusher in its range, capable of outputting 320 US tph. On the screening side, EvoQuip’s products have evolved to encompass the Harrier 220, a small yet robust machine designed for recycling, composting, topsoil, landscaping, and contract building industries, capable of outputting 90 US tph, to the highly aggressive scalping screen Colt 1600, which was built upon the features which have made the Colt 1000 a global success. The Colt 1600 is the largest screen in the EvoQuip range and can process up to 661 US tph, depending on application. EvoQuip’s range has also developed to include tracked mobile conveyors, high- and low-level feeders and radial stockpilers, designed to work alongside its range of crushing and screening equipment. More recently, hybrid offerings, designed to give customers alternative energy options to operate their equipment and digital solutions, such as T-Link telemetry providing customers with real-time information on the performance of their machine, have been at the forefront of EvoQuip’s evolution to address emerging industry needs.
Loyal Dealers & Customers
A strong leader in the compact crushing and screening industry, EvoQuip would not be the success it is without its loyal dealers and customers. While the brand started off in 2016 with just five dealers, this has since grown to 44 dealers from around the globe. This growing distribution network alongside attendance at exhibitions such as Conexpo, Bauma, World of Concrete and Hillhead continued to strengthen the brand, showcasing its offering to global audiences. Due to the COVID-19 pandemic, EvoQuip had to change initial celebratory plans for this milestone from an in-person event to a virtual one. Hosted by Northern Irish actor and comedian, Tim McGarry, dealers were treated to a personalized EvoQuip song, a timeline of the last five years, a live quiz where some of the team members’ knowledge was put to the test, a raffle and the first ever EvoQuip Dealer Awards. The EvoQuip Dealer Awards included several categories such as Global Leader in Industry Growth, Customer Support and Rental Business Growth, to name a few. Among the winners were Mobile Screening and Crushing (MSC) from New Zealand who won Global Dealer of the Year. MSC are a strong dealer in all areas and engage extremely well with the EvoQuip team. They achieve sales targets, have a strong online presence and are wholly invested in the EvoQuip brand. It is a partnership that will continue to flourish and grow.
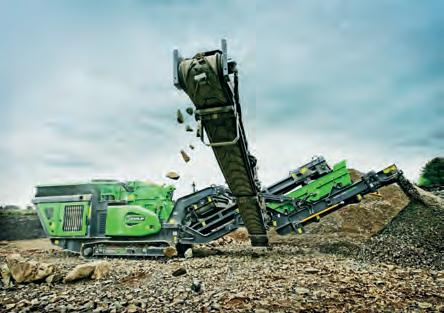

Cobra 290R.
Looking to the Future
Speaking of the last five years, Barry O’Hare, Business Line Director, EvoQuip said, “EvoQuip brings value to customers by providing intuitive equipment that is simple to operate and maintain, fuel efficient and easy to transport. User friendliness is at the heart of our brand and as new products have been developed, the focus has always been on simplicity and entry level customers. “Since joining EvoQuip over two years ago, I have seen the business grow from strength to strength and we couldn’t do that without our global distribution network. It is with the dedication of the EvoQuip team and the relationships we have built with our dealers that has enabled us to grow and maintain our place at the forefront of the compact crushing and screening world. “I’d like to thank our dealers and customers for their support over the last five years and together we look forward to the future. There are some really exciting, innovative products in the pipeline and with the help and expertise of our distribution network, we will continue to grow and dominate the global compact crushing, screening and conveying market.”
Frank Smyth of FJS Plant with their Regional Dealer of the Year Award.
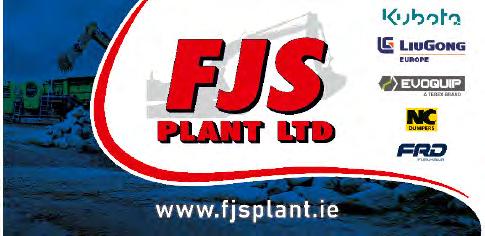
MB CRUSHER PRESENTS THREE NEW MODELS OF SORTING GRAPPLES
Pythagoras once said that 3 is a perfect number. To satisfy many construction sites, MB Crusher manufactured three new grapples, designed, and built with the company’s philosophy in mind: to simplify the work on-site, reduce the time spent processing material, and save on operational costs.
The new models are designed for smaller excavators: the MB-G350 and the MB-G450. The former weighs just over 13 stones and is compatible with mini excavators weighing from 1.3 to 2.6 tons. The latter weighs just over 45 stones and can be installed on midi excavators weighing 3 to 6 tons. Small and compact, versatile and safe, agile and precise, both grapples have a wider opening than any of the other grapples on the market: despite being small, they can still pick up and handle large materials. They are equipped with a fall prevention valve, guaranteeing safety on the job site. The parts prone to wear are made of Hardox steel. Both models are designed to have an electrical kit installed for dual-acting hydraulics: this way, the two grapples can utilize 360° rotation even with mini excavators that only have two hoses. Like the larger models, the MB-G450 sorting grapple comes with interchangeable blades, which can be flipped around, extending the life of the blades. Both units have two versions: with or without a rotation turret. Both grapples can have accessories installed to simplify managing materials: the clamshell kit is perfect when collecting and handling small material, picking up soil, gravel, and sand. The multi-purpose blade kit helps pick up oddly shaped materials. For the MB-G450 sorting grapple, you can install the tilting lift rubber protection kit to manage angular blocks and delicate material. Weighing at 254.32 stones and has a load capacity of 0.44 m3 /440L for versatile, compact, and reliable equipment, the new MB-G1000 grapple was explicitly designed for heavy work. Due to the work, the unit has been reinforced without losing its agility and ease of use. Two new features are the dual motor, which allows for greater rotation and closing force, and the balancing valves installed on the hydraulic cylinder, allowing the unit to be more precise when handling materials. This new model also comes with an inclined plate, allowing the unit to work regardless of the angle, and has the 360° hydraulic rotation, allowing the grapple to pick up materials in all working conditions efficiently. It’s also equipped with a safety valve, preventing accidental openings if the excavator’s pressure drops. There’s also a silent block, allowing the unit to work in areas where you need to be mindful of the noise. Depending on the work, the MB-G1000 model can be equipped with various accessories: the grip improvement kit for the blades, allowing the unit to handle materials with a better grip and greater control, perfect for materials of particular weight and shapes. The multi-purpose blade kit consists of a double blade: one side has teeth while the other is smooth. Another accessory is the tilted lift rubber protection kit, which handles angular block or delicate material. Lastly, there’s the clamshell kit to collect and handle small materials.
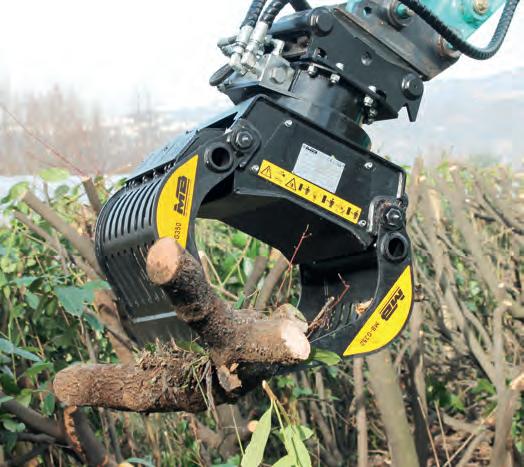
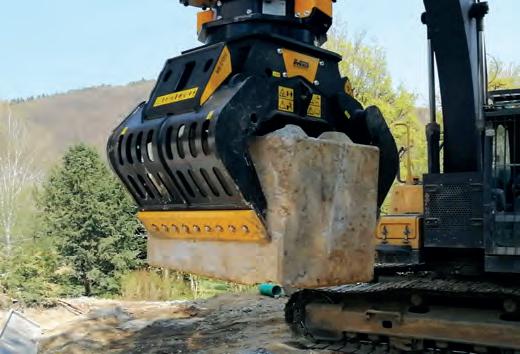

NEW METSO LT120 JAW CRUSHER AT WORK FOR COUNTY CLARE CONTRACTOR
FROM its base in County Clare, Atlantic Plant Hire operates nationwide providing a full range of plant hire and a contract crushing service. The company also carries out drilling and blasting work and is currently very busy with different sites operating around the country.
As Chris McCullough has been finding out, one of those big projects is the Macroom bypass in County Cork where Atlantic Plant Hire has a 2019 Metso LT106 crusher working and has just purchased another bigger machine, the Metso LT120. The Macroom job is costing €280 million to develop the 22kms stretch of dual carriageway scheduled to open to traffic in 2023. Gearoid O’Callaghan, the managing director of Atlantic Plant Hire, said the Metso machines were performing well on the various jobs. “We have been involved with the Macroom bypass project since June 2020 and will be there until the middle of next year. The Metso LT106 is a very reliable machine and is reducing the size of the stone after blasting into road making material. “Prior to the LT106 model we also ran a LT1213 machine. The output of the LT106 is ok and the reliability of the brand is a real influencer when it comes to making the decision of which machine to buy.” The LT106mobile jaw crusher is a primary crusher for aggregates production and recycling demolition and other waste, designed to be easily transported between sites. It is often used as a primary crusher in a multistage crushing process or as a stand-alone unit, ideal for medium-sized aggregates production, as well as recycling demolition waste such as crushing concrete. Powered by a CAT 300hp engine, the LT106 is equipped with Nordberg C106 jaw crushing unit, especially designed


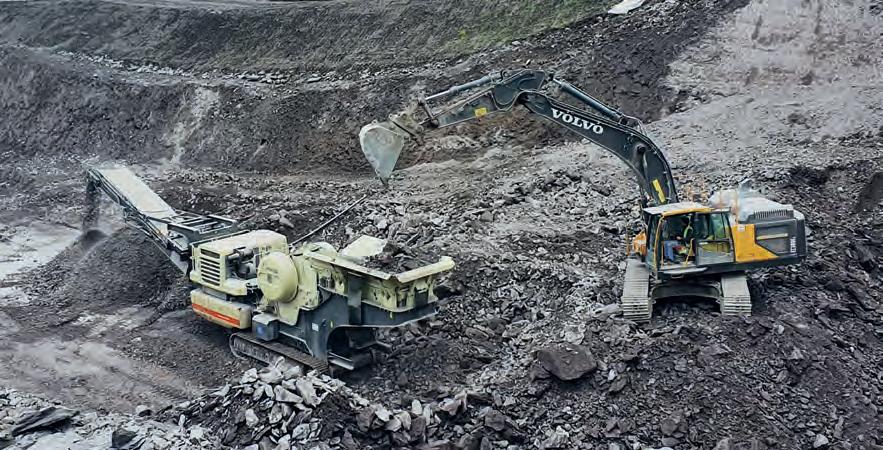
for crushing hard rock types such as granite, basalt and gneiss.
Moving on Up
However, to up their game and increase productivity on the Macroom job Gearoid decided to purchase the bigger Metso LT120 machine from McHale Plant Sales Ltd based in County Dublin. Gearoid said: “We have been dealing with McHale Plant Sales for years and find the company very easy to work with. It was a spur of the moment decision to purchase the LT120 and we were quite fortunate that they had the machine in stock. “I actually met up with the sales guy about a week ago on the Sunday. We had a chat about it, the machine was PDI’d and delivered to our site on the Tuesday, a real fast delivery,” he said. The bigger LT120mobile jaw crusher weighs in at 63 tonnes, has a Nordberg C120 crushing unit and is powered by a CAT 315hp engine. The machine purchased by Atlantic Plant Hire is a full spec model fitted with Metrics remote monitoring, ICr remote control, a long main conveyor, magnetic separator, automatic lubrication unit, radio remote control, water spraying system, belt protection plate and a rubber lining for the feeder and hopper. The Metso IC process control system enables single-button start and stop and features in-built troubleshooting as well as various parameter selections. All the Metso mobile crushers in the same crushing process can be linked with Metso IC. Furthermore, the whole process can be monitored and controlled conveniently from the excavator cabin with Metso ICr remote control software.
Easy to Transport
Thanks to its compact dimensions combined with agiletracks, the LT120 is a very easily transportable unit. It stands around 17m long, 3m wide and almost 4m tall. A strong chassis design with good clearance at both ends enables simple loading on a trailer. The feed hopper sides equipped with a patented securing system allow the unit to be ready for crushing only moments after arriving onsite. The side conveyor with its excellent stockpile capacity is easy to install on either side of the unit. Atlantic Plant Hire has been operating since 2005 and work in a lot of quarries around the country, big or small. They also work on a lot of wind farms as well. The company says its machines are maintained regularly and updated yearly to reduce breakdowns and increased durability and productivity. The range of equipment available for hire includes excavators, rockbreakers, dump trucks, tractor and dump trailers, bulldozers, drilling rigs, crushers, screeners and low-loaders. “We try and keep our machines fresh and exchange them every five to six thousand hours,” said Gearoid. “We are very happy with our Metso machines.”
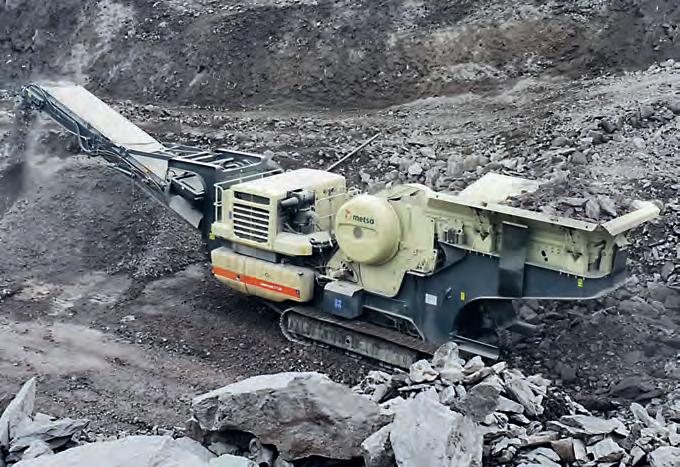
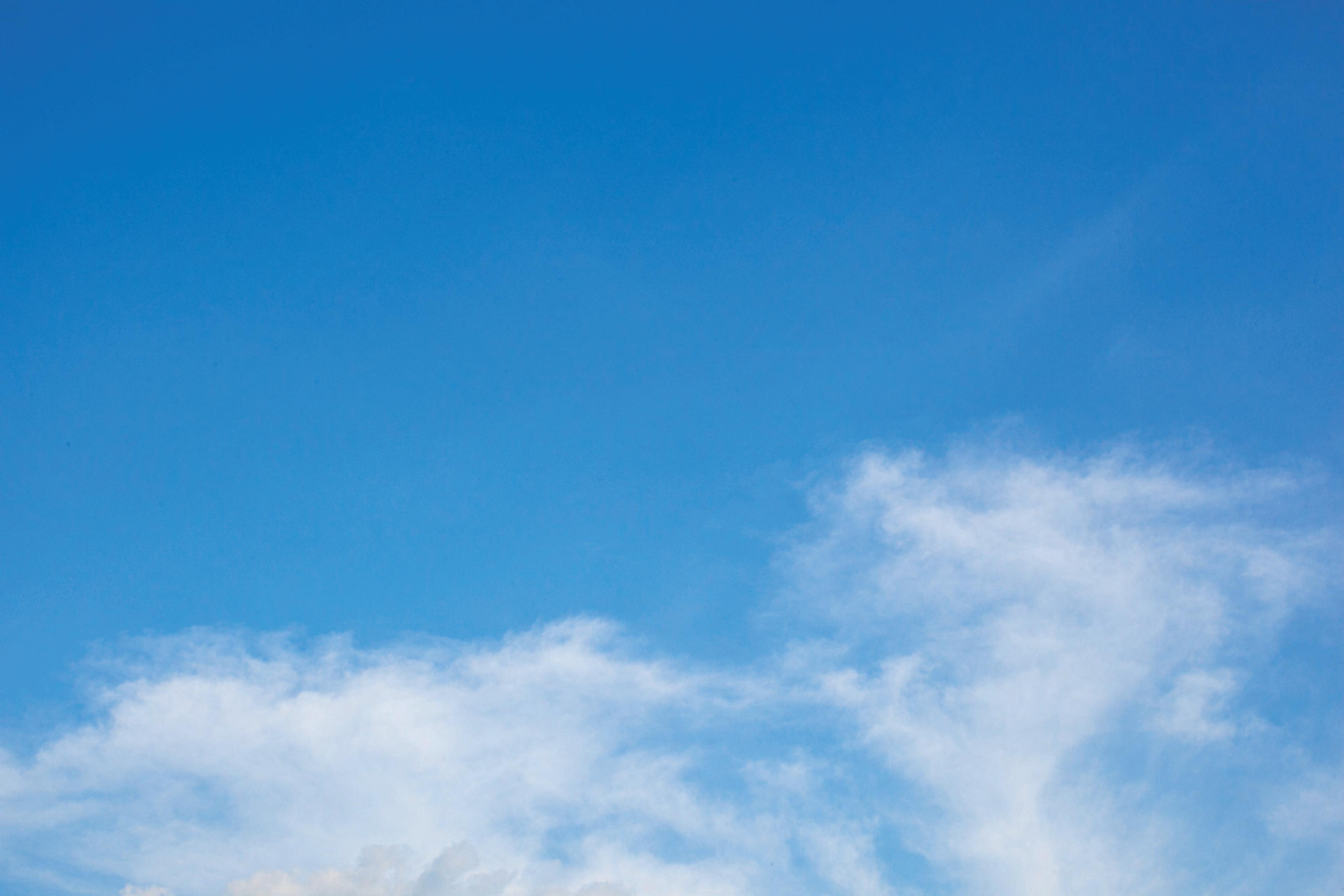
HOLYWELL HAULAGE INVESTS IN A MULTIMILLION-POUND KIVERCO WASTE RECYCLING PLANT
Holywell Haulage Limited has recently chosen Kiverco to design, build and install a new static waste processing system for their site in Hemel Hempstead, Hertfordshire.
The new plant will process Construction, Demolition, Commercial, and Industrial waste as part of a multi-million-pound investment that highlights Holywell’s commitment to sustainability by diverting all waste away from landfill. The new plant will be capable of processing up to 60tph and will include waste screens, air density separation systems, magnetic separation, and quality control points to ensure maximum purity of recyclable materials. Holywell Haulage Ltd is a well-known, successful total waste management company with over 20 years of experience within the waste industry. Managing Director at Holywell Haulage Ltd, Eamon Cullen, founded the business in 1998, and started with one truck doing small muck away jobs, before moving into the skip hire industry. Along with the help of his dedicated team, Eamon has developed the business, which is now recognised as one of the largest and most professional waste companies within the Hertfordshire, Bedfordshire, and Buckinghamshire region. Commenting on the recent investment, Eamon Cullen explains why he chose Kiverco: “Our core objectives were to ensure a higher quality of output material, divert 100% of the incoming waste from landfill and maximising our return on investment. With Kiverco’s state-of-the-art waste recycling plants, we are very confident that their systems will help us achieve our objectives and will provide plenty of capacity for future growth. JP and the Kiverco team were professional and knowledgeable and provided us with the information that we needed to make decisions on the plant specification. We are well aware of Kiverco’s expertise in waste processing and are very excited about this project.” Kiverco is one of the world’s leading providers of waste processing solutions, operating from their headquarters in Co Tyrone. They offer complete turnkey solutions to process waste streams such as Construction & Demolition (C&D) waste, Commercial & Industrial (C&I) waste, Municipal Solid Waste (MSW), Dry Mixed Recyclable (DMR), and compost. Kiverco’s installations now exceed 300 waste plants throughout the UK and Ireland, Europe, North America, and Australasia. The UK is one of their leading markets where they have been supplying plants for almost 30 years. Regional Sales Manager at Kiverco, JP Devlin, stated: “It was clear from our initial discussions that Eamon and his team wanted a reliable, high-performance waste recycling solution that worked efficiently and effectively, enabling maximum recovery of the various waste recyclables. We are delighted to be working with Holywell Haulage Ltd to help them achieve their commercial and environmental objectives and are very grateful that they have placed their order and confidence with Kiverco to deliver results.”
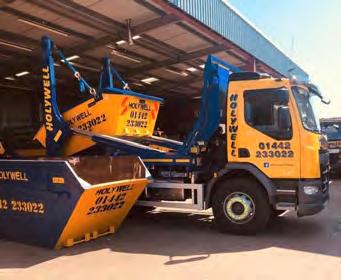
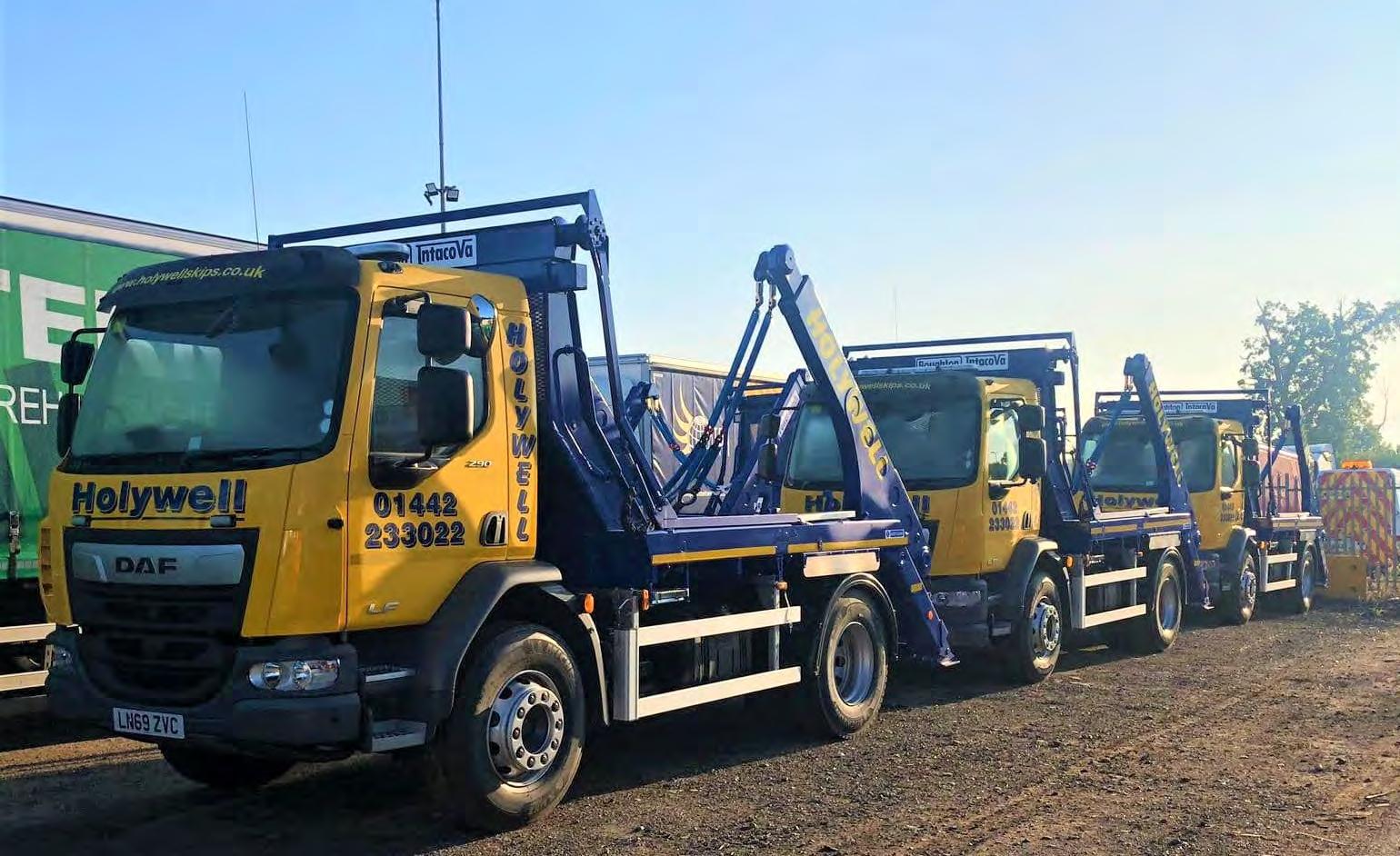
FLEET OF TESAB MACHINES PROVE RELIABLE WORKHORSES FOR ARC QUARRIES LIMITED
WITH high demand for stones all throughout the Covid-19 era, a fleet of reliable Tesab machines ensured Arc Quarries Ltd was able to fulfil customer orders, as Chris McCullough reports.
From their quarry based at Macosquin, on the outskirts of Coleraine, Arc Quarries Ltd supplies a range of aggregate to the construction industry and have been involved in some large projects over the last few years. Keeping the stone processed are a number of construction machines, including jaw crushers and cone crushers, supplied by Tesab in Omagh, some of which sport the traditional blue and white colours traditional to Arc Quarries Ltd. Tesab is a family of engineering companies located throughout Scandinavia and Northern Ireland, and are experts in the manufacture of equipment for the mining, quarrying, recycling, asphalt and concrete industries. Well known in the construction sector, Tesab manufactures a crusher range to suit any operation. One of the more popular pieces of equipment manufactured is the range of jaw crushers for crushing primary rock. Also there is a range of impact crushers for primary, secondary and tertiary applications and a cone crusher to complete the portfolio. Arc Quarries Ltd run a Tesab 800i jaw crusher, which is just one year old, and is running up to 14 hours per day. Aidan Caldwell, director of Arc Quarries Ltd, said he has been impressed with the Tesab equipment and therefore continues to invest in the brand. “Together with my son Ryan, who is also a company director, we have been running the quarry at Macosquin for the past three years,” said Aidan. “Business is currently quite good with a number of big construction jobs on the go. We supplied most of the stone to the new A6 road project which kept us busy for the last three years. All told we have over 30 lorries delivering stone and usually have 35 staff working to us in the business,” he said.
Efficient & Reliable
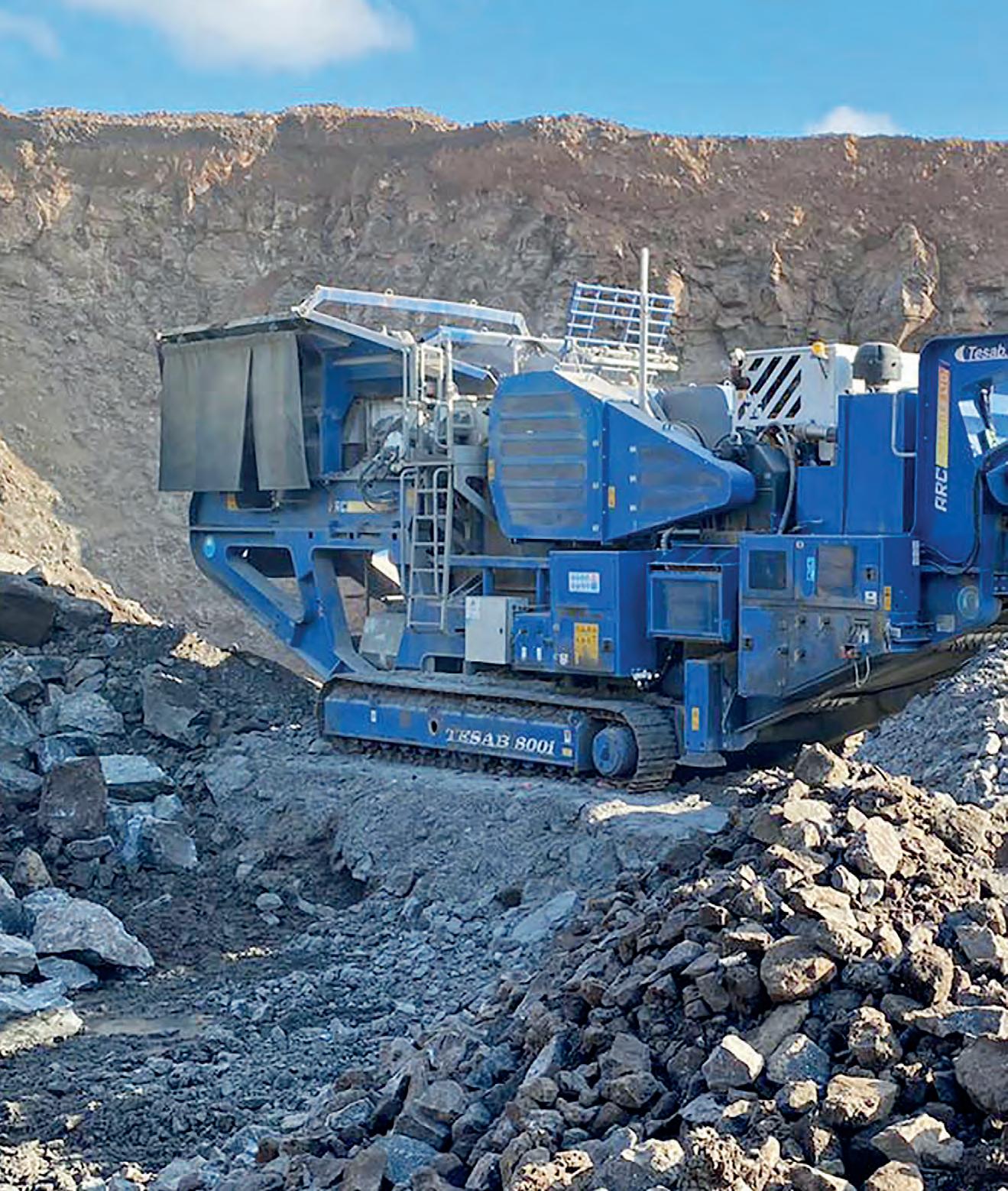
Based on the proven 10580, the Tesab 800i is designed specifically for the quarry market to crush primary rock at the quarry face. The unit features Tesab’s new and improved step deck vibrating feeders to improve material separation quality and the ability to handle dry, damp or wet material. It also has an additional two deck independent pre-screen for increased production, making the 800i a very efficient rock crushing machine. The 800i can process up to 400 tonnes per hour and can be supplied with a range of different engines to suit customer requirements. The crusher can be fed by an excavator as a standalone unit or can also integrate easily into the Tesab

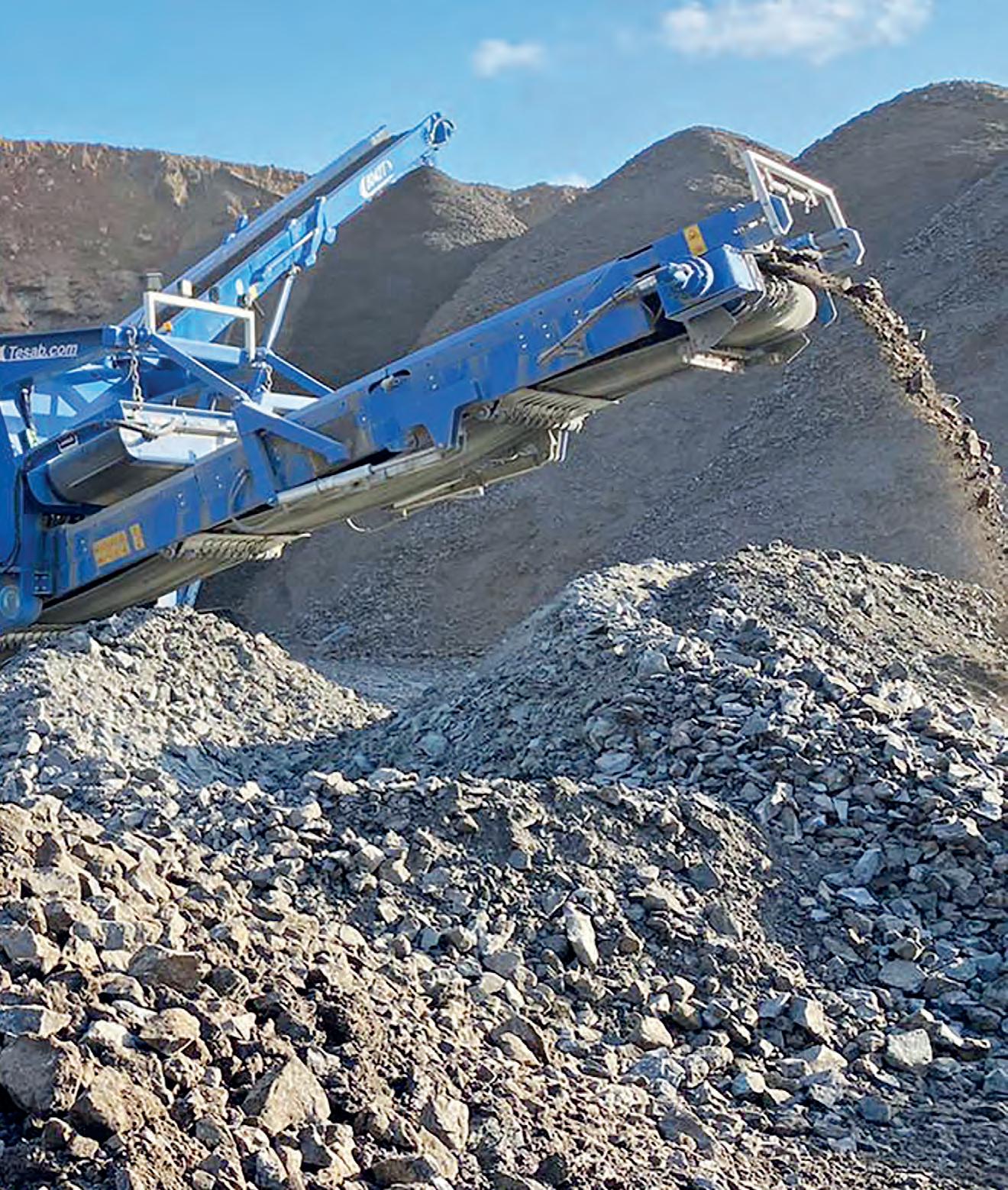
range of secondary crushers and screeners. Aidan said: “Our Tesab 800i is crushing four inch crusher run and is running up to 14 hours per day. We bought it brand new from Tesab and have had no trouble with it at all. Nothing on the machine has been touched since we got it. “I purchased the 800i with a two year extended warranty for that extra peace of mind, given the tough conditions under which it works. We actually run another 2018 Tesab 800i crusher that we bought second-hand and there is another 2009 Tesab 10570 crusher working in the quarry too. There is also a Tesab cone crusher we bought in 2019 in the line-up as well,” said Aidan. Arc Quarries Ltd use Tesab’s Trackstack machines in their quarry in alignment with other Tesab machines to keep the production lines rolling smoothly. Tesab’s Trackstack 8042T is a heavy duty and versatile mobile stockpiling machine suitable for a large range of applications, and can be setup very quickly on site. Featuring a unique ‘boomerang’ design, the feed boot height can be adjusted without altering the head drum position, which helps to ensure maximum flexibility without losing stockpile capacity. The Tesab 8042T can receive material directly from a crusher or screen or be installed in a close circuit application. With its Hi-Torque drive system this machine can be fed direct by a wheeled loader or excavator, when a direct feed hopper is fitted. The machine can process up to 600 tonnes per hour and has a stockpile capacity of 2,162 cubic metres or 3,460 tonnes. The Hi-Torque drive and engine size combine
efficiently to reduce fuel consumption.
Superb Support

Aidan added: “We run two Tesab Trackstack models, both purchased new. The first one is a Tesab 6536T we bought in 2020 and then the second one is the Tesab 8042T bought in March this year. “We use one to feed out of the cone crusher and the new 8042T is feeding out of the 800i jaw crusher. “The back-up service from Tesab is superb as the company is based down in Omagh, which is not that far away meaning if we ever need a part they have it on the road to me right away. You simply can’t beat them,” said Aidan.
MORE REASONS TO SMILE WITH A SANDVIK QJ241 MOBILE JAW CRUSHER

Longstanding customer Ben Bennett Jr Ltd recently took delivery of their fifth Sandvik mobile crushing and screening unit for their quarrying operation in Derbyshire; they are used to crush limestone to produce high quality grades of calcium carbonate for a variety of applications, including the pharmaceutical industry, and is commonly used in the manufacture of toothpaste.
Ben Bennett Jr Ltd currently owns and operates a Steel Rolling Mill and a Limestone Quarry, both of which were acquired by Ben Bennett Jr in 1935. Their head office is located in Rotherham, South Yorkshire, and their quarry, Grange Mill Quarry, is situated in Derbyshire. They employ approx. 45 people at the quarry and work two shifts during the day and night to keep up with demand. Their services include the production of aggregates and bulk tanker products for supply and transport to a wide variety of industries, including pharmaceuticals, food, rubber, glass, plastics, sealants and many others, and export globally. Grange Mill Quarry lies in the white peak of Derbyshire which is composed mostly of several types of limestone deposited during marine conditions in the early Carboniferous Period around 330 million years ago. Limestone, a sedimentary rock, formed and accumulated in clear, warm shallow seas with localised reef complex formations. The limestones are composed of the shells of organisms which are made up of the mineral Calcium Carbonate (CaCO3) which lived in these tropical environments.
High quality product
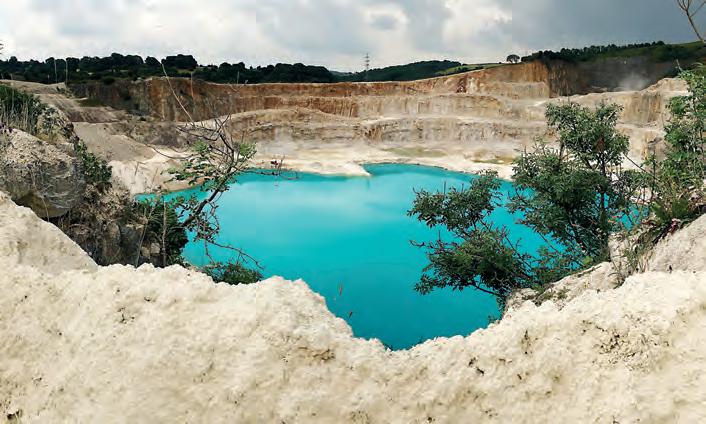
The Grange Mill deposit lies in the Bee Low Limestones which have typically thick beds and are of high chemical purity. Very few complete fossils are found in the deposit and there are no mineral veins to contaminate the limestone. This makes the material of high quality and due to its softness and low silica content, is ideal for grinding to powder and granules for use in a wide variety of products including glass production, animal feeds, rubber, sealants, carpets & adhesives. Also widely used in the pharmaceutical industry, the high quality grades of calcium carbonate are used as an effective dietary
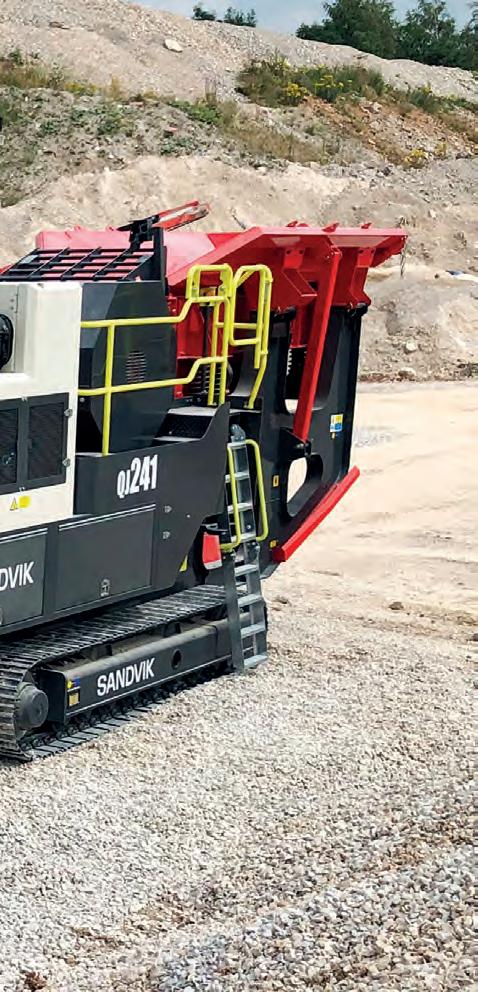

supplement, antacid and an ingredient in baking powder and toothpaste. The quarry supplies approx. 50,000 tonnes a year to the pharmaceutical industry. To process the limestone, the material is drilled, blasted and processed by the mobile crushing and screening plant supplied by Sandvik. Ben Bennett Jr first invested in a Sandvik unit back in 2013 and have purchased two screens, two crushers, and also a static screen over the years. Their current QJ241 mobile jaw crusher is set at a CSS of 75 mm and crushes the feed material down to 40 mm. This is then fed into a QA331, then a QA140 screen for processing down to 40–20mm, 20–10mm and -10mm. Needing to upgrade and replace their six year old mobile jaw crusher, Ben Bennett Jr didn’t hesitate in contacting Sandvik once again for the supply of a new unit, due to the reliability, familiarity of the equipment and aftermarket support provided. “With proximity to the customer support centre, this was a major gain for the supply of parts and local service whenever required” comments Andy Rawson, Director of the company. Andy continues, “The aftermarket support has been very good. People come out whenever we have needed assistance. A lot of the work we can now do ourselves as our operators are familiar with the equipment. That’s one of the reasons we continue to buy Sandvik as you don’t have to start back at square one”.
Maximum uptime
The new QJ241 will come with the added benefit of Sandvik Optitooth™ jaw plates. These are included as standard on all Sandvik Q-Range jaw crushers for extended life, increased throughput and reduced fuel consumption. The new model also comes fitted with Sandvik My Fleet remote monitoring system as standard with 7 years complimentary data access. Access to a wide range of live machine data will help to minimize operator intervention, enable planning of service and maintenance schedules thereby maximizing uptime and achieve optimum output at all times. These new features are in addition to the standard features with which the QJ241 has become synonymous; such as hydraulic drive, enabling the crusher to start under load, hydraulically adjustable jaw setting to maximize your output and jaw level sensor to control the feed rate into the crusher with minimal intervention. The QJ241 is also fitted with the latest emissions-compliant engine, dust suppression spray bars and onboard water pump as standard to minimize dust. In accordance with Sandvik’s environmental focus and sustainability targets, these are important factors for Ben Bennett Jr due to their location on the boundary of the Peak District National Park. They are committed to maintaining and protecting the biodiversity of the area and employ consultants to monitor their environmental impact on the local environment. Sandvik mobile crushers and screens have proven to be the ideal solution for Ben Bennett Jr and the repeat business and investment from them over the past eight years is testament to this. Sandvik Mobiles looks forward to continuing this business partnership and being the supplier of choice for years to come.
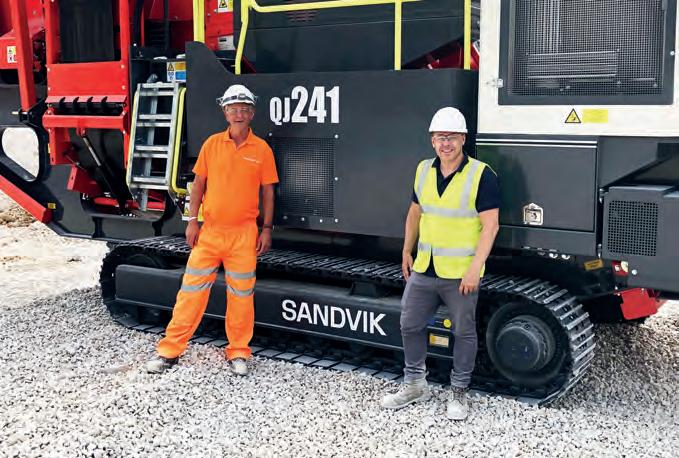

SUN SHINES ON EXCELLENT TURN OUT FOR VERTIKAL DAYS SHOW
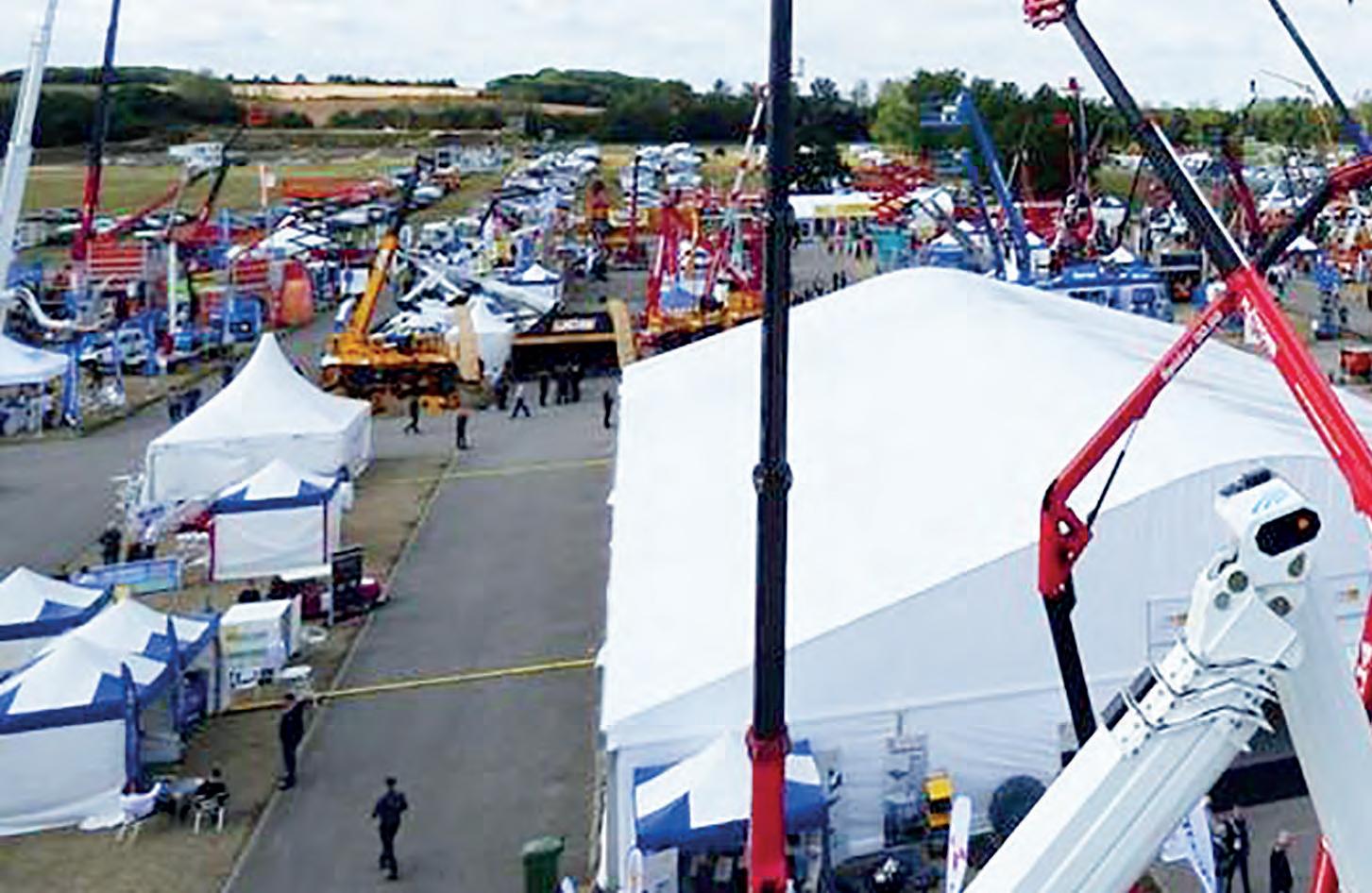
This year’s Vertikal Days, held for the first time at the East of England Showground in Peterborough, was the first UK equipment exhibition since the start of 2020, having been postponed twice due to government lockdown rules.
So, it was with some trepidation that the organisers of the event stuck with the September date, with potential weather issues and shorter days compared to the show’s usual mid-May dates. What a success it was, even with the risk of further restrictions in the face of the rising incidents of Covid-19, and with the fear that people would either stay away or be so concerned as to change the atmosphere of what is a sociable, people focused event. The weather was stunning, and almost 2,600 individual registered visitors attended, pretty good given the ongoing pandemic and absence of international visitors due to travel restrictions. The atmosphere was possibly the best ever, with everyone clearly happy to finally be able to meet up, talk and ‘kick the tyres’ of all the new equipment on show. Exhibitors were equally delighted with the turnout and the positive attitude with most reporting record order intake, with the show remaining busy from the starting
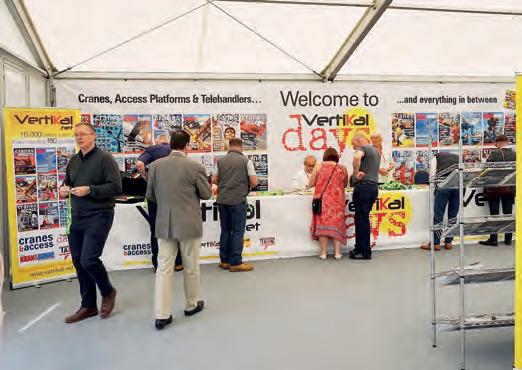
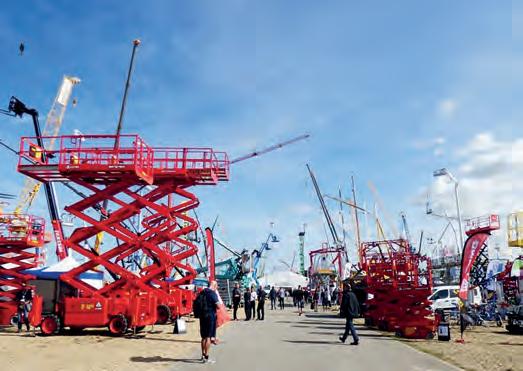



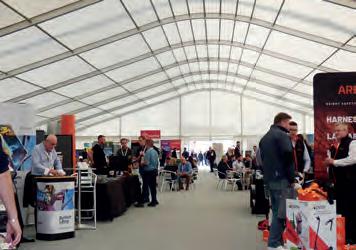
minutes to those visitors who arrived just before the closing time on Thursday.
Product Debuts
As to products, this was one of the first opportunities for the big Chinese aerial work platform manufactures, Dingli, LGMG and Sinoboom to demonstrate their larger machines, including big heavy duty electric scissor lifts and mid-sized boom lifts, while Sany made its debut with the 60 tonne SCE600TB telescopic crawler crane on Foster Cranes’ stand. Versalift took the opportunity to show its very first underbridge inspection platform, which came with the acquisition of Aspen last year. On the crane side Liebherr managed to bring its all new MK73 self-erecting mobile tower crane along, which has just gone into production, while Spierings demonstrated its all new e-Lift mobile tower crane which can operated from a standard electrical socket once on site. Another Dutch exhibitor was Rhinox, a brand new venture for a highly experienced fabrication company Van-Ginkel with its RX12CS crawler mounted heavy duty boom lift. The same applied to Omega Solutions which produces a unique heavy duty track mounted slewing scissor lift.
Going Electric
For those interested in the latest battery electric telehandlers, this was the first public opportunity to see the latest models with the two leading contenders in attendance. JCB had its all new 52560E – which it showed alongside its first 360 degree 555-210R telehandler – while Faresin had its popular 6.26 All Electric on display alongside other
CONTINUED ON NEXT PAGE
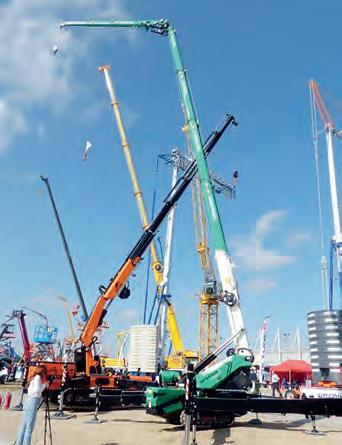
CONTINUED
models in the range. Word is that larger battery powered models are on the way. Spanish company Jaso used the show for the global launch of its new 18 tonne J198HPA hydraulic luffing tower crane, while the new Artic Crane Raptor 85 articulated luffing tower jib crane was on show. At the smaller end of the boom lift market was the new 22ft Nagano 09AC tracked model, this was also the first opportunity worldwide to see Skyjack’s new 63ft Rough Terrain scissor lift and Haulotte’s all new Pulseo battery powered Rough Terrain scissor lift. If truck mounted lifts were your thing, there was also plenty of new product launches, including the new 24 metre CTE MP-24C, Ruthmann’s new 30 metre T300 XS and GSR’s 21 metre B210PXJ. At the smaller end was Versalift’s new 13.5 metre Isuzu mounted VTA135-H pick-up, the new CPL/ Palfinger P130 pick up and Klubb’s new KT range of lightweight van mounts. Mast climbers and hoists were also well represented with Alimak, Mace -Geda, CLM and the Maber range.For the first time Italy’s Electroelsa exhibited, showcasing a new tower crane operator’s hoist. There were simply way too many new products to cover here, but here are a few photographs to give you a taste.

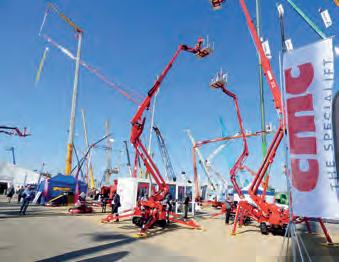


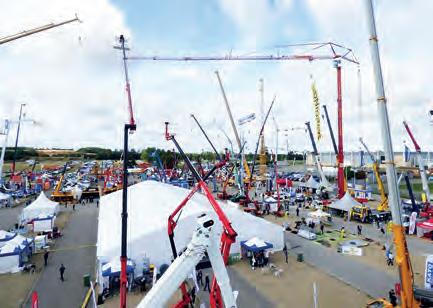

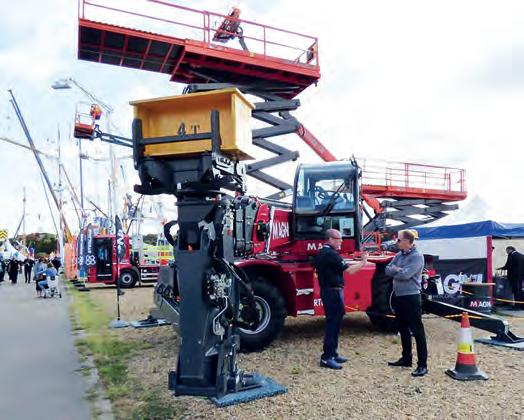
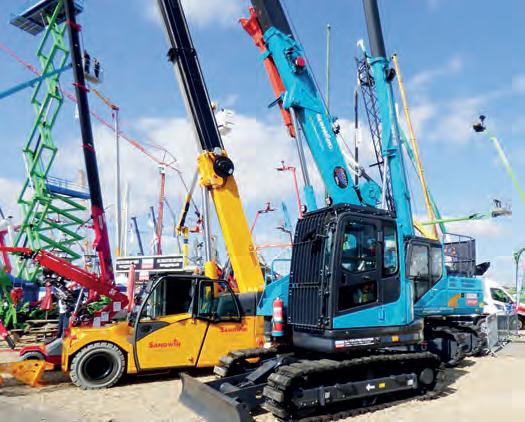