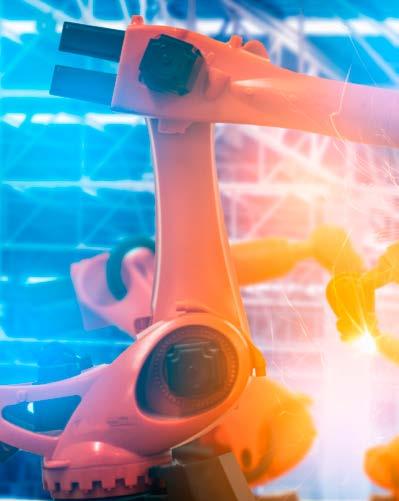
17 minute read
RIDE-project: digital twins op maat
Partners in RIDE-project op zoek naar efficiency- en productiviteitswinst
Door actief deel te nemen aan de Smart Welding Factory (SWF) hebben diverse maakbedrijven in Oost-Nederland de productie van hun lasrobots fors verhoogd. Dat smaakt naar meer en daarom doet een groot deel van hen ook mee aan het RIDE-project, de opvolger van SWF. In dit nieuwe project werken dertien partners, waaronder elf bedrijven, samen aan de digitalisering van hun processen. Het ultieme doel van RIDE is een digital twin op maat voor ieder deelnemend bedrijf.
Beperkte SWF zich hoofdzakelijk tot het versnellen en vereenvoudigen van het programmeren van lasrobots voor kleine series (seriegrootte 1), RIDE richt zich ook op de andere processen in metaalbewerkingsbedrijven: spuiten, stralen, buigen, kanten et cetera. Het is de bedoeling om al deze processen vanuit één 3D model aan te sturen/programmeren; niet alleen de productieprocessen zelf, ook alle indirecte processen er omheen. Dat kan veel efficiency- en productiviteitswinst opleveren, hetgeen niet alleen prettig is voor de deelnemende bedrijven, maar eigenlijk pure noodzaak. Want alle MKBmaakbedrijven zien zich geconfronteerd met dezelfde uitdagingen: er wordt een high-mix low-volume productie van hen verwacht, terwijl ze tegelijkertijd kampen met een gebrek aan capaciteit en (steeds meer) vakmanschap.
Digitalisering is antwoord
Ard Hofmeijer, directeur van het LAC in Hengelo, weet dat digitalisering een antwoord kan bieden op deze uitdagingen. Dat heeft het project Smart Welding Factory, dat formeel is afgerond, wat
RIDE moet er toe leiden dat MKB-bedrijven in de metaalindustrie de mogelijkheden en kansen van digitalisering meer gaan benutten.
hem betreft wel bewezen. De SWF-deelnemers zijn hun lasrobots gemiddeld 30 à 40 procent efficiënter gaan programmeren. Dat is het resultaat van samenwerking tussen de deelnemers. Al die bedrijven zijn bezig geweest met het leggen van hun eigen puzzelstukje. Ze hebben zich allemaal geconcentreerd op een aspect dat voor hen meest van belang was. En door alles bij elkaar te leggen, is de innovatie bij iedereen versneld. Hofmeijer: “We hebben binnen SWF voor en met de bedrijven allemaal digital twins gebouwd. LAC heeft hierbij met name programmeerkennis van robots ingebracht, de bedrijven hun proceskennis. Met als resultaat dat je nu op basis van een 3D model op elke lasrobot kunt lassen, zonder het product te hoeven programmeren. We hebben koppelingen gemaakt tussen CAD-pakketten, robots en lasapparatuur van alle fabrikanten die in de Nederlandse maakindustrie veelvuldig worden gebruikt.” En dat werkt, waarbij het mooie is dat SWF een vorm van open innovatie is: de deelnemers hebben er direct voordeel van gehad, nu kan iedereen gebruik maken van de ontwikkelde kennis via het SWFplatform, dat vanaf april beschikbaar is.
Kansen benutten
Volgens het zelfde principe wordt nu het RIDE project uitgevoerd. De afkorting staat voor Robotica, Industriële Digitalisering en Ecosystemen. Het doel van dit project is het introduceren, (door) ontwikkelen en implementeren van (verregaande) automatisering, robotisering en digitalisering binnen fabrieken/bedrijven in de metaalindustrie in Oost-Nederland. Dat gebeurt vanuit gezamenlijke kennisontwikkeling en investeringen op het gebied van productietechnieken, connected systems en digitization. Zo
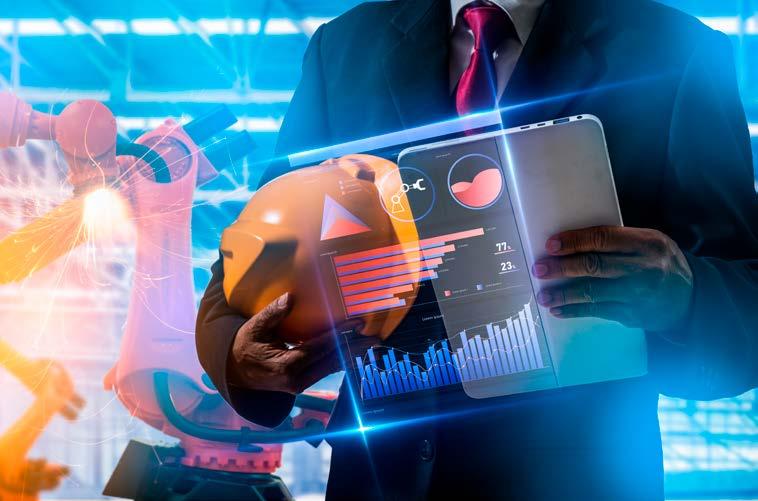
moet RIDE er toe leiden dat MKB-bedrijven in de metaalindustrie de mogelijkheden en kansen van digitalisering meer gaan benutten. Het LAC is opnieuw de penvoerder. De kennis en ervaring die de organisatie heeft opgedaan bij SWF wordt nu ingezet in RIDE. Hiervoor is een subsidie ontvangen van 3 miljoen euro op basis van co-financiering. Dat betekent dat de deelnemers er een zelfde bedrag insteken door investeringen in machines, software en tijd. “In totaal gaat het om een project van 6,5 miljoen euro”, zegt Hofmeijer. “Het loopt tot en met december 2023.”
No data, no talk
RIDE bereidt bedrijven voor op het gebruik van kunstmatige intelligentie. Hofmeijer: “Veel bedrijven zijn nog niet zo ver. Wij zeggen: begin maar eens met het verzamelen van data en te bepalen wat je precies wilt met je bedrijf. Dan weet je ook wat je wilt gaan ontwikkelen. Bijvoorbeeld een koppeling van CAD aan offline programmeren en aan ERP. Of een koppeling van lasprocessen aan snijmodellen. Om dat te kunnen doen heb je data nodig. Pas als je data gaat verzamelen ben je in staat systemen te gaan koppelen. Met natte-vinger-werk, bijvoorbeeld ruwe schattingen van productietijden, lukt dat gewoon niet. Het is echt: no data, no talk.”
Automatisering efficiënter aansturen
De basis van digitalisering is de digital twin. Hofmeijer legt uit: “Automatisering en digitalisering worden vaak over één kam geschoren, maar het zijn echt twee verschillende dingen. Met automatisering automatiseer je processen. Met digitalisering stuur je automatisering efficiënter aan. En een digital twin maakt het mogelijk om met digitalisering geautomatiseerde systemen aan elkaar te koppelen.” MKB-maakbedrijven kunnen er veel profijt van hebben door hiermee aan de slag te gaan. Hofmeijer: “In veel maakbedrijven zijn de processen allemaal losse eilandjes. Al die eilandjes hebben hun eigen oplossing gevonden voor hun probleem en op basis van mondelinge
RIDE-deelnemers
Aan het RIDE-project doen dertien partners mee. Dit zijn allemaal bedrijven en organisaties in Oost-Nederland. De partners zijn:
Aebi Schmidt Nederland (Holten) Gunnebo (Doetinchem) Pan Oston (Raalte) Contour Covering Technology (Winterswijk) Breman Machinery (Genemuiden) Almi Machinefabriek (Vriezenveen) Broshuis (Kampen) Evers Agro (Almelo) Dulasta Metaalbewerking (Staphorst) Hoopman Machines (Aalten) Schouten en Visschers Metaalwarenfabriek (Epe) ROC van Twente (Hengelo) LAC (Hengelo)
afspraken zijn procedures tussen die eilandjes ingericht. Dat houdt automatisch in: veel dubbel werk en veel mensafhankelijke factoren met een grote kans op fouten.” Dat kan allemaal worden geëlimineerd door een digital twin over al die processen heen te leggen; een 3D model dat lijntjes, verbindingen legt met alle andere processen en zorgt voor naadloze uitwisseling van informatie. De ideale digital twin bevat de virtuele kopieën van meerdere (directe) productieprocessen gekoppeld met omliggende gedigitaliseerde (indirecte) processen, zoals ontwerp en engineering (CAD, 3D tekeningen), werkvoorbereiding en robotprogrammering, CAM (automatisch offline programmeren), proces parameterinstellingen van bijvoorbeeld lassen, snijden, stralen en spuiten, real time monitoring en logging ten behoeve van kwaliteitsborging en het realiseren van KPI’s, planning/ERP.
Weg der geleidelijkheid
Is zo’n digital twin eenmaal gerealiseerd, dan is er sprake van integrale digitalisering. En dat biedt grote voordelen: sneller inzicht krijgen; sneller opstarten; verhoogde efficiëntie; minder fouten; meer doen met je huidige vakmensen; het realiseren van groei met optimale marges. De weg naar deze integrale digitalisering is echter lang. Daarom kiest RIDE net als de Smart Welding Factory voor de weg der geleidelijkheid, zodat het voor alle deelnemers behapbaar is. Iedere RIDE-deelnemer kan bovendien weer zijn eigen puzzelstukje kiezen. “We luisteren heel goed naar elk bedrijf waar de behoefte precies ligt”, legt Hofmeijer uit. “We kijken: wat is er aanwezig, wat doen jullie aan digitalisering, welk doel wil je bereiken. Het bouwen van een digital twin is afhankelijk van de aanwezige processen in de organisatie en welke van deze processen je aan elkaar wilt koppelen. Kortom: het is altijd maatwerk.” Net als in het SWF-project werkt het LAC weer nauw samen met de bedrijven. Want om van processen een digitale kopie te maken is niet alleen programmeerkennis nodig, maar ook proceskennis.
Meer doen met minder mensen
Ard Hofmeijer is ervan overtuigd dat digitalisering een must is voor het MKB in de metaal/maakindustrie om de uitdagingen van de nabije toekomst aan te kunnen, zeker gezien het toenemende gebrek aan vakmensen. Hij wijst op een veelzeggend staatje uit een publicatie van het Smart Industry team: nu zijn er voor het bedienen van een lasrobot gemiddeld nog drie mensen beschikbaar. Willen we de huidige stand van welvaart in Nederland behouden dan zal gezien de demografische ontwikkeling in 2030 één persoon vier lasrobots aan te gang moeten houden en moet de output 200 procent zijn van wat die nu is. “Daarvoor moet heel wat gebeuren. Dat gaat niet lukken als we elke lasklus moeten programmeren op een PC of iPad. We moeten data gaan verzamelen en hergebruiken. Dan kunnen we veel meer doen met minder mensen en kunnen we bedrijven gaan voorbereiden op het gebruik en het implementeren van kunstmatige intelligentie.”
Contour: ‘Sneller ontwikkelen én implementeren’
Contour Covering Technology in Winterswijk is een van de deelnemers aan het RIDE-project. Joris Pierik, manager Samenstellingen Fabricage, legt uit waarom.
“Dit project is voor ons een voortzetting van het project Smart Welding Factoy. Het geeft ons de mogelijkheid sneller te kunnen innoveren/ontwikkelen op het gebied van productieautomatisering en nieuwe productietechnologieën en deze ook te implementeren.”
Pierik somt op waarin de implementatie van productieautomatisering en nieuwe productietechnologieën voor Contour zal resulteren: “Vergroting van de productiecapaciteit, verlaging van de productiekosten, verkorting van doorlooptijden, verhoging van de flexibiliteit, verlaging van (interne) transportkosten en verlaging van het aantal (externe) transporten met als gevolg minder uitstoot.” Pierik ziet ook de duurzame versterking van de concurrentiepositie binnen Oost-Nederland als een belangrijk aspect van het RIDE-project. Contour steekt bij RIDE specifiek in op het werkpakket ‘New Manufacturing Technologies’, omdat hier voor het bedrijf momenteel het meest te winnen valt. Concreet wordt gedacht aan de implementatie van: een beits- en passiveerinstallatie (nieuw proces), cleanroom (uitbreiding op een bestaand proces), plaatbewerkingsinstallatie (nieuw proces), cobots (uitbreiding op een bestaand en een nieuw proces), AGV’s (nieuw proces), upgraden robotlasinstallatie (uitbreiding op een bestaand proces) en automatische zaagmachine (vernieuwing van een bestaand proces).

Contour steekt bij RIDE specifiek in op ‘New Manufacturing Technologies’ en denkt hierbij onder meer aan de implementatie van een plaatbewerkingsinstallatie, een nieuw proces.
LVD richt roboticabedrijf op
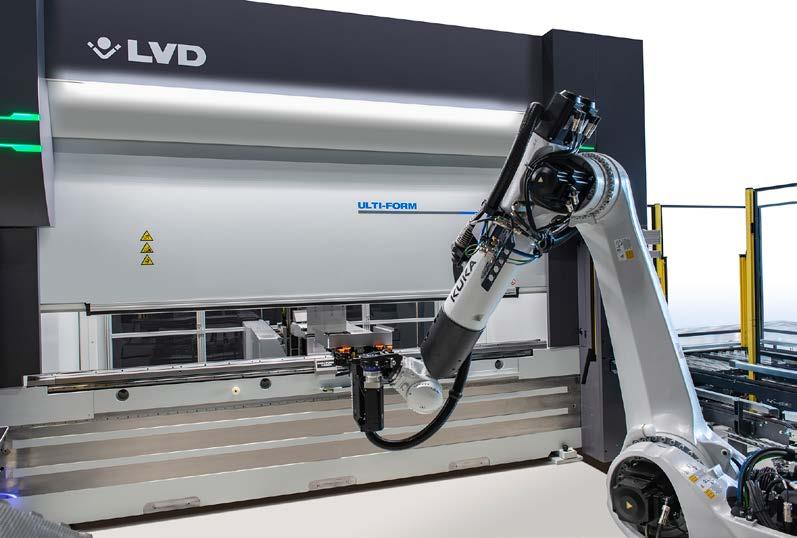
LVD Robotic Solutions gaat zich specialiseren in gestandaardiseerde robotoplossingen voor plaatbewerking met LVD-producten, zoals Dyna-Cell, Ulti-Form en Leancell, en de programmeersoftware CADMAN-SIM.
Revolverponsmachine met X-as van 5 meter
LVD introduceert de Strippit V30 1550, een revolverponsmachine van 30 ton voor hoge tonnages met een X-as van 5 meter.
Met deze uitzonderlijk lange X-as onderscheidt de Strippit V30 1550 zich van andere ponsmachines. Het systeem ponst platen van 5000 mm lang en 1500 mm breed zonder herpositionering, arbeidsintensieve handling of extra snijbewerkingen. Er zijn ook minder nabewerkingen, zoals lassen, wat de stukkosten omlaag brengt. De tandheugel staat garant voor de hoogste nauwkeurigheid en stevigheid over de volledige 5 meter van de X-as. De positioneringssnelheid is 80 m/min met een gecombineerde assnelheid van 104 m/min. De Strippit V30 1550 heeft een maximale slagsnelheid van 440 slagen/min met 25,4 mm centerafstand, in materiaaldiktes tot 6,35 mm.
Groot draagvermogen
Het geavanceerde positioneringssysteem van de machine biedt volgens LVD aan volle snelheid het grootste draagvermogen in de branche. De geavanceerde tafelpositionering van de Strippit V30 1550 heeft een ponsnauwkeurigheid van +/- 0,1 mm met een herhaalnauwkeurigheid van +/- 0,05 mm over de volledige tafel. De processtabiliteit zorgt voor nauwkeurig afgewerkte stukken. De Strippit V30 1550 is verder uitgerust met een veelzijdige, grote revolver met 48 stations en vier programmeerbare klemmen.
LVD neemt de Solutions Unit van Kuka Automation + Robotics in België over en richt LVD Robotic Solutions op. Dit nieuwe bedrijfsonderdeel zal de expertise en het marktbereik van de Belgische machinebouwer op het vlak van robotautomatisering vergroten. CEO Carl Dewulf spreekt van ‘een strategisch bijzondere en zelfs historische stap’.
Het nieuwe roboticabedrijf gaat de ervaring van de overgenomen Belgische automatiseringsafdeling van de Duitse robotproducent Kuka combineren met de expertise van LVD voor het technisch ontwerp van robotsystemen voor de plaatbewerking. Daarbij ligt de nadruk op semi- of volautomatisch offline geprogrammeerde robots, korte doorlooptijden en snelle omzetting van ‘art-to-part’ - van een 3D-digitaal model naar een gekant stuk.
Verder dan plaatbewerking
Maar de oprichting van LVD Robotic Solutions betekent veel meer: met de integratie van robottoepassingen in haar automatiseringsportfolio heeft LVD een volledig aanbod in handen om bedrijven in al hun productieactiviteiten te ondersteunen. Met een hoogstaand portfolio en de diepgaande domeinexpertise van de nieuwe medewerkers zal het nieuwe bedrijfsonderdeel klanten in de meest uiteenlopende takken van de industrie gepaste robotica-oplossingen kunnen bieden, ver buiten de markt van de plaatbewerking.
Automatiseringsstrategie
Met de overname van het Italiaanse automatiseringsbedrijf Compac zorgde LVD in 2019 al voor een significante uitbreiding met onder andere toren- en magazijnsystemen. De oprichting van LVD Robotic Solutions is een verdere stap in deze automatiseringsstrategie met als hoofddoel betaalbare automatisering in meer toepassingen aan te bieden. LVD ziet het geautomatiseerd manipuleren van
Robotoplossingen voor plaatbewerking
LVD Robotic Solutions zal zich specialiseren in gestandaardiseerde robotoplossingen voor plaatbewerking met LVD-producten, zoals Dyna-Cell, Ulti-Form en Leancell, en de programmeersoftware CADMAN-SIM. Daarnaast richt het bedrijfsonderdeel zich ook op andere industriële toepassingen zoals het ontbramen van stukken, coaten van metalen, handlen van onderdelen in de automobielsector, koppelen van persen, aanbrengen van lijm op de autoruit, picken van onderdelen in de productielijn en verpakken.
Centrum voor robotautomatisering
LVD Robotic Solutions neemt het engineering- en projectmanagementteam van Kuka Benelux over. De verkoop en service-activiteiten van Kuka-robots blijven als afzonderlijke entiteit van Kuka Benelux bestaan en richten zich naar integratoren en eindklanten, zoals LVD Robotic Solutions. Beide ondernemingen blijven opereren vanuit het kantoor in Houthalen-Helchteren. Als onderdeel van de transactie verwerft LVD de 7.000 vierkante meter grote vestiging van Kuka Benelux. Houthalen-Helchteren ligt in de provincie Limburg strategisch gepositioneerd tussen Nederland en Duitsland en kan van daaruit heel Europa bedienen, wat ideaal is voor klantenservice en internationaal bereik. LVD plant extra investeringen om op die locatie de activiteiten verder te ontwikkelen en een Centre of Excellence voor robotautomatisering op poten te zetten. www.lvdgroup.com
De klemmen kunnen afzonderlijk op de X-as geprogrammeerd en tijdens het ponsen naar een nieuwe positie verplaatst worden voor maximaal plaatgebruik. Bij het verplaatsen van één klem, houden de andere drie de plaat stevig op zijn plaats. Andere onderdelen: een grote 450 x 500 mm werkstukklep, LVD’s nieuwste Touch-P-sturing, een volledige borstel- of gecombineerde borstel-kogeltafel en een (optioneel) laad-/ontlaadsysteem van 4 m.
LVD heeft de eerste Strippit V30 1550 geïnstalleerd bij een bedrijf gespecialiseerd in geperforeerde metaaloplossingen voor industrieën gaande van ruimtevaart tot architectuur. De machine vervangt er een ponsmachine geïntegreerd met een haakse schaar, die platen van 1575 x 4025 mm verwerkt. allerhande stukken en uitvoeren van repetitief werk als een deel van de oplossing om het nijpend tekort aan geschoold personeel te omzeilen. Het zorgt bovendien voor meer arbeidsveiligheid. “Dankzij de digitalisatie van de productieflow kunnen de vandaag al schaars te vinden medewerkers zich toeleggen op opdrachten die meer waarde toevoegen”, zegt de wereldwijd opererende machinebouwer.
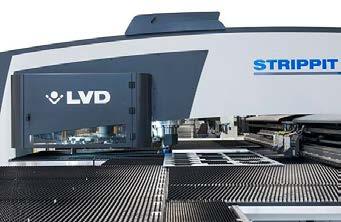
Met deze uitzonderlijk lange X-as onderscheidt de Strippit V30 1550 zich van andere ponsmachines. Het systeem ponst platen van 5000 mm lang en 1500 mm breed zonder herpositionering, arbeidsintensieve handling of extra snijbewerkingen.
Microjoints worden nanojoints
Trumpf presenteert op haar Intech huisbeurs van 17 tot 20 mei in Ditzingen een nieuw proces voor meer efficiëntie en proceszekerheid bij het lasersnijden: het nanojoint-proces. Nanojoints zijn kleine stoppunten waarbij de laser bij het snijden niet volledig door het plaatwerk snijdt. Ze zorgen ervoor dat de componenten niet kantelen terwijl de laser de componenten uitsnijdt.

De nanojoints laten slechts een nauwelijks zichtbaar merkteken achter wanneer de componenten worden gescheiden. “Met onze nanojoints kunnen gebruikers de procesbetrouwbaarheid tijdens het lasersnijden verbeteren en verschillende werkstappen efficiënter maken”, zegt productmanager Patrick Schüle.
Materiaal besparen
Met de nanojoints besparen gebruikers materiaal en kosten doordat de onderdelen beter genest kunnen worden. Afhankelijk van de vorm van de componenten kunnen gebruikers zelfs nesten zonder schrootskeletten. Bovendien kunnen medewerkers veel sneller en gemakkelijker de gesneden delen van de gesneden plaat verwijderen. Trumpf biedt de nanoverbindingen voor zijn lasersnijmachines uit de series TruLaser 5000 fiber, TruLaser 3000 fiber en TruLaser 1000 fiber. Het proces kan achteraf worden uitgerust met een software-update.
Minder nabewerking
Tot nu toe worden vaak microjoints gebruikt om het plaatwerk tijdens het snijden te fixeren. De medewerker breekt deze af wanneer hij de onderdelen sorteert. De nieuwe nanojoints hebben veel voordelen ten opzichte van conventionele microjoints. De processnelheid neemt toe omdat de laser de mini-punjes veel sneller kan produceren tijdens het snijden dan conventionele microjoints. Medewerkers hoeven nauwelijks kracht te gebruiken
Met het nieuwe softwarepakket Oseon voor productieplanning en -besturing kunnen bedrijven slankere productieprocessen creëren en productiviteitswinst behalen. De software omvat nieuwe opties om het transport van materialen flexibel en geautomatiseerd te beheren.
“Oseon vermindert de uitvaltijd en niet-productieve tijd, maakt beter gebruik van de machinecapaciteit en maakt het leven van de medewerkers gemakkelijker. De daaruit voortvloeiende productiviteitswinst kan oplopen tot 20 procent”, zegt productmanager Wolfgang Liertz. Dankzij de open interfaces is de software gemakkelijk in elke sector te implementeren.
Soepele materiaalstroom
Met de software kunnen gebruikers de materiaalstroom op de werkvloer volledig automatiseren, waardoor investeringen in een grootschalig opslagsysteem mogelijk niet meer nodig zijn. “Oseon laat gebruikers de materiaalstroom synchroniseren met hun productieschema. Zo kunnen ze sneller en flexibeler reageren op onverwachte gebeurtenissen zoals spoedorders en meer bestellingen verwerken in minder tijd”, zegt Liertz. Zodra de gebruiker zijn productieschema in Oseon heeft geladen, neemt de software de taak over om veel van de logistieke processen van de fabriek te beheren. Oseon ontvangt continu procesdata-updates van alle productiemachines. Naast de gegevens uit het productieschema en de machines bevat de software ook informatie over batches, materiaalvoorraden, de locaties van elke transportwagen en de onderdelen die nodig zijn op de werkvloer.
Barcodes en slimme dockingstations
Trumpf vertrouwt op een combinatie van barcodes en slimme dockingstations om de materiaalstroom efficiënt te beheren. Elke pallet die per kar of trolley wordt vervoerd, is voorzien van een barcode. Nadat de bewerkte onderdelen op de pallet zijn geplaatst, scant de medewerker deze barcode met een handscanner, waardoor de pallet aan die specifieke batch wordt ‘vastgebonden’. Vervolgens duwt hij de kar in een speciaal door Trumpf ontwikkeld dockingstation met verschillende ingebouwde sensoren. Als alternatief kan deze reis autonoom worden gemaakt door een AGV, die wordt bestuurd door Oseon. Zodra de kar of AGV succesvol is gedockt, stuurt het dockingstation alle informatie naar Oseon. Nu heeft de software alle gegevens die nodig zijn om het transport van de materialen efficiënt te organiseren. Naast het automatisch selecteren van de juiste volgorde voor het transporteren van materialen, stuurt Oseon ook automatisch transportopdrachten naar vrije AGV’s en naar medewerkers met transportwagens. Zo zorgt het ervoor dat de materialen altijd op het juiste moment op de juiste plaats zijn. Als het bedrijf een
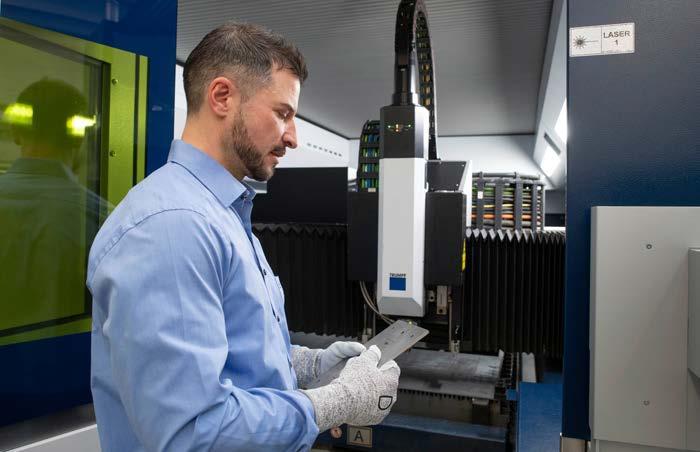
Medewerkers hoeven nauwelijks kracht te gebruiken om onderdelen met nanojoints te verwijderen. Dit bespaart tijd en ontlast het personeel in de productie.
Met de Oseon software kan de materiaalstroom op de werkvloer volledig worden geautomatiseerd.
om onderdelen met nanojoints te verwijderen. Dit bespaart tijd en ontlast het personeel in de productie. Handmatig nabewerken wordt meestal ook volledig geëlimineerd, omdat de nanojoints slechts een nauwelijks zichtbaar merkteken achterlaten wanneer de componenten worden gescheiden. Bij microjoints daarentegen is er een grotere beschadiging van de contouren, die de medewerker dan handmatig moet verwijderen.
spoedopdracht krijgt, kan Oseon zich eenvoudig aanpassen aan de nieuwe situatie door het materiaaltransportschema aan te passen. Dit minimaliseert de niet-productieve tijd die nodig is om te wachten op het lossen van een machine of het beschikbaar komen van meer grondstoffen.
Relevante informatie bij de hand
Oseon maakt het leven van productiemedewerkers ook makkelijker. Met behulp van een tablet kunnen ze alle relevante informatie over een order zien zonder hun werkomgeving te verlaten. Dat voorkomt fouten en bespaart tijd. Oseon laat werknemers ook gewoon op hun tabletscherm tikken om gebruiksvriendelijke instructies te krijgen bij elke stap in het productieproces. De software leidt hen door alle komende taken, van het laden van de machine met grondstoffen tot het verwijderen van de afgewerkte onderdelen.
Condition Monitoring
Om bedrijven te helpen hun machinedata te gebruiken om de productie te verbeteren, biedt Trumpf ook toegang tot zijn nieuwe Condition Monitoring-service. Het Predictive Service Center van Trumpf ontvangt actuele toestandsgegevens van alle digitaal verbonden machines op de werkvloer van een klant, zoals gegevens over de temperatuur of druk van afzonderlijke machinecomponenten. Telkens wanneer Trumpf abnormale zaken detecteert die een mogelijke storing of uitvaltijd zouden kunnen betekenen, wordt de klant proactief geïnformeerd. Ook worden hem mogelijke oplossingen aanbevolen per e-mail, via een melding in de service-app of in een telefoontje van een technisch expert. Dit stelt de klant in staat om problemen op te lossen voordat ze leiden tot problemen.

Toegankelijk voor elk bedrijf
De Oseon softare kan volgens Trumpf worden gebruikt door fabrikanten waar digitale connectiviteit nog in de kinderschoenen staat, maar ook in volwaardige slimme fabrieken. Dankzij de open interfaces is de software ook geschikt voor gebruikers die naast Trumpf machines ook machines van andere leveranciers in hun genetwerkte productie willen integreren. www.trumpf.com