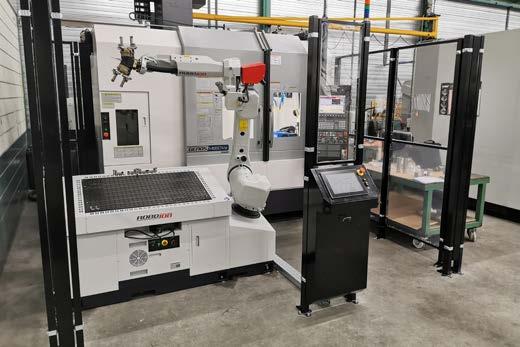
9 minute read
Nieuwe generatie geeft JEVA Metaalbewerking duw richting toekomst
Gerco en Wilco van Amerongen namen JEVA Metaalbewerking in 2015 over van vader Koos van Amerongen. De broers streven naar een professionelere en efficiëntere manier van werken en hebben daarom sinds de overname fors geïnvesteerd in nieuwe machines, automatisering en optimalisering. Met een stabiele basis werkt JEVA nu aan meer spreiding en verdere groei. Om dat te realiseren heeft de toeleverancier in april nog een nieuwe freesbank van Okuma met daarbij een robotarm van RoboJob in gebruik genomen.
JEVA Metaalbewerking uit Lopik is gespecialiseerd in het draaien en frezen van metalen en kunststoffen en in het uitvoeren van laswerk en assemblagewerkzaamheden. Hoewel de productie van enkelstuks tot de mogelijkheden behoort, focust het bedrijf zich voornamelijk op seriewerk van werkstukken met een volume tot 1 m3 . Met name klanten in de machinebouw vormen een stabiele basis voor de toeleverancier en ook in de toekomst verwacht JEVA door de transitie naar verduurzaming, veel nieuw werk uit die sector aan te trekken. “Voor 2015 stond verdere groei niet doelbewust op de agenda van JEVA. Dat is nu wel anders. Er lagen veel kansen in de markt en die grijpen we nu aan. We hebben risico’s genomen, investeringen gedaan en in korte tijd flinke stappen gemaakt om meer klanten uit andere industrieën en vakgebieden aan ons te binden. Door onze stabiele basis te koesteren en tegelijkertijd
De nieuwe Okuma Genos M660-V-e met een RoboJob Mill-Assist laat goed zien hoe JEVA processen wil optimaliseren.
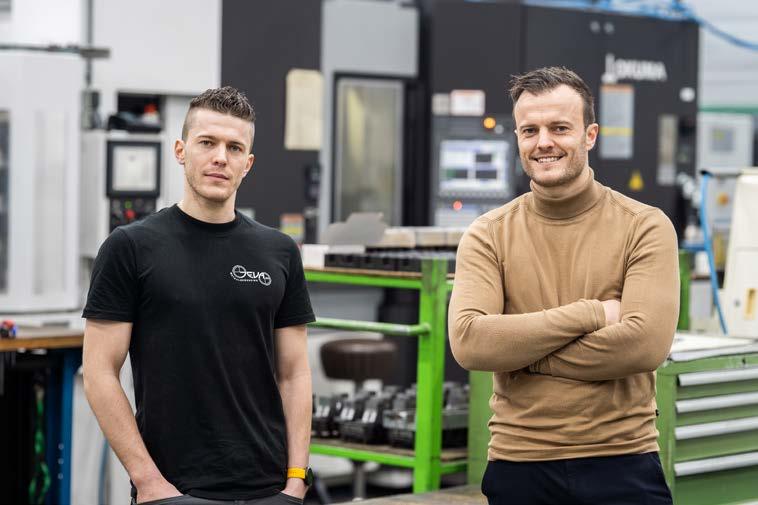
Wilco en Gerco van Amerongen leggen de focus op optimalisatie van de interne bedrijfsprocessen. (foto’s: JEVA Metaalbewerking)
meer spreiding in het klantenbestand te realiseren, willen we beter bestand zijn tegen economische schommelingen”, vertelt Gerco. Wilco vult aan: “Door het bedrijf verder te ontwikkelen kunnen we in de toekomst de levering van hoogwaardige producten blijven garanderen. Sinds de overname is er geïnvesteerd in vijf nieuwe machines en inmiddels groeien we qua beschikbare ruimte in de fabriek uit ons jasje. Dat betekent dat we nu druk bezig zijn om processen efficiënter in te richten.”
Meer capaciteit door hoger rendement
Ondanks dat Gerco en Wilco van plan zijn om in de toekomst de huidige fabriekshal uit te breiden om gehoor te kunnen blijven geven aan de groeiende vraag naar producten, wordt er eerst gewerkt aan het optimaliseren van de huidige bedrijfsprocessen. Reden is dat het verkrijgen van een vergunning voor uitbreiding lang op zich kan laten wachten. Om toch meer capaciteit te verkrijgen heeft JEVA het machinepark opnieuw ingedeeld om meer ruimte te verkrijgen. Daarnaast worden oude bewerkingsmachines stap voor stap vervangen voor nieuwe machines die meer mogelijkheden bieden, zoals vijfassig frezen en automatisering. Zo is recent een 21 jaar oude freesmachine vervangen voor een Okuma Genos M660-V-e die direct is voorzien van een RoboJob Mill-Assist E i 20-35. Gerco: “Innovatie is één van de belangrijkste pijlers bij JEVA Metaalbewerking en om die reden investeren we dus ook in nieuwe machines en systemen. Alleen op die manier kun je met hetzelfde aantal machines en personeel meer output genereren.” De mogelijkheden van nieuwe machines geven vaak al een behoorlijke productiviteitswinst. Niet alleen de snelheid en nauwkeurigheid geven een boost, maar ook de mogelijkheid om werkstukken in één opspanning compleet te kunnen bewerken. “Wil je meer capaciteit behalen zonder het machinepark verder uit te breiden, dan moet je de spiltijd verhogen. Dat kan alleen door neventijden te verkleinen. Met moderne machines die bijvoorbeeld vijfassig frezen mogelijk maken, kunnen we in één opspanning compleetbewerken. Dat scheelt aanzienlijk in tijd. Daarnaast is automatisering een ideale oplossing om de spiltijd te vergroten”, vertelt Wilco.
Kleinere series sneller leveren
Momenteel heeft JEVA 40% van de bewerkingsmachines voorzien van een automatiseringsoplossing om meer capaciteit te verkrijgen. Daarnaast zijn Gerco en Wilco van mening dat repeterend werk, lees “200 keer op een knop drukken”, niet meer door vakmensen gedaan moet worden. Ook daarom hebben de broers een strategie doorgevoerd, waarbij in de bemande uren de kleinere series en het specialistische werk wordt gemaakt en de machines worden voorbereid om ‘s nachts onbemand te kunnen produceren. “Door de 24/7 economie is onze business de afgelopen jaren al behoorlijk veranderd en dat zal in de toekomst steeds verder gaan. Bedrijven willen het liefst zo min mogelijk voorraad, waardoor de vraag naar korte levertijden enorm is toegenomen. Daarnaast hebben
producten alsmaar meer opties en variaties, waardoor series kleiner worden. Kleinere series sneller leveren, dat is de uitdaging en dit vraagt om een nieuwe stap in de automatisering van het bedrijfsproces”, aldus Gerco. Dankzij een mooie generatiemix heeft JEVA enerzijds de vakmensen in huis met veel ervaring en anderzijds de mensen die zijn opgegroeid met moderne technieken. “Als je veranderingen gaat doorvoeren in bedrijfsprocessen, zoals automatisering, dan is het belangrijk om werknemers mee te nemen in die transitie. Ons ideaalplaatje is dat 50% van de productie geautomatiseerd verloopt. Dat betekent dat je aan de ene kant vakmensen nodig hebt die specialistisch en kwalitatief werk kunnen afleveren, maar ook dat je mensen nodig hebt die de kwaliteiten hebben om met robots te werken”, vertelt Wilco.
Optimalisatie
Andere pijlers waar JEVA de focus op legt is de Lean 5S methode en digitalisering. Door overzicht te creëren in alle bedrijfsprocessen wil JEVA meer output genereren en een kwaliteitsverbetering realiseren. Op dit moment heeft het bedrijf al veel stappen gemaakt om papierloos te werken. De volgende stap is het digitaal opstellen van meetrapporten aan de machine. Gerco: “De digitaliseringkant vergt een enorme omschakeling van papier naar digitaal. Veel interne bedrijfsprocessen zoals de urenregistratie, het inscannen van orders en bepaalde onderdelen van de werkvoorbereiding zijn inmiddels gedigitaliseerd. De volgende stappen zijn het digitaliseren
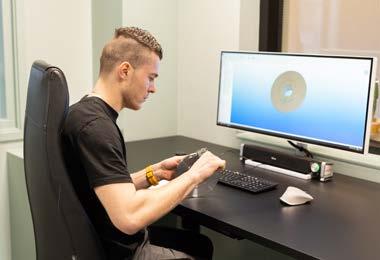
JEVA heeft veel stappen gemaakt om papierloos te kunnen werken
van de productie.” Wilco vervolgt: “Met digitalisering zouden we heel veel informatie uit de productie kunnen halen om processen efficiënter te maken. Dat betekent dat we machines moeten gaan koppelen, zodat we bijvoorbeeld in één overzicht kunnen zien wat de toestand is van het machinepark. Daarnaast kun je aan de hand van de spindeltijd direct zien wat het rendement is en aan de hand daarvan verbeteringen doorvoeren. En wat ook nuttig kan zijn is inzicht in de machine, zodat je onderhoud kan plannen in plaats van dat je achter de feiten aanloopt. Dat kan allemaal helpen om de capaciteit en kwaliteit te verhogen en daarom staat digitalisering dus ook hoog op onze agenda.”
jeva.nl
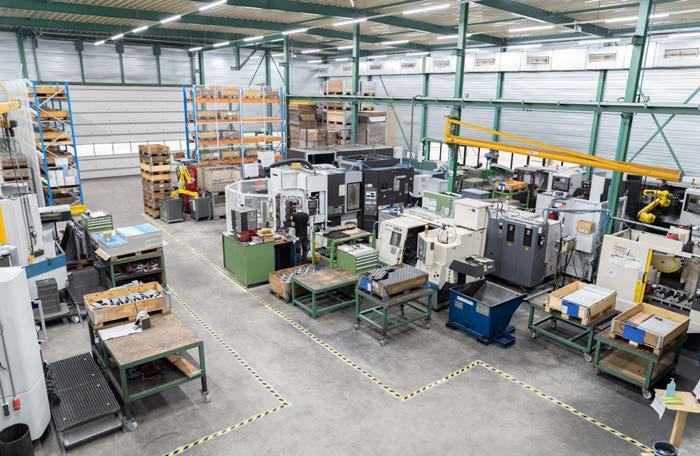
Volledige procescontrole met sensor-geïntegreerde gereedschappen
Onder de noemer Industry 4.0 zijn de afgelopen jaren al veel producten en oplossingen op de markt gekomen die meer inzicht en controle geven over het bewerkingsproces. Gedurende een gezamenlijk, interactief webinar presenteerden DMG Mori en Sandvik Coromant de voordelen van slimme, gereedschappen en bewerkingsmachines om een volledig gecontroleerd bewerkingsproces te realiseren.
Tijdens het webinar werd er live overgeschakeld naar het productiviteitscenter van Sandvik Coromant in Sandviken, Zweden. Daar werden op een NLX 2500|1250 draaicentrum van DMG Mori de voordelen van slim gereedschap gepresenteerd. “Door het terugkoppelen van de gereedschapsdata naar de machine, kan het gereedschap de machine in zekere zin real-time aansturen”, vertelt John Kooning, directeur van DMG Mori Nederland. Tom Dumont, Territory Manager bij Sandvik Coromant, vult aan: “Slimme gereedschappen bieden enorm veel voordelen. Zo kunnen gebruikers tijdig problemen in het proces opmerken, weet je altijd wat er intern in een product gebeurt en is het mogelijk om aan de hand van procesgegevens te optimaliseren zodat het maximale uit een bewerkingsmachine gehaald kan worden. Silent Tools Plus geeft de operator dus een paar extra ogen en oren. Het slimme gereedschap is daardoor ook een optimale oplossing voor operators die minder ervaring hebben met het draaien van interne
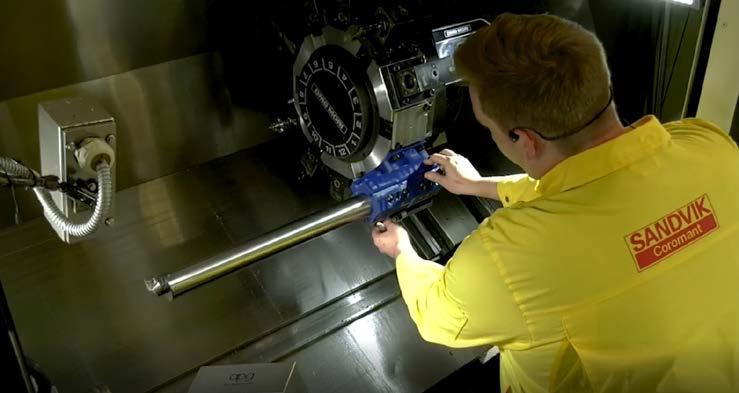
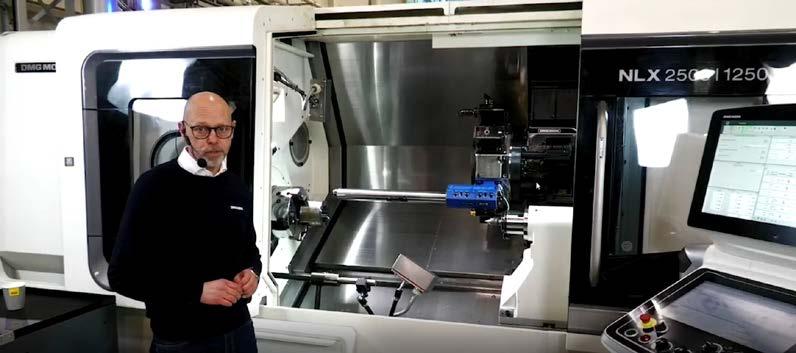
Dankzij geïntegreerde sensoren in de aangedreven Coromant Capto DTH Plus gereedschappen, zijn alle belangrijke parameters in één overzicht te zien.
diepe boringen. Al met al biedt slim gereedschap een hogere bezettingsgraad, een betere procesbeheersing en een kortere setup tijd.”
Fingerspitzengefühl geïntegreerd
Voor het betrouwbaar draaien van diepe interne boringen lieten de partners de Silent Tools Plus boorbaar in actie zien. Silent Tools Plus boorbaren zijn uitgerust met sensortechnologie die het ‘fingerspitzengefühl’ van ervaren vakmensen als het ware integreert in het gereedschap. Hierdoor kan het proces op basis van realtime waarnemingen geoptimaliseerd worden. Het gereedschap kan middels een bluetooth verbinding uitgelezen worden op het Silent Tools Plus dashboard. Dit stelt de gebruiker in staat om eenvoudig het gereedschap in te stellen, zoals bijvoorbeeld de centerhoogte. Daarnaast geeft het Silent Tools Plus dashboard aan of het gereedschap in contact is met het werkstuk. Dankzij een trillings- en een ruwheidsindicator komt informatie beschikbaar over het trillingsniveau en de oppervlakteruwheid. Aan de hand van deze gegevens kunnen procesparameters aangepast worden. Verder kan het gereedschap uitgerust worden met een snijkrachtsensor waarmee ook de doorbuiging van het gereedschap en de ontstane snijkracht kan worden waargenomen om deze zo nodig te compenseren in de programmering. Vooral wanneer een onderdeel van twee zijden moet worden bewerkt, is dit een handige oplossing.
Slimme aangedreven gereedschappen
Procesbeheersing en procescontrole spelen een steeds belangrijkere rol in de maakindustrie. Daarin is een interessante rol weggelegd voor sensortechnologie. “Verspaners hebben als grote uitdaging om de bezettingsgraad van het machinepark zo hoog mogelijk te houden. Handmatig gereedschap wisselen is tijdrovend en soms ook erg lastig, vooral bij machines met beperkte ruimte of wanneer de gereedschapspositie niet gemakkelijk bereikbaar of instelbaar is. In het ergste geval kan het tot wel 10 minuten duren om een gereedschap opnieuw te positioneren of in te stellen. Denk bijvoorbeeld aan schachtbeitels, boorbaren of boren en frezen in een aangedreven gereedschap. Maar ook aangedreven gereedschappen die niet meer optimaal functioneren, achterstallig onderhoud hebben en daardoor plotseling uitvallen, vastlopen of trillingsproblemen veroorzaken, kunnen de efficiëntie van het productieproces nadelig beïnvloeden. Binnen Sandvik Coromant hebben we twee oplossingen om de efficiëntie te verhogen en dat is het snelwisselsysteem Coromant Capto voor aangedreven gereedschappen en de digitale CoroPlus technologie voor aangedreven gereedschappen”, vertelt Ronny Booijink, Machine Tool Solutions Specialist, bij Sandvik Coromant. Het snelwisselsysteem reduceert de tijd benodigd voor meten, instellen en gereedschapswissels, waardoor de machine beter kan worden benut. Sandvik Coromant noemt een gemiddelde reductie van insteltijd van ongeveer zeven minuten per gereedschap. Op jaarbasis zijn dus behoorlijke besparingen mogelijk met een snelwisselsysteem. Door nu ook de CoroPlus met digitale sensortechnologie toe te voegen aan de aangedreven gereedschappen, genaamd Coromant Capto DTH Plus, worden er extra voordelen gecreëerd, zoals proceszekerheid, inzichtelijkheid en een efficiëntere planning van onderhoud. Sensoren in de gereedschapshouder houden bij wanneer het gereedschap aan onderhoud toe is. Echter dat niet alleen. Diverse verspaningsinformatie wordt inzichtelijk gemaakt via een digitaal dashboard dat net als bij de Silent Tools Plus boorbaar met behulp bluetooth verbonden is. Gegevens zoals de resterende levensduur van het gereedschap, de trillingen, de temperatuur in het gereedschap, het toerental en de draairichting zijn allemaal te vinden in het dasboard. Met die gegevens is het bewerkingsproces vergaand te optimaliseren.