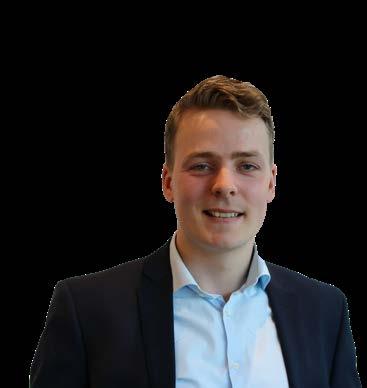
2 minute read
Column Hans Ouwehand (Siemens): Voor elke machine een Digital Twin
Voor elke machine een Digital Twin
Digital Twins worden tegenwoordig steeds meer toegepast in de industrie. Complexe producten en processen kunnen eerst uitvoerig digitaal getest en gesimuleerd worden, voordat deze in de fysieke wereld worden toegepast of geproduceerd. De Digital Twin neemt een steeds grotere vlucht. Dit heeft te maken met de hoeveelheid rekenkracht die we tegenwoordig beschikbaar hebben en de algoritmen die ontwikkeld zijn. Het concept Digital Twin is echter al veel ouder. NASA paste dit concept voor het eerst toe in 1970 met het Apollo 13 programma om eerst aanpassingen te kunnen testen voordat dit werd uitgevoerd in de ruimte. Het is dus niet echt nieuw, je hoort er steeds meer over, maar wat kan Digital Twin betekenen voor de verspaningstechnologie?
Column
Wat is nu eigenlijk een Digital Twin? Digital Twin is een digitale tweeling. Of te wel een virtuele dubbelganger. Dit kan zijn van een product, proces of een volledige productiefaciliteit. Deze virtuele dubbelganger bevat alle gegevens en simulatiemodellen van het daadwerkelijke, fysieke ontwerp. Dit maakt het mogelijk om snel analyses en simulaties uit te voeren in een virtuele omgeving welke overeenkomen met de werkelijkheid. Als een CNC-machine wordt ontwikkeld kan deze zodoende eerst volledig digitaal worden ontworpen in een tekenpakket, bijvoorbeeld NX-Mechatronic Concept Designer. Hierbij wordt niet alleen het mechanisch ontwerp van de machine bekeken (passen alle onderdelen op elkaar) maar wordt bijvoorbeeld ook gevalideerd dat de machine werkt. Dit betekent natuurlijk dat elke beweging, eigenschappen van materialen en kinematica moeten worden ingegeven om een near-perfect afspiegeling te krijgen van de werkelijkheid. Naast het mechanische deel moet daarom uiteraard ook het elektronische gedeelte van de machine worden meegenomen. De PLC- en CNC-besturing worden d.m.v. PLC Sim en Create My Virtual machine digitaal vormgegeven en gekoppeld aan het mechanische deel. Al deze software kan heden ten dage gewoon gebruikt worden. Het is reeds volledig ontwikkeld en in de markt verkrijgbaar.
Als de digitale machine is opgebouwd kan deze uitvoerig gesimuleerd en geanalyseerd worden. Zo kan bijvoorbeeld een gereedschapswisselcyclus uitgebreid getest worden. Is de cyclus juist geprogrammeerd? Raakt de spindelkop niet ergens de machine, wordt de wissel juist uitgevoerd in combinatie met het magazijn, gaan de deuren of luiken op tijd open, etc. etc.? Digitaal kunnen er zaken getest worden, die op een reële machine haast niet mogelijk zijn, zonder de machine ernstig te beschadigen. Crashen doen we dus in een Digital Twin.
Klopt het digitale model, dan kan de machine fysiek volgens dit digitale model worden gebouwd. Doordat fouten in het digitale model er zijn uitgehaald kan de machine veel sneller worden afgebouwd en hoeven er achteraf geen aanpassingen meer gemaakt te worden. Dit bespaart enorm veel kosten en tijd! Kortom, hoewel ‘Digital Twin’ nu nog voor veel mensen niet meer is dan een mooie kreet, is mijn verwachting dat in 2030 vrijwel alle machines worden geproduceerd en uitgeleverd met behulp van een Digital Twin.