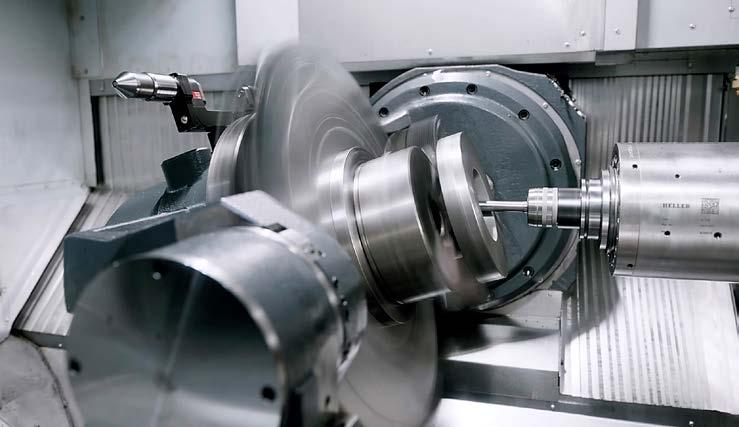
9 minute read
Heller integreert nieuwe technologie in vier- en vijfassers
Het Open House bood voor Heller een uitgelezen kans om de nieuwste technologieën te presenteren. Onder andere ‘Power Skiving’ voor het bewerken van tandwielen behoorde tot de hoogtepunten. (foto’s: Heller)
Heller heeft begin mei stevig uitgepakt tijdens het driedaagse Open House event in Nürtingen (D). Naast de nieuwste generatie vier- en vijfassige bewerkingscentra die onder spaan werden gepresenteerd, legde Heller vooral de focus op innovatieve geïntegreerde technologieën zoals ‘power skiving’ en wrijvingsroerlassen. Tevens kwamen uitgebreide diensten en toekomstbestendige digitaliserings- en automatiseringsoplossingen aan bod, waaronder een nieuw RSP palletmagazijn.
Bezoeker konden hun hart ophalen bij het Open House van Heller. Met live presentaties van machines, technologieën, processen, automatiseringsoplossingen en toepassingen, evenals exclusieve inzichten in de productiefaciliteiten van Heller, was er voor iedereen genoeg te beleven en te zien. “Onze huistentoonstelling bood voor ruim 850 bezoekers een diepgaand inzicht in de wereld van Heller. Met in totaal zes verschillende rondleidingen hebben we bezoekers een exclusief kijkje in onze keuken gegeven. Met name de productiefabriek, de montage- en reparatieafdeling en onze moderne scholingsruimte maakten indruk”, vertelt Reinhold Groß, de nieuwe CEO van Heller. Onder de machine highlights bevonden zich diverse vier- en vijfassige bewerkingscentra, zoals de tweede generatie van de HF 3500/5500 vijfassige bewerkingscentra. Deze kenmerken zich door nog meer flexibiliteit, productiviteit en nauwkeurigheid ten opzichte van hun voorgangers. Ook de vierde generatie van de H 4000/6000 bewerkingscentra stond in de schijnwerpers. Deze vierassers zijn ontwikkeld voor een hoge dynamiek, stabiliteit en productiviteit. Tot slot was de CP 6000 een echte publiekstrekker. Dit vijfassige frees-/ draaicentrum biedt krachtige compleetbewerking op één machine.
Innovatieve technologieën voor serieproductie
Tussen al het nieuws waren een aantal interessante ontwikkelingen te vinden. Zo heeft Heller voor het eerst het wrijvingsroerlassen geïntegreerd in zijn vier- en vijfassige machines. Met deze technologie is het mogelijk om verschillende werkstukken met elkaar te verbinden. Volgens Heller is de integratie van het flexibele verbindingsproces een belangrijke stap richting compleetbewerking. Door in één opstelling zowel de werkstukken te verspanen als te verbinden, worden er duidelijke voordelen behaald op het gebied van productiviteit en nauwkeurigheid.
Verder presenteerde Heller twee nieuwe methoden voor het produceren van tandwielen op verschillende vijfassige

bewerkingscentra. Power skiving maakt het mogelijk om zowel externe als alle soorten interne tandwieloverbrengingen te produceren op standaard vijfassige bewerkingscentra die zijn uitgerust met een draaifunctionaliteit. De tweede mogelijkheid voor het bewerken van externe tandwielen wordt mogelijk gemaakt door afwikkelen (Gear Hobbing). Deze technologie maakt de productie van verschillende tandvormen mogelijk. Beide processen kunnen via software achteraf worden ingebouwd en zijn geschikt voor de bewerking van complexe producten zoals planeetdragers. Een groot voordeel bij deze processen is de eenvoudige programmering via een HMIondersteunde gebruikersinterface.
Tot slot biedt Heller nu ook een softwarefunctie aan voor interpolatiedraaien. De door Siemens ontwikkelde softwarefunctie is tot stand gekomen dankzij de exclusieve ondersteuning van Heller. De softwarefunctie biedt een aantrekkelijk alternatief voor gebruikers die zelden een draaifunctie op een bewerkingscentrum nodig hebben, maar wel de flexibiliteit willen hebben om sporadisch draaibewerkingen uit te kunnen voeren.
Maximale productiviteit
Tijdens het open huis konden bezoekers diverse automatiseringsoplossingen ontdekken die zijn ontwikkeld om de bewerkingscentra van Heller flexibeler en productiever te maken. Tot de highlights behoorde onder andere het nieuwe RSP-palletmagazijn van STS voor geautomatiseerde palletbelading. Verder presenteerde Heller een FPC-palletmagazijn van Fastems en een robotoplossing van STS voor het beladen van werkstukken op een HF 5500. Tot slot werd het geautomatiseerd laden en lossen van gereedschap gepresenteerd op een HF 3500 met een Kuka KMR Cybertech. Naast automatisering kon digitalisering natuurlijk niet ontbreken op het open huis van de machinefabrikant. Heller presenteerde de zogenaamde Shopfloor Interface. Dit is een mobiel 360°-overzicht van alle gegevens die relevant zijn voor het montageproces. In combinatie met de Heller Services Interface ontstaat er meer transparantie in het machinepark, een vermindering van ongeplande stilstandtijden en een hogere productiviteit. Tevens liet Heller verschillende modules zien voor onder andere botsingsbeveiliging en magazijnoptimalisatie.
De bewerkingscentra van Heller zijn uit te rusten met verschillende automatiseringsoplossingen, waaronder het nieuwe RSP palletmagazijn van STS. Heller integreert verschillende technologieën om compleetbewerken mogelijk te maken. Nieuw is de integratie van wrijvingsroerlassen.
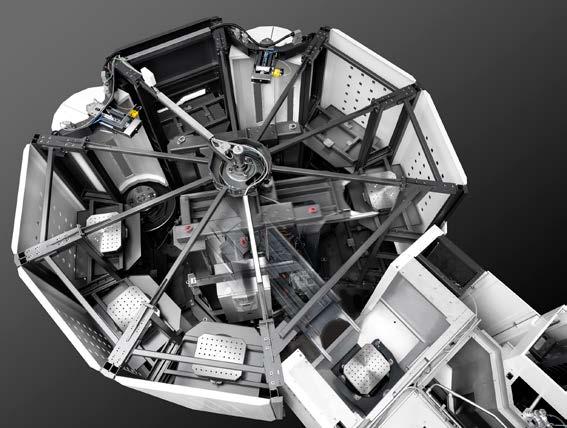
Nat verspanen van grafiet is teamprestatie
GF Machining Solutions, Fraisa en Blaser Swisslube hebben de handen ineengeslagen om een technologie te ontwikkelen voor het nat verspanen van grafiet. Met de zogenaamde GR3-technologie is het mogelijk om naast grafiet ook andere materialen op dezelfde machine en zelfs in dezelfde setup te bewerken. Medio mei organiseerde GF Machining Solutions op het hoofdkantoor in Biel (CH) een evenement om de voordelen van de GR3-technologie te presenteren.

Het verspanen van grafiet is nog altijd een flinke uitdaging voor gereedschap- en matrijzenmakers. Bij het droog verspanen ontstaat er veel stofvorming dat zelfs bij een afgesloten machine een weg naar buiten kan vinden. Veel bedrijven die grafiet verspanen klagen dan ook over de vieze werkplaats. Om stofvorming tegen te gaan kun je nat verspanen. Het probleem dat hierbij optreedt is dat de machine nauwelijks te reinigen is. Zodra de vloeistof met grafietdeeltjes opdroogt ontstaat er een harde zwarte laag in de machine die nauwelijks nog te verwijderen is. In verband met contaminatie is het daardoor vaak niet mogelijk om naast grafiet ook nog andere materialen op dezelfde machine te bewerken. Bovendien kunnen grafietdeeltjes tussen de bewegende delen komen van de machine, zoals bijvoorbeeld de geleidingen. Het gevolg is slijtage aan essentiële componenten en dus veel machineonderhoud. De GR3 technologie van GF Machining Solutions, Fraisa en Blaser Swisslube moet naar verluidt het probleem van grafiet verspaning oplossen.
“We werken veel samen met partners en universiteiten om innovatie te versnellen. Zo zijn we recent een samenwerking aangegaan met Hauser en Kellenberger om slijpen te integreren in een drieassige Mill X 400 frees-slijpcombinatie om de productiviteit en nauwkeurigheid te verbeteren. Tevens optimaliseren we vaak productieprocessen in samenwerking met de klant. Recent hebben we bijvoorbeeld de productie van een luchtvaartonderdeel samen met de klant geoptimaliseerd. Door de kracht van samenwerking wordt dat onderdeel nu 68% sneller geproduceerd en zijn de gereedschapskosten met 60% gedaald. Samenwerking is dus echt een must om grote verbeteringen te realiseren. De nieuwste GR3technologie is daar ook weer een mooi voorbeeld van”, vertelt Thomas Wengi, Managing Director bij GF Machining Solutions.
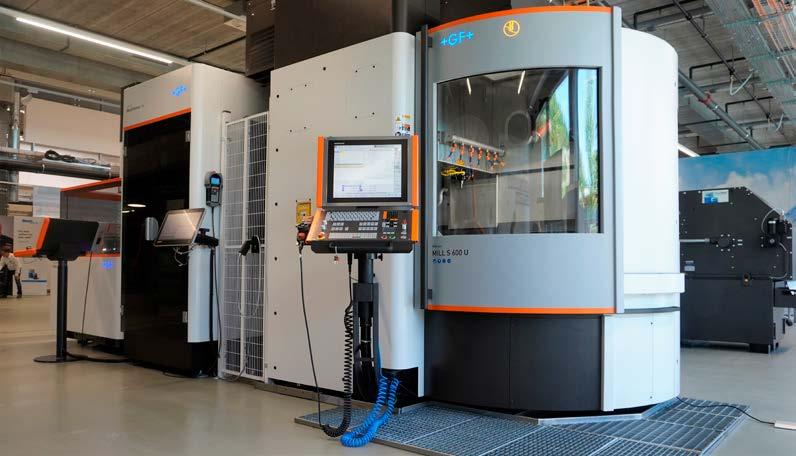
GF Machining Solutions zet in het Technologiecentrum in Biel een Mill S 600 U in voor het verspanen van grafiet.
Koelsmeermiddel absorbeert grafietstof
GR3 is het antwoord van GF Machining Solutions, Fraisa en Blaser Swisslube op het nat verspanen van grafiet én andere materialen in één machine. "Het is een perfect samenspel tussen machine, metaalbewerkingsvloeistof, filtratie en gereedschap", vertelt Tobias Roder, Head of global product management bij Blaser Swisslube. De partners hebben de technologie uitvoerig getest in het technologiecentrum van Blaser Swisslube en in de verspaningslaboratoria van Fraisa en GF Machining Solutions. Op alle drie de locaties werd tijdens het testen een onderdeel uit de praktijk gesimuleerd. Naast de verschillende gereedschapscoatings werden talrijke koelsmeermiddelen met elkaar vergeleken. Voor de GR3-technologie zijn de partners uitgekomen op de Blasogrind GTC 7 koelsmeermiddel van Blaser. Het koelsmeermiddel absorbeert optimaal het grafietstof en voorkomt zo dat stof vrij kan komen in de werkomgeving met als gevolg gezondere werkomstandigheden. Bovendien zorgt het voor een veel schonere machine en het beschermt optimaal tegen slijtage van het gereedschap.
Bespaar op gereedschap
Tijdens het bewerken reduceert een oliefilm de mate van contact tussen het grafiet en het gereedschapsoppervlak, waardoor de standtijd van het gereedschap wordt verlengd. “Normaal gesproken wordt grafiet bewerkt met gereedschappen die zijn voorzien van een slijtagebestendige diamantcoating. Met het koelsmeermiddel van Blaser kunnen we de standtijd van het gereedschap tot wel 5x verlengen. En wat helemaal interessant is, is dat de oliefilm zorgt voor een soepele snede, waardoor we ook standaard PVD-gecoate gereedschappen kunnen gebruiken. Uiteraard is de standtijd van deze gereedschappen wel korter dan dat van gereedschappen met een diamantcoating, maar ze zijn veel goedkoper”, zegt Jonas Meier, hoofd van het center of competence bij GF Machining Solutions.
Optimale oppervlaktekwaliteit
De soepele snede die dankzij de oliefilm wordt verkregen heeft ook een positief effect op de kwaliteit van het werkstukoppervlak. "De oliefilm vermindert de mate van contact tussen het grafiet en het gereedschapsoppervlak, wat de levensduur van het gereedschap verder verlengt. Deze technologie biedt uitstekende voordelen in de vorm van een betere componentkwaliteit, minder afkeur en aanzienlijk lagere productiekosten", aldus Dirk Kammermeier, hoofd productontwikkeling bij gereedschapsfabrikant Fraisa. Onder een microscoop is te zien dat er bij het nat verspanen veel minder korrels zijn uitgebroken dan bij het droogverspanen. Door het gladde werkstukoppervlak kan het grafiet volgens GF Machining Solutions geen olie opnemen. Meier: “We hebben ontzettend veel testen gedaan om te onderzoeken wat voor effect het koelsmeermiddel heeft op het grafiet. Je wilt immers niet dat de emulsie wordt opgenomen door het grafiet en later een negatieve invloed heeft op bijvoorbeeld het vonkproces waar de grafiet elektrodes worden ingezet. We hebben testen gedaan waarbij we een elektrode bedekt met olie 24 uur hebben laten drogen. Vervolgens hebben we onderzocht of deze olie in het materiaal is getrokken. Het resultaat is met 0,2% verwaarloosbaar en het vonkproces was vergelijkbaar met een elektrode die droog was verspaand.”
Filtratie middels centrifuge
Naast de machine, het gereedschap en het koelsmeermiddel is er nog een belangrijk aspect dat het natverspanen van grafiet middels de GR3-technologie mogelijk maakt, namelijk het filteren van het koelsmeermiddel. De partners maken gebruik van drie systemen om het stof en de spanen te filteren. Kleine hoeveelheden spanen en stof kunnen door een standaard spaanafvoersysteem in combinatie met een bandfilter worden gefilterd uit de emulsie. Wanneer het volume aan spanen groter wordt, wordt er gebruik gemaakt van een Knoll centrifuge die de deeltjes scheidt van de vloeistof. De vloeistof wordt na filtering met behulp van een pomp weer teruggevoerd naar de machine. Voor nog hogere spaanvolumes kiezen de partners voor een Ruma centrifuge en wanneer de spanen groter zijn dan 10 mm, wordt hier ook nog een spanentransporteur aan gekoppeld. Zo blijft het koelsmeermiddel schoon en kan het langdurig gebruikt worden voor de bewerking van verschillende materialen.
Meer materialen op één machine
Met de GR3 technologie hebben de partners niet alleen het probleem van stofvorming opgelost, maar het ook mogelijk gemaakt dat één enkele machine kan worden gebruikt voor de bewerking van verschillende materialen, zoals grafiet, koper en staal. Al deze materialen kunnen in hetzelfde productiesysteem worden bewerkt, zonder enige handmatige tussenkomst en met dezelfde instellingen en gereedschappen. Dure bewerkingen met meerdere machines zijn niet langer nodig voor het bewerken van verschillende elektrodematerialen. Al met al helpt de GR3 technologie matrijzenmakers om kostbare bewerkingen met meerdere machines te elimineren, een betere kwaliteit te bereiken, een gezondere werkomgeving te bieden en cyclustijden te optimaliseren. Volgens GF Machining Solutions zijn er door de implementatie van de GR3-technologie besparingen mogelijk van maar liefst 25 euro per spindeluur, waardoor de ROI heel interessant wordt.
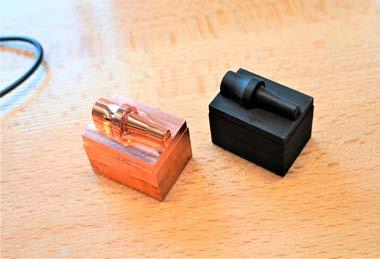
Een voorbeeld van een onderdeel van koper en grafiet die allebei op dezelfde machine zijn bewerkt.
