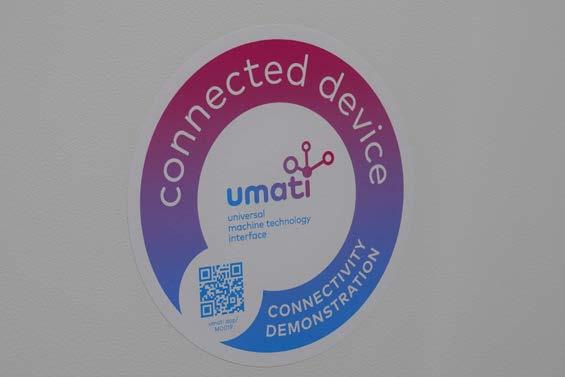
14 minute read
Umati maakt grote digitale fabriek mogelijk
Grote digitale fabriek. Umati maakt het mogelijk
In aanloop naar EMO Milano 2021 kondigde de beursorganisatie aan dat de beurshallen zouden worden omgetoverd tot de grootste digitale fabriek ooit. Na een dag rond slenteren door de beurshallen van Fiera Milano Rho was er op het eerste gezicht weinig te merken van dit initiatief. De gemiddelde beursbezoeker zal er dus waarschijnlijk weinig van gezien of gemerkt hebben. Toch was de digitale fabriek er zeker wel. Wie goed heeft opgelet heeft op menig machine een sticker van umati zien zitten. Een teken dat die machine was verbonden in een digitaal netwerk.
Bewerkingsmachines, robots, productiesystemen, ondersteunende technologieën en software oplossingen waren in overvloed aanwezig op EMO Milano. Maar wat maakt dan die digitale fabriek? Het initiatief van umati kwam het dichtst in de buurt. Meer dan 50 machines waren namelijk tijdens de beurs verbonden via de gestandaardiseerde interface. Op de stand van umati konden bezoekers op het vernieuwde umati-dashboard live de status van deze machines inzien.
Umati is ontwikkeld door een grote groep machinebouwers die de noodzaak zien van een open, onafhankelijke communicatiestandaard om de data tussen machines, componenten en installaties naadloos en betrouwbaar uit te kunnen wisselen met de IT-ecosystemen van gebruikers. Heinz-Jürgen Prokop, voorzitter van de Duitse branchevereniging VDW, gaf aan trots te zijn op de koppeling van umati met 50 verschillende machines. “De belangrijkste mijlpaal
De umati-sticker gaf aan welke machines op EMO verbonden waren met umati.
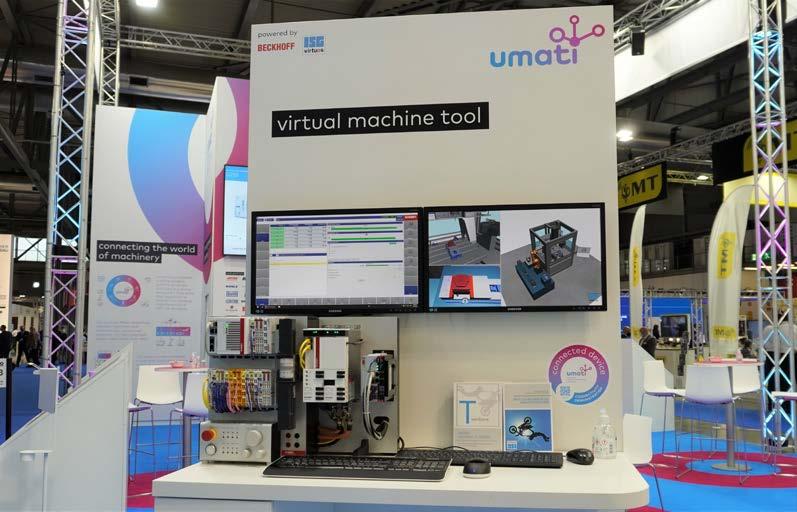
Op EMO Milano 2021 waren 50 machines verbonden via de universele OPC UA for Machinery interface. Op de stand van umati konden bezoekers op het vernieuwde umati-dashboard live de status van deze machines inzien. (foto’s: Tim Wentink)
voor de ontwikkeling van de universele OPC UA for Machinery interface was de publicatie van de specificatie bijna een jaar geleden. Dankzij deze specificatie die wereldwijd gratis verkrijgbaar is, kunnen alle bedrijven die gereedschapsmachines maken of daarvoor software aanbieden hun producten op basis van deze specificatie verder ontwikkelen. Dankzij de open communicatiestandaard is de digitalisering van het productieproces eenvoudiger en sneller te realiseren.”
Breed gedragen
De missie van umati is om het gebruik van de universele OPC UA for Machinery interface te bevorderen. Dit community- en marketinginitiatief richt zich inmiddels niet meer uitsluitend op de machinebouwindustrie, maar op de gehele machine- en installatiebouw. Umati heeft momenteel bijna 200 partners, waaronder meer dan 160 bedrijven. Dit zijn machinefabrikanten, softwareleveranciers en gebruikers. Ook houtbewerkingsmachines, oppervlaktetechnologie en glasmachines maken deel uit van umati met hun eigen OPC UA-specificaties.
Versie 2 gericht op auto-industrie
De eerste versie van de OPC UA for Machinery was bedoeld om een dataset te creëren die universeel toepasbaar is op alle werktuigmachines. Een subgroep van de zogenaamde Joint Working Group for Machine Tools werkt momenteel aan het standaardiseren van aanvullende analysegegevens voor KPIevaluaties. "Hierdoor wordt ook een groot deel van de machine- en productiegegevens die de auto-industrie al gebruikt, naar onze open interface overgebracht", belooft Prokop. Dit moet het voor machinefabrikanten gemakkelijker maken om acceptatie te krijgen voor de open interface met hun belangrijkste klantengroep. Publicatie van deze specificatie is gepland voor het eerste kwartaal van 2022.
Aansluiting van IT-, MES- en ERP-systemen
Het marktsucces van interfaces hangt af van het feit dat er zowel machines als software zijn die met de bijbehorende interfaces zijn uitgerust of deze kunnen verwerken. "Klanten vragen nu al wanneer hun IT-, MES- of ERP-systeem de gestandaardiseerde gegevens kan verwerken", vertelt Prokop. “We werken al een tijdje aan dit vraagstuk met een aantal vooraanstaande partners. Zo heeft SAP ons al meermaals ondersteuning geboden bij het geven van live demonstraties. Hier bij EMO Milano zijn we verheugd om de eerste productieklare interface-implementaties in bekende MES-systemen aan te kondigen in samenwerking met onze partners mpdv en IGHInfotec”, kondigde hij aan. Over het algemeen trekt umati wereldwijd grote belangstelling. Alleen al op de EMO waren elf machines van Chinese fabrikanten aangesloten.
Het gepatenteerde iGroove systeem van Sodick reduceert met een roterende draad het draadverbruik bij navonken tot wel 30%. Daarnaast heeft de technologie een positief effect op de oppervlaktekwaliteit en maatnauwkeurigheid van het werkstuk.
De Ridder presenteerde begin oktober tijdens de jaarlijkse Technologiedagen in het eigen TechCenter in Best een gepatenteerde technologie die het draadverbruik bij het draadvonken tot wel 30% kan reduceren. iGroove, zoals Sodick de technologie noemt, zorgt ervoor dat de draad tijdens de neergaande beweging om zijn as draait. Daardoor wordt bij het vonken een groter oppervlak van de draad ingezet, waardoor de draad egaler slijt en met een tragere snelheid loopt. Daarnaast heeft iGroove een positief effect op de oppervlaktekwaliteit van het werkstuk.
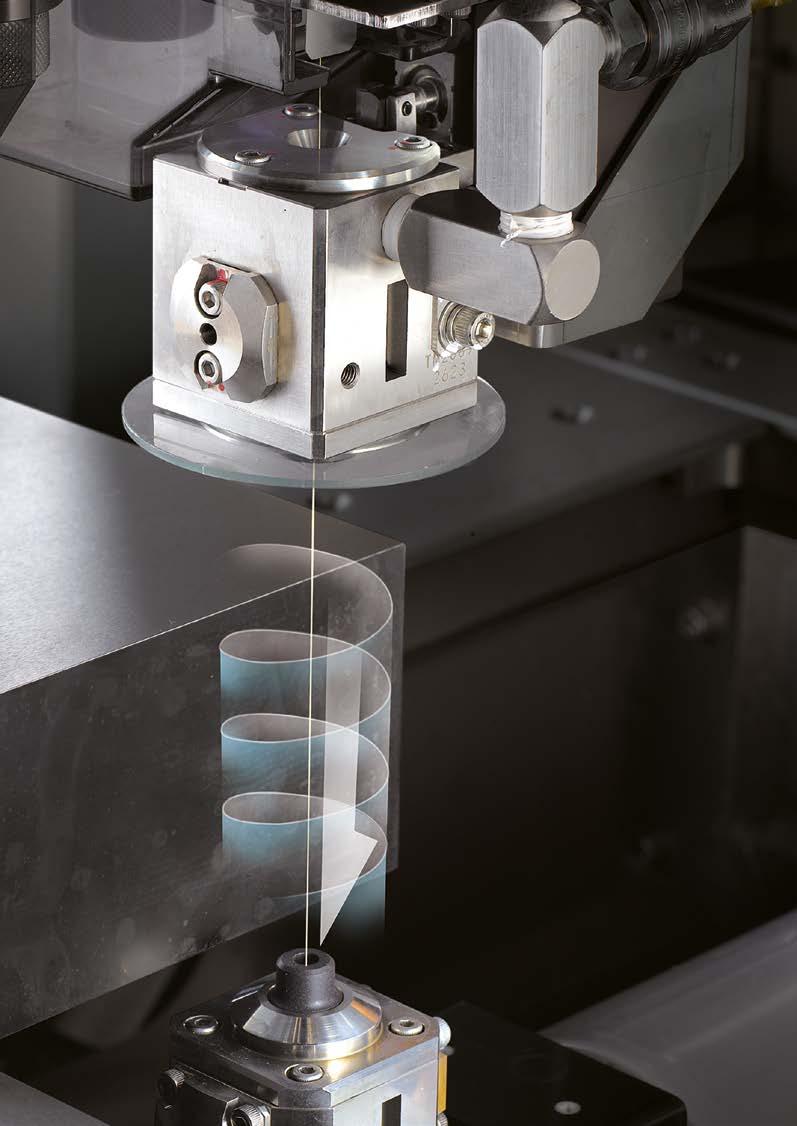
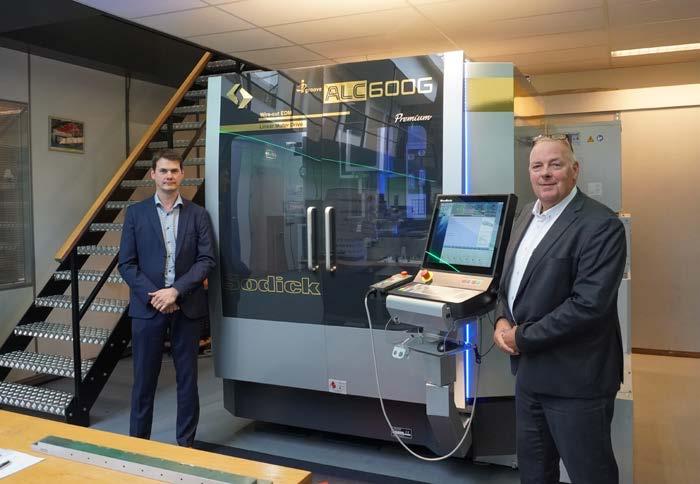
Tom Noens (l) en Hans Wisman presenteren in het TechCenter van De Ridder de voordelen van iGroove met behulp van een ALC600G draadvonkmachine.
De gepatenteerde iGroove technologie is een standaard functie op alle draadvonkmachines uit de ALC-serie van Sodick. Tijdens de technologiedagen presenteerde De Ridder de werking van iGroove op een ALC600G. Het nieuwe rotatiemechanisme van Sodick geeft de draad een extra functionaliteit, meer controle en een hogere procesbetrouwbaarheid. De draad draait, in tegenstelling tot conventionele vonkprocessen, tijdens de neergaande beweging om zijn as. Hierdoor worden werkstukken altijd van boven naar beneden bewerkt met het ‘verse’ oppervlak van de draad. “Het grote voordeel van iGroove is dat het draadverbruik fors wordt gereduceerd, terwijl tegelijkertijd een hogere oppervlaktekwaliteit en verbeterde geometrische nauwkeurigheid wordt bereikt”, aldus Hans Wisman, productspecialist bij De Ridder
Wiel met keramiek
Het iGroove rotatiemechanisme is gepositioneerd in de onderarm van de Sodick draadvonkmachine. Om de draad te roteren heeft Sodick een eenvoudige, maar vernuftige oplossing ontwikkeld. Het rotatiemechanisme is namelijk voorzien van een keramisch wiel met een holle ronding waar de draad in loopt. Het wiel wordt met behulp van een as iets uit het midden geplaatst. Omdat de draad onder spanning staat, probeert de draad het diepste punt van de holle ronding op te zoeken. Hierdoor begint de draad automatisch en constant te draaien. Het roterend vonken is bedoeld voor het navonken van werkstukken met een hoogte van 60 mm of meer. Omdat het keramische wiel op een as is gepositioneerd, kan het wiel zowel naar links als naar rechts bewogen worden. Zo kan de rotatierichting voor tegenlopend vonken worden aangepast. De juist rotatierichting wordt automatische gedefinieerd door de CNCbesturing
Live presenteren
“We hebben iGroove tijdens de Technologiedagen voor het eerst gepresenteerd en er was veel interesse in deze technologie. Daarom presenteren we volgend jaar een Sodick ALC draadvonkmachine met iGroove functie op TechniShow en een week later wederom op onze jaarlijkse Technologiedagen. Met de stijgende grondstofprijzen wordt het alsmaar interessanter om het verbruik te reduceren”, zegt Wisman. Tom Noens, tevens product specialist bij De Ridder vult aan: “De helft van de verbruikskosten bij het draadvonken komt op rekening van het draadverbruik. Met

Het iGroove rotatiemechanisme is gepositioneerd in de onderarm van de Sodick draadvonkmachine. Een keramisch wiel brengt de rotatie van de draad in stand.
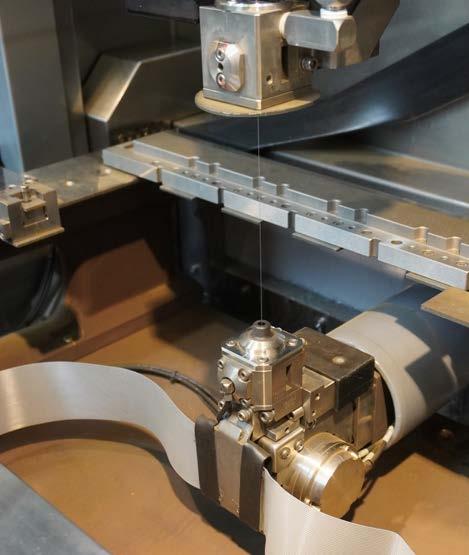
iGroove kan het draadverbruik bij het navonken met wel 30% gereduceerd worden. Dat betekent dus dat klanten fors kunnen besparen op de productiekosten.” Omdat de rotatie van de draad met het blote oog niet te zien is, maakt De Ridder gebruik van een speciaal klemmetje op de draad om de rotatie zichtbaar te maken.
Homogeen oppervlak
Naast dat iGroove het draadverbruik vermindert, zorgt de technologie ook voor een betere oppervlaktekwaliteit en geometrische nauwkeurigheid. Bij conventioneel draadvonken slijt de draad naarmate die verder in het materiaal komt. Vooral bij dikkere werkstukken ontstaat daardoor een oppervlak die taps toeloopt. Om de draadslijtage te compenseren en zo toch een recht oppervlak te verkrijgen, wordt de draad altijd iets onder een hoek gezet. Een andere mogelijkheid is om de voeding van de draad te verhogen, maar dit kan resulteren in het veelvuldig breken van de draad. Door de draad te roteren is het probleem van taps toelopende oppervlakken direct verholpen. Door de rotatie slijt de draad niet op één plaats, omdat er immers continu met het verse oppervlak van de draad gevonkt wordt. Daardoor is compensatie niet nodig en wordt er een hogere oppervlaktekwaliteit en maatnauwkeurigheid verkregen. Wisman: “Onder de microscoop kunnen we heel duidelijk zien wat het verschil is tussen een werkstuk dat met iGroove is gevonkt en een werkstuk dat met conventioneel draadvonken tot stand is gekomen. Met iGroove is duidelijk te zien dat het oppervlak homogener is. Dat wil zeggen dat we minder zwarte puntjes aantreffen op het oppervlak. Het is dus gladder.” De Ridder heeft inmiddels de eerste machines met iGroove verkocht en geleverd.
ALC-serie
Draadvonkmachines in de ALC-serie behoren tot de high-end machines van Sodick. De nieuwste technologieën worden toegepast in deze rijk uitgeruste machines. Naast iGroove is de ALC-serie nu ook voorzien van een nieuw ontworpen diëlectricum tank met een grotere capaciteit (de ALC400G-tank is vergroot van 675 liter tot meer dan 790 liter en de ALC600G-tank is vergroot van 850 liter tot meer dan 990 liter) en is het aantal filters verhoogd van drie naar vier om de filtratie-efficiëntie verder te verhogen. Verder is de ALC-serie voorzien van de nieuwste SPW-besturing met handige functies die de bediener optimaal assisteren en de TH COM functie die met behulp van sensoren het effect van temperatuurveranderingen in de machine minimaliseert en compenseert.

Een kijkje door de microscoop op het oppervlak van een werkstuk. Links (zonder iGroove) zijn duidelijk zwarte puntjes te zien die aantonen dat de oppervlaktekwaliteit niet homogeen is. Rechts (met iGroove) zijn er aanzienlijk minder onregelmatigheden waarneembaar.
Verspaner krijgt rekening voor CO2uitstoot gepresenteerd

Mazak wil met het Go Green initiatief het energieverbruik van machines reduceren om de CO2-uitstoot van klanten terug te dringen. (foto’s: Tim Wentink)
De CO-uitstoot gaat een grote rol spelen voor eigenaren van bewerkingsmachines. Niet alleen zullen producenten het energieverbruik en de uitstoot per product inzichtelijk moeten kunnen maken, ook gaat CO2-uitstoot belast worden met een CO2-heffing. Hoewel de grootste vervuilers in eerste instantie de heffing gaan betalen, zal dit uiteindelijk gevolgen gaan hebben voor iedereen in de keten. Om die reden heeft Mazak onder de vlag van ‘Go Green’ diverse oplossingen gepresenteerd om producenten te helpen met de reductie van CO2-emissies.
De CO2-uitstoot van het fabricageproces kan een groot deel uitmaken van de totale CO2-uitstoot die een product gedurende de levenscyclus uitstoot. Een middelgrote auto zal bijvoorbeeld tijdens zijn leven 25 ton CO2 produceren, waarvan ongeveer 5,6 ton terug te herleiden is naar het fabricageproces. Om de emissies van machinegebruikers te helpen reduceren, heeft Mazak het Go Green initiatief gestart. De Go Green-visie richt zich op het verbeteren en verduurzamen van bewerkingsmachines, zodat klanten het energieverbruik en daarmee de CO2-footprint kunnen verkleinen. Het uiteindelijke doel is dat de machines van Mazak in 2030 een vier keer grotere milieu-efficiëntie hebben dan de benchmark van 2010. “Voor lange tijd was het energieverbruik niet echt een topic in de maakindustrie. Energie was relatief goedkoop, waardoor energiezuinige oplossingen niet bovenaan de wensenlijst stonden bij de aanschaf van nieuwe bewerkingsmachines. Met de introductie van een CO2-taks die er zeker gaat komen in combinatie met de stijgende energiekosten, kan de maakindustrie niet meer om energiezuinig produceren heen”, vertelt Job van Berkel, directeur van Mazak Benelux.
Inzicht in CO2-uitstoot
Mazak richt zich met het 'Go Green'-initiatief op twee aspecten die betrekking hebben op de machinetechnologie. Machines worden ten eerste energiezuinig ontworpen en voorzien van een groot aantal energiebesparende technologieën. De nieuwe generatie van het vijfassige Variaxis i-800 NEO bewerkingscentrum is bijvoorbeeld al volgens de Go Green-visie ontworpen. Dankzij de energiebesparende technologieën stoot het bewerkingscentrum tijdens het verspanen 22,7% minder CO2 uit dan het vorige model. Met het Go Green initiatief wil Mazak klanten ook helpen bij het registreren, analyseren en optimaliseren van hun energieverbruik. Door het verbruik inzichtelijk te maken is het mogelijk om exact het energieverbruik en de CO2-uitstoot per onderdeel te berekenen. De oplossing die
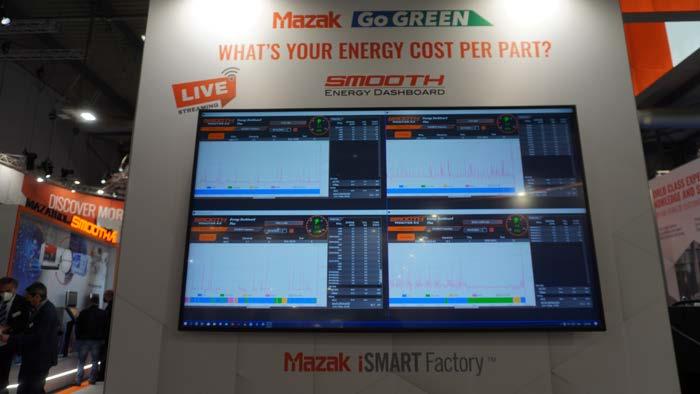
Mazak heeft diverse energiebesparende oplossingen ontwikkeld die door de stijgende energieprijzen en verwachte CO2-taks heel interessant kunnen zijn.
Mazak heeft ontwikkeld om het verbruik inzichtelijk te maken heet Smooth Energy Dashboard. Dit is een meetoptie die in real-time het stroomverbruik van de machine meet en machinegebruikers inzicht geeft in het energieverbruik en de CO2-uitstoot per product. “Er komt een moment dat toeleveranciers een rapport moeten kunnen overhandigen waarin wordt aangegeven hoeveel energie er bij de bewerking van een werkstuk is verbruikt. Met de oplossingen van Mazak kan daar nu al op geanticipeerd worden”, aldus Van Berkel.
Flexibele cobotautomatisering
Naast het Go Green initiatief dat Mazak op EMO Milano 2021 als primeur presenteerde, liet de machinebouwer ook diverse nieuwe automatiseringsoplossingen en bewerkingsmachines zien. Tot de highlights behoort de nieuwe, flexibele Ez Loader 10 cobot. De Ez Loader 10 is een draagbare plug-and-play collaboratieve robot die bij uitstek geschikt is voor metaalbewerkers die snel en eenvoudig de productie van kleine series willen automatiseren. In combinatie met een bewerkingsmachine, zoals het QTE 200 SG draaicentrum die Mazak op EMO presenteerde, ontstaat er een compacte automatiseringscel. De automatiseringscel is het resultaat van een samenwerking tussen Mazak en Fanuc. De cel bestaat uit de cobot die is uitgerust met een camerasysteem, Mazak-software, tabletterminal en een compact frame. Een van de belangrijkste verkoopargumenten van de Ez Loader is het vermogen om snel en gemakkelijk te worden verplaatst om verschillende machines te ondersteunen. Dit helpt om operators vrij te maken voor creatievere taken, de productiviteit te verhogen en productieknelpunten weg te nemen. De cobot kan samenwerken met een verscheidenheid aan Mazak Multi-Tasking-machines of verticale bewerkingscentra die zijn uitgerust met een automatische voordeur en robotinterface. Eenmaal verbonden met de machine met behulp van een kabel, herkent de software het machinemodel en past zich automatisch aan naar de juiste positie door drie positiemarkeringen op de machine te lezen met het camerasysteem. De installatie neemt slecht 15 minuten in beslag, waardoor de cobot heel flexibel inzetbaar is. De Ez Loader 10 heeft een maximaal bereik van 1.200 mm en kan een werkstukmassa van maximaal 5 kg hanteren.

Mazak Europe en BMO Automation slaan handen ineen
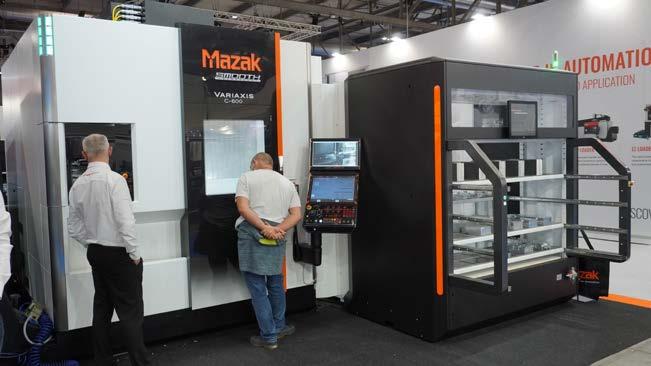
Op EMO Milano 2021 was de samenwerking tussen Mazak Europe en BMO Automation al duidelijk te zien. Het nieuwe, vijfassige C-600 bewerkingscentrum van Mazak werd namelijk gepresenteerd samen met de Platinum 50 van BMO.
Mazak Europe en BMO Automation hebben tijdens EMO Milano 2021 bekend gemaakt dat de twee bedrijven een strategische samenwerking aangaan. De nieuwe samenwerking stelt Mazak in staat om de nieuwe C600 en CV5 500 bewerkingscentra voortaan direct te leveren met een automatiseringsoplossing van BMO. De complete cel wordt dan uit één hand werkend geleverd in de kleuren van Mazak. Voor BMO is de samenwerking een mooie stap om de aanwezigheid in Europa verder uit te breiden.
Volgens Van Berkel is de vraag naar CNC-automatisering de laatste jaren sterk toegenomen. Dankzij de nieuwe samenwerking kan Mazak nu een selectie bewerkingscentra als totaalpakket uitrusten met de product- en palletautomatiseringsoplossingen van BMO. “Voor het automatiseren van kleine, vijfassige freesdelen konden we in het verleden niet altijd de meest efficiënte oplossing aanbieden. Dat terwijl de vraag naar laagdrempelige automatiseringsoplossingen in combinatie met productieve, betaalbare bewerkingsmachines sterk toeneemt. Met de oplossingen van BMO kunnen we nu een totaaloplossing aanbieden, waarmee klanten de capaciteit en het rendement van de bewerkingsmachine ten volle kunnen benutten.” De flexibele automatiseringsoplossingen van BMO zijn ontwikkeld voor het beladen en ontladen van CNC draai- en freesmachines. De systemen zijn geschikt voor het automatiseren van zowel series als enkelstuks.
C-600 met Platinum 50
Op de EMO was het resultaat van de samenwerking al duidelijk te zien. Hier werd namelijk het nieuwe, vijfassige C-600 bewerkingscentrum van Mazak gepresenteerd in combinatie met de Platinum 50 van BMO. De Platinum 50 is voorzien van een flexibele, ruimtebesparende ladekast met vier lades die voldoende werkstukken en pallets kan bevatten om lange perioden onbemand te produceren. De automatiseringsoplossing wordt aan de zijkant van de C-600 geplaatst, zodat de operator goed toegang heeft tot de bewerkingsruimte van de machine. Pallets en werkstukken worden met behulp van een zesassige Yaskawa-robot, met een laadvermogen van 50 kg, van en naar de bewerkingsmachine gebracht. De pallets zijn voorzien van nulpuntspansystemen voor een nauwkeurige positionering. Dankzij de samenwerking tussen de twee partijen wordt de software van BMO volledig geïntegreerd in de Smooth besturing van Mazak. “Frank Biemans, directeur van BMO Automation, is verheugd met de samenwerking: “Door de samenwerking met Mazak Europe kunnen we onze aanwezigheid in Europa sneller uitbreiden. Daarnaast brengen we samen een productiecel op de markt die plug & play is. De klant heeft daardoor nog maar één aanspreekpunt, want de afhandeling gaat volledig via Mazak. Dat is een belangrijk bijkomend voordeel.”