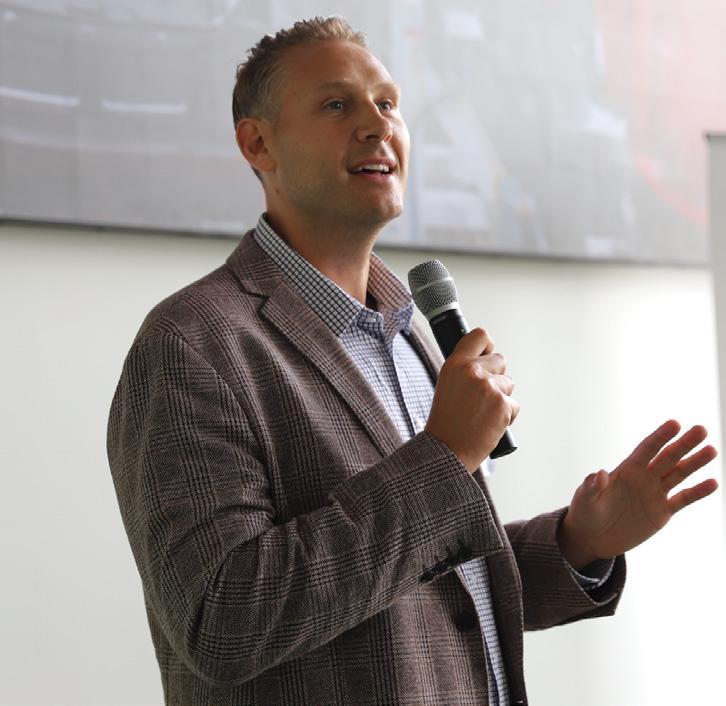
3 minute read
MARKFORGED TIPS “JUST IN PLACE” TO REPLACE “JUST IN TIME” IN AUSTRALIAN MANUFACTURING
The company says it is reinventing the wheel in this space
Persistent supply chain issues are driving Australian manufacturers to produce more parts locally to reduce their dependence on imports.
The focus is on harnessing the benefits of the latest technologies, with 3D printing – additive manufacturing, or AM – providing a fast, efficient and low-cost entry point.
The US-based Markforged states it is one of the world’s leading suppliers of AM printers, software and materials and says it has just launched its largest and fastest printer, the FX20, to an enthusiastic reception from Australian manufacturers and engineers.
At the Perth launch in late 2022, Markforged’s Senior Director, Asia Pacific, Richard Elving, said the perilous state of global logistics made it imperative for Australian manufacturers to become more self-sufficient.
“Given the current supply chain issues, which show no sign of improving any time soon, it’s time for a major shift in mind-set, time to completely reinvent manufacturing,” he said.
Decades ago, companies accepted the expense of holding substantial parts inventories as a necessary operating cost. Then along came “Just in Time” (JIT), enabling manufacturers to delegate that responsibility to their suppliers, who undertook to deliver parts promptly, whenever needed.
Unfortunately, JIT simply cannot function in a world where prompt, reliable import/export logistics no longer exist.
“The choice facing manufacturers is to go back to the bad old days of costly, high inventory levels, accept long delays that will hamstring their production schedules, or find a cost-effective way of sourcing components locally,” Richard said.
“In many cases this third option can be achieved at relatively low cost via a 3D printer that will consistently deliver industrial grade components right where they are needed. In this way, AM can replace ‘just in time’ with ‘just in place.’”
When introducing Markforged’s new printer, Richard said the team developing the FX20 had nicknamed it “The Beast”, because it offered more than twice the capacity of the largest Markforged printer made at the time.
“The good news is that this beast is actually a beauty, and one of its endearing features is that it works straight out of the box. Some of the large printers on the market can take literally weeks –even months – to install, set up and configure,” Richard said.
“With the FX20 you just plug it into the wall, fire up your browser and you’re in business. You can literally un-crate it in the morning and be printing in the afternoon,” he said.
The printer’s versatility is enhanced by the wide range of materials Markforged has developed –there are presently 28 different options.
Markforged says it is currently the only 3D printer in the world offering continuous carbon fibre reinforcement, for high-performance applications in aerospace, defence, automotive and oil and gas.
The FX20’s operating software is also updated on a continuous basis, to provide ongoing improvement of the operation and productivity of the printer.
Conventional manufacturing machinery requires ongoing maintenance and repairs if their initial productivity levels are to be sustained over time. By contrast Markforged says the output rate of the FX20 – like all printers in its range – will increase steadily throughout its working life.
“In summary, the FX20 will deliver advanced composite and metal industrial grade end use parts on demand, at the point of need and, importantly, at costs normally well below those of similar items conventionally manufactured,” Richard said. “Printers and materials of this quality seriously challenge the viability of traditional manufacturing methods, as well as the existing supply chain mentality. To all Australian manufacturers currently reliant on imported parts, and suffering delays and reputational damage in the process, I would pose one simple question – Is it better to get it overseas, or overnight?”
How Avicena re-invented the wheel
Award-winning WA company Avicena was quick to recognise the contribution 3D printing could make to the manufacture and ongoing operation of its ground-breaking Sentinel Biosecurity Platform, an accurate, rapid and scalable molecular diagnostic instrument capable of detecting diverse pathogens, including COVID-19.

In the company’s West Perth offices there is an alcove called the Print Room – but this is a print room with a difference. Alongside a traditional laser printer, busily churning out Avicena’s correspondence and documentation, are two Markforged 3D printers.
The smaller Mark Two printer has a footprint roughly the size of the laser printer. The second, an X7, is only slightly larger. Despite their diminutive size Avicena’s Chief Executive Officer, Tony Fitzgerald, says these two leading edge machines play a “small but significant” role in the company’s operations.
More than 100 components of the Sentinel system were designed – and are now produced – inhouse on the two printers.
For more information, visit www.markforged.com