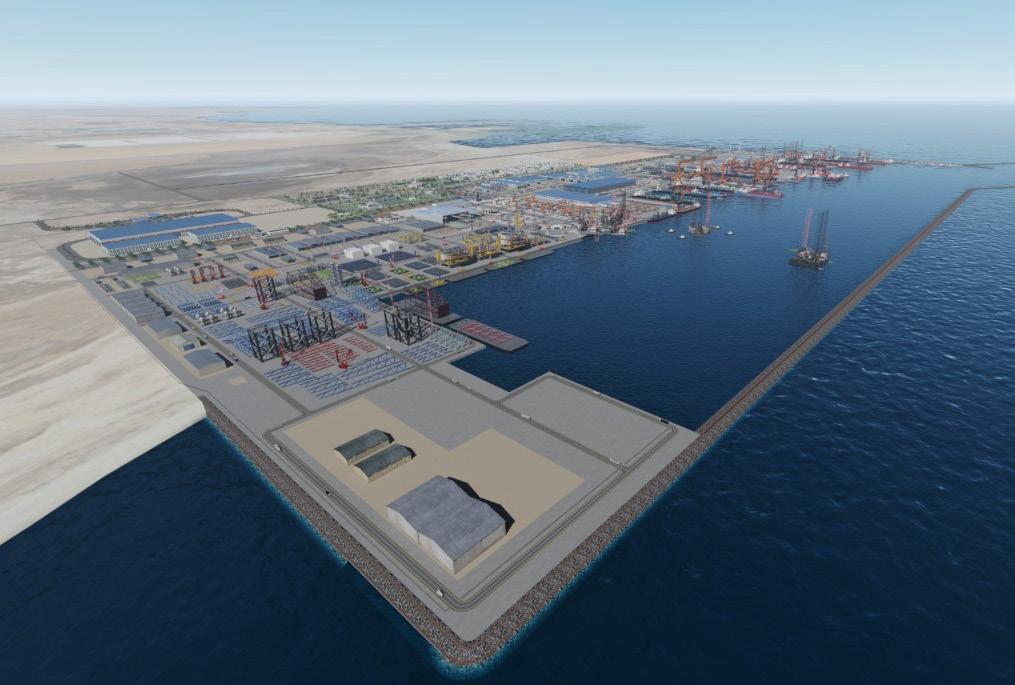
10 minute read
Shipyards
An artist’s impression of IMI yard in Saudi Arabia
Commercial operations well under way at Saudi Arabia’s IMI
Advertisement
The recent completion of a significant jackup rig maintenance, repair and overhaul (MRO) contract by Saudi Arabia’s International Maritime Industries (IMI) marks the first major rig repair project to have been undertaken by the company. IMI is described as the anchor facility within the vast new King Salman Global Maritime Industries Complex and construction at the 11 km 2 complexis still in progress, according to Julian Panter, the company’s Vice President of Business Development. This first rig upgrade project, therefore, was undertaken at nearby Dammam Shipyard, owned by Saudi group, Al Blagha. Completed safely and on time, the ARO Drilling-owned SAR201 left the Damman Shipyard towards the end of March. Co-operation on the project followed the signing of a Master Services Agreement between IMI and the shipyard, a formula that IMI hopes to use again, Panter said. Zone D, designated for rig construction and with a large dock measuring 490 m by 90 m, is likely to open within the next 12 months, he revealed. Three other zones will be completed and commissioned at the vast facility later in 2021 and during 2022. These have been purpose-designed for rig and ship maintenance and repair, shipbuilding and the construction of offshore support vessels. When fully operational, the King Salman Complex at Ras Al Khair, about 60 kms north of Jubail on Saudi Arabia’s Gulf coast, will be unique. It will be the first shipyard facility anywhere in the world to have the capability to construct, maintain, repair and upgrade both offshore assets and commercial vessels in one location. There will be multiple docks, including a 550 m-long shipbuilding dock in Zone C. Over the large dock in this zone, there will be two cranes which can work in tandem to lift over 2,050 tonnes. Meanwhile Zone A will have one of the world’s largest Synchrolifts with in-excess of 30,000-tonnes lifting capacity. The shipyard will have a total quay length of 9 kms Commercial operations have also begun in other areas of IMI’s business, Panter said. Engineering work has begun on newbuild ships and rigs following the signing of newbuilding contracts last September and this January respectively. The September deal involved the company’s first shipbuilding contract – a VLCC for Saudi Arabia’s national carrier, Bahri, a shareholder in IMI with a stake of 19.9%. The contract marks the first ship in a 10-year, 52-vessel off-take agreement between Bahri and IMI. Construction of the ship is being undertaken in partnership with South Korea’s Hyundai Heavy Industries (HHI), also an IMI shareholder with a 20% holding. Meanwhile, following the signing of Rig Purchase Agreements with ARO Drilling, a 50:50 joint venture between Saudi Aramco (with a 40.1% IMI stake) and Valaris Companies, construction of two Le Tourneau Super 116E jack-up rigs has begun. Through a subcontracting arrangement with UAE-based offshore and renewable energy construction firm Lamprell (a 20% shareholder in IMI), the rigs are being built at its shipyard in Hamriyah. Great emphasis is being placed on Saudisation of the IMI project – from head office staff right through to blue-collar workers in ship and rig construction and repair. This is a top priority for Fathi K. Al-Saleem, IMI’s Chief Executive, and a Saudi Aramco executive with experience across many sectors including oil and gas, chemicals, pipelines and refining. He is a specialist in economic analysis, investment appraisal and enterprise risk management. Speaking at an interview in 2018, Mr Al-Saleem stressed the importance of comprehensive Saudi involvement from senior management right down through the ranks to the shop floor. Human resource development, he said, would lie at the very centre of the shipyard’s business strategy. These first three projects provide clear evidence of this. The first 700-person annual contingent of apprentices has recently qualified and many will be sent to work on these first projects to gain hands-on experience.
New in-house design team for A&P
UK’s A&P Group plans to grow its in-house design team in response to greater demand for the certainty and precision it offers commercial marine clients. Based at A&P Falmouth, the commercial design team comprises five best-infield specialists and delivers projects from initial design through to planning, programming, installation and support. Established in 2010, A&P’s in-house design team has delivered numerous projects for commercial marine clients including Condor Ferries, James Fisher Shipping and ABC Maritime. Some of the most recent projects have included BWM system installations, exhaust system re-routes and replacements, the installation of new crane pedestals and other structural works. Steve Jones, Managing Director for Operations and Site Director at A&P Falmouth said, “The common requirement for all shipowners and operators is to build certainty into their operations. By expanding our design service and the breadth of our expertise, we will
Andrea Sabbion
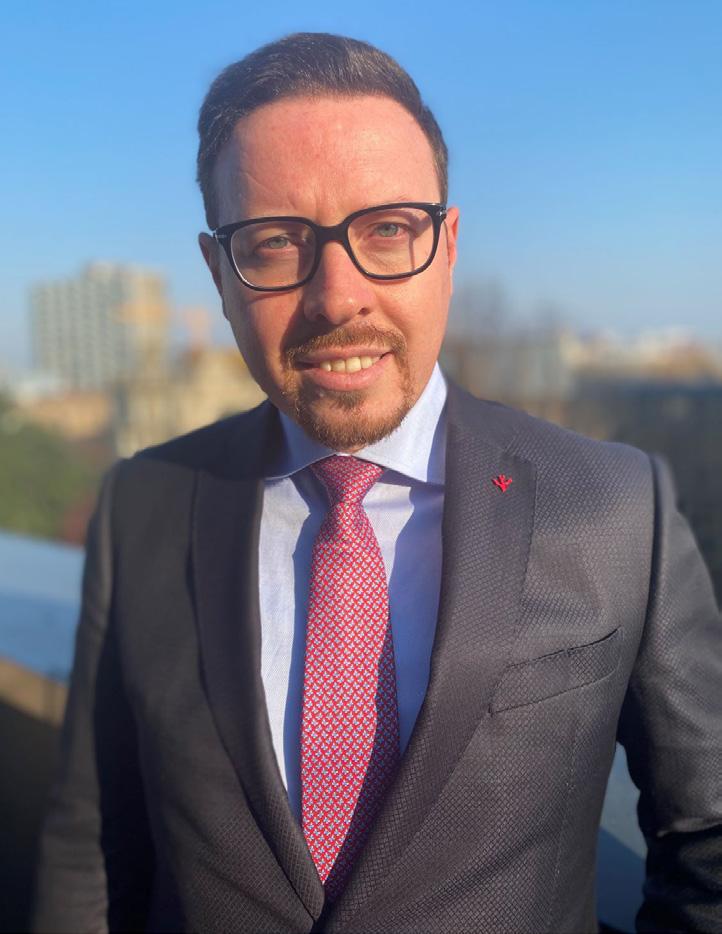
be able to help more commercial customers achieve these goals whilst also capitalising on the in-house skills and knowledge that differentiate our business.” The design team’s specialist skills include RF modelling, stability calculations, naval architecture, 3D scanning and manipulation of production drawings and BWM plans. The team also works with a select number of specialist subcontractors and design houses as projects require. A&P’s design team currently comprises a design manager, two mechanical design engineers, one electrical design engineer and a construction design engineer. All design work is subject to design review and governance checks, including Classification Societies and Flag Authorities. Meanwhile, A&P Falmouth, part of A&P Group, has appointed Andrea Sabbion as its new Business Development Director. A&P Falmouth is one of largest shiprepair complexes in the UK, operating three large graving docks and extensive alongside deep-water berthing providing capacity for vessels up to 100,000 tonnes. It is a renowned centre of excellence for ferries, mobilisation and demobilisation works, jack-ups, pontoons and tankers and provides a complete range of marine repair services from its on-site engineering, electrical, paint and fabrication workshops. Andrea’s remit is to showcase the company’s capabilities globally, and to maintain and further develop A&P Falmouth’s marine portfolio and secure additional maintenance, repair, conversion projects with both local and international clients. Steve Jones said, “I am delighted to welcome Andrea to our team. I am sure he will prove a great asset and will be successful in securing more work for Falmouth and the wider A&P Group.” Andrea was previously Group Sales Manager for Palumbo Shipyards in Monaco and before that he managed the shiprepair, towage and salvage desk at Italy’s main brokerage house, Banchero Costa. Andrea brings operational and commercial expertise to his role within the marine market with a special focus on shiprepair and conversion. Andrea Sabbion, Business Development Director at A&P Falmouth said, “A&P’s breadth of experience and capability makes it well placed to exploit future opportunities in domestic and international markets. I look forward to becoming part of its future success.” A&P Group has also appointed Mark Ellis as Commercial Director for A&P North East. Mark joins A&P North East after 10 years with the Holland’s Heerema Fabrication Group, which specialises in the engineering and fabrication of complex structures for the offshore, oil and gas and energy industries, where he was the Cost and Contracts Manager. Whilst at Heerema, Mark also worked as Senior Commercial Manager on the Cygnus Project, thought to be the largest gas find in the southern North Sea for 25 years, which required the construction of four gas topsides. Another notable project was the construction of the central hub for the Galloper Offshore Wind Farm. Prior to this, Mark worked in senior contract management roles at AMEC and Aker Kvaerner. In his new role, Mark will be responsible for continuing A&P’s commitment to best practice across the estimating and commercial teams, evaluating commercial and contractual risks and pursuing new business. Reporting to Managing Director Keith Henry, Mark will be based at A&P’s Hebburn facility. A&P Group is now using 100% renewable energy across all three of its facilities as it aims to improve its green credentials and meet UK Government targets. A&P Group operates facilities at Tyne, Tees and Falmouth and is committed to improving the sustainability of its services and reducing carbon emissions to ensure it meets UK Government’s legal requirement of bringing all greenhouse gas emissions to net zero by 2050. A&P Group’s decision to buy its energy from Haven Power, a company which only supplies energy from a renewable source, is the latest measure to help achieve this goal.
Many roles for H&W
InfraStrata, the London Stock Exchange-quoted group focused on strategic infrastructure projects and physical asset life-cycle management, issued its Interim Results last week. The company, among other things, owns and operates the assets of Harland & Wolff (H&W) in Belfast, which boasts two of the largest drydocks in Europe and one of only two docks licensed for marine waste disposal in the UK. The H&W site generates revenue from the fabrication, repair, conversion, recycling and support services for ships and assets in the defence, commercial, cruise and energy sectors. Importantly, H&W is one of only three UK shipbuilders suitable for major MOD contract work and has the only dock suitable for major cruise vessels in the UK. In addition to the above, the Company will utilise the 30,000 m 2 of undercover fabrication facilities for the Islandmagee gas storage project in the future. Clive Richardson, Chairman of InfraStrata, said, “We live in unprecedented times. Just like any other business, we are not immune to the challenges caused by the COVID-19 pandemic. Whilst the Company’s management is currently focussed on cash preservation, we have our eyes firmly set on the future. “When the lockdown is lifted, we expect to put in place a series of contracts at H&W. Commodities and people will start moving again in the coming weeks and months. Marine transportation, the only economically viable method of moving goods and people around in large quantities and numbers, respectively, will become even more important as our government seeks to stabilise our economy. As a key strategic infrastructure asset, we are ready to service our clients and bring them up to full operational capacity in support of our government’s economic objectives. “We have opened up H&W to provide six services to five unique sectors (defence, cruise & ferry, commercial, oil & gas and renewables).

Our business model is all-encompassing. The size and flexibility of H&W lends itself to providing the simplest of repair services through to complex offshore fabrication and shipbuilding.
Good start of the year at N-KOM
Over 40 marine and offshore projects have been completed during the first quarter of this year (2020), which is about a 13% increase compared to the same period last year. The yard has delivered more than 10 offshore projects in this quarter, a significant increase of over 50% compared to the same period last year. N-KOM has completed several BWM system installations and major works, as well as scrubber retrofit on several energy tankers, such as: • BWM system installation on-board the 210,000 m 3 Q-Flex LNG tanker Al Bahiya operated by STASCO • BWM system and major works on-board the 320,054 dwt ULCC
Madison Orca operated by Suntech Shipmanagement • BWM system installation on-board the 318,306 dwt ULCC Sea Lynx operated by Pantheon Tankers • Scrubber retrofit on-board the 114,516 dwt tanker Sperchios operated by Pleiades Shipping Agents S.A.
The yard has also carried out a number of projects on-board OSVs operated by Schlumberger, Halul, Trelco and Nakilat-SvitzerWijsmuller, which are still at the yard undergoing repairs and maintenance works. Work includes fabrication and installation of equipment platform, deck modification, fabrication and installation of new vent pipeline, piping renewal, crane load testing, equipment replacements, and other general services. N-KOM also expects the arrival of several oil and gas tankers for general drydocking for routine maintenance, routine drydocking inspections and BWM system installations in the coming months. To date N-KOM has successfully secured four energy vessels (LNG, LPG and crude oil tankers) as well as five offshore support vessels for routine drydocking, between May to August. SORJ
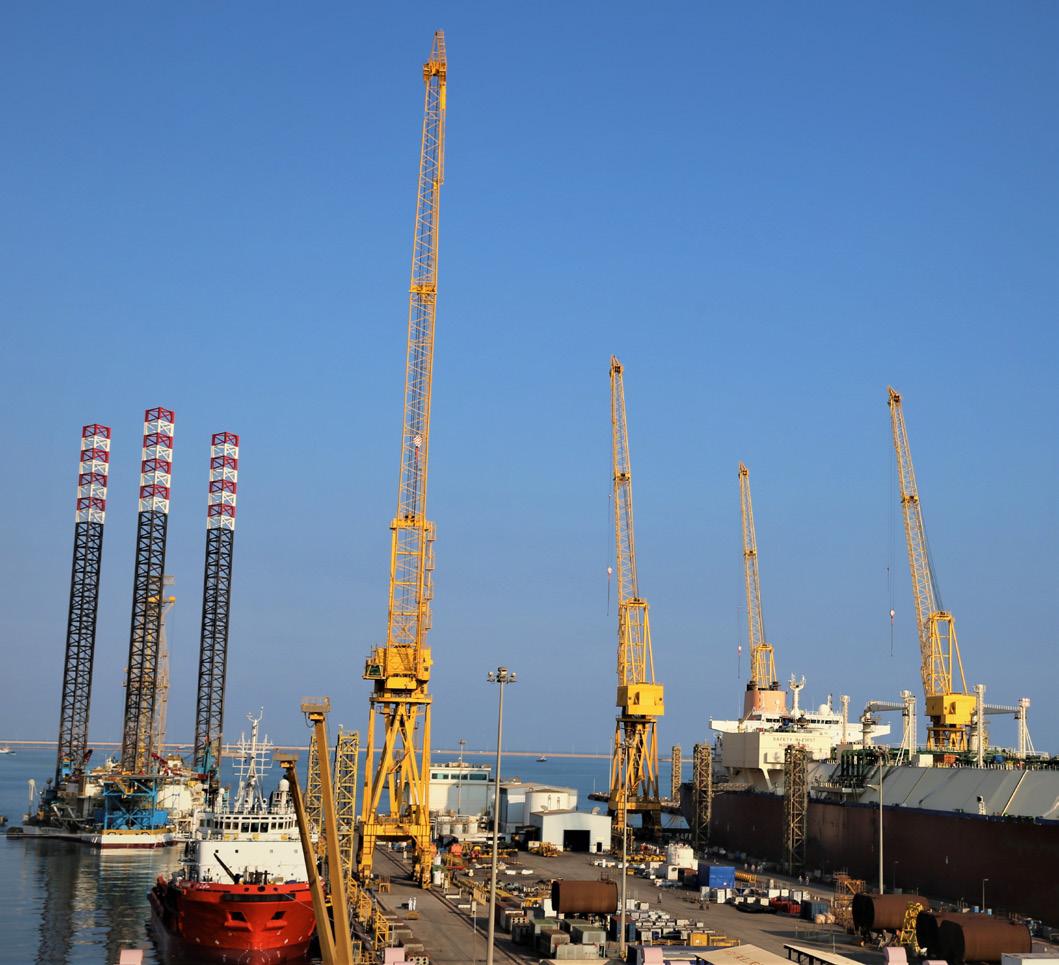
LNG and offshore repairs in N-KOM
years of excellence
Maritime Manpower
SHIPYARD PERSONNEL OIL & ENERGY PERSONNEL RIDING SQUADS CREWING

9 Puskin Street, Constanta, Romania T +40 241 586810 F +40 241 586805
www.nedcon.ro
Follow us on:
MLC 2006 Approved
Certified by Lloyd’s Register