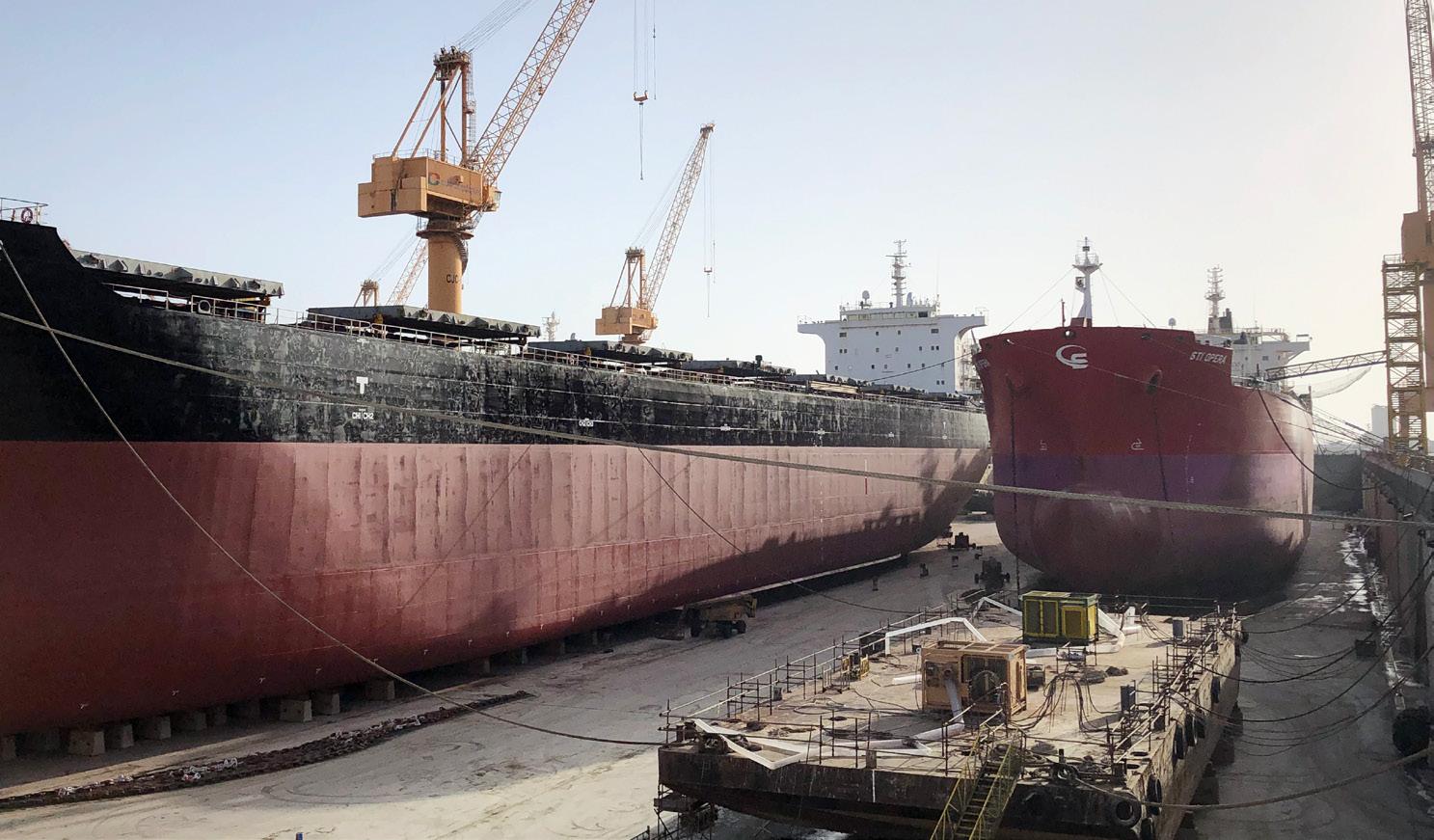
16 minute read
Repairs
General repairs in Oman Drydock Co
ODC continues to work during COCID-19
Advertisement
For many shiprepair yards, the COVID-19 pandemic has been highly problematical. However, during this period, Oman Drydock Co (ODC) did not suspend its operations and has experienced zero COVID-19 cases up until mid-May. Therefore, drydocking operations were not a challenge for shipowners during the period of the pandemic crisis. The challenge of obtaining and supplying critical spare parts was a challenge minimised by well-planned preorder confirmations. ODC implemented numerous preventative measures at all the company’s shipyard locations, which maintained high-level safety conditions within the operations to ensure business continuity during the outbreak, and to protect staff and clients. New shift working systems in production were also implemented to minimise unnecessary contact, and maintain social distancing. ODC has completed several projects involving BWM system installation and scrubber retrofitting - recently four VLOCs fitted with Alfa Laval scrubber systems sailed from the yard during early and mid-May, and the yard is currently working on a BWM system installation and drydocking on-board a MR Tanker. The yard has also carried significant steel work (250-400 tons) for grounding damage, the work carried out on schedule. During 2020, the yard has been consistently busy with some 19-20 ships simultaneously under repair up to April. Redelivery of more
than 850 projects since the yard’s inception and more than 50 ships so far for this year. These ships come from key owners and are of various types, the repair work ranging from medium to large workscope. Three of these projects involved ships from the Greek market - the bottom steel renewal on-board a Suezmax tanker from Avin International, the work involving more than 250 tons, and grounding damage to a VLCC, owned by Eastern Mediterranean, work carried out on the vessel’s bottom line and ballast tanks, involving some 400 tons, and a 20 year-old Suezmax tanker with extensive machinery and electrical repairs, and hull painting ODC has had a good start to the year with an impressive number of scrubber retrofits from key owners such as Oman Shipping and MSC. These have included scrubber retrofits onboard a series of four VLOCs, one VLCC and three containerships. This has enhanced the reputation of the yard being an approved base to carry out such retrofit work with competitive delivery times and quality work. Currently there a further 16 orders for scrubber retrofits, and the yard is confident for more such orders. On the BWM system installation market, ODC has become experienced with more than 25 units already installed for key owners such as Maersk, Norbulk Shipmanagement, Dynacom, etc. - there are more BWM systems to come. Since November last year, ODC has redelivered two LNG tankers, from NYK (UK) and SCI. There are already another two LNG tankers due in the yard with the yard expecting more throughout the year. Currently in the yard some eight commercial ships are under repair - two bulk carriers, one Suezmax tanker, two containerships, one VLOC, one MR Tanker and some barges. More commercial ships are expected prior to the end of the month. Meanwhile, ODC continues to grow by establishing discussions with shipowners in new markets and technical partners. During April, ODC successfully completed scrubber retrofits on-board a series of four 400,000 dwt Valemax ore carriers - Sohar Max, Saham Max, Liwa Max and Shinas Max. The scrubber equipment for all four ships was supplied by Alfa Laval. ODC also completed repairs on-board Norbulk Shipping’s 63,153 dwt bulk carrier Saddler Wells, the workspec including cargo hold blasting, and the installation of a BWM system. Daiichi Chou Marine’s two bulk carriers - 76,807 dwt bulk carrier Nenitia and 83,483 dwt Fidelity, were both in the yard recently for cargo hold blasting and BWM system installations. Recently in the yard were Executive Shipmanagement’s 45,896 dwt product tanker UACC Concensus, in the yard for Special and CAP1 surveys, Tanerska Plovida’s 166,739 dwt tanker Kriti Diamond, in for grounding damage repairs, and two containerships from MSC Shipmanagement, the 33,985 dwt MSC Ishyka and the 29,337 dwt MSC Lana, both ships in for special survey and scrubber installation. ODC has also completed afloat repairs to CMA CGM’s two containerships, the 199,855 dwt CMA CGM Jean Mermoz and the 202,684 dwt CMA CGM Antoine De St Expueri. A spokesman for ODC said, “For May, while we have many orders, we are yet to receive confirmation from owners regarding actual ETAs of the vessels and if personnel will be able to travel to Oman, due to the current COVID-19 crisis. The situation may become clear, closer to the end of April when all national governments take a decision regarding the lock down.”
Damen Sweden wins research vessel conversion
Sweden’s Damen Oskarshamnsvarvet, part of Holland’s Damen Shipyard Group, has won the public tender for a contract to undertake a major life-extension programme on the 514 gt survey and research vessel Ocean Surveyor, owned by SGU, Sweden’s national geological survey agency. The vessel will undergo the life-time

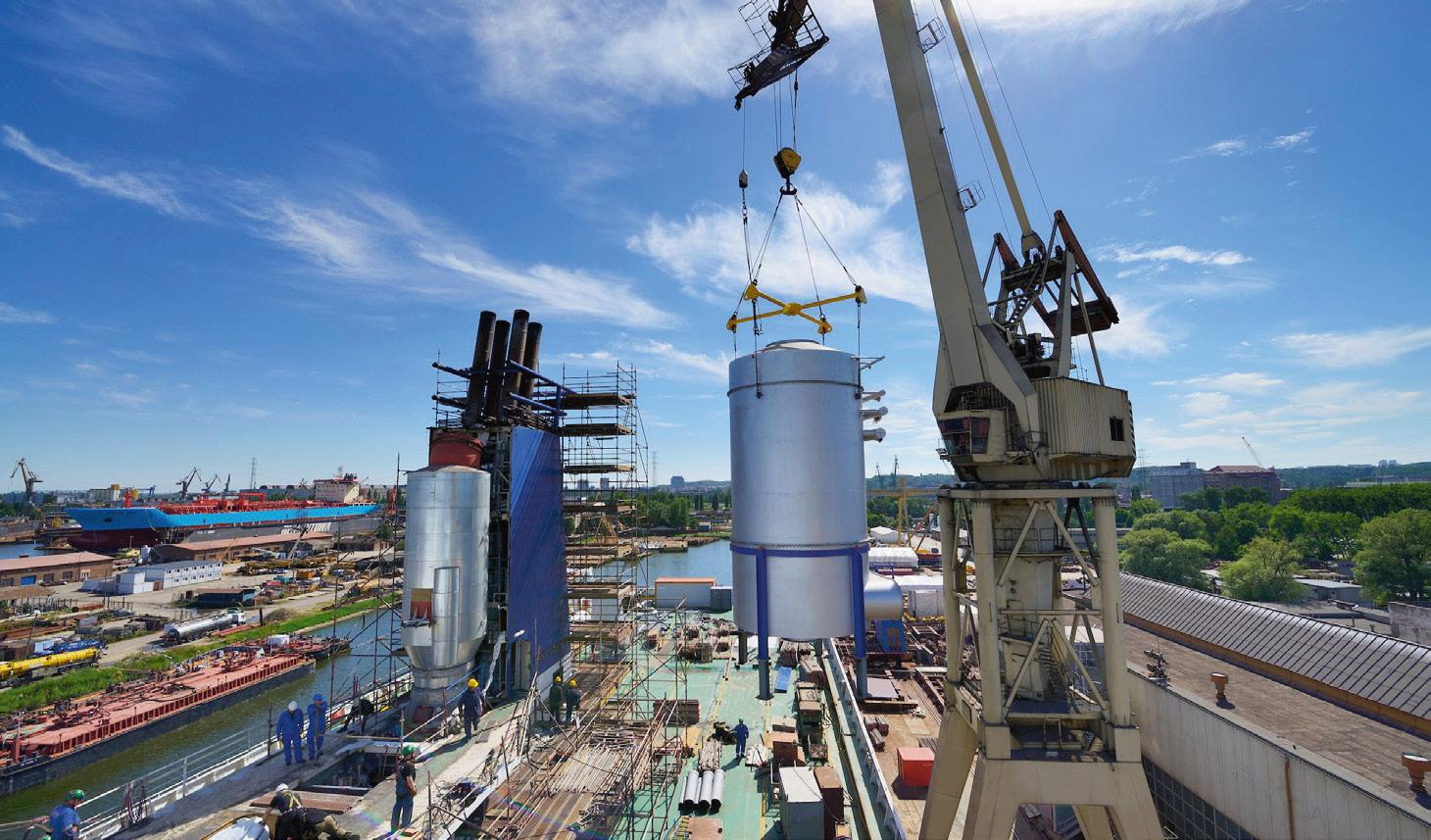
The Ocean Surveyor

extension over the course of 12 months. It will include the replacement of all the machinery, bridge and auxiliary systems including HVAC and a complete overhaul of all remaining equipment. A key aspect of the project will be the conversion of the propulsion and electrical systems from diesel to diesel electric. The overall objective of the year-long programme will be to deliver a modern, low-impact vessel with a good working environment for both the crew and the scientists working on-board and better overall accessibility. “We are happy to let Damen Oskarshamnsvarvet perform the extensive conversion of the vessel and are confident that she will be ready for another 25 years of marine surveying prior to the field season 2021. Ocean Surveyor is a key platform for many marine surveys conducted in Sweden, not only for SGU, but also for other operators hiring the vessel’s unique surveying facilities,” said Björn Bergman, operations manager at SGU. Built 1984 in Norway, the Ocean Surveyor is a twin hull, multi-purpose, survey and ROV support vessel constructed using Kevlar / FRP composite for operations mainly in coastal waters. With dimensions of 38 m long and 12 m wide she has accommodation for 15 personnel across 12 cabins and is equipped with DPS as well as various fixed hydro-acoustic measuring systems. The main deck is fitted with winches, cranes, an aft frame and a moon pool for deploying samplers and underwater cameras. There are two laboratories on-board - a wet lab for sediment and environmental sample analysis, and a space with a gamma spectrometer and sediment X-ray for the detailed study of samples. “We are delighted to have won this contract,” said Flip van der Waal, Managing Director at Damen Oskarshamnsvarvet Sweden. “The tender process was rigorous, requiring a lot of research and pre-engineering, and now that we have been awarded the project we are responsible for the entire design scope and the procurement as laid down by the SGU. In many ways it’s not so different from a newbuild. We are very confident that our capabilities and facilities are perfectly suited to this project – including our main hall where we will carry out the work. This covered environment is the ideal location to conduct work on a composite vessel such as this. We look forward to getting started.” Work will begin on the vessel on April 6 th 2020 and is scheduled for completion by end of March 2021.
Metalships continues with scrubber and BWM projects
As the COVID-19 outbreak continues, Spain being one of the hardest hit, Metalships, Viga, is setting up as many measures as needed to secure the safety of its clients and workers. So far, the yard’s repair activities continue normally with several projects on-going. These include Reederei Eicke’s 11,424 dwt containership Kornett, which recently underwent the installation of scrubbers plus standard drydocking works. Following the completion of this project, her sistership Laura Ann entered the yard to make the same installation and drydocking works plus steel renewals. According to Metalships’ Pablo de Celis and the shipowner’s superintendent, “The newly-installed ‘Open Loop’ Hybrid Ready SOx scrubber supplied by Finland’s Langh-Tech onboard the Kornett, is the first in-line-scrubber installed on a Sietas-built Type 168 vessel. Due to the slim outline of the in-line scrubber, the influence on measurements of the vessel (just below 10,000 gt) is at its lowest possible. The optimised system integration was planned by Hamburg’s HeavyLift@Sea GmbH, which has experience with scrubber conversions as well as Sietas-built ships. The Hamburg based pipe builder, Knaack & Jahn, delivered the pipework and is supervising the complex pipe installation on-board the vessel. “The Kornett gets the modern hybridscrubber-system as the first stage of extension. All conversion work was prepared by Metalships & Docks before the vessel arrived at the Shipyard, so that the time at the Shipyard is at its shortest possible.” “We chose Metalships & Docks because of its reliability and experience in these types of projects. This first project is going on time and the professionalism of yard’s staff makes us feel optimistic for the second ship, Laura Ann. We, together with shipyard, have found some ideas, which we all hope will work in order to deliver the second ship a bit faster.” The same work has now been completed on-board the sistership Laura Ann. According to Pablo de Celis, “The manoeuvre of installing the scrubber has been a complete success and we are pleased to start the last stage of this challenging project. Recently, we also received one more ship
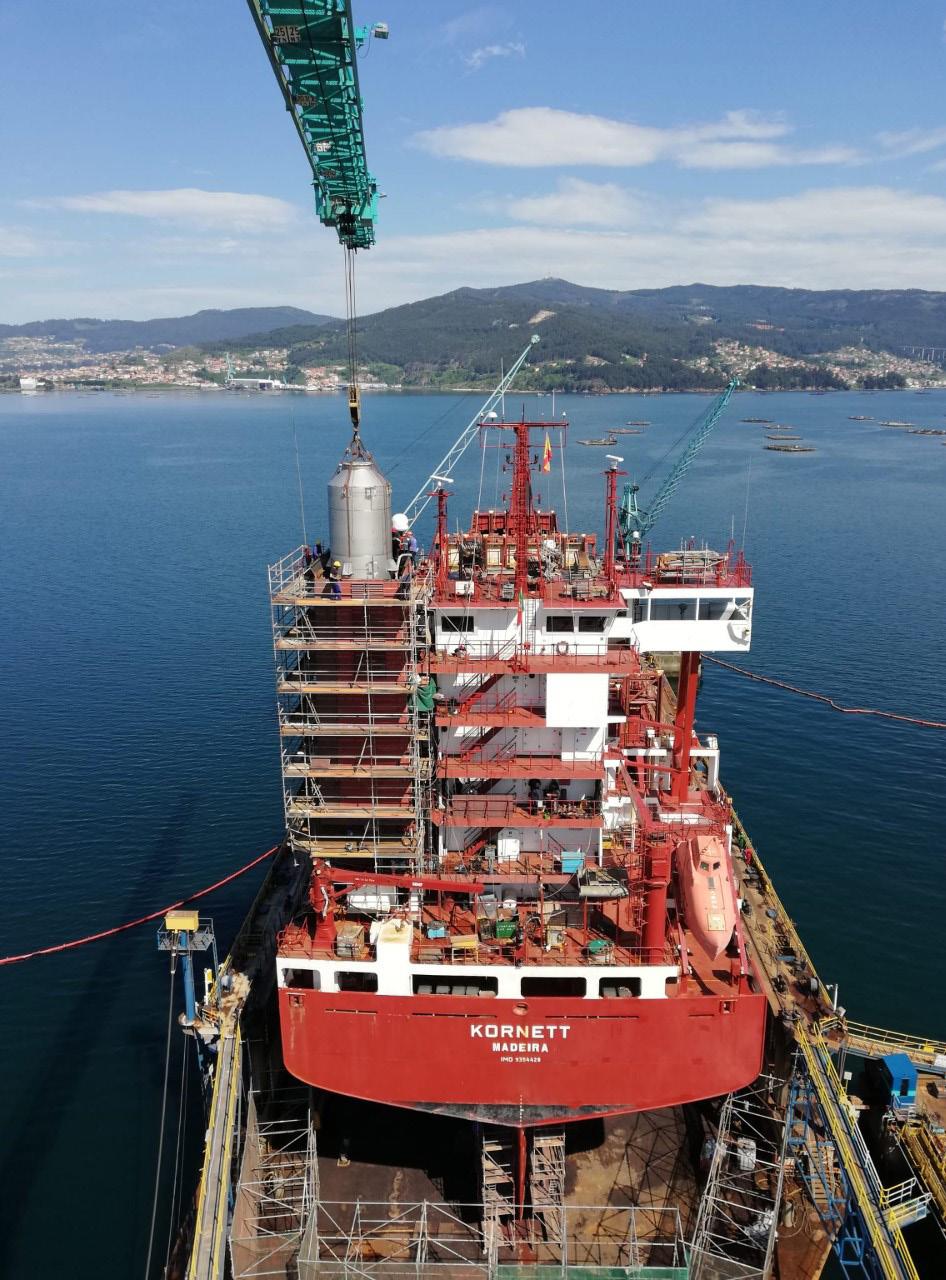
The scrubber being lowered on-board the Kornett
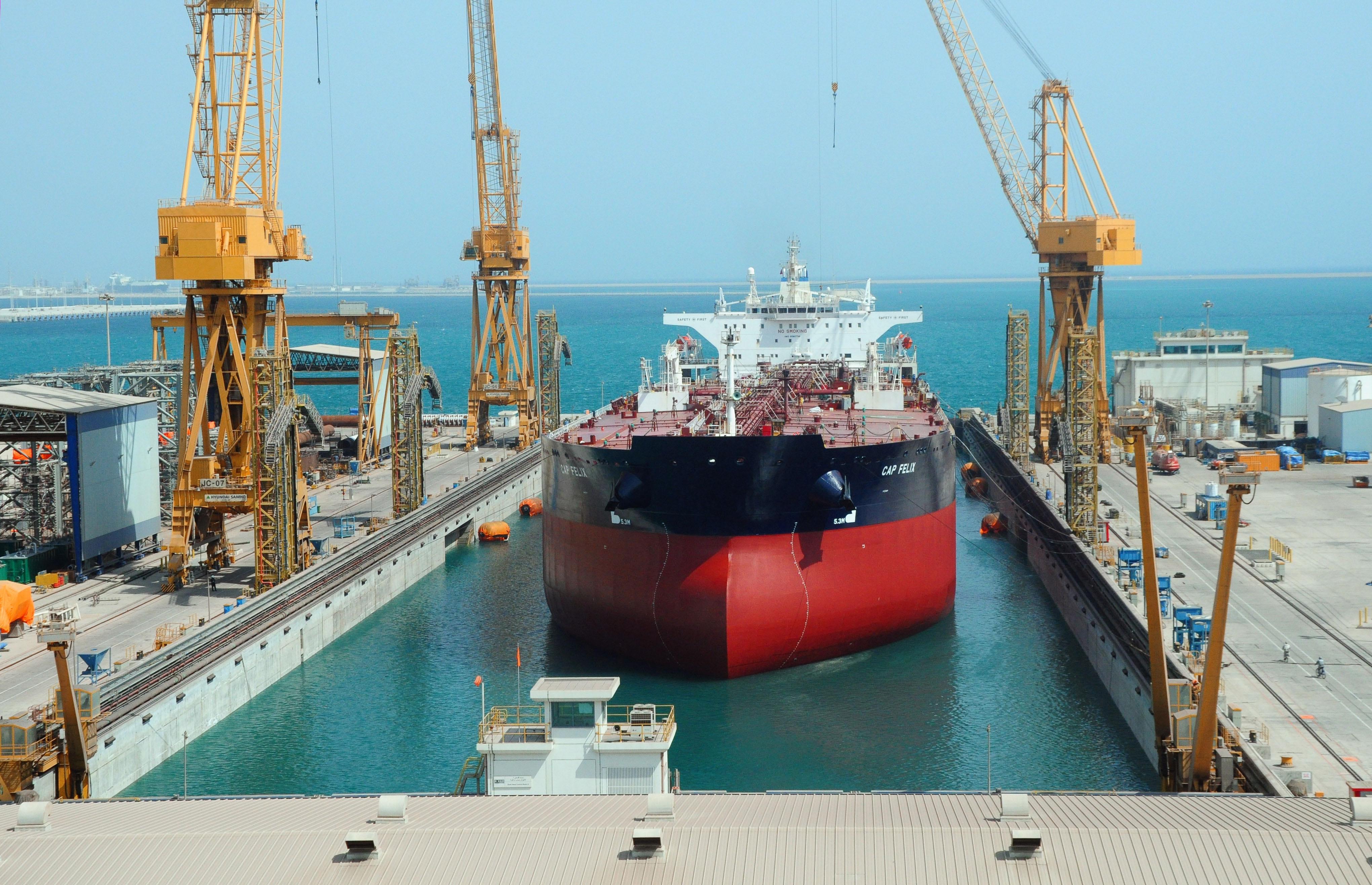
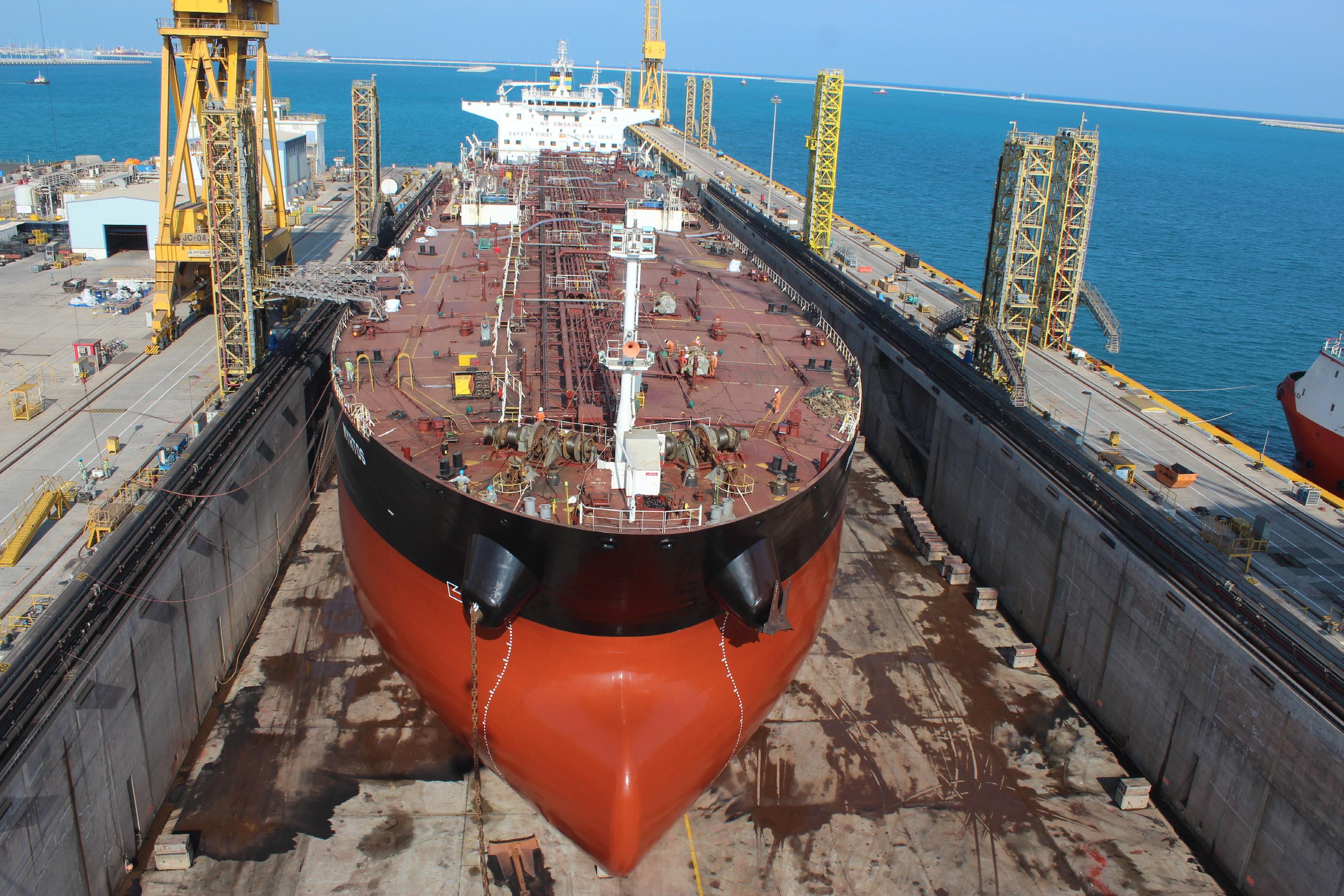
from our regular client USC Barnkrug, for installation of BWM system on-board the 4,155 dwt general cargo vessel Daroja, which will take place in May. The ship had already been in the yard during 2018. It’s worth mentioning that we have seen a significant growth of our market positioning in Germany, which lead us to sign several valuable contracts for BWM system and scrubber installations. As a result, we do expect similar projects in second half of the year.”
Conversion and general repair work at Remontowa
In Poland’s Remontowa Shiprepair Yard, Gdansk during March 2020, the mobilisation of the 4,801 gt cable layer Ile d’Ouessant, commissioned by Luis Dreyfus Armateurs, was completed. The project was to change the configuration and equipment of the ship, which entered the yard as a Platform Support Vessel (PSV) and adapting her to perform work as a cable layer - to lay and repair submarine telecommunication cables. According to Remontowa’s management team, “It was prestigious, very interesting work and one of the most technically advanced projects carried out at Remontowa. During the winter period, the ship also underwent drydocking and maintenance repairs. Exactly a year ago, during March 2019, the 13,978 gt Ile de Batz underwent a similar mobilisation
The Yeoman Bridge in Remontowa project in Remontowa. Remontowa also recently completed repairs on-board Odfjell’s 1997-built, 17,460 dwt chemical tanker Bow Oceanic. She underwent main engine overhaul as well as the large number of electric motors and the shaft generator inspections. She also had extensive steel renewals and pipeline replacements. The repair works also involved a number of minor repairs in the ballast and cargo tanks. Chemical tankers of this shipowner have systematically used Remontowa in recent years. These include Bow Fagus, Bow Atlantic, Bow Aratu, Bow Star, Bow Clipper, Bow Faith, Bow Guardian, Bow Gallant, Bow Pioneer and Bow Summer. DFDS Seaways’ 26,141 gt, 2007-built ro/ pax Athena Seaways has, once again, called at Poland’s Remontowa for repair work. The previous drydocking was exactly three years ago. This time, she underwent maintenance work on the hull, superstructure and funnel, as well as on car decks and in the fresh water tanks. The speed controllers and oil pump overhaul had been also processed. The two general cargo vessels from Wilson Shipmanagement were recently in Remontowa for repairs and maintenance – the 4,338 dwt Wilson Holla and the 2,516 dwt Wilson Onega, a new vessel in the Norwegian shipowner’s fleet. Both ships underwent hull maintenance and steel and pipe work. All nine ballast tanks were inspected on-board the Wilson Holla, with the Wilson Onega undergoing main engine, auxiliary engines and reduction gear overhaul. Four giant, over 200 m long vessels
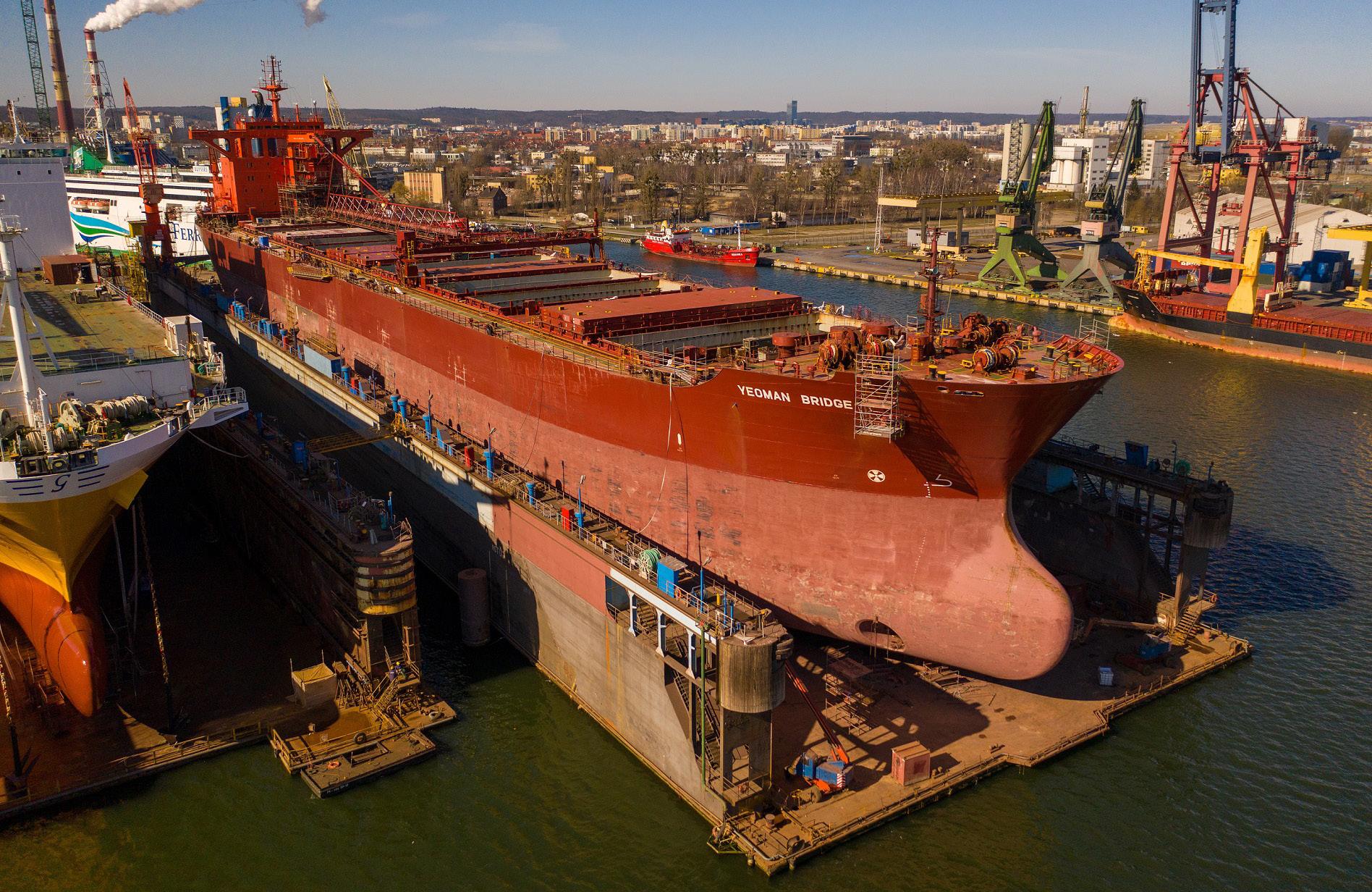
were repaired during the first half of April in Poland’s Remontowa – Tsakos Columbia Shipmanagement’s 39,382 dwt containership Irenes Remedy, Grimladi’s 47,365 gt car carrier Grande Marocco, SMT Shipping’s 96,772 dwt self-discharging bulk carrier Yeoman Bridge and Yang Ming Marine’s 57,320 dwt containership YM Express. The YM Express is one of the largest ships that has ever entered the inner port of Gdansk. Similarly to the two previouis vessels owned by the Yang Ming Marine Transport, the biggest and most important challenge during the repair was the main engine overhaul due to its sheer size. The engine cylinder head onboard the vessel weighed 11 tonnes and had a diameter of one piston of 1 m. She is the third containership of this shipowner repaired at Remontowa SA in the last few months, following the YM Essence and the YM Enlightenment. Remontowa has also just completed repairs of Boskalis’ 2,000 kW 1999-built backhoe dredger Nordic Giant. The scope of work onboard this vessel comprised hull maintenance, painting and dredger equipment repairs. She is 55 m long, 17 m wide and her moulded depth is 4 m. She can dredge up 23 m in depth. Immediately after the repairs she left the shipyard, she was towed to Sweden for a project related to laying the power cable on the bottom of the sea. Following succesful repairs on-board the 49,999 dwt chemical tanker Gerakas, Singapore’s World Tankers Management chose Remontowa for another of its fleet – the Klara for repairs and the installation of an the Erma First BWM system. Another major task of this repair was the Panama Canal modification, a change in the mooring system, which aims to adapt the ship to the new sailing conditions through the Panama Canal. The ship also underwent standard dock maintenance and inspection The yard has also carried out repairs to the Yeoman Bridge - one of the world’s largest selfunloading bulk carriers, following successful repairs to her sistership Yeoman Bontrup. This time the Yeoman Bridge called at Remontowa for class renewal, BWM system installation and comprehensive preparation for the scrubber assembly. Also recently in the yard was Eco Shipping’s ice-class 17,300 dwt general cargo vessel MYS Zhelaniya. After the bulb replacement the vessel was reclassified to correspond to the ice class IA. Hence the versatility of the ship has increased, she has gained the possibility of safe
icebreaker pilotage through the Northern Sea Route.
Stena Lagan arrives at Sedef Shipyard
Stena Line’s ro/pax ferry Stena Lagan arrived at Turkey’s Sedef Shipyard in Tuzla on April 18 th to begin her lengthening and passenger accommodation upgrade. The 27,510 gt 2005-built ferry will be lengthened by the insertion of a 36 m mid-body section, which will increase the vessel freight capacity from 2,238 lanemetres to 2,875 lanemetres and car capacity on the dedicated car deck from 170 to 280 cars. The vessel’s stern ramps will be upgraded from wire operation to hydraulic mode. At the same time Stena Lagan will be fitted with an additional 74 new passenger cabins, taking the total onboard to 194. Passenger capacity, meanwhile, will remain the same at 970. Following completion of this conversion and upgrade Stena Lagan will be a dedicated double-deck drive through ferry and will be deployed on a new, yet to be announced, Stena route, almost certainly in the Baltic. The same work package will be carried out on her sistership Stena Mersey in the last quarter of 2020. Both Stena Lagan and Stena Mersey have been operating on Stena’s Belfast-Liverpool (Birkenhead) route. Work underway at A&P UK’s A&P Group has deployed a strict programme of COVID-19 measures to ensure it can maintain its support to the maritime community as it emerges from the pandemic. Over this period, A&P has deployed a number of stringent measures at all three of its UK facilities, allowing them to remain operational and continue essential ship repair and maintenance works for the MoD, Royal Fleet Auxiliary and Seaborne asset community. David McGinley, CEO of Cammell Laird Ship Repairers and Shipbuilders and Atlantic & Peninsula Marine Services, owners of A&P, believes the industry must give customers additional reassurances that rigorous COVID-19 measures are in place, ahead of restrictions being lifted. “A&P Group’s number one priority has always been to safeguard the safety of our staff, customers and subcontractors but in the face of the unprecedented challenge of COVID-19, it has required even more rigorous checks and practices to ensure our vital work can continue. The alignment of the whole of the maritime industry will be necessary if we are to minimise the long-term impact of COVID-19 and ensure we can meet the needs of our customers.” During the pandemic, A&P Group has continued to deliver complex, large scale projects with minimum disruption to labour. A&P Falmouth has continued to provide critical support to the Royal Navy and Royal Fleet Auxiliary, with the workforce commencing a major refit to RFA Mounts Bay and delivering essential repairs to HMS Scott. At A&P Tyne, the team has completed the installation of cable repair equipment to Prysmian’s North Sea Giant at A&P Tyne, which is essential to the safe and continuous power of the National Grid. David added, “At A&P, our rigorous risk assessments, preplanning and ongoing communication with customers and ship staff have ensured we can limit the risk of the virus entering our facilities and minimum disruption to vessels as they arrive at our sites. Customers can be assured that they face minimum disruption when visiting our facilities as we’ve found effective ways to safeguard our workforce and customers whilst continuing to deliver The dredger Arco Beck in A&P Tees essential projects.” Projects delivered during the pandemic have included the upgrade of HMS Tamar by A&P Falmouth, as well as the full classification five yearly refit of Tamar Crossing’s Lyhner II. Falmouth Docks and Engineering Company, part of A&P Group, has provided multiple crew transfer services to Stena Drilling’s Stena Ice Max. It has supported the port calls of the Fugro Scout, Fugro Searcher, Alp Ace and the Komander Susan and continues to support ships at anchor and in lay-up with stores and fresh water using its afloat services. A&P Tyne has also carried out vital mobilisation work for Global Marine’s Normand Clipper and its on-site fabrication division has continued its work on Dreadnought, Boat 1 and Boat 2 on behalf of BAE Systems. A&P Tees has completed vital maintenance and repairs for suction dredger Arco Beck, which included urgent stern seal renewals. Intermediate Class surveys were carried out on the Ocean Falcon and Galway Fisher. A&P Group’s HSEQ track record has been commended with two awards from RoSPA in recent months. A&P Group has received the RoSPA Commended in the Engineering Services Sector Health and Safety Award and a RoSPA Gold Award in recognition of its work to ensure staff, clients and supply chain get home safely to their families at the end of every

working day. SORJ