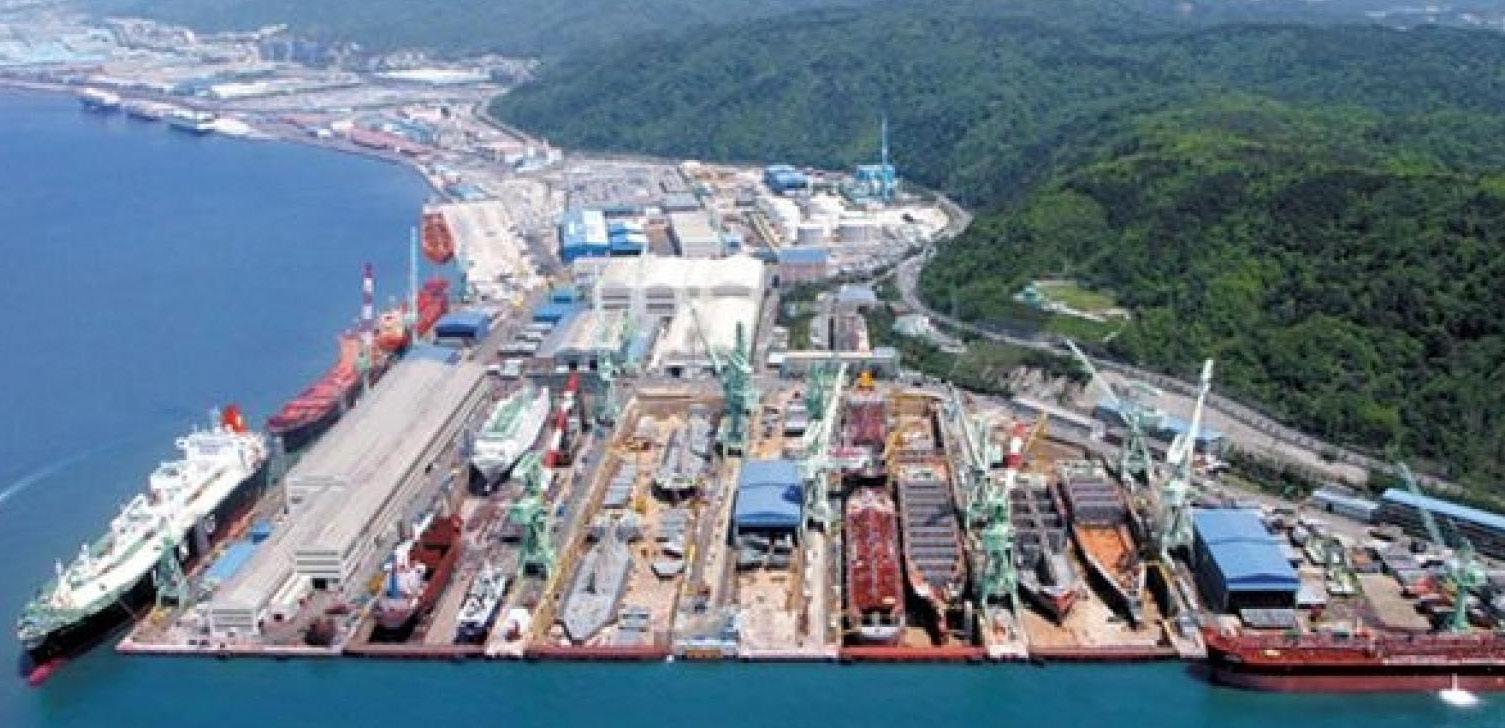
8 minute read
Paints & Coatings
South Korea’s Hyundai Mipo Dockyard
WBT coating from Chugoku
Advertisement
Following many years of extensive prototype trials in field tests, Japan’s Chugoku Marine Paints (CMP), is ready to launch a new solventfree epoxy coating that can be applied to water ballast tanks (WBT) with standard application equipment that meets new South Korean regulations under the Atmospheric Environment Conservation Act for the management of volatile organic compounds (VOCs). CMP has provided solvent-free epoxy coatings for the drinking water tanks of commercial ships for over 20 years as a standard product for most of the shipyards world-wide. However, solvent-free products require special equipment and the warming of the paints due to high viscosity in a cold temperature. Therefore, their use has been limited to specific areas due to difficulties of treatment. To overcome existing limitations in the application of solvent-free coatings in WBTs, due to the severe application conditions and limited revision margin in performance standard for protective coatings (PSPC) regulations, South Korea’s Hyundai Mipo Dockyard (HMD) and CMP have found the best solution to coat WBTs with a solvent-free epoxy coating that has matched quality control and best performance after delivery without failure. CMP’s new solvent-free epoxy coating Bannoh 5000 will be applied to the WBTs of three MR tankers to be built in HMD from April 2020. This will be the first application of a solventfree coating to a WBT in the world. Through the use of this new product, the shipyard could reduce solvent emissions by up to 90% for WBT. This makes Bannoh 5000 indispensable for South Korean shipyards for reducing total VOC emissions while maintaining current working processes. Additionally, Bannoh 5000 will be the first protective coating for ships that is applicable for all areas as a solvent-free multipurpose primer. CMP’s R&D director, Hideyuki Tanaka, said, “This new generation coating will catalyse a paradigm shift, changing the conventional approaches of protective coatings in the marine newbuilding market. Throughout this success, CMP’s solvent-free epoxy will be standardised for ballast water tanks as well as for the general areas of ships to protect the global environment in the future.”
Corrosion problem can be solved
According to a spokesman for Subsea Industries, suppliers of Ecospeed, “We are so used to corrosion on ships that no-one raises an eyebrow at the rust-stained hulls in any port or dock. It is, apparently, considered to be the way of things. It is true that steel will rust. But with the knowledge and resources available, we have long passed the point when we should have recognised that this is a problem, and solved it. “Corrosion on ships is rarely recognised as a failure of the coating, but that is precisely what it is. The first job of a hull coating is to prevent the gradual weakening and destruction of marine assets that is caused by corrosion. It remains a massive problem for shipping despite coating repairs every few years, eating up valuable days in drydock. Not only that, but current coating compounds also leak a million tonnes of toxic material into our oceans every year. “Corrosion is not some unavoidable fact of life. The basics of the subject have been well known for centuries, but they are worth reiterating. The iron in a steel hull is, effectively, trying to return to the state in which it was taken as an oxidised ore. Three things are needed for rust to form - metal, water, and oxygen. Energy, the galvanic difference between metals, stimulates the process, and impurities in the metal, seawater, water vapour, acids, salts, carbon dioxide and stresses hasten it. “While cathodic protection slows the corrosion on a ship, total prevention is only achieved by preventing metal, water and oxygen from coming into contact with each other. That is the primary job of a coating. The problem is simply that most coatings fail poorly in that task. “One reason for their failure is the permeability of zinc primers, epoxies and anti-fouling coatings usually used. Water can get through and behind the layers of coating where it can start the corrosion process while accelerating it by causing coating delamination. This is the sequence of coating degradation which opens the door for further corrosion. “A second reason is the use of heavy metals in coating systems such as copper. These have a high galvanic differential with the steel of the hull. In practice we see copper-based coatings
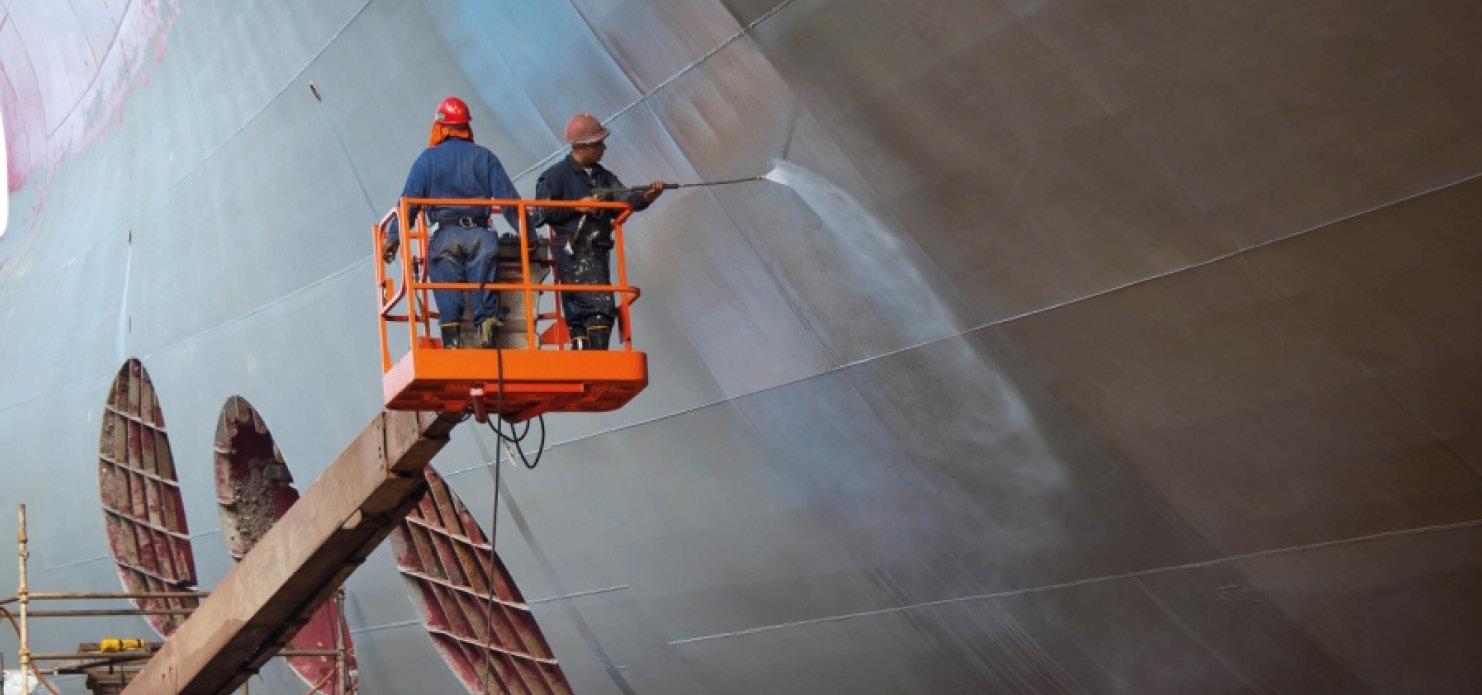
degrade very quickly – their difference in potential is the highest we encounter on ships. The fact that zinc, epoxy and anti-fouling, all of which have different surface tensions, are used together - further aggravates the problem. “Permeability, different surface tensions, poor adhesion and heavy metals are the four main factors that lead to an inferior protection on the ship hull. It is not difficult to see that if a coating has no heavy metal content and therefore can avoid potential differential, is impermeable to water and achieves superior adhesion, the problem is solved. If the steel hull is isolated from its surroundings, then galvanic activity and corrosion are cancelled. “Observation over 20 years on hundreds of ships protected with our coating systems, reveals a distinct absence of hull corrosion on any of them. We do not find corrosion on these hulls. With our glass-flake coating systems we have the solution. Their superior adhesion, impermeability and toughness fully isolate the steel hull. Even heavy corrosive environments in port or in seawater fail to touch the anodes or the steel surface of the hull. In fact, anodes become superfluous on an Ecospeed hull. “Environmentally our coatings are a vital solution because they contain no heavy metals, no zinc and no pesticides or other biocides. Extremely high concentrations of these elements are already found in the sediments around ports, estuaries and even far out at sea. It is clear that using them on ship hulls is not sustainable. “The subject of hull fouling is dealt with previously – but it should be mentioned here that anti-fouling coatings have already caused one international marine catastrophe with the extensive use of TBT, and are creating further catastrophes if their use is continued. The attachment of marine organisms to ship hulls seems to be little affected by the currently available anti-fouling materials, but the marine environment suffers severely from their accumulating toxicity. “Simple mechanical removal of these organisms from a hard, non-toxic surface is the obvious and most workable solution, provided the coating is designed to withstand this. We have seen more than 20,000 ships over the last 50 years – after some time they all have corroded, rough, degraded and inefficient hulls. “An amazing discovery we frequently make is that, on inspection of ships coated with our systems, we never see corrosion of any significance, even when there has been small impact damage. Not after two years, not after five years, not even after ten years. This proves that with an inert coating there is no influence on the steel, even when exposed to seawater. The conclusion is simple - the majority of the coating systems in general use today do not protect the hull sufficiently. They should be replaced with coatings that can do the job.”
Jotun to use Selektope
Norway’s Jotun will use Selektope in two anti-fouling products targeting customers within commercial shipping where increased protection against barnacle fouling is needed for idle ships during the outfitting period. I-Tech and Jotun are yet to formalise an agreement that binds orders for the commercialisation. Therefore, the company can not issue any statement regarding volumes and financial impact. Jotun will use I-Tech’s anti-fouling active agent Selektope in the products SeaQuantum Pro Ace and SeaForce Active Ace. These are the first products launched by Jotun that contain Selektope. Philip Chaabane, CEO, I-Tech, says, “Jotun’s choice to use Selektope is yet more evidence of our product’s prominent features and efficiency. I’m pleased to recognise that Jotun has introduced Selektope in two different product families bringing extreme performance for repelling barnacles from the hull and creating new opportunities for a range of different vessels at the new build phase and subsequent operations.” With this product introduction, Jotun becomes the third official customer to integrate Selektope as a key ingredient into advanced and fuel saving anti-fouling paints available to globally trading vessels. Previous communication from I-Tech states that there is yet another major, but non-disclosed, manufacturer of marine paints working through the final development steps prior to product commercialisation. Selektope is an organic, metal-free antifouling active agent added to marine coatings to prevent barnacles from settling on the coated surface by temporarily activating their swimming behaviour with non-fatal effect. This unique antifouling active agent delivers superior efficiency in extremely low concentrations (approximately 0.1% for each wet weight of paint - only a few grams/litre of paint). IMO has committed to reducing emissions from commercial shipping by 50% by 2050, compared to 2008 levels. Reduced hull biofouling will be one of the key factors required to achieve this target since even small amounts of bio-fouling on the hull can contribute to a significant increase in fuel consumption. Climate change will also lead to increased sea temperatures which in turn will accelerate bio-fouling risk. “Anti-fouling paints will be one of the key technologies required to achieve IMO’s 2050 CO 2 emission reduction targets. Selektope, with its high efficacy, precision and reduced environmental impact, will play a vital role in solving this challenge for the shipping industry,” Philip Chaabane concludes.
New Group Vice President at Hempel
There have been some management changes at Denmark’s Hempel - current Group Vice President for Hempel South & East Asia, Pernille Lind Olsen, becomes new Group Vice President for Hempel Europe & Africa starting on July 1 st 2020. At the same time, current Finance Director for Hempel Middle East Jonathan Mercer will take over Pernille Lind Olsen’s position as Group Vice President for Hempel South & East Asia. Pernille Lind Olsen has been with Hempel since November 2013. Since then, she has held positions as Group Product Director, Group Product & Portfolio Director and, most recently, Group Vice President for South & East Asia. Jonathan and Pernille become members of Hempel’s Operational Management Board. SORJ
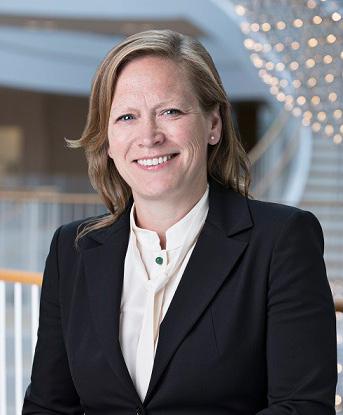
Pernille Lind Olsen