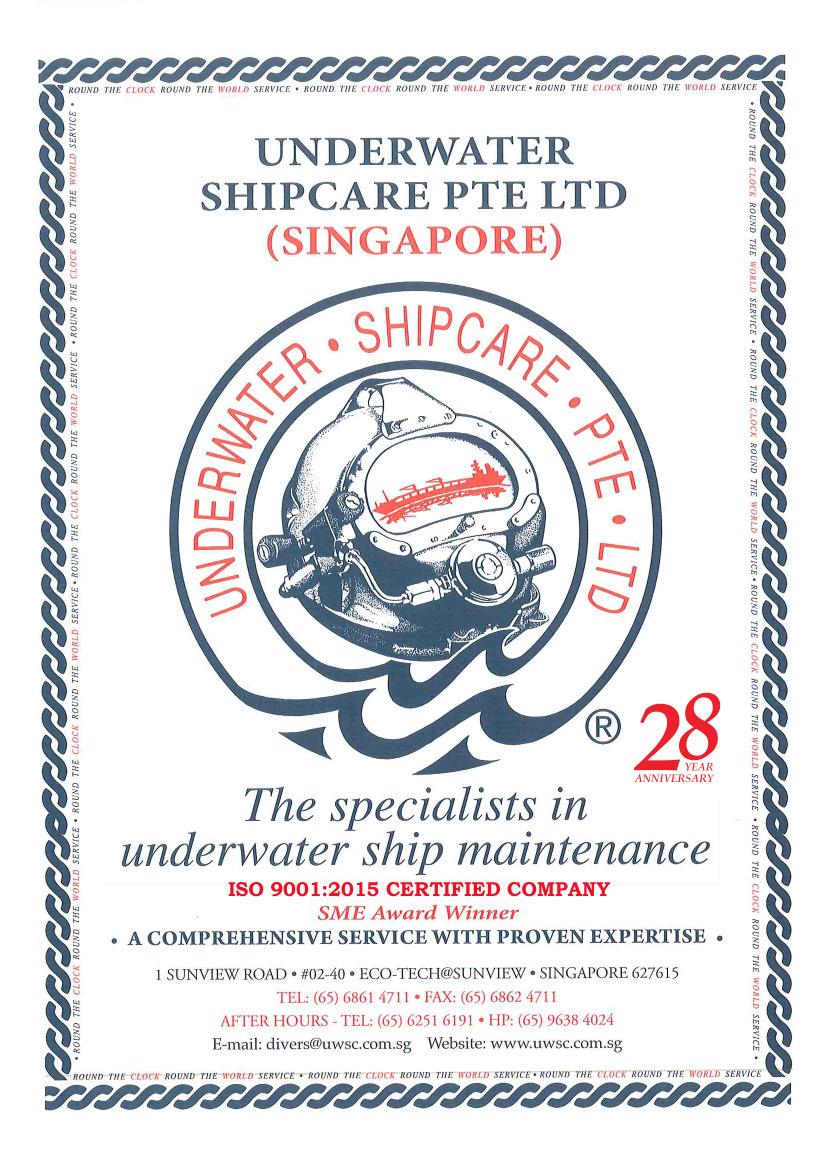
14 minute read
Underwater Repairs
HullWiper expands into Sri Lanka and Guinea
Dubai’s HullWiper has formed a partnership with World Subsea Services to bring sustainable and affordable hull cleaning solutions to vessels calling at the Port of Colombo in Sri Lanka. Strategically located in the Indian Ocean, Colombo Port is one of the country’s largest and busiest ports, particularly for container vessels.
Advertisement
“The shipping industry has moved into an era of performing eco-conscious operations, and with this comes the responsibility of ship owners and operators to use green solutions,” says Lalindu Jayawickrama, World Subsea Services CEO. “We are preparing now for the inevitable possibility that the option to clean hulls using traditional methods may become extremely limited by offering a service that will not disrupt business continuity for vessels.”
World Subsea Services joins HullWiper’s expanding family of partners around the world operating under their lease agreement introduced in 2017. The global network of hubs provides cost-effective, safe underwater hull cleaning solutions that protect both vessel’s expensive anti-fouling coatings and the marine ecosystem. HullWiper’s ROV is 100% environmentally friendly and uses adjustable seawater jets as the cleaning medium instead of brushes or abrasives, to minimise the risk of damage to coatings. Removing fouling from vessels’ hulls results in optimal performance, energy efficiency and reduced CO2 emissions, and avoids the expense of re-coating in case of damage. No divers are used, so there is no risk to human life.
“With our industry focusing more and more on efficient, sustainable operations, HullWiper’s cleaning solution is an effective tool to improve a vessel’s fuel economy and carbon footprint,” says Simon Doran, HullWiper MD. “Colombo’s strategic location in the Indian Ocean makes it a key hub, with vessels sailing to and from Europe, East Africa, the Persian Gulf, East Asia and elsewhere in South Asia. Having access to advanced hull cleaning technology services at this key port will be beneficial both for ship owners’ and operators’ bottom lines, and the marine environment.”
Meanwhile, HullWiper and Guinea’s Agemar have signed a lease agreement to meet the growing demand for hull cleaning solutions for vessels calling in Guinea. Agemar Guinea is part of global maritime consultancy and maritime logistics solutions provider, the Agemar Group. It is the latest addition to HullWiper’s growing family of partners around the world operating under their leasing programme introduced in 2017. The partnership supports the Guinean government’s goal to bring environmentally friendly solutions and operations into Guinean waters and to shipping in general.
Alessandro Di Battista, Agemar Guinea’s General Manager, says, “Guinea’s close proximity to major shipping lines makes this operational hub in West Africa an ideal strategic
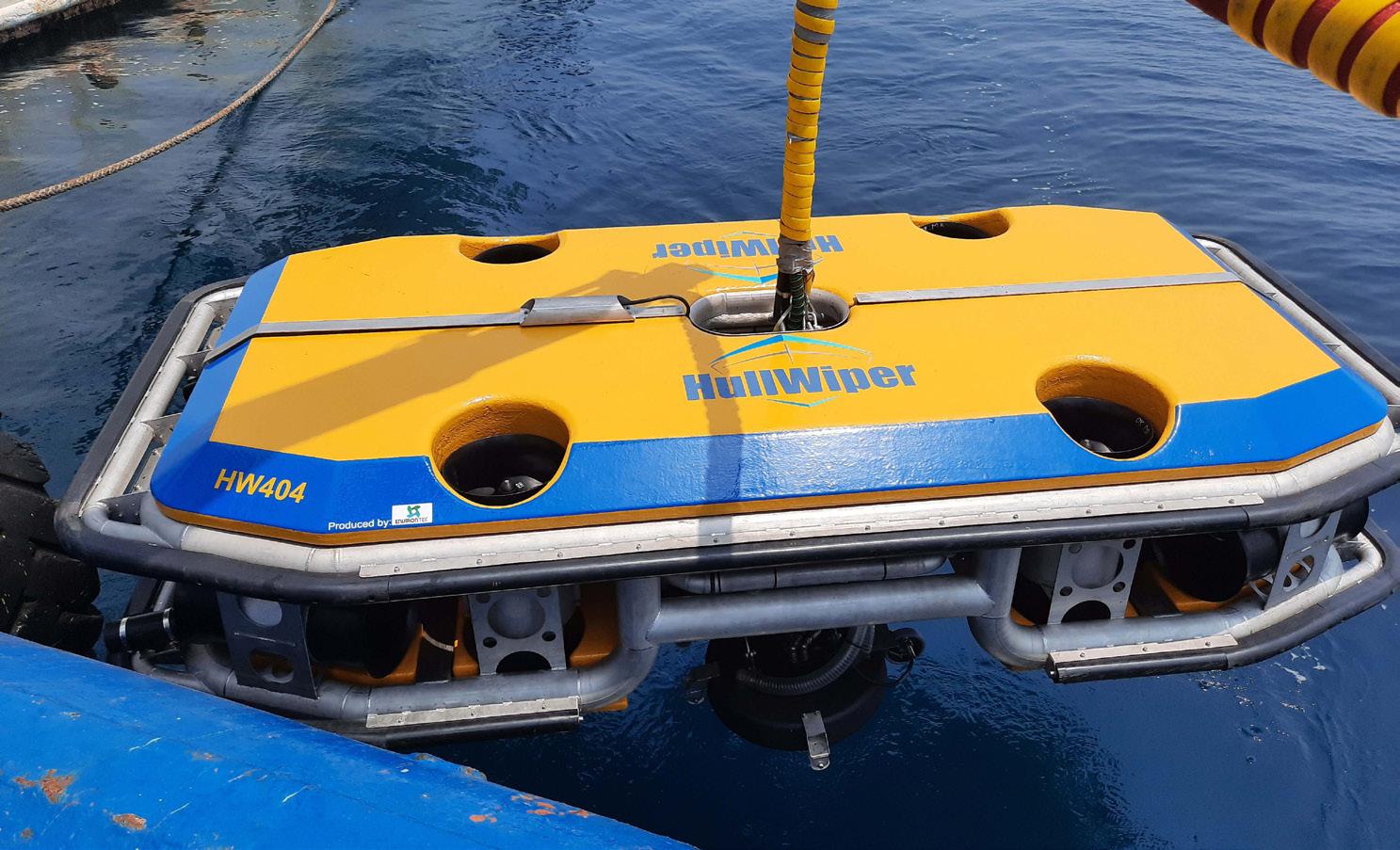
The HullWiper system
location for vessels to minimise on downtime deviations within the busy waterways as cleaning can be done day or night, in most weather conditions and whilst cargo or bunker fuel operations are underway or on a laden voyage. We have partnered with the industry leader in innovative eco hull cleaning solutions, with the environmental aspect being a core focus.”
HullWiper’s cutting-edge Remotely Operated Vehicle (ROV) technology carries the approval of several local port authorities including Merchant Shipping, Guinean Naval Society, Maritime Prefect, Autonomous Port of Conakry, Minister of Transport, Direction of Maritime Navigation, National Direction of Customs Department and the Harbour Master / Port Captain.
The ROV provides an eco-friendly, costefficient, brush- and diver-free alternative to traditional hull cleaning methods currently performed in Guinea, protecting lives and the marine environment while cleaning efficiently without compromising anti-fouling hull painting protection. The system uses adjustable seawater jets as the cleaning medium, instead of brushes or abrasives, to minimise the risk of damage to coatings. Removed fouling from vessels’ hulls significantly improves a vessel’s performance especially when vessels steam under full power rather than slow steaming. It also increases energy efficiency and ultimately reduces CO2 emissions.
HullWiper does not discharge removed residues and harmful materials into the sea. Instead, it collects them with a unique on-board filter for safe disposal onshore, thereby reducing the risk of cross-pollination of waters with alien species.
Simon Doran, HullWiper MD, added, “World-wide regulations are becoming increasingly stringent in the management of biofouling with milestones that need to be reached for the reduction of carbon emissions by 2030. By bringing our trusted, safe and reliable hull cleaning solution to Northwest Africa, Guinea is at the forefront of an environmental wave of change to this region’s maritime landscape.”
HullWiper is one of four founding members of IMO’s Global Industry Alliance (GIA) for Marine Biosafety. GIA works with IMO’s GloFouling Partnerships Project to help accelerate the development of technology solutions that help prevent hull fouling. The company is also actively involved within BIMCO and AMPP and are on technical steering committees, with input in the writing of active legislation for hull cleaning and inspection standards globally. HullWiper is compliant with IMCA and IMO guidelines and all operations are conducted in line with local and international regulations.
Since its launch in late 2013, HullWiper has expanded from its first base in Dubai to key locations across the Middle East, as well as ports in Australia, Denmark, Egypt, Gibraltar, Mauritius, Namibia, Norway, Panama, Sri Lanka, South Korea, Singapore, and Sweden. HullWiper has performed more than 1,400 hull cleans for vessels world-wide.
European activities of Hydrex
Belgium’s Hydrex’s teams recently carried out several rudder repairs on ships in Belgium and France. In all cases cracks were found that needed to be repaired to prevent them from spreading and causing further damage to the rudders.
A 230 m ro/ro ship in Zeebrugge had suffered cracks on both sides of the rudder flap. On the starboard side a branching crack was found while a single crack was present on the port side. Hydrex’s divers first drilled arrests on all extremities of the cracks to prevent them from spreading. They then positioned C-shaped plates over the crack arrests and secured these with wet welding. This allowed the owner to sail his ship without having to worry about the condition of the rudder - a permanent repair carried out during the ship’s next scheduled drydock visit at a more convenient time and location.
On two 229 m sisterships (bulk carriers) in Le Havre and Dunkerque respectively, cracks were found on the upper pintle corner of the hinge that connects the rudder flap to the main rudder blade. Fortunately these cracks could be repaired by grinding them out after a crack arrest had been drilled. The affected area was then filled with clad welding.
The cracks on these rudders were spotted during an underwater inspection before they caused problems for the ship. This once again shows the benefits of having regular inspections carried out by competent divers, followed by comprehensive and accurate reports. Our teams can detect any problem so that they can be corrected early and prevent the more costly repair which neglect and further damage would bring about. The affected area was then filled with clad welding.
Hydrex diver/technicians replaced the seals of both stern tube assemblies of a pipe-laying vessel berthed in Rotterdam. Using a Hydrex flexible mobdock the team was able to carry out the entire operation on-site and underwater, saving the owner an expensive and timeconsuming trip to drydock.
The team travelled to the vessel’s location on one of company’s workboats. These workboats are fully equipped as dive support stations with hydraulic cranes, winches, nautical and communication equipment, and a dive control room. They are stationed in Rotterdam and Antwerp which allows for a fast mobilisation throughout both ports.
Once the operation was confirmed all preparations were handled swiftly and the lightweight equipment was mobilised. The operation then started with the removal of the rope guard and a thorough underwater inspection of the first stern tube seal assembly. After the inspection the divers cleaned the assembly and installed the flexible mobdock. By doing this they created a dry underwater environment so that they could work in drydocklike conditions.
The split ring was then removed and brought to the surface to be cleaned. After cleaning the entire assembly, the divers removed the first seal and replaced it with a new one which was bonded. They then did the same for the other seals.
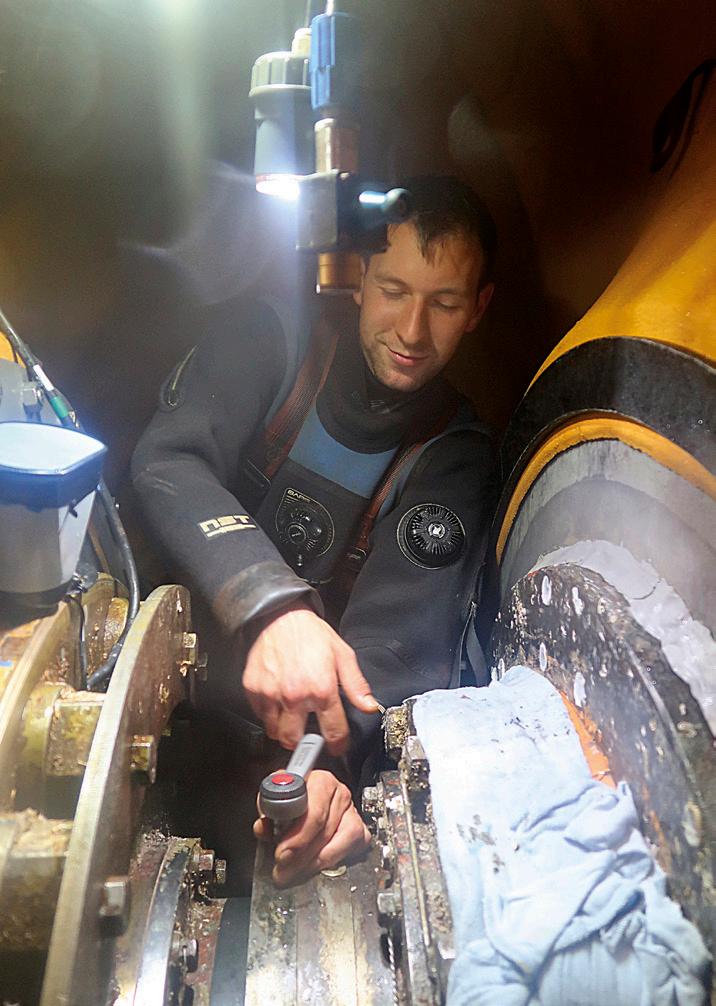
A Hydrex technician works inside a mobdock
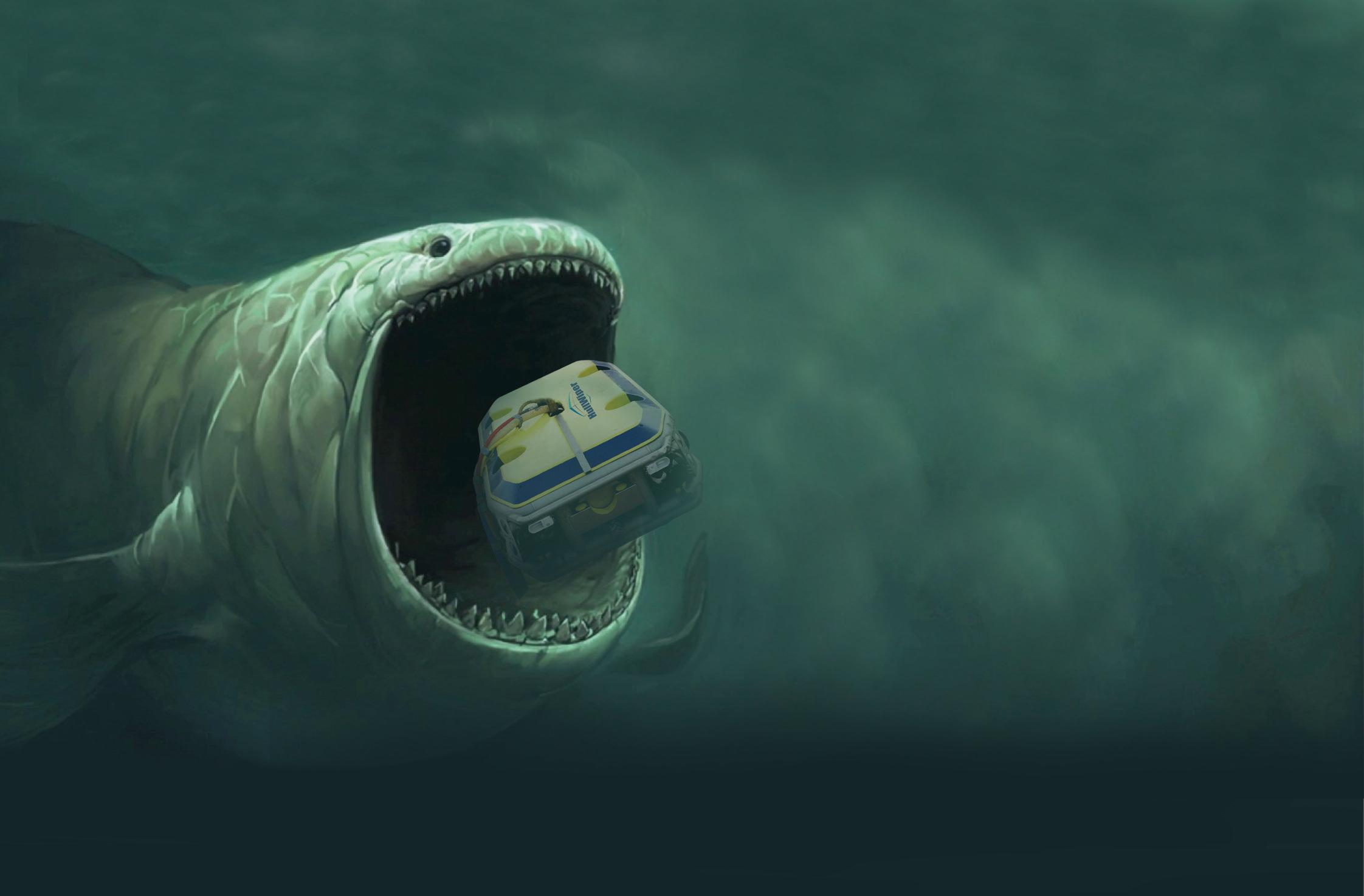
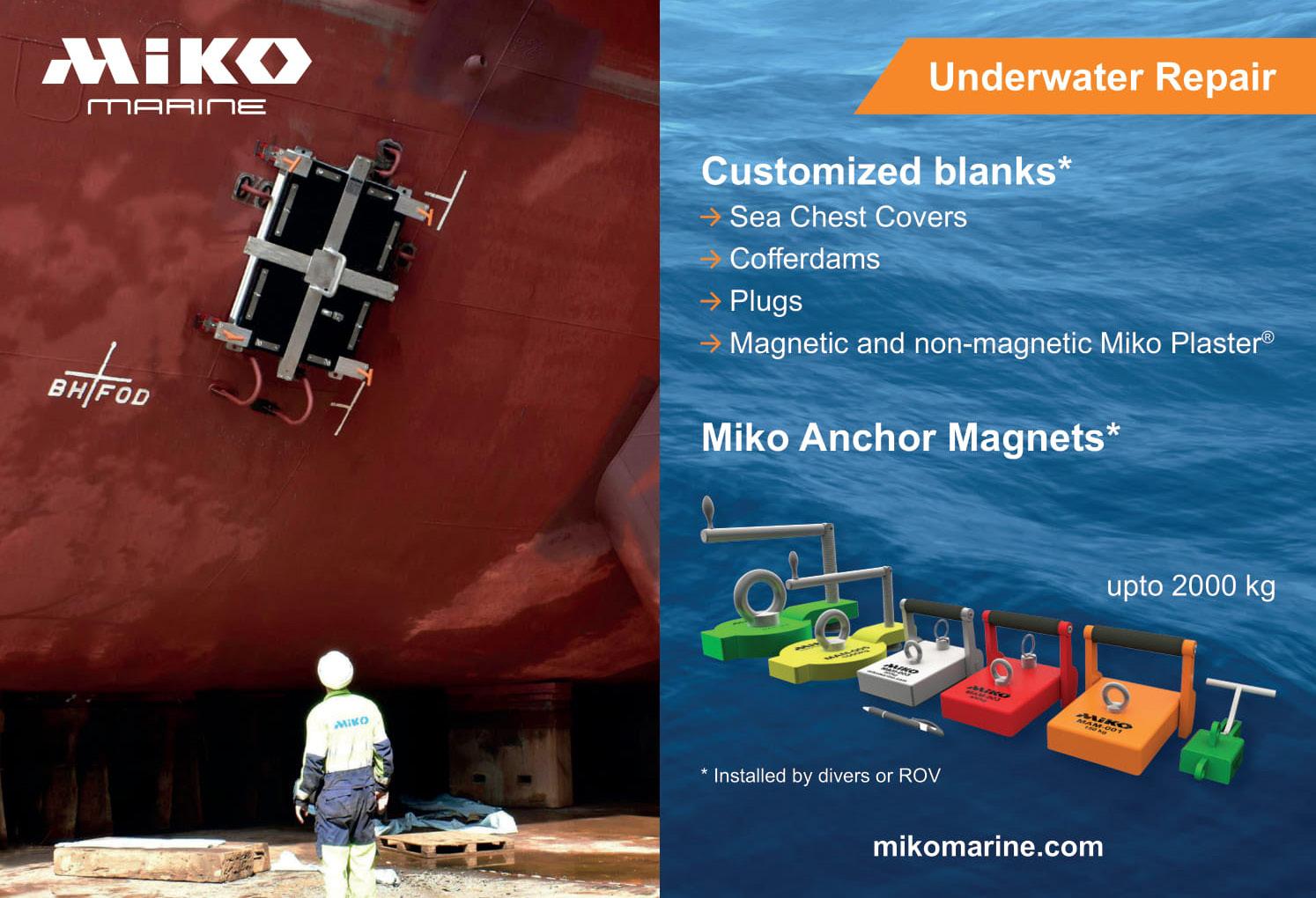
A successful operation was concluded with leakage tests, the removal of the flexible mobdock and the reinstallation of the rope guard. The procedure was repeated to remove the seals of the second stern tube assembly.
Working together with the OEM allowed Hydrex to provide the customer with original spare parts which guarantees the best quality material. A technician of the seal manufacturer was also present during the operation.
By organising everything from start to finish the owner did not have to worry about making any arrangements for the repair. After the seals had been successfully replaced he could sail his vessel to its next stop free of oil leaks.
Recently Hydrex diver/technicians carried out scrubber overboard pipe repairs in ports in Belgium, France, Malta and Spain. On a 397 m containership two pipes were replaced while one pipe was replaced on an oil tanker. In all cases the pipes were protected with a corrosion resistant coating produced by Subsea Industries. Exhaust scrubbers are systems that filter out all harmful toxins from exhaust gasses of marine diesel engines. These can severely corrode the pipes of the scrubber which can result in water ingress if not handled quickly enough.
One of Hydrex’s teams removed a bow thruster from a 170 m containership in Rotterdam. The unit needed to be overhauled and the operation had to be carried out within a very short window that would fit the schedule available to the vessel’s owner.
The team mobilised to the ship’s location using one of our workboats loaded with all the needed equipment. These workboats are stationed in Antwerp and Rotterdam and can be used for a wide range of operations, which enables rapid deployment and increases flexibility, which was essential during an operation like this.
Hydrex carried out the removal following the specific procedures required by the involved OEM. This allowed the removal the thruster unit with the blades still attached, speeding up the operation. Simultaneously the team sealed off the tunnel from the bow thruster room. Once the unit was lifted onto the quay it was prepared for transport to the workshop.
By performing the operation on-site and underwater our divers made it possible for the owner to keep the vessel out of drydock. The team worked in shifts around the clock. They finished the job well within the available time frame. This allowed the ship to sail on schedule, which was a key benefit for the owner.
Hydrex also removed a bow thruster from a 229 m bulk carrier. Two weeks later the overhauled unit was reinstalled. Both operations were completed during stops in Algeciras, Spain and had to be carried out within the tight schedule available to the charterer.
To keep the impact on the ship’s schedule to the absolute minimum divers performed an inspection of the bow thruster unit and tunnel, followed by some preliminary work while the vessel was berthed at a lay-by. The ship could then shift and start cargo operations while the team performed the rest of the operation without any hindrance to the loading schedule.
First Miko blanking set leaves for China
The first magnetic blanking set destined for the Brazilian offshore sector has left the Miko Marine’s fabrication plant in Haugesund, Norway. After six weeks of manufacture, the set is now en route to China’s Dalian Shipbuilding Industrial Co (DSIC). It will then be installed on-board a new FPSO being completed for Japanese platform builder MODEC. On leaving Dalian the new FPSO will be moved to the Bacalhau field offshore Brazil where it will be operated by Equinor.
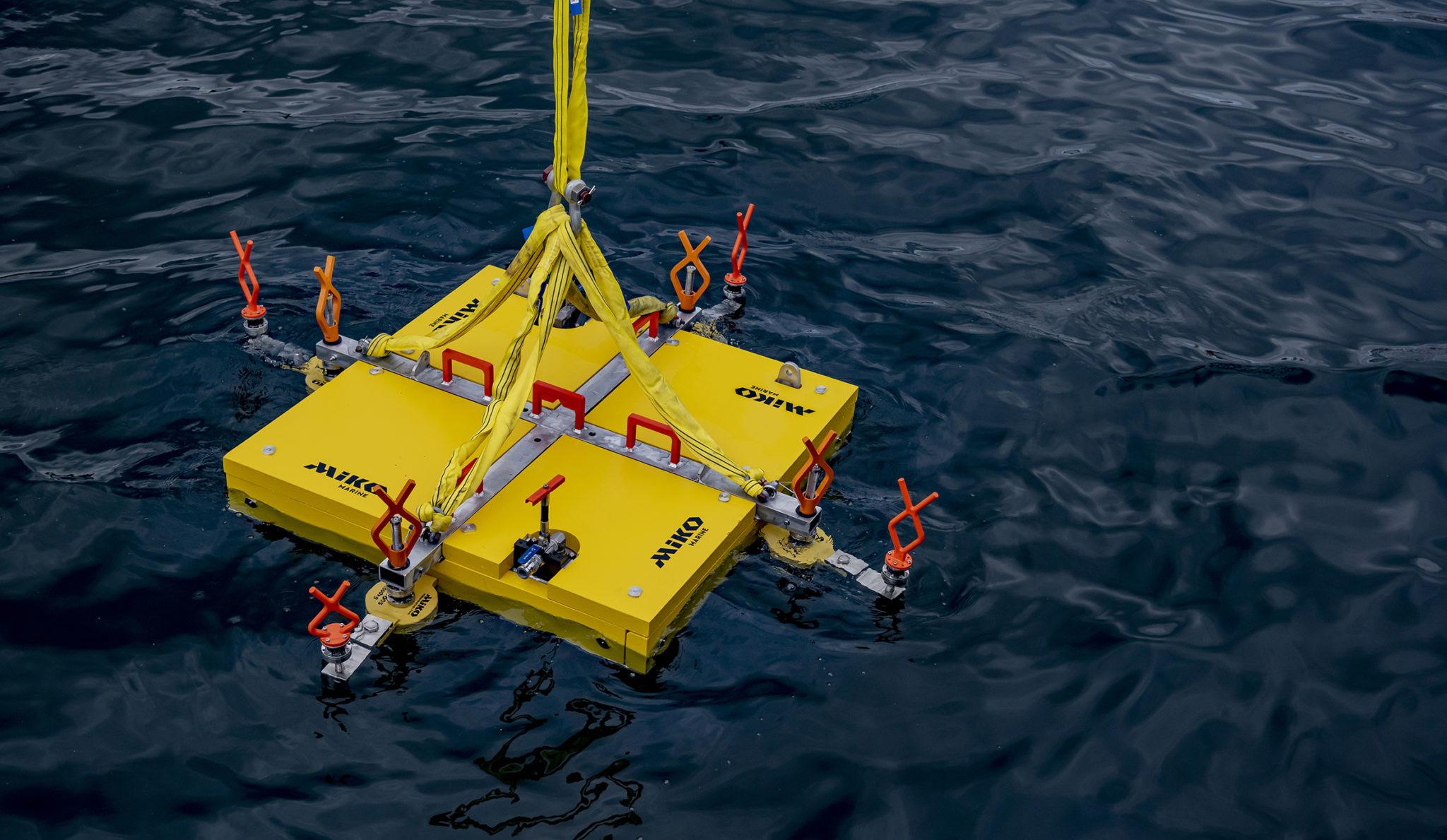
The Miko Marine magnetic blanking set
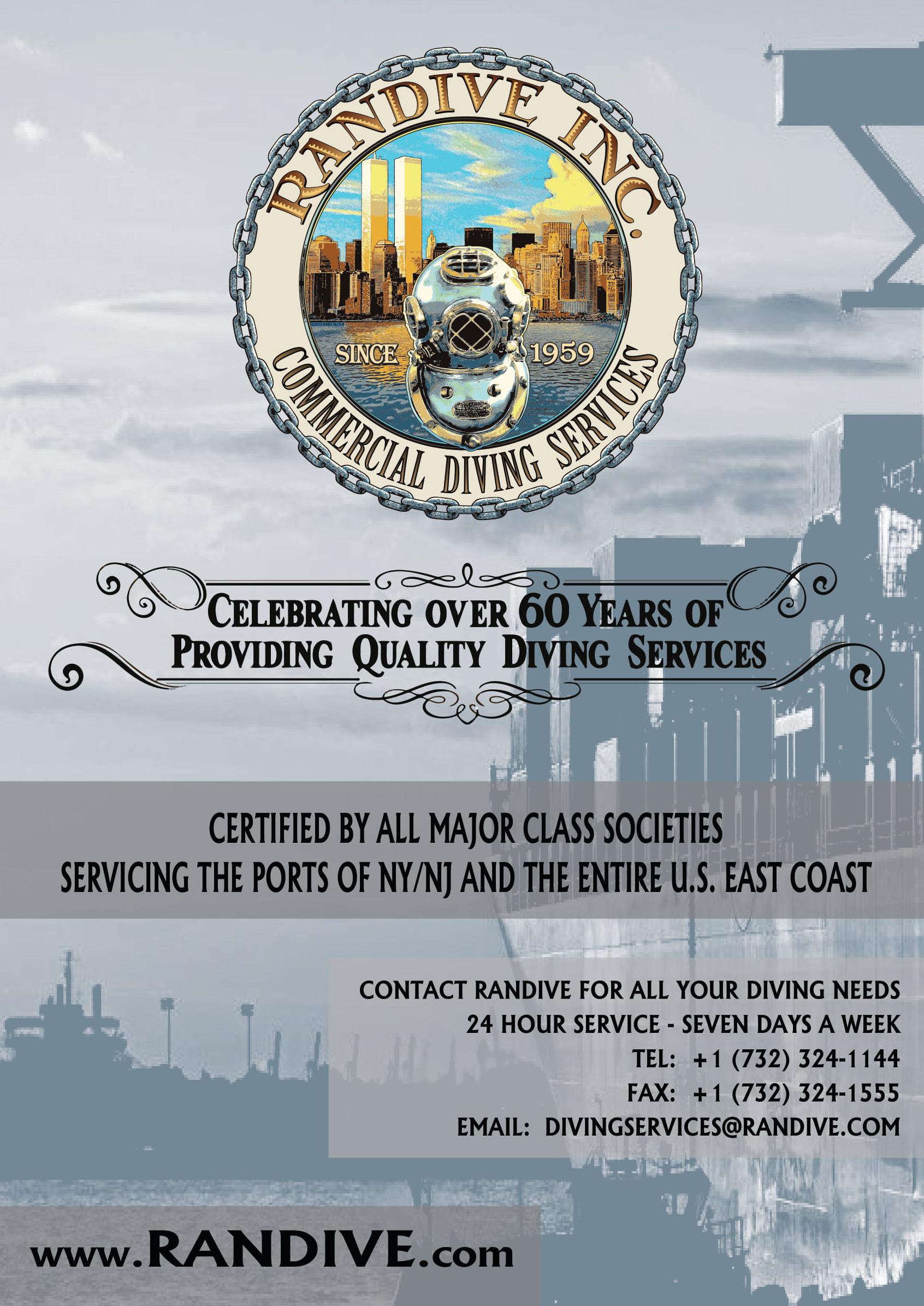
The new blanking set comprises four cofferdams that can be used for covering sea chests and three inlet pipe covers. Featuring Miko’s distinctive yellow trade mark colour scheme, their unique magnetic attachment system enables them to be quickly fitted over a hull opening by divers or ROV. They create an immediate water-tight seal without the need for any welding or hull attachments and can be quickly removed for recovery and storage until needed again. The ability to enable repairs and maintenance to be conducted without dry docking is seen as a major cost benefit and necessity for rigs and platforms which can remain on-station throughout.
Cato Stoll, managing director of Miko Marine, believes the delivery operation marks the completion of an important contract for Miko. “This is the culmination of a great deal of hard work and the application of detailed expertise by the Miko design team,” he said. “The team’s specialised knowledge and experience ensures that the magnetic blanking set will function safely and reliably for many years to come. When the new FPSO is on station offshore Brazil it will possess an operational cost benefit that is unique among FPSOs in the region. By designing and manufacturing the blanking set while the FPSO was under construction provided us with many benefits in terms of convenience and ease of work. Nevertheless, we frequently provide the same service as a retro-fit for ships and platforms whose operators want to avoid the cost and complications of ad hoc blanking contracts,” he said.
Miko has developed considerable experience in the design and manufacture of hull closures and cofferdams and has particular expertise in the use of magnetic technology. Each cofferdam or pipe blank is kept in place by a configuration of powerful Miko MAM permanent magnets. With each magnet being capable of holding up to 2,000 kg it is possible to achieve an immediate watertight seal for the closures without the need for any other fastening devices being fitted to the hull. Flotation material is integrated within the blanking plates and this makes them neutrally buoyant and easily handled under water by ROV. Each magnet is attached to its closure by a flexible joint which enables the plate to be manoeuvred and positioned precisely against the hull before it is tightened into place. When the repair work is finished the magnets are simply freed by having their release lever rotated by a diver or ROV, enabling the blank to be quickly retrieved by crane and stored on-board.
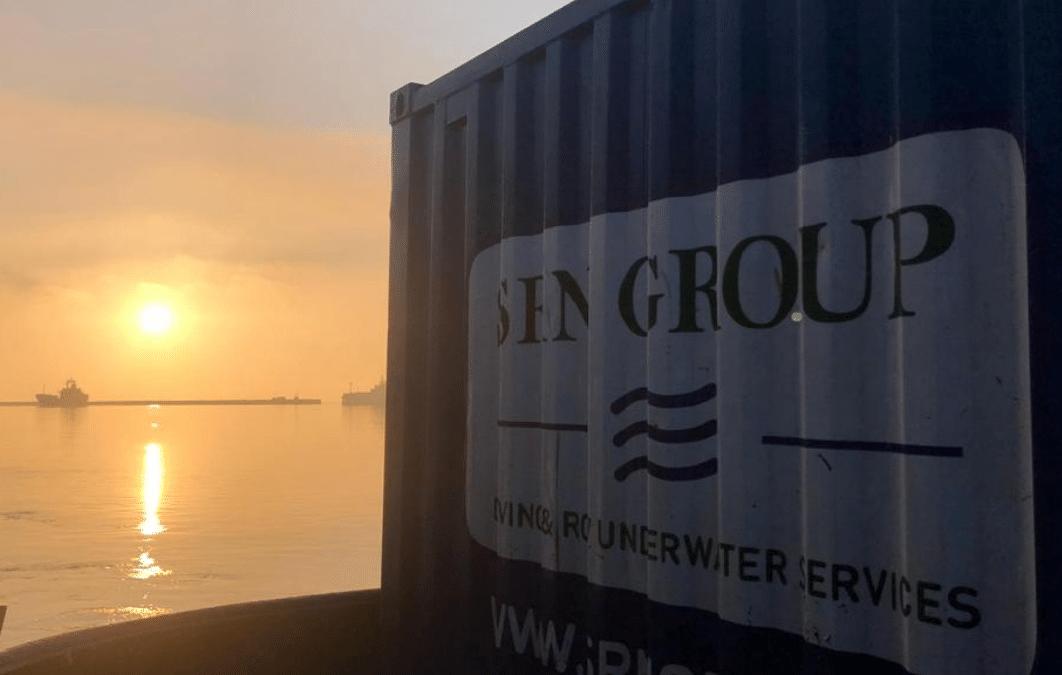
SGS has acquired SRN
SGS acquires SRN Group
US-based Subsea Global Solutions (SGS) has announced that it has acquired SRN Group Diving & ROV Underwater Services (Belgium), a leading underwater services and Remotely Operated Vehicle (ROV) hull cleaning firm based in Belgium. With this acquisition, SGS expands its global footprint to Europe, acquires industry leading ROV hull cleaning technology and increases the number of its home ports world-wide to 14.
Commenting on the acquisition, Paul Peters, CEO of SGS said, “This is a much awaited, critical milestone for SGS. We are absolutely delighted to expand our global footprint to North Europe, a strategic commercial and cruise shipping hub where most of our ship owner clients visit regularly. In addition to adding a key location to our network, we are excited to add a new ROV technology to our existing suite of environmentally friendly propeller and hull maintenance services. This acquisition will allow SGS to immediately deliver the much sought after environmentally friendly, ROV based hull cleaning services in the highly regulated ports like Rotterdam, Amsterdam as well as Portland, UK. We welcome our new colleagues on-board and look forward to working together.”
Manuella Maes and Pierre Klein, co-founders of SRN Group, added, “We are proud of what we have built with SRN in North Europe and West Africa (i.e., Tema, Lome, Takoradi, Abidjan etc.), having delivered a consistent and reliable service to our clients since our inception. Our Hull Cleaning ROV (CROV) technology has earned a well-deserved reputation in our key regions, and we look forward to seeing this technology being applied globally. It was time to join forces with a larger and more diverse underwater service provider like SGS in order to add further scale and depth to our operations and continue to innovate at a faster pace. We are excited to become part of the SGS family”.
Subsea Global Solutions is the globally formed corporation with wholly owned assets and personnel in USA (Miami, Tampa, Long Beach, Houston, and Port Angeles), the Caribbean (Curacao, Trinidad), Canada (Vancouver, Halifax, and Saint John), South Korea (Busan), Singapore, Australia (Sydney) and Brazil. With dedicated staff situated globally, Subsea Global Solutions has revolutionised the methods of repair and maintenance for ships and advanced procedures used in underwater marine construction. The name serves to accentuate the shared values of the SGS’ companies, and our commitment to be “The One Source for Global Underwater Solutions.” All offices are approved by the major classification societies.
The Ship Repair Network (SRN Group) was founded in January 2013 by co-founders Manuella Maes and Pierre Klein. The headquarters of the company is located in Stabroek- Antwerp (Belgium), close to the heart of the shipping industry and the port of entry into Europe. SRN has successfully transformed the ROV hull cleaning market in North Europe and WAF with its proprietary technology and approvals in key commercial ports such as Rotterdam and established a well-deserved reputation internationally.
SORJ