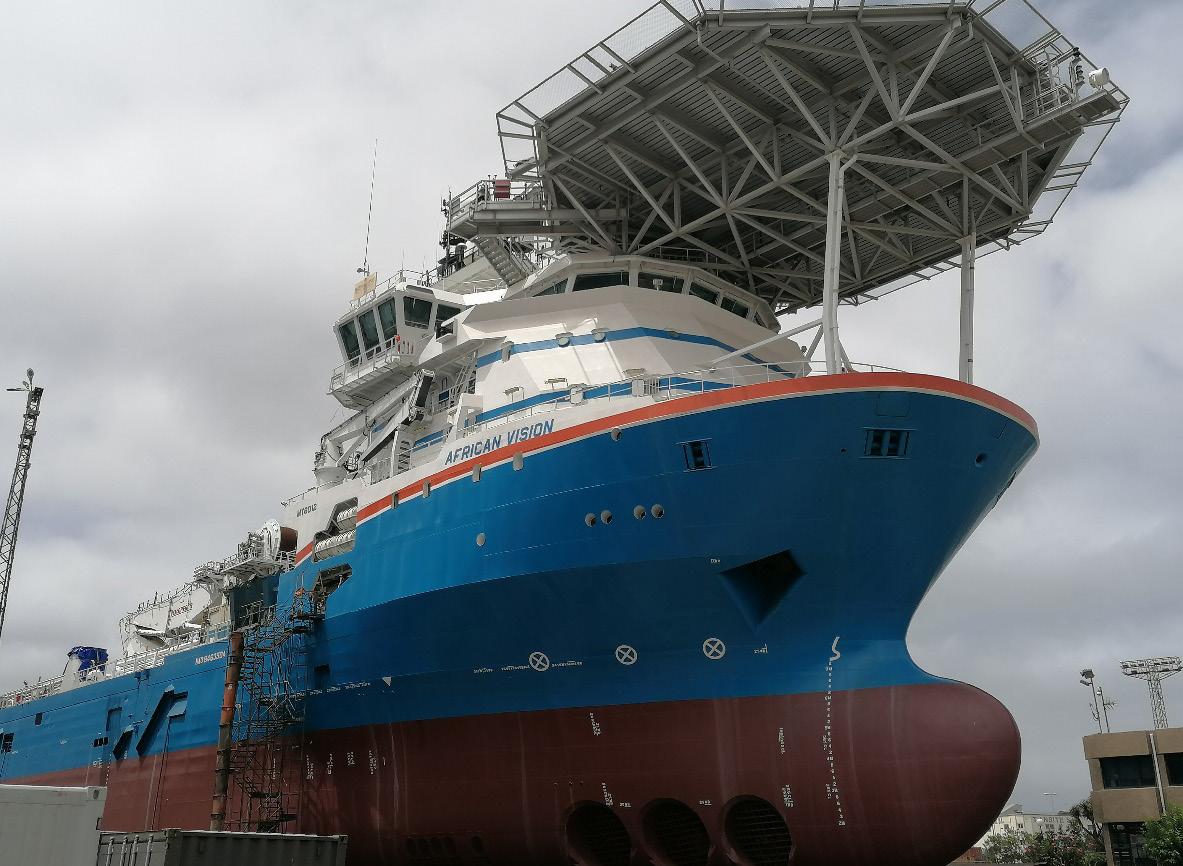
15 minute read
Repairs
Good 2021 for Astican
The activity at Astilleros Canrios (Astican), Las Palmas, during this year has been quite regular with most months being busy. February ended up being a very busy month, with a diversity of customers, vessel types, sizes, and repairs. The yard reports a total of 101 repair projects were completed during 2021, 61 on the yard’s Syncrolift shiplift system.
Advertisement
In the first and second quarter, Astican carried out a variety of work such as the replacement of the 35 tonne SNL crane onboard the non-self-propelled vessel Luft-1 and the first installation of a CMC on-board a drillship in the Canary Islands. It was also busy few months in the offshore market.
There were also major repairs on-board Fred Olsen’s 6,348 gt fast ferry Bentago Express and the yard was fortunate to drydock, for the first time, the world’s fastest and most modern trimaran, the 7,915 gt Bajamar Express, the longest vessel ever drydocked at Astican, with a clearance of only 80 cm on the shiplift.
During the autumn, Astican completed two important repairs, Mercy Ships’ 16,572 gt specialised hospital ship Africa Mercy and Odfjell Asia’s 9,999 dwt LPG tanker Bow Guardian. This latter ship is managed by Singapore’s Anglo Eastern.
For Astican, the Africa Mercy has been one of the most important projects this year. Extensive work has been completed to cover the hull and bulkheads plates, the frames, all structural members, internal piping, as well as hull treatment, steel work, and tank coating (blasting and painting).
Repairs to the ship required more than 70 tonnes of steel to make it as good as new. 80 access points in the hull had to be opened to accommodate the blasting equipment and tank work to ensure safety throughout the project. A lot of work was also carried out on the ship’s exterior, such as the deck cranes and funnel, which was structurally renovated. A total of 120 windows were replaced and up to 49 tonnes of paint was used to make the ship as good as new again.
Thanks to the 450 people involved in the project, Africa Mercy has gained 15 more years of service life to be able to continue her missionary work in Africa and provide medical and surgical care to people in need as it has been doing for more than 40 years.
After grounding the ship had several areas of steel damage from the bow to Frame 72. The steel in the flat bottom was cropped off and renewed as required by the owner and Class, this included, the two cargo holds and four water ballast tanks a total of some 97 tonnes of steel was renewed. Due to the grounding, the insulation of the cargo tank was affected, and it was renewed.
Astican also recently worked on-board Marine Platforms’ 4,845 gt OSV African Vision. Her length overall is 93.6 m, and her width is 19.7 m. The main work carried out were removal of stern azimuths thruster, box cooler cleaning, accommodation work, moonpool treatment and renewal of frames.
The African Vision on Astican’s Syncrolift
Ever Given enters Qingdao Beihei shipyard
The Shoei Kisen-owned 20,124 teu capacity 2018-built container vessel Ever Given, famous for blocking the Suez Canal in March last year, arrived at Qingdao Beihei Shipbuilding & Heavy Industries (BSIC) during October last year for three weeks of repair work, which included significant repairs to the vessel damaged bulbous bow.
BSIC, part of China Shipbuilding Industry Corporation (CSIC), has more than 330 hectares of land, 9 kms of coastline, nearly 6 kms of wharf length, two shipbuilding dry docks (500,000 dwt and 300,000 dwt), two shiprepairing dry docks (300,000 dwt and 150,000 dwt), and one floating dock for ship-repairing (100,000 dwt).
Offshore projects at Sembcorp Marine
From the offshore market (FPSOs and FPUs), Sembcorp Marine currently has six projects underway. During October last year, the Tuas Boulevard Yard (TBY) carried out the load-out and tandem lift of the Vito Host mega-topside structure for the Vito FPU Project – both mark notable firsts for Sembcorp Marine’s newbuild track record.
Following the load-out, the mega-topside structure was transported via the yard’s heavylift vessel Elite Prosperity and lifted onto the FPU hull using a pair of goliath cranes with a combined 30,000-tonne lifting capacity and 100 m hook height.
Sembcorp Marine is working expediently at the request of Norway’s Equinor, to plan the remaining scope of work for the Johan Castberg FPSO to accommodate the available transportation window for the towing operations to Norway. The construction of the topside modules, module integration and final completion, which are not part of the Sembcorp Marine’s scope of work, will be performed in Norway.
Recently, Sembcorp Marine entered into an exclusive Front-End Engineering and Design (FEED) contract with Siccar Point Energy E&P to deliver a FPSO design solution for the Cambo field in the UK Continental Shelf. The solution is based on Sembcorp Marine’s proprietary Sevan
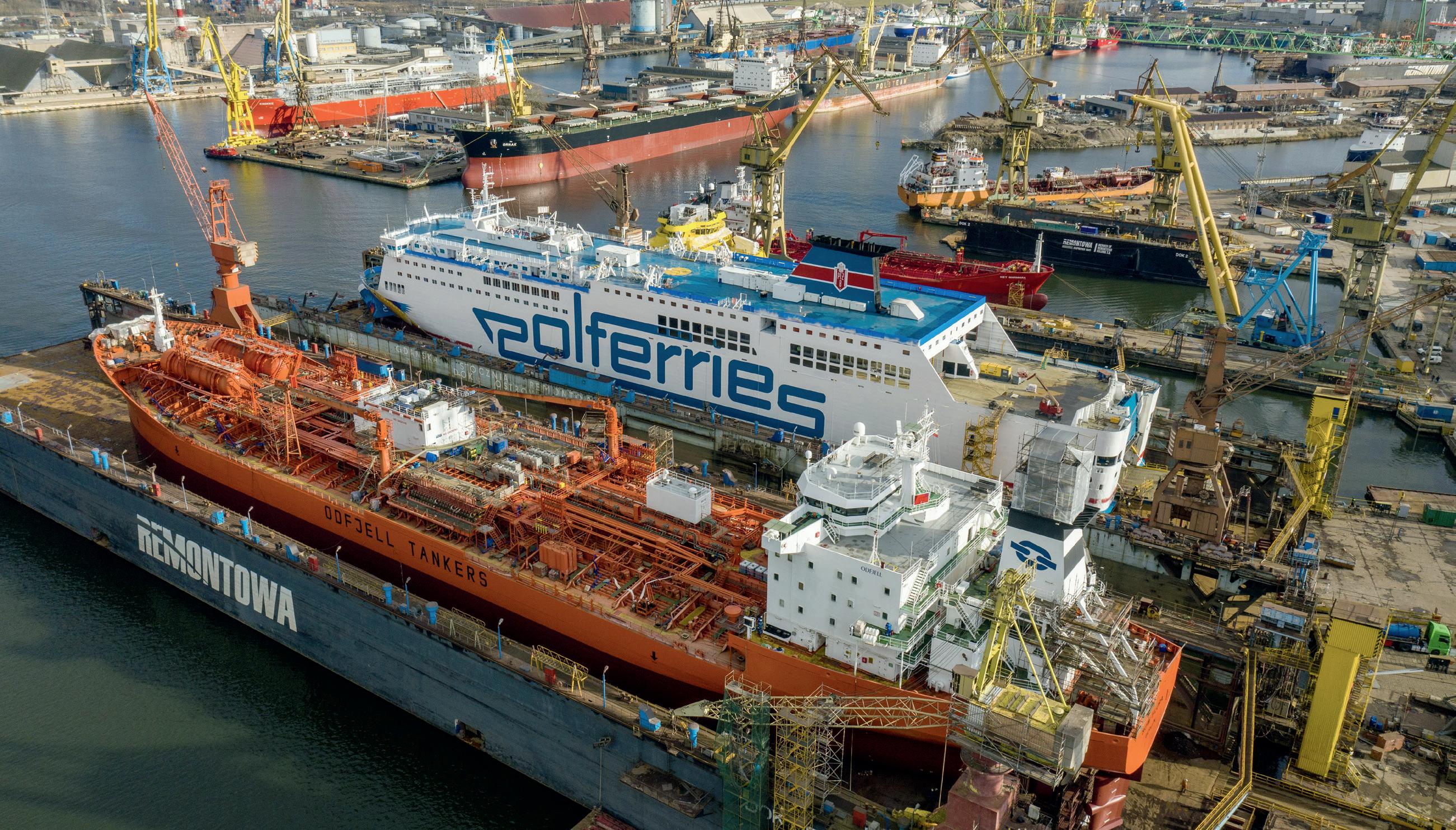
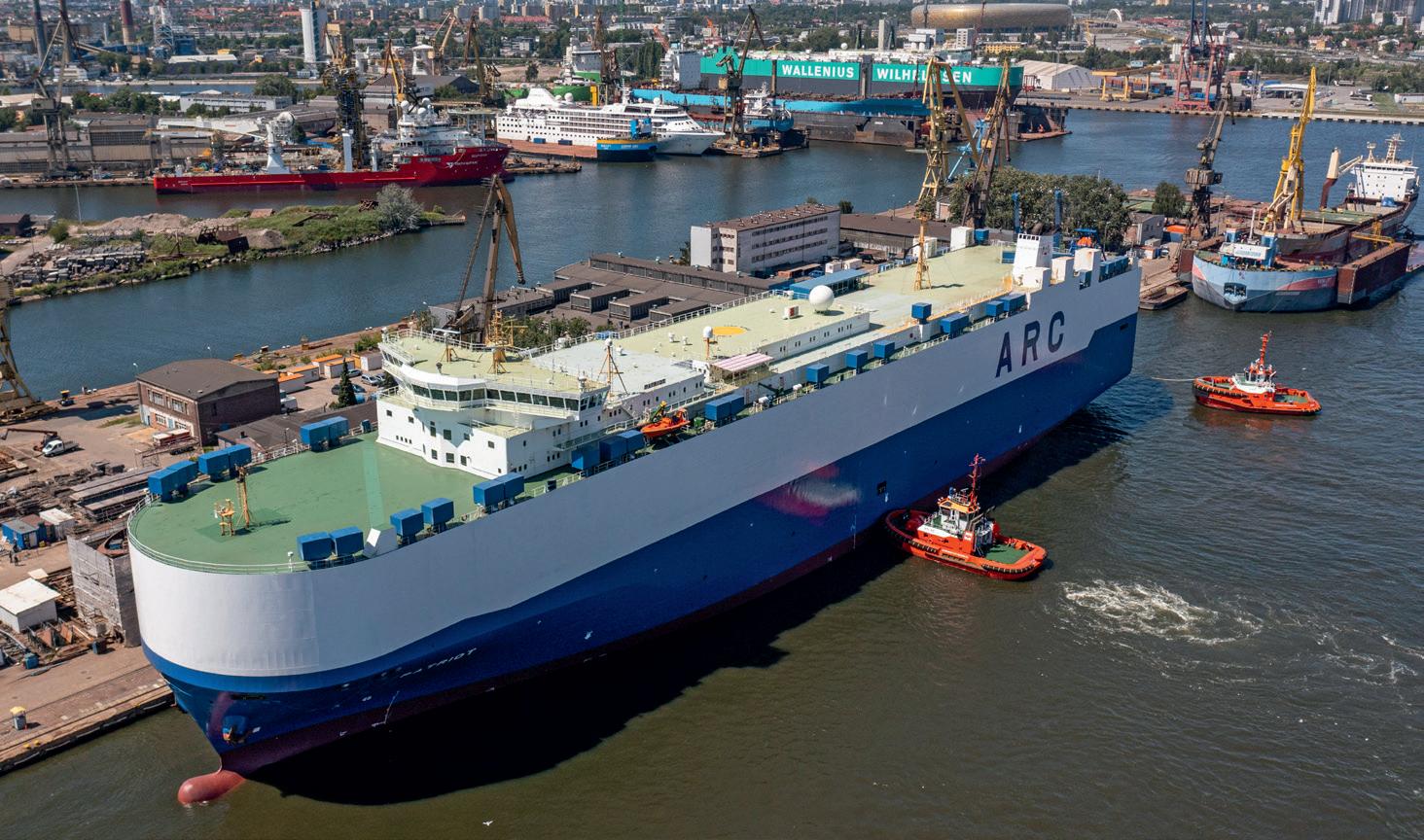
Tandem lift of the Vito Host mega-topside structure onto the FPU hull by a pair of goliath cranes, with combined 30,000-tonne lifting capacity and 100 m hook height, at TBY
geostationary circular hull, a cost-effective alternative to traditional ship-shaped and turretmoored designs. The Group is continuing with pre-FID (final investment decision) work on the Cambo FPSO in anticipation of a FID soon.
During September 2021, Sembcorp Marine secured the FEED contract for the Dorado FPSO project. Other projects underway in the Sembcorp Marine shipyards are: • Shell Vito - Newbuild Floating Production Unit (FPU) • Shell Whale - Newbuild FPU • NOC - Gallaf Batch 2 - Wellhead Platforms • Shapoorji - FPSO Conversion
Meanwhile, Sembcorp Marine’s Brazilian yard, Estaleiro Jurong Aracruz, is carrying out modification and integration work on the FPSO P-71 oil and gas vessel slated for deployment at the Itapu field offshore Brazil. The vessel is expected to be delivered in the last quarter of 2022.
Sembcorp Marine is also very much involved in the LNG market with three projects currently underway. On the newbuilding side, it is building a LNG bunker vessel for MOL, for TotalEnergies, the yard is currently working the Tyra West Redevelopment Project - topsides and bridges, a FPSO newbuilding is currently underway for Technip Energies’ Karish project and for Karmol LNGT Powership Asia, a FSRU conversion and upgrade is currently underway.
As well as the oil & gas and LNG markets, Sembcorp Marine is also well involved in the renewables market. Current projects underway include: • Ørsted - Hornsea 2 Offshore Wind Farm - Offshore Hook-up and Commissioning of Offshore Substation and Reactive Compensation Station Topsides • Jan De Nul - Formosa 2 Offshore Wind Farm - Wind Turbine Jacket Foundations • RWE Renewables - Sofia Offshore Wind Farm - Offshore Converter Platform Sembcorp Marine’s on-going wind farm projects are advancing well. Following the successful installation of Ørsted’s OSS and RCS topsides for the largest AC offshore substation at Hornsea 2 Offshore Wind Farm in October 2021, the Group will commence the offshore hook-up and commissioning of the topsides in November 2021, with completion scheduled in the first quarter of 2022.
It has also made steady progress on Jan De Nul’s Formosa 2 Offshore Wind Farm project, with the completion of four wind turbine jacket foundations. The first pair of completed jacket foundations sailed away in October 2021 while the second pair set off in early November 2021. Fabrication works are underway for the remaining 11 jacket foundations with expected completion by end 2021.
In addition, the Group marked the construction commencement of the Sofia Offshore Wind Farm’s Offshore Converter Platform with a First Steel Cutting Ceremony held in September 2021.
Sembcorp Marine has several repairs and upgrade projects currently in progress, including the LNG major reliquefaction plant installation project on-board Teekay Gas’ 173,400 m3 LNG tanker Magdala, as well as restoration work on-board Eastern Pacific Shipping’s 63,014 dwt containership MSC Messina and PRIMCO’s 76,000 dwt bulk carrier Galapagos. The Group is also undertaking various green refit projects, including the drydocking and repair of 141,740 dwt tanker Polar Enterprise, which involve the installation of a BWM system installation.
As the cruise market slowly returns, Sembcorp Marine has secured contracts to carry out refurbishment and revitalisation work on Royal Caribbean Cruise Line’s 142,714 gt Royal Princess and Windstar Cruises’ 5,307 gt Wind Spirit. Both cruiseships will arrive in December 2021 for repair work.
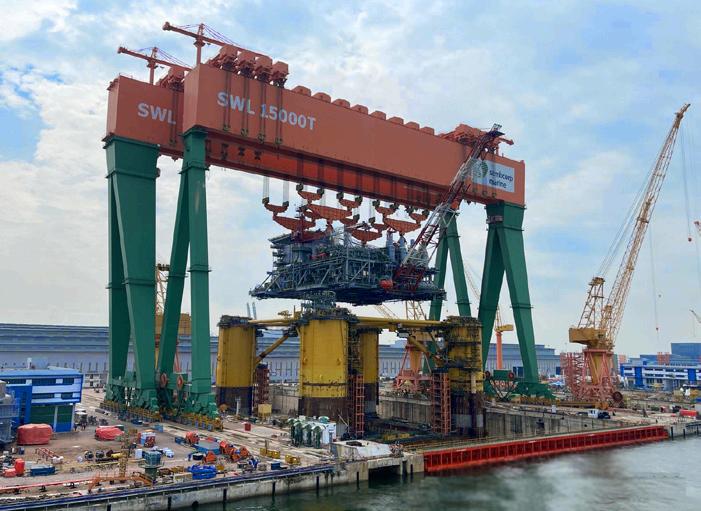
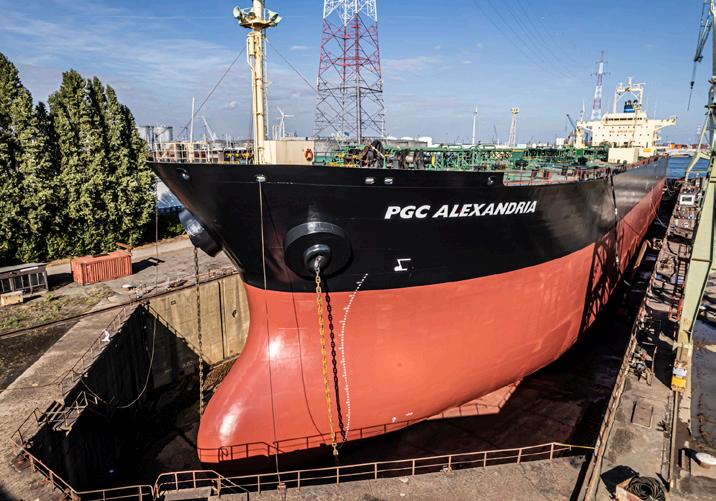
The PGC Alexandria in EDR Antwerp
Recent repairs at EDR
Recent repair projects in Belgium’s EDR Antwerp include three containerships from Germany’s Offen Rederei. These were the 74,477 dwt MSC Alicante, the 74,375 dwt MSC Madrid and the 74,456 dwt MSC Barcelona. These are three vessels of a six vessel agreement with Offen involving second special surveys and BWM system installation.
EDR also successfully completed another survey of the heavy lift crane Brabo, including full overhaul of her Voith Schneider propulsion system. The yard has now completed three repair containership projects for Holland’s Seatrade, Groningen involving the 24,901 gt sisterships Seatrade Blue, the Seatrade Red and Seatrade Orange. These are the final vessels of a multi vessel deal with Seatrade, all including first special surveys including extensive paint application.
During October EDR completed a third special survey of Paradise Shipping’s 74,996 product tanker PGC Alexandria. Lauterjung Reederei’s 34,296 dwt containership MSC Samira III was in the yard for a second life project.
All repair teams have been fully occupied with various projects at lay by berth or at commercial berth in the Port of Antwerp. These have included Mercy Ship’s 37,000 gt hospital ship Global Mercy, Unibaltic Shipping’s 3,500 dwt chemical tanker Amazonith and Eisho Shipping’s 28,316 dwt bulk carrier Globe Explorer .
International owners at Astander
Some new and regular customers from France, The Netherlands, Spain, Germany, Norway, Belgium, United Kingdom, Poland, Denmark and Greece have made Spain’s Astilleros Santander (Astander) recently reach new record occupancy rates.
Asphalt carriers, cement carriers, chemical/ product tankers, containerships, general cargo vessels, passenger and cruiseships, PSVs, ro/ ro vessels, dredgers, vehicle carriers and even a weather vessel have visited Astander’s drydocks and repair berths so far this year.
In addition to standard drydockings and maintenance jobs some more demanding special projects such as an important outfitting,
Hull work at Astander
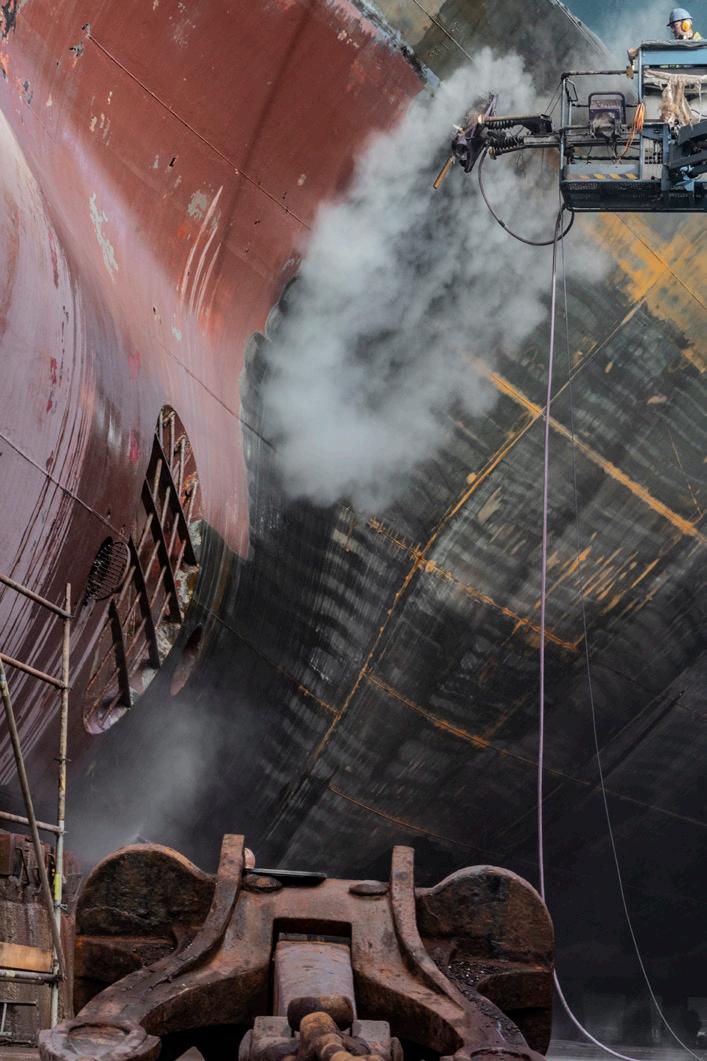
a life extension project of a containership, a number of BWM system retrofits, and dryscrubber retrofit on-board a ro/pax ferry, have also been completed.
Astander is firmly committed to reduce its impact on the environment and this year a new step forward has been given by eliminating gritblasting and introducing hydrojetting for all hull treatment jobs and designing new enclosed paint cabins to avoid spraying paint into the environment and overspray - among other inhouse measures. Astander has been the first shiprepair yard in Spain to fully replace grit by water.
A spokesman for Astander said, “In connection with this commitment, it is very specially rewarding to co-operate with our customers in their projects to minimise the emissions to the atmosphere. Two such projects are presently being carried out at Astander during the last two months of the year - a rigid sail is being installed on a general cargo vessel. This will reduce the power demand from the main engine and the fuel consumption and pollutant emissions will consequently be reduced as well.
The second project is quite a unique and innovative project. It concerns the installation of a dry scrubber solution that uses a sodiumbased sorbent that removes SOx and particles.
It is being installed on a ro/pax vessel.
Activities at Damen Brest and Rotterdam
The former drillship Hidden Gem (ex Vitoria 10000) recently entered drydock at Holland’s Damen Shiprepair Rotterdam, Schiedam to begin the drydock phase of the 61,042 dwt 2010-built vessel’s conversion into a subsea mining vessel for her new owners’ The Metals Co and its partner Allseas. As part of the conversion project Hidden Gem is being fitted with a 4.5 kms riser which will be used for the recovery polymetallic nodules from the ocean floor and transfer them to the service and then to the shore. Hidden Gem is scheduled to be operational for pilot nodule collection tests by mid-2022.
Cunard’s 149,215 gt 2003-built transatlantic liner/cruiser vessel Queen Mary 2 recently drydocked at Damn Shiprepair Brest for scheduled drydocking work. This is the first time this vessel has drydocked away from German yards. Also recently in this yard was the 172,600 m3 capacity 2018-built LNG tanker Vladimir Vize. She is owned jointly by China’s COSCO and Japan’s Mitsui OSK Lines and operating for the Yamal LNG project in Siberia.
Fincantieri and Wärtsilä complete Windstar renovation
Wärtsilä has successfully completed a major project to renovate three Windstar cruise ships carried out at the Palermo shipyard of Italy Fincantieri since 2019 with the first of the three sister vessels, the Star Breeze, being completed in 2020. This was followed by the Star Legend in mid-2020, and finally the Star Pride in
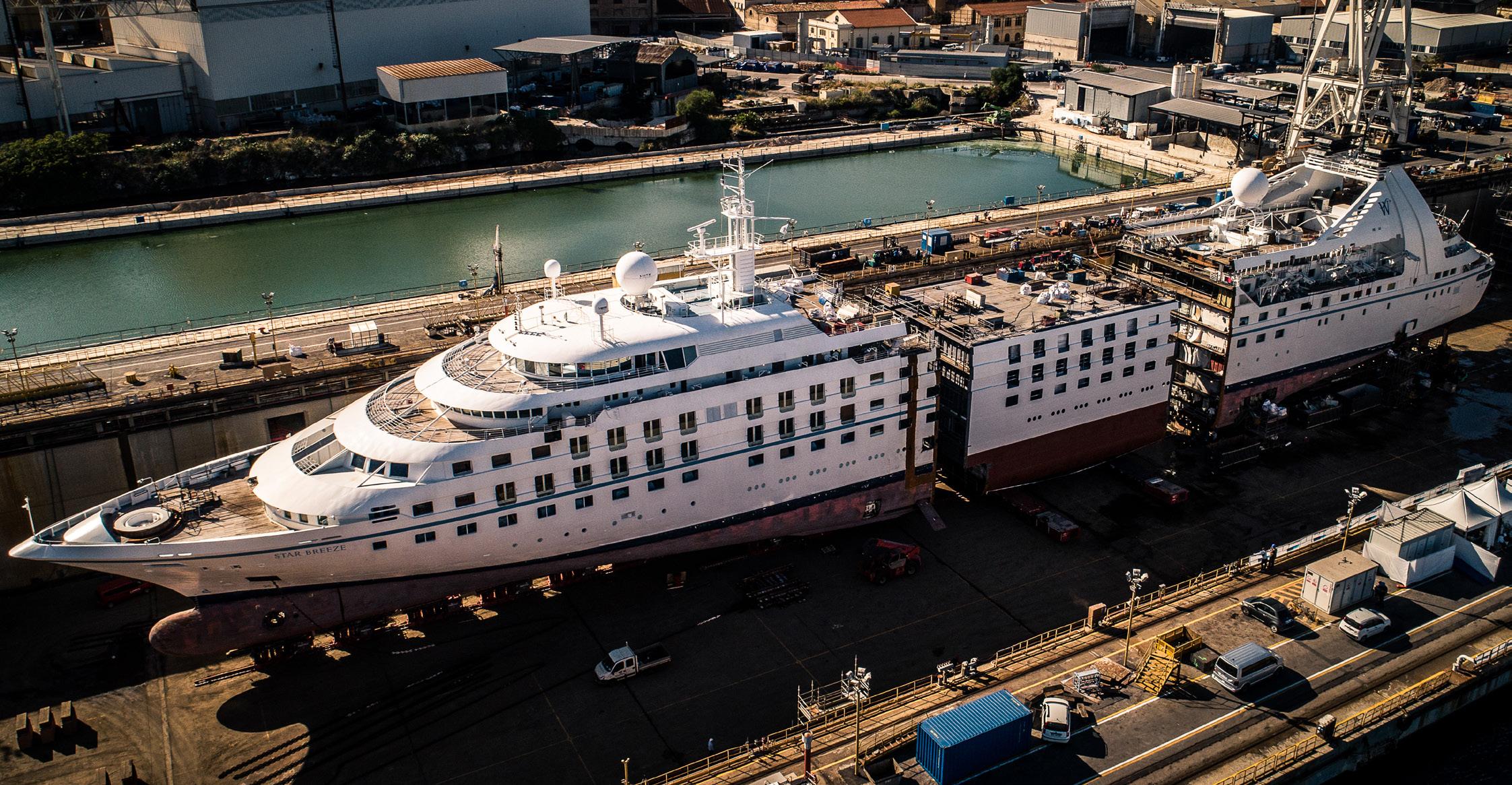
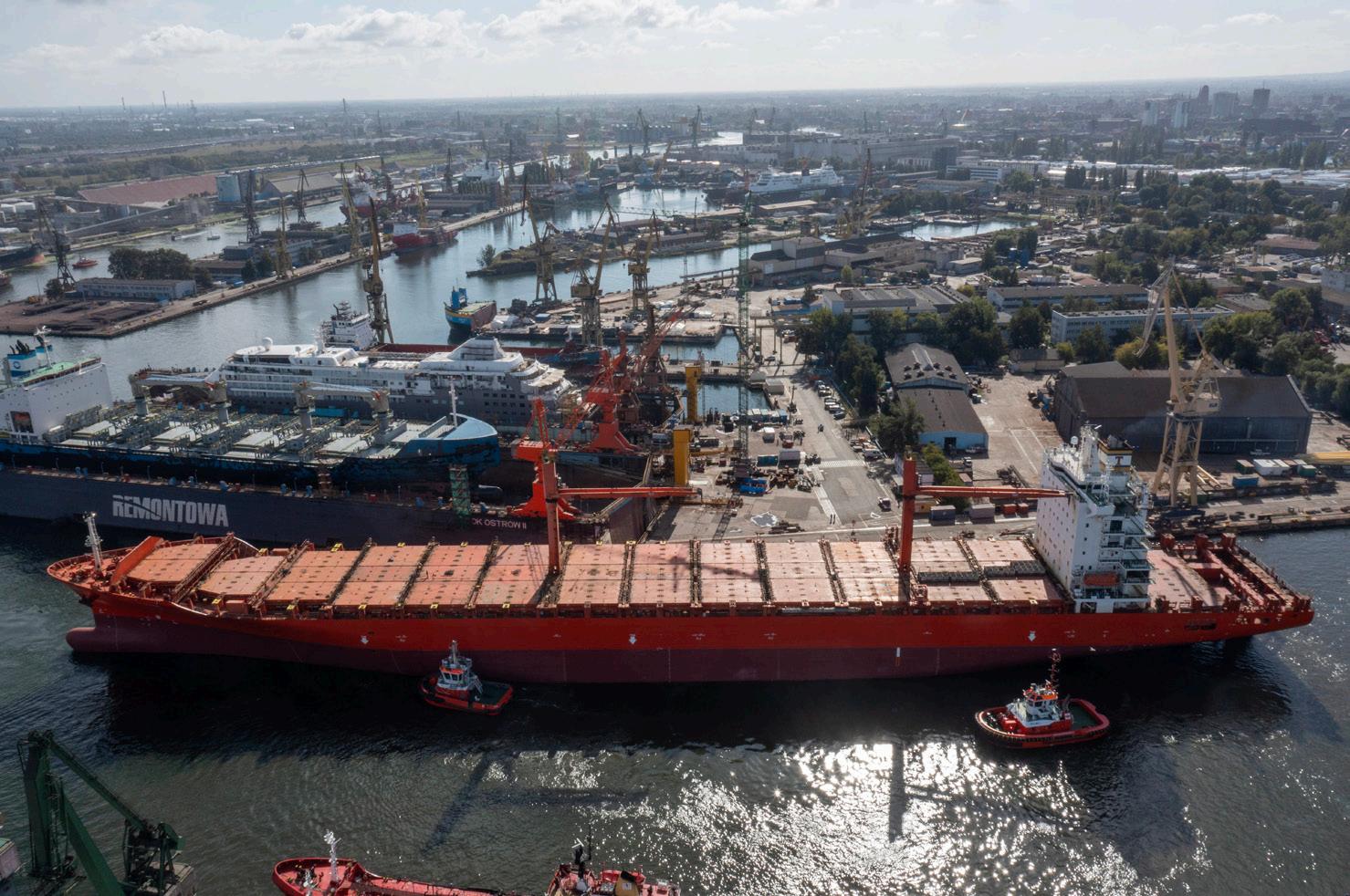
The Irenes Resolve in Remontowa
October 2021. The renovation included the ships being extended in length from 135 m to 160.6 m. The project was part of Windstar’s US$250m Star Plus initiative.
The ships were each cut in half at the shipyard and a new 25.6 m mid-ship section added, providing an extra 50 staterooms accommodating 100 more passengers. At the same time, the ships’ engines were removed and replaced to provide greater efficiency, better environmental performance, and extended range for the vessels. The new Wärtsilä engines will run on distillate fuels for compliance with the 2020 sulphur cap regulations.
“This successful technical cooperation with Wärtsilä has enabled our two companies to achieve a successful renovation and the smooth functioning of the joint project,” says Andrew Toso, Deputy Director, Services, Fincantieri. “As the technical partner for this very large conversion project, it is extremely satisfying to have it concluded in a way that meets all the objectives. The renovations represented the largest portfolio of products and systems that we have ever assembled for a single service project. We have worked closely with Fincantieri for a number of years, and this project will certainly strengthen our relationship,” says Ivan Catalfamo General Manager Project Sales, Wärtsilä.
“Our thanks to both Wärtsilä and Fincantieri for their completion of a complex remodel that turned out beautifully. The stretching and renovation of these three all-suite yachts not only expands our guest capacity from 212 to 312, it also upgrades our environmental sustainability and operating efficiency, all of which are important to us,” added Chris Prelog, President, Windstar Cruises.
Wärtsilä’s scope of supply for each of the three vessels included two Wärtsilä 26 main engines, two Wärtsilä 26 auxiliary engines, four Wärtsilä customised selective catalytic reduction (SCR) systems for emissions control, gear boxes, power take-off solutions, and controllable pitch propeller control upgrading. Wärtsilä also re-engineered the alarm, monitoring and automation system, and the power management system, as well as retrofitting the existing on-board systems. Extensive renovation work was also carried out to the entire electrical and automation network.
World-wide attendance at Remontowa
Containerships from almost all over the world regularly call at Poland’s Remontowa Ship Repair Yard, Gdansk. During this year (2021), there have already been some 12 containerships repaired. During September last year, two record-breaking vessels of this type left the yard.
The first of these was NSB Group’s 79,501 dwt Buxcliff (300 m x 40 m). She is one of the longest ships ever repaired at the yard and the largest drydocked at Remontowa. The Buxcliff entered the yard’s largest floating dock. As always with the drydocking of any ship in Remontowa - the stability, buoyancy and strength calculations preceded this operation. In addition, to ensure that we handle the 300 m ship safely, we carried out a finite-element method analysis. It helps to determine the distribution of forces affecting both the hull and the floating dock precisely. The reason for the containership’s visit was a special survey. The associated scope of work included steel replacements, maintenance of the hull and holds, and container lashing equipment.
The shipyard workers also repaired 40 hatch covers, each weighing several dozen tonnes. But first, they dismantled and transported them ashore using a Remontowa-owned floating sheerleg, repaired quayside, transported again by the crane, and re-installed on-board the ship. The shipyard also gave the engine room a thorough face-lift. The scale of this project is best shown by the numbers involved: • 1,000 m2 of insulation and renewed 10,000 m2 of surface in the engine room. The yard also replaced around 200 tonnes of steel and exchanged 1.5 kms of a rubber channel with the seal. • The yard grit-blasted 15,000 m2 of hull surface and painted 100,000 m2 of ship surface, coated four times!
The second box ship was Tsakos Conbulk Services (TCB)’s 51,060 dwt Irenes Resolve (257 m x 32 m). The Tsakos Group is one of the largest Greek shipowners who has previously entrusted ships to be serviced at Remontowa. In the early days of the COVID-19 pandemic in 2020, the yard efficiently repaired the 39,382 dwt containership Irenes Remedy.
Work involved on the Irenes Resolve included extensive work on her propulsion system’s components, along with standard inspections of the bottom-outboard fittings and many others. After dismantling and removing the propeller, the shipyard workers checked and verified the condition of the shaft cone. While in the dock, the ship underwent maintenance, grit-blasting and coating of the hull. In addition, steel replacement was completed in the tanks and holds. As was the case with the Buxcliff, almost all hatch covers were reconditioned on the Irenes Resolve. The hatch covers, each weighing some 32.5 tonnes, were dismantled and transported to the shipyard quay. The ship was also retrofitted with a BWM system supplied by Greece’s Erma First. First, the yard specialists prefabricated pipelines for the BWM system, then mounted on the ship and connected to the seawater system.
SORJ