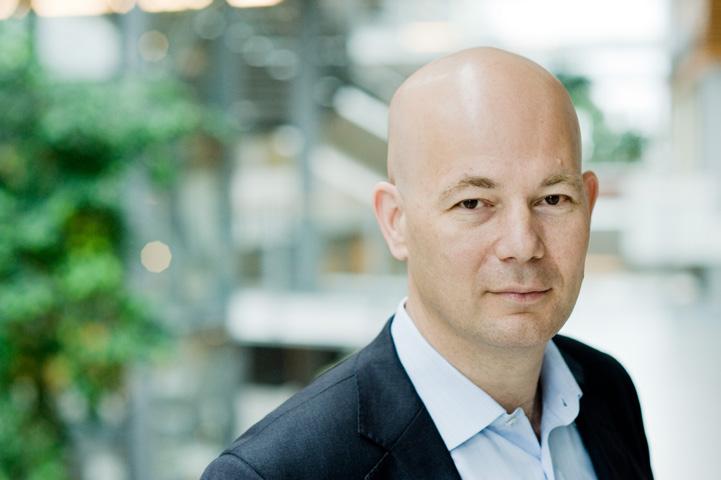
7 minute read
Electrical Repairs
Heerema contract for Bakker Sliedrecht
Holland’s Bakker Sliedrecht will electrify the crane vessels Thialf and Sleipnir, owned by Holland’s Heerema Marine Contractors, so that they can be powered with green shore power. Wind turbines at the quay of the Caland Kanaal in Rotterdam generate this sustainable energy. The shore power connection allows the vessels to turn off their diesel generators, which significantly reduces noise and CO2, nitrogen, sulphur dioxide and particulate matter emissions.
Advertisement
The electrification of the vessels is part of a shore power project, in which, in addition to Heerema, power company Eneco, the Port of Rotterdam Authority and the City of Rotterdam are also participating.
As part of the project, nine modern wind turbines with a total capacity of 27 MW will replace 10 existing wind turbines on the headland at Rozenburg. Since August, the project consortium has been building a socalled e-house on the quay near the canal. This is a gigantic socket that can supply 20 MW (2 x 10 MW) of green wind energy.
The offshore company’s Thialf and Sleipnir are the largest crane vessels in the world. About 400 people can live and work on-board. During the winter period, the crane vessels are regularly moored in the Caland Kanaal in Rotterdam, for maintenance or in preparation of projects at sea. Then all on-board facilities are powered by diesel generators. By connecting the ships to sustainable shore power from the new e-house, they can be turned off. That saves the amount of emissions as from 5,000 diesel cars. CO2-emissions into the air are reduced with 15,000 tonnes and the vessels produce hardly any noise. Heerema will reduce its CO2footprint with the project.
In order to use this sustainable shore power, Bakker Sliedrecht is carrying out various adjustments on-board. Bakker Sliedrecht will, among other things, supply the required transformers, shore connection switchboards and interface to the existing power distribution system. Bakker Sliedrecht will also expand the existing installations and switchboards and install the low and high voltage cables. The voltage must be converted from 11 kV to 4.16 kV. All new equipment will be installed on-board the Thialf early next year. After that the work at the Sleipnir will start. That crane vessel is brandnew, which is why fewer electrical adjustments are required there and the work package is less extensive.
Heerema consciously opted for Bakker Sliedrecht. “We have a long-term relationship together. We are Heerema’s preferred supplier and have supplied significant parts and equipment for the crane vessels, varying from switchboards to generators and propulsion systems,” say Project Manager Andy Waterstreet and Account Manager John Hollemans of Bakker Sliedrecht. “Now we are delivering the shore supply switchboards on-board so that the crane vessels can actually use the sustainable electricity from shore.”
The construction of electrical infrastructure on vessels and land installations is a specialty of Bakker Sliedrecht, whether it concerns high, medium or low voltage. In addition to Heerema’s crane vessels, more ships and companies in the port of Rotterdam will be able to use the sustainable shore power in the future. In these projects Bakker Sliedrecht can also play a part.
Høglund’s Børge Nova
Remote installation and commissioning of a full system during COVID-19
By Børge Nova, CEO of Høglund Marine Solutions

The Sleipnir (right) and the Thialf at anchor in the Caland Kanaal near Rotterdam
“The events of 2020 presented a significant challenge for Norway’s Høglund engineering teams and forced us to look at how we could develop our processes to also manage remote commissioning and ensure we continued to deliver for our customers. As the world went into lockdown, businesses had to make the sudden adjustment towards remote working, and so did we.
“Working remotely with complex automation systems on-board vessels that typically requires a very hands-on approach at the commissioning stage can be a significant challenge, and this was the situation facing a team of Høglund project engineers in early 2020, when part-way through the job we suddenly had to start working remotely.
“Systems such as the Integrated Automation System (IAS), Power Management System (PMS) and alarm systems are the nervous systems of vessels, carrying their vital signals. Very often, these systems get overlooked despite their criticality for many ship systems and overall performance of the vessel, so remote repair and maintenance is not a standard part of the delivery. Consequently, a software error, flat battery, or bug somewhere in the system can cause a mission critical problem.
“Our existing capability for remote access proved extremely handy during the pandemic, as it provided useful background when the need arose to start installing systems without physical presence.
“Since November 2019, one of our engineer teams had been working on the commission and installation of the Integrated Automation System (IAS), Power Management (PMS), Cargo Handling (CHS) and Ship Performance Monitor (SPM) for a series of six new 50,000 dwt tankers. As we entered 2020 and COVID-19 started reaching more countries, Vietnam – where the yard was located - went into strict lockdown and our engineers could no longer be physically present at the yard to do the job.
“This unprecedented situation forced us to think differently and develop further ways we could work remotely and avoid derailing the overall plan behind these newbuilds.
“Being separated from the hardware that we are working on was not an entirely new concept to our engineers at Høglund, as we offer remote servicing capabilities as part of our support package when we supply automation technology and software to our clients. These capabilities allow our shore-based engineers to access automation systems and software, and when random faults do occur, they can easily diagnose the issue and support the crew. However, we had never installed and commissioned our automation solutions 100% remotely, so we had to rely heavily on our existing remote servicing capability.
“We used online tools to gain virtual presence at the yard, work closely with the engineers on-site, and access and control the software within the systems. These new remote arrangements were instrumental in allowing us to work with the team at the yard on carrying out this complex task.
“Throughout the summer of 2020, at the height of global travel restrictions, Høglund managed to deliver, install and commission the IAS, PMS, CHS and SPM on the tankers – all remotely. Additionally, this significant feat was achieved despite the added complexity created by the major time difference from the teams being at opposite sides of the world, alongside the language barriers.
“With the project finalised and the systems successfully installed and commissioned, the critical hardware onboard the vessel is now in the hands of reliable, modern and effective automation technology. The day-today management of the vessel is also easier for the crew and operators, and the level of complexity of the command-and-control interfaces of essential vessel hardware has substantially decreased. Furthermore, thanks to our arrangements to improve accessibility to integrated and seamless operational data, owners and operators can now gain insights into vessel performance and pursue efficiency gains.
“By drawing on previous remote engineering experience, Høglund managed to complete the installation of the essential automation hardware and deliver three of the six newbuildings for the customer remotely. The collaboration with our partners at the yard was a crucial part of this project and the yard team’s contribution played a key role in the successful completion of the commissioning.”
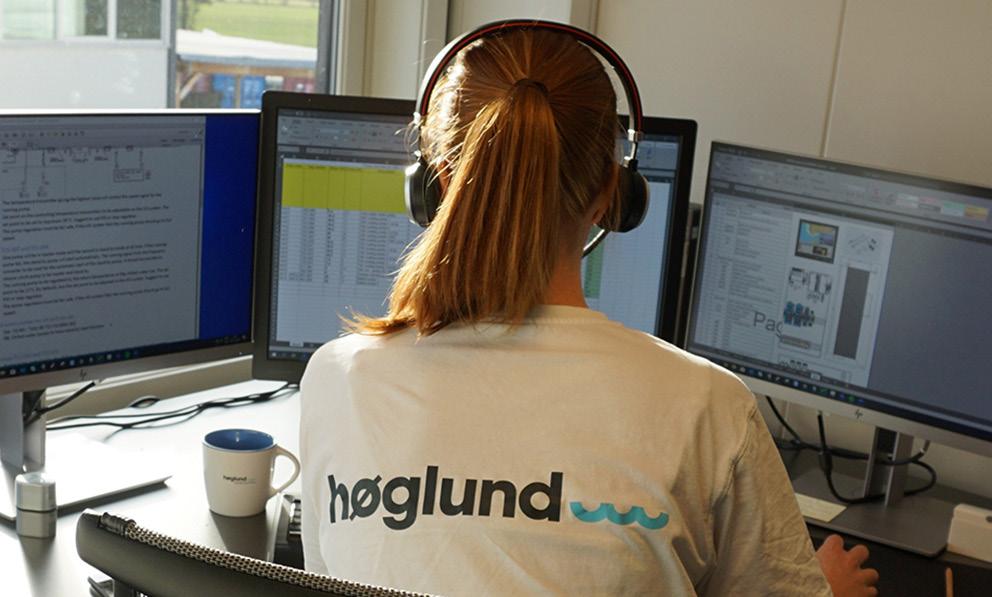
Høglund uses online tools to gain virtual presence at a shipyard
SORJ
Brian McConville is awarded a CBE
Owner and Chairman of MJM Group, Brian McConville, has been awarded a CBE in the Queen’s New Year Honours List, recognising him for his services to both the economy and charity in Northern Ireland.
On hearing the news Brian said, “I am honoured and privileged to receive a CBE in the New Year Honours List. It is very much a shared recognition of the MJM family and a welcome and positive beginning to 2021, particularly after the challenges of 2020.”
Brian started his business more than 35 years ago in Rathfriland, Northern Ireland. The organisation remains in this family ownership with the second generation also working in the business. MJM Group is a globally recognised leader in the marine and land-based construction sectors comprising MJM Marine, Mivan Marine and Topglass.
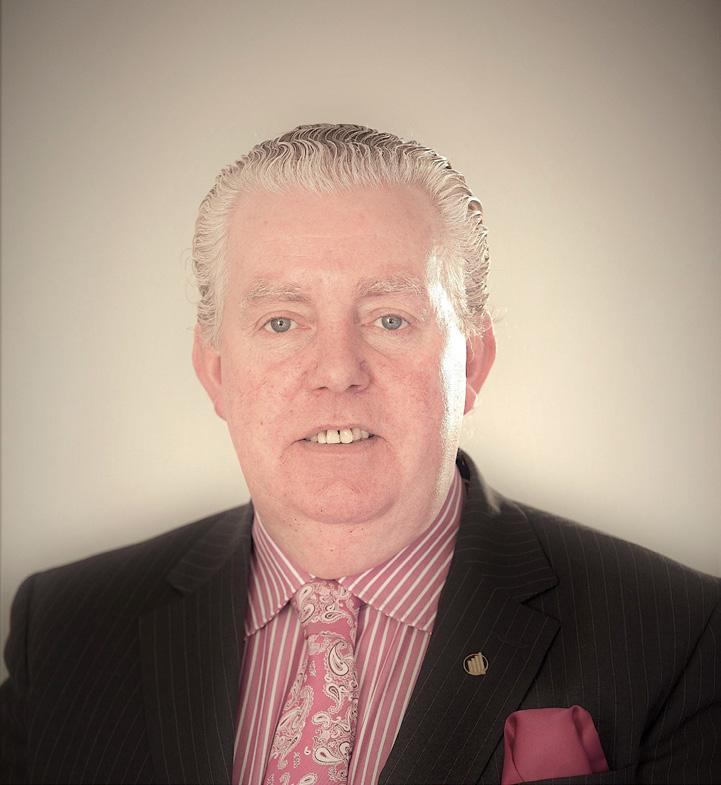
Brian McConville