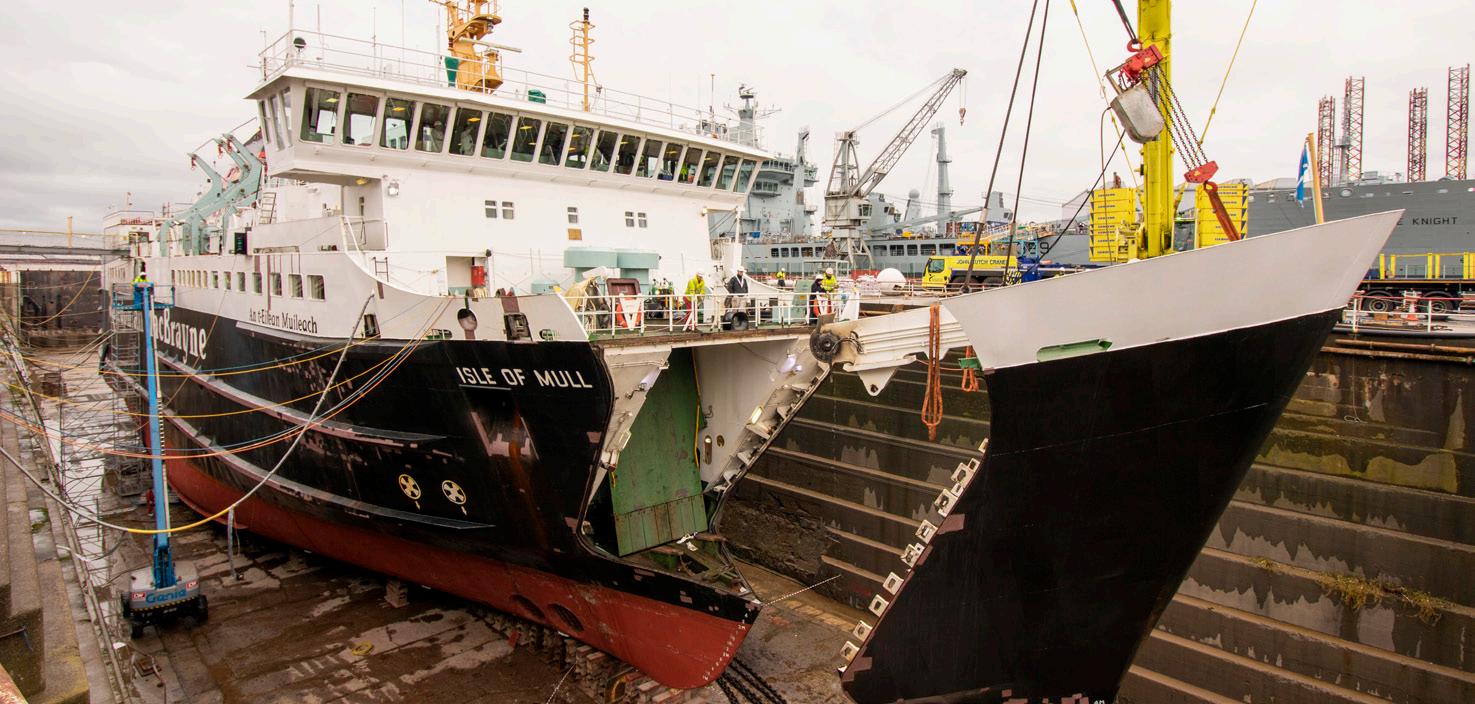
36 minute read
FRONT COVER
Repairs
Work on the bow visor of the Isle of Mull at Cammell Laird
Advertisement
Atlantic & Peninsular Marine Services operates two repair companies in the UK – A&P Group and Cammell Laird. A total of 42 extraordinary drydockings and unscheduled repairs contributed to A&P Group’s strong performance in 2020 - despite the challenges of operating during a pandemic.
Boskalis’ 8,234 gt offshore construction/ diving support vessel Rever Polaris, renamed Boka Polaris , visited A&P Tyne in November for hull repairs and upgrades. Plates were templated, profiled and rolled at A&P’s on-site fabrication facility and a number of smaller welds were also carried out. New structural members were also profiled and fitted to the tanks to provide additional stiffening.
While the vessel was in the drydock, other works included a full repaint of the hull, sea chests and vertical sides; replacement of the umbilical supports in the dive bell; manufacture of new hot water pipes and removal of the external stairs for steel repairs.
Prysmian’s 9,778 gt offshore supply ship Normand Pacificalso visited A&P Tyne in 2020 for a complex blend of fabrication, mobilisation and marine work. Due to a tight schedule, A&P began the manufacture of the new 54 tonne mezzanine structure, stairs and grillages on-site 28 days prior to the vessel’s arrival.
Mobilisation involved multiple contractors on site and stringent consideration of COVID-19 guidance. A number of significant lifts were involved in order to ready the mezzanine for the addition of deck grating, handrails and cable trays, and its subsequent installation on the vessel.
The team also assisted with the installation of the azipod thruster and a new 120 tonne A Frame lifting system for the vessel’s Searex ROV. The A Frame lift involved all three of A&P Tyne’s dockside cranes and took a full day to complete. Once complete, hydraulic and electrical work was undertaken and more than 300 hydraulic hoses on the offshore crane were replaced.
At A&P Falmouth, the team delivered a comprehensive programme of major steel repairs for Kahrs Bereederung’s 9,313 dwt containership Samskip Expressafter she ran aground while sailing to Ireland. A 76 day stay at A&P Falmouth involved extensive repairs to the shell plating and several areas of the ship’s ballast pipework. A&P fabricated temporary support pillars to protect the structure of the vessel throughout the repairs and ensured that work on adjacent areas didn’t take place simultaneously. In total more than 60 tonnes of steel was replaced in seven different areas of the hull.
Meanwhile, A nine day project to replace bow visor hinge pins and bearings for CalMac Ferries’ 4,719 gt ro/pax ferry Isle of Mull has been completed by UK’s Cammell Laird, Birkenhead.
Delivered as part of the vessel’s annual survey, the project involved a multi-disciplinary approach from Cammell Laird’s planning, technical and lifting teams in order to remove the vessel’s 33 tonne bow visor and replace its hinge pins and bearings. The programme involved a series of heavy lifts using 200 tonne jacks and a 350 tonne mobile crane to transfer the bow visor to rigging on the bottom of Cammell Laird’s No 6 drydock.
Following replacement of the bow visor’s main hinge pins and bearings, Cammell Laird reinstalled the bow visor and carried out a series of inspections and water tests to ensure that seal integrity had not been compromised.
Cammell Laird has recently secured a new four-year contract for the annual maintenance and dry docking of CalMac’s five largest vessels, which provide an essential service between the Inner and Outer Hebrides and the Scottish Mainland. All five ferries will dock annually at Cammell Laird, with the first vessels arriving in early 2021.
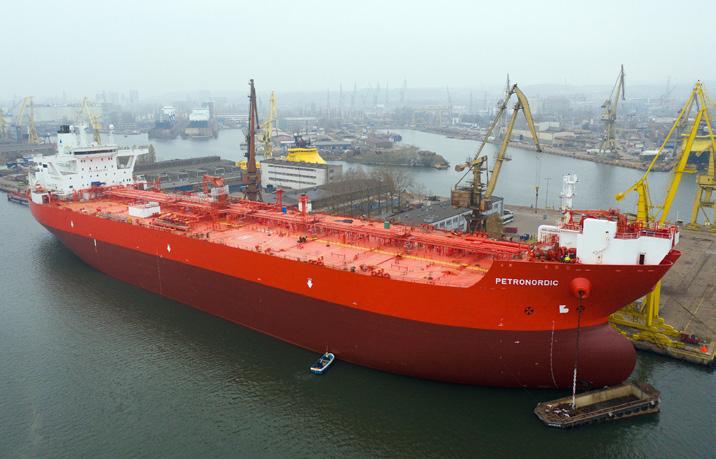
Busy times at Remontowa
Nissen Kaiun’s 14,022 dwt reefer vessel Star Care is the second ship belonging to this Japanese shipowner to be drydocked at Poland’s Remontowa, Gdansk this year. Work on both vessels has included the installation of a scrubber system. This follows the successful repair of some four ships from Nissen Kaiun drydocked in 2019, work on these vessels also including the installation of BWM systems.
Teekay Shipping’s 92,995 dwt shuttle tanker Petronordic returned to the yard for a CAP Survey of 12 cargo tanks (plus two slop tanks). The yard also repaired the bow loading system. In addition, it carried out an overhaul of engine room equipment, as well as pipe work and hull maintenance with painting work. During Petronordic’s stay in the yard, Teekay, whose logo has so far appeared on the tanker’s funnel, was rebranded to Altera reflecting the change in the ownership structure. In the first half of November, the repair of OSM Shipmanagement’s 20,209 gt car carrier Viking Constanza was completed, and in the same month her sistership City of Oslo called at Remontowa. OSM Shipmanagement manages these vessels for Norway’s Gram Car Carriers. The scope of repair works on City of Oslo was very similar to the work carried out on-board the Viking Constanza and included bow thruster
The Petronordic completes repairs in Remontowa
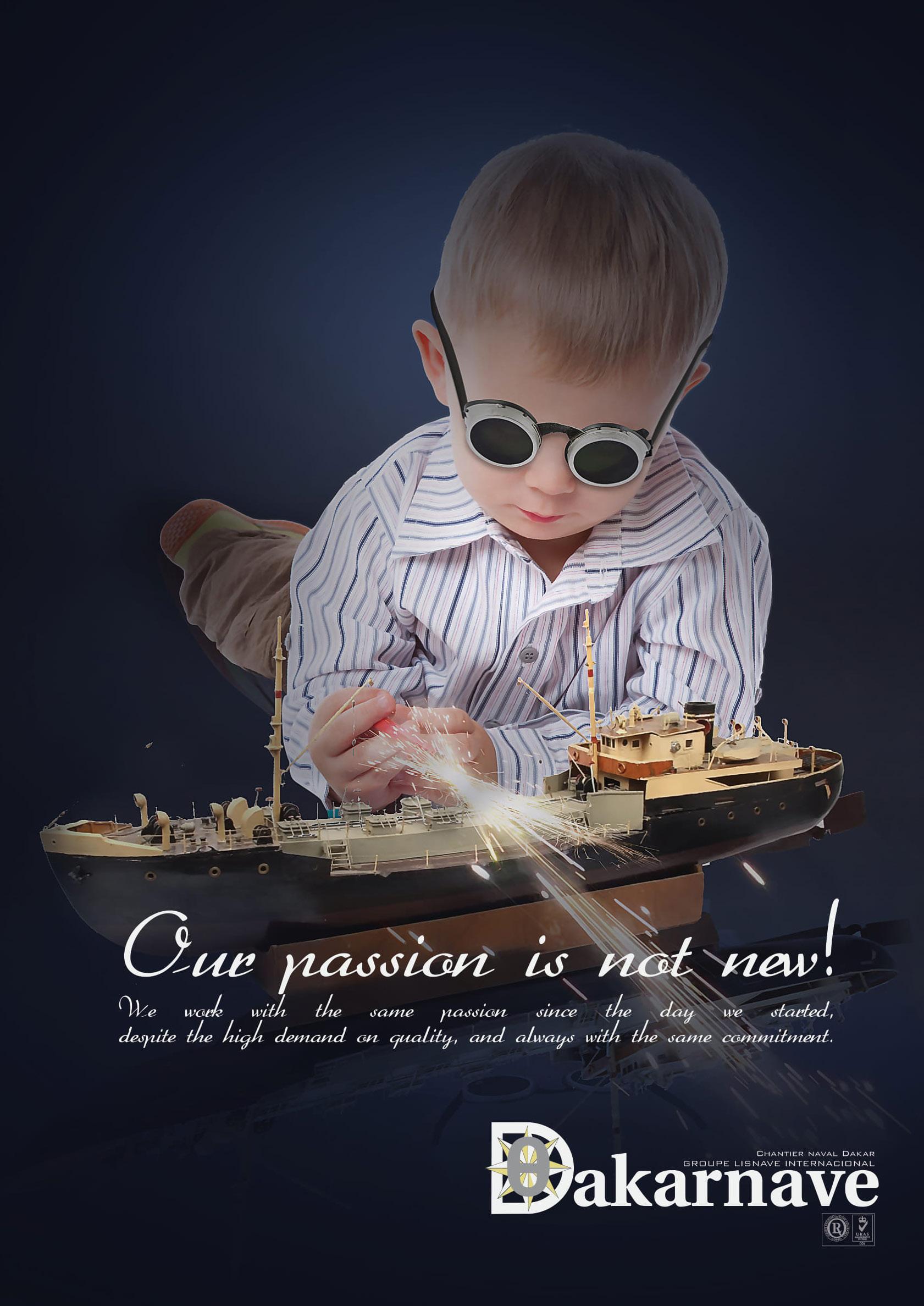
overhaul and numerous steel renewals in the tanks. Hull treatment was also carried out in the drydock. An important part of the schedule was also pipe work, related to the future installation of BWM systems.
At the beginning of the New Year, the repair of another car carrier managed by OSM Ship Management was carried out by Poland’s Remontowa, Gdansk. The ship involved was the 39,362 gt Viking Amber. Viking Amber is a much longer and higher unit, hence the scope of work differed in many respects from previous vessels of this operator - hull treatment was performed in the drydock and electrical and steel work (mainly in one tank) was carried out.
The main work on-board Brittany Ferries’ 35,592 gt ro/pax ferry Mont St. Michel was the Alfa Laval BWM system installation. Other repair work carried out included the overhaul of the four main engines and one auxiliary engine. There was also a large scope of steel work in various parts of the ship, as well as pipe work, electrical work, boiler and pump inspections. Remontowa also carried out hull maintenance, funnels and car decks – the yard cleaned a very large number of ballast, fuel and oil tanks, and numerous technical rooms were also subject to conservation. Both stabilisers were also overhauled.
Finnlines’ 45,923 gt ro/pax ferry Finnstar was in Remontowa at the turn of a year. Work carried out included extensive painting and drydock work, cleaning of 14 tanks, cross over pipe, ventilation and exhausts overhaul, involving over 12 fans. Additionally, extensive pipe- work was involved. Remontowa replaced the entire insulation for four scrubbers and carried out work related to the replacement of 70 lashing pots on the lowest cargo deck.
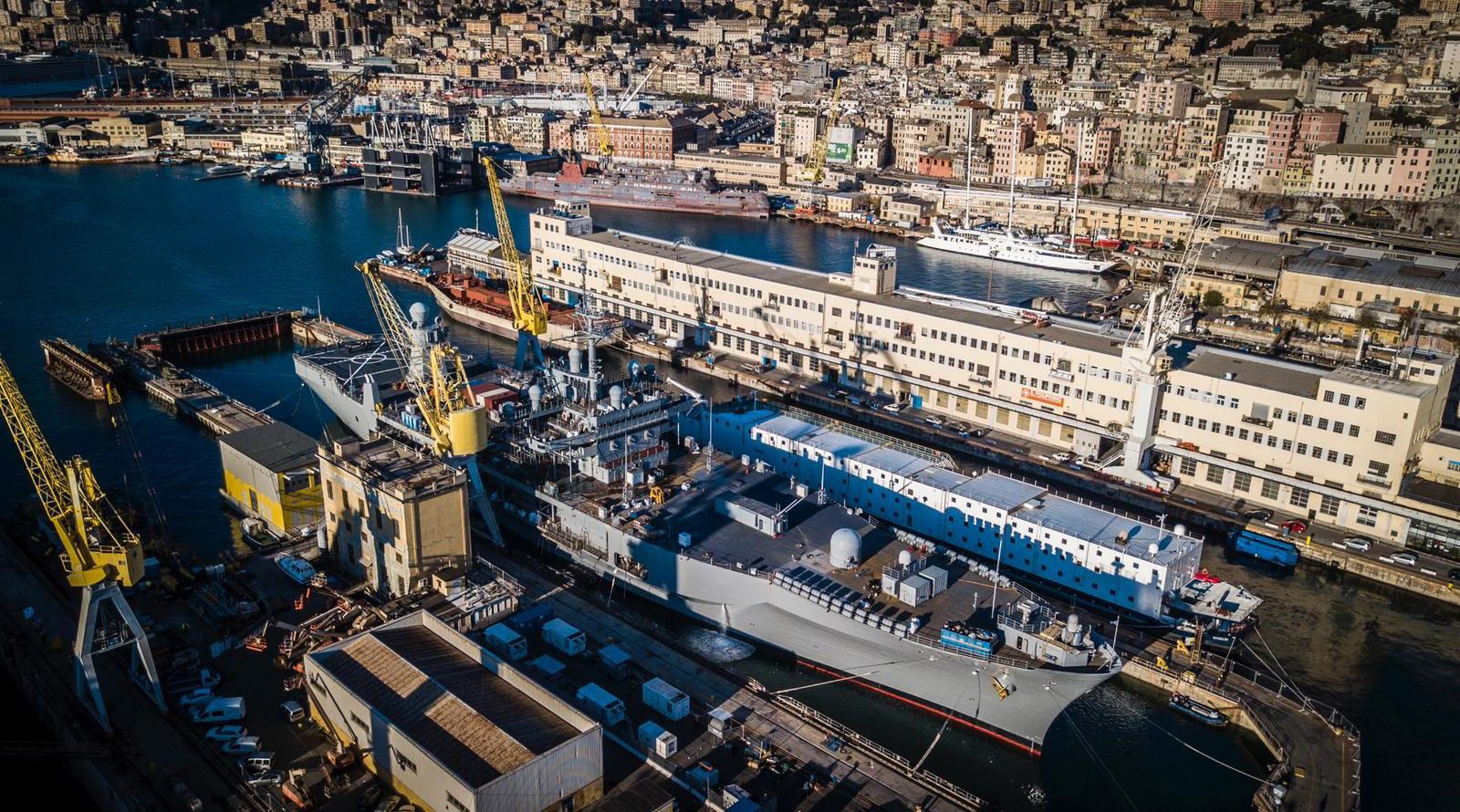
Navantia busy during the start of 2021
Spain’s Navantia Shiprepairs’ Ferrol Estuary started the New Year with Kitaura Kaiun’s 65,935 dwt containership NYK Meteor, which was drydocked in Dock No 3 in Ferrol, and Sinokor Tanker’s 126,750 m3 LNG tanker Bering Energy continued alongside awaiting a second drydocking prior to its final delivery, once its re-activation process has been undertaken.
Navantia Shiprepairs’ Cadiz Bay focused its activity on the drydocking and repair works of five commercial vessels, three Spanish naval vessels and a newbuilding naval unit. The yard continued with the drydocking of Allseas Marine’s 127,435 dwt pipe-layer Solitaire, which is still undergoing steel repairs and surface treatment work. ArmasTransmediterrenea’s 26,375 gt ro/pax ferry Marie Curie underwent hull surface treatment and general drydocking works. Spain Guardia’s patrol boat Rio Segura had hull surface treatment works and general drydocking work along with pipe renewals and propulsion system works.
Carnival Cruise Line’s 70,367 gt cruiseship Carnival Fascination returned to the yard to have her name changed to Century Harmony for her new owners – Century Harmony Cruises Ltd, and some final work after being sold, and Carnival Cruise Lines’ 101,509 gt Carnival Victory was also in the yard.
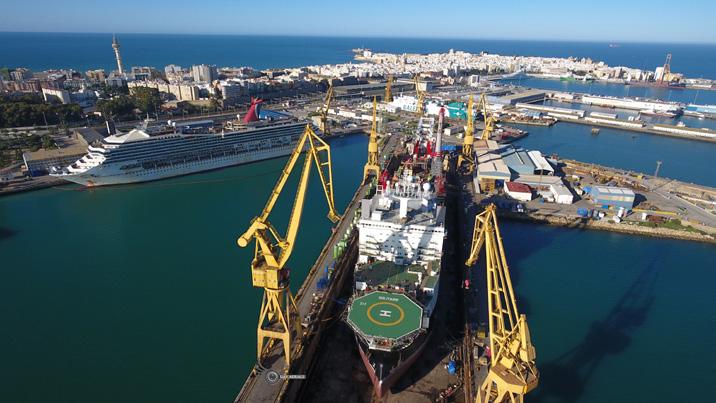
The Solitaire in Navantia Cadiz The USS Mount Whitney in drydock in Genoa
US Navy contract completed by San Giorgio del Porto
The USS Mount Whitney refit project was completed in December 2020 at Italy’s San Giorgio del Porto, Genoa, part of the GIN Holdings Group. After more than four months the vessel has left Genoa for Gaeta where she has already resumed her normal service activities. The vessel is one of two Blue Ridgeclass amphibious command ships of the US Navy and is the flagship and command ship of the US’ Sixth Fleet. USS Mount Whitneyalso serves as the Afloat Command Platform (ACP) of Naval Striking and Support Forces NATO. The project in numbers: • 18,500 tonnes weight, 189 m long by 33 m wide • 300,000 hours worked to complete the work • 200 workers (average) engaged each day on-board the ship • 148 days laid up, 109 of which were in drydock • 33 tonnes weight, 15 m length and 570 mm diameter (measurements of the stern tube shaft), removed, refitted in drydock, transported to the yard’s workshop, machining the sleeves and the flange • 33 tonnes weight, 15 m length and 600 mm diameter - propeller tail shaft characteristics aligned in the workshop with stern tube shaft, installing new fitted coupling bolts • 28 tonnes weight and 6 m diameter - measurements of the disassembled and reassembled rudder and propeller • 2,000 m2 - flight deck area restored and certified.
Meanwhile, Saipem’s 26,600 displacement tonnes field development ship Saipem FDS has arrived in San Giorgio del Porto for maintenance work. With the arrival in Genoa of the Saipem FDS in the shipyard, San Giorgio del Porto has consolidated its collaboration with Italy’s Saipem. The Saipem FDS is a multipurpose vessel capable of being employed

The Clansman arrives in Liverpool
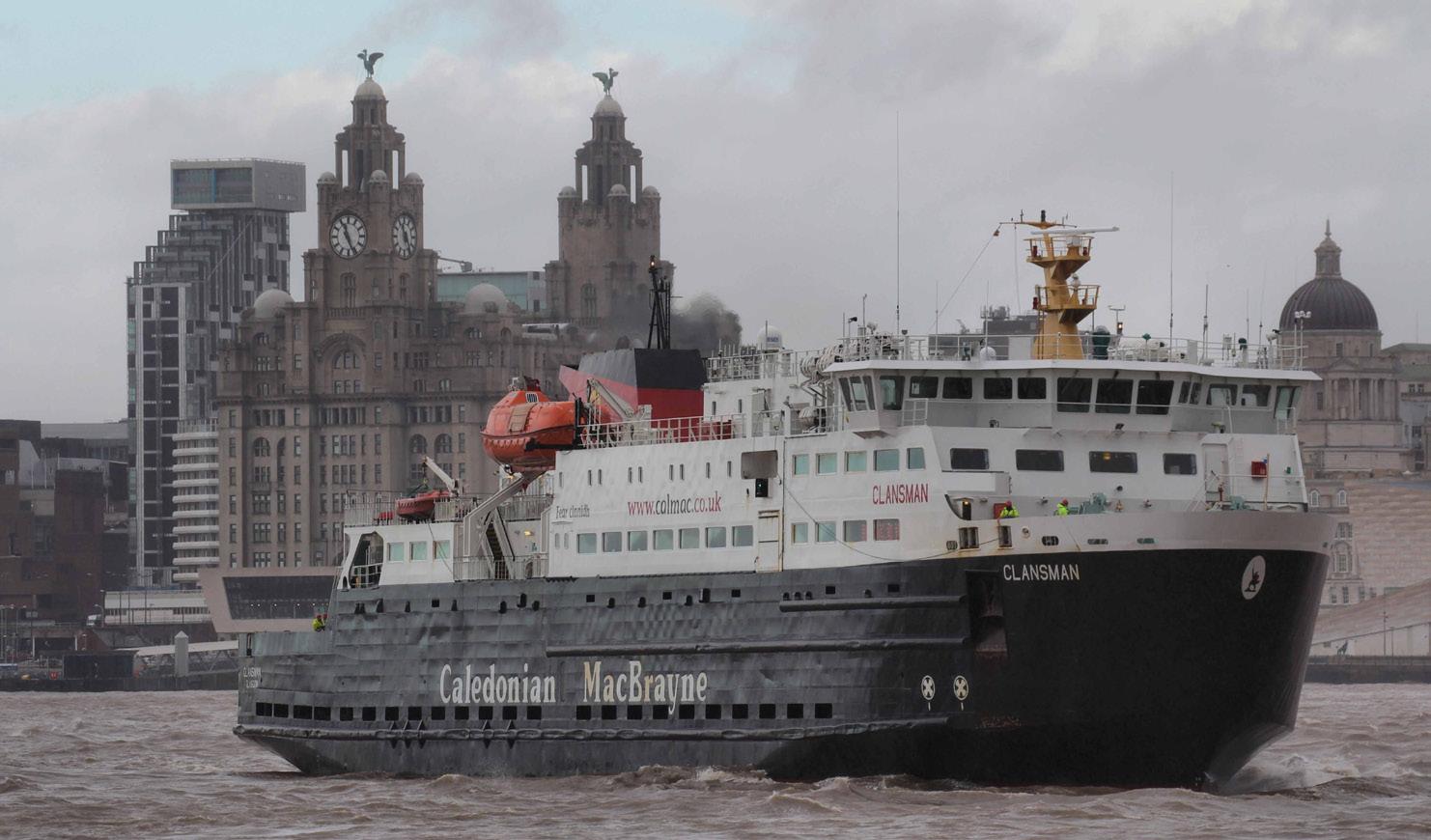
with great versatility in the development of offshore fields in ultra-deep waters.
During 2012, she was in Chantier Naval de Marseille (CNdM), also part of the GIN Group. The current project in Genoa will include mechanical and carpentry maintenance work, part of which will be carried out in the drydock and part in the basin, with the employment of almost 200 people/day including technicians and engineers. The work on the ship will be completed in about three months.
CalMac contract for Cammell Laird
UK’s Cammell Laird Shiprepairers & Shipbuilders, Birkenhead has secured a new contract with one of the UK’s largest ferry operators, CalMac Ferries, for the annual maintenance and drydocking of five ro/pax vessels in its fleet.
CalMac Ferries has awarded Cammell Laird a four-year contract with the option to extend it for two further one year periods. The contract includes the 5,499 gt Clansman, the 8,680 gt Loch Seaforth, the 3,504 gt Lord of the Isles, the 5,626 gt Finlaggan and the 5,506 gt Hebrides – all of which provide an essential lifeline service from the Inner and Outer Hebrides to the Scottish Mainland. All five ferries are expected to dock at Cammell Laird between October and March each year, with the first vessels arriving in early 2021.
Neil Harden, Commercial Director at Cammell Laird Limited said, “We have enjoyed a long-standing relationship with CalMac Ferries, but this is the first time we’ve been awarded a contract of this length. This is particularly significant as it allows us to undertake more long term and strategic planning, which in turn will deliver greater cost efficiencies, value and vessel availability for CalMac.
“We have the optimum facilities to support CalMac’s fleet with four docks to suit the larger vessels, plus the afloat berthing facility in the wet basin is used for MCA life raft deployments and running engines under load after major overhauls.”
Julie Philpott, Director of Asset Management from CalMac Ferries added, “The team at Cammell Laird demonstrated a strong knowledge of our vessels and scored particularly highly on the technical and quality aspects of their competitive contract tender. We look forward to continuing with our long-standing relationship with the team at Cammell Laird. The longer term contract will afford us significant benefits, all of which help to maximise vessel availability and continue offering the best service for our customers.”
Successful period at Metalships
Spain’s Metalships, Vigo, has managed a successful period of carrying out repair projects during the COVID-19 pandemic. According to Metalships’ Aroa de Celis “Our workforce is doing a commendable job. The challenge during this current situation is- prior to any vessel berthing at Metalships - strict measures must be followed as part of the mandatory obligation from the authorities. All the employees must do a weekly COVID-19 test because this is the way to work correctly. At Metalships there are several vessels currently in the yard for maintenance work, as well as unprecedented number of dredgers.
Metalships recently carried out repairs to two TSHDs - Dragus’s - 5,000 m3 Victor Horta, afloat for seven days and in drydock for 20 days, and DEME’s 1,045 m3 Jose Duarte, which underwent grounding damage repairs on one of the yard’s slipways for some three weeks.
Aroa de Celis explains why DEME chose to rely on Metalships to prepare its vessel for a speedy return to service. “They wanted a partner who could provide quick and reliable repair works. From our perspective, we are delighted to be able to strengthen our relationship with such an important client”.
Meanwhile, Jose Duarte, registered in Portugal and built in 2018, is 70 m long and 11 m breadth. The vessel was affected by bad weather with the propeller badly damaged. The vessel is being accommodated in the slipway for
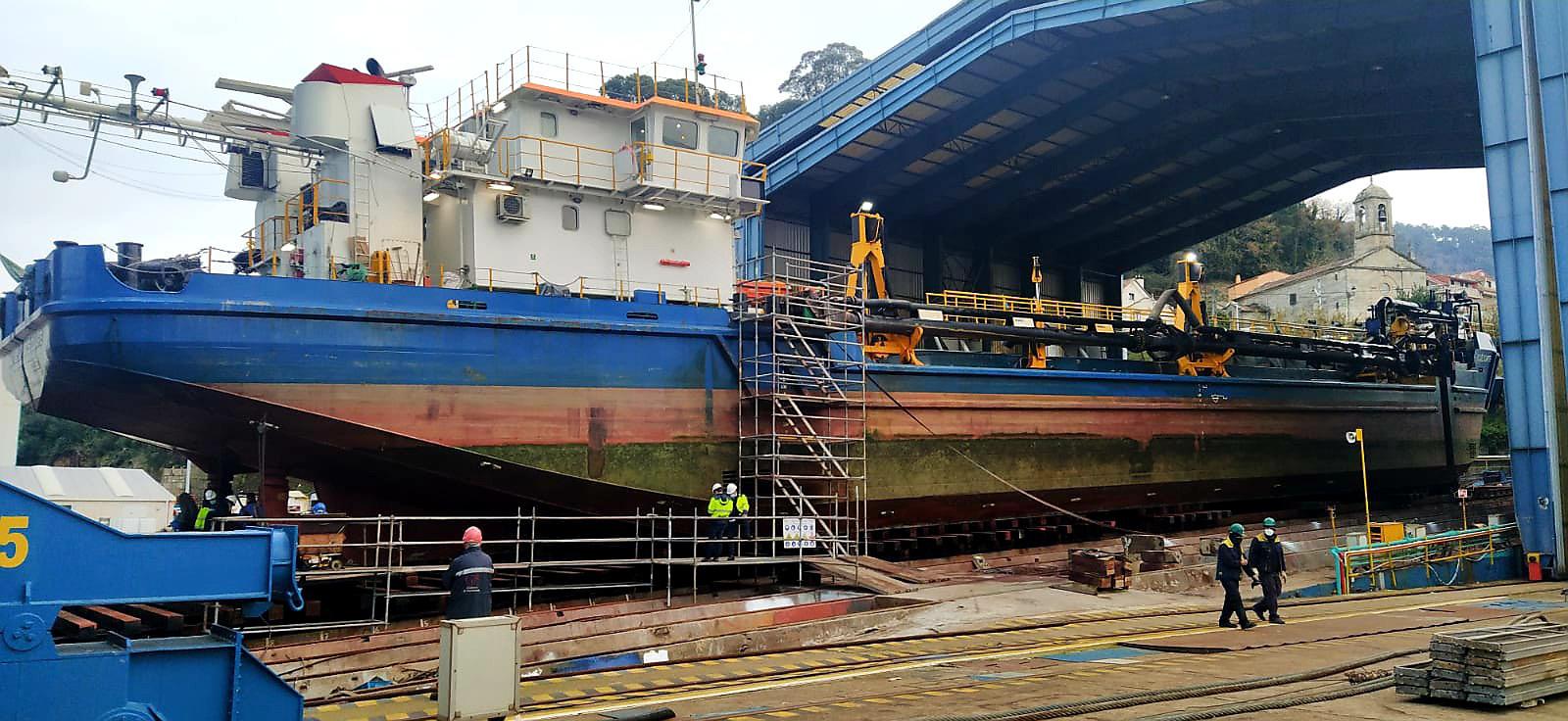
The Jose Duarte on the slipway at Metalships

The Ghasha and Al Khaznah in HRDD
some weeks.
Simultaneously, the yard has continued with the afloat repairs of Spanish Government’s 1,401 gt Vizconde de Eza, one of the most sophisticated fisheries and oceanographic research vessels in the world repairs. She has been in the yard for some two months.
The final phase of construction of Sea Cloud Spirit for the Germany’s Sea Cloud, which owns two sailing ships for exotic luxury cruises. The three-masted sailing cruiseship is in the outfitting quay continuing the remaining work before being delivered to her German Owner.
LNG tanker repair/conversion work at HRDD
China’s HuaRun DaDong Shipyard (HRDD) has, since the COVID-19 outbreak, strengthened its epidemic control systems and implemented additional strict safety protocols to ensure the shipyards normal operation. HRDD has successfully reached its target in 2020 thanks to close and transparent co-operation between its workers, shipyard management and its valued customers.
HRDD is especially proud of the successful execution of repairs and retrofits of eight LNG tankers of both membrane type and spherical type. In addition, HRDD completed a LNG tanker to FSRU conversion project (See Front Cover). All the projects were completed and redelivery to owners was on-time and with good quality. The 173,400 m3 LNG tanker Sevilla Knutsen, which is operated by the Norway’s Knutsen OAS Shipping, was repaired in HRDD in May/ June 2020, which included the vessel’s second special survey. The main work scope included overhaul of cargo pumps/spray pumps, cryogenic valves, safety equipment overhaul, cargo tank global testing, compressor motor overhauling, dual fuel generators, reduction gear overhauling, installation of a BWM system as well as application of hull silicon paint. The vessel’s two sisterships Ribera Del Duero Knutsen and Valencia Knutsen arrived in HRDD in July and September 2020 respectively to also undergo second special survey dockings including BWM retrofits.
The 172,000 m3 LNG tanker SCF Mitre, which is operated by SCF Management was repaired in HRDD in September 2020. It was

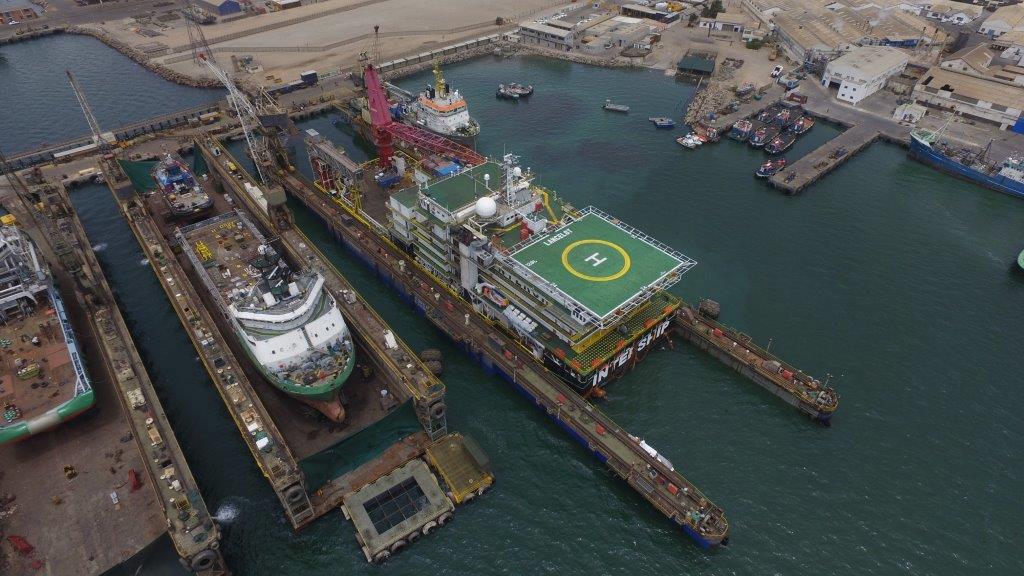
The accommodation barge Lancelot (right) in Namdock
the vessel’s first special survey, and the work scope was mainly overhauling of the cargo pumps/spray pumps, cargo tanks cryogenic valves and safety valves, cargo tank global testing, five sets of DF engines overhaul, as well as boiler maintenance and marine systems.
The most critical project of 2020 was the FRSU conversion, which involved the conversion of the 138,105 m3 GTT membrane-type Golar Viking to a FSRU unit - FSRU LNG Croatia. The main work included Regas Module installation, vent mast fabrication and installation, sea water heating system, cryogenic pipe modifications, BOG compressor overhaul, LNG feed pump modifications, cargo tank safety valve modifications, gas dome modification, cargo tank opening for inspection, cargo containment system partial repairs, cargo pump maintenance, 16.5 MW power module fabrication and installation, etc.
The project was commenced in March 2020 and was completed in September 2020. The total conversion period was six months. The FSRU LNG Croatia has now arrived at the terminal on Krk Island in the northern Adriatic Sea offshore Croatia, and has already started operations. The vessel will provide clean energy to the Croatian national grid and the annual delivery capacity will be up to 2.6bn m3of natural gas to Croatian consumers.
In additional, three Moss type LNG tankers owned by National Gas Shipping Company in Abu Dhabi – the Ghasha, Al Khaznah and Shahamah were repaired in HRDD between 2019/2020. The main workscope included high pressure boiler retubing, turbine overhaul, and cryogenic valve/safety valves overhauls, etc.
A spokesman for HRDD said, “With vast experiences of shiprepairs and conversions during the past 25 years, as well as many years of preparations for the LNG tanker repair market, supported by Hudong-Zhonghua and many specialised partners such as GTT (France) and Gabadi (Spain), HRDD is already active and involved in LNG tanker repair business and LNG related conversion projects.
“HRDD is confident in its capacities, skilled workers and the shipyard’s LNG Team to say we are ready to provide professional services for LNG tanker repairs and conversions to shipowners on a world-wide basis.”
During 2020, HRDD completed some 220 shiprepair projects and conversions with a turnover of RMB2.23bn. Among these 220 vessels, were 56 ships for scrubber retrofitting, 109 ships for BWM system installation, five LNG tanker repairs, one FSRU conversion, as well as LNG fuel conversion of a 15,000 teu containership owned by Germany’s Hapag Lloyd.
Offshore contract for Namdock
Namibia’s EBH Namibia (Namdock) is currently busy with a number of repair projects, the largest involving Internships Group Holdings’ 14,217 gt offshore accommodation barge Lancelot. She is scheduled to be in the yard for some 45 days, spending the majority of that time in drydock. The major work scope onboard this vessel has involved coatings, steel work, pipping and propulsion overhauls. She has been working over recent months offshore South Africa.
Also, in the yard were the Namibianregistered fishing vessel Jupiter 1, the 8,222 dwt general cargo vessel Catalina, the 2,593 gt tug/OSV Komodo, the fire-fighting vessel Afri Ekulu, the small fishing vessel Gajaja, and two offshore vessels from France’s Bourbon Offshore - the 3,703 dwt OSV Bourbon Explorer 511 and the 2,293 gt anchor-handler Luzolo .
Strategically located on the west coast of Africa in Walvis Bay, Namibia, Namdock is a leader in the West African shiprepair market and offshore oil and gas sector, having gained global recognition for its extensive dry dock capacities and exceptional client service - even in the face of a global pandemic.
Seville yard gets busy
Spain’s Astilleros Guadalquivir, Seville, started repair work during 2015. Since then, more than 50 vessels of all types have passed through its facilities, especially ferries, tankers, dredgers and general cargo vessels. The dimensions of its drydock (143.5 m x 23.5 m) and the auxiliary dock (150 m), in addition to its location just 200 kms from the Strait of Gibraltar, makes Astilleros Guadalquivir a privileged enclave for shiprepair.
According to a statement by Juan Cuenca, COO of the company, “During the first four years, the workload has remained stable, reaching repair peaks of up to 20 ships in just 12 months, not counting the scrapping of others. However, the current situation, caused by the world-wide pandemic, has slowed down, not only in the shipping sector for repairs, but also shipbuilding. These consequences have been reflected in the activity of Astilleros Guadalquivir.
“However,” he acknowledges, “the improvement in the health situation in the last quarter of the year, the measures adopted by the company and the business meetings held to publicise our facilities have borne fruit. As a consequence, since October 2020, the hiring of personnel and the acquisition of machinery has been restarted, which has allowed expanding capacities and obtaining new contracts.”
The best example of this situation has been the recent repair of Boeckmans’ 2,499 dwt general cargo ship Maremka. At 82.3 m in length, recent work carried out on-board this vessel has included the overhaul of the main and auxiliary engines, the maintenance of the hatches, repairs of the steel tanks, removal of the shaft tail and the installation of a new vocine
The Maremka in drydock
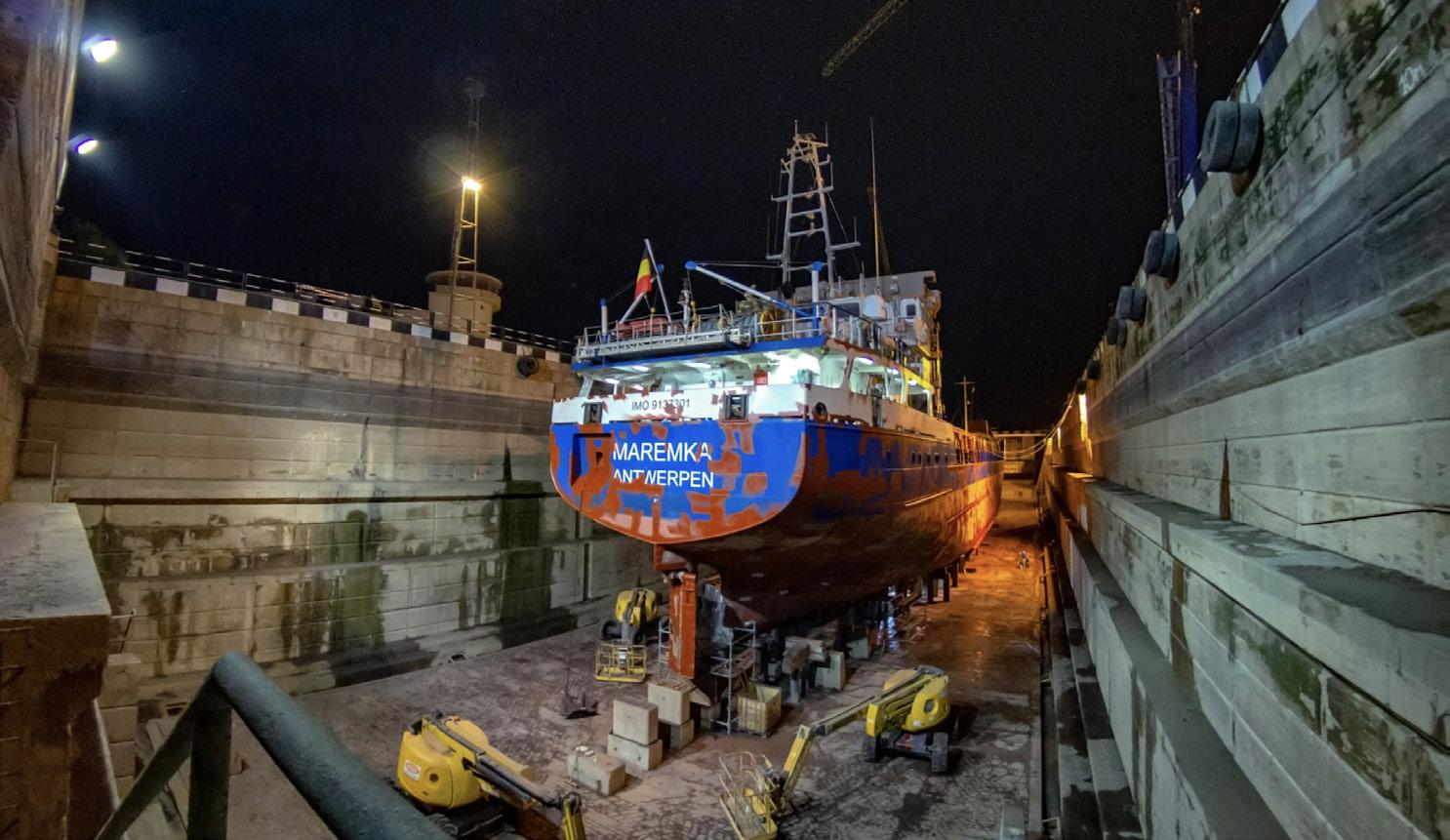
bearing.
The yard is also currently carrying out alongside and drydocking repairs on-board Thun’s Ship Management’s 9,891 dwt cement carrier Nordanhav. At 126.7 meters in length, the yard will carry out major mechanical repairs.
According to the CCO of Astilleros Guadalquivir, Pablo de Celis, “The end of 2020 was slow, but we have started the year with the full occupation of our pier and berths during January and February. Another five projects have already been signed for the next few months. From that point of view, we are very happy that these clients have decided to support Astilleros Guadalquivir when the world market and COVID-19 restrictions are so complicated everywhere.
“However, these changes have helped us to strengthen our collaboration with many companies, and, as a result, our order book in 2021 shows a positive first and second quarter. That said, our squad service, which deals with repairs in all Spanish ports and North Africa is having quite busy months undertaking afloat repairs from many types of ships from Suezmax to small general cargo vessels”.
Detyens report a steady start to 2021
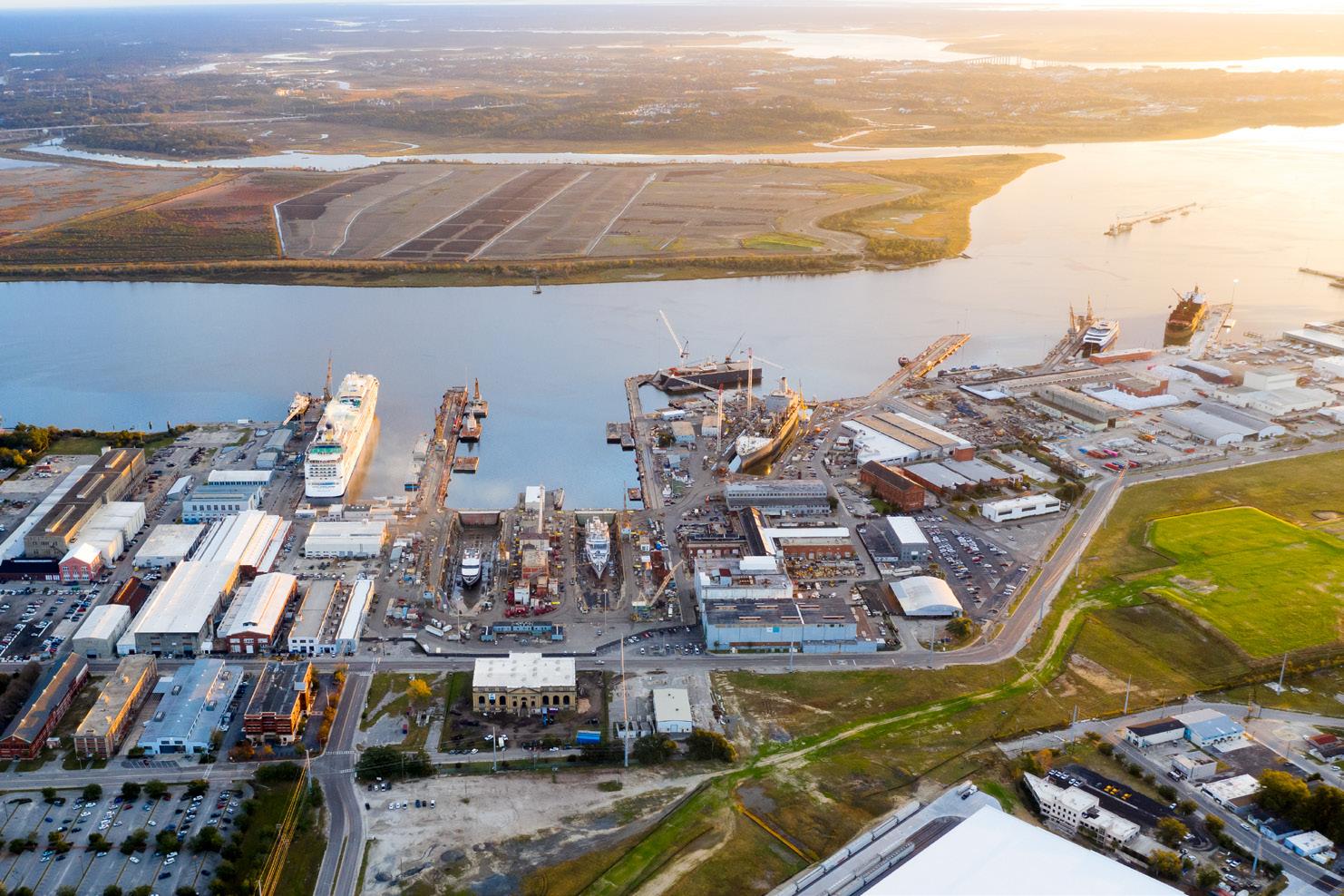
US’ Detyens Shipyard, Charleston, is reporting a fairly slow year during 2020, due to the COVID-19 pandemic. However, there have recently been some projects of note in the yard following a project involving Norwegian Cruise Lines’ 93,530 gt, 2007-built (Jewel Class) cruiseship Norwegian Gem, which spent some time in the yard during December 2020 to replace her five main engine stacks.
Detyens has also recently completed an emergency three day drydocking of USS Vessel Management’s 19,687 dwt, 2008-built automated tug/barge unit ATB Brownsville, the vessel undergoing repairs to her port rudder and starboard and port shaft seals.
Meanwhile, currently in the yard is the USNS Puerto Rico, a US Navy high-speed expeditionary transport vessel. This contract is part of the US$10.9m US Navy repair contract between Detyens and the US Navy, involving an approximate 75 day stay in the yard. Among ships due in the yard during the coming weeks is a Dutra-owned scow barge, Great Lakes Dock and Dredge (GLDD)’s 15,233 kW cutter suction dredger (CSD) Texas and Laredo Offshore Services’ jack-up lift boat Brazos .
Detyens Shipyard operates three graving dry docks and a boat lift. The three graving docks are No. 1 – 189.5 m x 29.5 m, No. 2 – 181.7 m x 29.2 m and No. 5 – 229.0 m x 33.5 m. The boat lift (HLB-1) measures 122.0 m x 24.9 m. The yard operates four tower cranes and eight portal cranes, with various capacities up to 100 tonnes. There are also eight piers for alongside work covering some 2,500 m. The water depth in the yard’s facilities is 10.7 m.
An aerial view of Detyens Shipyard
A good 2020 at Lisnave
Despite the current pandemic, Portugal’s Lisnave, Setubal, successfully completed, during last year (2020) repair projects involving 76 vessels, 72 of which required drydocking operations. Despite a reduction in freight rate levels in the tanker market, the main repair market for Lisnave, it represented nearly 36% of the total number of vessels repaired. The average volume of work for each vessel in routine drydockings suffered only a small reduction.
During 2020, Lisnave continued to be actively involved with the retrofitting of Ballast Water Management (BWM) systems, with the completion of good number of installations from various manufacturers.
Following the trends from previous years, tankers (27 in total) and LPG tankers (14) were the most significant market segments for Lisnave representing a total of 55% of the yard’s activity. However, the continuing efforts to diversify the yard’s activity resulted in a relevant share of
containerships entering the yard for general repairs, representing some 15% of the total activity of Lisnave. More specialised vessels like dredgers (five), and offshore vessels, such as a DP crane vessel and FFPV units, have also called at Lisnave for drydocking and repairs during 2020, in addition to a number of passenger vessels.
The vessels repaired by Lisnave during 2020 originated from 46 different clients located in 19 countries. The geographical distribution was led by UK, Norway, Singapore, Germany and Belgium.
Continuing the trends of previous years, the high number of repeat customers during 2020 reveals the recognition of the quality of the service level provided to shipowners/ managers by Lisnave. So far, Lisnave started this unpredictable 2021 with a fair number of different repair projects.

Knutsen OAS’ shuttle tanker Raquel Knutsen in Lisnave
Busy start of 2021 for ART Shipyard
Turkey’s ART Shipyard had a busy start to 2021 with a wide range of projects including LPG tankers, ro/ro ships, containerships and bulk carriers. ART Shipyard, established in 2019 by Besiktas Group in the Tuzla Bay area, is located just outside Istanbul, and attracts a great number of leading owners for drydocking and BWM system retrofits.
Closing 2020 with a total number of 125 repair projects since its inauguration, ART Shipyard has managed to secure shiprepair and retrofit projects from well-known international shipowners and ship managers. Last year (2020) was remarkable with 40 BWM system installations and the interest in this market appears to be continuing on 2021.
Currently in the yard are Ishima’s 47,203 dwt chemical tanker Glenda Melissa, in for standard drydocking and BWM system installation, d’Amico’s 37,056 dwt bulk carrier Cielo di San Francisco, and Thome Ship Management’s 39,802 dwt bulk carrier Hanyang .
In the coming days ships are due from the following shipowners (all involving BWM system installations - Tide Line’s Elbana di Navigazione, Augusta Due and d’Amico.
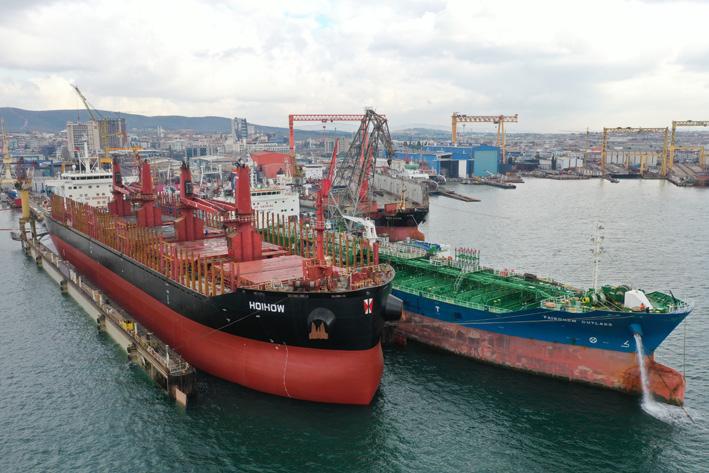
Ships in ART Shipyard
SORJ
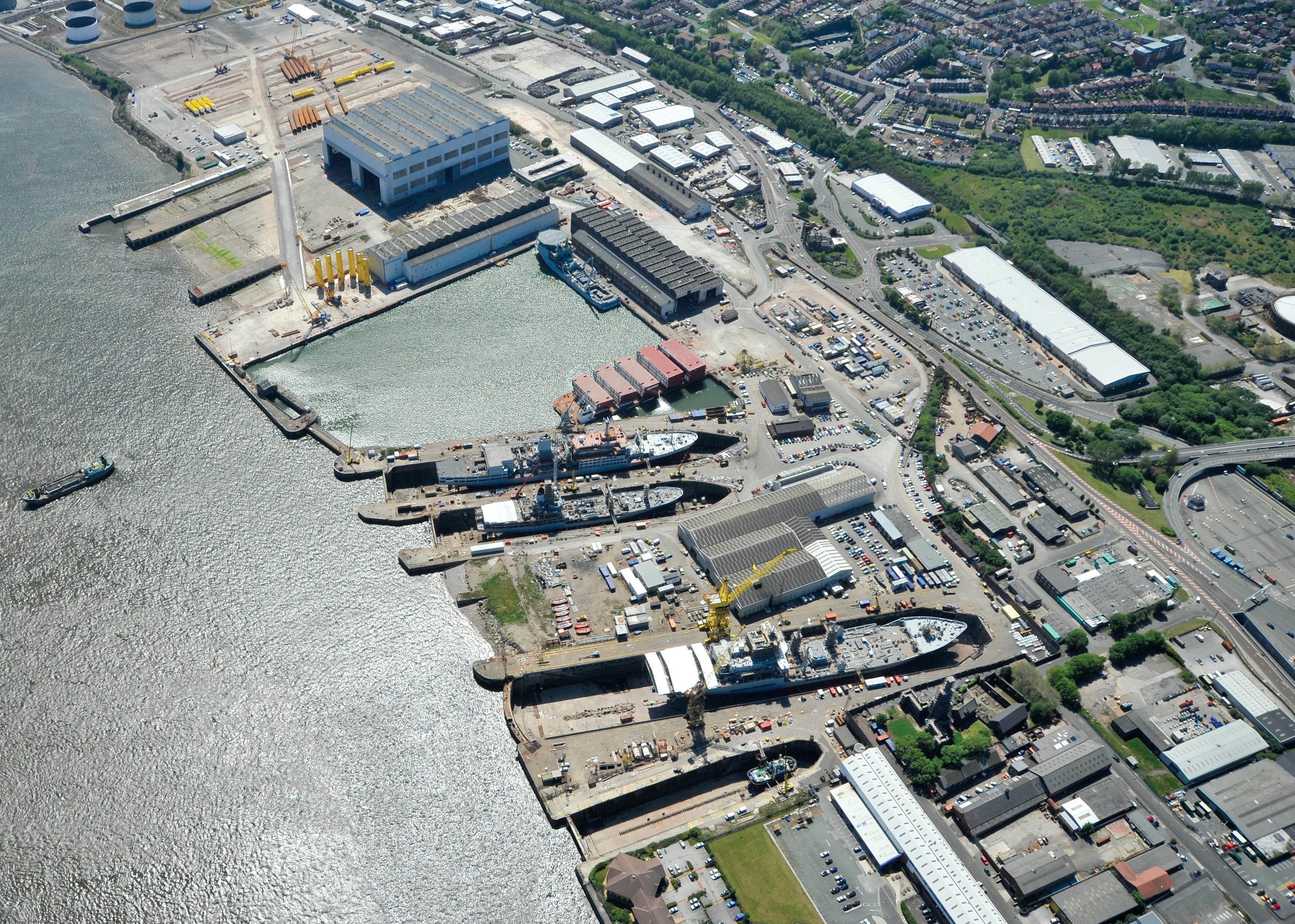
Specialists in Marine Fabrication & Engineering
Cammell Laird Shipyard | Campbeltown Road Birkenhead | Merseyside | CH41 9BP T: +44 (0) 151 649 6600
www.cammell-laird.com
Shipyards
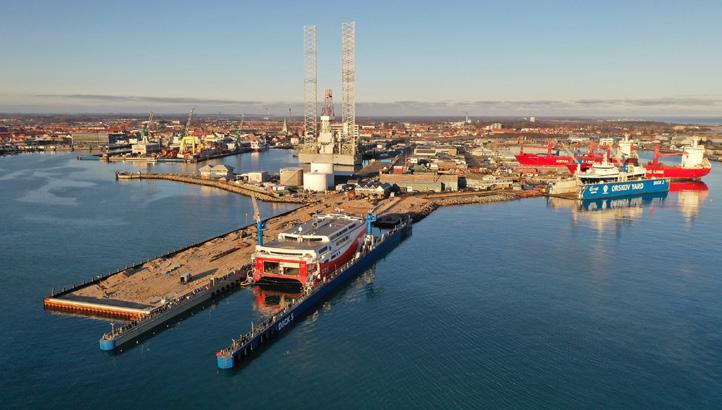
The Skane Jet entering Orskov’s new floating dock
First ship in Orskov’s new floating dock
The first vessel to use Denmark’s Orskov Yard’s new 10,000 ton lifting capacity floating Dock 5, recently opened in Fredrikshavn, was the 1998-built Incat 92 m wave-piercing catamaran Skane Jet, owned by FRS, which entered the new drydock on January 16th .
It was a tight fit for the 26 m wide catamaran fast ferry as the new floating dock measures 180 m x 30 m x 14 m, with a design draught of 13 m and draught above keel blocks is 8.5 m. The new floating dock is fitted with two 10 tonne capacity wingwall-mounted cranes. Dock 5 was built by Turkey’s Hat-San Shipyard in Yalova. Meanwhile, other vessels undergoing repair at this yard while the Skane Jet entered the new floating dock included: • Windea La Cour – 5,897 gt 2016-built offshore wind turbine service vessel, owned by Germany’s Bernard Schulte Offshore, Hamburg • Normand Installer – 14,506 gt 2006-built offshore construction support vessel, owned by Norway’s Solstad Offshore, Skudeneshavn and on charter to SBM Offshore • HDMS Vaedderen (F 359) – 3,500 tonne full load displacement, 1992-built ocean patrol vessel, owned by the Royal Danish Navy • Brennholm – 2,666 gt 2006-built fishing vessel, owned by Norway’s Brennholm AS, Bergen • Polar Nanoq – 2,522 gt 2001-built fishing vessel, owned by Greenland’s Polar Seafood, Nuuk
New shiprepair yard on US West Coast
The large shipyard on the US West Coast at San Francisco, has now re-opened for repair activities. The yard has two graving docks, which are supported by extensive machine and steel workshops. The dimensions of the two graving docks are – Dock No. 2 – 219.5 m x 29.9 m and Dock No. 3 – 207.3 m x 27.6 m
During December 2020, the yard had a number of ships in for repairs: • USCG ice breaker Healy - she had a fire in one of her propulsion motors. This was an emergency repair to swap out a 100 tonne motor through the side of the ship • USS Emory S. Land, a Military Sealift Command (MSC) sub tender. This is a 200 day service life extension project (SLEP) that includes full hull/freeboard preservation, major steel work, engine overhauls and other general repairs • USNS Kaiser, a MSC operated fleet oiler/ resupply ship, in for her bi-yearly alongside yard survey. Work includes - house preservation, replenishment gear repairs, engine/machinery inspections/repairs, steel repairs • USNS City of Bismarck, a MSC operated fast transport ship, in for alongside repairs including aluminum welding repairs • Bell Shimada, a NOAA-operated research ship, in for alongside repairs including upgrades to support science experiments on her upcoming voyage
First repair project for Western Shiprepair’s new floating dock
Lithuania’s Western Shiprepair, Klaipeda, part of the Estonian headquartered BRLI Grupp, has commissioned its new Panamax capacity floating dock FD170, the largest floating dock in the Baltic States. The new dock repaired its latest vessel at the end of December 2020 – DFDS’ 25,263 gt 1999-built ro/ro Optima Seaways, which was followed by Polferries’ 17,790 gt 1981-built ro/pax Baltivia.
At the same time as the drydocking of the Polish ferry, the yard was also repairing two ferries from the fleet of Germany’s TT-Line in its two other floating docks – the 15,955 gt 1993-built Marco Polo in FD12 and the 26,790 gt 1995-built Robin Hood in FD219. This is part of a four-year project at the yard to introduce two large floating docks to its facilities.
The floating dock was acquired from the Riga Shipyard at the end of last year (2020) and underwent repairs and upgrading. Currently, the dock with a length of 201 m, a width of 35 m and a lifting capacity of 30,000 tonnes is undergoing upgrading and repairs. The yard’s existing floating dock has a length of 200 m, a width of 30 m and a lifting capacity of 27,000 tonnes.
It was in early July, last year (2020) another floating dock was permanently installed at Western Shipyard and drydocked its first vessel, the Minerva, for general repairs. This unit has a length of 235 m, a width of 45 m and a lifting capacity of 33,000 tonnes. The floating dock was acquired by BLRT Grupp in 2016 from the Adriatic Shipyard Bijela in Montenegro. It has been reconditioned and totally modernised.
According to Veronika Ivanovskaja, BLRT Grupp, Chairman of the Board, “Enormous progress in the field of ship repair has been made and the Group is reaching a completely new level, providing further momentum for us and for the ship owners in repair and modernisation of large vessels. Western Shiprepair yard will become the largest ship repair hub and, together with the shipyards in Tallinn and Turku, will enable the Group to compete with the greatest shiprepair companies of Western and Northern Europe.
“As a result, several hundred new jobs have been created. In certain periods, it is necessary to involve a large number of highly qualified specialists of various profiles in various types of projects. A good climate for this has been ensured in Lithuania - specialists in shipbuilding and shiprepair are prepared in higher and vocational educational institutions.
There is no upper limit quota for foreign employees in Lithuania, thus it’s possible to recruit the highly qualified specialists if necessary. Improving its legislation to attract foreign workers, Lithuania adheres to the same principles as Germany, France, Poland and Finland.
“This creates favourable conditions for the development of entrepreneurship and for economic support. Unfortunately, due to the challenges faced in connection with recruiting foreign labour in Estonia, we were forced to adjust our development plans and to give up the idea of having a large dock we planned to
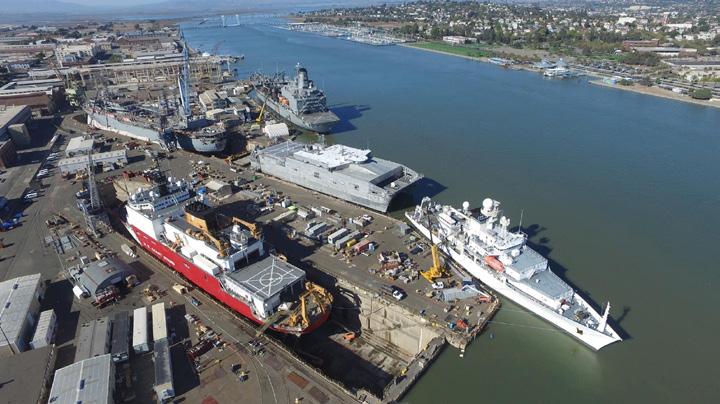
An aerial view of Mare Island Shipyard
install in the middle of this year, in Tallinn.”
Over the past few years, BLRT Grupp has invested some 100m to increase competitiveness of Western Shipyard Group companies and to develop capacity in Klaip da.
New repair facility for Italy
The Medcenter Container Terminal in Gioio total of 3m+ teu. Tauro has 3.4 kms of quays, an alongside Gioio Tauro is situated in the Reggio water depth of 18 m, a container yard capacity Calabria region of Italy on the Tyrrhenian Sea, of 75,000 teu and a handling capacity of 4.2 closed to the Strait of Messina. MSC is a major teu/year. During 2020 the facility handled a user of the port. The port authority of southern Europe’s largest container port, Gioio Tauro Port Authority (Autorita Portuale Di Gioio Tauro e Della Calabria) is to establish a new shiprepair and maintenance facility within the port and has issued a tender to buy a second-hand floating dock capable of accommodating today’s latest generation of large containerships.
Italian containership and cruise vessel giant MSC has expressed an interest in investing in the new shiprepair yard as well as co-managing it. SORJ
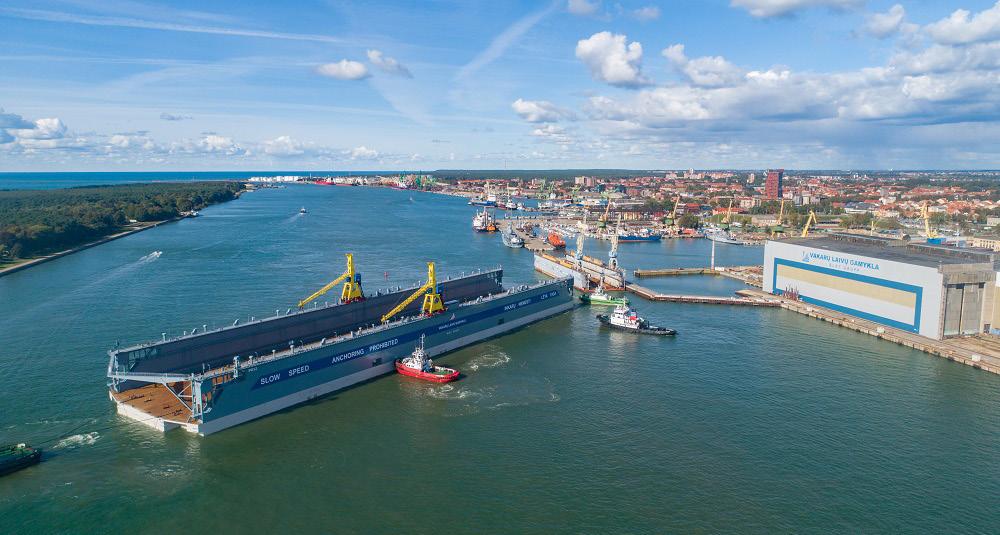
The new floating dock arriving in Western Shipyard
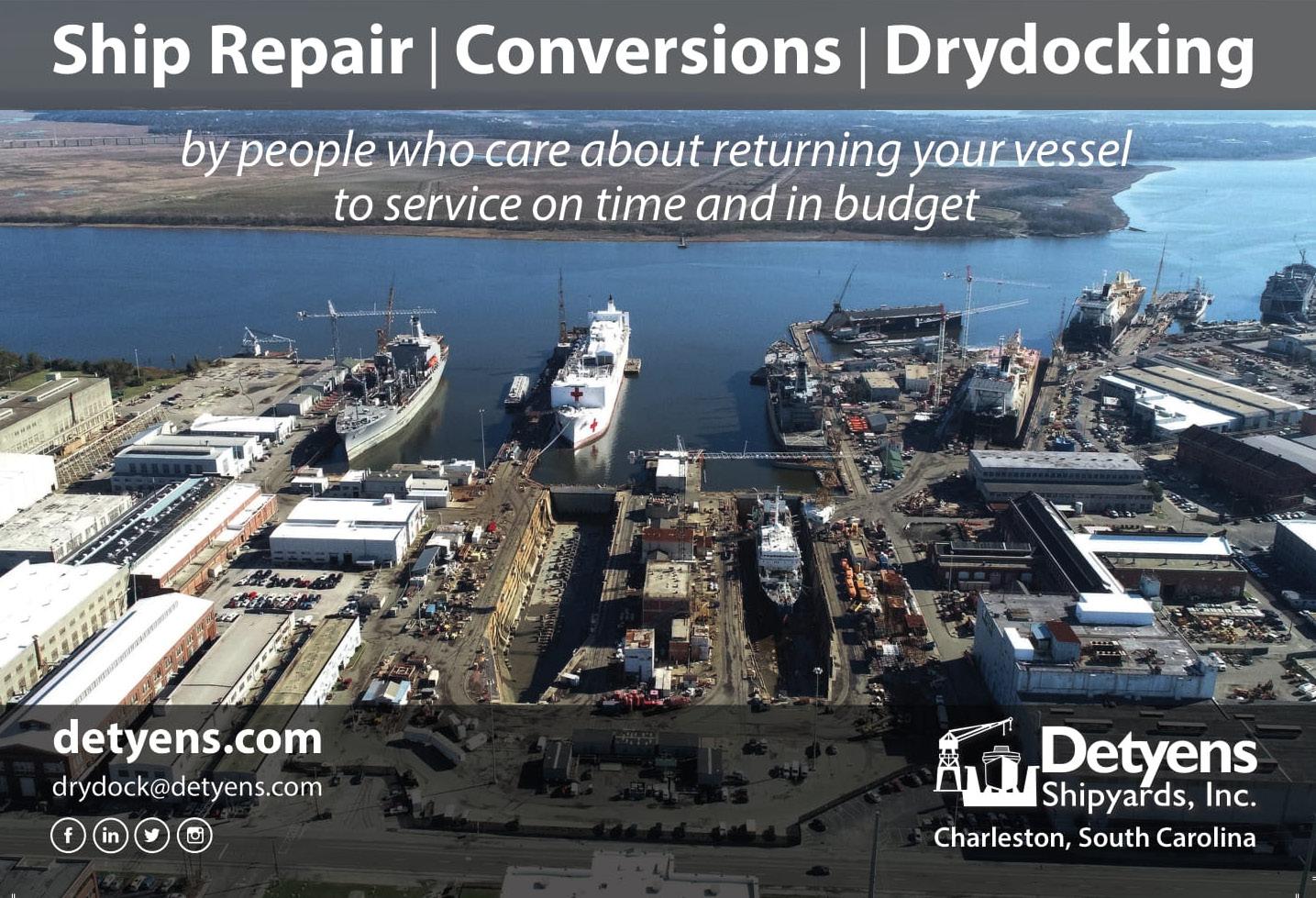
Newport Shipping rolls out the NMS Platform
Newport Shipping has unveiled Newport Maritime Services (NMS), an innovative online portal which, according to NMS, has been specifically designed to ease the complexities of shiprepair and retrofit works. Digitalisation has made its mark in the shipping sector, with many bespoke online tools now being utilised daily to operate and manage the world’s merchant vessel fleet. This new online platform is in addition to the offer to shipowners made by Newport Shipping over the past few years to offer financial assistance to projects involving the retrofit of BWM and scrubber systems.
NMS’ Managing Director, Ege Akcasoy said, “NMS is a new way of managing shiprepair and retrofit projects via a bespoke, online platform. The NMS platform enables shipowners and fleet operators to obtain instant quotes for routine maintenance works, have real-time visibility of shipyard availability, involving NMA’s partner yards, and get priority access to drydock slots, all at the click of a mouse.
“Digitalisation is on the agenda of all companies operating in the shipping industry, but the sector also remains true to its traditional roots. We wanted to introduce an online tool that works in harmony with the people that make the ship repair sector what it is today, enabling greater transparency and thereby validating the trust and personal relationships that this industry is built on.”
NMS is also offering project management for repair, refit and conversion projects, through a network of a team of some 12 technical superintendents – five locally based in China, and seven from NMS’ offices in Greece and Turkey. There is also a momentum at NMS to increase the number in the technical team.
NMS’ current list of partner yards involves just 10 repair yards throughout the world – seven in mainland China, one in Singapore, one in Indonesia, one in the Middle East (Oman) and one in Europe (Turkey). The main partner is PaxOcean, which operates yards in Singapore, China (Zhoushan) and Indonesia (Batam). Akcasoy continues, “We are looking to increase the number of partner yards as shipowners throughout the world begin to utilise the NMS facility.”
Subscribers to the NMS platform will have access to instant quotations for a wide range of routine maintenance and repair work (only from current partnered shipyards), as well as the ability to book slots at a partner shipyard with a real-time view on the yard’s current availability. The platform will also provide access to a full set of bespoke solutions in repair, retrofit and conversions with a low carbon focus from an exhaustive list of trusted Newport Shipping supplier partners, especially in the BWM and scrubber system installation market.
This is a potential game-changer for those responsible for the management of multiple vessels, empowering them with a level of transparency and control that more traditional methods cannot give, and also significantly de-risking the whole process. The team behind the NMS platform has poured over 60 years of organisational experience into refining the design, layout, functionality and operational aspects of the system and is confident that it will benefit users in a number of ways.
Akcasoy further explains, “NMS is a fullyautomated booking and management platform for high-quality drydocking, retrofit and conversion projects at its partnered shipyards. It combines priority access, on-demand quotes, price stability and live yard availability in a streamlined way that ultimately saves shipowners time and money. In addition to this, the visibility that the platform allows through each stage of the process helps to reduce risk and future-proof shiprepair operations.”
The extended payment arrangement, available to qualifying clients and their assets,


ESAB and YASKAWA have signed a global co-operation agreement to jointly develop and market a line of pre-engineered robotic welding systems called XCellerator.
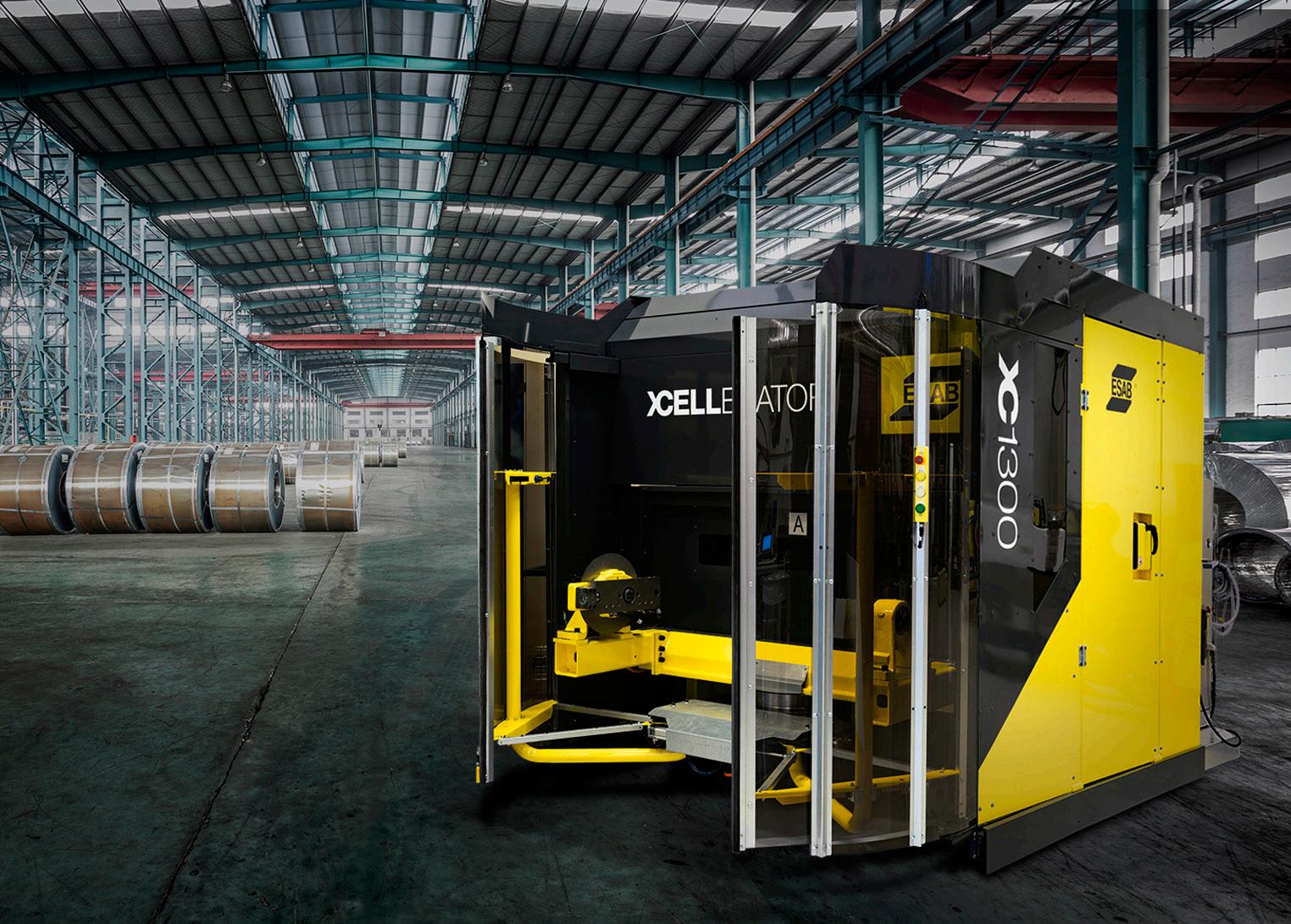
provides a payback period of up to 24 months, with an initial down payment on completion of work followed by equal monthly instalments. Newport undertakes a rigorous due diligence and credit evaluation exercise before offering the service, which is secured by an irrevocable payment guarantee letter governed by English law.
The introduction of this new digital tool also stands to support the industry with its Environmental, Social and Governance (ESG) mandate. Audit trails, data points, real-time information and the transparency that comes with further digitalisation all serve to help the shiprepair and conversion sector clearly communicate what it is doing and how it is doing it. Through implementation of the right processes and digital tools to communicate information in the right way, NMS believes that the sector can attract interest from a broader set of investors and tentatively look forward to a more prosperous and sustainable future.
ESAB and Yaskawa co-operate
The ESAB Group and Yaskawa have announced the signing of a global co-operation agreement to jointly develop and market a line of preengineered robotic welding systems called XCellerator. The XCellerator systems will be engineered and built by Yaskawa and marketed by ESAB through its global sales channels.
Each company will contribute their special expertise to create a product which is greater than the sum of their individual contributions. In creating the XCellerator line of pre-engineered robotic welding cells, Yaskawa brings more than 30 years of experience producing leading-edge robots, robotic controllers and robot cells to this effort. For its part, ESAB brings its deep expertise in welding processes, filler metals, equipment and automation together with their proprietary WeldCloud weld operations management infrastructure. Together they have produced an integrated robotic welding solution that truly exemplifies these two great companies.
Pre-engineered cells like XCellerator are the fastest, simplest path toward automation. They improve productivity per worker by three to five times and offer a compelling return on investment. Factory-built and tested, they take the risk out of robotic system investments. The cells especially appeal to small and mediumsized manufacturers and fabricators that value easy installation, set-up and operation, enabling them to take a confident step toward automating their welding operations.
Yaskawa is a world-leading manufacturer of inverter drives, servo drives, machine controllers, and industrial robots. For more than 100 years, the company philosophy has been based on the principle of highest quality. This philosophy has helped Yaskawa to become one of the top global companies in the field of electrical drive
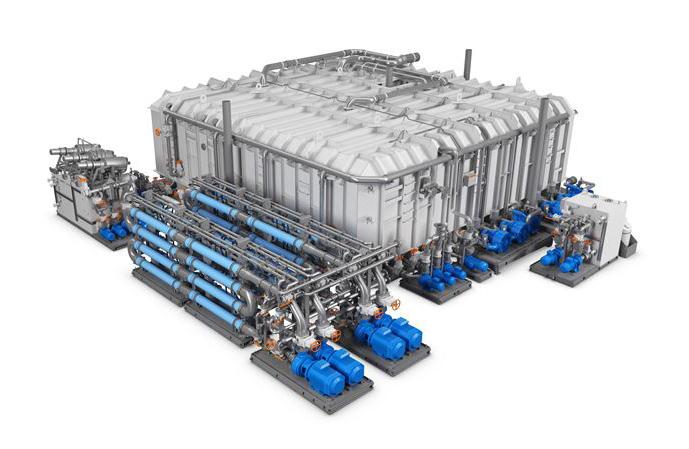
The Wärtsilä advanced wastewater and dry waste treatment system
technology. Inventor of the word Mechatronics and its strong focus on research and development has yielded innovations that have contributed significantly to the success of many industries, among them machine construction, mining, machine tooling, automotive construction, packaging and semiconductors. As supplier of MOTOMAN industrial robots, Yaskawa is also one of the world’s biggest robot manufacturers. The company operates manufacturing and development facilities in Asia, Europe and North America.
Carnival agreement for Wärtsilä
Wärtsilä has signed a framework agreement with Carnival Corporation covering the supply and installation of Wärtsilä’s advanced wastewater and dry waste treatment systems for up to 32 vessels across many of its operating brands. The framework is consistent with Carnival’s policies for compliance with the latest and most stringent environmental legislation. Signing of the framework took place in October 2020. Wärtsilä’s Membrane Bioreactor waste water treatment plants are well proven in the handling of black and grey waste water. The system surpasses the most demanding standards currently set by IMO for sewage discharge, including paragraph 4.2 of MEPC 227 (64), which applies to special areas.
Similarly, Wärtsilä’s dry waste handling systems comply with the most stringent IMO Marpol requirements, and are designed to minimise greenhouse gas emissions. Wärtsilä’s advanced technologies and vast experience were cited as being major considerations in the award of this contract.
“There is increased awareness within the cruise industry of environmental sustainability, and Wärtsilä is proud and ready to support this focus with the most advanced and compliant solutions. We continue to work with Carnival to enhance their goals for waste reduction, in line with their internal strategy,” says Arto Lehtinen, Director at Wärtsilä Water and Waste.
“We very much appreciate Wärtsilä’s support and their capabilities in delivering high quality, reliable solutions tailored to our specific requirements. The environmental legislation barrier for the cruise industry is set very high, so we seek the latest technologies to ensure compliance. The Wärtsilä solution selected for the framework more than meets this standard,” says Jon McKeown, Senior Vice President global strategic sourcing from Carnival Corporation.
The Wärtsilä equipment will be delivered and installed on-board different ships across many of the operating brands between now and 2025.
This framework agreement shows, despite the current challenges, that environmental compliance and sustainability remains a top priority for Carnival and proves Wärtsilä’s advanced waste system solutions are there to meet and surpass the most stringent legislations.
SORJ