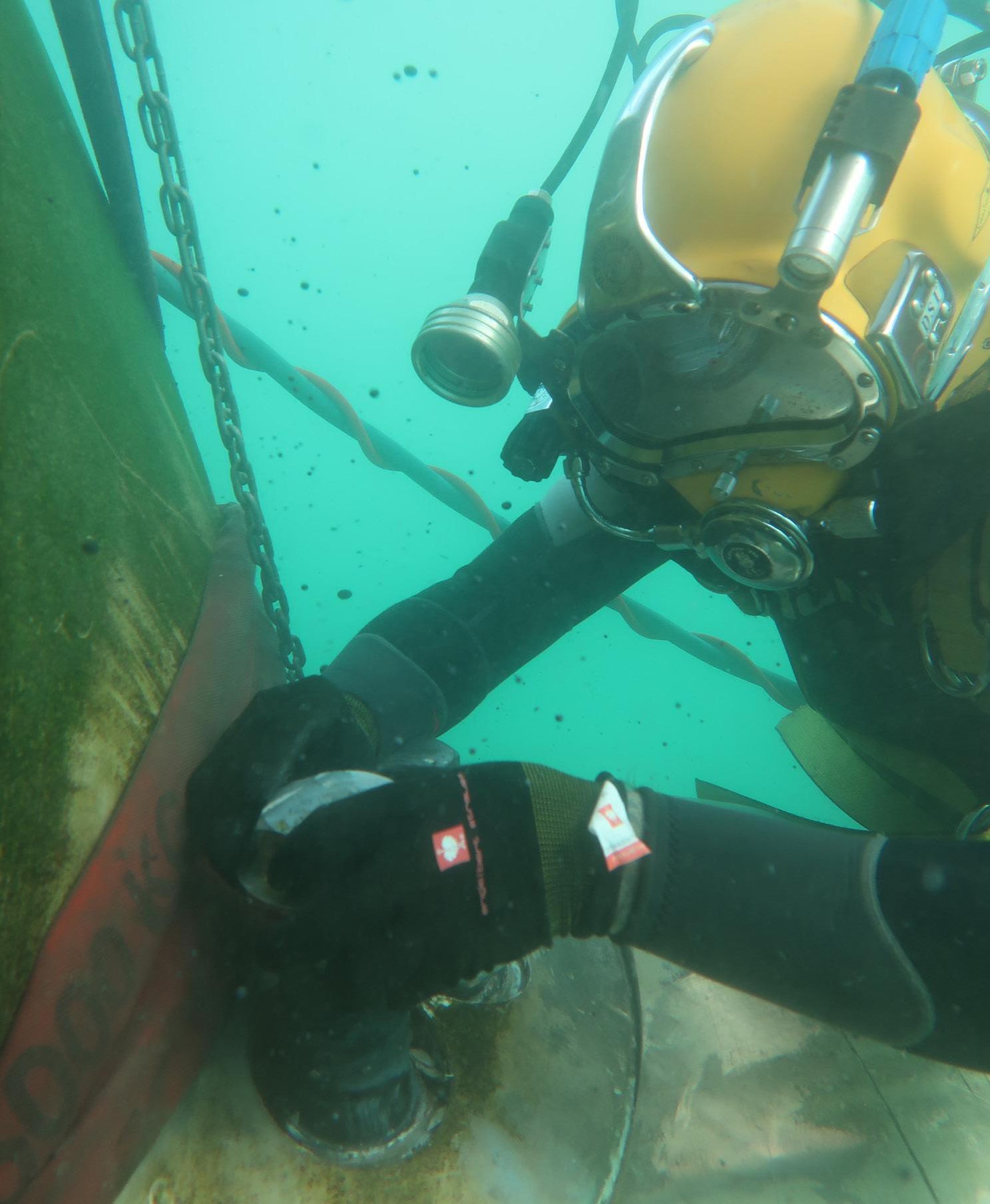
17 minute read
Underwater
Activities at Hydrex
One of Hydrex’s diver/technician teams reently carried out an underwater stern tube seal repair on a 300 m containership berthed in Antwerp. The ship was suffering from an oil leak, making an immediate repair necessary. Using a Hydrex flexible mobdock the team was able to carry out the entire operation on-site and underwater, saving the owner an expensive and timeconsuming trip to drydock.
Advertisement
Once the operation was confirmed all preparations were handled swiftly and the lightweight equipment was mobilised immediately from Hyrex’s headquarters in Antwerp. After arriving on-site, the diving team first set up a monitoring station next to the vessel. The operation then started with the removal of the rope guard and a thorough underwater inspection of the stern tube seal assembly.
After the inspection the divers cleaned the assembly and installed the flexible mobdock. By doing this they created a dry underwater environment so that they could work in drydocklike conditions.
The split ring was then removed and brought to the surface to be cleaned. After cleaning the entire assembly, the divers removed the first seal and replaced it with a new one which was bonded. The procedure was repeated with the other seals. A successful operation was concluded with leakage tests, the removal of the flexible mobdock and the reinstallation of the rope guard.
Working together with the OEM allowed Hydrex to provide the customer with original spare parts which guarantees the best quality material. A technician of the seal manufacturer was also present during the operation.
By organising everything from start to finish the owner did not have to worry about making any arrangements for the repair. After the seals had been successfully replaced he could sail his vessel to her next stop free of oil leaks.
Meanwhile, oil was leaking from a propeller blade of a general cargo vessel, which could not use her propeller anymore and the blade seal needed to be replaced. Time was critical and a fast and on-site solution was essential in keeping the ship on schedule. Hydrex therefore mobilised a team to the ship’s location in São Vincente, Cape Verde to perform emergency repairs.
The team started the repair with the installation of chain blocks to rig the blade. They then removed the blade bolts and lifted the blade. The damaged blade seal was replaced with a new one. After the new seal was installed the blade was repositioned and the bolts were secured again.
A successful oil pressure test and an underwater inspection of the entire propeller were performed, concluding the repair. With the oil leak repaired the vessel was able to leave Cape Verde with a working propeller. The owner could keep to the sailing schedule without any delay.
Removing a propeller blade allows Hydrex to perform work on the propeller while the vessel stays afloat, but sometimes one or more blades need to be replaced or overhauled. Divers can remove them and replace them or reinstall them when they return from the workshop.
A good example was the operation on a ro/ ro ship berthed in Tasmania. This operation consisted of the underwater replacement of the damaged blade as well as the opposite blade of the main propeller of the vessel.
This propeller was designed with a special system to close it off from water ingress during a blade replacement. The operation was performed under supervision of an engineer of the propeller’s OEM.
Once the first blade had been lifted, a spare blade was lowered into the water and put in position. After it was secured and the bolts put on torque, the ship crew turned the propeller 180° to bring the opposite blade in 12 o’clock position. The Hydrex diver/technicians then repeated the same procedure on this blade.
The operation was finished swiftly to enable the owner to sail his ship on schedule. No costly drydock visit had to be planned.
A Hydrex diver/technician removing propeller blade bolts
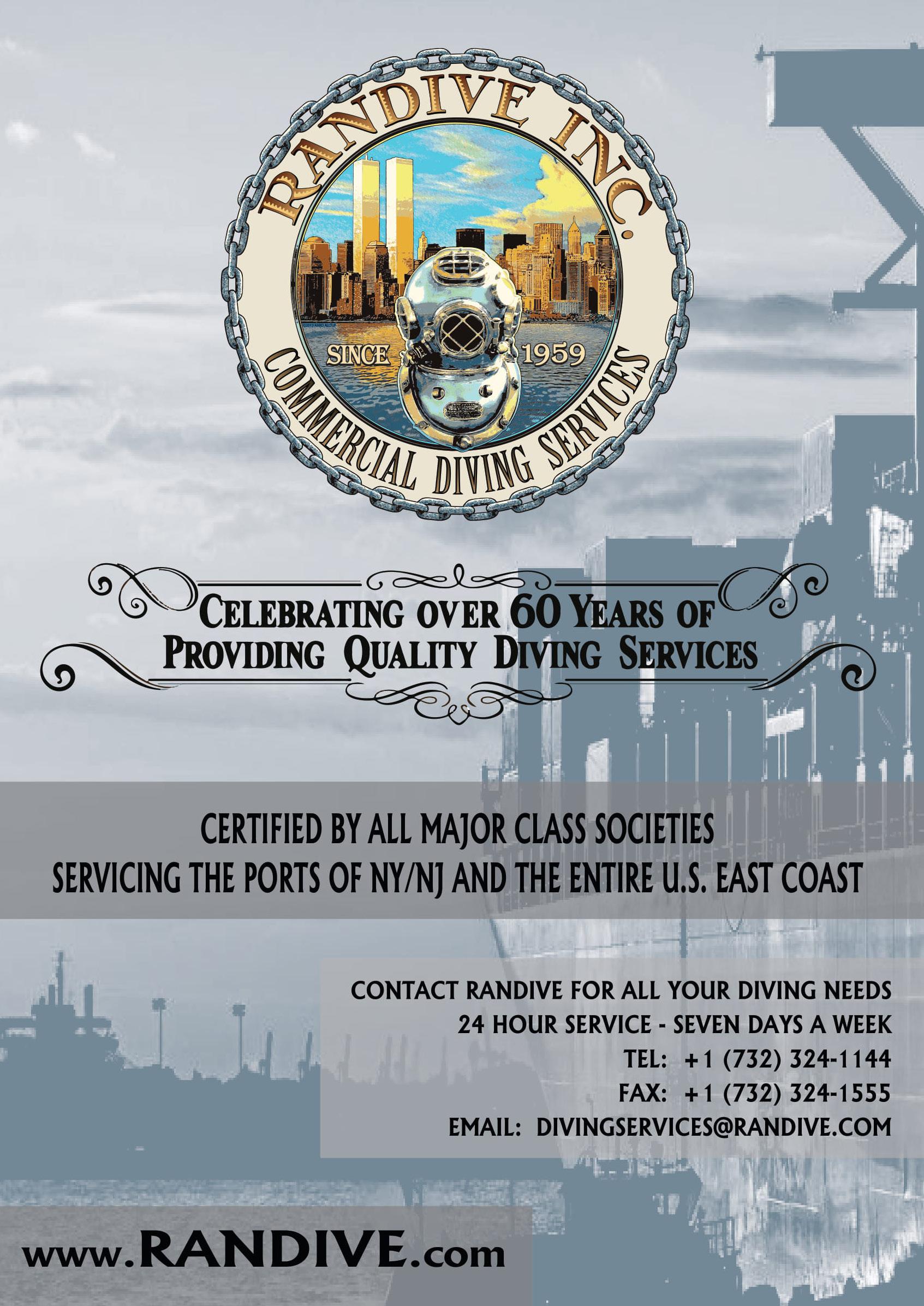
Underwater hull repairs often require large inserts
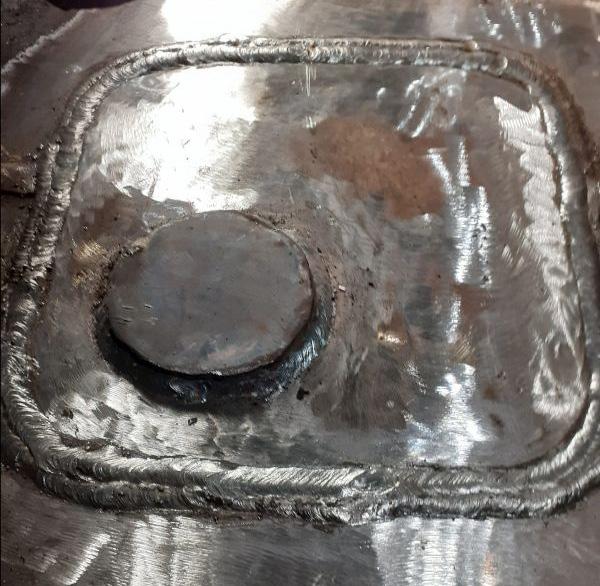
An insert
Underwater hull repairs do not always involve the installation of large inserts. Sometimes only a small part of the hull has been affected. This is often the case when an area on the hull suffers erosion damage. Hydrex has several options available to repair the hull plating.
This type of smaller damage forms over time as the result of the recurring impact of, for instance, water or the bob of a measuring tape on the exact same spot over and over again. On vessels this occurs regularly in the ballast tanks under sounding pipes or bell mouths.
Hydrex offers class approved permanent repairs for this type of damage. These combine underwater cofferdam installation and inside dry welding. Both parts of such an operation are performed by the same team of in-house trained diver/welders working at the highest quality standards. In most cases normal commercial activities can continue without disruption. If the damage is caught before the hull has been penetrated fully, clad welding can be used to fill up the area. This is also a permanent repair that will avoid a condition of class.
A 175 m tanker suffered cavitation damage to the inside shell plating of one of its ballast water tanks. Hydrex mobilised a team to Algeciras to perform a permanent insert repair that would prevent an unscheduled drydock visit for the vessel. The team sailed with a workboat and all necessary equipment to the ship which lay at anchorage in Algeciras.
The divers started the operation by installing a cofferdam on the waterside of the affected plating. Next, they removed the bellmouth pipe covering the area on the inside. They could then safely remove the plug and the cement box which had been installed as a temporary solution. The damaged plating was then cleaned and prepared for the operation.
As agreed with the classification society, the team then cut away an area measuring 350 mm x 300 mm. Next, they prepared the edges of the hole for the insert and positioned the new plate. The insert was then welded following the Hydrex class-approved procedure for insert plates, using a full penetration weld.
An independent inspector carried out ultrasonic testing and the repair was approved by the classification surveyor who was present during the operation. The team then reinstalled the bellmouth pipe and removed the cofferdam. Simultaneously one of the pipe reducers in the engine room was replaced by our team. This part of the operation was also approved after ultrasonic testing.
The operation in Algeciras was performed to the highest quality standards by in-house trained diver/welders. Hydrex has a wide range of cofferdams at its disposal as well as certified plating which can mobilise immediately to any location around the world.
Repairs like this can be carried out above or below water, according to the circumstances, with external cofferdams. Normal commercial activities can therefore continue without disruption. These operations follow the Hydrex procedure for welding cracks and inserts in the vessel’s shell plating and they are approved by the major classification societies.
Ecospeed applied to overboard pipes
Recently Subsea Industries’ Ecospeed coating system was applied on the scrubber overboard pipes of two oil tankers. The applications took place in China and Singapore. A lasting, chemically resistant coating was needed that could withstand the hazardous pollutants of the exhausts and protect the areas surrounding the outlets.
Because of the tight regulations on emissions in the shipping industry, the installation of an exhaust scrubber system has become increasingly widespread. This unfortunately has also led to an increase of corrosion damage on scrubber pipes and outlets which results in water ingress in the engine room, ballast tanks and cargo holds.
Ecospeed however is highly chemically resistant. Using the coating to protect the exterior outlets as well as the interiors of scrubbers will prevent corrosion damage and the resulting consequences.
There are also several other benefits that make Ecospeed the perfect choice. • The coating system is highly chemically resistant. Taking into account the nature of the process taking place inside the scrubber, this is essential for customers • Ecospeed lasts the lifetime of a vessel. No repaints will need to be scheduled during future
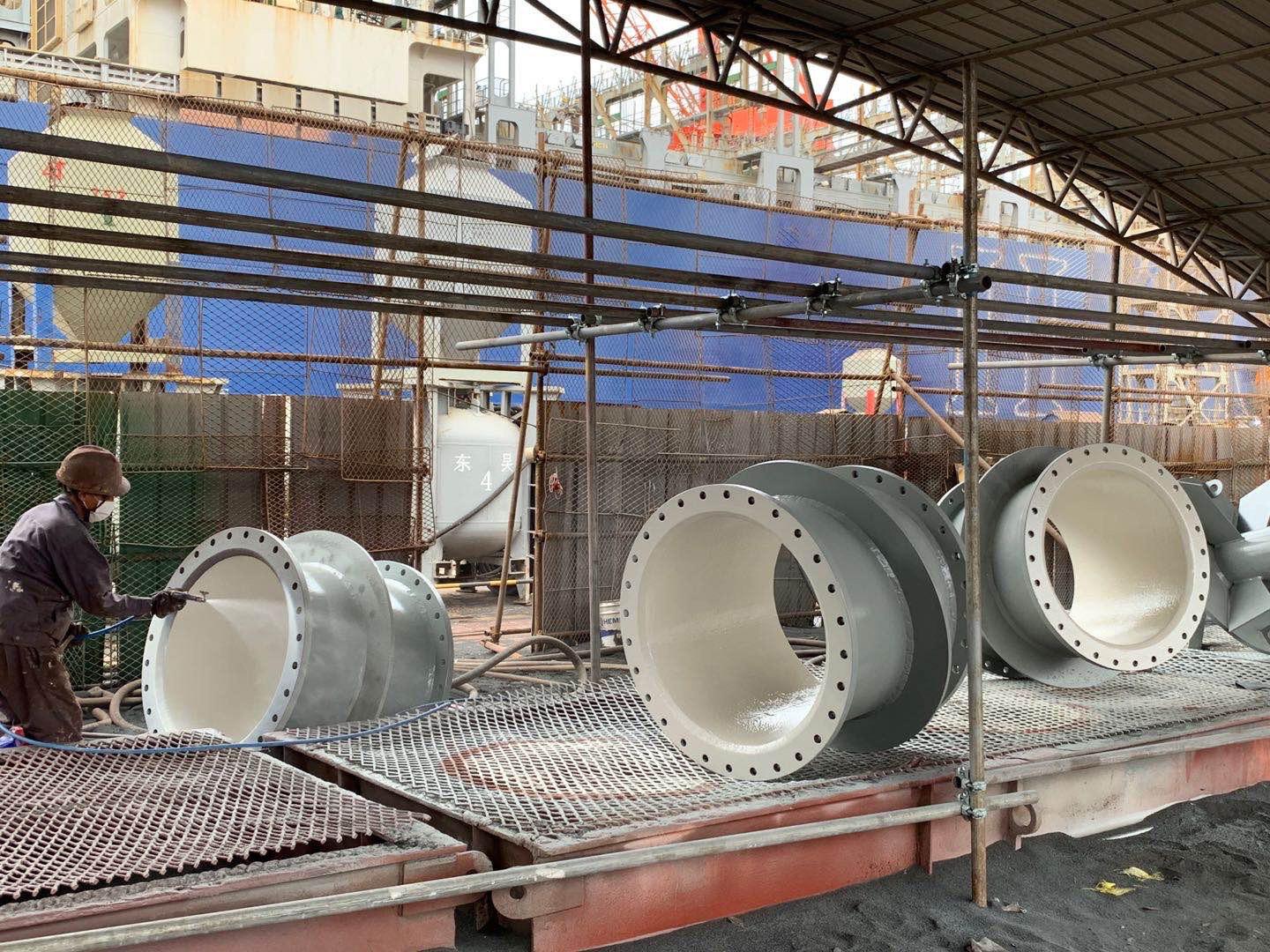
Application of Ecospeed on scrubber overboard pipes in China
dockings of the ship. This saves on time and money • It is a true biocide-free solution. Independent research has proven that the coating is 100% toxin-free and that there is no negative effect on the water quality or the marine environment at any point of its application or use • Ecospeed fits in seamlessly with the environmental idea behind scrubber systems. It is a lasting, chemically resistant coating that will withstand the hazardous pollutants and protect the scrubbers for the lifetime of the vessel
In-water repairs by SGS
A valued client contacted US-based Subsea Global Solutions (SGS) with an urgent enquiry regarding a vessel in transit and re-routing to Freeport, Bahamas. The vessel was experiencing water ingress from a leaking shaft seal that needed repair—in a hurry, to preserve the perishable cargo.
A spokesman for SGS said, “SGS reacted fast, mobilising two teams to work around the clock composed of OEM certified diver technicians from Miami, Houston, and Long Beach. We began our proven underwater shaft seal repair procedure by removing the rope guard by way of underwater arc gouging to expose the stern seal assembly. Once the rope guard was removed, the diver technicians found a combination of fishing line & fishing nets wrapped around the shaft and stuck in the seal system, which is now believed to be the root cause of the seal damage. Once the debris was removed, we templated the sterntube and propeller hub to ensure a proper fit for the SGS underwater Transhab adaptor plates. With our underwater Transhab Habitat installed, we performed our HSE safety checks to ensure the Transhab was safe and secure for our diver technicians to enter. Once confirmed, the two teams worked around the clock to minimise the vessels downtime.
“Being an OEM certified service provider, the team removed all existing shaft seals and we rebonded the new shaft seals in their place. Due to the grooving in the shaft liner, the seal housing was released to make room for a distance ring to ensure the new seals were operating on a new running surface. With our Transhab design, no water entered the sterntube during this critical process. After the seal bonding was completed and the spacer rings were installed, pressure tests for each seal chamber were completed and witnessed by the vessel Master and the attending Class Surveyor. A quick break down and removal of our Transhab equipment immediately followed so we could begin reinstalling the rope guard and get the vessel and it’s perishable cargo sailing to its destination. The rope guard was refitted and welded using SGS ‘Class A’ wet welding procedures with our certified diver technicians.”
Also, recently, another valued client contacted SGS to exchange a retractable azimuthing thruster for its managed semi-submersible rig stationed in Pearl Harbour. As SGS successfully completed similar thruster overhauls with this same rig two times prior, we attended once again to take on the challenge of exchanging the four retractable azimuthing stern thrusters with limited clearance between the flat bottom of the rig and the ocean seabed. In conjunction with this service, SGS tackled a full Class UWILD, full Hull Cleaning, and installation/ removal of blanks on all 16 sea chests to ensure the rig was cleared for its drydock extension.
SGS mobilised two teams composed of 14 expert diver technicians to execute the various projects in less than 35 days from Long Beach, Port Angeles, and Miami. Once the teams were on site, one team began the UWILD, hull cleaning, and sea chest blanking operations while the other began installing a custom engineered track beam system to the flat bottom of the rig. The track beam system sits perpendicular to the rig’s hull and is designed to carry the load of the retractable azimuthing thruster when disconnected from the steering pipe in the retraction column.
Since retractable azimuthing thrusters are not designed for underwater dismounting, this specialised system is required. Additionally, the engineered track beam system allows SGS to overcome clearance limitations from the flat bottom of the rig to the ocean seabed. The bottom clearance was insufficient for SGS’s standard thruster exchange protocol using buoyancy control solutions. The track beam system leverages a precision-built thruster cradle—which houses the retractable thruster— and is hydraulically driven on the track beam system under the control of our diver technicians. In general terms, this system is a trolley to get the thruster from point ‘A’ (underneath the rigs hull) to point ‘B’ (a picking zone for the crane to safely retrieve the thruster cradle) and vice versa with the overhauled replacement thruster.
All was going to plan when the project suddenly hit a roadblock—the crane could not safely pick the thruster cradle at the intended position as an obstruction from the rig was interfering with the crane booms required picking position—causing a 76.2 mm (3’) lead from the centre of the thruster cradle. At this position, the crane could only safely achieve a 20 tonne load versus the planned load at 23 tonnes. After review with the various parties involved, it was decided that SGS needed to incorporate enhanced buoyancy control solutions to float the thruster to a safe picking zone to avoid delays with the project.
Thankfully, SGS is always prepared for ‘Plan B’ and installed sufficient buoyancy to allow the dive team to safely float the 23 tonne thruster cradle to a position for the crane to retrieve with absolute confidence. SGS proceeded with the remainder of the project using this methodology for the reinstallation of the overhauled replacement thruster.
SGS adapted and overcame, as we do with all technical repairs that are bound to invite barricades into the planned work scope. The UWILD, hull cleaning, and sea chest blanking operations were finished swiftly. The projects were completed in a safe, professional, and
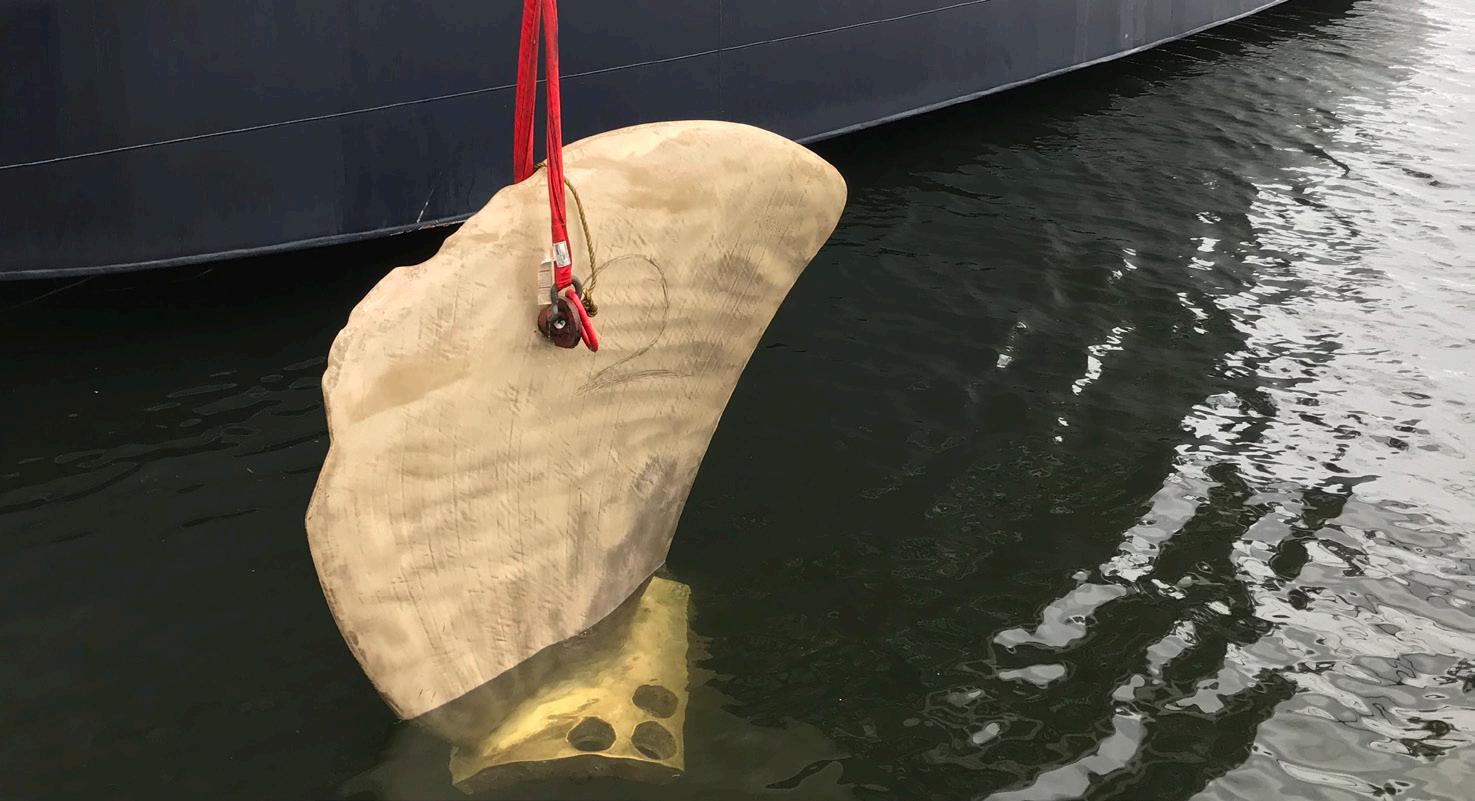
The damaged propeller blade being removed by SGS technicians
efficient fashion six days ahead of schedule to ensure our clients’ expectations were met.
A spokesman for the client said, “We thank all of the parties involved in this project for their professionalism and collaboration, it was our honour to have worked alongside your teams. Having worked with several dive companies in my position as a rig project manager, I can say I’ve easily seen the most consistent performance from SGS by far. They perform their work diligently with a level of commitment & respect from the top down.”
Meanwhile, a long time cruise client contacted SGS with an enquiry to provide an underwater solution to repair/replace five damaged propeller blades on one of their vessel’s port side pods during her stay in Port Everglades, Florida. The vessel was experiencing excessive vibration while underway and needed an effective solution. SGS provided the client with various repair options including underwater propeller blade cropping, underwater propeller blade balancing, and possibly an underwater propeller blade exchange. Since the replacement propeller blades were available, it was decided to perform the underwater propeller blade exchange.
SGS’ Miami facility prepared for the vessels arrival by mobilising two teams composed of six expert commercial diver technicians and an overseeing Project Manager to execute the underwater repair services. Due to the global pandemic, SGS also provided the client with a virtual streaming portal so they could monitor the project remotely without visiting the job site. This is one of the many ways SGS has adapted to the global pandemic the world is facing.
SGS started its underwater repair process by establishing load rated rigging points above the propeller using 4F Class A wet welding procedures to allow safe transfer of the propeller blades. Once established, the team removed the existing propeller blades without incident or delay - concluding the removal process. SGS then proceeded to install the replacement propeller blades while ensuring the OEM acceptable tolerances were met for proper seating into the alignment channels of the existing propeller housing and installed the propeller blade fasteners to the required torque specifications. Lastly, the team re-welded the propeller blade fastener keepers using Class A wet welding procedures and removed the overhead rigging points allowing us to perform Mag Particle Inspections (MPI) and re-establish a corrosion protection barrier.
The project was completed to the client’s satisfaction in a safe, professional, and efficient manner. Despite the challenges faced, SGS adapted and executed the project to the client’s expectation.
The HullWiper ROV
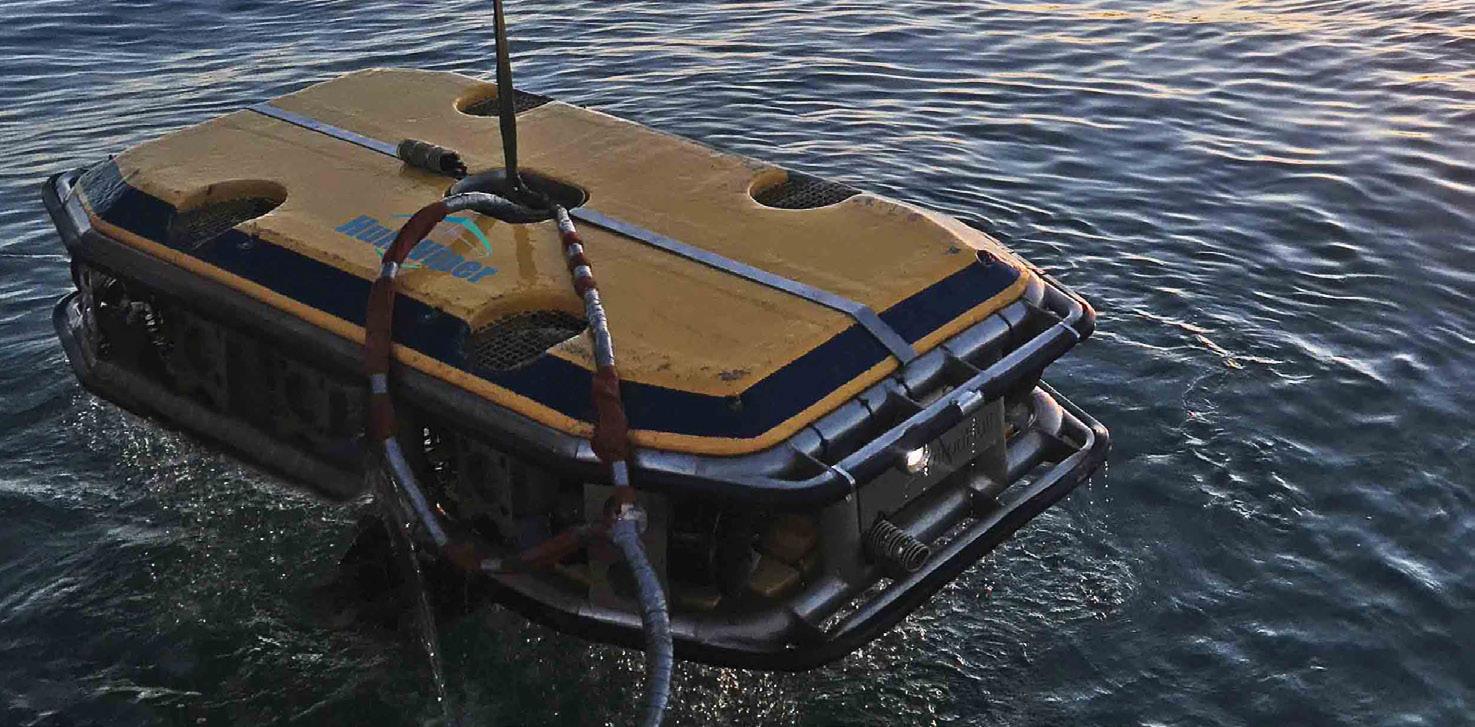
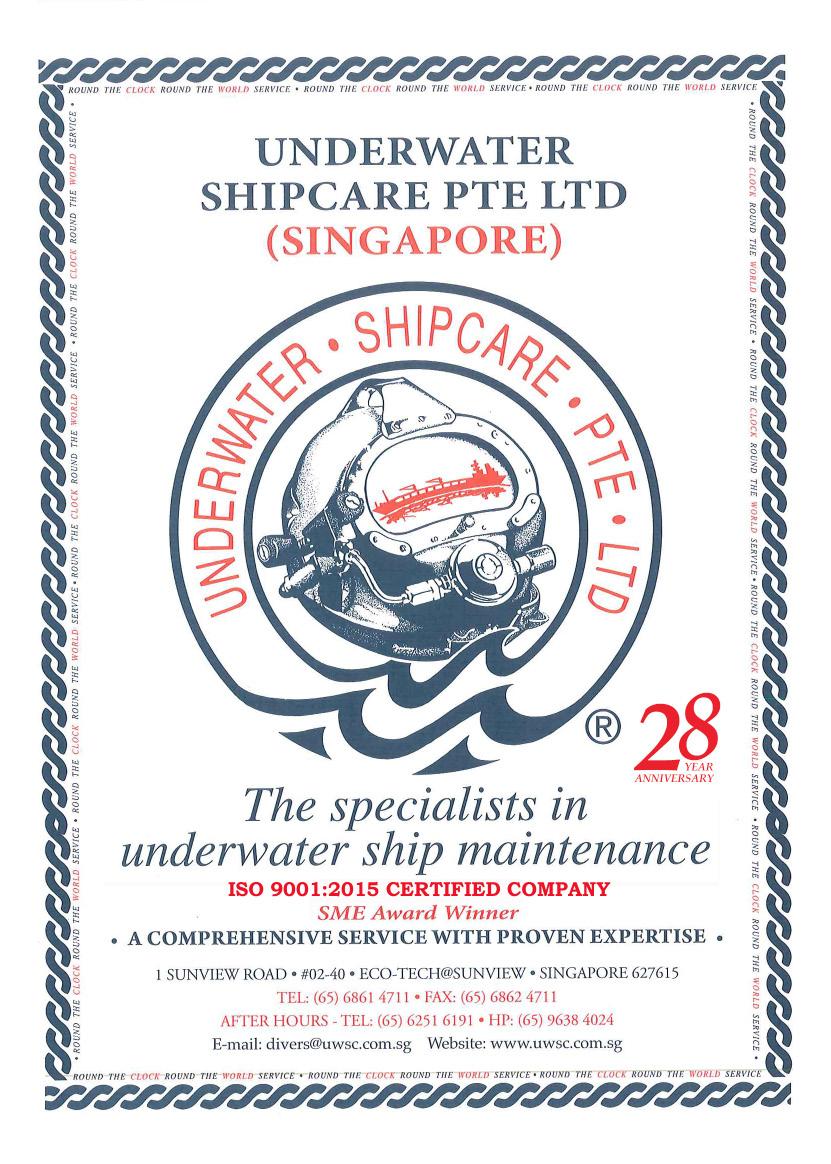
HullWiper to be used on laid-up ships
As the second wave of COVID-19 makes its appearance across the globe, the entire supply chain is once again being disrupted. The maritime industry which includes shipping, sailing and boating activities has been hit hard by the spread of coronavirus. This slowdown has again left a significant number of vessels sitting still in the waters. Shipowners and operators are forced to put ships in hot or warm lay-ups as a temporary solution to mitigate the dismal market conditions as a result of reduced
consumer goods demand, halted cruising and short-sea trips as a result of travel restrictions.
Biofouling has been an incessant menace in the shipping industry for centuries and now, it looks like it’s going to get far worse. Vessels sitting idle in warm water are particularly in the hot seat as marine organisms delight in static submerged surfaces making ship hulls below the waterline the ideal target.
An increase in accumulated marine organisms on vessel hulls not only creates a mountain of admin but hurts the budget too. Although the accumulation of biofouling is unavoidable, solutions are not far off. From diver and brush cleaning to remotely operated vehicles, ships can, during these uncertain times, avoid the growth of these critters.
Traditional hull cleaning methods might get the job done but there are unfortunately financial and environmental consequences that can’t be ignored. These include but are not limited to: • Scratching expensive anti-fouling coating when using brushes • Risk of injury and sometimes even life for hull cleaning divers • Removed biofouling is not collected and disposed of in a safe manner but rather released back into the sea which can cause detrimental impacts on marine ecosystems • Diving is limited to good weather conditions during daylight hours • Slower and less effective cleaning
Fortunately, technological advances in maritime solutions are on the rise. HullWiper’s innovative ROV leaves vessel hulls clean and unscathed by using high-pressure sea-water jets to dislodge accumulated biofouling. The unit is operated from shore with no divers involved. This allows for cleaning to be conducted 24/7, in most weather conditions, during the night or while cargo operations are underway.
Not only does HullWiper clean hulls more effectively than conventional methods, the ROV also cleans faster ensuring there is no delay to tight fleet schedules. Instead of letting removed fouling enter indigenous water and disrupt the marine ecosystem, HullWiper’s unique filtering feature captures removed organisms to safely dispose of onshore.
New dive tank for Phoenix
US-based Phoenix International has announced the construction of a new test tank at its Bayou Vista, LA facility as part of strategic growth initiatives for the New Year. The oneatmosphere dive tank measures 4.11 m (outside diameter) x 12.2 m high and holds 150,280 litres.
This tank will be utilised for multiple subsea applications, such as underwater weld testing (both wet and dry habitat conditions), underwater Non-Destructive Testing (NDT) applications, and performance trials including underwater welding certifications and underwater tooling calibration and testing.
Some features of the tank include an open walkway encircling the top to maintain a fully accessible workspace, and strategically placed viewports around the tank which will allow monitoring of activities both inside and outside of the dedicated dive control station.
Core Samples, geo technical and civil engineering requirements are being completed, and ground-breaking is currently underway for the foundation. Phoenix plans to have the tank completed by the 4th quarter of this year (2021).
Regarding the new tank, Phoenix Area Manager Troy Turner said, “The tank will play an essential role in conducting diver certifications, training, development, and testing, as well as the development and application of new underwater technologies that Phoenix has become known for. It will also be available to our clients who require specific underwater testing for any equipment or materials prior to project execution.”
SORJ
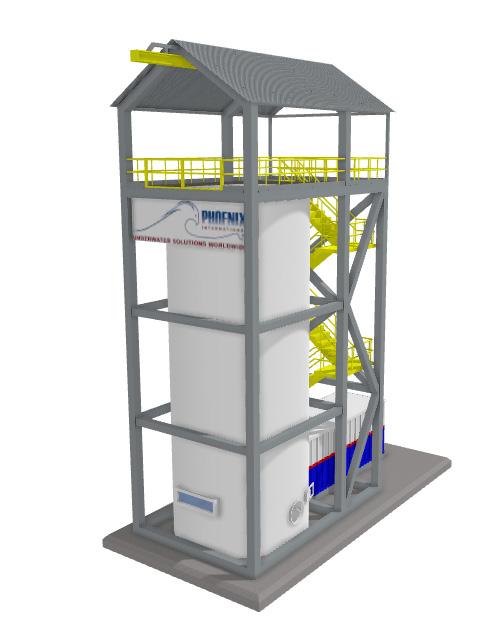
The new Phoenix dive tank
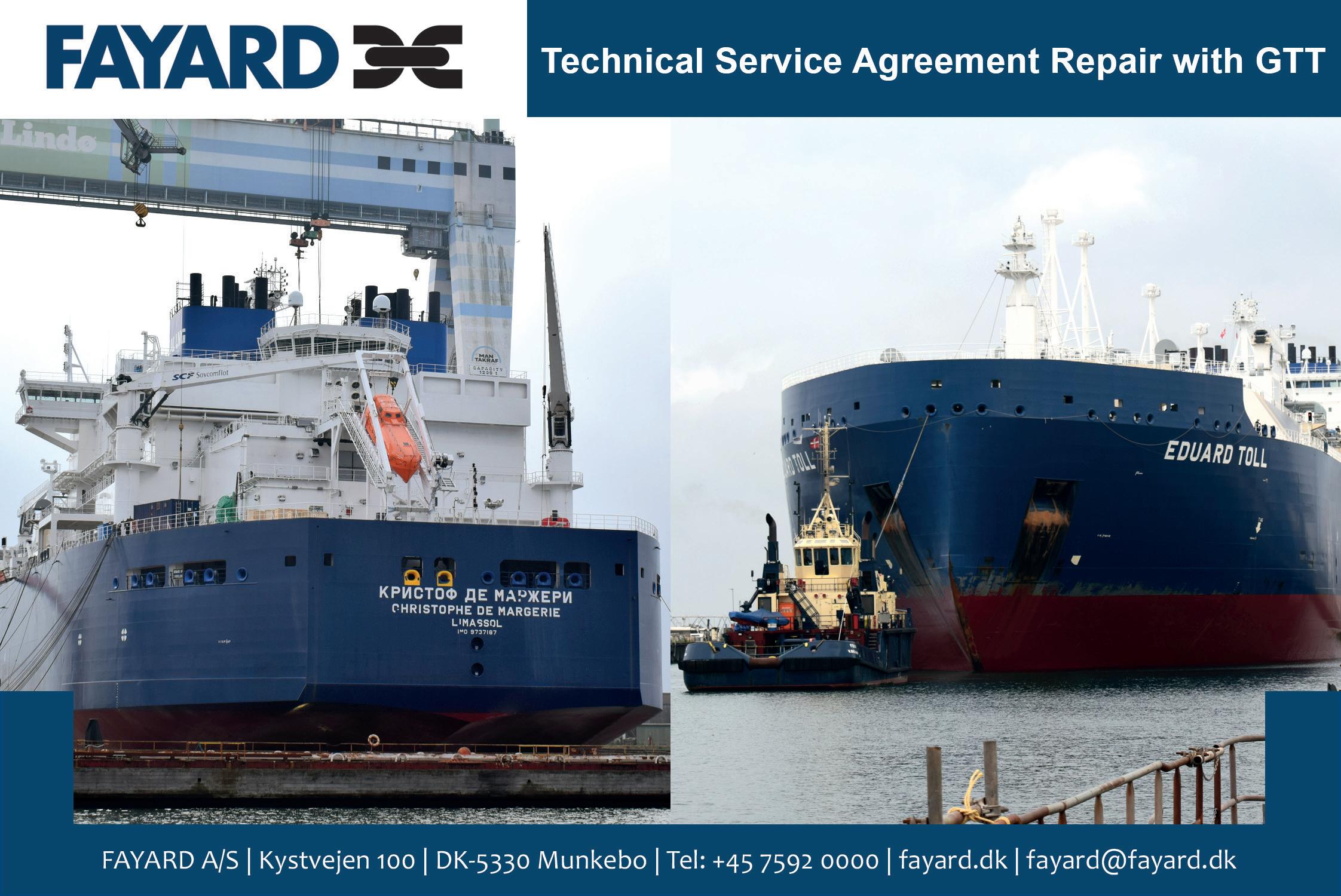
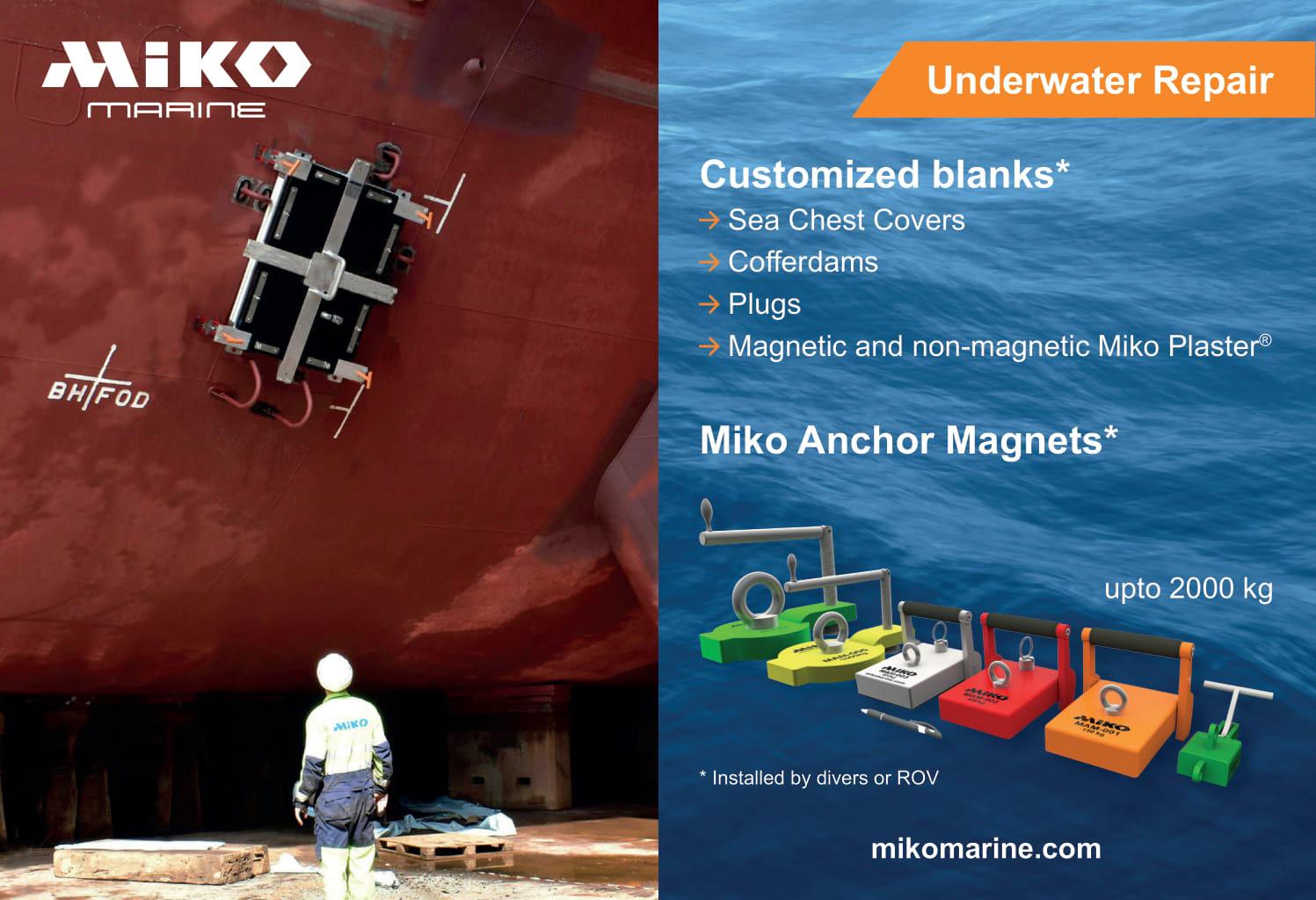