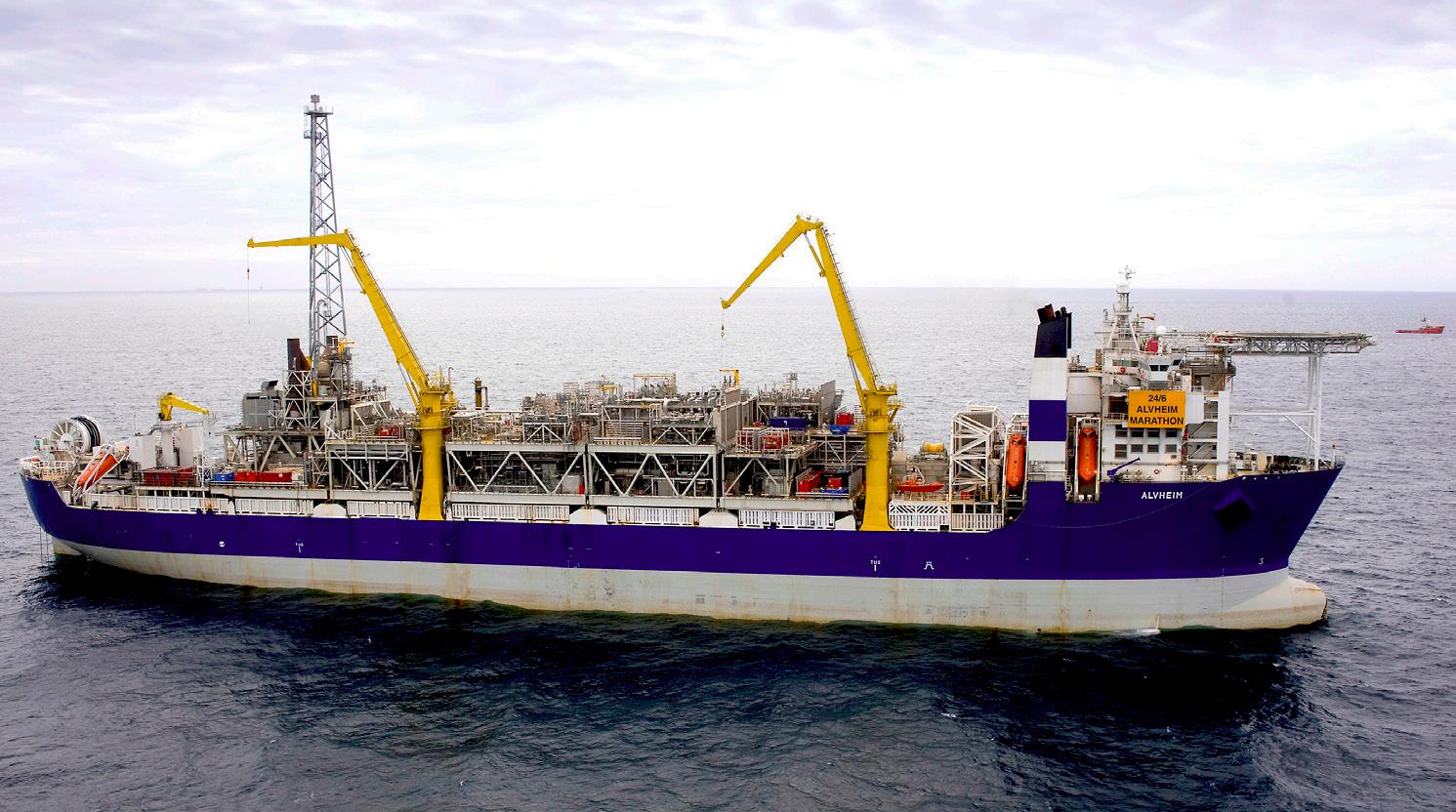
13 minute read
Offshore
Offshore contracts for Sulzer
The FPSO Sangomar
Advertisement
MODEC contract for MAN Energy
Japan’s MODEC has placed an order for six compressor trains for an FPSO unit with MAN Energy Solutions, which will be deployed on the Sangomar field approximately 100 kms south of Dakar, Senegal. Together with the nearby Rufisque and Sangomar Offshore blocks, it is one of the world’s largest oil & gas discoveries of the last decade.
“We are delighted and proud to have been selected to provide the memorable first FPSO for Senegalese waters,” commented Yuji Kozai, President and CEO of MODEC. “We consider West Africa where numerous offshore oil and gas fields have been discovered in recent years, as one of our most important core regions, and this contract award should geographically reinforce our business portfolio. We are equally pleased to be a part of the team that will provide a needed energy resource for the people of the Republic of Senegal. We look forward to cooperating closely with our clients and partners to make this project a success.”
“Senegal has a bright energy future ahead and we are proud that MAN Energy will take an active part by providing high-end technology solutions for the Sangomar field,” states Patrik Meli, Senior Vice President, Managing Director of MAN Energy Solutions Switzerland Ltd. “Gas is becoming economically and environmentally the world’s most significant energy source for the next couple of decades. This important order is a further testimonial of the trust put in our well-founded technology knowhow in the energy sector.”
The total order comprises six centrifugal compressor trains - one low pressure (LP), three medium pressure (MP) and two high pressure (HP), which are all driven by fixed speed electric motors. All compression systems will be designed, manufactured and tested by MAN Energy Solutions in Zurich (Switzerland). The machines will be ready for installation in the fourth quarter of 2021.
Once they are in operation, the compression systems will help in maintaining the pressure of the Sangomar field, thus maximising the quantity and efficiency of hydrocarbon production. The FPSO will be capable of processing 100,000 bbls of oil and 130m ft3 of gas/day. First production is planned for 2023.
Basil Zweifel, Vice President Sales and Execution Upstream and Midstream at MAN Energy Solutions, adds, “We are honoured to have the opportunity to work with MODEC on this project within the emerging energy market of Senegal. MAN Energy Solutions provides energy-efficient, highly reliable and cost-effective compression solutions. These are crucial requirements for new generation projects like Sangomar.”
Operators in the oil and gas market are continuously streamlining their production and optimising equipment performance. For Aker BP, which operates the FPSO Alvheim, this has led to the company awarding Sulzer a contract to retrofit a water injection pump (WIP) to meet its 2030 growth strategy.
As part of an on-going retrofit programme, Aker BP has been discussing future requirements of the WIP with Sulzer, taking advantage of the company’s expertise in pump design and manufacturing. In a first step, the original sevenstage WIP was modified to reduce it to six stages and the impeller trimmed to meet a change in performance requirements. Following on from this, many options of future process conditions were tabled but the final decision settled on was a 40% increase in flow and a 30% reduction in head.
The main prerequisites of the retrofit are to use the existing barrel and WIP motor while avoiding major modifications to the surrounding infrastructure. Teti Aure, Business Development Manager at Sulzer explains, “Our Norwegian
Aker BP’s Alvheim FPSO vessel
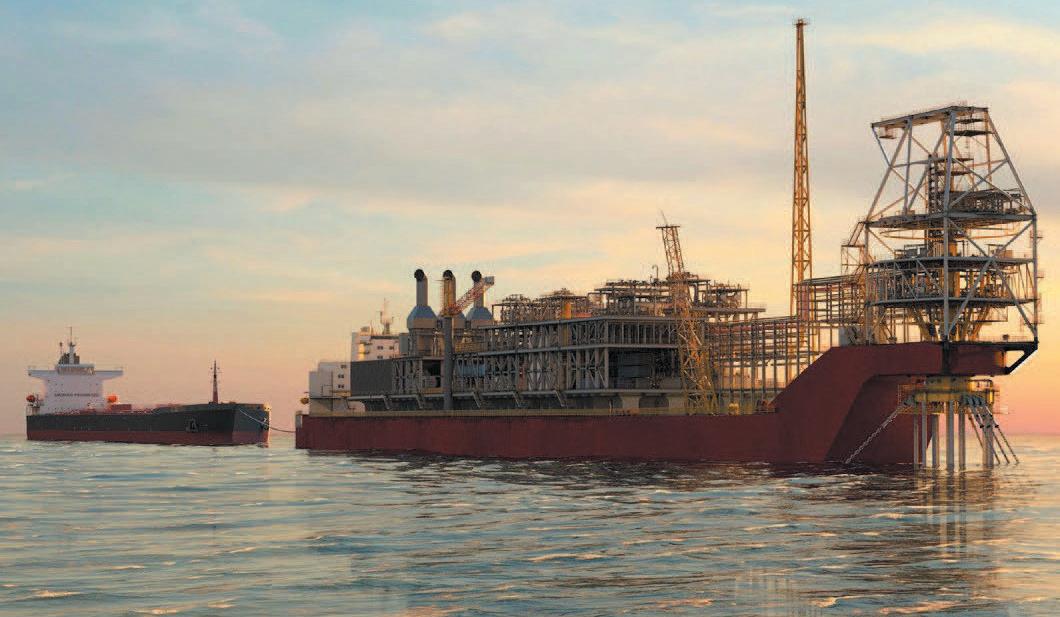
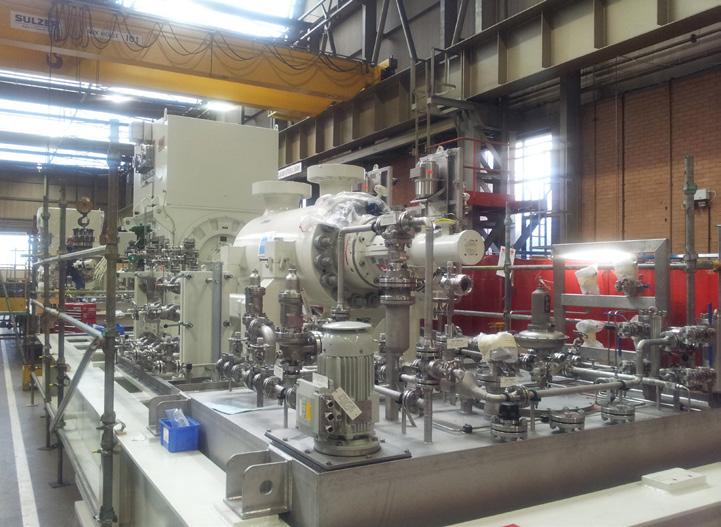
The Sulzer water treatment plant
service centre was supported by the company’s pump design centre in Leeds, UK, which is experienced with NORSOK standards. We have delivered a large number of projects with new hydraulics and new cartridge requirements, enabling customers to meet future process requirements.”
Sulzer’s retrofit solution is a hybrid cartridge design, which will be configured to fit within the existing pump barrel and maintain common components where possible to limit design and spare component changes. To meet net positive suction head (NPSH) margin requirements, the existing booster pumps will be retrofitted with larger diameter impellers to take into account future process conditions.
The new higher power booster motor, conforming to API 610 margins required for additional flow and head, will be supplied in the same frame size, avoiding any modifications to the baseplate and simplifying installation.
Karl Johnny Hersvik, CEO of Aker BP, said, “The development at Alvheim is an example for the entire Norwegian oil and gas industry. We must continuously work with efficiency – improve flow efficiency, find new reservoirs and phase in new wells – while continuously working to reduce costs. We will continue to ensure that Alvheim becomes a pattern field on the Norwegian continental shelf in the years to come.”
Meanwhile, work is underway in China to convert a former tanker into a FPSO, which will operate in the Marlim oil field off the coast of Brazil. When it enters service in 2023, the FPSO Anna Nery will have a production capacity of 70,000 bbls of oil/day and a storage capacity of 1.6m bbls.
A key part of the vessel’s functionality will be its high-capacity seawater treatment and injection (SWTI) system, capable of delivering 38,000 m3 (8.36m gallons) of seawater/day for enhanced oil recovery waterflood injection. At the heart of the process is a specialist sulphate removal membrane technology that protects the oil reservoir against barium and strontium sulphate scaling as well as reservoir souring.
In operation, the main water injection pumps will handle a combination of purified seawater and produced water from the well. Since produced water contains sand and other erosive materials, the pumps will include a number of features designed to increase durability, including double pressurised seals and tungsten carbide coatings on all wear surfaces.
The contract includes four 6 MW (8,000 hp) HPcp Type BB5 barrel pumps powering the water injection system, along with four BBS booster pumps that take filtered water from the treatment module and deliver it to the water injection pumps. In addition, Sulzer is also supplying a number of OH2 pumps which will be used to clean the membranes in the purification system.
The four WIP will include an integrated oil lubrication system and will be supplied with direct drive electric motors. These motors will be constructed to comply with the Brazilian INMETRO standard for operation in potentially explosive atmospheres. The pumps will be manufactured at Sulzer’s global plants, with installation and commissioning support provided by the company’s local facilities in Brazil. The availability of local support and expertise is a key benefit for Yinson, as the Anna Nery is contracted to operate in Brazilian waters for at least 25 years. In addition to the WIP contract, Sulzer will supply more than a dozen pumps for other systems on the vessel.
We have established an excellent working relationship with our colleagues at Yinson,” says Mike Sorrell, Key Account Manager at Sulzer. “We are very proud that Sulzer technologies have been selected for such an important and high-profile asset, and we look forward to supporting our partners during construction and in the field, as well as working on future projects together.”
SAP SE and DNV GL combine for the offshore industry
US-based SAP SE and DNV GL have teamed up to deliver a new industry cloud solution, Corrosion Under Insulation (CUI) Manager, designed to tackle a major problem facing the integrity of oil and gas plants.
Corrosion Under Insulation Manager is one of the latest industry cloud solutions built and run on the open SAP Cloud Platform. These industry solutions use intelligent technologies, such as artificial intelligence and advanced analytics, to create compelling user experiences and to digitalise and automate operations. SAP and partners focus on solutions for the core business of our customers in their industries to help optimise end-to-end processes and to enable the development of new and differentiating business models.
“In collaboration with DNV GL, we will deliver the first industry cloud solution for the oil and gas industry,” said Benjamin Beberness, SAP Oil and Gas Business Unit Global Vice President.
CUI is the largest maintenance cost for offshore and onshore installations with insulated
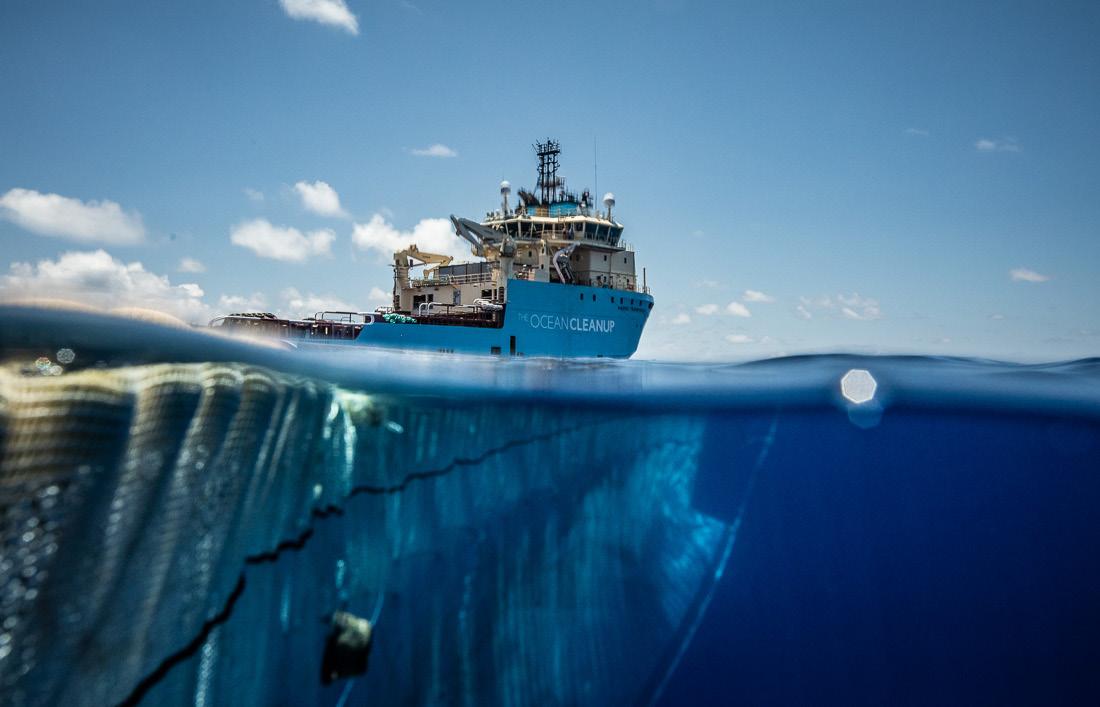
A.P. Møller-Maersk has extended its partnership with The Ocean Cleanup for three years
pipes. In close collaboration with the industry, DNV GL has developed a new risk-based methodology, published a new recommended practice and turned the insights into an easy-to-use interface with the CUI Manager. Through the strength of DNV GL’s models and the integration with SAP Asset Intelligence Network and the SAP Asset Strategy and Performance Management application, this solution will provide an efficient and standardised way to address the risk of CUI.
CUI Manager continuously assesses and calculates the CUI risk, helping integrity engineers and managers prevent failure, increase safety and manage hidden threats. It optimises asset strategy and planning by providing detailed, instant insights on current and planned risk as well as the resulting cost development. The solution’s full integration with SAP Asset Strategy and Performance Management enables calculation and visualisation of the complete risk picture using SAP Cloud Platform.
“The combination of DNV GL’s deep technical insight and state-of-the-art software solutions with SAP’s cloudbased solutions for intelligent asset management will generate significant value for our customers,” said DNV GL - Oil & Gas, CEO, Liv A. Hovem. “We look forward to bringing additional solutions to the market jointly with SAP in the near future.”
MSS continues with clean-up strategy
Denmark’s A.P. Møller-Maersk has extended its partnership with The Ocean Cleanup for three years, and Maersk Supply Service (MSS) will continue to provide marine support to rid the ocean for plastic. At the same time, MSS is launching a Plastic Policy to increase its focus on how it can reduce plastic waste from its own operations and supply chain.
Since 2018, MSS has provided marine support for The Ocean Cleanup. Its anchor-handlers Maersk Launcher, Maersk Transporter and Maersk Handler and crews have been supporting various test phases of the off-shore operation in the Pacific Ocean and the North Sea. The first collection of plastic waste was turned into new, fully recycled products in fall 2020.
“Our seafarers sail the ocean every day and see the increasing problem with plastic polluting our oceans. As a responsible maritime operator, MSS is committed to ensuring the oceans remain a healthy environment for future generations to come. We look forward to continuing the collaboration with The Ocean Cleanup and providing project management and marine support over the coming years,” says Steen S. Karstensen, CEO of MSS.
“By introducing a Plastic Policy, Maersk Supply Service is strengthening its focus on how it can reduce plastic waste. The policy has three navigating principles: • Use our marine expertise to help come up with solutions to rid plastic from the oceans
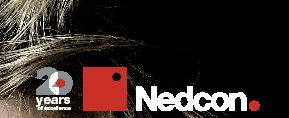
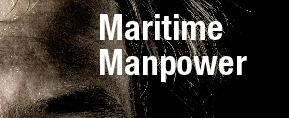
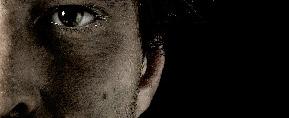
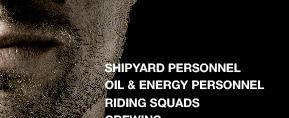
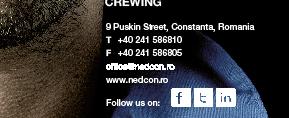
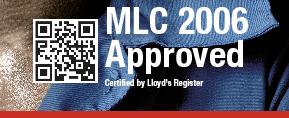

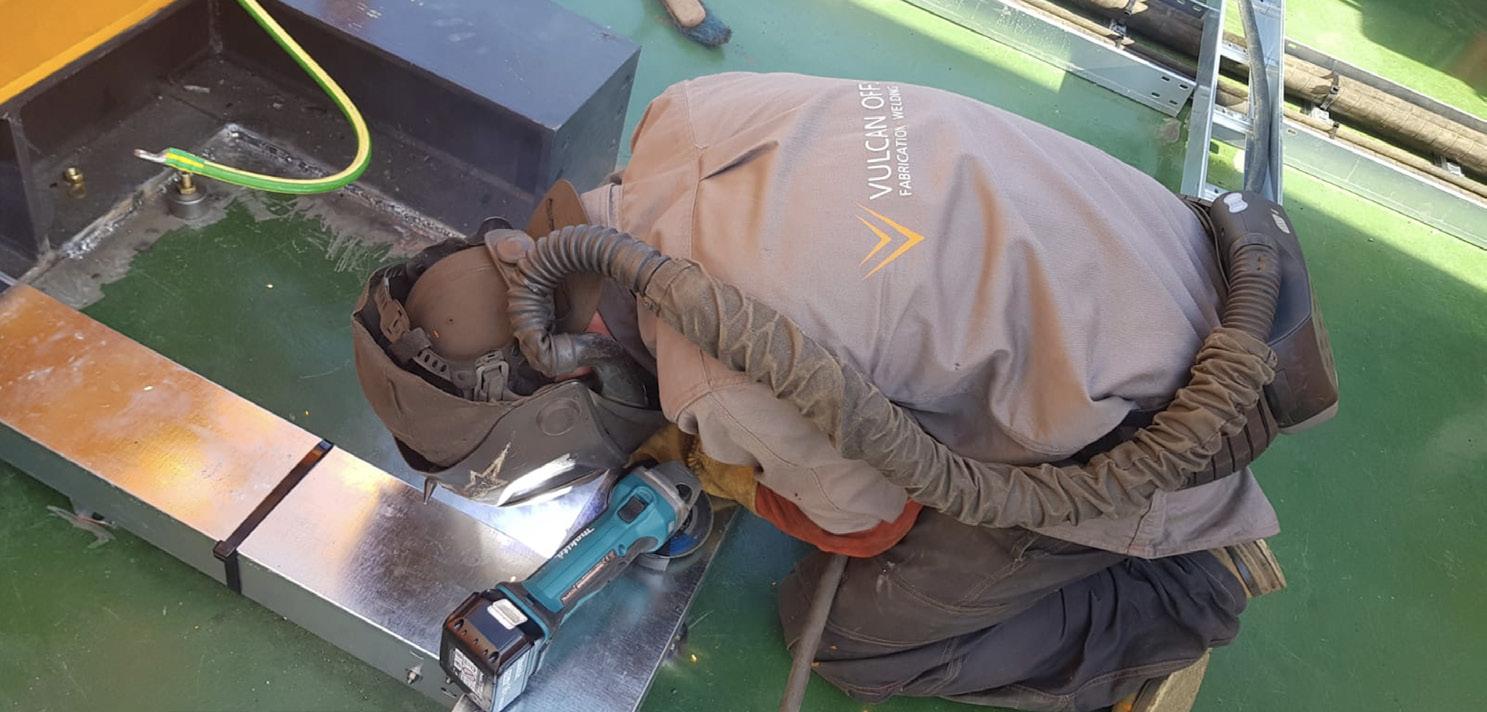
Work on the cable lay barge by Vulkan Offshore
•Avoid unnecessary plastic in our operations • Engage with suppliers, partners, customers and employees to find solutions to minimise plastic use. We will be transparent about our results and learnings
“Plastic waste in our oceans is an increasing issue. With the new Plastic Policy, we commit to how we will work to reduce our plastic footprint and actively take part in solving this global environmental problem. We will do this in partnerships and close collaboration – with our employees, suppliers, partners, customers and industry peers. A great takeaway from the collaboration with The Ocean Cleanup is the willingness people have to find solutions that are both impactful for the marine industry and are bettering for the environment. We believe that we can make a change and we can do more together,” says Karstensen.
Cable-layer mobilisation by Vulcan Offshore
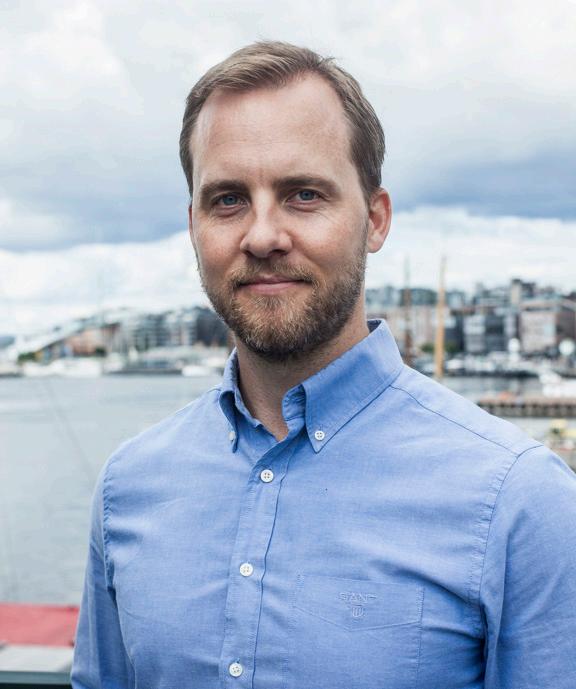
UK’s Vulcan Offshore has put an unnamed cable-lay vessel mobilisation at the centre of its multifaceted offshore service offering. Southampton-based Vulcan is a specialist in fabrication, welding and computer numerical control (CNC) machining for the marine and subsea industries. It principally works for cable lay companies that own or charter vessels for laying offshore wind farm or fibre optic cables for the telecommunications industry.
When a vessel, barge, or workboat prepares for an upcoming project, Vulcan’s clients typically have to modify and fit out the deck with winches, launch and recovery systems (LARs), cable engines, steps, ladders, and access platforms, etc. As the vessels perform different functions depending on the job, equipment needs to be fabricated or welded to the deck of the ship.
Chris Scrutton, managing director at Vulcan, said, “We offer a comprehensive welding and fabrication service, which can be delivered in our workshop, on- and offshore. It’s proved to be a differentiator that we’re ideally located [near the Southampton port] on the south coast and we have personnel skilled in MMA [manual metal arc], MIG [metal inert gas], and TIG [tungsten inert gas] welding - we also have welders who are CSWIP 3.2 certified.”
As Scrutton explained, this breadth of welding expertise is important because of the varied requirements within the industry. For example, MMA or MIG welding might be used onsite, while TIG is specifically related to stainless steel, most commonly in the Vulcan workshop. Nondestructive testing (NDT) via magnetic particle inspection (MPI) or dye penetration is also integral to many scopes of work.
He added, “The sector is apparently buoyant as we move through 2021 and we are keen to align ourselves with continued activity in the renewable energy sector, especially around wind farm installation. Meanwhile, as internet usage continues to grow, we have a long-term role to play in fibre optic cable laying.”
Equinor agreement for Yxney
Norway’s Equinor has signed a deal with Yxney to roll out the Maress software for data driven decarbonisation for their chartered offshore service fleet operating in Norway. The new contract is a timely fit with Equinor’s expressed ambition to half their maritime emissions in Norway by 2030 compared with 2005, and globally by 2050, compared with 2008.
These ambitions are embedded in the company’s climate roadmap that were launched earlier this year. Using Maress to facilitate close co-operation with the vessel owners and suppliers of innovative technology will enable Equinor to unlock significant fuel and emissions savings.
Maress will be used to track the footprint and efficiency of Equinor’s chartered fleet of PSVs and anchor-handlers operating on the Norwegian Continental Shelf. The fleet chartered by Equinor Marine Operations on medium and long-term contracts currently numbers around 30 vessels. The agreement with Yxney has a two-year duration, with an option to extend.
“Maress will allow Equinor to follow the effect of efficiency measures and facilitate systematic improvements and best practice across the various ship owners in the chartered fleet,” says Yxney CEO Simen Sanna Gjord.
Noting that an increasing number of vessels chartered by Equinor are battery hybrid powered, Sanna adds, “Maress can help Equinor and the ship owners to gain a deeper understanding of the emissions reductions achieved by battery installation, and how batteries impact fuel consumption in the various areas of operation.”
Sanna reports that the combined savings of the 250+ vessels using Maress globally in 2020 will be in excess of 50,000 tonnes of CO2. “This is clear evidence of the effectiveness of datadriven decarbonisation, and the contribution to greener shipping that Maress can provide for ship owners and operators,” he concludes.
SORJ
Simen Sanna Gjord - Co-Founder & CEO of Yxney