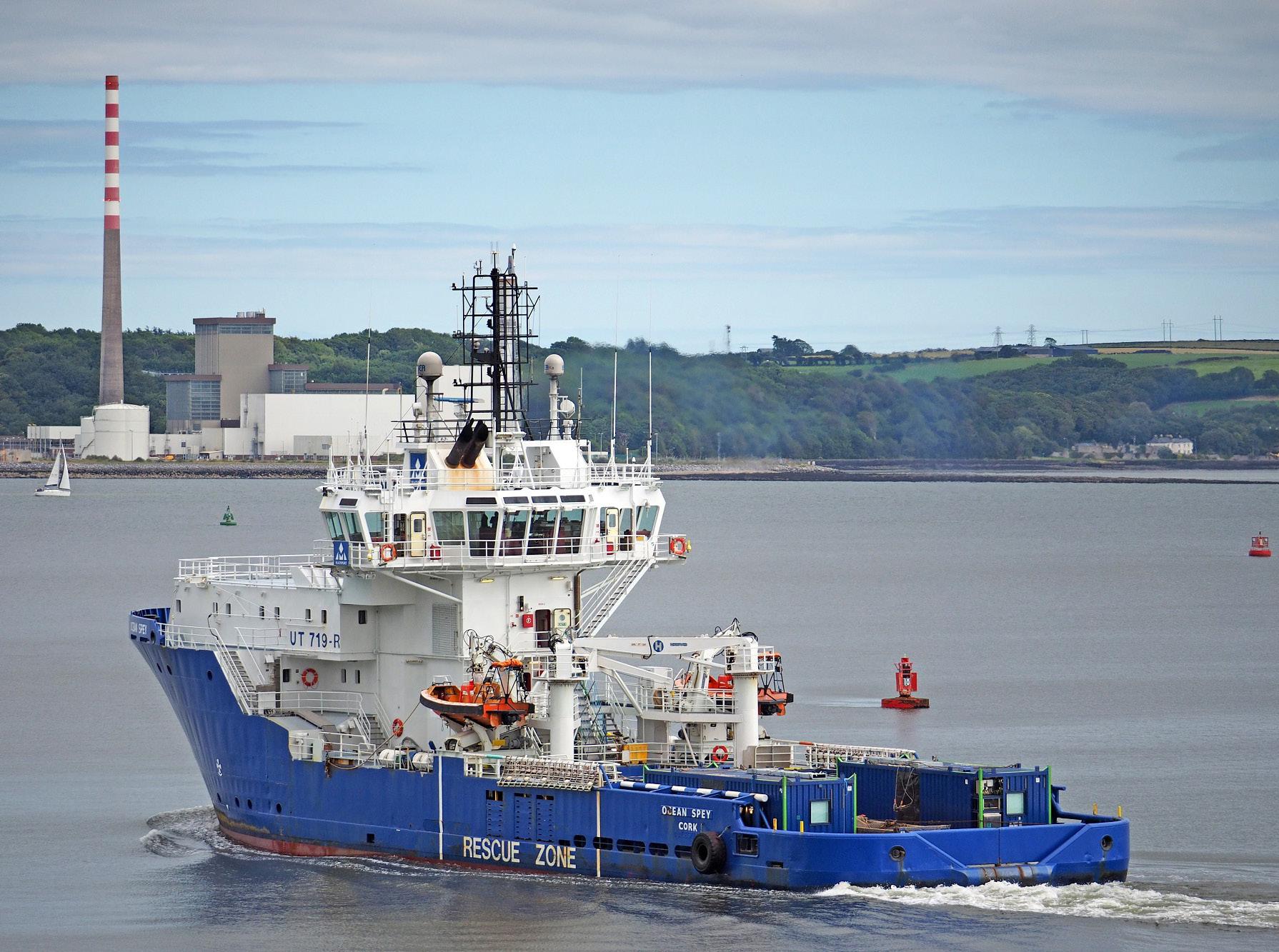
17 minute read
Machinery Repairs
Machinery
Nigerian installation and OSV retrofit for Royston Marine
Advertisement
UK’s Royston Marine has completed the installation of an electronic fuel management system on-board a new offshore surfer crew boat, which will be operated by Norfin Offshore Group to support its marine and offshore operations in Nigeria. The scope of work involved the supply of an enginei system, featuring on-board HMIs (human machine interface) and remote web management portal, for its latest new building delivery of the 20 m boat, which was designed and constructed in Singapore.
The enginei system was commissioned when the boat arrived in Nigeria in November 2020, where Royston provided training as part of its aftersales care and support package to ensure the operator and crews are fully familiar with EFMS operations. Offering comprehensive, easy-to-understand fuel data analysis and reporting options, enginei is an advanced fuel monitoring system. It can be installed as part of a comprehensive suite of digital marine technologies, delivering long-term operational efficiency and performance.
Following the installation of similar systems on its 120T BP anchor-handler and 35 m fast crew boat, Norfin Offshore has continued to invest in enginei technology to meet its requirements for cost effective, regionally supported electronic fuel management systems, which help to improve fleet operations.
Norfin Offshore Group provides a comprehensive range of services including ship building, shipowners and operators, vessel managers to various shipowners and oil majors in West Africa and the South East Asia region. With the recent launch of Norfin Offshore Shipyard in Akwa Ibom, Nigeria – the group sees a growing demand for more enginei systems to be installed on its upcoming newbuild OSVs.
The enginei system has been installed by Royston’s Singapore-based operation, which is seeing strong demand from regional vessel owners and operators looking for easy-touse and flexible technology with accurate measurement, control and analysis of fuel consumption.
This latest installation takes the number of vessels deploying enginei to more than 300 plus in over 14 countries, including OSVs such as anchor-handlers, jack-ups, PSVs and crew boats, operating in the UK, Europe, Asia, North Africa, West Africa, North and South America and the Middle East.
Enginei uses Coriolis flowmeters and sensors to accurately monitor the fuel being consumed by a vessel’s engine. This provides the ability to acquire comprehensive real time engine and vessel performance measurements beyond the usual RPM, GPS and fuel inputs to take in a wide range of other engine control unit outputs.
The data is displayed live through a touch screen bridge display. Information is also transmitted remotely to the enginei web portal where the state-of-the-art interface enables the rapid production of intuitive online reports and trending graphs, as well as providing alerts and map dashboard tracking with weather overlays, showing a detailed operational profile for a vessel.
Meanwhile, work to overhaul main propulsion diesel engines on three Mainport vessels has been completed by marine engineering and propulsion specialist Royston. The work saw engineers from UK’s Royston complete major overhauls on two Bergen KRM9 main engines on-board the 1,864 gt OSV Ocean Spey, as part of a planned maintenance programme of critical power systems.
Completed by the Royston team while the vessel was docked in Cork dockyard, the servicing involved the engines being disassembled to install overhauled cylinder heads, fuel pumps and injectors. Valves, pistons and conrods, cylinder liners, bearing blocks, crankshaft were also checked, and essential repair and replacement work carried out before reassembly and inspection of the engines.
Similar work to overhaul two Niigata 6L28BXE main engines on-board the 309 gt tug Celtic Rebel has also been completed as part of a package of engineering support provided by Royston. This saw the removal and inspection of two units, overhaul of the fuel injection equipment and 12,000-hour overhaul on two NHP30 turbochargers.
Two Cummins KTA38 propulsion engines onboard the 476 gt tug Mainport Kells were also serviced earlier in 2020 by engineers as part of scheduled maintenance and refurbishment ahead of the boat being transferred to new owners in France. This also saw the replacement of 12-cylinder heads with service exchange heads as part of the 50,000 running hours service of the main port engine. Engineers carried out incremental load testing in line with the engine manufacturers’ specifications on all the vessels following completion of the work.
The Ocean Spey and Celtic Rebel are currently part of a fleet of survey and research ships, seismic support vessels and tugboats owned and operated by Cork-based Irish Mainport Holdings, which is a provider of marine services to ship-owners, exporters, importers, oil companies, survey companies and offshore wind companies.
Royston has completed services to diesel engines on-board Mainport vessels including the Ocean Spey
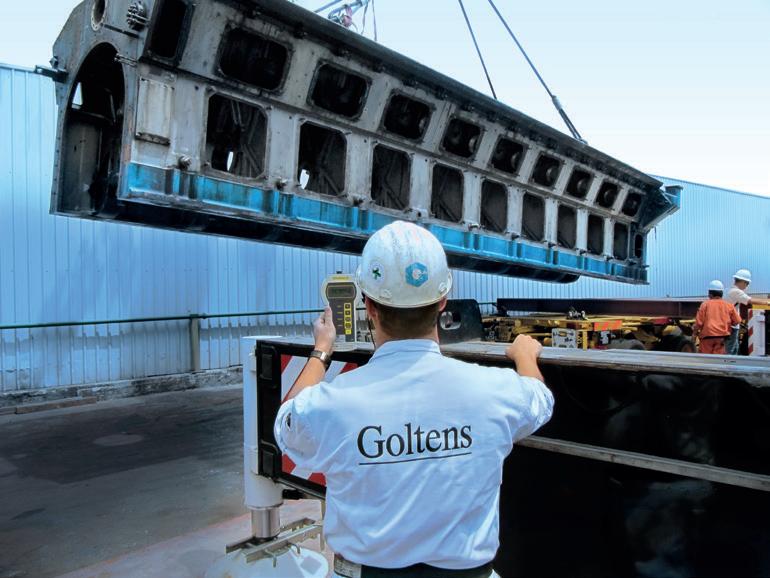
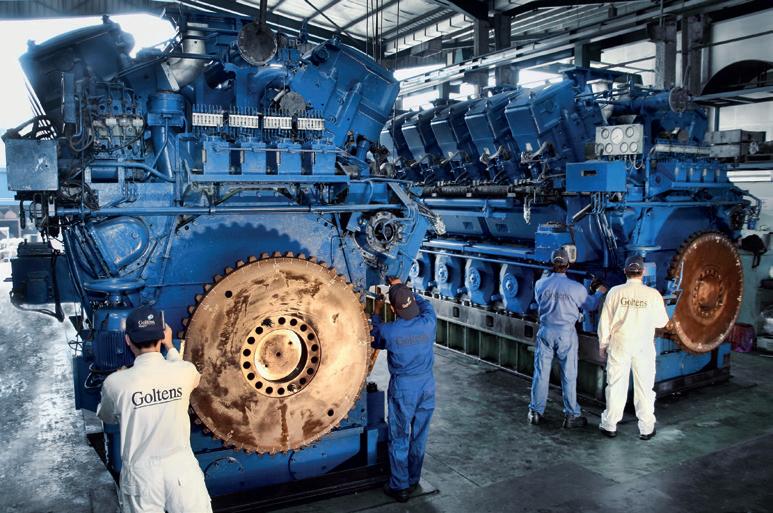

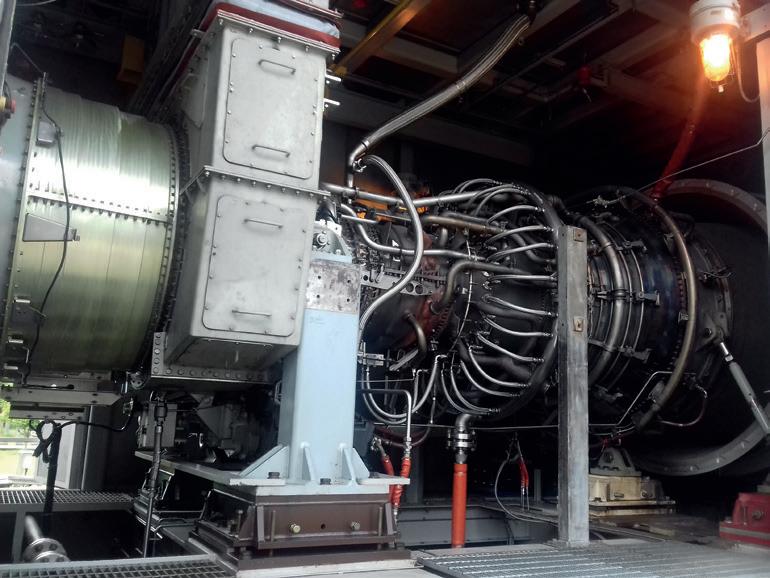



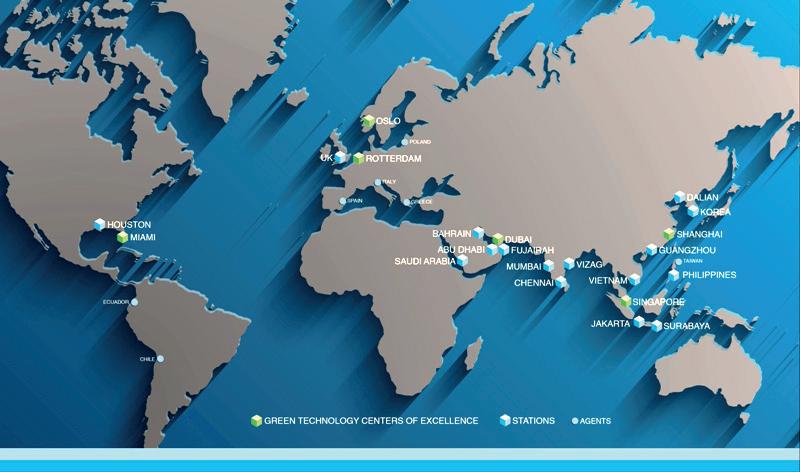
Cruiseship contract for Thordon
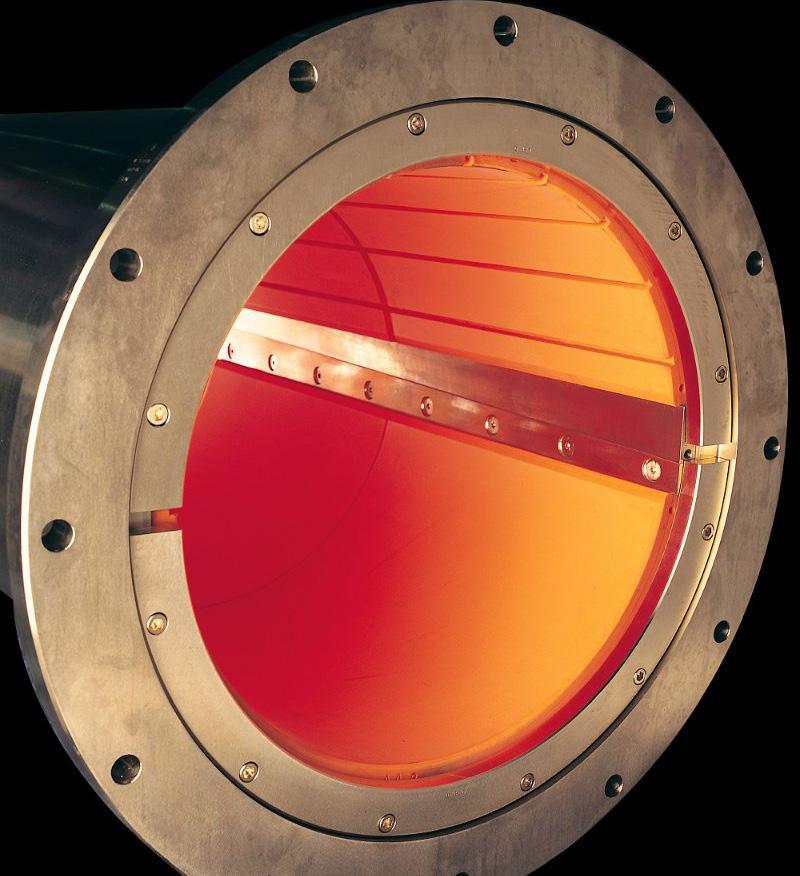
The new Thordon Bearings’ shaft bearing
A recent inspection of the 20-year-old waterlubricated propeller shaft bearings installed on a twin-screw cruise ship were found to be within classification society parameters and suitable for continued use for a further 10 years of operation. At the shipowner’s request, Thordon Bearings – the market leader in water lubricated bearing technologies – attended the docking at France’s Damen Shiprepair Brest, France, to assess the propeller shaft liners and outboard bearings of the 2,500 passenger-capacity cruiseship. The award-winning COMPAC bearings were installed in 1999.
The condition of the 83,000 gt vessel’s shaft liners – themselves indicative of successful bearing performance – was equally impressive. Gus Juarez, Thordon Bearings’ technician from the Global Service & Support team involved in the inspection, said, “There were some minor circumferential marks on the shaft liners, but they looked well-polished. There was no indication of circumferential grooving or damage. All liners were determined to be in satisfactory shape.”
Copies of all the inspection videos were provided to the Lloyd’s Register (LR) surveyor and shipowner representatives following the October drydocking. According to Butt, the reliability and near-obsolescent maintenance requirement of a seawater lubricated shaftline is one of the main reasons why the cruise sector increasingly favours a conventional propeller shaft arrangement over a podded propulsion system.
The shaft inspection at the yard is the second cruiseship to emerge from a drydocking with a Thordon bearing in near perfect condition after decades of operation. In September 2015, during the inspection of a sistership, surveyors recorded a bearing wear down of 7 mm. This was 17 years after the system was installed.
Thordon has supplied water-lubricated bearing systems to cruise ships operated by, among others, Princess Cruises, Seabourn, Disney Cruises, Viking Cruises, MSC Cruises, P&O Cruises, Oceania, and Regent Seven Seas.
Wärtsilä retrofits for Taiwanese and Norwegian owners
Wärtsilä will supply its Fixed Pitch Propeller (FPP) and EnergoProFin solutions for two containerships owned by Taiwan’s Yang Ming Lines. As containership operators continue to seek energy savings through slow steaming, the necessary engine adjustments need to be matched by the propeller arrangement. The Wärtsilä solutions enable this adjustment, allowing the speed of the two vessels to be reduced from 24 to 18 knots.
The two vessels, the YM Mobility and the YM Milestone, are the last in a series of four Yang Ming ships to be retrofitted with the Wärtsilä FPP and EnergoProFin solutions. The two earlier retrofit projects have resulted in energy savings in the region of three to five percent. The newly designed Wärtsilä propeller mass is approximately 27% lighter than the ships’ existing propellers. The EnergoProFin post-swirl device reduces energy losses from the flow around and behind the propeller. The Wärtsilä equipment is scheduled for delivery in March and June 2021 to the Changhong Shipyard in China where the retrofitting will take place.
Meanwhile, the Wärtsilä Hybrid Upgrade solution has been selected for retrofitting two offshore construction vessels owned by Norway’s Østensjø Rederi. The upgrading project will allow less use of the ships’ engines with correspondingly lower levels of exhaust emissions while operating in dynamic positioning (DP) mode, and will also lower emission levels in all other operational modes.
The two 9,464 gt ships, the Edda Fauna and Edda Flora, were built in 2008. The customer opted for the Wärtsilä Hybrid Upgrade solution in order to give the ships a more attractive environmental profile for potential charterers. The Wärtsilä Hybrid Upgrade solution will include the company’s new electronic DC bus-link, which allows a vessel to operate in DP 2 and 3 modes with a closed DC bus in hybrid, and an open bus on the AC system. The reduced running of the engines saves fuel and lessens the carbon footprint, while engine maintenance requirements are also alleviated.
By combining its competences in marine electrical, automation and engine technology, Wärtsilä has brought together multiple functions and systems to deliver a single integrated hybrid power module that combines engines, an energy storage system, and power electronics optimised by a unique and highly sophisticated, energy management system (EMS).
The EMS functions as the ‘brain’ in the Wärtsilä Hybrid System optimising the energy flows between the different power sources, storage and consumers to achieve the highest efficiency possible.
Wärtsilä has also won a further order for the company’s LPG Fuel Supply System (LFSS). Norway’s BW LPG had ordered the system to be retrofitted to three LPG tankers in 2018, and an additional eight systems in February 2020. This latest order for three vessels brings the total to be delivered to the same customer to 15, thereby emphasising its satisfaction with the technology.
The initial order was placed following Wärtsilä’s successful full-scale testing of the system in 2018 with a full-sized 2-stroke marine engine operating on LPG fuel. This was the world’s first such testing protocol. For the retrofitting, Wärtsilä has been designated as the system integrator, which involves not only installation of the system, but also the required ship design modifications. Retrofitting of the latest three systems for BW LPG will take place at the end of 2021 or the beginning of 2022.
Wärtsilä has also signed a five year extension to its Optimised Maintenance Agreement (OMA) with Golar Management Norway, the operator and manager of a fleet of LNG tankers and FSRUs. The agreement covers a total of 16 ship installations - 14 with Wärtsilä 50DF dual-fuel engines, plus two with Wärtsilä 34DF dual-fuel and Wärtsilä 20DF dual-fuel engines. The extension contract was signed in December
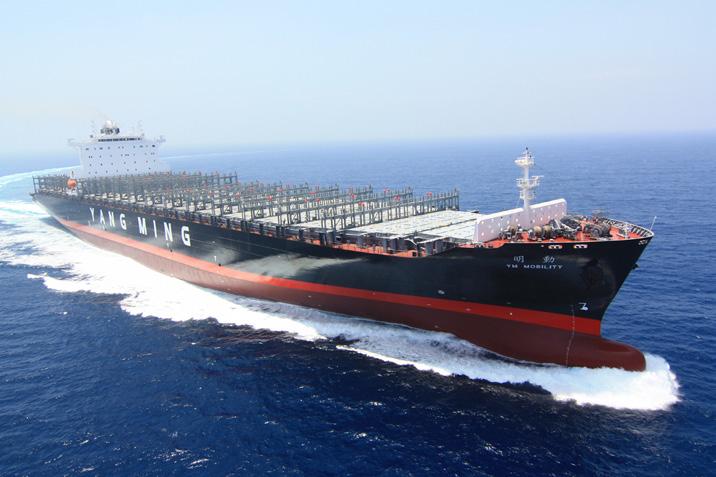
The YM Mobility
2020.
The agreement will enable Golar to pursue a predictive maintenance strategy enabled by Dynamic Maintenance Planning and Asset Diagnostics. Wärtsilä’s Operational Support provides round-the-clock remote support and actionable advice from Wärtsilä Expertise Centres. The combination of advanced diagnostics and Wärtsilä’s deep equipment expertise greatly enhances the safety, reliability and efficiency of the equipment and systems installed. It will also provide flexibility in maintenance scheduling by conducting maintenance based on actual equipment condition optimised for the vessels’ operations.
The new five-year Lifecycle Solution agreement includes 14 vessels that have had a five-year OMA earlier and two new additional vessels.
Cruiseship and LNG retrofits for MAN Energy
The Ultra-compact SCR (Selective Catalytic Reduction) system adapts to limited space and will meet exacting Norwegian emission standards – a retrofit reflects general cruiseindustry desire to move towards sustainability.
MAN Energy Solutions’ after-sales division in Augsburg, Germany– MAN PrimeServ Augsburg – has developed an SCR solution that will be retrofitted on-board Phoenix Reisen’s 28,856 gt Amadea, a cruiseship managed by BSM Cruise Services. Also known as Das Traumschiff, the Amadea is well-known in Germany as the main filming set for a very popular television series.
The retrofit devised by MAN PrimeServ Augsburg calls for the integration of two of MAN’s SCR systems, one each into both of the Amadea’s four-stroke MAN 7L58/64 propulsion-engines, to ensure maximum performance. Installation will begin in September 2021.
The retrofit reflects a general desire by Phoenix to enhance its environmental friendliness and, more immediately, will enable the vessel to meet emission standards in the key Norwegian Heritage Fjord market. For the project, MAN PrimeServ prioritised keeping hazardous emissions to a minimum while maintaining engine performance and propulsion efficiency.
MAN PrimeServ Augsburg has previously retrofitted the Amadea’s turbochargers – in the process improving engine efficiency and significantly reducing CO2 emissions – and also introduced MGO instead of HFO injection nozzles in order to minimise black-carbon emissions. The combined work carried out on the vessel reflects MAN Energy Solutions’ desire to increasingly become a supplier of complete propulsion solutions.
The MAN SCR solution will bring the Amadea’s engines from Tier 0 status to Tier III emission level, and will reduce NOx emissions by 90%, equivalent to savings of 600 tonnes/ year. MAN’s SCR system is the greenest solution available on the market with the highest operational readiness and safety - the SCR will be available from just 15% engine load, enabling clean operation, also during slowsailing in the fjords as well as close to port and populated areas.
The fully modular SCR solution will be integrated into the Amadea’s engine-control system. With its closed-loop system and a weather station that uses environmental data, the NOx-reduction rate is maximised and ammonia-slip minimised to 10 ppm, comparable to that of a car. Low ammonia slip is not just good because ammonia is a greenhouse gas and affects the climate, but also because it reduces urea consumption, enabling the urea-tank size to be reduced.
A feasibility study run by MAN PrimeServ at the beginning of the project confirmed the suitability of the compact, modular SCR system for the limited space available on-board the vessel. Its integration into the narrow funnel is only possible due to the special 87cpsi honeycombs and their high reactivity in a twolayer slim reactor design.
Meanwhile, Norway’s BW LPG has announced that it will retrofit a further three MAN B&W 6G60ME-C9.2 type engines to MAN B&W 6G60ME-C9.5-LGIP dual-fuel types, capable of operating on fuel oil and LPG. This is another option of a 4+4+4+3 contract with MAN PrimeServ – MAN Energy Solutions’ after-sales division.
MAN Energy Solutions announced the first four retrofit orders in September 2018 in advance of the official launch of the ME-LGIP engine at its Research Centre Copenhagen, and exchanged the contract publically with BW LPG during the event. Two + four options were subsequently confirmed with this new third option making a total of 15 vessels for ME-LGIP retrofits.
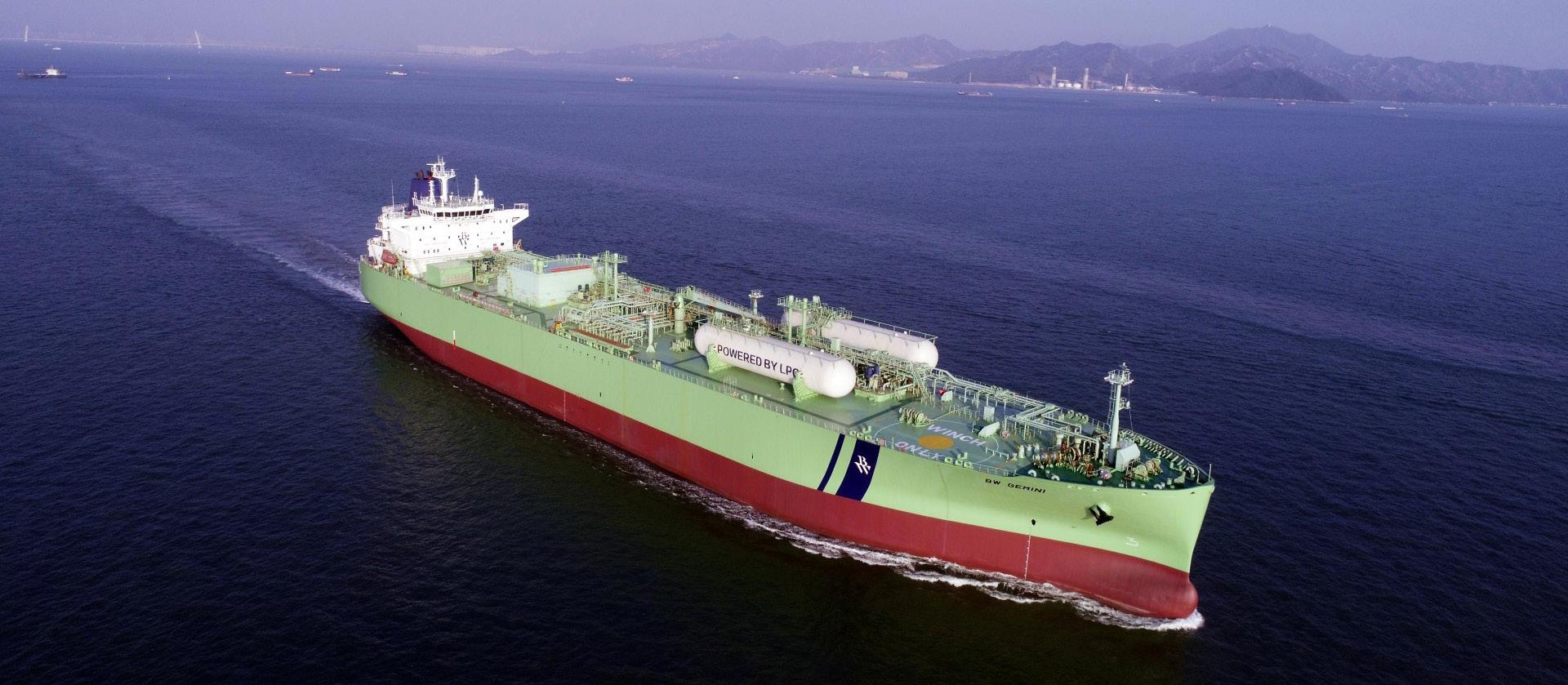
The confirmation of the latest option follows on the heels of the successful ME-LGIP conversion in late-October 2020 of the main engine on-board BW LPG’s LPG carrier, BW Gemini making it the world’s first commercial vessel to be propelled by a two-stroke LPG dual-fuel engine.
With LPG as a marine fuel, the BW Gemini’s output efficiencies rise by around 10% against fuel oil, which will in turn generate notable gains in total voyage fuel-economics. This, along with other advantages, secures LPG’s position as a long-term, sustainable marine fuel.
Cost-wise, LPG is also a better option than compliant fuel oil, with high lifetime-savings prospects. By leveraging LPG as a marine fuel, BW LPG’s tankers benefit from savings due to lower fuel consumption and full dual-fuel flexibility, which guards against price sensitivity to post-2020 fuel price fluctuations. Furthermore, the ability to use LPG cargo as a supplemental fuel source also reduces time and fees for fuel bunkering.
Harnessing LPG propulsion translates into cleaner, more efficient engines that are cheaper to maintain. In addition, the fuel flexibility of dual-fuel engines ensures full redundancy for uninterrupted operations.
Simultaneously, MAN PrimeServ’s research showed that a retrofit would be the most environmentally friendly solution. A retrofitted tanker generates 35 times lessCO2-emissions compared to a newbuild vessel and, compared to 2020-compliant fuels, using LPG as a fuel would reduce SOx by 99%, CO2 by 15%, NOx by 10%, and particulate matter by 90%.
ABB Turbocharging/ Hyundai agreement
A new agreement between ABB Turbocharging, Hyundai Global Service (HGS) and Hyundai Heavy Industries’ Engine & Machinery Division (HHI-EMD) has established a ‘total service solution’ for ABB and Hyundai customers, delivering optimal efficiency and emissions performance across the entire vessel.
Under the agreement, ABB Turbocharging will support HGS in providing long-term maintenance and service to its customers. As part of this support, HGS will be able to access ABB’s global network of turbocharging service stations. By adding this turbocharger service capability, HGS can offer customers a complete lifetime service agreement covering engines and turbochargers.
HHI-EMD, HGS and ABB have also agreed to co-operate more closely on data sharing. This will enable the companies to help customers further reduce their operating costs and minimise emissions by maintaining the highest possible engine efficiency. Insights gained rough data sharing will also facilitate the development of more data-based offerings to further enhance customers’ service experiences.
In addition, HHI-EMD and ABB will collaborate on the development of eco-friendly, efficient upgrade solutions for existing HiMSEN four-stroke engines, further supporting their customers in delivering more sustainable operations.
Lee Ki Dong, CEO & President of Hyundai Global Service, said, “The agreement with ABB Turbocharging means that HGS becomes a one-stop service company covering both engine and turbocharger service. We are delighted to enter this partnership with ABB, which enables us to offer even better value to our customers.”
Roland Schwarz, Head of Global Service, ABB Turbocharging, added, “The strengthened relationship with HGS and HHI-EMD will enhance service options for customers of ABB turbochargers. Through dedicated offerings, leveraging our global network and sharing data, we are supporting HGS to provide top-quality service for our products.”

ABB Turbocharging, HGS and HHI-EMD strengthen turbocharge service partnership
Tallink to use Qtagg’s EcoPilot
As part of its on-going programme to increase fuel efficiency, Estonia’s Tallink Grupp has installed Qtagg’s EcoPilot system on the 34,386 gt cruise ferry Isabelle. EcoPilot is a voyage optimisation tool incorporating autonomous speed and power control as well as weather routing. The software controls the propulsion machinery to arrive on time at lowest total cost. The unique feature of EcoPilot is that it manages the entire voyage by calculating an optimum power plan and executing it automatically, with little or no manual intervention. The verified results on Isabelle have been a reduction of 7% in fuel consumption and emissions.
The 2,500 pax, twin CP propeller ferry Isabelle was built in 1989 and acquired by Tallink seven years go. The vessel is usually deployed on a daily cruise service between Stockholm, Sweden and Riga, Latvia.
EcoPilot gives the captain full control over the ship’s performance and new ways to achieve sustainable operation of the vessel. During more than 50 voyages during the summer, using EcoPilot has given a reduction of 7% in fuel consumption and emissions. These results were verified by sailing with the EcoPilot system operational and non-operational on alternate round trips.
By linking various on-board systems, EcoPilot simplifies and digitalises the ship operation process for the personnel. An intuitive user interface combines all the required information and covers all technical needs and routines.
The system offers route planning/optimisation and fuel efficiency monitoring. With intuitive quick steps, the user can plan and optimise the route in seconds. Follow-up and re-planning is completed directly in the chart with clear information on the ship’s resulting performance and progress.
Weather forecasts are automatically updated, and the route is re-optimised when added information is available. Thus, the ship arrives at
the next port just-in-time at the lowest cost with a minor intervention from the crew. The system enables on-board ship performance analysis and strategic planning. Ship-to-shore links enable remote support from Qtagg.
EcoPilot connects the entire propulsion chain, so that normally independent systems work together to optimise the ship’s performance. The system reads data from sensors monitoring more than 60 parameters in real time, including engine performance, propeller performance, rudder lift and drag forces, ship motion and navigational information. Data from previous voyages together with weather and sea forecasts are used to minimise the total fuel consumption for each voyage. EcoPilot is an intelligent speed pilot, which will automatically give the best result in any weather condition.
During the voyage, the system automatically adapts to changing operational requirements, operator input, sea, and ship conditions, continuously using all available information to ensure on-time arrival at the lowest cost, every voyage. SORJ
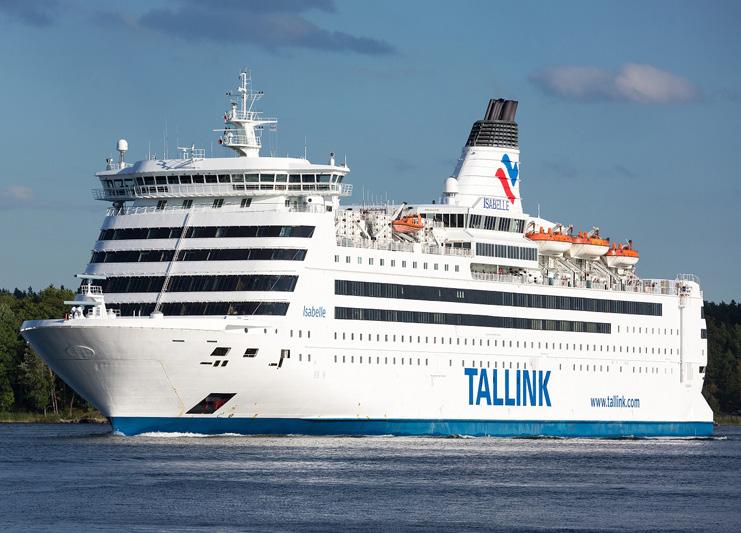
Tallink’s ro/pax ferry Isabelle
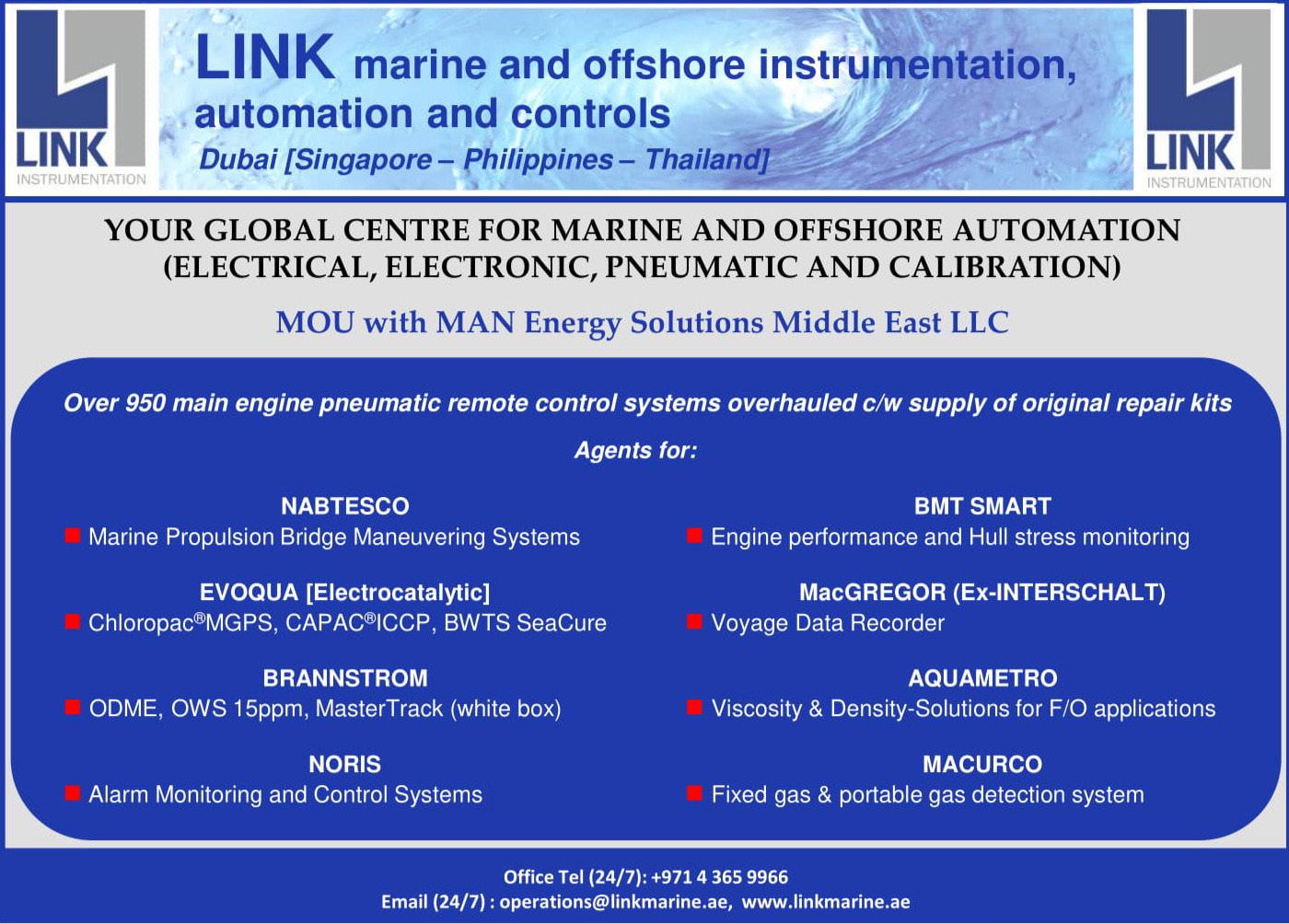