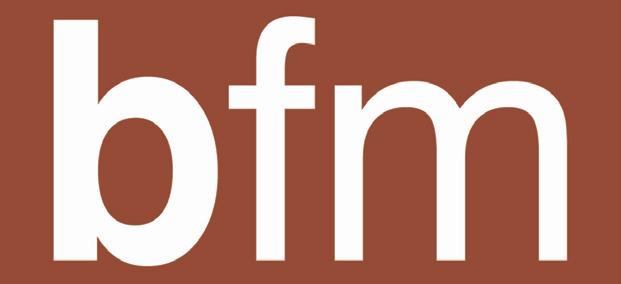
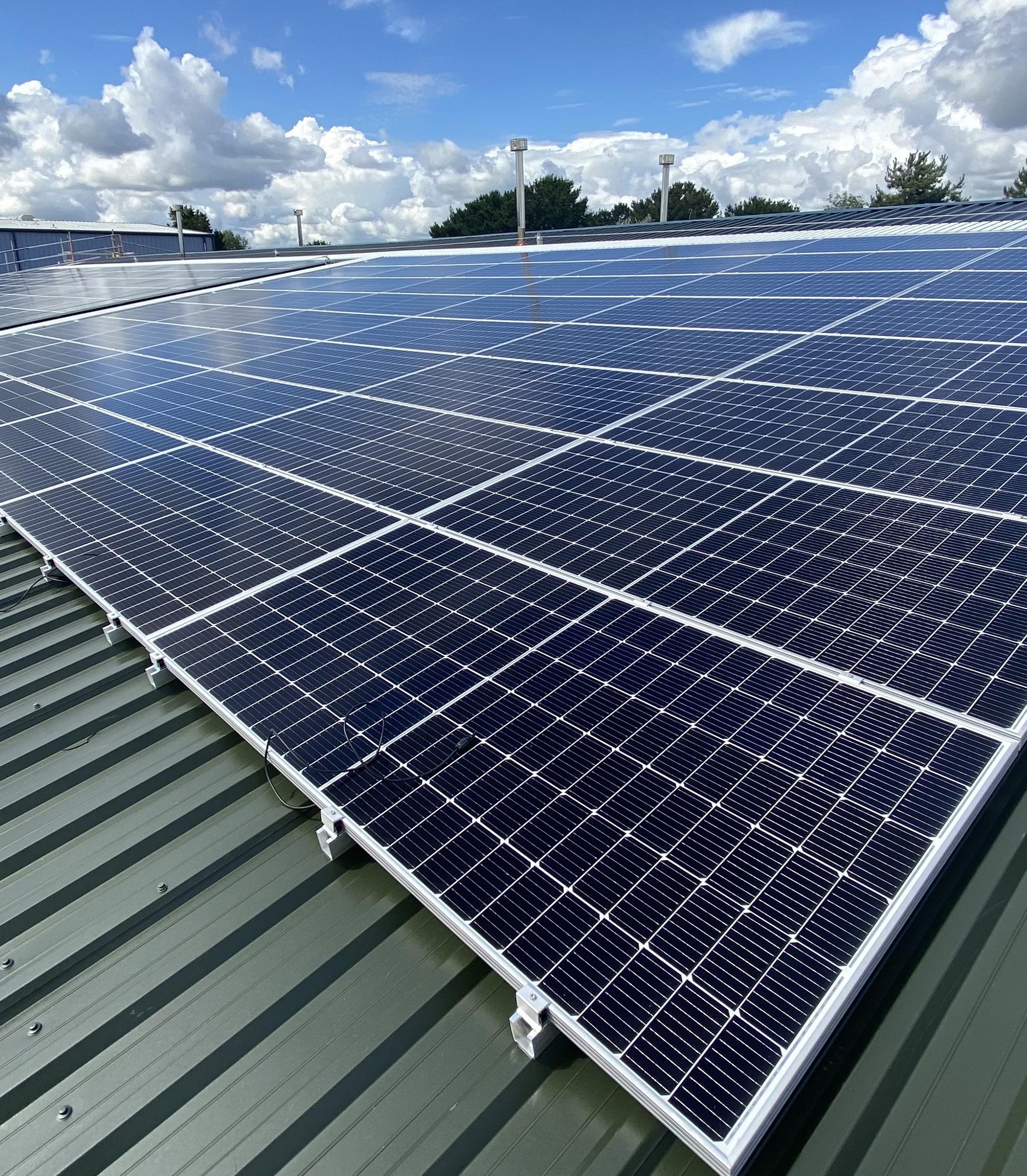
Solar panels are an effective way of improving the energy efficiency of a project. But this can be costly, with large up-front payments often limiting their use.
The Crown Commercial Service’s Leasing and Loan Finance Dynamic Purchasing System (DPS) a range of financing options make securing solar panels for your project simple and achievable. Whether you are looking for a hire purchase, a finance lease, and operating lease or an asset secured loan, you can find the finance solution that will work for you.
Jangro, the largest network of independent janitorial distributors in the UK and Ireland, is delighted to announce that it has achieved its second year of being Planet Mark certified.
This renewal means that the company has been successful in reducing its carbon emissions by at least 5% over the past twelve months. In fact, in the latest reporting period (1 Jan 2021 – 31 Dec 2021), emission sources including electricity, natural gas, water, fleet, business travel, waste, and paper were reduced by 6.9 per cent per employee.
Through this ongoing accreditation, Jangro is furthering its commitment to realising a brighter and more sustainable future. It continues to measure and reduce its footprint, plan long-term
ambitions and motivate its team to innovate. Additionally, it remains committed to measuring its social value contributions (the net social and environmental benefits generated by its team).
Jo Gilliard, CEO of Jangro, comments, ‘We take our responsibility to the planet seriously and are committed to helping our customers do the same. After all, making more environmentally responsible decisions is essential for the long-term future of the cleaning and hygiene industry. We are proud that as well as “talking the talk,” we can demonstrate
that real action is taking place. Our continued certification with Planet Mark highlights our constant efforts to measure and reduce our footprint, and, hopefully, inspire others in the sector to do the same.’
As part of the Planet Mark certification, Jangro has committed to making a yearon-year reduction of its carbon footprint by 5% annually. Planet Mark is a sustainability certification that verifies and measures carbon and social data to reduce emissions and achieve the United Nations Sustainable Development Goals (UN SDGs).
View Jangro’s latest Planet Mark certificate at https://www.planetmark. com/member/jangro/.
For more information about Jangro, visit www.jangro.net.
For more information about Planet Mark, visit www.planetmark.com.
The Public Sector Sustainability Association (PSSA) provides a professional association and network for all those working in the Public Sector who have a common interest in sustainability. For more information on joining, please visit www.pssa.info
Union Industries, the employee-owned manufacturer of high-speed industrial roller doors, is celebrating its 50th anniversary.
With a history that stretches further back than 1972, the celebration marks the incorporation of the business as Union Industries.
The anniversary was commemorated by a glamourous black-tie event at the stunning Grantley Hall in North Yorkshire attended by current and former employees as well as its founders, Paul and Isobel Schofield, who are affectionately known by colleagues, friends and customers as Mr and Mrs S.
In addition, the company confirmed that each of its 76 employees would receive a 5% pay increase as well as £1,000 to help with the rising cost of living.
Originally a tarpaulin maker and repairer known as Ralph Ellerker, which was founded in 1795, the business was acquired by Paul, who with Isobel, transformed the company into Union Industries.
Known for its ‘Best of British’ strapline, the Leeds-based company manufactures a range of industrial products, most notably its market-leading range of rapid roll doors.
From its landmark factory and head office, known as Angel’s Wing on account of the pair of giant golden angels that adorn its entrance atrium which were acquired by Mr S from a movie prop maker, Union Industries produces its highly regarded products.
The current range includes the Ramdoor, Bulldoor,
Matadoor, Lion Door, Picadoor and the unique Eiger Freezer Door.
These fast-acting doors are installed in distribution centres, warehouses, factories and storage facilities to improve logistics and save heat loss for companies across the UK and Europe. Its portfolio of clients includes amongst others; Tesco, Cummins, Co-op, BAE Systems, Ocado, Jaguar Land Rover and DHL International.
In 2014 its founders Mr & Mrs S took the decision to safeguard the future of the company in Leeds by transitioning to an Employee Owned (EO) structure where the majority of company shares are held by the Union Industries Employee Ownership Trust.
Under Union Industries’ EO scheme, every employee can buy their own shares in the company in addition to being beneficiaries of the EO Trust. New starters who join the company are also given shares after 12 months of employment.
The business has continued to go from strength to strength. Although Union Industries has always boasted a committed workforce, becoming Employee Owned has further empowered its team.
This includes an added financial incentive because of an annual tax-free bonus, but also the ability to have a
say in the running and future direction of the business.
Andrew Lane, Managing Director of Union Industries, said: “This is a celebration of more than just a business, but a place where innovation and creativity can be expressed and being the best of British is more than just a saying, it’s something we passionately believe in and achieve through our products, our people and the way we work every day.
“This landmark anniversary is a great way to celebrate and recognise the brilliant people we work alongside every day. Union Industries is a special place to work. Whilst being an employeeowned company in the UK isn’t unique, our version of it really embraces the people within the business and strengthens the family bond we have here.
“We are also really grateful to our large customer base, which has supported and continues to support Union Industries by investing in our best-in-class products that improve efficiency, productivity and sustainability.”
Humidity control specialist, Condair, has released a new podcast about how food manufacturers can enhance their productivity by controlling their production area’s humidity.
In a 10-minute interview with BusinessNet Explorer, Dave MarshallGeorge, Sales Director at Condair, explains how paying more attention to a manufacturing or storage area’s ambient humidity, can improve manufacturing yield and profits.
Dave explains, “Accurate humidity management in food and beverage production has many benefits. There are a huge range of applications. Humidification is frequently used to reduce evaporative losses, prevent static issues and extend shelf-life of produce. Dehumidification can be employed to more efficiently dry a product, eliminate condensation, reduce cold storage overheads or prevent products sticking to conveyors.
“As a humidity control specialist, we work with food and beverage manufacturers to identify areas of potential improvement across a production line, and then implement systems to maintain the ideal environment to realise those benefits. For example, we work in the meat sector to reduce evaporative losses from carcasses during primary chilling, with cheese manufacturers to reduce weight losses during cheese ripening, with bakers to optimise proving and oven baking, and distilleries and wine makers to prevent evaporation through casks.”
In this podcast Dave provides
an overview of the potential for productivity improvements in a variety of applications and offers advice on how manufacturers might takes steps to start improving their processes. “Properly understanding the environmental profile of an area is key.” Dave continues, “This isn’t just an average temperature and humidity level in a room. It can include the micro-climate directly next to the product and being aware of any temperature differences between product and atmosphere. If a product is cooler than the air, this can lead to condensation, and if it’s warmer than the air, to moisture loss through evaporation.
“Using multiple data loggers is a good idea to properly assess the atmospheric profile of an area. However, for any manufacturer interested in exploring how they might improve profits through improved humidity control, I’d recommend having a free site
assessment from their local Condair sales engineer. We offer free on-site reviews and are always happy to talk to food and beverage manufacturers about possible improvements they can make.” Dave concludes.
The podcast is available on Spotify, Google Podcasts, Soundcloud and Apple iTunes by searching for “Condair Podcast”, or on the Condair.co.uk website.
The Condair Group is the world’s leading specialist in humidity control and evaporative cooling, with energy efficient, hygienic and innovative technologies for commercial, industrial and heritage applications. Condair is represented in the UK by Condair Limited, which offers system design, manufacture, supply, installation, commissioning, maintenance and spares.
You can find out more by visiting the company’s website at www.condair.co.uk.
Eco-friendly water filtration company, EcoPure Waters, has announced the launch of its new website.
The new website is intended to encapsulate EcoPure Waters’ innovative approach to water provision, offering its customers the very best in water purification, highquality branding opportunities, and customer service, while also tackling the issue of single-use plastics in the hospitality industry.
“We couldn’t be more pleased with how our new website has turned out”, said Paul Proctor, Director of EcoPure Waters. “We wanted to create an online presence that reflects our pioneering ambition to provide the world’s leading luxury brands with a world-leading solution to water provision. We feel our new website, with its sophisticated design and
refreshingly elegant look and feel, achieves that goal in style”.
“Having listened to the needs of our existing customers, we felt it was important for our new website to showcase the benefits of our products and services, keep our audience up to date with our latest news and updates, and provide visitors with a more streamlined navigation experience”, said Simon Chapman, Business Manager at EcoPure Waters. “We also updated our ‘personalised bottle branding’ tool so that visitors to the website can see how their logo will look when printed on our range of vintage swing stopper and designer screwtop reusable glass bottles.”
“As well as demonstrating our capability to meet the needs of the world’s premier brands, our new website also reflects our expansion into new geographic
markets”, Proctor added. “Our client base across Europe is growing faster than ever before, and our international arm, EcoPure Waters International, is also experiencing growth at an unprecedented rate. We are delighted to be unveiling our new website to our clients, partners, and stakeholders, and we look forward to all the benefits it will offer”.
EcoPure Waters has been manufacturing, supplying, and maintaining market-leading water purification systems and custom-branded glass bottles for over 25 years, helping over 700 clients worldwide save money, reduce environmental impact, and create powerful branding opportunities.
To find out more about EcoPure Waters, please visit www.ecopurewaters.com.
Your roof is one of the most important parts of your building, and a properly installed and maintained roof will provide reliable service, protecting your estate and all its occupants for many years.
As you plan your next project, it’s important to ensure that all decisions to upgrade are based on the current condition and performance of the roof to ensure you take any unknowns out of your budgeting process.
Whether you are looking to refurbish an existing roof or undertake a new-build project at your site, there are a variety of waterproofing systems facilities managers will consider ensuring the right system is specified for the right application. We’ll take a closer look at some of the best waterproofing systems to consider for your roofing assets.
With an extremely long lifespan of up to 50 years, modified bituminous
membranes are durable enough to withstand whatever weather conditions come their way and flexible enough to contour easily to the shape of the building without cracking.
Available in two kinds of application methods: torchon and self-adhesive (flamefree), both options can be designed into tapered roof insulation schemes that will mitigate ponding water and improve the overall thermal efficiency of the building
Offering quick installation and aesthetically striking results, standing seam metal roofs are popular for new-build, refurbishment and asbestos encapsulation projects. Metal roofs are incredibly low maintenance making them ideal for commercial estates, and are 100% recyclable at the end of their life.
Standing seam metal roofs can last up to 50 years, making it one of the
market’s most durable and long-lasting options.
Flame-free roofing systems have become an increasingly important solution to the healthcare sector’s flat roofing requirements, significantly mitigating the danger of roof fires.
Liquid waterproofing can be tailored to strengthen and waterproof a failing roof as part of a refurbishment project, or be used in new-build projects looking for a smooth and modern aesthetic finish.
Green roofs can be combined with bituminous membrane and standing seam metal systems to provide long-lasting waterproofing and multiple benefits to a business’s environmental initiatives. By improving the thermal efficiency of a building, a green roof can also contribute to your site’s netzero carbon operational targets. Many facilities managers and landlords are now incorporating a solar PV energy system into their roofing design to significantly reduce the operational carbon output and save money on the overall running costs.
With a breadth of waterproofing solutions to consider on the market today, each will have its own advantages and disadvantages depending on the application and Garland UK can support your next roofing project with expert advice from a local Technical Manager.
Fire safety is an important consideration in the building industry, and everyone involved in construction or property management should choose materials and processes to help prevent fires. This is especially important in multi-tenanted buildings like apartment complexes and retirement/nursing homes, where a fire can quickly spread and put lives at risk.
Many people don’t realise that most entrance mats are not flame-retardant, meaning they can fuel a fire and spread it around the building more quickly. Most building operators and landlords know the risks and will ask tenants to remove mats that aren’t classified as flame-retardant. Learn more about Flame-Retardant Entrance Mats with this guide provided by First Mats.
The classifications and regulations can be complex, but they are designed to help you choose the right materials for your property.
International classifications are designed to ensure that any product or component with a classification marking has been tested to the same standards. Construction products should have been tested and graded against EN 13501-1, the European standard for reaction to fire. The ‘fire retardant’ marking means the materials have passed testing, including exposure to a naked flame and a radiating heat source. This ensures that the materials will not contribute to the spread of fire and will provide a measure of protection in the event of a fire.
For floor coverings and mats, the potential grades that can be awarded are:
A1 fl – the ‘fl’ is an abbreviation for ‘floor’; a floor covering with this rating is
considered nonflammable with no risk of smoke formation.
A2 fl – nonflammable floor coverings with low levels of organic binding agents
B fl – a flameretardant product that has passed the radiating heat test with an intensity of 8kW/m2
C fl – a flame-retardant product that has passed the radiating heat test with an intensity of 4.5kW/m2
A1 fl and A2 fl levels cannot be achieved by the vast majority of floor coverings, including vinyl and textiles. When you are looking for matting, you need to keep an eye out for B fl and C fl markings. These both mean that the mats have been tested and classified as fire-retardant.
It’s important to note that fire retardant does not mean the item cannot be set alight. It means that the materials used help to stop the spread of any fire that does manage to take hold.
C fl classifications and below should be considered a fire risk. Using these products can present a danger to anyone in a building where they are installed.
When a fire occurs, smoke can quickly fill a room or hallway, making it difficult for evacuees and firefighters to see and breathe. For this reason, the amount of smoke produced by burning material is an important factor in fire safety. The EN13501-1 standard includes a test to measure the smoke produced by burning material. The smoke is graded on a scale from ‘s1’ to ‘s2’, with ‘s1’ indicating a manageable or acceptable amount of
smoke and ‘s2’ meaning that too much smoke is produced. When choosing materials for a building, it is important to look for products with an ‘s1’ smoke rating to ensure that the amount of smoke produced in the event of a fire will not impede evacuations or rescue efforts.
Combining the two grades will give us a marking for the flooring and smoke production. Your mat should be marked as either Bfl-s1 or Cfl-s1.
As fire regulations have tightened, finding and fitting an entrance mat with the form and function you want for your building and residents has become more difficult. However, fire-retardant entrance mats are available in a huge range of colours and sizes, with deep piles for comfort, durable finishes for longevity and very respectable dust, dirt and water retention. Check the classifications before purchasing to ensure they will suit your building.
First Mats started life as safety matting specialists but has since expanded to become a complete industrial and commercial supplies company. First Mats focus on providing safety-focused products that improve the wellbeing of staff through qualityapproved products backed up by extensive knowledge.
For more information, go to www.firstmats.co.uk
Healthcare Estates® is a unique event that consists of the prestigious IHEEM Annual Conference, Awards Dinner and the UK’s largest trade exhibition for the sector.
Build innovative and productive partnerships in asset management, integrate efficient patient-centred environments by collaborating with the right people, find inspiration, and foster aspirational attitudes.
Visit www.healthcare-estates.com
Pete Sellars, IHEEM CEO said “Our aim is to make our flagship event as inclusive as possible both for our members and everyone from the healthcare efm community who has worked tirelessly to meet the challenges of the past two years. This revised pricing structure will undoubtedly encourage increased delegate attendance at our conference and exhibition. I am delighted that we have the opportunity to return to a live event this year and I look forward to meeting many of you in person at Manchester Central.”
It is estimated that 10 million people carry out some form of work above the ground every year. It is a day-to-day requirement of many industries – construction, agriculture, and roof work to name a few, and whilst it does remain a vital part of our economy, there is no doubt surrounding the great risks that working at height poses. This is foregrounded by Health & Safety Executive (HSE) who, in their latest Workplace Fatal Injuries report, revealed that falling from height still remains the predominant cause of fatal injuries and accidents in the workplace. 29 fatal injuries were caused by falls from height, accounting for 24% of deaths in the workplace over the year. As well as being a real eye-opener for employers across the country, this should
provoke serious discussions about the supervision, health, competency, and training of those working at height.
The Work at Height Regulations 2005 requires employers and managers in control of any working at height activity to guarantee that the work is properly planned, well supervised, and executed by competent people. This involves making sure that the correct equipment is utilised, and that it is safe to use. Employers should also be certain that employers working at height possess the correct skills, knowledge, training, and experience to do so.
With so many regulations in place, something doesn’t quite add up as to why workers are still suffering fatal injuries from falling from height. It is
impossible to witness all that is going on behind closed doors, so it is certainly possible that various industries are not adhering to the working at height regulations as they should. This has proven detrimental to not only the lives of workers but also to employers and businesses across the country. Ultimately, it is a breach of the Health and Safety Act 1974, and employers face some stiff penalties including 12-months imprisonment, unlimited fines, or both.
Working at height is the most common cause of fatal and serious injury in the construction industry and yet, in quite the staggering revelation, the Building Safety Group (BSG) recently reported an 84% increase in the number of working at height breaches
occurring on construction sites. These findings, which also see falling from height account for over 60% of fatal injuries serve to spotlight the perennial importance of having the adequate training and precautions in place before working at height. These injuries mainly involve falling from ladders, scaffolds, working platforms, roof edges and through fragile roofs.
The most common safety breaches involve having a lack of safety measures in place. In fact, the main cause of falls from height is ladders, averaging around 515 injuries per year. Most ladder falls can be prevented but occur as a result of rushed preparation or a lack of awareness about how weight transfer can affect ladders. Other breaches include not providing harnesses, additional platforms to take weight off fragile surfaces and not securing
structures like scaffolding. It is pivotal for workers to have sufficient room to move materials when working at height, including an awareness of how much space is needed, how to create larger surface areas and eliminating all route blockages.
The Work at Height Regulations 2005 requires all employers and self-employed contractors to undertake all necessary risk assessments before any work at height carried out in order to ensure that all work is organised and executed safely. The approach to follow is the work at height hierarchy of controls involving avoiding, preventing, and mitigating risks. A method
statement is a useful way of recording the hazards involved in specific work at height tasks and communicating the risk and precautions required to all those involved in the work. In addition, there are various safety critical medicals designed specifically for those who work at height. This involves employees to undergo a series of medical assessments to determine whether they are healthy and safe enough to work at height.
Baxi Commercial Solutions has released a new guide entitled Schools and the Heat Decarbonisation Challenge with the aim of supporting schools in setting achievable pathways to more sustainable heat.
The report assesses the different heating technologies, solutions and approaches that will need to be available to schools to reduce heatassociated energy usage and emissions in their buildings while prioritising performance and practicality.
Baxi’s new guide:
• explores the currently available options to achieve more sustainable heating in older primary and secondary school buildings
• outlines the value of planning phased refurbishment programmes to achieve optimal outcomes and long-term goals
• illustrates the achievable carbon and energy savings from a stepwise approach.
Heating is one of the UK’s primary sources of emissions, accounting for around a third of the nation’s total greenhouse gas emissions. Decarbonising heat in buildings is therefore key to achieving the UK’s ambitious 2050 net zero target. But it’s a huge challenge and one that can be particularly problematic in existing school buildings.
Andy Green, Director at Baxi Commercial Solutions said:
“As heat experts, we understand the issues that schools are up against when tackling heat decarbonisation in their buildings, particularly with the energy crisis squeezing already tight budgets.
“Ultimately, the goal is to transition to low carbon heating technology such as heat pumps. But school buildings are often complex projects for refurbishment. Estates and facilities managers, consultant engineers, M&E contractors and installers can face an array of issues, with time, budget, available power and physical space just some of the typical limitations.”
As full decarbonisation is unlikely to be achieved overnight in older or poorly insulated school buildings with high thermal demand, plotting an achievable pathway to improved sustainability can be vital to deliver successful outcomes.
Using smart simulation software, the Baxi guide analyses the achievable energy and carbon savings from a phased refurbishment programme in theoretical secondary and primary schools. The simulated stages include initial measures to improve energy efficiency, the installation of a more efficient, future-ready system, and a multivalent approach involving air source heat pumps to decarbonise a large portion of the annual heat demand.
“The heat decarbonisation challenge is far from new,” Andy continued. “But the energy and climate crises make it clear that we in the heating industry need to act now to help UK schools progress towards more sustainable, affordable heat. Ensuring robust design
practice is key. By working together, heating manufacturers and professionals can help schools get the most from their heating budget while ensuring best practice for heat decarbonisation.
“Even with the support outlined today by the new Prime Minister, it’s essential that schools understand all the available options to drive down heat-related energy consumption in their buildings. Full decarbonisation may not necessarily happen overnight, but, as our report shows, there is considerable value to be gained from taking even the first few steps on their pathway.”
Schools and the Heat Decarbonisation Challenge is available now for free download at: www.baxi.co.uk/ landing/knowledge-centre/ schools-decarbonisation
Industry action plan reveals that 85% of firms are concerned that their company might one day be subject to pollution-related penalties
Almost two thirds (62%) of manufacturing businesses in the UK are unaware of the steps they should be taking to remedy pollution, leading to widespread concern that their firm might one day be subject to pollution-related penalties.
Research carried out by drainage experts Metro Rod, which has now been released as an industry whitepaper and action plan, identified that 85% of manufacturing businesses are currently concerned their company might be subject to pollution-related penalties. Worryingly, only 23% of respondents correctly identified that if their business was found to be in breach of environmental legislation, they would be subject to both an unlimited fine and could be found guilty of a criminal offence with potential for imprisonment.
Concerning for the industry, is that just two in five manufacturing businesses (40%) said they have drainage plans which comply with the Environment Agency’s pollution prevention guidance; less than half (45%) know where their surface water and foul water drains are located, and only 39% know how to access them.
Metro Rod has used the research, which it undertook with a cross-section of people working at management level in manufacturing businesses across the UK, to produce a pollution prevention action plan. The report will better educate manufacturers on the steps they can take to minimise pollution through controlling trade effluent, ensuring the sector is better protected from the risk of flooding, operational downtime
and fines from causing environmental harm.
Chris Nelson, senior technical manager at Metro Rod, said: “The Environment Agency’s pollution prevention guidance for businesses is promoted as best practice for organisations of any shape, size and sector. However, there is no targeted advice for the manufacturing sector, which is more prone to discharging trade effluent – liquid waste generated from industrial or trade processes – into the sewer network.
“There are serious legal implications for businesses found not to be complying with their environmental obligations, but our research shows that knowledge of this in the manufacturing sector is minimal. Aside from legal punishment, any business in this position could face a costly impact on its reputation, daily operations and ultimately contribute to environmental issues.
“Though some of the findings in our research make for stark reading, it’s not too late to take action. The data shows that more can – and should – be done within the manufacturing industry to ensure businesses are taking the necessary steps to reduce their impact on the environment, and there is support available to help achieve that, starting with our new industry whitepaper, which is packed with useful advice and an action plan for manufacturers.
“What’s vital now, is that the industry works together to drive greater knowledge of how drainage networks at manufacturing sites work, and the necessary action required to protect the environment. Doing so will simultaneously ensure industry-wide compliance, help companies safeguard their operations and reduce costs. But most importantly, it will better protect the environment we all love and care for, to create a better future for us all.”
The report – ‘Unveiling pollution awareness in the manufacturing industry’ – is available to download here.
more information about
& Facilities Management magazine, or to register for your free monthly copy, please visit www.bfmmagazine.co.uk
In this article, we discuss reasons why a disinfection, sampling and flushing strategy may not have worked as intended, leaving undesirable levels of TVCs.
TVC stands for ‘total viable count’, a laboratory test that indicates the level of heterotrophic organisms within a sample. Heterotrophs are a large group of organisms that can be further divided into fungi, yeasts, moulds and bacteria. Therefore, the results of a TVC test may offer an indication of the ‘general level’ of contamination within a system.
Microbiological monitoring of domestic hot and cold water supplied from the public mains is not usually required. It should be used, however, to assess the efficacy of a process, e.g. disinfection.
Disinfection is a process which removes or renders inactive pathogenic microorganisms, typically using chemical or thermal treatment methods. Hot and cold water services should be cleaned, flushed and disinfected, as specified in BS 8558:2015 and detailed in PD 855468:2015.
Disinfection is used following a new installation, alteration, or refurbishment to prove that the water is “wholesome” and fit to drink, as, during construction works, the inside of pipework and components can become contaminated and “dirty”.
The number of heterotrophic organisms (TVCs) can indicate changes in water quality and as such, the number of these organisms is included in the Water Supply (Water Quality)
Regulations as one of many ‘indicator parameters’. PD 855468:2015 states that Total Viable Counts (TVCs) should be included in the post disinfection sampling plan as an assessment of water quality.
The HSE’s HSG 274 Part 2 document also states microbiological samples are required to confirm effective disinfection.
In healthcare, HTM04-01 Part B also does not recommend routine microbiological monitoring for TVCs, however, in our experience, hospital Infection Control Officers and Microbiologists are becoming increasingly interested in TVC sampling and what they contain.
At present, all reputed sources stipulate that the readings should demonstrate “no abnormal change”, “i.e. measurements should show no sudden and unexpected increases as well as no significant rising trend over time.” However, no recommended action levels are stated.
PD 855468:2015 describes that TVC results over a 2 log difference above that found in incoming water, remedial action should be taken, referencing the WHO’s Water Safety in Buildings 2011 document.
Whatever parameters your organisation has decided to work to, must be detailed in the Water Safety Plan.
HSG 274 Part 2 pp.42-44 provides guidances of when and how to carry out cleaning and disinfection works referencing BS8558. Although, it is worthy of note that the BS8558:2015 revision included the British Standards ‘published document’ titled ‘PD 855468:2015 guide to flushing and disinfection of services supplying water for domestic use within buildings’ which should be referred to for the correct process.
The sampling method used, should be taken from “Examining Food, Water & Environmental Samples from Healthcare
Environments Microbiological Guidelines” and although written for Legionella sampling, BS 7592 could also be followed.
But why am I still getting TVCs after disinfecting and flushing?
System disinfection and a Legionella flushing regime are traditional remedial actions to take following a positive bacteriological sample result, but, as the title of the blog suggests, this may not always work. There are several reasons why these actions may not work, the following are some tips derived from experience and previous learnings;
• Did the entire system receive sufficient disinfection?
PD 855468:2015 states that “The key for sentinel outlets should be tested to ensure the required concentration is reached” – was this recorded?
PD 855468:2015 states that “all other outlets should be subjected to a fast and simple test showing the presence of absence of disinfectant” – was this recorded?
• Did the TVC counts return after an initial clear result?
Both the HTM04-01 and HSG 274 capture that any microbiological samples should be taken between 2-7 days after the system has been refilled –to mitigate the risk of receiving false negative sample results.
• Was the pH of the water checked and contact time adjusted to suit?
PD 855468:2015 states that the efficacy of chlorine is pH-dependent, so pH values in excess of 7.6 will require additional contact time.
• Did the sampling methods follow the updated guidance?
• Were the samples taken aseptically?
i.e. without touching the screw thread of the sample bottle, without touching the inside of the cap of the sample
bottle and without touching the inside of the sample bottle.
• Were the samples stored correctly?
Hot and cold samples to be packaged separately in a cool, dark, insulated container, samples should be kept at 2-8°C
• Did the water samples get analysed in time?
Samples are to arrive at the laboratory as soon as possible, certainly within 24 hours.
• Was there a sampling plan in place?
Sampling at the correct locations for the correct indicators should be agreed upon by the Water Safety Group. Guides on sampling plans are described in BS 8680, BS 7592, PD 855468, HSG 274 Part 2 and HTM04:01 Part B.
It is also important that a control sample from the incoming supply is taken so that outlet readings can be compared, as knowing what your “baseline” TVC levels are will help understand what “abnormal change” is or what should be expected. It is also important to know if high TVC levels are in the incoming water supply!
• Was the system installation completed before disinfection and associated sampling took place?
All parts of the system should be included in the process and should not take place until all works have finished. Phased completion and occupation should be carefully managed.
• Was there an outlet flushing programme in place from system completion to sampling to receiving the results to handover?
PD 855468 advocates weekly flushing (twice weekly in healthcare premises) to maintain a flow of water, in accordance with ACoP L8 and HSG 274 Part 2. During the commissioning of projects, the responsibility for the water risks lies with
the contractors as defined in CDM Regulations 2015.
• Were all outlets included in the flushing regime?
Don’t forget the toilets! A quick way to turnover high volumes of water.
• How long to run water to prevent legionella and other bacteria?
HSG 274 Part 2 advises to “Flush the outlets until the temperature at the outlet stabilises and is comparable to supply water”.
• HSG 274 Part 2 advises “If water turnover is anticipated to be low initially, it may be advisable not to commission certain parts of the system, such as cold water storage tanks, until the building is ready for occupation. This will ensure flushing during low use periods will draw directly on the mains supply rather than intermediate storage”
Make sure any parts of the system such as these, are commissioned correctly.
• Have all strainers and filters been emptied and cleaned during the commissioning process?
• Are all the hot and cold water temperatures within the correct parameters?
• Is the hot water circulation system balanced?
• Has dead leg pipework been kept to a minimum?
•vHave dead ends been eliminated?
• Was a risk assessment completed and updated during the project?
• Was a Legionella Risk Assessment completed before handover?
There are many reasons why bacteria can colonise a water system, and these reasons are covered extensively in guidance documents and other Water Hygiene Centre blogs. This blog aimed to empathise the importance of correct disinfection, sampling and flushing processes following a new installation or refurbishment works, hopefully, it has helped give food for thought.
Manchester Metropolitan University is reinforcing its position at the forefront of sustainability with smart building technology. Its new Grosvenor East building is set to inspire upcoming generations of actors, journalists, writers and linguists.
When it completed the new home for its Faculty of Arts and Humanities in 2020, Manchester Metropolitan University achieved a productive, comfortable and safe working environment. The building also integrates a smart building system capable of providing real-time access to data to support energy efficiency while minimising operational and maintenance costs.
Sustainability is becoming more important in the world of higher education. According to a 2021 survey by Times Higher Education, a university’s sustainability is more important than location for prospective international students. It’s an area where Manchester Metropolitan University excels, as shown by its top spot on the People & Planet League, an environmental ranking of UK universities.
Vice-chancellor Prof Malcolm Press commented: “Sustainability forms an integral part of everything that we do, from our teaching and research to the way that we build and use our campus. We know the environment is one of the top concerns for people of all ages.”
Its carbon management plan sets out the university’s strategy to cut emissions by 44% – or 5,051 tonnes of CO2 – between 2020 and 2026. This includes initiatives to boost energy efficiency and invest in new efficient buildings. For example, the new Grosvenor East building has been certified as excellent under the UK’s Building Research Establishment Environmental Assessment Method (BREEAM). The six-storey building features
a 180-seat theatre space that is capable of multiple configurations, an atrium, TV and radio studios, tuition and rehearsal spaces, as well as a café, bar and restaurant.
In terms of building control, a cutting-edge webbased Building Management System (BMS) provides automated control, as well as 24/7 web browser access to alarms, trends and scheduling for temperature, lighting and air quality. Based on the ABB Cylon® ASPECT® control platform, this provides backwards compatibility and web connectivity for the university’s installed base of 1200 Cylon Unitron devices and has therefore future-proofed the campus.
“We use energy efficiency and flexible infrastructure to attract students by showing them that we are serious about sustainability,” said Peter Fallon, Chief Engineer at Manchester Metropolitan University. “This relies on web-based technology so that our technicians have access to control and monitor systems wherever they are on campus.”
A key element of the system is the control engine, which is based on ABB‘s Cylon® NEXUS device. This enables the BMS to pull data from devices that would otherwise be inaccessible to a web-based scheme and restricted to specific computer terminals. Therefore, the device has improved the system’s reach and capability.
Commenting on the project, Dean Reddy, ABB’s UK Product Marketing Specialist for Building Automation UK said: “The
Grosvenor East building is an important new landmark in Manchester and one of first within Manchester Metropolitan University to use the new ABB Cylon® ASPECT® so it was positive to see its deployment was smooth. This is important as the smart building control system is one of the final work packages in any commercial building project.”
See here for more information about how smart automation can decrease energy consumption in buildings.
ABB’s Electrification Business Area is a global leader in electrical products and solutions, operating in more than 100 countries, with over 200 manufacturing sites. Our 50,000+ employees are dedicated to transforming how people live, connect and work by delivering safe, smart and sustainable electrification solutions. We are shaping the future trends of electrification, differentiating through technological and digital innovation while delivering an outstanding experience through operational excellence for our customers across utilities, industry, buildings, infrastructure and mobility. For more information visit https://go.abb/electrification.
Leading roofscape and sustainability solutions firm, Langley has announced a major business restructuring and transformation programme following a period of rapid growth.
The Langley Group, which has operated under the Langley name since the 1960s, has brought its core offerings under one roof as it invests in its mission to deliver the most innovative, future-proofed roofscape solutions for the built environment that have a lasting, positive impact.
By restructuring the business, Langley will provide a much broader, convenient and effective customer experience across its diverse offerings which span design, supply, build, maintenance and training.
The Group will now operate three core business units: Roofing Solutions, Eco Solutions and Regeneration to deliver holistic and integrated roofing, green-infrastructure and rooftop development and extension services designed to help customers successfully
meet the challenges of climate change while also addressing societal pressures – including the cost-of-living crisis, lack of affordable housing and limited access to green space.
Langley Roofing Solutions and Langley Regeneration will be headed up by Managing Director Dean Wincott.
Langley Roofing Solutions delivers high-performance, compliant and sustainable waterproofing, and safety systems for refurbishment and new build developments across the public and private sectors.
Langley Regeneration provides expert feasibility, design, planning and installation of rooftop developments, helping customers to capitalise on the roof-space above existing buildings to create much needed new housing and contributing
to estate regeneration.
Langley Eco Solutions leads the way in greeninfrastructure and design, including sustainable roofing, water management, solar energy, decarbonisation and biodiversity. The business unit, led by Managing Director Mike Brogan, provides green, blue and bio-solar roofs, green walls and podium landscaping.
Tony Silvestri will remain Group CEO for Langley and commented on the business’ transformation: “Langley has been through a transformational period of growth in recent years and I’m incredibly proud to share the future vision and structure of the business with our customers, colleagues and partners as we enter a new era.
“We’re committed to our vision of For Better Living, innovating in everything we do, improving the lives of everyone we work with and having a positive impact on the world around us.
“By bringing the vast expertise, knowledge and specialisms across our teams under one roof, we will be even better equipped to deliver greater sustainability and social and economic value for every Langley customer.
We’re excited to continue working closely with our partners across all sectors to rise to the challenge of creating an environment that is healthier, safer and greener for everyone.”
UK businesses are set to significantly increase their investment in green energy as global supply chains and energy prices pinch.
Now more than ever, facilities managers across the UK are looking to take control of rising energy costs and diminished profit margins whilst sustaining a competitive edge. As a result, many are taking action by making choices that will ultimately improve their bottom line without negatively affecting building occupants or critical infrastructure.
Solar PV systems are one of the most advanced renewable energy technologies and by far the most advantageous for businesses to consider. Once a solar system is installed, there is an instant reduction in the amount of power supply from
the National Grid, which can be an extremely useful offset as energy tariffs continue to climb.
Solar PV has the fastest return on investment of any onsite renewable energy generation, potentially in as little as 4 years and typically within 7 years. Ground source heat pumps, for example, usually take 12 years. Modern solar PV panels are built to last; where for example, Garland UK’s Solarise system will still generate at least 80% of the initial output 25 years after installation, ensuring continued benefits for years to come.
If you have been considering installing a solar PV system, now is the time to do it. With government incentives such
as the Super-Deduction Tax, companies can claim 130% capital allowances on solar PV systems, which is available to benefit from until March 2023.
In addition, many solar PV systems also come with various financing options, such as asset leasing, meaning a project can start straight away without the upfront capital.
Solar Benefits For Business Solar immediately reduces your energy costs and positively impacts the environment by using fewer fossil fuels and reducing reliance on the National Grid:
• Cut your electricity bills
• Reduce your carbon emissions
• Increase your property value
• Fast return on investment
• Payback in as little as 4 years
• Super Tax deduction (available until the end of March 2023)
• Operational leasing available
• Low maintenance
• Quick installation
We always recommend conducting a detailed solar yield analysis on your roof, so you are provided with comprehensive data and insights to make the most informed decision on your roofing assets.
It is essential to have a clear return on investment with a solar installation; for example, with Solarise, commercial businesses typically see a
return on their investment in as little as 4 years.
For a recent 5,000 m2 Garland UK project, a public sector client was looking to reduce their energy costs and operational carbon to support their organisation’s environmental goals to achieve net zero.
See below a snapshot of the Solar Yield Analysis results below:
A local Garland UK Technical Manager will carry out a free site survey to assess the condition of your roof assets and complete a Solar Yield Analysis, which will provide:
• Expert advice on selecting the most suitable system for your business
• Guidance on how much power your site needs
• Negated carbon emissions
• Clear return on investment and financial analysis
• Support with SuperDeduction Tax or Financing options
To discuss how your roofing assets can generate an energy cost saving, speak to a local Technical Manager at Garland UK. www.garlanduk.com
A key part of being environmentally sustainable is implementing green cleaning processes to reduce a building’s footprint on the environment.
When helping a facility, there are 4 main areas we focus on to increase sustainability throughout whilst ensuring that there is no sacrifice in cleanliness levels.
As sustainable becomes priority, there is a shift away from the use of harsh chemicals to reduce their negative impact on the environment.
Too often facility managers rely on chemicals to provide a thorough clean; however, there are alternatives. Microfibre has fast gained attention because of its ability to remove fine particles, bacteria, microbes, and oilshidden in surface crevices, that cotton cloths cannot reach.
In some cases, the use of microfibre allows chemicals to be cut out of the cleaning process, with
up to a 95% reduction in chemical volume used.
There is also an increase in the use of stabilised aqueous ozone which is being utilised by facilities to ensure a safe, chemicalfree solution which can be used on all washable surfaces as a single cleaner and disinfectant. It’s also suitable against bacteria and viruses but provides a higher level of safety for all using it.
50% of all plastic produced out of 380million tons per year, is for single-use purposes –used for just minutes
then thrown away!
Every facility should look to move away from buying single use cleaning chemicals through different methods.
Implementing a system whereby operatives have a specific reusable trigger bottle for each area of the cleaning categories, means that you will not need to constantly purchase the ready to use products.
But what do you do about the correct dosing of cleaning chemical? If using Stabilised Aqueous Ozone as your main cleaning solution, there are no dilution rates required, but if you do still have need for a few chemicals in the facility, you could implement the probiotic
For more information about Building & Facilities Management magazine, or to register for your free monthly copy, please visit
www.bfmmagazine.co.uk
portable dosing system, which measures the correct amount for each process.
Traditionally, when cleaning a facility there is often a reliance on water; however, a considerable amount of this valuable resource is wasted through mopping or cleaning surfaces with a cloth.
Now’s the time to start taking measures to decrease water usage. Not only will limiting water usage cut operational costs, it will decrease the business’ impact on the environment.
You can do this by using products, such as microfibre cloths, which drastically reduce the amount of water required for a thorough clean.
In addition to cleaning
with microfibre, there are other steps facility managers can take to reduce water usage:
• fix leaking taps
• choose e_cient showers, toilets, taps, plumbing and appliances that save water
• consider using rainwater storage
• reuse water where possible to reduce the consumption of clean water where it is not needed
These simple steps are essential for facilities to achieve top recognition for sustainable cleaning
There are many changes happening in the cleaning industry since the pandemic and its important
to keep up to speed with what is going on and what equipment and processes are available to help facilities cut down on time and money and resources.
The simplest way of doing this is to keep in regular contact with your hygiene & janitorial supplier who should be knowledgeable as to what solutions are available to make reductions in the facility.
If you want help achieving the gold level of sustainability in your cleaning processes, reach out to us at Chespack Hygiene. We’ve been helping facilities achieve their goals for over 28 years and we are ready to help you achieve yours.
www.chespackhygiene.com
The Public Sector Sustainability Association (PSSA) provides a professional association and network for all those working in the Public Sector who have a common interest in sustainability. The aim of the association is to bring together a wide group of people working across all areas of the Public Sector – to help educate, train, support and connect as we work towards a more sustainable future.
Becoming a Corporate Member of the Public Sector Sustainability Association highlights your organisations commitment to sustainability and offers a unique platform to reach our membership of committed and influencial sustainability professionals in Government, Local Authorities, NHS, Education and Housing Associations. The PSSA offers two levels of Corporate Membership (Gold and Silver), both providing a fantastic opportunity to gain recogniton and exposure with our Public Sector membership.
• Comprehensive listing in Suppliers Directory
• Unlimited opportunity to supply press releases, articles & news to feature on PSSA website
• One release for inclusion in monthly Newsletter
• Opportunity to promote your own events/webinars/training courses to PSSA members
• Logo on PSSA homepage as ‘Gold/Silver Member’ of the PSSA
• Introductory email sent to our members as the latest Gold/Silver Member of the PSSA
• Logo - ‘Gold/Silver Member of the PSSA’ to use on your own websites/materials Additional Gold Member benefits -
• Potential to conduct research/surveys through the PSSA (Gold Member ONLY)
• 2 x Advertising Banners to appear on the PSSA Newsletter (Gold Member ONLY)
• 3 x Full Page Advertisements within either Energy Manager magazine or Building & Facilities Management magazine (Gold Member ONLY)
• Opportunity to present at regular PSSA Webinars (Gold Member ONLY)
The rate for Gold Member status is £1,495+VAT per annum. The rate for Silver Member status is £895+VAT per annum.