


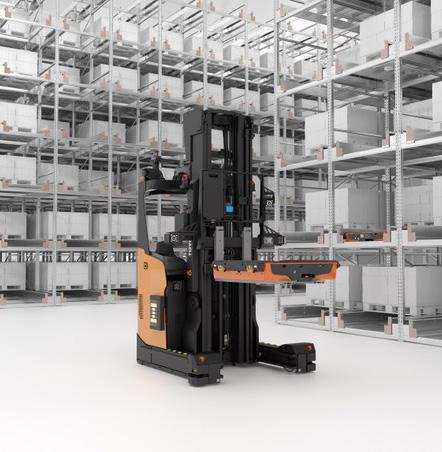
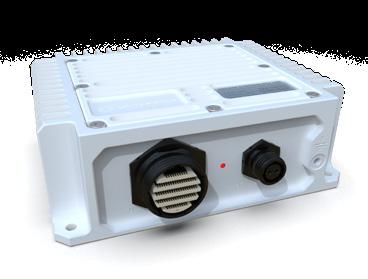

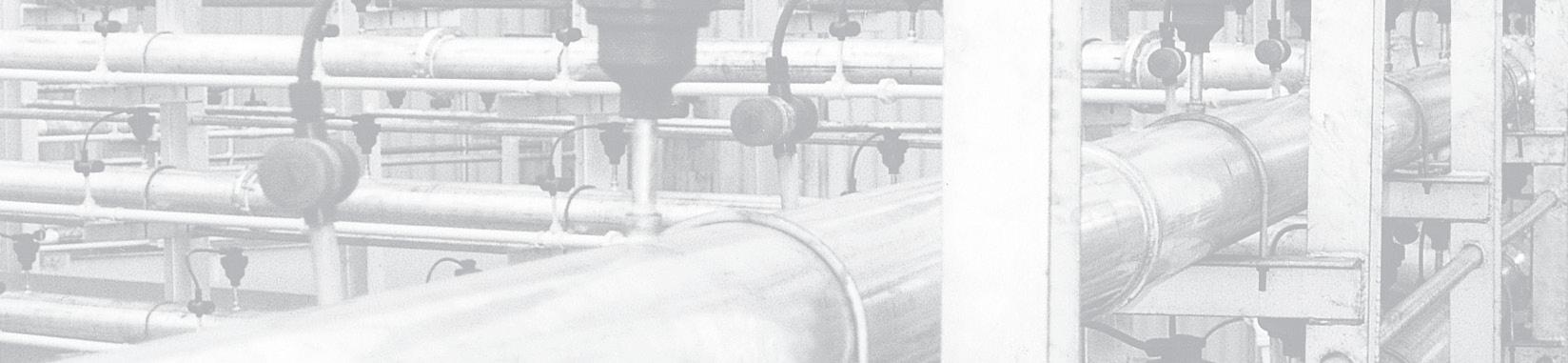
We are a leading provider of custom solutions for the handling of bulk materials for processing businesses across various industries. Dynamic Air has over five decades of expertise in designing and manufacturing pneumatic conveying systems and equipment for handling dry bulk solids.
At Dynamic Air, we set the standard for excellence in bulk solids handling. With a relentless focus on quality, reliability, and customer satisfaction, we deliver reliable, high-quality pneumatic conveying systems, equipment, and custom solutions that exceed expectations. BULKBUSTERTM
We never take a cookie-cutter approach just to cut costs up front; we know that the right solution will save you money in the many years to come. Our tailored solutions involve thoughtful planning, meticulous engineering and precise manufacturing that optimize efficiency and productivity.
Sales Director: James Scrivens
Production: Sarah Daviner
Accounts Manager: Avery Hudson
Office Manager: Katie Brehm
BULK SOLIDS TODAY is published 6 times a year by Abbey Publishing Ltd
ADVERTISING & EDITORIAL
Please contact us at:
Tel: 01933 316931
Email: editorial@bulksolidstoday.co.uk advertising@bulksolidstoday. co.uk
Web: www.bulksolidstoday.co.uk
Twitter: www.twitter.com/ BulkSolidsToday
CIRCULATION
To receive a copy free of charge, please send your details to subs@bulksolidstoday.co.uk
No part of this publication may be reproduced by any means without prior permission from the publishers. The publishers do not accept any responsibility for, or necessarily agree with, any views expressed in articles, letters or supplied advertisements.
ISSN: 1365/7119
Jaisen Kohmuench, Eriez® President and CEO, announces the appointment of Todd Loudin as Vice President of Global Sales. In this pivotal role, Loudin will leverage his expertise to drive revenue growth and enhance Eriez’ global market presence.
With more than three decades of experience in international business and sales management, Loudin has a proven track record of success. He most recently held a senior executive position at Valmet, a global leader in flow control solutions, where he significantly expanded market share and strengthened customer relationships.
As part of the Eriez executive leadership team, Loudin will apply his deep understanding of international sales dynamics and pipeline management to advance Eriez’ efforts to diversify its business worldwide.
“We are proud and excited to welcome Todd to the Eriez team,” says Kohmuench. “Todd’s visionary leadership will be integral to our work to more closely unify and better support our 12 global subsidiaries across six continents.” He adds,
“We are confident that Todd’s contributions will have a positive impact on shaping Eriez’ future and elevating the organization.”
Loudin earned a bachelor’s degree in marketing and business from Kent State University and an Executive MBA from Loyola University Maryland. Throughout his career, Loudin has been actively engaged in prominent professional organizations, including serving on the International Society of Automation (ISA ANSI) Standards Committee for more than 12 years.
Established in 1942, Eriez is a global leader in separation technologies. Our commitment to innovation has positioned us as a driving market force in several key technology areas, including magnetic separation, flotation, metal detection, and
material handling equipment. The company’s 1,000+ employees are dedicated to providing trusted technical solutions to the mining, food, recycling, packaging, aggregate, and other processing industries. Headquartered in Erie, Pennsylvania, USA, Eriez designs, manufactures, and markets on six continents through 12 wholly owned international subsidiaries and an extensive sales representative network. For more information, visit eriez.com.
For companies that need to increase storage space and optimise their use of manpower, Toyota Material Handling Europe now offers Swarm Automation Storage – a complete automated solution based on the combination of three proven components. The concept offers aisle-free storage density, up to 80% denser than selective racking, at a much lower cost compared to alternative high-density solutions, and the flexibility to fit into existing available space, with optional scalability if more storage or higher throughput are required.
This automated storage and retrieval system, combines three components, namely the proven Toyota Radioshuttle and high-density storage system, working with the company’s RAE automated reach truck, and controlled by Toyota’s T-ONE warehouse execution system that interacts with the user’s own warehouse management software. Size and structure of the storage system are flexible as it can be configured to maximise use of available space, and the number of shuttles and AGFs (automated guided forklifts) can be scaled according to operational demands.
This storage solution is principally designed for storing palletised loads. These loads are transported by the shuttle unit(s) through storage channels within the specially designed racking
system. Loads are fed into the system by the automated reach truck(s), that also moves the shuttle unit(s) between different channels. The storage system can be configured to suit the application, providing FIFO (first in, first out) or LIFO (last in, first out) scheduling.
The system is ideal for different storage needs like a finished goods warehouse in manufacturing or to hold replenishment inventory for picking stations. Other typical storage and handling requirements come with high volumes of stock in bulk storage or when allocating valuable extra space for buffer storage at inbound and outbound areas.
Among the many benefits, flexibility is an important characteristic. Being adaptable to the available space, the storage system can also be built on a higher level of the facility, providing clear working
space below. All three system components are proven, which guarantees reliable operations and optimal use of manpower. With a simple easy-to-integrate control system, automation also stands for safety and accuracy, eliminating the risk of damage or injury. Furthermore, the storage solution offers significant cost benefits by eliminating driver expenses, reducing damage through precise handling, saving energy with even movement, optimising space utilisation. Overall, a cost-effective solution compared to alternatives.
Jose Gener, Vice President Sales & Marketing explains: “We see many companies that want to increase the use of their available space. Automation is an increasingly popular route for our customers to take, given the current challenges on the labour market. So, combining these key products into an off-the-shelf solution simply makes sense.”
Axil Integrated Services has added two Manchestermanufactured Schmitz Cargobull S.CS FREEPOST semi-trailers to its busy fleet – citing the look, quality and payload benefits of the product as key reasons behind the deal.
The high-spec curtainsiders are the first trailers from Schmitz Cargobull to be put into service by the Cannock-based business. They will be paired with new Scania tractor units and used for hazardous waste collections across the UK.
Mark Downes, Director of Logistics and Fulfilment at Axil, says: “The new trailers look fantastic, offering exactly the right image for our forward-thinking business. We have traditionally leased our trailers, and these are among the first that we have purchased outright. They are spot on for our operations.”
Designed specifically to meet the needs of the UK & Irish market – the S.CS FREEPOST
offers quick, easy and safe side loading by incorporating a bolted galvanised steel cant rail and fixed aluminium roof sheet, as well as a reinforced chassis structure.
Axil worked closely on the specification with Aaron Howarth, Schmitz Cargobull Area Sales Manager for the East Midlands, even down to the artwork for the eye-catching silver livery.
“Paired with the new Scanias, they do look very smart,” adds Downes. “The drivers have been very complimentary, they particularly like the lay-out – for instance where the storage boxes and fire extinguisher are located. The pillarless design also makes loading and unloading easier, and we’ve opted for a tail-lift on the back. The fact they are built in Manchester means we are supporting British manufacturing too. Overall, it’s a great package.”
The unique design of the
S.CS FREEPOST is focused on handling, the safety of the goods and the safety of the driver and those loading the vehicle. With no sliding posts, the trailers offer the driver free, lateral loading and unloading with a side aperture height of up to 3,200mm.
To facilitate unloading, the curtain can be tensioned from both the front and the rear. Driver safety is improved further by the Schmitz Cargobull Susi-Rail, with electrical and pneumatic connections which can be moved to the edge of the trailer to make coupling easier.
In addition, due to the bolted design, should the cant rail get damaged either by fork-lift masts or even a bridge strike it is possible to replace one of the five individual sections rather than having to replace the whole rail – which can be extremely costly.
Like all Schmitz Cargobull trailers, the S.CS FREEPOST is equipped with the ultradurable, repair-friendly MODULOS chassis with a 10year guarantee against rustthrough. The manufacturer’s TrailerConnect® telematics system is factory fitted as standard.
Axil provides nationwide waste management solutions to some of the UK’s bestknown brands across a range of sectors including aerospace, automotive, food, manufacturing and pharmaceutical. Its innovative total waste management services focus on reducing customers’ business costs, while also reducing the impact on the environment.
A leading equipment hirer has invested in £17 million worth of new JCB machines as the company prepares to mark its 20th birthday.
Plant Hire UK was founded in 2005 and since that time has placed more than £200 million worth of orders with JCB – equivalent to more than 5,000 new JCB machines. The latest order for more than 300 machines includes a range of JCB Loadalls, tracked excavators and site dumpers.
Operating out of its headquarters in Haydock, Lancashire, Managing Director Graham Jones says he is proud to have one of the most modern fleets in the industry, which serve many of the UK’s leading housebuilders.
Graham Jones said: “Some years ago I decided to make Plant Hire UK 100% loyal to JCB, with machines supplied and supported by Gunn JCB. Since then, I have only ever purchased JCB equipment, underlining Plant Hire UK’s commitment to support its customers with the best machines and the best back-up in the industry. Customers, both old and new, will continue to receive market leading support as the group invests in its ambitious plans for the future”.
JCB Chief Operating Officer Mark Turner said: “JCB is immensely proud of its partnership with Plant Hire UK, and we thank Graham for his confidence in us and for his unwavering loyalty to JCB and we look forward to continuing to work with him and his team for many more years to come”.
Unlike other valves that seal with friction, Posi-flate’s unique butterfly valve uses an inflatable seat to seal with air pressure. Thus it requires less torque and a smaller actuator, resulting in lower cost. Plus, the seat automatically compensates for wear, providing longer life. Some users have reported over six million cycles and the valves are still going strong.
Less friction
Low torque
Low maintenance
Lower actuator costs
Longer valve life
More reliable
Fabricated by Shanghai Zhenhua Heavy Industries Co. Ltd. (ZPMC), the new 5,000 tonne Floating Sheerleg Crane, will be the largest of its type in the Middle East and Africa.
The crane allows heavy loads to be lifted as high as 120 meters above water, meeting the growing demand for large-scale offshore projects.
Drydocks World today signed a contract with Shanghai Zhenhua Heavy Industries Co. Ltd. (ZPMC) to acquire a new generation 5,000 tonne Floating Sheerleg Crane, which will help meet the growing demand for large-scale offshore projects.
The signing ceremony took place in Dubai, attended by His Excellency Sultan Ahmed bin Sulayem, Group Chairman and CEO of DP World, Captain Rado Antolovic, PhD, CEO of Drydocks World, You Ruikai, the Chairman of ZPMC, and senior management from both companies.
The design, construction, testing, and commissioning phase is expected to take approximately 24 months, with completion scheduled in the second quarter of 2026.
Once operational, the crane will boost Drydocks World’s heavy-lifting capabilities, allowing it to meet the growing demands of large-scale projects, such as high-voltage offshore converter platforms and Floating Production Storage and Offloading (FPSO) vessel topsides. The company’s latest investment will leverage its existing expertise, exemplified by the successful execution of significant projects such as the conversion of Tango FLNG and Excalibur FSU vessels, the refurbishment and conversion of Firenze FPSO and the ongoing EPC project on UK Norfolk
Offshore Wind Platforms.
The crane features a 160-meter-long A-frame, allowing heavy loads of up to 5,000 tonnes to be lifted 120 meters above the water, and a 600-tonne fly jib that can extend its reach to 180 meters. This capability enables the installation of larger vessel modules constructed in the yard and lifted onto the vessel for assembly, both nearshore and offshore. The crane can accommodate up to 50 personnel offshore, thereby reducing the need for support vessels. Its versatility also makes it well-suited for the construction of offshore platforms, bridges, and marine developments.
H.E. Sultan Ahmed bin Sulayem, Group Chairman and CEO of DP World, said: “Our investment in a such a significant piece of equipment marks a strategic milestone for Drydocks World, and demonstrates our commitment to enhancing our offerings to customers and achieving operational excellence worldwide. Once operational, this giant crane will strengthen our leadership in the maritime industry and boost our ability to support projects that drive regional economic growth.”
Captain Rado Antolovic, PhD, CEO of Drydocks World, said: “Acquiring the Middle East and Africa’s largest crane of this type is a transformative step for Drydocks World. As offshore vessels continue to grow in size, the need for advanced lifting solutions with features
like angled booms has become increasingly important. This new sheerleg crane, with its ability to handle heavier modules and expedite project timelines, enables us to manage more extensive and complex projects, further solidifying our status as a global leader in the maritime and offshore energy industries. ZPMC’s proven expertise in highcapacity crane manufacturing makes them the ideal partner to significantly enhance our lifting capabilities and ensure our success in mega-projects both regionally and internationally.”
You Ruikai, Chairman of ZPMC, said: “Our partnership with Drydocks World builds on a history of successful projects with DP World and opens doors for future projects together. We are proud to collaborate on this project, delivering a state-of-theart crane that combines power with cutting-edge technology for maximum efficiency and safety.”
Constructed from high-strength steel, the crane boasts advanced safety technologies and a sophisticated integrated control system for enhanced operational efficiency. The automatic ballasting system guarantees stability, and the integration of a high-capacity ballast water treatment plant also highlights Drydocks World’s dedication to environmental sustainability.
If you would like to subscribe to receive a regular copy of the digital edition of Bulk Solids Today magazine, you can subscribe on our website - www.bulksolidstoday.co.uk
If you are interested in advertising within Bulk Solids Today magazine or supplying editorial content, please feel free to get in touch using the details on our website or below.
Bulk Solids Today is sent to our digital readership of over 9,000 Chief Engineers, Operations Managers and Technical Managers from within sectors including Chemicals, Food & Drink, Mining, Quarrying, Transport/Distribution, Recycling & Waste Management and more.
www.bulksolidstoday.co.uk
Bobcat is dedicated to enabling its customers to carry out all their work quickly and efficiently. That is why the company offers not only an ever-growing selection of compact machines, all of which are intended as tool carriers, but also an extensive and continuously developing range of attachments to be used on these machines.
The power available, coupling systems, hydraulics and the Attachment Control Device (ACD) on Bobcat machines are all designed to facilitate the quick change of attachments and to allow customers to perform a wide range of tasks with the same machine. Working with attachments is an attractive choice from an investment point of view, especially for multidisciplinary companies.
“We supply one of the most extensive programs of attachments, with which you can carry out all common activities in construction, landscaping, agriculture, demolition, recycling and material handling. That is why all of our compact machines have been developed as tool carriers,” explains Katinka Kincses, Product Manager Attachments at Bobcat EMEA.
“Yet it is important to choose the right products from Bobcat. For example, a skid-steer loader is strong and agile, but for use on sensitive terrain where you do not want to disturb the soil too much, it is better to use a compact track loader. Power also plays a role. If
you want to use a forestry mulcher, a wheel saw or a snow plough, you will need to purchase a heavy-duty machine. If you want to work at a high driving speed, a skid-steer loader is not suitable and it is better to use a compact wheel loader. If lifting height and reach are important, a compact wheel loader or a telehandler are the more obvious choices. Compact wheel loaders also have the advantage that the driver sits higher and has a better view of the work area.”
Kincses believes that a customer should only purchase a specialist machine if they do the same, specialist work all day long. “For golf course maintenance, a ride-on mower from Bobcat is a great investment, but in most other cases a multi-purpose tool carrier is a wiser investment, because you can carry out more work and projects, work all year round and therefore use the machine more intensively. You often see that a new customer buys a machine with three or four attachments and gradually adds another three or four attachments, so that they can do as much work as possible with the same machine.”
Once customers have made their choice of machine, they can choose from more than 120 attachments on offer from Bobcat, many of which are intercompatible between different Bobcat tool carriers. For convenience, Bobcat has subdivided
the attachments based on activity: including demolition, construction, roadworks, landscaping, forestry, agriculture and material handling.
The range is particularly wide, especially for landscaping and road construction, but many attachments can be used for general work: such as buckets, grabs, clamps, pallet forks, roller brushes, dozer blades, graders, rakes, flail mowers, trenchers, drills and demolition hammers. In addition, there are specialist attachments such as vibrating rollers, concrete mixers, concrete buckets, planers, highpressure water cleaners, work platforms, woodchippers and even a tree transplanter.
Bobcat has integrated a lot of functionality into the machines and attachments to enhance their connectivity and operation. The company’s Bob-Tach system for connecting attachments is the industry standard, but since (the early 2000s) the Power Bob-Tach system has also been available, which allows the operator to connect and disconnect nonhydraulic attachments without the need to leave the cab. Another useful feature is the speed management system which allows adjustment of the travel speed independently from the engine speed, allowing for higher productivity.
The ACD is built into the attachment. It is a CANbus system that controls the communication between the machine and the attachment. Thanks to the ACD, the machine recognizes the attachment and automatically adjusts the settings of, among other things, the joystick controls and the hydraulics.
The driver can adjust the settings on the display in the machine and receive an overview of the operating hours, performance and status of the attachment. If an operator uses remote control to work their machine, all functions for controlling the attachment are also automatically available.
BOBCAT WITH BOBCAT
Katinka Kincses advises customers to use Bobcat attachments on their Bobcat carriers: “Our machines and attachments are optimally matched and tested. For example, you can be sure that the attachment’s software is always up to date and functions works optimally through controls available in the cab; that the hydraulic system is suitable for its tasks and that you can use all functions of the attachment. If there are technical problems, Bobcat can solve them within the warranty period and you are not stuck between two suppliers pointing fingers at each other.
“A good example of the adaptation of machine and attachment is the combination of the new FRC
200XT forestry cutter and the S86 or T86 top-ofthe-range loaders. To work with powerful tools like this, these machines have the option of a high-flow function and a super-flow function, which increases the standard flow of the auxiliary hydraulics from 87 l/min to 138 l/min or 159 l/min. To use the forestry cutter, a special ready-to-use forestry kit must also be installed on the loader, which protects the engine, machine, couplings and operator.
As Attachments Product Manager, Katinka Kincses is responsible for product development, marketing, additional services and training.
“I view my department as the voice of the customer. We map out their wishes and conduct field research to develop new attachments and new functions. We have two important principles.
“The first is the fact that job sites are becoming smaller and that the demand for compact machines and compact attachments is increasing. In addition, ease of use is becoming increasingly important. Many companies are struggling with staff shortages, which means you need to offer alternatives to human labour.
“Young and inexperienced employees must also be able to operate the machines and attachments without extensive training, so that productivity is still maintained. This can also be done through automation. For example, look at the modern grader. There is so much technology there that the machine can perform its work almost autonomously.”
From her position of responsibility for product development, Katinka Kincses does not want to say too much now about the latest attachment launches planned by Bobcat. She comments: “But we are working on interesting things that will see the light of day next year.”
For more information about Bobcat and Bobcat products, visit www.bobcat.com
Astute Systems is excited to announce the September 2024 launch of its GXA-1, an NVIDIA®powered computer, which will be showcased to key stakeholders marking a significant step towards engaging with potential UK customers. These customers include users of autonomous equipment where fast real time edge processing is required including earth movers, so relevant to agriculture, construction and power sectors (including wind farms, oil and gas pipelines, solar technology), mining, as well as to shipping and logistics and border security.
Companies who have already made the investment in this type of equipment need to ensure that these high value assets can perform at peak capacity. Engineered for SWaP-sensitive (Size, Weight, and Power) platforms, the GXA-1 is the ultimate solution for enabling autonomy in harsh environments. Purpose-built to endure extreme conditions —including extreme temperatures, moisture, vibration, and shock—the GXA-1 ensures reliable performance where it matters most.
Astute Systems highlights that the GXA-1 is ideal for those content with Commercial Off-The-Shelf (COTS) systems. For companies with developers already familiar with the NVIDIA® Software Development Kit (SDK), the GXA-1 offers seamless migration, making it an attractive option for those looking to transition to a more rugged solution or seeking Modified Off-The-Shelf (MOTS) versions
tailored to their specific environmental needs. Prequalification units with a developer kit are now available, offering a head start to those interested in early adoption.
Key features (see attached specification for full data):
• Based on the NVIDIA® Jetson AGX OrinTM Industrial SoM
• AI Performance 248 TFLOPS
• Mass storage options (dual M.2 M key SSD)
• 10 Gigabit Ethernet data plane port
• Multiple legacy analogue inputs ideal for existing DVE (Degraded Visual Environment) day/night cameras.
• Enabling autonomous workloads
Ross Newman, Founder of Astute Systems comments “We believe we have the best solution for autonomous machinery and deployment in harsh environments: the NVIDIA high performance; the perfect SWaP optimisation and proven technology. Or put another way, we’re faster, quicker, lighter and better value than anything currently available delivering the best performance per watt of any device in this class.”
For more information on current UK partners and global re-sellers, check out: https://astutesys.com https://astutesys.com/reseller https://astutesys.com/mining/
If you would like to subscribe to receive a regular copy of the digital edition of Bulk Solids Today magazine, you can subscribe on our websitewww.bulksolidstoday.co.uk
If you are interested in advertising within Bulk Solids Today magazine or supplying editorial content, please feel free to get in touch using the details on our website or below.
Bulk Solids Today is sent to our digital readership of over 9,000 Chief Engineers, Operations Managers and Technical Managers from within sectors including Chemicals, Food & Drink, Mining, Quarrying, Transport/ Distribution, Recycling & Waste Management and more.
www.bulksolidstoday.co.uk bst@abbeypublishing.co.uk
Tuf-Lok ring grip pipe and tube couplings are rugged, heavy duty, self-aligning and self-grounded couplings with a high end pull. They can be used for almost any application where pipe or tube ends need to be connected. The Tuf-Lok self-aligning couplings install quickly and easily with little effort.
Features
• Self-aligning
• Self-grounding
• High pressure rated
• Full vacuum rated
• Stainless or mild steel
• Usable on thin or thick wall pipe or tube
• Low cost
• Reusable
• Absorbs vibration
• Externally leakproof
The Modu-Kleen Series 725 top removal bin vent filter by Dynamic Air allows vented discharge air to be exhausted while preventing any outside atmospheric air from entering the storage silo or surge bin. This is ideal for venting storage bins and silos which contain hygroscopic materials that absorb moisture from the atmosphere. Materials such as granulated sugar and salt remain lump free and are handled much easier. Each filter is independent and can be easily removed without having to enter any kind of filter housing, making maintenance and troubleshooting quick and easy. This also makes maintenance far safer when trying to filter hazardous or toxic materials. An added benefit is its modular nature. If additional filter area is required, it can be added easily and at very little additional cost. Pressure differential and automatic self-cleaning controls are standard.
https://www.dynamicair.com/product/modu-kleen-binvent-filterseries-725/
The Series 486 inflatable seated butterfly valve from Posi-flate is suitable for many applications, such as food, chemical and pharmaceutical. The stainless steel valve features a fully machined 316L stainless steel housing and a single piece disc and shaft that is available in a number of materials including 316L stainless steel and Hastelloy. The disc may be polished to a mirror finish or coated with PTFE, nylon or other high-performance coating. The Posi-flate Series 486 butterfly valve is ideal for powders, granules, slurries and liquids and is available in sizes 2” (50mm) to 20” (500mm). Typical applications include loading and unloading of process material, sterile air control, and outlet valves for storage containers or hoppers.
The inflatable seat design of the Posi-flate butterfly valve provides a better seal by utilizing air pressure to expand the seat against the disc, providing more sealing area and an even pressure distribution against the disc every time. The seat automatically compensates for wear when it inflates against the disc, extending valve life considerably. Because the Posi-flate disc only makes casual contact with the seat during opening and closing, torque requirements are substantially lower. This ease of movement also allows the disc to come to a perfect 90-degree position every time. Additionally, the smooth profile of the disc helps material flow easier and reduces build-up. For unique fail-safe monitoring, a pressure switch can be utilized to verify a perfect seal.
Posi-flate
Milton Keynes, United Kingdom +44-1908-622366
E-mail: sales@posiflate.co.uk
https://www.posiflate.com
The total ship order value exceeds 14.3 billion RMB, delivery from 2026 to 2027
COSCO SHIPPING Development has signed an investment, construction and leasing agreement for 42 bulk carriers on 30th August. This milestone marks the largest shipbuilding and leasing transaction since the company transformed into a shipping industry and finance operator in 2016.
According to the transaction, the company will entrust a subsidiary of COSCO SHIPPING Heavy Industry to invest in the construction of 20 bulk carriers and CSSC Chengxi to invest in the construction of 22 bulk carriers, including five 64,000-ton ships, two 82,000-ton ships and 35 80,000-ton ships, with a total ship order value of more than RMB 14.3 billion. These ships will be delivered in succession from 2026 to 2027 and will be leased to COSCO SHIPPING Bulk for a long term. The ships in this transaction are energy-saving and environmentally friendly green ships, some of which are methanol-ready environmentally friendly bulk carriers.
In the face of the ship leasing market with both challenges and opportunities in recent years,
COSCO SHIPPING Development has actively seized the opportunity of the green and low-carbon transformation of the shipping industry, studied and explored the market potential in the sub-sectors, and accurately matched customer needs to provide solutions.
As an industry and finance operator focusing on the main line of the shipping and logistics industry, the company currently owns more than 140 ships and has layouts in multiple sub-sectors such as container ships, bulk carriers, and multi-purpose pulp ships. Through this transaction, the scale of the company’s high-quality ship assets will leap forward significantly, after the company ordered bulk carriers and multipurpose pulp ships in the early stage. The company invested in high-quality shipping capacity with newer ship types, green and environmentally friendly, reasonable configuration and strong versatility, laying the foundation for further consolidating the high-quality assets of the company’s shipping leasing business, highlighting the strategic positioning of shipping industry and finance operators, and helping the company to accelerate its progress towards the goal of value-oriented industry and finance investors and innovative industry and finance service providers.
Magway Limited, a pioneering developer of zero-emission goods transport systems, is set to showcase its innovative magnetic propulsion bulk material handling technology at Wincanton’s W² Innovation Centre.
Magway’s cutting-edge technology, designed to enhance the sustainability and efficiency of bulk material transport, will be showcased at logistics giant Wincanton’s state-of-the-art Innovation Centre in Rockingham, Northamptonshire. This centre, adjacent to The WEB – Wincanton’s automated shared user facility for high volume fulfilment, is a hub for the latest in supply chain innovation which benefits Britain’s businesses.
For six years, Magway has been at the forefront of magnetic propulsion, continuously pushing boundaries and refining its system. Magway’s technology enables precise control over the horizontal and vertical movement of loads up to 250kg, with a throughput capacity of 1,000 tonnes per hour. Remarkably, the system operates at less
than 20% of the energy and operating costs of traditional solutions, while producing zero emissions.
Phill Davies, CEO of Magway, stated:
“Every year, over 100 billion tonnes of bulk materials—equivalent to two-thirds the mass of Mount Everest—are transported globally using traditional conveyors and trucks. In order to achieve net zero, businesses need to innovate in their supply chain processes and embrace new technologies. Our system offers a compelling alternative, providing unparalleled efficiency and sustainability.
“This is the first Magway demonstrator outside of our own controlled test environment, and we’re extremely excited to showcase our technology and vision for sustainable, efficient bulk material movement. Working with these leading organizations, we can ‘Move Mountains Together’.”
Magway’s initiative is supported by
industry leaders including construction materials supplier GRS Group, Warwick Manufacturing Group, Mackley Engineering, KPMG and NatWest.
Paul Durkin, Chief Customer and Innovation Officer, at Wincanton commented:
“We are delighted to welcome Magway and its cutting-edge magnetic propulsion technology to our Innovation Centre. Innovation is at the heart of everything we do for our customers, and we are committed to collaborating with global innovators like Magway to drive emerging technology and sustainability in supply chain and logistics. Since its opening in 2021, our Innovation Centre has welcomed over 5,000 visitors, and we look forward to many more experiencing this new technology.”
Gary Coles, Integrated Solutions Director at GRS Group, said:
“As a supplier of essential bulk materials for UK construction, we’re always looking for innovations to improve efficiency and support our journey to net zero. As soon as we heard about Magway, we were keen to get involved. We’re excited to see how this remarkable technology could improve material movement at a GRS site that’s one of London’s busiest processing plants.”
NatWest’s Clean Transport Accelerator, in partnership with WMG, recently welcomed Magway into its fold. This fully funded program provides specialised support to businesses developing clean transport solutions, facilitating the rapid deployment of innovative ideas into the market.
Richard Hill, Head of Mobility and Logistics at NatWest, remarked:
“Magway’s transformation from concept to a sustainable business model has the potential to revolutionise the bulk goods movement. The accelerator is dedicated to nurturing ventures
like Magway, ensuring swift market entry and maximizing the benefits of groundbreaking innovations for the UK.”
Headquartered in Wembley, London, Magway is a pioneering zero-emissions magnetic propulsion material handling system, revolutionising bulk material movement in the construction and mining sectors. Committed to a sustainable future, Magway’s innovative solutions aim to meet global net-zero targets by 2050.
The latest ATEX 22 rated Electro Overband Magnet, designed and built by Bunting, is destined for installation in a UK biomass plant. The nature of the waste wood means that the storage and transportation areas within the plant are classified as ATEX Zone 22, where an atmosphere of air and flammable substances, in the form of powder or dust, is not likely to occur in normal operation, but if it does occur, will persist for a short period only.
Bunting is one of the world’s leading designers and manufacturers of magnetic separators, eddy current separators, metal detectors and electrostatic separators, with globally located manufacturing facilities.
Overband Magnets use strong magnetic forces to attract and automatically remove tramp ferrous metal from conveyed materials. In a wood waste biomass plant, this includes a diverse range of ferrous metal including, but not limited to, nails and screws.
An Electro Overband Magnet features an electromagnetic coil immersed in cooling oil and
mounted inside a sealed metal box. The magnetic field generated by the electromagnetic coil is projected down towards the conveyor transporting the biomass. The electromagnetic box sits between fourpulleys around which runs a rubber cleaning-belt.
In operation, the magnetic field of the electromagnet attracts tramp ferrous metal up from the conveyed biomass towards the bottom face of the magnet and onto the continually rotating rubber belt. The belt has slats that catch the attracted metal, moving it away from the conveyed material and out of the magnetic field, where it falls under gravity into a waste discharge area.
The nature of ferrous metal means that two metal pieces striking each other could create sparks. Such collisions could occur during the extraction of the metal from the conveyed material, or as the metal collides with the surface of the belt, where there could be other items of separated metal. This causes a risk hazard when handling biomass.
Biomass is derived from organic materials, either
specifically grown for use in combustion or the byproducts of other processes (recycling, agriculture, paper and pulp, timber). The Dangerous Substances and Explosive Atmospheres Regulations (2002) (DSEAR) defines a dangerous substance as one which has the potential to give rise to fires, explosions or other energetic events (HSE, 2003).
Therefore, biomass is classed as a dangerous substance and operators must comply with DSEAR. A key requirement of this legislation is that areas where a flammable atmosphere could arise are demarcated into zones.
When included in a biomass plant, Overband Magnets are located in areas that fall under the Zone 22 ATEX rating, meaning that the area is where an explosive atmosphere in the form of a cloud of combustible dust in air is not likely to occur in normal operation but, if it does occur, will persist for a short period only.
Designing an Electro Overband Magnet for installation within an ATEX Zone 22 presents a number of challenges. Motors, connection boxes, and many other standard components can all be purchased rated to ATEX 22. The Overband Magnet is shrouded in a metal casing, with extended guards
reaching down beneath the magnet as far as is practically possible. The rubber cleaning-belts are flame-retardant and anti-static (FRAS).
However, the area of potential metal collision and creation of a spark is directly underneath the magnet, where the separated metal is attracted up to the selfcleaning belt. This area has to remain open for the metal separation to occur. To reduce the already low risk potential of metal striking metal and causing a spark, the Overband Magnet has a fast-moving and continually revolving rubber belt with slats to move any metal away from the capture area quickly and efficiently.
“Understanding the installation and the DSEAR Directive and then limiting the risks is how we design Electro Overband Magnets for ATEX Zone 22 locations,” explained Adrian Coleman, Bunting’s Technical Director. “We regularly build ATEX 22 rated Electro Overband Magnets along with Eddy Current Separators, Drum Magnets, and Permanent Overband Magnets.”
For further information, please contact us on press@buntingmagnetics.com or visit our website:
Bunting-Redditch – www.bunting-redditch.com
Coperion has developed a new discharge gate valve for controlled bulk material flow from storage bins and hoppers to downstream process steps. This valve is suited for a variety of applications in the chemical and plastics industries with its impressively compact yet very robust construction. One particular feature of this new discharge valve is that it closes securely and reliably while material is flowing, but usually also when the product column is stationary, making this a perfectly suited gate valve for demanding applications. This new valve that is well thought out in design and construction secures operators a singularly reliable technology solution and makes installation and maintenance simple. Latest manufacturing technology enables compact design
Coperion manufactures this discharge valve using a precision casting process, enabling its compact and lightweight design. Its intelligent geometry, select guide elements and the form of the seal ensure that the FFU universal gate valve can
be used for a wide variety of applications with the most diverse demands — even in combustible areas (ATEX). This new geometry is what allows the gate valve to be used in the usual way even when the bulk material is stationary and best of all, its highquality, robust construction ensures dependable operation over time. Various models with manual or pneumatic drive are available in sizes DN 150 to 400 (6 to 16 inches) and can be implemented in a variety of customer-specific options.
“Decades of experience in handling a variety of bulk materials, comprehensive expertise in plant construction, and years-long partnerships with our customers allows us to develop new products that are precisely tailored to customer needs. With the new Coperion FFU universal gate valve, we offer a simple, cost-effective and flexible solution for numerous discharge applications in a variety of industries,” said Markus Reinke, Head of Component Sales at Coperion in Weingarten. www.coperion.com
Rotary valves are a proven equipment to discharge and convey bulk solids, to isolate pressure differentials or are used as flame barrier or explosion propagation isolation in ATEX zones.
With more than fifty years of experience, the UK based Gericke RotaVal is a leading company for these products. As part of the Gericke group of companies, they can combine the expertise from a dedicated rotary valve manufacturer with the global experience from many successfully supplied powder processing and bulk handling installations.
Rotary valves are found in many pneumatic conveying systems. They can also act as a safety device to isolate different process steps (airlock, flame barriers, explosion propagation valve). Another application is metering, for example when filling FIBCs.
The design and manufacturing of rotary valves beyond the commonly used size ask for specific knowledge and large machining centers. Large rotary valves are used for large throughputs or for handling of large
size and lumpy particles, for example in the petrochemical, chemical and aggregates industries.
With in-house development and production Gericke RotaVal has a large experience of building valves up to sizes of 600 by 1200 mm, often with special coatings.
The Swiss Gericke Group has been designing and manufacturing equipment and systems for automated bulk material processes, as well as providing design and engineering services, for more than 130 years. Gericke bulk materials processing technology can be found throughout the world in many sectors including the food, chemical, pharmaceutical, plastics and construction material industries.
Gericke’s fully owned group companies employ more than 350 experienced professionals and are located in Switzerland, Germany, Great Britain, The Netherlands, France, USA, Brazil, Singapore, Indonesia, Malaysia, Thailand and China.
DEVELON, FORMERLY DOOSAN CONSTRUCTION EQUIPMENT, IS USING THE RESOURCE & WASTE MANAGEMENT (RWM) SHOW BEING HELD AT THE NEC IN BIRMINGHAM IN THE UK FROM 11TH-12TH SEPTEMBER 2024, TO PRESENT FOR THE FIRST TIME A NEW DESIGN OF WHEEL LOADER AIMED AT THE WASTE HANDLING INDUSTRY.
Based around the successful Develon DL280-7 wheel loader model, part of the award-winning DL-7 range of wheel loaders from Develon, the new waste wheel loader pre-production model on the Develon Stand Number MEA120 at RWM increases safety and efficiency for the operator.
The new waste wheel loader has a novel design featuring a strong, light weight loader frame and a unique and innovative lifting arm that minimises the front end weight of the machine, providing an impressive super high lift and reach capability to deliver a higher dump height, whilst maintaining excellent manoeuvrability. The light weight loader frame is designed to offer optimum strength and heavy duty axles contribute to the exceptional stability of the new waste loader.
The super high reach on the new Develon waste wheel loader is designed for loading material into high sided containers such as walking or moving floor trailers specially developed for transporting waste. For assured loading, the new waste loader is equipped with a high tip bucket supported by two robust cylinders. The lower bucket pivot pins have internal greasing lines to prevent them being damaged by material carried by the loader.
The new loader incorporates a waste kit with heavy engineering and strength at its core, including
an exoskeleton around the machine and further protection provided by mesh type windshield guards, articulation guards, belly protection and fuel tank guards. The unit also features an air intake mesh and the cab has specialised air filtration. Other features of the new waste loader include a reversible fan to clear the radiator, a heavy duty radiator guard, rim covers for the wheels and solid tyres with suspension cut outs.
Safety features include high visibility chevrons on the rear of the machine and a fire suppression system, with internal and external actuation points on the front and rear of the loader.
Inside the spacious cab, the new waste wheel loader offers significantly enhanced operating comfort, with joystick controls and a leather type upgraded operator seat. The seat is equipped with fully adjustable horizontal and vertical suspension settings, a pneumatic lumbar function and seat heating as standard. There is a 3-point safety belt with alarm icons on the 8 inch touchscreen monitor and on the gauge panel, which features a new layout and anti-reflective glass. The operator can also benefit from an optional 360o camera system with AI person detection to ensure the safety of personnel in close vicinity to the machine.
The operator has an excellent field of vision from the cab, with the large glass window area minimising blind spots around the cab. The new waste wheel loader also offers the option of electrically adjustable rear view mirrors for added safety.
Full LED working lights are installed on the cab (four on both the front and rear as standard, with the option of six each at the front and rear). For higher pedestrian safety, the LED lights on the rear bonnet have an automatic strobe function to indicate when the wheel loader is reversing.
Included in the information at the operator’s fingertips on the touchscreen is the feed from the optional weighing system, the HVAC controls (heating, ventilation and air conditioning), Radio & Bluetooth devices (music streaming, hands-free) and the operator help function.
Overall, the cab interior offers a large, quiet and more comfortable operator environment, which improves safety and productivity and helps the operator work with high concentration. The operator also has increased leg room, an enlarged storage area and cool-box position and an improved air conditioning system (with optimized air circulation).
For more on Develon, please visit the website: https://eu.develon-ce.com/en/
The Bella dryer/cooler offers thermal efficiencies to 80 percent or better because air flows around material while it is suspended in the weightless zone. The result is a more consistent material.
For QMS, sustainability and the reduction of any negative impact on the environment are key features of the QMS offering, operations and manufacturing process. Although proud of its existing sustainability systems, QMS is now introducing further steps to reduce any negative impact on the environment through using up to date manufacturing equipment and techniques that are energy and emissions efficient. The company has also introduced measures to ensure that all staff are trained in modern manufacturing techniques and environmental awareness as well as how to efficiently use resources. By the way very nature of screening and crushing product lines, from manufacturing to logistics, QMS strives to be a leading sustainability partner for its customers, aiming to help them achieve more sustainable business practices. “Our sustainable business strategy is based on international guidelines and principles and embedded in our everyday business practices. We’ve established sustainability goals for 2030 - circularity, climate change and
people - that are given the same prominence as traditional business targets. These will remain a core consideration in our development of solutions for the mining, mineral excavation, recycling and generic construction industries,” says company managing director Jonathan Beck.
As part of these goals, QMS has developed rebuild solutions that prolong its mineral processing equipment lifecycles and implemented recycling programmes for steel and wear parts, as well as launching a range of initiatives to support its avowed aim of making its products and packaging ‘circular’. “We also aspire to dramatically reduce waste from production through reducing waste or repurposing what might otherwise be waste, thus minimising the number of new materials we need to create,” explains Jonathan Beck, who adds: “QMS has also reduced carbon emissions through reformed logistics approaches and aims at our new factory development to capture waste heat released in
production processes and redistribute it to warm our facilities. As QMS manufactures energy efficient equipment, we also help our customers reduce their carbon footprints.”
The QMS way of doing things is essentially a way of facing a world with resource scarcity, with the company believing that it has developed successful strategies for sustainable development. In fact QMS has embraced the philosophy of the ‘circular economy’ where resource input and waste, emissions, and energy leakage are minimised by slowing, closing, and narrowing energy and material loops. This means that components and materials are kept in the loop for as long as possible. “We are continually striving to see a manufacturing process where waste no longer exists, and everything recirculates back into the process to convert into another product, component, or material,” adds Jonathan.
Waste avoidance, life cycle extension through remanufacturing or reuse, and improved recycling techniques are seen by all at QMS as important strategies for sustainable manufacturing. The manufacturing operation itself is continually invested in so as to use the most efficient processes, with the new manufacturing plant – which is being constructed – set to be energy, noise, emissions, heat, light and waste efficient. Pollution from the existing plant is already minimised and will be further reduced when the new factory comes online. Furthermore, the company recycles as much of the materials used as is possible as well as using recycled materials where applicable throughout QMS’s operations.
“Contaminated materials at the factory are now recycled/reused, as well as all equipment demonstration materials, whenever possible, and dealt with by a professional waste processing company if required. Our manufacturing plant is made from materials that minimise noise, with the new factory being designed to further reduce noise pollution. Furthermore our equipment is designed to operate to national decibel limits and capable of working in inner city environments when required,” explains Jonathan.
Manufacturing efficiency is further enhanced via QMS’s focus on product design. The company has found through its long and proud history that the best way to reduce material waste is to use less material from the beginning. Designing parts using methodologies such as value engineering and design for manufacturability have drastically improved efficiency. Jonathan Beck explains: “Where possible we recycle scraps and factory returns. Even when we are unable to use the recycled material, we sell it on to those who can so as to continue the material life cycle. All our
production processes are optimised to utilise all available material as we view every scrap of discarded material representing an opportunity to improve process efficiency.”
Renewable materials are also used where possible, and through QMS’ aftermarket and spare parts business, the company aims to ensure that customer plants are kept operational for longer, with oil, water, steel, plastic etc being recycled and reused. In addition, QMS plants are energy and fuel efficient using renewable sources of power where possible and using clean energy via the grid as their primary power source.
All QMS equipment is by its very nature manufactured to maximise the world’s minerals mineral resources, proving their worth in efficiently dealing with virgin deposits. QMS equipment is also equally adept at recycling in order to reduce construction materials so that they may be reused and recycled. To this end QMS produces washing plant that is energy and water efficient, reusing as much of the water as possible, whilst the extensive range of crushers and screens operate under the maxim of ‘reduce, recycle, reuse’ as they reduce materials, sort by size, enabling former waste materials to form valuable products further continuing the material life cycle.
“Our aim is to use energy more efficiently with the manufacturing plant and offices being equipped with energy efficient technology. This also extends to company transport, where travel is kept to a minimum, and where possible, we use fuel efficient vehicles. Equipment deliveries are coordinated so that a minimum of vehicles is used, and when exporting, we send our equipment by container, by sea. The process of making our systems, equipment, parts, offices, production processes, are continually developed, measured and improved so as to further improve our sustainability,” concludes Quarry Manufacturing & Supplies managing director Jonathan Beck.