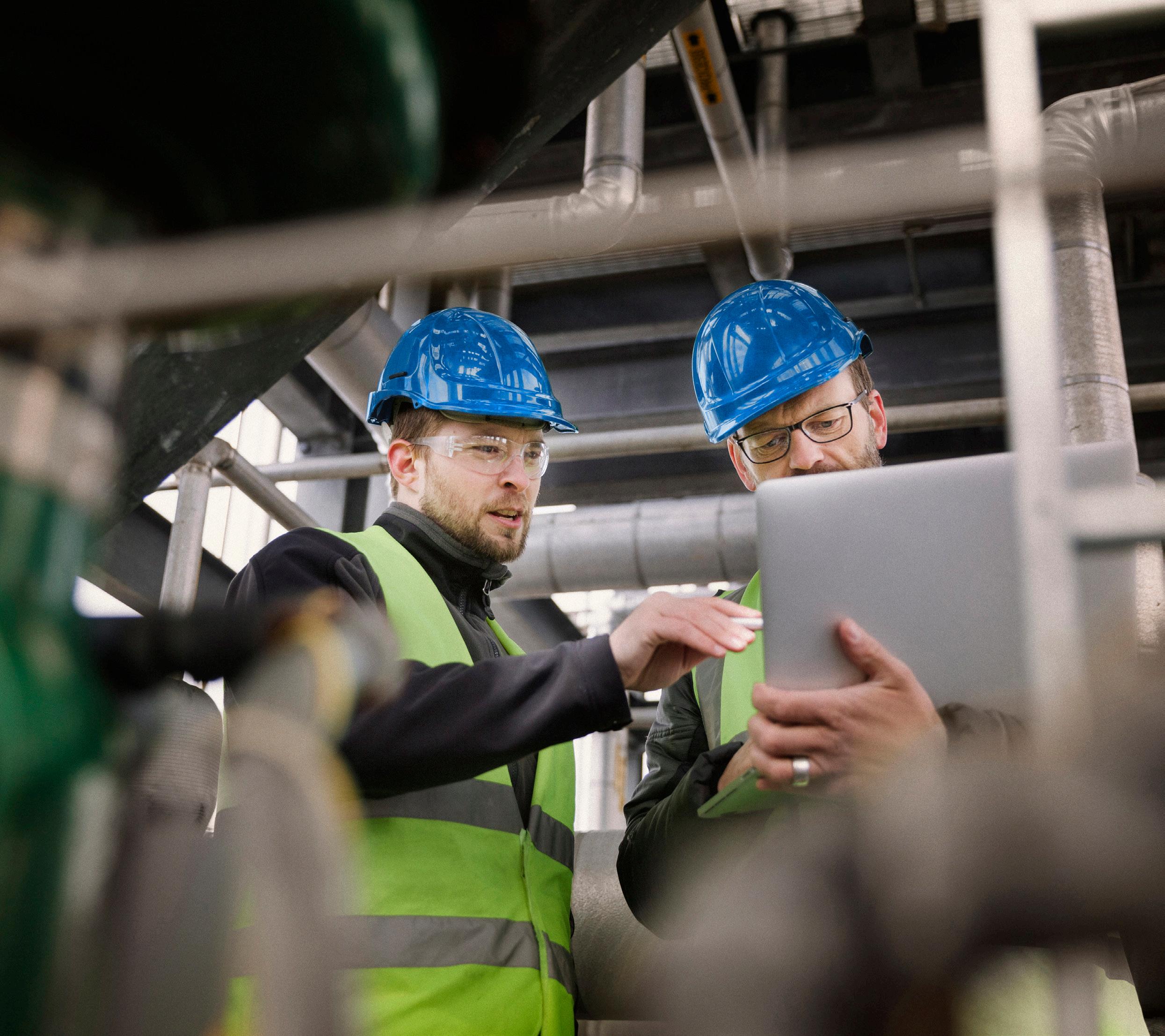
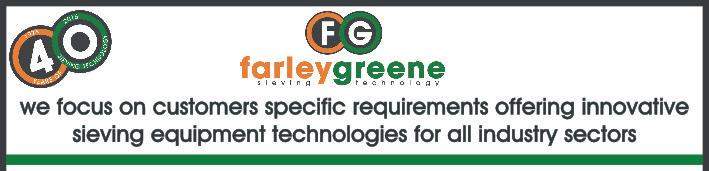

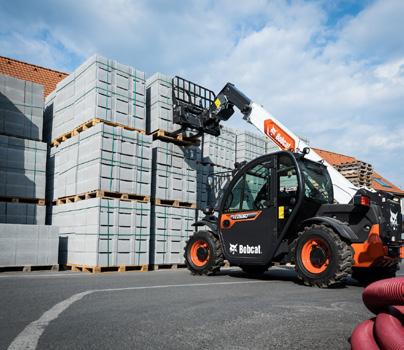
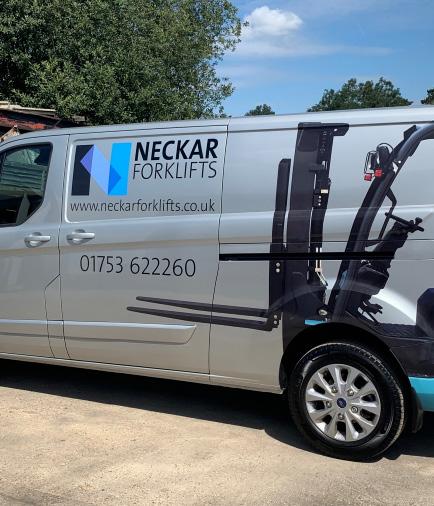
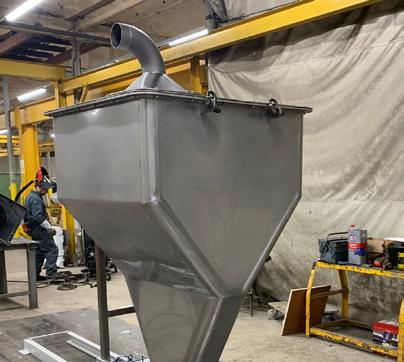
From micron sized powders to large pellets and everying in between, Dynamic Air can move your dry granular materials gently, reliably and with significant reductions in product degradation and/or system wear.
Dynamic Air dense phase pneumatic conveying systems have been proven in over 15,000 installations worldwide. They handle a wide range of materials and bulk densities at rates from less than a hundred kilograms per hour to 400 tonnes per hour, over distances exceeding 1500 metres.
Each Dynamic Air system is custom designed from one of our sixteen different conveying concepts. So you get a conveying solution that fits your process perfectly, without compromises.
Our high material-to-air ratios reduce energy and compressed air requirements. Our low conveying velocities provide significant process savings in both operation and maintenance.
Issue
Sales Director: James Scrivens
Production: Sarah Daviner
Accounts Manager: Avery Hudson
Office Manager: Katie Brehm
BULK SOLIDS TODAY is published 6 times a year by Abbey Publishing Ltd
ADVERTISING & EDITORIAL
Please contact us at:
Tel: 01933 316931
Email: editorial@bulksolidstoday.co.uk advertising@bulksolidstoday. co.uk
Web: www.bulksolidstoday.co.uk
Twitter: www.twitter.com/
BulkSolidsToday
CIRCULATION
To receive a copy free of charge, please send your details to subs@bulksolidstoday.co.uk
No part of this publication may be reproduced by any means without prior permission from the publishers. The publishers do not accept any responsibility for, or necessarily agree with, any views expressed in articles, letters or supplied advertisements.
ISSN: 1365/7119
All contents © Abbey Publishing Ltd 2017
Briggs Equipment has completed the acquisition of UK materials handling specialist, Neckar Forklifts Limited and Maxim GB Ltd.
From their sites in Windsor and Castleford, these businesses have more than 50 years of industry experience and offers a full range of forklift sales, hire solutions, driver training, service support, fleet management and warehouse planning.
The acquisition provides Briggs Equipment with increased coverage across key areas of England and further strengthens its position as the UK and Ireland’s premier Asset Management and Engineering Services specialist.
Pete Jones, Briggs Equipment’s Group Managing Director, commented: “This acquisition is another significant milestone for our Group and is an extremely positive way to start 2023.
“Neckar and Maxim have a proven track record of longterm success and operates within areas of the UK that are strategically very important to us. Their loyal and diverse customer portfolio demonstrates the capability of the business and
we are determined to deliver the appropriate investment support and guidance to help Neckar and Maxim reach their full potential.”
Ian Capes, of both Neckar Forklifts and Maxim GB, commented: “We are delighted to announce our acquisition by Briggs Equipment and we can’t wait to start working as part of a successful and ever-evolving Group.
We have undergone an intensive period of due diligence
to ensure that our unique culture and ambition would be preserved. With Briggs Equipment we have a parent company that is committed to the long-term success of every business within its Group, and I’m proud to say that Neckar Forklifts and Maxim are now part of the Briggs family.
“We now look forward to working closely with our new colleagues and reaching new heights in this exciting new chapter for our business.”
Bulk Solids Today is the bi-monthly digital journal covering the storage, processing and handling of materials ranging from fine powders to the heaviest raw materials.
To subscribe to Bulk Solids Today magazine or for more information, please feel free to visit www.bulksolidstoday.co.uk
Rushlift GSE, the specialist airport ground support equipment and services provider, has won a 56-month extension to its successful, longrunning GSE contract with Europe’s leading short-haul airline, easyJet.
The new multi-million pound deal continues an existing five-year agreement with Rushlift GSE to supply, manage and maintain easyJet’s ground-handling fleet at London’s Gatwick Airport, the low-cost carrier’s largest and busiest base with around 210 departures a day at peak.
In total over 570 ground support assets will be managed by Rushlift GSE under a progressive programme of innovation and equipment enhancement, which includes an on-going transition from diesel to electric vehicles. As part of this programme Rushlift is in the process of introducing eight Mallaghan bendi-belts, an advanced electric powered baggage conveyor that has the ability to bend through 90 deg, delivering bags deep into the baggage hold. The investment will help to reduce turn-around times, ease demands on staff and reduce manual handling strain.
As under the existing contract, Rushlift GSE will supply, maintain and support a wide variety of vehicles of different manufacture, along with related handling equipment – from TLD pushback tugs, TBL tractors, electric baggage tugs and baggage carts, to steps, low loaders, belt loaders, ground power units and vans. During the course of 2022 Rushlift supplied easyJet
with over 100 additional items of GSE. All vehicles will be regularly serviced under a set maintenance regime, with fast, on-site breakdown response and support.
In line with the expansion of Rushlift GSE’s Gatwick operations the business has opened a new 36,000 sq ft service centre and workshop close to the airside access gates.
“Our business demands a keen focus on cost and efficiency – and a fast turn-around of aircraft on the ramp is absolutely critical to our success,” says Dan Chapman, Regional Operations and Contracts Manager, at easyJet. “Over the last five years, Rushlift GSE has proved to be a highly dependable partner, providing us with reliable and efficient ground support equipment and helping us to meet our sustainability targets through a structured transition to electric GSE vehicles. This has given us every confidence to extend our close working arrangement for a further 56 months.”
Tim Willett, General Manager at Rushlift GSE, commented:
“We are delighted that easyJet has chosen to endorse our close working relationship by extending our contract. With 75% of easyJet’s ground support fleet now electric, we look forward to continuing to support the business in completing its transition to electric powered GSE equipment. And with the opening of our new maintenance and workshop facilities at Gatwick, we’re offering our continued commitment to providing the high level of service and support expected by one of the industry’s leading airlines.”
In 2017 easyJet took the unprecedented step of deciding to lease ground support equipment directly, through Rushlift GSE, and bring in contractors that would supply labour resources only. This was a radical move and a first for the sector. The initiative was recognized at the 2018 International Airport Review Awards, taking the trophy for Airside Operations.
For further information on Rushlift GSE go to https://www. rushlift.co.uk
Gericke has delivered a material handling system for the storage, batching and pneumatic transport of various types of calcium carbonate powders to several mixers. For the production of adhesives and sealants different types of calcium carbonate powders have to be delivered in the correct amounts to the mixers. In addition to ground calcium carbonate powder that can be characterised with mostly free flowing properties, also precipitated calcium carbonate powder have to be handled. Due to the sub-micron particles of the precipitated calcium carbonate these powders are very challenging to handle as they are very cohesive and exhibit poor flowing performance.
Extensive trials were initially performed with various types of calcium carbonate powders in the Gericke test centre to evaluate the best pneumatic conveying conditions allowing an energy efficient and safe transport of the powders over 70 – 130m of conveying distance with minimal residues. As a result, the Gericke PulseFlow® PTA dense phase pneumatic conveying system achieved the lowest gas flow consumption per weight of transported product. This in turn also means the lowest energy requirement.
With the Gericke PulseFlow® PTA dense phase pneumatic conveying system a pressure vessel is used for transporting the powders as slowly moving product plugs
powered by air velocities in the range of 4 –12 m/s. This in contrast to lean phase pneumatic conveying systems which operate with air velocities usually much above 20 m/s.
Due to the cohesive character of the precipitated calcium carbonate a special fluidising discharge system was used to maintain a steady discharge of the pressure vessel. The fluidising discharge system prevents the formation of rat holing and funneling effects in the vessel, which would reduce the conveying capacity and ultimately lead to failures in conveying and complete discharging of the loaded powder.
In the real plant the various calcium carbonate powder were fed according to the recipe into a weighed pressure vessel. Once the correct filling was reached the pneumatic transport started with conveying the powder to
the dedicated destination above various mixers. Before stopping the conveying system and switching over to the next mixer the pipeline was purged to remove residues in the conveying pipe.
Unlike other valves that seal with friction, Posi-flate’s unique butterfly valve uses an inflatable seat to seal with air pressure. Thus it requires less torque and a smaller actuator, resulting in lower cost. Plus, the seat automatically compensates for wear, providing longer life. Some users have reported over six million cycles and the valves are still going strong.
• Less friction
• Low torque
• Low maintenance
• Lower actuator costs
• Longer valve life
• More reliable
Hyundai Material Handling has unveiled a range of Heavy Line diesel forklift trucks, with an improved cab environment, EU Stage V emissions-compliant engines and the option of Hyundai’s HiMate telematic monitoring system. There are 10 models on offer, with lift capacities of 7-30 tonnes and they build on the successful launch last year of the lighter models in the diesel forklift lineup.
• Ten machines with lift capacities of 7-30 tonnes
• Improved cab environment with additional space and visibility
• EU Stage V Hyundai and Cummins diesel engines
• Load sensing Main Control Valves for
• Hyundai HiMate telematics deliver fleet management solution
Designed after extensive consultation with customers, Hyundai’s next generation forklift cab features a revised console layout and a smaller steering wheel, to deliver increased working space for the operator. A one-piece constant radius windscreen provides improved forward visibility without edge distortion, while fully glazed doors also contribute to a reduced in-cab noise level, cut by up to 5.9dB.
A new console incorporates a colour display with easy access buttons for regularly used functions. The multifunction screen delivers relevant machine
operating data and can provide in-cab service alert and diagnostic codes when required. A second 7” display shows the rear view camera images.
The new load sensing Main Control Valve provides increased control, with fingertip levers delivering improved response to operator input. As an option, you can choose for an air suspended seat or a swivel seat which can be rotated 20° to the left and 10° to the right, for improved reverse direction visibility and to ease access to the cab. For models from 12T and up the premium seat has both air suspension and swivel.
All of the Heavy Line models are powered by EU Stage V diesel engines, from Hyundai and Cummins, offering improved performance and reduced
emissions. The Cummins B Series engines no longer require Exhaust Gas Recirculation (EGR), simplifying service and maintenance on the heavier models. These machines also boast an engine power button in the cab, that allows the operator to choose between Standard (80%) or Power (100%) settings, according to the demands of the application, reducing fuel consumption when full power is not required.
With an electrically powered side-tilting cab structure, access to the powertrain is simplified, for ease of regular maintenance. Fuel filter life has been extended from 500 to 1,000 hours, while long-life hydraulic oil now means change intervals can be extended to 5,000 hours, reducing cost of ownership and downtime for the customer.
Heavy Line forklifts are equipped with two levels of Hyundai’s proven HiMate telematics system as an option, using GPS technology to transmit data to allow remote monitoring and diagnostics. The standard HiMate system provides real-time monitoring of machine location and operating information, with geofencing alerts delivering an additional level of security against machine theft or unauthorised use. The premium HiMate adds driver access control through code or card, fully customisable start-up questionnaires, drive style monitoring and collision detection.
Machines with a Cummins engine can also be optioned with Engine Connected Diagnostics, supplied in cooperation with the engine manufacturer, delivering tailored maintenance and remote troubleshooting, further reducing
the possibility of costly downtime for the customer.
Hyundai’s Heavy Line diesel forklift range starts with the 7-tonne 70D-9V, running through to the 30-tonne capacity 300D-9VC. With an extensive line-up of 10 models, there is now a dedicated machine to meet every customer operation, in a wide variety of materials handling sectors.
“We have really listened to the needs of our customers to develop these Heavy Line machines,” said Christopher Thompson, Head of Sales at Hyundai Materials Handling.
“These new forklifts deliver an improved driver’s ‘office’ in the cab and increased access through HiMate in the fleet manager’s office. Our next generation forklifts put the operator and the fleet manager in control.”
The robust OMRON TM20 improves cycle times and comes with a two-year warranty after registration
OMRON, a leading provider of industrial automation solutions, has announced the launch of its new OMRON TM20 cobot with a payload of 20 kg. The new cobot is ideal for tasks such as palletizing, machine tending and material handling. Whilst managing heavy payloads, the OMRON TM20 has a small footprint and a reach of 1,3 meters.
The OMRON TM20 is the latest addition to the OMRON family of TM cobots, which are known for their ease of use, reliability, and safety. It is designed to work seamlessly with other OMRON products, including sensors, controllers, and software, to provide a comprehensive automation solution for industrial customers.
One of the key features of the OMRON TM20 is its lightweight design, weighing in at just 33 kg. This makes it easy to integrate with mobile robots, providing greater flexibility and efficiency in industrial environments. The robot also comes equipped with special joint covers to protect it from cutting oil and other hazardous materials, making it suitable for use in machine tending applications.
“We are excited to launch the OMRON TM20, which expands the capabilities of our
cobot family and gives customers the ability to automate heavy payload applications,” Fernando Vaquerizo, Fixed and Cobots Product Marketing Manager at OMRON Europe. “The OMRON TM20 is designed to be easy to use, reliable and safe. It relieves operators from tasks that involve heavy lifting, while working safely side by side with people.”
OMRON’s ROI calculator supports companies in the process of evaluating an investment in collaborative robots, including easy and affordable leasing opportunities. In addition, OMRON offers a wide range of support services, including installation, training, and maintenance, to ensure customers get the most out of their investment.
Key features and benefits:
• 20 kg payload capacity for handling heavier parts and materials
• Reach of 1300mm ideal for palletizing applications
• Cycle improvements thanks to faster joints
• 24 months warranty after registration
The OMRON TM20 collaborative robot is available for pre-orders now. For more information on the OMRON TM20 and other OMRON cobots, please visit the company’s website at http:// industrial.omron.eu/cobots
If you would like to subscribe to receive a regular copy of the digital edition of Bulk Solids Today magazine, you can subscribe on our websitewww.bulksolidstoday.co.uk
If you are interested in advertising within Bulk Solids Today magazine or supplying editorial content, please feel free to get in touch using the details on our website or below.
Bulk Solids Today is sent to our digital readership of over 9,000 Chief Engineers, Operations Managers and Technical Managers from within sectors including Chemicals, Food & Drink, Mining, Quarrying, Transport/ Distribution, Recycling & Waste Management and more.
www.bulksolidstoday.co.uk
bst@abbeypublishing.co.uk
Tuf-Lok ring grip pipe and tube couplings are rugged, heavy duty, self-aligning and self-grounded couplings with a high end pull. They can be used for almost any application where pipe or tube ends need to be connected. The Tuf-Lok self-aligning couplings install quickly and easily with little effort. Features
• Self-aligning
• Self-grounding
• High pressure rated
• Full vacuum rated
• Stainless or mild steel
• Usable on thin or thick wall pipe or tube
• Low cost
• Reusable
• Absorbs vibration
• Externally leakproof
A new High-Volume Open-Chute Tipper from Flexicon allows discharging of non-dusty, freeflowing and/or agglomerated bulk materials from multiple drums or boxes simultaneously, as well as from Gaylords, totes or bins individually.
The bed of the unit’s hydraulically-tipped housing can accommodate containers from 940 to 1115 mm in height, having an individual or combined footprint of up to 1825 x 2435 mm. Typical applications for multiple containers include simultaneous dumping of four 210L drums, or four boxes, each having a footprint of 915 to 1220 mm.
Pallets weighing up to 2265 kg are forklift-loaded into the three-sided unit and secured, after which a grate is lowered onto the container(s) to prevent shifting. The lifting assembly is raised to a height of 1955 mm and tipped hydraulically, causing material to slide through a smooth, three-sided chute into receiving vessels.
Twin hydraulic cylinders pivot the platform-chute assembly to discharge angles of 45 or 60 degrees beyond horizontal, including a motion-dampening feature at the termination
of container rotation. Impact-resistant side panels and custom guard panels with a light curtain ensure safe operation.
The tipper is available in heavy-duty, all-stainless construction to sanitary standards (shown) or in carbon steel with durable industrial coatings and stainless steel material contact surfaces.
It is also available with optional receiving hoppers configured with Flexicon mechanical or pneumatic conveyors to transport discharged material to any plant location.
The company also manufacture other configurations of drum/box/container tippers as well as flexible screw conveyors, tubular cable conveyors, pneumatic conveying systems, bulk bag dischargers, bulk bag conditioners, bulk bag fillers, manual dumping stations, weigh batching and blending systems, and engineered plant-wide bulk handling systems with automated controls.
For information contact Flexicon Europe Ltd, +44 (0)1227 374710, sales@flexicon.co.uk, www.flexicon.co.uk
Dynamic Air’s HDP 4000 Full-Line Concept dense phase pneumatic conveying system has many advantages over more traditional dense phase concepts with regard to degradation and energy consumption. The system utilizes our DC-5 Air Saver technology to achieve an optimum pressure balance while counteracting forces of friction. The Full-Line Concept system conveys materials at low velocity and high density while utilizing very low air consumption.
https://www.dynamicair. com/systems/hdp4000.html
Dynamic Air Inc. St. Paul, MN
(651) 484-2900
e-mail: systemsales@ dynamicair.com
www.dynamicair.com
you are interested in advertising within Bulk Solids Today or contributing editorial, please do get in touch using the details below:
(Note: Doosan Infracore is replacing the DOOSAN brand on its construction equipment and introducing its new brand named DEVELON which is now in a transition period)
August Lücking GmbH & Co. KG is a 123 year old building materials producer based in northwest Germany. About two years ago, the company purchased a Doosan DL420CVT-5 wheel loader to feed materials for the brick production process. The purchase decision was based on trials that showed enormous fuel savings of more than 9 l/h, which were confirmed when the new machine began operation. As a result, when the time came for a new wheel loader to be bought, the decision was made from the start: the new machine should also be a Doosan DL420CVT, this time the next generation DL420CVT-7 model.
When the purchase of the original wheel loader was on the agenda about two years ago, a Doosan DL420CVT-5 was tested on site in the
company’s brick factory. The requirements for the loading of clay for the bricks are particularly challenging. The clay has a high density and therefore a high weight. In addition, the material is extremely sticky and tough. In order to penetrate the material with the shovel, a high degree of even force and high traction are required, especially on wet surfaces. The tyres also play a major role here. Lücking relies on special tyres whose profile is more like that of a tractor than a wheel loader. The grooves of the tread on ‘standard tyres’ clog up quickly due to the greasy consistency. These difficult conditions also drive up fuel consumption.
The previous machine, a competitor’s wheel loader with a conventional converter transmission, required an average of around 23 l/h of fuel under these conditions. When the authorized signatory at Lücking, Richard Lemke, asked the wheel loader sales manager at Doosan, Marc Glesius, about the consumption to be expected
under these conditions during the handover for the test operation, he cited 14 l/h, a value that Lemke found difficult to believe.
Richard offered Marc the following bet: “If the DL420 with the CVT transmission only consumes 14 l/h, i.e. around 10 litres less, I will buy it immediately.” The rest, as they say, is history. The test consumption was the targeted 14 l/h and the wheel loader has now been in service at the company for two years.
Richard Lemke added: “In times of enormously high fuel and energy prices, 10 l/h naturally make an enormous difference. In the last two years, the consumption of the DL420CVT-5 has levelled off at the 14 l/h already determined in the test operation. We also did not record any unscheduled machine failures during this period. Therefore, only a Doosan wheel loader with a CVT transmission came into consideration when purchasing a new vehicle. We are confident that the new wheel loader can confirm these positive experiences.”
One of the main factors behind the low fuel consumption is the variable transmission. Marc Glesius said: “This transmission combines the advantages of a mechanical and hydrostatic transmission and excludes the disadvantages
of both systems. The variable transmission switches continuously from the hydrostatic drive to the mechanical drive as the speed increases and depending on the application-related requirements. The advantages that this system offers include, in particular, the excellent traction that a hydrostatic transmission offers and driving over longer distances with a direct mechanical transmission. It owes the fuel savings to the lower engine speed compared to conventional transmissions, which is necessary to achieve maximum speed and traction.”
Founded in 1899 from an agricultural business in Paderborn, the brickworks today employs 170 people at its production site in Warburg Bonenburg. This fifth generation family-owned company is a modern, efficient industrial business with its own vehicle fleet.
Every year, 200,000 m³ of bricks, 300,000 m² of prefabricated ceilings and 50,000 m² of prefabricated walls are produced, as well as staircases, balconies and prefabricated parts for special applications.
For more on Doosan construction equipment, please visit the website: www. eu.doosanequipment.com
Compact Tractors, E19e Electric Excavator & TL25.60 Telehandler
Bobcat Is exhibiting at SaMoTer 2023, the most important exhibition in Italy for the construction machinery sector, presenting several recently launched product lines and models for the first time in the country.
SaMoTer provides an ideal platform to show visitors the new Ground Maintenance Equipment (GME) range from Bobcat, which includes compact tractors, small articulated loaders (SAL), mini track loaders, mowers and turf equipment. Building on the company’s success in the North American market, Bobcat aims to rank within the top three GME players in Europe and to double growth in the global GME market by 2027.
Compact Tractors Provide Versatility for Countless Applications
All Bobcat GME models are robust and versatile, providing excellent productivity and great comfort. Representing the range, a cabbed version of the new CT2535 compact tractor will be on display on the Bobcat stand at SaMoTer for the first time in the Italian market.
Bobcat is offering three Compact Tractor
platforms – the 1000, 2000 and 4000 series –which feature nine new models from 25 to 58 HP designed to meet the different needs of customers in the EMEA region. Each model varies in size and engine horsepower, with the option to choose between manual and hydrostatic transmission, and between open canopies (ROPS) and cabs.
Bobcat’s proven Bob-Tach system comes as standard on all machines with the frontend loader option, enabling users to switch effortlessly between different Bobcat attachments, to carry out multiple jobs easily, delivering value and versatility for customers’ businesses.
Francesca Biagini, Italy, Greece & Iberia Attachments - GME Sales Manager, comments: “These machines are versatile tool carriers thanks to their total compatibility with a wide range of Bobcat attachments that allow users to maximize productivity in any application such as gardening, agriculture, construction, roads and snow clearing, to name a few.”
Videos of the new Compact Tractors: Action video https://youtu.
be/1nI3xwK19W8
Machine walkaround video https://youtu.
be/OJTeLTEJENc
New Bobcat TL25.60
Another star at SaMoTer 2023 is the super compact TL25.60 telehandler, launched at Bauma 2022 and being presented for the first time at SaMoTer, Ideal for the construction, rental and general handling sectors, the TL25.60 is the eleventh fixed-frame telehandler model in the latest R-Series range from Bobcat and is the smallest machine in the line.
Designed for maximum ease of use, the TL25.60 offers excellent stability, optimal comfort and safe operation in a wide range of applications. Equipped with a 75 HP Bobcat Stage V engine, the machine boasts a rated operating capacity of 2500 kg and a maximum lift height of 5.9 m.
Despite its super-compact dimensions, the TL25.60’s cab is identical to that in the larger Bobcat R-series models, making it the most spacious compact telehandler on the market today.
Action video https://youtu.be/JsZ0Sh7or10
The Bobcat stand will offer the opportunity to see a selection of the company’s most popular mini-excavators, including the E20z, E27z and E55z/E60 models, as well as the first appearance of the new 2 tonne E19e electric mini-excavator, introduced in October 2022, part of the company’s ever-expanding range of electrified machines.
The E19e offers zero emissions, low noise, reduced vibration and the same excellent performance as the popular diesel-powered E19 model.
This machine will build on the success of the E10e, the world’s first electric 1 tonne miniexcavator from Bobcat, demonstrating that the company is a true pioneer in the field of batterypowered machines and will continue to invest in research and development to accelerate this important trend.
The E19e is also extremely versatile, with a wide range of compatible attachments available. For example, Bobcat’s hydraulic grapple is the only one on the market for this size category.
Action video https://youtu.be/0hljmHt9RWU
For more information about Bobcat and Bobcat products, visit the website www.bobcat.com
Hyundai Material Handling has unveiled a range of Heavy Line diesel forklift trucks, with an improved cab environment, EU Stage V emissions-compliant engines and the option of Hyundai’s HiMate telematic monitoring system. There are 10 models on offer, with lift capacities of 7-30 tonnes and they build on the successful launch last year of the lighter models in the diesel forklift line-up.
Features include:
• Ten machines with lift capacities of 7-30 tonnes
• Improved cab environment with additional space and visibility
• EU Stage V Hyundai and Cummins diesel engines
• Load sensing Main Control Valves for improved operator control and efficiency
• Hyundai HiMate telematics deliver fleet management solution
Designed after extensive consultation with customers, Hyundai’s next generation forklift cab features a revised console layout and a smaller steering wheel, to deliver increased working space for the operator. A one-piece constant radius windscreen
provides improved forward visibility without edge distortion, while fully glazed doors also contribute to a reduced in-cab noise level, cut by up to 5.9dB.
A new console incorporates a colour display with easy access buttons for regularly used functions. The multifunction screen delivers relevant machine operating data and can provide in-cab service alert and diagnostic codes when required. A second 7” display shows the rear view camera images.
The new load sensing Main Control Valve provides increased control, with fingertip levers delivering
improved response to operator input. As an option, you can choose for an air suspended seat or a swivel seat which can be rotated 20° to the left and 10° to the right, for improved reverse direction visibility and to ease access to the cab. For models from 12T and up the premium seat has both air suspension and swivel.
All of the Heavy Line models are powered by EU Stage V diesel engines, from Hyundai and Cummins, offering improved performance and reduced emissions. The Cummins B Series engines no longer require Exhaust Gas Recirculation (EGR), simplifying service and maintenance on the heavier models. These machines also boast an engine power button in the cab, that allows the operator to choose between Standard (80%) or Power (100%) settings, according to the demands of the application, reducing fuel consumption when full power is not required.
With an electrically powered side-tilting cab structure, access to the powertrain is simplified, for ease of regular maintenance. Fuel filter life has been extended from 500 to 1,000 hours, while long-life hydraulic oil now means change intervals can be extended to 5,000 hours, reducing cost of ownership and downtime for the customer.
Heavy Line forklifts are equipped with two levels of Hyundai’s proven HiMate telematics system as an option, using GPS technology to transmit data to allow remote monitoring and diagnostics. The
standard HiMate system provides real-time monitoring of machine location and operating information, with geofencing alerts delivering an additional level of security against machine theft or unauthorised use. The premium HiMate adds driver access control through code or card, fully customisable start-up questionnaires, drive style monitoring and collision detection.
Machines with a Cummins engine can also be optioned with Engine Connected Diagnostics, supplied in cooperation with the engine manufacturer, delivering tailored maintenance and remote troubleshooting, further reducing the possibility of costly downtime for the customer.
Hyundai’s Heavy Line diesel forklift range starts with the 7-tonne 70D-9V, running through to the 30-tonne capacity 300D-9VC. With an extensive line-up of 10 models, there is now a dedicated machine to meet every customer operation, in a wide variety of materials handling sectors.
“We have really listened to the needs of our customers to develop these Heavy Line machines,” said Christopher Thompson, Head of Sales at Hyundai Materials Handling.
“These new forklifts deliver an improved driver’s ‘office’ in the cab and increased access through HiMate in the fleet manager’s office. Our next generation forklifts put the operator and the fleet manager in control.”
The airborne dust created by many manufacturing facilities that generate, handle, transport, process or store materials that cause or become combustible dust is no mere housekeeping problem. Once those particles have settled in difficult-to-reach places throughout a site, any subsequent disturbance can produce a potentially explosive dust cloud.
The creation of a risk mitigation plan is therefore necessary for most facilitiesincluding many that would not traditionally be considered ‘dangerous.’ Along with studying legislation requirements in your region, reducing the likelihood of an incident is the best possible step, beginning with ‘Is my dust actually combustible?’
This isn’t as straightforward as it might sound. Few people would smoke a cigarette while refueling their car, yet many wouldn’t think twice about lighting up while taking a break from working on home renovations that have produced an abundance of sawdust.
Any fine material that can catch fire when mixed with air is a potential risk. Examples
include most solid organic materials (sugar, flour, wood, etc.), metals, and more. In fact, even partly oxidized aluminum dust generated from plasma cutting can be considered explosive under certain circumstances –only a proper risk assessment can provide reassurance.
Sending a sample of your dust to a qualified lab is a good place to start. If it’s shown to be combustible, further tests will determine if it’s explosive, how quickly that can happen, and how much force it can carry. This information will help direct the selection of equipment needed to mitigate the hazard.
While managing any one or more of the well-known Fire Triangle’s elements of oxygen, heat and fuel can decrease the fire risk, explosion risk-management strategies must consider another two elements. Dust dispersion and dust confinement produce the Explosion Pentagon — and may require a separate strategy to address any remaining explosion risks.
The Explosion Pentagon’s fuel element is
the finely dispersed dust cloud. As a rule of thumb, a cloud dense enough to screen your hand from view would be considered a risk — or, in more practical terms, a dust layer of just 0.5mm. But, rather like how propane gas is only dangerous between 1.8 – 8.4% concentration volumes in the air — particle size is a key factor. Germany’s Occupational Safety & Health Institute documents outline the results of its testing of a variety of dust samples, including their particle size and concentration required to allow combustion.
Sawdust, for example, is generally only a risk when smaller than 63 microns — the finer the dust, the more reaction surface it has with oxygen — and in a concentration above 30g/ m3. So, let’s say the smoker we mentioned earlier has been working in a 150m3 room, and there’s a 0.5mm layer of dust on the 50m2 floor. That would result in 0.025m3 of dust, and, at a typical density of 600kg/ m3, that equates to 15kg, which, if it became airborne, would produce a dust concentration of 100 g/m3 — creating an obvious danger.
Knowing the properties of your dust is paramount. Three main parameters should be tested; the first being Pmax, or the maximum pressure that can be reached on the basis of particle size. Next is the speed with which the pressure rise occurs, bearing in mind that this will vary according to room or vessel volume. Multiplying that pressure rise by the volume provides the Kst, which enables us to standardize how fast the pressure rises and define four risk categories: from St0 (does not explode) to St3 (very strong explosion). It should be noted, however, that a weaker St1 explosion is no less dangerous than an St3 event.
The final main parameter concerns knowing the minimum required ignition energy, which will enable safer handling. Other parameters include glowing temperature, whether the dust is conductive, and whether self-ignition is possible. All of these factors are very specific to a particular dust generated in a particular process, so seeking professional advice is always recommended.
Once you have determined the combustibility of your dust, you can develop a plan to mitigate the risks in your process. First, although good housekeeping is only a partial solution, audit your process to identify
where nuisance dust is generated, released, or accumulates – and deal with it. These often include intake and mixing locations, bag dumps, welding or cutting stations, beams, and light fixtures. In each location, analyze the production processes, housekeeping practices, dust control measures, and potential ignition sources present.
Bear in mind that when dust builds up in several locations, a flame front can create a pressure wave that leads to a chain reaction, dislodging and feeding on more dust as it moves through the building – as happened during the notorious Imperial Sugar plant explosion that killed 14 people. Also, a supposedly empty vessel is usually more dangerous than a full vessel – so, for example, opening an inspection hatch on a silo may cause lingering deposits on ledges to become airborne and increase risk.
Even the equipment employed to mitigate the problem can be a danger zone, with dust collectors being responsible for 30% of such explosions. Cleaning the filter media or emptying dust bins can also create locally dangerous dust clouds.
Many standards and codes may influence decisions on dust control, including local, state, and European regulations. Knowing the regulations that apply to your facility is critical, and process owners should always research the regulatory requirements in their area.
As of July 2003, there are two directives issued by the European Union that are related to the protection of employees and equipment from risks related to potentially explosive atmospheres 1999/92/EC and 2014/34/EU (ATEX Directives).
ATEX directives make it clear that the responsibility for evaluating the risks and creating an explosion protection document lies with the employer/process owner. Process owners are responsible for the selection of their combustible material management strategy and to assure compliance with all applicable codes and standards.
Having decades-long experience in providing high-quality dust collectors that have become an integral part of many plants’ combustible dust mitigation strategies, Donaldson can help review process owners’ mitigation strategies and provide the optimal dust collection solution for their chosen strategy.
Solids handling equipment maker, Ajax Equipment, has supplied material transfer specialists, Coveya, with two retractable stainless steel triple screw feeders with hoppers for powder handling.
Sitting above the triple screw feeders, the hoppers feature two stage plane flow symmetry to encourage mass flow of the powder. The triple screw feeders aid the flow of powder by providing active extraction from the entire length and width of the hopper’s outlet while delivering a controlled discharge and feed rate. Using a triple screw feeder means the product can be distributed evenly across the width of a belt conveyor handling another bulk product. Mounting the pair of multi-screw feeders and hoppers on rails allows each of the powder handling systems to be withdrawn from the line.
“Ajax worked closely with us to ensure that the
screw feeders were manufactured with our unique application in mind and conducted tests on the material to determine the optimal shape of the screw feeders receiving hopper,” said Winston Herbert, sales executive, Coveya.
Commenting, Lewis Shaw, technical sales engineer at Ajax Equipment, said, “Ajax always recommends material testing in the development of handling and processing solutions as it provides valuable insight into how to work with a material effectively and reliably. Testing of the aggregate powder showed a hopper with two-stage design as well as manufacturing the equipment in stainless steel would help ensure material flow.”
For more information on Ajax Equipment call +44(0)1204 386723, email: sales@ajax.co.uk and visit www.ajax.co.uk.
A new High-Volume Open-Chute Tipper from Flexicon allows discharging of non-dusty, freeflowing and/or agglomerated bulk materials from multiple drums or boxes simultaneously, as well as from Gaylords, totes or bins individually.
The bed of the unit’s hydraulically-tipped housing can accommodate containers from 940 to 1115 mm in height, having an individual or combined footprint of up to 1825 x 2435 mm. Typical applications for multiple containers include simultaneous dumping of four 210L drums, or four boxes, each having a footprint of 915 to 1220 mm.
Pallets weighing up to 2265 kg are forklift-loaded into the three-sided unit and secured, after which a grate is lowered onto the container(s) to prevent shifting. The lifting assembly is raised to a height of 1955 mm and tipped hydraulically, causing material to slide through a smooth, three-sided chute into receiving vessels.
Twin hydraulic cylinders pivot the platform-chute assembly to discharge angles of 45 or 60 degrees beyond horizontal, including a motion-dampening feature at the termination
of container rotation.
Impact-resistant side panels and custom guard panels with a light curtain ensure safe operation.
The tipper is available in heavy-duty, all-stainless construction to sanitary standards (shown) or in carbon steel with durable industrial coatings and stainless steel material contact surfaces.
It is also available with optional receiving hoppers configured with Flexicon mechanical or pneumatic conveyors to transport discharged material to any plant location.
The company also manufacture other configurations of drum/box/container tippers as well as flexible screw conveyors, tubular cable conveyors, pneumatic conveying systems, bulk bag dischargers, bulk bag conditioners, bulk bag fillers, manual dumping stations, weigh batching and blending systems, and engineered plant-wide bulk handling systems with automated controls.
For information contact Flexicon Europe Ltd, +44 (0)1227 374710, sales@flexicon.co.uk, www.flexicon.co.uk
The IVECO Daily has built up a reputation for being among the most capable commercial vehicles on the road, and that mission-focused DNA is present and correct in the new eDaily. In addition to maintaining the core strengths of its combustion siblings, this EV can provide up to 15kW ePTO onboard power capable of running everything from ariel platforms to compactors.
There are many benefits to going electric in addition to the environmental good zero-emissions vehicles can deliver. An up to 50% reduction in maintenance costs, less driver fatigue due to silent running, and more affordable charging thanks to programmable scheduling for off-peak times. However, one of the biggest benefits for operators is that the IVECO eDAILY can function as a mobile power source.
While onboard power of around 2.3kW is good enough to run small power tools, IVECO eDaily’s trio of ePTO options up to 15kW has the power to
run essential equipment for any mission. A 2.5kW setup is ideal for running tail lifts aiding the of loading heavy goods, while the 400v 15kW option can easily operate refrigeration units or even lifesaving equipment found on emergency vehicles. Alternatively, a 15kW mechanical ePTO can power pumps for cranes or heavy-duty lifting equipment. Functioning independently from the traction motor, ePTO can run even when the vehicle is off.
All of this power comes courtesy of IVECO eDaily’s innovative modular batteries. Operators are able to choose from vehicles with one, two, or three batteries to precisely match their mission’s need for range or payload. If the vehicle’s role changes at any point, a visit to an IVECO dealership can see the battery configuration changed within as little as two hours.
Thanks to IVECO eDaily’s artificial intelligence software, the vehicle is able to learn the habits of its role to help preserve the required power its missionspecific equipment demands.
IVECO UK Light Business Line Director, Mike Cutts said “The IVECO eDaily’s 15kW ePTO is a game changer. Operators looking for an electric commercial vehicle that can also power large scale equipment now have a solution. We are proud to lead the class and deliver the functionality customers require.”
In addition to the eDaily’s impressive EV capabilities, it retains all of the standard vehicle’s headline-grabbing strengths inherent in its hardy truck-based chassis. An unrivalled 3.5-tonne towing capability, class-leading turning circle, and impressive up to 4.6-tonne payload make this vehicle the same Daily that operators value, just electric.
When it comes to charging, the IVECO eDAILY features 80kW rapid charging alongside 7kW and an optional 22kW. It’s possible to add 62 miles of range to this eLCV in just 30 minutes. The EV also has the ability to pre-condition the vehicle, something that can maximise changing efficiency and set the cabin to a comfortable temperature ready for your departure. Utilising the eDaily’s companion app not only allows you to check on vital vehicle information, but also schedule charging for when electricity rates are cheaper.
The all-electric IVECO LCV is now on sale and can be ordered from IVECO’s nationwide dealer network.
To discover more about the IVECO eDAILY and its advanced features please visit https://edaily.iveco. com/en/