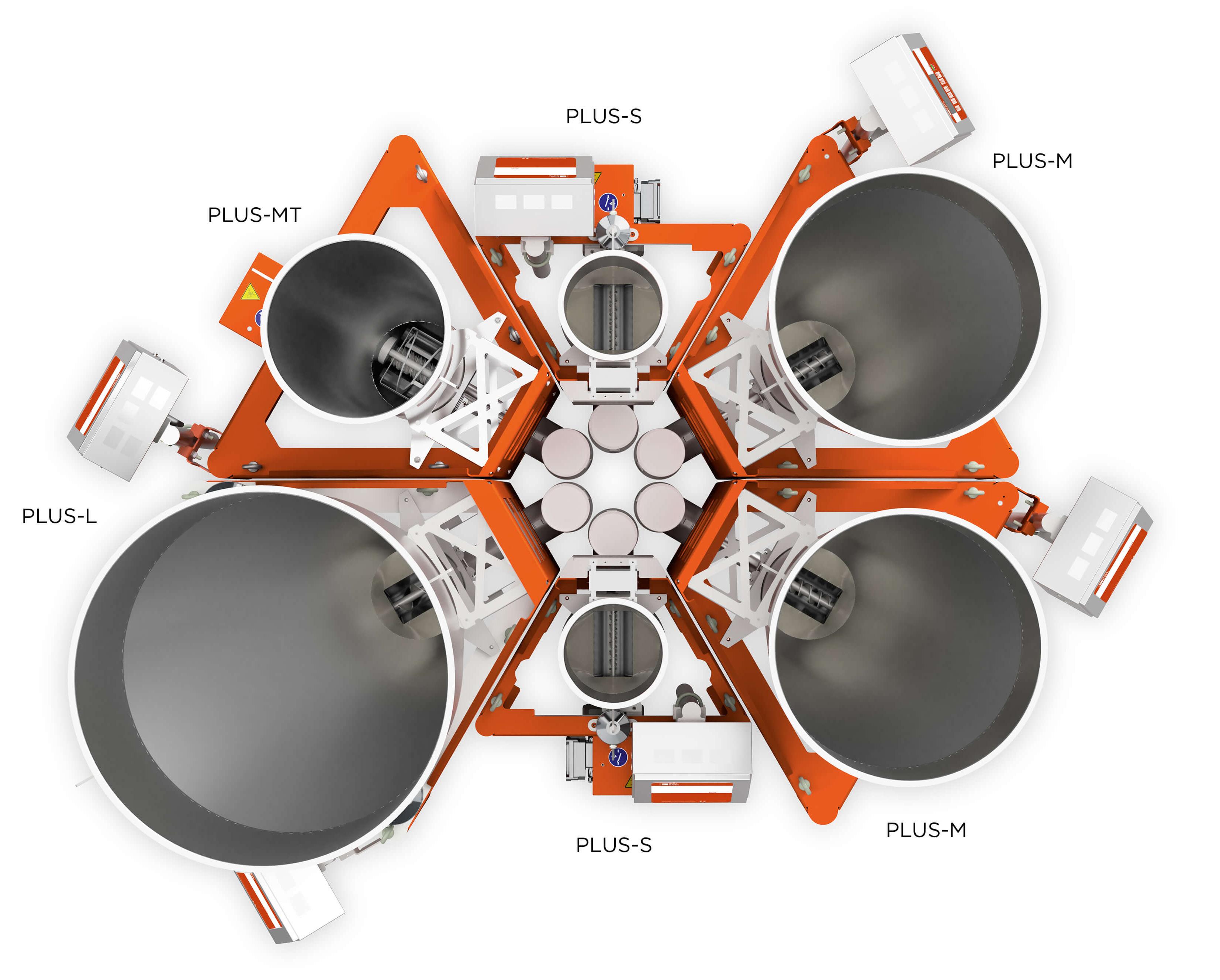
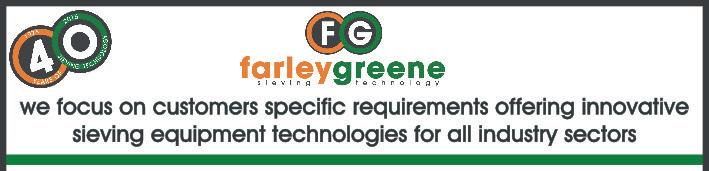

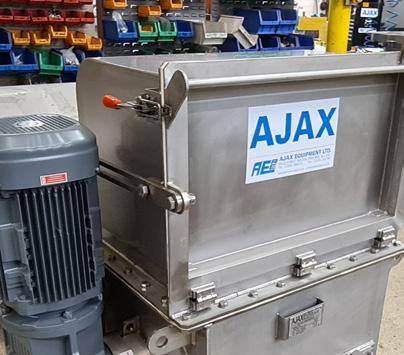
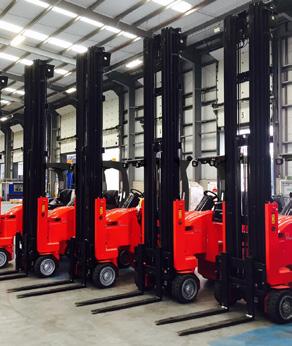
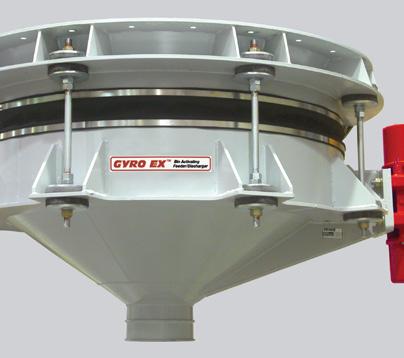
From micron sized powders to large pellets and everying in between, Dynamic Air can move your dry granular materials gently, reliably and with significant reductions in product degradation and/or system wear.
Dynamic Air dense phase pneumatic conveying systems have been proven in over 15,000 installations worldwide. They handle a wide range of materials and bulk densities at rates from less than a hundred kilograms per hour to 400 tonnes per hour, over distances exceeding 1500 metres.
Each Dynamic Air system is custom designed from one of our sixteen different conveying concepts. So you get a conveying solution that fits your process perfectly, without compromises.
Our high material-to-air ratios reduce energy and compressed air requirements. Our low conveying velocities provide significant process savings in both operation and maintenance.
Issue
Sales Director: James Scrivens
Production: Sarah Daviner
Accounts Manager: Avery Hudson
Office Manager: Katie Brehm
BULK SOLIDS TODAY is published 6 times a year by Abbey Publishing Ltd
ADVERTISING & EDITORIAL
Please contact us at:
Tel: 01933 316931
Email: editorial@bulksolidstoday.co.uk advertising@bulksolidstoday. co.uk
Web: www.bulksolidstoday.co.uk
Twitter: www.twitter.com/
BulkSolidsToday
CIRCULATION
To receive a copy free of charge, please send your details to subs@bulksolidstoday.co.uk
No part of this publication may be reproduced by any means without prior permission from the publishers. The publishers do not accept any responsibility for, or necessarily agree with, any views expressed in articles, letters or supplied advertisements.
ISSN: 1365/7119
All
2023 sees Narrow Aisle Ltd, the independently owned British warehouse truck manufacturer, celebrate the 25thanniversary of its successful distribution partnership with Sunbelt Material Handling of the USA.
Sunbelt has played a key role in developing the market for Narrow Aisle’s pioneering range of Flexi articulated very narrow aisle (VNA) lift trucks across North, Central and South America since 1998 and sells to both end users and dealerships.
With physical locations in Dallas, Austin, San Antonio, Oklahoma City and Tulsa, Sunbelt also provide after-sales support services to the USA’s growing number of Flexi articulated VNA forklift users.
Donald Houston, managing director of Narrow Aisle Ltd, commented: “Maintaining healthy and long-lasting relationships with partners is essential to business success and our association with Sunbelt must be one of the most enduring and mutually rewarding transatlantic business partnerships in the global materials handling industry.
“For over a quarter of a century Sunbelt has been instrumental in opening the Americas to the Flexi brand and today the US is one of Narrow Aisle’s most significant export markets. We look forward to continuing to work with our friends
at Sunbelt to grow Flexi sales in the US for the next 25 years and beyond.”
Sunbelt Material Handling’s president, Matt Maddock, said: “With American third party and fulfillment logistics operators increasingly challenged to reduce labour costs and make maximum use of the storage and order picking space areas that they have available, we see plenty of growth potential in the US market for Flexi articulated forklift trucks.”
The Flexi truck’s iconic articulated design delivers safe and highly space and throughput efficient operation within narrow aisle storage units. And, because
Flexi trucks can be used to load and unload delivery vehicles and transport palletised loads directly to and from their pallet location, ‘double handling’ is eliminated and fewer types of forklift are required. As a result, materials handling costs can be reduced by up to 50%.
Manufactured to meet the globally recognised ISO/TPS quality standards using tier one components, well over 15,000 Flexis have been supplied to users in more than 70 different countries worldwide.
www.flexi.co.uk
www.sunbeltmh.com
To subscribe to Bulk Solids Today magazine or for more information, please feel free to visit www.bulksolidstoday.co.uk
Bulk Solids Today is the bi-monthly digital journal covering the storage, processing and handling of materials ranging from fine powders to the heaviest raw materials.
JCB has won one of its biggest orders of the year after a 900-machine deal was signed with national builders’ merchant Jewson.
The order for machines worth more than £12 million is the biggest ever placed by Tool Hire - the rental division of Jewson - in the 20 years since JCB first began supplying the company.
And the special anniversary is being marked in electrifying style – literally – as the new fleet of machines includes 19C-1 E electric mini excavator models and 1TE electric site dumpers. As well as being considerably quieter, the electric models offer zero emissions at the point of use and comparable performance
to diesel counterparts. Each delivers a full day’s typical operation on a single charge.
Steve Fox, JCB Global Major Accounts MD said: “We are delighted to mark 20 years of supplying Jewson Tool Hire with an order of such magnitude, which is testament to the quality of JCB’s compact equipment range. The addition of electrically-powered machines demonstrates that Jewson is looking to the future and the opportunities that zero emissions machines present.”
The order also includes JCB 8008 micro excavators, JCB 16C-1 mini excavators, 1T site dumpers and VMT160-80 vibratory tandem rollers. The
machines will be supplied by JCB dealer Gunn JCB.
Jewson Business Development Director Mark Esling said: “JCB is a key partner, and we are proud to mark such an important anniversary of working together. We are aligned on our core values of supporting the trade and empowering builders, tradespeople, and contractors across all industries with the best products, services and expertise and we look forward to a bright future together.”
Jewson, which is based in Binley, Coventry, entered the micro excavator market in 1995 and first bought JCB machines in 2003 when the company purchased 70 JCB micros.
One SAMSON Eco Hopper type EH60 has been tested successfully and put into operation in China. Thanks to the environmentally friendly design and the installed filter systems it makes an important contribution to the reduction of dust emissions during ship loading and unloading processes.
The internal screen of the chute is constructed so that the dust filter elements are isolated from the main flow of material, and the filter operation is optimised. The design follows sustainability principles. It reduces the air flow to a minimum so that the filter surface and electricity consumption can also be lowered. Close to the hood there is a system for the reduction of the turbulence, which is often caused by side winds. The hopper is reinforced which in turn gives optimised stability to the entire unit.
Eco Hoppers from SAMSON Materials Handling are suitable for operation in ports and terminals to handle bulk materials with almost any characteristics and flow properties. Mr. Gang Gong, the managing director of AUMUND China says: “The customer is very satisfied with the Eco Hopper unit and is interested in taking our working relationship to the next level.”
Approximately 13 million of tonnes of goods pass through the inland river port each year at Dagang Port of Zhen Jiang, where the Yangtze and the Grand Canal meet, creating a major shipping hub in China.
Unlike other valves that seal with friction, Posi-flate’s unique butterfly valve uses an inflatable seat to seal with air pressure. Thus it requires less torque and a smaller actuator, resulting in lower cost. Plus, the seat automatically compensates for wear, providing longer life. Some users have reported over six million cycles and the valves are still going strong.
• Less friction
• Low torque
• Low maintenance
• Lower actuator costs
• Longer valve life
• More reliable
Bosch Rexroth, one of the world’s leading suppliers of drive and control technologies, has won the 2023 Hermes Award for its Smart Flex Effector at the Hannover Messe held in Germany in April. The Hermes Award is considered one of the most important technology prizes worldwide. The Hanover Messe is the world’s premier trade fair for industry, providing a central platform for innovation, networking and orientation in the age of industrial transformation.
The company’s second Hermes award follows its win at the Hanover Messe 2021 for the SVA R2, the world’s most compact electrical Subsea Valve Actuator, which helps to significantly reduce CO2 emissions from process systems and minimises environmental risks. Developed by Bosch Research, the Smart Flex Effector compensation module, on the other hand, gives industrial robots a sense of touch similar to that of the human hand.
Flex Effector:
The Smart Flex Effector is a cutting-edge module designed to enhance precision and expand the possibilities of industrial robots and Cartesian systems. With its active measurement function in six degrees of freedom, this intelligent compensation module serves as a valuable tool in various applications.
By incorporating highresolution position sensors, the Smart Flex Effector allows for the detection of position deviations in the tool. These deviations are then actively corrected by the manipulator through precise movements. Real-time readjustment is made possible by
the advanced sensor technology embedded in the compensation element. Furthermore, the measured values obtained from the module offer insights into process quality, enabling quality monitoring and data logging. This innovative compensation module finds wide application in automation technology and robotics, particularly in handling and joining processes that require strict tolerances. Whether it’s for achieving precise joinings, documenting quality and recording tool points, or automatically compensating for position drifts in the rotary axes, as well as in the X, Y, and Z directions, the Smart Flex Effector proves to be an indispensable solution.
According to Professor Reimund Neugebauer, President of the Fraunhofer Society and Chairperson of the Hermes Award, the Smart Flex Effector is expected to play a key role in solving pressing economic, societal, and demographic challenges: from optimising industrial assembly to increasing productivity in agriculture to supporting medical and nursing staff in the form of assistance robots. “The Smart Flex Effector is driving efficiency and diversity in the uses of robots, creating quantifiable value for industry, the environment and society,”
said Professor Neugebauer in a congratulatory message to Bosch Rexroth.
“This award makes us incredibly proud. Both Bosch Rexroth and Bosch Research teams have put a lot of heart and soul into the development of the intelligent end effector, so the award is more than deserved!” noted the teams’ representatives at the Hanover Messe.
Bosch Rexroth, through Bosch Rexroth Africa, offers its clients in Africa access to the latest technologies, innovations, and technical support from Germany. Leveraging the well-established local knowledge, expertise, and end-user relationships of the Bosch Rexroth Africa Group, the company aims to achieve strategic growth throughout Africa.
If you would like to subscribe to receive a regular copy of the digital edition of Bulk Solids Today magazine, you can subscribe on our website - www.bulksolidstoday.co.uk
If you are interested in advertising within Bulk Solids Today magazine or supplying editorial content, please feel free to get in touch using the details on our website or below.
Bulk Solids Today is sent to our digital readership of over 9,000 Chief Engineers, Operations Managers and Technical Managers from within sectors including Chemicals, Food & Drink, Mining, Quarrying, Transport/Distribution, Recycling & Waste Management and more.
www.bulksolidstoday.co.uk
Flowcrete, a brand of CPG UK, are pleased to announce a new addition to our screed range, Isocrete Ultimate K-Screed. Used in conjunction with approved sand and cement for semi dry cementitious screeds, Isocrete Ultimate K-Screed is a liquid additive suitable for most commercial applications.
Flowcrete’s award-winning Isocrete Floor Screeds range has been a market leader in the UK since 1969 and is still going strong so we are excited to share that our range is expanding with our latest addition Isocrete Ultimate K-Screed.
Offering compelling speed of application benefits, less waste and exceptional strength, Isocrete Ultimate K-Screed is applied through Flowcrete’s licensed contractor network.
Isocrete Ultimate K-Screed, which can be pumped and subsequently dosed, delivers a screed that can be trafficked or overlaid quickly due to the reduced water content within the mix. This gives the benefit of rapid drying and rapid strength gain enabling less down time than traditional methods as well as assisting with the work schedule. It can also be incorporated in underfloor heating with a thickness as low as 50mm and has a high compressive strength meaning it can withstand load and construction traffic.
Stuart Smith, Construction Products Group (CPG) UK & Ireland’s sales manager for flooring said: “Isocrete Ultimate K-Screed dosages can be amended to suit specific applications depending on floor finish and strength requirements. A sand testing and compressive strength service is
offered to ensure that the required criteria is achieved.
“This unique formulation allows the system to be trafficked in as little as 24 hours, has a 3-day drying time, and a compressive strength of >40N/mm in comparison to the rest of our range.
“At Flowcrete, we are dedicated to maintaining the utmost quality for our flooring products. That’s why we are constantly seeking ways to enhance our offerings and expand our portfolio.
“Our latest addition is a testament to our commitment to continuous improvement and it is evident at every stage of the process, from specification, individual project assessments, and expert guidance on the best subfloor solutions. This unwavering dedication extends seamlessly to the installation phase, facilitated by our experienced network of skilled contractors whose expertise, combined with our built-in total quality control measures, guarantees exceptional results.
“But our dedication doesn’t end there. We take pride in offering a remarkable 10-year warranty after installation, a
testament to the unwavering trust we have in Isocrete Ultimate K-Screed and our unmatched services.”
Flowcrete is one of Construction Product Group (CPG) UK’s portfolio of leading construction product brands, which also includes illbruck, Tremco, Dryvit, Nudura and Nullifire.
These high-performance building materials - including roofing and waterproofing solutions, as well as sealing, bonding, insulation, fire protection systems and modern methods of construction – together provide one point of call for specifiers and contractors.
As well as exceptional products, as a CPG company, Flowcrete customers also have access to enhanced resources, including technical support from industry experts.
Full training, including CPDs, application training (both practical and theory) and on-site support such as surveys, complete the service package.
If you have any questions regarding Isocrete Ultimate K-Screed additive or any other flooring query, please get in touch with us, we will be happy to help.
If you would like to subscribe to receive a regular copy of the digital edition of Bulk Solids Today magazine, you can subscribe on our websitewww.bulksolidstoday.co.uk
If you are interested in advertising within Bulk Solids Today magazine or supplying editorial content, please feel free to get in touch using the details on our website or below.
Bulk Solids Today is sent to our digital readership of over 9,000 Chief Engineers, Operations Managers and Technical Managers from within sectors including Chemicals, Food & Drink, Mining, Quarrying, Transport/ Distribution, Recycling & Waste Management and more.
www.bulksolidstoday.co.uk
bst@abbeypublishing.co.uk
Tuf-Lok ring grip pipe and tube couplings are rugged, heavy duty, self-aligning and self-grounded couplings with a high end pull. They can be used for almost any application where pipe or tube ends need to be connected. The Tuf-Lok self-aligning couplings install quickly and easily with little effort. Features
• Self-aligning
• Self-grounding
• High pressure rated
• Full vacuum rated
• Stainless or mild steel
• Usable on thin or thick wall pipe or tube
• Low cost
• Reusable
• Absorbs vibration
• Externally leakproof
Charles Jackson & Co, an agricultural cereal grain company, has rolled-out Inseego’s AIpowered fleet dashcam solution to its specialist haulage operation to target safety and insurance improvements. This latest development followed the successful adoption of the AI cameras on plant equipment used to transport and load grain and animal feed at the company’s storage, cleaning and drying facilities in Buckby, Northamptonshire.
“We have been hugely impressed with quality and accessibility of video footage, which has already provided us with added insight into our onsite plant equipment,” explained Martyn Moylan, Training & Safety Manager at Charles Jackson & Co Ltd. “Since the initial installation of the AI cameras last year, we have experienced a clear reduction in speeding and driver distraction events, so it made complete sense to extend the solution to our haulage fleet. The ability to prevent incidents from happening in the first place, by proactively alerting the driver to their behaviour, has been particularly useful.”
Charles Jackson & Co’s haulage service provides deliveries and collection nationwide –from farm or store, to mill or port – operating a
fleet of HGVs and a mix of tipper, curtain-side and bulk blowing trailers. With vehicles operating night and day, often using higher-risk rural roads, the company needed an advanced camera solution that safeguards its drivers and other road users.
“The combination of live tracking, incident alerting and driver status monitoring will help us encourage responsible driving and reduce collisions. If an incident does occur, we will be able to quickly respond to ensure driver welfare and manage the insurance claims process, as well as using video and supporting data to undertake an effective investigation. Individual or anonymised footage will also support our targeted driver feedback and training strategy,” adds Moylan.
Steve Thomas, Managing Director of Inseego UK Ltd commented: “Our comprehensive fleet and video telematics offering means we can work closely with our customers to develop technology solutions that meet their precise operational requirements. We are seeing a growing demand from vehicle and plant operators as they recognise the proven safety, insurance and efficiency improvements that can be made.”
Solids handling specialist, Ajax Equipment, has supplied leading speciality chemical producer with a lump breaker and block tip chute. The stainless steel lump breaker will reduce large frozen blocks of an enzyme to the size required for a chemical process.
Commenting, Eddie McGee, managing director, Ajax Equipment said, “Lump Breakers offer an efficient, adaptable and easy to operate way to reduce the particle size of a wide range of materials across many industries. Size reduction can be achieved through four mechanisms: dynamic impact, shearing/cutting and crushing. To develop the lump breaker’s design, Ajax conducted a range of material tests which would determine which of the mechanisms would best suit the needs
of the enzyme blocks and water treatment process. Crucially the tests were carried out with frozen blocks of the material the site handled.”
Efficient Size Reduction
To achieve effective size reduction of the frozen enzyme blocks, Ajax Equipment’s lump breaker uses a combination of ‘dynamic impact’ and wedging mechanisms. The rotor’s profile was specially designed to apply the force needed to initiate a failure crack through the material. The material is then crushed against the lump breaker’s walls and through the grille.
For more information on Ajax’s equipment call +44(0)1204 386723, email: sales@ajax.co.uk and visit www.ajax.co.uk.
An impressive fleet of machines from DEVELON (formerly known as Doosan Construction Equipment) has been at work for about a year in recovery work on the long-abandoned area of the former Innocenti factory in the Rubattino district, on the outskirts of Milan in Italy. This part of the Lambrate region has previously experienced depopulation and the closure of manufacturing sites.
It is a 400,000 m2 construction site, one of the most important in the city, where various DEVELON machines are carrying out the demolition of the yards, targetted reclamation, screening and recovery of materials.
Five DEVELON excavators including DX350LC-7, DX340LC-7, DX300LC-7 and DX245NHD-7 models equipped with grapples, hammers and crushers are dedicated to the demolition of floors, crushing the reinforced concrete to be able to separate out the rebar. The rubble produced is then moved for screening on site by two Doosan DL380-
7 wheel loaders and a Doosan DA30 articulated dump truck (ADT).
Once the demolition has been completed, which Is scheduled for July 2023, part of the 70,000 m3 of screened material will be used as raw material to build the base on which an imposing logistics centre will be built which will occupy a large part of the area. Excess material will be sent to authorized external facilities.
All of the site’s activities are managed by Turinbased Unica Spa company, one of the leading Italian groups in the sector of reclamation, recovery and development of the urban and industrial areas of decommissioned industries.
With its integration of skills, Unica Spa is able to operate with four industrial divisions - reclamation, demolition, construction and projects/investments - having all the necessary personnel and means all available in-house. Unica Spa currently has a permanent staff of over 100 employees. In 2022, more than 100 contracts were completed and over
110,000 tonne of waste was disposed of or sent for recovery, with the company’s constant commitment to environmental sustainability, ranking it among the top five national companies in the sector.
Unica Spa not only manages impressive construction sites in the Milan area, the company has been active on important work in Cortina for the demolition of the old ice bobsled track aimed at the construction of the new Olympic track.
For all of these activities, Unica Spa has chosen to rely on Develon machinery.
Paolo Andreini, President of Unica SpA, states: “For three years we have been using Develon machines with which we are fully satisfied both in economic terms but above all in terms of meeting our needs, thanks to their undisputed quality. Our Develon fleet consists of over 30 machines, all of which we own, including excavators of all sizes, loaders and dump trucks.
“We are a well-capitalised company able to directly support investments to deal with the important orders that we continue to acquire. This policy is giving us important results and this is possible thanks to excellent partners such as Develon and the dealer, DMO, in the figure of Gianmaria Lupis, whom I know I can count on for every need.”
Gianmaria Lupis, DMO commercial manager for Lombardy, adds: “The fully trusted commercial relationship between Unica Spa and DMO is continuing to translate into important equipment orders. In just three years, DMO has supplied
a complete fleet of machines, from the 8 tonne DX85 mini-excavator to the DX140LC-7 to several DX245NHD-7, to the Demolition machines, as well as several DX300LC-7, DX340LC-7, DX350LC-7 and DX380LC-7 excavators, DL300-7 and DL3807 wheel loaders and two DA30 dump trucks.
“All the numerous accessories and attachments we have are also strictly Develon. The excellent relationship with the president Paolo Andreini is also due to the fact that he knows he can count on the complementary services that DMO guarantees, such as fast rental for emergencies and the continuous specialized assistance service directly on site, essential considering the number of Develon machines constantly at work.”
For more on DEVELON, please visit the website: https://eu.develon-ce.com/en/
Develon, formerly known as Doosan Construction Equipment, has underscored its very successful debut at the Plantworx Exhibition by winning the Best Live Demonstration Award from the organisers, recognizing the best overall use of outdoor space and best stand set up. The Best Live Demonstration Award is one of the onsite awards for those exhibitors at Plantworx who made a big impact on the onsite judges who assessed companies’ stands and demonstration areas. The awards were presented at the Exhibitor’s Reception on the first evening of the show.
The Best Live Demonstration Award category was judged by Nick Drew (Earthmovers) and Peter Haddock (Content with Media) – who were unanimous that this prize should go to Develon. Their statement about the Develon stand read as follows: “There was a lot of thought and preparation that went into this stand – it really had the wow factor. The stand and the demo area have a really nice feel and flow and the whole stand was not just a ‘Tent in a field’ but a truly impressive stand.”
Kevin Lynch, Marketing Communications Managerfor Develon, said: “We are delighted to win The Best Live Demonstration Award, especially with the transition we are making with the Develon brand and making its first appearance at Plantworx. The excellent Demo show on the stand carried out by our operators, Nigel Horton and Alex Humpage, brings across the high performance, innovation, versatility and durability of Develon equipment in an exciting and very watchable way.”
The Demonstration area on the Develon stand at Plantworx features the new DX250WMH-7 material handler being launched at the show. Joining the DX250WMH-7 in the Demonstration area is the Develon DL80-7 compact wheel loader, the DX55R-7 5.7 tonne mini-excavator, the DX225LC-7 23 tonne crawler excavator and the DL420CVT-7 wheel loader.
The DX250WMH-7 is one of several products on display being seen for the first time in the UK. They include the new DX63-7 6 tonne mini-excavator and the new 14.6 tonne DX140LC-7K crawler excavator in the Static section of the stand.
Together with the DX62R-7, the DX63-7 is one of two new 6 tonne mini-excavators from Develon, completing the roll out of the next generation of machines from the company, with a new shared global styling design. Both models are powered by the D24 Stage V compliant diesel engine providing 44.3 kW (59.4 HP) of power. Despite offering an 8% increased torque of 26.5 kgm/rpm, the D24 engine still provides a 7% decrease in engine fuel consumption. Like all of Develon’s new generation mini-excavators, the DX63-7 is designed to offer maximum performance, optimum stability, increased versatility, enhanced operator comfort, controllability, durability, ease of maintenance and serviceability.
The new DX140LC-7K 14.6 tonne crawler excavator, replaces the company’s successful DX140LC-7 model.
Whilst the performance and working range are the same as the DX140LC-7, the new machine incorporates many improvements that enhance safety and convenience both for the operator and for working on site, together with a better operator experience, particularly from a maintenance point of view.
The upgraded serviceability of the DX140LC-7K includes better access to the DEF tank and the fuel refilling hose. This is combined with a much easier approach for the operator to the engine compartment via new anti-slip steps and handrails positioned behind the cab. The DX140LC-7K also has a new flattened engine cover design that has reduced the maximum height of cover components on the back
of the machine from 1285.5 mm and 1320 mm down to a uniform 1070 mm across all of the back of the machine. This now offers much better visibility for the operator both to the rear and to the right hand side of the machine.
Joining the DX63-7 and DX140LC-7K in the Static area of the Develon stand is the DX27Z-7 and DX85R-7 mini-excavators, the DX100W-7 wheeled excavator, the DL80TL-7 compact wheel loader and the DL280-7 wheel loader.
Equipped with an MG22 Sorting Grapple, the new DX250WMH-7 25 tonne Stage V compliant material handler is being demonstrated by Develon for the first time in the UK, for use in the solid waste, recycling, demolition and forestry industries. Designed to carry out the toughest tasks, the DX250WMH-7 is built with front and rear stabilizers, and a boom and arm specifically designed for material handling tasks. A standard feature is the hydraulic cab riser, which gives the operator better all-around visibility of the attachment and work area.
The DX250WMH-7 material handler is easy to operate with ergonomic joysticks and a steering wheel. The machine comes equipped with two-way auxiliary and rotate circuit hydraulics to improve efficiency. The operator can use buttons on the joysticks or an optional foot pedal to control auxiliary attachments. The new DX250WMH-7 material handler is powered by the 6-cylinder, turbocharged Develon DL06V water-cooled diesel engine, providing an output (SAE J1995) of 141 kW (189 HP) at 1900 RPM.
Coperion K-Tron announces the expansion of the original ProRate™ PLUS feeder portfolio with more solutions for feeding powders. A ProRate PLUS-MT twin screw feeder will be added to the product line that will be available end of April 2023. Together with the recently introduced ProFlow™ bulk solids activator the new twin screw feeder is an efficient solution for feeding powder additives in plastics applications. Last year Coperion K-Tron developed a completely new feeder line built on 100 years of feeding experience to provide a robust and reliable feeder for simple feeding applications in the plastics industry. The ProRate PLUS continuous gravimetric feeder line is an economical solution and offers a quick return on investment due to its good priceperformance ratio and fast delivery times. The original product line featured three single screw feeders that are ideal for the feeding of pellets, granules and other free-flowing bulk materials in secondary plastics applications.
For more difficult to handle materials Coperion K-Tron is expanding the ProRate PLUS product line with a new twin screw feeder, the PLUS-MT. This
gravimetric feeder with its horizontal agitator ensures that the two screws are always optimally filled with material. The twin screw technology also has the advantage of reducing pulsations and the screws have a self-cleaning effect. Twin screw feeders are ideal for difficult to handle powder additives such as talc, calcium carbonate or carbon black. The steep design of the hopper walls allows poorly flowing bulk solids to be fed reliably without an additional vertical agitator. Should material bridging or ratholes still occur, one or more ProFlow bulk solids activators can be mounted on the hopper to promote material flow.
The new ProRate PLUS-MT twin screw feeder can handle throughputs from 40 up to 1800 dm3/h [1.4 to 63.6 ft3/h], depending on bulk material characteristics. With individual bulk solids tests in our test centers, we can determine more precisely what the exact feeding range is for a specific bulk material.
Together with the new ProFlow™ solution, the scope of the original ProRate PLUS single screw feeders has been expanded to include moderate
flowing powders and flakes. The solution is available for all four models (PLUS-S, PLUS-M, PLUS-L, PLUS-MT) and can be installed on new equipment or as a “mounting kit” on existing feeders.
The ProFlow bulk solid activator consists of an electromagnetic vibrating device, which activates the feed hopper to keep bulk materials moving. The device operates at an optimized frequency and amplitude to ensure minimal energy consumption and maximum product flow. Thanks to its smart electronic control, ProFlow only uses 3.6 Watts of electricity. Tests with a wide range of bulk materials have shown that ProFlow is an ideal solution for a variety of bulk materials. ProFlow has no wear parts and since it is mounted outside of the product contact area, there is no additional cleaning effort needed.
For the smaller PLUS-S model, the ProFlow activator is implemented in conjunction with specially developed overflight screws. Overflight screws have wings that help move the bulk material into the throat of the feeder and positively promote improved screw fill.
The ProRate PLUS feeder line features a spacesaving trapezoidal shape which allows up to six feeders to be easily grouped around an extruder inlet within a 1.5 meter [5 ft] radius. The four feeder models PLUS-S, PLUS-M, PLUS-L and PLUS-MT cover a wide range of throughputs. The ProRate PLUS feeders are capable of handling feed rates from 3.3 up to 4800 dm3/h [0.12 up to 400 ft3/h], depending on the material. Theoretically, a feeding system with six ProRate PLUS-L feeders can feed up to 28.8 m3/h [1017 ft3/h] on a footprint of only 7 m2 [75 ft2].
ProRate feeders are highly standardized and include a variety of design features to optimize performance and ease of use. Simple access for cleaning and maintenance, even within a cluster, is provided thanks to a patent-pending rail system called “ProClean™ Rail”. ProClean Rail makes it possible to retract the base unit toward the rear of the feeder and rotate it for access to the feeding section and screw element while keeping the feeder in position. In addition, the bellows and screws use the latest magnet technology for simple but robust mounting. The magnet connections allow these parts to be released without tools while at the same time providing the required holding force for optimal and safe operation.
Thanks to the high level of standardization of the feeders, the number of spare parts required for an emergency stock is minimal. Many parts are
identical for all three models and can be used as exchange parts for all devices.
All ProRate PLUS feeders are equipped with P-SFT load cells, featuring reliable Smart Force Transducer single wire weighing technology. Each feeder also comes equipped with its own prewired and pre-tested ProRate PLUS PCM control module. The PCM is mounted to the feeder stand, with adjustable height positioning. Most feeders only need a basic motor control unit (PCM-MD) while one feeder per group of eight is equipped with an advanced version featuring an integrated user interface and line control functionality (PCM-KD).
ProRate PLUS feeders and the ProFlow bulk solids activator are suitable for use in hazardous locations rated NEC Class II, Div. 2, Group F & G and ATEX 3D/3D (outside/inside).
Preconfigured pneumatic refill solutions are available for each feeder size. Each feeder can be outfitted with either a filterless vacuum receiver for pellet applications or a vacuum receiver with a cartridge filter for applications where there may be dust that must be kept out of the air only line of the vacuum conveying system. Refill solutions include a compact support stand, level indicators, butterfly valves and electrical terminal boxes as well as one or more vacuum blowers as needed. The Series 4 MPC controller is ideal for up to 24 vacuum receivers on one blower with one back-up blower.
The GYRO EX bin activating feeder and discharger produces a controlled gyratory motion to positively withdraw granular materials from bins, storage silos and hoppers at any desired feed rate for a more consistent and reliable discharge.
At the heart of the GYRO EX bin activating feeder and discharger is the drive that produces a radial force creating a uniform circular motion on both the upper activation cone and the lower discharge cone. It is this annular radial vibratory motion which imparts the force to the material, assuring a more reliable and predictable material discharge.
A unique feature of the GYRO EX bin activating feeder and discharger is that the stored material load is completely supported by the upper bin activation cone which has a lower cone angle than the discharge cone, assuring an uninterrupted and positive discharge of the stored material.
The GYRO EX bin activating feeder and discharger can also be started and stopped as desired because material is not allowed to accumulate or stagnate in the lower discharge cone which might create packing or plugging problems. Irrespective of the particle size, the GYRO EX bin activating feeder and discharger is well suited for almost any size material and the rate can easily be increased or decreased by adjusting the gap between the inlet opening and the upper activation cone.
https://www.dynamicair.com/products/ vibratory/gyroex.html
Dynamic Air Ltd.
Milton Keynes, United Kingdom
Phone: 44 1908 622344
E-mail: sales@dynamicair.co.uk
www.dynamicair.com
To subscribe to Bulk Solids Today magazine or for more information, please feel free to visit www.bulksolidstoday.co.uk
An old machine in Gorazdze in Poland had been in operation for many decades, and was to be replaced by a SCHADE Cantilever Reclaimer with the conveying capacity doubled to 400 tonnes per hour, and an associated Belt Conveyor. SCHADE was responsible for the engineering, design, fabrication and supply. With the support of AUMUND Group Field Service the installation was supervised and the machines were commissioned within an extremely tight timeframe.
The order presented a challenge on several levels. The equipment had to be integrated into the existing infrastructure and adapted to the design of the building, which had been constructed in the 1970s. In the very compact hall FGD gypsum and limestone are stored on two stockpiles. The materials are conveyed from here to the onward process of the cement plant. Due to the low ceiling
height of the building, the assembly of the new equipment had to be carried out while the plant continued to operate normally. Jochen Delank, Project Manager at SCHADE Lagertechnik says, “The SCHADE equipment needs to move safely despite table edges and foundation slabs that had shifted during the long period of operation. The design of the Cantilever Reclaimer, with a total weight of approx. 90 tonnes, consequently had to be adapted to the ground conditions.”
Operation was to be interrupted for as short a period as possible. After assembly of the new equipment the installation team only had 10 days to dismantle the old machine and to switch operation over to the new equipment. After the final connection stages of commissioning, the Cantilever Reclaimer and Belt Conveyor were handed over by SCHADE on time.
www.aumund.com
When looking for an engineering company, it is often not so easy to find a suitable company to supply you with a complete new production line or equipment. You want an experienced partner who has excellent process engineering knowledge, designs new innovative solutions and is prepared to take care of financial details and schedule. Each member of a project team at Gericke specialises in different areas and has unique qualities in the development, management and realisation of a project.
The following example illustrates the added value that an experienced engineering team can achieve: A client needs to replace a silo in an existing plant due to contamination risks, improve safety facilities and increase production capacity at the same time.
Gericke’s project teams combine different disciplines so that planning can be comprehensive. In addition to project management, it includes process engineering design, mechanical and
electrical design, aspects of occupational safety and explosion protection, documentation, spare parts concept, installation supervision and commissioning.
These tasks require a lot of prior knowledge and practical experience in order to meet the customer’s requirements within the desired time frame.
What are the most important points that contributed to a successful result?
High-precision measurements on site, especially when expanding an existing plant.
This project required the replacement of two silos, each with a capacity of 90 m3, the expansion of the transport equipment from one to two transport screws per silo and the installation of stainless steel piping. All components had to be accommodated in the existing footprint and connected to the existing equipment.
Gericke’s mechanical and process engineers provided detailed 3D drawings and product specifications to ensure everything was accurately prepared for installation.
To reduce installation time, Gericke uses semiassembled plant components. They are built in halls next to the installation site. This is more cost effective for the customer as it results in less downtime on site.
Gericke engineers take care of all transport, external installation personnel, construction and safety requirements - all in cooperation with the customer to ensure that internal guidelines are met.
With 3D scanning and design software, Gericke can use images from the existing space and incorporate the new technology.
Other aspects were integrated into the solution:
- Because the product is highly flammable, spark detection and a shut-off valve were incorporated into the system.
- The previous system required manual intervention to discharge the product from the silos. Gericke has automated this with diverter valves so that manual work is no longer required.
- An important technical task was to reduce the source of contamination.
- Flexible piping was removed due to hygiene
requirements and replaced with stainless steel pipes.
- Detailed documentation and certificates were provided.
- In-house training was provided to staff to show them how to safely maintain the equipment and what spare parts to have on hand to avoid downtime.
National Pile Croppers has always been proud of the continuous R&D that goes in to making its hydraulic pile croppers more efficient, safer, customer focused and productive. The latest development of this non-stop development programme is the new version of the company’s Quad XXL cropper which is proving to be an essential tool on HS2.
As the leading supplier of hydraulic pile croppers across the world, National Pile Croppers (NPC) array has been in demand on large multi-site infrastructure projects for some time. The croppers have now found a particular niche on HS2 where a variety of contractors and civil engineering companies have used the UK manufactured and supported croppers to great success. As with any NPC product however, there is constant vigilance of where refinements can be made, with the needs of HS2 in particular leading to the revision of members of the NPC armoury.
With a project as big and as demanding as HS2, there has arisen a requirement for even larger more powerful pile croppers. “As we always work closely with our customers to ensure that they are getting the very best in hydraulic pile cropping, we soon identified a need for an even larger cropper,” says NPC director Lee Aston. This has led directly to the development of the new Quad XXL.
“We have a well-proven and existing range of Quad croppers that cover virtually any requirement, with our Quad XL 1000 cropper for one being designed to be used for the reduction of augured (round) piles up to 1050mm in diameter. As with the entire Quad range, it utilises four powerful and fully synchronised rams with specially designed blades to give a superb pile cut. The cropper will also hold the cut pile section safely for removal to a designated safe area. Best utilised on piles with ‘de-bonded’ reinforcement bars, it has proved to be the ideal solution when reducing contiguous and secant piled walls with spacing as close as 150mm. However, on some parts of HS2, the
Quad XL although effective, needed to be supersized to make it even more productive,” adds Lee.
The new Quad XXL is a true cropping behemoth being designed and developed to deal with piles of between 900 and 1200m in size. Weighing in at a mighty 3,675kg, it is best used on an excavator of at least 31t in weight. “Although big, the new Quad XXL is still easy to use, and our experienced support staff are at hand from the initial order to the
installation on site to make sure that customers get what they pay for. Operation is still simple, with the cropper being lowered to the ideal height, with the jaws then being closed until pile sections ‘pop’ free. The broken pile section then can be easily removed for recycling to a dumper or a specified area.
“The feedback we’ve received has been beyond our expectations. Our customers seem to want more and more of the Quad XXL as the targets and deadlines shorten on HS2. Despite its size and power, the new Quad XXL is as efficient as the other members of the Quad range, delivering an effective solution wherever it has been used,” conclude Lee Aston.
The new Quad XXL from National Pile Croppers is now available for hire or purchase throughout the UK and will be introduced globally in the coming months.
New Quad XXL technical specifications
• Pile Size: 900-1200 mm
• Weight: 3675 Kg
• Length: 2363 mm
• Width: 2363 mm
• Height: 2363 mm
• Excavator min size: 30 tonnes
• Max operating pressure: 275 bar
• Flow rate: 90-180 L/min
www.nationalpilecroppers.com
TheBella dryer/cooler
offers thermal efficiencies to 80 percent or better because air flows around material while it is suspended in the weightless zone. The result is a more consistent material.