
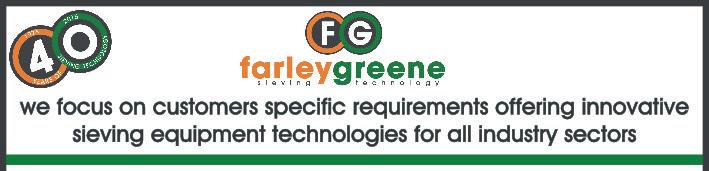
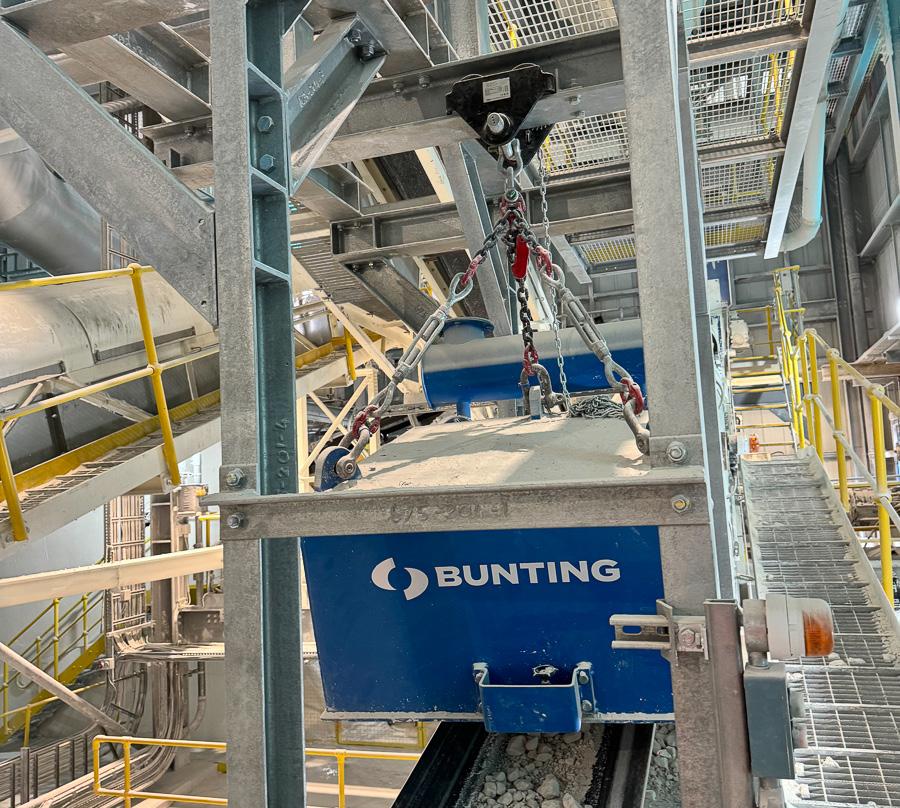
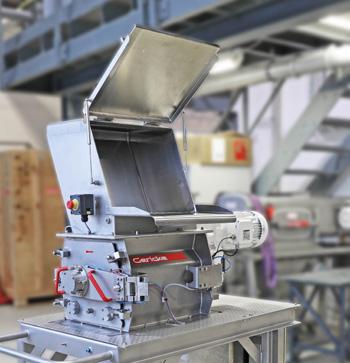

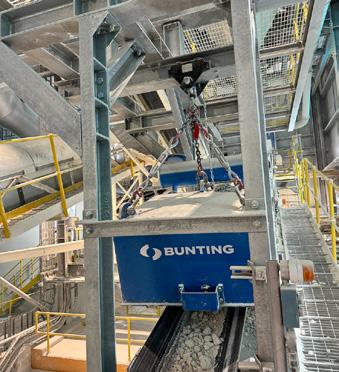

We are a leading provider of custom solutions for the handling of bulk materials for processing businesses across various industries. Dynamic Air has over five decades of expertise in designing and manufacturing pneumatic conveying systems and equipment for handling dry bulk solids.
At Dynamic Air, we set the standard for excellence in bulk solids handling. With a relentless focus on quality, reliability, and customer satisfaction, we deliver reliable, high-quality pneumatic conveying systems, equipment, and custom solutions that exceed expectations. BULKBUSTERTM
We never take a cookie-cutter approach just to cut costs up front; we know that the right solution will save you money in the many years to come. Our tailored solutions involve thoughtful planning, meticulous engineering and precise manufacturing that optimize efficiency and productivity.
Sales Director: James Scrivens
Production: Sarah Daviner
Accounts Manager: Avery Hudson
Office Manager: Katie Brehm
BULK SOLIDS TODAY is published 6 times a year by Abbey Publishing Ltd
ADVERTISING & EDITORIAL
Please contact us at:
Tel: 01933 316931
Email: editorial@bulksolidstoday.co.uk advertising@bulksolidstoday. co.uk
Web: www.bulksolidstoday.co.uk
Twitter: www.twitter.com/ BulkSolidsToday
CIRCULATION
To receive a copy free of charge, please send your details to subs@bulksolidstoday.co.uk
No part of this publication may be reproduced by any means without prior permission from the publishers. The publishers do not accept any responsibility for, or necessarily agree with, any views expressed in articles, letters or supplied advertisements.
ISSN: 1365/7119
Danfoss Power Solutions today announced the launch of its PLUS+1® Autonomous Control Library (ACL) 3.2 software for off-highway machinery.
PLUS+1 ACL 3.2 consists of new and updated blocks that enhance machine self-guidance capabilities through improved obstacle and hazard detection and environmental landmark identification.
Danfoss PLUS+1 ACL software comprises preprogrammed and pretested software blocks covering areas such as perception, positioning, and navigation. The software enables users to add autonomous functionality to mobile machinery by integrating the blocks into their machine software applications, eliminating the need to develop software from scratch. Designed
for in-house engineering teams at original equipment manufacturers and distributors, PLUS+1 ACL software reduces development time and costs.
PLUS+1 ACL 3.2 includes the following new and updated software blocks:
• Post Detect improves localization by identifying and using rectangular posts around the machine as landmarks, both indoors and outdoors.
• Reflector Detect identifies reflectors in the machine’s surroundings, which can be used to define the machine’s path or improve its location within the environment.
• Projected Path Area creates zones in the machine’s immediate trajectory to better detect obstacles when the machine is turning.
• Obstacle Detect Area enables defined zones to be created around the machine, which can be used to stop or adjust machine motion when an obstacle is detected within these zones.
• Lidar Filter improves performance in foggy and dusty conditions by reducing noise from the incoming lidar signal, providing more accurate and efficient detection capabilities with fewer false positives.
The new and updated ACL 3.2 blocks enhance Level 3 autonomous functionality by helping prevent collisions and improving machine positioning when GPS is not available. Level 3 autonomy introduces automated driving features to mobile machinery, enabling task consistency regardless of operator experience. This improves precision and productivity while enhancing safety.
“Better productivity, safety, and efficiency for end users, along with ease and speed of development for OEMs, is increasing the uptake of autonomous machines. ACL 3.2 delivers on both fronts,” said Adam Khaw, Head of Autonomy, Danfoss Power Solutions. “We will continue to work closely with our customers to enhance this world-class software platform, enabling OEMs to develop and manufacture highquality machines that set a new benchmark for speed to market.”
To learn more about Danfoss Power Solutions’ capabilities in autonomy, visit the Danfoss autonomous solutions webpage.
Gericke has long experience in grinding and calibrating agglomerates and bulk solids. The Gericke Nibbler GNB has been used successfully in the bulk solids industry for decades. It can deagglomerate dry, greasy or partially moisture containing products in an energy-efficient manner or to bring them to the desired target particle size.
The latest generation of Gericke GNB nibblers creates more value for users. The focus is on expanding process applications while reducing cleaning time and extending the service life of the nibbler screen.
The new features of the Gericke GNB offer various advantages. The target particle size can be easily adjusted by changing the shaker. This makes it possible to process a wide variety of products on the same granulator. It is now possible to set the optimum clearance between the beater unit to the screen insert for each screen and product without opening the machine. The metal contact monitoring system protects against incorrect adjustment. At the same time, this option also helps to detect ignition sources in an ATEX environment.
The option of moving the beater unit out of the housing on guide rods is popular in various industries. This option significantly reduces the cleaning effort and allows easy inspection of the machine.
The Gericke Nibbler GNB has already been used in various industries to the full satisfaction of many customers. For example, in the food industry or in the production of building materials with frequent colour changes or for materials that tend to stick together or compact.
In order to determine the optimum process parameters and the best machine configuration, Gericke offers the possibility of carrying out tests on a Gericke
GNB. Either with a rental machine directly at the customer’s premises or in a Gericke test centre.
The possible options can be assessed directly, and the optimum machine configuration can be worked out together.
About Gericke
The Swiss Gericke Group has been designing and manufacturing equipment and systems for automated bulk material processes, as well as providing design and engineering services, for more
than 130 years. Gericke bulk materials processing technology can be found throughout the world in many sectors including the food, chemical, pharmaceutical, plastics and construction material industries. Gericke’s fully owned group companies employ more than 350 experienced professionals and are located in Switzerland, Germany, Great Britain, The Netherlands, France, USA, Brazil, Singapore, Indonesia, Malaysia, Thailand and China.
ROCK.ZONE GmbH, a global leader in innovative excavator attachments, has taken a major step forward by acquiring MultaVex Oy’s patented VIBRAscreening bucket technology. This acquisition allows – ROCK.ZONE to enhance its product offering, further solidifying its commitment to delivering industry-leading solutions for the construction sector. With this addition, the company is better positioned to meet growing global demand, especially in material screening and recycling.
A Strategic Move Toward Market Leadership
With this acquisition, – ROCK. ZONE continues to build on its vision to be the foremost provider of high-quality excavator attachments. The Vibra screening bucket, known for its unique vibratory screening technology, fits perfectly into – ROCK. ZONE´s portfolio, which already includes crusher buckets (Rockcrusher), screening buckets (Rockscreener) and hydraulic
drum cutter (Rockwheel).
“We’ve always aimed to provide cutting-edge solutions to our clients worldwide. Integrating MultaVex VIBRA- screening bucket into our lineup strengthens our position in the global market. It’s a strategic move that allows us to continue offering exceptional products designed by the original inventors”, Robert
Piasecki, managing partner of –ROCK.ZONE GmbH, “Aligned with our existing product line, the new model will be named ROCKSORTER – the VIBRA Screening Bucket.”
Why the ROCKSORTER Screening bucket is a GameChanger
The Rocksorter Vibra screening bucket is a unique solution
designed for superior material separation, thanks to its wave-like vibratory motion.
Precision Material Separation:
The vibratory mechanism allows for the efficient separation of various materials, from soil to large tree stumps, boosting productivity on-site.
Maintenance-free: Operates without rotating parts, ensuring minimal maintenance and consistently low operating costs
Adaptable Sieve Sizes:
The bucket’s sieve can be quickly adjusted from 25mm to larger sizes, and with optional accessories, it can be reduced for more delicate applications.
Low Operating Costs: The VIBRA bucket consumes less energy and has lower wear-andtear compared to other screening buckets, making it a cost-effective choice.
Heavy-Duty Models Available: For the most demanding applications, every VIBRA bucket is available in a reinforced “Heavy Duty” version with additional teeth and durability enhancements.
Perfect Synergy: Innovation Meets Global Reach
With the acquisition of the Vibra bucket, – ROCK.ZONE not only adds another highperformance tool to its lineup but also reinforces its commitment to excellence in screening and recycling technologies. The screening bucket will now be available globally through – ROCK.ZONE’s extensive distribution network, which spans over 80 countries.
Minimum Agent Oy, Kalle Tuominiemi acted as a consultant in the arrangements for the business transaction.
“Robert Piasecki is the perfect partner to take over MultaVex. Not only does he have a clear vision for the future, but he also recognizes the potential of outstanding products. His dedication and passion for quality are unmatched, ensuring the success of the VIBRA technology on the global market”,
KalleTuominiem.
“I’m proud to see the Vibra bucket become part of – ROCK.ZONE’s exceptional product family. With their vast distribution network and commitment to quality, I am confident that our innovation will continue to thrive and reach new markets around the world”, Eero Paski, the founder of MultaVex and inventor of the VIBRA bucket
As – ROCK. ZONE continues to grow, the acquisition of the Vibra screening bucket underscores the company’s mission: to provide original, highquality attachments that offer real solutions to the challenges faced by professionals in construction, demolition, and recycling. This addition strengthens –ROCK.ZONE’s position as the go-to manufacturer for innovative tools that consistently deliver superior performance.
“ With the acquisition of the Vibra screening bucket, – ROCK. ZONE sets the standard – in the future, when screening is done, it will be with –ROCK.ZONE”, Robert Piasecki
Unlike other valves that seal with friction, Posi-flate’s unique butterfly valve uses an inflatable seat to seal with air pressure. Thus it requires less torque and a smaller actuator, resulting in lower cost. Plus, the seat automatically compensates for wear, providing longer life. Some users have reported over six million cycles and the valves are still going strong.
• Less friction • Low torque • Low maintenance • Lower actuator costs • Longer valve life
• More reliable
Gericke, a leader in industrial mixing technology, announces the introduction of its latest innovation: a double shaft reactor based on the GMS Double Shaft Mixer series, capable of reaching temperatures up to 400°C.
This cutting-edge reactor is designed for a variety of high-performance industrial applications, including the impregnation of activated carbon used in high-performance filters. It showcases Gericke’s commitment to advancing industrial processing technology.
The double shaft reactor is engineered to handle complex processes involving solids, liquids, and gas phases. The most intricate multi-step process, which includes several heating and cooling stages, spans approximately 24 hours. This duration underscores the necessity for gentle mixing, even for robust materials like carbon.
While achieving 400°C in a stainless steel machine might seem straightforward, the true
challenge lies in the details. One significant hurdle is managing the thermal expansion of materials due to the dual shafts, which must be meticulously calculated. Additionally, a comprehensive thermodynamic model of the mixer is essential to accurately size all inlets and insulation for both heating and cooling cycles.
Beyond high temperatures, the reactor must also accommodate pressure and vacuum swings, which significantly influence reaction kinetics. Releasing a vacuum can enhance various processes by facilitating the transport of agents into the material’s pores. This capability highlights the reactor’s sophisticated design and adaptability.
By precisely adjusting temperature and pressure conditions, Gericke has transformed a standard stainless steel machine into an intelligent reactor. This innovation not only meets the demands of highperformance filter production but also sets a new standard in the industry.
If you would like to subscribe to receive a regular copy of the digital edition of Bulk Solids Today magazine, you can subscribe on our website - www.bulksolidstoday.co.uk
If you are interested in advertising within Bulk Solids Today magazine or supplying editorial content, please feel free to get in touch using the details on our website or below.
Bulk Solids Today is sent to our digital readership of over 9,000 Chief Engineers, Operations Managers and Technical Managers from within sectors including Chemicals, Food & Drink, Mining, Quarrying, Transport/Distribution, Recycling & Waste Management and more.
www.bulksolidstoday.co.uk
Bobcat has announced an even wider choice of snow clearance solutions, probably the largest on the market. The range combines an expanded number of carriers that now includes compact tractors as well as compact wheel, skid-steer and compact track loaders and telehandlers, with a vast array of attachments such as snowblowers, angle brooms, scrapers, salt and sand spreaders, snow V-blades, snow blades and snow pushers.
The Snow Solutions range covers every winter application, including clearance of snow and ice on urban and country roads; pavements; car parks and other out-of-town locations. To enhance working on snow, Bobcat also offers optional steel tracks to go over the tyres on the compact tractors and wheeled loaders as well as individual tyre snow chains or snow tracks.
The Bobcat range ensures that customers have performance matched to their Bobcat machine, allowing them to work harder using products with stronger components and construction, backed by the best dealer support, parts and service available. Further peace-of-mind is provided by the 12-month warranty on every serial-numbered Bobcat attachment.
Bobcat now offers three Compact Tractor platforms – the 1000, 2000 and 4000 series – which feature nine models from 25 to 58 HP designed to meet the varying needs of customers in Europe, the Middle East and Africa (EMEA). Bobcat Compact Tractors are designed to increase productivity, versatility and reliability. Whatever
the application, these machines help to get the job done efficiently thanks to their robust construction, smooth operation, flexible configuration and full compatibility with a wide range of Bobcat attachments.
Bobcat Snowblowers are top performing snow removal tools working at maximum efficiency, clearing snow off driveways, parking lots, pavements and roads. The snowblower attachments feature a new and extremely durable direct-drive, sprocketstyle chute that operators can rotate to throw snow up to 12 m in virtually any direction and place it wherever the job requires - even in hard-to-reach places. The snowblower range has also been extended with new models to take full advantage of the faster travel speeds, higher productivity and excellent visibility available with Bobcat compact wheel loaders.
Bobcat 3-point Rear Snowblowers are perfect for blowing snow away from concrete or gravel driveways and parking lots. These snowblowers function from the rear PTO and 3-point hitch of the compact tractors. They are powerful, productive and easy to operate.
There are four sizes of Bobcat Angle Broom attachment with widths from 132 to 213 cm, designed to sweep away light snow, dirt, dried mud and other debris quickly and efficiently. The angle broom attachment can sweep flush to a kerb or wall on the right hand side. Reversible rotation allows the operator to sweep snow away from garage doors, gutters and other obstacles with ease, using the loader’s fingertip controls.
The Bobcat Scraper attachment, available with disk diameters of 46 or 56 cm, is highly efficient at dislodging packed snow and ice, providing an environmentally friendly alternative to the use of chemicals or salt, leaving behind a smooth surface for walking or travelling along.
The hydraulic Salt and Sand Spreader is ideal for spreading in confined areas, such as car parks and pedestrian zones, where larger equipment cannot be used. This attachment has a generous hopper capacity of 330 l. The hopper can be used as a bucket to allow the spreader to be filled from a pile.
The Bobcat Snow V-Blade is a versatile, hydraulically operated attachment offering five different blade configurations to help operators move snow fast. The blade has on-the-go fingertip control and angles 30° right or left to continuously push snow to either side of the loader, straight or scoop configurations to push large amounts of snow, or a V-configuration to plough through the deepest snow.
The Bobcat Snow Blade, available in seven widths from 152 to 274 cm, is designed to quickly remove light or moderate snow from pavements and
driveways. The moldboard on the snow blade angles right or left up to 30° and high visibility masts help locate the blade corners. Customers can choose between standard or heavy-duty options, to best suit their application.
The Bobcat Snow Pusher attachment is available in two sizes with widths of 244 cm and 300 cm, respectively. Designed to push snow with speed and efficiency, the flotation and oscillation of the moldboard keeps the snow pusher in contact with the ground without damaging equipment or property, allowing for snow removal even over decorative and uneven surfaces. As the snow pusher has rubber skis and an edge as standard, the operator can clear snow quickly, without damaging the ground.
Large capacity buckets, with widths from 168 to 254 cm and capacities from 690 to 1530 l, are also available for handling snow. They have high backs to help with pushing snow and straight sides to penetrate snow piles.
To watch a video of the Bobcat Snow Solutions range in action, please go to: https://bobcat.click/ SnowSolutions
For more information about Bobcat and Bobcat products, visit www.bobcat.com
Sensor Technology Ltd is excited to announce an update to its TorqSense SGR521 transducer, a significant enhancement in our innovative TorqSense rotary strain gauge series. In addition to standard digital outputs such as RS232 and USB, the TorqSense SGR521 now features an optional Ethernet output, providing users with enhanced connectivity and data transfer capabilities. This allows for seamless integration with various systems and facilitates real-time monitoring and analysis.
The SGR series transducer utilises non-contact technology, effectively eliminating the common drawbacks associated with slip rings, and employs modern strain gauge signal conditioning techniques to deliver a remarkable torque measuring solution. With a broad array of capabilities, the SGR521 transducer offers:
• Torque Measurement Ranges: Available from 175 mNm to 13,000 Nm
• High Accuracy: ±0.1%, ensuring reliable measurements
• Mechanical Overload Capability: An impressive 400% overload capacity
• Overrange Reading: Up to 250%
• Rapid Sampling Rate: A high digital sample rate of 4000 samples per second
The Ethernet output supports high-speed data transfer, enabling smooth integration into networked systems and enhancing remote monitoring capabilities. This empowers users to operate with greater efficiency and effectiveness. This innovative connectivity solution is poised to transform how torque measurements are captured, analysed, and utilised across diverse applications.
The TorqSense SGR521 transducer connects effortlessly to a Local Area Network (LAN), allowing for seamless integration with existing structured cabling and infrastructure. This capability makes the transducer instantly accessible to any device on the network, significantly enhancing operational efficiency and data accessibility. Users can access the transducer from any location within the premises where structured cabling is present or extend their reach through wireless networking technologies. Furthermore, if the network is connected to the internet or gateways and VPNs are implemented, the accessibility of the transducers can be extended indefinitely. This means that monitoring and control can occur from virtually anywhere in the world, providing unparalleled flexibility for users.
Historically, our transducers relied on technologies that allowed only a single device to connect and consume data at a time. With the introduction of Ethernet connectivity, multiple devices can now access the transducer simultaneously, allowing for collaborative data monitoring and analysis. By implementing standard Internet Protocols, any network- or internet-connected device—from smartphones and tablets to PCs, laptops, and even Arduino or Raspberry Pi development systems— can easily access the transducer. Communication occurs primarily through low-overhead UDP packet transmissions, ensuring efficient data exchange. This is complemented by an embedded web server, enhancing the user experience by facilitating easy access to data and configuration settings.
To maximise these advancements, our TorqView Advanced Torque Monitoring Software has been updated to support network functionality. This integration streamlines data visualisation and reporting, empowering users with the tools they need to harness the full potential of our torque measurement systems.
At Sensor Technology Ltd, we are dedicated to advancing the field of torque measurement with our innovative solutions. The TorqSense SGR521 transducer, with its Ethernet output and exceptional performance characteristics, represents a significant step forward in providing high-quality, reliable torque measurement solutions; and is the ideal solution for torque measurement, testing, feedback, and control across a wide range of applications, including drive mechanisms and process control.
If you would like to subscribe to receive a regular copy of the digital edition of Bulk Solids Today magazine, you can subscribe on our websitewww.bulksolidstoday.co.uk
If you are interested in advertising within Bulk Solids Today magazine or supplying editorial content, please feel free to get in touch using the details on our website or below.
Bulk Solids Today is sent to our digital readership of over 9,000 Chief Engineers, Operations Managers and Technical Managers from within sectors including Chemicals, Food & Drink, Mining, Quarrying, Transport/ Distribution, Recycling & Waste Management and more.
www.bulksolidstoday.co.uk bst@abbeypublishing.co.uk
Tuf-Lok ring grip pipe and tube couplings are rugged, heavy duty, self-aligning and self-grounded couplings with a high end pull. They can be used for almost any application where pipe or tube ends need to be connected. The Tuf-Lok self-aligning couplings install quickly and easily with little effort.
Features
• Self-aligning
• Self-grounding
• High pressure rated
• Full vacuum rated
• Stainless or mild steel
• Usable on thin or thick wall pipe or tube
• Low cost
• Reusable
• Absorbs vibration
• Externally leakproof
Toyota Material Handling UK (TMHUK) has announced that work is set to begin on the construction of a new purpose-designed Fleet Management Centre to support its growing UK Rental and Used equipment business.
The new unit will be built on the Old Dalby Trading Estate, Melton Mowbray – the industrial park where Toyota’s existing Fleet Management Centre is located, reaffirming the company’s commitment to the East Midlands region.
Building work is expected to take 18-months and, when complete, the centre will provide modern and sustainable office space, indoor and outdoor storage and state-of-theart workshop facilities, where equipment will be refurbished to the highest standards before being made available to rent or buy.
Stuart Reilly, TMHUK’s Director – Rental & Used, said: “Our facilities at Old Dalby were originally built as a military storage depot at the start of World War Two and has served us well over the past 24-years.”
He added: “Year-on-year growth has seen us operationally complete in excess of 12,000 trucks per annum and it’s time for an upgrade to support the largest rental fleet in the UK.
“Project FMC 2.0 will be a true reflection of the Toyota brand and provide exceptional facilities for members of the TMHUK fleet management team for many years to come.”
Bulk Solids Today is the bi-monthly digital journal covering the storage, processing and handling of materials ranging from fine powders to the heaviest raw materials. To subscribe to Bulk Solids Today magazine or for more information, please feel free to visit www.bulksolidstoday.co.uk
Eriez, a global leader in magnetic separation, detection and material handling technology, will showcase a wide array of its latest packaging and processing equipment at PACK EXPO 2024 in Chicago from November 3-6. The featured innovations, specifically designed to meet the growing regulatory and consumer quality demands within the food and processing industries, focus on enhancing product purity, operational safety, and overall efficiency.
Visitors to Booth N-5121 can view live demonstrations of Eriez equipment, including vibratory feeders, metal detectors, and magnetic separators.
“Our equipment is engineered to tackle challenges, whether routine or complex,” says Craig Lorei, Eriez Global Market Manager-Light Industry. “We strive to be a partner and a solutions provider, not just an equipment manufacturer.”
Lorei adds, “Our equipment empowers companies to achieve higher levels of quality control and production efficiency, enabling them to remain competitive and compliant in an increasingly stringent
and demanding marketplace.”
Eriez experts will be available for Q&A sessions and consultations, providing visitors with the chance to discuss tailored solutions for their specific operational challenges. To learn more about Eriez’ extensive range of equipment for food, packaging, and processing, visit the company at PACK EXPO Booth N-5121 or explore products online bit.ly/eriezpackexpo.
Established in 1942, Eriez is a global leader in separation technologies. Our commitment to innovation has positioned us as a driving market force in several key technology areas, including magnetic separation, flotation, metal detection, and material handling equipment. The company’s 1,000+ employees are dedicated to providing trusted technical solutions to the mining, food, recycling, packaging, aggregate, and other processing industries. Headquartered in Erie, Pennsylvania, USA, Eriez designs, manufactures, and markets on six continents through 12 wholly owned international subsidiaries and an extensive sales representative network. For more information, visit eriez.com.
Atherton Material Handling has installed a Bunting Suspension Electro Magnet at a calcium carbonate quarry in Melton, UK. The Suspension Electro Magnet removes tramp ferrous metal prior to a metal detector, reducing the number of metal detection trips and increasing productivity.
Bunting is one of the world’s leading designers and manufacturers of magnetic separators, eddy current separators, metal detectors and electrostatic separators, with globally located manufacturing facilities.
Atherton Material Handling originally contacted Bunting to find a solution to the problem of a metal detector in the quarry tripping too frequently. Tom Higginbottom, Bunting’s Technical Sales Engineer, was invited on site by the Atherton team to review the installation.
Bunting had supplied the original metal detector, a model TN77 series, which was identifying tramp metal that could damage crushers, screens, and conveyors. The metal detector was operating perfectly, but the quantity of tramp metal contamination resulted in frequent tripping, and the need to stop the conveyor for removal of the metal. Even though the metal detector’s performance was providing the ideal protection of processing plant, the frequency of metaltrips was affecting productivity.
Bunting recommended the installation of a Suspension Magnet prior to the metal detector. This would remove all tramp ferrous metal, which is magnetic, leaving the metal detector to focus on non-ferrous tramp metal such as manganese steel digger teeth.
The troughed conveyor transporting the quarried calcium carbonate was 600mm wide, carrying a densely
packed 100mm burden depth of material. This led to the recommendation of a Suspension Electro Magnet, which produces a strong, deep field powerful enough to attract tramp ferrous metal at the bottom of the burden.
The selected Suspension Electro Magnet, model 60 OCW 20, is cooled by oil and weighs just over one tonne. The magnet width is wider than the conveyor, at 925mm, and stretches along the conveyor 925mm. This provides plenty of dwell time under the magnet for the magnetic attractive
force to pull the ferrous tramp metal through the burden.
The Suspension Electro Magnet has three suspension points, which connect up to a handgeared travelling trolley, installed by Atherton Material Handling. This system enables the easy moving of the Suspension Electro Magnet away from the conveyor for safe and effective removal of all captured tramp ferrous metal off the magnet face. In operation, the maintenance crew manoeuvers the Suspension Electro Magnet into position over a chute before turned off the magnetic field and allowing all captured metal to discharge from the face of the magnet, under gravity, into a separate collection area.
The Suspension Electro Magnet, suspended 200mm above the conveyor, generates 650
Gauss on the surface of the belt, which is enough magnetic force to remove a wide range of tramp ferrous metal.
Once installed, the resultant reduction in the number of times the metal detector trips will reduce production downtime without any compromise on protecting the crushers and other processing equipment from tramp metal damage.
“We worked closely with the Atherton Material Handling team to find a solution for their client,” explained Tom. “The final solution not only maintains and improves important protection against tramp metal damage, but also makes it easy and safe to operate and clean the Suspension Electro Magnet.”
For further information, please contact us on press@buntingmagnetics.com or visit our website: www.bunting-redditch.com
The Modu-Kleen Series 725 top removal bin vent filter by Dynamic Air allows vented discharge air to be exhausted while preventing any outside atmospheric air from entering the storage silo or surge bin. This is ideal for venting storage bins and silos which contain hygroscopic materials that absorb moisture from the atmosphere. Materials such as granulated sugar and salt remain lump free and are handled much easier. Each filter is independent and can be easily removed without having to enter any kind of filter housing, making maintenance and troubleshooting quick and easy. This also makes maintenance far safer when trying to filter hazardous or toxic materials. An added benefit is its modular nature. If additional filter area is required, it can be added easily and at very little additional cost. Pressure differential and automatic self-cleaning controls are standard.
https://www.dynamicair.com/product/modu-kleen-binvent-filterseries-725/
The Series 486 inflatable seated butterfly valve from Posi-flate is suitable for many applications, such as food, chemical and pharmaceutical. The stainless steel valve features a fully machined 316L stainless steel housing and a single piece disc and shaft that is available in a number of materials including 316L stainless steel and Hastelloy. The disc may be polished to a mirror finish or coated with PTFE, nylon or other high-performance coating. The Posi-flate Series 486 butterfly valve is ideal for powders, granules, slurries and liquids and is available in sizes 2” (50mm) to 20” (500mm). Typical applications include loading and unloading of process material, sterile air control, and outlet valves for storage containers or hoppers.
The inflatable seat design of the Posi-flate butterfly valve provides a better seal by utilizing air pressure to expand the seat against the disc, providing more sealing area and an even pressure distribution against the disc every time. The seat automatically compensates for wear when it inflates against the disc, extending valve life considerably. Because the Posi-flate disc only makes casual contact with the seat during opening and closing, torque requirements are substantially lower. This ease of movement also allows the disc to come to a perfect 90-degree position every time. Additionally, the smooth profile of the disc helps material flow easier and reduces build-up. For unique fail-safe monitoring, a pressure switch can be utilized to verify a perfect seal.
Posi-flate
Milton Keynes, United Kingdom +44-1908-622366
E-mail: sales@posiflate.co.uk
https://www.posiflate.com
Gericke has long experience in grinding and calibrating agglomerates and bulk solids. The Gericke Nibbler GNB has been used successfully in the bulk solids industry for decades. It can deagglomerate dry, greasy or partially moisture containing products in an energy-efficient manner or to bring them to the desired target particle size.
The latest generation of Gericke GNB nibblers creates more value for users. The focus is on expanding process applications while reducing cleaning time and extending the service life of the nibbler screen.
The new features of the Gericke GNB offer various advantages. The target particle size can be easily adjusted by changing the shaker. This makes it possible to process a wide variety of products on the same granulator. It is now possible to set the optimum clearance between the beater unit to the screen insert for each screen and product without opening the machine. The metal contact monitoring system protects against incorrect adjustment. At the same time, this option also helps to detect ignition sources in an ATEX environment.
The option of moving the beater unit out of the housing on guide rods is popular in various industries. This option significantly reduces the cleaning effort and allows easy inspection of the machine.
The Gericke Nibbler GNB has already been used in various industries to the full satisfaction of many customers. For example, in the food industry or in the production of building materials with frequent colour changes or for materials that tend to stick together or compact.
In order to determine the
optimum process parameters and the best machine configuration, Gericke offers the possibility of carrying out tests on a Gericke GNB. Either with a rental machine directly at
the customer’s premises or in a Gericke test centre.
The possible options can be assessed directly, and the optimum machine configuration can be worked out together.
R. TODD SWINDERMAN, P.E. / CEO EMERITUS / MARTIN ENGINEERING
The conveyor technology experts at Martin Engineering are responding to the U.S. Mining Safety and Health Administration’s (MSHA) new dust emissions final rule by offering simple, makesense solutions for staying compliant.
Often, these rule changes cause a ripple effect internationally and serve as a template for similar policies worldwide. Martin engineers have dedicated years to reducing conveyor-borne dust by designing accessories and engineered solutions that improve workplace safety and production efficiency. In this article, Martin Engineering experts offer field-tested advice and methods that have delivered measurable results for mines and bulk handlers around the world for decades.
On August 1, 2024, the MSHA final rules came into effect. MSHA measures the dust personal exposure level (PEL) in a time weighted average (TWA) by a personal dust monitor carried by trained workers throughout their eight-hour shift. The volume is measured in micrograms (μg) in cubic meters (m3). The final rule establishes a new PEL of 50 μg/m3 for a full-shift exposure, calculated as an 8-hour TWA, and an action level of 25 μg/m3. These standards also apply to miners diagnosed with or showing early signs of pneumoconiosis (aka
- black lung).
MSHA mandates operators seek to install or repair equipment that offer engineering controls which control or eliminate sources of dust. This is supplemented with administrative controls (signs, policies, etc.). Temporary personal protective equipment (PPE) is also required for exposures above the PEL but is not considered a long-term solution.
Conveyor belt dust is largely generated at the loading and discharge zones. Passive dust reduction means no machinery or electricity such as air cleaners, pumps or HAVC are needed. Passive dust reduction strategies include:
• Fully enclosed transfers – Completely enclosing the loading, stilling and settling zones contain the dust. Items like dust curtains and dust bags control airflow and capture dust.
• Shorter or sloped loading – Transfer chutes that minimize the impact of cargo on the belt reduce the amount of turbulence and volume of dust within the loading zone.
• Belt training – Belt training when entering and leaving the loading zone ensures centered belt loading and minimizes material shifting. It also controls belt drift for less spillage and dust along the run.
• Preventing belt sag between idlers – The belt can dip slightly between idlers, creating gaps that release dust and fines. Using an impact cradle with shockabsorbent polyurethane bars reduces strain on the belt and creates an even belt plane. Cradles can extend along the entire length of the stilling zone.
LOWER BELT SPEEDS
Many sources suggest belt speeds of 2 m/s (394 fpm) or less for reducing dust generation. However, with lower belt speeds, the belt width must increase to convey the same tons-per-hour creating a capital cost vs operating cost dilemma. The Conveyor Equipment Manufacturers Association (CEMA) Classification and Definitions of Bulk Materials (ANSI/CEMA 550-2003) lists miscellaneous properties of bulk materials that benefit from lower belt speeds:
• B-1 Aeration-Fluidity
• B-6 Degradable-Size Breakdown
• B-8 Dusty
• B-20 Very Light and Fluffy
IDLER SPACING AND BELT TENSION
Managing belt tension so the sag between idlers is minimized reduces the number of escape points for fugitive spillage and dust from material trampling and splash. Splash is material spread after impact on the belt during loading. Material trampling is the particle-to-particle movement created by the change in the bulk material profile as it goes over the idlers. The higher the belt tension, the lower the trampling loss.
Similar to turbulent air caused by impact, at a critical speed, bulk material moving over idlers loses contact with the belt at the idler and is launched into the air, falling back onto the belt at a slightly lower speed and releasing dust. Keeping the belt sag to 1% between idlers is a frequent specification.
Idler spacing is critical to controlling belt sag. To reduce gaps where spillage and emissions can escape and retain an even belt profile in the
loading zone, idlers should be placed as closely together as possible. Outside of the loading zone, CEMA has some recommendations based on volume and belt width.
The amount of dust that can become airborne is directly proportional to the volume and speed of the airflow through the transfer point. If the openings in the chute work are restricted to the practical minimum, the inward airflow is restricted. A useful dust control strategy is to capture the material shortly after discharge and keep the stream coalesced as tightly as possible to reduce induced air. Extend enclosures apply dual skirting to seal the enclosure and use dust curtains to control airflow and allow dust to settle back into the material stream.
Conveyor transfer points have a history of being drafted rather than designed. Design tools and material flow modeling software helps reduce dust emissions in the transfer point design phase. How the conveyor is operated and maintained also has a significant effect on dust generation and release. In initial conveyor system designs, emphasis is commonly placed on maximizing production. But experts recommend operators engage in feasibility studies on how the conveyor systems create and emit dust with the goal of improving air quality and workplace safety while still increasing operational efficiency.
www.martin-eng.com
Bobcat has added a new Remote Engine Disable/ Enable feature on the company’s Machine IQ telematics platform. The new feature allows customers in Europe to remotely enable or disable their machine’s engine through the Owner Portal or Machine IQ app. With Remote Engine Disable/Enable, operators and owners can shut down their machine with a few clicks, deterring theft and aiding in quick machine recovery.
Machine IQ, launched last year in Europe, allows connected-machine owners to monitor the health of their Bobcat machine and remotely track information that enhances maintenance, security and performance. The new Remote Engine Disable/Enable feature represents the first two-way update for the telematics system, allowing operators to both send commands to and receive data from the machine. Remote Engine Disable/Enable via Machine IQ can be activated in Bobcat skid-steer and compact track loaders, miniexcavators and compact wheel loaders connected to the system.
“Enabling advanced theft deterrence provides critical peace of mind for our Machine IQ users, and Remote Engine Disable/Enable allows our European customers to protect their equipment and allow only authorised usage. This feature also demonstrates our ability to interact with machines via two-way communication using telematics. Today marks another major milestone for what Bobcat continues to do - to empower our customers to accomplish more,” said Tomas Plechaty, Machine IQ Senior Program Manager at Bobcat EMEA.
Available with Premium Machine IQ subscriptions, this innovative solution empowers customers to remotely prevent theft and unauthorized use in just a few clicks. If unauthorized use is suspected, customers can log into their Bobcat Owner Portal or Machine IQ app to select the asset, and click ‘Remote Engine Disable/Enable’ in the sidebar. Only administrative users can access this feature, and all Remote Engine Disable/Enable activity is tracked in the asset’s history table. Upon executing the disable command, any attempt to start an engine in an off state will fail. If the machine is in operation, the engine will shift into derate mode.
• Deter theft, and potentially recover stolen machines. By remotely disabling engines, unauthorized use can be stopped, and recovery efforts aided.
• Can lower insurance rates: Demonstrating a proactive commitment to investment protection can make customers eligible for lower theft-related premiums.
• More benefits for Premium subscribers: Remote Engine Disable/Enable extends functionality for Premium subscribers, creating more value for customers.
• Boosts resale value: Unlocks future-proof security making resale a more attractive, and potentially higher-value, investment for discerning buyers.
• Improve payment compliance for rentals: Remote Engine Disable/Enable can be used for delinquent rental accounts, encouraging prompt payment and reducing revenue loss.
• Enforce safe operating procedures, prevent potential damage: Engine operation can be temporarily disabled in response to unauthorized use, unsafe behaviour or potential machine misuse.
With Machine IQ, customers
have 24/7 access to crucial machine information on their smartphones or computers. Equipped with this information, customers can optimize machine use and plan jobs for maximum profitability by keeping idle times to a minimum and tracking fuel consumption. Service planning is made easy with maintenance notifications, saving operators time and money by allowing them to efficiently schedule machine maintenance and manage job sites during planned downtime.
Dealers and customers can choose from two options: a Standard package with basic telematics and a Premium package with additional advanced features. According to Tomas Plechaty, the subscription options let users tailor their experiences and access the level of connectivity and insights that best suit their needs. “With a focus on simplicity for the user, we are confident that the packages will meet the needs of customers and dealers across the globe, and help them grow their businesses,” he said.
Machine IQ comes factory-installed with many equipment models and can easily be installed on compatible Bobcat machines in the field. Customers should contact their local dealer to check compatibility. Bobcat customers can access Machine IQ by visiting my.bobcat.com, creating an account and logging in. Alternatively, the mobile app for Machine IQ can be downloaded from Google Play/ Apple Store.
Since 1958, Bobcat has been empowering people to accomplish more. As a leading global manufacturer of compact equipment, Bobcat has built a proud legacy of innovation and a reputation for delivering smart solutions to customers’ toughest challenges. Backed by the support of a worldwide network of independent dealers and distributors, Bobcat now offers extensive lineups of compact machinery (including loaders, excavators, telehandlers, compact tractors and mowers) and material handling equipment (including forklifts and warehouse solutions), plus a broad range of attachments, parts and services. The Bobcat brand is owned by Doosan Bobcat.
Doosan Bobcat is a company within the Doosan Group. Doosan Group is a top-tier global enterprise that has proudly served customers and communities for more than a century. Doosan Bobcat is based in Bundang, South Korea.
The Bella dryer/cooler offers thermal efficiencies to 80 percent or better because air flows around material while it is suspended in the weightless zone. The result is a more consistent material.
One of the largest premium flour and ingredient companies in North America, Ardent Mills, recently implemented automatic testing on several of its conveyor Fortress Technology metal detectors. A number of the company’s packaging lines are now also using digital reporting to enhance efficiency, food safety and traceability.
Ardent Mills has an expansive national footprint. Comprising over 40 locations producing flour, quinoa and pulses, organic and gluten-free products, Ardent Mills recognises the importance of embracing the newest digital technologies to ensure that every aspect of its operations remain true to its quality standards. Processing around 22.4 million bags of packed milled product annually, over the last 12 months Packaging Engineer Manvine Bharj and her team, supported by local Fortress food safety specialists, has set up Halo Automatic Testing on six inline conveyor packaging lines.
At the mills that ship packed product direct to retailers and commercial bakeries, Ardent implements an end-of-line HACCP testing point, just before palletising. “We intentionally test our inspection equipment more often than our customers’ conformance requirements stipulate, as it provides extra quality assurance and fills us with confidence that our products are the safest they can be,” notes Manvine.
Activating the technologies pre-installed on their Halo Ready Fortress metal detectors has proven to be an efficiency and safety gamechanger for many of the mills’ quality managers. The resulting operational savings have been equally rapid. Manvine estimates the ROI on the original Stealth Metal Detector investment has been achieved in six months or less. “Halo provides the perfect blend of inspection continuity, contaminant detection, machine performance and safety,” adds the Packaging Engineer.
Like many mills and bulk processors, one of the greatest challenges when performing repeatable manual tests is the amount of time and labour it requires and simulating the same conditions for each test. UK Sales Director Phil Brown explains: “Manual testing in milling environments often requires placing a test sample in the exact middle of each grain bag, passing this through the metal detector, removing it from the line, opening the packaging and removing the test sample, and inspecting it again. Testing all three metals, every two hours is a lot of heavy lifting, sifting, repacking and potential waste. Not to mention, replicating this test manually is
extremely challenging to do accurately.”
Halo Automatic Testing instead independently tests all three metals in the exact geometric centre of each Stealth metal detector aperture. The technology then mimics the disturbance caused by a test contaminant calibrated to the precise size, metal type and speed of each product bag as it passes through the metal detector aperture.
“With automated tools like Halo and Contact 4.0 we are proactively preventing issues for our team members, all while improving customer service and overall food safety,” reports Manvine.
In order to distinguish between a real metal detection reject and when a Halo test is being performed, the milling business requested one customisation – a blue light system to alert operators when a test is running.
“This feature alone has made a huge impact on our labor demands and potential product waste. Without this blue light we would have to either sift and rework every 50lb test sack assuming it was contaminated, or simply reject and waste it. That could have added up to re-inspecting 12 sacks, 600lbs of flour, per line, every shift,” highlights Manvine
oversight allows them to immediately address issues and ensure the inspection process doesn’t cause a bottleneck,” exalts Manvine.
With many sites moving towards paper-lite processes, automating QA documentation has been a crucial step in maximising both equipment and operator efficiency, reports the milling business.
As a web-based networked system, Contact 4.0 allows operators to monitor multiple metal detectors. “Our quality managers loved Contact 4.0 as soon as it was implemented. As a networked system, it’s so easy to go into the centralised browser, select and email shift reports and view when tests were performed. Having this complete
The cohesive Contact 4.0 reporting system allows authorised employees to troubleshoot performance issues remotely. Test failure, fault or non-conformity events can trigger an automatic email alert, detailing when an event occurred on a specific machine.
With more facilities eager to switch and activate similar efficiency-enhancing programs, the packaging engineer anticipates ongoing integration projects. Citing real-time information as being the enabler for smarter decision making, Manvine believes that rolling out new technology also ignites curiosity and drives operators to do even better. www.fortresstechnology.co.uk