
22 minute read
Tuning building systems in the near future
By John Bourne, Project Engineer, A.G. Coombs Advisory
ABSTRACT
Building tuning is an important part of delivering high performing new buildings with lower operating costs and higher rental yields. It is also a ‘must have’ on existing buildings that are looking for significant improvements in energy efficiency, HVAC system performance and occupant satisfaction.
Tuning currently relies heavily on data collected via Building Management and Controls Systems (BMCS). As Operational Analytics, Internet of Things (IOT) devices and cloud computing capabilities become common practice the amount of information we have increases exponentially and the way in which we tune buildings will evolve. This step-change in technology will have a flow-on effect to other aspects of building operations, including maintenance services and life cycle asset management.
INTRODUCTION
This paper presents an overview of the building tuning process and how it is evolving with the introduction of data-driven analytics, IOT devices Building Information Modelling (BIM) and cloud computing capabilities within buildings.
The building tuning process involves a number of stakeholders, including the building owner, facility manager, maintenance staff, design engineers and installation contractors. The objectives of the tuning process revolve around improving tenant satisfaction, reducing energy and water consumption and improving plant stability. Ultimately, from a building owner’s perspective, building tuning is about reducing operating costs and increasing the capital value of a building asset. For new buildings, tuning often commences following practical completion. This can be a requirement of an environmental rating (e.g. Green Star) or driven by the owner as a project requirement. For existing buildings, building tuning can be undertaken at any time.
There are various inputs into building tuning, including energy and water metering data, tenant feedback, maintenance reports, condition audits and data collected from a BMCS.
As operational analytics platforms flood the market, building owners are receiving an overwhelming amount of information about their buildings. The challenge for a building tuning process is to filter this data and tune the algorithms such that the most relevant items are identified and prioritised. Too much unstructured information can be paralysing.
Building tuning is now also able to be completed across multiple building assets and portfolios. Using dashboards to present large amounts of data collected from multiple different sources downstream, in a clear and consistent manner, enables comparison of our building systems and equipment at a much greater scale.
Buildings are becoming smarter. IoT devices, able to be quickly and easily added and interfaced with our buildings, are also increasing the breadth of data we’re collecting from our buildings. This is particularly beneficial for condition monitoring and sub-metering applications. As more third-party devices are added to buildings
Indoor Environment Quality NABERS Energy/ Water Rating
Reduced Operating Costs
Improved Equip Lifecycle + Reduced Maintenance Costs Building Tuning
Tenant Satisfaction
CIBSE Soft Landings Green Star Design and As-Built Rating
Figure 1 - Why do we tune buildings
the communications infrastructure supporting them is also changing, to facilitate high-speed interfaces and seamless monitoring from a central dashboard.
The outputs of building tuning can also inform decisions around lifecycle replacement of equipment and proactive maintenance activities to optimise/prioritise capital vs operational expenditure.
1. BUILDING TUNING
1.1 Why do we tune buildings?
Building tuning is primarily undertaken to reduce operational costs and improve the financial value of a building asset (rental yield and capital value). This is achieved by targeting the following objectives:
• Reduce the energy and water consumed by the building (energy and water) and compare actual consumption to what was predicted. • Optimise the performance of plant and equipment in order to improve stability and reduce operational stress. • Improve tenant comfort and satisfaction .
Often the requirement for tuning is dictated by the requirements of an environmental rating, such as CIBSE Soft Landings or Green Star Design and As-Built. However, it can also be driven by building owners and facility managers looking to reduce operating costs and improve their NABERS (Energy and Water) or Green Star Performance credentials. Aside from reduced operating costs, it has been shown that an improvement in NABERS Energy Rating relates to an improvement in the capital value of the asset [1] and an increase in rental yields.
There are also additional rating tools (WELLS and NABERS IEQ), which have a focus on indoor environment quality. These tools are also starting to become a focus within building tuning programs.
1.2 Who is involved?
Building Tuning for new buildings requires input from the facility manager, the client/building owner, head contractor and services subcontractors (in particular, the controls sub-contractors), the services designers, the Independent Commissioning Agent (ICA) and commissioning manager (if appointed).
For existing buildings, building tuning also involves maintenance contractors, tenants and a technical services specialist.
1.3 When does tuning take place?
Building Tuning can commence immediately following practical completion and continue throughout the operational life of the building. Typically, for new buildings, there will be a minimum requirement for building tuning for between 12 and 36 months after practical completion.
For existing buildings, tuning can commence at any stage. It is important for building tuning to encompass whole year/s of climatic conditions. Many symptoms of poor building performance are masked by seasonal changes or caused by operational upgrades and fitouts. For this reason, it is also recommended that a building tuning program commence after any modifications to the building (e.g. upgrades and fitouts).
1.4 What does building tuning involve?
At a high level, building tuning is about continuously monitoring and improving the performance of a building. The scope of building tuning can vary widely between buildings. The objectives and extent of building tuning should be clearly specified by the client. The scope will typically include the following items as a minimum:
• Collect and review tenant feedback/satisfaction. Where there is dissatisfaction, investigate whether there is an underlying issue or whether a change can be made to improve the level of tenant satisfaction without compromising other targets. • R eview the energy and water usage periodically and compare to the predicted usage. This should be completed on the building as a whole and using end-use-breakdowns and sub-metering data. The total building energy and water use should also be correlated with utility bills periodically.
• Validate the performance of control systems under various conditions (occupancy, seasonal changes, etc.) to ensure they are achieving their design intent. This can involve verifying the conditions (temperature, humidity,
CO2 etc.) are within design tolerances. It also involves verifying control loops, such as chiller staging and reset strategies to ensure they are operating optimally.
1.5 How do we tune buildings?
The building tuning relies on data collection and analysis in order to make informed decisions about potential improvements. Most buildings now incorporate a BMCS, providing the ability to extract information about a building’s performance and identify opportunities for improvement.
Implement changes to system operation Systems put into automatic operation
Collect Data on system performance
This relies heavily on accurate documentation within controls functional descriptions, operation and maintenance manuals and the original design intent/ criteria. For new buildings, energy models are also used as a reference for building performance. The relevant experience of personnel is also important in making fact based tuning decisions.
BMCS’s use a large number of input and output points, combined with control loops, to monitor and control our building systems. Comparing and correlating all this information to identify improvement opportunities can be a difficult task. It is also difficult to accurately predict the impact that any changes will make on the overall system performance. For example, a BMCS can trend the COP of a chilled water system. When we compare this to an energy model, or another trend log, we need to factor in the ambient temperature and humidity, the operating load of the chillers and cooling towers and any change in plant condition or recent maintenance activities.
There are now additional tools that are available to building tuning teams to collect and analyse performance data. Operational Analytics packages and smart IoT devices are becoming more prevalent in modern buildings. Building tuning in the future will need to understand and make use of these tools to ensure they are accurately and purposefully driving performance improvements.
2. NEW TECHNOLOGIES Analytics is often promoted as a silver bullet to improve the performance of buildings. References are also being made by some suppliers in the industry to artificial intelligence and virtual engineers. Some of these statements can be misleading. The sections below provide an overview of some of the available technologies.
Investigate anomalies and develop opportunities for improvement Review Data and identify anomalies
Figure 2: Building Tuning Process
2.1 Operational analytics
Operational Analytics encompasses a broad range of products with an even broader range of implementation strategies. At its core, operational analytics uses rule-based algorithms and data collected from sites to determine when a condition or system has broken the rules. Data is often ‘crunched’ off-site, using cloud computing to process the vast amount of information. This can greatly increase the ability of building tuning teams to diagnose and address less obvious performance issues. If the analytics packages are relying on BMCS data, the information must be setup and stored in a logical manner.
Operational analytics packages are often sold with the promise of maintenance savings and reductions in energy use. It is difficult to quantify and verify the claims. Identifying issues is only one first step in the building tuning process. There is also an argument to be made about the BMCS being used to provide ‘analytics type’ feedback on system performance. Equally, it is often assumed that the BMCS is able to provide adequate, structured information to the analytics package for processing.
The other area where operational analytics is being used is to analyse performance of equipment/systems within buildings across portfolios. Using dashboards to display information in a consistent format drawn from any number of different sources enables fast and direct comparison of performance.
Titanium
Humidity Matters

A complete range of humidification solutions to maintain the correct levels of humidity (40-60% rH) enhancing human immune system reaction and significantly reducing infection from seasonal respiratory viruses
CAREL Australia Pty Ltd
PO BOX 6809, Silverwater Bus. Ctr. N.S.W. 1811 Unit 37, 11-21 Underwood Rd Homebush N.S.W. 2140 Tel. (+61) 02 8762 9200 - Fax (+61) 2 9764 6933 - sales.au@carel.com
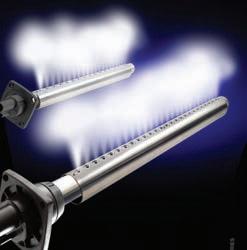
40-60%rH optimum humidity level
2.2 Where does the BMCS stop and operational analytics begin?
The line between what a BMCS provides and what an Analytics package should provide is still blurred. There are multiple levels of analytics, ranging from alarming and fault identification to dynamically monitoring, correlating and reporting on system efficiencies and the effectiveness of control loops such as reset strategies.
We believe that a BMCS should be used to manage and control plant on an “if this, then that” basis. This includes provision of setpoints to plant and sub-systems, conditions for resetting setpoints, monitoring of plant status and general conditions inside and outside a building. The BMS is well suited to providing instant alarms, such as equipment faults.
Analytics packages can then collect and use historical data as inputs into algorithms to identify where opportunities exist for improvements. Each algorithm is comparing the multiple sources of processed data to a set of rules (defined by users) over extended periods of time. It is critical that the objective of the rules is understood so that anomalies and spurious alarms can be identified and dismissed, enabling refinement of the rules to more accurately satisfy the tuning objectives.
2.3 Artificial intelligence and machine learning
There has been much hype about analytics engines using machine learning and artificial intelligence.
Machine learning is the next evolution of rules-basedalgorithms. Machine learning is based on algorithms automatically refining themselves based on experience (large quantities of data) [2] . In the context of building services, it is the evolution of understanding what is normal or abnormal. This evolution can take several forms, which are sub categories of machine learning:
• Supervised learning • Unsupervised learning • R einforced learning
There are a several examples of machine learning in practice within the HVAC&R industry presently, but it is not as advanced as in other markets. Machine learning examines data to find patterns and anomalies. Once identified, human interaction is usually required to act on the data presented.
Artificial Intelligence is a much broader and more objective term, often having connotations to human intelligence. AI is often categorised into “Applied Artificial Intelligence” and “Artificial General Intelligence”. The former better describes current AI applications with the HVAC industry, where we have specific goals (e.g. energy optimisation). AI is able to make assumptions, test the assumptions, learn and then act autonomously in the same way a human would. AI is about automating judgements [3] and can rely on all three types of machine learning. The implications of AI will be significant; however, its use is not as widespread in our industry as are led to believe (under this definition). Sophisticated automation is often confused for artificial intelligence.
2.4 Asset analytics
Unlike operational analytics, asset analytics is focused on specific assets (and families of assets) within building systems. This includes information about the make and model, location, age, condition and capacity of the equipment. Asset analytics also feeds into life cycle plans, which are used to determine when an item of equipment should be scheduled for replacement.
Historically, life cycling planning for asset replacement has been based on generic lifespans nominated in technical guidelines (such as CIBSE Code M). More recently, however, asset analytics and performance data (which can come from operational analytics) is starting to be used to provide a more accurate assessment of an asset’s condition and the proposed timeframe for replacement.
2.5 Internet of things (IoT)
There is a rapidly increasing number of third party devices that can quickly and easily be installed and interfaced to existing systems in our buildings. Wireless IoT devices, such as clip-on current transformers, can be easily retrofitted for sub-metering and interfaced with existing monitoring platforms (or displayed via online portals). Another example is the Movus condition monitoring device. This wireless device uses multiple sensors, including a microphone, accelerometers (for vibration), temperature and pressure data to determine when a rotating piece of equipment is operating abnormally. The machine learning component of this device tunes the definition of what is considered abnormal, based on how often equipment operates at specific duties.
By adding new types of sensors in the field, the data set available for operational analytics expands and can also feed into asset analytics and drive proactive, conditionbased maintenance.
With the increasing uptake of environmental rating schemes focusing on indoor environmental quality, IoT devices can facilitate flexible remote monitoring of air quality. Additionally, the uptake of hotdesking in our offices has opened up opportunities for occupancy sensing and the use of setback conditions for air conditioning and ventilation systems.
The infrastructure in our buildings is having to evolve to accommodate these third-party devices. Buildings are now being specified with Integrated Communication Networks (ICNs), which provide a common, high-speed backbone to interface directly to third party devices directly over IP. Additionally, BMCS’s are also following suit and providing more downstream devices with IP communications capabilities.
As our buildings fill with these devices, consideration needs to be given to who owns the data captured by the devices. Can the engineering tools and algorithms be interrogated and modified by facility managers and engineers or is this functionality restricted to the supplier? The definition of ownership is also unclear (especially regarding machine-generated data) and currently only legally defined in specific contracts rather than in legislation [4] .
2.6 Virtual engineers
Another idea that has been promoted with the implementation of analytics packages is notion of a ‘virtual engineer’. The theory is that the analytics package performs the role of a (human) engineer in the building tuning process.
It is important to understand that there is a difference between identifying potential issues (carried out by virtual engineers) and interrogating them to determine the appropriate course of action. Building Tuning includes both of these actions and should also include tuning of the Virtual Engineer!
2.7 BIM and the virtual twin
BIM is currently still falling short of its true potential. Good progress has been made in some areas (for documentation and digital construction), however the focus has been on the build phase of projects. BIM for Facility Management (FM) and for use as an engineering tool are still not fully developed. This space is changing rapidly. The ability to transfer knowledge from the design and construction phase to the operational phase of a building is greatly improved with the use of BIM to FM. Building owners are now starting to drive this requirement rather than passively receiving whatever documentation is provided at completion of the construction phase.
The goal is to create a digital twin of the actual building. The digital twin takes input data from the design, fabrication and commissioning process, as well as realtime performance data from various sources. Doing so allows us to create a digital ecosystem for operational management. From a building tuning perspective, we can diagnose performance deficiencies faster, accurately simulate proposed tuning activities to assess the outcomes and develop more granular end-usebreakdowns for energy and water systems to benchmark their performance.
Existing buildings, without BIM models, are often where the greatest opportunities lie for building tuning. There is an increasing trend for existing buildings to have their records digitised and managed through cloud based document management systems. Existing buildings can also be scanned and modelled in the virtual world with relative ease, where performance parameters, commissioning results, condition audits and operation and maintenance data can be stored and used. Consideration then also needs to be given to storage and maintenance of this data.
3. TUNING BUILDINGS IN THE NEAR FUTURE In the near future, how we tune buildings will evolve to include tuning (or sharpening) the tools we use, as much as it will be about tuning building performance. Analytics algorithms and data management will become much more common methods of measuring and assessing building performance. However, in the near future, these tools will still be used to identify symptoms of poor performance. Building Tuning as a process will continue to be about diagnosing the root cause of the symptoms, developing a solution and monitoring the impact of the change. Further into the future, as machine learning develops, some aspects of this process may also become automated.
In addition to current building tuning objectives, there will be a shift towards analysing and comparing building performance on a much larger scale, across multiple assets. The ability to import and display data from different controls systems is expected to be common practice for building portfolios and will enable direct comparison of whole buildings against each other.
Tuning will also increasingly feed into asset life cycle programs and proactive maintenance strategies. With more information available, digital twinning and predictive models for energy and water usage will edge closer to actual usage, enabling more accurate forecasting of operating costs and CO2 emissions.
As cloud computing increases the capacity to crunch data collected from site, there is an increasing need to ensure that the BMCS’s and analytics packages, as part of a tuning program, are implemented in a logical manner that does not burden the existing network and provides clear and logical information for building owners and facility managers. We are starting to move away from using the BMCS to monitor all our equipment and will instead use high speed interfaces, IP enabled devices and
integrated back bones to facilitate interfaces to a range of sub-systems. In order to accommodate this change, the following will need to be considered:
• Specifying ICN backbones and communication protocols, allowing for vendor independence. • Naming conventions. • BMCS/EMS and IOT data structured and stored in a logical manner to enable easy interrogation by third party packages. • How and where will information be stored and processed - edge computing or cloud ser vers. • Who owns the data.
We recommend considering the accuracy of the underlying data (is the BMS data real?), how different data sources are merged and engaging proficient advisors who can help deploy, manage and verify the systems and architecture to achieve good management of the facility.
It is also likely that building tuning in general will become more common in the near future, potentially being nominated as part of facility management and maintenance contracts. In order for this to be successful, there must be clear objectives and a building tuning scope of work.
CONCLUSION The overarching objectives of building tuning will largely remain unchanged; however, changes are expected to come from the tools that we use in order to diagnose symptoms and identify opportunities for improvement. In order to utilise these tools to their full effect, the scope of building tuning will need to extend to include tuning of the algorithms and the devices we rely on to identify performance issues.
With the exponential increase in data, the benefits of thorough building tuning will also be to feed into life cycle planning, financial performance metrics, portfolio-scale comparisons and more accurate forecasting of energy consumption.
The current wave of digital technology, including as BIM to FM and digital twins, will give us even more information about our buildings. In order to continue effectively tuning buildings in the near future, an understanding of how these tools are facilitated by building infrastructure and how they can be applied is critical.
REFERENCES
[1] IPD: Department of Industry NABERS Energy Analysis, Investment Property Databank Ltd (2013) [2] Mitchell, T, “Machine Learning”, McGraw-Hill, P1 (March 1, 1997) [3] Moore A, “When AI Becomes an Everyday Technology”, Harvard Business Review (June 2019) [4] Van Asbroeck B, et al, “Big Data & Issues & Opportunities: Data Ownership, Bird&Bird (March 2019), Accessed 29/7/2019, https://www.twobirds.com/en/news/articles/2019/global/ Big%20Data%20and%20Issues%20and%20Opportunities%20 Data%20Ownership
BIBLIOGRAPHY
• AIRAH: AIRAH DA27 Building Commissioning Application Manual, Australian Institute of Refrigeration, Air Conditioning and Heating (2011) • AIRAH: AIRAH DA28 Building Management and Control Systems, Australian Institute of Refrigeration, Air Conditioning and Heating (2011) • ASHRAE: ASHRAE Commissioning Guideline 1.1-2007 American Society of Heating, Refrigeration and Air-Conditioning (2007) • CIBSE: CIBSE Commissioning Code M, Chartered Institute for Building Services Engineers (2003) • HVAC HESS: Heating, Ventilation & Air-Conditioning High Efficiency Systems Strategy (September 2013) • Smith, A; “Building Tuning – Getting your Buildings to Work Properly”, A.G. Coombs Advisory – Advisory Note (2015) • Smith, A; “Using Analytics for Improving Building Performance”, A.G. Coombs Advisory – Advisory Note (2016) • Iriondo, R:“Differences between AI and Machine Learning and Why it Matters”, https://medium.com/datadriveninvestor/ differences-between-ai-and-machine-learning-and-why-itmatters-1255b182fc6 (2019) ‘This paper was presented at the AIRAH 2019 Future of HVAC conference and first published in the November 2019 of Ecolibrium’.
ABOUT THE AUTHOR John is presently employed as a project engineer for A.G. Coombs Advisory. John has over 12 years’ experience in the building services industry, having performed a diverse range of roles ranging from design of mechanical HVAC systems and trigeneration systems, ICA, building tuning, commissioning management and energy audits. John has also been heavily involved in post completion issue resolution, requiring detailed investigation and complex analysis of systems including laboratories and energy plant. John’s primary area of focus currently is commissioning management and Independent Commissioning Agent roles.
FEATURE ARTICLES Sustainability requires a high level of integration between HVAC, lighting, and security systems. The art of building sustainability skillfully combines this integration with other technological and supporting elements that must endure over the long term. When these additional elements are maintained over the life of your building, true building sustainability emerges. To learn more about the ART of Building Sustainability please visit reliablecontrols.au.com/TABS11E19.
Ensure a strong level of interoperability by using open protocols which have third-party listing laboratories to verify adherence to your protocol’s form and function.
Employ a single sign on (SSO) architecture with compliance to scalable credentialing architectures and secure tunneling methodologies such as BACnet virtual private networks (B/VPN).
Specify integrated FDD (IFDD) that delivers real-time fault detection, step-by-step root-cause diagnostics while using all your existing cabling structures, including twisted-pair networks. 1
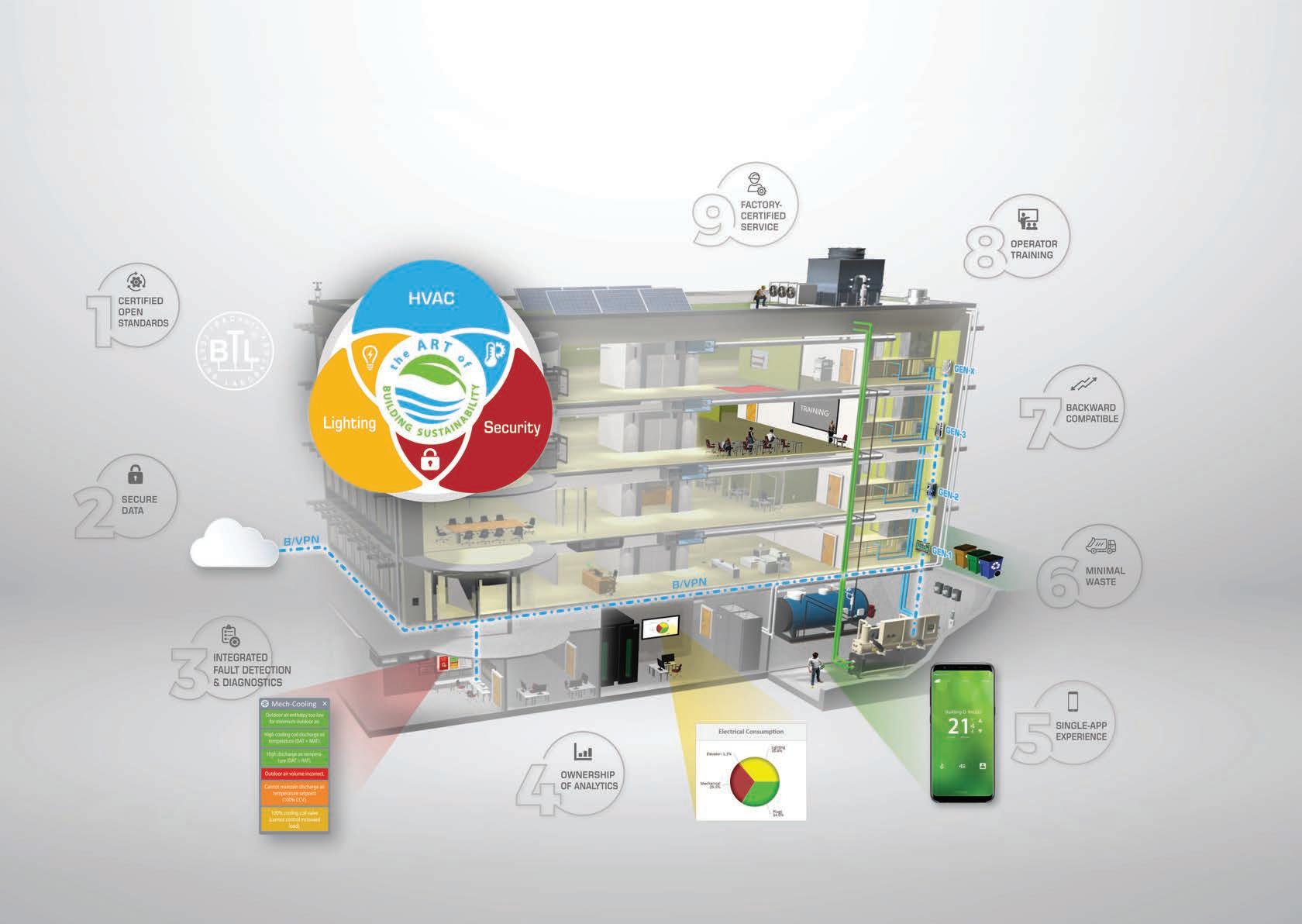
Insist on timely analytics for all stakeholders with complete control of formatting and scheduling while retaining full ownership of your data and the reports generated.
Choose from a global network of factory-certified service partners who are passionate about long term, consistent, local support for you and your buildings. Stay on top of regular advances in technology with supplier-certified, multi-lingual online educational videos, technical documentation, software updates, and advanced face-to-face classroom courses.
Enjoy the long-term benefits of suppliers who engineer a path forward to new technologies while remaining backwards compatible without third-party gateways or hardware replacement.
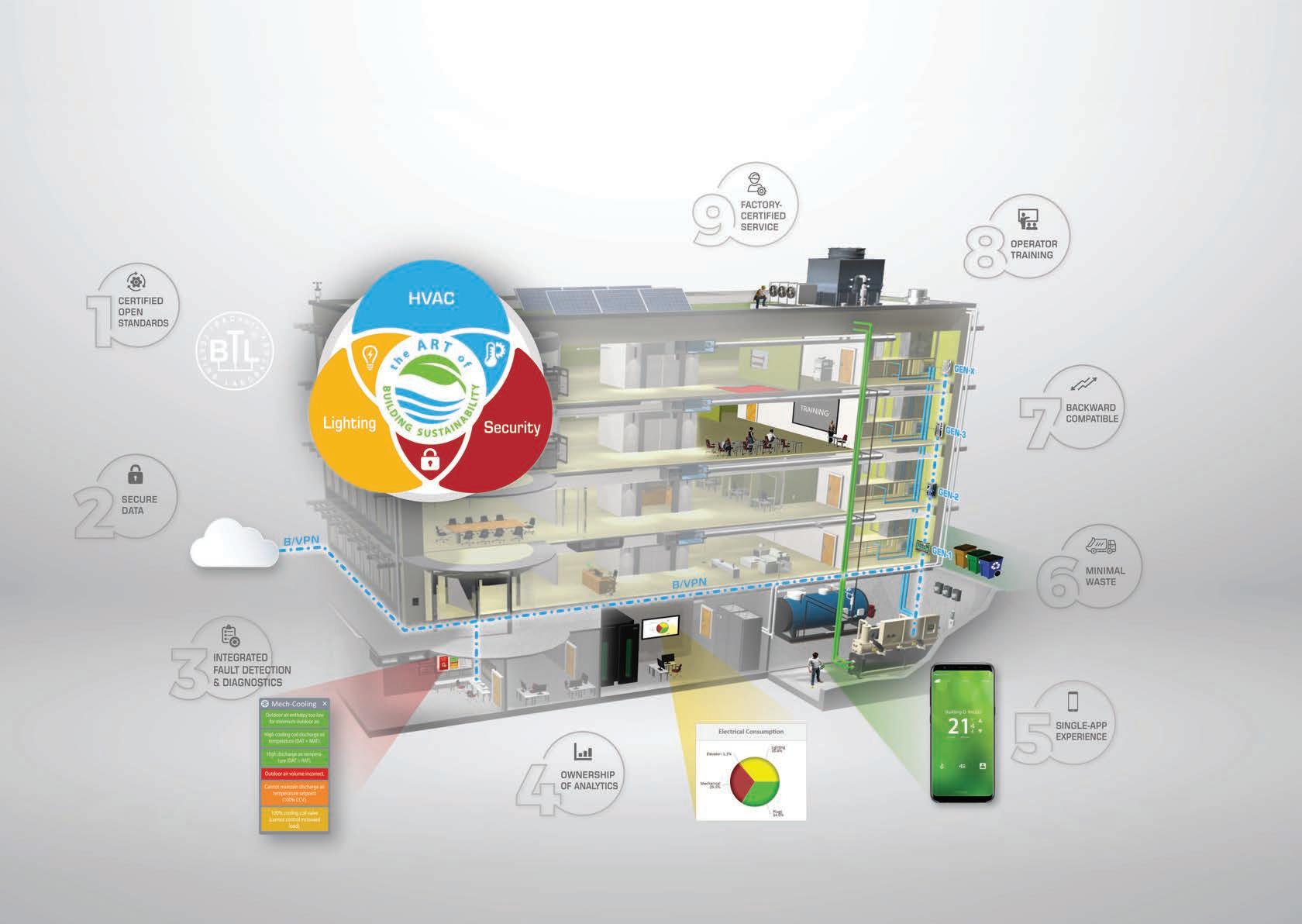
Select lifecycle-centric manufacturers who minimize the negative impacts of waste with long-term warranty and repair services while adhering to WEEE, RoHS and NABERS directives.
Create better-connected spaces with real-time access to occupancy, lighting, ventilation, and thermal comfort levels, using a holistic single app on the occupant’s mobile device.
KEYWATCHER
By David Ishak, AST Pty Ltd
EXPANDED ELECTRONIC KEY CONTROL WITH CUSTOM MANAGEMENT REPORTS
KeyWatcher is a versatile electronic key cabinet solution backed up by a powerful software interface that allows for the management of keys an organisation may consider high risk or may carry financial or liability. Security has become one of a facilities highest priorities, KeyWatcher gives you the peace of mind that you have control over your vital assets by completely controlling your keys right down to an individual user while providing detailed live data as well as full reporting and auditing.
THE INTEGRATED SOLUTION KeyWatcher is designed for complete interactivity with your other business systems. Your Access Control, HR and Contractor Management system can all be integrated to control access to your keys by providing details such as user information and access levels to our software. These interfaces can also have the ability to deny egress until a key is returned to the cabinet. Alarms and notifications are created for keys that are not returned on time and management can be notified immediately when critical keys are removed and returned.
KMAAS (KEY MANAGEMENT AS A SERVICE)
Hosted and Managed Services available
KMaaS has been designed and developed in Australia, not only to modernise and simplify the user experience, but it has brought key management back to the fore front of technology. KMaaS gives the KeyWatcher the flexibility to become a wireless installation, taking away the requirement for costly and needless IT infrastructure. Locking in the security of AWS KMaaS delivers a flexible and robust service which can include integration, web based user invitations and key reservations. All data is encrypted via a Telstra VPN for end to end privacy and security.

