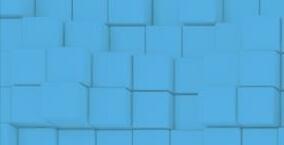
14 minute read
INKS, COATINGS, AND ADHESIVES
Stafford Corrugated Products, Inc.

Advertisement
Stafford Corrugated Products Is Your Number 1 Source for Parts, Accessories, and Technical Support
It’s a well-documented fact that the Corrugated Container Industry is a leading economic indicator of the overall strength of our economy. Th e strength of the Corrugated Industry in 2021 refl ects the tremendous growth of Staff ord Corrugated Products as well. Looking forward, we anticipate this growth to continue for both the industry and Staff ord. 2021 proved itself to be a very challenging year for both suppliers and producers of Corrugated materials. If there is one thing that the COVID-19 Pandemic has taught us, it is that the Corrugated Box is here to stay!
For more than 30 years, Staff ord Corrugated Products has been a resource to the Corrugated Industry as a supplier of quality replacement and consumable parts for all makes of Corrugated machinery. As a result, Staff ord has earned the reputation of being the “go-to” guys when it comes to seeking solutions to everyday maintenance and production needs for parts and equipment. On practically a daily basis, someone from our Technical Team will receive a message from a customer asking, “Do you guys make this?” From consumable parts to complete machinery enhancement systems, Staff ord has you covered. We are constantly adding new items to our ever-growing portfolio, and we look forward to adding even more as our industry continues to grow.
Staff ord is proud to off er our industry the RODICUT Die Cut Anvil Blanket. Th ere is a RODICUT Anvil Cover for every conceivable make of Rotary Die Cutter ever produced. Available in single width, double wide and almost every width in between, we’ve got you and your Rotary Die Cutter covered! Th e unique “knuckle locking” compression system makes these Anvil Covers the easiest to install as well as rotate. Made to meet or exceed OEM specifi cations, our Anvil Covers contribute to longer cover life and better quality fi nished die cut sheets. In addition, Staff ord’s team of Technical Sales Reps have a combined total of over 260 years of relevant industry experience. We are here to assist you and your operating crews to maximize your investments and maintain optimum uptime. Our knowledge base allows us to off er you in person training and troubleshooting of many common issues that box plants today must contend with. Is your Die Cutter equipped with a freewheeling, equalizing compensation system manufactured by a diff erent company? Staff ord has more total years of experience and can off er you training as well as spare and replacement parts.
Is your Cutting Die Cylinder littered with stripped holes or broken bolts? Are your operators unable to utilize every hole in the cutting die to get optimum performance? Staff ord off ers the service of sending fully trained crews to your facility and overhaul the entire cylinder. All of the existing inserts are removed and replaced and every hole on that cylinder is replaced with brand new inserts. Th is service is performed in your plant over a weekend when the machine is not running so as not to interfere with your production schedule. Your cutting die cylinder becomes brand new, once again!
Staff ord Corrugated Products wishes to thank our loyal customers for their trust and support. We look forward to working with you in 2022 and beyond.
For more information, please contact your local Staff ord Technical Sales/ Service representative or call our Customer Support Team at 800-2825787. Check out the most comprehensive and critically acclaimed product catalog in the industry on our web site at www. go2staff ord.com. And watch for the grand opening of our new World Headquarters and factory. A better and more effi cient way to serve you.
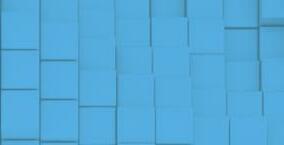

Stafford Cutting Dies, Inc.
Stafford Cutting Dies Enhances Product Delivery System
If you are tired of damaged or late cutting die deliveries, Staff ord Cutting Dies is the solution you are looking for. With 14 delivery vehicles positioned across 4 locations covering the southeast and northeast, we can deliver your dies on time, undamaged and press ready.
Additionally, this system allows us to pick up your cutting dies in need of repair or revision without the necessity to package them or contract with outside couriers. Our driver loads your tooling in our vans, takes them to our nearest service center for repair or revision, then returns them as requested, generating effi cient and timely turnaround times.
Give us an opportunity to show you how our enhanced delivery system can make your job easier.
Guy Earley Sales/Marketing Manager GuyE@gostaff ord.com 704-821-6330 www.gostaff ord.com
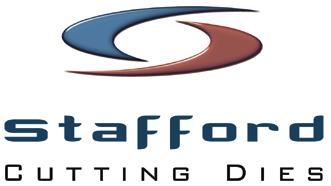
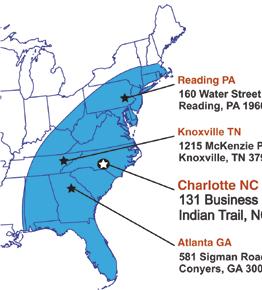


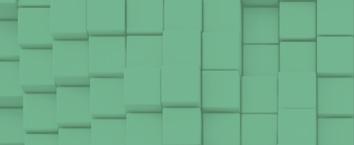
Flint Group Paper & Board
Sustainability in Paper & Board Packaging
When we look back at the history of packaging, sustainability is one of the landmark changes that has shifted not only how packaging is designed, developed and produced—but how it interacts with consumer needs and the world around us. What started as a ripple of change has become a tidal wave, and the drive for packaging to be “greener” is now front and center for brands, printers and consumers alike.
Th e statistics certainly back this up. A recent study by McKinsey & Company (mck.co/3yxn6Uq) found that 60 to 70 percent of consumers in the United States would be willing to pay more for sustainable packaging. Fifty-two percent of consumers said they would buy more sustainably packaged products if they did not cost more. Th e study also found that “consumers are more or less equally interested in recyclable and recycled plastic packaging and in fi berbased packaging.”
What this data tells us is that when the consumer is faced with two comparable like-for-like products, but one is perceived to have more sustainable packaging, they are more likely to choose the greener option. Should the two products be pitched at a similar price point, the advantage becomes even more pronounced. As sustainability is now playing a key part in purchase decisions, it becomes core to long-term brand strategy and commercial success.
Sustainability through the lens of an ink maker.
At Flint Group, our customers rely on our expertise to deliver more environmentally oriented solutions, without compromising on the performance and quality that’s essential to ensuring packaging retains its functionality along with brand integrity. We understand that talking a good game of sustainability is nothing if we can’t back it up with action and strategy that creates a better world.
For our team, that means developing a portfolio of products that is ethically managed, reduces overall ecological impact, is designed and built responsibly and supports the need for circularity, as the closed loop economy becomes the norm, not the exception.
Helping to ‘close the loop.’
Flint Group Paper & Board understands that not all brands and printers have the same sustainability objectives when selecting their inks and coatings. Th erefore, we have developed a range of products to ensure we meet a wide variety of customer needs.
INTRODUCING TERRACODE Responding to the specifi c needs of the paper and board packaging industry to deliver solutions for improved sustainability, packaging innovation and on-shelf presentation, as well as e-commerce supply chain robustness, Flint Group off ers a range of water-based inks and coatings under the TerraCode brand; a dynamic bio-renewable product off ering that can be tailor-made for converters’ individual printing needs.
SUSTAINABLE SOURCING OF FEEDSTOCKS An important consideration during TerraCode’s development program has been the sourcing of carefully selected feedstocks. Ethical debates have occurred globally related to crops, normally used for food production, being diverted to industrial applications. Th e United Nations estimates that nearly 1 billion people globally are suff ering food shortages. At Flint Group, we are acutely aware of the importance of ethical sourcing.
Flint Group believes a sustainable source is equally as important as the renewable content of a product. Th erefore, we have extended our strict raw material review policy to include renewable source information.
THE TECHNOLOGY Ensuring tailored solutions for specifi c printer converter and brand owner needs, Flint Group’s development teams have created three product series:
TerraCode Bio is designed with the highest level of bio-renewable content. Greater than 90% of the resin system is made from renewable resources. TerraCode Bio provides excellent print quality and press stability.
TerraCode Hybrid is a combination of renewable and conventional raw materials where a typical formulation contains in excess of 50% renewable resin content. Th e formulation has been balanced with highly eff ective synthetic ingredients for applications that require the maximum performance and protection.
TerraCode Balance is built on biomass balance technology and off ers the same performance as conventional acrylic systems.
Th e TerraCode range has been designed to support a wide variety of Paper & Board packaging applications that are biorenewable content (BRC) certifi ed through NAPIM and sustainably sourced. Th e range is available print-ready or via a convenient Flint Group building block package.
Please contact us to discuss how we can work with you to build a more sustainable tomorrow.
Deanna Klemesrud Global Marketing Director – Packaging Inks Deanna.klemesrud@fl intgrp.com 763-238-9216
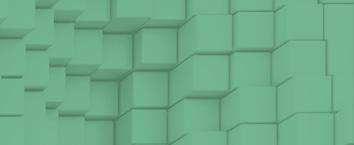
Astral Adhesives & Coatings, Inc.

Astral Innovates to Meet Customer Needs | Quick Response to Supply Chain Challenges and Introduction of New Products are Highlights of 2021
Astral Adhesives & Coatings, Inc. continues to be a leading supplier to the packaging industry, providing customized coatings for the paper and paperboard market. Th is past year presented many challenges within the supply chain and distribution, and Astral responded by creating custom solutions to ensure clients had everything they needed to run their business.
By operating out of two manufacturing facilities centrally located in the United States, Astral has double the operations capabilities and overlapping inventories. Th is production model has helped the company meet customer needs on time and with full service, despite slower shipping times, raw materials shortages, and bearing occasional additional freight costs to ensure there are no disruptions at the customer level.
“Having redundant manufacturing capabilities has helped us weather the storm successfully,” said Vikas Singhal, president of Astral Adhesives & Coatings, Inc. “We are operating in the most diffi cult environment I’ve seen in my 30 years in the business. Supply challenges coupled with freight constraints make it an unparalleled operating environment.
“Astral joins many in the industry who report frequent price increases. Th is has put pressure on margins, while continued shortages make planning diffi cult. Labor availability also continues to be an issue. Yet, despite these challenges, we have been able to introduce new products, grow our top line, and increase our market share. We are well positioned to support the packaging industry going forward.”
Th e company is working on various new opportunities in the “take out” folding carton market, heat seal, and anti-corrosion markets. In addition, Astral has entered the “cohesive” market with an exciting new product that has been fully commercialized. Recyclable and durable products highlight Astral’s multipurpose coating line, changing the way consumers bring home meals and essential food items.
A long-time industry leader, Astral’s principals have more than 50 years of experience in the coatings business and are committed to fi nding solutions to the most challenging projects. Groundbreaking technologies in the paperboard industry and coating formulas come together to create sustainable, superior products.
Singhal credits his customers for driving Astral’s pioneering approach to creating new products.
“We are always changing and growing as a company, mainly because we listen to our clients, so we know specifi cally what they need,” Singhal said. “By partnering with our customers, we are able to create the customized new products they need to succeed in their business, which helps us lead the way in the paperboard packaging industry.”
Contact: Vikas Singhal President vikas@astralcoatings.com 562-676-5607

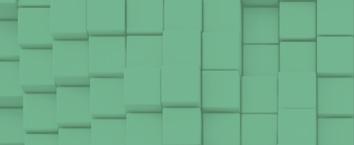
BCM Inks
Color ConneXion®/MyInkIQ – The ecommerce software solutions for better printed corrugated boxes
According to eMarketer, ecommerce in 2021 was expected to grow at 17.9%, on top of an unparalleled growth of 32.4% in 2020. As ecommerce grows, so does the demand for ecommerce boxes to showcase print on the inside and outside of the box to capture the “unboxing” experience for the consumer. Printing on the inside and outside of the box in one pass does present some unique challenges such as: • Color consistency, particularly if inside and outside of package are diff erent substrates • Scuff and rub resistance, as the print transitions from inside to outside print • Specialized coating requirements, needed to enhance and/or protect the package
BCM Inks products, expertise, and exclusive software (Color ConneXion® and MyInkIQ) provide a total solution so printers can maximize the ability to print on the inside and outside of the box effi ciently and eff ectively.
In 2016, BCM introduced a revolutionary online color management software, Color ConneXion®. Color ConneXion® is updated and enhanced on a regular basis with new features through over-the-air software updates. Today, we are proud to introduce the most recent version of Color ConneXion® which includes some of the following unique features: • Designed specifi cally for the corrugated market • Remote color approvals • User friendly • Unlimited seat licenses • Remote access • Information is backed up safely and securely to the cloud • Ability to pair with multiple spectrophotometers • Job building functionality based off press and anilox roll confi gurations • Ability to store pH, viscosity, and dryer settings for future reference and better repeatability • Individual and job reporting functionality • Historical reporting functionality • Suggestive color correction • Enhanced communication within the departments
Printers have recognized a reduction in waste, reduced downtime, faster set-ups, and more consistent color after implementing Color ConneXion® software.
BCM’s other exclusive software, MyInkIQ, allows users to easily submit orders and color matches online. Once the order or color match is submitted, the user receives updates throughout the process until delivery. Th e MyInkIQ also provides easy access to the color/formula library to eliminate color/formula duplication. Users have the ability to run sales and VOC reports and view order history, amongst many other features.
To learn more about our ecommerce printing solutions, our software solutions, or our many ink innovations, contact BCM Inks at 800-678-6238 or sales@bcminks.com. sales@bcminks.com 800-678-6238 www.bcminks.com
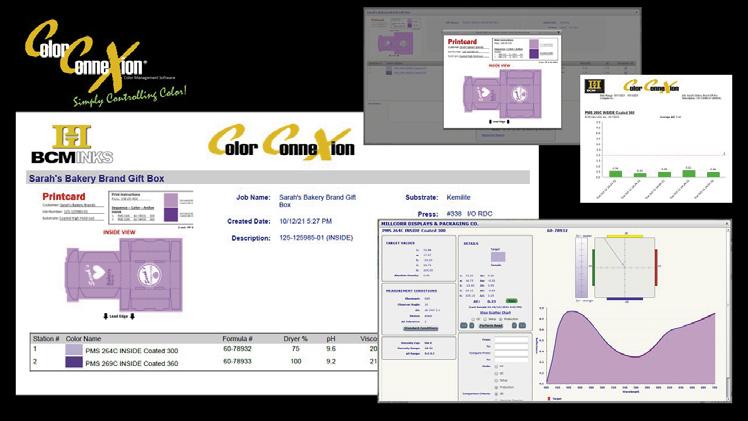
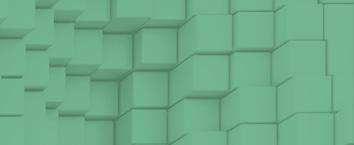
INX International Ink Co.

INX International Ink Co. is a global manufacturer of high-performance printing inks and coatings for pack-
aging, digital, and commercial print
applications. We bring global brands a strategic advantage no other ink manufacturer in the world can match. From chemical formulation to best manufacturing practices; from technical innovation to fi eld service and support; from all types of printing inks and coatings to new digital platforms; INX International stands ready with global capabilities and local solutions.
We off er a wide range of inks, coatings, and overprints for various methods of corrugated printing—from simple brown box needs, to specialized high-end graphics on demanding substrates. Whether your printing project requires simple line work, a few vignettes, or complex color combinations with process work; we have the perfect corrugated ink system. Our
latest system INXhrc off ers a high renewable content, which provides excellent print quality, combined with sustainability.
Our BECB-05 and BSR-06 UV curable inkjet inks are optimized for use on Barberán Jetmaster single-pass industrial printers for corrugated and plastic printing with numerous end applications. Th e high-performance inks consist of standard CMYK colors with Orange + Green or Orange + Violet as an option when wider color gamut is required. We also off er an opaque white. Th ese are extremely low odor, and have high durability, excellent rub resistance, and superior fl exibility to reduce cracking and chipping during die cutting.
Along with advanced product technology, INX delivers a range and level of services unlike other major ink manufacturers, beginning with an entire group of application specialists to help improve pressroom effi ciencies and reduce costs. From pressroom assessments and press fi ngerprinting, to product selection and trial support with continuous improvement recommendations, our technical team takes a proactive approach to service. Our structured approach focuses on increased effi ciencies and throughput, waste reduction, quality improvements, and lower applied costs.
Contact our sales team at: info@inxintl.com 800-631-7956
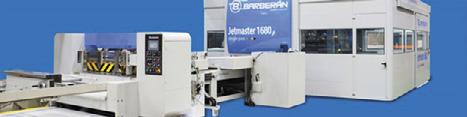
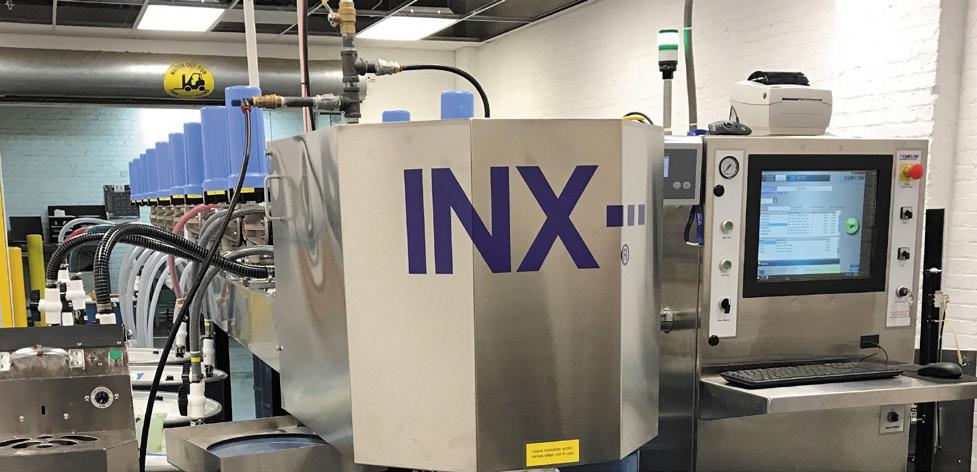