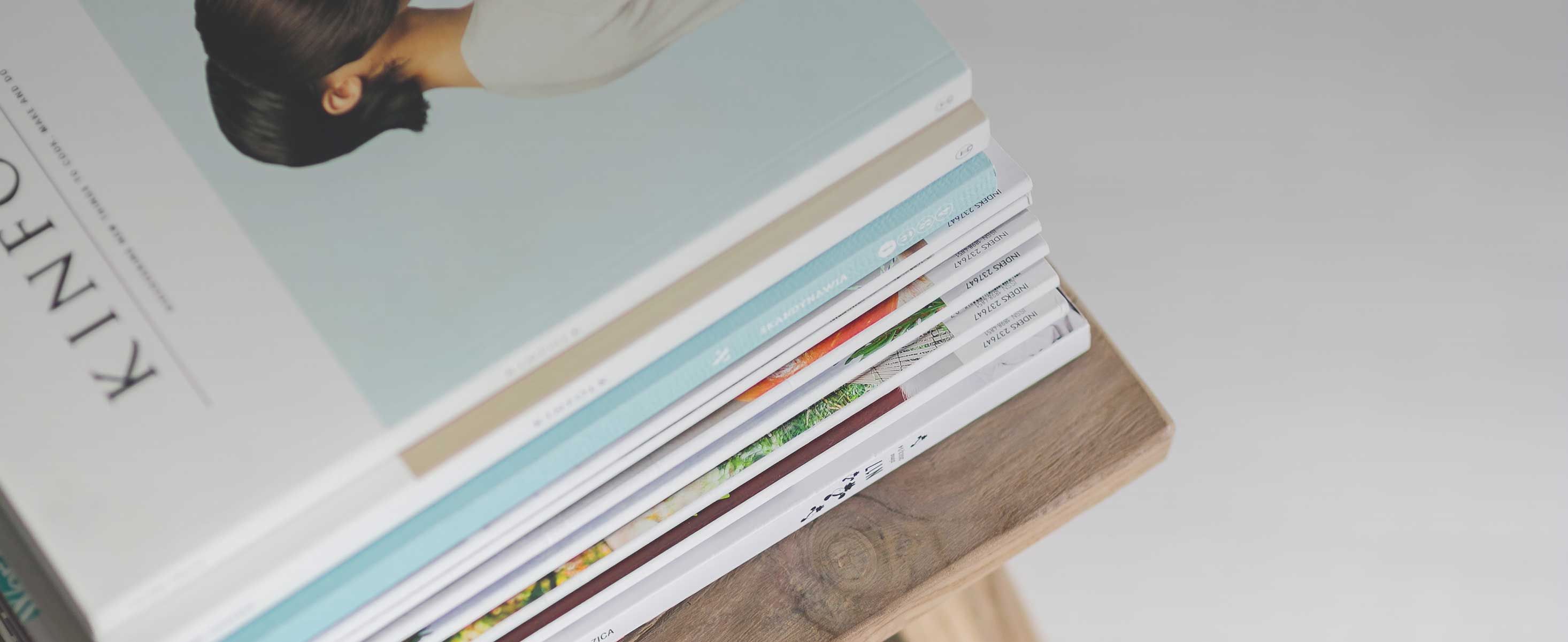
3 minute read
SPECIAL SECTION CORRUGATED WEEK 2022
blows, which is a much bigger, more expensive problem.
Effi ciency Meets Quality
Advertisement
Th e key to benefi ting fully from cleaning and drying automation is accomplishing time savings alongside maintaining the overall print quality that brands and consumers have come to expect.
Operators generally spend huge amounts of time cleaning and are nonproductive at all stages of the process. It can take 10 or 15 minutes for each plate every time to stop. And that’s for each and every print job that could happen multiple times throughout the shift. Imagine having a four-, fi ve-, or six-color print job and that most of these machines are anywhere from 2.1 to 2.8 meters wide; it’s an extremely time-consuming task to accomplish manually.
During the production run, a huge amount of time is lost from stopping the machine to clean hickeys off and to clean debris from the printing plate in order to maintain print quality, the demand for which is ever-increasing from customers. Th is all contributes to a loss of operating effi ciency.
Printers are reliant on their operators to go into the unit to clean off the defects and get the machine running again. It’s all lost time on a regular basis—on every job, every shift, every day, many, many times over.
Automation removes all the manual requirements to clean and dry the plate, accomplishing it instead with just a push of a button in one pass, with the ability to clean and dry each and every plate singly or consecutively throughout the machine. All the ink and all the paper fi bers can be easily captured in each clean in a matter of minutes—with systems that require only seconds of contact with the printing plate in the production room—versus 10 minutes on average with each stop for an operator to do it manually.
Today’s state-of-the-art automated cleaning technology can save around 98% of time from stopping the press during production and 80% of time lost at the beginning and end of a print run, so the ROI is signifi cant.
Looking Ahead
Over the past few years, the corrugated industry has seen a sharp rise in the demand for increased print quality and complexity. Printers are seeking presses with more print units to achieve this quality work and the complexity of color. With that, there has been a trend of integrating lots of energy into presses to achieve a better drying eff ect. It’s a common misconception that more and more power and even bigger, wider cassettes are needed to achieve a strong drying result.
Tests have shown that there can be too much energy fl owing into the ink and that having a large module— or lots of energy per print unit— can be counterproductive as the ink fi lm layer can only absorb so much energy. Overheating can also result in pigment melting, which reverses the drying eff ect. A more targeted system—intelligently controlled, closed-loop, and with minimal intervention—is the most effi cient and best-performing solution.
Beyond profi tability, companies are continually striving to be more sustainable, and the two can be achieved hand in hand with good, reliable, proven equipment. Case by case, we hear from printers using state-of-the-art cleaning and drying technologies that they are reaping the benefi ts by hitting targets that they’ve never hit before in production. We’re also having many repeat customers come back for new machines that they’re investing in and for retrofi tting old machines.
Th ere’s a need for printers to adapt and invest in the latest automated technology to increase time and to become more competitive. Th ere’s no doubt that these technologies will become a standard installation on new machines in the future, and the trend is already evident.
On the cutting edge, alongside cleaning and drying technology, are inspection systems that complete a fully closed-loop system that can further enhance both productivity and quality. Th ose on the forefront of the next revolution are analyzing data and measuring metrics through connected machines and IoT technology.
Myles Le-Monte
Shepherd is a sales executive, new markets, at Baldwin Technology.
Lee Simmonds is sales manager, U.K., Ireland, and Nordic regions, at Baldwin Technology.